不锈钢配管焊接区腐蚀原因分析
不锈钢焊缝腐蚀原因及处理方案

不锈钢焊缝腐蚀原因及处理方案
不锈钢焊缝腐蚀是指在不锈钢焊接过程中,焊缝处出现的腐蚀现象。
这种腐蚀会导致不锈钢焊接件的使用寿命缩短,甚至出现安全隐患。
不锈钢焊缝腐蚀的原因主要有以下几点:
1. 焊接时产生的气孔、夹杂物和氧化皮等缺陷会破坏不锈钢的保护膜,从而形成腐蚀点。
2. 不锈钢焊接时,由于热影响区的晶粒尺寸增大,导致晶间腐蚀的发生。
3. 在高温高压环境下,不锈钢焊缝处容易发生应力腐蚀开裂。
针对不锈钢焊缝腐蚀问题,可以采取以下的处理方案:
1. 选择优质的不锈钢焊接材料,并严格控制焊接工艺,避免在焊接过程中产生缺陷。
2. 在不锈钢焊接过程中,采用合适的保护气体,减少氧化皮的产生,从而提高不锈钢的耐腐蚀性能。
3. 针对晶间腐蚀问题,可以采用焊缝后热处理的方法,使晶粒尺寸重新变小,降低晶间腐蚀的发生。
4. 针对应力腐蚀开裂问题,可以通过降低焊接件的应力水平来减少应力腐蚀开裂的风险。
总之,要想有效解决不锈钢焊缝腐蚀问题,必须从材料、工艺和环境等多个方面进行综合考虑,采取相应的措施来降低腐蚀的风险,提高不锈钢焊接件的使用寿命。
- 1 -。
不锈钢腐蚀原因及预防措施详解

不锈钢腐蚀原因及预防措施详解一、不锈钢引起点蚀的因素及防止措施不锈钢极好的耐腐蚀性能是由于在钢的表面形成看不见的氧化膜,使其成为是钝态的。
该钝化膜的形成是由于钢暴露在大气中时与氧反应,或者是由于与其他含氧的环境接触的结果。
如果钝化膜被破坏,不锈钢就将继续腐蚀下去。
在很多情况下,钝化膜仅仅在金属表面和局部地方被破坏,腐蚀的作用在于形成细小的孔或凹坑,在材料表面产生无规律分布的小坑状腐蚀。
出现点蚀很可能是存在与去极剂化合的氯化物离子,不锈钢等钝态金属的点蚀常起因于某些侵蚀性阴离子对钝化膜的局部破坏,保护有高耐腐蚀性能的钝态通常需要氧化环境,但正好这也是出现点蚀的条件。
产生点蚀的介质是在C1-、Br-、I-、ClO4-溶液中存在Fe3+、Cu2+、Hg2+等重金属离子或者含有H2O2、O2等的Na+、Ca2+碱和碱土金属离子的氯化物溶液。
点蚀速率随温度升高而增加。
例如在浓度为4%-10%氯化钠的溶液中,在90℃时达到点蚀造成的重量损失最大;对于更稀的溶液,最大值出现在较高的温度。
防止点蚀的方法:(1)避免卤素离子集中。
(2)保证氧或氧化性溶液的均匀性,搅拌溶液和避免有液体不流动的小块区域。
(3)或者提高氧的浓度,或者去除氧。
(4)增加pH值。
与中性或酸性氯化物相比,明显碱性的氯化物溶液造成的点蚀较少,或者完全没有(氢氧离子起防腐蚀剂的作用)。
(5)在尽可能低的温度下工作。
(6)在腐蚀性介质中加入钝化剂。
低浓度的硝酸盐或铬酸盐在很多介质中是有效的(抑制离子优先吸咐在金属表面上,因此防止了氯化物离子吸咐而造成腐蚀)。
(7)采用阴极防腐。
有证据表明,用与低碳钢、铝或锌电隅合阴极保护的不锈钢在海水中不会造成点蚀。
含钼2%-4%的奥氏体型不锈钢具有良好的耐点蚀性能。
使用含钼奥氏体型不锈钢可显著减少点蚀或一般腐蚀,腐蚀介质例如氢化钠溶液、海水、亚硫酸、硫酸、磷酸和甲酸。
二、不锈钢的晶间腐蚀及预防措施含碳量超过0.03%的不稳定的奥氏体型不锈钢(不含钛或铌的牌号),如果热处理不当则在某些环境中易产生晶间腐蚀。
304不锈钢焊接位置生锈处理

304不锈钢焊接位置生锈处理问题描述304不锈钢是一种常见的金属材料,因其耐腐蚀、美观大方而被广泛应用于各种工业和家居领域。
然而,在某些情况下,304不锈钢焊接位置可能会出现生锈现象,这不仅影响其美观,还可能影响其结构和功能。
因此,对于304不锈钢焊接位置生锈的处理显得尤为重要。
原因分析304不锈钢焊接位置生锈的原因可能包括以下几点:1. 焊接过程中的高温导致金属表面氧化层的形成,从而影响了不锈钢的抗腐蚀性能。
2. 焊接过程中未能完全清除金属表面的污垢和油脂,这些污垢和油脂会加速不锈钢的腐蚀。
3. 焊接后的处理不当,如未能及时进行酸洗或抛光处理,导致不锈钢表面受损。
4. 使用环境湿度较高或存在腐蚀性介质,如盐分、酸性气体等,加速了不锈钢的腐蚀。
处理方法针对304不锈钢焊接位置生锈的问题,可以采取以下处理方法:1. 酸洗处理:使用酸洗液如硝酸、硫酸等对不锈钢表面进行清洗,去除表面的氧化层和污垢。
酸洗液的浓度和时间需根据具体情况进行调整,以达到最佳效果。
2. 抛光处理:使用抛光机或砂纸等工具对不锈钢表面进行打磨,去除表面的划痕、氧化层和不平整区域。
抛光过程中需注意控制力度和方向,避免对金属表面造成过度磨损。
3. 钝化处理:在不锈钢表面涂覆一层钝化膜,增强其抗腐蚀性能。
钝化处理可以采用热浸镀、电镀、化学镀等方法,根据具体情况选择合适的处理方式。
4. 使用防锈涂料:在不锈钢表面涂覆一层防锈涂料,隔绝金属表面与外界环境的接触,从而起到防止生锈的作用。
防锈涂料的选择应考虑其与基材的相容性、耐磨性、抗腐蚀性等因素。
5. 提高焊接质量:优化焊接工艺参数,提高焊接接头的质量和致密性,减少焊接缺陷和气孔等问题的出现。
同时,加强焊接过程中的质量控制,确保每个环节都符合规范要求。
6. 加强使用环境的管理:尽量避免将不锈钢置于潮湿、盐雾等恶劣环境中,如无法避免则应采取相应的防护措施,如使用防水涂层、阳极氧化等。
7. 定期维护保养:定期对不锈钢表面进行清洗、检查和维护,及时发现并处理存在的问题,确保其长期保持良好的使用状态。
不锈钢设备点腐蚀原因分析与防护措施

从而相对于晶内的铬更为活泼。 如果存在水溶液条件 , 就形成了以课露的铬为 阳极 , 以不锈钢为阴极的原电池。 大的阴极面积产生了阳极控制, 因而腐蚀作 用很严重, 导致晶问破裂或点蚀。 这称之为 “ 焊接接头晶间腐蚀”这种钢称之 , 为“ 活化处理 的钢。 采用低碳的奥氏体不锈钢可以减轻这个问题 。 钝化膜是保护不锈钢的主要屏 障, 但另一方面具有钝化特性的金属或 合金 , 钝化能力越强则对点蚀的敏感性越高, 不锈钢较碳钢易发生点腐蚀就
2 不锈钢 的点 腐蚀 机理 、
在 金 属表 面 局部 地 方 出现 向深 处 发展 的腐 蚀小 孔 , 余表 面 不腐 蚀 或 其
腐蚀很轻微, 这种形态成为小 孔腐蚀, 简称点蚀 , 又称孑蚀 。 L 金属腐蚀按机 理 分为 化学 腐蚀 和 电化 学腐 蚀 。 腐蚀 属 于 电化学 腐蚀 中的局 部腐 蚀 。 种 点 一 点蚀是由局部充气电池产生 , 类似于金属的缝隙腐蚀。 另一种更常见的点蚀 发生在有钝化表现或被高耐蚀性氧化物覆盖的金属上 。 21 . 、不锈钢 的耐腐蚀 原理 不锈钢的重要因素在于其保护性氧化膜是 自愈性的 ( 例如它不象选择 性氧化而形成的那些保护性薄膜)致使这些材料能够进行加工而不失去抗 , 氧化性。 合金必须含有足够量的铬以形成基本上由C , rO 组成的表皮 , 以便 当薄膜弄破时有足够数目的铬( r ) c 阳离子重新形成薄膜 。 如果铬的比例低 于完全保护所需要的比例 , 铬就溶解在铁表面形成的氧化物 中而无法形成有 效保护膜。 起完全保护作用所需的铬的 比例取决于使用条件 。 在水溶液中, 需要1 的铬产生 自钝化作用形成包含大量c 2 rO 的很薄的保护膜。 在气态氧 化条件下,低于 10 " ,1 00 C时 2的铬有很好的抗氧化性,在高于 10  ̄时, 00 1的铬也有很好的抗氧化 陛。 7 当金属含铬量不够或某些原因造成不锈钢 晶界 出现贫铬 区的时候 , 就不能形成有效的保护性膜。 22 . 、氯离子对不锈钢钝化膜的破坏 处于钝态的金属仍有一定的反应能力, 即钝化膜 的溶解和修复 ( 再钝 化) 处于动 平衡状态。 当介质 中 含有活性阴离子 ( 的如氯离子 ) , 常见 时 平 衡便受到破坏 , 溶解占优势。 其原因是氯离子能优先地有选择地 吸附在钝化 膜上 。 把氧原子排挤掉 , 然后和钝化膜中的 阳离子结合成可溶性氯化物, 结 果在新嚣 出的基底金属的特定点上生成小蚀坑 ( 孔径多在2 ~ 0 m)这 O 3¨ , 些小蚀坑称为孔蚀核, 亦可理解为蚀孔生成的活性中心。 氯离子的存在对不 锈 钢 的钝态 起 到直 接 的破 环作 用 。
大直径不锈钢管道运行过程的腐蚀分析及处理措施

图5 管道 内壁充气保护措 施图
晶间腐蚀 , 造 成晶界 的耐腐蚀性下 降。 其次 , 热裂纹 的形
成也与焊接过程有 着非常大 的关 系, 检验结 果表 明焊缝 成 型歪歪扭扭 焊道 忽大 忽小 , 由此可见焊接 过程经 常停 顿, 以致局部熔焊区域金 属补充困难 , 熔焊金属凝固时形
一
该大型综合性场馆 自从投入使用后一直处于间隔性
使用状 态 ,从更换取样管段发现管道 内沉积物较多 ,说
明管道 系统在 日常 的使用 中没有做到定期 冲洗和除氯 , 加之焊后对管道 内壁焊缝表 面进行打磨抛光后残存微小 裂纹 、夹杂及 表面气孔 等缺 陷 ,使得焊缝融合线 、热影 响区成 为氯离 子作用下 的点蚀形核 区域 ,随着管 内沉积 物的不断增加越来越加重对 管壁及 焊缝 的腐蚀 。
通过 以上工艺处理措施 的应用 ,该不 锈钢给水管道 系统重新安装投入使用至今 ,系统管道运行正常 ,未再
成显微 热裂纹。 当氯 离子或 其他微 量的酸、 碱、 盐的溶解
物 与上 述有缺 陷的焊缝 表面接触 时, 就会 引起该处 的电
出现 由于点腐蚀导致管道破损失效的现象 。
化学腐蚀的产生 。 另外 , 不锈钢表面的各种缺陷如表面硫 化物夹 杂、 晶界碳化 物沉积 、 表面沟槽 处等地方, 氧化 膜
仍可能再钝化 , 若再钝化阻力小, 蚀孔就不再长大。 当受
到促 进 因素影响, 小蚀孔继续长大 至—定临界尺寸时, 金 属表面出现宏观可见的蚀孔 , 这个特定点成为孔蚀源 。 蚀 孔—旦形成则加速生长 。
5 6
2 0 1 3 年 第8 期
点蚀容易发生 ,而后又容易加 速进行 。 3 . 2 焊 缝缺 陷加速 腐蚀 生成
不锈钢管腐蚀开裂分析
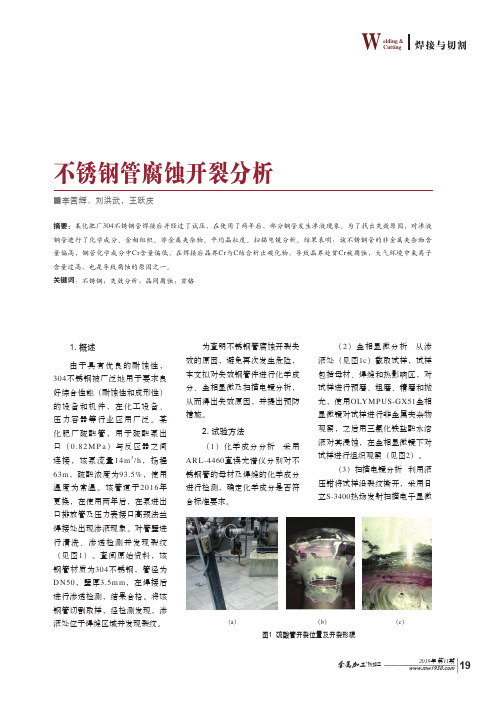
2019年 第11期热加工W焊接与切割elding & Cutting19不锈钢管腐蚀开裂分析■李国辉,刘洪武,王跃庆摘要:某化肥厂304不锈钢管焊接后并经过了试压,在使用了两年后,部分钢管发生渗液现象。
为了找出失效原因,对渗液钢管进行了化学成分、金相组织、非金属夹杂物、平均晶粒度、扫描电镜分析。
结果表明:该不锈钢管的非金属夹杂物含量偏高,钢管化学成分中Cr 含量偏低,在焊接后晶界Cr 与C 结合析出碳化物,导致晶界处贫Cr 被腐蚀,大气环境中氯离子含量过高,也是导致腐蚀的原因之一。
关键词:不锈钢;失效分析;晶间腐蚀;贫铬1. 概述由于具有优良的耐蚀性,304不锈钢被广泛地用于要求良好综合性能(耐蚀性和成形性)的设备和机件,在化工设备、压力容器等行业应用广泛。
某化肥厂硫酸管,用于硫酸泵出口(0.82M P a )与反应器之间连接,该泵流量14m 3/h ,扬程63m ,硫酸浓度为93.5%,使用温度为常温。
该管道于2016年更换,在使用两年后,在泵进出口排放管及压力表接口高颈法兰焊接处出现渗液现象。
对管壁进行清洗、渗透检测并发现裂纹(见图1)。
查阅原始资料,该钢管材质为304不锈钢,管径为D N50,壁厚3.5m m ,在焊接后进行渗透检测,结果合格。
将该钢管切割取样,经检测发现,渗液处位于焊缝区域并发现裂纹。
为查明不锈钢管腐蚀开裂失效的原因,避免再次发生危险,本文拟对失效钢管件进行化学成分、金相显微及扫描电镜分析,从而得出失效原因,并提出预防措施。
2. 试验方法(1)化学成分分析 采用A R L-4460直读光谱仪分别对不锈钢管的母材及焊缝的化学成分进行检测,确定化学成分是否符合标准要求。
(2)金相显微分析 从渗液处(见图1c )截取试样,试样包括母材、焊缝和热影响区,对试样进行预磨、粗磨、精磨和抛光,使用OLYMPUS-GX51金相显微镜对试样进行非金属夹杂物观察,之后用三氯化铁盐酸水溶液对其浸蚀,在金相显微镜下对试样进行组织观察(见图2)。
316L不锈钢管道腐蚀原因分析及预防措施

@>Q R 不锈钢管道腐蚀原因分析及预防措施!!毕航铭!中海福陆重工有限公司"广东!珠海!+!'$+$#摘要!针对南海某采油平台投产前不锈钢管道腐蚀的问题"进行取样分析$试验所得结论为氯离子含量超标导致不锈钢管线腐蚀严重$本文探究了氯离子对&!(B 不锈钢管线造成破坏的基本原理"同时"从海洋平台管线建造角度出发"针对如何有效预防不锈钢管线腐蚀问题提出建议"为后续海洋平台建造项目提供借鉴$关键词!&!(B 不锈钢&氯离子&点蚀&南海中图分类号 D W '..-"文献标志码*文章编号 "$'+,"',!"$"&#$$&$$(!"# !$-!"$.,'/001-"$'+,"',-"$"&-$%-$+8-'/;&#&"04*%$%'&"-"0."(("&#"-'-!+(%S %-4#"-J %'&B (%&0"(@>Q R14'#-/%&&14%%/+#2%/#-%=C3A 9:O 79:E =G G >=T ]?.+'c $&79S *J .8('/$8=+H 0I (J H 0e 2.2&/L !f ;L ;0N .&*3J +*30=2/*&F 89&4(')4!D H 0S /N N /L 7/9/@L 1A 79K 0L L L 100K I 7I 79:@/N A I N 0X S /O O 7L L 7/979:/@@L H /N 0I K A 1@/N O 791H 0G /?1H [H 79A G 0A 7L L A O I K 08A 98A 9A K P U 08R D H 0S /9S K ?L 7/9/J 1A 7908@N /O1H 010L 17L 1H A 11H 0S H K /N 7807/9S /910910h S 008L 1H 0L 1A 98A N 8K 0A 879:1/L 0N 7/?L S /N N /L 7/9/@L 1A 79K 0L L L 100K I 7I 0K 790L R D H 7L I A I 0N 0h I K /N 0L 1H 0J A L 7S I N 79S 7I K 0L /@8A O A :0S A ?L 08J P S H K /N 7807/9L 1/&!(BL 1A 79K 0L L L 100K I 7I 0K 790R a N /O1H 0I 0N L I 0S 17Q 0/@/@@L H /N 0I K A 1@/N O I 7I 0K 790S /9L 1N ?S 17/9;@/N H /M1/0@@0S 17Q 0K PI N 0Q 091S /N N /L 7/9/@L 1A 79K 0L LL 100K I 7I 0K 790L ;M 0I ?1@/N M A N 8N 0K 0Q A 91N 0S /O O 098A 17/9L ;A 98I N /Q 780N 0@0N 09S 0@/N L ?J L 0e ?091/@@L H /N 0I K A 1@/N OS /9L 1N ?S 17/9I N /Y0S 1L R :%;<"(!&!L 1A 79K 0L L L 100K &!(K V S H K /N 7907/9V I 71179:0N /L 7/9V 1H 0G /?1H[H 79A G 0A =!引!言在海洋%电厂%化工过程%采矿%石油化工%油气%医药等许多工程应用中"因为&!(B 不锈钢具备优异的耐腐蚀性能%良好的耐高温氧化及耐热性等工程性能"同时也具备优良的焊接性能"极大地吸引了许多研究人员%工程师%制造商以及产品的最终用户的关注"在海洋平台管线中广泛应用于淡水管线%饮用水管线%化学药剂注入管线等+!$,,$目前"国内外研究主要从海水温度%溶解氧%海洋微生物%流速和盐度等方面探究了不锈钢在海洋环境下的腐蚀行为"从不同角度列举了不锈钢在耐腐蚀方面的研究进展$针对本文案例"主要从盐度方面来分析不锈钢管线发生点蚀的成因+.$!",$南海某平台淡水系统管线材料为*G D ^*&!"'*&!"^标准中D ]&!('&!(B 型不锈钢$平台在陆地建造阶段"管线试压用水经过严格水质检测"[K v浓度低于"+I IO &平台出海之后"该管系输送淡水$但在平台试运行阶段出现了不锈钢管道泄漏$经检测"泄漏处水样[K v浓度为"($O :'B "严重超标$通过现场取样"并对泄露段不锈钢管线材质进行化学成分检查%非金属夹杂物检查%显微组织检查等"!基金项目(中国海洋石油集团有限公司/&$$米水深级导管架设计及建造关键技术研究0![4Z Z [X b g !&+5g g G ".5["$"$X $!#$作者简介(毕航铭!!''&)!#"男"硕士研究生"助理工程师"主要从事导管架及海洋平台方面的研究$W X O A 7K (%&,$+&+',"e e -S /O $第!$卷!第%期!"$"&年!"月海洋工程装备与技术Z [W *4W 45C 4W W \C 45W >)C ]^W 4D*4<D W [34Z B Z 5_`/K -!$"4/-%<0S -""$"&第%期毕航铭(&!(B不锈钢管道腐蚀原因分析及预防措施*&!!*!判定管道泄漏原因为管壁发生了由内而外的点蚀$在管道腐蚀点处"有积液痕迹$当水汽蒸发时"[K v 浓缩"积液处[K v浓度会升高"即使&!(B不锈钢本身具备较强的耐腐蚀性能"在此[K v超标的情况下"极易发生点蚀+!,"蚀穿管壁并破坏表面油漆涂层"出现泄漏$本文基于以上案例"从建造角度分析事故原因"并提出有效的预防措施"供今后工程项目参考$>!分析方法截取长约!+$O O泄漏管段试样"如图!所示"分别进行化学成分分析检查%材料点腐蚀试验%穿孔外观检查%非金属夹杂物检查%显微组织检查%扫描电镜及能谱分析检查等"分析管道失效原因$可初步判断泄露管段上的腐蚀类型为点蚀"点蚀处孔洞内外径大小不一致"内小外大"且管段外表面以穿孔为圆心"均匀向周围扩散$图!!泄漏管段a7:-!!B0A T A:0I7I0K790!-!!化学成分分析检查采用火花直读光谱仪!赛默飞世尔D H0N O/C[*](&$$#分析试验件原材料化学成分"分析结果如表!所示$经与*G D^*&!"'&!"^"$!'中标准值分析比对"确认该试验件原材料合格$表>!原材料化学成分分析结果 <4E T6'9E>!.*%7#)'/)"72"#"-'-'/;&#&"0('<7'4%(#'/ <4E T元素[G7^9]G[N47^/标准值&$-$&+&!-$$&"-$$&$-$%+&$-$&$!(-$$$!.-$$!$-$$$!%-$$"-$$$&-$$穿孔一侧管材$-$!($-&.$-'($-$&+$-$!%!(-++!$-$."-$&未穿孔一侧管材$-$!($-&.$-',$-$&,$-$!%!(-+'!$-$'"-$&判断合格合格合格合格合格合格合格合格!-"!材料点腐蚀试验为验证管材的抗点腐蚀性能"分别从穿孔一侧和未穿孔一侧取样"按5='D!,.',"$!(中的方法*"使用!$$:a0[K&*(3"Z溶解于'$$O B3"Z 中"制成溶液"在""d下进行,"H腐蚀试验$试验后观察管材内表面"未穿孔一侧的管材除在数字记号/"0内发生轻微腐蚀"其余位置无腐蚀"如图"所示&穿孔一侧未发生腐蚀"如图&所示$该实!!!A#试验前!J#试验后图"!未穿孔侧管线内壁a7:-"!C990N L?N@A S0/@I7I0M71H/?1K0A T A:0I/791验表明"材料本身具备抗点腐蚀的能力"记号内的轻微腐蚀是由于附着异物引起的"原材料本身无问题$!A#试验前!J#试验后图&!穿孔侧管线内壁a7:-&!C990N L?N@A S0/@I7I0M71H K0A T A:0I/791!-&!穿孔外观检查使用体视显微镜!奥林巴斯G2r!(#观察穿孔"孔洞呈现阶梯状"内壁孔径最小"外壁孔径最大"外表面的腐蚀以穿孔为圆心"以波纹状向周围扩散"如图%所示$根据点蚀扩散控制模型理论+","该穿*&"!*海洋工程装备与技术第!$卷孔宏观外形符合点蚀特征$图%!穿孔外观a 7:-%!3/K 0A I I0A N A 9S 0!-%!非金属夹杂物检查根据点蚀发生的原理"点蚀优先在金属钝化膜的某些敏感位置成核+","包括钝化膜薄弱区%晶格缺陷晶界%非金属夹杂!硫化物夹杂#等$因此"对测试件进行非金属夹杂物检查$分别检查未穿孔一侧管材%腐蚀坑周围的非金属夹杂物"详见图+%($对比分析可知"出现的点状物为少量氧化物及少量硅酸盐"未出现异常"可见腐蚀与原材料非金属夹杂物基本无关联$图+!未穿孔一侧管材非金属夹杂物!!$$#O #a 7:-+!4/9X O 01A K K 7S 80J N 7L A 19/9X I0N @/N A 108L 780/@1H 0I 7I 0!!$$#O#图(!腐蚀坑处非金属夹杂物!!$$#O #a 7:-(!4/9X O 01A K K 7S 80J N 7L A 1S /N N /L 7/9I 71L !!$$#O #!-+!显微组织检查分别取穿孔一侧基体%未穿孔一侧基体%穿孔处%小蚀坑处的样品"以截面为观察面"经镶嵌%磨抛后"使用王水在室温下侵蚀"洗净吹干后置于金相显微镜!奥林巴斯=r +&^#下观察$焊缝两侧的管材均为单相有孪晶的奥氏体组织"晶界细而清晰"视场内有少量沿管纵向分布的,铁素体&在未穿孔的一侧"晶粒细小而均匀的等轴状"发生穿孔的一侧晶粒呈现略粗大的不规则形状"未见明显异常"如图,%.所示$图,!未穿孔一侧管材基体组织!+$#O #a 7:-,!^A 1N 7h 17L L ?0/91H 09/9X I0N @/N A 108L 780/@1H 0I 7I 0!+$#O#图.!穿孔一侧管材基体组织!+$#O #a 7:-.!^A 1N 7h 17L L ?0/91H 0I 0N @/N A 108L 780/@1H 0I 7I 0!+$#O #在穿孔%小蚀坑处的显微组织与基体组织无明显差异"均为有孪晶的单相奥氏体组织"偶有沿纵向分布的,铁素体"未见明显异常"如图'所示$在穿孔和蚀坑内壁未见明显的沿晶特征"说明管线母材本身无异常$在小蚀坑的底部发现点蚀迹象"表明小蚀坑正在进行第三阶段腐蚀"一旦蚀穿材第%期毕航铭(&!(B 不锈钢管道腐蚀原因分析及预防措施*&&!*!料"将形成另一处穿孔$图'!小蚀坑显微组织!"$$#O #a 7:-'!^7S N /L 1N ?S 1?N 0/@L O A K K 0N /L 7/9I 71L !"$$#O #!-(!扫描电镜及能谱分析使用扫描电镜!\0:?K ?L ."&$高分辨冷场发射扫描电镜#检查穿孔内表面边缘和内腔的微观形貌"可见在穿孔附近的内表面存在较多点蚀痕迹"如图!$所示&穿孔的内腔壁显示出材料压延变形的层状结构"如图!!所示&内壁可见清晰的晶界"但未发现腐蚀沿晶界深入材料的痕迹&内腔上的点蚀孔内壁表现与内腔相同的形貌$这些形貌特征表明"在穿孔内发生的是均匀腐蚀"而非材料发生了晶间腐蚀$使用能谱分析内腔和管壁内表面的微区成分"结果见表"$图!$!穿孔处内表面!!"$u #a 7:-!$!C 990N L ?N @A S 0/@I0N @/N A 108A N 0A !!"$u #图!!!内壁上的蚀坑!%$$u #a 7:-!!!W N /L 7/9I 71L /91H 07990NM A K K !%$$u #表!穿孔外表面能谱分析结果6'9E ?!+%(0"('4%!"B 4%(&B (0')%%-%(,;&2%)4(B 7'-'/;&#&(%&B /4&元素化学成分!M 1-c #[Z 4A *K G 7]G [K b [N ^9a 047^/内腔腔壁"!-",!$-++$-%.'$-&.$-!($-$!$-$&$-",!"-.(!-&+%+-!%(-!"!-%%蚀孔"$-$,!%-+!$-(!$-&+$-%($-!($-!&$-$'$-$(!"-!$$-'!%&-+.+-,'!-"$内壁".-$!&-,$-"$-%$-&$-"$-$$-$$-"!$-!$-(&'-%+-!!-!表面''%'$(,.!.&$%&!!能谱分析结果"在穿孔内腔%内壁表面均有[K元素腐蚀的痕迹"表明腐蚀是由于[K v 引起的&同时发现b %4A 等元素"表明腐蚀介质应是从海水引入的"如图!"%!&所示$经过上述多轮试验分析可知"该项目所用&!(B 不锈钢管母材符合规范要求"具备抗点蚀能力"管线中无非金属夹杂物影响"其失效的根本原因是不锈钢管线受到[K v含量超过"+I I O 的污染水腐蚀&发生腐蚀的管道处于)型弯低洼处"当[K v含量超标在此处产生积液时"由于[K v半径小%穿透力强"能够穿过钝化膜"与内部金属表面结合"形成可溶性物质+&,"因而产生点腐蚀$*&%!*海洋工程装备与技术第!$卷图!"!外表面能谱a7:-!"!W h10N9A K L?N@A S0090N:P L I0S1N?O图!&!内腔点蚀孔能谱a7:-!&!C910N9A K S A Q71P I71179:H/K0090N:P L I0S1N?O!管线腐蚀的预防与处理根据上文实验结果可知"&!(B不锈钢管线发生点蚀是由于海水在管线内)型弯低洼处产生积液"导致[K v含量超标"故而形成点蚀$因此"不锈钢管线的防腐蚀工作应针对在盐雾环境下对海水的预防"并贯穿于采办%验货%材料存放%现场施工及腐蚀修复等全过程"各环节需严格按照要求执行$!!#采办(由于建造场地位于海边"应要求材料供应商按照规格书关于材料保护运输的规定"对其运送至场地的材料进行保护$不锈钢管线端部"用塑料盖封堵保护"尽可能保证管内干燥$运输过程中避免不锈钢管与其他异种金属接触"建议独立包装运输$!"#验货(入库之前应尽快组织材料验货$将材料保护作为必要检查项"以确保在预制安装之前管线内部[K v含量水平较低$对于未按要求防护材料的"应及时整改$仔细检查不锈钢管线来料表面%端部"若出现明显锈斑%锈迹"建议要求厂家换货处理"保证材料到货质量$!&#存放(对于存放于室外的管线"需用洁净的帆布做好遮蔽%包裹"避免材料直接曝露在近海环境下"易导致管线表面腐蚀$!%#涂装(在&!(B不锈钢外部进行防腐涂料涂装"是防止外部环境引起不锈钢表面点腐蚀的一种经济有效的手段+%,$建造工程中应严格根据防腐规格书执行"在喷涂前后"均应做好端面防护"用塑料盖封堵管线端部"防止水%污垢进入管线内部$涂装完毕后在转运及安装过程中"应使用帆布包裹"避免管线在转运过程中划伤"破坏防腐油漆涂层$!+#试压(不锈钢管线系统试压"应保证试压用水[K v含量不超过"+I I O$管路应设置足够的)型弯泄放点"防止产生积液$水压测试完毕后应用干燥%无油的高速压缩空气吹扫%干燥"并满足项目相关的露点要求"最后进行密封处理$!(#轻微锈蚀处理(对于不锈钢管外壁轻微锈蚀处"应引起足够重视"采用酸洗钝化膏进行除锈处理"防止锈蚀进一步扩大"产生电化学腐蚀"造成管道穿孔失效$其原理是"通过涂抹酸洗钝化膏"在不锈钢管线表面形成一种又密又薄且覆盖性良好的%能牢固附着在金属表面的钝化膜"降低腐蚀速率++,$@!结!语随着我国海洋石油工业进军深蓝的步伐愈发坚定"减少海洋平台不锈钢管线的失效发生"对于保障平台安全"将深海开发战略落实到位具有重要意义$在建造过程中"对于&!(B不锈钢管的保护应该是全方位%多角度的$本文通过对失效管道试件的多角度实验分析"采用排除法一一排查"得出了外部因素引进[K v含量超标的液体介质是导致管道腐蚀穿孔的主要原因"并简要介绍了点腐蚀的腐蚀机理$对&!(B不锈钢管线的整个建造流程"提出了合理化建议$希望加强各环节的过程管控力度"杜绝外部因素导致的不锈钢管线腐蚀"确保海洋平台的安全高效生产$参考文献+!,王晓强"吕伟超"赵联瑞"等-在氯离子环境下不锈钢腐蚀原因分析和预防措施+g,-容器与管道""$!'"!'#(&.%$-+",常青-深海环境对&!(B不锈钢临界点蚀温度的影响+<,-哈尔滨(哈尔滨工程大学""$!(-+&,张鸣伦"王丹"王兴发"等-海水环境中[K v浓度对&!(B不锈钢腐蚀行为的影响+g,-材料保护""$!'"+!!!#(&+-+%,张国庆-海洋油气开发工程&!(B不锈钢的腐蚀及防护+g,-涂料工业""$"$"+$!'#(($-++,杨媚媚"刘忠斌"吕建伟-不锈钢工艺管线外表面防腐蚀保护+g,-全面腐蚀控制""$!$""%!&#("'&$-+(,B R W L S A K A8A R^7S N/L1N?S1?N0A98[/N N/L7/9=0H A Q7/N/@*C G C &!(B<?I K0hD N0A108J P^0A9L/@C/9471N7879:A98]K A L O A第%期毕航铭(&!(B不锈钢管道腐蚀原因分析及预防措施*&+!*!=A L087/9C O I K A91A17/9A98<0I/L717/9i g j RG?N@A S0o[/A179:LD0S H9/K/:P;"$!&;""&k%!%(Ri,j]A?K790=/7K K/1A98g w N x O0]0?K170N R)L0/@G1A79K0L L G100K L79 1H0C98?L1N P k\0S091A98a?1?N0<0Q0K/I O091L i g j R]N/S087A W9:7900N79:;"$!%;.&k&$'&"!R+.,赵向博"顾彩香"张小磊-不锈钢腐蚀影响因素分析及防腐蚀性能研究进展+g,-全面腐蚀控制""$!%"".!&#(+"+(-+',G N78H A N;4R W@@0S1/@*:79:D N0A1O091L/91H0\0I A L L7Q A17/9 ]/10917A K/@<?I K0hG1A79K0L LG100KG&""$+i g j R[/N N/L7/9;"$$';(+E!$F k(+$(("Ri!$j4R G N797Q A L A9R G09L717U A17/9/@*?L109717SG1A79K0L LG100K L k[?N N091<0Q0K/I O091L;D N098L;A98a?1?N0<7N0S17/9L i g j R^01A K K/:N A I H P;^7S N/L1N?S1?N0;A98*9A K P L7L;"$"!;E!$F k !&&!%,Ri!!j^R*R*N A@79A98g R*R G U I?9A N R*40M)980N L1A9879:/@ C910N:N A9?K A N G1N0L L[/N N/L7/9[N A S T79:\0L7L1A9S0/@ ]7I0K790G100K1H N/?:H5N A79=/?98A N P[H A N A S10N A98[N P L1A K K/:N A I H7SD0h1?N0G1?870L i g j R[/N N/L7/9G S709S0;"$$.;+!E!F k!!'!".Ri!"j[R5A N S7A R C910N:N A9?K A N[/N N/L7/9/@60K808g/791L/@*?L 109717SG1A79K0L LG100K LG1?8708J P)L79:A9W K0S1N/S H0O7S A K^797S0K K i g j R[/N N/L7/9G S709S0;"$$.;+$E.F k"&'$"&',R。
304不锈钢焊接管开裂原因分析

304不锈钢焊接管开裂原因分析摘要:304不锈钢管路在例行检查过程中发现多处裂纹,该管路最大运行压力约40MPa,内部介质温度为-40~60℃,外部为舱室,管路材质为0Cr18Ni10Ti奥氏体不锈钢,型号规格为φ42mm×6mm,管线服役过程中存在压力及温度变化,裂纹分布于焊缝附近,通过无损检测、宏观观察、金相检测、扫描电镜断口观察及能谱分析等方法进行了研究分析。
结果表明:高压空气不锈钢管发生了刀状腐蚀开裂失效,属于晶间腐蚀的一种,裂纹位于焊缝熔合线处,焊接工艺不当导致熔合线区域抗晶间腐蚀能力下降以及外来腐蚀介质是导致晶间腐蚀产生的原因。
关键词:钢管开裂;应力腐蚀;补焊1外观检查和材料化学成分分析失效不锈钢焊接管的宏观形貌如图1所示。
表面多处发生开裂,开裂位置外表面已被打磨。
经观察,焊接管裂纹多位于焊接处附近,有环向开裂亦有轴向开裂,图1(d)裂纹呈“H”型横纵交错,且裂纹已裂穿焊接管壁厚方向,焊接处呈黄褐色锈蚀形态特征,附近观察到有焊接过程中飞溅的焊料滴落附近。
线切割切取几处开裂较严重位置,其外表面形态如图1(b)所示,对应各自内表面宏观形貌如图1(c)所示,裂纹均已裂穿,且钢管内表面裂纹附近有圆圈痕迹,呈历经高温灼烧的补焊形貌特征。
将图1(d)处裂纹打开,断口如图1(e)所示,表面呈银灰色,敲开过程中发生塑性变形,从各断口扩展流线判断,开裂起始于外表面,沿图中箭头所指方向扩展,源区略呈暗灰色。
利用超景深体式显微镜观察裂纹处钢管内壁形貌如图1(f)所示,图1(g)为酸洗处理后的内表面形貌。
从失效焊接管基体上取样分析材料的化学成分,结果如表1所示,符合GB/T20878—2007《不锈钢及耐热钢牌号及化学成分》中对06Cr19Ni10的化学成分规范要求。
图1不锈钢焊接管开裂宏观形貌2理化检验2.1无损检测参照标准NB/T47013.5—2015《承压设备无损检测第5部分渗透检测》对高压空气不锈钢管整体外表面除漆后进行渗透检测,结果在焊缝边缘发现1处裂纹,裂纹方向平行于焊缝,指示长度15mm。
不锈钢焊接接头晶间腐蚀性能浅究

不锈钢焊接接头晶间腐蚀性能浅究不锈钢材料是当前我们生产、生活中经常见到的一种材料,它具有很多优点,但这种不锈钢材料用于冷加工成形与进行焊接作业时,时常会对其实际抗腐蚀性能造成影响,若其抗腐蚀性能不强,很容易被腐蚀,影响到构建的稳定性,因此在成形与焊接不锈钢产品后,在焊后不进行热处理的情况下,要求母材与焊接头的抗腐蚀性能必须足够强,特别是抗晶间腐蚀性能。
为此必须掌握不锈钢焊接接头晶间腐蚀的检验方法,了解造成焊接接头晶间腐蚀的原因,并采取相关策略努力提高不锈钢焊件抗晶间腐蚀能力。
1 不锈钢焊接接头晶间腐蚀检验在氧化与弱氧化环境中晶间腐蚀经常会出现在奥氏体不锈钢中,一旦不锈钢件出现这种腐蚀,腐蚀会从不锈钢表面沿晶界深入内部,对不锈钢材料的实际机械强度会造成严重影响,出现晶间腐蚀的材料,稍受外力断裂现象就有可能沿晶界线发生,只观看材料表面很难判断出晶间腐蚀,晶间腐蚀有高危性的特点。
这就要求在用不锈钢材料制作设备时,母料与焊接接头的实际抗晶间腐蚀性能必须足够强。
为使焊接构件足够牢固,必须检查焊接接头的晶间腐蚀性。
在测定不锈钢对晶间腐蚀的敏感情况时,一般采用的是加速法。
这种方法主要是采用适当腐蚀剂,在一定条件下,加速选择性腐蚀晶间,找一个万能材料试验机,把试样放置于上面,弯曲材料然后再评定,我们用与介质接触的面作为检验面,借助高倍放大镜对弯曲试样处的表面进行观察,看有无晶间腐蚀引发的裂纹。
2 判别晶间腐蚀裂纹位于试样弯曲部位棱角处的裂纹以及无裂纹的滑移线、皱纹等以上情况不一定都是由于晶间腐蚀引发的裂纹,发生晶间腐蚀的试验,在实施冷弯曲操作时,其表面鳞状裂纹随处可见,对试样进行敲击金属声响不会出现,在很难评定的情况下,可借助金相法进行判断,在实施断面金相检查时,若发现局部腐蚀发生于晶界或其毗邻区域,晶粒脱落,沿晶界腐蚀推进,并且推进有一定均匀性。
这种沿晶界形成的腐蚀通常为晶间腐蚀。
3 焊接接头抗晶间腐蚀能力控制奥氏体不锈钢发生晶间腐蚀通常是由于晶界碳化铬发生沉淀析出造成的,不锈钢晶界区缺乏铬是晶间腐蚀的主要原因,因此可从控制不锈钢焊接处碳化铬的沉淀来防止发生晶间腐蚀,具体可从沉淀碳化铬的分量情况、部位以及形成沉淀物的动力方面进行考虑。
焊缝腐蚀原因

焊缝腐蚀原因全文共四篇示例,供读者参考第一篇示例:焊缝腐蚀是指焊接结构中焊缝部位出现的腐蚀现象。
焊缝腐蚀会严重影响焊接结构的使用寿命和安全性,因此有必要深入了解焊缝腐蚀的原因,以便采取有效的预防措施。
一、焊缝腐蚀的原因1. 电化学腐蚀:焊缝的热影响区、残余应力区和变形区往往是金属的腐蚀敏感区域。
在潮湿的环境中,金属表面会形成一层氧化膜,通过氧化还原反应,金属内部的电子会从阳极流向阴极,形成电流,从而导致电化学腐蚀。
焊缝处的这些区域往往由于热处理或变形而容易发生电化学腐蚀。
2. 焊接材料的选择:焊接时选择的焊丝、焊剂、保护气体等材料的化学成分会对焊缝的腐蚀性能产生影响。
如果焊接材料的成分与基体金属的成分差异较大,容易产生织状腐蚀或晶间腐蚀现象。
焊接时保护气体的纯度和流量也会影响焊缝的腐蚀性能。
3. 焊接工艺:焊接过程中的热影响和残余应力会导致焊缝区域的晶粒重新排列和晶界处的化学成分变化,从而使焊缝易受腐蚀侵蚀。
焊接过程中产生的氧化物、残渣等杂质也会降低焊缝的抗腐蚀性能。
4. 使用环境:焊接结构所处的环境条件也会对焊缝的腐蚀性能产生影响。
如高温、高湿度、有机酸、氯化物等腐蚀性物质会加速焊缝的腐蚀过程,导致焊缝的失效。
5. 设计缺陷:焊接结构的设计是否合理、焊缝的质量是否达标等因素也会影响焊缝的腐蚀性能。
如果焊接结构存在设计缺陷,如凹凸不平的焊缝表面、未能清理焊后残渣等,都会使焊缝易受腐蚀侵蚀。
二、预防焊缝腐蚀的措施1. 选择合适的焊接材料和工艺:在焊接时选择合适的焊接材料和工艺,尽量减少焊接过程对金属的影响,保证焊缝的质量;合理选择焊接材料的化学成分,避免与基体金属产生不利的化学反应。
2. 采用防腐措施:在焊接后对焊缝进行防腐处理,如涂覆防腐漆、电镀、热浸镀等,形成一层保护膜,阻止金属与外部腐蚀性介质直接接触,延长焊缝的使用寿命。
3. 控制焊接结构的使用环境:避免焊接结构长期处于高温、高湿度、腐蚀性介质等环境中,通过改善环境条件来延缓焊缝的腐蚀过程。
不锈钢均匀腐蚀的原因

不锈钢均匀腐蚀的原因
不锈钢均匀腐蚀的原因主要有以下几个:
1. 腐蚀介质:不锈钢在某些强氧化性介质(如盐水、酸溶液、碱溶液等)的作用下,会发生腐蚀反应。
这些介质中的氧气或氯离子会与不锈钢表面的铬元素发生反应,导致铬的离子化和析出,进而破坏不锈钢的腐蚀抵抗能力。
2. 不锈钢表面缺陷:不锈钢表面的缺陷(如划痕、凹陷、氧化层不连续等)会导致介质在这些缺陷处聚集,并进一步加速腐蚀的发生。
缺陷处的局部电位较低,容易被剧烈腐蚀。
3. 温度和湿度:高温和高湿度环境下,不锈钢容易发生均匀腐蚀。
高温会加快腐蚀反应的速率,而高湿度的环境则提供了足够的水分供腐蚀介质的反应。
4. 不锈钢材质:不同材质的不锈钢在腐蚀性介质中的腐蚀抵抗能力是不同的。
不同牌号的不锈钢中添加的合金元素和比例不同,因此其腐蚀抵抗性也不同。
一些低合金不锈钢在特定条件下容易发生均匀腐蚀。
综上所述,不锈钢均匀腐蚀的原因是多方面的,涉及到腐蚀介质、表面缺陷、温度湿度和不锈钢材质等因素的综合作用。
正确选择合适的不锈钢材质和采取必要的防护措施,可以减少不锈钢的均匀腐蚀。
不锈钢管道焊接处海水腐蚀失效分析与机理研究
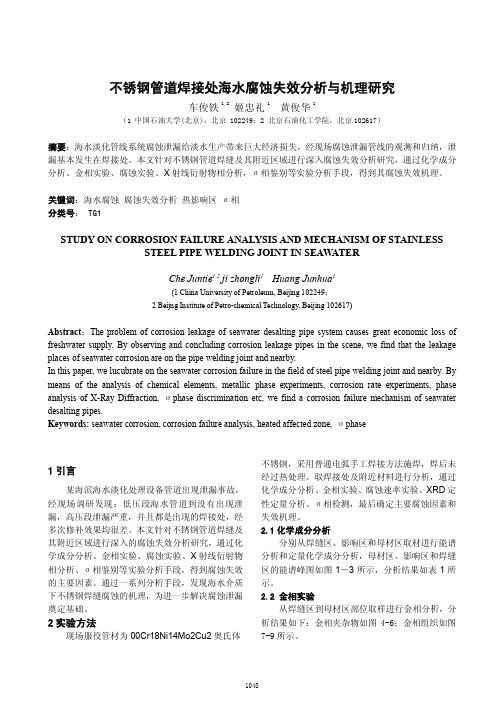
焊缝区(WZ)和影响区(HAZ)进行实验,测得极化 曲线如图 10-13 所示。 通过计算机数值拟合,按弱极化区三参数法计 算,分别求得三个区域的腐蚀电化学动力参数和腐 蚀电流及腐蚀速率。数据拟合结果如表 2 所示:
BMZ
700 600 500 400 300 200
500 400 300 200
WZ
【2】 [1] + -
6 中看出,母材主要含有简单氧化物(小黑点) ,少 量简单硫化物, 还有少量硫化物和 SiO2 的复合夹杂 物。该结果与化学成分含量分布基本一致。图 7 为 热影响区分布不均匀的粗大晶粒组织;图 8 为焊缝 区细小晶粒且晶枝状分布的组织;图 9 为母材均匀 细小的奥氏体组织。从金相组织角度可以看出,由 于热影响区晶粒粗大,分布不均,且夹杂物含量较 高,耐海水腐蚀能力急剧下降。母材为细小均匀晶 粒,耐腐蚀性均匀,钝化膜稳定,因而耐海水腐蚀 能力较好。焊缝为细小晶枝状分布晶粒,具有很好 的材料强度和耐腐蚀性,且由于晶粒细小,钝化膜 不易破坏,因而耐海水腐蚀能力强。 腐蚀实验测得极化曲线如图 10-13 所示。热影 响区测得的极化曲线,在阴极极化向阳极极化的过 程中有不稳定现象,尤其是在熔合线附近,这与热 影响区组织不均匀性相关。从极化曲线中看出,热 影响区的腐蚀电位较负,大致在-256 到-373 mv; 而母材和焊缝区的腐蚀电位较正,分别是-35 mv 和 -104 mv。通过计算机数值拟合,按弱极化区三参 数法计算,结果如表 2 所示:母材区和焊缝区的腐 蚀速率为 8.03×10 和 6.46×10
图 5 焊缝区夹杂物
图 6 母材区夹杂物
图 7 热影响区组织
图 8 焊缝区组织
图 9 母材金相组织
1049
2.3 腐蚀实验 用 SCE(汞/甘汞——饱和 KCl)电极作为参 比电极来衡量工作电极的电位 ,辅助电极为暗黑铂 电极,采用 407 合成胶密封试样。电化学实验介质 溶液的组成为: 4.35 % NaCl 水溶液 (模拟海 水成份) ,温度为 25 ℃。试样有效工作面积约 0.5 cm2,扫描速率为 2 mV/s。分别取母材区(BMZ)、
不锈钢锈蚀原因分析

不锈钢锈蚀原因分析分析一:1.在焊接过程中,不锈钢材料中的炭化物的析出,造成抗腐蚀性能下降;2.打磨产生的高温,造成不锈钢特性退化。
在现在的工艺基础上建议的改善方案:1.保持材料的清洁(在焊接前先清洁材料),在焊接时防止来自外部的碳、氧、氮等杂质侵入(对氩气纯度的检查,保持充分的氩气屏蔽);2.避免过度的打磨,并考虑降温、散热措施。
分析二:不锈钢由于其特殊的金相组织和表面钝化膜,使得它在一般情况下较难与介质发生化学反应而被腐蚀,但并不是在任何条件下都不能被腐蚀。
在腐蚀介质和诱因(如划伤、飞溅、割渣等)存在的条件下,不锈钢也能与腐蚀介质发生缓慢的化学和电化学反应被腐蚀,而且在一定条件下的腐蚀速度相当快而产生锈蚀现象,尤其是点蚀和缝隙腐蚀。
所以不锈钢焊接打磨后要防生锈,一定要对其采取保护措施。
例如打磨后使用不锈钢光亮剂、钝化膏等对其表面进行处理,起到防锈的作用。
分析三:1.在焊接过程中,不锈钢材料中的炭化物的析出,造成抗腐蚀性能下降;2.打磨产生的高温,造成不锈钢特性退化。
在现在的工艺基础上建议的改善方案:1.保持材料的清洁(在焊接前先清洁材料),在焊接时防止来自外部的碳、氧、氮等杂质侵入(对氩气纯度的检查,保持充分的氩气屏蔽);2.避免过度的打磨,并考虑降温、散热措施。
浅谈不锈钢:一:钝化处理:用铬酸盐溶液与金属作用在其表面生成三价或六价铬化层的过程,叫做钝化,亦名铬化。
多用于铝、镁及其合金的处理,对钢铁也能形成铬化层,单独的时候很少用,常和磷化配套使用,以封闭磷化层的孔隙,使磷化层中裸露的钢铁钝化,以抑制残余磷化加速剂的腐蚀作用,防护能力能够逐步增加。
钝化时一般用重铬酸钾溶液(2~4克/升,有时也加入1~2克磷酸),在80-90摄氏度浸啧2-3分钟取出,水洗就OK了。
二:化学腐蚀1 、表面污染:附着在工件表面的油污、灰尘及酸、碱、盐等在一定条件转化为腐蚀介质,与不锈钢件中的某些成分发生化学反应,产生化学腐蚀而生锈。
焊缝腐蚀原因
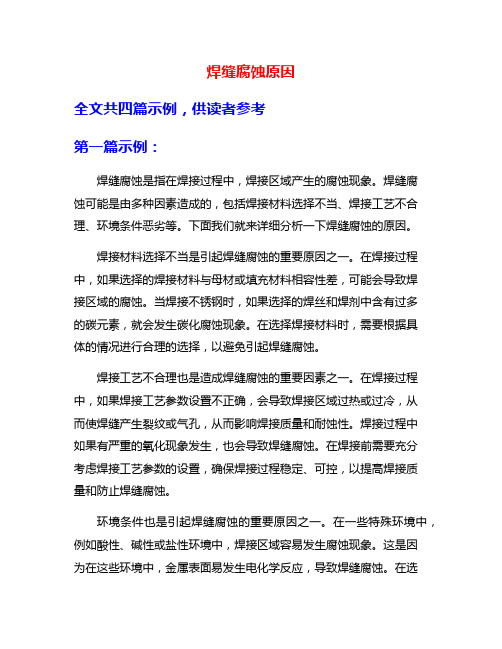
焊缝腐蚀原因全文共四篇示例,供读者参考第一篇示例:焊缝腐蚀是指在焊接过程中,焊接区域产生的腐蚀现象。
焊缝腐蚀可能是由多种因素造成的,包括焊接材料选择不当、焊接工艺不合理、环境条件恶劣等。
下面我们就来详细分析一下焊缝腐蚀的原因。
焊接材料选择不当是引起焊缝腐蚀的重要原因之一。
在焊接过程中,如果选择的焊接材料与母材或填充材料相容性差,可能会导致焊接区域的腐蚀。
当焊接不锈钢时,如果选择的焊丝和焊剂中含有过多的碳元素,就会发生碳化腐蚀现象。
在选择焊接材料时,需要根据具体的情况进行合理的选择,以避免引起焊缝腐蚀。
焊接工艺不合理也是造成焊缝腐蚀的重要因素之一。
在焊接过程中,如果焊接工艺参数设置不正确,会导致焊接区域过热或过冷,从而使焊缝产生裂纹或气孔,从而影响焊接质量和耐蚀性。
焊接过程中如果有严重的氧化现象发生,也会导致焊缝腐蚀。
在焊接前需要充分考虑焊接工艺参数的设置,确保焊接过程稳定、可控,以提高焊接质量和防止焊缝腐蚀。
环境条件也是引起焊缝腐蚀的重要原因之一。
在一些特殊环境中,例如酸性、碱性或盐性环境中,焊接区域容易发生腐蚀现象。
这是因为在这些环境中,金属表面易发生电化学反应,导致焊缝腐蚀。
在选择焊接材料和焊接工艺时,需要考虑到环境条件的影响,选择适合特定环境的焊接材料和工艺,以减少焊缝腐蚀的发生。
焊缝腐蚀是由多种因素造成的,包括焊接材料选择不当、焊接工艺不合理、环境条件恶劣等。
为了避免焊缝腐蚀的发生,需要综合考虑上述因素,并在焊接前进行充分的分析和评估,以提高焊接质量和防止焊缝腐蚀的发生。
需要加强对焊接操作人员的培训和指导,提高他们的焊接技术水平和质量意识,以确保焊接质量和安全生产。
第二篇示例:焊缝腐蚀是指焊接接头处出现的腐蚀现象,是焊接工艺中一种常见的问题。
焊缝腐蚀严重影响焊接接头的力学性能和使用寿命。
引起焊缝腐蚀的原因有很多,主要包括以下几个方面:一、金属结构和焊接材料的选择不当。
在焊接过程中,如果选择的金属结构和焊接材料不匹配,则可能会引起焊缝腐蚀。
不锈钢腐蚀的机理
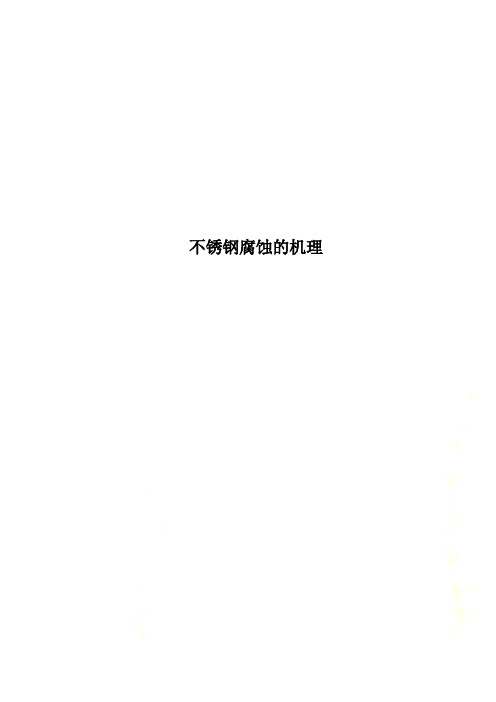
不锈钢腐蚀的机理不锈钢腐蚀的机理1 氯离子对不锈钢腐蚀的机理在化工生产中,腐蚀在压力容器使用过程中普遍发生,是导致压力容器产生各种缺陷的主要因素之一。
普通钢材的耐腐蚀性能较差,不锈钢则具有优良的机械性能和良好的耐腐蚀性能。
Cr 和Ni 是不锈钢获得耐腐蚀性能最主要的合金元素。
Cr 和Ni 使不锈钢在氧化性介质中生成一层十分致密的氧化膜,使不锈钢钝化,降低了不锈钢在氧化性介质中的腐蚀速度,使不锈钢的耐腐蚀性能提高[1 ] 。
氯离子的活化作用对不锈钢氧化膜的建立和破坏均起着重要作用。
虽然至今人们对氯离子如何使钝化金属转变为活化状态的机理还没有定论,但大致可分为2 种观点。
成相膜理论的观点认为,由于氯离子半径小,穿透能力强,故它最容易穿透氧化膜内极小的孔隙,到达金属表面,并与金属相互作用形成了可溶性化合物,使氧化膜的结构发生变化,金属产生腐蚀。
而吸附理论则认为,氯离子破坏氧化膜的根本原因是由于氯离子有很强的可被金属吸附的能力,它们优先被金属吸附,并从金属表面把氧排掉。
因为氧决定着金属的钝化状态,氯离子和氧争夺金属表面上的吸附点,甚至可以取代吸附中的钝化离子,与金属形成氯化物,氯化物与金属表面的吸附并不稳定,形成了可溶性物质,这样导致了腐蚀的加速。
电化学方法研究不锈钢钝化状态的结果表明,氯离子对金属表面的活化作用只出现在一定的范围内,存在着1 个特定的电位值,在此电位下,不锈钢开始活化。
这个电位便是膜的击穿电位,击穿电位越大,金属的钝态越稳定。
因此,可以通过击穿电位值来衡量不锈钢钝化状态的稳定性以及在各种介质中的耐腐蚀能力。
2 应力腐蚀失效及防护措施2. 1 应力腐蚀失效机理[2 ]在压力容器的腐蚀失效中,应力腐蚀失效所占的比例高达45 %左右。
因此,研究不锈钢制压力容器的应力腐蚀失效显得尤为重要。
所谓应力腐蚀,就是在拉伸应力和腐蚀介质的联合作用下而引起的低应力脆性断裂。
应力腐蚀一般都是在特定条件下产生: ①只有在拉应力的作用下。
不锈钢管焊接过程中遇到的问题及解决办法

304不锈钢管耐大气腐化基础下非跟着小气中的氯化物的露量而变卦的。
因而,接近海洋大约其他氯化物污染流关于不锈钢管的腐化是极替首要的。
必定质的雨火,只需对钢外表的氯化物淡度止做用时才是重要的。
304不锈钢管能够习惯各种用途,其内观上不会有明显的改变。
果彼,在墟落流露运用的不锈钢管能够依据报价,加拿大移民,市场供应状况,力教功用、制作加工功用和里观去挑选。
工业状况在不氯化物污染的工业状况中,不锈钢管能暂时事情,基础上保持有锈蚀,能够在里构成污膜,但该将污膜清除先,借坚持灭本有的灼烁中观。
在有氯化物的工业状况中,将构成不锈钢管锈蚀。
在304不锈钢管的焊接进程中常会碰到一些题目,不锈钢焊条施焊进程中焊条凝结至整根长度的1/3时,焊条尾部会发红(以致药皮开裂)、飞溅增大、焊缝杰出、焊缝成形好转、脱渣困难。
当焊条尾部发红时,焊芯尺寸有较大的伸长和拓展,使药皮承受极大的扩张力(药皮线胀系数与焊芯线胀系数不一致,且药皮强度低于焊芯的强度)而引起药皮开裂,使焊条技术性急剧下降。
为了淘汰或防止304不锈钢管焊条的尾部发红和药皮开裂征象。
- 1、下载文档前请自行甄别文档内容的完整性,平台不提供额外的编辑、内容补充、找答案等附加服务。
- 2、"仅部分预览"的文档,不可在线预览部分如存在完整性等问题,可反馈申请退款(可完整预览的文档不适用该条件!)。
- 3、如文档侵犯您的权益,请联系客服反馈,我们会尽快为您处理(人工客服工作时间:9:00-18:30)。
作 者 简 介 : 璐 ( 7 一 ) 女 , 程 师 。 电话 : O 1 ) 6 6 8 5 贾 1 6 9 , 工 ( 5 6 1 2 0 2
ቤተ መጻሕፍቲ ባይዱ 8
现
代 冶 金
第3 8卷
1 . 。 取 样 位 置 如 图 4所 示 , 析 结 果 如 图 5所 35 分 示 。 由 图 5可 以 看 出 , 含 量 为 9 1 , 低 于 Ni .2 略
( ) 洗过 程 中按 材料 不 同 区分 酸 洗 液配 比及 3酸 酸洗 时间 , 酸洗过 后须进 行相应 的循环 冲洗 , 时发 及 现 由于 焊接 产生 的 问题 , 避免 在 使用 后 发现 配管 的
问题 。
2 3 焊接后配 管酸洗 过程分析 . 目前 国内酸洗有 槽式 酸洗法 和循环 酸洗法 两种
3 预 防方 案
( ) 制原材 料 , 1控 在确 保原材 料符合 要求 的情 况
下 , 定正 确的焊 接方法及 酸洗工 艺 。 确
图 5 样 品分 析 结 果
() 2 严格控制焊接过程 , 区分材料 , 减少焊接过程 中处于易产 生缺陷 的温 度的时间 。如 1 — 88型铬镍奥 氏体不锈钢易产生晶间腐蚀的温度是 6 O 0 。 O ~10 0 C。
局 部也易产 生 晶问腐蚀现 象即所 渭的刀 蚀 。
总的来讲就是 : rNi C — 奥氏体不锈 钢的焊接 部位
在 4 0 8 0。 , 影 响 区 以 敏 化 区 形 态 出 现 可产 5  ̄ 5 C时 热
生晶 间腐蚀 ; 含有 T 成分 的 C — i 氏体钢 在 固溶 i rN 奥 区熔合 线温度时会产生晶间腐蚀现象 。 同时随着在处 于该温度 时间的加长 , 晶间腐蚀 会加重 。
因此 对 于 0 r 8 1 M0 T 焊 接 区 的 热 影 响 区 C l Ni2 2 i
图 4 取 样 位 置
发 生腐蚀 的主要 原 因为 : 此种 材 料 出现 晶间腐 蚀有 两个 温度 段 , 热影 响 区在 这两个 温度 区间 上 由于 没 有控 制好温 度与时 间的 比例 而产生 了晶 间腐 蚀 。
1 不锈 钢 配 管焊 接 区腐 蚀 现 象
不锈钢 配管 在焊 接酸 洗后 , 焊缝 的热影 响 区 、 在
法 兰与 管子 焊接 部 位 、 子 焊缝 与母 材 接 口处 等 部 管 分发生 了腐蚀 现象 , 体如 图 1 具 ~3所示 。
图 2 酸 洗 后 法 兰 与 管 子 焊 接 部 位 腐 蚀 现 象
在 40 5 C 5 ~8 0。 加热 的部分称 为敏化 区。 而对 于含有
1 . ~ 1 . 的范 围 , 光 谱 分 析设 备 的 检测 误 O5 35 从 差及 材料标 准要求来 讲 , 结果 符合标 准要求 。 焊接 材 料采用 A2 7 0 焊条 , 有相应 的材料 保证 书。焊接材料 的选用及 质量符合 要求 。
方式 。
槽 式 酸洗 法工 序 为 : 脂一 水 冲洗一 酸洗 一 水 脱 冲洗一 中和一钝 化一水 冲洗一 干燥一 封 口。 循 环酸 洗法 工序 为 : 试漏 一 水 冲洗一 酸 洗一 水
中和一钝 化一水 冲洗一 干燥 一封 口。 经过 检查 , 锈 钢配 管焊 接后 采 用 的是 槽式 酸 不
2 不 锈 钢 配 管 焊 接 区 腐 蚀 原 因 分 析
2 1 宏 观 分 析 .
() b
从 图 1 3中可 以看 出 , 锈钢 配管 在焊 接酸 洗 ~ 不 后, 出现的过度腐蚀 集 中在 焊缝处 的焊接热影 响区范
() c
() d
图 3 酸洗 后 管 子 焊 缝 与母 材 接 口处 腐 蚀
围内, 而焊 缝无损 坏 , 由此 可见 焊缝 质量 没有 问题 。
2 2 原 材 料 及 焊 接 材 料 检 查 .
图 1 酸 洗 后 焊 缝 的 热 影 响 区 腐 蚀 现 象
本体材料为 0 r 8 l Mo Ti含 Ni 1 . %~ C lNi2 2 , 量 05
收 稿 日期 :0 90 —0 2 0 —82
第 3 8卷 第 2期
2 1 0 0年 4月
现 代 冶 金
M o e n M e al r d r t lu gy
V o .3 N o 1 8 .2 A pr 2 0 . 01
不 锈 钢 配 管焊 接 区腐 蚀 原 因分 析
贾 璐
( 钢 集 团 苏 州 冶 金 机 械 厂 ,江 苏 苏 州 2 5 5 ) 宝 111
Ti 分 的 C — 奥 氏体 钢 , 于其 碳 化 物 不 是 以 成 rNi 由 C。 r C 形式 沉 淀 而是 以 Ti 式沉 淀 , 。 C形 因此 其 热影
响区 只有粗 晶 的固溶 区而没有 敏化 区 。但是 ,含有
T 成 分的 C ~ 奥 氏体钢 , 固溶 区 紧邻熔 合线 的 i rNi 在
理状态 , 常温下 为单相奥 氏体组织 。理论上 来说 , 在 在焊 接 热影 响 区 中约 4 O 5 C的 区域存 在 由介 5 ~8 0。 稳奥 氏体 中脱 溶 沉 淀碳化 物 的现象 。C — 奥 氏体 rNi 不 锈 钢的 热影 响 区 由于这 种碳 化物 的沉 淀 , 常会 常 导致 增 大腐 蚀 的敏 感性 , 在腐 蚀介 质 中易 发生 晶问 腐蚀 现象 。因此 c — 奥 氏体不锈钢 的热影 响 区中 rNi
摘 要 :分析 了设 备 不锈 钢 配 管 在 焊 接 酸 洗 后 发 生 腐 蚀 的 原 因 , 出 了相 应 的 预 防 方 案 。 提
关 键 词 :不锈 钢 配 管 ;焊 接 区 ;腐蚀
中 图 分 类 号 : G4 1 7 T 4 .
引 言
设备 配管尤 其是 轧机 的高压 液压 配管采 用不 锈 钢材 质 的较 多 。 不锈 钢配 管在 制造 过程 中 , 焊接 区 在 及周 边极 易 产 生裂 纹 , 的 裂 纹 甚 至在后 道 工 艺 或 有 经过 一段 时间后 才显 现 出来 。