TPM个别改善
【标杆学习】TPM管理:生产效率化个别改善

【标杆学习】TPM管理:生产效率化个别改善立即加星标,第一时间看好文01故障为0改善1、关于故障(1)制造部门的关心不足①在工时上、不让作業者做与生产以外的事②安全上、不允许动设备③没有达成机构(2)故障解析的能力较弱①损坏的部位的描述没有充分的完成②没有将故障品进行解体分析③故障原因的追究不充分、交換后就完了④防止再次发生、恶化的防止没有水平开展⑤在现场的故障解析不足(3)保养系统运用弱①点检周期・点检场所・点检方法・判断基准等的基准不全面②部品交换、加油等看过后能明白保全时间表不全面③故障的履历要素(4)予知保全的分析能力较弱①予知保养是设备进行定期的观察状态及测定値的变化,异常的判定的方法(有区分简易诊断和精密诊断)②简易诊断固定后、实施精密诊断③精密诊断,振动量、电流负荷、适当的时间、动作时间、温度、音等进行数値化进行管理,时常能把握変化点体制的建立2、故障低減的思路(1)故障的分类整理①简单的故障和困难的故障进行分类、优先简单的额故障进行递减対策。
②分类・层别方法,线别/发生地方/故障模式/原因别等(2)故障解析①对设备增加适应力→机械、电気适应力+温度・湿度・振动・粉尘3、故障解析的强化方法①現象的明確化:在现场的确认实物进行原因的调查、记录。
②暂时処理:更换损坏的部品、但是这不是真的故障対策!③原因追究的准备:故障的设备、部品的说明书、使用系统构成图等要理解机能、构造、使用方法④原因追究:故障的原因全面分析徹底的追究发生原因⑤対策:不合理地方的复原、立即实施改善、还要进行水平开展。
⑥恶化:防止再次发生同样的故障修正点检基准、检讨检出能力的提高4、故障対策的重点项目1)清扫:①异物、沾脏、由于异物造成设备的强制恶化的防止②设备的磨损、破裂、划伤、腐蚀、変形、泄漏、龟裂、及温度、振动、异音等潜在缺陷的显在化2)补油:①烧坏、磨损、温度上升的防止3)紧固:①螺钉,螺母的紧固部品的脱落、折损、防止腐蚀②发出咯咯的异音4)使用条件的遵守:①明确使用条件并遵守5)劣化的复原:①劣化的早期检出,利用定期点検来发现②劣化的复原,整理基准6)设计上的弱点改善7)运转、保全技能的提高02切换的改善1、关于切换(1)混乱的状态难以把握①作业方法上的问题(手顺、方法、作业者的技能)②治工具的问题(治工具的形状、机构、精度)③设备上的问题(精度、调整)④技术上的问题(必须进行技术改善的位置)⑤作业管理上的问题(考核)(2)手顺不明确①没有形成手顺化②不遵守作业手顺(3)调整的检讨不足和未实施一次成功①没有检讨调整的时间、比率较高②调整为0对一次成功的检讨不足2、切换改善(1)整理整顿①治工具的定置管理②不寻找、不移动、不使用(2)外切换与内切换的明确化①外切换与内切换进行区分并手顺化②作业排除的检讨③作业手顺的修正(3)外切换与内切换移管①事前调整准备化(事前组立、整套交换)②治具的共通化和简单手动操作③调整的外切换移管④中介治具的采用,调整排除(4)内切换的方法检讨和时间短缩①固定方法的検讨螺丝固定→油圧固定②并行操作的実施1人→2人作业时间短缩(5)调整的排除1)调整的目的①位置决②中心③尺寸④合适时间⑤平衡2)调整的原因①误差积累②标准化不足③刚性不足3)调整的分析和一次成功方法的检讨03刃具浪费的改善1、关于刃具浪费(1)刃具的寿命①刃具的材质、形状②切削条件(切入量、速度)③产品材质、硬度④产品要求质量(寸法精度、表面粗糙程度)⑤设备的刚性(2)不遵守定数更换条件理由:①基准暧昧②刀片发生磨损③品质悪化、随便交换(3)妨碍无人运转理由:①品质有偏差②刃具寿命短、不足8小时③发生瞬间停止(4)刃具费的低减问题点:①不使用的旧刀具进行保管②没有刃具费的管理指标③刃具的种类多④刀具的入出库管理松懈⑤没有刀具的使用履历记录⑥没进行刀具的磨损度管理(可以使用也交换、不能使用了却继续使用)2、刃具寿命予测①刃具的磨损,由于刃具切削抵抗磨损、基准尺寸不能持续维持更换,达到理想的状态。
2-2.94 TnPM课堂——TPM管理的改善意义和实质内容
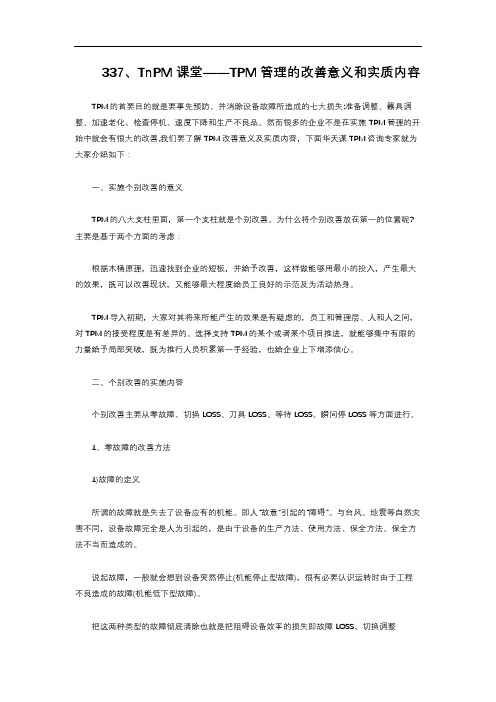
337、TnPM课堂——TPM管理的改善意义和实质内容TPM的首要目的就是要事先预防、并消除设备故障所造成的七大损失:准备调整、器具调整、加速老化、检查停机、速度下降和生产不良品。
然而很多的企业不是在实施TPM管理的开始中就会有很大的改善,我们要了解TPM改善意义及实质内容,下面华天谋TPM咨询专家就为大家介绍如下:一、实施个别改善的意义TPM的八大支柱里面,第一个支柱就是个别改善。
为什么将个别改善放在第一的位置呢?主要是基于两个方面的考虑:根据木桶原理,迅速找到企业的短板,并给予改善,这样做能够用最小的投入,产生最大的效果,既可以改善现状,又能够最大程度给员工良好的示范及为活动热身。
TPM导入初期,大家对其将来所能产生的效果是有疑虑的,员工和管理层、人和人之间,对TPM的接受程度是有差异的。
选择支持TPM的某个或者某个项目推进,就能够集中有限的力量给予局部突破,既为推行人员积累第一手经验,也给企业上下增添信心。
二、个别改善的实施内容个别改善主要从零故障、切换LOSS、刀具LOSS、等待LOSS、瞬间停LOSS等方面进行。
1、零故障的改善方法1)故障的定义所谓的故障就是失去了设备应有的机能。
即人“故意”引起的“障碍”。
与台风、地震等自然灾害不同,设备故障完全是人为引起的,是由于设备的生产方法、使用方法、保全方法、保全方法不当而造成的。
说起故障,一般就会想到设备突然停止(机能停止型故障),很有必要认识运转时由于工程不良造成的故障(机能低下型故障)。
把这两种类型的故障彻底清除也就是把阻碍设备效率的损失即故障LOSS、切换调整LOSS、瞬停空转LOSS、速度低下LOSS、不良修理LOSS等都彻底消除。
故障就像是冰山一角。
水下面潜藏着的垃圾、污垢、粘着原材料、摩损、喀嗒声、松动、破烂、腐蚀、变形、瑕疵、裂缝、温度、震动、声音异常等等潜在隐患。
然后这些潜在的隐患慢慢变成故障。
2)设备故障的原因导致设备故障发生的原因,从管理角度分析,有以下几点:(1)设备使用、管理部门不关心(2)未对故障进行详细的分析(3)保全系统作用弱(4)预知保全的对应能力弱3)设备零故障的考虑方向要达到零故障可以从以下七个方面进行考虑:故障的分类整理;故障解析和问题处置;基本要求遵守;使用条件的保证;劣化的复原;设计上的弱点改善;提升运行、保全的技能。
设备综合效率管理及个别改善活动 (TPM八本柱之个别改善)

设备综合效率管理及个别改善活动(TPM八本柱之个别改善)蓝草咨询的目标:为您提升工作业绩优异而努力,为您明天事业腾飞以蓄能!蓝草咨询的老师:都有多年实战经验,拒绝传统的说教,以案例分析,讲故事为核心,化繁为简,互动体验场景,把学员当成真诚的朋友!蓝草咨询的课程:以满足初级、中级、中高级的学员的个性化培训为出发点,通过学习达成不仅当前岗位知识与技能,同时为晋升岗位所需知识与技能做准备。
课程设计不仅注意突出落地性、实战性、技能型,而且特别关注新技术、新渠道、新知识、创新型在实践中运用。
蓝草咨询的愿景:卓越的培训是获得知识的绝佳路径,同时是学员快乐的旅程,为快乐而培训为培训更快乐!目前开班的城市:北京、上海、深圳、苏州、香格里拉、荔波,行万里路,破万卷书!蓝草咨询的增值服务:可以提供开具培训费的增值税专用发票。
让用户合理利用国家鼓励培训各种优惠的政策。
报名学习蓝草咨询的培训等学员可以申请免费成为“蓝草club”会员,会员可以免费参加(某些活动只收取成本费用)蓝草club定期不定期举办活动,如联谊会、读书会、品鉴会等。
报名学习蓝草咨询培训的学员可以自愿参加蓝草企业“蓝草朋友圈”,分享来自全国各地、多行业多领域的多方面资源,感受朋友们的成功快乐。
培训成绩合格的学员获颁培训结业证书,某些课程可以获得国内知名大学颁发的证书和国际培训证书(学员仅仅承担成本费用)。
成为“蓝草club”会员的学员,报名参加另外蓝草举办的培训课程的,可以享受该培训课程多种优惠。
课程背景:制造型企业普遍存在着如何提高设备运行效率及生产经营效率的迫切需求,TPM的个别改善提供了系统的方法论。
本课程希望给予企业现场管理人员掌握设备效率改善的方法,以及充分运用个别改善的固有技术,为企业推行全面精细化管理提供帮助。
培训对象:设备维护人员,设备经理培训目标:通过培训能够提升学员对制造现场的改善意识掌握通过设备综合效率的计算导出改善设备效率的方法;系统地理解和运用个别改善的固有技术。
TPM的八大重点
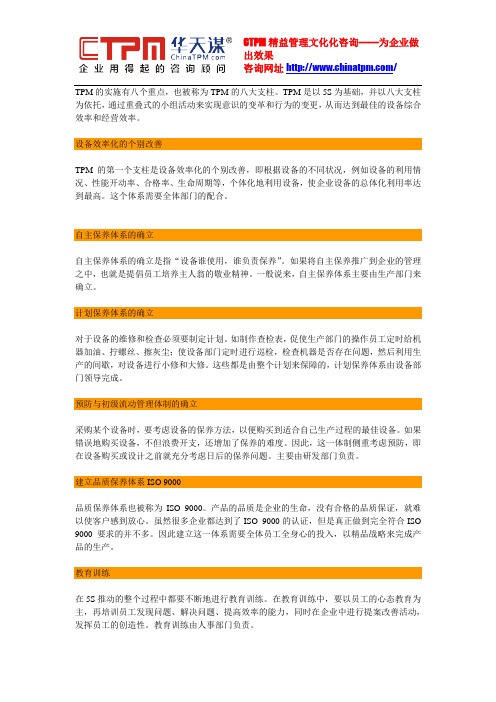
TPM的实施有八个重点,也被称为TPM的八大支柱。
TPM是以5S为基础,并以八大支柱为依托,通过重叠式的小组活动来实现意识的变革和行为的变更,从而达到最佳的设备综合效率和经营效率。
设备效率化的个别改善TPM的第一个支柱是设备效率化的个别改善,即根据设备的不同状况,例如设备的利用情况、性能开动率、合格率、生命周期等,个体化地利用设备,使企业设备的总体化利用率达到最高。
这个体系需要全体部门的配合。
自主保养体系的确立自主保养体系的确立是指“设备谁使用,谁负责保养”。
如果将自主保养推广到企业的管理之中,也就是提倡员工培养主人翁的敬业精神。
一般说来,自主保养体系主要由生产部门来确立。
计划保养体系的确立对于设备的维修和检查必须要制定计划。
如制作查检表,促使生产部门的操作员工定时给机器加油、拧螺丝、擦灰尘;使设备部门定时进行巡检,检查机器是否存在问题,然后利用生产的间歇,对设备进行小修和大修。
这些都是由整个计划来保障的,计划保养体系由设备部门领导完成。
预防与初级流动管理体制的确立采购某个设备时,要考虑设备的保养方法,以便购买到适合自己生产过程的最佳设备。
如果错误地购买设备,不但浪费开支,还增加了保养的难度。
因此,这一体制侧重考虑预防,即在设备购买或设计之前就充分考虑日后的保养问题。
主要由研发部门负责。
建立品质保养体系ISO 9000品质保养体系也被称为ISO 9000。
产品的品质是企业的生命,没有合格的品质保证,就难以使客户感到放心。
虽然很多企业都达到了ISO 9000的认证,但是真正做到完全符合ISO 9000要求的并不多。
因此建立这一体系需要全体员工全身心的投入,以精品战略来完成产品的生产。
教育训练在5S推动的整个过程中都要不断地进行教育训练。
在教育训练中,要以员工的心态教育为主,再培训员工发现问题、解决问题、提高效率的能力,同时在企业中进行提案改善活动,发挥员工的创造性。
教育训练由人事部门负责。
管理间接部门的效率化与5S活动类似,生产部门、设备部门、开发部门需要实施TPM以外,其他部门也要配合TPM的推行。
TPM自主保养推进的7大步骤与改善思维

TPM自主保养推进的7大步骤与改善思维在开展自主保养时,不可寄希望于一下解决所有问题,为此将目标和内容整理为7步,这就是“步进式自主保养”。
理想的方法是,彻底地做到每一步,待达到一定程度,再进入下一步。
TPM管理之自主保养的7个步骤为:初期清扫就是以设备为中心彻底清扫灰尘、垃圾等。
我们要将清扫变检查,检查能发现问题,发现设备的潜在缺陷,并及时加以处理。
同时通过清扫可有助于操作人员对设备产生爱护之心。
设备方面的目标:1.除去垃圾、污垢,使潜在的缺陷显现出来2.使老化,缺陷复原3.寻找垃圾、污垢发生源人员方便的目标:1.通过简单的清扫工作,熟悉小组活动2.圈长学习领导统御3.通过眼看、手触提高珍惜设备的心思,持有疑问和好奇心管理者的指导、援助:1.通过职能模式,起模范带头作用2.教导员工清扫重点处和清扫、注油、强化锁固的重要性为了保持和提高第一阶段初期清扫的成果,就要杜绝灰尘、污染等的根源(发生源),为此可采取消除或加盖、密封等对策。
对难于维护保养的部位,如加油、清扫、除污等,也应采取有效对策,提高设备的可维护保养性。
活动内容:1.进行飞散防止对策2.改善清扫困难度,缩短时间设备方面的目标:1.防止垃圾、污垢的发生、粘附,提高设备的可靠性2.确实维持设备的清扫状态,提高保全性人员方面的目标:1.学习机械的动作、加工的原理2.以身边的垃圾、污垢为课题来改善设备,学习其思专方法,推行方法3.对改善设备持有兴趣和积极性4.体会改善成功的喜悦管理者的指导、援助:1.教导机械的动作、加工原理2.通过哪里—哪里,什么—什么的分析技巧,教导分析现象的思考方法、手段3.增加让改善构思具体化的频度根据第一、第二步活动所取得的体会,编写一个临时基准,以保养自己分管的设备,如清扫、加油,紧固等基本条件。
设备方面的目标:1.改善供油困难处(个所)2.实施目视管理3.确实维持设备的基本条件(清扫、注油、强化锁固)使防止老化的活动能够扎根人员方面的目标:1.制定自己的基准并遵守2.指导遵守的要性,学习何谓管理3.每个人都具有职责意识和团队精神管理者的指导、援助:1.准备润滑管理规定2.教导润滑、点检,指导实际技能3.教导清扫、注油基准的制定方法,指导协助编制为了充分发挥设备的固有功能,要学习设备结构、功能及判断基准,检查设备各主要部分的外观,发现设备的缺陷并使之复原,同时使自己掌握必要的检查技能。
TPM个别改善活动
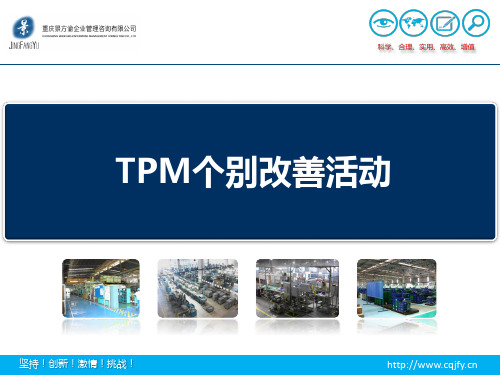
谢
科学!合理!实用!高效!增值!
谢
PM分析的步骤
PM分析,针对慢性不良通过以下步骤来找到原因并采取对策。 1.现象的明确化 2.现象的物理分析 3.讨论成立条件 把现象进行充分的分类 图示结构,构造 用物理的角度解析现象,从原理,原则方面说明 全面研讨 对条件成立便会发生的现象进行整理
4.讨论和4M(人,机,料, 法)的关联
(7) 不良修理Loss
初期效率Loss
超负荷Loss 散热Loss 良品重量 (16)模具/器工具Loss (15) Energy Loss 有效ENERGY 良品数量 不良Loss 初期效率Loss CUT Loss 收缩Loss 添加Loss (14) 效率Loss
坚持!创新!激情!挑战!
[单位成本的效率化]
投入时间(日历) 负荷时间
运转时间
(1) 故障Loss (2) 准备调整Loss
纯工作工时
停止Loss (3) 更换品种Loss 清扫检查 等待指示 等待材料 其他停止Loss 等待工作 等待 确认质量 (调整测定) 不良Loss (5)空转瞬间停止LosM个别改善活动
坚持!创新!激情!挑战!
个 别 改 善 的 进 行 方 法
在主题别项目 活动中,向16 大零损失挑战
示范设 备设定
项目小组 组 成
16大损失 掌握确认
决定主题 制作推动 计 划
个别改善 项目活动
提高设备 固有的 信赖度 提高使用 信赖度 防止再发: 标准 重新检讨
坚持!创新!激情!挑战!
生产活动16大LOSS与个别改善 个别改善的着眼点
工时 < 人> <设备> 经过时间 计划停止 计划停止 (8) SD Loss
TPM之个别改善概论

路漫漫其悠远 2020/4/13
大綱
一.個別改善和生產力的提昇 二.損失的意義 三.妨害效率化的16大損失 四.推行生產效率化的方法 五.個別改善的進行方法 六.總合效率 七.損失別改善的方法
路漫漫其悠远
路漫漫其悠远
• 何謂生產力
生產活動中以最小的投入量(INPUT)得到最 大的產出量(OUTPUT)之生產效率化指標。 此指標稱之為生產力。
線示範工程
表
•人機圖
2 組成專案小組 3 掌握現狀之損失
• 專案小組組成
•16大損失之定義 •損失分析確認表 •某工程損失分析例
4 設定改善主題及目 •目標設備設定例個別改善主題一
標
覽表
•評估水準之設定例設備總合效率 之評估水準
5 擬定改善計畫
•擬定基本計畫個別改善 •個別改善計畫表例
改善十大步驟~2
極限值
路漫漫其悠远
時間
路漫漫其悠远
慢性損失的原因
發生原因 發生原因
發生原因
發生原因 發生原因 發生原因
發生原因 發生原因
原因 之
掌握
(單一原因)
(複數原因)
(複合原因的組合)
原因之追究與掌握有困難
路漫漫其悠远
應有狀態 - 現狀 = 損失
應有狀態
應有狀態的八個看法
使設備發揮、維持最高機能 和性能所必須具備的條件
T公司是生產汽車零件擁有員工500名的企業。以往雖然以加班或假 日上班來負荷承包量的增加,但因降低成本而由董事長要求在一定時間 內完成生產計劃。於是廠長李先生以引進TPM為對策,藉由謀求現有設 備的效率化,考慮不加班或假日不上班在一定時間內達成生產,並依更 有效率化地降低成本。
TPM体系结构介绍

1、生产系统效率化的个别改善
支柱简称
个别改善
自主维护 专业维护 开发管理 品质维护 人才培养
T P M 的 八 大 支 柱
2、建立操作人员的自主维护制 3、建立维护部门的计划维护体制 4、建立产品、设备开发管理体制 5、建立品质维护体制 6、建立教育、训练体制 7、建立管理、间接部门的效率化体制 8、建立安全、卫生和环境的管理体制 3
初期清扫 (清扫点检)
第2
灰尘.脏污的发生源、飞散的防止,及改 发生源、困难 善清扫.给油.锁紧.点检困难部份,以缩 部位对策 短点检时间
自主保养暂定 基准的制作 要 作成行动基准,使能在短时间内完成 清扫.给油.锁紧.点检(要定出平时 或定期做上述各项事项的时间表)
第3
自主保养展开的步骤
步骤 名 第4 第5 第6 第7 总点检 自主点检 标准化 自主管理 彻底化 称 活动内容
合计 故障时间150分钟 请计算MTBF MTTR
10
自主保养步骤——STEP 0(事前准备)
设备综合效率:OEE=时间稼动率×性能稼动率×良品率 时间稼动率> 90%; 性能稼动率> 95%; 良 品 率> 99%; 世界级的OEE > 85%。我国较先进的制造企业OEE效率远远低于85%
投入时间 稼动时间
●
● ● ● ●
●
● ● ● ●
●
●
● ●
● ● ●
教育培训
●
4
●
●
●
设备维护基础工作的重要性
结论:在设备进入正常运行阶段,日常保养极端重要!
5
搞错没有!又弄 坏了叫我修!
我是生产的人,你 是修理的人
自己的设备由自己保养
TPM个别改善
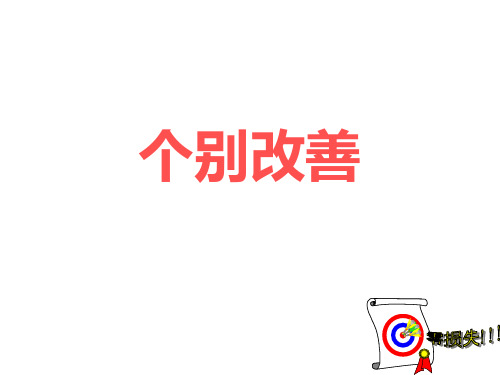
什么时候完成 你的目标是什么
持续改善
小组活动
Step 2-1 暴露并消除非正常状况
经验表明大多数损失起源于设备的恶化 在你所选主题区域内的部分在进行综合的 分析之前应进行修复并保持一个基本的状 况。 所以,应该为你的区域建立并保持清理、 润滑、点检的标准
这与自主维护相关联
个别改善 修复 & 创新
什么状况?
未来状况
创新: ex) 速度提升
“象新的” 状况 修复: ex) 没有故障
现在状况
绩效
1500 CC 普通车
个别改善
& 自主维护 ~ 3000 CC 快车 个别改善 能力提升
原先的 “象新的” 状况 状况恶化
自主维护 修复到 “象新的” 状 况 并保持“象新的
”状况
•通过坚决地消除损失和提高绩效来使设备、工序和车间的综 合效率达到最大化。 •提升员工的持续改善和团队合作的能力。
>损失
•故障,设置和切换,小停车,速度损失,开停机,质量缺陷 ,返工等等。
•或- “任何消耗资源但不创造任何价值的人类活动。”
知道你的损失在哪里-数据,数据,数据!
个别改善
个别改善 自主维护
主题没有包含方向和措施, 没有涉及工艺或生产, ( 0 )
理解现状使用了历史数据,
如前12个月的
(3)
没有研究来建立基本状况 (0)
在活动板上展示了修复前后的图片 (2)
没有做根源分析 (0)
进行了分析但没有提出解决方案 (1)
主题包含方向和措施, 涉及工艺或生产, (2) 有措施来明确你知道你的目标 是实际的且是有挑战性的
柱
持续不断的小组改善活动(工具和方法)
TPM强化改善5阶段

2011年09月28日本站原创关键字:TPM TPM强化TPM改善TPM第一时期—初期清扫;现在期通过对现场的完全5S以及对设备的修理修复,将我们的工作场所变成一个整齐洁净、舒服美观的现场。
通过第一时期的实施,最重要作用是改变了职员的认识,提升了大伙儿的意愿,强化了大伙儿的执行力,并在实施过程中培养了职员发觉现场问题的能力;TPM第二时期—困难点/发生源计策;在改善过程中,往往就会暴露出之前无法看到的问题,我们对其解决,对周围的内容着手进行改善,取得实质性的成效,在胜利的欢乐中加强自信。
我们在现在期已逐步培养出职员改善的能力。
TPM第三时期—总点检;这一时期的重点是让职员深入了解设备,了解与自己天天相处的生产现场,并以点检的形式形成自主治理模式,通过标准化的日常治理,建立一个防范于未然的机制。
职员参与治理的意愿和现场改善能力的提升,为我们最终建立自主治理体制奠定了坚实的基础。
TPM第四时期—提高点检效率〔目视化治理〕;为了更好的实施我们的日常治理,我们应该建立一个看得见的治理模式,让大伙儿一目了然。
第四时期确实是以此为目标,利用目视化治理那个工具,提高点检效率,提高劳动生产率。
TPM第五时期—自主治理体制建立;通过企业长时刻推行TPM,就能够实现我们的理想目标,建立一个全员参与的自主治理体制。
在那个体制下,我们不但能够自己解决各种各样的〝冰山〞,同时还能够积极防止〝冰山〞的产生,达到故障、不良、白费的〝零〞目标。
2011年09月28日本站原创关键字:TPM TPM差不多原理TPM原理TPM治理TPM作为一种治理工具,他不仅有自己的使用方法,还有自己的使用原那么,假如只是了解方法而没有遵循原那么,就会使其变成空中楼阁,无法真正贴合我们现场。
那个地点简单说明一下他的使用原那么。
第一,TPM强调的是全员参与,也确实是说,在企业里上至总经理,下至一线职员都需要参与进TPM推进过程中,专门是企业领导,更要有一种〝我是领导,我来示范〞的理念。
TPM管理如何在实操中进行个别化改善

TPM管理如何在实操中进行个别化改善?
TPM管理作为一种先进的生产管理方式,正逐渐被越来越多的企业所采用。
然而,在实操中,如何实现个性化改善却是很多企业面临的难题。
本文,深圳天行健精益生产管理咨询公司就这一问题作出如下解答:
设定目标:首先,需要明确改善的目标,例如提高设备的利用率、降低故障率等。
收集数据:通过收集设备运行数据和故障数据,可以了解设备的运行状况和存在的问题,为后续的改善提供依据。
分析问题:对收集到的数据进行分析,找出设备存在的问题和潜在的改善点。
可以采用一些常用的工具,如故障模式与影响分析(FMEA)、鱼骨图等。
制定改善计划:根据问题分析的结果,制定相应的改善计划。
计划应具体明确,包括改善的具体内容、责任人、时间节点等。
实施改善:按照制定的改善计划,组织人员进行改善工作。
在改善过程中,要充分发挥团队的协作和创造力,提出创新的解决方案。
持续改进:改善工作不应停留在一次行动,而是要持续进行。
通过定期的维护和保养,及时处理设备问题,确保设备的稳定运行。
培训和宣传:为了使TPM管理取得更好的效果,需要对全员进行培训和宣传,提高员工的技能水平和参与意识。
通过以上的步骤,可以实现TPM管理的个别化改善。
每个企业的具体情况不同,需要根据自身的实际情况来确定改善的重点和方向。
TPM管理需要全员的参与和共同努力,通过不断的改善和持续的学习,可以提高设备的效率和可靠性,为企业的发展提供有力支持。
TPM个别改善(ppt文档)

知道你的损失在哪里-数据,数据,数据!
1: 了解现状并设置目的
了解现状
用数据说话 !
设置你的目的
你怎么知道你的目标是可以达到的?
什么时候完成? DATE / / 99
你的目标是什么?
5W’s & 1H What 目的? 什么
Why 必要性? 为什么
Where 位置? 在哪里
计划: 数据分析
做: 改善
检查: 结果怎样? No
Yes
行动: 不会再发生!
活动板 “QC Story”
同级推广
- 5W1H - 7 QC tools (Pareto, Fishbone, e -Why why 分析 -生产组织法 -PM 分析 -FMEA(故障模式和影响分析)
操作工做展示 •激励的提高 •改善的推广
绩效
1500 CC 普通车
个别改善
& 自主维护 ~ 3000 CC 快车 个别改善 能力提升
原先的 “象新的” 状况 状况恶化
自主维护 修复到 “象新的” 状 况 并保持“象新的
”状况
年
1
2
3
4
5
个别改善 TPM小屋
(Protecting / maintaining the improved building)
持续改善
小组活动
Step 1-2 设பைடு நூலகம்你的目的
设置SMART的目的
Specific 具体的 Measurable可衡量的 Achievable可以达成的 Realistic现实的 Time bound在时间限度内的
使用你的 SMART 的目的
“你怎么知道你的目标是可以达成的?”
TPM的个人建议

TPM工作建议TPM是指全员生产性保全活动,TPM工作是为了更好的落实设备工装维护、管理工作,响应公司TPM小组推进目标,形成全员参与的良好氛围,切实做好设备、工装日常保养、维护,减少或防止设备、工装突发故障发生,保持和恢复设备、工装精度和性能,提升设备、工装状态和管理水平,保持生产顺利进行。
TPM的八大支柱是:个别改善、自主保全、专业保全、开发管理、品质保全、人才培养、事务改善、环境改善。
TPM活动的6S是整理、整顿、清扫、清洁、素养、安全。
以6S为切入点,开展TPM活动。
6S是TPM活动的基础,是TPM活动的突破口;6S同样要程序、规范管理:确定区域、人员、标准、周期、方法,并有检查评估方案;6S 中必然发现根源性的问题——引入清除六源内容。
TPM的寻找和清除“六源”活动,“六源”为污染源、浪费源、故障源、缺陷源、事故危险源、清扫困难源。
公司开展TPM自主保全活动展开的五大阶段:1)、初期清扫(清扫点检)2)、发生源、困难处的对策3)、总点检4)、点检效率化5)、自主管理。
第一阶段:初期清扫1、初期清扫的目的:①以设备本体为中心的垃圾、尘埃、污染彻底排除。
②防止强制劣化。
③透过清扫找出潜在缺陷,并予显现及处置。
2、经由清扫接触设备的各部位(看、摸),可发现部位的不良点有振动、发热、松动、症兆。
3、初期清扫的要求:①要将看得见和看不见的地方都清扫干净;②对清扫工作要进行规范化管理,制定清扫标准,并按标准实施清扫;③长期坚持不懈,把清扫工作当作日常工作的一部分,持续实施。
4、对设备的清扫必需做到操作工人自己动手,且进行全面清扫,维修人员对清扫活动进行技术支持。
5、经常为设备清扫是发现设备微小问题和变化,从而预防大问题、严重故障出现的最实用方法;第二阶段:发生源、困难处的对策1、TPM第二阶段的主要内容是发生源及困难部位改善对策。
TPM 第二阶段的目的是:改善垃圾、污垢、污染的发生源,飞散的防止或清扫、加油、点检的困难处所,以缩短清扫、加油、点检时间和学习设备改善的思考方法,以提升实质的效果。
tpm的稿件

tpm的稿件1.有关TPM的诗歌朗诵.宣誓的稿件TPM:全员生产维护1.自主维护自主维护就是每一个操作人员维护和保养自己的设备,对自己的设备进行日常点检、加油、更换零件、修理、早期发现故障和校正精度等。
自主维护的开展分七个步骤:初期清扫、发生源和难点问题的解决、制定自主维护的临时标准、总检点、自主检点、标准化、自主管理的最终落实。
2.个别改善个别改善就是为了实现公司的经营方针和经营目标而进行的一些具体和重大的项目改善活动。
开展个别改善需要解决三个问题:首先,有效把握自己部门及岗位存在的问题和损耗;其次,对照公司或部门目标,决定在某个时期内需要解决的项目;最后,以最短的时间完成课题改善活动,达到改善目标。
个别改善有七个基本步骤:课题的选定、现状把握、要因分析、对策制定和实施、效果评价、标准化、评价和反省。
3.专业维护专业维护就是专门的设备维护部门对设备进行预防维护和计划维护,并通过诊断技术来提高设备状况的预知力。
将设备管理的职能进行细分是必要的,设备的日常管理交给生产部门进行自主管理,同时要拥有高水平、专业化的维护队伍。
专业维护全要有能力指导和帮助自主维护活动的开展。
专业维护队伍的建立也不排除请外部专业机构实施某些特殊的维护业务。
4.初期管理产品设计的初期管理是指实现易于制造的产品设计的过程。
把顾客的需求即使用的方便性需求,和生产现场的情况即生产的方便性需求结合到设计中去是初期管理的重要内容。
设备和生产技术的初期管理是指通过生产技术革新,达到新产品的垂直导入(即在很短的时间内完成新产品的试验,并快速开始批量生产)以及设备的维护预防设计。
5.事务改善事务改善是间接部门的事务革新活动,TPM是全员参与的持久的集体活动,没有管理间接部门的支持,活动是不可能持续下去的。
活动的内容包括生产管理、销售管理、行政后勤管理以及其他间接管理业务的改善活动。
事务改善的目的是改进管理系统,消除各类管理损耗,减少间接人员,提高办事效率,更好的为生产活动服务。
- 1、下载文档前请自行甄别文档内容的完整性,平台不提供额外的编辑、内容补充、找答案等附加服务。
- 2、"仅部分预览"的文档,不可在线预览部分如存在完整性等问题,可反馈申请退款(可完整预览的文档不适用该条件!)。
- 3、如文档侵犯您的权益,请联系客服反馈,我们会尽快为您处理(人工客服工作时间:9:00-18:30)。
这与自主维护相关联
-
20
持续改善
小组活动
Step 2-2 暴露并消除非正常状况
从检查主题区域开始来查找这个区域为什么会恶 化的线索。使用故障部位图(Fugui Map)和故障 清单(Fugui list)辨明具体的问题。消除这些问 题,将主题区恢复到基本的状况,并再次衡量( 应会有所收益) 用起草清理、润滑、点检标准(一点课程)来确保 所得到的收益不会流走。通过AM发展团队来将这 些新标准放入AM系统。
1
2
3
4
-
年
5
7
个别改善 TPM小屋
(Protecting / maintaining the improved building)
个别改善 (通向更高层的建筑体)
自主维护
(基-础)
8
个别改善的阶段1
损失的定义 识别损失
优选 选择主题
责任 目标 登记
筛选 参与
递交计划
-
-重要的 ? -影响是否太 ? -在三个月内完成 ? -能否同级推广 ?
个别改善
-
1
TPM 活动的架构
行业内的一流企业:有良好效益,有持续发展动力的企业
评价指标: 质量 成本 交期 安全 生产力 士气
建立高生产性的生产线 建立不产生不良 培育技能好的员工
八 大
自 计 个 品 初 事环教
主 划 别 质 期 务境育
T
保 保 改 保 管 改安培
P
支
全 全 善 全 理 善全训
M
柱
持续不断的小组改善活动(工具和方法)
活
动
两
目视管理
内
基
容
石
彻底的-「 5S」运动
2
个别改善内容
• 什么叫改善? • 损失介绍 • 改善的步骤 • 改善活动板简介
-
3
用日语表达的改善
•KAI = 变化 •ZEN = 好 (为了更好) •KAIZEN = 改善
-
4
集中改善的目的
个别改善
通往世界级制造工厂的必由之路
>目的
•通过坚决地消除损失和提高绩效来使设备、工序和车间的综 合效率达到最大化。
•提升员工的持续改善和团队合作的能力。
>损失
•故障,设置和切换,小停车,速度损失,开停机,质量缺陷 ,返工等等。
•或- “任何消耗资源但不创造任何价值的人类活动。”
知道你的损失在哪里-- 数据,数据,数据!
5
个别改善 自主维护
什么时候完成? DATE / / 99
你的目标是什么?
-
16
5W’s & 1H What 目的? 什么
Why 必要性? 为什么
Where 位置? 在哪里
问题 * 那是什么?
* 这是为了什么? * 如果那个操作被取消,会发生什么? *什么其它的应当做? * 为什么现在在做这件事? * 为什么这是必要的? * 为什么用这种方法? *位置在哪? *为什么那里? *能否把事情组合到一个地方? *位置是应该改变?
18
1. 设置目的
设置目的
你如何知道你的目标是可以达到的?
什么时候完成 你的目标是什么
-
19
持续改善
小组活动
Step 2-1 暴露并消除非正常状况
经验表明大多数损失起源于设备的恶化 在你所选主题区域内的部分在进行综合的 分析之前应进行修复并保持一个基本的状 况。 所以,应该为你的区域建立并保持清理、 润滑、点检的标准
-经理 -主管 -项目组
改善多少 ? 什么时候 ? -> 行动计划
TPM办公室
9
个别改善的阶段 2
计划: 数据分析
做: 改善
检查: 结果怎样? No
Yes
行动: 不会再发生!
活动板 “QC Story”
同级推广
- 5W1H - 7 QC tools (Pareto, Fishbone, e -Why why 分析 -生产组织法 -PM 分析 -FMEA(故障模式和影响分析)
么做
* 做这件事将花费多少? -
17
持续改善
小组活动
Step 1-2 设置你的目的
设置SMART的目的
Specific 具体的 Measurable可衡量的 Achievable可以达成的 Realistic现实的 Time bound在时间限度内的
使用你的 SMART 的目的
“你怎么知道你的目标是-可以达成的?”
回答以下问题
我们在做什么?
我们为什么这么做?
对业务的好处是什么?
要考虑的地方
工艺中的瓶颈.
有很大损失的设备
所有线都通用的设备
能够在三个月内完成
-
13
0: 选择你的主题
选择你的主题
当输送系统进入堆积模式时,大多数在运输带上的 盒子被损坏了。这意味着大多数的盒子被浪费了。 另外,损坏的盒子会进入设备,造成设备损坏。
When什 次顺? 么时候
*那是什么时候? *这为什么那个时候做? *做这个事情最合理的时间应是何时? *这个事情能否在另一个时间做?
Who 人? 谁
* 为什么这个人做这个操作? * 这项工作是否需要特殊的资格? * 是否有其它人在别处做同样的事情?
How 怎 方法?
* 为什么用这种方法做? * 那是否是做这件事的最好方法,或者我们能否用更好的方法做这件事?
-
14
持续改善
小组活动
Step 1-1 理解现状 收集问题的历史数据. 找出停机时间分析, 工程记录, 备件使用情况等 等,等等
在你的主题内收集关于具体问题的现在的详细信 息
知道你的损失在哪里-数据,数据,数据!
-
15
1: 了解现状并设置目的
了解现状
用数据说话 !
设置你的目的
你怎么知道你的目标是可以达到的?
小组活动
Step 0 小组怎样选择主题
主题由团队全体选定,必须针对团队 的目标和指标
作为一个团队问以下问题?
这是否是一个值得关注的问题?
你的老板是否会支持你的工作?
通过团队的努力,团队能否自己完成
这项工作?
通过这次经历,你能得到什么吗?
这能否锻炼你的创造力?
-
12
持续改善
小组活动
Step 0 选择这个主题的理由
操作工做展示
•激励的提高
-
•改善的推广
10
持续改善
通向成功改善的八个步骤
Step 0 选择主题 Step 1 理解现状 Step 2 暴露并消除不正常状况 Step 3 分析原因 Step 4 对改善进行计划 Step 5 执行改善 Step 6 检查结果 Step 7 采取措施已防再发生
-
11
持续改善
个别改善 修复 & 创新
什么状况?未来状况创新: ex) 速度提升
“象新的” 状况 修复: ex) 没有故障
现在状况
-
6
绩效
1500 CC 普通车
个别改善
& 自主维护 ~ 3000 CC 快车 个别改善 能力提升
原先的 “象新的” 状况 状况恶化
自主维护 修复到 “象新的” 状况 并保持“象新
的”状况