纯电动汽车制动系统计算方案
新能源车辆制动系统方案范本(四篇)

新能源车辆制动系统方案范本____年新能源车辆制动系统的方案第一部分:电动汽车制动系统1. 制动能量回收技术由于电动汽车在行驶过程中存在能量损耗的问题,制动能量回收技术成为了一项重要的创新内容。
通过引入制动能量回收装置,将制动时产生的能量转化为电能储存起来,以供驱动电动汽车使用。
这种技术不仅提高了能源利用效率,也减少了对电池的依赖,延长了电池使用寿命。
2. 制动力分配系统由于电动汽车的动力系统与传统车辆存在一定的差异,制动力分配系统需要进行相应的调整。
根据电动汽车的动力性能和质量分布等因素,合理分配前后轮制动力,提高制动效果和稳定性,并减少制动过程中的能量损耗。
3. 制动辅助系统为了提高电动汽车的安全性和稳定性,制动辅助系统也需要进行改进。
包括提供制动效果的预警系统、自动刹车系统等,以确保驾驶员在遇到紧急情况时能够及时做出反应并减少事故的发生。
第二部分:氢燃料电池汽车制动系统1. 高效制动液氢燃料电池汽车的制动系统液压系统对制动液的要求更加严格,需要使用高效制动液。
这种制动液具有较高的沸点和阻尼性能,能够更好地适应高速制动和长时间制动,提高制动稳定性和耐久性。
2. 制动力调整系统氢燃料电池汽车的动力系统与传统汽车有所不同,制动力调整系统应根据氢燃料电池汽车的特性和行驶状态进行调整,以提高制动效果和稳定性。
3. 制动信号传输系统由于氢燃料电池汽车使用的是电子制动系统,制动信号传输系统也需要进行改进。
采用更先进的传输技术,确保制动信号的准确传输,提高制动反应速度和安全性。
结论:随着新能源汽车的快速发展,制动系统作为汽车安全的核心保障之一,也需要进行相应的创新和改进。
____年的新能源汽车制动系统方案包括电动汽车制动系统和氢燃料电池汽车制动系统,通过引入制动能量回收技术、制动力分配系统和制动辅助系统等新技术,提高制动效果、稳定性和安全性,推动新能源汽车的进一步发展。
新能源车辆制动系统方案范本(二)____年新能源车辆制动系统方案一、引言二、背景分析1. 新能源车辆市场需求增加:随着环境保护要求的提高和汽车市场的竞争加剧,新能源车辆的市场需求有望继续增加。
纯电动汽车制动系统的组成
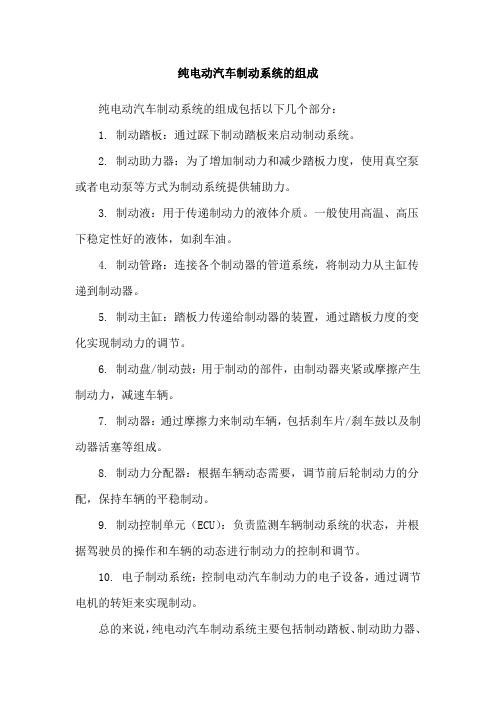
纯电动汽车制动系统的组成
纯电动汽车制动系统的组成包括以下几个部分:
1. 制动踏板:通过踩下制动踏板来启动制动系统。
2. 制动助力器:为了增加制动力和减少踏板力度,使用真空泵或者电动泵等方式为制动系统提供辅助力。
3. 制动液:用于传递制动力的液体介质。
一般使用高温、高压下稳定性好的液体,如刹车油。
4. 制动管路:连接各个制动器的管道系统,将制动力从主缸传递到制动器。
5. 制动主缸:踏板力传递给制动器的装置,通过踏板力度的变化实现制动力的调节。
6. 制动盘/制动鼓:用于制动的部件,由制动器夹紧或摩擦产生制动力,减速车辆。
7. 制动器:通过摩擦力来制动车辆,包括刹车片/刹车鼓以及制动器活塞等组成。
8. 制动力分配器:根据车辆动态需要,调节前后轮制动力的分配,保持车辆的平稳制动。
9. 制动控制单元(ECU):负责监测车辆制动系统的状态,并根据驾驶员的操作和车辆的动态进行制动力的控制和调节。
10. 电子制动系统:控制电动汽车制动力的电子设备,通过调节电机的转矩来实现制动。
总的来说,纯电动汽车制动系统主要包括制动踏板、制动助力器、
制动液、制动管路、制动主缸、制动盘/制动鼓、制动器、制动力分配器、制动控制单元和电子制动系统等组成部分。
纯电动汽车刹车制动力分配策略研究
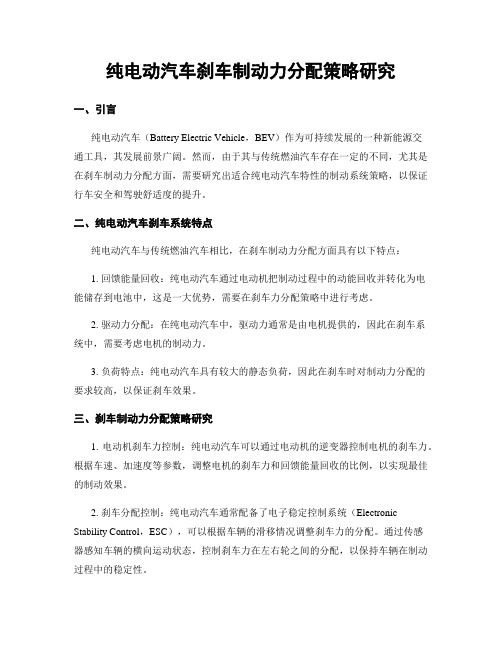
纯电动汽车刹车制动力分配策略研究一、引言纯电动汽车(Battery Electric Vehicle,BEV)作为可持续发展的一种新能源交通工具,其发展前景广阔。
然而,由于其与传统燃油汽车存在一定的不同,尤其是在刹车制动力分配方面,需要研究出适合纯电动汽车特性的制动系统策略,以保证行车安全和驾驶舒适度的提升。
二、纯电动汽车刹车系统特点纯电动汽车与传统燃油汽车相比,在刹车制动力分配方面具有以下特点:1. 回馈能量回收:纯电动汽车通过电动机把制动过程中的动能回收并转化为电能储存到电池中,这是一大优势,需要在刹车力分配策略中进行考虑。
2. 驱动力分配:在纯电动汽车中,驱动力通常是由电机提供的,因此在刹车系统中,需要考虑电机的制动力。
3. 负荷特点:纯电动汽车具有较大的静态负荷,因此在刹车时对制动力分配的要求较高,以保证刹车效果。
三、刹车制动力分配策略研究1. 电动机刹车力控制:纯电动汽车可以通过电动机的逆变器控制电机的刹车力。
根据车速、加速度等参数,调整电机的刹车力和回馈能量回收的比例,以实现最佳的制动效果。
2. 刹车分配控制:纯电动汽车通常配备了电子稳定控制系统(Electronic Stability Control,ESC),可以根据车辆的滑移情况调整刹车力的分配。
通过传感器感知车辆的横向运动状态,控制刹车力在左右轮之间的分配,以保持车辆在制动过程中的稳定性。
3. 制动系统与驱动系统的协同控制:纯电动汽车的驱动系统和刹车系统可以进行协同控制,以提高整车的刹车性能和能量回收效率。
通过电动机控制器和制动系统的信息交互,实现驱动力和制动力的协同分配,既能保证刹车安全,又能最大程度地回收能量。
4. 基于车辆动力学模型的刹车制动力分配策略:通过建立纯电动汽车的动力学模型,考虑车辆的质量、惯性、制动器特性等因素,基于最优化算法确定最佳的刹车力分配策略,以实现制动距离的最小化和驾驶舒适性的提升。
四、刹车制动力分配策略的实验验证和优化1. 实验设备与测试方法:建立实验台架,采用刹车力测量传感器对刹车力进行实时监测,在不同速度和路况下进行刹车测试,以评估刹车力分配策略的性能。
纯电动汽车制动器的设计与创新
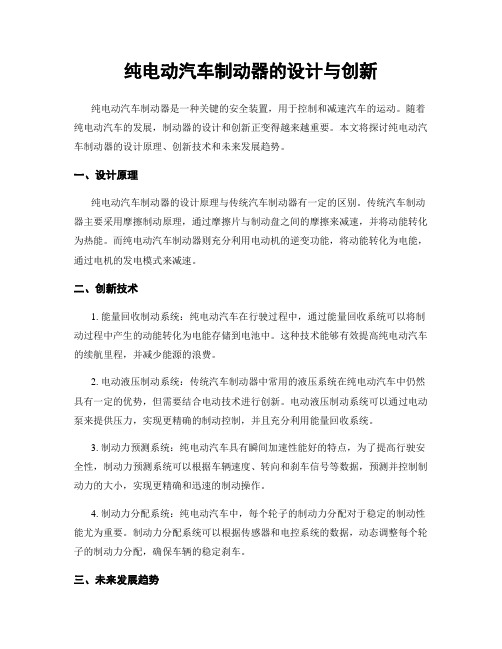
纯电动汽车制动器的设计与创新纯电动汽车制动器是一种关键的安全装置,用于控制和减速汽车的运动。
随着纯电动汽车的发展,制动器的设计和创新正变得越来越重要。
本文将探讨纯电动汽车制动器的设计原理、创新技术和未来发展趋势。
一、设计原理纯电动汽车制动器的设计原理与传统汽车制动器有一定的区别。
传统汽车制动器主要采用摩擦制动原理,通过摩擦片与制动盘之间的摩擦来减速,并将动能转化为热能。
而纯电动汽车制动器则充分利用电动机的逆变功能,将动能转化为电能,通过电机的发电模式来减速。
二、创新技术1. 能量回收制动系统:纯电动汽车在行驶过程中,通过能量回收系统可以将制动过程中产生的动能转化为电能存储到电池中。
这种技术能够有效提高纯电动汽车的续航里程,并减少能源的浪费。
2. 电动液压制动系统:传统汽车制动器中常用的液压系统在纯电动汽车中仍然具有一定的优势,但需要结合电动技术进行创新。
电动液压制动系统可以通过电动泵来提供压力,实现更精确的制动控制,并且充分利用能量回收系统。
3. 制动力预测系统:纯电动汽车具有瞬间加速性能好的特点,为了提高行驶安全性,制动力预测系统可以根据车辆速度、转向和刹车信号等数据,预测并控制制动力的大小,实现更精确和迅速的制动操作。
4. 制动力分配系统:纯电动汽车中,每个轮子的制动力分配对于稳定的制动性能尤为重要。
制动力分配系统可以根据传感器和电控系统的数据,动态调整每个轮子的制动力分配,确保车辆的稳定刹车。
三、未来发展趋势未来纯电动汽车制动器的设计与创新将面临一些挑战和发展方向。
1. 轻量化:纯电动汽车制动器需要满足电动汽车的高效率和高性能要求,同时也需要提高续航里程。
因此,制动器的轻量化将成为未来的发展趋势,通过采用新材料和新工艺,减轻制动器的重量,提高整车的能效。
2. 智能化:未来纯电动汽车制动器将更加智能化。
智能制动控制系统可以根据车辆行驶状态、路况和驾驶者的行为,实现主动的制动力控制,提供更准确和平稳的制动效果。
新能源汽车制动系统解析(三)

◆文/江苏 高惠民新能源汽车制动系统解析(三)(接上期)二、集成动力制动模块化与自动驾驶随着车辆行驶稳定程序系统(ESP)和安全带、安全气囊等被动安全系统的引入,驾驶安全性得到了提高,道路交通死亡和严重伤害的情况在过去几十年中不断减少。
但由于人们对个人移动性的需求快速增加,这导致更高的交通密度,交通复杂性和对驾驶员的压力越来越大。
统计数据显示,驾驶员仍然是事故的重要来源。
为了进一步提高驾驶安全性,并将驾驶员从车辆引导的复杂任务中解放出来,几乎所有的汽车制造商和零件供应商都全力投入到自动驾驶(HAD)汽车的研发中。
这些自动驾驶新技术与减少CO 2和提高能源效率的电气化相同,将在未来几年内推向市场。
至少在几个特定环境的用例中,车辆应该能够在没有人类驾驶员帮助或指导的情况下提供驾驶能力。
根据车辆具备的自动驾驶程度,美国汽车工程师协会(Society of Automotive Engineers,SAE)将其划分为L0-L5的自动驾驶等级。
如图20所示。
若用“眼、手、脚”三个方面来判断车辆的自动驾驶程度,L0阶段则需要驾驶员的“眼、手、脚”全部参与来操作汽车。
随着自动驾驶程度的提高,自动驾驶系统逐渐提供更多的驾驶辅助功能,进而能实现“脱脚”,“脱手”再到“脱眼”功能。
自动驾驶汽车技术架构如图21所示。
在自动驾驶的子系统图20 SAE自动驾驶等级划分图21 自动驾驶系统技术架构功能中,车辆制动系统担任了重要的角色。
尤其是新型制动系统需要为自动驾驶提供主动制动、能量回收和车辆稳定性控制等功能,同时在L3级别以上的自动驾驶中,还对制动系统冗余备份功能提出了需求。
1.制动系统架构新技术通过动力传动系统的电气化和对优化能源效率的需求,新的制动系统已被引入市场。
除了传统的真空伺服制动系统外,还有新的节能制动系统,如机电伺服制动助力器(例如iBooster)。
值得一提的是,第一代iBooster能与ESP+主动蓄能器(Smart Actuator)组成3-Box方案,而第二代iBooster能与ESP配合组成2-Box方案,这两种制动系统方案能实现车辆的主动制动、能量回收及车辆纵、横向稳定性控制等功能,但是也存在着结构不够紧凑,单个部件不能实现制动压力解耦等缺点。
纯电动汽车制动器原理与设计

纯电动汽车制动器原理与设计纯电动汽车是未来交通发展的重要方向,其中制动系统是保证行车安全的核心组成部分。
本文将介绍纯电动汽车制动器的原理与设计。
一、纯电动汽车制动器的原理纯电动汽车的制动器与传统燃油汽车存在一些不同之处。
传统燃油汽车通常采用液压制动系统,而纯电动汽车则常常采用电子制动系统。
电子制动系统包括:再生制动、摩擦制动和电子控制单元。
1. 再生制动纯电动汽车在行驶中,电动机可以变为发电机,将制动能量转化为电能,并将之存储到电池中。
这种方式被称为再生制动。
在再生制动模式下,电机通过制动扭矩来减速车辆。
2. 摩擦制动如果再生制动无法满足需要,纯电动汽车将会使用摩擦制动来减速。
摩擦制动通过制动盘或制动鼓与轮胎发生摩擦,将车辆减速。
摩擦制动是常用的制动方式,用于控制车辆的速度和停车。
3. 电子控制单元电子控制单元是纯电动汽车制动器的核心部分,它负责监测车辆状态、控制制动力度以及协调再生制动和摩擦制动的转换。
电子控制单元将车辆的实时数据进行处理,并根据司机的制动需求来实施相应的制动操作。
二、纯电动汽车制动器的设计1. 制动器类型选择纯电动汽车制动器的类型通常包括:电磁制动器、摩擦制动器和再生制动器。
不同类型的制动器有各自的适用场景和优缺点。
设计者需要根据车辆的使用情况和性能要求来选择合适的制动器类型。
2. 制动力度调整电子控制单元负责控制制动力度,可以根据速度、加速度和司机的制动需求来调整制动力度。
设计者需要考虑适当的制动力度范围,以满足不同驾驶情况下的制动要求。
3. 制动系统集成纯电动汽车的制动系统需要与其他系统进行集成,如动力系统和车辆稳定性控制系统。
制动系统和其他系统的协调性设计可以提高整车的性能和安全性。
4. 制动器的热管理纯电动汽车的制动器在长时间制动或制动过程中会产生大量的热量。
为了保证制动器的正常工作,设计者需要考虑有效的热管理系统,如散热风扇、散热片和冷却液等。
5. 制动器的可靠性和耐久性纯电动汽车制动器的可靠性和耐久性对行车安全至关重要。
2024年新能源车辆制动系统方案(三篇)
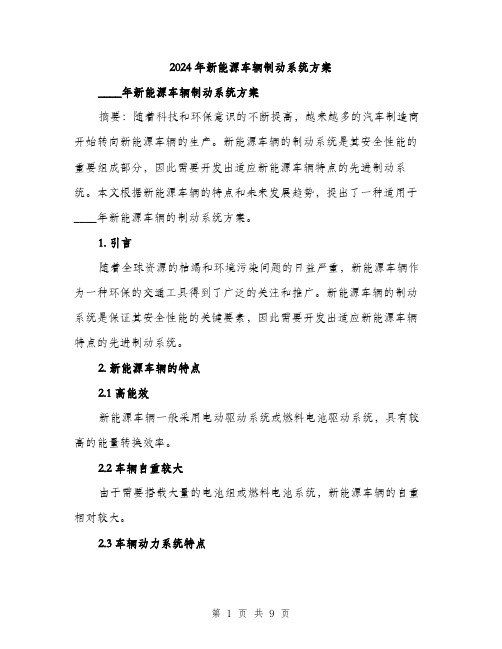
2024年新能源车辆制动系统方案____年新能源车辆制动系统方案摘要:随着科技和环保意识的不断提高,越来越多的汽车制造商开始转向新能源车辆的生产。
新能源车辆的制动系统是其安全性能的重要组成部分,因此需要开发出适应新能源车辆特点的先进制动系统。
本文根据新能源车辆的特点和未来发展趋势,提出了一种适用于____年新能源车辆的制动系统方案。
1. 引言随着全球资源的枯竭和环境污染问题的日益严重,新能源车辆作为一种环保的交通工具得到了广泛的关注和推广。
新能源车辆的制动系统是保证其安全性能的关键要素,因此需要开发出适应新能源车辆特点的先进制动系统。
2. 新能源车辆的特点2.1 高能效新能源车辆一般采用电动驱动系统或燃料电池驱动系统,具有较高的能量转换效率。
2.2 车辆自重较大由于需要搭载大量的电池组或燃料电池系统,新能源车辆的自重相对较大。
2.3 车辆动力系统特点电动驱动系统或燃料电池驱动系统的特点是提供持续平稳的输出功率。
3. 制动系统方案基于新能源车辆的特点,我们提出了以下制动系统方案。
3.1 能量回收制动考虑到新能源车辆的高能效特点,我们应该充分利用车辆制动过程中产生的能量并回收利用。
设计制动系统时,应采用能量回收装置,将制动过程中的动能转换为电能存储到电池中,以供车辆的其他功耗使用,提高车辆的综合能效。
3.2 先进的制动控制系统由于新能源车辆的动力输出响应较快,制动系统的响应时间也要求更短。
因此,我们需要设计一种响应速度快、精确度高的制动控制系统。
可以采用电子制动系统,通过传感器实时监测车辆状态,并通过算法提前预测车辆的制动需求,从而实现更快、更准确的制动操作。
3.3 重量轻、结构简化针对新能源车辆自重较大的特点,我们需要在设计制动系统时尽量减少组件的重量,并采用结构简化的设计。
可以采用轻量化材料,如碳纤维等,来替代传统的制动系统组件,以减轻车辆自重并提高整车的能效。
4. 制动系统方案实施4.1 技术研发为了实现以上制动系统方案,需要进行相关的技术研发。
纯电动汽车制动系统的设计与优化
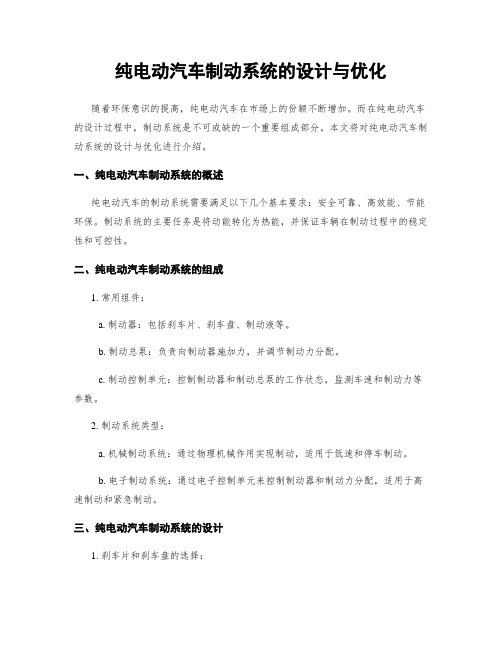
纯电动汽车制动系统的设计与优化随着环保意识的提高,纯电动汽车在市场上的份额不断增加。
而在纯电动汽车的设计过程中,制动系统是不可或缺的一个重要组成部分。
本文将对纯电动汽车制动系统的设计与优化进行介绍。
一、纯电动汽车制动系统的概述纯电动汽车的制动系统需要满足以下几个基本要求:安全可靠、高效能、节能环保。
制动系统的主要任务是将动能转化为热能,并保证车辆在制动过程中的稳定性和可控性。
二、纯电动汽车制动系统的组成1. 常用组件:a. 制动器:包括刹车片、刹车盘、制动液等。
b. 制动总泵:负责向制动器施加力,并调节制动力分配。
c. 制动控制单元:控制制动器和制动总泵的工作状态,监测车速和制动力等参数。
2. 制动系统类型:a. 机械制动系统:通过物理机械作用实现制动,适用于低速和停车制动。
b. 电子制动系统:通过电子控制单元来控制制动器和制动力分配,适用于高速制动和紧急制动。
三、纯电动汽车制动系统的设计1. 刹车片和刹车盘的选择:在纯电动汽车上,由于电机的反扭矩可以实现制动功能,对刹车片和刹车盘的要求相对较低。
可以选择轻量化的材料,降低整车质量,提高能源利用效率。
2. 制动液的选择:纯电动汽车的制动系统也可以使用常规的刹车液,但考虑到环保和能源浪费的问题,选择可再生液体制动介质是一个更加可行的选择。
3. 制动总泵的设计:纯电动汽车的制动总泵需要能够适应电机反扭矩带来的制动需求。
因此,在设计制动总泵时,需要根据电机的特性来确定制动力的输出需求,以保证制动系统的稳定性和可控性。
4. 制动控制单元的设计:制动控制单元需要能够实时监测车速、制动力等参数,并通过控制制动总泵和制动器来实现制动力的调节。
同时,还需要考虑电池能量的管理,以避免长时间制动造成能量浪费。
四、纯电动汽车制动系统的优化1. 刹车片和刹车盘的优化:可以通过优化材料的选择和结构的设计,降低刹车片和刹车盘的摩擦噪音和磨损,提高刹车的效能和使用寿命。
2. 制动液的优化:可以研究和开发可再生液体制动介质,减少对自然资源的依赖,提高能源利用效率。
纯电动车的制动系统毕业设计
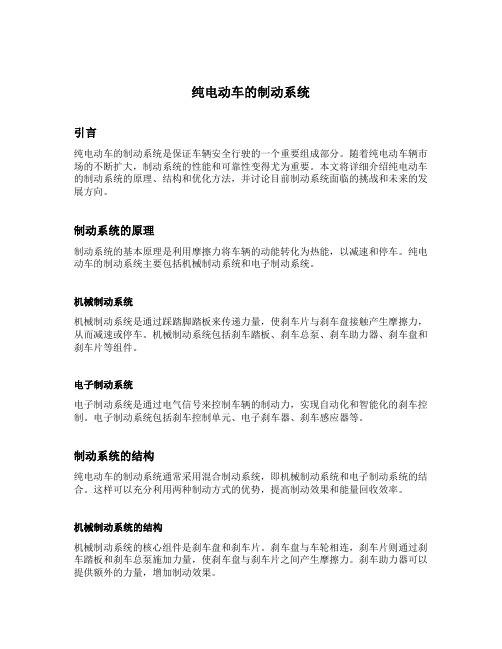
纯电动车的制动系统引言纯电动车的制动系统是保证车辆安全行驶的一个重要组成部分。
随着纯电动车辆市场的不断扩大,制动系统的性能和可靠性变得尤为重要。
本文将详细介绍纯电动车的制动系统的原理、结构和优化方法,并讨论目前制动系统面临的挑战和未来的发展方向。
制动系统的原理制动系统的基本原理是利用摩擦力将车辆的动能转化为热能,以减速和停车。
纯电动车的制动系统主要包括机械制动系统和电子制动系统。
机械制动系统机械制动系统是通过踩踏脚踏板来传递力量,使刹车片与刹车盘接触产生摩擦力,从而减速或停车。
机械制动系统包括刹车踏板、刹车总泵、刹车助力器、刹车盘和刹车片等组件。
电子制动系统电子制动系统是通过电气信号来控制车辆的制动力,实现自动化和智能化的刹车控制。
电子制动系统包括刹车控制单元、电子刹车器、刹车感应器等。
制动系统的结构纯电动车的制动系统通常采用混合制动系统,即机械制动系统和电子制动系统的结合。
这样可以充分利用两种制动方式的优势,提高制动效果和能量回收效率。
机械制动系统的结构机械制动系统的核心组件是刹车盘和刹车片。
刹车盘与车轮相连,刹车片则通过刹车踏板和刹车总泵施加力量,使刹车盘与刹车片之间产生摩擦力。
刹车助力器可以提供额外的力量,增加制动效果。
电子制动系统的结构电子制动系统主要包括刹车控制单元、电子刹车器和刹车感应器。
刹车控制单元负责控制制动力的大小和分配,电子刹车器通过电气信号来实现制动力的传递。
刹车感应器可以检测车辆的速度和制动力,控制制动系统的工作状态。
制动系统的优化方法为了提高纯电动车的制动效果和能量回收效率,可以采取以下优化方法:1.使用高性能刹车片和刹车盘,提高摩擦力和散热性能;2.采用可调节刹车力的刹车控制单元,根据不同的行驶情况调整制动力的大小;3.引入能量回收系统,将制动时产生的能量转化为电能储存起来,供车辆使用;4.优化整个制动系统的协调控制算法,提高制动系统的响应速度和稳定性。
制动系统面临的挑战纯电动车制动系统在面临以下挑战时需要进一步改进:1.纯电动车辆的重量比传统燃油车辆更大,需要更高的制动力;2.随着电动车市场的发展,制动系统的可靠性和耐久性要求也越来越高;3.刹车片和刹车盘的摩擦材料对环境的污染较大,需要寻找更环保的替代材料;4.制动系统的智能化和自动化程度需要进一步提高。
纯电动汽车制动器的工作原理与设计分析
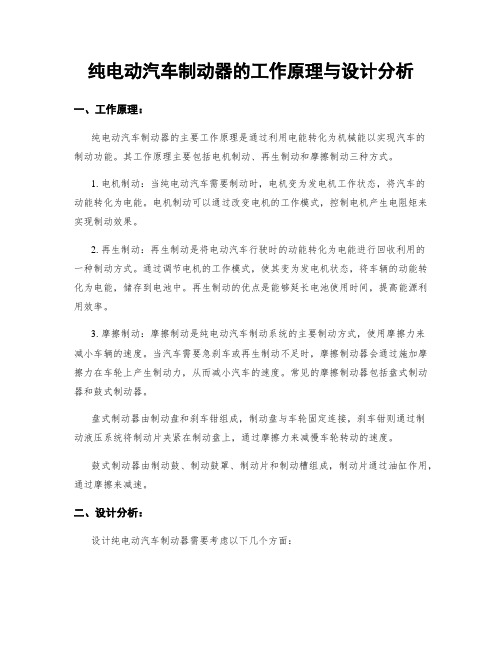
纯电动汽车制动器的工作原理与设计分析一、工作原理:纯电动汽车制动器的主要工作原理是通过利用电能转化为机械能以实现汽车的制动功能。
其工作原理主要包括电机制动、再生制动和摩擦制动三种方式。
1. 电机制动:当纯电动汽车需要制动时,电机变为发电机工作状态,将汽车的动能转化为电能。
电机制动可以通过改变电机的工作模式,控制电机产生电阻矩来实现制动效果。
2. 再生制动:再生制动是将电动汽车行驶时的动能转化为电能进行回收利用的一种制动方式。
通过调节电机的工作模式,使其变为发电机状态,将车辆的动能转化为电能,储存到电池中。
再生制动的优点是能够延长电池使用时间,提高能源利用效率。
3. 摩擦制动:摩擦制动是纯电动汽车制动系统的主要制动方式,使用摩擦力来减小车辆的速度。
当汽车需要急刹车或再生制动不足时,摩擦制动器会通过施加摩擦力在车轮上产生制动力,从而减小汽车的速度。
常见的摩擦制动器包括盘式制动器和鼓式制动器。
盘式制动器由制动盘和刹车钳组成,制动盘与车轮固定连接,刹车钳则通过制动液压系统将制动片夹紧在制动盘上,通过摩擦力来减慢车轮转动的速度。
鼓式制动器由制动鼓、制动鼓罩、制动片和制动槽组成,制动片通过油缸作用,通过摩擦来减速。
二、设计分析:设计纯电动汽车制动器需要考虑以下几个方面:1. 制动效果:确保制动器能够提供稳定而可靠的制动效果,能够在不同路况和工况下实现精确的制动控制。
制动器的设计应能够适应不同车速和负载条件下的制动需求。
2. 系统安全:纯电动汽车的制动系统安全性非常重要。
制动器的设计应具备高可靠性,必须能够保证制动器在极端情况下的稳定性和可控性,以确保乘车人员的安全。
3. 能源回收利用:再生制动对电池充电具有重要作用,设计制动器时应注重提高再生制动效能,实现对行驶中的动能的回收与储存。
4. 制动耐久性:纯电动汽车的制动器在长时间使用过程中必须具备较好的耐久性,在高强度的工作状态下不出现失效或损坏,能够长期稳定工作。
纯电动汽车电液制动力分配计算方法
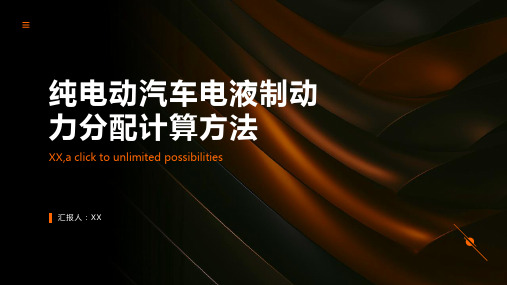
05
纯电动汽车电 液制动力分配 计算方法的未 来发展
01
纯电动汽车电液制动力 分配计算方法的概述
纯电动汽车电液制动力分配计算方法的定义
纯电动汽车电液制 动力分配计算方法 是一种用于计算纯 电动汽车电液制动 系统制动力分配的 方法。
该方法基于车辆动 力学和制动系统原 理,通过数学模型 和算法实现制动力 分配的计算。
局限性
纯电动汽车电液制动力分配计算方法的优势
提高制动性能:通过精确计算和控制,实现更快速、更稳定的制动效果。 节能环保:减少对传统制动系统的依赖,降低对环境的污染。 提升驾驶体验:提供更加平稳、舒适的制动感觉,提高驾驶安全性。 降低维护成本:减少机械部件的磨损和更换,降低维修保养成本。
纯电动汽车电液制动力分配计算方法的局限性
纯电动汽车电液制动力 04 分配计算方法的应用场
景
纯电动汽车电液制动力分配计算方法在车辆设计中的应用
制动系统设计:根据电液制动力分配计算方法,优化制动系统的设计,提高制动性能和安全性。
车辆稳定性控制:通过电液制动力分配计算方法,实现车辆在不同行驶状态下的稳定性控制, 提高车辆行驶的平稳性和安全性。
添加标题
在计算过程中,该方法会根据车辆的实时状态和车轮 的附着条件,对制动力进行动态调整,以确保车辆在 制动过程中的稳定性和安全性。
添加标题
该方法通过综合考虑车辆的行驶状态、车轮的附着条 件以及驾驶员的制动意图等因素,计算出最优的制动 力分配方案。
添加标题
纯电动汽车电液制动力分配计算方法的原理基于对车 辆动力学和制动系统特性的深入理解和研究,能够为 纯电动汽车的制动系统设计和优化提供重要的理论支 持和实践指导。
提升车辆稳定性:合理分配电液制动力,降低车辆在高速行驶或紧急制动 情况下的侧滑和失控风险,提高车辆行驶稳定性。
纯电动汽车制动器的工作原理与效能分析
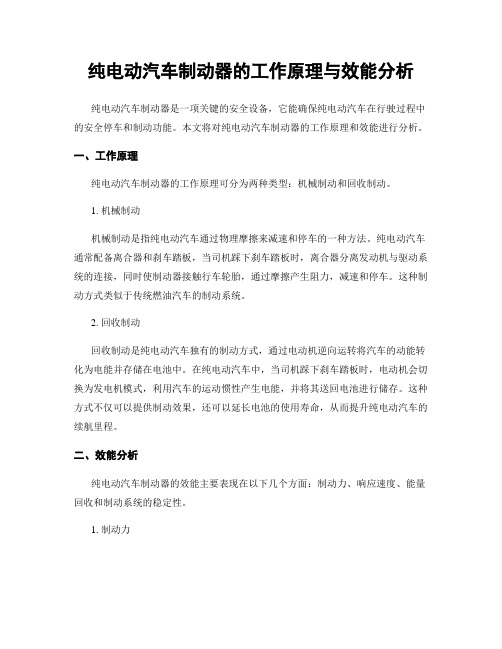
纯电动汽车制动器的工作原理与效能分析纯电动汽车制动器是一项关键的安全设备,它能确保纯电动汽车在行驶过程中的安全停车和制动功能。
本文将对纯电动汽车制动器的工作原理和效能进行分析。
一、工作原理纯电动汽车制动器的工作原理可分为两种类型:机械制动和回收制动。
1. 机械制动机械制动是指纯电动汽车通过物理摩擦来减速和停车的一种方法。
纯电动汽车通常配备离合器和刹车踏板,当司机踩下刹车踏板时,离合器分离发动机与驱动系统的连接,同时使制动器接触行车轮胎,通过摩擦产生阻力,减速和停车。
这种制动方式类似于传统燃油汽车的制动系统。
2. 回收制动回收制动是纯电动汽车独有的制动方式,通过电动机逆向运转将汽车的动能转化为电能并存储在电池中。
在纯电动汽车中,当司机踩下刹车踏板时,电动机会切换为发电机模式,利用汽车的运动惯性产生电能,并将其送回电池进行储存。
这种方式不仅可以提供制动效果,还可以延长电池的使用寿命,从而提升纯电动汽车的续航里程。
二、效能分析纯电动汽车制动器的效能主要表现在以下几个方面:制动力、响应速度、能量回收和制动系统的稳定性。
1. 制动力纯电动汽车制动器的制动力直接影响到车辆的刹车效果和安全性。
制动力越大,车辆刹停的距离越短,对于紧急情况的应对能力也更强。
因此,制动器的设计需要确保提供足够的制动力,以满足安全需求。
2. 响应速度纯电动汽车制动器的响应速度对于车辆的制动效果和操控性能至关重要。
合理设计的制动器需要能够快速响应司机踩下刹车踏板的动作,并在较短的时间内产生足够的制动力。
快速响应的制动器可以提升驾驶者的制动体验和驾驶安全。
3. 能量回收纯电动汽车制动器的回收制动功能可以将车辆的动能转化为电能,并存储在电池中。
能量回收的优势在于延长纯电动汽车的续航里程,同时降低对摩擦制动的依赖,减少制动器的磨损和能量损失。
因此,优秀的纯电动汽车制动器应该能够高效地回收能量,并将其储存起来供电池使用。
4. 制动系统的稳定性纯电动汽车制动器在长期使用中需要保持稳定的性能表现和可靠的工作状态。
纯电动汽车制动器工作原理及优势分析
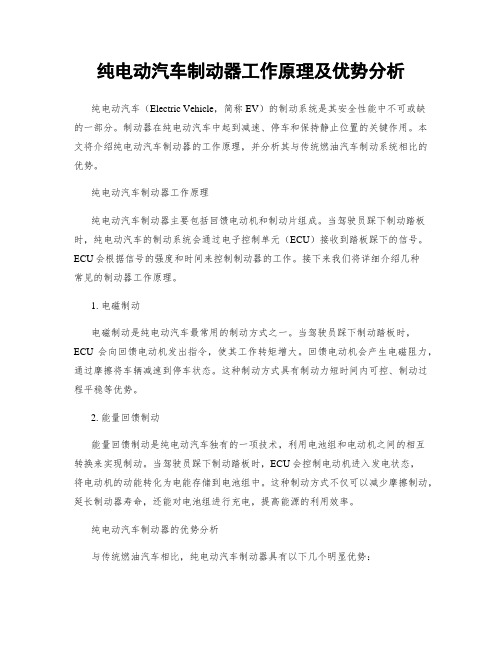
纯电动汽车制动器工作原理及优势分析纯电动汽车(Electric Vehicle,简称EV)的制动系统是其安全性能中不可或缺的一部分。
制动器在纯电动汽车中起到减速、停车和保持静止位置的关键作用。
本文将介绍纯电动汽车制动器的工作原理,并分析其与传统燃油汽车制动系统相比的优势。
纯电动汽车制动器工作原理纯电动汽车制动器主要包括回馈电动机和制动片组成。
当驾驶员踩下制动踏板时,纯电动汽车的制动系统会通过电子控制单元(ECU)接收到踏板踩下的信号。
ECU会根据信号的强度和时间来控制制动器的工作。
接下来我们将详细介绍几种常见的制动器工作原理。
1. 电磁制动电磁制动是纯电动汽车最常用的制动方式之一。
当驾驶员踩下制动踏板时,ECU会向回馈电动机发出指令,使其工作转矩增大。
回馈电动机会产生电磁阻力,通过摩擦将车辆减速到停车状态。
这种制动方式具有制动力短时间内可控、制动过程平稳等优势。
2. 能量回馈制动能量回馈制动是纯电动汽车独有的一项技术,利用电池组和电动机之间的相互转换来实现制动。
当驾驶员踩下制动踏板时,ECU会控制电动机进入发电状态,将电动机的动能转化为电能存储到电池组中。
这种制动方式不仅可以减少摩擦制动,延长制动器寿命,还能对电池组进行充电,提高能源的利用效率。
纯电动汽车制动器的优势分析与传统燃油汽车相比,纯电动汽车制动器具有以下几个明显优势:1. 能量回馈纯电动汽车制动器通过能量回馈技术,将电动机所产生的动能转化为电能并存储在电池组中。
这不仅能够延长电池组的寿命,还能有效地利用制动能量,提高能源的利用效率。
相比之下,传统燃油汽车的制动器是通过摩擦产生能量转化为热能,浪费了大量的能源。
2. 制动力短时间内可控纯电动汽车制动器采用电子控制技术,能够精确控制制动力的大小。
驾驶员在制动过程中可以通过踏板的力度来实现制动力的调节,提高驾驶的舒适性和安全性。
而传统燃油汽车的制动器则需要驾驶员通过改变踩踏踏板的力度来调节制动力的大小,操作相对比较复杂。
纯电动汽车制动系统的组成

纯电动汽车制动系统的组成
纯电动汽车的制动系统是保证车辆安全驾驶的重要组成部分,由
制动器、制动液压系统、制动传动机构和制动盘等部分组成。
制动器是纯电动汽车的重要零件之一,作用是将旋转中的车轮转
动能转化为热能消耗,从而使车辆减速停车。
制动器通常由刹车片、
刹车鼓等部件组成,其工作原理是通过将制动器中的刹车片搭在车轮上,使汽车停止运动。
制动液压系统是牵引车刹车的核心,主要包括制动泵、灵活软管、分配阀和刹车偏心等部分。
当司机踩下制动踏板时,制动泵将刹车液
传送至制动器内,使刹车片迅速紧贴车轮并起到制动作用。
制动传动机构包括制动踏板、刹车杠和连接杆等部分,其作用是
将司机的制动指令传递至制动装置,控制汽车的速度和停车。
同时,
为了保证汽车驾驶的安全性,制动系统还配备了制动盘。
制动盘是制动器上最重要的部分之一,能够将摩擦热转换成制动
能量。
制动盘通常由钢制材料或碳陶瓷材料制成,能够承受高温的摩
擦作用,具有更高的耐用性和制动性。
总之,纯电动汽车的制动系统是车辆安全性、运动性和舒适性的
重要保障,其中的每个部分都有其独特的作用,相互配合并运作,才
能为汽车提供更加安全、稳定和高效的制动性能。
因此,司机们在正
常驾驶过程中,一定要保持良好的维护和保养,以确保车辆的安全和稳定性。
电动汽车制动系统的设计
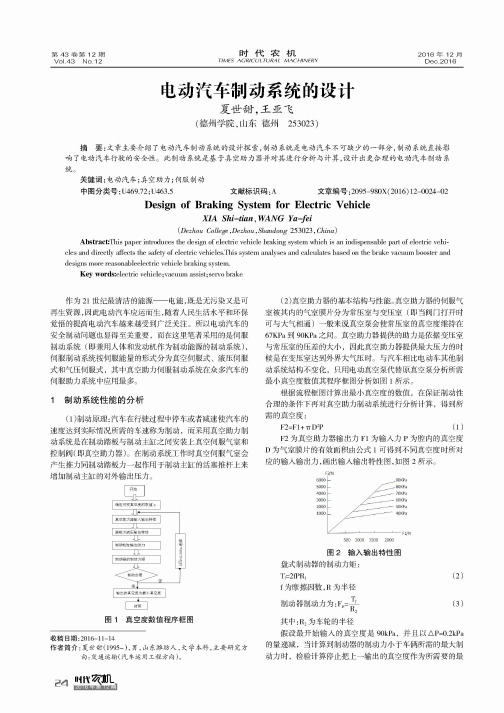
文献标识码:A
X 文章编号:2095-980 (2016)12-0024-02
Design of Braking System for Electric Vehicle
XIA Shi-tian, WANG Ya—fei
(Dezhou College ,Dezhou,Shandong 253023, China) Abstract:This paper introduces the design of electric vehicle braking system which is an indispensable part of electric vehi cles and directly affects the safety of electric vehicles.This system analyses and calculates based on the brake vacuum booster and designs more reasonableelectric vehicle braking system. Key words:electric vehicle;vacuum assist;servo brake
制动器制动力为:F滋= R12
⑴
其中:R2为车轮的半径 假设最开始 输 入 的 真 空 度 是 90kPa,并 且 以 A P=0.2kPa
的 量 递 减 ,当 计 算 到 制 动 器 的 制 动 力 小 于 车 俩 所 需 的 最 大 制
动 力 时 ,检验计算停止把上一输出的真空度作为所需要的最
夏 世 甜 ,王 亚 飞 :电动汽车制动系统的设计_________________
(2)真空助力器的基本结构与性能。真空助力器的伺服气
纯电动汽车制动器工作原理分析
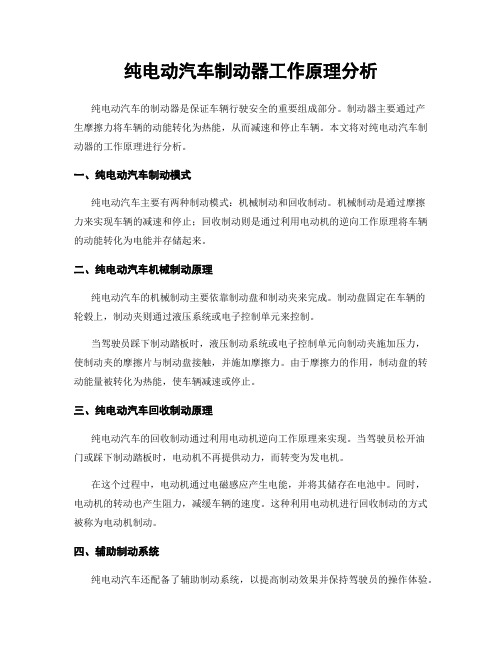
纯电动汽车制动器工作原理分析纯电动汽车的制动器是保证车辆行驶安全的重要组成部分。
制动器主要通过产生摩擦力将车辆的动能转化为热能,从而减速和停止车辆。
本文将对纯电动汽车制动器的工作原理进行分析。
一、纯电动汽车制动模式纯电动汽车主要有两种制动模式:机械制动和回收制动。
机械制动是通过摩擦力来实现车辆的减速和停止;回收制动则是通过利用电动机的逆向工作原理将车辆的动能转化为电能并存储起来。
二、纯电动汽车机械制动原理纯电动汽车的机械制动主要依靠制动盘和制动夹来完成。
制动盘固定在车辆的轮毂上,制动夹则通过液压系统或电子控制单元来控制。
当驾驶员踩下制动踏板时,液压制动系统或电子控制单元向制动夹施加压力,使制动夹的摩擦片与制动盘接触,并施加摩擦力。
由于摩擦力的作用,制动盘的转动能量被转化为热能,使车辆减速或停止。
三、纯电动汽车回收制动原理纯电动汽车的回收制动通过利用电动机逆向工作原理来实现。
当驾驶员松开油门或踩下制动踏板时,电动机不再提供动力,而转变为发电机。
在这个过程中,电动机通过电磁感应产生电能,并将其储存在电池中。
同时,电动机的转动也产生阻力,减缓车辆的速度。
这种利用电动机进行回收制动的方式被称为电动机制动。
四、辅助制动系统纯电动汽车还配备了辅助制动系统,以提高制动效果并保持驾驶员的操作体验。
1. 制动助力系统:纯电动汽车通常配备了制动辅助泵,通过增加液压制动系统的压力来增强制动效果。
这种助力系统可以提供额外的制动力,保证制动距离更短。
2. 制动能量回收系统:部分纯电动汽车采用制动能量回收系统,在制动过程中将制动能量转化为电能并存储起来,用于充电电池。
这种系统可以提高能量利用效率,延长行驶里程。
3. 制动控制系统:纯电动汽车还配备了制动控制系统,通过传感器和电子控制单元监测车辆行驶状态,并根据驾驶员的操作来控制制动盘和制动夹的工作。
这种系统可以提供精确的制动力和响应速度,提高行驶安全性。
五、制动器的优势和不足纯电动汽车制动器相较于传统内燃机汽车的制动器具有以下优势:1. 高效能量回收:纯电动汽车的回收制动可以将车辆的动能转化为电能并存储起来,提高能量利用效率。
纯电动汽车制动力分配优化设计
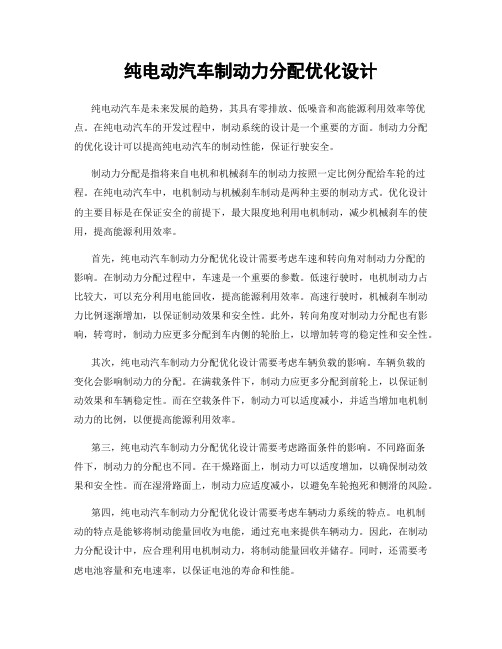
纯电动汽车制动力分配优化设计纯电动汽车是未来发展的趋势,其具有零排放、低噪音和高能源利用效率等优点。
在纯电动汽车的开发过程中,制动系统的设计是一个重要的方面。
制动力分配的优化设计可以提高纯电动汽车的制动性能,保证行驶安全。
制动力分配是指将来自电机和机械刹车的制动力按照一定比例分配给车轮的过程。
在纯电动汽车中,电机制动与机械刹车制动是两种主要的制动方式。
优化设计的主要目标是在保证安全的前提下,最大限度地利用电机制动,减少机械刹车的使用,提高能源利用效率。
首先,纯电动汽车制动力分配优化设计需要考虑车速和转向角对制动力分配的影响。
在制动力分配过程中,车速是一个重要的参数。
低速行驶时,电机制动力占比较大,可以充分利用电能回收,提高能源利用效率。
高速行驶时,机械刹车制动力比例逐渐增加,以保证制动效果和安全性。
此外,转向角度对制动力分配也有影响,转弯时,制动力应更多分配到车内侧的轮胎上,以增加转弯的稳定性和安全性。
其次,纯电动汽车制动力分配优化设计需要考虑车辆负载的影响。
车辆负载的变化会影响制动力的分配。
在满载条件下,制动力应更多分配到前轮上,以保证制动效果和车辆稳定性。
而在空载条件下,制动力可以适度减小,并适当增加电机制动力的比例,以便提高能源利用效率。
第三,纯电动汽车制动力分配优化设计需要考虑路面条件的影响。
不同路面条件下,制动力的分配也不同。
在干燥路面上,制动力可以适度增加,以确保制动效果和安全性。
而在湿滑路面上,制动力应适度减小,以避免车轮抱死和侧滑的风险。
第四,纯电动汽车制动力分配优化设计需要考虑车辆动力系统的特点。
电机制动的特点是能够将制动能量回收为电能,通过充电来提供车辆动力。
因此,在制动力分配设计中,应合理利用电机制动力,将制动能量回收并储存。
同时,还需要考虑电池容量和充电速率,以保证电池的寿命和性能。
最后,纯电动汽车制动力分配优化设计需要考虑驾驶员的需求和习惯。
不同驾驶员对制动力的需求和喜好有所差异。
纯电动汽车制动器的工作原理及性能分析

纯电动汽车制动器的工作原理及性能分析纯电动汽车制动器是负责将汽车减速或停车的关键系统之一。
在纯电动汽车中,制动器与传统内燃机汽车的制动系统有所不同。
本文将详细介绍纯电动汽车制动器的工作原理及性能分析。
一、纯电动汽车制动器的工作原理纯电动汽车制动器主要有电力回生制动和摩擦制动两种工作原理。
(一)电力回生制动电力回生制动是指将电动机由驱动状态转换为发电状态,将其用于制动的一种工作方式。
在纯电动汽车中,电动机同时作为驱动和制动装置。
当驾驶员松开油门或踩下制动踏板时,电动机自动进入发电状态,并通过电子控制系统将其感应发电的能量回馈到电池中。
这种回馈的能量转化为电能被储存起来,以供之后的驱动使用。
电力回生制动的工作原理简单且高效。
当车辆减速或停车时,电能的回收可以减少刹车片与刹车盘之间的摩擦,降低了能量的损耗,提高了能源利用效率。
同时,电力回生制动还可以延长刹车系统的使用寿命。
(二)摩擦制动摩擦制动是通过刹车盘和刹车片之间的摩擦来减速或停车的一种制动方式,与传统内燃机汽车的制动系统类似。
当驾驶员踩下制动踏板时,制动系统通过液压作用原理,使刹车盘与刹车片之间产生摩擦,从而实现汽车的制动。
摩擦制动的主要优点是制动力度可调,制动响应时间快。
然而,在高速度制动时,摩擦制动会消耗大量能量,导致能源的浪费,并且容易引起刹车系统的热量积聚,造成制动系统的磨损。
二、纯电动汽车制动器的性能分析纯电动汽车制动器的性能对于行驶的安全性和驾驶的舒适性都起着重要作用。
以下是对纯电动汽车制动器的性能进行分析。
(一)制动能力制动能力是纯电动汽车制动器的最基本指标之一。
它衡量了制动系统在一定时间内实现车辆减速或停车的能力。
制动能力直接影响着纯电动汽车的安全性能。
制动能力较强的车辆能更快、更稳定地停下来,因此制动能力的提升是纯电动汽车制动器性能改善的核心任务之一。
(二)制动平衡性制动平衡指的是车辆在进行制动时,各个车轮之间制动力的分配情况。
电动汽车刹车系统的制动控制算法研究

电动汽车刹车系统的制动控制算法研究第一章:绪论随着汽车工业的快速发展,电动汽车已成为新时代的代表性车型。
与传统汽车相比,电动汽车有着更加高效、环保的特点。
这得益于电动汽车采用了先进的电力系统,而其中刹车系统则是电动汽车的核心组成部分之一。
由于电动汽车的驱动模式与传统汽车不同,因此其刹车系统的制动控制算法也自然不同。
本文将对电动汽车刹车系统的制动控制算法进行探究,以期为电动汽车制造商提供合适的制动控制方法。
第二章:电动汽车刹车系统的发展2.1 传统汽车刹车系统的发展传统汽车刹车系统主要分为液压刹车系统和气制动系统。
液压刹车系统通常使用传统的踏板式制动系统。
在这种系统中,当驾驶员踩下制动踏板时,刹车鼓会受到压力,从而使制动器夹紧刹车片,制动效果显著。
气制动系统则是通过空气压力来实现制动,因此在载重时制动效果更佳。
2.2 电动汽车刹车系统的发展电动汽车刹车系统的发展经历了三个阶段:机械刹车、液压刹车和电子刹车。
在机械刹车中,驾驶员需要使用物理力量来控制刹车系统。
液压刹车则使用了液压压力来控制刹车,已经普遍应用于传统汽车中。
电子刹车则是通过电子信号控制刹车,已成为电动汽车刹车系统的标准。
第三章:电动汽车刹车系统的工作原理3.1 刹车信号传输与传统汽车不同,电动汽车通常使用电子信号来控制所有的操作,包括刹车。
在电动汽车中,当驾驶员踩下刹车踏板时,信号会发送到车辆控制单元,控制单元随即调整制动力度。
3.2 刹车控制算法电动汽车刹车控制算法是使刹车力精准控制的关键,主要有如下几种类型:3.2.1 脚踏力控制算法脚踏力控制算法是电动汽车刹车控制中应用最广泛的一种算法,主要根据驾驶员踏下刹车踏板时,车辆控制单元所获得的负载信息来控制刹车力度。
这种方法简单易于掌握,广泛应用于目前的电动汽车中。
3.2.2 制动负荷分配算法制动负荷分配算法是基于车轮制动负荷来进行算法控制。
这种算法将刹车力度分配到每个车轮上,从而实现对车辆的平衡制动。
比亚迪腾势纯电制动系统结构和工作原理

比亚迪腾势纯电制动系统结构和工作原理比亚迪腾势纯电动汽车的制动系统结构和工作原理如下:
1. 制动系统结构:
比亚迪腾势纯电动汽车的制动系统主要由制动器、制动泵、真空助力器、ABS控制模块等组成。
其中,制动器分为盘式制动器和鼓式制动器两种类型,分别位于前轮和后轮上。
制动泵是提供制动力的主要部件,通过将制动液加压,将压力传递给制动器。
真空助力器用于增加制动踏板的力量,使制动更加轻松。
ABS控制模块则用于控制制动系统的防抱死功能,确保制动过程中的稳定性。
2. 工作原理:
在制动过程中,当驾驶员踩下制动踏板时,制动泵中的活塞会受到压力,将制动液推入制动器中,从而使制动器产生制动力。
同时,真空助力器会放大制动踏板的力量,使制动更加轻松。
ABS控制模块会根据车轮的转速和车速等信息,控制制动系统的制动力,防止车轮抱死,保持车辆的稳定性。
总之,比亚迪腾势纯电动汽车的制动系统通过制动器和制动泵等部件产生制动力,并通过ABS控制模块等设备实现防抱死功能,确保车辆在制动过程中的稳定性和安全性。
- 1、下载文档前请自行甄别文档内容的完整性,平台不提供额外的编辑、内容补充、找答案等附加服务。
- 2、"仅部分预览"的文档,不可在线预览部分如存在完整性等问题,可反馈申请退款(可完整预览的文档不适用该条件!)。
- 3、如文档侵犯您的权益,请联系客服反馈,我们会尽快为您处理(人工客服工作时间:9:00-18:30)。
目录前言 (1)一、制动法规基本要求 (1)二、整车基本参数及样车制动系统主要参数 (2)2.1整车基本参数 (2)2.2样车制动系统主要参数 (2)三、前、后制动器制动力分配 (3)3.1地面对前、后车轮的法向反作用力 (3)3.2理想前后制动力分配曲线及 曲线 (4)3.2.1理想前后制动力分配 (4)3.2.2实际制动器制动力分配系数 (4)五、利用附着系数与制动强度法规验算 (9)六、制动距离的校核 (11)七、真空助力器主要技术参数 (12)八、真空助力器失效时整车制动性能 (12)九、制动踏板力的校核 (14)十、制动主缸行程校核 (16)十一、驻车制动校核 (17)1、极限倾角 (17)2、制动器的操纵力校核 (18)前言BM3车型的行车制动系统采用液压真空助力结构。
前制动器为通风盘式制动器,后制动器有盘式制动器和鼓式制动器两种,采用吊挂式制动踏板,带真空助力器,制动管路为双回路对角线(X型)布置,安装ABS系统。
驻车制动系统为后盘中鼓式制动器和后鼓式制动器两种,采用手动机械拉线式操纵机构。
一、制动法规基本要求1、GB21670《乘用车制动系统技术要求及试验方法》2、GB12676《汽车制动系统结构、性能和试验方法》3、GB13594《机动车和挂车防抱制动性能和试验方法》4、GB7258《机动车运行安全技术条件》400N二、整车基本参数及样车制动系统主要参数2.1整车基本参数2.2样车制动系统主要参数本车型要求安装ABS三、 前、后制动器制动力分配3.1地面对前、后车轮的法向反作用力在分析前、后轮制动器制动力分配比前,首先了解地面作用于前后车轮的法向反作用力(图1)。
由图1,对后轮接地点取力矩得:1z g duF L Gb mh dt=+……………………(1) 式中:1z F —地面对前轮的法向反作用力,N ; G —汽车重力,N ;b —汽车质心至后轴中心线的水平距离,m ; m —汽车质量,kg ; g h —汽车质心高度,m ; L —轴距,m ;dudt—汽车减速度2/m s 。
对前轮接地点取力矩,得:2z duF L Ga mdt=-……………………(2) 式中:2z F —地面对后轮的法向反作用力,N ; a —汽车质心至前轴中心线的距离,m 。
12()()z g z g G F b h LG F a h Lϕϕ⎧=+⎪⎪⎨⎪=-⎪⎩ (3)图1制动工况受力简图3.2理想前后制动力分配曲线及β曲线3.2.1理想前后制动力分配在附着系数为ϕ的路面上,前、后车轮同时抱死的条件是:前、后轮制动器制动力之和等于附着力;并且前后制动器制动力1F μ、2F μ分别等于各自的附着力,即:121122z z F F GF F F F μμμμϕϕϕ⎧+=⎪=⎨⎪=⎩……………………(4) 221141(2)2g g g h L G Gb F b F F h G h μμμ⎤=++⎥⎥⎦ (5)3.2.2实际制动器制动力分配系数实际前、后制动器制动力公式如下:211111122222222/42/4d F p n BF r R d F p n BF r R μμππ⎫⋅=⋅⋅⋅⋅⎪⎪⎬⋅⎪=⋅⋅⋅⋅⎪⎭……………………(6) 式中:1p 、2p :前后轮缸液压,Pa ; 1d 、2d :前后轮缸直径,m ;1n 、2n :前后制动器单侧油缸数目(仅对于盘式制动器而言); 1BF 、2BF :前、后制动器效能因数;1r 、2r :前、后制动器制动半径,m ; R :车轮滚动半径,m 。
又由公式:211112212111222F d BF r F F d BF r d BF r μμμβ⋅⋅==+⋅⋅+⋅……………………(7) 由于121F F μμββ=- (8)得到211F F μμββ-= (9)根据以上计算,可绘出空、满载状态时理想前后制动器制动力分配曲线(I 线)和实际前、后制动器制动力分配线(β线),如图2:图2:I 线和β线由公式:0gL bh βϕ-= (10)得实际同步附着系数0ϕ,此时前、后同时抱死。
由以上计算公式,可以算出制动器制动力分配系数,空、满载同步附着系数,计算结果见下表:表1制动器制动力分配系数,空满载同步附着系数名称符号 盘/盘中鼓式 盘、鼓式制动器制动力分配系数 β 0.684 0.686 满载同步附着系数 0ϕ 0.962 0.975 空载同步附着系数0ϕ0.500.52因实际满载同步附着系数0ϕ=0.962(0.975)与ϕ=1接近,会出现前后轮同时抱死的稳定情况;空载状态下同步附着系数0ϕ=0.50(0.52)<ϕ=1,这需要通过BM3车装配的ABS 系统的EBD 标定来避免缺陷。
设计方案可行。
在不同附着系数的路面上制动时,前、后轴都抱死,此时前后轴的制动力为:12()()xb g xb gG F b h LG F a h Lϕϕϕϕ⎧=+⎪⎪⎨⎪=-⎪⎩……………………(11) 满载状态下,在不同附着系数里面上的前、后轴的制动力如表2所示:表2 满载时前、后制动力将不同制动力代入到公式(6)可得到理想前后制动器的液压,再减去ABS 的波动误差0.1Mpa 可得到0.1~1的路面附着系数的实际轮缸液压具体如下表3所示:表3表4 满载前、后制动器制动力6 8731 4042 8731 39877 10189 4717 10189 46538 11647 5392 11647 53199 13104 6067 13104 598410 14562 6742 14562 6650表2与表3的数据对比,可以得出:前后制动器提供的制动力满足制动需求。
五、利用附着系数与制动强度法规验算利用附着系数见图3.法规要求:(1)、制动强度在0.1-0.61之间,前后轴曲线应在直线q=(z+0.07)/0.85以下。
(2)、车辆处于各种载荷状态时,前轴的附着系数利用曲线应位于后轴的附着系数利用曲线之上。
但制动强度在0.15~0.8之间的M1车辆,对于Z值在0.3~0.45时,若后轴利用附着曲线位于q=z+0.05以下,则允许后轴附着系数利用曲线位于前轴附着系数利用曲线之上。
图3:利用附着系数曲线六、制动距离的校核制动距离公式为:222max 1()3.6225.92V S V j ττ'''=++……………………(12) V —制动初速度,100km/h ; max j —最大制动减速度,2/m s ;2τ'+2τ''—制动器起作用时间,0.2~0.9s 取222ττ'''+=0.2s在ϕ=1的路面上,max j g ϕ==9.82/m s >6.432/m s (ϕ=0.8,max j =7.842/m s )制动距离(V =100km/h ),S =44.9<70m (S =57.5m )七、真空助力器主要技术参数真空助力器采用双模片式,膜片直径为8+9英寸 真空助力比:7八、真空助力器失效时整车制动性能助力器完全失效时,制动力完全由人力操纵踏板产生,最大踏板力要求:M1类车≤500N ,此时真空助力器输入力:vi p p p F i F η=⨯⨯ (13)p F —最大制动踏板力,500N ; p i —制动踏板杠杆比,3.34;p η—踏板机构传动效率,0.95,; 代入相关数据,可以得到:vi F =1586.5N根据真空助力器输入输出特性曲线可得到此时真空助力器的输出力:图:真空助力器输入输出特性曲线vo F =1283.29N系统压力通过下式计算:24vomF P d π=……………………(14) 代入相关数据得:P =2.88Mpa在真空助力器失效后,制动力将会明显减小,首先需要判断无真空助力时,制动系统提供的制动力时候大于地面对车轮的摩擦力,即车轮是否抱死。
满载时,前后制动器制动力分别为:表5盘/盘中鼓式盘/鼓式 1F μ41404203.285满载时,在附着系数为0.7的路面上,前、后轮同时抱死时,地面对车轮的制动力:1()=7879xb g GF b h N L ϕϕ=+ 2()=4778xb g GF a h N Lϕϕ=- 从结果可以看出,当真空助力器失效后,制动器制动力小于地面对车轮的摩擦力,因此在制动过程中,前、后轮均不抱死。
由公式: 12+F F j mμμ= (15)可以算出减速度。
表6由以上计算可知,当真空助力器失效后,在满载状态下,制动减速度和制动距离均满足各法规的应急制动性能要求。
九、制动踏板力的校核分析整个制动过程,在附着系数为ϕ(ϕ≤0ϕ)的路面上制动时,前轮的压力首先抱死,当管路中压力继续升高时,前轮制动力不再随管路中压力的升高而增大,但后轮制动力却随压力的升高继续增大,直到后轮也抱死,后轮抱死拖滑时,管路中的压力已经足够大,此时的踏板力即是整车在附着系数ϕ(ϕ≤0ϕ)的路面上制动所需的最大踏板力,显然,当ϕ=0ϕ时,前后轮同时抱死,此时所需要的踏板力即是整车制动的极限踏板力。
若不考虑ABS 作用,管路的抱死压力应该是在地面的附着系数达到同步附着系数时管路中的压力,满载状态时,ϕ=1,校核前轮刚要抱死时的踏板力。
此时, 1112518xb F F N μ== 代入公式(6),得P=8.60Mpa由液压公式(13)得满载状态下,表5所需踏板力:踏板力小于500N ,符合法规对制动踏板的要求,设计方案合理。
十、制动主缸行程校核制动主缸工作行程可通过下式计算:()22112222+2444f r m d d V V V d πδπδλπ⎡⎤⎛⎫+++⎢⎥ ⎪⎝⎭⎣⎦=软……………………(16) 软管膨胀量计算:H H L V K L P =⋅⋅软 (17)式中:1δ、2δ 前、后制动器制动行程,实验数据:0.2~0.4mm ,取0.3mm ; f V 、r V 、V 软 前、后轮缸及软管因膨胀而吸收的液量,3cm ; H K 常数,()634.3910/cm N cm -⨯⋅;前、后轮缸及软管因膨胀而吸收的液量通过做P V -试验得到。
当在附着系数为1ϕ=的路面上,管路抱死压力见表3,表3由上图曲线得到前、后轮缸的需液量分别为32.84f V cm =,30.89r V cm =。
软管膨胀量:V 软=30.61cm总需液量:3=2()=8.06f r V V V V cm ++总软主缸工作行程:22112222+2102904423.1113.1423.8144m d d V mm d πδπδλπ===⨯⨯总(+)<30mm23.1/3076.7%=缸有效行程大于主缸全行程的60%,建议将主缸行程增大至18+18。