轮胎外轮廓设计
联合收割机用15-24 10PR农业轮胎的设计
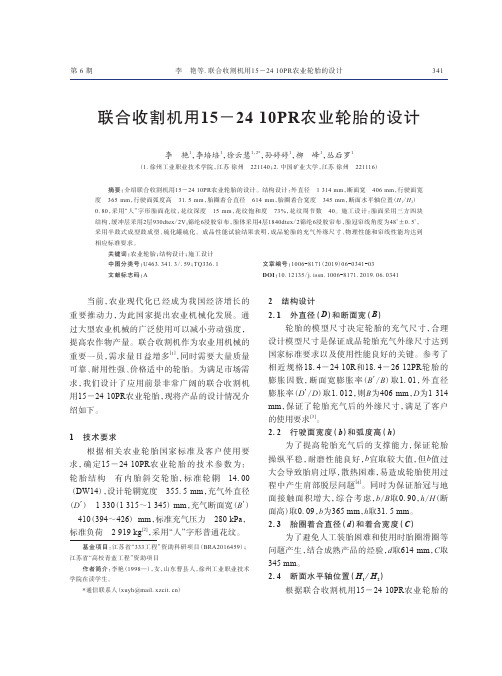
第 6 期李 艳等.联合收割机用15-24 10PR农业轮胎的设计341联合收割机用15-24 10PR农业轮胎的设计李 艳1,李培培1,徐云慧1,2*,孙婷婷1,柳 峰1,丛后罗1(1.徐州工业职业技术学院,江苏徐州 221140;2.中国矿业大学,江苏徐州 221116)摘要:介绍联合收割机用15-24 10PR农业轮胎的设计。
结构设计:外直径 1 314 mm,断面宽 406 mm,行驶面宽度 365 mm,行驶面弧度高 31.5 mm,胎圈着合直径 614 mm,胎圈着合宽度 345 mm,断面水平轴位置(H1/H2) 0.80,采用“人”字形胎面花纹,花纹深度 15 mm,花纹饱和度 73%,花纹周节数 40。
施工设计:胎面采用三方四块结构,缓冲层采用2层930dtex/2V3锦纶6浸胶帘布,胎体采用4层1840dtex/2锦纶6浸胶帘布,胎冠帘线角度为48°±0.5°,采用半鼓式成型鼓成型、硫化罐硫化。
成品性能试验结果表明,成品轮胎的充气外缘尺寸、物理性能和帘线性能均达到相应标准要求。
关键词:农业轮胎;结构设计;施工设计中图分类号:U463.341.3/.59;TQ336.1 文章编号:1006-8171(2019)06-0341-03文献标志码:A DOI:10.12135/j.issn.1006-8171.2019.06.0341当前,农业现代化已经成为我国经济增长的重要推动力,为此国家提出农业机械化发展。
通过大型农业机械的广泛使用可以减小劳动强度,提高农作物产量。
联合收割机作为农业用机械的重要一员,需求量日益增多[1],同时需要大量质量可靠、耐用性强、价格适中的轮胎。
为满足市场需求,我们设计了应用前景非常广阔的联合收割机用15-24 10PR农业轮胎,现将产品的设计情况介绍如下。
1 技术要求根据相关农业轮胎国家标准及客户使用要求,确定15-24 10PR农业轮胎的技术参数为:轮胎结构 有内胎斜交轮胎,标准轮辋 14.00(DW14),设计轮辋宽度 355.5 mm,充气外直径(D′) 1 330(1 315~1 345) mm,充气断面宽(B′) 410(394~426) mm,标准充气压力 280 kPa,标准负荷 2 919 kg[2],采用“人”字形普通花纹。
33×12-20(7.50)SAS实心轮胎的设计

33×12-20(7.50)SAS 实心轮胎的设计韦昌交(贵州轮胎股份有限公司,贵州 贵阳 550201)摘要:介绍33×12-20(7.50)SAS 实心轮胎的设计。
结构设计:外直径 852 mm ,断面宽 295 mm ,行驶面宽度 282 mm ,行驶面弧度高 15 mm ,胎圈着合直径 503 mm ,胎圈着合宽度 195 mm ,断面水平轴位置(H 1/H 2) 0.879 1,采用有向牵引型大块横向花纹,花纹深度 40 mm ,花纹周节数 20,花纹饱和度 51%。
施工设计:胎面采用先进的三段式结构,开炼机自动缠绕方式成型,平板硫化机硫化。
成品轮胎试验结果表明,轮胎的外缘尺寸、静负荷性能、物理性能和耐久性能均符合国家标准要求。
关键词:实心轮胎;结构设计;施工设计;静负荷性能;物理性能;耐久性能中图分类号:U463.341+.5 文章编号:1006-8171(2021)02-0079-04文献标志码:A DOI :10.12135/j.issn.1006-8171.2021.02.0079作者简介:韦昌交(1982—),男,贵州望谟人,贵州轮胎股份有限公司工程师,学士,主要从事轮胎结构设计和工艺管理工作。
E -mail :weichangjiao@实心轮胎是一种适用于低速、高负荷运行车辆的工业用轮胎。
优良的安全使用性能有利于提高工作效率,由于其使用寿命长、耐疲劳和免维护等特点而被广泛用于各种工业车辆、工程机械和拖挂车辆等,主要应用场所为港口、机场、铁路及大中型工矿企业和各种货物装卸作业场所。
实心轮胎形变小、运行稳定、抗刺穿且无需充气,避免了频繁补胎、换胎的繁重劳动,可提高车辆的使用率和工作效率,在低速、高负荷的运行车辆中,实心轮胎完全可以替代充气轮胎[1-5]。
为满足市场需求,我公司经市场调研后开发了33×12-20(7.50)SAS 实心轮胎,主要用于滑移式装载机和曲臂高空作业平台车轮,现介绍其设计过程如下。
车辆轮胎的轮廓优化设计

车辆轮胎的轮廓优化设计随着社会的发展和科技的进步,人们对交通工具的需求越来越大。
作为交通工具中不可或缺的部分,轮胎的性能和质量直接关系着交通工具的安全和效率。
为了提升轮胎的使用寿命和性能,越来越多的厂商开始进行轮胎的轮廓优化设计。
本文将从轮胎轮廓的设计目的、优化设计的方法及其影响进行详细的分析。
一、设计目的轮胎轮廓的设计目的在于提升轮胎的性能,主要包括以下方面:1.降低轮胎的燃油消耗由于轮胎在车辆行驶过程中的滚动阻力会消耗大量的燃油,因此降低轮胎的滚动阻力是轮廓设计的重要目标之一。
通过合理的轮廓设计,可以减小轮胎与地面间的接触面积,从而减小滚动阻力。
2.提升轮胎的抓地力和稳定性轮胎的抓地力和稳定性对车辆的驾驶安全有着至关重要的影响。
通过优化轮廓设计,可以增加轮胎与地面之间的摩擦力,提升轮胎的抓地力和稳定性,从而保证车辆行驶时的安全性。
3.减小轮胎的磨损轮胎的磨损会对轮胎的使用寿命产生不利的影响。
通过优化轮廓设计,可以减小轮胎与地面的接触面积和轮胎的变形量,从而减小轮胎的磨损,提高轮胎的使用寿命。
二、优化设计方法轮廓优化设计的方法主要包括根据仿生学原理设计、利用数值计算模拟、通过试验验证等方法。
1.根据仿生学原理设计仿生学是一种以生物为蓝本,应用现代工程学、计算机科学、材料科学等多学科知识模拟人造装置、系统和方法的学科,其重要性和应用前景在车辆轮胎的轮廓设计领域得到了广泛关注。
在车辆轮胎的轮廓优化设计中,仿生学的应用主要是通过模拟动物的足部结构和运动方式,设计出能够在特定道路状态下具有优良性能的轮胎轮廓。
例如,以猫科动物的爪子为蓝本,设计出了能够在露天泥泞路面行驶的轮胎轮廓。
2.利用数值计算模拟轮胎轮廓优化设计普遍采用数值计算模拟方法,通过数值计算模拟,可以预测轮胎在车辆行驶过程中的动态性能和静态性能及其受外界影响的响应。
数值计算模拟体现了优化设计的科学性和精确性,并且适用范围广泛。
3.通过试验验证设计出的轮胎轮廓需要经过试验验证来确定其实际性能。
12.00R20_矿山专用全钢子午线轮胎的设计

12.00R20矿山专用全钢子午线轮胎的设计王 刚 孙成林 王金帅新途轮胎有限公司摘 要:介绍12.00R20矿山专用全钢子午线轮胎的设计。
结构设计:外直径1132mm,断面宽312mm,行驶面宽度255mm,行驶面弧度高h=8mm,Copyright©博看网. All Rights Reserved.44应用技术APPLIED TECHNOLOGY 速度50km/h 、充气压力900kPa 、单胎负荷4000kg ,胎面花纹为大块矿山型花纹。
二、结构设计1.外直径(D )和断面宽(B )根据车型、矿区环境和实际使用情况,并结合普通矿山产品出现的“大肚子”“站立性不好”等问题,以自然平衡轮廓设计理论作为数学模型、经典力学原理作为架构,通过有限元方法进行模拟分析,对肩部过渡和圈部弧线进行合理优化,最终确定外直径D 为1132mm 、断面宽B 为312mm ,该结果满足全钢子午线轮胎模具尺寸和轮胎产品标准要求。
2.行驶面宽度(b )和弧度高(h )轮胎与地面直接接触的平面称为行驶面,b 和h 是影响运动状态下轮胎稳定性和耐磨性能的关键设计参数。
该类型轮胎使用工况较为恶劣,接地稳定性和耐磨性能也至关重要。
在设计中,需要增大轮胎接地面积,并提升其抓着性能,同时也要考虑矿区路况下的通过性,综合考虑最终确定b 为255mm ,h 为8mm 。
3.胎圈着合直径(d )和着合宽度(C )根据轮辋的直径尺寸来确定着和直径d ,根据轮辋宽度Rm 来确定着合宽度C 。
此规格使用的标准轮辋为8.50。
为确保轮胎与轮辋配合紧密,获得良好的气密性能,并提高胎圈部位的刚性支撑,同时能够很好地装卸轮胎,轮胎与轮辋采用过盈配合,即d为511mm ;C 采用加宽14.1mm 设计,即C 为230mm 。
4.断面水平轴位置(H 1/H 2)为保证轮胎的综合性能,全钢子午线轮胎设计中,断面水平轴位置需与轮胎断面最宽点匹配,该部位是轮胎断面中最薄、变形最大的位置,对轮胎性能有重大影响。
轮胎各部件结构设计

B4 B1 B3 B2
DC
DT
DJ
D F
以12.00R20 S811 18P.R为例 带束层宽度2#=204mm,1#=176mm, 3#=180mm,4#=110mm 2#/b=204/226=0.9027
1 6 .5
110 176 180 204
2 .5
22 34
42
7 .5
胎侧总厚度DC=胎侧胶厚度+胎体厚度+内衬层厚 度;胎侧胶厚度根据实际使用环境和路况来确定, 高速路况可以薄点,较差路面可以厚些;胎体厚 度根据所用材料和半成品压延厚度来确定;内衬 层厚度≥2.5mm,气密层厚度≥ 1.2mm;DF为侧板 和活络 块分型处厚度;
L
h
⑽肩下反弧R的确定 对于全钢载重子午胎,肩下一般不采用切线,而采 用一反弧,反弧R过肩部端点和R1相切,一般b较 大,R较小, b较小,R较大。 以12.00R20 S811 18P.R为例 结合其它方法途径搜集的数据,综合权衡确定R为 180mm.
b'
R
L
h
R1
H
Rn
D
d
⑾下胎侧圆弧半径R2的确定: R2=〔1/4×(B-C-2a)2 +(H1-Hc)2〕/(B-C-2a) 式中a为轮辋曲线宽的2/3.Hc为 轮辋曲线高. 一般情况下,R2 弧的延长线与 着合位置线的交点距离着合宽 度端点大约0~5mm. 以12.00R20 S811 18P.R为例 R2=〔1/4×(326-252-2×24.5)2 +(150.5-46)2〕/(326-2522×24.5) =443.06mm. 取R2=353mm.
轮胎各部件结构设计
2、外胎技术设计
1) 、外胎断面轮廓曲线的设计; 2) 、 胎面花纹形状的设计;
12R22.5节油型轮胎的设计
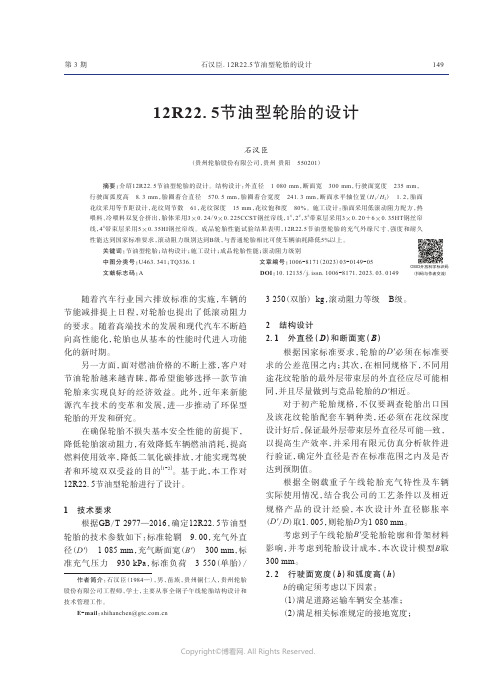
12R22.5节油型轮胎的设计石汉臣(贵州轮胎股份有限公司,贵州贵阳 550201)摘要:介绍12R22.5节油型轮胎的设计。
结构设计:外直径 1 080 mm,断面宽 300 mm,行驶面宽度 235 mm,行驶面弧度高 8.3 mm,胎圈着合直径 570.5 mm,胎圈着合宽度 241.3 mm,断面水平轴位置(H1/H2) 1.2,胎面花纹采用等节距设计,花纹周节数 61,花纹深度 15 mm,花纹饱和度 80%。
施工设计:胎面采用低滚动阻力配方,热喂料、冷喂料双复合挤出,胎体采用3×0.24/9×0.225CCST钢丝帘线,1#,2#,3#带束层采用3×0.20+6×0.35HT钢丝帘线,4#带束层采用5×0.35HI钢丝帘线。
成品轮胎性能试验结果表明,12R22.5节油型轮胎的充气外缘尺寸、强度和耐久性能达到国家标准要求,滚动阻力级别达到B级,与普通轮胎相比可使车辆油耗降低5%以上。
关键词:节油型轮胎;结构设计;施工设计;成品轮胎性能;滚动阻力级别中图分类号:U463.341;TQ336.1 文章编号:1006-8171(2023)03-0149-05文献标志码:A DOI:10.12135/j.issn.1006-8171.2023.03.0149随着汽车行业国六排放标准的实施,车辆的节能减排提上日程,对轮胎也提出了低滚动阻力的要求。
随着高端技术的发展和现代汽车不断趋向高性能化,轮胎也从基本的性能时代进入功能化的新时期。
另一方面,面对燃油价格的不断上涨,客户对节油轮胎越来越青睐,都希望能够选择一款节油轮胎来实现良好的经济效益。
此外,近年来新能源汽车技术的变革和发展,进一步推动了环保型轮胎的开发和研究。
在确保轮胎不损失基本安全性能的前提下,降低轮胎滚动阻力,有效降低车辆燃油消耗,提高燃料使用效率,降低二氧化碳排放,才能实现驾驶者和环境双双受益的目的[1-2]。
21570R17.5 H168公路型轮胎的设计

276 轮 胎 工 业2020年第40卷215/70R17.5 H168公路型轮胎的设计刘 玄,杨和涛(中策橡胶集团有限公司,浙江杭州310018)摘要:介绍215/70R17.5 H168公路型轮胎的设计。
结构设计:外直径 742 mm,断面宽 206 mm,行驶面宽度 168 mm,行驶面弧度高 7 mm,胎圈着合直径 442.5 mm,胎圈着合宽度 178 mm,断面水平轴位置(H1/H2) 1.03,采用纵向条形花纹,花纹深度 12 mm,花纹饱和度 70%,花纹周节数 75。
施工设计:采用三复合挤出胎面,胎体采用2层2200dtex/2 DSP聚酯帘布,带束层采用3+8×0.23ST钢丝帘线,采用胶囊反包、指形正包成型机成型,B型胶囊硫化机硫化。
成品性能测试结果表明,成品轮胎的充气外缘尺寸、强度性能、耐久性能和高速性能均达到相关标准要求。
关键词:公路型轮胎;半钢子午线轮胎;结构设计;施工设计;成品性能中图分类号:U463.341+.6;TQ336.1 文章编号:1006-8171(2020)05-0276-02文献标志码:A DOI:10.12135/j.issn.1006-8171.2020.05.0276近年来,随着公共交通的发展以及乘客对车辆舒适性要求的提高,用于中小型巴士的215/70R17.5轮胎使用量越来越大。
为了提升我公司在细分市场的份额,通过市场调研,设计开发了215/70R17.5 H168半钢子午线轮胎。
现将产品的设计情况简介如下。
1 技术要求根据GB/T 2977—2016,确定215/70R17.5 H168半钢子午线轮胎的技术参数如下:轮辋 6.0,充气外直径(D′) 747(737~757) mm,充气断面宽(B′) 211(200~222) mm,标准充气压力 600 kPa,单胎标准负荷 1 320 kg。
2 结构设计2.1 外直径(D)和断面宽(B)合理设计轮胎的模具尺寸不仅能保证轮胎的充气外缘尺寸,而且是轮胎获得最佳使用性能的主要环节[1],根据子午线轮胎的特点以及胎体骨架材料的特性,参照我公司现有产品的设计特点,断面宽膨胀率(B′/B)取1.024,B为206 mm;子午线轮胎因为有带束层以及冠带层的束缚,外直径变化很小,参照我公司现有产品的设计,外直径膨胀率(D′/D)取1.007,D为742 mm。
轮胎外轮廓设计
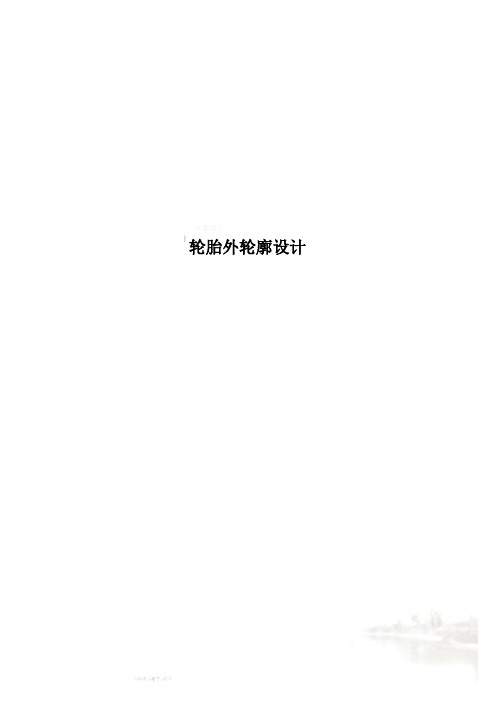
轮胎外轮廓设计外胎轮廓设计一、设计目的通过查阅资料独立完成橡胶制品课程设计,加强对专业知识的掌握;对10.00—20轮胎的轮廓设计有了一定的了解;通过研究斜交载重轮胎的结构设计程序,掌握技术设计内容:外胎外轮廓设计、胎面花纹设计、内轮廓设计;掌握斜交轮胎的施工设计。
对橡胶工艺、轮胎工艺及橡胶制品工艺等区域的知识有更深一步的了解。
同时在运用计算机软件作图中,增强了对AutoCAD软件的熟悉与应用。
提高了自主学习的能力和自我思考的能力。
二.主要技术参数表1 10.00—20轮胎的技术参数参数充气外直径/mm充气断面宽/mm标准轮辋花纹类型层级单胎最大负荷/Kg相应气压/KPa1.主要技术参数的确定①充气外直径D ′=1055mm②充气断面宽B ′=278mm 2.负荷能力计算确定外胎充气外缘尺寸D ′和B ′后,必须通过计算,验算其负荷能力是否符合国家标准,再进行外缘轮廓设计及计算,因此验算轮胎负荷能力是进行轮胎结构设计的基础。
负荷能力的计算公式为海尔公式,是一个在轮辋与充气轮胎断面宽之比等于62.5%的标准条件下(理想轮辋)得出的实验式, 若比值超出此范围,必须换算为在标准理想轮辋的充气轮胎断面宽才能使用此公式。
斜交轮胎负荷计算基本公式及负荷系数K 值的选取,载重轮胎和轿车轮胎选取不相同。
--=⨯⨯⨯⨯⨯⨯+320.5851.390.2310.4259.810(1.0210)()RW K P B D B111180arcsin141.3W B B B -=⨯o o式中:W -负荷能力,kNK -负荷系数【K =1.1(双胎),K =1.14(单胎)】P -内压,kPaD R-设计轮辋直径,cmW 1-轮辋名义宽度,cmB - 为62.5%的理想轮辋上的轮胎充气断面宽,cm B 1-安装在设计轮辋上的新胎充气断面宽,cm0.231-采用公制计算的换算系数,若用英制计算,此公式不必乘0.231。
已知条件:D=l055mm ,B 1=278mm, W 1=190mm ,P=810kPa ,D R= 508mm ,K D(双胎)= 1.l ,K S(单胎)= 1.l4将已知数值代入公式中,首先求取B 值,再求W D双胎负荷,最后计算单胎负荷W S。
如何在Blender中制作高质量的轮胎模型

如何在Blender中制作高质量的轮胎模型在Blender中制作高质量的轮胎模型是一项非常有挑战性的任务,但只要你掌握了一些技巧和技能,就能够轻松地创造出逼真而精美的轮胎模型。
在本教程中,我将向你介绍一种可行的方法。
第一步是创建轮胎的基本几何形状。
在Blender中,你可以使用圆柱体来作为轮胎的起始模型。
选择添加一个圆柱体,并设置合适的半径和高度。
确保圆柱体的分段数足够高,以便后续的细节调整。
接下来,我们需要调整轮胎的轮廓形状。
选择轮胎模型并进入编辑模式,然后使用顶点操作来调整轮廓曲线。
在顶部视图中,可以使用顶点的平移,缩放和旋转来改变形状。
根据实际轮胎的设计,你可以调整不同部位的曲线,以获得所需的外形。
一旦你满意轮胎的轮廓,下一步是创建轮胎的纹理和花纹。
在Blender中,你可以使用纹理贴图来模拟轮胎的花纹。
你可以使用一个无缝的轮胎贴图,或者根据自己的需要制作一个。
在材质选项卡中,为轮胎材质选择正确的纹理类型,例如漫反射或置换纹理。
然后,将所选纹理加载到纹理槽中,并设置合适的参数,如贴图坐标和重复。
确保调整纹理的缩放和位置,使其符合轮胎的大小和形状。
通过使用纹理坐标节点以及节点编辑器中的其他技巧,你可以进一步增强轮胎的质感和细节。
例如,你可以使用“细胞噪声”节点来模拟轮胎表面的皱纹效果,或者使用“噪波”节点来添加磨损和磨砂效果。
完成纹理和花纹后,下一步是添加轮胎的轮辋和其他细节。
你可以使用Blender的建模工具来创建轮辋。
选择一个合适的构造方式,例如创建多边形网格或者使用线框建模工具。
根据实际需求,你可以添加螺栓,刹车盘,气嘴等等细节来增加真实感和细节层次。
利用Blender的复制和镜像功能,可以快速创建和对称处理这些细节。
最后一步是调整轮胎的材质和渲染设置。
利用Blender的材质节点编辑器,你可以进一步调整轮胎的颜色,反射率,折射率等属性,以达到所需效果。
在渲染选项中,你可以选择合适的渲染引擎和光源设置,以获得逼真的渲染结果。
第三章 轮胎结构设计方法
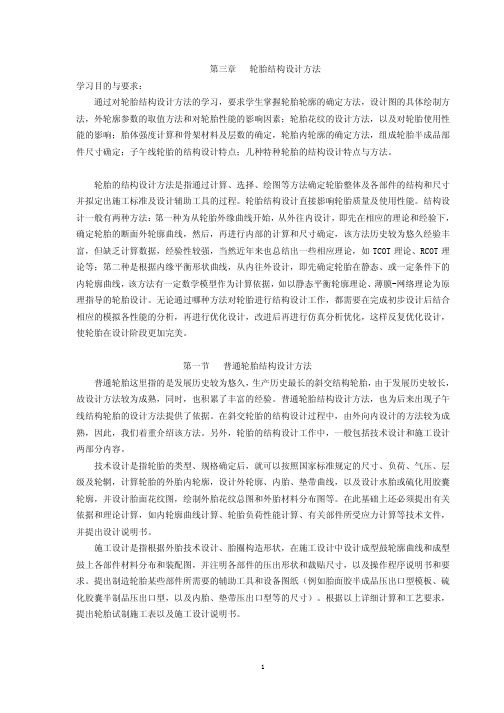
Bm = 25.9 ×
180o − sin −1 ( 141.3o
17.78 ) 25.9
= 25.9 × 0.96 = 25.047(cm)
WD = 0.231 × 1.1 × 0.425 × 9.8 × 10 −3 × (1.02 × 10 −2 × 588) 0.585 × 25.0471.39 (50.8 + 25.047)
胎断面图的基本框架尺寸,他们包括断面宽(B) 、外 直径 (D) 、 断面高 (H) 、 下胎侧高 (H1) 、 上胎侧高 (H2) 、 着合直径(d) 、着合宽度(C) 、行驶面宽(b) 、行驶 面高(h)等组成。 1)轮胎断面宽 B 确定 轮胎断面宽是指胎体断
面的最宽位置,位于水平轴上,对于常规轮胎来说是 胎侧变形最大的位置。其值的确定直接影响技术指标 要求的充气断面宽 B′,是决定轮胎外形合格与否的 重要参数。 断面宽 B 值的确定按照式(3-1-1)即:
3
轿车轮胎负荷计算基本公式(3-1-3)(3-1-4)为:
1.39 W = 0.231K × 0.425 × 9.8 × 10 −3 × (1.02 × 10 −2 P ) 0.585 × Bd ( D R + Bd )
(3-1-3)
Bd = B0.70 − 0.637d
180o − sin −1 135.6o W1 B′
=20(KN)
WS = 20 × 1.14 = 22.8( KN ) ,(增加气压70kPa)
4
三、外胎外轮廓尺寸的确定方法 所谓轮胎的外轮廓设计,实质是对能够生产出相应技术指标要求的充气外轮廓尺寸的成品轮 胎的模具内轮廓形状尺寸的确定过程,这里定义的轮胎尺寸,实际上是指硫化模具的内缘轮廓尺 寸。在结构设计过程中,一类主要的设计方法如前所述,先对轮胎外轮廓尺寸进行确定,轮胎外 轮廓的主要尺寸组成及代号见图 3-1-2。 1.外胎轮廓尺寸的确定 轮胎的轮廓尺寸是外
轮胎外轮廓设计

轮胎外轮廓设计外胎轮廓设计设计目的通过查阅资料独立完成橡胶制品课程设计,加强对专业知识的掌握;对10.00—20轮胎的轮廓设计有了一定的了解;通过研究斜交载重轮胎的结构设计程序,掌握技术设计内容:外胎外轮廓设计、胎面花纹设计、内轮廓设计;掌握斜交轮胎的施工设计。
对橡胶工艺、轮胎工艺及橡胶制品工艺等区域的知识有更深一步的了解。
同时在运用计算机软件作图中,增强了对AutoCAD 软件的熟悉与应用。
提高了自主学习的能力和自我思考的能力。
二•主要技术参数表1 10.00 —20轮胎的技术参数图1轮辎断面图三.9.00-20斜交载重轮胎主要尺寸选取1 •主要技术参数的确定①充气外直径 D ' =1055mm②充气断面宽B' =278mm2. 负荷能力计算确定外胎充气外缘尺寸D'和B'后,必须通过计算,验算其负荷能力是否符合国家标准,再进行外缘轮廓设计及计算,因此验算轮胎负荷能力是进行轮胎结构设计的基础。
负荷能力的计算公式为海尔公式,是一个在轮辋与充气轮胎断面宽之比等于62.5%的标准条件下(理想轮辋)得出的实验式,若比值超出此范围,必须换算为在标准理想轮辋的充气轮胎断面宽才能使用此公式。
斜交轮胎负荷计算基本公式及负荷系数K 值的选取,载重轮胎和轿车轮胎选取不相同。
W 0.231 K 0.425 9.8 10 3(1.02 102P)0.585B1.39(D R B)o . w180 arcsin -____ B LB B,141.30式中:W —负荷能力,kNK —负荷系数【K = 1.1 (双胎),K = 1.14 (单胎)】P—内压,kPaD R—设计轮辋直径,cm W W-轮辋名义宽度,cmB1B —为62.5%的理想轮辋上的轮胎充气断面宽,cmB1 —安装在设计轮辋上的新胎充气断面宽,cm0.231-采用公制计算的换算系数,若用英制计算,此公式不必乘0.231。
已知条件:D=l055mm,B i=278mm, W i=190mm,P=810kPa,D R= 508mm,心(双胎)=1.l,K S(单胎)=1.14将已知数值代入公式中,首先求取B值,再求W D双胎负荷,最后计算单胎负荷W S。
汽车轮胎轮廓对操控的影响
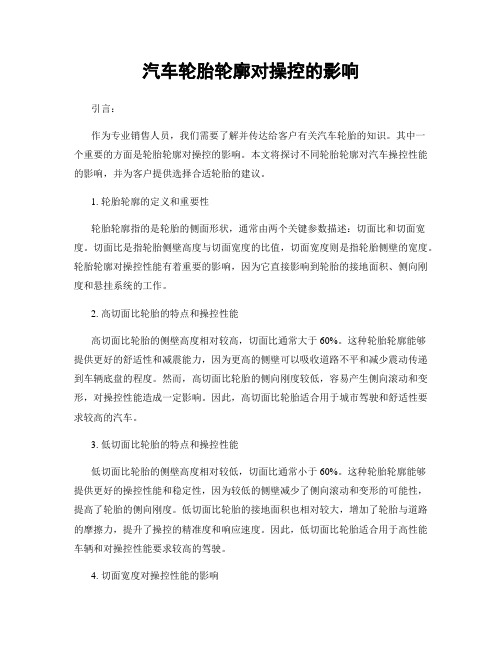
汽车轮胎轮廓对操控的影响引言:作为专业销售人员,我们需要了解并传达给客户有关汽车轮胎的知识。
其中一个重要的方面是轮胎轮廓对操控的影响。
本文将探讨不同轮胎轮廓对汽车操控性能的影响,并为客户提供选择合适轮胎的建议。
1. 轮胎轮廓的定义和重要性轮胎轮廓指的是轮胎的侧面形状,通常由两个关键参数描述:切面比和切面宽度。
切面比是指轮胎侧壁高度与切面宽度的比值,切面宽度则是指轮胎侧壁的宽度。
轮胎轮廓对操控性能有着重要的影响,因为它直接影响到轮胎的接地面积、侧向刚度和悬挂系统的工作。
2. 高切面比轮胎的特点和操控性能高切面比轮胎的侧壁高度相对较高,切面比通常大于60%。
这种轮胎轮廓能够提供更好的舒适性和减震能力,因为更高的侧壁可以吸收道路不平和减少震动传递到车辆底盘的程度。
然而,高切面比轮胎的侧向刚度较低,容易产生侧向滚动和变形,对操控性能造成一定影响。
因此,高切面比轮胎适合用于城市驾驶和舒适性要求较高的汽车。
3. 低切面比轮胎的特点和操控性能低切面比轮胎的侧壁高度相对较低,切面比通常小于60%。
这种轮胎轮廓能够提供更好的操控性能和稳定性,因为较低的侧壁减少了侧向滚动和变形的可能性,提高了轮胎的侧向刚度。
低切面比轮胎的接地面积也相对较大,增加了轮胎与道路的摩擦力,提升了操控的精准度和响应速度。
因此,低切面比轮胎适合用于高性能车辆和对操控性能要求较高的驾驶。
4. 切面宽度对操控性能的影响切面宽度是指轮胎侧壁的宽度,对操控性能也有一定的影响。
较宽的切面宽度可以增加轮胎与道路的接触面积,提供更好的抓地力和操控性能。
然而,过于宽的切面宽度可能会增加轮胎的滚动阻力,导致燃油消耗增加。
因此,在选择轮胎时,需要根据车辆类型和使用需求综合考虑切面宽度。
结论:轮胎轮廓对操控性能有着重要的影响,不同的轮胎轮廓适用于不同的驾驶需求。
高切面比轮胎适合城市驾驶和舒适性要求较高的汽车,而低切面比轮胎适合高性能车辆和对操控性能要求较高的驾驶。
28×9-15 14PR叉车轮胎的设计

第 5 期贺李萍等.28×9-15 14PR叉车轮胎的设计279 28×9-15 14PR叉车轮胎的设计贺李萍,司飞飞,周 康(风神轮胎股份有限公司,河南焦作454003)摘要:介绍28×9-15 14PR叉车轮胎的设计。
结构设计:外直径 690 mm,断面宽 228 mm,行驶面宽度 210 mm,行驶面弧度高 0,胎圈着合直径 387 mm,胎圈着合宽度 178 mm,断面水平轴位置(H1/H2) 0.942 3,花纹深度 18 mm,花纹周节数 24,花纹饱和度 77%。
施工设计:胎面采用两方三块结构,胎体采用4层1400dtex/3V1和2层1400dtex/3V2锦纶6浸胶帘布,缓冲层采用2层930dtex/2V3锦纶6浸胶帘布,轮胎采用半芯轮式成型机成型、胶囊硫化机硫化。
成品性能检测结果表明,轮胎的充气外缘尺寸和物理性能符合相关设计和国家标准要求。
关键词:叉车轮胎;结构设计;施工设计中图分类号:U463.341 文章编号:1006-8171(2019)05-0279-03文献标志码:A DOI:10.12135/j.issn.1006-8171.2019.05.0279随着我国工业现代化进程的不断推进,电动叉车被广泛使用于工业生产中,叉车轮胎作为承受载荷、传递动力的重要部件,其结构与性能尤为重要。
为满足市场需要,扩充轮胎品牌的规格及花纹型号,我公司特开发了28×9-15 14PR AIND11叉车轮胎,现将轮胎设计情况简介如下。
1 技术要求根据GB/T 2982—2014《工业车辆充气轮胎规格、尺寸、气压与负荷》,确定28×9-15 14PR叉车轮胎主要技术参数为:标准轮辋 7.0,充气外直径(D′) 710(700~733) mm,充气断面宽(B′) 220(213~236) mm,标准充气压力 970 kPa,速度 25 km·h-1,最大负荷 3 050 kg,气门嘴型号 DG07C。
14.00R24NHS港口专用全钢工程机械子午线轮胎的设计

22314.00R24NHS 港口专用全钢工程机械子午线轮胎的设计王若飞,崔志武,王晓娟,陈 宇,宋朝兴(风神轮胎股份有限公司,河南 焦作 454003)摘要:介绍14.00R24NHS 港口专用全钢工程机械子午线轮胎的设计。
结构设计:外直径 1 410 mm ,断面宽 368 mm ,行驶面宽度 320 mm ,行驶面弧度高 20 mm ,胎圈着合宽度 274 mm ,胎圈着合直径 610 mm ,断面水平轴位置(H 1/H 2) 0.739 1,胎面采用块状花纹,花纹深度 64 mm ,花纹饱和度 72.2%,花纹周节数 28。
施工设计:胎面采用3层结构,胎体采用3+9+15×0.225ST 钢丝帘线,带束层采用4层结构,其中1#带束层采用3+9+15×0.175+0.15HT 钢丝帘线,2#和3#带束层采用3+9+15×0.220+0.15HT 钢丝帘线,4#带束层采用3×7×0.20HE 钢丝帘线,采用一次法两鼓/三鼓成型机成型,采用蒸锅式硫化机硫化。
成品性能试验结果表明,成品轮胎的充气外缘尺寸、物理性能和静负荷性能均达到国家标准及相应设计要求。
关键词:港口专用全钢工程机械子午线轮胎;结构设计;施工设计中图分类号:TQ336.1 文章编号:2095-5448(2024)04-0223-04文献标志码:A DOI :10.12137/j.issn.2095-5448.2024.04.0223随着我国经济的蓬勃发展,内外贸港口运输需求增大,港口集装箱吞吐量相应递增,港口的生产作业模式也在发生改变,港口机械逐步向多样化、大型化、无人化等领域发展[1]。
港口集装箱堆高机以通用叉车技术为基础,集成了部分起重功能,主要用于集装箱的搬运和堆垛作业,具有可频繁转向与制动、机动灵活、操作简单等特点。
本工作主要介绍专为港口集装箱堆高机开发的14.00R24NHS 港口专用全钢工程机械子午线轮胎(简称14.00R24NHS 专用轮胎)的设计。
14.00R25工程机械子午线轮胎的设计

14.00R25工程机械子午线轮胎的设计程 超,张 鹏,龙云山,朱仕翻,张 甲(贵州轮胎股份有限公司,贵州贵阳 550008)摘要:介绍14.00R25工程机械子午线轮胎的设计。
结构设计:外直径 1 370 mm,断面宽 375 mm,行驶面宽度 315 mm,行驶面弧度高 14 mm,胎圈着合直径 632 mm,胎圈着合宽度 266.7 mm,断面水平轴位置(H1/H2) 0.87,胎面采用块状花纹,花纹深度 26 mm,花纹饱和度 68.8%,花纹周节数 34。
施工设计:胎面冠部胶采用抗刺扎、抗切割和高耐磨胶料,基部胶采用低生热胶料,采用4层带束层结构,1#—3#带束层采用3+9+15×0.22+0.15HT钢丝帘线,4#带束层采用3×7×0.22HE钢丝帘线,胎体采用3+9+15×0.22+0.15钢丝帘线,采用一次法成型机成型、单模蒸锅式硫化机硫化。
成品轮胎性能试验结果表明,轮胎的充气外缘尺寸和耐久性能均达到国家标准和企业标准要求。
关键词:工程机械子午线轮胎;结构设计;施工设计;成品轮胎性能中图分类号:U463.341+.5/.6;TQ336.1 文章编号:1006-8171(2020)12-0722-04文献标志码:A DOI:10.12135/j.issn.1006-8171.2020.12.0722近年来因为矿业的发展,整个矿山市场复苏,80 t级重型自卸车因为作业运行相对较为便捷,对路况要求较刚性自卸车低,并且前期投入较小,所以得到市场的高度认可,受终端市场的青睐,整个行业重型自卸车市场保有量逐年激增,相应工程机械轮胎需求出现爆发式增长[1]。
但是,传统斜交轮胎质量缺陷多、使用寿命短,因此不能满足矿业工程机械轮胎需求。
为了维护行业竞争力并提高企业经济效益,本工作对14.00R25工程机械子午线轮胎进行设计开发,以期消除斜交轮胎产品不抗刺扎和切割以及生热鼓包等问题,提高产品品质,为客户创造更高的价值。
轮胎外轮廓设计(参考资料)
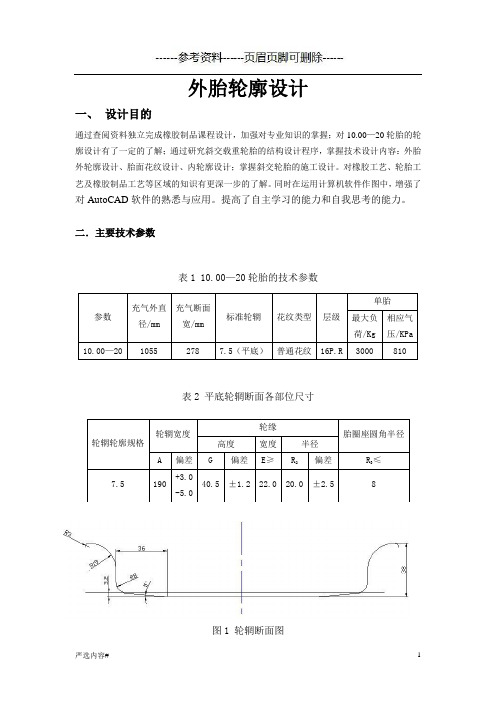
外胎轮廓设计一、 设计目的通过查阅资料独立完成橡胶制品课程设计,加强对专业知识的掌握;对10.00—20轮胎的轮廓设计有了一定的了解;通过研究斜交载重轮胎的结构设计程序,掌握技术设计内容:外胎外轮廓设计、胎面花纹设计、内轮廓设计;掌握斜交轮胎的施工设计。
对橡胶工艺、轮胎工艺及橡胶制品工艺等区域的知识有更深一步的了解。
同时在运用计算机软件作图中,增强了对AutoCAD 软件的熟悉与应用。
提高了自主学习的能力和自我思考的能力。
二.主要技术参数表1 10.00—20轮胎的技术参数参数充气外直 径/mm 充气断面 宽/mm 标准轮辋花纹类型层级 单胎最大负 荷/Kg 相应气压/KPa10.00—20 10552787.5(平底) 普通花纹 16P.R 3000 810表2 平底轮辋断面各部位尺寸图1 轮辋断面图轮辋轮廓规格轮辋宽度 轮缘胎圈座圆角半径高度宽度 半径 A偏差 G偏差E ≥R 2偏差R 3≤ 7.5190+3.0 -5.040.5 ±1.2 22.0 20.0 ±2.58三.9.00—20斜交载重轮胎主要尺寸选取 1.主要技术参数的确定①充气外直径D ′=1055mm ②充气断面宽B ′=278mm2.负荷能力计算确定外胎充气外缘尺寸D ′和B ′后,必须通过计算,验算其负荷能力是否符合国家标准,再进行外缘轮廓设计及计算,因此验算轮胎负荷能力是进行轮胎结构设计的基础。
负荷能力的计算公式为海尔公式,是一个在轮辋与充气轮胎断面宽之比等于62.5%的标准条件下(理想轮辋)得出的实验式, 若比值超出此范围,必须换算为在标准理想轮辋的充气轮胎断面宽才能使用此公式。
斜交轮胎负荷计算基本公式及负荷系数K 值的选取,载重轮胎和轿车轮胎选取不相同。
--=⨯⨯⨯⨯⨯⨯+320.585 1.390.2310.4259.810(1.0210)()R W K P B D B111180arcsin141.3W B B B -=⨯o o式中:W -负荷能力,kNK -负荷系数【K =1.1(双胎),K =1.14(单胎)】 P -内压,kPaD R -设计轮辋直径,cmW 1-轮辋名义宽度,cmB - 为62.5%的理想轮辋上的轮胎充气断面宽,cmB 1-安装在设计轮辋上的新胎充气断面宽,cm0.231-采用公制计算的换算系数,若用英制计算,此公式不必乘0.231。
11060-12摩托车轮胎的不同轮廓设计及性能对比
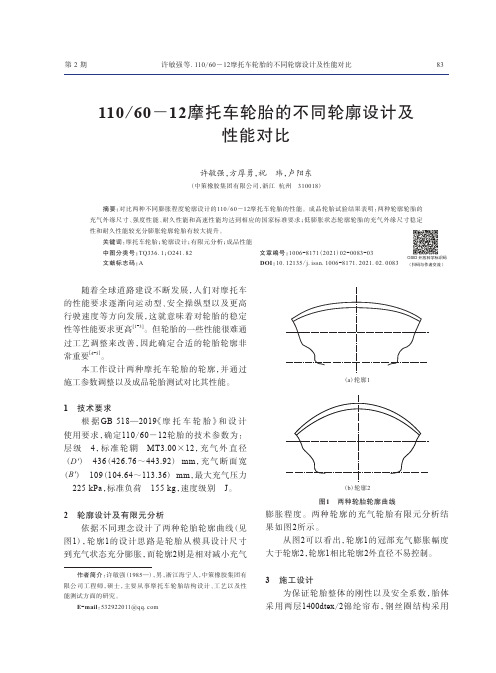
第 2 期许敏强等.110/60-12摩托车轮胎的不同轮廓设计及性能对比83 110/60-12摩托车轮胎的不同轮廓设计及性能对比许敏强,方厚勇,祝 玮,卢阳东(中策橡胶集团有限公司,浙江杭州310018)摘要:对比两种不同膨胀程度轮廓设计的110/60-12摩托车轮胎的性能。
成品轮胎试验结果表明:两种轮廓轮胎的充气外缘尺寸、强度性能、耐久性能和高速性能均达到相应的国家标准要求;低膨胀状态轮廓轮胎的充气外缘尺寸稳定性和耐久性能较充分膨胀轮廓轮胎有较大提升。
关键词:摩托车轮胎;轮廓设计;有限元分析;成品性能中图分类号:TQ336.1;O241.82 文章编号:1006-8171(2021)02-0083-03文献标志码:A DOI:10.12135/j.issn.1006-8171.2021.02.0083随着全球道路建设不断发展,人们对摩托车的性能要求逐渐向运动型、安全操纵型以及更高行驶速度等方向发展,这就意味着对轮胎的稳定性等性能要求更高[1-3]。
但轮胎的一些性能很难通过工艺调整来改善,因此确定合适的轮胎轮廓非常重要[4-5]。
本工作设计两种摩托车轮胎的轮廓,并通过施工参数调整以及成品轮胎测试对比其性能。
1 技术要求根据GB 518—2019《摩托车轮胎》和设计使用要求,确定110/60-12轮胎的技术参数为:层级 4,标准轮辋 MT3.00×12,充气外直径(D') 436(426.76~443.92)mm,充气断面宽(B') 109(104.64~113.36) mm,最大充气压力 225 kPa,标准负荷 155 kg,速度级别 J。
2 轮廓设计及有限元分析依据不同理念设计了两种轮胎轮廓曲线(见图1),轮廓1的设计思路是轮胎从模具设计尺寸到充气状态充分膨胀,而轮廓2则是相对减小充气(a)轮廓1(b)轮廓2图1 两种轮胎轮廓曲线膨胀程度。
两种轮廓的充气轮胎有限元分析结果如图2所示。
轻量化12r22.5全钢载重子午线轮胎的设计

660 轮 胎 工 业2019年第39卷轻量化12R22.5全钢载重子午线轮胎的设计隋 斌,王秀梅,李园园,许传亮(青岛双星轮胎工业有限公司,山东青岛266400)摘要:介绍轻量化12R22.5全钢载重子午线轮胎的设计。
结构设计:外直径 1 071 mm,断面宽 288 mm,行驶面宽度 210 mm,行驶面弧度高 6 mm,胎圈着合直径 569.5 mm,胎圈着合宽度 228 mm,断面水平轴位置(H1/H2) 0.882,胎面花纹为4条直线花纹沟,花纹深度 14 mm,花纹饱和度 80%,花纹周节数 55。
施工设计:采用双复合挤出胎面;3+0°带束层结构,1#和2#带束层采用4+3×0.35ST钢丝帘线,3#带束层采用5×0.30HI钢丝帘线,0°带束层采用3×7×0.20HE钢丝帘线;胎体采用3×0.24/9×0.225CCST钢丝帘线;采用一次法胶囊成型机成型、热板式硫化机硫化。
成品性能试验结果表明,轮胎的充气外缘尺寸、强度性能、耐久性能和高速性能满足国家标准及相应设计要求。
关键词:全钢载重子午线轮胎;轻量化;结构设计;施工设计中图分类号:U463.341+.3/.6;TQ336.1 文章编号:1006-8171(2019)11-0660-03文献标志码:A DOI:10.12135/j.issn.1006-8171.2019.11.0660随着国内道路状况的提升和国家最新法规政策的实施,整车轻量化成为国内各大主机厂的发展目标。
轮胎作为车辆主要配件,轻量化发展也成为一种趋势。
本工作设计了轻量化12R22.5全钢载重子午线轮胎,以满足市场需求。
1 技术要求根据GB/T 2977—2016的要求,确定轻量化12R22.5全钢载重子午线轮胎的技术参数为:充气外直径(D′) (1 085±15.405) mm,充气断面宽(B′) (300±12) mm,标准轮辋 9.00,层级 18,标准充气压力 930 kPa,标准负荷 3 550 kg。
abaqus 轮胎建模教程

Abaqus 轮胎建模教程简介Abaqus是一种强大的有限元分析软件,常用于模拟复杂的结构力学问题。
在这个教程中,我们将介绍如何使用Abaqus进行轮胎建模和分析。
轮胎是车辆中至关重要的部件之一,建立准确的轮胎模型可以帮助我们更好地理解轮胎的性能和行为。
步骤1:创建轮胎几何模型在Abaqus中,我们可以使用多种方法来创建几何模型。
在这个教程中,我们将使用简单的方法来创建轮胎的二维轮廓。
首先,打开Abaqus软件并创建一个新的模型。
接下来,选择创建几何模型的方法。
我们可以使用Abaqus 提供的绘图工具,也可以导入已经准备好的CAD模型。
在这个教程中,我们将使用绘图工具来创建轮胎几何模型。
创建几何模型的关键是确定轮胎的基本形状,例如总体尺寸、轮胎壁厚、胎纹等。
我们可以根据实际需求和数据来定义这些参数。
在实际应用中,通常需要使用更复杂的方法来获取轮胎几何参数。
完成轮胎几何模型的创建后,我们可以对其进行进一步的编辑和调整,以确保其符合设计要求。
在Abaqus中,我们可以使用各种编辑工具来修改几何模型的各个方面。
步骤2:设置轮胎材料属性完成轮胎几何模型的创建后,我们需要为轮胎指定材料属性。
Abaqus提供了许多预定义的材料模型,我们可以根据实际材料的力学性质来选择合适的材料模型。
在设定材料属性时,我们需要指定材料的弹性模量、泊松比、密度等参数。
这些值通常可以从实验数据或文献中获取。
Abaqus还允许我们定义材料的非线性行为,例如超弹性和塑性行为。
步骤3:创建轮胎网格完成轮胎几何模型和材料属性的设置后,我们需要对轮胎进行网格划分。
网格划分决定了模型在有限元分析中的精度和计算效率。
Abaqus提供了多种网格划分方法,例如等尺度划分和非等尺度划分。
我们可以根据实际需求和计算资源来选择合适的网格划分方法。
在网格划分过程中,我们还可以调整网格的密度和形状,以进一步优化有限元模型的精度和计算效率。
步骤4:定义轮胎加载条件在进行轮胎分析之前,我们需要定义轮胎的加载条件。
基于CATIA的轮胎轮廓参数化模板设计

基于CATIA的轮胎轮廓参数化模板设计李 华,张 敏,吴东霞,程丽娜(中策橡胶集团有限公司,浙江杭州310018)摘要:基于CATIA软件平台,对轮胎轮廓图进行参数化设计,并结合了CAA技术实现其快速系列化。
在CATIA平台创成式曲面设计模块中,通过创建关键参数、制定规则和编写检查驱动几何元素的生成,实现轮廓图模板的制作,结合CAA编程,提高了系列化扩展的自动化程度。
该设计方法可缩短轮胎开发设计周期,降低开发成本,提高设计自动化水平。
关键词:轮胎;轮廓;CATIA软件;参数设计;模板设计;CAA二次开发中图分类号:TQ336.1+1;TP391.7 文章编号:1006-8171(2021)04-0218-04文献标志码:A DOI:10.12135/j.issn.1006-8171.2021.04.0218轮胎设计形式选择多样,同花纹系列的轮胎规格数量常达几十个,经常需要耗费大量的设计时间。
随着轮胎行业的迅速发展,轮胎产品不论在产品规格线还是在花纹设计上的更新速度都越来越快,如何有效提高产品质量、缩短开发周期、降低开发成本、提高企业的市场快速响应能力,从而提高企业的盈利能力,已成为轮胎企业关注的重点。
在全球制造业为争夺数字化创新领导者地位展开如火如荼的竞争大环境下,全球三分之二的工业企业表示,生产价值链的数字化是其首要任务之一[1]。
现阶段的轮胎设计,众多轮胎企业已从以往的AutoCAD平台上的2D图形设计,转到Computer Aided Three-Dimensional Interface Application(CATIA),UG,Pro/Engineer,SolidWorks等三维设计平台上来。
CATIA软件采用全新的、基于组件的开放式体系结构,利用其参数化驱动模板设计配合Component Application Architecture(CAA)二次开发,能够有效缩短轮胎开发周期,将系列化产品快速投入市场,提高企业竞争力并提升企业形象[2-4]。
- 1、下载文档前请自行甄别文档内容的完整性,平台不提供额外的编辑、内容补充、找答案等附加服务。
- 2、"仅部分预览"的文档,不可在线预览部分如存在完整性等问题,可反馈申请退款(可完整预览的文档不适用该条件!)。
- 3、如文档侵犯您的权益,请联系客服反馈,我们会尽快为您处理(人工客服工作时间:9:00-18:30)。
外胎轮廓设计
一、 设计目的
通过查阅资料独立完成橡胶制品课程设计,加强对专业知识的掌握;对10.00—20轮胎的轮廓设计有了一定的了解;通过研究斜交载重轮胎的结构设计程序,掌握技术设计内容:外胎外轮廓设计、胎面花纹设计、内轮廓设计;掌握斜交轮胎的施工设计。
对橡胶工艺、轮胎工艺及橡胶制品工艺等区域的知识有更深一步的了解。
同时在运用计算机软件作图中,增强了
对AutoCAD 软件的熟悉与应用。
提高了自主学习的能力和自我思考的能力。
二.主要技术参数
表1 10.00—20轮胎的技术参数
参数
充气外直 径/mm 充气断面 宽/mm 标准轮辋
花纹类型
层级 单胎
最大负 荷/Kg 相应气
压/KPa
10.00—20 1055
278
7.5(平底) 普通花纹 16P.R 3000 810
表2 平底轮辋断面各部位尺寸
图1 轮辋断面图
轮辋轮廓规格
轮辋宽度 轮缘
胎圈座圆角半径
高度
宽度 半径 A
偏差 G
偏差
E ≥
R 2
偏差
R 3≤ 7.5
190
+3.0 -5.0
40.5 ±1.2 22.0 20.0 ±2.5
8
三.9.00—20斜交载重轮胎主要尺寸选取 1.主要技术参数的确定
①充气外直径D ′=1055mm ②充气断面宽B ′=278mm
2.负荷能力计算
确定外胎充气外缘尺寸D ′和B ′后,必须通过计算,验算其负荷能力是否符合国家标准,再进行外缘轮廓设计及计算,因此验算轮胎负荷能力是进行轮胎结构设计的基础。
负荷能力的计算公式为海尔公式,是一个在轮辋与充气轮胎断面宽之比等于62.5%的标准条件下(理想轮辋)得出的实验式, 若比值超出此范围,必须换算为在标准理想轮辋的充气轮胎断面宽才能使用此公式。
斜交轮胎负荷计算基本公式及负荷系数K 值的选取,载重轮胎和轿车轮胎选取不相同。
--=⨯⨯⨯⨯⨯⨯+320.585 1.390.2310.4259.810(1.0210)()R W K P B D B
1
1
1180arcsin
141.3W B B B -=⨯
o o
式中:W -负荷能力,kN
K -负荷系数【K =1.1(双胎),K =1.14(单胎)】 P -内压,kPa
D R -设计轮辋直径,cm
W 1-轮辋名义宽度,cm
B - 为62.5%的理想轮辋上的轮胎充气断面宽,cm
B 1-安装在设计轮辋上的新胎充气断面宽,cm
0.231-采用公制计算的换算系数,若用英制计算,此公式不必乘0.231。
已知条件:D=l055mm ,B 1=278mm, W 1=190mm ,P=810kPa ,D R = 508mm ,K D (双胎)= 1.l , K S (单胎)= 1.l4
将已知数值代入公式中,首先求取B 值,再求W D 双胎负荷,最后计算单胎负荷W S 。
B=B 1×[1800-arc sin (W 1/B 1)]/141.30 =278×[1800-arc sin (190/278)] /141.30=269.3(mm)
--=⨯⨯⨯⨯⨯⨯+320.585 1.390.2310.4259.810(1.0210)()D R W K P B D B
=0.231×1.1×0.425×9.8×10-3×(1.02×10-2×810)0.585×26.931.39(50.8+26.93) =27.5(KN )
W S =27.5╳1.14=31.38(KN ) (增加气压70kPa )
11
W
B
四.外胎外轮廓断面曲线设计 1.外胎各部位尺寸的确定 ①轮胎断面宽B 的确定
B B=
B /B
'
' B -胎模型断面宽,mm ;B ′-轮胎充气断面宽,mm ;B ′/B -断面膨胀率
轿车轮胎断面向扁平化发展,断面高宽比已成系列化,H/B 值分别为0.95、0.88、0.82等。
低于0.82的超低断面轮胎,大部分属子午结构,分别为78,70,65和50系列(即H/B 值为0.78,0.70,0.65,0.50)。
一般斜交轮胎H/B >1, B'/B 值在0.9~1.17之间;H/B<l , B'/B 在1.00~1.07之间。
取H/B=0.990 B'/B=1.130 又已知B ′=278mm 则B=246mm
②轮胎外直径D 和断面高H 的确定
/D D D D
'
=
' 一般H/B>l 的人造丝斜交轮胎,D ′/D<l ,约为0.990~0,999;尼龙斜交轮胎则不同,其H/B 值无论是大于或小于1,充气外直径均增大,一般约增加0.1~2.5%。
设骨架材料为尼龙帘线,取 D ′/D=1.009,又已知D ′=1055mm ,则D=1045mm
2.胎圈部位尺寸的确定
①胎圈着合宽度C
此宽度根据设计轮辋宽度W 1而定,一般胎圈着合宽度等于设计轮辋宽度W 1,有时C 可略小于W 1,以改善轮胎的耐磨性能和增大胎侧刚性,但减少的数值不宜过大,以15~25mm 为宜。
设定C=173mm 。
②胎圈着合直经d
装于平底式轮辋的载重轮胎,为便于装卸,胎圈着合直径d 比轮辋直径应大0.5~1.5mm 。
设定d=508.8mm. ③胎圈部位倾斜角度
平底式轮辋的载重轮胎,胎圈部位角度为0°~1°.设定胎圈部位倾斜角度为0.6°. ④ 胎圈轮廊曲线
胎圈轮廓根据轮辋轮缘曲线确定,由胎圈弧度半径R4和胎踵弧度半径R5组成 a.胎踵弧度半径R5比轮辋相应部位弧度半径大0.5~1.0mm 。
b.胎圈弧度半径R4比轮辋轮缘相应部位弧度半径小0.5~1.0mm ,其半径圆心点较轮辋轮缘半径圆心点位置略低1~1.5mm ,使轮胎紧贴于轮辋上。
3.断面高及水平轴位置的确定
断面水平轴位于轮胎断面最宽处,是轮胎在负荷下法向变形最大的位置,用H1/H2值表示。
H1/H2取值过小即断面水平线位置偏低,接近下胎侧,使用过程中,应力、应变较集中
于胎圈部位,易造成胎侧子口折断; H1/H2值过大则断面水平轴位置较高,应力和应变集中于胎肩部位,容易造成肩空或肩裂。
模型断面高: =1/2 ×(1045-508.8)=268.1mm.
21
2
1(
)
H
H H H =
+, 计算得知: H 1=H-H 2
一般上断面高均大于下断面高,因此设定H 2=138mm ,H 1=130.1mm 。
4.胎冠部位尺寸的确定
①行驶面宽度b 和弧度高h 的确定
由表查得载重轮胎普通花纹:b/B=0.75~0.80;h/H=0.035~0.055,不妨设定该载重轮胎的b/B=0.76,h/H=0.040,又已得知轮胎断面宽B=246mm ,H=268.1mm ,则b=186.96mm ,h=10.724mm.
②胎冠弧度半径的确定
设定胎冠断面形状为正弧形,则弧度半径Rn 根据行驶面宽度b 和弧度高h 计算, 计算公式为:
282
n b h R h =+
α'=0.01745a n L R
1
22(sin )n
b R α-= 式中:α—行驶面弧度的夹角;0.01745—常数,即为π/180; Rn —胎冠弧度半径,mm ;La ′—行驶面弧长,mm 。
对普通花纹的载重轮胎,采用一个弧度半径Rn ,又得知b=186.96mm ,h=10.724mm 则计算得知:Rn=412.8mm ,α=26.20,La ′=188.56mm.
4.胎侧部位尺寸的确定
胎侧孤度半径R 1、R 2、R 3的确定
一般下胎侧弧度半径R2应大于上胎侧弧度半径R 1,而R 1和R 2的圆心均设在断面水平轴上。
a. 上胎侧弧度半径计算公式为:
式中: 222
211
()()4H h B b L R B b
-+--=- L -胎肩切线长度(L 在轮胎断面中心轴的投影长度约为H2的50%),mm 。
已知H 2=138mm ,h=10.724mm ,B=246mm ,b=186.96mm ,将L=½H2=69mm 代入上式即可
计算出R1=208.5mm
)(2
1
d D H -=
b .下胎侧弧度半径的确定
22
11211
(2)()42R B W a H H R B W a
--+-=--
式中:H R — 轮辋轮缘高度,mm ;
a —下胎侧弧度曲线与轮缘曲线交点至轮辋轮缘垂线间距离( ~ ),mm ;
A — 轮辋轮缘宽度,mm ;W1—轮辋宽度,mm ;
B —轮胎断面宽度,mm ;H1—轮胎下断面高,mm ;
已知A=22.0mm ,a=33/48A=15.125mm ,B=246mm ,W 1=190mm ,H 1=130.1mm ,H R =40.5带入上式计算得出R 2=318.2 mm
c.下胎侧自由半径 R3的确定
一般R3约为R2的25~40%,设定R3为R 2×30%=95.5mm
③ 胎肩轮廓的确定
胎肩部采用切线形的设计方法。
5.外轮廓最终尺寸(单位:mm )
五.外轮廓断面图
[此文档可自行编辑修改,如有侵权请告知删除,感谢您的支持,我们会努力把内容做得更好]
3
2=a A 43。