铝电解槽内衬筑炉施工中的问题及改进策略
关于电解槽铝母线施工过程中存在的问题及对策

( 3 ) 铝 焊板应符合 G B f3 8 8 0中 1 0 6 0标准 以上 , 铝板 材料标 准厚度允许偏差应符合 G B 3 8 8 0 — 3 , 标准 : 十 0 . 1 0 ~0 . 5 。
4 . 2 软 铝母 线 的加 工
( 1 ) 软铝母线加工工艺流程如下 :
号料放样一确 定下料长度 尺寸一铝 软带下料一焊接 坡 口制 作一铝板 1 0片/ 束 ( 实 际情况而 定) 一一次 点焊一 压制成型一 平
台 上 点 胎 控 制 焊 接 尺 寸 一 对 反 坡 口 处 理 一 修 正 成 型 一 打 捆 入 库— 出厂 。
图 2 图 3
焊接前为保证焊接质量先在 8 2 2钢 平 台上 焊 接 胎 具 , 施 焊 时
作为反变形措 施, 首先试 焊两个待成功 ( 2 ) 软 铝 带 下料 时利 用 Q 1 1 - 1 XI O 0 0 剪 板 机 或 自制 机 动 剪 板 要 留一定的焊接预 留量 , 后 大 批 组对 施 焊 。 在 图 2 是 直 接 组装 形 成 , 图 3 在 装 胎 时安 装 基准 机进行 剪切下料 , 制 作 一 伸 缩 式 圆盘 支 承 铝 软 带 圈 料 , 使 下 料 长
要 特 别 保 护好 加 工 面 , 首先 把 母 线 1 与 母 线 2成一 度 公差控制在± O . 5 m m, 并保 证切 口为 9 0 。 角, 上下剪刃 间隙可调 面 一 定 要对 齐 , 定的夹角 固定在胎具上, 留出焊板位置 , 调整好角度 , 然后用夹 具 节, 下剪刃装 有一水平调整机构 可调整 间隙, 避免剪 切时边缘 剪 口有 毛 刺 。
固定在胎具上 , 特 别应注意的是 由于在 焊接过程 焊接变形 , ( 3 ) 利用压 力机压成 型 , 胎 具制作用 5 m m钢板 , 气 焊 加 热 制 据热力学原理在其纵 向将产 生焊接变形 , 5 0 ~ 2 0 0 mm 的 母 线 下垫 一 块 钢 板 , 垫 板 厚 度 需进 行 作成 软铝带成型外形尺 寸, 考虑铝 软带成型后 有一定 的回弹, 将 需 在 距 焊 缝 1 一般 钢板 厚度 为 8 4 m m, 其变形 量与焊接 速度及周 围 弧度 适 当放 小, 用 l O mm 以上 厚度的钢板焊接 成上下胎 , 同时应 试 焊确定 , 均要在焊板与母线接 口 加 筋板支承 , 防止受力变形 , 下胎具 进行二次 点焊 软带片头应对 环境温度有关 。母线焊接焊片组焊完后, 焊缝宽度为 1 2 ~ 1 5 a r m, 高度为 2 - 5 m m。 齐, 片头参差 不齐应小 于 2 m m, 捆 扎入库 , 软 铝带应有 妥善存放 处的周围进行封焊 ,
电解槽筑炉施工技术探讨

电解槽筑炉施工技术探讨【摘要】电解槽筑炉施工是整个电解槽施工中的一个重要环节,筑炉施工质量的好坏,直接关系到电解槽今后的生产寿命。
在施工中,通过严格控制进场原材料质量,选用适宜的机具设备,采用科学合理的施工工艺,对确保筑炉施工的质量具有十分重要的意义。
【关键词】电解槽;筑炉施工;技术措施中图分类号:tq151.1+5文献标识码: a 文章编号:引言电解槽是电解生产的主要热工设备。
电解槽把氧化铝中的铝转变成金属钒的过程其转变的主要是以冰晶石和氧化铝熔体作为电解质,以碳素材料作为两极,直流电在电极间产生热能并保持正常的电解温度,使冰晶石和氧化销熔体变成离子状态,同时实现电化学反成。
一、筑炉施工前应具备的条件1、对土建的要求车间封闭及屋面防雨、防风必须完成。
室内3.5米平台浇筑完成,经养护满足设计强度要求。
车间内轨道,、滑触线及车间照明必须完工。
通往车间引道铺设完成,并满足设计强度要求。
2、对安装的要求车间内的天车安装调试完成,保证正常使用。
电解槽槽壳安装完成,已标注中心线和水平线并经三方联检合格,签发工序交接证书后方可进行筑炉工作。
3、对施工环境的要求车间内的临时采暖完成,确保施工温度不低于+5、所使用的各种原材料的自然温度在0℃以上。
方可进行施工。
4、对设备机具的要求施工所需的各种设备机具应及时进入施工现场,按施工平面布置图就位,并进行设备的检查和试运转,确保施工中正常使用。
5、对施工人员的要求参加施工的人员应提前学习施工方案、熟悉工程图纸及有关筑炉等规程并参与施工交底,通过实际培训,掌握操作技术要领。
6、对施工材料的要求:筑炉材料必须有出厂合格证及材料化验单,根据材质的性质、保温程度、砌筑部位进行严格的挑选,分类堆放并表示明确。
耐火砖砌筑时,应进行选砖。
不同规格型号的砖、碳块挑选加工后,分类、分型号进行堆放,并做好标志牌,标志牌应标清型号、材质、代号、数量。
碳块到货后应严格仔细检查,对于受潮、麻点、裂纹等缺陷超过规定标准的碳块严禁使用。
试论大型预焙铝电解槽炉底结壳成因及应对策略

试论大型预焙铝电解槽炉底结壳成因及应对策略摘要:日常维护和管理大型预焙电解槽,在铝电解生产工作中,是一件重要工作。
主要是对炉膛进行合理的管理,在产生过程中,要保持炉底的整洁,这是保证电解槽正常运行的基础工作,同时也是提升铝电解生产质量的关键部分。
一般情况下,铝电解槽中的材料和热收支在生产过程中应动态平衡。
但如果电解槽中的氧化铝没有发生溶解,而在炉底形成了沉淀,就会破坏电解槽中的材料与热收支的平衡,且还会影响到磁场的变化,长期处于这种情况,电解槽就会发生一些问题,出现问题槽和病害槽的情况,这很容易导致事故。
关键词:大型预焙;铝电解槽;炉底结壳1铝电解槽炉底沉淀结壳的成因1.1电解槽热场不合理电解槽热场不合理主要有的原因是设计的不合理与运行电流强度的不合理,对炉底形成结壳有着重要的影响。
其根本是电解槽热收入小于热支出,电解质和槽底混合物凝固沉淀在阴极表面上越来越多,不能及时熔掉,越来越厚,形成坚硬的结壳层。
在好的电解槽热场中,底部内衬的900℃等温线要在阴极炭块层的下面,否则炉底温度过低则不利于熔解物料,形成沉淀引起结壳。
1.2氧化铝浓度偏大尽管现在电解槽方面提升使用了智能控制技术,能够把氧化铝的浓度管控在较低的范围,使其在生产过程中的氧化铝不产生沉淀,但是行业目前的系列运行基础数据的采集自动化、智能化与作业机械化、精细化的限制,在生产过程中如换极、填加覆盖料、处理堵料、处理结包等作业,仍有大量的过剩物料进入电解槽中,电解质未能及时全部溶解,沉积在电解槽的底部,慢慢的形成炉底结壳。
1.3分子比过低在铝电解生产中,需要特别注意的技术控制参数是分子比。
过低的分子比电解质会因为初晶温度较低而处于低温状态的情况,导致电解质粘度较大,电解质流动性变差,导电能力减小,会影响氧化铝的扩散以及溶解速度,没有及时进行溶解的氧化铝会因冷凝会沉积在电解槽的底部,慢慢地就会由沉淀转化成在的炉底结壳。
1.4电解质水平较低电解质对于电解铝的生产来说有着十分重要的作用。
电解铝生产中存在的隐患及防范措施

电解铝生产中存在的隐患及防范措施电解铝生产是靠矿山煤、电、铝产业链发展起来的,它在生产过程当中存在的安全隐患与井下的顶板、瓦斯等五大隐患有所不同。
那么,在电解铝生产中到底存在哪些隐患,怎样去防范呢?这得从电解铝的工艺说起:电解铝是用直流电使电解槽的两极产生热量熔融冰晶石和氧化铝,保持一定的电解温度来实现电化学反映,反应生成二氧化碳和铝。
二氧化碳、氟化氢气体及部分氧化铝粉尘成为电解烟气经烟管送净化处理,铝液经真空包吸出运到浇铸车间,倒入混合炉后浇铸成铝锭。
这一工艺流程,我们新一代铝业人苦苦经营了十年,十年的探索路让我们对隐患有一种特殊的认识。
在这条不断探索、不断求知、不断地去学习、不断成长的征途上也伴随着一起起事故的发生。
关于“11·6”铝水烫伤人员的事故经过分析:那是在2022年11月6日下午4:05时,浇铸车间发生的一起启拉母线的结晶器内铝水爆炸事故,造成陈某等5人被铝水烫伤,通过组织有关人员进行事故原因分析认为:第一个是二次冷却水管被人踩动发生扭曲而改变了喷水方向,水流向结晶器引起铝水爆炸;第二个是受伤人员轮岗时违反规章管理制度未穿戴好劳保用品而造成烫伤。
事后为了不再有类似的事故的发生,采取了以下防范措施:1.重新认真组织员工学习《安全规程》及有关规章管理制度,并要求工作人员穿戴好劳保用品;2.加强工作现场管理,为工作人员创造一个良好的安全环境。
对以上发生的事故进行分析,此类事故属烫伤事故,事故源于高温的铝液。
这就是在电解铝生产过程当中存在的隐患之一。
让我们来看看这是怎么一回事:在电解铝生产过程当中,电解的温度应当保持在945℃—965℃,也就是说液态铝水的温度只有控制在此范围以内才能完成理论上的电化学反应,生成铝。
可见,这样高的温度相对人体所能承受的常温之比悬殊甚大,要是以人体所能承受的温度40℃来计算,铝液的温度相当于人体温度的21—24倍还要多,在电解铝生产过程当中,虽然人们采用在电解质熔液表面加盖了保温料,尽可能减少热扩散和热辐射,从而避免高温直接对人体的伤害,同时用以提高电流效应,但是在出铝、换阳极、测两水平、打渣、捞块等工作时,必须与高温的铝液接触,这就难免再次发生类似的烫伤事故。
铝电解槽扎固问题分析及相应改进措施探讨

解槽 阴极 装置 同铝 液直接 接触 , 与 电化 学反应 , 参 是
决 定 电解槽 寿命 的关键 。
/一
间缝 渗入 电解质 和铝液 导致 早 期 破 损 的 占 8 % , 2 侧 部渗 入 电解 质和 铝液 导致早 期破 损 的 占 1 % , 他 0 其
占8 %。这 充 分 表 明 , 电解 槽 早 期 破 损 的 主 要 部 位 是 阴极 装置 的底 部 。铝 电解 槽 的 扎 固 , 特别 是 底 部
黄 昕 , 义伦 , 先 琼 , 晓 宏 刘 赵 金
( 中南 大学 机 电工程 学 院 , 沙 4 0 3 长 1 8) 0
摘 要 : 结合生产实际 , 从扎固的工艺、 糊料 、 设备 、 质量检测等方 面对电解槽扎 固的现状进 行综合分析 。分 析表明, 基础理
论研究缺乏、 国家 标 准 不 完 善 、 产 设 备 陈 旧 、 生 检测 方法 落 后 是 造 成 铝 电 解 槽 扎 固 质 量 不 高 的 主 要 原 因 。 目 前 急 需 加 强扎 固 的 基 础理论研究, 并在 此 基 础 上 完 善 糊 料 、 固 工 艺 和质 量 检测 的 国家 标 准 , 发 自动 化 扎 固 设 备 和先 进 检 测 方 法 , 高 扎 固 质 量 从 而 扎 开 提
F g 1 P e b k n l mi u r d cin c l i . r - a i g au n m e u t el o s
作者简介 : 黄
昕( 9 8 , 湖北大悟 县人 , 1 7 一) 男, 博士生 , 主要从事
( e t h rig cn e c agn ) r
和 经济效 益 。电解 槽 一 旦 出现 破 损 必须 停 槽 修 理 ,
浅谈铝电解槽改造以及内衬破损原因

浅谈铝电解槽改造以及内衬破损原因【摘要】本文首先对现今铝电解槽的使用和改造情况进行了基本概述,随后就电解槽改造途径进行了相关探讨,最后对技改电解槽典型的内衬破损状况和原因给予了一定的分析。
【关键词】铝电解槽;改造途径;破损原因0.引言现代铝电解槽改造从哪些方面着手,早期破损槽中存在的设计、施工质量、焙烧启动等问题,可以给改造的过程指引一个方向,这一直是我们关注的重点。
所以要认真探索电解槽改造途径,进而有效实现延长槽寿命达到节能减排,增加效益的目的。
1.铝电解槽现状二十世纪八十年代,因为国家提出的“优先发展铝”方针,使我国的电解铝工业得到了迅猛的发展。
2000年,全国电解铝厂约130家,相当于世界其它所有国家的电解铝厂数量。
2007年,我国电解铝产量已达到1318万吨,居世界首位,同时,电解铝技术取得了很大的突破。
在大型预焙阳极电解槽的设计、制造和生产技术等领域有了自身的大型铝电解技术体系,目前300KA至400KA以上的铝电解槽技术已经成熟,达到国际先进水平,得到了普遍的应用。
大型铝电解槽投入生产,紧随而来的是而关于电解槽寿命问题,在160KA 电解槽时期,整体槽寿命就比国外电解槽寿命短,如今该难题尚且存在。
铝电解生产中,影响铝电解槽寿命的原因无非就是以下几点:即结构设计,槽内衬材料,筑炉和施工质量的问题,也有焙烧启动的方式、方法问题,更有电解槽早期管理和工艺要求问题。
上述各个环节以及在此过程中的优劣,都会对槽寿命造成重大影响。
多年前,我国电解铝厂从国外引进了铝电解槽焦粒焙烧干法启动技术,将落后的铝液焙烧技术取代了。
虽然焦粒焙烧并不是我国的知识产权技术,但是对于我国的电解铝厂而言应该算得上是技术上的进步。
此外,应用铝电解槽焙烧技术,槽寿命并无显著提高。
最早使用焦粒焙烧技术的是白银铝厂,而电解槽的寿命海上徘徊在1500天左右。
这样不难看出,就目前国内电解铝厂而言,单单用焦粒焙烧干法来启动的方式,想达到提高铝电解槽的寿命的要求是不太现实的。
铝电解槽阴极内衬施工要点
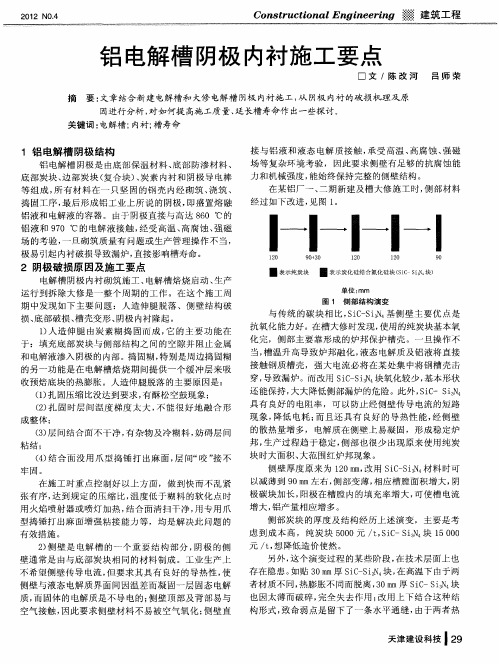
张有 序 , 到规 定 的压 缩 比, 度 低 于糊 料 的 软化 点 时 达 温 用火 焰 喷射 器或 喷 灯 加热 , 结合 面清 扫 干净 , 用专 用 爪 型 捣 锤打 出麻 面 增 强粘 接 能力 等 ,均 是 解 决此 问题 的 有 效措 施 。 2 侧 壁 是 电解 槽 的一 个 重 要 结 构 部 分 , ) 阴极 的侧 壁 通 常是 由与底 部 炭块 相 同 的材 料制 成 。工业 生产 上 不 希望 侧 壁传 导 电流 , 要 求其 具有 良好 的导 热性 , 但 使
侧 壁 与液 态 电解 质 界面 问因温 差 而凝 固一 层 固态 电解 质 , 固体 的 电解 质 是 不 导 电的 ; 壁顶 部 及 背部 易 与 而 侧
空气接 触 , 因此要 求 侧 壁材 料 不 易被
建筑工程 嚣 osrcin l n ier g iC n t t a gnei u o E n
关键词 : 电解槽 ; 内衬; 槽寿命
1铝 电解槽 阴极结构
铝 电解 槽 阴极 是 由底 部 保温 材 料 、 部 防渗 材料 、 底
底 部 炭块 、 部 炭块 ( 边 复合 块) 炭 素 内衬 和 阴 极 导 电棒 、 等 组 成 , 有 材 料 在 一 只坚 固 的钢 壳 内经 砌筑 、 筑 、 所 浇 捣 固工 序 , 后 形 成铝 工 业上 所 说 的 阴极 , 最 即盛 置熔 融 铝 液 和 电解 液 的容器 。 由于 阴极直 接 与高 达 8 0 ℃的 6
21 N. 0 0 2 4
C n tut n l n ier g 麓 建筑工程 osr c o a gn ei i E n
铝 电解 槽 阴极 内衬 施 工要点
铝电解槽扩容槽结构的改进与优化
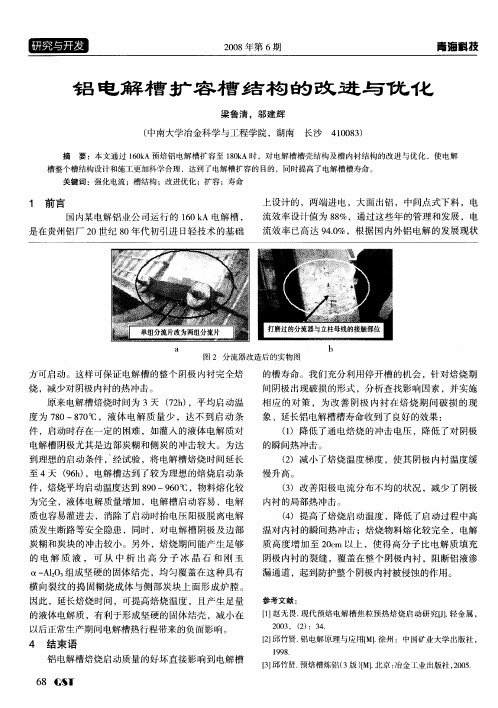
的立缝相互错开 ;4 由于 s N 结合 S 砖强度大 ,不 () i , i C 易 加 工 ,因 此 角 砖 、加 工 块 用 普 通 13 m 的侧 部 炭 2m
§T 6 9
20 年第 6 08 期
青 海 斟 技
石 油 焦对预 焙 阳极 质 量 的影 响及 控 制
张国林
( 中南 大学冶 金科 学 与工程 学 院 ,湖南
()减小了焙烧温度梯度 ,使其阴极内衬温度缓 2 慢升高。
()改 善 阳极 电流分 布 不均 的状况 ,减 少 了 阴极 3 内衬 的局部 热 冲击 。 ()提 高 了焙烧 启 动温 度 ,降 低 了启 动过 程 中高 4 温对 内衬 的瞬 间热 冲击 ;焙 烧物 料 熔化 较 完全 ,电解
度 。2 0 年该公司根据现有的供 电设施 尚有提供系列 05 电流的能力 ,为充分利用 已有铝 电解设备 ( 电力 、电 解 槽 ) 的潜力 ,通过 适 当提 高铝 电解 系列 电流 ( 即强 化 电流)的方法提高铝产量 ,从而用较小 的投资获得
较 大 的经济 效 益 。 扩 容改 造 的 电流 强度 是 在原 有 的 10A 电流基 础 6k
1 引言
铝 电解 用 预 焙 阳极 被 称 为是 电解 槽 的 “ 脏 ” 心 ,
是在贵州铝厂 2 世纪 8 年代初引进 日轻技术的基础 0 0
h
图 2 分流 器 改 造 后 的 实物 网
方可启 动 。这样 可保 证 电解槽 的整 个 阴极 内衬 完 全焙 烧 ,减 少对 阴极 内衬 的热冲击 。 原 来 电解 槽 焙烧 时 间为 3天 (2 ) 7h ,平均 启 动温 度 为 70 80 ,液 体 电解 质 量 少 ,达 不 到 启 动 条 8 7 ℃ 件 ,启动 时存 在一定 的困难 ,如灌 入 的液 体 电解 质对 电解槽 阴极 尤 其是边 部 炭糊 和侧 炭 的冲击 较 大 。为达 到理 想 的启 动 条件 ,经试 验 ,将 电解槽 焙 烧 时 间延 长 至 4天 (6) 9 h ,电解槽 达 到 了较 为理 想 的焙 烧启 动条 件 ,焙烧平 均启 动温度 达到 80—90C,物 料熔 化较 9 6 ̄ 为完 全 ,液体 电解 质量 增加 ,电解槽 启动 容 易 ,电解
200kA电解槽内衬结构分析与改进方案

Analysisandimprovementofliningstructurein200kA pot
LiuSiren,ZhaoXinliangandXuLusheng
(ChinaNon-ferrousMetalIndustry'sForeignEngineeringandConstructionCo.,Ltd.,Beijing100029,China)
Abstract:Theinsulationperformanceof200kApotline'slininginaforeignprojectissystematicallystudied,andextensiveresearchfortheliningstructure iscarriedoutonthebasisofmeasureddataforthepotswhichareunderproductionstatus.Theanaloguesimulationofphysicalfieldhasbeenundertaken forthepots,thedeficiencyoftheliningstructureisanalyzedandsomeoptimizationmethodsandimprovementmeasurementsareproposed. Keywords:pot;analoguesimulation;energybalance;lining
40.026 63.919 87.812 111. 706 135.599 159.492 183.386 207.279 231.173 255.066
图 2 电解槽槽壳温度分布
22 铝液流速场测试 我们将纯铁棒插入到铝液层中,在铝液中停留
电解槽维修年总结

电解槽维修年总结简介电解槽是电解铝生产过程中重要的设备之一,它用于将氧化铝转化为铝金属。
为了确保电解槽的正常运行和生产效率,必须定期进行维修和保养。
本文将对电解槽维修过程中的问题和解决方案进行总结和分析。
维修过程中的常见问题1. 阳极覆盖层脱落阳极覆盖层脱落是电解槽维修过程中最常见的问题之一。
这会导致阳极的效能下降,进而影响铝的产量和质量。
造成覆盖层脱落的原因可能是材料质量不过关,也可能是运行过程中过度磨损或接触急剧变化所引起的应力。
2. 电解液泄漏电解液泄漏是另一个常见的维修问题。
电解液泄漏可能会造成环境污染,同时还会损害设备和工人的安全。
泄漏的原因可能是密封件老化,设备磨损或腐蚀引起的。
3.电解槽电流不稳定电解槽电流的稳定对于铝的产量和质量至关重要。
如果电流不稳定,可能会导致铝的产量下降或出现质量问题。
导致电流不稳定的原因可能是电极老化,电解液浓度变化,或电源供应问题。
解决方案1. 更换阳极覆盖层为了解决阳极覆盖层脱落的问题,可以考虑更换阳极。
选择质量更好的阳极材料,以提高阳极的耐磨性和使用寿命。
此外,定期检查和保养阳极也是必要的,例如进行覆盖层的清理和修补。
2. 检查和更换密封件为了避免电解液泄漏,必须定期检查和更换密封件。
选择耐腐蚀和耐磨的密封件,确保其质量和密封性能。
此外,定期清洗和保养设备,可以减少密封件的磨损和腐蚀。
3. 跟踪电解槽参数为了解决电解槽电流不稳定的问题,必须定期跟踪关键参数,例如电解液浓度,电极磨损情况,电源供应稳定性等。
根据参数变化及时采取调整措施,例如调整电解液的浓度,更换老化的电极,确保电源供应稳定等。
结论电解槽维修是电解铝生产过程中不可或缺的一部分。
解决常见问题和及时维护保养对于电解槽的正常运行和生产效率至关重要。
通过更换阳极覆盖层,检查和更换密封件,以及跟踪关键参数,可以提高电解槽的维修质量和效果,确保铝的产量和质量达到预期目标。
以上是对电解槽维修年总结的简要概述。
铝电解槽传统槽内衬扎固工艺存在的问题及原因分析
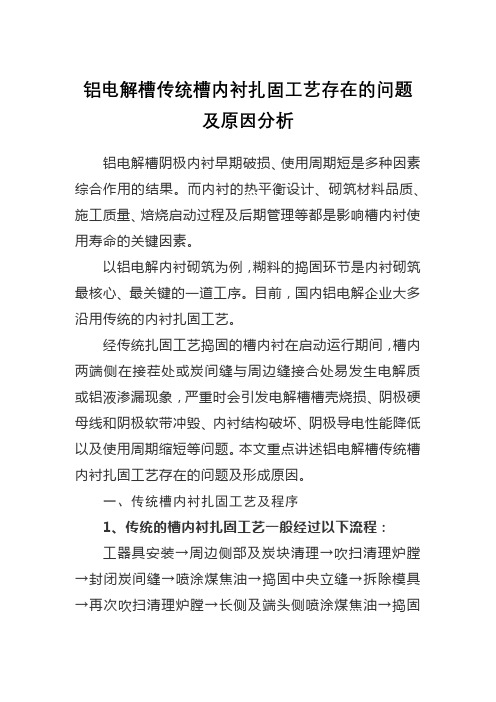
铝电解槽传统槽内衬扎固工艺存在的问题及原因分析铝电解槽阴极内衬早期破损、使用周期短是多种因素综合作用的结果。
而内衬的热平衡设计、砌筑材料品质、施工质量、焙烧启动过程及后期管理等都是影响槽内衬使用寿命的关键因素。
以铝电解内衬砌筑为例,糊料的捣固环节是内衬砌筑最核心、最关键的一道工序。
目前,国内铝电解企业大多沿用传统的内衬扎固工艺。
经传统扎固工艺捣固的槽内衬在启动运行期间,槽内两端侧在接茬处或炭间缝与周边缝接合处易发生电解质或铝液渗漏现象,严重时会引发电解槽槽壳烧损、阴极硬母线和阴极软带冲毁、内衬结构破坏、阴极导电性能降低以及使用周期缩短等问题。
本文重点讲述铝电解槽传统槽内衬扎固工艺存在的问题及形成原因。
一、传统槽内衬扎固工艺及程序1、传统的槽内衬扎固工艺一般经过以下流程:工器具安装→周边侧部及炭块清理→吹扫清理炉膛→封闭炭间缝→喷涂煤焦油→捣固中央立缝→拆除模具→再次吹扫清理炉膛→长侧及端头侧喷涂煤焦油→捣固长侧及端头侧→转移工器具至另一侧→捣固另一侧→炭帽捣固→清理炉膛。
2、内衬扎固准备及中央立缝扎固:在捣固槽一侧安装压缩机、风包、风管、扎固枪等工器具;将槽内阴极炭块的表面、侧面、炭间缝及周边侧砖所粘附污渍清理干净;使用预制好的模具封闭炭间缝两侧。
捣固前,沿每条炭间缝喷涂厚度约2~3mm煤焦油,按设计要求铺设糊料后逐层完成中央立缝捣固。
3、中央立缝捣固完成后,拆除模具,对槽内散落的糊料及杂物进行吹扫清理。
4、、长侧面和端头面扎固长侧面与端头面的扎固工作分两部分完成,具体扎固步骤如下:在周边炭块边缘及侧砖表面(即与糊料能够接触到的位置)喷涂煤焦油。
首次喷涂一个长侧面和一个端头面;扎固时,每一层糊料要预留错台,其目的是在捣固另一部分糊料层时便于在接茬处搭接,不产生垂直通缝。
通常情况下,预留接茬的位置不选在槽端头中部(即出铝口或火眼位置),通常会选择在靠近角部或角部。
完成一侧糊料捣固后,转移设备、工器具至另一侧并按预留接茬逐层完成。
简析电解铝行业中的电解槽维修策略

简析电解铝行业中的电解槽维修策略摘要:电解铝行业中电解槽运行是否正常直接影响铝电解生产成本和经济指标,而加强铝电解槽的维修是保障其正常运行的重要途径,基于此,本文结合大型铝电解槽,简述了电解铝行业中电解槽维修的必要性,对电解铝行业中电解槽的破损原因及其维修策略进行了简要分析。
关键词:电解铝行业;电解槽;维修;必要性;破损原因;策略一、电解铝行业中电解槽维修的必要性随着节能环保概念的不断深入,电解铝行通常新建具有烟气净化系统、自动控制系统、输送系统的环保性能较好、劳动强度较低、产量高的大型铝电解槽加。
这种大型铝电解槽熔炼面积较大、电流强度和电磁场较高、下料和打壳点多等特点,铝电解槽投产运行后需定期巡检、维护和维修。
如不了解大型电解槽的维修,不制定合理有效地巡检、维修制度,不采取定期维护和维修,发生零配件损坏、零配件报废、各系统发生故障瘫痪等事故,会对正常生产带来一定的影响,因此必须加强对其进行维修。
二、电解铝行业中电解槽破损的原因分析1、铝电解阴极材料对槽寿命的影响。
(1)阴极内衬侧部碳块。
由于国内碳化硅结合氮化硅侧块价格比较昂贵,我国自主开发的大型预焙槽绝大多数首次采用碳块与氮化硅结合的复合型砖块。
尤其桥头铝电公司在建设初期电解槽内衬侧部碳块采用带试验性质的90mm厚半石墨化普通碳块粘30mm厚的碳化硅材料砌筑成的前后复合块,在使用过程中由于两种材料的膨胀系数不一样,在正常生产中出现大面积碳化硅脱落和碳块消耗过快的现象,造成侧部漏电和侧部红炉帮,给电解槽的平稳运行及槽寿命带来极大影响。
(2)阴极碳块。
铝用阴极碳块在电解过程中不仅要承受高温冰晶石熔体的侵蚀,还要承受熔盐的电解过程的电化学作用,因此阴极碳块材料的好坏,直接影响阴极使用寿命。
而目前预焙铝电解槽除少数采用普通阴极碳块外,绝大部份采用半石墨质阴极碳块,其最大缺点是体积膨胀率较大,使阴极碳块在铝电解生产过程中,易产生变形和向上隆起,尤其在抗热冲击性能和抗热钠方面较差,在焙烧过程中钠和电解质向阴极碳块渗透,造成阴极起层脱落,形成充蚀坑。
铝电解槽阴极内衬施工工艺改进

铝电解槽阴极内衬施工工艺改进通过对铝电解槽内衬易损部位的分析与探讨,对铝电解槽阴极内衬一些改进的施工工艺进行了介绍。
标签:电解槽;阴极内衬;施工0 前言铝电解槽以冰晶石和氧化铝熔体作为电解质,以炭素材料作为两极,直流电经阳极导入电解液和铝液层,而后从阴极流出,直流电在电极间产生热能并保持正常的电解温度900℃~950℃,使冰晶石和氧化铝熔融体变成离子状态,完成电化学反应,在阴极上析出液态金属铝。
电解槽的阴极内衬既是析出铝液的贮存之处,又是电解过程的导体,这就要求阴极材料必须既具有良好的导电性,又具有较强抵抗熔融盐和金属铝液侵蚀的能力,为此,电解槽的阴极内衬主要以炭素材料为主,如:用半石墨质阴极炭块作为槽底的主要组成部分,施工过程中既要考虑到导电性即尽可能降低阴极砌体的电阻值,增强导电性能,又要考虑到砌体的致密性,增强砌体抗侵蚀性与抗渗透性。
1 铝电解槽阴极内衬施工工艺介绍铝电解槽阴极内衬施工工艺流程如图1所示。
由图1可以看出,电解槽的内衬施工工序较多,再加上电解槽的改造一般是成批进行,从客观上要求阴极内衬的施工必须“流水线”进行,而“流水线”作业的一大特点就是上下工序制约较强,一环紧扣一环,只要中间某一道工序不能顺利进行,就会导致下道工序的停工,从而造成延误工期与劳动力的闲置。
2 铝电解槽阴极内衬渗铝状况与分析铝电解槽阴极内衬的受损程度直接影响到铝电解槽生产是否正常,电解槽的停产检修大部分与阴极内衬破损、槽底渗铝、槽底隆起、铝液铁含量上升等因素有关,停产检修主要是进行阴极内衬的检修。
在某铝厂大量铝电解槽阴极内衬拆除过程中发现,铝液渗透主要分布在以下部位:(1)阴极窗口部位,这主要是阴极钢棒融化,铝液从阴极窗口渗出;(2)阴极炭块内,这主要是阴极炭块组开裂,铝液往下渗透,出现阴极炭块内夹杂铝液;(3)侧部炭块后部,这主要是铝液经不严密的侧部炭块之间的缝隙渗透到侧部炭块后部;(4)底糊内,这主要是底糊出现夹层,铝液直接渗透到致密性差的夹层内;(5)干式防渗料表面或干式防渗料内部,在阴极炭块组开裂后,铝液沿着裂缝往下渗透,直至干式防渗料表面,干式防渗料与铝液反应生成一种致密的化合物,阻止铝液的进一步往下渗透,但是如果干式防渗料捣打不均匀密实,铝液沿着干式防渗料的薄弱部位继续往下渗透,从而出现有的铝液只渗透到干式防渗料表面,有的直接渗透到干式防渗料内部的现象。
铝电解设备管理存在的问题与改进策略

铝电解设备管理存在的问题与改进策略作者:张晓辉来源:《西部论丛》2020年第16期摘要:随着我国经济的快速发展,国家越来越重视铝电解设备管理中存在的问题。
为了进一步提高铝电解管理效率,需要根据实际情况了解铝电解工程工艺,明确整体电解工作的运转流程,满足国内不断提高的铝电解工程施工工艺需求,确保其可逐渐进入到高效率阶段,降低铝电解设备中存在的安全隐患。
因此本文主要针对铝电解设备管理存在的问题与改进策略进行简要分析,并提出合理化建议。
关键词:铝电解设备;设备管理;问题与策略1.前言随着社会的不断发展,铝电解行业面临着严峻的产能过剩的情况,其价格与生产成本不断倒挂。
在新的社会市场竞争背景下,企业必须要选择新的经营管理方式,应用新型的市场竞争策略,尽可能激烈的市场竞争中谋求一定的席位。
对此,相关行业要不断的改进铝电解生产工艺,引进新型的设施设备,提高设备的运转效率,逐步提升铝电解设备的固定资产收益效率。
2.铝电解设备管理基本情况2.1设备前期的工作效率低在铝电解设备管理过程中,常常出现较多的设备前期管理问题。
此时,设备管理部门与采购部门之间的沟通较少。
有时只是直接使用采购部门所采购的设施设备,对设备的设计以及选择参与力度低,甚至根本没什么发言权。
在设备正式投入生产运行前,没有配备专业的人员检查设备是否符合运行标准,直接将采购的设备组装使用,导致产后的维修成本大大增加,与设备生产供应商之间的联系也更加频繁。
除此之外,设备在管理时,部分企业往往都是赶货状态。
忽视了设备的前期检查以及选择工作,导致设备不符合实际的生产条件,故障频发,维护成本直线上升,设备的使用价值和生产价值低。
2.2设备维护维修资金耗费大在铝电解设备管理过程中,铝电解企业大多数采用定期维护的方式对设备进行检查,缺乏日常维护管理工作,基本依据设备的采购时间以及投入时间安排周期进行大修、中修以及小修。
该种维修制度虽然可以减少部分非计划性故障停机工作,具备计划性强和预防性高等优势,但并未考虑到设备的实际运行情况,维修时间灵活性差,部分设备经常出现维修不足以及维修过度等情况。
铝电解槽筑炉工程施工要点阐述

铝电解槽筑炉工程施工要点阐述摘要:随着科学技术的发展,电解铝技术也随之进步,国内外500KA、600KA 等大型电解槽已陆续投入生产,再加上现阶段城市化进程对于电解铝的强烈需求,就在很大程度上推动了电解铝事业的发展。
实际发展中,电解槽在达到使用寿命后需要电解槽等附属设备进行施工,而电解槽的筑炉质量就在很大程度上影响着电解铝的使用状态和生命周期,就需要相关人员加强对铝电解槽筑炉技术的研究,在了解其施工要点的基础上对其质量进行保证。
本文就从铝电解槽筑炉技术入手,浅谈其工程的施工要点。
关键词:铝电解槽;筑炉工程;施工要点;技术手段铝电解槽作为现阶段工业产业发展的重要设备,很大程度上影响着电解铝行业的发展,多以为了保证电解铝行业的发展壮大,相关人员就需要加强对铝电解槽的重视,保证电解槽的质量。
但是电解槽技术较为复杂,流程较多,尤其是在筑炉环节,需要更强的技术,相关人员就很容易在该环节出现失误,造成筑炉作业的问题,影响筑炉的质量。
在此基础上,相关人员就需要在作业环节加强对铝电解槽筑炉工程施工的重视,积极研究其作业流程和作业方法,然后掌握先进的工程施工技术要点,以保证筑炉工程的质量。
一、铝电解槽筑炉工程概述现国内外大型预焙阳极电解槽多数采用摇篮架结构,主要由槽体、内衬组成。
按电解液的不同分为水溶液电解槽、熔融盐电解槽和非水溶液电解槽三类。
当直流电通过电解槽时,在阳极与溶液界面处发生氧化反应,在阴极与溶液界面处发生还原反应,以制取所需产品。
对电解槽结构进行优化设计,合理选择电极和隔膜材料,是提高电流效率、降低槽电压、节省能耗的关键。
铝电解槽就是用来进行电解铝作业的电解槽,在现阶段工业化的发展过程中发挥重要作用。
而筑炉则是电解槽作业中的主要作业之一,是指砌筑工业炉窑的工程。
筑炉质量直接影响炉子使用寿命,并且影响产品的产量和质量。
所以筑炉环节就需要遵循砌体尺寸准确、错缝砌筑、砖缝大小符合要求,保证膨胀缝砌筑质量,砌体表面勾缝,工作面平整,保证拱顶的砌筑质量等原则,这样才能够保证工程的质量【1】。
铝电解槽内衬筑炉施工质量研究

铝电解槽内衬筑炉施工质量研究摘要:电解槽的寿命是影响整个电解铝工艺质量的重要因素,过短寿命的电解槽是制约电解生产发展的消极因素。
近年来,对铝电解槽寿命的延长措施,一直是各个电解铝相关企业不断探索和追求的。
本文将从铝电解槽内衬筑炉施工过程中较易出现的一些问题入手,详细分析出现问题的各种原因,最后以此为依据提出改进筑炉施工质量的相关措施,从而提升铝电解槽寿命。
关键词:铝电解槽;内衬筑炉施工质量;改进措施引言:在我国铝电解的具体生产过程中,电解槽的槽型经历了多种发展,随着我国科学技术的不断进步,对电解槽的设计进行了多方面的改进,使得电解槽的寿命相比于十年前已经翻倍提高,其总体寿命不断显示出上升的态势。
本文对影响铝电解槽寿命的最重要因素——槽内衬筑炉的施工质量展开细致的分析和讨论。
一、铝电解槽内衬筑炉施工中较易出现的问题(一)阴极炭块出现的问题及原因探究对多个质量已经出现问题的破损电解槽分解研究发现,内部的阴极炭块质量出现问题是造成电解槽破损的主导原因。
对于阴极炭块质量的把握有一定的难度,原因是当前我国国内市场中生产阴极炭块的厂家非常多,制造方式各有差异,有些厂家生产时采用振动成型,有些则利用挤压成型,导致其质量常常不尽相同。
事实上,无论是阴极炭块的哪种成型方式,最关键的是要把握好阴极炭块的成型工艺。
从对诸多破损电解槽的详细分析,可以大致总结出阴极炭块可能出现的一些问题:①阴极炭块局部产生裂纹、发生起层和出现横向断裂等现象,这是由于成型的阴极炭块在出入库时没有受到严谨的检查,使得一些不合格的产品成为铝电解槽内衬筑炉的组成部分,融入施工过程;②阴极炭块作为铝电解槽的阴极筑砌在槽底部时,出现高温爆裂现象,这说明阴制作极炭块所需的原材料投入使用之前工作人员对其的保存不够严密,使其中掺杂了其他杂质。
或者是在对制作炭块所需原材料进行配比时,称量缺乏准确性也容易造成高温爆裂。
阴极炭块出现裂缝,会使得电解铝液与炭块发生反应从而生成化合物,这会增加炭块的体积,铝液会从裂缝中渗漏出来再与钢棒发生反应,生成合金铝,长此以往就会导致漏炉。
铝电解槽内衬筑炉施工质量分析

铝电解槽内衬筑炉施工质量分析摘要:在铝电解的生产中,电解槽寿命是制约电解生产发展的重要因素,虽然国内电解槽300KA以上的槽型发展比较快,设计院从设计方面做了很多的改进,生产企业从焙烧启动、后期的生产管理也在不断的提高,但电解槽的寿命问题是直接影响电解铝的生产成本和生产效率的核心,延长铝电解槽寿命是电解铝企业的一贯追求。
目前电解槽的寿命在不断提高,从2005年的1200-1500天的使用寿命提高到目前的2000天以上,电解槽槽寿命总体呈上升趋势,笔者从铝电解槽内衬筑炉施工质量进行分析探讨。
关键词:铝电解槽;破损原因;施工质量引言:文章主要对电解槽内衬质量的分析,找出了在内衬砌筑中的几个问题,并且按照找出问题采取了相应的措施,使电解槽的寿命有了明显的提高,有效遏制早期破损槽的发生,总之要提高铝电解槽的寿命,不仅从电解槽槽壳设计、碳素材料、施工质量等各环节做好,而且更重要的是从电解槽的焙烧启动及正常的生产管理进行严格控制。
1 施工中容易出现的原因1.1阴极炭块的问题从早期破损的电解槽看,阴极炭块的质量是导致早期破损的直接原因,目前阴极炭块的生产厂家多,质量参差不齐。
其中有些生产厂家是振动成型,有些厂家是挤压成型,不管是挤压成型还是振动成型,关键在于阴极炭块在生产过程中的工艺控制,针对出现的几台早期破损槽的分析看,阴极炭块的横向断裂、起层、局部出现裂纹,说明生产厂家在产品出入库存在问题,没有严格检查,导致不合格的产品进入施工现场;原材料在使用前保管不好,掺入了杂质(煤矸石等),阴极炭块在生产过程中杂质挥发或高温爆裂,出现阴极炭块空洞,导致电解槽从空洞处漏炉,另外在配比过程中的计量不准也是造成上述现象的因素之一,如果阴极炭块破损或裂缝,导致铝液中的钠与炭块中的炭作用生成化合物,使炭晶格间的距离增大,使炭块的体积膨胀,很容易使铝液和电解质液沿炭块的裂纹渗透,至致接触到阴极钢棒生成合金铝,严重时导致漏炉。
1.2侧部炭块的问题目前各铝企业中依据设计院设计不同而结构各不相同,有普通的碳素侧部块,有氮化硅结合碳化硅侧部复合块,有氮化硅结合碳化硅。
微探铝电解槽阴极内衬施工工艺改进

微探铝电解槽阴极内衬施工工艺改进发表时间:2017-09-04T15:07:53.063Z 来源:《防护工程》2017年第9期作者:于发强[导读] 本文将对铝电解槽内衬的易损部位进行分析与讨论,并提出相应的铝电解槽阴极内衬施工工艺改进策略。
新疆众和股份有限公司新疆 830013 摘要:近几年来我国的经济水平得到了飞速的提升,铝电解工业同样获得了快速的发展。
铝电解槽作为其中的核心设备,其性能的优劣会对生产指标产生重要影响。
综上所述,本文将对铝电解槽内衬的易损部位进行分析与讨论,并提出相应的铝电解槽阴极内衬施工工艺改进策略,以期提升施工质量,延长铝电解槽的使用寿命。
关键词:铝电解槽;阴极;内衬;施工工艺;改进策略前言冰晶石与氧化铝熔体作为铝电解槽的主要电解质,会将炭素材料作为两级。
在直流电通过阳极会导入至电解液与铝液层中,之后会通过阴极流出。
直流电通过电极的过程中,会产生一定的热量,同时还会将电解温度保持在900 -950 的范围内,使其中的冰晶石与氧化铝熔融题成为最终的离子状态,即电化学反应完成的表现形式,还会在阴极中以液态的形式将金属铝析出。
因此在施工过程中,不仅要将阴极砌体的电阻值充分考虑,还应强调砌体的密封性,从而起到将砌体抗侵蚀性增强的作用。
一、铝电解槽阴极内衬渗铝的问题分析导致铝液渗漏的原因较为复杂,由于铝电解槽阴极内衬的受损程度会对铝电解槽生产过程产生重要影响,因此在对其进行停产检修的过程中,发现其内衬的破损与槽底渗漏、铝液铁含量上升等多方面的因素有关。
而出现铝液渗透的主要部分为以下几点:第一,阴极窗口部分[1]。
其主要是由于阴极钢棒融化而造成的铝液渗透,之后从阴极的窗口中渗出。
第二,在阴极的炭块内部出现铝液渗透问题。
主要是由于阴极炭块组的开裂造成,使得阴极的炭块内部夹杂铝液现象出现。
第三,在侧部的炭块后方,该部分出现铝液渗透的主要原因为铝液经过没有严密密封的炭块缝隙中出现渗透。
第四,底糊内部。
铝电解槽内衬筑炉施工质量分析

铝电解槽内衬筑炉施工质量分析摘要:随着技术的不断更新近些年以来电解槽的寿命在逐渐延长,从2005年的1200-1500天的使用寿命提升到现在的2000天以上,电解槽寿命总体上在呈现出逐步上升的态势。
本文从铝电解槽内衬筑炉施工质量方面展开论述。
关键词:铝电解槽;内衬筑炉;施工质量引言:在铝电解生产运行的历程中,电解槽的寿命同电解生产发展有着非常密切的联系,在国内,电解槽300KA以上的槽型技术模式较为普遍,设计者在设计过程中做出了技术改进,生产企业在焙烧启动、后期的生产管理方面不但提升了自身的技术程度。
但是迄今为止电解槽的寿命问题严重地影响着电解铝的生产成本以及效率,铝电解槽内衬筑炉施工质量直接影响着铝电解槽的寿命,延长铝电解槽寿命是电解铝企业技术发展过程中的主要目标所在。
1、施工中存在的问题讨论1.1 阴极炭块的问题从以往破损的电解槽来看,阴极炭块质量偏差是致使电解槽破损的根本诱因,迄今为止在市场经济潮流的冲击之下,阴极炭块的生产商家数量诸多,质量也是良莠不齐。
有的生产厂家属于振动成型,有些生产厂家属于挤压成型,无论哪种类型,主要取决于阴极炭块在生产历程中的工艺技术控制。
本文特从若干台早期破损槽为例展开分析。
如图所示,阴极炭块的横向出现断裂、起层、局部裂纹等现象:图1 阴极炭块的横向断裂、起层、局部的裂纹现象上述可以说明厂家在产品出入库环节出现了问题,在这些环节没有进行严格的检查和鉴别,使质量不过关的产品流入施工现场;原材料在投入到使用过程之前,没有妥善保管,掺入了杂质,比如煤矸石等。
阴极炭块在生产的历程中存在杂质挥发或者高温爆裂的现象,致使阴极炭块空洞,由此导致的结果是电解槽从空洞处漏炉,如图2所示:图2 阴极炭块空洞现象除此之外,在配比的时候计量不准也可以引发上述现象,若是由于阴极炭块破损或裂缝导致铝液中的钠与炭块中的炭发生化学作用之后生成化合物,使炭晶格间的距离开始增大,炭块的体积随之膨胀,极其容易引发铝液和电解质液沿炭块的裂纹渗透,直到接触到阴极钢棒生成合金铝,在严重的时候可能引起漏炉。
[建筑]有关电解槽砌筑施工中几个问题的探讨
![[建筑]有关电解槽砌筑施工中几个问题的探讨](https://img.taocdn.com/s3/m/e55eed17aeaad1f347933f83.png)
有关电解槽砌筑施工中几个问题的探讨影响铝电解槽寿命的因素是多方面的。
本文仅就内衬砌筑质量进行探讨,以期将砌筑施工质量而影响寿命因素得以排除,给铝电解槽生产提供优质槽内衬。
一、炭块组制作据资料介绍,铝电解槽早期破损多为阴极钢棒被铝液融熔侵蚀,生成铝-铁合金。
按其受侵蚀情况分钢棒的底面和顶面侵蚀,底面受侵蚀是由于铝液从炭缝的缝隙中漏下所致;而顶面受侵蚀则是因漏下的铝液又顺炭块燕尾槽的裂缝渗入造成。
所以改进炭块组制作的连接方式,避免磷生铁浇注时产生的炭块裂纹,用炭糊连接的方法是行之有效的。
事实证明,同样是我们施工的##铝厂,一期的电解槽就要比二期的破损比例大得多,因为前者是磷生铁连接,后者是炭糊连接。
就目前来说,全国有的扩建厂仍沿用磷生铁连接的方法,加之老电解厂多为磷生铁连接,其槽大修也离不开这种方法,所以有必要研究这方面的工艺改进,以减少炭块的开裂。
炭块的裂纹一般都发生在燕尾槽的端角上,这是因为热应力容易在端角处集中。
即所谓"端角效应"。
磷生铁的浇注温度为1300℃左右,要想减少炭块的开裂倾向就应该对炭块和阴极钢棒进行预热。
有关资料介绍,预热温度为100~150℃〔见《筑炉工手册》681~683页〕。
对此,我们进行了试验,结果为炭块开裂率5%左右,如果能提高预热温度,势必可以减少炭块的开裂,当然预热温度不能一味提高,这样会使炭块过烧、氧化、损耗,相反会影响炭块组的使用寿命。
钢棒与炭块的导热系数不同〔钢为50千卡/平方米.时.度,炭块为0.2千卡/平方米.时.度,两者相差250倍〕,热膨胀系数也不同,当磷生铁水注入后,钢棒受热快、膨胀大,同样热量传给热膨胀系数小的炭块,将会造成炭块开裂。
所以在提高预热温度的前提下还应考虑造成钢棒和炭块的温度差。
在青铜峡铝厂5万吨电解铝工程的施工中,我们使用的阴极炭块是##铝厂生产的,阴极钢棒的材质是A3。
预热钢棒和炭块是一同在电加热箱里进行的,电阻丝根据钢棒和炭块的位置设置,靠近钢棒的电阻丝密集些、低垂些。
- 1、下载文档前请自行甄别文档内容的完整性,平台不提供额外的编辑、内容补充、找答案等附加服务。
- 2、"仅部分预览"的文档,不可在线预览部分如存在完整性等问题,可反馈申请退款(可完整预览的文档不适用该条件!)。
- 3、如文档侵犯您的权益,请联系客服反馈,我们会尽快为您处理(人工客服工作时间:9:00-18:30)。
铝电解槽内衬筑炉施工中的问题及改进策略
发表时间:2019-05-09T09:14:54.357Z 来源:《新材料.新装饰》2018年9月上作者:张剑林鹏程刘栋博
[导读] 在铝电解的生产中,电解槽寿命是制约电解生产发展的重要因素,虽然国内电解槽300KA以上的槽型发展比较快,设计院从设计方面做了很多的改进,生产企业从焙烧启动、后期的生产管理也在不断的提高,但电解槽的寿命问题是直接影响电解铝的生产成本和生产效率的核心,延长铝电解槽寿命是电解铝企业的一贯追求。
目前电解槽的寿命在不断提高,从
(江西科技学院土木工程学院)
摘要:在铝电解的生产中,电解槽寿命是制约电解生产发展的重要因素,虽然国内电解槽300KA以上的槽型发展比较快,设计院从设计方面做了很多的改进,生产企业从焙烧启动、后期的生产管理也在不断的提高,但电解槽的寿命问题是直接影响电解铝的生产成本和生产效率的核心,延长铝电解槽寿命是电解铝企业的一贯追求。
目前电解槽的寿命在不断提高,从2005年的1200-1500天的使用寿命提高到目前的2000天以上,电解槽槽寿命总体呈上升趋势,笔者从铝电解槽内衬筑炉施工质量进行分析探讨。
关键词:铝电解槽;破损原因;施工质量
引言:
文章主要对电解槽内衬质量的分析,找出了在内衬砌筑中的几个问题,并且按照找出问题采取了相应的措施,使电解槽的寿命有了明显的提高,有效遏制早期破损槽的发生,总之要提高铝电解槽的寿命,不仅从电解槽槽壳设计、碳素材料、施工质量等各环节做好,而且更重要的是从电解槽的焙烧启动及正常的生产管理进行严格控制。
1. 施工中容易出现的原因
1.1阴极炭块的问题
从早期破损的电解槽看,阴极炭块的质量是导致早期破损的直接原因,目前阴极炭块的生产厂家多,质量参差不齐。
其中有些生产厂家是振动成型,有些厂家是挤压成型,不管是挤压成型还是振动成型,关键在于阴极炭块在生产过程中的工艺控制,针对出现的几台早期破损槽的分析看,阴极炭块的横向断裂、起层、局部出现裂纹,说明生产厂家在产品出入库存在问题,没有严格检查,导致不合格的产品进入施工现场;原材料在使用前保管不好,掺入了杂质(煤矸石等),阴极炭块在生产过程中杂质挥发或高温爆裂,出现阴极炭块空洞,导致电解槽从空洞处漏炉,另外在配比过程中的计量不准也是造成上述现象的因素之一,如果阴极炭块破损或裂缝,导致铝液中的钠与炭块中的炭作用生成化合物,使炭晶格间的距离增大,使炭块的体积膨胀,很容易使铝液和电解质液沿炭块的裂纹渗透,至致接触到阴极钢棒生成合金铝,严重时导致漏炉。
1.2侧部炭块的问题
目前各铝企业中依据设计院设计不同而结构各不相同,有普通的碳素侧部块,有氮化硅结合碳化硅侧部复合块,有氮化硅结合碳化硅。
普通的碳素侧部块在运行到1000天左右时,氧化和侵蚀后几乎不复存在,主要是理化指标达不到要求,另外表面裂纹及龟裂导致普通的碳素侧部块快速氧化和侵蚀,造成早期破损。
氮化硅结合碳化硅侧块与普通碳素异型块组成的侧部复合块,是由生产厂家整体将氮化硅结合碳化硅侧块与碳素异型块粘结后供货,在施工过程中出现粘结强度达不到指标而分离,从而使两种炭块之间产生缝隙导致早期破损,另外普通的碳素侧部块表面裂纹及龟裂导致普通碳素侧部块快速氧化和侵蚀,启动初期伸腿以上的普通碳素侧块脱落,造成早期破损。
氮化硅结合碳化硅主要的问题是理化指标达不到标准,在运行到1000天以上是与电解质接触部位侵蚀严重,几乎二分之一以上的厚度已经侵蚀完。
1.3内衬材料的质量
铝电解槽内衬的阴极碳素材料质量直接影响着电解槽的使用寿命和电能消耗等,在日常的大修理中,由于使用的阴极碳素材料比较混杂而各自的理化指标也不尽相同,这就给电解槽的早期破损造成不利的因素,而阴极碳素材料在生产、采购等到方面都比较困难,迫使在电解槽的施工中采用几家的碳素材料,在实际操作中也很难达到阴极碳素材料一体化。
在生产中出现周围糊料、阴极炭块脱落和阴极炭块断裂等现象也时有发生,这就给电解槽的早期破损创造了条件。
2. 改进内衬砌筑
2.1阴极炭块的生产厂家的选择
针对阴极炭块比较杂又比较多的情况下,对阴极炭块的生产厂家进行实地考察,从各厂家的生产规模、生产工艺、原材料的进货渠道、阴极炭块的焙烧、炭块的加工等等了解,确定3-4家合格供应商,每次从这几家比价确定每批次的供应厂家,绝对不能选择贸易商供应阴极炭块,贸易商选择的阴极炭块厂家是以价格为目的,以次充好,炭块质量难以保证。
2.2电解槽阴极炭块的组装
针对阴极炭块的缺陷,首先是从源头把关,组装前检查是否有裂纹、缺棱、掉角等现象,其次是组装后的检查,通过比电阻测试仪和外观质量的检查,第三是在安装阴极炭块前进行检查,通过打音、表面观察等措施,确保阴极炭块的质量。
第四是用电子吊钩称对扎入的糊料量进行计量,确保每组阴极炭块扎入的糊料量不低于设计要求的重量,第五是阴极炭块的外观尺寸一定要规范,目前的阴极炭块的尺寸偏差大,尽可能的将尺寸偏差相近的安装在一起。
另外阴极炭块在阴极炭块的两长侧和两短侧都开槽,防止侧部和立缝渗漏,从筑炉内衬工艺上消除缺陷。
杜绝有缺陷炭块组进入电解槽中,保证了安装到电解槽中的每一块阴极炭块组的质量。
2.3改进筑炉施工工艺
从进入电解槽内衬砌炉开始,先划出每层的高度控制线和伸缩缝的控制线,改变以往的随意性砌筑,这样不但操作时方便,更主要是能保证纵横伸缩缝的位置和高度控制线,达到规范操作的目的。
在电解槽四周的砌筑时,严格控制各层的灰缝,在钢棒孔和耐火砖的空隙中用氧化铝填满填实不能留有空隙,保证在铝液、电解质渗漏时无渗漏空间,从源头堵住渗漏,防止从钢棒孔中漏炉发生。
另外在扎固工艺时,首先控制好糊料的温度和加热搅拌。
在几年前曾经出现每批中的糊料不一样,其中有的糊料油份较大有些糊料油份较小,而且骨料也不一样,这样在扎固时就会出现油份较大的温度高,油份较小的温度低,同时油份大的容易出现返桨现象,油份小的出现扎不在一起的现象,所以为避免糊料温度不均匀,在扎固前一天将糊料放入预热炉,按规定进行预热,同时为避免生产厂家每批或每锅的配比不均匀性,将糊料二次进入混捏锅进行搅拌,待搅拌均匀后运到施工现场,力求糊料达到均衡。
其次在扎固时对各区域进行划分,划分的目的就是各捣固机手在扎自己的区域外同时还要延伸200mm到两边区域进行扎固,这样避免在接搓处的漏扎现象,保证整体的扎固效果[1]。
2.4严格控制内衬材料质量
电解槽的内衬材料是延长槽寿命的关键因素之一,而阴极碳素材料最为关键,它是在高温和熔盐强烈侵蚀的环境下工作的,所以碳素材料质量好坏直接影响到电解槽的寿命。
在每台槽中应尽量使用同一厂家的碳素材料,尽可能达到电解槽内衬素材料一体化。
严格控制内衬碳素材料的理化指标,对超标的材料禁止使用,防止由于内衬碳素材料而引起的早期破损。
另外阴极内衬材料在运输中和保管时必须符合技术要求,严禁日晒雨淋、强烈震动和受潮。
2.5改善扎槽的设备和工器具
为了杜绝扎固进程中使用墙壁风源的问题,保证扎固中风压的稳定性,用自备空压机进行供风,满足了扎固工艺要求,达到了预期目标,从而保证扎固中糊料的温度。
另外还对缺棱、角的捣固锤及时进行更换和加工,保证扎固过程中各个角落的扎固质量,为整体扎固质量提供保障,避免由于扎固质量而造成的早期破损。
为防止扎固糊出现分层现象,改进扎固工具,采用梅花锤捣固使周围糊层间紧密衔接,有效解决原工艺糊料层间拉毛不好及层间结合差的现象,扎固和拉毛过程一次完成,有利于提高了电解槽的扎固质量。
结论:
简而言之,本文从电解槽内衬施工中容易出现的原因进行分析,结合容易出现的原因提出了施工质量改进的措施,槽寿命有了明显的提高[2]。
参考文献
[1]邱竹贤.预焙槽炼铝(第3版)[M].北京:冶金工业出版社,2015.
[2]何允平,董民杰.铝电槽寿命的研究[M].沈阳:东北工学院出版社。
2018.。