无损检测技术对比研究
锂电池安全性能无损检测技术研究进展

节能环保的新能源汽车是汽车行业发展的一个方向,也是我国的未来发展战略,电池作为新能源汽车的储能元件和供电电源,在新能源汽车上具有核心作用。
锂电池由于具有能量密度大、自放电率低、循环寿命长等优点,在新能源汽车领域得到了广泛应用。
但受应用环境、电池材料和生产工艺等不够完善等因素影响,电池组会出现能量效率降低、寿命缩短、电动汽车的续驶里程减小等问题,甚至导致燃烧、爆炸事故的发生,存在安全隐患。
NO.1锂电池安全隐患分析锂离子电池一般由正极、负极、正极引线、负极引线、中心管子、隔膜、电解质和电池外壳等组成。
电池正极为金属氧化物、掺杂化合物等,电池负极为碳素材料,电池电解液由无机锂盐和有机溶剂组成。
锂电池属于二次电池,通过锂离子在正负极之间的移动实现电池的充放电。
锂电池工作原理示意如图1所示。
图1 锂电池工作原理示意锂电池分为柱形锂电池与方形锂电池,又根据电池外包材料的不同分为铝壳锂电池、钢壳锂电池和软包锂电池。
近几年国内外锂电池的安全事故、召回数据表明,锂离子电池的安全事故主要表现为过热、燃烧和爆炸。
锂离子电池发生安全事故的主要原因是热积聚或热失控,表现为无法正常、及时散热或压力局部突增,进而导致电池失控,引起起火、爆炸等事故,一定程度上会威胁人身安全。
内部材料、制造工艺、非正常使用、使用疲劳等因素均有可能导致电池发生故障。
锂电池的生产包含极片制作、电芯组装、后处理等多个复杂工序,在生产过程中,可能出现划痕、颗粒、边缘破损、极片穿孔等十几种缺陷,因此,在出厂使用前,需要对锂电池进行缺陷检测,评估其安全性能。
笔者将锂电池存在的缺陷分为表面缺陷、电极缺陷以及内部缺陷三部分进行阐述,分别介绍其缺陷种类及其相应的检测方法。
NO.2锂电池安全性能检测方法01表面缺陷检测锂电池的表面缺陷主要是由原材料本身受损或仅生产线上受到误碰产生的,其主要表现为划痕、褶皱、鼓包、凹痕、凹坑、针眼、露铝、脏污等,其中针眼、露铝等严重缺陷会影响电池的安全性能。
CT无损检测:金标准

CT无损检测:金标准CT无损检测,即计算机断层扫描无损检测,是一种先进的检测技术,广泛应用于多个领域。
本文将深入探讨CT无损检测在金标准方面的表现,主要包括检测精度、检测范围、图像分辨率、安全性、检测速度、检测成本、可重复性和适用性等方面。
一、检测精度CT无损检测具有极高的检测精度,能够准确识别出微小的缺陷和异常。
通过高分辨率的图像,可以清晰地呈现出物体的内部结构和细节,为精确诊断提供有力支持。
二、检测范围CT无损检测的检测范围广泛,适用于各种材料和部件的检测。
无论是金属、非金属,还是复合材料,CT无损检测都能提供准确的检测结果。
三、图像分辨率CT无损检测的图像分辨率极高,能够呈现出物体的详细结构和特征。
高分辨率的图像有助于更准确地识别缺陷和异常,提高检测的准确性。
四、安全性CT无损检测是一种非侵入性的检测方法,不会对被检测物体造成损伤或破坏。
在检测过程中,无需进行任何破坏性试验,从而确保了被检测物体的完整性和安全性。
五、检测速度随着技术的不断进步,CT无损检测的检测速度得到了显著提升。
高速扫描和数据处理能力使得CT无损检测能够快速完成大面积或复杂结构的检测,提高了检测效率。
六、检测成本虽然CT无损检测设备的购置和维护成本相对较高,但其高精度、高效率和广泛的适用性使得总体检测成本相对较低。
此外,CT无损检测避免了因破坏性试验导致的额外成本和浪费。
七、可重复性CT无损检测的结果具有高度的可重复性,确保了检测的准确性和可靠性。
相同条件下,同一物体进行多次检测的结果一致性较好,为产品质量控制和失效分析提供了有力支持。
八、适用性由于其独特的优势,CT无损检测在许多领域都具有广泛的适用性。
例如,在航空航天、汽车制造、电子设备、医疗诊断等领域,CT无损检测已成为不可或缺的检测手段。
总之,CT无损检测在金标准方面表现出色,具有高精度、广范围、高分辨率、高安全性、高效率、低成本、高可重复性和广泛应用领域等优点。
常用风力发电机组叶片无损检测技术对比分析
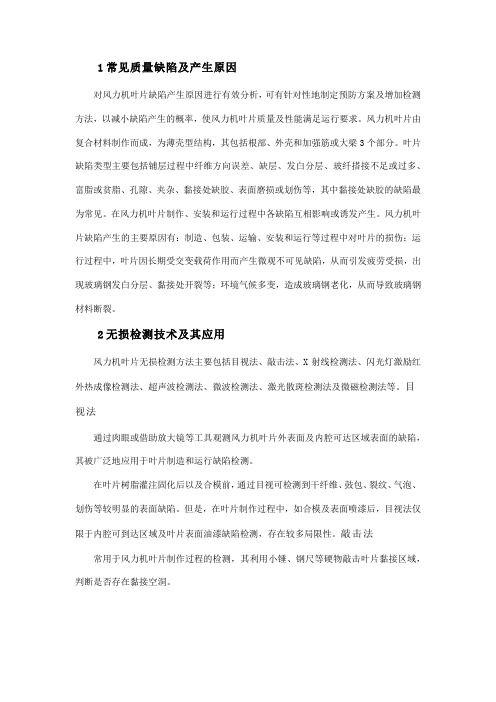
1常见质量缺陷及产生原因对风力机叶片缺陷产生原因进行有效分析,可有针对性地制定预防方案及增加检测方法,以减小缺陷产生的概率,使风力机叶片质量及性能满足运行要求。
风力机叶片由复合材料制作而成,为薄壳型结构,其包括根部、外壳和加强筋或大梁3个部分。
叶片缺陷类型主要包括铺层过程中纤维方向误差、缺层、发白分层、玻纤搭接不足或过多、富脂或贫脂、孔隙、夹杂、黏接处缺胶、表面磨损或划伤等,其中黏接处缺胶的缺陷最为常见。
在风力机叶片制作、安装和运行过程中各缺陷互相影响或诱发产生。
风力机叶片缺陷产生的主要原因有:制造、包装、运输、安装和运行等过程中对叶片的损伤;运行过程中,叶片因长期受交变载荷作用而产生微观不可见缺陷,从而引发疲劳受损,出现玻璃钢发白分层、黏接处开裂等;环境气候多变,造成玻璃钢老化,从而导致玻璃钢材料断裂。
2无损检测技术及其应用风力机叶片无损检测方法主要包括目视法、敲击法、X射线检测法、闪光灯激励红外热成像检测法、超声波检测法、微波检测法、激光散斑检测法及微磁检测法等。
目视法通过肉眼或借助放大镜等工具观测风力机叶片外表面及内腔可达区域表面的缺陷,其被广泛地应用于叶片制造和运行缺陷检测。
在叶片树脂灌注固化后以及合模前,通过目视可检测到干纤维、鼓包、裂纹、气泡、划伤等较明显的表面缺陷。
但是,在叶片制作过程中,如合模及表面喷漆后,目视法仅限于内腔可到达区域及叶片表面油漆缺陷检测,存在较多局限性。
敲击法常用于风力机叶片制作过程的检测,其利用小锤、钢尺等硬物敲击叶片黏接区域,判断是否存在黏接空洞。
但是,当声音无明显差别时,会造成缺陷无法判定或漏判。
该检测法仅对检测较大的缺胶缺陷有效,由于在敲击过程中有可能造成叶片表面微观损伤,因此对环境及检测经验要求较高。
X射线检测法X射线检测法为射线实时成像检测(RTR)技术,在复合材料检测领域得到了广泛应用,其检测原理如图1所示。
X射线检测技术可用于检测缺胶空洞、夹杂、垂直于玻璃钢表面的裂纹、富脂、部分褶皱等风力机叶片常见缺陷,在判断叶片缺胶空洞及夹杂等体积型缺陷方面优势明显。
复合材料结构件无损检测技术分析

复合材料结构件⽆损检测技术分析复合材料结构件⽆损检测技术分析摘要:本⽂通过对复合材料结构件缺陷和损伤特点的分析,介绍可应⽤于复合材料结构缺陷包括⽬视检查法、声阻法、射线检测技术、超声检测技术、声- 超声技术、涡流检测技术、微波检测技术在内的⽆损检测技术。
并对⽆损检测技术的技术关键进⾏剖析,展望了⽆损检测技术的未来发展。
关键词:复合材料⽆损检测缺陷随着航空制造技术的不断发展,复合材料以其⾼的⽐强度、⽐刚度及良好的抗疲劳性和耐腐蚀性获得⼴泛应⽤。
由于纤维增强复合材料具有导电性差、热导率低、声衰减⾼的特点,在物理性能⽅⾯呈显著的各向异性,使得它对波传播所引起的作⽤与普通⾦属材料相⽐具有很⼤的差异,因⽽其⽆损检测技术与⾦属的检测⼤不相同,复合材料检测⽇益成为该领域的重点和难点。
在这种情况下,航空航天检测迫切需要有⼀种更有效的⼿段来提⾼复合材料构件的⽣产质量或修理⽔平。
复合材料构件的成型过程是极其复杂的,其间既有化学反应,⼜有物理变化,影响性能的因素甚多,许多⼯艺参数的微⼩差异会导致其产⽣诸多缺陷,使产品质量呈现明显的离散性,这些缺陷严重影响构件的机械性能和完整性。
由于复合材料结构制造质量的离散性,必须通过⽆损检测来鉴别产品的内部质量状况,以确保产品质量,满⾜设计和使⽤要求。
随着先进复合材料技术研究与应⽤的⾼速增长,复合材料⽆损检测技术也迅速发展起来,已成为新材料结构能否有效和扩⼤应⽤的关键。
⼀、复合材料结构件缺陷的产⽣与特点先进复合材料中的缺陷类型⼀般包括: 孔隙、夹杂、裂纹、疏松、纤维分层与断裂、纤维与基体界⾯开裂、纤维卷曲、富胶或贫胶、纤维体积百分⽐超差、铺层或纤维⽅向误差、缺层、铺层搭接过多、厚度偏离、磨损、划伤等, 其中孔隙、分层与夹杂是最主要的缺陷。
材料中的缺陷可能只是⼀种类型, 也可能是好⼏种类型的缺陷同时存在。
缺陷产⽣的原因是多种多样的, 有环境控制⽅⾯的原因, 有制造⼯艺⽅⾯的原因, 也有运输、操作以及使⽤不当的原因, 如外⼒冲击、与其他物体碰撞和刮擦等。
复合材料无损检测方法
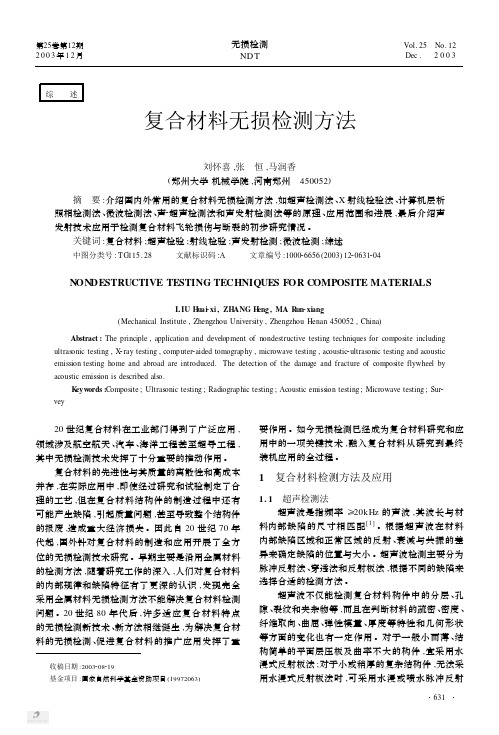
AU 技术的基本原理为 ,采用压电换能器或激 光照射等手段在材料 (复合材料或各向同性材料) 表 面激发脉冲应力波 ,应力波在内部与材料的微结构 (包括纤维增强层合板中的纤维基体 ,各种内在的或 外部环境作用产生的缺陷和损伤区) 相互作用 ,并经 过界面的多次反射与波型转换后到达置于结构同一 或另一表面的接收传感器 (压电传感器或激光干涉 仪) ,然后对接收到的波形信号进行分析 ,提取一个 能反映材料 (结构) 力学性能 (强度和刚度) 的参量 , 称为应力波因子 。
声2超声 (Acoustic2Ultrasonic ,简称 AU) 技术又 称应力波因子 ( Stress Wave Factor , 简称 SWF) 技 术 。与通常的无损检测方法不同 ,AU 技术主要用 于检测和研究材料中分布的细微缺陷群及其对结构 力学性能 (强度或刚度) 的整体影响 ,属于材料完整 性评估技术[9 ,10 ] 。
钢结构桥梁焊接无损检测技术的应用及发展研究
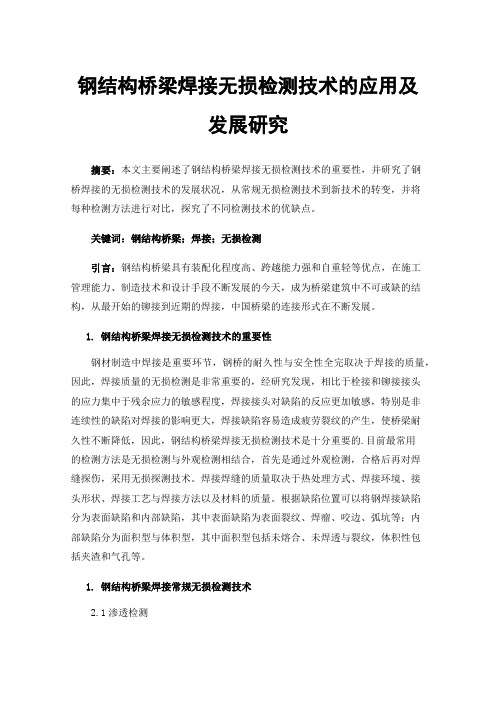
钢结构桥梁焊接无损检测技术的应用及发展研究摘要:本文主要阐述了钢结构桥梁焊接无损检测技术的重要性,并研究了钢桥焊接的无损检测技术的发展状况,从常规无损检测技术到新技术的转变,并将每种检测方法进行对比,探究了不同检测技术的优缺点。
关键词:钢结构桥梁;焊接;无损检测引言:钢结构桥梁具有装配化程度高、跨越能力强和自重轻等优点,在施工管理能力、制造技术和设计手段不断发展的今天,成为桥梁建筑中不可或缺的结构,从最开始的铆接到近期的焊接,中国桥梁的连接形式在不断发展。
1.钢结构桥梁焊接无损检测技术的重要性钢材制造中焊接是重要环节,钢桥的耐久性与安全性全完取决于焊接的质量,因此,焊接质量的无损检测是非常重要的,经研究发现,相比于栓接和铆接接头的应力集中于残余应力的敏感程度,焊接接头对缺陷的反应更加敏感,特别是非连续性的缺陷对焊接的影响更大,焊接缺陷容易造成疲劳裂纹的产生,使桥梁耐久性不断降低,因此,钢结构桥梁焊接无损检测技术是十分重要的.目前最常用的检测方法是无损检测与外观检测相结合,首先是通过外观检测,合格后再对焊缝探伤,采用无损探测技术。
焊接焊缝的质量取决于热处理方式、焊接环境、接头形状、焊接工艺与焊接方法以及材料的质量。
根据缺陷位置可以将钢焊接缺陷分为表面缺陷和内部缺陷,其中表面缺陷为表面裂纹、焊瘤、咬边、弧坑等;内部缺陷分为面积型与体积型,其中面积型包括未熔合、未焊透与裂纹,体积性包括夹渣和气孔等。
1.钢结构桥梁焊接常规无损检测技术2.1渗透检测渗透检测法需要先涂抹在构件表面一层着色剂,在毛细作用下,在一段时间后,着色剂会进入构件的开口缺陷中,接下来可以清洗掉着色剂,在构件干燥后再涂抹显像剂,显像剂会吸收剩余的着色剂,使裂痕处于明显状态中,根据着色剂的痕迹可以直观的发现焊缝缺陷的形状和位置。
渗透检测的方法优点是对检测的钢结构没有在尺寸和形状上具有较高的要求,对于开口型的构件缺陷能够被清晰的反映出来,但是渗透检测方法的缺点是检测的速度很慢,检测效果需要等待一段时间才可以显示效果,同时对于闭口型的裂纹和焊缝内部的气孔,这种检测方法是很难发现的,并且检测试剂不具有环保特征,对自然界存在一定的污染,灵敏度没有磁粉检测高。
(完整版)无损检测技术及其应用
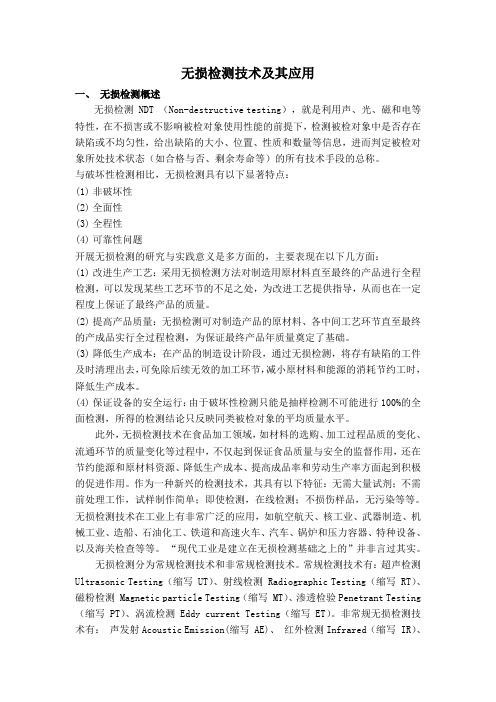
无损检测技术及其应用一、无损检测概述无损检测 NDT (Non-destructive testing),就是利用声、光、磁和电等特性,在不损害或不影响被检对象使用性能的前提下,检测被检对象中是否存在缺陷或不均匀性,给出缺陷的大小、位置、性质和数量等信息,进而判定被检对象所处技术状态(如合格与否、剩余寿命等)的所有技术手段的总称。
与破坏性检测相比,无损检测具有以下显著特点:(1) 非破坏性(2) 全面性(3) 全程性(4) 可靠性问题开展无损检测的研究与实践意义是多方面的,主要表现在以下几方面:(1) 改进生产工艺:采用无损检测方法对制造用原材料直至最终的产品进行全程检测,可以发现某些工艺环节的不足之处,为改进工艺提供指导,从而也在一定程度上保证了最终产品的质量。
(2) 提高产品质量:无损检测可对制造产品的原材料、各中间工艺环节直至最终的产成品实行全过程检测,为保证最终产品年质量奠定了基础。
(3) 降低生产成本:在产品的制造设计阶段,通过无损检测,将存有缺陷的工件及时清理出去,可免除后续无效的加工环节,减小原材料和能源的消耗节约工时,降低生产成本。
(4) 保证设备的安全运行:由于破坏性检测只能是抽样检测不可能进行100%的全面检测,所得的检测结论只反映同类被检对象的平均质量水平。
此外,无损检测技术在食品加工领域,如材料的选购、加工过程品质的变化、流通环节的质量变化等过程中,不仅起到保证食品质量与安全的监督作用,还在节约能源和原材料资源、降低生产成本、提高成品率和劳动生产率方面起到积极的促进作用。
作为一种新兴的检测技术,其具有以下特征:无需大量试剂;不需前处理工作,试样制作简单;即使检测,在线检测;不损伤样品,无污染等等。
无损检测技术在工业上有非常广泛的应用,如航空航天、核工业、武器制造、机械工业、造船、石油化工、铁道和高速火车、汽车、锅炉和压力容器、特种设备、以及海关检查等等。
“现代工业是建立在无损检测基础之上的”并非言过其实。
超高性能混凝土配合比及无损检测技术的研究肖研

超高性能混凝土配合比及无损检测技术的研究肖研发布时间:2022-10-23T13:07:23.346Z 来源:《建筑模拟》2022年第13期作者:肖研[导读] 本文主要对超高性能混凝土配合比及无损检测技术展开研究,介绍了超高性能混凝土性能特点,讨论了超高性能混凝土的无损检测方法,进行了超高性能混凝土配合比试验分析,主要针对混凝土配合比展开正交试验,确定影响因素及考核指标,最后进行极差分析确定最佳配合比,按照相应配合比进行混凝土试块生产,以超声回弹法进行无损检测,结果均符合要求。
广东省有色工业建筑质量检测站有限公司广东广州 510725摘要:本文主要对超高性能混凝土配合比及无损检测技术展开研究,介绍了超高性能混凝土性能特点,讨论了超高性能混凝土的无损检测方法,进行了超高性能混凝土配合比试验分析,主要针对混凝土配合比展开正交试验,确定影响因素及考核指标,最后进行极差分析确定最佳配合比,按照相应配合比进行混凝土试块生产,以超声回弹法进行无损检测,结果均符合要求。
关键词:超高性能混凝土;配合比;无损检测技术超高性能混凝土具有抗震性好、稳定性高、流动性强等优势,目前在深海钻井平台、桥梁、污水管道、高层建筑等工程当中都有广泛应用。
超高性能混凝土的无损检测方法主要有回弹法、超声法、超声波回弹综合法以及拔出法等。
本文还着重对超高性能混凝土配合比展开试验分析,运用正交试验法,通过极差分析最终确定最佳配合比。
1.超高性能混凝土性能特点1.1抗渗性特点超高性能混凝土具有良好的抗渗性情况下,可有效抵御外界因素影响,使混凝土结构具有更强的耐久性。
而若超高性能混凝土不具备良好的抗渗性,就会使混凝土结构容易受到水的侵蚀,从而影响结构稳定性以及完整性,通常会在设计使用年限之内发生质量缺陷。
1.2强度特征超高性能混凝土其强度高低主要取决于水泥使用情况,水泥用量越多,超高性能混凝土就会有越高强度,但是要注意水泥用量也不能过多,以免因过量使用水泥而增加水化热影响,使混凝土结构内部的温度出现异常升高情况,增加内外温差,进而更容易引发裂缝[1]。
红外无损检测的数值模拟及其对比性研究
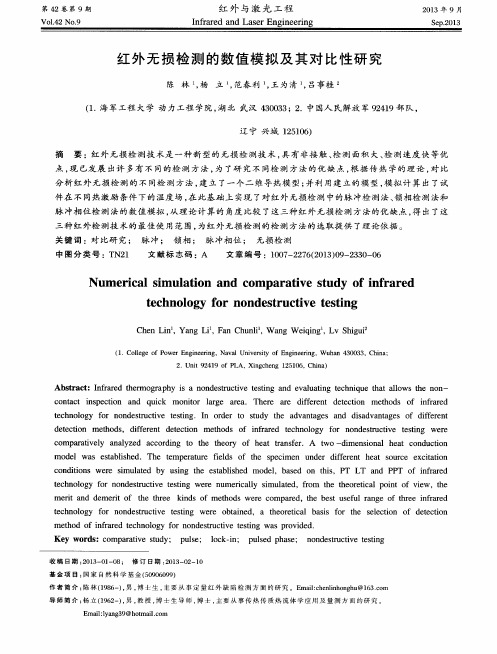
第4 2卷 第 9期
VO1 . 42 N O. 9
红 外 与 激 光 工 程
I n f r a r e d a n d La s e r En g i n e e r i n g
2 01 3年 9 月
Se p. 2 01 3
红 外 无 损 检 测 的 数 值 模 拟 及 其 对 比 性 研 究
Байду номын сангаас关 键词 :对 比研 究 ; 脉冲; 锁相 ; 脉 冲相 位 ; 无损 检测
中 图 分 类 号 :T N2 1 文 献 标 志 码 :A 文 章 编 号 :1 0 0 7 — 2 2 7 6 ( 2 0 1 3 ) 0 9 — 2 3 3 0 — 0 6
Num e r i c a l s i mu l a t i o n a nd c o mp a r a t i v e s t ud y o f i n f r a r e d t e c h n o l o g y f o r n o n d e s t r u c t i v e t e s t i ng
d e t e c t i o n me ho t ds ,d i f f e r e n t d e t e c t i o n me t ho d s o f i n f r re a d t e c h no l o g y f or n o n d e s t r u c iv t e t e s t i n g we r e c o mp ra a t i v e l y a n a l y z e d a c c o r d i n g t o t he t h e o r y o f h e a t t r a n s f e r . A t wo — di me n s i o n l h a e a t c o n d u c t i o n mo d e l w a s e s t a b l i s h e d. Th e t e mp e r a t u r e f ie l d s o f t h e s p e c i me n u n d e r d i f f e r e n t h e a t s ou r c e e x c i t a t i o n
航空装备检测

浅析中美航空装备无损检测技术摘要:本文主要介绍了我国当前航空装备无损检测技术研究的现状以及主要成就,并介绍了美国在装备无损检测技术方面的应用及其主要的检测技术方法,并通过对比提出一些装备无损检测技术的发展方向。
关键字:航空装备、无损检测、美国延长包括飞机在内的航空装备的安全使用期是现代航空装备的发展趋势。
无损检测(NDT)或无损评价(NDE)技术在航空装备的全寿命过程中起着极其重要的作用,它对保证飞行安全、延长飞机寿命都具有非常重要的意义。
随着在航空技术中采用损伤容限理论替代过去的安全寿命设计理论,无损检测技术在航空装备中的应用观点也发生了根本性的变化,这就是无损检测技术应当对装备的全寿命(从摇篮到坟墓)负责,它不但应当能(实现传统意义下的)检测出已经存在的缺陷或裂纹,还应当能对裂纹发展规律进行预测,以保证损伤容限理论的正确实施。
无损检测技术是一项典型的具有低投入、高产出特点的工程应用技术。
我们很难找到其他任何一个应用学科分支,其涵盖的技术知识之渊博、覆盖的基本研究领域之众多、所涉及的应用领域之广泛能与无损检测相比。
1982年10月,时任美国总统的里根在发给美国无损检测学会(ASNT) 成立20周年的贺电中曾说过,(无损检测)能给飞机和空间飞行器、发电厂、船舶、汽车和建筑物等带来更大程度的可靠性,没有无损检测(美国)就不可能享有目前在飞机、船舶和汽车等众多领域和其他领域的领先地位。
作为一门应用性极强的技术,只有与国家大型工程项目结合,解决国家大型和重点工程项目中急需解决的安全保障问题,无损检测技术才能有用武之地和广阔的发展空间。
航空装备的无损检测涉及面很广,它包括航空材料的检测、航空结构件制造过程的检测和在役设备(飞机)的检测等,虽然都属无损检测,但其检测重点和涵盖的领域有着很大差别。
本文在论及航空装备无损检测技术的时候,重点将放在在役装备的检测上。
一、我国航空装备无损检测工作现状我国航空领域的无损检测总体上位列世界先进水平,其研究和技术人员能自行解决和攻克航空领域面临的各类复杂的技术疑难问题。
无损检测实验报告

无损检测实验报告无损检测实验报告导言:无损检测是一种广泛应用于工程领域的技术,通过对材料和结构的检测,能够发现内部缺陷、裂纹以及其他潜在问题,而无需破坏性地对其进行测试。
本实验旨在探究无损检测技术在实际应用中的可行性和效果。
一、背景介绍无损检测技术是一种非破坏性的测试方法,广泛应用于航空航天、汽车制造、建筑工程等领域。
其原理是通过对材料的电磁、超声、磁粉等特性进行测试,从而判断材料的质量和完整性。
相比传统的破坏性检测方法,无损检测具有速度快、成本低、对材料无损伤等优点。
二、实验目的本实验旨在通过无损检测技术对不同材料进行测试,验证其可行性和准确性。
同时,通过对比不同无损检测方法的结果,探讨其适用范围和优缺点。
三、实验方法本实验选取了金属材料和混凝土材料进行测试。
对于金属材料,采用超声波检测和磁粉检测两种方法进行测试;对于混凝土材料,采用雷达检测和红外热像仪检测两种方法进行测试。
1. 超声波检测超声波检测是一种通过声波在材料中传播的原理进行测试的方法。
实验中,利用超声波探头对金属材料进行扫描,通过接收到的回波信号判断材料内部是否存在缺陷。
2. 磁粉检测磁粉检测是一种通过磁场在材料表面形成磁粉堆积的方法进行测试。
实验中,将磁粉涂覆在金属材料表面,通过观察磁粉在材料表面的分布情况,判断材料是否存在裂纹或缺陷。
3. 雷达检测雷达检测是一种利用电磁波在材料中传播的原理进行测试的方法。
实验中,将雷达探头对混凝土材料进行扫描,通过接收到的回波信号判断材料内部是否存在空洞或裂缝。
4. 红外热像仪检测红外热像仪检测是一种通过检测材料表面的热辐射进行测试的方法。
实验中,将红外热像仪对混凝土材料进行扫描,通过观察热像仪显示的图像,判断材料是否存在温度异常或结构问题。
四、实验结果与分析通过对金属材料和混凝土材料进行不同无损检测方法的测试,得到了以下结果:1. 超声波检测超声波检测在金属材料的缺陷检测中表现出较高的准确性和可靠性。
焊缝检测的国内外标准对比分析总结的真好

焊缝检测的国内外标准对比分析,总结的真好1. 概述对于日常工件的无损检测而言,标准是最重要的工作依据。
从工件的检测方法选择、检测过程的注意事项,到工件的最终评定、报告的参数出具,往往都需要遵循一定的、供需双方均认可的标准规范。
随着国际合作的不断加强,我们和国外的交流也日益广泛。
其中,涉及到产品质量验收时,应该遵循何种标准、采取怎样的验收级别,这往往是供需双方讨论的焦点之一。
因此,将国内焊接构件焊缝无损检测标准和国外、国际标准进行一定的对比,分析其在日常生活中的应用,对于我们的工作,也是非常有好处的。
2. 国内、外焊缝无损检测标准钢结构焊缝的无损检测在国内已有成熟标准,以锅炉压力容器部门运用最为广泛,如GB/T11345,NB/T47013、GB/T3323和TB/T1558等。
近来铝合金轻量化材料的使用,使铝合金焊接结构的探伤检验也变得越来越重要,由于国内起步较晚,实用标准还不是很多。
随着航空航天和高铁技术的发展,铝合金焊接结构件越来越多。
如高速动车组全部采用铝合金车体,大量使用预制型材、板材以焊接方式连接,如法国阿尔斯通的全铝焊接车体,德国克诺尔的铝合金焊接风缸等,由于国内尚无成熟检验标准,不得不按外方要求采用国际标准进行检验,因此关于铝合金焊接结构件的无损检测标准的研究正在开展之中。
国内外关于焊接结构件的无损检测主要有下列所示标准:o GB/T 14693 焊缝无损检测符号o GB/T 3323金属熔化焊焊接接头射线照相o GB/T 12605钢管环缝熔化焊对接接头射线透照工艺和质量分级o GB/T 11345钢焊缝手工超声波探伤方法和探伤结果的分级o GB/T 15830钢制管道对接环焊缝超声波探伤方法和检验结果的分级o JB/T 9212常压钢质油罐焊缝超声波探伤o JB/T 6061焊缝磁粉检验方法和缺陷磁痕的分级o JB/T 6062焊缝渗透检验方法和缺陷磁痕的分级o NB/T 47013承压设备无损检测o TB/T 1558对接焊缝超声波探伤o ISO 5817焊缝钢、镍、钛及各自合金熔化焊接头(除波束焊外)不完整性质量分级o ISO 10042焊缝铝及其合金弧焊接头不完整性质量分级o ISO 17636-1焊缝无损检测射线检测 X和伽马射线胶片技术o ISO 17636-2焊缝无损检测射线检测 X和伽马射线电子成像技术o ISO 10675-1焊缝的无损检测第1部分钢、镍、钛及其合金制品射线检测的评价可接受水平o ISO 10675-2焊缝的无损检测第2部分铝合金制品射线检测的评价可接受水平o ISO 17640焊缝无损检测超声波检测检测技术、验收等级和结果评估o ISO 11666焊缝无损检测焊接接头超声波检测验收等级o ISO 17638焊接无损检测焊接接头磁粉检测o ISO 23278焊缝的无损检测焊接接头磁粉检测验收等级o ISO 3452无损检测渗透检测o ISO 23277焊缝无损检测焊缝渗透检测验收等级o JIS Z3105铝焊缝的射线照相检验方法和底片评级方法o JIS Z3080铝焊缝超声波斜角探伤方法及检验结果的等级分类方法o JIS Z3081铝管焊缝超声波斜角探伤方法及检验结果的等级分类方法o ASTM E1032焊接件的射线透照检测方法o ASTM E390钢熔化焊射线检验标准底片o ASTM E1648用于铝熔焊检验的射线照相参考底片3.国内、外焊缝检验标准对比分析由于ASTM标准中关于焊缝检验需要采用相应的图谱进行比对,这种方式对于要求较高的焊缝而言,相对难以评判,因此国内若无特殊需求一般很少采用。
风电机组叶片无损检测技术研究与进展

风电机组叶片无损检测技术研究与进展风电机组叶片在运行时除了承受气动力作用外,还承受重力、离心力等其他力的影响,再加上雨雪、沙尘、盐雾侵蚀、雷击等破坏,使叶片基体及表面容易受到损伤,这些损伤如未及时发现与维修会导致风电机组发电效率下降、停机,甚至发生损毁等事故。
因此,风电机组叶片损伤检测对保障风电机组安全高效运行、降低风电机组寿命周期内发电成本有重大意义。
01风电叶片主要缺陷、损伤类型及损伤原因风电叶片是复合材料设计制作的特殊结构,其内部结构如图1所示。
其损伤主要原因有:1)疲劳损伤。
风力发电机在长期运行中,由于疲劳作用叶片会出现微小裂缝、裂纹和缺陷等,最终导致叶片的断裂或失效。
2)延迟失效。
当叶片被暴露在恶劣环境下,比如高温、低温、潮湿或强风等条件下,其寿命会显著降低,可能会导致延迟失效。
3)冲击损伤。
当叶片受到外部冲击或碰撞时,容易出现破裂、裂纹和断裂等问题。
4)腐蚀损伤。
当叶片表面受到化学物质、海水或大气污染等因素的侵蚀时,会出现腐蚀损伤,导致叶片性能下降或失效。
5)材料老化。
随着使用时间的增加,叶片材料的力学性能逐渐下降,这可能会导致叶片的失效。
图1图1 风电叶片内部结构示意风电叶片局部损伤风电叶片的局部损伤通常指在使用过程中,叶片某些区域出现了裂纹、划痕、腐蚀等问题。
这些损伤可能会影响叶片的性能和可靠性,甚至危及风力发电系统的安全。
1叶片表面裂纹叶片运行进入中期后,叶片表面受疲劳载荷作用容易产生裂纹,尤其是前缘处受拉伸载荷的影响容易产生横向疲劳裂纹(裂纹沿叶展方向为纵向裂纹,垂直于叶展方向为横向裂纹)。
叶片表面裂纹产生的原因有:1)涂层本身耐候性(耐紫外、风沙、雨蚀等)不满足设计要求,整体出现龟裂等;2)涂层底部的复合材料部分存在缺陷,导致叶片运行过程中出现应力集中,裂纹在涂层面上表现出来,如图2和图3所示。
图2 叶片表面横向裂纹图3 叶片表面纵向裂纹2叶片表面或内部分层如果叶片生产制造过程中存在一些区域粘接不良,在长期交变载荷的作用下,叶片表面、前后缘、主梁、腹板等部分可能会发生分层,如图4和图5所示。
荧光粉探伤配比标准
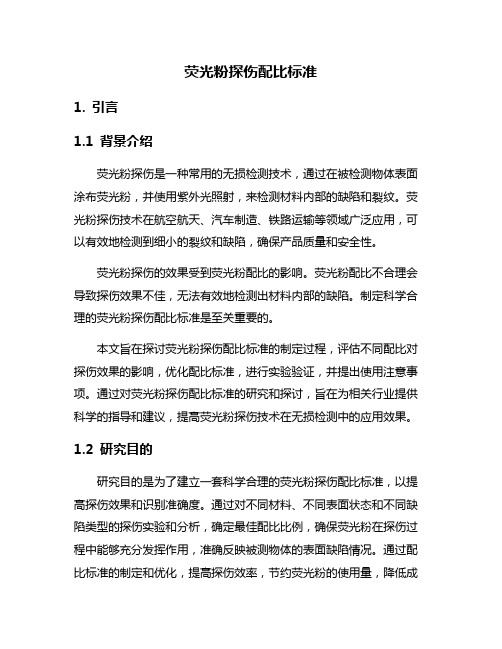
荧光粉探伤配比标准1. 引言1.1 背景介绍荧光粉探伤是一种常用的无损检测技术,通过在被检测物体表面涂布荧光粉,并使用紫外光照射,来检测材料内部的缺陷和裂纹。
荧光粉探伤技术在航空航天、汽车制造、铁路运输等领域广泛应用,可以有效地检测到细小的裂纹和缺陷,确保产品质量和安全性。
荧光粉探伤的效果受到荧光粉配比的影响。
荧光粉配比不合理会导致探伤效果不佳,无法有效地检测出材料内部的缺陷。
制定科学合理的荧光粉探伤配比标准是至关重要的。
本文旨在探讨荧光粉探伤配比标准的制定过程,评估不同配比对探伤效果的影响,优化配比标准,进行实验验证,并提出使用注意事项。
通过对荧光粉探伤配比标准的研究和探讨,旨在为相关行业提供科学的指导和建议,提高荧光粉探伤技术在无损检测中的应用效果。
1.2 研究目的研究目的是为了建立一套科学合理的荧光粉探伤配比标准,以提高探伤效果和识别准确度。
通过对不同材料、不同表面状态和不同缺陷类型的探伤实验和分析,确定最佳配比比例,确保荧光粉在探伤过程中能够充分发挥作用,准确反映被测物体的表面缺陷情况。
通过配比标准的制定和优化,提高探伤效率,节约荧光粉的使用量,降低成本。
在实验验证阶段,将对标准进行不断调整和完善,进一步验证其可行性和有效性。
最终的目标是为用户提供一份可靠的荧光粉探伤配比标准,保证探伤结果准确可靠,为工程质量和安全保驾护航。
通过本研究,希望能为相关领域的科研人员和工程技术人员提供参考,推动荧光粉探伤技术的发展和应用。
2. 正文2.1 荧光粉探伤配比标准的制定荧光粉是一种常用的探伤辅助剂,能够帮助检测人员在检测金属表面裂纹和缺陷时更加直观和准确。
荧光粉探伤配比标准的制定是为了保证探伤效果和安全性。
在制定荧光粉探伤配比标准时,需要考虑到材料的种类、厚度、表面处理等因素。
需要确定荧光粉的种类和粒度。
不同种类的荧光粉适用于不同类型的金属材料,而粒度的选择会影响到探伤的灵敏度和分辨率。
需要确定荧光粉与溶剂的比例。
无损检测技术对比研究

无损检测技术对比研究作者:李新蕾邹伟光莫永兴许衎来源:《工业技术创新》2018年第02期摘要:对常见的无损检测技术进行对比研究,优选性能更优越的无损检测方法。
分别采用射线检测技术(RT)、传统超声检测技术(UT)、超声波衍射时差法(TOFD)和相控阵超声检测技术(PAUT)对同一对接焊缝进行无损检测,从定量、定位、定性等方面探讨其优劣势。
TOFD检测对缺陷定位、定量的准确性和适用性具有独特优势,且具有操作方便、检测快捷、灵活性强等特点,在四种无损检测方法中性能最好。
后续应继续探索提高其检测精度的途径,并加强其缺陷定性可行性的研究。
关键词:相控阵超声检测;射线检测;超声检测;超声波衍射时差法中图分类号:TB553 文献标识码:A 文章编号:2095-8412 (2018) 02-102-04工业技术创新 URL: http: // DOI: 10.14103/j.issn.2095-8412.2018.02.023引言近年来,我国工业快速发展,对各类生产服务设备、设施的安全性和可靠性提出了更高要求。
无损检测技术是检测以上性能的常用技术[1-7]。
本文对四种常见的无损检测技术——射线检测技术(RT)、传统超声检测技术(UT)、超声波衍射时差法(TOFD)和相控阵超声检测技术(PAUT)开展对比研究,从定量、定位、定性等方面对相应技术的优劣势进行探讨。
1 试板与设备1.1 试板试板上有厚度为30 mm的20#钢对接焊缝。
焊缝长度为300 mm,采用手工焊接,坡口为X型,检测面打磨合格。
试板编号为HA-030-02。
1.2 设备(1)RT检测,采用XXQ-3005型X射线机;(2)UT检测,采用武汉中科HS600型超声波探伤仪;(3)TOFD检测,采用以色列ISONIC 2007超声波探伤记录仪;(4)PAUT检测,采用以色列ISONIC PA STAR型超声相控阵检测系统。
2 方法与结果2.1 RT检测采用柯达胶片和前、后屏厚度均为0.1 mm铅箔增感屏。
基于人工智能技术的机器人辅助无损检测技术研究
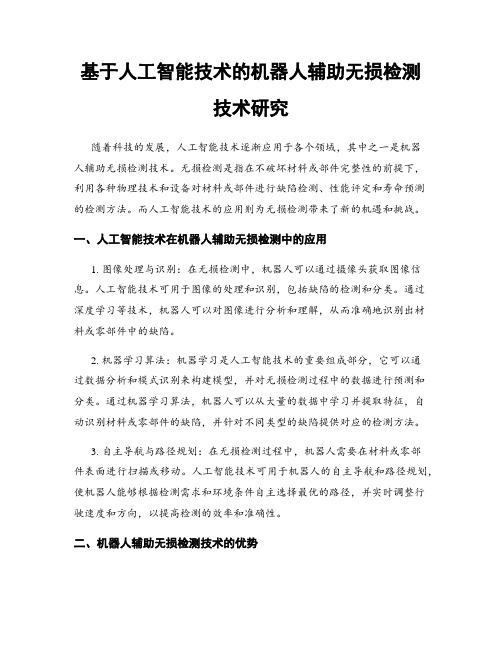
基于人工智能技术的机器人辅助无损检测技术研究随着科技的发展,人工智能技术逐渐应用于各个领域,其中之一是机器人辅助无损检测技术。
无损检测是指在不破坏材料或部件完整性的前提下,利用各种物理技术和设备对材料或部件进行缺陷检测、性能评定和寿命预测的检测方法。
而人工智能技术的应用则为无损检测带来了新的机遇和挑战。
一、人工智能技术在机器人辅助无损检测中的应用1. 图像处理与识别:在无损检测中,机器人可以通过摄像头获取图像信息。
人工智能技术可用于图像的处理和识别,包括缺陷的检测和分类。
通过深度学习等技术,机器人可以对图像进行分析和理解,从而准确地识别出材料或零部件中的缺陷。
2. 机器学习算法:机器学习是人工智能技术的重要组成部分,它可以通过数据分析和模式识别来构建模型,并对无损检测过程中的数据进行预测和分类。
通过机器学习算法,机器人可以从大量的数据中学习并提取特征,自动识别材料或零部件的缺陷,并针对不同类型的缺陷提供对应的检测方法。
3. 自主导航与路径规划:在无损检测过程中,机器人需要在材料或零部件表面进行扫描或移动。
人工智能技术可用于机器人的自主导航和路径规划,使机器人能够根据检测需求和环境条件自主选择最优的路径,并实时调整行驶速度和方向,以提高检测的效率和准确性。
二、机器人辅助无损检测技术的优势1. 高效性:机器人可以自动进行无损检测任务,不受人员疲劳和时间限制,能够持续工作并保持一致的检测质量。
同时,机器人在检测过程中可以实时记录数据和图像,并将其与数据库进行对比和分析,以提供准确的检测结果。
2. 全面性:机器人无损检测技术可以对各种材料和部件进行检测,包括金属、陶瓷、塑料等。
无论是在制造业、航空航天、能源等领域,还是在建筑工程、桥梁检测等领域,机器人都能够提供全面而准确的检测服务。
3. 安全性:通过机器人进行无损检测,可以将人员从危险环境中解放出来,降低人工操作的风险和工伤事故的发生。
同时,机器人可以在恶劣环境下工作,如高温、高压、放射性环境等,以保证检测作业的顺利完成。
焊缝内部缺陷无损检测方法的应用对比研究
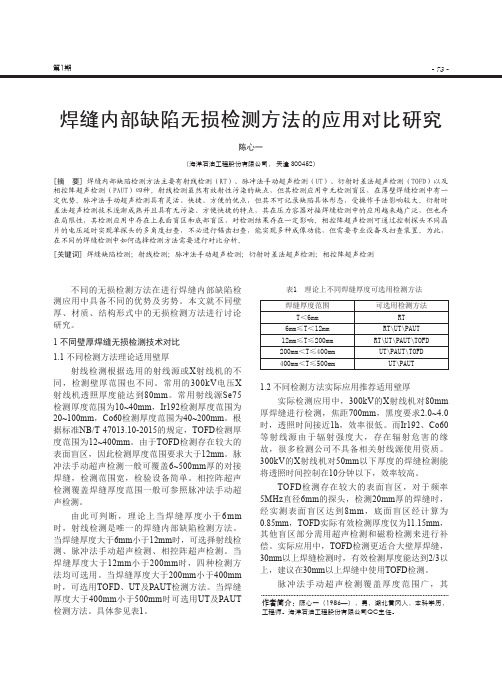
- 73 -第1期焊缝内部缺陷无损检测方法的应用对比研究陈心一(海洋石油工程股份有限公司, 天津 300452)[摘 要] 焊缝内部缺陷检测方法主要有射线检测(RT)、脉冲法手动超声检测(UT)、衍射时差法超声检测(TOFD)以及相控阵超声检测(PAUT)四种。
射线检测虽然有放射性污染的缺点,但其检测应用中无检测盲区,在薄壁焊缝检测中有一定优势。
脉冲法手动超声检测具有灵活、快捷、方便的优点,但其不可记录缺陷具体形态,受操作手法影响较大。
衍射时差法超声检测技术逐渐成熟并且具有无污染、方便快捷的特点,其在压力容器对接焊缝检测中的应用越来越广泛,但也存在局限性,其检测应用中存在上表面盲区和底部盲区,对检测结果存在一定影响。
相控阵超声检测可通过控制探头不同晶片的电压延时实现单探头的多角度扫查,不必进行锯齿扫查,能实现多种成像功能,但需要专业设备及扫查装置。
为此,在不同的焊缝检测中如何选择检测方法需要进行对比分析。
[关键词] 焊缝缺陷检测;射线检测;脉冲法手动超声检测;衍射时差法超声检测;相控阵超声检测作者简介:陈心一(1986—),男,湖北黄冈人,本科学历,工程师。
海洋石油工程股份有限公司QC主任。
不同的无损检测方法在进行焊缝内部缺陷检测应用中具备不同的优势及劣势。
本文就不同壁厚、材质、结构形式中的无损检测方法进行讨论研究。
1 不同壁厚焊缝无损检测技术对比1.1 不同检测方法理论适用壁厚射线检测根据选用的射线源或X 射线机的不同,检测壁厚范围也不同。
常用的300kV 电压X 射线机透照厚度能达到80mm 。
常用射线源Se75检测厚度范围为10~40mm ,Ir192检测厚度范围为20~100mm ,Co60检测厚度范围为40~200mm 。
根据标准NB/T 47013.10-2015的规定,TOFD 检测厚度范围为12~400mm 。
由于TOFD 检测存在较大的表面盲区,因此检测厚度范围要求大于12mm 。
超声波探伤仪标定方法对比试块

超声波探伤仪标定方法对比试块超声波探伤仪是一种常用的无损检测仪器,广泛应用于航空航天、汽车制造、石油化工等领域。
在使用超声波探伤仪进行检测之前,需要对其进行标定,以确保其准确性和可靠性。
本文将对超声波探伤仪的标定方法进行对比试块,并探讨不同方法的优缺点,以期为相关领域的工作者提供参考。
一、背景超声波探伤是一种利用超声波在材料中传播和反射的物理规律来检测和评定材料内部缺陷的方法。
超声波探伤仪是通过发射超声波脉冲并接收反射波信号来实现对被测材料检测的仪器。
由于被测材料的性质、形状、尺寸等因素不同,因此超声波探伤仪需要进行标定以适应不同的检测要求。
而标定试块的选取和应用则是实现超声波探伤仪标定的关键。
二、标定方法和试块对比1. 金属块标定方法金属块是一种常用的标定试块材料,其具有高密度和均匀性好的特点,能够提供稳定的超声波传播效果。
使用金属块进行标定可以获得较为准确的结果,适用于许多金属材料的检测。
金属块标定方法在对非金属材料的检测时存在局限性,如对塑料、陶瓷等材料的检测效果较差。
2. 参考试块法参考试块法是一种通过使用与被测材料相似的试块进行标定的方法。
这种方法能够较好地模拟实际被测材料的性质和结构,从而提高了标定的准确性和可靠性。
参考试块的选取需要考虑到与被测材料的相似性,这在实际应用中比较困难。
3. 标准试块法标准试块法是指使用经过标准化处理的试块进行标定,例如美国国家标准与技术研究院(NIST)制定的各种标准试块。
这种方法的优势在于具有可追溯性和国际通用性,能够确保标定结果的准确性和可比性。
标准试块的成本较高,且需要严格的存储和保养,同时也存在一定的局限性。
三、方法比较及总结通过对以上三种标定方法的比较可得出以下结论:金属块标定方法适用范围广,成本低廉,但在对非金属材料的检测时效果差;参考试块法能够较好地模拟实际被测材料,但试块的选取难度较大;标准试块法具有可追溯性和国际通用性,但成本较高且需要严格保养。
锚杆无损检测对比试验研究
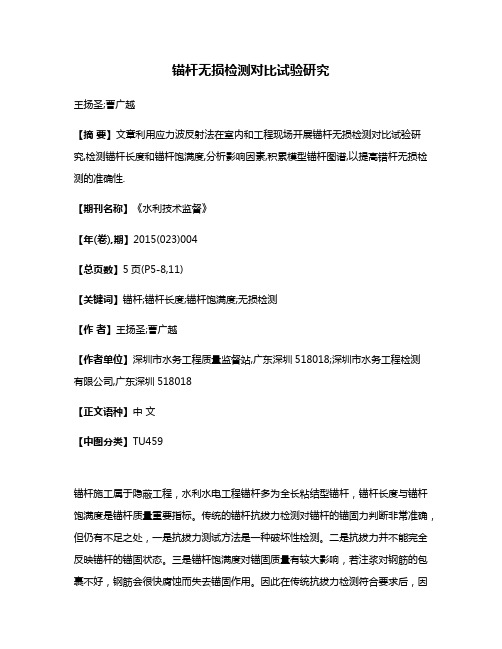
锚杆无损检测对比试验研究王扬圣;曹广越【摘要】文章利用应力波反射法在室内和工程现场开展锚杆无损检测对比试验研究,检测锚杆长度和锚杆饱满度,分析影响因素,积累模型锚杆图谱,以提高错杆无损检测的准确性.【期刊名称】《水利技术监督》【年(卷),期】2015(023)004【总页数】5页(P5-8,11)【关键词】锚杆;锚杆长度;锚杆饱满度;无损检测【作者】王扬圣;曹广越【作者单位】深圳市水务工程质量监督站,广东深圳518018;深圳市水务工程检测有限公司,广东深圳518018【正文语种】中文【中图分类】TU459锚杆施工属于隐蔽工程,水利水电工程锚杆多为全长粘结型锚杆,锚杆长度与锚杆饱满度是锚杆质量重要指标。
传统的锚杆抗拔力检测对锚杆的锚固力判断非常准确,但仍有不足之处,一是抗拔力测试方法是一种破坏性检测。
二是抗拔力并不能完全反映锚杆的锚固状态。
三是锚杆饱满度对锚固质量有较大影响,若注浆对钢筋的包裹不好,钢筋会很快腐蚀而失去锚固作用。
因此在传统抗拔力检测符合要求后,因锚杆饱满度不足造成崩塌的事故仍时有发生。
另外,传统的拉拔力检测也无法测出锚杆的实际长度,而锚杆无损检测技术能够快速准确无损地检测锚杆长度与锚杆饱满度。
无损检测技术近年来快速发展,柯玉军[1]等人应用声波透射、散射和反射理论,提出了预应力孔道灌浆密实度检测的方法;宋克民[2]采用双排列电阻率法实现对垂直铺塑防渗工程施工质量进行无损检测,测量结果表明该方法是有效的;董廷朋[3]等人利用瞬变电磁法地下隐蔽工程质量进行检测。
在锚杆无损检测方面,国内外学者进行了大量研究并取得丰富成果。
郭世明[4]等1995年至1998年在大朝山水电站采用应力波法对近千根锚杆进行了质量检测,说明采用应力波法对锚杆质量进行检测是可行的。
李义[5-7]等人在实验室进行了圆桶内水泥、树脂端锚实验和试块内水泥锚杆模拟夹层及离层实验,并对应力波在不同边界约束和轴向拉伸荷载作用下锚杆中的传播规律进行了研究。
- 1、下载文档前请自行甄别文档内容的完整性,平台不提供额外的编辑、内容补充、找答案等附加服务。
- 2、"仅部分预览"的文档,不可在线预览部分如存在完整性等问题,可反馈申请退款(可完整预览的文档不适用该条件!)。
- 3、如文档侵犯您的权益,请联系客服反馈,我们会尽快为您处理(人工客服工作时间:9:00-18:30)。
无损检测技术对比研究李新蕾,邹伟光,莫永兴,许衎(杭州华安无损检测技术有限公司,浙江杭州 310023)摘 要: 对常见的无损检测技术进行对比研究,优选性能更优越的无损检测方法。
分别采用射线检测技术(RT)、传统超声检测技术(UT)、超声波衍射时差法(TOFD)和相控阵超声检测技术(PAUT)对同一对接焊缝进行无损检测,从定量、定位、定性等方面探讨其优劣势。
TOFD检测对缺陷定位、定量的准确性和适用性具有独特优势,且具有操作方便、检测快捷、灵活性强等特点,在四种无损检测方法中性能最好。
后续应继续探索提高其检测精度的途径,并加强其缺陷定性可行性的研究。
关键词: 相控阵超声检测;射线检测;超声检测;超声波衍射时差法中图分类号:TB 553 文献标识码:A 文章编号:2095-8412 (2018) 02-102-04工业技术创新 URL : http: // DOI : 10.14103/j.issn.2095-8412.2018.02.023引言近年来,我国工业快速发展,对各类生产服务设备、设施的安全性和可靠性提出了更高要求。
无损检测技术是检测以上性能的常用技术[1-7]。
本文对四种常见的无损检测技术——射线检测技术(RT )、传统超声检测技术(UT )、超声波衍射时差法(TOFD )和相控阵超声检测技术(PAUT )开展对比研究,从定量、定位、定性等方面对相应技术的优劣势进行探讨。
1 试板与设备1.1 试板试板上有厚度为30 mm 的20#钢对接焊缝。
焊缝长度为300 mm ,采用手工焊接,坡口为X 型,检测面打磨合格。
试板编号为HA-030-02。
1.2 设备(1)RT 检测,采用XXQ-3005型X 射线机;(2)UT 检测,采用武汉中科HS600型超声波探伤仪;(3)TOFD 检测,采用以色列ISONIC 2007超声波探伤记录仪;(4)PAUT 检测,采用以色列ISONIC PA STAR 型超声相控阵检测系统。
2 方法与结果2.1 RT检测采用柯达胶片和前、后屏厚度均为0.1 mm 铅箔图1 RT 检测缺陷图像增感屏。
焦距为700 mm ,管电压为310 kV ,曝光时间为5 min 。
RT 检测缺陷图像如图1所示。
2.2 UT检测UT 检测技术等级为B 级。
耦合剂为机油,试块型号为CSK-IA/IIA-2,探头型号为2.5Z10×10K2。
补偿为4 dB ,评定线灵敏度为φ2×40-18 dB 。
2.3 TOFD检测根据NB/T 47013.10-2015标准,选择尺寸为Ф6 mm 的晶片、频率为5 MHz 的探头、角度为60°的楔块。
灵敏度设置是在试板母材上将直通波波幅设置为满屏的40%~80%。
TOFD 检测盲区覆盖图如图2所示。
在对比试块上测得表面盲区为6.5 mm ,计算得底面盲区高度为1.6 mm [8]。
TOFD 检测图谱如图3所示。
2.4 PAUT检测检测探头所使用的晶片数为32个,每个晶片宽度为0.5 mm 。
晶片为一维线性阵列排序,探头频率为5 MHz 。
一次波和二次波通常可对检测区域进行全覆盖[9]。
李新蕾,等:无损检测技术对比研究图2 TOFD 检测盲区覆盖图图5 C 扫描图图3 TOFD 检测图谱过软件测量即可得到缺陷长度、深度、高度及缺陷偏移位置。
3 讨论检测数据整理如表1所示。
结合检测图像和检测数据,展开如下讨论:(1)RT 检测由于是将缺陷投影在胶片上,故对缺陷的长度定量较为准确,但无法确定缺陷高度及其在试板厚度方向上的位置。
射线检测后期成本高,检测效率低,且射线辐射对人体有伤害。
(2)UT 检测中的超声波通常是由一个压电晶片产生的,只能产生一个固定的波束,其缺陷长度的定量准确性不如RT 检测。
UT 检测对缺陷在试板厚度方向上的定位较为准确,偏差在5 mm 内,但由于缺陷信号与表面反射信号难以区分,故对表面成型差的焊缝存在一定的盲区。
由于不能得到缺陷的直观图像,使得定性困难,故必须依靠大量的实践经验,不断验证和总结,才能得出较为准确的判断。
超声检测成本低,检测效率较高。
(3)TOFD 检测由于是利用缺陷端点的超声衍射波传播时间差等信息来定量、定位评价缺陷,故具有检测效率高、灵敏度高等特点。
其在缺陷的长度、深度和高度检测上具有很高的精度,偏差在2 mm 内。
但由于其表面盲区较大,故通常需要补充超声波或爬波检测,对于结构复杂的工件不能实现有效的定性检测。
TOFD 检测设备投入较大,但检测成本低,检测效率高。
(4)PAUT 检测得到的扇形扫查和C 扫描图像中,缺陷长度与实际偏差在3 mm 内,对缺陷与焊缝中心线的距离定位非常准确。
通过比较可见,PAUT 检测具有独特的优势。
由图4和图5可知,缺陷在试板厚度方向和焊缝宽度方向上的定位、定量更为直观,准确性更为可靠。
PAUT 检测前期设备投入较大,对操作人员检测技能要求很高,但检测成本低、操作方将探头放置在探头前沿距离焊缝边缘为20 mm 的位置处,平行移动探头进行扇形扫查[10]。
缺陷1和缺陷2的扇形扫查图如图4a 和图4b 所示。
对试板焊缝进行全面扫查,获得如图5所示的C 扫描图,从中可以看到缺陷的俯视位置和侧视位置。
通(a) 缺陷1(b) 缺陷2图4扇形扫查图2018年第02期工业技术创新Industrial Technology Innovation表1 检测数据对比检测方法RT检测UT检测TOFD检测PAUT检测缺陷编号12121212缺陷长度/mm3042274532453242缺陷深度/mm//17.216.215.513.812.610.7缺陷高度/mm////22.92.73.8缺陷偏移位置/mm//////0.40.2便、检测快捷。
4 结论和建议PAUT检测对缺陷的长度、深度、高度均具有较高的检测精度,且能够检测缺陷距离焊缝中心线的距离,在四种无损检测方法中性能最好。
后续还需在以下方面加以改进:(1)PAUT检测对缺陷高度的检测准确度略逊于TOFD检测,应探寻降低检测过程中干扰因素的途径;(2)PAUT检测只能大概了解缺陷的形状和走势,应加强其缺陷定性可行性的研究。
参考文献[1] 方发胜, 李新蕾, 莫永兴, 等. 大厚度半焊满焊缝TOFD检测方法[C]// 2013远东无损检测新技术论坛. 2013: 76-78.[2] 谭育二. 相控阵超声波检测在机车牵引电机机座焊缝探伤中的应用[J]. 金属加工: 热加工, 2014(14): 72-74.[3] 郑辉, 林树青. 超声检测: 第2版[M]. 北京: 中国劳动社会保障出版社, 2008.[4] 强天鹏. 衍射时差法(TOFD)超声波检测技术[M]. 北京: 中国作者简介:李新蕾(1985—),通信作者,男,浙江杭州人,工程师。
研究方向:无损检测新技术。
E-mail: lixinlei@劳动社会保障出版社, 2012.[5] 肖武华, 孔令昌. 相控阵检测技术在缺陷定位、定性、定量准确性的探讨[J]. 河南科技, 2013(14): 32-33.[6] 李奎元, 孔令昌, 肖武华. 金属材料相控阵检测缺陷定位、定性、定量准确性分析与比较[J]. 无损探伤, 2012, 36(3): 11-14. [7] 薛永盛, 李玉军. TOFD检测上表面盲区的讨论[J]. 无损探伤,2014, 38(4): 41-43.[8] 白艳, 邢涛. TOFD技术检测盲区的研究[J]. 森林工程, 2010,26(4):50-52+63.[9] 肖武华, 孔令昌, 李明阳. 相控阵检测技术在缺陷定位、定性、定量中的准确性[J]. 中国特种设备安全, 2013(8): 24-26.[10] 周正干, 彭地, 李洋, 等. 相控阵超声检测技术中的全聚焦成像算法及其校准研究[J]. 机械工程学报, 2015, 51(10): 1-7.李新蕾,等:无损检测技术对比研究Comparative Research on Nondestructive Testing TechnologiesLI Xin-l e i, Z OU Wei-gua ng, MO Yong-xing, XU Kan(Hangzhou HUAN NDT Technology Co., Ltd., Hangzhou 310023, China)Abstract: Commonly used nondestructive testing technologies are compared to select the utmost of them.By using X-Ray Testing Technology (RT), the traditional Ultrasonic Testing Technology (UT), method of Time of Flight Diffraction (TOFD) and Phased Array Ultrasonic Testing Technology (PAUT), the same butt weld is tested to discuss their advantages and disadvantages from aspects including quantitation, qualitation and positioning. Among them, TOFD has unique advantages for the accuracy and applicabilityof positioning and quantitative, and has the characteristics of convenient operation, quick test and strong flexibility. TOFD has the best performance among the four nondestructive testing methods. In the future, one should continue to explore the ways to improve its testing accuracy and strengthen the research on the feasibility of defect qualitation.Key words: Phased Array Ultrasonic Testing; X-Ray Testing; Ultrasonic Testing; Time of Flight Diffraction。