转炉冷料量的确定
转炉炼钢项目5装料操作
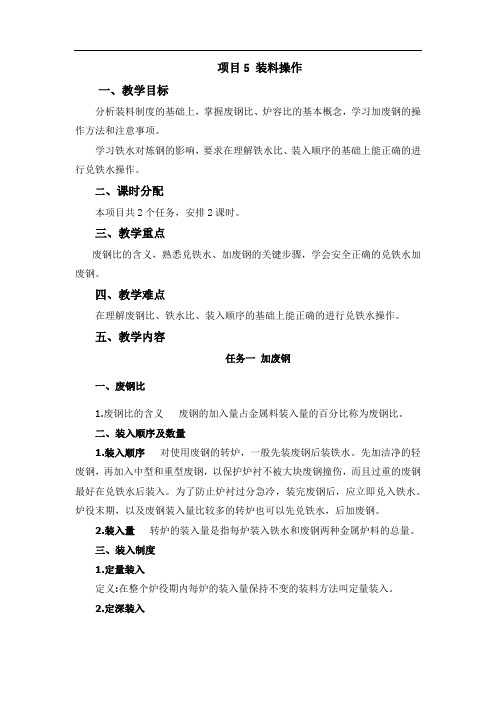
项目5 装料操作一、教学目标分析装料制度的基础上,掌握废钢比、炉容比的基本概念,学习加废钢的操作方法和注意事项。
学习铁水对炼钢的影响,要求在理解铁水比、装入顺序的基础上能正确的进行兑铁水操作。
二、课时分配本项目共2个任务,安排2课时。
三、教学重点废钢比的含义,熟悉兑铁水、加废钢的关键步骤,学会安全正确的兑铁水加废钢。
四、教学难点在理解废钢比、铁水比、装入顺序的基础上能正确的进行兑铁水操作。
五、教学内容任务一加废钢一、废钢比1.废钢比的含义废钢的加入量占金属料装入量的百分比称为废钢比。
二、装入顺序及数量1.装入顺序对使用废钢的转炉,一般先装废钢后装铁水。
先加洁净的轻废钢,再加入中型和重型废钢,以保护炉衬不被大块废钢撞伤,而且过重的废钢最好在兑铁水后装入。
为了防止炉衬过分急冷,装完废钢后,应立即兑入铁水。
炉役末期,以及废钢装入量比较多的转炉也可以先兑铁水,后加废钢。
2.装入量转炉的装入量是指每炉装入铁水和废钢两种金属炉料的总量。
三、装入制度1.定量装入定义:在整个炉役期内每炉的装入量保持不变的装料方法叫定量装入。
2.定深装入定义:在一个炉役期间,随着炉衬的侵蚀炉子实际容积不断扩大而逐渐增加装入量以保证熔池深度不变的装料方法称定深装入。
3.分阶段定量装入定义:根据炉衬的侵蚀规律和炉膛的扩大程度,将一个炉役期划分成3~5个阶段,每个阶段实行定量装入,装入量逐段递增的装料方法叫做分阶段定量装入。
操作:一、加废钢1.指挥手势2.准备工作3.加废钢操作步骤炉前指挥人员站立于转炉和转炉操作室中间近转炉的侧旁(同兑铁水位置)。
待兑铁水吊车开走后即指挥进废钢。
其基本操作步骤为:(1)指挥摇炉工将炉子倾动向前(正方向)至进废钢位置。
(2)指挥吊废钢的吊车工开吊车至炉口正中位置。
(3)指挥吊车移动大、小车将废钢斗口伸进转炉炉口。
(4)指挥吊车提升副钩,将废钢倒入炉内。
如有废钢搭桥,轧死等,可指挥吊车将副钩稍稍下降,再提起,让废钢松动一下,再倒入炉内。
转炉冶炼操作的关键点
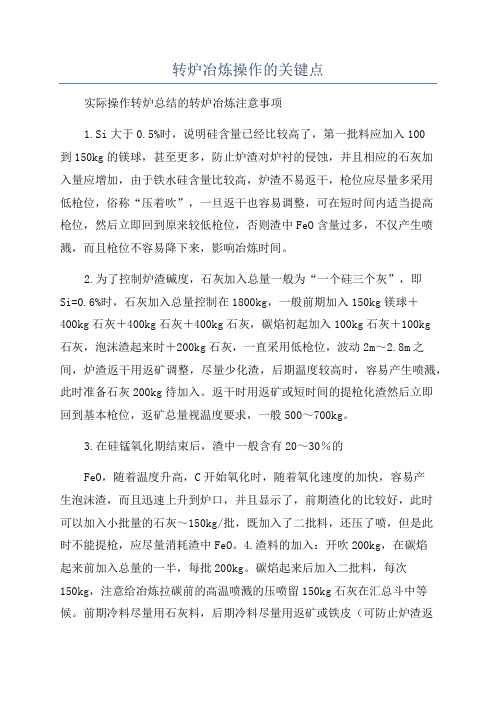
转炉冶炼操作的关键点实际操作转炉总结的转炉冶炼注意事项1.Si大于0.5%时,说明硅含量已经比较高了,第一批料应加入100到150kg的镁球,甚至更多,防止炉渣对炉衬的侵蚀,并且相应的石灰加入量应增加,由于铁水硅含量比较高,炉渣不易返干,枪位应尽量多采用低枪位,俗称“压着吹”,一旦返干也容易调整,可在短时间内适当提高枪位,然后立即回到原来较低枪位,否则渣中FeO含量过多,不仅产生喷溅,而且枪位不容易降下来,影响冶炼时间。
2.为了控制炉渣碱度,石灰加入总量一般为“一个硅三个灰”,即Si=0.6%时,石灰加入总量控制在1800kg,一般前期加入150kg镁球+400kg石灰+400kg石灰+400kg石灰,碳焰初起加入100kg石灰+100kg石灰,泡沫渣起来时+200kg石灰,一直采用低枪位,波动2m~2.8m之间,炉渣返干用返矿调整,尽量少化渣,后期温度较高时,容易产生喷溅,此时准备石灰200kg待加入。
返干时用返矿或短时间的提枪化渣然后立即回到基本枪位,返矿总量视温度要求,一般500~700kg。
3.在硅锰氧化期结束后,渣中一般含有20~30%的FeO,随着温度升高,C开始氧化时,随着氧化速度的加快,容易产生泡沫渣,而且迅速上升到炉口,并且显示了,前期渣化的比较好,此时可以加入小批量的石灰~150kg/批,既加入了二批料,还压了喷,但是此时不能提枪,应尽量消耗渣中FeO。
4.渣料的加入:开吹200kg,在碳焰起来前加入总量的一半,每批200kg。
碳焰起来后加入二批料,每次150kg,注意给冶炼拉碳前的高温喷溅的压喷留150kg石灰在汇总斗中等候。
前期冷料尽量用石灰料,后期冷料尽量用返矿或铁皮(可防止炉渣返干)。
5.Si小于0.4%时,说明硅含量已经比较低了,相应的石灰加入量应减少,由于硅含量比较低,碳焰起来的较早,应及时提前加入二批料。
铁水硅低时炉渣容易返干,注意提前提枪化渣。
6.不论硅高低,开吹时尽量采用30秒高、30秒次高再到正常的低枪位,可以帮助化好前期渣。
铁水硅高条件下转炉的冶炼操作

铁水硅高条件下转炉的冶炼操作总结及对策9月份共有188炉造双渣,喷溅16炉,喷溅率8.5%。
造成石灰消耗、钢铁料消耗升高。
下表为8月份消耗与9月份造双渣消耗对比:一、16炉喷溅原因分析:除1#炉丙班、3#炉甲班没有喷溅外,其余10个小组都有喷溅,情况如下:具体分析:1、侥幸心理没造双渣,有5炉,造成4炉小喷,1炉中喷。
2、中期化渣早,控制不住,喷溅,有4炉。
通过分析此类喷溅特点是:倒渣后,吹炼枪位较高,在8~9分钟之间化渣,此类炉渣往往在提枪后30秒左右就能化透,比正常化渣时间提前了约2~3分钟。
炉渣呈泡沫渣,这时熔池内正处于碳氧强烈反应期,生成的大量的CO气泡携带着钢渣从炉口喷出。
3、中后期温度高造成的喷溅1炉。
分析为一次性加入冷料多,熔池温度骤然下降,温度上来后造成喷溅。
4、前期小喷7炉。
主要为泡沫渣喷溅。
渣量大,渣层厚,氧化铁聚集。
碱度低,生成的气体带动炉渣涌出。
5、从总体废钢来看,废钢数量较少,平均为每炉12吨;铁块每炉平均25吨。
二、铁水硅含量高,给转炉操作带来一定影响,造成金属、温度损失大,冶炼时间延长,为保证生产的顺利进行,特对铁水硅高条件下的转炉的操作做如下规定:操枪工接到倒罐站兑铁情况后必须对硅量进行计算,铁水硅含量≥0.8 %时必须采用双渣操作,具体操作如下:1、废钢的确定:铁水硅在0.8%~1.1%之间,铁水温度在1290~1310℃之间,加入废钢10吨,渣钢5吨,铁块为12~16吨;铁水硅>1.1%,铁水温度大于1310℃,加入废钢10吨,渣钢5吨,铁块为15~20吨。
2、头批渣料的确定:要求上炉留渣量大于1/2。
在留渣量为1/2左右时,头坯料为石灰6.5吨左右,轻烧白云石2.5吨左右;全部留渣时,要求石灰5.5吨左右,轻烧白云石2.5吨左右。
以保证前期石灰尽快熔化,炉渣碱度迅速达到1.7左右,氧化镁达到8%以上,减少炉衬的浸蚀。
3、硅高铁水降枪吹炼时火焰较少,火焰呈暗红色且火焰较直。
转炉物料平衡与热平衡计算.
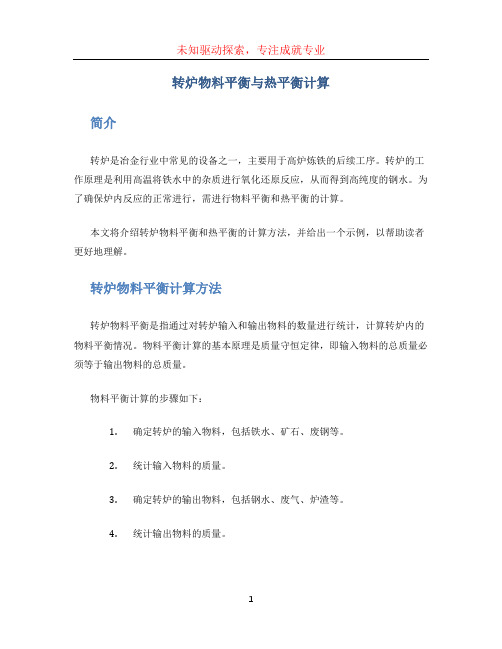
转炉物料平衡与热平衡计算简介转炉是冶金行业中常见的设备之一,主要用于高炉炼铁的后续工序。
转炉的工作原理是利用高温将铁水中的杂质进行氧化还原反应,从而得到高纯度的钢水。
为了确保炉内反应的正常进行,需进行物料平衡和热平衡的计算。
本文将介绍转炉物料平衡和热平衡的计算方法,并给出一个示例,以帮助读者更好地理解。
转炉物料平衡计算方法转炉物料平衡是指通过对转炉输入和输出物料的数量进行统计,计算转炉内的物料平衡情况。
物料平衡计算的基本原理是质量守恒定律,即输入物料的总质量必须等于输出物料的总质量。
物料平衡计算的步骤如下:1.确定转炉的输入物料,包括铁水、矿石、废钢等。
2.统计输入物料的质量。
3.确定转炉的输出物料,包括钢水、废气、炉渣等。
4.统计输出物料的质量。
5.比较输入物料的总质量和输出物料的总质量,若两者相等,则物料平衡成立;若不相等,则存在物料的损失或增加。
下面以一个具体的例子来说明转炉物料平衡的计算过程。
假设一个转炉的输入物料包括1000kg的铁水、200kg的矿石和100kg的废钢。
经过转炉反应后,得到800kg的钢水、400kg的废气和100kg的炉渣。
通过统计计算,我们可以得到输入物料的总质量为1000kg + 200kg + 100kg = 1300kg,输出物料的总质量为800kg + 400kg + 100kg = 1300kg。
两者相等,说明物料平衡成立。
转炉热平衡计算方法转炉热平衡是指通过对转炉内的能量输入和输出进行统计,计算转炉的热平衡情况。
热平衡计算的基本原理是能量守恒定律,即输入能量的总量必须等于输出能量的总量。
热平衡计算的步骤如下:1.确定转炉的输入能量,包括燃料的热值、还原剂的热值等。
2.统计输入能量的总量。
3.确定转炉的输出能量,包括钢水的热值、废气的热值等。
4.统计输出能量的总量。
5.比较输入能量的总量和输出能量的总量,若两者相等,则热平衡成立;若不相等,则存在能量的损失或增加。
转炉热平衡和物料平衡的计算
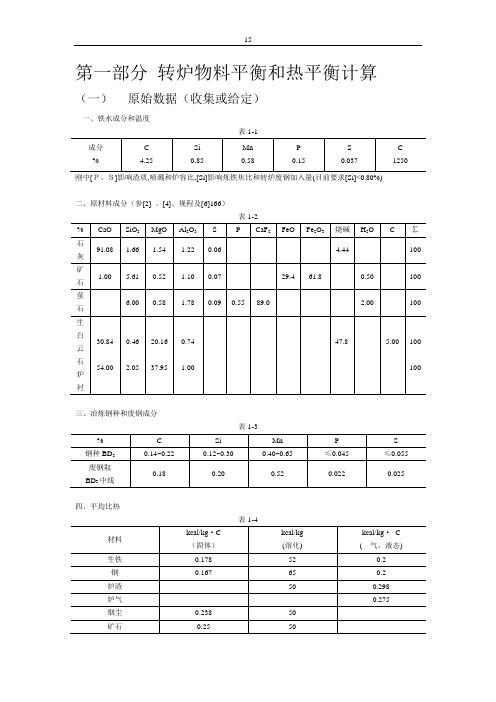
第一部分转炉物料平衡和热平衡计算(一)原始数据(收集或给定)一、铁水成分和温度表1-1刚中[P、S]影响渣质,喷溅和炉容比,[Si]影响炼铁焦比和转炉废钢加入量(目前要求[Si]<0.80%)二、原材料成分(参[2] 、[4]、规程及[6]166)表1-2三、冶炼钢种和废钢成分表1-3四、平均比热表1-4五、反应热效率(认为25℃与炼铁温度下两者数值近似)表1-5*参氧气转换炉炼钢原理(美),冶金工业出版社74年版75页六、有关参数的选用1、渣中铁珠占渣重的8%;2、金属中90%[C] →CO 10%[C]→CO2;3、喷溅铁损占铁水量的1%;4、炉气平均温度1450℃;含自愿氧0.5%;烟尘量占铁水量的1.6% 其中有77%FeO和20%Fe2O3;(作课程设计时刻改为;烟尘量占铁水量的1.16%。
参[4]31)5、炉衬侵蚀占铁水量的0.5%;6、氧气成分为98.5%O2和1.5%N;(作课程设计时可改为:99.5%O2和0.5%N2,参[4]31)。
(二)物料平衡计算由铁水成分冶炼钢种可选用单渣发不留渣的操作。
为简化计算,物料平衡以100kg铁水为计算基础。
一、炉渣量及炉渣成分的计算炉渣来自元素的氧化,造渣材料和炉衬侵蚀等。
1.铁水中各元素的氧化量%表1-6说明:[Si]——碱性渣操作时终点[Si]量为痕迹;[P]——单渣发去磷约90%(±5%);[Mn]——终点余锰量约30~40%,这里实测为30%;[S]——转炉去硫约30~50%,这里取40%;[C]——终点碳与钢种及磷量有关,要求出钢后加铁合金增碳的量能满足钢的规格中限,即:[C]终点=[C]中限—[C]增碳这里取[C]终=0.15%,可满足去磷保碳与增碳两个条件。
2、铁水中各元素的氧化量,耗氧量和氧化产物量的计算。
表1-73.造渣剂成分及数量:(选自国内有关生产炉)1)矿石成分及重量的计算(1.0kg矿石/100kg铁水)表1-8S*:反应式为[S]+( CaO)= (CaS)+[O]其中:(CaS)重为0.001×7232=0.002[㎏][S]消耗(CaO) 重为0.001×5632=0.002[㎏][O]微量,可不计。
转炉炼钢物料平衡与热平衡计算
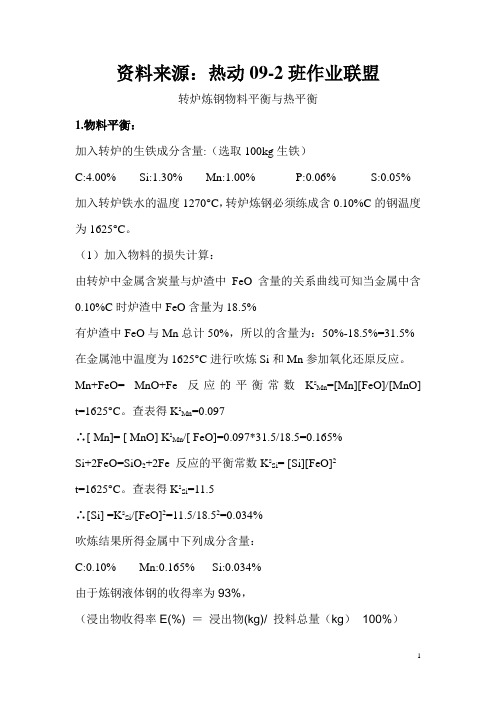
资料来源:热动09-2班作业联盟转炉炼钢物料平衡与热平衡1.物料平衡:加入转炉的生铁成分含量:(选取100kg生铁)C:4.00% Si:1.30% Mn:1.00% P:0.06% S:0.05% 加入转炉铁水的温度1270°C,转炉炼钢必须练成含0.10%C的钢温度为1625°C。
(1)加入物料的损失计算:由转炉中金属含炭量与炉渣中FeO含量的关系曲线可知当金属中含0.10%C时炉渣中FeO含量为18.5%有炉渣中FeO与Mn总计50%,所以的含量为:50%-18.5%=31.5% 在金属池中温度为1625°C进行吹炼Si和Mn参加氧化还原反应。
Mn+FeO= MnO+Fe 反应的平衡常数K s Mn=[Mn][FeO]/[MnO] t=1625°C。
查表得K s Mn=0.097∴[ Mn]= [ MnO] K s Mn/[ FeO]=0.097*31.5/18.5=0.165%Si+2FeO=SiO2+2Fe 反应的平衡常数K s Si= [Si][FeO]2t=1625°C。
查表得K s Si=11.5∴[Si] =K s Si/[FeO]2=11.5/18.52=0.034%吹炼结果所得金属中下列成分含量:C:0.10% Mn:0.165% Si:0.034%由于炼钢液体钢的收得率为93%,(浸出物收得率E(%) =浸出物(kg)/ 投料总量(kg)×100%)各成分的损失:C:4.00-0.93×0.1=3.97kgMn:1.00-0.93×0.165=0.85kgSi:1.3-0.93×0.034=1.27kg由锰与氧化铁的还原反应铁的损失:Fe:Mn损×[ FeO]/[ MnO]=0.85×18.5/31.5=0.5 kg∴总的损失量为:M损=3.97+0.85+1.27+0.5=6.59(2)氧化还原反应消耗氧气量和产物的量:在不加入废钢和矿石时,约有1/9的C燃烧生成CO2氧的利用率为99%。
转炉热量及物料平衡计算和年度物料计划

转炉热量及物料平衡计算和年度物料计划一、转炉热量及物料平衡计算1 计算的原始数1) 金属料成分和温度。
表1为金属料成分和温度。
表1金属料成分和温度项目化学成分%温度℃C Si Mn P S铁水 4.10 0.65 0.40 0.105 0.025 1300 废钢0.15 0.25 0.6 0.020 0.020 25 2) 原料成分。
表2为原料成分。
表2 原料成分项目化学成分%烧减% CaO SiO2MgO FeO烧碱Fe2O3石灰90 0.55 3.5 5 2.5 矿石8 5.5 10 70 轻烧白云石51.5 3.0 30.5 46.5炉衬 2.0 2.0 85生白云石32 1.5 203) 终点渣成分。
表3为终点渣成分。
表3 终点渣成分化学成分%碱度FeO Fe2O3 MgO3.5 10 7 84) 冶炼终点。
钢种化学成分%温度℃C Si Mn P S终点0.08 0 0.15 0.020 0.020 1650 5) 其它计算的条件各物质的质量热容见表5,炼钢温度下的反应热效应见表6。
表5 铁、钢、炉渣、炉气和矿石的平均质量热容项目 固态平均质量热容kJ/(kg·℃) 熔化潜热 kJ/kg液态或气态平均质量热容 kJ/(kg·℃)铁水 0.745 218 0.837 钢水 0.669 272 0.837 炉渣 209 1.247 炉气1.141烟尘 209 0.996 矿石1.017209表6 炼钢温度下的反应热效应反应式△H kJ/kg)()(2CO21][气气=+O C11639 )(2)(2CO][气气=+O C34834)()(2MnO21]M [液气=+O n6594 )(2)(2SiO]S [液气=+O i29202 2P P2O5 18980P2O54CaOP2O54880 )(32)(2)(O Fe 232液气液=+O Fe 6460 )()(2)(FeO21液气液=+O Fe4250)(2)()(2SiOO C 2O C 2SiO固固固∙=+a a16206) 转炉冶炼的加料情况见表7。
提高45t转炉冷料比降低铁水消耗

( 4) 减少热量支出, 可通过降低出钢温度来实现。 综上所述, 通过提高铁水入炉温度, 以绝大部分 生铁块取代废钢, 辅以向炉内添加碳质发热剂的工 艺手段降低铁水消耗, 同时在降低热量支出方面采 取优化造渣和供氧制度, 减少石灰消耗, 降低出钢温 度, 加强科技攻关和工序协调配合以及各项基础管
( 2) 造渣制 度。造渣料加入遵循 早 化渣、低 碱度、高 M gO 的炉渣控 制原则。在保证有效去除 磷、硫的情况下尽量少加石灰, 炉渣碱度控制在 2. 2 ~ 2. 6。并适当增加轻烧镁球用量, 终渣 M gO 控制 在 8% ~ 9% 之间。
( 3) 温 度控 制。温度 控制遵 循 前期快 速升 温、过程升温平稳 的原则。
根据 铁 水 温 度和 成 分, 在 铁 水 温 度 低 于 1 260# , 硅含量小于 0. 40% 的炉次中, 向炉内加入 8~ 12kg / t煤球, 可增加转炉热量收入。根据 158炉 的数据统计, 炉内温度可升高 25~ 35# , 但会增加 氧气消耗, 延长 1~ 2m in冶炼时间。 4. 3 低铁耗、高冷料比的冶炼工艺
第 3期
唐 山森等: 提高 45 t转炉冷料比 降低铁水消耗
∀ 11∀
表 1 铁水和生铁块化学成分
项目
C /%
S i /%
M n /%
P /%
S /%
T /#
铁水
3. 8~ 4. 3
0. 2 ~ 1. 56
420004转炉操作规程
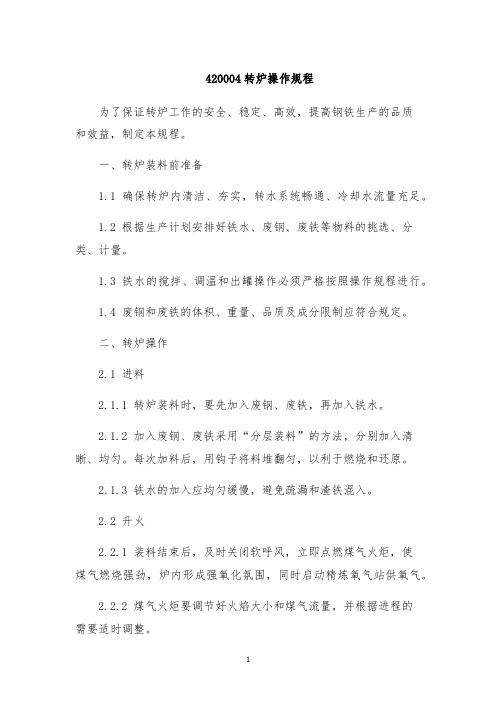
420004转炉操作规程为了保证转炉工作的安全、稳定、高效,提高钢铁生产的品质和效益,制定本规程。
一、转炉装料前准备1.1 确保转炉内清洁、夯实,转水系统畅通、冷却水流量充足。
1.2 根据生产计划安排好铁水、废钢、废铁等物料的挑选、分类、计量。
1.3 铁水的搅拌、调温和出罐操作必须严格按照操作规程进行。
1.4 废钢和废铁的体积、重量、品质及成分限制应符合规定。
二、转炉操作2.1 进料2.1.1 转炉装料时,要先加入废钢、废铁,再加入铁水。
2.1.2 加入废钢、废铁采用“分层装料”的方法,分别加入清晰、均匀。
每次加料后,用钩子将料堆翻匀,以利于燃烧和还原。
2.1.3 铁水的加入应均匀缓慢,避免疏漏和渣铁混入。
2.2 升火2.2.1 装料结束后,及时关闭软呼风,立即点燃煤气火炬,使煤气燃烧强劲,炉内形成强氧化氛围,同时启动精炼氧气站供氧气。
2.2.2 煤气火炬要调节好火焰大小和煤气流量,并根据进程的需要适时调整。
2.3.1 转炉升火后,要根据工序进行适时升速,以提高生产效率。
2.3.2 不能一次性升速过快,应缓慢升速,防止废钢、废铁未还原干净,造成渣混入钢液。
2.4 吹氧2.4.1 在早期,吹氧应以高流量、高速度为主,以促进钢液的渣化和炭氧化。
2.4.2 渣被吹到炉头前,将大量产生热,并与冶炼硅湿熔,将高矮硅还原为石墨。
2.4.3 在后期,要控制好吹氧量,以防止钢液中碳过低,造成钢质降低。
2.5 吹碱2.5.1 吹氧结束后,要及时吹碱,使钢液中的氧化物与碱反应,将多余的碱转化为钙、镁等碱土金属氧化物。
2.5.2 吹碱量应适量,不能过多,以防止碱的过量损伤转炉衬里。
2.6 出钢2.6.1 出钢时应控制好出钢速度和钢液温度,以防止钢液的溅跳和结壳。
2.6.2 出钢量应按规定决定,以保证钢液的质量和产量。
2.7.1 出钢后,要对钢液炉缸和炉头部位进行一次清理和夯实。
2.7.2 渣铁出渣时,先放入小块稳定性好的渣铁,进入后以最小的速度,小块渐次加大,放完渣铁后,开启软呼风3-5分钟,镇住渣门,等待渣流延长。
一种转炉过程冷料加入方法
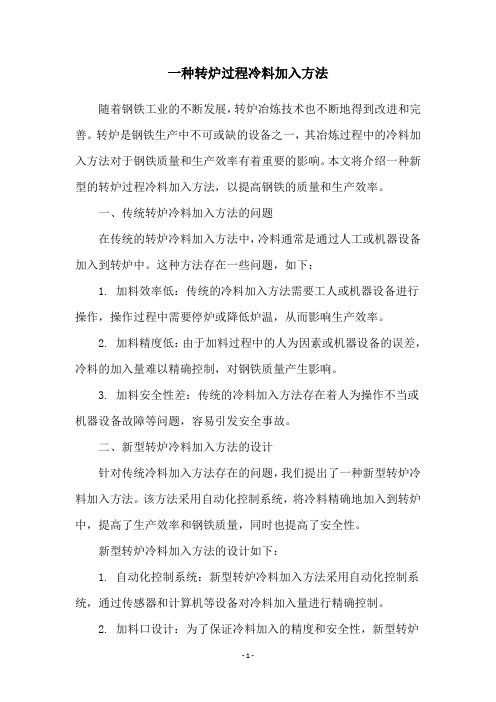
一种转炉过程冷料加入方法随着钢铁工业的不断发展,转炉冶炼技术也不断地得到改进和完善。
转炉是钢铁生产中不可或缺的设备之一,其冶炼过程中的冷料加入方法对于钢铁质量和生产效率有着重要的影响。
本文将介绍一种新型的转炉过程冷料加入方法,以提高钢铁的质量和生产效率。
一、传统转炉冷料加入方法的问题在传统的转炉冷料加入方法中,冷料通常是通过人工或机器设备加入到转炉中。
这种方法存在一些问题,如下:1. 加料效率低:传统的冷料加入方法需要工人或机器设备进行操作,操作过程中需要停炉或降低炉温,从而影响生产效率。
2. 加料精度低:由于加料过程中的人为因素或机器设备的误差,冷料的加入量难以精确控制,对钢铁质量产生影响。
3. 加料安全性差:传统的冷料加入方法存在着人为操作不当或机器设备故障等问题,容易引发安全事故。
二、新型转炉冷料加入方法的设计针对传统冷料加入方法存在的问题,我们提出了一种新型转炉冷料加入方法。
该方法采用自动化控制系统,将冷料精确地加入到转炉中,提高了生产效率和钢铁质量,同时也提高了安全性。
新型转炉冷料加入方法的设计如下:1. 自动化控制系统:新型转炉冷料加入方法采用自动化控制系统,通过传感器和计算机等设备对冷料加入量进行精确控制。
2. 加料口设计:为了保证冷料加入的精度和安全性,新型转炉冷料加入方法采用了特殊的加料口设计。
具体来说,该加料口采用了自动开合的设计,可以根据需要进行开合,从而实现冷料的精确加入。
3. 加料管道设计:为了保证冷料加入的平稳和安全,新型转炉冷料加入方法采用了特殊的加料管道设计。
具体来说,该加料管道采用了双层结构,内层管道用于输送冷料,外层管道则用于输送惰性气体,从而防止冷料与空气接触产生火花,引发安全事故。
三、新型转炉冷料加入方法的优点新型转炉冷料加入方法相比传统的冷料加入方法,具有以下优点: 1. 加料效率高:新型转炉冷料加入方法采用自动化控制系统,可以实现自动化加料,提高生产效率。
转炉炼钢车间原材料准备及供应
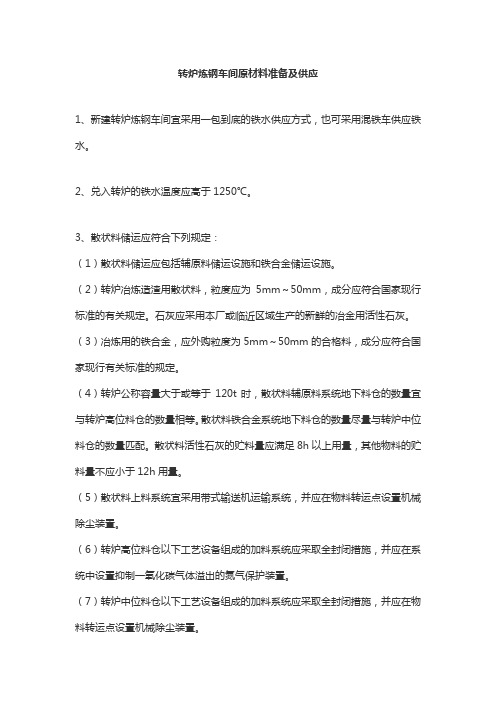
转炉炼钢车间原材料准备及供应1、新建转炉炼钢车间宜采用一包到底的铁水供应方式,也可采用混铁车供应铁水。
2、兑入转炉的铁水温度应高于1250℃。
3、散状料储运应符合下列规定:(1)散状料储运应包括辅原料储运设施和铁合金储运设施。
(2)转炉冶炼造渣用散状料,粒度应为5mm~50mm,成分应符合国家现行标准的有关规定。
石灰应采用本厂或临近区域生产的新鲜的冶金用活性石灰。
(3)冶炼用的铁合金,应外购粒度为5mm~50mm的合格料,成分应符合国家现行有关标准的规定。
(4)转炉公称容量大于或等于120t时,散状料辅原料系统地下料仓的数量宜与转炉高位料仓的数量相等。
散状料铁合金系统地下料仓的数量尽量与转炉中位料仓的数量匹配。
散状料活性石灰的贮料量应满足8h以上用量,其他物料的贮料量不应小于12h用量。
(5)散状料上料系统宜采用带式输送机运输系统,并应在物料转运点设置机械除尘装置。
(6)转炉高位料仓以下工艺设备组成的加料系统应采取全封闭措施,并应在系统中设置抑制一氧化碳气体溢出的氮气保护装置。
(7)转炉中位料仓以下工艺设备组成的加料系统应采取全封闭措施,并应在物料转运点设置机械除尘装置。
(8)铁合金在贮运过程中应防止混料、淋雨或沾水。
(9)炼钢车间不应设铁合金破碎加工设施。
(10)炼钢车间根据需要可设置合金烘烤干燥设施。
(11)炼钢车间辅原料上料系统根据需要可设置石灰筛分设施。
(12)铁合金宜由本企业内部铁合金库贮存和供给。
4、转炉装料废钢应符合下列规定:(1)转炉装料废钢比,可根据转炉容量大小在10%~20%选用。
废钢的硫、磷总量应小于0.1%,夹渣应小于10%。
(2)转炉装料前,废钢应进行挑拣分类和必要加工处理,并应分类堆存。
(3)单块废钢尺寸和重量应符合现行国家标准《废钢铁》GB 4223的有关规定。
5、转炉装料废钢严禁混入爆炸物或封闭容器。
6、废钢加料料槽应按废钢堆密度0.7t/m3~1.0t/m3和一槽装炉的原则设计。
转炉冷料量的确定
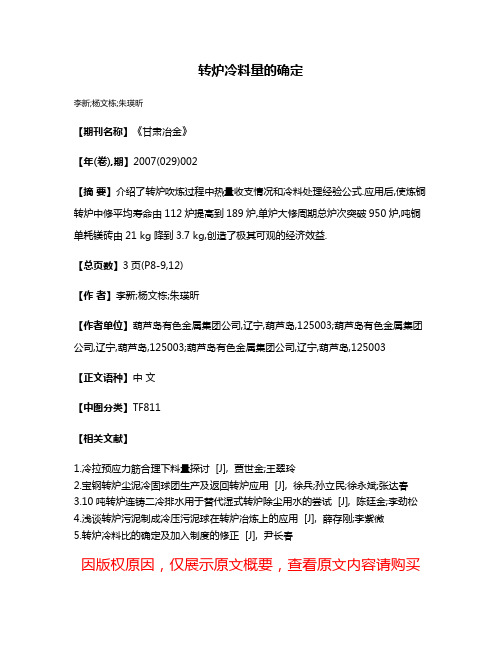
转炉冷料量的确定
李新;杨文栋;朱瑛昕
【期刊名称】《甘肃冶金》
【年(卷),期】2007(029)002
【摘要】介绍了转炉吹炼过程中热量收支情况和冷料处理经验公式.应用后,使炼铜转炉中修平均寿命由112炉提高到189炉,单炉大修周期总炉次突破950炉,吨铜单耗镁砖由21 kg降到3.7 kg,创造了极其可观的经济效益.
【总页数】3页(P8-9,12)
【作者】李新;杨文栋;朱瑛昕
【作者单位】葫芦岛有色金属集团公司,辽宁,葫芦岛,125003;葫芦岛有色金属集团公司,辽宁,葫芦岛,125003;葫芦岛有色金属集团公司,辽宁,葫芦岛,125003
【正文语种】中文
【中图分类】TF811
【相关文献】
1.冷拉预应力筋合理下料量探讨 [J], 贾世金;王翠玲
2.宝钢转炉尘泥冷固球团生产及返回转炉应用 [J], 徐兵;孙立民;徐永斌;张达春
3.10吨转炉连铸二冷排水用于替代湿式转炉除尘用水的尝试 [J], 陈廷金;李劲松
4.浅谈转炉污泥制成冷压污泥球在转炉冶炼上的应用 [J], 薛存刚;李紫微
5.转炉冷料比的确定及加入制度的修正 [J], 尹长春
因版权原因,仅展示原文概要,查看原文内容请购买。
浅析 PS 转炉吹炼冷量加入量

浅析 PS 转炉吹炼冷量加入量发表时间:2020-12-15T10:19:31.993Z 来源:《科学与技术》2020年22期作者:张扬[导读] 基于物料守恒、能量守恒和反应动力学原理,建立了PS转炉铜锍吹炼造渣张扬铜陵有色金属集团股份有限公司摘要:基于物料守恒、能量守恒和反应动力学原理,建立了PS转炉铜锍吹炼造渣期冷量的计算公式。
研究结果对优化冷料添加进而实现节能降耗具有指导意义。
关键字:ps转炉冷料加入量计算1、前言目前,国内外研究者建立了铜锍吹炼过程的静态计算模型。
基于 Briskly平衡法建立了锍、气、渣三相平衡计算模型,该模型在实际生产中得到运用;运用了吉布斯自由能最小热力学平衡计算法得到了吹炼期间转炉内铜锍温度的变化情况;薛丽华等根据元素守恒原理计算出吹炼过程的理论耗氧量和全息氧率;从热力学原理角度建立富氧吹炼的节能模型和热经济模型;姚俊峰等利用传热原理合理假设建立了冷料熔化速率和熔化时间的动力学模型。
然而,上述静态模型不能满足对生产过程进行实时调度的需要。
2、PS转炉吹炼概况铜锍吹炼是火法炼铜工艺的关键工序之全世界约85%的冰铜采用 Peirce- Smith(PS)转炉吹炼-2)。
P转炉吹炼为间歇式熔池反应过程,是具有非线性、强耦合的非封闭系统。
将熔炼过程得到的铜锍送至PS转炉进行吹炼,在此过程中鼓入空气或富氧空气、添加熔剂以维持反应进行,同时投放冷料吸收剩余热量,最终形成粗铜。
吹炼过程分为两个阶段:即FeS发生系列氧化造渣反应产出大量炉渣(称为造渣期),和Cu2S发生系列氧化反应产出粗铜(称为造铜期)。
吹炼造渣期反应为放热反应,反应所放出的热量不仅能满足维持反应温度的需求(通常为1523±10K范围内),还能产生大量剩余热量。
因此,在反应过程中需要加入冷料来平衡剩余热量,以维持稳定的反应温度,增加粗铜产量。
该过程中的剩余热量大小对冷料的添加和转炉的寿命等参数影响很大。
转炉的座数与容量的确定

转炉的座数与容量的确定接到设计任务书后首先要根据生产规模和产品方案选定炼钢方法,确定炉子的座数和容量。
9.1.1 车间内的转炉座数要保持车间的正常生产,就必须有一定数目的炉子经常处于吹炼状态,根据国内外生产实践普遍认为:转炉车间保持1至2座转炉同时吹炼比较合理,炉子太多,反而相互干扰,影响正常生产,设备利用率低。
由于炉衬材质的改进和溅渣护炉技术的采用,炉衬寿命大幅度提高,无需再按照3吹2或2吹1的生产方式配置修砌和待吹转炉,所以车间内的常吹炉座数即为车间内的炉座总数。
9.1.2 转炉容量转炉的容量一旦确定下来,车间的生产能力就基本确定下来了。
确定容量的方法是根据炼钢产品方案,同时参照同类车间的生产经验,选取平均先进指标进行初步计算,最后再按照转炉标准系列选择炉子的公称容量。
下面结合一个实例来介绍转炉容量的计算步骤。
(1)根据生产规模和产品方案计算出年需要钢水量:良坯收得率年需良坯量年需钢水量= 如:年需不同钢种的连铸方坯150万吨,连铸薄板坯150万吨。
连铸坯收得率:95%,则 年需钢水量=万吨316%95300= (2)计算年出钢炉数,按2吹2计算: 冶炼周期作业率日历时间=冶炼周期年炼钢时间年出钢炉数=⨯⨯⨯22 %5.79%100365290%100==日历天数转炉作业天数转炉作业率=⨯⨯ 转炉年有效作业天数:日历天数扣除大于20分钟以上的一切检修和故障时间总和,转炉工艺设计技术规范规定,当转炉与单台连铸机配合全连铸时为275~290天。
本例取290天;冶炼周期按转炉容量大小确定,<30t 为28~32分钟,30~100t 为 32~38分钟,>100t 为38~45分钟;本例取40分钟,则年出钢炉数=2×365×79.5%×24×60/40=20880炉每天出钢炉数=年出钢炉数/年作业天数=20880/290=72炉平均炉产钢水量=年产钢水量/年出钢炉数=3160000/20880=151t(3)按标准系列确定炉子的容量为了简化设计和便于设备配套,转炉容量应符合国家规定的标准系列容量,还应该与高炉和轧钢标准系列设备的生产能力相匹配。
一种转炉过程冷料加入方法

一种转炉过程冷料加入方法摘要:转炉冷料加入是钢铁冶炼过程中的一个关键环节。
本文介绍了一种新的转炉冷料加入方法,通过在转炉顶部设置冷料加入装置,实现了冷料的均匀加入,提高了冷料利用率,降低了能耗和成本,同时也提高了钢水质量。
关键词:转炉;冷料;加入装置;能耗;钢水质量一、引言钢铁冶炼是现代工业发展的重要基础,其中转炉冶炼是一种常用的钢铁冶炼方式。
在转炉冶炼过程中,冷料加入是一个关键环节,对钢水质量和生产效率都有着重要影响。
传统的冷料加入方式是在转炉底部加入,但存在着冷料堆积不均匀、冷料利用率低、成本高等问题。
为解决这些问题,本文提出一种新的转炉冷料加入方法,通过在转炉顶部设置冷料加入装置,实现了冷料的均匀加入,提高了冷料利用率,降低了能耗和成本,同时也提高了钢水质量。
二、传统冷料加入方式存在的问题1. 冷料堆积不均匀传统的冷料加入方式是在转炉底部加入,由于转炉内部空间狭小,冷料很容易堆积不均匀,导致炉内温度分布不均,影响钢水质量。
2. 冷料利用率低由于冷料加入位置在底部,冷料很容易被炉内高温气体燃烧,导致冷料利用率低,造成能耗浪费和成本增加。
3. 成本高传统的冷料加入方式需要大量的人力和物力进行操作,成本较高。
三、新的冷料加入方法本文提出的新的冷料加入方法是在转炉顶部设置冷料加入装置,具体操作步骤如下:1. 在转炉顶部设置冷料加入装置将冷料加入装置设置在转炉顶部,通过管道将冷料输送到加入装置。
2. 调整冷料加入速度根据炉内温度和冷料加入量,调整冷料加入速度,保证冷料均匀加入,避免冷料堆积不均匀。
3. 监测炉内温度通过炉内温度监测系统,实时监测炉内温度分布情况,根据需要调整冷料加入速度和位置,保证炉内温度分布均匀。
四、新方法的优点1. 冷料加入均匀通过在转炉顶部设置冷料加入装置,可以实现冷料的均匀加入,避免了传统冷料堆积不均匀的问题,提高了钢水质量。
2. 冷料利用率提高由于冷料加入位置在顶部,冷料不易被炉内高温气体燃烧,冷料利用率得到提高,节约了能源和成本。
冷料计量的改进建议

冷料计量的改进建议
在转炉吹制冰镧时,将冷料作为辅助物料添加到转炉中,其主要功能是调整炉温,以确保转炉中的冰铜吹炼温度保持在一个合理的范围之内,从而防止出现一系列问题。
尤其是低级冰铜吹炼,由于其反应放热大,温度升高迅速,操作难度大,各种经济技术指标均不能满足,此时添加冷料就变得非常重要。
合理的冷料比不但可以调整炉内温度,还可以使余热得到最大程度的利用,使冷料中的金属铜得到回收,并与造渣反应相结合。
具有调整渣性的功能。
在大冶冶炼厂,转炉的平均品位和平均水平分别为32%和27.9%。
在生产中,炉温方面,(北京有色金属研究院10月进行了一次炉温试验,发现一次最高温度超过1313摄氏度。
筛时最高可达1330℃)炉使用寿命较短,以炉次计算,仅17.6炉次/炉,而耐火材料的单耗为45 kg/t· Cu。
很明显,这很反常。
为了改变这一现状,作者建议首先从工艺参数的角度出发,根据各个参数的相关性,找到主要的影响因素,然后在实际操作中确定关键参数,从而实现制冷率的正规化,并实现工艺参效的真正指导生产。
针对转炉实际运行情况,只对一次循环的冰铜吹炼进行了材料及热量平衡的计算。
转炉设计参数选择
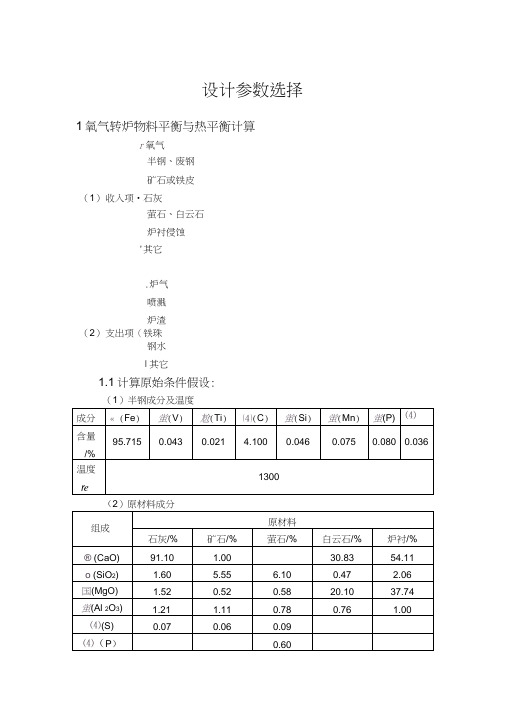
设计参数选择1氧气转炉物料平衡与热平衡计算r氧气半钢、废钢矿石或铁皮(1)收入项•石灰萤石、白云石炉衬侵蚀'其它.炉气喷溅炉渣(2)支出项(铁珠钢水I其它1.1计算原始条件假设:(1)半钢成分及温度(2)原材料成分(4)平均比热容(5)冷却剂用废钢作冷却剂,其他成分与冶炼钢种成分的中限皆同(6)反应热效应(25 C)(7)根据国内同类转炉的实验数据选取①渣中铁珠量为渣量的8%;②金属中碳的氧化,其中90%的碳氧化成CO, 10%碳氧化成CO2;③喷溅铁损为铁水量的1%;④炉气和烟尘量,取炉气平均温度1450r。
炉气中自由氧含量为0.5%烟尘量为铁水量的1.6%,其中「(FeO)=77% , ■ (Fe2O3)=20%;⑤炉衬侵蚀量为铁水量的0.5%;⑥氧气成分,(O2)=99.5%、(N2)=0.5%。
(8)终点成分2转炉炉型主要参数参数确定方法有两种方法:① 直接推荐法;② 推荐经验公式。
由北京钢铁设计研究总院推荐的一套经验公式。
主要包括:(1)炉容比(V/T); (2)高宽比(H/D); (3)熔池深度直径比(h/D); (4) 炉口直径比(d0/D); (5)帽锥角(日);(6)出钢口参数;(7)转炉的公称吨位。
3炉型设计计算新转炉的炉型和各部位尺寸可根据经验公式计算,结合现有转炉生产实际并通过模型试验来确定。
炉型尺寸的选择依据:生产规模、原材料条件、工艺操作方法。
① 确定所设计炉子的公称容量② 选择炉型设计程序]③确定炉型主要设计参数④ 计算熔池尺寸 ⑤ 确定整个炉型尺寸(1) 原始条件① 炉子平均出钢量为120t ,钢水收得率为92.62%,则金属装入量为:120G129.562 : 130t92.62%② 原料:半钢,采用单渣不留渣操作。
③ 氧枪喷嘴采用四孔拉瓦尔喷孔, (2) 熔池尺寸的计算1)熔池直径 2)熔池深度(h )本文采用筒球形熔池深度计算公式 金属熔池的体积为:V 熔池=0.79hD 2 -0.046D 3因而V 熔池 0.046D 3 h = 20.79D 2(3) 炉帽尺寸1) 炉口直径dd =(0.43~ 0.53)D ,本文 d 取 2200mm 。
炼钢部分各种计算公式汇总

炼钢部分各种计算公式汇总1、转炉装入量装入量=钢坯(锭)单重×钢坯(锭)支数+浇注必要损失钢水收得率(%)-合金用量×合金收得率(%)2、氧气流量Q=V tQ-氧气流量(标态),m 3min 或 m3hV-1炉钢的氧气耗量(标态),m 3; t-1炉钢吹炼时间,min 或h 3、供氧强度 I=Q TI-供氧强度(标态),m3t ·min ;Q-氧气流量(标态),m3min;T-出钢量,t注:氧气理论计算值仅为总耗氧量的75%~85%。
氧枪音速计算α=(κgRT)1/2m/sα—当地条件下的音速,m/s ;κ—气体的热容比,对于空气和氧气,κ=1.4;g —重力加速度,9.81m/s 2;R —气体常数,26.49m/κ。
马赫数计算 M=ν/αM —马赫数;ν—气体流速,m/s ;α—音速,m/s 。
冲击深度计算h 冲=K P 00.5·d 00.6ρ金0.4(1+H 枪/d c ·B)h 冲—冲击深度,m ;P 0—氧气的滞止压力(绝对),㎏/㎝2;d 0—喷管出口直径,m ;H 枪—枪位,m ;ρ金—金属的密度,㎏/m 3;d c —候口直径,m ;B —常数,对低粘度液体取作40;K —考虑到转炉实际吹炼特点的系数,等于40。
在淹没吹炼的情况下,H=0,冲击深度达到最大值,即 h max =P 00.5·d 00.6ρ金0.4有效冲击面积计算 R=2.41×104(h νmax)2R —有效冲击半径,m ;νmax —液面氧射流中心流速,m/s ;νmax =ν出d 出H ·P 00.404ν出—氧射流在出口处的流速,m/s 。
金属-氧接触面积计算在淹没吹炼时,射流中的金属液滴重是氧气重量的3倍,吹入1m3氧气的液滴总表面积(金属-氧气的接触面积): S Σ=3G 金r 平均·ρ金G 金—1标米3氧气中的金属液滴重量=3×1.43㎏;r 平均—液滴的平均半径,m ;ρ金—金属液的密度,7×103㎏/m 3。
转炉炼钢物料平衡计算

1.转炉炼钢物料平衡计算计算原始数据基本原始数据:冶炼钢种及其成分、铁水和废钢成分、终点钢水成分(表1);造渣用溶剂及炉衬等原材料的成分(表2);脱氧和合金化用铁合金的成分及其回收率(表3);其他工艺参数(表4)。
aa [C]和[Si]按实际产生情况选取;[Mn]、[P]和[S]分别按铁水中相应成分含量的30%、10%和60%留在刚水中设定。
10%与氧生成CO2。
表4 其他工艺参数设定值名称参数名称参数终渣碱度W(CaO)/W(SiQ)= 渣中铁损(铁珠)为渣量的6%萤石加入量为铁水量得% 氧气纯度99%,余者为N2生白云石加入量为铁水量得% 炉气中自由氧含量%(体积比)炉衬蚀损量为铁水量得% 气化去硫量占总去硫量得1/3终渣刀3 (FeO)15%,而W(Fe2O3)/ 金属中[C]的氧化产90%C氧化成CO,10%C氧化成含量(按向钢中刀w(FeO)=13,即物CQ传氧量3 (Fe2O3) W(Fe2O3)=5% 废钢量=3 (FeO折算)W(FeO)=% 由热平衡计算确定,本计算结果烟尘量为铁水量的%,即废钢比为% 为铁水量得%(其中W(FeO)75%,喷吹铁损W(Fe2O3)为20%)为铁水量得1%物料平衡基本项目收入项有:铁水、废钢、溶剂、氧气、炉衬损失、铁合金。
支出项有:钢水、炉渣、烟尘、渣中铁珠、炉气、喷溅。
计算步骤以100kg铁水为基础进行计算。
计算脱氧和合金化前的总渣量及其成分总渣量包括铁水中元素氧化,炉衬蚀损和加入溶剂的成渣量。
其各项成渣量分别列于表5-表7。
总渣量及其成分如表8所示。
由CaO还原出的氧量;消耗的CaO量=x 56/32=石灰加入量计算如下:由表 5 —表7可知,渣中已含(CaO)=- +++=;渣中已含(SiC2)=+++=。
因设定的终渣碱度R=,故石灰加入量为:[R刀3 (SiQ)-刀3 (CaO)]/[ w (CaO 石灰)-R Xw (SiO2 石灰)]=%x %)=。
- 1、下载文档前请自行甄别文档内容的完整性,平台不提供额外的编辑、内容补充、找答案等附加服务。
- 2、"仅部分预览"的文档,不可在线预览部分如存在完整性等问题,可反馈申请退款(可完整预览的文档不适用该条件!)。
- 3、如文档侵犯您的权益,请联系客服反馈,我们会尽快为您处理(人工客服工作时间:9:00-18:30)。
m ge u rku eln o 1 . gnpro pe Iic a ni r leoo ibnf . a s mbi s idcs f m2 k t37k i e t c pr ts r tc s e b nmc eet ni c e s ie r d d o s n o . e e o d a e c i s
的重要手 段 。
= : :
送 风 显 热
热 收 入项
一
热 支 出 项
. ,, 爝气带走热
C 6反应热 、 . f u
自 热 一 lS转 炉 姓 避风显热 P
~ 炉体停风敬失热
2 转炉冷料量是左右热平衡的关键
转炉铜锍 吹炼是一个 自然过程。共 分两个周 期, 即造渣期和造铜期。造渣期主要是硫化铁 的氧
Ke r s o v re l p t h r l q i b i ;l e s a ;f cos y wo d :c n e rc d i u ;t ema e ul ru t o n i m i -p m f a t r ,
1 前言
、
中的两个周期热量收支情况见图 l 。
热收 入项
温度低于 110℃时, 5 熔体有凝结的危险 , 风眼 易粘结、 堵塞; 温度高于 130℃时, 0 转炉炉衬 耐火 材料的损坏明显加快。生产实践证 明, 铜锍 吹炼温 度控制在 l 7 0℃就足够 了。控制炉温 的办法主要 2
( ldoN neru t s ru s o t. H ldo150 C ia Huua ofr sMe l G op .Ld , uu a 20 3, hn ) o a C
Ab ta t T i r ceit d cdtetema ee u n x e dtr i aini h o v r rbo igpo e s h p l sr c :hsat l nr u e h r l v n ea d ep n i est t tec n et lw n rc s ,tea pi i o h r u u o n e - c t no hefr l b u h o vre l p t h eut idctsta ecp e n e e v rg f-p ni h ai ft omuaao t ecn e rc d i u.T ers s n iae h t p rc vr r ea el esa te o t t o n l h t o o t a i n p r rp i as rm 1 i st 8 i s oa tv i si tp9 0 t esn l tv v r a i .An h at  ̄ ari rie fo 1 2 t s d me o 1 9 t me .T tlso et me s o 5 o t igesoe o ehu le h l f dte
中图分类号 :F 1 T 81 文献标识码 : A
Dee m i to n t e W eg to l n u n Co v re t r na in o h ih fCod I p ti n e t r
,ห้องสมุดไป่ตู้
L n,YANG e — o g,ZHU n -i IXi W nd n Yi g x n
转炉 冷料 量 的确 定
李 新, 杨文栋 , 朱瑛 昕
葫芦岛 15 0 ) 20 3 ( 葫芦岛有色金属集团公 司, 辽宁
摘
要 : 了转炉吹炼过程 中热量收支情 况和冷料 处理经验公 式。应 用后 , 介绍 使炼铜转 炉 中修平 均寿命 由 1 1 2炉
提高到 19炉 , 8 单炉大修周期 总炉次 突破 9 0炉 , 5 吨铜单耗镁砖由 2 s 1k 降到 3 7k , . g创造了极其可观的经济效益 。 关键词 : 炉冷料量 ; 转 热平衡 ; 寿命 ; 因素
化及其造渣放热 , 造铜期 主要是硫化亚铜的氧化放 热, 反应 式 如下 :
造渣 期 : I+ 0 +2 i2 2 e SO 2 s 3 2 SO = FO・ i2
+2 0 S 2+l0 0 0 J 3 .9k
在转炉铜锍吹炼的造渣期 和造铜期 内, 10 以 0 k 铜锍为计算基础的热平衡见表 l表 2 g 、 。 从表 l2可 以看 出: 、 转炉铜锍吹炼两个周期 中 均有大量的过剩热量 , 这些过剩热量极易造成炉温
过高。而转炉铜锍吹炼过程的正常温度一般都控制 在 l10一l3 o℃范 围内 , 5 o 见表 3 。
造 铜期 : I 2 2 u+I 2 274U C2 s+0 = C s + 1. 0
从两个反应式来看 , k 的 FS氧化造渣反应 lg e 可以放出 5 8 J .51 的热量, k 的 C 【 lg uS氧化生成金 属铜可以放出 13 J的热量。第 l .71 【 周期 的反应热 要 比第 2 周期的反应热多得多。转炉铜锍吹炼过程
造渣反应 热 ——
热 支 出项
冷料 的吸 热与熔★ 热 军 烟 气带走 热 摊渣带走 热 炉 体等炉 等数热 失热
影响转炉炉体寿命 的因素很多, 如炉体的热平
.
衡、 炉体耐火材料的质量 、 砌炉质量、 工人 的实际操 作水平以及工艺技术条件的控制等等 , 其中炉体热 平衡是影响转炉炉体寿命 的重要 因素之一 , 严格控 制好转炉生产 中的热平衡是延长转炉炉体使用寿命
维普资讯
第2 9卷第 2期 20 0 7年 4月
甘
肃
冶
金
V0 . 9 No 2 12 . Ap ., 0 7 r 20
GAN U MEI I RG S , 工U Y ' A
、
文章 编号 :6 46 (07 0 -0 80 17 -4 12 0 ) 200 - 2 2