FL3B-MKNOTE_CONGO_0911_A_1300
NuMicro N9H30系列开发板用户手册说明书

NuMicro®FamilyArm® ARM926EJ-S BasedNuMaker-HMI-N9H30User ManualEvaluation Board for NuMicro® N9H30 SeriesNUMAKER-HMI-N9H30 USER MANUALThe information described in this document is the exclusive intellectual property ofNuvoton Technology Corporation and shall not be reproduced without permission from Nuvoton.Nuvoton is providing this document only for reference purposes of NuMicro microcontroller andmicroprocessor based system design. Nuvoton assumes no responsibility for errors or omissions.All data and specifications are subject to change without notice.For additional information or questions, please contact: Nuvoton Technology Corporation.Table of Contents1OVERVIEW (5)1.1Features (7)1.1.1NuMaker-N9H30 Main Board Features (7)1.1.2NuDesign-TFT-LCD7 Extension Board Features (7)1.2Supporting Resources (8)2NUMAKER-HMI-N9H30 HARDWARE CONFIGURATION (9)2.1NuMaker-N9H30 Board - Front View (9)2.2NuMaker-N9H30 Board - Rear View (14)2.3NuDesign-TFT-LCD7 - Front View (20)2.4NuDesign-TFT-LCD7 - Rear View (21)2.5NuMaker-N9H30 and NuDesign-TFT-LCD7 PCB Placement (22)3NUMAKER-N9H30 AND NUDESIGN-TFT-LCD7 SCHEMATICS (24)3.1NuMaker-N9H30 - GPIO List Circuit (24)3.2NuMaker-N9H30 - System Block Circuit (25)3.3NuMaker-N9H30 - Power Circuit (26)3.4NuMaker-N9H30 - N9H30F61IEC Circuit (27)3.5NuMaker-N9H30 - Setting, ICE, RS-232_0, Key Circuit (28)NUMAKER-HMI-N9H30 USER MANUAL3.6NuMaker-N9H30 - Memory Circuit (29)3.7NuMaker-N9H30 - I2S, I2C_0, RS-485_6 Circuit (30)3.8NuMaker-N9H30 - RS-232_2 Circuit (31)3.9NuMaker-N9H30 - LCD Circuit (32)3.10NuMaker-N9H30 - CMOS Sensor, I2C_1, CAN_0 Circuit (33)3.11NuMaker-N9H30 - RMII_0_PF Circuit (34)3.12NuMaker-N9H30 - RMII_1_PE Circuit (35)3.13NuMaker-N9H30 - USB Circuit (36)3.14NuDesign-TFT-LCD7 - TFT-LCD7 Circuit (37)4REVISION HISTORY (38)List of FiguresFigure 1-1 Front View of NuMaker-HMI-N9H30 Evaluation Board (5)Figure 1-2 Rear View of NuMaker-HMI-N9H30 Evaluation Board (6)Figure 2-1 Front View of NuMaker-N9H30 Board (9)Figure 2-2 Rear View of NuMaker-N9H30 Board (14)Figure 2-3 Front View of NuDesign-TFT-LCD7 Board (20)Figure 2-4 Rear View of NuDesign-TFT-LCD7 Board (21)Figure 2-5 Front View of NuMaker-N9H30 PCB Placement (22)Figure 2-6 Rear View of NuMaker-N9H30 PCB Placement (22)Figure 2-7 Front View of NuDesign-TFT-LCD7 PCB Placement (23)Figure 2-8 Rear View of NuDesign-TFT-LCD7 PCB Placement (23)Figure 3-1 GPIO List Circuit (24)Figure 3-2 System Block Circuit (25)Figure 3-3 Power Circuit (26)Figure 3-4 N9H30F61IEC Circuit (27)Figure 3-5 Setting, ICE, RS-232_0, Key Circuit (28)Figure 3-6 Memory Circuit (29)Figure 3-7 I2S, I2C_0, RS-486_6 Circuit (30)Figure 3-8 RS-232_2 Circuit (31)Figure 3-9 LCD Circuit (32)NUMAKER-HMI-N9H30 USER MANUAL Figure 3-10 CMOS Sensor, I2C_1, CAN_0 Circuit (33)Figure 3-11 RMII_0_PF Circuit (34)Figure 3-12 RMII_1_PE Circuit (35)Figure 3-13 USB Circuit (36)Figure 3-14 TFT-LCD7 Circuit (37)List of TablesTable 2-1 LCD Panel Combination Connector (CON8) Pin Function (11)Table 2-2 Three Sets of Indication LED Functions (12)Table 2-3 Six Sets of User SW, Key Matrix Functions (12)Table 2-4 CMOS Sensor Connector (CON10) Function (13)Table 2-5 JTAG ICE Interface (J2) Function (14)Table 2-6 Expand Port (CON7) Function (16)Table 2-7 UART0 (J3) Function (16)Table 2-8 UART2 (J6) Function (16)Table 2-9 RS-485_6 (SW6~8) Function (17)Table 2-10 Power on Setting (SW4) Function (17)Table 2-11 Power on Setting (S2) Function (17)Table 2-12 Power on Setting (S3) Function (17)Table 2-13 Power on Setting (S4) Function (17)Table 2-14 Power on Setting (S5) Function (17)Table 2-15 Power on Setting (S7/S6) Function (18)Table 2-16 Power on Setting (S9/S8) Function (18)Table 2-17 CMOS Sensor Connector (CON9) Function (19)Table 2-18 CAN_0 (SW9~10) Function (19)NUMAKER-HMI-N9H30 USER MANUAL1 OVERVIEWThe NuMaker-HMI-N9H30 is an evaluation board for GUI application development. The NuMaker-HMI-N9H30 consists of two parts: a NuMaker-N9H30 main board and a NuDesign-TFT-LCD7 extensionboard. The NuMaker-HMI-N9H30 is designed for project evaluation, prototype development andvalidation with HMI (Human Machine Interface) function.The NuMaker-HMI-N9H30 integrates touchscreen display, voice input/output, rich serial port serviceand I/O interface, providing multiple external storage methods.The NuDesign-TFT-LCD7 can be plugged into the main board via the DIN_32x2 extension connector.The NuDesign-TFT-LCD7 includes one 7” LCD which the resolution is 800x480 with RGB-24bits andembedded the 4-wires resistive type touch panel.Figure 1-1 Front View of NuMaker-HMI-N9H30 Evaluation BoardNUMAKER-HMI-N9H30 USER MANUAL Figure 1-2 Rear View of NuMaker-HMI-N9H30 Evaluation Board1.1 Features1.1.1 NuMaker-N9H30 Main Board Features●N9H30F61IEC chip: LQFP216 pin MCP package with DDR (64 MB)●SPI Flash using W25Q256JVEQ (32 MB) booting with quad mode or storage memory●NAND Flash using W29N01HVSINA (128 MB) booting or storage memory●One Micro-SD/TF card slot served either as a SD memory card for data storage or SDIO(Wi-Fi) device●Two sets of COM ports:–One DB9 RS-232 port with UART_0 used 75C3232E transceiver chip can be servedfor function debug and system development.–One DB9 RS-232 port with UART_2 used 75C3232E transceiver chip for userapplication●22 GPIO expansion ports, including seven sets of UART functions●JTAG interface provided for software development●Microphone input and Earphone/Speaker output with 24-bit stereo audio codec(NAU88C22) for I2S interfaces●Six sets of user-configurable push button keys●Three sets of LEDs for status indication●Provides SN65HVD230 transceiver chip for CAN bus communication●Provides MAX3485 transceiver chip for RS-485 device connection●One buzzer device for program applicationNUMAKER-HMI-N9H30 USER MANUAL●Two sets of RJ45 ports with Ethernet 10/100 Mbps MAC used IP101GR PHY chip●USB_0 that can be used as Device/HOST and USB_1 that can be used as HOSTsupports pen drives, keyboards, mouse and printers●Provides over-voltage and over current protection used APL3211A chip●Retain RTC battery socket for CR2032 type and ADC0 detect battery voltage●System power could be supplied by DC-5V adaptor or USB VBUS1.1.2 NuDesign-TFT-LCD7 Extension Board Features●7” resolution 800x480 4-wire resistive touch panel for 24-bits RGB888 interface●DIN_32x2 extension connector1.2 Supporting ResourcesFor sample codes and introduction about NuMaker-N9H30, please refer to N9H30 BSP:https:///products/gui-solution/gui-platform/numaker-hmi-n9h30/?group=Software&tab=2Visit NuForum for further discussion about the NuMaker-HMI-N9H30:/viewforum.php?f=31 NUMAKER-HMI-N9H30 USER MANUALNUMAKER-HMI-N9H30 USER MANUAL2 NUMAKER-HMI-N9H30 HARDWARE CONFIGURATION2.1 NuMaker-N9H30 Board - Front View Combination Connector (CON8)6 set User SWs (K1~6)3set Indication LEDs (LED1~3)Power Supply Switch (SW_POWER1)Audio Codec(U10)Microphone(M1)NAND Flash(U9)RS-232 Transceiver(U6, U12)RS-485 Transceiver(U11)CAN Transceiver (U13)Figure 2-1 Front View of NuMaker-N9H30 BoardFigure 2-1 shows the main components and connectors from the front side of NuMaker-N9H30 board. The following lists components and connectors from the front view:NuMaker-N9H30 board and NuDesign-TFT-LCD7 board combination connector (CON8). This panel connector supports 4-/5-wire resistive touch or capacitance touch panel for 24-bits RGB888 interface.Connector GPIO pin of N9H30 FunctionCON8.1 - Power 3.3VCON8.2 - Power 3.3VCON8.3 GPD7 LCD_CSCON8.4 GPH3 LCD_BLENCON8.5 GPG9 LCD_DENCON8.7 GPG7 LCD_HSYNCCON8.8 GPG6 LCD_CLKCON8.9 GPD15 LCD_D23(R7)CON8.10 GPD14 LCD_D22(R6)CON8.11 GPD13 LCD_D21(R5)CON8.12 GPD12 LCD_D20(R4)CON8.13 GPD11 LCD_D19(R3)CON8.14 GPD10 LCD_D18(R2)CON8.15 GPD9 LCD_D17(R1)CON8.16 GPD8 LCD_D16(R0)CON8.17 GPA15 LCD_D15(G7)CON8.18 GPA14 LCD_D14(G6)CON8.19 GPA13 LCD_D13(G5)CON8.20 GPA12 LCD_D12(G4)CON8.21 GPA11 LCD_D11(G3)CON8.22 GPA10 LCD_D10(G2)CON8.23 GPA9 LCD_D9(G1) NUMAKER-HMI-N9H30 USER MANUALCON8.24 GPA8 LCD_D8(G0)CON8.25 GPA7 LCD_D7(B7)CON8.26 GPA6 LCD_D6(B6)CON8.27 GPA5 LCD_D5(B5)CON8.28 GPA4 LCD_D4(B4)CON8.29 GPA3 LCD_D3(B3)CON8.30 GPA2 LCD_D2(B2)CON8.31 GPA1 LCD_D1(B1)CON8.32 GPA0 LCD_D0(B0)CON8.33 - -CON8.34 - -CON8.35 - -CON8.36 - -CON8.37 GPB2 LCD_PWMCON8.39 - VSSCON8.40 - VSSCON8.41 ADC7 XPCON8.42 ADC3 VsenCON8.43 ADC6 XMCON8.44 ADC4 YMCON8.45 - -CON8.46 ADC5 YPCON8.47 - VSSCON8.48 - VSSCON8.49 GPG0 I2C0_CCON8.50 GPG1 I2C0_DCON8.51 GPG5 TOUCH_INTCON8.52 - -CON8.53 - -CON8.54 - -CON8.55 - -NUMAKER-HMI-N9H30 USER MANUAL CON8.56 - -CON8.57 - -CON8.58 - -CON8.59 - VSSCON8.60 - VSSCON8.61 - -CON8.62 - -CON8.63 - Power 5VCON8.64 - Power 5VTable 2-1 LCD Panel Combination Connector (CON8) Pin Function●Power supply switch (SW_POWER1): System will be powered on if the SW_POWER1button is pressed●Three sets of indication LEDs:LED Color DescriptionsLED1 Red The system power will beterminated and LED1 lightingwhen the input voltage exceeds5.7V or the current exceeds 2A.LED2 Green Power normal state.LED3 Green Controlled by GPH2 pin Table 2-2 Three Sets of Indication LED Functions●Six sets of user SW, Key Matrix for user definitionKey GPIO pin of N9H30 FunctionK1 GPF10 Row0 GPB4 Col0K2 GPF10 Row0 GPB5 Col1K3 GPE15 Row1 GPB4 Col0K4 GPE15 Row1 GPB5 Col1K5 GPE14 Row2 GPB4 Col0K6GPE14 Row2GPB5 Col1 Table 2-3 Six Sets of User SW, Key Matrix Functions●NAND Flash (128 MB) with Winbond W29N01HVS1NA (U9)●Microphone (M1): Through Nuvoton NAU88C22 chip sound input●Audio CODEC chip (U10): Nuvoton NAU88C22 chip connected to N9H30 using I2Sinterface–SW6/SW7/SW8: 1-2 short for RS-485_6 function and connected to 2P terminal (CON5and J5)–SW6/SW7/SW8: 2-3 short for I2S function and connected to NAU88C22 (U10).●CMOS Sensor connector (CON10, SW9~10)–SW9~10: 1-2 short for CAN_0 function and connected to 2P terminal (CON11)–SW9~10: 2-3 short for CMOS sensor function and connected to CMOS sensorconnector (CON10)Connector GPIO pin of N9H30 FunctionCON10.1 - VSSCON10.2 - VSSNUMAKER-HMI-N9H30 USER MANUALCON10.3 - Power 3.3VCON10.4 - Power 3.3VCON10.5 - -CON10.6 - -CON10.7 GPI4 S_PCLKCON10.8 GPI3 S_CLKCON10.9 GPI8 S_D0CON10.10 GPI9 S_D1CON10.11 GPI10 S_D2CON10.12 GPI11 S_D3CON10.13 GPI12 S_D4CON10.14 GPI13 S_D5CON10.15 GPI14 S_D6CON10.16 GPI15 S_D7CON10.17 GPI6 S_VSYNCCON10.18 GPI5 S_HSYNCCON10.19 GPI0 S_PWDNNUMAKER-HMI-N9H30 USER MANUAL CON10.20 GPI7 S_nRSTCON10.21 GPG2 I2C1_CCON10.22 GPG3 I2C1_DCON10.23 - VSSCON10.24 - VSSTable 2-4 CMOS Sensor Connector (CON10) FunctionNUMAKER-HMI-N9H30 USER MANUAL2.2NuMaker-N9H30 Board - Rear View5V In (CON1)RS-232 DB9 (CON2,CON6)Expand Port (CON7)Speaker Output (J4)Earphone Output (CON4)Buzzer (BZ1)System ResetSW (SW5)SPI Flash (U7,U8)JTAG ICE (J2)Power ProtectionIC (U1)N9H30F61IEC (U5)Micro SD Slot (CON3)RJ45 (CON12, CON13)USB1 HOST (CON15)USB0 Device/Host (CON14)CAN_0 Terminal (CON11)CMOS Sensor Connector (CON9)Power On Setting(SW4, S2~S9)RS-485_6 Terminal (CON5)RTC Battery(BT1)RMII PHY (U14,U16)Figure 2-2 Rear View of NuMaker-N9H30 BoardFigure 2-2 shows the main components and connectors from the rear side of NuMaker-N9H30 board. The following lists components and connectors from the rear view:● +5V In (CON1): Power adaptor 5V input ●JTAG ICE interface (J2) ConnectorGPIO pin of N9H30Function J2.1 - Power 3.3V J2.2 GPJ4 nTRST J2.3 GPJ2 TDI J2.4 GPJ1 TMS J2.5 GPJ0 TCK J2.6 - VSS J2.7 GPJ3 TD0 J2.8-RESETTable 2-5 JTAG ICE Interface (J2) Function●SPI Flash (32 MB) with Winbond W25Q256JVEQ (U7); only one (U7 or U8) SPI Flashcan be used●System Reset (SW5): System will be reset if the SW5 button is pressed●Buzzer (BZ1): Control by GPB3 pin of N9H30●Speaker output (J4): Through the NAU88C22 chip sound output●Earphone output (CON4): Through the NAU88C22 chip sound output●Expand port for user use (CON7):Connector GPIO pin of N9H30 FunctionCON7.1 - Power 3.3VCON7.2 - Power 3.3VCON7.3 GPE12 UART3_TXDCON7.4 GPH4 UART1_TXDCON7.5 GPE13 UART3_RXDCON7.6 GPH5 UART1_RXDCON7.7 GPB0 UART5_TXDCON7.8 GPH6 UART1_RTSCON7.9 GPB1 UART5_RXDCON7.10 GPH7 UART1_CTSCON7.11 GPI1 UART7_TXDNUMAKER-HMI-N9H30 USER MANUAL CON7.12 GPH8 UART4_TXDCON7.13 GPI2 UART7_RXDCON7.14 GPH9 UART4_RXDCON7.15 - -CON7.16 GPH10 UART4_RTSCON7.17 - -CON7.18 GPH11 UART4_CTSCON7.19 - VSSCON7.20 - VSSCON7.21 GPB12 UART10_TXDCON7.22 GPH12 UART8_TXDCON7.23 GPB13 UART10_RXDCON7.24 GPH13 UART8_RXDCON7.25 GPB14 UART10_RTSCON7.26 GPH14 UART8_RTSCON7.27 GPB15 UART10_CTSCON7.28 GPH15 UART8_CTSCON7.29 - Power 5VCON7.30 - Power 5VTable 2-6 Expand Port (CON7) Function●UART0 selection (CON2, J3):–RS-232_0 function and connected to DB9 female (CON2) for debug message output.–GPE0/GPE1 connected to 2P terminal (J3).Connector GPIO pin of N9H30 Function J3.1 GPE1 UART0_RXDJ3.2 GPE0 UART0_TXDTable 2-7 UART0 (J3) Function●UART2 selection (CON6, J6):–RS-232_2 function and connected to DB9 female (CON6) for debug message output –GPF11~14 connected to 4P terminal (J6)Connector GPIO pin of N9H30 Function J6.1 GPF11 UART2_TXDJ6.2 GPF12 UART2_RXDJ6.3 GPF13 UART2_RTSJ6.4 GPF14 UART2_CTSTable 2-8 UART2 (J6) Function●RS-485_6 selection (CON5, J5, SW6~8):–SW6~8: 1-2 short for RS-485_6 function and connected to 2P terminal (CON5 and J5) –SW6~8: 2-3 short for I2S function and connected to NAU88C22 (U10)Connector GPIO pin of N9H30 FunctionSW6:1-2 shortGPG11 RS-485_6_DISW6:2-3 short I2S_DOSW7:1-2 shortGPG12 RS-485_6_ROSW7:2-3 short I2S_DISW8:1-2 shortGPG13 RS-485_6_ENBSW8:2-3 short I2S_BCLKNUMAKER-HMI-N9H30 USER MANUALTable 2-9 RS-485_6 (SW6~8) FunctionPower on setting (SW4, S2~9).SW State FunctionSW4.2/SW4.1 ON/ON Boot from USB SW4.2/SW4.1 ON/OFF Boot from eMMC SW4.2/SW4.1 OFF/ON Boot from NAND Flash SW4.2/SW4.1 OFF/OFF Boot from SPI Flash Table 2-10 Power on Setting (SW4) FunctionSW State FunctionS2 Short System clock from 12MHzcrystalS2 Open System clock from UPLL output Table 2-11 Power on Setting (S2) FunctionSW State FunctionS3 Short Watchdog Timer OFFS3 Open Watchdog Timer ON Table 2-12 Power on Setting (S3) FunctionSW State FunctionS4 Short GPJ[4:0] used as GPIO pinS4Open GPJ[4:0] used as JTAG ICEinterfaceTable 2-13 Power on Setting (S4) FunctionSW State FunctionS5 Short UART0 debug message ONS5 Open UART0 debug message OFFTable 2-14 Power on Setting (S5) FunctionSW State FunctionS7/S6 Short/Short NAND Flash page size 2KBS7/S6 Short/Open NAND Flash page size 4KBS7/S6 Open/Short NAND Flash page size 8KBNUMAKER-HMI-N9H30 USER MANUALS7/S6 Open/Open IgnoreTable 2-15 Power on Setting (S7/S6) FunctionSW State FunctionS9/S8 Short/Short NAND Flash ECC type BCH T12S9/S8 Short/Open NAND Flash ECC type BCH T15S9/S8 Open/Short NAND Flash ECC type BCH T24S9/S8 Open/Open IgnoreTable 2-16 Power on Setting (S9/S8) FunctionCMOS Sensor connector (CON9, SW9~10)–SW9~10: 1-2 short for CAN_0 function and connected to 2P terminal (CON11).–SW9~10: 2-3 short for CMOS sensor function and connected to CMOS sensorconnector (CON9).Connector GPIO pin of N9H30 FunctionCON9.1 - VSSCON9.2 - VSSCON9.3 - Power 3.3VCON9.4 - Power 3.3V NUMAKER-HMI-N9H30 USER MANUALCON9.5 - -CON9.6 - -CON9.7 GPI4 S_PCLKCON9.8 GPI3 S_CLKCON9.9 GPI8 S_D0CON9.10 GPI9 S_D1CON9.11 GPI10 S_D2CON9.12 GPI11 S_D3CON9.13 GPI12 S_D4CON9.14 GPI13 S_D5CON9.15 GPI14 S_D6CON9.16 GPI15 S_D7CON9.17 GPI6 S_VSYNCCON9.18 GPI5 S_HSYNCCON9.19 GPI0 S_PWDNCON9.20 GPI7 S_nRSTCON9.21 GPG2 I2C1_CCON9.22 GPG3 I2C1_DCON9.23 - VSSCON9.24 - VSSTable 2-17 CMOS Sensor Connector (CON9) Function●CAN_0 Selection (CON11, SW9~10):–SW9~10: 1-2 short for CAN_0 function and connected to 2P terminal (CON11) –SW9~10: 2-3 short for CMOS sensor function and connected to CMOS sensor connector (CON9, CON10)SW GPIO pin of N9H30 FunctionSW9:1-2 shortGPI3 CAN_0_RXDSW9:2-3 short S_CLKSW10:1-2 shortGPI4 CAN_0_TXDSW10:2-3 short S_PCLKTable 2-18 CAN_0 (SW9~10) Function●USB0 Device/HOST Micro-AB connector (CON14), where CON14 pin4 ID=1 is Device,ID=0 is HOST●USB1 for USB HOST with Type-A connector (CON15)●RJ45_0 connector with LED indicator (CON12), RMII PHY with IP101GR (U14)●RJ45_1 connector with LED indicator (CON13), RMII PHY with IP101GR (U16)●Micro-SD/TF card slot (CON3)●SOC CPU: Nuvoton N9H30F61IEC (U5)●Battery power for RTC 3.3V powered (BT1, J1), can detect voltage by ADC0●RTC power has 3 sources:–Share with 3.3V I/O power–Battery socket for CR2032 (BT1)–External connector (J1)●Board version 2.1NUMAKER-HMI-N9H30 USER MANUAL2.3 NuDesign-TFT-LCD7 -Front ViewFigure 2-3 Front View of NuDesign-TFT-LCD7 BoardFigure 2-3 shows the main components and connectors from the Front side of NuDesign-TFT-LCD7board.7” resolution 800x480 4-W resistive touch panel for 24-bits RGB888 interface2.4 NuDesign-TFT-LCD7 -Rear ViewFigure 2-4 Rear View of NuDesign-TFT-LCD7 BoardFigure 2-4 shows the main components and connectors from the rear side of NuDesign-TFT-LCD7board.NuMaker-N9H30 and NuDesign-TFT-LCD7 combination connector (CON1).NUMAKER-HMI-N9H30 USER MANUAL 2.5 NuMaker-N9H30 and NuDesign-TFT-LCD7 PCB PlacementFigure 2-5 Front View of NuMaker-N9H30 PCB PlacementFigure 2-6 Rear View of NuMaker-N9H30 PCB PlacementNUMAKER-HMI-N9H30 USER MANUALFigure 2-7 Front View of NuDesign-TFT-LCD7 PCB PlacementFigure 2-8 Rear View of NuDesign-TFT-LCD7 PCB Placement3 NUMAKER-N9H30 AND NUDESIGN-TFT-LCD7 SCHEMATICS3.1 NuMaker-N9H30 - GPIO List CircuitFigure 3-1 shows the N9H30F61IEC GPIO list circuit.Figure 3-1 GPIO List Circuit NUMAKER-HMI-N9H30 USER MANUAL3.2 NuMaker-N9H30 - System Block CircuitFigure 3-2 shows the System Block Circuit.NUMAKER-HMI-N9H30 USER MANUALFigure 3-2 System Block Circuit3.3 NuMaker-N9H30 - Power CircuitFigure 3-3 shows the Power Circuit.NUMAKER-HMI-N9H30 USER MANUALFigure 3-3 Power Circuit3.4 NuMaker-N9H30 - N9H30F61IEC CircuitFigure 3-4 shows the N9H30F61IEC Circuit.Figure 3-4 N9H30F61IEC CircuitNUMAKER-HMI-N9H30 USER MANUAL3.5 NuMaker-N9H30 - Setting, ICE, RS-232_0, Key CircuitFigure 3-5 shows the Setting, ICE, RS-232_0, Key Circuit.NUMAKER-HMI-N9H30 USER MANUALFigure 3-5 Setting, ICE, RS-232_0, Key Circuit3.6 NuMaker-N9H30 - Memory CircuitFigure 3-6 shows the Memory Circuit.NUMAKER-HMI-N9H30 USER MANUALFigure 3-6 Memory Circuit3.7 NuMaker-N9H30 - I2S, I2C_0, RS-485_6 CircuitFigure 3-7 shows the I2S, I2C_0, RS-486_6 Circuit.NUMAKER-HMI-N9H30 USER MANUALFigure 3-7 I2S, I2C_0, RS-486_6 Circuit3.8 NuMaker-N9H30 - RS-232_2 CircuitFigure 3-8 shows the RS-232_2 Circuit.NUMAKER-HMI-N9H30 USER MANUALFigure 3-8 RS-232_2 Circuit3.9 NuMaker-N9H30 - LCD CircuitFigure 3-9 shows the LCD Circuit.NUMAKER-HMI-N9H30 USER MANUALFigure 3-9 LCD Circuit3.10 NuMaker-N9H30 - CMOS Sensor, I2C_1, CAN_0 CircuitFigure 3-10 shows the CMOS Sensor,I2C_1, CAN_0 Circuit.NUMAKER-HMI-N9H30 USER MANUALFigure 3-10 CMOS Sensor, I2C_1, CAN_0 Circuit3.11 NuMaker-N9H30 - RMII_0_PF CircuitFigure 3-11 shows the RMII_0_RF Circuit.NUMAKER-HMI-N9H30 USER MANUALFigure 3-11 RMII_0_PF Circuit3.12 NuMaker-N9H30 - RMII_1_PE CircuitFigure 3-12 shows the RMII_1_PE Circuit.NUMAKER-HMI-N9H30 USER MANUALFigure 3-12 RMII_1_PE Circuit3.13 NuMaker-N9H30 - USB CircuitFigure 3-13 shows the USB Circuit.NUMAKER-HMI-N9H30 USER MANUALFigure 3-13 USB Circuit3.14 NuDesign-TFT-LCD7 - TFT-LCD7 CircuitFigure 3-14 shows the TFT-LCD7 Circuit.Figure 3-14 TFT-LCD7 CircuitNUMAKER-HMI-N9H30 USER MANUAL4 REVISION HISTORYDate Revision Description2022.03.24 1.00 Initial version NUMAKER-HMI-N9H30 USER MANUALNUMAKER-HMI-N9H30 USER MANUALImportant NoticeNuvoton Products are neither intended nor warranted for usage in systems or equipment, anymalfunction or failure of which may cause loss of human life, bodily injury or severe propertydamage. Such applications are deemed, “Insecure Usage”.Insecure usage includes, but is not limited to: equipment for surgical implementation, atomicenergy control instruments, airplane or spaceship instruments, the control or operation ofdynamic, brake or safety systems designed for vehicular use, traffic signal instruments, all typesof safety devices, and other applications intended to support or sustain life.All Insecure Usage shall be made at customer’s risk, and in the event that third parties lay claimsto Nuvoton as a result of customer’s Insecure Usage, custome r shall indemnify the damagesand liabilities thus incurred by Nuvoton.。
downloadthis 0.3.3 用户指南说明书
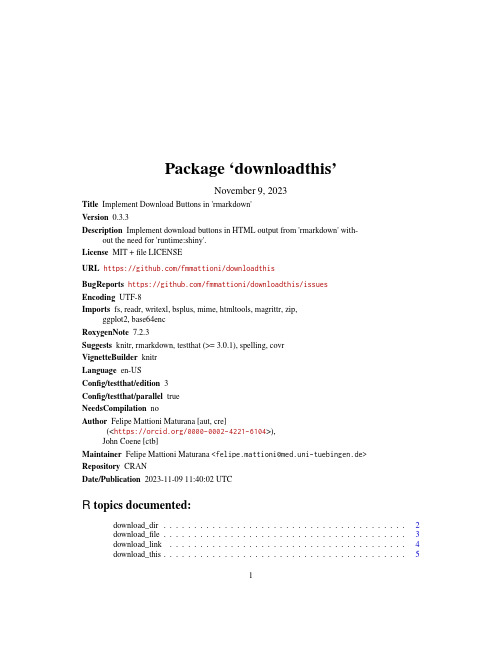
Package‘downloadthis’November9,2023Title Implement Download Buttons in'rmarkdown'Version0.3.3Description Implement download buttons in HTML output from'rmarkdown'with-out the need for'runtime:shiny'.License MIT+file LICENSEURL https:///fmmattioni/downloadthisBugReports https:///fmmattioni/downloadthis/issuesEncoding UTF-8Imports fs,readr,writexl,bsplus,mime,htmltools,magrittr,zip,ggplot2,base64encRoxygenNote7.2.3Suggests knitr,rmarkdown,testthat(>=3.0.1),spelling,covrVignetteBuilder knitrLanguage en-USConfig/testthat/edition3Config/testthat/parallel trueNeedsCompilation noAuthor Felipe Mattioni Maturana[aut,cre](<https:///0000-0002-4221-6104>),John Coene[ctb]Maintainer Felipe Mattioni Maturana<*********************************.de>Repository CRANDate/Publication2023-11-0911:40:02UTCR topics documented:download_dir (2)download_file (3)download_link (4)download_this (5)12download_dir Index8 download_dir Download a directoryDescriptionThe path is converted into a.zipfile.Usagedownload_dir(path,output_name,button_label="Download data",button_type=c("default","primary","success","info","warning","danger"), has_icon=TRUE,icon="fa fa-save",self_contained=FALSE,...)Argumentspath Path to directory.output_name Name of of the outputfile.button_label Character(HTML),button labelbutton_type Character,one of the standard Bootstrap typeshas_icon Specify whether to include fontawesome icons in the button labelicon Fontawesome tag e.g.:"fa fa-save"self_contained A boolean to specify whether your HTML output is self-contained.Default to FALSE....attributes(named arguments)and children(unnamed arguments)of the button, passed to htmltools::tag().Valuehtmltools::tag,<button>Examples##Not run:##Directory path as an exampledownload_dir(path=system.file("assets",package="downloadthis"),output_name="example dir",button_label="Download directory",download_file3 button_type="success",has_icon=TRUE,icon="fa fa-save",self_contained=FALSE)##End(Not run)download_file Download a localfile or multiplefilesDescriptionIn case multiplefiles are chosen,thefiles will be converted to a.zipfile.Usagedownload_file(path,output_name,button_label="Download data",button_type=c("default","primary","success","info","warning","danger"), has_icon=TRUE,icon="fa fa-save",self_contained=FALSE,...)Argumentspath Path to thefile(s).If multiplefiles are chosen,a vector must be passed to this argument.output_name Name of of the outputfile.If not specified,it will take the sourcefile’s name if onefile is specified.In case of multiplefiles,the output_name must be speci-fied.button_label Character(HTML),button labelbutton_type Character,one of the standard Bootstrap typeshas_icon Specify whether to include fontawesome icons in the button labelicon Fontawesome tag e.g.:"fa fa-save"self_contained A boolean to specify whether your HTML output is self-contained.Default to FALSE....attributes(named arguments)and children(unnamed arguments)of the button, passed to htmltools::tag().Valuehtmltools::tag,<button>4download_linkExamples##Not run:##One file exampledownload_file(path=system.file("assets/css/all.min.css",package="downloadthis"),output_name="CSS file from downloadthis",button_label="Download css file",button_type="danger",has_icon=TRUE,icon="fa fa-save",self_contained=FALSE)##Multiple files examplepath_files<-list.files(path=system.file("assets/css",package="downloadthis"),s=TRUE)download_file(path=path_files,output_name="Files from downloadthis",button_label="Download files",button_type="danger",has_icon=TRUE,icon="fa fa-save",self_contained=FALSE)##End(Not run)download_link Downloadfile from a web addressDescriptionIt associates your download button to a web link.This might be an alternative when yourfile is too big for being handled by download_this().Usagedownload_link(link,button_label="Download data",button_type=c("default","primary","success","info","warning","danger"), has_icon=TRUE,icon="fa fa-save",self_contained=FALSE,...)Argumentslink A web address for downloadthing thefile.button_label Character(HTML),button labelbutton_type Character,one of the standard Bootstrap typeshas_icon Specify whether to include fontawesome icons in the button labelicon Fontawesome tag e.g.:"fa fa-save"self_contained A boolean to specify whether your HTML output is self-contained.Default to FALSE....attributes(named arguments)and children(unnamed arguments)of the button, passed to htmltools::tag().Valuehtmltools::tag,<button>Examples##Not run:##Link in Github repodownload_link(link="https:///fmmattioni/downloadthis/raw/master/inst/example/file_1.pdf", button_label="Download pdf file",button_type="danger",has_icon=TRUE,icon="fa fa-save",self_contained=FALSE)##End(Not run)download_this Download data frames,lists,or any R objectDescriptionWrapper around bsplus::bs_button()to provide a download button for HTML outputs in R Markdown.Internally,the function writes thefile to tempdir(),encodes it,and produces the down-load button.Currently,Internet Explorer does not support downloading embeddedfiles.For down-loading links,files,or directories,see download_link(),download_file(),and download_dir().Usagedownload_this(.data,...,output_name=NULL,output_extension=c(".csv",".xlsx",".rds"),button_label="Download data",button_type=c("default","primary","success","info","warning","danger"),icon="fa fa-save",self_contained=FALSE,csv2=TRUE,ggsave_args=list())Arguments.data A data frame or(named)list to write to disk.See’Examples’for more details....attributes(named arguments)and children(unnamed arguments)of the button,passed to htmltools::tag().output_name Name of of the outputfile,if NULL uses the deparsed.data object.output_extensionExtension of the outputfile.Currently,.csv,.xlsx,and.rds are supported.Ifa(named)list is passed to the function,only.xlsx and.rds are supported.button_label Character(HTML),button labelbutton_type Character,one of the standard Bootstrap typesicon Fontawesome tag e.g.:"fa fa-save",set to NULL toself_contained A boolean to specify whether your HTML output is self-contained.Default toFALSE.csv2A boolean to specify whether to use readr::write_csv2()in case the output_extension is chosen as’.csv’.If FALSE,readr::write_csv()will be used instead.De-fault to TRUE.ggsave_args List of arguments to pass to ggplot2::ggsave,e.g.:list(height=5).Valuehtmltools::tag,<button>WarningThis example will write the mtcars dataset to tempdir()and produce the download button for thefile mtcars dataset.csv with the fa fa-save icon on the Download data label.Examples##Not run:#Passing a data frame to the functionmtcars%>%download_this(output_name="mtcars dataset",output_extension=".csv",button_label="Download data",button_type="warning",has_icon=TRUE,icon="fa fa-save")#Passing a list with data frames to the functionlist(mtcars,iris)%>%download_this(output_name="mtcars and iris datasets",output_extension=".xlsx",button_label="Download data",button_type="warning",has_icon=TRUE,icon="fa fa-save")#Passing a named list with data frames to the functionlist("mtcars dataset"=mtcars,"iris dataset"=iris)%>% download_this(output_name="mtcars and iris datasets",output_extension=".xlsx",button_label="Download data",button_type="warning",has_icon=TRUE,icon="fa fa-save")#Passing any R object to the functionvector_example<-1:10linear_model<-lm(mpg~gear,data=mtcars)list(mtcars,iris,vector_example,linear_model)%>%download_this(output_name="datasets,vector,and linear model",output_extension=".rds",button_label="Download as rds",button_type="warning",has_icon=TRUE,icon="fa fa-save")##End(Not run)Indexdownload_dir,2download_file,3download_link,4download_this,5tag,2,3,5,68。
B066 全尺寸折叠蓝牙键盘 说明书

B066全尺寸折叠蓝牙键盘说明书注惫:正确操作本产品,请仔细阅读用户手册., 1�::::�1:n一”.干口,店..支持系统Wi n/iOS/ A ndroid系统切换Fn+Q 切换iOS系统Fn+W切换Android系统Fn+E 切换W in系统• iOS系统连接使用说明:• Win10系统连接使用说明:• And roid系统连接使用说明:二二,.......,...,..L话打开键盘电源开关,蓝色灯亮起,二-沃王翠选对码模式,按Fn+C对码蓝灯闪烁进入选择洹逢,按Fn+C对码监灯闪烁进入选对码通模道式,,按Fn+C对廿纽砂丁闪灼o!IA对码模式u I巨,=·-一I 2. 在蓝开牙始如,进阳行而搜索造模式',约却开< 2打开牙“进M毁尽模式.O-;a---wI今• 气,俨I 3. 峦刮殴备皿择“蓝牙·,进行搜索.. I ,. I""'—芷,二,.....,__,_1111111.�,,._,.回Q•心一真气阔袋之·二,玉四"Bluetoot h5 1 K可board"然后点击配对名连接a e--• 1 • Ill一0 .. -然后点击配对名连接O夏...宜牙' C.·暮.,, ... ,», 删”“,已孟棒·以为叫曾..行官4提示连接配对成功,您就可以舒适地使用您的健盘了_5, 提示诈符成功,你就可以舒适地使用仿的键盘了.4提,连接配对成功,您就可以舒适地使用您的键盘了注酌寸成功切舌下次使用只凳卧J开监才售盘电源及使用设岱的蓝牙,蓝牙售盘将会自动搜索1车梓十次使用过的设备,不需要再进行配对操作,产品功能!OS/Android Windows Windows直接按对应功能Fn+ 对应功能直接按对应功能Esc 返回桌面E,c 主页Esc Esc仑仑仑F1a_ 搜索F1a_ 搜索F1a_ FlF2Eij 全选F2问全选F2百F2F3� 复制F3Cl! 复制F3QJ F3F4困粘贴F4\31 粘贴F4\3) F4F5X, 剪切F5i 剪切F5.4, FSF6 上—曲Fti 上—曲•• F6, ,田F7 暂停闱磁F7 暂停序砬t F7 F71>11�II�IIF8 下一曲F B 下一曲F8 FB田田田F9 llfl,c 静音F9 .i x 雌F9 tlll x F9F10Ill 音量高」、F10呵)吉量减小F10`) FlOF11q汹旮三增人,,, 心旮三l曾入F11 心F llF12丛锁屏F12Ii 锁F12 Iii F12三系统切换语言:Windows: Alt+Shilt 邯奂语言Android : Shilt+空格键切换语言iOS: Ctrl+空格键切换语言技术规格触控板功能说明(iOS13.4.1以上),须切换到iOS系统键盘尺寸:342.35x114.7x10.9 mm(打开)182.25x114.7x19.5 mm(折叠)使用触摸板工作电流:<11 m A使用按键工作电流:<4mA工作距离:10m锤电池容盘:140 m Ah工作电压:3.7V触拉板功能说明(WindowslO),须切涣到Win dows忠充m畔妇邸左键II XillU:l'�--• =lll,/;$-b“器芦忒窗口m二指向下扫-皿桌面触摸板尺寸:56.1 x45.1 mm铸斋军乐:222 g待机电流:<1 mA休眠电流:17�A休眠时间:10分钟唤醒方式按健唤醒"Iii大右放--nt标-e,g换ig-i击开击廿荒点分小一i鲸E点杠杠笘器器mEEEEm汇m翌匮===m芒七,")鄱冒芯氐111�==-m芷R====-“兰DI烹王窗口,可丐千出,可5于自定义的方法:设至-辅助功能-触控-辅助触控-设备-点击键盘配对名,然后对单指点凡指点/三指点击进行功能自定义.触拉板功能说阻(Android).须切换到Android系统i_键缸g泗mmm双指点击-返回上页m单捂移动光标沿动状态显示LE D·对码.打开电源开关,蓝牙指示幻蓝灯亮起,按下对码盐,蓝灯闪烁屯电指和红色,充词汀灭·低电压指示.当刮玉低千3.3V,红色指示灯闪烁多通道连接·连接第五时,先按Fn+�1, 再按Fn+C对码,开始连接·连接第2个设备前,先按一次Fn+�2, 再按Fn+C对码,开始连接·连接第3个设备前,先按一次Fn+I勾3• 再按Fn+C对码,开始连接·在多个设备同时使用,按Fn+书11/和心3切换,即可自由切换到已连接的设备故障分析请与售后服务人员联系知识产权信息未经本司的许可,禁止复制本用户手册的内容.安全提醒诘不要打开或修理该设备,谘不要在潮渥环境内使用设备,话用干布擦拭该设备质保条歆本设备自购买之日起,提供1年保修服务键盘保养l、诮勿将设备暴需在液体和潮湿的环境中或使其淋雨,清勿在浴缸髦水槽、桑拿房、游泳池或蒸汽房附近使用.2、清勿将设备暴露于过高或过低的温度下.3、满勿长时间放盗在阳光直射的地方.4、请勿靠近阴火如烹任用炉、蜡烛或者壁炉.5、避免使用锋利器物刮擦产品,及时给产品进行充电以保证正常使用.常见间题解答1, 平板无法连接蓝牙键盘?1)请或诏囡粒妇有进入酌寸状态然后卧可刊顷嘻妞讶搜索设备进行连接.2)检查蓝牙键盘电昼是否充足,电丞不足也会导致无法连接,请将蓝牙键盘充电后再使用.2、键盘扑坊寸在使用途中一直闪烁?键盘指示灯在使用途中一直闪烁,表示电池即将没电,请尽快将键盘充电.3, 设备显示蓝牙键盘断开连接酌砬在顷时间内不使用,设备为了省暇芍自动关闭崖才坊能,按键盘任意键唤醒蓝牙连接自动恢复.保修卡用户填写资料公司或个人全称通讯地址电话所购产品名称及型号购买曰期邮缠,',',',..,','4证·咯�^ii)`连地.呕g二:醴妇缸5.,m�芒g见�,公时甩兰*戏}磕误不非情·呈l止·g心()有123本(((“K·',','B066Bluetooth keyboardUser' s ManualNote: Please read the user manual care u lly b efore you startus;ng th;, product丿勹『Compatible SystemWin /iOS /AndroidSystem switchingFn+Q iOS Fn+W Android Fn+E Win• iOS Connection Instructions:二巴芒芯""'=它::孟:::'.岫.二三飞2竺“二:c畔""'81�toolh"'""'_.,,••心·。
KS8863MLL_FLL_RLL_DEMO_BOARD_V1-201203
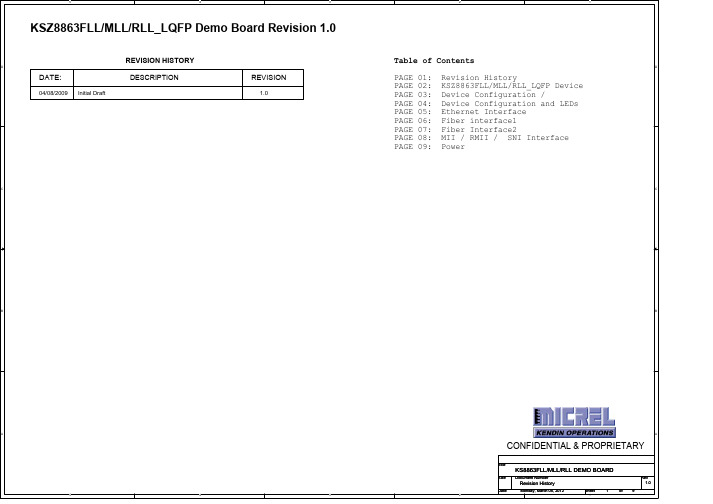
7 7
7 7
J13
1
2
3
4
CON4A
Test Mode,4V
Ext_V2 R12 4.7K
FXSD2
7
+3.3A
Force FX Mode R8
4.7K
JP77
FXSD2
1
2
3
4
5
6
7
8
R9
B
Do not populate
HEADER 4X2
TX Mode
1K
cap if pull down
is used
SCL_MDC INTRN SCRS3 SCOL3 VDDC GND
SMRXC3 SMRXD30 SMRXD31 SMRXD32 SMRXD33 SMRXDV3
C 6
3,4
SPIQ
3
SPISN
4
P1LED1
4
P1LED0
3,4
P2LED1
3,4
P2LED0
1-2 for FLL, 3-4 for MLL/RLL J12
SMRXDV3
2,8
R131 1K
+3.3V
+3.3V
JP103
1 2
B
3
3X1
R106 4.7K
P1LED1
R114 1K
2
JP104
1 2
3
3X1
R107 4.7K
P1LED0
2
R115 1K
PORT 2
+3.3V
+3.3V
JP201
1 2
3
3X1
R111 4.7K
美的小子弹相机硬件说明书 A310、A311 2020 01 02

Mini Bullet Camera Hardware ManualA310, A3112020/01/02Table of ContentsPrecautions 3 Safety Instructions (5)Introduction 6List of Models (6)Package Contents (7)Physical Description (8)Installation Procedures 9Step 1: Install the Camera (9)Step 2: Waterproof and Connect the Cable(s) (11)Using the Cable Gland (11)Using an Optional Power Adapter (13)Step 3: Connect to Network (14)Step 4: Access the Camera Live View (14)Other Accessories 15 How to Install / Remove the Memory Card (15)Accessing the Camera 16Configure the IP Addresses (16)Using DHCP Server to Assign IP Addresses (16)Using the Default Camera IP Address (18)Access the Camera (22)PrecautionsRead these instructionsRead all the safety and operating instructions before using this product.Heed all warningsAdhere to all the warnings on the product and in the instruction manual. Failure to follow the safety instructions given may directly endanger people, cause damage to the system or to other equipment.ServicingDo not attempt to service this product yourself as opening or removing covers may expose you to dangerous voltage or other hazards. Refer all servicing to qualified service personnel.TrademarksACTi and ACTi logo are registered trademarks of ACTi Corporation. All other names and products used in this manual are registered trademarks of their respective companies.LiabilityEvery reasonable care has been taken during the writing of this manual. Please inform your local office if you find any inaccuracies or omissions. ACTi will not be held responsible for any typographical or technical errors and reserves the right to make changes to the product and manuals without prior notice.Federal Communications Commission StatementThis equipment has been tested and found to comply with the limits for aclass B digital device, pursuant to Part 15 of the FCC Rules. These limits aredesigned to provide reasonable protection against harmful interference in a residential installation. This equipment generates, uses, and can radiate radio frequency energy and, if not installed and used in accordance with the instructions, may cause harmful interference to radio communications. However, there is no guarantee that interference will not occur in a particular installation. If this equipment does cause harmful interference to radio or television reception, which can be determined by turning the equipment off and on, the user is encouraged to try to correct the interference by one or more of the following measures: ∙Reorient or relocate the receiving antenna.∙Increase the separation between the equipment and receiver.∙Connect the equipment into an outlet on a circuit different from that to which the receiver is connected.∙Consult the dealer or an experienced radio/TV technician for help.Warning: Changes or modifications to the equipment that are not expressly approved by the responsible party for compliance could void the user’s authority to operate the equipment.European Community Compliance StatementThis product has been tested and found to comply with the limits for Class BInformation Technology Equipment according to European Standard EN 55022 and EN 55024. In a domestic environment, this product may cause radio interference in which cause the user may be required to take adequate measures.Safety InstructionsCleaningDisconnect this product from the power supply before cleaning.Accessories and Repair PartsUse only the accessories and repair parts recommended by the manufacturer. Using other attachments not recommended by the manufacturer may cause hazards.Water and MoistureInstall other devices (such as PoE injector, alarm, etc.) that will be used with the camera in a dry place protected from weather.ServicingDo not attempt to service this product yourself. Refer all servicing to qualified service personnel.Damage Requiring serviceDisconnect this product from the power supply immediately and refer servicing to qualified service personnel under the following conditions.1) When the power-supply cord or plug is damaged2) If liquid has been spilled, or objects have fallen into the product.3) If the inner parts of product have been directly exposed to rain or water.4) If the product does not operate normally even by following the operating instructions in thismanual. Adjust only those controls that are covered by the instruction manual, as improper adjustment of other controls may result in damage, and will often require extensive work by a qualified technician to restore the product to its normal operation.Safety CheckUpon completion of any service or repairs to this product, ask the service technician to perform safety checks to determine if the product is in proper operating condition.IntroductionList of ModelsThis hardware manual contains the following models:4MP Mini Bullet with D/N, Adaptive IR, Extreme WDR, SLLS,Fixed lens6MP Mini Bullet with D/N, Adaptive IR, Superior WDR, SLLS,Fixed lensPackage ContentsPhysical DescriptionInstallation ProceduresStep 1: Install the Camera1. Mark the screw holes or attach the bundled drill template on the target surface.NOTE: Depending on the surface where you will install the camera, it may be necessary to drill three (3) holes and use the supplied screw tox.2. If the cable will pass through the surface, drill the cable hole within the radius of thecamera bracket. If the cable will be routed along the surface, route the cable through the gap on the bracket.3. Mount the camera to the surface using the three (3) screws.4. Loosen the knob to adjust the camera tilt and orientation. The camera can be panned bytwisting the bracket stem.5. Adjust the camera angle and orientation.Sample of Wall Installation6. Tighten the knob and the set screw to fix the tilt angle position.orStep 2: Waterproof and Connect the Cable(s)If the camera will be installed indoors, simply connect the network side cable to the camera Ethernet port.However, if the camera will be installed outdoors, ensure that the cable connections and the network side cable itself are also protected from water and other environmental factors. Use the bundled cable gland for the Ethernet connector and use waterproof tape to protect the other cable connection.Using the Cable GlandThis section describes how to waterproof the cable-out or “pigtail” of the camera using the bundled cable gland. Before connection, prepare an exterior-grade Ethernet cable with RJ-45 connector.Perform the following to waterproof the “pigtail” using the cable gland: 1. Attach the washer to the Ethernet connector of the camera.2. Detach the clamping nut and sealing insert from the gland body:Gland BodyClamping NutSealing Insert3.Insert the clamping nut into the Ethernet cable.4.Insert the sealing insert through the Ethernet cable.5.Insert the cable through the gland body.6.Push the sealing insert into the gland body.7.Connect the RJ-45 connector to the camera connector.8.Attach the gland body to the camera connector.9.Attach the clamping nut to the gland body to complete the cable solution.NOTE: Make sure the clamping nut is tightly attached to the cable gland body and the sealing insert is squeezed tightly.Using an Optional Power AdapterThe camera can be powered by a Power over Ethernet (PoE) switch that is IEEE802.3af compliant. In case of using a non-PoE switch or your PoE switch has a limited power supply, you can purchase a power adapter and directly connect the camera to a power outlet. NOTE: The power adapter is not bundled in the package.After connecting the power adapter, waterproof the cable connection by using waterproof tape.Step 3: Connect to NetworkConnect the other end of the network cable to a PoE switch or injector. Then, connect the switch or injector to a network, PC, and a power source. See Power-over-Ethernet (PoE) connection example below.PoE Injector / Switch Power CableEthernet CableCameraStep 4: Access the Camera Live ViewAfter making the connections, access the camera live view to adjust the viewing angle of the camera and configure the settings according to your preference. See Accessing the Camera on page 16 for more information.Other AccessoriesHow to Install / Remove the Memory Carding the bundled wrench, loosen the two (2) screws to remove the cover.2.Push the microSD card into the memory card slot with the metal contacts facing thelens.3.Secure the two (2) screws to attach the cover. Make sure the rubber on the cover is inplace.Accessing the CameraConfigure the IP AddressesIn order to be able to communicate with the camera from your PC, both the camera and the PC have to be within the same network segment. In most cases, it means that they both should have very similar IP addresses, where only the last number of the IP address is different from each other. There are 2 different approaches to IP Address management in Local Area Networks – by DHCP Server or Manually.Using DHCP Server to Assign IP AddressesIf you have connected the computer and the camera into the network that has a DHCP server running, then you do not need to configure the IP addresses at all – both the camera and the PC would request a unique IP address from DHCP server automatically. In such case, the camera will immediately be ready for the access from the PC. The user, however, might not know the IP address of the camera yet. It is necessary to know the IP address of the camera in other to be able to access it by using a Web browser.The quickest way to discover the cameras in the network is to use the simplest network search, built in the Windows system –just by pressing the “Network” icon, all the cameras of the local area network will be discovered by Windows thanks to the UPnP function support of our cameras.In the example below, we successfully found the camera model that we had just connected to the network.By double-clicking with the left mouse on the camera model, it is possible to automatically launch the default browser of the PC with the IP address of the target camera filled in the address bar of the browser already.If you work with our cameras regularly, then there is even a better way to discover the cameras in the network– by using IP Utility. The IP Utility is a light software tool that can not only discover the cameras, but also list lots of valuable information, such as IP and MAC addresses, serial numbers, firmware versions, etc, and allows quick configuration of multiple devices at the same time.The IP Utility can be downloaded for free from /IP_UtilityWith just one click, you can launch the IP Utility and there will be an instant report as follows:You can quickly see the camera model in the list. Click on the IP address to automatically launch the default browser of the PC with the IP address of the target camera filled in the address bar of the browser already.Using the Default Camera IP AddressIf there is no DHCP server in the given network, the user may have to assign the IP addresses to both PC and camera manually to make sure they are in the same network segment.When the camera is plugged into network and it does not detect any DHCP services, it will automatically assign itself a default IP:192.168.0.100Whereas the default port number would be 80. In order to access that camera, the IP address of the PC has to be configured to match the network segment of the camera.Manually adjust the IP address of the PC:In the following example, based on Windows 7, we will configure the IP address to192.168.0.99 and set Subnet Mask to 255.255.255.0 by using the steps below:1 23 4Manually adjust the IP addresses of multiple cameras:If there are more than 1 camera to be used in the same local area network and there is no DHCP server to assign unique IP addresses to each of them, all of the cameras would then have the initial IP address of 192.168.0.100, which is not a proper situation for network devices – all the IP addresses have to be different from each other. The easiest way to assign cameras the IP addresses is by using IP Utility:With the procedure shown above, all the cameras will have unique IP addresses, starting from 192.168.0.101. In case there are 20 cameras selected, the last one of the cameras would have the IP 192.168.0.120.Later, by pressing the “Refresh” button of the IP Utility, you will be able to see the list of cameras with their new IP addresses.Please note that it is also possible to change the IP addresses manually by using the Web browser. In such case, please plug in only one camera at a time, and change its IP address by using the Web browser before plugging in the next one. This way, the Web browser will not be confused about two devices having the same IP address at the same time.Access the CameraNow that the camera and the PC are both having their unique IP addresses and are under the same network segment, it is possible to use the Web browser of the PC to access the camera.You can use Microsoft Internet Explorer to access the camera.When using Internet Explorer browser, the ActiveX control for video stream management will be downloaded from the camera directly – the user just has to accept the use of such control when prompted so. No other third party utilities are required to be installed in such case.Hardware Manual21The following examples in this manual are based on Internet Explorer browser in order to cover all functions of the camera.Assuming that the camera’s IP address is 192.168.0.100, you can access it by opening the Web browser and typing the following address into Web browser’s address bar:http://192.168.0.100Upon successful connection to the camera, the user interface called Web Configurator would appear together with the login page. The HTTP port number was not added behind the IP address since the default HTTP port of the camera is 80, which can be omitted from the address for convenience.When you login, you will be asked to set a password. Follow the on-screen instructions to continue.Copyright © 2019, ACTi Corporation All Rights Reserved7F, No. 1, Alley 20, Lane 407, Sec. 2, Ti-Ding Blvd., Neihu District, Taipei, Taiwan 114, R.O.C.TEL : +886-2-2656-2588 FAX : +886-2-2656-2599Email:**************。
Mitsubishi Electric FX3U FX3UC系列用户操作手册-模拟控制版说明书
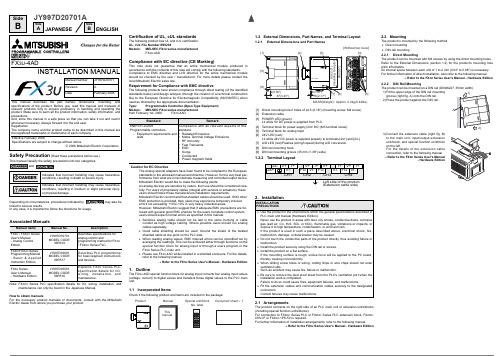
SideBSideASideBJAPANESEENGLISHJY997D20701ASafety Precaution (Read these precautions before use.)linked to serious results.In any case, it is important to follow the directions for usage.Associated ManualsNote:FX 3UC Series PLC specification details for I/O, wiring, installation, andmaintenance can only be found in the Japanese Manual.How to obtain manualsFor the necessary product manuals or documents, consult with the Mitsubishi Electric dealer from where you purchase your product.Manual name Manual No.DescriptionFX 3U / FX 3UC Series User's Manual - Analog Control EditionJY997D16701MODEL CODE:09R619Describes specifications for analog control andprogramming method for FX 3U / FX 3UC Series PLC.FX 3U /FX 3UC Series Programming Manual - B a s i c & A p p l i ed Instruction Edition JY997D16601MODEL CODE:09R517Describes PLC programming for basic/applied instructions and devices.FX 3U Series User’s Manual - Hardware EditionJY997D16501MODEL CODE:09R516Explains FX 3U Series PLC specification details for I/O,w i r i n g , i ns ta l l a t i o n , a n dmaintenance.Certification of UL, cUL standardsThe following product has UL and cUL certification.UL, cUL File Number:E95239Models:MELSEC FX 3U series manufacturedFX 3U -4ADCompliance with EC directive (CE Marking)This note does not guarantee that an entire mechanical module produced in accordance with the contents of this note will comply with the following standards.Compliance to EMC directive and LVD directive for the entire mechanical module should be checked by the user / manufacturer. For more details please contact the local Mitsubishi Electric sales site.Requirement for Compliance with EMC directiveThe following products have shown compliance through direct testing (of the identified standards below) and design analysis (through the creation of a technical construction file) to the European Directive for Electromagnetic Compatibility (89/336/EEC) when used as directed by the appropriate documentation.Type:Programmable Controller (Open Type Equipment)Models:MELSEC FX 3U series manufactured from February 1st, 2006FX 3U -4ADCaution for EC DirectiveThe analog special adapters have been found to be compliant to the European standards in the aforesaid manual and directive. However, for the very best per-formance from what are in fact delicate measuring and controlled output device Mitsubishi Electric would like to make the following points;As analog devices are sensitive by nature, their use should be considered care-fully. For users of proprietary cables (integral with sensors or actuators), these users should follow those manufacturers installation requirements.Mitsubishi Electric recommend that shielded cables should be used. If NO other EMC protection is provided, then users may experience temporary induced errors not exceeding +10%/-10% in very heavy industrial areas.However, Mitsubishi Electric suggest that if adequate EMC precautions are fol-lowed with general good EMC practice for the users complete control system, users should expect normal errors as specified in this manual.•Sensitive analog cable should not be laid in the same trunking or cable conduit as high voltage cabling. Where possible users should run analog cables separately.•Good cable shielding should be used. Ground the shield of the twisted shielded cable at one point on the PLC side.•When reading analog values, EMC induced errors can be smoothed out by averaging the readings. This can be achieved either through functions on the special function block for analog input or through a users program in the FX 3U Series PLC main unit.•Please use FX 3U -4AD while installed in a shielded enclosure. For the details,refer to the following manual.→ Refer to the FX 3U Series User's Manual - Hardware Edition1.OutlineThe FX 3U -4AD special function block for analog input converts four analog input values (voltage, current) to digital values and transfers those digital values to the PLC main unit.1.1Incorporated ItemsCheck if the following product and items are included in the package:StandardRemarkEN61131-2:2003Programmable controllers-Equipment requirements and testsCompliance with all relevant aspects of the standard.•Radiated Emissions•Mains Terminal Voltage Emissions •RF immunity •Fast Transients •ESD •Surge•Conducted•Power magnetic fields1.2External Dimensions, Part Names, and Terminal Layout1.2.1External Dimensions and Part Names1.2.2Terminal Layout2.Installation2.1ArrangementsThe product connects on the right side of an PLC main unit or extension units/blocks (including special function units/blocks).For connection to FX 3UC Series PLC or FX 2NC Series PLC extension block, FX 2NC -CNV-IF or FX 3UC -1PS-5V is required.For further information of installation arrangements, refer to the following manual.→ Refer to the FX 3U Series User's Manual - Hardware Edition[1]Direct mounting hole:2 holes of φ4.5 (0.18") (mounting screw: M4 screw)[2]Extension cable[3]POWER LED (green):Lit while 5V DC power is supplied from PLC.[4]Terminal block for power supply (24V DC) (M3 terminal screw)[5]Terminal block for analog input [6]24V LED (red):Lit while 24V DC power is supplied properly to terminals [24+] and [24-].[7]A/D LED (red):Flashes (at high speed) during A/D conversion. [8]DIN rail mounting hook[9]DIN rail mounting groove (35 mm (1.38") wide)INSTALLATION PRECAUTIONS•Use the product in the environment within the general specifications described in PLC main unit manual (Hardware Edition).Never use the product in areas with dust, oily smoke, conductive dusts, corrosive gas (salt air, Cl 2, H 2S, SO 2, or NO 2), flammable gas, vibrations or impacts, or expose it to high temperature, condensation, or wind and rain.If the product is used in such a place described above, electrical shock, fire,malfunction, damage, or deterioration may be caused.•Do not touch the conductive parts of the product directly, thus avoiding failure or malfunction.•Install the product securely using the DIN rail or screws.•Install the product on a flat surface.If the mounting surface is rough, undue force will be applied to the PC board,thereby causing nonconformity.•When drilling screw holes or wiring, cutting chips or wire chips should not enter ventilation slits.Such an accident may cause fire, failure or malfunction.•Be sure to remove the dust proof sheet from the PLC's ventilation port when the installation work is completed.Failure to do so could cause fires, equipment failures, and malfunctions.•Fit the extension cables and communication cables securely to the designated connectors.Contact failures may cause malfunctions.2.2MountingThe product is mounted by the following method. •Direct mounting •DIN rail mounting2.2.1Direct MountingThe product can be mounted with M4 screws by using the direct mounting holes.Refer to the External Dimensions (section 1.2) for the product’s mounting hole pitch information.An interval space between each unit of 1 to 2 mm (0.04" to 0.08") is necessary. For further information of direct installation, also refer to the following manual.→ Refer to the FX 3U Series User's Manual - Hardware Edition2.2.2DIN Rail MountingThe product can be mounted on a DIN rail (DIN46227, 35mm width).1)Fit the upper edge of the DIN rail mounting groove (right fig. A) onto the DIN rail. 2)Press the product against the DIN rail.3)on the left.→ Refer to the FX 3U FX 3U -4ADINSTALLATION MANUALThis manual describes the part names, dimensions, mounting, and specifications of the product. Before use, read this manual and manuals of relevant products fully to acquire proficiency in handling and operating the product. Make sure to learn all the product information, safety information, and precautions.And, store this manual in a safe place so that you can take it out and read it whenever necessary. Always forward it to the end user.RegistrationThe company name and the product name to be described in this manual are the registered trademarks or trademarks of each company.Effective February 2006Specifications are subject to change without notice.© 2006 Mitsubishi Electric CorporationManual Number JY997D20701Revision ADateFebruary 20063.Wiring*1For FX 3U Series PLC (AC power type), the 24V DC service power supply is also4.4Performance Specification4.5Input characteristicsThe input characteristics in each input mode are as follows.For the details of the input characteristics, refer to the following manual.→ Refer to the FX 3U / FX 3UC Series User’s Manual- Analog Control EditionSideBSideASideBJAPANESEENGLISHJY997D20701ASafety Precaution (Read these precautions before use.)This manual classify the safety precautions into two categories:linked to serious results.In any case, it is important to follow the directions for usage.Associated ManualsNote:FX 3UC Series PLC specification details for I/O, wiring, installation, andmaintenance can only be found in the Japanese Manual.How to obtain manualsFor the necessary product manuals or documents, consult with the Mitsubishi Electric dealer from where you purchase your product.Manual name Manual No.DescriptionFX 3U / FX 3UC Series User's Manual - Analog Control EditionJY997D16701MODEL CODE:09R619Describes specifications for analog control andprogramming method for FX 3U / FX 3UC Series PLC.FX 3U /FX 3UC Series Programming Manual - B a s i c & A p p l i ed Instruction Edition JY997D16601MODEL CODE:09R517Describes PLC programming for basic/applied instructions and devices.FX 3U Series User’s Manual - Hardware EditionJY997D16501MODEL CODE:09R516Explains FX 3U Series PLC specification details for I/O,w i r i n g , i ns ta l l a t i o n , a n dmaintenance.Certification of UL, cUL standardsThe following product has UL and cUL certification.UL, cUL File Number:E95239Models:MELSEC FX 3U series manufacturedFX 3U -4ADCompliance with EC directive (CE Marking)This note does not guarantee that an entire mechanical module produced in accordance with the contents of this note will comply with the following standards.Compliance to EMC directive and LVD directive for the entire mechanical module should be checked by the user / manufacturer. For more details please contact the local Mitsubishi Electric sales site.Requirement for Compliance with EMC directiveThe following products have shown compliance through direct testing (of the identified standards below) and design analysis (through the creation of a technical construction file) to the European Directive for Electromagnetic Compatibility (89/336/EEC) when used as directed by the appropriate documentation.Type:Programmable Controller (Open Type Equipment)Models:MELSEC FX 3U series manufactured from February 1st, 2006FX 3U -4ADCaution for EC DirectiveThe analog special adapters have been found to be compliant to the European standards in the aforesaid manual and directive. However, for the very best per-formance from what are in fact delicate measuring and controlled output device Mitsubishi Electric would like to make the following points;As analog devices are sensitive by nature, their use should be considered care-fully. For users of proprietary cables (integral with sensors or actuators), these users should follow those manufacturers installation requirements.Mitsubishi Electric recommend that shielded cables should be used. If NO other EMC protection is provided, then users may experience temporary induced errors not exceeding +10%/-10% in very heavy industrial areas.However, Mitsubishi Electric suggest that if adequate EMC precautions are fol-lowed with general good EMC practice for the users complete control system, users should expect normal errors as specified in this manual.•Sensitive analog cable should not be laid in the same trunking or cable conduit as high voltage cabling. Where possible users should run analog cables separately.•Good cable shielding should be used. Ground the shield of the twisted shielded cable at one point on the PLC side.•When reading analog values, EMC induced errors can be smoothed out by averaging the readings. This can be achieved either through functions on the special function block for analog input or through a users program in the FX 3U Series PLC main unit.•Please use FX 3U -4AD while installed in a shielded enclosure. For the details,refer to the following manual.→ Refer to the FX 3U Series User's Manual - Hardware Edition1.OutlineThe FX 3U -4AD special function block for analog input converts four analog input values (voltage, current) to digital values and transfers those digital values to the PLC main unit.1.1Incorporated ItemsCheck if the following product and items are included in the package:StandardRemarkEN61131-2:2003Programmable controllers-Equipment requirements and testsCompliance with all relevant aspects of the standard.•Radiated Emissions•Mains Terminal Voltage Emissions •RF immunity •Fast Transients •ESD •Surge•Conducted•Power magnetic fields1.2External Dimensions, Part Names, and Terminal Layout1.2.1External Dimensions and Part Names1.2.2Terminal Layout2.Installation2.1ArrangementsThe product connects on the right side of an PLC main unit or extension units/blocks (including special function units/blocks).For connection to FX 3UC Series PLC or FX 2NC Series PLC extension block, FX 2NC -CNV-IF or FX 3UC -1PS-5V is required.For further information of installation arrangements, refer to the following manual.→ Refer to the FX 3U Series User's Manual - Hardware Edition[1]Direct mounting hole:2 holes of φ4.5 (0.18") (mounting screw: M4 screw)[2]Extension cable[3]POWER LED (green):Lit while 5V DC power is supplied from PLC.[4]Terminal block for power supply (24V DC) (M3 terminal screw)[5]Terminal block for analog input [6]24V LED (red):Lit while 24V DC power is supplied properly to terminals [24+] and [24-].[7]A/D LED (red):Flashes (at high speed) during A/D conversion. [8]DIN rail mounting hook[9]DIN rail mounting groove (35 mm (1.38") wide)INSTALLATION PRECAUTIONS•Use the product in the environment within the general specifications described in PLC main unit manual (Hardware Edition).Never use the product in areas with dust, oily smoke, conductive dusts, corrosive gas (salt air, Cl 2, H 2S, SO 2, or NO 2), flammable gas, vibrations or impacts, or expose it to high temperature, condensation, or wind and rain.If the product is used in such a place described above, electrical shock, fire,malfunction, damage, or deterioration may be caused.•Do not touch the conductive parts of the product directly, thus avoiding failure or malfunction.•Install the product securely using the DIN rail or screws.•Install the product on a flat surface.If the mounting surface is rough, undue force will be applied to the PC board,thereby causing nonconformity.•When drilling screw holes or wiring, cutting chips or wire chips should not enter ventilation slits.Such an accident may cause fire, failure or malfunction.•Be sure to remove the dust proof sheet from the PLC's ventilation port when the installation work is completed.Failure to do so could cause fires, equipment failures, and malfunctions.•Fit the extension cables and communication cables securely to the designated connectors.Contact failures may cause malfunctions.2.2MountingThe product is mounted by the following method. •Direct mounting •DIN rail mounting2.2.1Direct MountingThe product can be mounted with M4 screws by using the direct mounting holes.Refer to the External Dimensions (section 1.2) for the product’s mounting hole pitch information.An interval space between each unit of 1 to 2 mm (0.04" to 0.08") is necessary. For further information of direct installation, also refer to the following manual.→ Refer to the FX 3U Series User's Manual - Hardware Edition2.2.2DIN Rail MountingThe product can be mounted on a DIN rail (DIN46227, 35mm width).1)Fit the upper edge of the DIN rail mounting groove (right fig. A) onto the DIN rail. 2)Press the product against the DIN rail.3)on the left.→ Refer to the FX 3U3.Wiring3.1Applicable Cable and Terminal Tightening TorqueThe size of the terminal screws is M3.The end disposal of the cable shows below.Tighten the terminal to a torque of 0.5N m to 0.8N m.•When one wire is connected to one terminal•When two wires are connected to one terminal3.2Power Supply WiringFor the power supply wiring, refer to the following manual.→ Refer to the FX 3U / FX 3UC Series User’s Manual- Analog Control Edition3.3Wiring of Analog Input→ For the terminal layout, refer to Subsection 1.2.2*1For FX 3U Series PLC (AC power type), the 24V DC service power supply is alsoavailable. *2terminal.*3Use a 2-core twisted shield wire for analog input line, and separate it from otherpower lines or inductive lines.*4For the current input, short-circuit the [V+] terminal and the [I+] terminal. *5If there is voltage ripple in the input voltage or there is noise in the externalwiring, connect a capacitor of approximately 0.1 to 0.47µF 25 V.3.4GroundingGrounding should be performed as stated below.•The grounding resistance should be 100Ω or less.•Independent grounding should be performed for best results.When independent grounding is not performed, perform "shared grounding"of the following figure.→ For details, refer to the FX 3U Series User's Manual- Hardware Edition.•The grounding wire size should be AWG 14 (2 mm 2).•The grounding point should be close to the PLC, and all grounding wire should be as short as possible.4.Specification4.1Applicable PLCThe version number can be checked by monitoring D8001 as the last three digits indicate it.4.2General SpecificationThe items other than the following are equivalent to those of the PLC main unit. For other general specifications, refer to the manual of the PLC main unit.→ For details, refer to the FX 3U Series User's Manual- Hardware Edition.4.3Power Supply SpecificationSTARTUP ANDMAINTENANCE PRECAUTIONS•Do not disassemble or modify the unit.Doing so may cause failure, malfunction or fire.* For repair, contact your local Mitsubishi Electric distributor.•Do not drop the product or do not exert strong impact, doing so may cause damage.DISPOSAL PRECAUTIONS•Please contact a company certified in the disposal of electronic waste forenvironmentally safe recycling and disposal of your device.TRANSPORT ANDSTORAGE PRECAUTIONS•During transportation avoid any impact as the product is a precision instrument.Check the operation of the product after transportation.Model name ApplicabilityFX 3U Series PLC Ver. 2.20 (from the first product) and laterFX 3UC Series PLCVer. 1.30 (from the product manufactured in August, 2004 with SER No. 48) and laterItemSpecificationDielectric withstandvoltage500V AC for one minuteConforming to JEM-1021Between all terminals and ground terminal of PLCmain unitInsulation resistance 5M Ω or more by 500V DC megger Item SpecificationA/D conversion circuit driving power 24V DC ±10%, 90mA for 24V DCConnect a 24V DC power supply to the terminal block.CPU driving power5V DC, 110mA5V DC power is supplied internally from the main unit.4.4Performance Specification*1Change the offset and gain values to change the input characteristics. However,the resolution doesn’t change even when the offset and gain values change.When the analog value direct indication is enabled in the input mode 2, 5, or 8,the offset value and the gain value don’t change. *2The offset and the gain should satisfy the following condition:1V ≤ (Gain - Offset)*3The offset and the gain should satisfy the following condition:3 mA ≤ (Gain - Offset) ≤ 30 mA*4The input characteristics vary depending on the input mode to be used.For the details of the input characteristics, refer to the following manual.→ Refer to the FX 3U / FX 3UC Series User’s Manual- Analog Control Edition4.5Input characteristicsThe input characteristics in each input mode are as follows.For the details of the input characteristics, refer to the following manual.→ Refer to the FX 3U / FX 3UC Series User’s Manual- Analog Control EditionInput mode Input modeAnalog inputrange Digital outputrange 0Voltage input mode -10 to +10V -32000 to +320001Voltage input mode-10 to +10V -4000 to +40002Voltage input modeAnalog value direct indication -10 to +10V -10000 to +100003Current input mode 4 to 20mA 0 to 160004Current input mode4 to 20mA 0 to 40005Current input modeAnalog value direct indication 4 to 20mA 4000 to 200006Current input mode -20 to +20mA -16000 to +160007Current input mode-20 to +20mA -4000 to +40008Current input modeAnalog value direct indication-20 to +20mA-20000 to +20000FX 3U -4ADINSTALLATION MANUALThis manual describes the part names, dimensions, mounting, and specifications of the product. Before use, read this manual and manuals of relevant products fully to acquire proficiency in handling and operating the product. Make sure to learn all the product information, safety information, and precautions.And, store this manual in a safe place so that you can take it out and read it whenever necessary. Always forward it to the end user.RegistrationThe company name and the product name to be described in this manual are the registered trademarks or trademarks of each company.Effective February 2006Specifications are subject to change without notice.© 2006 Mitsubishi Electric CorporationManual Number JY997D20701Revision ADateFebruary 2006。
海尔电子洗衣机产品说明书

Section 6: Parts DataDC50X264310131211216547Cabinet GroupKey Part Number Description Quantity * 9960-285-008Door Assy., Loading Complete-Wht (2)* 9960-285-011Door Assy., Loading Complete-SS (2)* 9960-285-007Door Assy., Loading Complete-Chrome/BLK/SS (2)1 9960-284-002Door Assy., Loading-SS(ring only) (2)1 9960-284-004Door Assy., Loading-Chrome(ring only) (2)2 9982-353-002Plate Assy., Hinge (Wht) No Pin (2)2 9982-353-001Plate Assy., Hinge (SS) No Pin (2)* 9545-012-015Screw, Hinge to Door (8)* 8640-413-002Nut, Hinge to Door (8)3 9212-002-004Glass, Door (2)4 9206-413-002Gasket, Glass Black (2)* 9548-117-000Support, Door Glass (2)5 9206-420-005Gasket, Outer Rim Black (2)6 9244-082-001Handle, Loading Door (2)* 9545-018-017Screw, Handle 1/4-20 x 3/8 (4)* 9531-033-003Stud, Door Catch (2)* 8640-413-001Nut, Hex (2)* 8640-413-003Nut, Acorn (2)* 9086-015-002Catch, Loading Door (2)* 8638-190-009Pop Rivet for mtg. catch (4)* 8641-582-006Lockwasher (4)* 8640-399-001Spring Nut (6)7 9989-521-003Panel Assy., Front- Lower (Wht) (1)7 9989-521-001Panel Assy., Front- Lower (SS) (1)8 9989-517-003Panel Assy., Front- Upper (Wht) (1)8 9989-517-001Panel Assy., Front- Upper (SS) (1)* 9277-054-001Insulation Front Panel, half moon (top) (2)* 9277-054-002Insulation Front Panel, half moon (bottom) (2)9 9545-008-014Screw, FLHDCR, 10B x 1 (14) (6)* 8641-585-001 Lockwasher* 8640-399-001Nut, Spring (12)10 9544-069-002Strap, Hinge (Wht) (2)10 9544-069-005Strap, Hinge (SS/Black) (2)* 9545-012-028Screw, Hinge to Panel (8)11 9545-052-001Screw, Door to Hinge Strap (Special Black Type) (2)12 8641-436-003Washer, Fiber (2)13 9021-041-001Acceptor, Coin (1)* 9486-149-001Retainer, Coin Acceptor (2)14 9545-053-002Screw (4)* 9801-099-001Switch, Optical (1)Cabinet Group ContinuedKey Part Number Description Quantity15 9994-032-001Escutcheon, Upper (1)16 9435-039-002Trim, Overlay-Upper Blue (1)16 9435-039-001 Trim, Overlay-Upper Black (1)17 9994-033-001Escutcheon, Lower (1)18 9435-023-001Trim, Overlay-Lower Blue (1)18 9435-031-001Trim, Overlay-Lower Black (1)* 9545-020-009Screw (20)19 9412-167-002Nameplate Stack Dryer Express Blue (1)19 9412-167-001Nameplate Stack Dryer Express Black (1)20 9866-005-001Lint Drawer Assembly Blue (2)20 9866-005-004Lint Drawer Assembly Black (2)21 9435-024-001Overlay Trim, Lint Drwr-Blue (1)21 9435-032-001Overlay Trim, Lint Drwr-Black (1)* 9532-074-003Felt Seal ( back of lint screen assembly ) (2)* 9805-033-002Lint Screen Assembly ONLY (no front) (2)* 9555-057-008Replaceable Lint Screen Only (2)22 8650-012-004Lock and Key, Lint Drawer (2)* 6292-006-010Key 6101 only (2)* 9095-043-001Cam, Lock (2)* 9545-008-001Lint Screen Strap Hold Down Screws 10Bx 1/4 (32)23 9857-198-001Controls Assy, Blue (1)23 9857-198-003Controls Assy, Black (1)* 9627-869-001Harness, Electronic Control (1)24 8650-012-003Lock and Key, Control (1)* 9095-041-001Cam, Lock (1)* 6292-006-007Key only 6324 (1)* 9627-855-003Harness, Heat Sensor (1)* 8640-276-002Wire Nut Connector Grey (4)25 9501-004-003Sensor Temp Control (2)26 9501-008-001Bracket for Heat Sensor Mounting (Under Basket) w/ sensor..2* 9545-045-005Screw, Round Head (Mounts sensor; phillips head) (2)* 9209-037-002Gromm.et, 3/16 ID (2)* 8544-006-001Leg, Leveling 1/2” (4)* 9074-320-001 Cover, Cabinet (Top) (1)* 9277-041-017 Insulation Cabinet Cover (1)* 9732-276-001Kit for Dryers without Neutral and using 208-240 volt (1)* 9732-102-013LP Kit for 50Lb Stk Dryers (1)* 9732-243-001Stack Dryer Trunion Puller (1)* 9544-041-002 Strap - Bead Tie (1)27 9942-038-005 Vault, Coin Box (1)* 9545-008-024 Screws, Mounting-Coin Vault (2)28 9897-099-002 Coin Box Assy, Large Blue (1)28 9807-099-004 Coin Box Assy, Large Black (1)191526252792531089Control Parts GroupKey Part Number Description Quantity * 9857-198-001Controls Assy, Electronic Mounted With Membrane Switch, BLU (1)* 9857-198-003Controls Assy, Electronic Mounted With Membrane Switch, BLK (1)1 9826-008-001 Trough Assembly (1)2 9032-062-002 Button-Push, Control, Blue (2)2 9032-062-001 Button-Push, Control, Black (2)3 9538-166-011Spacer-Metal, 4mm (4)4 9486-158-001 Retainer-Push Button (2)5 8640-424-002Nut-Hex, Elastic stop, #4-40 (4)6 8652-130-038Terminal-Grounding clip (1)7 9534-365-001Spring-Flat, Control (1)8 9545-008-001Screw-Hex, #10B x 1/4 (2)9 9545-044-010 Screw-Hex, #10B x 1/4 (10)9 8641-582-005Washer-External tooth, #6 (10)10 9435-038-001Overlay-Control, Coin, Black (1)10 9435-038-002Overlay-Control, Coin, Blue (1)11 9021-041-001Acceptor-Coin, Optical (1)* 9486-149-001Retainer, Coin Acceptor (1)12 9545-053-002Screw (4)* 9801-099-001 Optical Sensor, Replacement (1)Note: Jumpers required if using 1.5 Control on Older Machines (P9 Connection)* 8220-155-001 Wire Assy, Jumper, 30Lb Stack Coin (1)* 8220-155-002 Wire Assy, Jumper, 50Lb Stack Coin (1)Door Switch GroupPart NumberDescription Quantity9539-487-001Door Switches (2)Hinge Plate Cover1 9074-340-002 Cover-Hinge, Black .....................................................................22 8636-008-010 Screw-TRHDCR, 10B x 3/8, Black.. (4)12Bearing Housing GroupKey Part Number Description Quantity J1 9241-189-002 Housing, Bearing (2)J2 9036-159-003Bearing, Ball Rear..................................................................... .2 * 9538-183-001 Spacer, Bearing (2)* 9036-159-001Bearing, Ball Front .................................................................... .2 J5 9545-017-017Bolt, 1/2 x 3/4 . (8)J7 8640-417-002Nut, 1/2 (8)* 9803-201-001Bearing Housing Complete Ass’y (includes bearings,spacer) (2)J4 9545-017-018Screw 1/2 x 1 1/2 (4)Burner Housing GroupKey Part Number Description Quantity * 9803-207-001 Housing Assembly, Burner (2)1a 9452-730-001Service Burner Plate Front... (2)1 9452-729-001 Service Plate baffl e Recirculation Chamber Clean Out (2)* 9545-008-006Screws (8)2 9545-008-001Screw (16)18 9003-220-001Angle, Burner Support (2)* 9545-008-006Screw (4)17 9048-020-002Burner, Main (4)* 9545-008-006Screw 10AB x 3/8” (4)* 9454-824-001 Panel, Back Burner Housing (2)4 9545-008-001Screw 10B x1/4” (8)5 9875-002-003Electrode Assy, Ignition (2)19 9545-045-001Screw, Electrode Mtg 8B x 1/4” (4)7 9379-186-001Valve, Gas Shut Off (1)8 9857-134-001Control Assy, Gas (2)9 9381-012-001Manifold, Assy (2)* 9425-069-021Orifi ce, Burner-Natural #27 (4)* 9425-069-022Orifi ce, Burner-LP #44 (4)10 9029-175-001Bracket, Manifold (2)22 8615-104-038Pipe Plug in end of Burner Manifold (2)* 9545-008-006Screw (4)12 9576-203-002Thermostat, Hi-Limit (2)* 9538-142-001Spacer, Hi-Limit (4)* 9545-045-007 Screw 8B x 3/4” (4)13 9074-329-001Cover, Hi-Limit Stat Ignitor (2)* 9545-008-006Screw (6)* 9576-207-008Thermostat, Safety Shutoff (2)* 9545-008-006Screw (4)15 9825-062-001Cover, Safety Stat (2)* 9545-008-024Screw (6)16 9857-116-003Control, Ignition Fenwall (3 trybox) (2)* 9732-102-013Kit, LP Conversion 50Lb Stack Kit (2)* 9838-018-003Welded One Piece Gas Pipe Assembly (1)Part # 8533-085-001 9/14Burner Housing Group Photos10221092221851A141594851613Rear ViewKey Part Number Description Quantity * 9627-861-001Wire Harness Overtemperature Switch/Air Switch (2)* 9801-098-001Switch Assy, Air Flow (2)1 9539-461-009Switch, Air Flow (2)2 9029-200-001 Bracket, Switch- Air Flow (2)3 9008-007-001Actuator, Switch (2)4 9451-169-002Pin, Cotter (2)5 9545-020-001Screw 4-40 x 5/8” (4)* 8640-401-001Nut, Special Twin .#4-40 (2)* 9550-169-003Shield, Switch (2)6 9376-322-001Motor, Drive (2)7 9452-770-001Plate, Motor Mounting (1)* 9545-029-008Bolt 3/8” - 16 x 3/4” (8)* 8641-582-003Lockwash Spring 3/8 (8)8 9545-018-019Screw, Motor Plate to Back Assy. 1/4-20x 2 1/2 (8)* 8641-582-007Lockwasher 1/4 (8)9 9538-163-006Spacr (8)* 8641-581-017Flat Washer 1/4 x 7/8 (24)* 9209-086-002Rubber Grommet (8)* 9538-166-006Grommet Spacers (8)* 9545-028-013Screw, Set (4)10 9962-018-002Back Assy, Blower Hsg (2)11 9991-053-001Support Assy, Intermed. Pulley (2)12 9545-029-010Bolt, Rd Hd 3/8-16 x 1 1/4 (6)12 8640-415-004Nut Flange Wizlock 3/8” - 16 (6)12 8641-581-035Washer, Flat (6)13 9545-029-003Bolt, 3/8-16 x 1 1/2 (2)14 9861-022-001Arm Assy-Tension, Complete (2)* 9487-200-003Ring-Retaining (6)15 9908-048-003Pulley Assy, Intermediate with bronze fl ange bearing (2)* 9036-145-002Bronze Flange Bearing (4)16 9908-047-002Pulley Driven Tumbler (2)17 9040-076-009Belt, Drive Motor (2)18 9040-073-011Belt, Driven Intermediate to Tumbler (2)19 9534-151-000Spring, Tension (2)20 9099-012-005Chain, Tension (2)21 9248-022-002Hook, Tension (2)* 9451-146-001Pin, Damper Hinge (2)* 9074-334-001 Cover Duct Upper (1)22 9973-032-001 Heat Recirculation Assembly Duct (2)* 9453-169-013Motor Pulley - Driver (1)* 9545-028-013Set Screws (2) (2)* 9278-043-001Impeller23 8641-581-026Washer, Flat 1/2” for Tumbler Pulley (2)24 9545-017-009Bolt, 1/2”-13 x 1 1/4 (2)25 8641-582-016Washer, Star 1/2” for Tumbler Pulley (2)* 9545-008-001Screw 10 Bx 1/4” (6)* 9545-014-004Bolt, 5/16-18 x 5/8” (8) (8)5/16-18* 8640-400-003Nut,* 9538-184-001Spacer, Shaft (2)* 9487-234-005Ring Tolerance (2)* 9125-007-001Damper Inside Duct Exhaust (2)* 9125-007-002Damper Inside Duct Exhaust (1)* 8520-141-000Nut, Spring (4)* 9074-335-001Cover Duct Lower (1)* 9545-008-024Screw 10ABx 3/8” (72)* 9029-173-001Bracket for Wire Harness Under Burner Housing (2)Part # 8533-085-001 9/14Part # 8533-085-001 9/14Rear View Photos1264722Rear Panel & Cover GroupKey Part Number Description Quantity19208-090-001Rear Guard Side Panel 1 (2)4 9545-008-024Screws 10 AB x 3/8 (30)5 8502-649-001Label - Connection Electrical (1)8 9208-089-001Rear Guard Back Panel (2)10 8502-600-001Label Warning & Notice (1)11 8502-645-001Label - Instructions (1)12 9109-113-001Transition Assembly Outlet (1)13 9074-320-001 Top Cover Dryer Panel (1)14 9550-188-001 Top Burner Housing Heat Shield Inlet (1)15 9074-321-001 Top Panel Burner Housing Cover (1)Part # 8533-085-001 9/141851113121514Tumbler GroupKey Part Number Description Quantity 9848-131-001Tumbler Assembly Galvanized w/spider (2)G2 9568-013-001Spider Assembly (2)G3 9497-226-002Rod, Tumbler (6)G4 8640-417-005Nut, 1/2 - 13 (6)G6 8641-590-002Washer, Special (6).............................................................................AR G7 9552-013-000Shim* 9848-130-002Tumbler Assembly Stainless Steel (2)G1 9848-130-001Tumber Assembly Galvanized (2)Part # 8533-085-001 9/14Control Assembly GroupKey Part Number DescriptionQuantity* 9857-189-001 Control Assmbly Complete (all below included) .............................1* 9108-117-001 Control Box Cover ..................................................................... 1* 8220-001-478 Wire Assembly Green 7” ............................................................ 1* 8639-621-007 Screw #10-32 x 12 Green ............................................................1* 8641-582-006 Lockwasher Ext Tooth #10 ..........................................................13 9897-026-002 Terminal Block Main Power Middle ...............................................14 9897-026-001 Terminal Block ............................................................................2* 9545-045-012 Screw #8 ABx 1/2 for terminal block ............................................6 5 8711-011-001 Transformer Ignition ...................................................................2* 9545-008-024 Screws 10AB x 3/8” ...................................................................46 9982-348-001 Plate Assembly MTG Ignition Control............................................2* 9545-008-024 Screws 10B x 1/4” MTG Above Plate and Others ...........................47 9857-116-003 Ignition Control ..........................................................................2* 8640-411-003 #6-32 Nuts ................................................................................48 9631-403-009 Wire Assembly High Voltage Upper ..............................................19 9627-860-001 Wire Harness Ignition Control Upper ............................................110 9627-860-002 Wire Harness Ignition Control Lower ............................................1* 9053-067-002 Bushing Wire 7/8” .......................................................................413 9200-001-002 Fuseholder Assembly ..................................................................314 8636-018-001 Fuse 1.5 Amp .............................................................................315 5192-299-001 Relay Power ...............................................................................216 9897-035-001 Terminal Block Assembly Main Power Inlet ...................................1* 9545-008-024 Screw #8 AB x 1/2” ....................................................................2* 8220-062-036 Wire Assembly Red/Black 14” ......................................................1* 8220-062-037 Wire Assembly Red/White 14” .....................................................1* 8220-062-038 Wire Assembly White 14” ............................................................221 9627-864-004 Wire Harness Motor Extension .....................................................2* 9527-007-001 Stand Off - Wire Saddle / Arrowhead ..........................................13* 9545-031-005 Screw 6 B x 3/8” ........................................................................422 9558-029-003 Strip Terminal Marker (Behind Input Power) ..................................124 9627-863-001 Wire Harness Main Extension Access Under Burner Housing .........123 9631-403-008 Wire Ass’y - High Voltage Lower ..................................................125 9627-859-001 Wire Harness - Main Power (1)Part # 8533-085-001 9/14Control Assembly GroupPart # 8533-085-001 9/1416252223245Coin AccecptorKey Part Number Description Quantity1 9021-041-001Coin Accecptor, Optical (1)Replacement (1)2 9801-099-001Sensor-Optical,3 9545-039-002Screw, Heighth Bar, 3mm (2)* 9486-136-001 Retainer, Coin Acceptor (1)* 9545-053-002 Screw (4)Part # 8533-085-001 9/14NotesPart # 8533-085-001 9/14NotesPart # 8533-085-001 9/14Section 7: VoltageConversionPart # 8533-085-001 9/14Part # 8533-085-001 9/14Instructions - Convert a Dual Voltage Stack Dryer from 120V to 208-240V with Neutral Wire Only1. Remove incoming power from the dryer. Use a known working voltmeter to check power.2. Remove the cover of both the upper and lower control box assemblies from the dryer using a 5/16” wrench.3. Move the black/blue wire from the N position of the main power terminal block to the L2 position of the mainpower terminal block in the upper control box assembly. See Figure 6 below.4. Move the white wire of the upper motor harness to an upper inner left terminal in the middle terminal block in thelower control box assembly. See Figure 6 below.5. Move the orange wire of the upper motor harness to an upper inner left terminal in the middle terminal block inthe lower control box assembly. See Figure 6 below.6. Move the white wire of the lower motor harness to a lower inner left terminal in the middle terminal block in thelower control box assembly. See Figure 6 below.7. Move the orange wire of the lower motor harness to a lower inner left terminal in the middle terminal block in thelower control box assembly. See Figure 6 below.8. Reconnect power to the dryer and test to ensure proper operation; one line voltage to L1, one line voltage to L2,the neutral to N, and the earth ground to E.9. Reinstall the cover of both the upper and lower control box assemblies from the dryer using a 5/16” wrench.Part # 8533-085-001 9/14NotesPart # 8533-085-001 9/14Section 9: MaintenancePart # 8533-085-001 9/14MaintenanceDaily1. Clean lint screen by unlocking and sliding out in their tracks for access. Use soft brush ifnecessary. Failure to do so will slow drying and increase gas usage and temperatures through out the dryer.2. Check lint screen for tears. Replace if necessary.Monthly1. Remove lint accumulation from end bells of motor.2. Clean lint from lint screen compartment.3. Remove lint and dirt accumulation from top of the dryer and all areas above, and around theburners and burner housing. Failure to keep this portion of the dryer clean can lead to a buildup of lint creating a fi re hazard.4. Inspect Recirculation burner housing for excessive buildup.5. Place a few drops of light oil on top and bottom pivots of the clothes door hinge.6. Grease bearings and shaft of intermediate drive pulley.Quarterly1. Check belts for looseness, wear or fraying.2. Inspect gasket of door glass for excessive wear.3. Check tightness of all fasteners holding parts to support channel.4. Check tightness of tumbler shaft retaining nut. MUST MAINTAIN 150 FOOT LBS.5. Remove lint accumulation from primary air ports in burners.6. Grease pivot pins and tension arms where in contact with each other.Semiannually1. Remove and clean main burners.2. Remove all orifi ces and examine for dirt and hole obstruction.3. Remove all lint accumulation. Remove front panel, lint screen housing and remove lintaccumulation.Annually1. Check intermediate pulley bearings for wear.2. Check and remove any lint accumulation from exhaust system.NOTE: DRYER MUST NOT BE OPERATED WITHOUT LINT SCREEN IN PLACE。
万元内录影棚设备预算表课件

首页 清单
M-AUDIO Axiom(真理) 61 USB MIDI键盘
61键键速响应半配重键盘,具有触后功能 8个可分配的触发垫 8个可分配的旋钮 9个可分配的推子 15个按钮,其中包含6个走带控制按钮 弯音和调制轮 8度音 上/下;移调 上/下 4个独立的可以配置的键盘区域 15个按钮和夜光LCD显示屏,可以显示所有的前面板程序参数 延音和表情踏板接口 内置USB MIDI接口,提供标准的MIDI输入输出接口 可以通过USB供电或电源适配器供电 Windows XP和Mac OS X即插即用 20个固化存储器 通过SysEx传送memory dump 全新的Enigma编辑软件可以存储无限多的预设 所有的控制器按钮都可以被分配MIDI值和通道 控制器哑音功能可以在将它们移动到期望位置之前关闭所有控制器的输出; Snapshot功能可以记录当前所有设定
4
首页 清单
MAC Pro MC250CH/A 图片
外部接口 正 面 ( 左 ) 背 面 ( 右 )
机箱内部
5
首页 清单
003 Factory Complete
功能特性:
• 专业003 Factory 系统, 为音频/MIDI界面整合了高品质8路触感控制界面 • 包括Pro Tools LE软件在录音, 编辑, 混音所需的一切, 超大规模的捆绑产品包括超过70个虚拟乐
合
计
单价(元)
20000 1399
24000 22000 4500
5800 1200 315 588 188 272 2500 5000
50
数量
1 2 1 1对 1对 2 1 2 1 2 2 1 1 2
总额(元)
20000 2798
A-T Controls 31-F3 3-Way Flanged Direct Mount Ball

31F3Series-2R-20211210Copyright 2013 A-T Controls, Inc.PneumaticElectricSee automated data sheets for pre-sized assembliesEasy to Automate!This 3-way ball valve offers diverting and mixing flow patterns, often eliminating the need for two valves. The full port design is easily automated and is available with various seat materials. The bolts on side flanges make for easy seatchanges as necessary to accomodate your service. Available in L or T port configurations.Cincinnati, Ohio FAX (513) 247-5462********************3-Way 300# Flanged Direct Mount Ball Valvematerial, consult factoryFLOW PATTERNScustomer. Automated assemblies rotate counter-clockwise standard from the factory when energized. For L-Ports that would be L1 to L2 and T3 to T4 for T-ports. By specifying FCCW or DAR actuators, multiple flow patterns can be achieved to meet process requirements.CRN3-Way Flanged Ball Valve Full Port, L or T Option ANSI Class 300# 1-1/2” THRU 3” = Qty. 12 pcs | 4” = Qty. 18 pcs | 6” = Qty. 30 pcs^ 1-1/2” THRU 3” = 4 pcs, 4” = 6 pcs., 6” = 12 pcsTFM™ is a trademark of Dyneon™, a 3M Company.Kalrez is a registered trademark of DuPont Performance Elastomers.NOTE: At temperature, valves are limited by either the valve body/end cap pressure ratings, seat pressure ratings, or packing/stem seal/gaskets;whichever is lower.Published torques are based on full differential pressure with clean water.Consult the Application Sizing Guide forassistance with sizing actuators.Cincinnati, Ohio FAX (513) 247-5462********************Actuators are sized based on clean/clear fluid.SERIES 31-F3 3-Way 300# Flanged Direct MountFlanged 3-WayClass 300 Double Acting Assembly For operating temperatures in excess of 175° F with Buna-N seals in the actuator, an extended bracket is required. FKM seals in the actuator require an extended bracket for more than 300° F. Please consult factory for sizing information.Actuators are sized for clean liquid surface with a specific gravity of 1 and at 70° F.SAMPLE PART #31C-3X-300/2R8D-_ _ _(2) Valve Series (4) End Connection (6) Valve Size(5) Seat, Lining, & TrimMaterial(7) Actuator(8) Accessories/Options(3) Body/Ball/StemMaterial(9) Accessories(10) Special Designation Refer to Series 31 IOM for all repair kit, seat and gasket part numbers.See the last page of catalog for How To Order detail and options.See Automated Part Number Matrix for complete part number and options.31F3Series-2R-20211210Copyright 2013 A-T Controls, Inc.Flanged 3-WayCincinnati, Ohio FAX (513) 247-5462********************Specify flow pattern when ordering. See automated part number matrix for complete part number and options.SERIES 31-F3 3-Way 300# Flanged Direct MountClass 300 Spring Return Assembly Note: A number following the actuator model (Ex: 2R6S4), indicates the number of springs per side. For a standard (5 spring per side) actuator, the spring designation is omitted from the automated part number.Actuators are sized for clean liquid surface with a specific gravity of 1 and at 70° F.For operating temperatures in excess of 175° F with Buna-N seals in the actuator, an extended bracket is required. FKM seals in the actuator require an extended bracket for more than 300° F. Please consult factory for sizing information.^ Actuator sized for 400 PSIG. For higher pressure, use a 2R0S4.# Actuator sized for 400 PSIG. For higher pressure, use a 2RBSR60.SAMPLE PART #31C-3X-300/2R9S4-_ _ _(2) Valve Series (4) End Connection (6) Valve Size(5) Seat, Lining, & TrimMaterial(7) Actuator(8) Accessories/Options(3) Body/Ball/StemMaterial(9) Accessories(10) Special Designation Refer to Series 31 IOM for all repair kit, seat and gasket part numbers.See the last page of catalog for How To Order detail and options.See Automated Part Number Matrix for complete part number and options.31F3Series-2R-20211210Copyright 2013 A-T Controls, Inc.Flanged 3-WayCincinnati, Ohio FAX (513) 247-5462********************NOTE: Heater and thermostat standard (2) auxiliary switches standardOther options available - call for detailsActuators are sized based on clean/clear fluid.SERIES 31-F3 3-Way 300# Flanged Direct MountClass 300 Electric Assembly For operating temperatures in excess of 158° F with an electric actuator, an extended bracket is required. Please consult factory for sizing information.Actuators are sized for clean liquid surface with a specific gravity of 1 and at 70° F.SAMPLE PART #31C-3X-300/WEF1-_ _ _(2) Valve Series (4) End Connection (6) Valve Size(5) Seat, Lining, & TrimMaterial(7) Actuator(8) Accessories/Options(3) Body/Ball/StemMaterial(9) Accessories(10) Special Designation Refer to Series 31 IOM for all repair kit, seat and gasket part numbers.See the last page of catalog for How To Order detail and options.See Automated Part Number Matrix for complete part number and options.31F3Series-2R-20211210Copyright 2013 A-T Controls, Inc.HOW TO ORDER: Manual Valves®Chemraz® is a registered trademark of Greene, Tweed & Co.Markez® is a registered trademark of Marco Rubber & Plastic Products Inc.Perlast® is a registered trademark of Precision Polymer Engineering Limited.TFM TM is a trademark of Dyneon TM, a 3M Company.SAMPLE PART #31C-F3-0200-XXX-_ _ _(2) Valve Series (4) End Connection(5) Valve Size(6) Seat, Lining, & TrimMaterial(7) Special Designation (8) Additional Specials(9) Special Designation(3) Body/Ball/StemMaterial(10) O-RingDesignation (11) AdditionalSpecialsRefer to Series 31 IOM for all repair kit, seat and gasket part numbers.31F3Series-2R-20211210Copyright 2013 A-T Controls, Inc.SAMPLE PART #31C-3X-200/2R3D-_ _ _(2) Valve Series (4) End Connection (6) Valve Size(5) Seat, Lining, & TrimMaterial(7) Actuator(8) Accessories/Options(3) Body/Ball/StemMaterial(9) Accessories(10) Special Designation Refer to Series 31 IOM for all repair kit, seat and gasket part numbers.HOW TO ORDER: Automated Valves9955 International Blvd.Cincinnati, Ohio PHONE (513) 247-5465FAX (513) 247-5462********************31F3Series-2R-20211210Copyright 2013 A-T Controls, Inc.。
Polycom QDX 6000 系列产品用户手册说明书
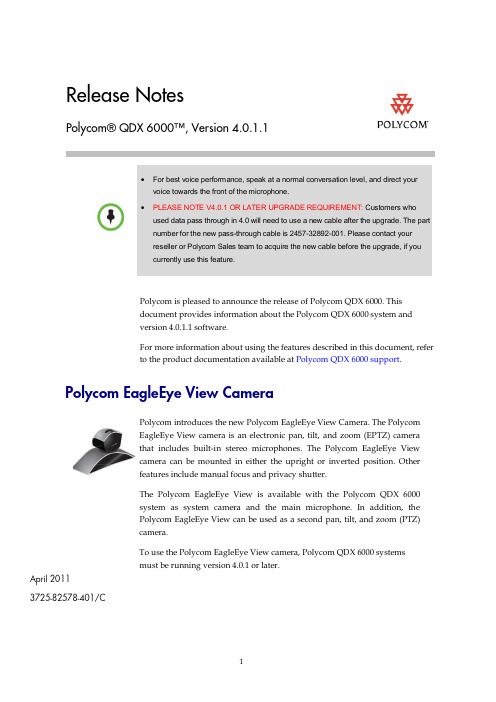
Release NotesPolycom® QDX 6000™, Version 4.0.1.1• For best voice performance, speak at a normal conversation level, and direct yourvoice towards the front of the microphone.• PLEASE NOTE V4.0.1 OR LATER UPGRADE REQUIREMENT: Customers whoused data pass through in 4.0 will need to use a new cable after the upgrade. The partnumber for the new pass-through cable is 2457-32892-001. Please contact yourreseller or Polycom Sales team to acquire the new cable before the upgrade, if youcurrently use this feature.Polycom is pleased to announce the release of Polycom QDX 6000. Thisdocument provides information about the Polycom QDX 6000 system andversion 4.0.1.1 software.For more information about using the features described in this document, referto the product documentation available at Polycom QDX 6000 support .Polycom EagleEye View CameraPolycom introduces the new Polycom EagleEye View Camera. The PolycomEagleEye View camera is an electronic pan, tilt, and zoom (EPTZ) camerathat includes built-in stereo microphones. The Polycom EagleEye Viewcamera can be mounted in either the upright or inverted position. Otherfeatures include manual focus and privacy shutter.The Polycom EagleEye View is available with the Polycom QDX 6000system as system camera and the main microphone. In addition, thePolycom EagleEye View can be used as a second pan, tilt, and zoom (PTZ)camera.To use the Polycom EagleEye View camera, Polycom QDX 6000 systemsmust be running version 4.0.1 or later.Polycom EagleEye View Camera as the main PTZ control cameraPolycom EagleEye View Camera as the second PTZ control cameraNote: The part number of the serial cable for second PTZ camera control is2457-32891-001.New CablesThe Polycom QDX 6000 has the following additional cables.CablesDescriptionPN: 2457-32890-001 An EagleEye View camera cable. One end of this cable is an HDCI connector to theEagleEye View camera, the other end breaks out to the following connectors,▪ A DB-9 male connector to QDX serial port for camera control. ▪An S-Video connector to QDX camera input. ▪ Two RJ-9 connectors to QDX MIC inputs.PN: 2457-32892-001 A DB-9, male-female, serial cable for transparent data pass-through;Cables DescriptionPN: 2457-32891-001A DB-9, female-female, serial cable for second camera PTZ control.What’s New in Version 4.0.1.1The version 4.0.1.1 software includes the features and functionality of version4.0.1. Systems running version 4.0.1.1 software can use the Polycom EagleEyecamera as the main camera or as a second camera.Using the Polycom EagleEye CameraThe camera will be detected automatically once the system starts up.The Polycom EagleEye camera does not support hot- plugged in with QDX 6000, whichmeans if the Polycom EagleEye camera is unplugged during usage, you need to detectthe camera manually before using it again.To detect the Polycom EagleEye camera manually:1.Connect the Polycom EagleEye camera to the Main/ Document camerainput.2.Press and set Main/Document camera as video source.3.Go to System > Admin Settings > General Settings > Serial Ports.4.Set RS-232 Mode to Camera PTZ.5.Click Detect Camera.What’s New in Version 4.0.1The version 4.0.1 software includes the features and functionality of version4.0.0, with the following additions.MulticastYou can configure the QDX 6000 system to allow users to stream audio andvideo from one to many viewers. Viewers watch the conference from thesystem's web interface. You can start streaming only when QDX 6000 is in a call.Points to note about streaming:•To send a stream across a subnet, multicasting must be enabled on thenetwork or you can unicast to a particular IP address, which will forwardthe stream to that IP address.•The number of viewers is limited only by your network topology.To configure the QDX system for a streaming call:1 Go to System > Admin Settings > Network > IP > Multicast.2 Configure these settings:3 Go to System > Admin Settings > General Settings > Security > SecuritySettings > >.4 Enable Allow Video Display on Web .To stream a conference:1 Go to System > Admin Settings > Network > IP > Multicast , select theEnable Multicast option.2In the browser address line, enter the system’s IP address, for example, http:// 10.11.12.13, to go to the system’s web interface. Go to Admin Settings >General Settings > Security , set the Remote Access password and theMeeting password.3 Place the video call to other participants.> ).To stop streaming a conference:1Go to System > Admin Settings > Network > IP > Multicast . 2Clear the Enable Multicast selection.To view a streamed conference:1 On a computer running Windows XP or Windows Vista operating system,open an Internet Explorer 6.x, 7.x, or 8.x.2 In the browser address line, enter http://xxx.xxx.xxx.xxx/m_multicast.htm,where “ xxx.xxx.xxx.xxx” is the QDX 6000 system's IP address.3 In the prompted window, enter the user name "meeting" and the meetingpassword set on your QDX 6000 system.The stream starts automatically.To stop viewing the streamed conference:>> Close the web browser.This stops the stream but does not end the call.Camera Control for the Second PTZ CameraQDX 6000 V4.0.1 supports camera control for the second PTZ camera.To connect a second PTZ camera to the QDX 6000 system:1 Connect a second camera supporting PTZ, such as Polycom EagleEye Viewcamera, to DOC camera input and serial control. The Polycom female-maleconvert cable (labeled as “2ND CAMERA”) MUST be used to connect thesecond camera serial port to the QDX serial control port.Note: The part number of the serial cable for second PTZ camera control is2457-32891-001. This cable can be easily recognized by the “2ND CAMERA”label on one end of the cable.2 Set Doc camera as video source.3 Go to System > Admin Settings > General Settings > Serial Ports, and setRS-232 Mode to Camera PTZ. Then click Detect Camera to detect thecamera manually.Notes:•IR signal cannot be received through the second PTZ camera.•PTZ speed setting is not available for this camera. OthersCorrected Issues in 4.0.1.1The following table lists corrected issues in version 4.0.1.1.Corrected Issues in 4.0.1The following table lists corrected issues in version 4.0.1.Known limitationsThe following table lists the known limitations for the version 4.0.1.1 release. If aworkaround is available, it is noted in the table.InteroperabilityPolycom QDX 6000 systems are tested extensively with a wide range ofproducts. The following list is not a complete inventory of compatibleequipment; it simply indicates the products that have been tested forcompatibility with the 4.0.1.1 release.Video conferencing systems use a variety of algorithms to compress audio andvideo. In a call between two systems, each end transmits audio and video usingalgorithms supported by the other end. In some cases, a system may transmit adifferent algorithm than it receives. This process occurs because each systemindependently selects the optimum algorithms for a particular call, and differentproducts may make different selections. This process should not affect thequality of the call.Copyright Information© 2010 Polycom, Inc. All rights reserved. No part of this document may bereproduced or transmitted in any form or by any means, electronic ormechanical, for any purpose, without the express written permission of Polycom,Inc. Polycom, Inc. retains title to, and ownership of, all proprietary rights withrespect to the software contained within its products. The software is protectedby United States copyright laws and international treaty provision. License IssuesOpenSSL LicenseCopyright (c) 1998-2007 The OpenSSL Project. All rights reserved.Redistribution and use in source and binary forms, with or without modification,are permitted provided that the following conditions are met:1 Redistributions of source code must retain the above copyright notice, thislist of conditions and the following disclaimer.2 Redistributions in binary form must reproduce the above copyright notice,this list of conditions and the following disclaimer in the documentationand/or other materials provided with the distribution.3 All advertising materials mentioning features or use of this software mustdisplay the following acknowledgment:"This product includes software developed by the OpenSSL Project for usein the OpenSSL Toolkit. (/)"4 The names "OpenSSL Toolkit" and "OpenSSL Project" must not be used toendorse or promote products derived from this software without priorwritten permission. For written permission, please contact************************.5 roducts derived from this software may not be called "OpenSSL" nor may"OpenSSL" appear in their names without prior written permission of theOpenSSL Project.6 Redistributions of any form whatsoever must retain the followingacknowledgment:"This product includes software developed by the OpenSSL Project for usein the OpenSSL Toolkit (/)"THIS SOFTWARE IS PROVIDED BY THE OpenSSL PROJECT ``AS IS''AND ANY EXPRESSED OR IMPLIED WARRANTIES, INCLUDING, BUTNOT LIMITED TO, THE IMPLIED WARRANTIES OFMERCHANTABILITY AND FITNESS FOR A PARTICULAR PURPOSEARE DISCLAIMED. IN NO EVENT SHALL THE OpenSSL PROJECT ORITS CONTRIBUTORS BE LIABLE FOR ANY DIRECT, INDIRECT,INCIDENTAL, SPECIAL, EXEMPLARY, OR CONSEQUENTIALDAMAGES (INCLUDING, BUT NOT LIMITED TO, PROCUREMENT OF SUBSTITUTE GOODS OR SERVICES; LOSS OF USE, DATA, OR PROFITS;OR BUSINESS INTERRUPTION) HOWEVER CAUSED AND ON ANYTHEORY OF LIABILITY, WHETHER IN CONTRACT, STRICT LIABILITY, OR TORT (INCLUDING NEGLIGENCE OR OTHERWISE) ARISING INANY WAY OUT OF THE USE OF THIS SOFTWARE, EVEN IF ADVISED OF THE POSSIBILITY OF SUCH DAMAGE.This product includes cryptographic software written by Eric Young(*****************).ThisproductincludessoftwarewrittenbyTimHudson(*****************).Original SSLeay LicenseCopyright(C)1995-1998EricYoung(*****************)Allrightsreserved. This package is an SSL implementation written by Eric Young(*****************).Theimplementationwaswrittensoastoconformwith Netscape’s SSL.This library is free for commercial and non-commercial use as long as the following conditions are adhered to. The following conditions apply to all code found in this distribution, be it the RC4, RSA, lhash, DES, etc., code; not just the SSL code. The SSL documentation included with this distribution is covered by the same copyright terms except that the holder is Tim Hudson(*****************).Copyright remains Eric Young's, and as such any Copyright notices in the code are not to be removed.If this package is used in a product, Eric Young should be given attribution as the author of the parts of the library used. This can be in the form of a textual message at program startup or in documentation (online or textual) provided with the package.Redistribution and use in source and binary forms, with or without modification, are permitted provided that the following conditions are met:1 Redistributions of source code must retain the copyright notice, this list ofconditions and the following disclaimer.2 Redistributions in binary form must reproduce the above copyright notice,this list of conditions and the following disclaimer in the documentationand/or other materials provided with the distribution.3 All advertising materials mentioning features or use of this software mustdisplay the following acknowledgement:"This product includes cryptographic software written by Eric Young(*****************)"The word 'cryptographic' can be left out if the routines from the librarybeing used are not cryptographic related :-).4 If you include any Windows specific code (or a derivative thereof) from theapps directory (application code) you must include an acknowledgement:"This product includes software written by Tim Hudson(*****************)"THIS SOFTWARE IS PROVIDED BY ERIC YOUNG ``AS IS'' AND ANYEXPRESS OR IMPLIED WARRANTIES, INCLUDING, BUT NOT LIMITEDTO, THE IMPLIED WARRANTIES OF MERCHANTABILITY ANDFITNESS FOR A PARTICULAR PURPOSE ARE DISCLAIMED. IN NOEVENT SHALL THE AUTHOR OR CONTRIBUTORS BE LIABLE FORANY DIRECT, INDIRECT, INCIDENTAL, SPECIAL, EXEMPLARY, ORCONSEQUENTIAL DAMAGES (INCLUDING, BUT NOT LIMITED TO,PROCUREMENT OF SUBSTITUTE GOODS OR SERVICES; LOSS OF USE,DATA, OR PROFITS; OR BUSINESS INTERRUPTION) HOWEVERCAUSED AND ON ANY THEORY OF LIABILITY, WHETHER INCONTRACT, STRICT LIABILITY, OR TORT (INCLUDING NEGLIGENCEOR OTHERWISE) ARISING IN ANY WAY OUT OF THE USE OF THISSOFTWARE, EVEN IF ADVISED OF THE POSSIBILITY OF SUCHDAMAGE.The license and distribution terms for any publically available version orderivative of this code cannot be changed. I.e. this code cannot simply becopied and put under another distribution license [including the GNUPublic License.]DisclaimerThis software is provided 'as is' with no explicit or implied warranties in respectof its properties, including, but not limited to, correctness and fitness forpurpose.Trademark Information© 2011, Polycom, Inc. All rights reserved. POLYCOM®, the Polycom "Triangles"logo and the names and marks associated with Polycom's products aretrademarks and/or service marks of Polycom, Inc. and are registered and/orcommon law marks in the United States and various other countries. All othertrademarks are property of their respective owners. No portion hereof may bereproduced or transmitted in any form or by any means, for any purpose otherthan the recipient's personal use, without the express written permission ofPolycom.。
键盘III(多形态PIN009013)操作手册说明书

SO Shift Out
RS Record Separator (IS)
51 Shift In
US Unit Separator (IS)
DEL Delete1
NOTE: ICCI Communication Control (FEI Format Effector liS I Inrormation Separator
SOH DCl
!
1
0010 2
STX DC2
11
2
0 0 1. 1 3
ETX DC3
#
3
0100 4
EOT DC4
S
4
0101 5
ENQ NAK
%
5
0110 6
ACK "SYN
&
6
0 1 1 1 7 " BEL ETB
,
7
1000 8
as CAN (
8
1001 9
HT
EM
)
9
1 0 1 0 10
LF
leased.
10. The four function keys (top row of numeric pad) are enclosed
as listed below:
~
ASCll Characters
I
FS
II
GS
ill
US
IV
RS
11. All hexboard characters generate the corresponding ASCll
o
b7 be b, b. b, bzb.
oo1 o
1
The code table position for the character "K" may also be represented by the notation "column 4, row II" or alternatively as "4/11." The decimal equivalent of the binary number formed by bits b1 , b., and b" collectively, forms the column number, and the decimal equivalent of the binary number formed by bits b., b" bz, and b .. collectively, forms the row number.
Freescale Kinetis E 系列 KE06 微控制器开发板用户指南说明书
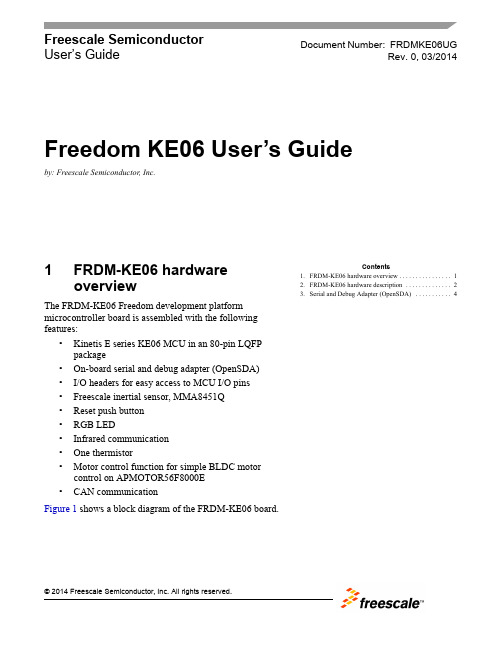
Freescale Semiconductor User’s Guide1FRDM-KE06 hardware overviewThe FRDM-KE06 Freedom development platform microcontroller board is assembled with the following features:•Kinetis E series KE06 MCU in an 80-pin LQFP package•On-board serial and debug adapter (OpenSDA)•I/O headers for easy access to MCU I/O pins •Freescale inertial sensor, MMA8451Q •Reset push button •RGB LED•Infrared communication •One thermistor•Motor control function for simple BLDC motor control on APMOTOR56F8000E •CAN communication Figure 1 shows a block diagram of the FRDM-KE06 board.Document Number:FRDMKE06UGRev. 0, 03/2014Contents1.FRDM-KE06 hardware overview . . . . . . . . . . . . . . . . 12.FRDM-KE06 hardware description . . . . . . . . . . . . . . 23.Serial and Debug Adapter (OpenSDA) . . . . . . . . . . . 4Freedom KE06 User’s Guideby: Freescale Semiconductor, Inc.FRDM-KE06 hardware descriptionFigure1. FRDM-KE06 block diagramThe FRDM-KE06 features two microcontrollers, the target MCU and a serial and debug adapter (OpenSDA) MCU. The target MCU is a Kinetis E series KE06 family device. The OpenSDA MCU is a Kinetis K series K20 family device, the K20DX128VFM5.2FRDM-KE06 hardware description2.1Power supplyThe FRDM-KE06 offers a design with multiple power supply options. It can be powered from the USB connector, the V IN pin on the I/O header, an off-board 1.71-3.6V supply from the 3.3V pin on the I/O header or 3.3V from motor control board. The USB and V IN supplies are regulated on-board using a 3.3V linear regulator to produce the main power supply. The other two sources are not regulated on-board. Note that KE06 on FRDM board can be powered by 5V or 3.3V.The following figure shows the schematic drawing for the power supply inputs and the on-board voltage regulator.FRDM-KE06 hardware descriptionFigure 2. FRDM-KE06 power supplyTable 1 provides the operational details and requirements for the power supplies.Note that the OpenSDA circuit is only operational when a USB cable is connected and supplying power to J6. However, the protection circuitry is in place to allow multiple sources to be powered at once.Table 1. Power supply requirementsSupply Source Valid RangeOpenSDA Operational?Regulated on-board?OpenSDA USB (J6)5VYes Yes V IN Pin on I/O header 4.3-9V Yes Yes 3.3V Pin on I/O header 1.71-3.6V Yes No 3.3V Pin on motor control header3.3VYesNoTable 2. Power suppliesPower Supply Name DescriptionVDD_PERIPHPeripheral power supply, including RGB LED, Key buttons, infrared, thermistor, reset circuit.J14 Pin1&2 connected, 3.3V power supply;J14 Pin2&3 connected, 5V power supply.Serial and Debug Adapter (OpenSDA)Notes:1.J9 and J10 are not populated by default on the production version. The two pins of these headers are shorted together by 0 ohm resistor R12 and R26 on the PCB. To measure the energyconsumption of either the KE06 or the OpenSDA MCU, the 0 ohm resistor between these pins must first be cut. A current probe or a shunt resistor and voltage meter can then be applied to measure the energy consumption on these rails. When the MCU current measurement is done, this 0 ohm resistor can be soldered on again.2.To better get ADC accuracy on KE06, it is recommended that a 0 ohm resistor R13 be soldered on. Ensure there is no power supply from P3V3_MOTOR and P3V3 sourced from I/O headers.3Serial and Debug Adapter (OpenSDA)OpenSDA is an open-standard serial and debug adapter. It bridges serial and debug communications between a USB host and an embedded target processor as shown in Figure 3.VDD_KE06KE06 MCU power supply.Header J9 provides a convenient means for KE06 energy consumption measurements.Header J14 for KE06 power supply selection: 3.3V or 5V.J14 Pin1&2 connected, 3.3V power supply,J14 Pin2&3 connected, 5V power supply.P3V3_SDAOpenSDA circuit power supply. Can be 3.3V only.Header J10 provides a convenient means for K20 energy consumption measurements.P5V_SDA INPUT [J6 Pin1] Input 5V Power supplied from the OpenSDA USB connector. P5-9V_VIN INPUT [J4 Pin16] Power supplied from the V IN pin of the I/O headers.P3V3_MOTOR INPUT [J2 Pin13] Input 3.3V power supplied from motor control header.P5V_USB OUTPUT[J4 Pin10] Output 5V to the I/O headers.Sourced from J6 USB (P5V_SDA) supply through a back drive protection Schottky diode.Table 2. Power suppliesSerial and Debug Adapter (OpenSDA)Figure3. OpenSDA block diagramOpenSDA is managed by a Kinetis K20 MCU built on the ARM® Cortex™-M4 core. The OpenSDA circuit includes a status LED (D4) and a reset pushbutton (SW1). The pushbutton asserts the reset signal to the KE06 target MCU. It can also be used to place the OpenSDA circuit into Bootloader mode by holding down the reset pushbutton while plugging the USB cable to USB connector J6. Once the OpenSDA enters bootloader mode, other OpenSDA applications such as debug app can be programmed. SPI and GPIO signals provide an interface to the SWD debug port of the KE06. Additionally, signal connections are available to implement a UART serial channel. The OpenSDA circuit receives power when the USB connector J6 is plugged into a USB host.3.1Debugging InterfaceSignals with SPI and GPIO capability are used to connect directly to the SWD of the KE06. These signals are also brought out to a standard 10-pin (0.05”) Cortex Debug connector (J7) as shown in Figure 4. It is possible to isolate the KE06 MCU from the OpenSDA circuit and use J7 to connect to an off-board MCU. To accomplish this, cut the 0 ohm resistor R58. This will disconnect the SWD_CLK pin to the KE06 so that it will not interfere with the communications to an off-board MCU connected to J7.When KE06 on FRDM board is 5V powered, and the OpenSDA is power off, there need to connect an external debugger to debug KE06 on board.Serial and Debug Adapter (OpenSDA)Figure4. SWD debug connector to KE063.2Virtual Serial PortA serial port connection is available between the OpenSDA MCU and UART1 pin PTC7 (TXD1) and PTC6 (RXD1) of KE06. Several of the default OpenSDA applications provided by Freescale, including the MSD Flash Programmer and the P&E Debug Application, provide a USB Communications Device Class (CDC) interface that bridges serial communications between the USB host and this serial interface on the KE06.3.3KE06 Microcontroller3.3.1Clock SourceThe Kinetis KE06 microcontrollers feature an on-chip oscillator compatible with two ranges of input crystal or resonator frequencies: 32 kHz (low frequency mode), 4-20 MHz (high frequency mode).The KE06 on the FRDM-KE06 is clocked from an 8 MHz crystal.3.3.2Serial PortThe serial port interface signals used with OpenSDA are UART1 pin PTC7 (TXD1) and PTC6 (RXD1). These signals are also connected to I/O header J1.3.3.3ResetThe PTA5/RESET signal on the KE06 is connected externally to a pushbutton SW1. The reset button can be used to force an external reset event in the target MCU. The reset button can also be used to force the OpenSDA circuit into bootloader mode when plugging the USB cable to J6. See Section3, “Serial and Debug Adapter (OpenSDA)” section for more details.Serial and Debug Adapter (OpenSDA)3.3.4DebugThe sole debug interface on all Kinetis E Series devices is a Serial Wire Debug (SWD) port. The primary controller of this interface on the FRDM-KE06 is the onboard OpenSDA circuit. However, a 2x5-pin (0.05”) Cortex Debug connector, J7, provides access to the SWD signals for the KE06 MCU. The following table shows SWD connector signals description for KE06:3.4ThermistorOne thermistor (RT1) is connected to two ADC inputs (PTF4/ADP12, PTF5/ADP13) of KE06 for evaluating the ADC module.Figure 5. Thermistor connectionTable 3. ARM JTAG/SWD mini Connector DescriptionPin FunctionConnection to KE061VTref 3.3V or 5V KE06 power supply (VDD_KE06)2SWDIO/TMS PTA4/SWD_DIO 3GNDGND4SWDCLK/TCK PTC4/SWD_CLK 5GND GND 6SWO/TDO NC 7NC NC 8TDI NC 9NC NC10RESETPTA5/RESETSerial and Debug Adapter (OpenSDA)3.5Infrared PortOne infrared Rx port and one Tx port (as shown in the following figure) are connected to ACMP0 input pin (ACMP0_IN1) and UART0 TXD0 pin of KE06 to demonstrate the capability of SCI0 modulated by a flextimer to generate infrared signals and use ACMP0 as a filter to receive the SCI data via infrared signal.Figure6. Infrared connection3.6Key buttonsTwo key buttons are connected to PTH3/4 to demonstrate KBI function of KE06, which can capture both falling edge and rising edge of key button input, as shown in the following figure.Serial and Debug Adapter (OpenSDA)Figure7. Key buttons connection3.7Three-axis accelerometerA Freescale MMA8451Q low power, three-axis accelerometer is interfaced through an I2C bus and two GPIO signals as shown in the following table. By default, the I2C address is 0x1D (SA0 pulled high).Table4. Accelerometer signal connectionsMMA8451Q KE06SCL PTA3SDA PTA2INT1 PTD4INT2 PTD3Serial and Debug Adapter (OpenSDA)Figure8. Accelerometer connection3.8RGB LEDThree PWM-capable pins are connected to a red, green, blue LED. The signal connections are shown in the table below.Table5. RGB LED Signal ConnectionsRGB LED KE06Red Cathode PTG5/FTM2CH3Green Cathode PTG6/FTM2CH4Blue Cathode PTG7/FTM2CH5Serial and Debug Adapter (OpenSDA)Figure9. GB LED connection3.9CANThe CAN phy on KE06 FRDM board is 3.3V powered.Table6. CAN signal connectionCAN Phy KE06D CAN_TXR CAN_RXSerial and Debug Adapter (OpenSDA)Figure10. CAN3.10Input/Output HeadersThe KE06 microcontroller is packaged in an 80-pin LQFP. Some pins are utilized in on-board circuitry, but many are directly connected to one of four I/O headers (J1, J2, J3, J4 and J5). J1 and J2 also function as motor control headers to provide access to a motor control board such as simple BLDC motor driving board APMOTOR56F8000E.Serial and Debug Adapter (OpenSDA)Figure11. I/O headers3.11Arduino CompatibilityThe I/O headers on the FRDM-KE06 are arranged to allow compatibility with peripheral boards (known as shields) that connect to Arduino and Arduino-compatible microcontroller boards. The pins on the headers share the same mechanical spacing and placement as the I/O headers on the Arduino Uno Revision 3 board design. See Figure11 for compatible signals.Document Number:FRDMKE06UG Rev. 003/2014Information in this document is provided solely to enable system and software implementers to use Freescale products. There are no express or implied copyright licenses granted hereunder to design or fabricate any integrated circuits based on the information in this document.Freescale reserves the right to make changes without further notice to any products herein. Freescale makes no warranty, representation, or guarantee regarding the suitability of its products for any particular purpose, nor does Freescale assume any liability arising out of the application or use of any product or circuit, and specifically disclaims any and all liability, including without limitation consequential or incidental damages. “Typical” parameters that may be provided in Freescale data sheets and/or specifications can and do vary in different applications, and actual performance may vary over time. All operating parameters, including “typicals,” must be validated for each customer application by customer’s technical experts. Freescale does not convey any license under its patent rights nor the rights of others. Freescale sells products pursuant to standard terms and conditions of sale, which can be found at the following address: /SalesTermsandConditions.How to Reach Us:Home Page:Web Support:/supportFreescale, the Freescale logo, and Kinetis, are trademarks of FreescaleSemiconductor, Inc., Reg. U.S. Pat. & Tm. Off. All other product or service names arethe property of their respective owners. ARM and Cortex are the registered trademarksof ARM Limited. ARMCortex-M4 is the trademark of ARM Limited.© 2014 Freescale Semiconductor, Inc.。
Fiio K3 用户手册说明书

K3 Complete User manual1、Product introductionK3 is a multi-function USB DAC for PC-HiFi. Being connected to a computer, it can work such as USB decoding, USB digital interface, audio decoding and amplification, etc.Product features:●Dual USB AUDIO mode●Flagship decoding capability PCM384k/DSD256●RGB work indicator●Dual headphone outputs, dual digital audio outputs●ADC type volume controlList of items included in package(please check to make sure that all items are included)1)USB A-Type C cable 1pc2)Spare foot pad 4pcs3)Quick user guide 1pc4)Warranty card 1pc(Note: The products, accessories, user interface and other illustrations in the manual are schematic and are for reference only. Due to product updates and upgrades, the actual product and schematic diagram may be slightly different. Please refer to the actual product.)2、Ports and indicators explained:①2.5mm balanced headphone output interface:Connect a 2.5mm earphone to this jack, balance the boost function will be started up automatically, which can improve the output power by about 50%.②3.5mm single-ended headphone output interface:Connect a3.5mm headset to this jack③Bass boost switch:When the switch is turned to the left, bass boost is OFF; and switch to the right, the bass boost is ON;④Low/high gain switch: When the switch is turned to the left, it means low gain, the switch to the right means high gain, and the high gain can be adjusted based on different types of headphones;⑤RGB indicator: This light is located next to the power/volume knob. While playing music, the indicator will display different colors according to the sampling rate.⑥Power/Volume knob: Turn the knob clockwise to stop and turn the power on, then continue to rotate to increase the volume. Turn counterclockwise to decrease the volume, continue to rotate and hear the beep and turn off the power. When the power is off, the white dot on the knob points to the RGB light;⑦Linear output: Directly driven by OPA1612, to ensure the high quality of sound reproduction, suitable for speakers, amps, decoders, etc.;⑧USB mode selection switch: When the switch is set to 1.0, it is USB Audio 1.0 drive-free mode, when the switch is dialed to 2.0, it represents USB Audio 2.0 drive mode;⑨Type C USB interface: Connect the computer (Windows system or OS system) to get power to K3. The audio input must use this port;⑩COAX OUT: Coaxial output port, this digital output port is used to connect speakers, amplifiers or decoders with coaxial input;⑪OPT OUT: Optical output port for connecting speakers, amplifiers or decoders with optical input.3, the usage stepsStep 1, select the appropriate USB mode and connect to the computer with the data cable●USB Audio 1.0, decoding sampling rate can reach 96k/24bit, noneed to driveAfter connecting the data cable, turn the power/volume knob clockwise until you hear a click and the device turns on.Select the K3 device on the computer side.●USB Audio 2.0, decoding sampling rate can reach 384k/DSD256,driver needs to be install in Windows.After connecting the data cable, turn the power/volume knob clockwise until you hear a click and turn the device on.For the MAC computer, there is no need to install the driver, but need to select K3 as sound device in Mac.For Windows system computers, please go to FiiO official website to download and install USB driver, download link /q1mkiifaq, driver installation tutorial please see Appendix 1 of this document, select K3 as output device on the computer.●How to select K3 as sound device:For example, Windows 7 system, right click on the desktop taskbar volume icon, then select the playback device to enter the "sound" management interface, finally Choose speaker “FiiO Q-series” as default.note:✧USB mode(1.0 to 2.0) switch needs to re-plugged and connectedto the computer✧Because K3 needs power from the source, and power supply anddata translate share the same slot, it is designed for desktopcomputers or notebooks. Mobile devices are not recommended.✧When the phone is turned on or plugged in, the indicator lightwill flash then keep ON.✧When K3 is turned off or disconnected, the indicator will be off. Step 2, select output jack according to the usage sceneScene 1: Connect to the headset using a 2.5mm or 3.5mm portnote:✧When both headphone jack and a BAL jack are plugged in, only theBAL jack will be valid;✧If you want to use the 3.5mm headphone jack, please unplug the2.5mm balanced jack device;Scene 2: Connect to active speaker or amplifier with a 3.5mm audio cablenote:line out is controlled by the power/volume knob and can work with2.5mm/3.5mm output at the same time ; but recommend to eject the2.5mm/3.5mm headphones while using the line out.Scene 3: Connect to the amplifier with coaxial inputnote:✧The coaxial output supports up to 192k sampling rate and DOPoutput of DSD64. If the device does not support, please adjust the audio output settings of the PC player;✧Power/volume knob adjustment is invalid to the coaxial outputvolume.Scene 4: Connect to the device with optical input portnote:✧The coaxial output supports up to 192k sampling rate and DOPoutput of DSD64. If the device does not support, please adjust the audio output settings of the PC player;✧Power/volume knob adjustment is invalid to the optical outputvolume.Step 3, play the song on the computer using the music app First select K3 as the output device in the playback settings of the playback software. Take FB2000 as an example. Appendix document 2 is for reference. Then play the music and adjust the power/volume knob tothe appropriate volume to enjoy the music.note:✧It is recommended to adjust the volume of the computer to themaximum. Control the output volume of the unit by adjusting the volume knob.●When playing songs with different sampling rates, the indicatorlight will change to display a specific color accordingly.Playing the music with 48KHz sample rate or below, it will display blue;Playing the music with sample rate above 48KHz, it will display yellow;When playing a DSD track, it will display green.●BassWith the bass boost function switch on, there will be a strong bass effect when playing music.●GainThe maximum output with high gain is 6dB higher than the low gain, which is suitable for higher impedance headphones.Please change the gain switch according to the following steps safely:Turn off K3 first ---- turn the gain switch to the high gain position ---- turn on the unit then gradually adjust to appropriate volume.note:Switching to high gain during use will increase the output power suddenly, which may damage your headphones and hurt your ears.5, safety instructions★When the system is abnormal, try to re-plug in the USB cable.★Before using, please adjust it to appropriate volume (the LINE OUT volume can be adjusted).★To avoid pop sound that can hurt your ears, it is not recommended to wear headphones before plugging the headphones.★Do not repair by yourself, disassemble or put the product in a place with water★When using headphones, you will not be able to hear the external environment. For your personal safety, please do use headphones in a dangerous environment.★Switching to high gain during use will increase the output power suddenly, which may damage your headphones and hurt your ears.6, troubleshootingThe following are some of the problems that may occur during the use and some solutions you could try. If you encounter an unsolvable problem, please contact FiiO customer service center(****************).Fault 1: No sound output●Check whether this unit is turned on.●Check whether the latest driver is downloaded on the official website and installed correctly.●Check whether Control Panel\All Control Panel Items \Sound shows "FiiO Q series"●Check whether the ‘FiiO Q series’ in the "playback device" is the default device●Check whether the headset is plugged in totally.●Check whether the volume is too low, increase the volume of the connected device or adjust the volume knob of K3 to increase the volume of the unit.Fault2: Small sound●When using a high-impedance earphone, it is recommended to set the GAIN switch to “H”.●You can increase the volume of the connected device or adjust the volume knob of K3 to increase the volume of the unit.●In-ear earphone and headphones are recommended for PO or BAL output, and insertion of line output may result in less sound7, Specification listNote: Specifications are subject to change and are subject to change without notice.8, learn moreTo learn more about FiiO products, please go to .Appendix 1: How to install driverNote: Please install the driver for K3 as follows (take win7 32-bit system as an example)First visit driver download link to download the official latest driver, as shown below:After the download is complete, unzip it,then double-click"FiiO_USB_DAC_Driver-V4.47.0.exe" to drive the application installer.After running the program, follow the steps below:You can customize which disk to install on, or you can install it on the C drive as default. If the default C drive is installed, click "install"During the installation process, you may encounter 2-3 anti-virus software interception. You need to manually select “Allow this operation” or “Allow all operations of the program”. “Allow loading” (this process is very important if you block the operation or Blocking loading will lead to failed driver installation)Appendix 2, FB2000 choose K3 operation tutorialOpen FB2000, select menu "Library - Configuration" to enter the parameter option setting interface, as below:The "Play" - "Output" device can be selected, for example, KS: K3, click "Apply", and then click "Confirm", as shown below:After selecting the output device, return to the main interface, select and play a song. Adjust it to appropriate volume, plug in your headphone and enjoy the music.To play DSD songs, you can choose the following output:。
A4TECH 无线键盘使用说明书

Radio Wireless Keyboard User’s GuideBrand : A4TECHModel: RFKB-23THIS DEVICE COMPLIES WITH PART 15 OF THE FCC RULES. OPERATION IS SUBJECT TO THE FOLLOWING TWO CONDITIONS: (1) THIS DEVICE MAY NOT CAUSE HARMFUL INTERFERENCE AND (2) THIS DEVICE MUST ACCEPT ANY INTERFERENCE RECEIVED, INCLUDING INTERFERENCE THAT MAY CAUSE UNDESIRED OPERATION.Federal Communications Commission RequirementsThe equipment has been tested and found to comply with the limits for Class B Digital Device, pursuant to part 15 of the FCC Rules. These limits are designed to provide reasonable protection against harmful interference in a residential installation. This equipment generates, uses and can radiate radio frequency energy and, if not installed and used in accordance with the instruction, may cause harmful interference to radio communication. However, there is no guarantee that interference will not occur in a particular installation. If this equipment does cause harmful interference to radio or television reception, which can be determined by turning the equipment off and on, the user is encouraged to try to correct the interference by one or more of the following measures:z Reorient of relocate the receiving antenna.z Increase the separation between the equipment and receiver.z Connect the equipment into an outlet on a circuit different from that to which the receiver is connected.z Consult the dealer or an experienced radio/TV technician for help.The changes or modifications not expressly approved by the party responsible for compliance could void the user's authority to operate the equipment.Getting Ready1.Turn off the power of your computer.2.Remove the existing keyboard (and mouse for the A4Tech® WirelessDesktop).3.Install the AA alkaline batteries in the Wireless keyboard. Remove the batterycompartment cover on the bottom of the keyboard by squeezing the cover infrom the tab to release it.4.Install the AAA alkaline batteries in the Wireless mouse (for the A4Tech WirelessDesktop).(a) Remove the battery compartment cover on the bottom of the mouse bypressing down on the tab. Insert the batteries as shown in side the batterycompartment. Replace the cover.(b)Or press the up cover and move backward as shown here, and by sliding the cover off. Insert thebatteries as shown inside the battery compartment. Replace the cover.Setting Up the Keyboard or Wireless Desktop1.Make sure that your computer is turned off.2.Connecting the Receiver’s Keyboard Cable:(a)When connecting to an IBM AT keyboard port, use the 5-pin DIN connector already attached to the keyboard cable.(b)When connecting to a PS/2-style with adapter, 6-pin DIN keyboard port, it work only for the signal of keyboard..(c)When connecting to USB port, it can work to receive the signal of keyboard and mouse.3.Connecting the Receiver’s Mouse Cable (Wireless Desktop): Connect the receiver’s green mouse cable to the computer’s PS/2 mouse port4.Place the receiver eight inches (20 centimeters) from anyelectromechanical device.Installing the Mouse Software-iWheelWorks andKeyboard software-iKeyWorksOfficeBefore you can take advantage of the many features your mouse and keyboardoffers, you must install the driver. The driver is in the installation diskette thatcame packaged with your mouse and keyboardWindows 95/98/Me/2000/NT4.0 installationInsert the installation diskette into your floppy disk drive.Click the Start button and then click Run.In the Run dialog window, type A:\setup, where “A” is the letter of your floppy disk drive.Click OK and follow the instructions on your screen to complete the installation.Selecting the Frequency ChannelThe Wireless keyboard and Mouse operates on two frequency channels. To prevent interference when using twoRF Mice in close proximity a different frequency channel should be used for each mouse. Refer to thefollowing to change the frequency channel for your keyboard and mouse: Set the frequency channel on the receiver to 1 or 2. Set the frequency channel on the keyboard and mouse to 1 or 2.The Wireless keyboard and mouse ID codeEach keyboard and mouse is assigned a unique ID code at manufacture, so the receiver only picks up the signal from your mouse and prevents other Wireless keyboard or mouse radio signals from operating on your computer. This feature can also be disabled, allowing other Wireless pointingdevices to operate your computer.Connecting the Wireless Mouse ID CodeWhen the driver installation is finished your computer reboots and the Wireless Mouse window (shown on the right)appears.CONNECT ID: Move the Wireless Mouse for a few seconds to establish a connection, then click Connect ID. Theunique ID code of your mouse is recognized and another RF pointing device will not function on your computer.Exit: Click Exit if no other RF pointing devices are within 3 meters range or if you want other RF pointing devices to beable to access your computer.Changing the Wireless Mouse ID CodeYou can use a new Wireless Mouse on your computer without changing the Radio receiver; you just need to change the ID code. Refer to the following:1. Press [Shift + Alt + F11] or [Shift + Alt + F12] to call up the Wireless Mouse ID Code window.2. Move the Wireless Mouse for a few seconds to establish a connection, then click Connect ID.3. The new ID code is connected and the Wireless Mouse window closes.4. Click Exit to close the Wireless Mouse ID code window.Connecting the Wireless Keyboard ID CodeManually establish communication between the receiver and keyboard.(a) Press any key from the keyboard(b) Press the ID Connect button on the receiver the green LED light will show you the keyboard ID be connect. If the green LED light is off then keyboard ID is disconnect.。
3B SCIENTIFIC NTC温度传感器说明书

3B SCIENTIFIC® PHYSICS1Instruções de operação08/17 JS/SD1 Resistência PTC em invólucro de metal2 Cabo de conexão com conectores de 4 mmA sonda resistora PTC é projetada para a utilização na categoria I.∙ Utilizar somente fontes de tensão comtransformador isolador de segurança que garantam desligamento seguro da rede de alimentação. ∙ Nunca conectar a sonda resistora emcircuitos de corrente de rede. ∙ Monitorar e garantir, por princípio, corrente etensão, para que a potência de 0,2 W e a corrente contínua de 30 V não seja ultrapassada.A sonda resistora PTC pode ser imersa em água fervente na operação.Cuidado ao fazer experiências com água quente. Perigo de queimadura!∙ Cuidado! Não expor a fonte a líquidos. ∙ Retirar o plugue da tomadacaso a fontetenha sido submersa.A sonda resistora PTC à prova de água, 100 Ω é utilizada em experiências de análise da dependência da temperatura de uma resistência de semicondutor com coeficiente positivo de temperatura (PTC). Para isto, a sonda é imersa em água e a corrente que passa pelasonda é medida com tensão conhecida. Sonda:B59100C050A070 Resistência a 25 °C: 100 Ω (±10 %) T Sense :50 °C Temperatura máxima: 120 °C Potência máxima: 0,2 W Tensão máxima: 30 V DC Categoria: CAT IConexão:Conectores desegurança de 4 mm Comprimento total: 0,75 m Peso:aprox. 40 g123B Scientific GmbH ▪ Rudorffweg 8 ▪ 21031 Hamburgo ▪ Alemanha ▪ Alterações técnicas reservadas © Copyright 2017 3B Scientific GmbH∙Medir a corrente em dependência da temperatura da água com tensão contínua de 4 V e, a partir daí, calcular a resistência.∙Na medida em que o aparelho em si deva ser descartado, ele não deve ser descartado no lixo comum. Em caso de utilização em lares privados, ele pode serdescartado nas empresas locais legalmente habilitadas para descarte.∙ Cumprir as determinações de descarte de lixo eletrônico.R / k ΩϑR / k Ωϑ。
ScanDIMM-SO204 DDR3 Boundary-Scan Based Digital Te
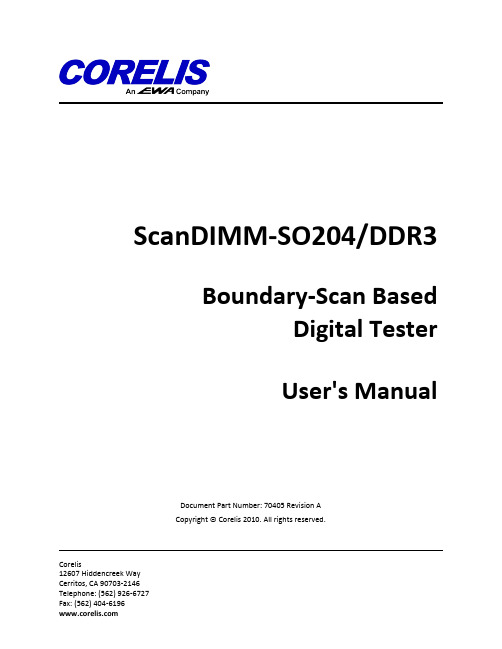
ScanDIMM-SO204/DDR3Boundary-Scan BasedDigital TesterUser's ManualDocument Part Number: 70405 Revision ACopyright © Corelis 2010. All rights reserved.Corelis12607 Hiddencreek WayCerritos, CA 90703-2146Telephone: (562) 926-6727Fax: (562) 404-6196Table of ContentsChapter 1: Product Overview. . . . . . . . . . . . . . . . . . . . . . . . . . . . . . . . . . . 1 Introduction. . . . . . . . . . . . . . . . . . . . . . . . . . . . . . . . . . . . . . . . . . . . . . . . . . . . 1 Features of the ScanDIMM-SO204/DDR3. . . . . . . . . . . . . . . . . . . . . . . . . . . . . . . . . . . 1 ScanDIMM-SO204/DDR3 Specifications. . . . . . . . . . . . . . . . . . . . . . . . . . . . . . . . . . . . 2Chapter 2: ScanDIMM-SO204/DDR3 Installation. . . . . . . . . . . . . . . . . . . . . . . . 4 . . . . . . . . . . . . . . . . . . . . . . . . . . . . . . . . . . . . . . . . . . . . . . . . . . . . . 4 OverviewScanDIMM-SO204/DDR3 Hardware. . . . . . . . . . . . . . . . . . . . . . . . . . . . . . . . . . . . . . . 4 ScanDIMM-SO204/DDR3 Software. . . . . . . . . . . . . . . . . . . . . . . . . . . . . . . . . . . . . . . 5 Connecting to the Boundary-Scan Controller. . . . . . . . . . . . . . . . . . . . . . . . . . . . . . . . . 5 Indicator LEDs. . . . . . . . . . . . . . . . . . . . . . . . . . . . . . . . . . . . . . . . . . . . . . . . . . . 6 Mating Connectors. . . . . . . . . . . . . . . . . . . . . . . . . . . . . . . . . . . . . . . . . . . . . . . . 7 . . . . . . . . . . . . . . . . . . . . . . . . . . . . . . . . . . . . . . . . . . . . . . . . . . . . 7 AccessoriesChapter 3: Preparation of Test Input Files. . . . . . . . . . . . . . . . . . . . . . . . . . . . 8 Overview. . . . . . . . . . . . . . . . . . . . . . . . . . . . . . . . . . . . . . . . . . . . . . . . . . . . . 8. . . . . . . . . . . . . . . . . . . . . . . . . . . . . . . . . . . . . . . . . . . . . . . . . . . . 8 PreparationAdd the ScanDIMM BSDL File. . . . . . . . . . . . . . . . . . . . . . . . . . . . . . . . . . . . . . . . . . 8 Add BSDL Files Dialog. . . . . . . . . . . . . . . . . . . . . . . . . . . . . . . . . . . . . . . . . . . . . . . 9 TAP Pins Not Found in Netlist Warning (Safe to Ignore). . . . . . . . . . . . . . . . . . . . . . . . . . . . 9 Insert a TAP Break. . . . . . . . . . . . . . . . . . . . . . . . . . . . . . . . . . . . . . . . . . . . . . . . 10 Testing the Socket Power and Ground Pins. . . . . . . . . . . . . . . . . . . . . . . . . . . . . . . . . . 10Chapter 4: Executing Selftest. . . . . . . . . . . . . . . . . . . . . . . . . . . . . . . . . . 11 Overview. . . . . . . . . . . . . . . . . . . . . . . . . . . . . . . . . . . . . . . . . . . . . . . . . . . . . 11 Infrastructure Test. . . . . . . . . . . . . . . . . . . . . . . . . . . . . . . . . . . . . . . . . . . . . . . 11 . . . . . . . . . . . . . . . . . . . . . . . . . . . . . . . . . . . . . . . . . . . . . . . . . . . . . . . 11 StepsChapter 5: Troubleshooting. . . . . . . . . . . . . . . . . . . . . . . . . . . . . . . . . . . 13 . . . . . . . . . . . . . . . . . . . . . . . . . . . . . . . . . . . . . . . . . . . . . . . . . . . . . 13 OverviewNotes. . . . . . . . . . . . . . . . . . . . . . . . . . . . . . . . . . . . . . . . . . . . . . . . . . . . . . . 13Chapter 6: Legal and Contact Information. . . . . . . . . . . . . . . . . . . . . . . . . . . 14Chapter 1:Product Overview IntroductionThe ScanDIMM-SO204/DDR3 Digital Tester module provides an easy-to-use method for structurally testing 204-pin Small Outline Dual Inline Memory Module (SO-DIMM or SODIMM) sockets. Through the use of boundary-scan technology, theScanDIMM-SO204/DDR3 Digital Tester provides 196 fully bi-directional test signals. A Boundary-Scan Test Access Port (TAP) connects to a host computer, which provides virtually unlimited memory depth for testing each of the SO-DIMM socket pins. The 204-pin sockets are often used for Double Data Rate Dynamic Random Access Memory (DDR3 SDRAM) modules. The ScanDIMM-SO204/DDR3 offers an accurate and easy-to-use mechanical and electrical solution for connecting test equipment to SO-DIMM sockets.Features of the ScanDIMM-SO204/DDR3•Tests 204-pin DDR3 SO-DIMM sockets•Tests for opens on the socket's power and ground pins• 1.5V DIMM interface, 3.3V tolerant• 1.8V TAP interface, 3.3V tolerant•LEDs indicate power status and active TAP connection•Compatible with the Corelis ScanExpress boundary-scan test development tools and other third party softwareThe figure below shows the ScanDIMM-SO204/DDR3 module with Pin 1 of the TAP IN connector identified.Figure 1-1. ScanDIMM-SO204/DDR3 module (top view)ScanDIMM-SO204/DDR3 SpecificationsSize and Form FactorMechanical Compatibility JEDEC MO-268C (204-pin DDR3 SO-DIMM)Dimensions67.6 mm x 30.00 mm ± 0.15 mm[2.66 inches x 1.18 inches ± 0.01 inches]PCB thickness 1.00 mm ± 0.10 mm[0.039 ± 0.01 inches]Connector Keying 1.5V-compatibleMaximum Test Clock (TCK) FrequencyMaximum TCK Frequency25 MHzLEDsPWR Indicates the 1.5V power source is presentTAP ON Indicates the TAP is connectedTAP ConnectorsTAP IN Connector10-pin Single Row 0.100-inch spacing(Samtec part no. TSM-110-01-G-SH or equivalent) Power Requirements (Provided by the 204-pin mating socket)1.50 V0.250 A (Maximum)Operating EnvironmentTemperature0° C to 55° CRelative Humidity10% to 90%, non-condensingAbsolute Maximum RatingsTable 1-1. Absolute Maximum RatingsRecommended Operating ConditionsTable 1-2. Recommended Operating ConditionsDC Electrical Characteristics (SO-DIMM Socket Interface)(1.5V DC Over Recommended Operating Conditions)Table 1-3. DC Electrical Characteristics (SO-DIMM Socket Interface)DC Electrical Characteristics (JTAG Interface)(1.8V DC Over Recommended Operating Conditions)Table 1-4. DC Electrical Characteristics (JTAG Interface)Chapter 2:ScanDIMM-SO204/DDR3 Installation OverviewTo ensure reliable operation of the ScanDIMM-SO204/DDR3, it is important to connect it properly to both the Corelisboundary-scan controller and the 204-pin DDR3 SO-DIMM socket on the unit under test (UUT).ScanDIMM-SO204/DDR3 HardwareThe ScanDIMM-SO204/DDR3 product consists of the following components:•ScanDIMM-SO204/DDR3, Corelis P/N 10408•User's Manual, Corelis P/N 70405•Host Adapter Cable, 10-pin, Corelis P/N 15336The ScanDIMM-SO204/DDR3 product is also available in a 'mirrored' version that is functionally identical but has a reversed form factor.The ScanDIMM-SO204/DDR3/Mirrored product consists of the following components:•ScanDIMM-SO204/DDR3/Mirrored, Corelis P/N 10409•User's Manual, Corelis P/N 70405•Host Adapter Cable, 10-pin, Corelis P/N 15336The files related to the ScanDIMM-SO204/DDR3 are installed by the ScanExpress installer.Ensure that all materials listed are present and free from visible damage or defects before proceeding. If anything appears to be missing or damaged, contact Corelis at the number listed on the title page immediately.The figure below shows the ScanDIMM-SO204/DDR3 and the cables that are included with the product.Figure 2-1. ScanDIMM-SO204/DDR3 and Cable AccessoriesScanDIMM-SO204/DDR3 SoftwareThe ScanExpress CD installs the files to a subdirectory of the ScanExpress TPG application.The default location is:"C:\Program Files\Corelis\ScanExpressTPG\ScanDIMM-SO204-DDR3".Table 2-5. ScanDIMM-SO204/DDR3 FilesConnecting to the Boundary-Scan ControllerThe external boundary-scan controller connects to the ScanDIMM-SO204/DDR3 TAP IN connector via the 10-pin Host Adapter Cable.Connect one end of the Host Adapter Cable P/N 15336 to the TAP IN connector of the ScanDIMM-SO204/DDR3.Connect the 10-pin cable from the boundary-scan controller (ScanTAP-4, ScanTAP-8, etc.) to the other end of the adapter cable. The TAP Voltage for the boundary-scan controller should be set to 1.8VThe figure below shows a block diagram for the a typical TAP connection to a ScanDIMM-SO204/DDR3 module.Figure 2-2. Block Diagram of Connection to a ScanDIMM-SO204/DDR3This table shows the pin assignments for the TAP IN connector.Table 2-6. TAP IN Connection ListThe TAP IN connector conforms to the popular Corelis 10-pin TAP connector pinout except that it is a single row (10 x 1) instead of dual row (5 x 2). The Host TAP Adapter Cable P/N 15336 is a 1:1 adapter cable. The pin assignment is standard, connecting to any Corelis controller using the appropriate standard 10-pin TAP cable. It is best to use the PCI-1149.1/Turbo equipped with a ScanTAP-4 Intelligent Pod, with one TAP connected to the ScanDIMM-SO204/DDR3 and with additional TAP(s) connected to the UUT. Other Corelis controllers like the NetUSB-1149.1/E can also be used so that the UUT can connect on a separate TAP.The figure below shows the TAP connections for a ScanDIMM-SO204/DDR3 module on TAP1 and the Target UUT on TAP2.Figure 2-3. Connection of a ScanDIMM-SO204/DDR3 Module and the Target using Separate TAPs Indicator LEDsTwo LEDs indicate the status of the ScanDIMM-SO204/DDR3 module. D1 is labeled PWR. It illuminates if theScanDIMM-SO204/DDR3 is receiving power from the target (through pins 57, 60 and 176). If the LED is not illuminated, the ScanDIMM-SO204/DDR3 module is not powered up. D2 is labeled TAP ON. It indicates that a connection to a controller is detected. The ScanDIMM-SO204/DDR3 module will not operate unless D2 is illuminated.Mating ConnectorsThe table below shows the mating connectors needed to make cables for the Boundary-Scan connector.Table 2-7. Mating Connectors for the ScanDIMM-SO204/DDR3 AccessoriesAdditional TAP Adapter Cables (P/N 15336) can be ordered from Corelis:Table 2-8. Cable Accessories for the ScanDIMM-SO204/DDR3Chapter 3:Preparation of Test Input Files OverviewThe ScanDIMM-SO204/DDR3 integrates easily with a boundary-scan test plan. When the ScanDIMM-SO204/DDR3 is installed in a socket, the socket behaves like a boundary-scan component. Once the ScanDIMM-SO204/DDR3 is plugged into the socket on the target board, the boundary-scan test system will automatically test the socket. However, regeneration of the boundary-scan tests with ScanExpress TPG is required.PreparationCopy the provided BSDL file to your local project directory.Add the ScanDIMM BSDL FileWhile in the "Preparation:BSDL Files" stage of ScanExpress TPG, click "Add..." to launch the "Add BSDL Files" dialog.Figure 3-1. ScanExpress TPG Test Preparation: Select BSDL FilesAdd BSDL Files DialogFigure 3-2. Add BSDL Files DialogUncheck the box "Show Only Devices Connected to JTAG Signals"Select the Device that corresponds to the DIMM socket on the board in the left pane.Select the BSDL File for the ScanDIMM-SO204-DDR3 in the right pane.Click "Add".Click "Close" to exit the Add BSDL Files dialog.TAP Pins Not Found in Netlist Warning (Safe to Ignore)In some cases a popup message may appear that indicates that the ScanDIMM TAP pins are not found in the netlist. The TAP connection between the boundary-scan controller and ScanDIMM module won't be in the board netlist and this warning is safe to ignore.Figure 3-3. TAP Pins Not Found in Netlist Warning (Safe to Ignore)Insert a TAP BreakThe ScanDIMM is now in the scan chain. Insert a "TAP Break" by selecting the last device in the scan chain before the ScanDIMM, right clicking and selecting "Insert TAP Break"Figure 3-4. ScanExpress TPG Test Preparation: ScanDIMM BSDL File AddedTesting the Socket Power and Ground PinsTo test the power and ground pins on the ScanDIMM-SO204/DDR3 socket, the constraint file should have the following syntax added:SENSE_HIGH VDDSENSE_LOW GNDVDD and GND are the net names of the 1.5V SDRAM power and ground signals on the target board. This syntax may already be present to test other power or ground connections in the target system.ScanExpress TPG will automatically add these constraints if the power and ground nets are specified during the Power and Ground screen of the preparation phase.Chapter 4:Executing Selftest OverviewScanExpress Runner (sold separately) can load and run the compact vector file, ScanDIMM-SO204-DDR3_Selftest_inf.cvf, and quickly verify that the ScanDIMM-SO204/DDR3 is functional. Both the ScanExpress Runner software and a Corelis Boundary-Scan controller such as the PCI-1149.1/Turbo are required to execute this file.Infrastructure TestThe infrastructure test verifies the TAP connection between the controller and the ScanDIMM-SO204/DDR3. It also verifies that the boundary-scan infrastructure of the device on the ScanDIMM-SO204/DDR3 is fully functional. The infrastructure test requires a Corelis Boundary-Scan controller, a ScanDIMM-SO204/DDR3 unit and a Host TAP cable (P/N 15336). The following steps execute an infrastructure test.Steps1.Remove any memory modules from the Unit Under Test (UUT) DIMM socket(s) to be tested.2.Install the ScanDIMM-SO204/DDR3 in the socket.3.Connect the Host TAP Adapter cable P/N 15336 to the "TAP IN" connector on the ScanDIMM-SO204/DDR3.4.Connect the 10-pin TAP cable from the external controller to the other end of the Host TAP Adapter cable.5.Apply power to the UUT.6.Make sure that both LEDs on the ScanDIMM-SO204/DDR3 illuminate.7.Double-click on the ScanExpress Runner Icon.8.Select New Test Plan from the File menu and click on the Add button.9.With the file browser, find and select the "ScanDIMM-SO204-DDR3_Selftest_inf.cvf" file. Click OK.10.Select Controller from the Setup menu, then choose the appropriate Boundary-Scan controller.11.Set the TCK frequency to 1 MHz and the TAP voltage to 1.8V.12.Select Run Test. The test should run and pass.The figure below shows a passing infrastructure test.Figure 4-1. ScanExpress Runner Infrastructure TestTroubleshooting OverviewUse the following general guidelines to troubleshoot problems when the ScanDIMM-SO204/DDR3 is added to the test system.1.Make sure the ScanDIMM-SO204/DDR3's TAP Voltage is set to 1.8V2.Make sure power is being supplied to the ScanDIMM-SO204/DDR3, the boundary-scan controller, and the target. TheScanDIMM-SO204/DDR3's green LEDs will be illuminated if power (1.5V) is being supplied to the DIMM socket and the boundary-scan controller is connected.3.Run the provided self-test and make sure that it passes.4.Reduce the TCK (test clock) frequency to 1 MHz. The TCK frequency can be set too high for the scan chain andsometimes using a lower frequency will allow the test steps to pass. Once the scan chain is known to be stable, then the TCK frequency can be increased to the maximum frequency that will allow the test steps to pass.Notes1.DDR3 modules are not backwards compatible with DDR2 modules and DDR3 modules will not fit into DDR2 sockets;forcing them can damage the ScanDIMM and/or the board.Legal and Contact InformationPRINTING HISTORYRevision A, May 2010GENERAL NOTICEInformation contained in this document is subject to change without notice. CORELIS shall not be liable for errors contained herein for incidental or consequential damages in connection with the furnishing, performance, or use of material contained in this manual.This document contains proprietary information that is protected by copyright. All rights reserved. No part of this document may be reproduced or translated to other languages without the prior written consent of CORELIS. This manual is a CORELIS proprietary document and may not be transferred to another party without the prior written permission of CORELIS. CORELIS assumes no responsibility for the use of or reliability of its software on equipment that is not furnished by CORELIS.ENVIRONMENTAL NOTICEThis product must be disposed of in accordance with the WEEE directive.TRADEMARK NOTICEScanExpress and ScanDIMM are trademarks of Corelis Inc.Other products and services named in this manual are trademarks or registered trademarks of their respective companies. All trademarks and registered trademarks in this manual are the property of their respective holders.PRODUCT WARRANTYFor product warranty and software maintenance information, see the PRODUCT WARRANTY AND SOFTWARE MAINTENANCE POLICY statement included with your product shipment.EXCLUSIVE REMEDIESTHE REMEDIES CONTAINED HEREIN ARE THE CUSTOMER'S SOLE AND EXCLUSIVE REMEDIES. CORELIS SHALL NOT BE LIABLE FOR ANY DIRECT, INDIRECT, SPECIAL, INCIDENTAL, OR CONSEQUENTIAL DAMAGES, WHETHER BASED ON CONTRACT, TORT, OR ANY OTHER LEGAL THEORY. Product maintenance agreements and other customer assistance agreements are available for Corelis products. For assistance, contact your nearest Corelis Sales and Service Office.RETURN POLICYNo items returned to CORELIS for warranty, service, or any other reason shall be accepted unless first authorized by CORELIS, either direct or through its authorized sales representatives. All returned items must be shipped pre-paid and clearly display a Return Merchandise Authorization (RMA) number on the shipping carton. Freight collect items will NOT be accepted. Customers or authorized sales representatives must first contact CORELIS with notice of request for return of merchandise. RMA's can only originate from CORELIS. If authorization is granted, an RMA number will be forwarded to the customer either directly or through its authorized sales representative.CONTACT INFORMATIONFor sales inquiries, please contact *****************.For any support related questions, please enter a support request at /support or email *******************. For more information about other products and services that Corelis offers, please visit .。
EVOS FL EVOS FL彩色成像系统说明书

EVOS™ FL ColorImaging Systems for Fluorescenceand Transmitted Light ApplicationsCatalog Numbers AMF4300, AMEFC4300Doc. Part No. ZP-PKGA-0494Pub. No. MAN0007717Rev. A.0For Research Use Only. Not for use in diagnostic procedures.OverviewThe EVOS ™FL and EVOS ™ FL Color Imaging Systemshave two types of controls: manual and onscreen. Manual controls include the the stage X–Y axis knobs, focusing knobs, objective selection wheel, phase annuli selector, and the light cube selection lever. Onscreen controls are located in the control bar at the bottom of the display screen. The channel bar at the top of the display screen shows the selected light cube or transmitted light position.2Basic OperationNote: For detailed instructions, refer to theEVOS ™ FL Imaging System User Guide (Pub. No. MAN0007988), which is provided on the USB flash drive. You can also dowload it from the EVOS ™ FL Imaging System product page at .1. Turn on the instrument using the power switch ❶ on the right side of the base.2.Plug a USB flash drive into one of the USB ports ❷ on the right side of the instrument.3. Place the sample ❸ on the stage, using a vessel holder if needed.4. Set magnification with the objective selection wheel ❹ on the front of the instrument.5.Pull the light cube selection lever ❺ all the way toward the front of the instrument. The channel bar will highlight the “Transmitted” position.CAUTION! UV HAZARD. Avoid exposure to light beam and use protective shields.NEVER look directly at UV light!1236. Turn on illumination with theLIGHT ONbutton located on the left side of the control bar.7. Focus the sample with ❻.8. Optional: T o take a picture of thetransmitted light image, click the Capture button on the control bar.9.Place the light shield box❼ on the stage, over the sample.10.Move the light cube selection lever ❺ to the desired fluorescence channel. The channel bar will highlight the selected light cube.11. With the Find & Focus tab active, turn onfluorescence illumination using the LIGHT ON button .12. Adjust the focus as necessary.13. Adjust the onthe control bar as needed.14. Click the Capture button .15. Repeat steps 10–14 to capture in eachfluorescence channel.16. Click the Overlay tab to show all channelsin color overlay mode.17. Adjust Brightness and Contrast foreach channel to bring them into desired balance.18. Click the Save button to save the colorimage (for details, refer to the EVOS ™ FL Imaging System User Guide).36LIGHT ON button Illumination slider Capture button75Overlay tab Brightness and ContrastSave buttonHelpful TipsIn Find & Focus or Actual Mode , the Color option (for EVOS ™ FL, Cat. No. AME4300) can be turned off to display a grayscale image. This often shows more details than a color image.4Onscreen Controls1. Active Channel (highlighted)2. Login Button3. Control Bar Tabs• Find & Focus • Actual- Exposure Time Slider • Overlay- Overlay Color Dialogue Box4. Light ON/OFF Button5. Illumination Slider6. Exposure Time Slider7. Image Capture Button8. Color Option9. Scalebar/Toolbar Options 10. Setting Control Button 11. Save Image Button 12. Info Display Bar 13. Selected ObjectiveFor EVOS ™ FL Color (Cat. No. AMEFC4300), use the live image Brightness , Contrast , Saturation , and HueIn Find & Focus Mode , the exposure time is set to 100 ms to assist real-time focusing, moving the stage, etc. The illumination level is approximately 60% of the amount used for image capture to minimize photobleaching and phototoxicity. Clicking longer exposure time during image capture to provide a higher-quality image.In Actual Mode , turning on the illumination results in full-powered illumination and actual exposure times for live viewing of the sample. With longer exposure times (more than 200 ms) there will be a lag between moving the focus knob and seeing the focus change onscreen.32Color option Color Adjustment button5Focusing knobsPower switchObjective selection wheelCondenser Power input jackPhase annulus selectorStage X-axis knob USB and DVI portsCoarse stage positioning knobs X-axis stage brakeStage Y-axis knobY-axis stage brakeLight cube selection leverVessel holderLCDLimited Product WarrantyLife Technologies Corporation and/or its affiliate(s) warrant their products as set forth in the Life Technologies’ General Terms and Conditions of Sale found on Life Technologies’ website at /us/en/home/global/terms-and-conditions.html. If you have any questions, please contact Life Technologies at /support.Information in this document is subject to change without notice.DISCLAIMERTO THE EXTENT ALLOWED BY LAW, THERMO FISHER SCIENTIFIC AND/OR ITS AFFILIATE(S) WILL NOT BE LIABLE FOR SPECIAL, INCIDENTAL, INDIRECT, PUNITIVE, MULTIPLE OR CONSEQUENTIAL DAMAGES IN CONNECTION WITH OR ARISING FROM THIS DOCUMENT, INCLUDING YOUR USE OF IT.Revision history Pub. No. MAN0007717Important Licensing InformationThis product may be covered by one or more Limited Use Label Licenses. By use of this product, you accept the terms and conditions of all applicable Limited Use Label Licenses.Manufacturer: Life Technologies Corporation | 22025 20th Ave SE St #100 | Bothell, WA 98021TrademarksAll trademarks are the property of Thermo Fisher Scientific and its subsidiaries unless otherwise specified.© 2017 Thermo Fisher Scientific Inc. All rights reserved./support | /askaquestion02 October 2017。
3B SCIENTIFIC 音波传播实验包说明书

3B SCIENTIFIC® PHYSICS230 V, 50/60 Hz: 1018469 / U8557180-230 115 V, 50/60 Hz: 1018468 / U8557180-115Istruzioni per l'uso04/15 TL/UDUn utilizzo conforme garantisce il funzionamento sicuro del kit. La sicurezza non è tuttavia garan-tita se il kit non viene utilizzato in modo appro-priato o non viene trattato con cura.∙In caso di rottura del cavo, danni visibili all’alloggiamento o altri difetti, non collegarepiù l'alimentatore a spina alla rete elettrica. ∙Qualora venga a contatto con liquidi, con-trassegnare l'alimentatore aspina come di-fettoso e non riutilizzarlo.∙L'impiego dell'alimentatore a spina è con-sentito per un grado di inquinamento 1 e 2.1 Asta in acciaio inossidabile da 400 mm2 Tappetino di appoggio (3 pz.)3 Asta in acciaio inossidabile da 100 mm4 Asta in alluminio da 100 mm5 Asta in legno duro da 200 mm6 Asta in PVC da 200 mm7 Asta in acciaio inossidabile da 200 mm8 Asta in ottone da 100 mm9 Asta in vetro da 200 mm10 Asta in acrilico da 200 mm11 Asta in alluminio da 200 mm12 Asta in rame da 100 mm13 Scatola microfono14 Massa battente con tubo di protezione (2pz.)15 Alimentatore a spina16 Sonda microfono (2 pz.)Acciaio inossidabile: 100, 200, 400 mmAlluminio: 100, 200 mmRame: 100 mmOttone: 100 mmLegno duro: 200 mmPVC: 200 mmAcrilico: 200 mmVetro: 200 mmDiametro:10 mmKit completo:Dimensioni: circa 430x310x80 mm3Peso: circa 2,2 kgScatola microfono:Larghezza di banda: 10 Hz – 42 kHzAmplificazione: da 20 a 70 volteImpedenza di uscita: 1 kSegnale di uscita: commutabile tra segna-le, livello, impulsoSegnale: 0 – 14 V ppLivello: 0 – 7 V CCImpulso: Low: 0 VHigh: 8 V CCLunghezza: 150 msIngressi: 2 jack da 3,5 mmUscite: 2 prese BNCAlimentazione: Alimentatore a spina12 V CA, 700 mA,grado di inquinamento2, classe di protezione 2Dimensioni: circa 100x75x35 mm3Peso inclusoalimentatore a spina: circa 450 gIl kit è costituito da: aste campione di lunghezze emateriali differenti, due sonde microfono, una scato-la microfono con alimentatore a spina per la regi-strazione, l'amplificazione e l'emissione dei segnalia un oscilloscopio, tre tappetini di appoggio.Nelle aste, con l'ausilio di una piccola massa bat-tente, si avviano per eccitazione a impulso onde sonore che si propagano lungo le aste stesse, vengono riflesse all'estremità e vengono rilevate acusticamente tramite sonde microfono. Se le aste sono lunghe, l'oscillogramma mostra treni di oscil-lazione chiaramente distinti l'uno dall'altro. Se le aste invece sono corte, per via della formazione di onde stazionarie l'oscillazione avrà un andamento sinusoidale. Dalla lunghezza dell'asta e dal tempo tra due treni di oscillazioni o dal periodo dell'oscil-lazione sinusoidale è possibile rilevare la velocità del suono specifica dei materiali.Il kit 1018468 è predisposto per una tensione di rete di 115 V (+/- 10%), il kit 1018469 di 230 V (+/-10%)Apparecchi necessari:1 kit propagazione del suono in aste1018551 1 oscilloscopio USB 2x50 MHz 1017264 2 cavi ad alta frequenza1002746Fig. 1Struttura sperimentale∙Sistemare l'asta campione e la sonda micro-fono su un tappetino di appoggio ognuna (Fig. 1).∙Collegare la sonda microfono con l'ingresso A della scatola microfono e posizionarla a una distanza di circa 1 mm presso una delle due parti frontali dell'asta campione.∙Seguire le istruzioni per l’uso della sca tola microfono. Regolare la scatola microfono al massimo dell'amplificazione e del segnale (commutatore nella posizione superiore). Con l'ausilio del cavo ad alta frequenza, col-legare l'uscita della scatola microfono al ca-nale CH1 dell'oscilloscopio. Impostazioni dell'oscilloscopio ad es. base tempo: 40 μs/DIV, deflessione verticale: 2 V/DIV CC, trigger: sorgente CH1, tipo fron-te, modalità normale, soglia 1 – 2 V.Nota:La corretta scelta della soglia di trigger e l'inten-sità della battuta sono determinanti per il suc-cesso degli esperimenti. Nella modalità normale, quando l'ampiezza del segnale scende al di sotto della soglia di trigger, l'oscillogramma vie-ne "congelato". Se la soglia di trigger è troppo bassa, la parte iniziale dell'oscillazione viene sovrascritta e risulta rappresentata solo la parte in attenuazione. In presenza di una soglia di trigger troppo alta, invece, se la battuta è troppo debole non si ha alcuna rappresentazione.∙ Con la massa battente, colpire l'asta sullaparte frontale opposta (Fig. 1).Tale eccitazione a impulso genera un'onda so-nora che si propaga nell'asta.6.1 Propagazione del suono in aste lunghe Se le aste sono lunghe, l'oscillogramma mostra treni di oscillazione chiaramente distinti l'uno dall'altro (Fig. 2).Fig. 2 Treni di oscillazioni in un'asta in acciaio inossidabile da 400 mm dopo un'eccitazione a impul-so6.2 Propagazione del suono in aste corte Se le aste invece sono corte, per via della for-mazione dionde stazionariel'oscillazione pre-senterà un andamento sinusoidale (Fig. 3).Fig. 3 Oscillazione sinusoidale in un'asta in acciaio inossidabile da 100 mm dopo un'eccitazione a impul-so6.3 Determinazione della velocità del suonolongitudinale Aste lunghe:∙ Leggere sull'oscillogramma per mezzo deicursori il tempo T 1 ad es. tra due massimi dei treni di oscillazioni.Determinare la velocità del suono c da T 1 e dallalunghezza dell'asta L , ad es. per l'asta in acciaio inossidabile da 400 mm (v. 6.1):x 20,8m m4938162µs sL c T ⋅===. Si noti che, nel tempo T 1, l'onda sonora at-traversa l'asta due volte. Aste corte:∙Leggere sull'oscillogramma per mezzo dei cursori il tempo T 2 ad es. tra due massimi dell'oscillazione sinusoidale.∙Determinare la velocità del suono c da T 2 e dalla lunghezza dell'asta L , ad es. per l'asta in acciaio inossidabile da 100 mm (v. 6.2):x 20,2m m487841µs sL c T ⋅===. Si noti nuovamente che, nel tempo T 2, l'on-da sonora attraversa l'asta due volte.6.4 Onde sonore trasversaliIn corpi solidi, per via della deviazione, possono manifestarsi anche onde sonore trasversali. ∙ Eseguire la disposizione sperimentale se-condo Fig. 4. Prendere come asta campione l'asta in acciaio inossidabile da 400 mm. Osservare una distanza di circa 1 mm tra le sonde microfono e l'asta campione. Impo-stazioni dell'oscilloscopio ad es. base tem-po: 20 μs/DIV, deflessione verticale: CH1 2 V/DIV CC, CH2 1 V/DIV CC, trigger: sor-strato in Fig. 4.Note:L'intensità della battuta influisce sulla qualità dell'oscillogramma.Per sopprimere o smorzare onde trasversali stazionarie, è possibile tenere l'asta leggermen-te premuta al centro contro la base con la mano in piano.Adeguare la soglia di trigger all'altezza degli impulsi come da indicazioni di cui al punto 6.Fig. 5 Oscillogramma di un'onda trasversale in un'asta in acciaio inossidabile da 400 mmLa Fig. 5 mostra l'oscillogramma relativo alla generazione di onde sonore trasversali in un'a-sta in acciaio inossidabile lunga 400 mm. La curva di misurazione gialla corrisponde al se-gnale registrato dalla sonda microfono sul lato eccitatore, la curva di misurazione blu al segna-le registrato dalla sonda microfono sul lato op-posto.∙ Leggere sull'oscillogramma per mezzo deicursori il tempo T fra il primo minimo del se-gnale eccitatore e il primo massimo del se-gnale in arrivo.Calcolare la velocità del suono trasversale ad es. per l'asta in acciaio inossidabile lunga 400 mm (v. sopra). A tale scopo, utilizzare la ∙Non impiegare detergenti o soluzioni ag-gressive per la pulizia del kit.∙Per la pulizia utilizzare un panno morbido eumido.∙Smaltire l'imballo presso i centri di raccolta ericiclaggio locali.∙Non gettare il kit neirifiuti domestici. Per losmaltimento delle ap-pare- cchiatureelettriche, rispet- tarele disposizioni vigenti alivello locale.3B Scientific GmbH ▪ Rudorffweg 8 ▪ 21031 Amburgo ▪ Germania ▪ 。
松下KX-FL328CN体机打印机传真机使用说明书

松下KX-FL328CN体机打印机传真机使用说明书KX-FLM663CN 1 2请在使用本机前仔细阅读快速参考指南中的安全和重要信息,并将其保存好。
请务必使用本机附带的USB 缆线。
L 本机与来电显示兼容。
您必须向服务供应商/电话公司申请并取得相应的服务。
感谢您购买Panasonic 机。
商标:L Microsoft、Windows、Windows Vista 和PowerPoint 是Microsoft Corporation 在美国或其它国家的注册商标或商标。
L Pentium 是Intel Corporation 在美国和其它国家的商标。
L 屏幕截图的翻印获得了Microsoft Corporation 的许可。
L Adobe 和Reader 是Adobe Systems Incorporated 在美国或其它国家的注册商标或商标。
L 3M 是Minnesota Mining and Manufacturing Company 的商标或注册商标。
L Avery 是Avery Dennison Corporation 的注册商标。
L XEROX 是Xerox Corporation 的注册商标。
L 在此认定的所有其它商标均属于其各自的所有者。
版权:L 本手册的版权属于松下系统网络科技株式会社,仅可能复制作内部使用。
未经松下系统网络科技株式会社的书面同意,其它任何全部或部分复制均不得进行。
Panasonic System Networks Co. Ltd. 20082 重要信息重要信息为了安全为取得最佳性能激光放射墨盒和硒鼓L 当更换墨盒或硒鼓时,不要让灰尘、水或液接触1 类激光产品到硒鼓。
否则可能会影响打印质量。
L 为取得最佳性能,建议使用Panasonic 原装墨盒和硒本机的使用激光。
若进行说明书中未鼓。
我们对于使用非Panasonic 墨盒或硒鼓导致的问注明的控制、调节或操作,可能会导致危险的放射。
- 1、下载文档前请自行甄别文档内容的完整性,平台不提供额外的编辑、内容补充、找答案等附加服务。
- 2、"仅部分预览"的文档,不可在线预览部分如存在完整性等问题,可反馈申请退款(可完整预览的文档不适用该条件!)。
- 3、如文档侵犯您的权益,请联系客服反馈,我们会尽快为您处理(人工客服工作时间:9:00-18:30)。
EC A30
RX780 RS780
1.8V 82.5R/130R 1.1V 158R/90.9R
100M DIFF
+3V
+3V_CLK_VDD
CLK_48M_USB_R R164 10K_4 SEL_SATA 24 PCIE_REQ_WWAN# CLKREQ3# SEL_HTT66 SEL_27
A
C355 C313 C359
22
R222
8.2K_4
CLK_PD# +3V
T59 T53 T49 T54 T48
CLKREQ0# CLKREQ1# CLKREQ2# CLKREQ3# CLKREQ4#
NB CLOCK INPUT TABLE
To SB 14.318MHz To NB 14.318MHz NB CLOCKS HT_REFCLKP RX780 100M DIFF RS780
*10P_4 *10P_4 *10P_4
R214 *8.2K_4
1 SEL_HTT66 0* 1 SEL_SATA 0 * 1 SEL_27 0*
66 MHz 3.3V single ended HTT clock SEL_SATA 100 MHz differential HTT clock 100 MHz non-spreading differential SRC clock 100 MHz spreading differential SRC clock 27MHz and 27M SS outputs 100 MHz SRC clock SEL_27
RP30 RP31
1 3 1 3
2 0_4P2R_4 4 2 0_4P2R_4 4
CLK_SBREFP CLK_SBREFN CLK_SBSRCP CLK_SBSRCN
8 8 10 10
To NB Diff 100MHz To SB Diff 100MHz
C
RP37 RP36 RP35
QFN64
1 3 1 3 1 3
NC or 100M DIFF OUTPUT
HT_REFCLKP HT_REFCLKN
8 8
To NB Diff 100MHz To SB 48MHz To RTS5159 48MHz
51 23 45 44 39 38
R274 R275 R205 R279 R278
CLK_48M_USB 11 CLK_48M_USB_CR EXT_SB_OSC 10 EXT_NB_OSC 8
RP33
To NB Diff 100MHz
CLK_SBREFP_R CLK_SBREFN_R CLK_SBSRCP_R CLK_SBSRCN_R NBGPP_CLKP_R NBGPP_CLKN_R CLK_PCIE_NEW_R CLK_PCIE_NEW#_R CLK_PCIE_WLANP_R CLK_PCIE_WLANN-R CLK_PCIE_WANP_R CLK_PCIE_WANN_R CLK_PCIE_LANP_R CLK_PCIE_LANN_R
5
4
3
2
1
PCB STACK UP
LAYER 1 : TOP LAYER 2 : SGND LAYER 3 : IN1
D
MK-Note Block Diagram -- AMD CONGO
Clock Gengerator
D
LAYER 4 : SVCC LAYER 5 : IN2 LAYER 6 : IN3 LAYER 7 : SGND1 LAYER 8 : BOT
CLK_PCIE_WLANP CLK_PCIE_WLANN CLK_PCIE_WANP CLK_PCIE_WANN CLK_PCIE_LANP CLK_PCIE_LANN
23 23 24 24 19 19
To Mini PCIE Slot (WLAN) To Mini PCIE Slot (WWAN) To LAN Controller
T61 T63 T60 T62
2 0_4P2R_4 4 2 0_4P2R_4 4 2 0_4P2R_4 4
C338 CG_XIN 33P/50V_4 C350 33P/50V_4 2 Y4 14.318MHZ 1 CG_XOUT 11,15,27 PCLK_SMB 11,15,27 PDAT_SMB
CPUK8_0T CPUK8_0C ATIG0T ATIG0C ATIG1T ATIG1C SB_SRC0T SB_SRC0C SB_SRC1T SB_SRC1C SRC0T SRC0C SRC1T SRC1C SRC2T SRC2C SRC3T SRC3C SRC4T SRC4C SRC6T/SATAT SRC6C/SATAC SRC7T/27M_SS SRC7C/27M_NS HTT0T/66M HTT0C/66M 48MHz_0 REF0/SEL_HTT66 REF1/SEL_SATA REF2/SEL_27 TGND0 TGND1 TGND2 TGND3 TGND4 TGND5 TGND6 TGND7 TGND8 TGND9
T42 T44 T64 T65 2 0_4P2R_4 4 22_4 22_4 33_4 158/F_4 90.9/F_4 HT_REFCLKN REFCLK_P 100M DIFF 14M SE (1.8V) NC 100M DIFF 100M DIFF 100M DIFF 100M DIFF 14M SE (1.1V) vref 100M DIFF(IN/OUT)*
R186 *261/F_4 CLK_CPUP CLK_CPUN CLK_NBGFXP CLK_NBGFXN 8 8 5 5 To CPU Diff 200MHz
+3V_CLK_VDD
+3V L39
C
+3V_CLK_48 BLM18AG601SN1D_6 C483 2.2U/6.3V_6 +1.2V_CLK_VDDIO
1
Rev 1A 1 of 42
Sheet
5
2
5
4
3
2
1
CLK_GEN_SLG8SP628
+3V +3V_CLK_VDD L40 BLM18EG601SN1D_6 C484
D
02
+1.2V +1.2V_CLK_VDDIO
3.3V(250mA)
L27 C325 0.1U/10V_4 C286 0.1U/10V_4 C287 0.1U/10V_4 C285 0.1U/10V_4 C315 0.1U/10V_4 C347 0.1U/10V_4 C354 0.1U/10V_4 BLM18AG601SN1D_6 C339 22U/6.3V_8 C284
B
100M DIFF
R165 10K_4 19 PCIE_REQ_LAN# CLKREQ4#
65 66 67 68 69 70 71 72 73 74
SLG8SP628
R4004/R4005 (value may change) NB_OSC
REFCLK_N GFX_REFCLK RES CHIP 82.5 1/16W +-1%(0402) --> CS08252FB11 RES CHIP 130 1/16W +-1%(0402)L-F --> CS11302FB15 RES CHIP 158 1/16W +-1%(0402) --> CS11582FB00 RES CHIP 90.9 1/16W +-1%(0402) --> CS09092FB15 GPP_REFCLK GPPSB_REFCLK
Place within 0.5" of CLKGEN
50 49 30 29 28 27 37 36 32 31 22 21 20 19 15 14 13 12 9 8 42 41 6 5 54 53 64 59 58 57 NBHT_REFCLKP_R NBHT_REFCLKN_R CLK_48M_USB_R SEL_HTT66 SEL_SATA SEL_27 RP34 1 3 CLK_CPUP_R CLK_CPUN_R CLK_NBGFXP_R CLK_NBGFXN_R RP32 1 3 1 3 2 0_4P2R_4 4 2 0_4P2R_4 4
Size Date:
Camera Module
A
Accelerometer (APS)
Int. KB
T/P
4
Battery
Quanta Computer Inc.
PROJECT : Congo
Document Number
Block Diagram
Friday, September 11, 2009
Internal SPK
Card Reader Realtek RTL5159
USB PORT X 3
4 in 1 Socket
SD/MMC/MS/MS-Pro
LPC BUS
ITE8502E
A
SPI Flash Charger
3
USB USB
Camera Conn. Bluetooth (BDC-2)
CLOCK GEN SLG8SP628
Friday, September 11, 2009
1
Rev 1A of 42
Sheet
2
5
4
3
2
5
4
3
2
1
03
+1.2V_VLDT
D
U26A AL4 AL3 AL2 AL1 Y6 Y5 W7 W6 U6 U5 R7 R6 M8 M7 L6 L5 J6 J5 H4 H3 T3 T4 T2 T1 P3 P4 P2 P1 M2 M1 K3 K4 K2 K1 H2 H1 P6 P5 M3 M4 P8 P9 V2 V1 VLDT_B4 VLDT_B3 VLDT_B2 VLDT_B1 L0_CADIN_H15 L0_CADIN_L15 L0_CADIN_H14 L0_CADIN_L14 L0_CADIN_H13 L0_CADIN_L13 L0_CADIN_H12 L0_CADIN_L12 L0_CADIN_H11 L0_CADIN_L11 L0_CADIN_H10 L0_CADIN_L10 L0_CADIN_H9 L0_CADIN_L9 L0_CADIN_H8 L0_CADIN_L8 L0_CADIN_H7 L0_CADIN_L7 L0_CADIN_H6 L0_CADIN_L6 L0_CADIN_H5 L0_CADIN_L5 L0_CADIN_H4 L0_CADIN_L4 L0_CADIN_H3 L0_CADIN_L3 L0_CADIN_H2 L0_CADIN_L2 L0_CADIN_H1 L0_CADIN_L1 L0_CADIN_H0 L0_CADIN_L0 L0_CLKIN_H1 L0_CLKIN_L1 L0_CLKIN_H0 L0_CLKIN_L0 L0_CTLIN_H1 L0_CTLIN_L1 L0_CTLIN_H0 L0_CTLIN_L0 VLDT_A4 VLDT_A3 VLDT_A2 VLDT_A1 L0_CADOUT_H15 L0_CADOUT_L15 L0_CADOUT_H14 L0_CADOUT_L14 L0_CADOUT_H13 L0_CADOUT_L13 L0_CADOUT_H12 L0_CADOUT_L12 L0_CADOUT_H11 L0_CADOUT_L11 L0_CADOUT_H10 L0_CADOUT_L10 L0_CADOUT_H9 L0_CADOUT_L9 L0_CADOUT_H8 L0_CADOUT_L8 L0_CADOUT_H7 L0_CADOUT_L7 L0_CADOUT_H6 L0_CADOUT_L6 L0_CADOUT_H5 L0_CADOUT_L5 L0_CADOUT_H4 L0_CADOUT_L4 L0_CADOUT_H3 L0_CADOUT_L3 L0_CADOUT_H2 L0_CADOUT_L2 L0_CADOUT_H1 L0_CADOUT_L1 L0_CADOUT_H0 L0_CADOUT_L0 L0_CLKOUT_H1 L0_CLKOUT_L1 L0_CLKOUT_H0 L0_CLKOUT_L0 L0_CTLOUT_H1 L0_CTLOUT_L1 L0_CTLOUT_H0 L0_CTLOUT_L0 F4 F3 F2 F1 Y9 Y8 AB6 AB5 AC7 AC6 AE6 AE5 AE9 AE8 AH3 AH4 AK3 AK4 AK1 AK2 Y1 Y2 Y4 Y3 AB1 AB2 AB4 AB3 AD4 AD3 AF1 AF2 AF4 AF3 AH1 AH2 AF6 AF5 AD1 AD2 AB8 AB9 V4 V3