第3章 涡流检测技术
涡流检测——精选推荐
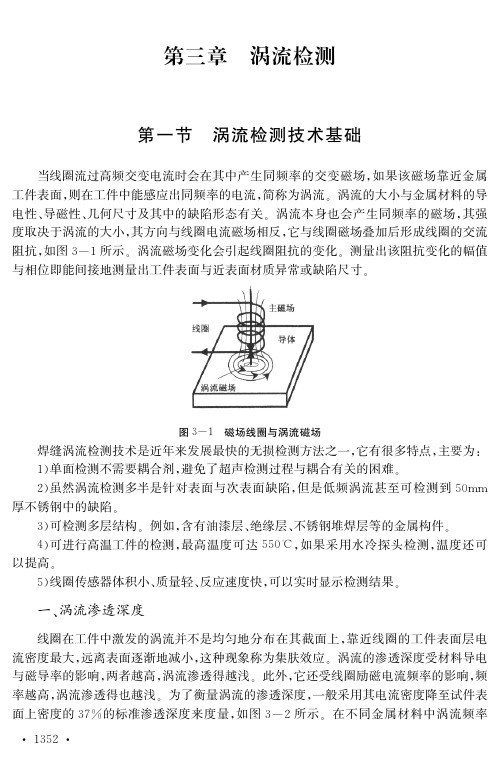
第三章!涡流检测第一节!涡流检测技术基础当线圈流过高频交变电流时会在其中产生同频率的交变磁场!如果该磁场靠近金属工件表面!则在工件中能感应出同频率的电流!简称为涡流"涡流的大小与金属材料的导电性#导磁性#几何尺寸及其中的缺陷形态有关"涡流本身也会产生同频率的磁场!其强度取决于涡流的大小!其方向与线圈电流磁场相反!它与线圈磁场叠加后形成线圈的交流阻抗!如图="&所示"涡流磁场变化会引起线圈阻抗的变化"测量出该阻抗变化的幅值与相位即能间接地测量出工件表面与近表面材质异常或缺陷尺寸"图="&!磁场线圈与涡流磁场焊缝涡流检测技术是近年来发展最快的无损检测方法之一!它有很多特点!主要为$ &%单面检测不需要耦合剂!避免了超声检测过程与耦合有关的困难"!%虽然涡流检测多半是针对表面与次表面缺陷!但是低频涡流甚至可检测到@>;;厚不锈钢中的缺陷"=%可检测多层结构"例如!含有油漆层#绝缘层#不锈钢堆焊层等的金属构件"%可进行高温工件的检测!最高温度可达@@>e!如果采用水冷探头检测!温度还可以提高"@%线圈传感器体积小#质量轻#反应速度快!可以实时显示检测结果"一!涡流渗透深度线圈在工件中激发的涡流并不是均匀地分布在其截面上!靠近线圈的工件表面层电流密度最大!远离表面逐渐地减小!这种现象称为集肤效应"涡流的渗透深度受材料导电与磁导率的影响!两者越高!涡流渗透得越浅"此外!它还受线圈励磁电流频率的影响!频率越高!涡流渗透得也越浅"为了衡量涡流的渗透深度!一般采用其电流密度降至试件表面上密度的=#R的标准渗透深度来度量!如图="!所示"在不同金属材料中涡流频率&&&@!=与渗透深度的关系如图="=所示!图="!!涡流电流密度的变化图="=!不同材料的涡流标准渗透深度与频率的关系二!线圈的类型按线圈励磁与接收信号的方式可把线圈划分为"&#只采用单一线圈产生主磁场并探测涡流信号的绝对线圈$如图="?$所示!!#为了消除线圈与工件间隙变化%工件材质与温度改变等对线圈阻抗的影响$采取双线圈反向连接形成有互补功能的差动线圈$如图="?%所示!=#励磁与接收线圈分开的单线圈输出方式$称为双线圈$如图="?3所示!#在励磁与接收分离的双线圈结构中再以差动线圈方式输出的称为差动输出双线圈$如图="?,所示!不同的线圈有不同的功能并适合于对应的检测要求!图="?!涡流探伤的线圈形&&=&=@三!缺陷信号定性分析严格地说!缺陷信号隐含在线圈阻抗值之内!因此只有进行阻抗分析才能对信号进行分析"影响线圈阻抗的主要因素是涡流磁场!它与材料和设备参数有关"其中材料的电导率受其合金成分#硬度#残余应力和温度的影响"材料按导磁特性可分为铁磁材料与非铁磁材料两类!铁磁材料的磁导率很高!对线圈阻抗的影响远远大于其它参数"尺寸因素表现在工件形状#厚度与缺陷的尺寸上"设备参数主要有线圈类型#尺寸#励磁频率和线圈与工件相邻表面间的距离$0+W."9W W!简称提离%等"线圈的交流阻抗是一个矢量!它由幅值与相位角两部分组成!因此可以采用矢量图进行分析"$&%材料电导率的影响非铁磁材料电导率与线圈工件间的提离对线圈阻抗的影响见图="@"由图中可知!高导电性材料涡流与其磁场强度大!除部分地抵消主磁场外也使损耗增高!于是引起线圈电抗降低!电阻增加"而线圈的提离最初是引起线圈电阻的改变!它与电导引起变化方向之间有一夹角!"$!%线圈励磁频率的影响励磁频率除了对涡流渗透深度产生影响外!还对线圈的阻抗产生影响"如图="A"图="C所示"图="@!材料电导率与提离对线圈阻抗的影响图="A!频率!>P*F对黄铜阻抗的影响从图="A"图="C中可以看出!变换频率可以改变祸流损耗状态与材料的检测工作点"例如对黄铜而言!提高频率$!>P*F"&(*F%!最初涡流损耗增加!电阻增大"继续增加频率!涡流只集中在表面!使损耗下降!最后甚至会出现使线圈提离只影响其电抗的&&&@?=图="#!频率&>>P*F对黄铜阻抗的影响图="C!频率增加到&(*F对黄铜阻抗的影响条件!"=#铁磁材料磁导率的影响当线圈靠近铁磁材料时$线圈磁场使铁磁材料中的磁畴方向逐渐平行于磁场方向$线圈磁通增加"达到@B.Q$@为磁通密度$.为磁导率$Q为磁场强度#从而增加线圈的电抗$见图="D!铁磁材料中的电导率%线圈提离与涡流频率对线圈阻抗的影响与非铁磁材料的规律相似$见图="&>!从图中可以看出$提离引起阻抗的变化与非铁磁材料的方向相反!图="D!铁磁材料的磁导率与提离和线圈阻抗的关系"#材料缺陷的影响涡流检测裂纹时采用阻抗图进行定性分析可以提供清晰的信号变化方向!例如在碳素钢上裂纹主要影响涡流强度%磁导率及线圈提离变化引起阻抗改变方向接近垂直$于是在碳素钢上容易检测裂纹$如图="&&所示!反之在非铁磁材料如铝合金上$裂纹信号是&&@&=@图="&>!铁磁材料的电导率与提离和线圈阻抗的关系夹在导电与提离信号之间的!只有当裂纹较深时才容易分辨"一般地说!缺陷信号都具有突变的特征!而材料电导率与磁导率的变化相对来说比较缓慢"图="&&!表面裂纹对线圈阻抗的影响#@$线圈阻抗的特点线圈与工件的提离对其阻抗影响很大!并且是一种干扰信号!应尽量地抑制它"检验铁磁材料时!线圈阻抗的电抗成分比检验非铁磁材料时线圈电抗大很多!特别是检测含铁素体的不锈钢焊缝与堆焊层时!局部铁素体含量变化对缺陷信号会产生干扰"线圈阻抗与电导率%磁导率%提离和励磁频率等参数间的关系均呈非线性函数的特点"因此!对每种线圈结构都要进行具体的数值分析才能达到提取有效缺陷信号的目的"第二节!缺陷信号的提取一!涡流场的数字模拟由前所述!缺陷信号是隐含在涡流电磁场中的!所以分析涡流场对线圈阻抗的影响是提取缺陷信号与复原缺陷形态的基础"但是除极简单的情况外!导体内电磁场参数间的函数关系还没有解析表达式"因此!目前均采用数字模拟技术来研究线圈阻抗%涡流磁场与缺陷参数间的关系!以达到优化线圈结构!选择合理的涡流频率与解释检验结果等目的"例如图="&!$与%分别是采用二维模拟技术对称平线圈检测=个分层结构工件时得到的阻抗轨迹与两个导电层&&&@A=中的涡流密度分布!从图中可以看到"材料电导率与磁导率#间隙距离和线圈提离对阻抗影响的数值关系"以及两个导电层内涡流场的分布!图="&!!二维轴对称平线圈检测带间隙的二层铝板其阻抗与涡流分布数字模拟图例图="&=!检测铁素体工件缺陷时涡流在缺陷两侧分布的数字模拟图="&=是平线圈检测铁素体工件时"采用计算机三维数字模拟技术观察人工缺陷对涡流分布流线的影响!从图中可以看到在缺陷的两侧都有闭合的环流以及涡流沿缺陷表面与深度方向渗入的形态!通过改变材料性能#涡流频率与线圈尺寸等参数还可以观察涡流分布的变化"达到优化提取缺陷信号的目的!图="&?是镍铬合金管中应力腐蚀裂纹$7H H%的双带区有限元分析模型"用来模拟应力腐蚀裂纹中局部导电现象!其中内采用模型计算层导电带的电导率不为零"但是小于材料本身!环带宽3与环带电导率!>与测量确定"其结果见图="&@!由图中可见"其预计值与实测值非常接近!图="&?!应力腐蚀裂纹的双带区有限元分析模型从以上三个例子中可见"利用数字模拟技术研究祸流检测中的物理现象是一种行之&&#&=@有效的方法与发展的必然趋势!图="&@!计算机数字模拟计算的结果与实际测量结果的比较二!线圈结构的有限元分析目前"利用光刻技术开发微型阵列式线圈与超小型探头是一个重要的方向"如若对线圈与探头进行优化设计"可对单层或双层线圈模型进行有限元分析与数值计算!光刻线圈的设计类型与数字模型见表="&!模拟的结果如图="&A 与图="&#所示!从图中可以得出"双层收发型阵列式线圈结构6与H 对提离不敏感"并且有较好的信号相位分离特性!而单层收发型阵列式线圈除了结构Q =外其它都有较好的性能"可做进一步开发与工程应用!上述例子表明"有限元分析与有限差分法分析同样是研究缺陷信号规律#预测线圈阻抗与优化线圈结构的可靠方法"目前已广泛地应用于工程设计与实际测量中!可以相信"未来甚至会出现功能更强与更加可靠的数字仿真软件来研究与解决涡流检测中所面临的各种困难!表="&!光刻线圈的设计类型与数字模型线圈结构线圈类型线圈细节$俯视图%代号收发分离测电压K6H&C @=&&线圈结构线圈类型线圈细节!俯视图"代号!收发分离测电压!单线圈测阻抗图="&A!各种类型线圈对提离干扰降低的比率图图="&#!各种线圈的信号相位分离能力三!信号处理为了更好地辨认与解释缺陷信号#需要对传感器测量到的原始数值作进一步的加工处理#以便于把信号的信噪比提高#能够清晰地反应到二维阻抗平面上或者在计算机的屏幕上绘制出缺陷的投影图形$典型的信号处理过程如图="&C所示$从图中可以看出#由相位探测器输出的连续信号波形K!J"经过前置滤波去掉模拟信号中的噪声#再经模数转换器!K%Q"把模拟量变换成数字量K!("#通过数字信号处理器进行处理后输送数字波形Y!("#再经过数模转换器!Q%K"与模拟滤波器得到处理后的波形Y!J"$采用数字信号处理有以下优点&&"提高精度!模拟滤波器的精度很难超过&>"=#数字系统的字长为&?位时可达到&>"?的精度$’’&@D=图="&C !涡流信号数字处理过程与波形示意图!!可靠性高!数字系统只有二值电平">与&!#不受温度$噪声与电磁场的影响%=!频域广!可得到极低"’&*F !到极高")&>(*F !频率的滤波功能%!分时复用!现代的处理器速度非常高#一个通道数据的处理时间很短%因此#可以在同步信号的控制下#分时处理多通道的数据#例如个通道以上的数据%四!多频涡流由频率对线圈阻抗影响的定性分析中可知#调整励磁频率可改变线圈阻抗与各参数间的函数关系#以便更好地分离缺陷信号%但是只用单一频率励磁#对于探头扫查过程中不断发生的线圈提离变化与其它参数的改变还是不能很容易地提取出有效的缺陷信号%因此#为了能够从两种以上的干扰信号中把它分离出来#可以采用多种不同的励磁频率来达到%例如图="&D 中是一个典型的双频率检测系统%主频>>经分频后得到频率为>&与>!的励磁电压#通过功放同时加到差动线圈上%检测的信号经放大后由两个同步相位探测器输出#对应于频率>&得到的阻抗相量分量为K &#K !&对应于>!得到另一阻抗相量分量为K =#K ?%从个已知相量分量中分离出缺陷信号类似于解联立方程%例如#设K &"K ?分量都与缺陷N &$线圈提离N !和铁素体含量N =等独立参数有关#如图="!>所示%于是得出’K &$K N &&K N !&K N =K !$K N &&K N !&K N ="=%&!等等%或写成通式’K 5$/=5$&K <5"=%!!对于各参数的微小变化可以近似地认为线性关系成立#即K N 5B ?N 5N 5#其中?N 5为常数%(>A =&(因此上式可改写为!K 5$/=5$&?<5N 5"=%=#过去上述方程的解是通过电路完成的$目前%缺陷信号的分离处理过程可通过数字计算机更快捷&更精确地得到$图="&D !多频涡流系统原理图图="!>!多频涡流参数分布的相量投影示意图五!脉冲涡流按照脉冲电子学理论%一个窄脉冲电压或电流含有很多不同频率的谐波分量%因此采用脉冲电压励磁线圈就包括了多频涡流检测的功能$另外对脉冲涡流磁场现象的分析是采用时间与信号幅度的方式%比阻抗相量法更容易%因此得到普遍的应用$线圈中的电流脉冲会在工件表面激发起涡流脉冲%该脉冲向工件深度方向传播"渗透#%其强度是时间的函数$类似于雷达波传播的过程%强度也不断衰减且遇到目标时会产生反射$由于脉冲含有多种频率的谐波分量%不同频率的涡流分量其渗透深度不同%衰减也不同%低频成分可渗透到较深的区域%因此在脉冲的波形上能反应出随渗透深度而改变的特点$如果在波形上选择若干特征点作为监测指标%则可以较容易地分离出缺陷信号%如图="!&所示$例如%取时间较早的J &点代表线圈提离%中间点J !既含有提离也包括缺陷的成分%而J =点与线圈提离无关%仅仅是缺陷的特征点等$当然面对一种特定的线圈结构%应当通过分析与试验手段选取特征点%才能达到提取缺陷信号的目的$第三节!焊缝的涡流检测技术目前%焊缝的涡流检测主要采用多频涡流或脉冲涡流检测方法%并且已成功地应用于核反应堆中不锈钢管道焊缝与堆焊层缺陷的检测%同样也应用于海洋采油平台钢结构焊缝疲劳裂纹的检测以及油气输送管道内外壁腐蚀与裂纹的检测$’&A =&’图="!&!脉冲涡流波形与探测的特征一!钢焊缝收发分离式线圈的涡流检测如果采用发射与接收线圈分离的探头结构!因为铁磁材料的磁导率很大!因此可以选取两个线圈的间距M满足常状态下两者之间耦合很小的条件!见图="!!"但是当长而深的裂纹在探头的下面通过时!涡流环路会发生变形!涡流磁场强度也发生变化!促使两线圈之间通过涡流场增大耦合!从而增加接收线圈的输出电压"#&$分离线圈的信号图="!!!收发分离式线圈涡流探头检测钢制件裂纹的示意图当频率为&>>P*F时!分离式线圈的裂纹信号与提离信号的相位差接近D>T"裂纹信号主要是因电阻性涡流损耗的改变而引起的!信号幅度只与裂纹的深度和长度有关!几乎不发生相位角的变化"反之!线圈提离信号却逆时针旋转接近D>T!如图="!=$所示"当收发线圈中心距M较大时!对深而长的表面裂纹非常灵敏!但对&;;左右的提离变化并不敏感!因此适合于检验带余高焊缝的表面裂纹"在不同线圈中心距的条件下!裂纹信号幅度与其深度和长度间的关系见图="!=%与图="!=3"由图中可见!线圈中心距与裂纹长度间存在一个最佳信号幅值区!例如M为&!;;时!对深度=;;的缺陷最大信号幅度出现在缺陷长度为&@;;左右"裂纹信号还与线圈轴线和裂纹方向间的夹角(有关!见图="!=,"当夹角(增大时!信号幅度很快下降"#!$收发分离式线圈的阻抗图由于分离式线圈的缺陷信号是接收线圈的输出电压!因此其阻抗图是按照归一化电压绘制的"图="!?表示检测碳素钢件时!接收线圈输出电压与频率和提离的关系!随着频率的提高!线圈输出电压的电抗成分下降!在&>>P*F左右最佳"经研究得出!可以采用无因次特征值N来表示线圈输出与各参数之间的关系!见式#="?$"其中线圈中心距-值影响最大!可见双线圈的设计其中心距是一个关键因素"对N-%%&A!=图="!=!分离线圈式探头涡流检测裂纹信号的特征N -$#1D 7&>%?M !>.P 0!=%?"式中!M ###线圈间距!;;"$>###检验频率!*F "$.P ###相对磁导率$0###电阻率!K %3;"&图="!@表示出检测不锈钢件时接收线圈输出电压与频率和提离的关系’同样当频率大于&>P *F 时’随着频率的提提离的关系’同样当频率大于&>P *F 时’随着频率的提高’线圈的输出电压下降&一般当N -大于&>时’几乎所有金属材料的阻抗轨迹曲线都很接近’甚至可以按照同一条曲线处理&分离线圈式涡流探头已用在核容器支撑构件焊缝(接管焊缝与汽轮机轴中心孔等表面裂纹的检测上’由于探头的裂纹信号幅度不受焊缝余高的影响’因而取得了较好的效果&此外’这种探头还成功地用于不锈钢焊缝与铸造不锈钢粗晶阀体的检测&二!钢焊缝的脉冲涡流检测采用脉冲涡流可以检测铁素体钢焊缝’其原理是在线圈中建立起初始励磁电流与振荡的条件’然后在适当的瞬间切断励磁电路’于是线圈中的电流会通过一个高阻尼电阻另外形成回路’见图="!A $&这时伴随着线圈中储存电磁能量的释放’电流会出现峰值’与其对应也会产生电压峰值’随后呈现指数衰减’见图="!A %&当线圈的自身分布电容较大时’电压达到峰值后还可能产生振荡衰减’见图="!A 3&可以利用场效应三极管实现脉冲电流的励磁与切断’其典型脉冲电路见图="!A ,’%=A =&%图="!?!碳素钢件双线圈的输出电压与频率和的关系!M B&!;;"提离B>"&>>;;#图="!@!不锈钢件双线圈的输出电压与频率和提离的关系!M B&!;;"提离B>"&>>;;#励磁电流与线圈产生的电压波形见图="!A-$在图="!A-中"电压波形可划分为=个具有时间特征的模式段$时间模式段&的变化与材料性质有关"而峰值高度!时间模式段!#对材质的变化特别是裂纹的存在更加灵敏"以致不需要很大的放大就可以检测出峰值信号的变化$如果把上述脉冲涡流检测的物理现象应用到铁素体钢焊缝裂纹的检测上"还应当把线圈提离与裂纹信号分开$试验已经证明%峰值后的时间长度!时间模式段=#只与线圈的提离有关$这样就可以利用高速峰值探测器来实现焊缝裂纹的检测$ !&#脉冲信号分析在人工缺口试样上对线圈提离与模式段=的延迟时间和缺口深度与时间模式段!的电压峰值测量结果见图="!#$$可见裂纹深度影响模式段!的峰值"而线圈的提离只改变模式段=的延迟时间$图="!#%给出了与上述关系对应的阻抗值与相位角的变化"从图中可以看出"线圈提离引起很大的相位角变化"而裂纹深度只影响阻抗的幅值"两者的&&&A?=图="!A !焊缝脉冲涡流检测的原理变化方向是互相垂直的!图="!#!模式段!线圈电压峰值与缺口深度和模式段=延迟时间与线圈提离之间的关系"!#阵列探头利用上述原理$在低碳钢焊缝脉冲涡流检测中采用的是多线圈阵列元件探头!它是由&A 个线圈组成的$每个线圈元件均可以上下自由滑动&=’@;;的行程$以促成与焊缝余高变化有较好的浮动匹配!元件按照方阵排列$使其覆盖区较大$线圈都采用长&C ;;%直径&’#;;的铁心缠绕A >匝而成$外面再用塑料管封装并由磷青铜弹簧保持其&@A =&&对焊缝表面的压力!元件的中心间距为A;;"探头中的各线圈元件都是单独励磁"以免形成各元件间的电磁耦合"典型的探头结构见图="!C!图="!D给出了该探头在含有余高的低碳钢焊缝上"实际测量热影响区疲劳裂纹的结果!从图中可以看出"裂纹信号的峰值电压很高"线圈提离的变化只影响峰值后的延迟时间"两者很容易分开!图="!C!焊缝涡流检测多线圈阵列探头结构示意图图="!D!有余高的低碳钢焊缝裂纹与线圈提离信号参数的数值范围!&D;;厚"三!涡流检测在不锈钢堆焊层上的应用核容器与石油加氢裂化容器不锈钢堆焊层的组织粗大"结晶方向性强!采用超声检测堆焊层内的缺陷与层下裂纹时"会出现较大的衰减与噪声干扰!反之"采用涡流检测比较成功"特别是检测C;;厚堆焊层与合金钢母材间的裂纹效果更好!用调幅方式的多频涡流是基于低频成分能渗透到较大深度的原理!试验表明"频率为@>P*F#!C>P*F与A>>P*F的高频绝对线圈探头"能较好地检测表面裂纹#表面轮廓与堆焊层内的铁素体含量!选择频率为@>>*F#!C>>*F与@>>>*F的低频绝对线圈探头"可测量堆焊层的厚度!选用频率@>>*F#!C>>*F与@>>>*F的低频绝对发射"差动接收双线圈探头"则能检测出堆焊层内缺陷#堆焊层与母材间的平面剥离和堆焊层下裂纹!经过优化的信号由融合算法可以分离与抑制堆焊层粗糙表面引起的提离信号与奥氏体堆焊层内局部铁素体含量变化引起的干扰信号!图="=>给出了一个典型的多频涡流检测硬件系统方框图!它具有单频或多频与线$$&AA=圈通道!通道"的选择功能#提供频率范围达&>*F"&>(*F$相位选择范围>T"=A>T$最大增益达&&>,6#>’@*F"&>P*F的低通与高通滤波系统可分为?!挡进行分级调节#该系统采用&A位模数转换器!K%Q"可提供高精度数字信号$通过串口与计算机通信#图="=>!核容器不锈钢堆焊层缺陷与层下裂纹多频涡流检测硬件系统方框图系统的软件具有消除噪声&抑制线圈提离与铁素体含量等因素的干扰以及确定涡流信号性质等功能#采用非线性函数展开方式$按照最小平方吻合原理进行回归分析$对密集的和单独的涡流信号都可提取有关缺陷尺寸的信息$以确定缺陷尺寸与分布#此外$还可以管理检测参数的校准与标定$滤波系数的计算与在线信号融合分析以及缺陷的投影显示等功能#’’&#A=。
《无损检测》涡流检测课件

为;
Z Z0 R1 jL1
• 若次级线圈的 R2 Rr 0
• 则由式(3-17)得:
Z R1 jL1(1 K 2 )
K 2 M 2 /(L1L2 )
第3章 涡流检测技术
• 在 R2 Rr 从 变化为0的过程中,(或从0增至 )
视在阻抗Z在以视在电阻R为横坐标,视在电抗X为 纵坐标的阻抗平面图上变化,其轨迹近似为一半圆 (图3-7),即所谓初级线圈阻抗平面图:
回路中所产生的为感生电流,回路中所产生的感应电动
势 Ei则等于所包围面积中的磁通量Φ随时间变化的负值,
Ei= -dΦ/dt
(3-6)
其负值表明闭合回路内感应电流所产生的磁场总是阻碍 产生感应电流的磁通的变化,即法拉第电磁感应定律。
其感应电动势: Ei= -N*dΦ/dt
(3-7)
第3章 涡流检测技术
rd 2
注意:
(3-19)
对于特定试件,特征频率既非试验频率的上限
也非下限,也不一定是应该采用的最佳试验频率, 它只是一个参考数或特征值,但它含有除缺陷外 棒材尺寸和材料性能的全部信息。
第3章 涡流检测技术
• 3.2 涡流检测基础知识 • 3.2.1 • 3.2.1.1 金属的导电性
欧姆定律:I=U/R R=ρ× L/S
(3-1) (3-2)
3.2.1.2 金属的磁特性
物质在外磁场作用下感生出磁场的物理过程称 为磁化。
RL S
第3章 涡流检测技术
• 物质磁性的大小可用磁导率μ表示,说明 了物质所感生出的磁场的强度B与强度为H 的外磁场的关系。即:
第3章 涡流检测技术
•
图3-6 藕合线圈互感电路
其中:Z = Z0 + Ze 称为初级线圈的视在阻抗。
《涡流检测技术》课件

根据涡流信号的变化,可以得知材料内部 是否存在缺陷。
涡流检测技术的应用领域
1
航空领域
用于飞机发动机叶片等高精度设
制造领域
2
备的测试。
用于制造工艺控制、质量检测、
零部件分选等方面。
3
电子领域
用于电子元器件检测,例如PCB板 故障等。
常见的涡流检测设备
缺陷检测仪
可以进行表面缺陷及小型裂 纹的检测,并有利于精确判 别缺陷位置及长宽比。
涡流检测技术的原理
涡流检测原理
材料内部存在一定大小的涡流损耗,用感 应线圈检测涡流损耗来检测材料表面和近 表面的问题。
电磁感应探头
探头内含有感应线圈,由其生成磁场对材 料进行检测。
电磁感应原理
交流电流经过线圈时产生强磁场,磁场作 用于导电物体内的自由电子,形成涡流, 涡流会阻碍原有的电流,产生电磁感应信 号。
• 设备操作步骤需熟 知,若无经验可咨 询专业技师。
线管探伤仪
可进行管道内壁的检测,广 泛应用于石化、冶金、船舶 等领域。
分选机
通过涡流检测进行尺寸分选 及表面缺陷检测,提高工作 效率。
涡流检测技术的优势和局限
1 优势
2 局限
能够检测高品质材料的小型缺陷,检测 速度快、非破坏性、适用于多种材料。
无法检测非导体材料,检测结果易受工 作人员经验和工作环境影响。
操ቤተ መጻሕፍቲ ባይዱ涡流检测设备的注意事项
环境要求
• 避免电磁干扰频繁 出现的场所进行操
• 作 操。 作区域需干燥无 水,以免影响检测 效果。
安全要求
• 检测设备带电,请 勿将设备接到液体 或潮湿环境中。
• 在操作时需佩戴防 护手套等个人防护 用品。
涡流检测—涡流检测技术(无损检测课件)

检测线圈的分类
穿过式线圈 检测管材、棒材和线材,用于在线检测
探头式线圈 放在板材、钢锭、棒、管、坯等表面上用,尤其适用于局部检
测,通常线圈中装入磁芯,用来提高检测灵敏度,用于在役检测 内插式线图
管内壁、钻孔。用于材质和加工工艺检查
第3节 涡流检测的基本原理
4. 设备器材
一般的涡流检测仪主要由振荡器、探头、信号输出电 路、放大器、信号处理器、显示器、电源等部分组成
第3节 涡流检测的基本原理
5. 检测技术
缺陷检测即通常所说的涡流探伤。主要影响因素包括工作 频率、电导率、磁导率、边缘效应、提离效应等。
➢ 工作频率是由被检测对象的厚度、所期望的透入深度、要 求达到的灵敏度或分辨率以及其他检测目的所决定的。检 测频率的选择往往是上述因素的一种折衷。在满足检测深 度要求的前提下,检测频率应选的尽可能高,以得到较高 的检测灵敏度。
5. 检测技术
➢ 边缘效应:当检测线圈扫查至接近零件边缘或其上面的孔 洞、台阶时,涡流的流动路径就会发生畸变。这种由于被 检测部位形状突变引起涡流相应变化的现象称为边缘效应。 边缘效应作用范围的大小与被检测材料的导电性、磁导性、
检测线圈的尺寸、结构有关。
5. 检测技术
➢ 提离效应:针对放置式线圈而言,是指随着检测线圈离开 被检测对象表面距离的变化而感应到涡流反作用发生改变 的现象,对于外通式和内穿式线圈而言,表现为棒材外径 和管材内径或外径相对于检测线圈直径的变化而产生的涡 流响应变化的现象。
4. 设备器材
检测仪器的基本组成和原理: 激励单元的信号发生器产生交变电流供给检测线 圈,放大单元将检测线圈拾取的电压信号放大并 传送给处理单元,处理单元抑制或消除干扰信号, 提取有用信号,最终显示单元给出检测结果。
涡流检测技术(六).

11
3.信噪比最高:选择待测因素与主要干扰 相位差最大的频率
4. 检测频率正比于运动速度:自动探伤时, 激励频率≥10倍伤波调制频率,调制频率 正比于试件线圈相对运动速度
以上各方面综合考虑
12
平衡回路:用无缺陷部位调节,使回路 输出=0
灵敏度[放大倍数,增益]:S=Δy/Δx; 标准伤信号幅度在屏幕中部,刚刚达到 报警线
职责:高级无损检测人员制定规范 检测规范之下还有工艺指导书或工艺卡
8
3.5.2 检测准备
1.检测方法和设备的选择(依据探测对象的形状大小数 量和等级要求)
2.检测线圈的选择(试件形状和大小,线圈的参数及拾 取信号的方式必须与仪器适配,检测时要适合于被检 缺陷。)
3.检测条件(清除试件上的金属粉、氧化皮、油脂。) 4.对比试样的准备(种类;人工伤尺寸) 5.仪器预调整(预热,初调) 6.附加装置调整(传送装置;接近开关等)
中心频率的选择原则? 3.5.3 管棒材穿过式线圈自动探伤,试件传
送速度30m/min,缺陷与线圈作用距离为 5mm,估算伤波的调制频率和线圈的激励 频率。
18
样) 1. 材料与探测试件五同:材质、形状、大小、加
工工艺、表面状态相同 2. 无自然缺陷 3. 人工缺陷与自然缺陷形状相似,尺寸准确
2
对比试样两例
1. 测试系统综合性能的对比试样
深0.2
深0.5
深1.0
2. 螺栓孔探伤用对比试样
3
3.4.4 涡流探伤仪综合指标
1.探头式涡流探伤仪的综合指标(略) 2.穿过式涡流探伤仪的综合指标 探测灵敏度:能检测出的最小缺陷尺寸,
13
相位的选择
相位:移相器输出的控制信号的相位 原则:控制信号相位和主要干扰方向相差
(完整版)涡流检测技术

视在电阻
阻抗的归一化
经过归一化处理
后的电阻和电抗都 是无量纲的量,并 且都恒小于1。
归一化阻抗图的特点
• (1)它消除了原边线圈电阻和电感的影响,具有通用性。 • (2)阻抗图的曲线簇以一系列影响阻抗的因素作为参量。 • (3)阻抗图形定量地表示出各影响阻抗因素的效应大小和方向。 • (4)对于各种类型的工件和检测线圈,有各自对应的阻抗图。
进行涡流检测的步骤:(探针式涡流探伤仪为例)
I. 摸清被检零件的裂纹规律
如零件的材料组织与特性、结构形状、制造时的加工方法、装 配位置、使用时间、受力状态、可能产生或经常产生裂纹的部 位、裂纹的方向等。
II. 参考试件的准备和制作
最好采用报废的有自然缺陷(裂纹)的相同零件作为参 考试件。
也可用无自然裂纹的零件,在容易产生疲劳裂纹的部位用机械加 工法,或腐蚀法,或电火花加工人工缺陷的参考试件。
金属试件上涂、压力等的监控; 试件尺寸、形状测量等。
主要应用
• (1)能检测出材料和构件中的缺陷,例如裂纹、折叠、气孔和夹杂等。 • (2)能测量材料的电导率、磁导率、检测晶粒度、热处理状况、材料
的硬度和尺寸等。
• (3)金属材料或零件的混料分选。通过检查其成分、组织和物理性能
涡流检测的主要用途及影响感生涡流的特性的主要因素
目的 探伤
材质试验
厚度及位移 等的测量
检测因素 试件中的裂纹、腐 蚀、凹坑、夹杂、 气泡等
电导率 磁导率
提离效应、厚度效 应、充填效应等
典型应用
管、棒、线、板材等的探伤; 机制件的探伤; 飞机维护及管道系统的维护检查; 疲劳裂纹的监视。
测量金属试件的电磁参数; 金属热处理状态的鉴别; 金属材料的分选; 金属材料成分含量、杂质含量的鉴 别。
第3章涡流检测技术

? 逆磁质:
? 感生磁场微弱、与外磁场方向相反的物质,如铜。
? 铁磁质:
? 感生磁场强的物质,如铁,钴、镍及其合金。
? 磁导率:
相对磁导率 :
3.2.1.3 电磁感应
? 1.电磁感应:
? 当穿过闭合导电回路所包围面积的磁通量发生变化时,回路中将产生 电流的现象。
? 法拉第感应定律 感应电动势
? 2. 自感应:
? 3.2.2 涡流检测技术原理
3.2.1 与涡流检测相关的电学和磁学基本知识
? 3.2.1.1 金属的导电性
? 3.2.1.2 金属的磁特性 ? 3.2.1.3 电磁感应
3.2.1.2 金属的磁特性
? 磁化:
? 物质在外磁场作用下感生出磁场的物理过程称为磁化。
? 顺磁质:
? 感生磁场微弱、与外磁场方向相同的物质,如铝。
? 表面或近表面缺陷检测 ? 只适用于导电材料 ? 非接触,无需耦合 ? 检测速度快,易于实现自动化 ? 适用于高温检测 ? 适用于异型材料和小零件检测
3.1.3 涡流检测的发展过程
? 1879年,英国人休斯利用感生涡流对不同的合金进行了判 断实验。
? 20世纪50年代初,德国的福斯特等人提出阻抗平面图分析 法和相似定律。
? 涡流检测根据线圈视在阻抗(信号)的变化特征获得被检材料的物理 特性或工艺特性(信息)。
of Penetration
(Skin Depth)
Eddy Current Density
High Frequency High Conductivity High Permeability
1/e or 37 % of surface density
Depth
Eddy Current Density Low Frequency Low Conductivity Low Permeability
涡流检测技术
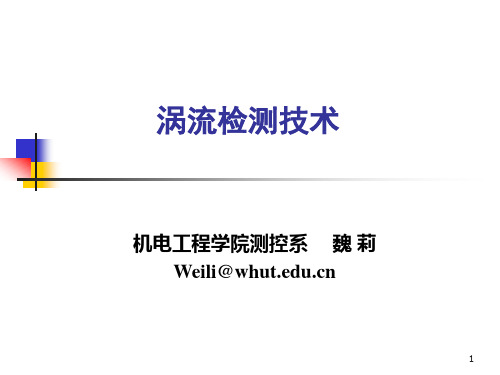
B l E dl s t ds
31
2.2 涡流检测基础知识
二、麦克斯韦电磁方程组
D l H dl I 0 S t ds B l E dl s t ds
D ds q B ds 0
s s
0
D E r 0 E B H r 0 H J E
2
2
RS RZ R1 X S X Z X1
44
2.3 涡流阻抗分析法
复阻抗平面图
横轴:RS 纵轴:XS R2从∞逐步递减 到零
45
2.3 涡流阻抗分析法
2. 阻抗的归一化
横轴 纵轴
RS R1 L1 XS L1
46
2.3 涡流阻抗分析法
二、有效磁导率和特征频率
1.有效磁导率
8
2.1 涡流检测概述
二、涡流检测原理
9
2.1 涡流检测概述
三、涡流检测方法
激励线圈产生交变磁场
导体中感应出涡流
涡流磁场改变原磁场 线圈电压阻抗变化
间 接 方
法
判断导体的特性
10
2.1 涡流检测概述
1.涡流检测线圈及其分类
◆ 按相对位置分
◆ 按使用方式分 ◆ 按激励源分
◆ 按输出信号分
11
2.1 涡流检测概述
a a
0
0
0
J
J0
0
j kr
2
a
0
0
0
0
0
a
0
0
0
2
1
0
0
48
2.3 涡流阻抗分析法
eff
J1 j ka 2 j ka J 0 j ka
涡流检测技术应用课件.文客久久资料库

涡流检测技术应用课件.文客久久资料库一、教学内容本节课我们将探讨《涡流检测技术》教材的第3章“涡流检测原理及其应用”。
详细内容主要包括:涡流检测的基本原理、检测传感器的设计与制作、信号处理与分析方法以及涡流检测技术在工业领域的具体应用。
二、教学目标1. 理解并掌握涡流检测的基本原理。
2. 学会设计并制作涡流检测传感器。
3. 掌握涡流检测信号的处理与分析方法。
三、教学难点与重点教学难点:涡流检测信号的处理与分析方法。
教学重点:涡流检测的基本原理及其在实际应用中的关键问题。
四、教具与学具准备1. 教具:涡流检测实验装置、演示PPT、涡流检测传感器样品。
五、教学过程1. 实践情景引入(5分钟):通过展示工业生产中涡流检测技术的应用案例,引发学生对涡流检测的兴趣。
2. 基本原理讲解(15分钟):详细讲解涡流检测的基本原理,包括电磁感应、趋肤效应等。
3. 传感器设计与制作(10分钟):介绍涡流检测传感器的设计原理与制作方法。
4. 信号处理与分析方法(10分钟):讲解涡流检测信号的处理与分析方法,如快速傅里叶变换、滤波等。
5. 例题讲解(15分钟):结合实际案例,讲解涡流检测技术在工业领域的应用。
6. 随堂练习(5分钟):让学生运用所学知识,分析实际涡流检测问题。
六、板书设计1. 涡流检测基本原理2. 涡流检测传感器设计与制作3. 涡流检测信号处理与分析方法4. 涡流检测技术在工业领域的应用七、作业设计1. 作业题目:分析涡流检测技术在金属管道内壁腐蚀检测中的应用。
答案:涡流检测技术可以检测金属管道内壁的腐蚀情况。
通过分析检测信号,可以得到腐蚀的位置、大小和程度,从而为管道维护提供依据。
2. 作业题目:简述涡流检测信号处理与分析方法。
答案:涡流检测信号处理与分析方法包括:快速傅里叶变换、滤波、时域分析、频域分析等。
八、课后反思及拓展延伸本节课通过理论与实践相结合的方式,让学生了解了涡流检测技术的基本原理和应用。
涡流检测技术
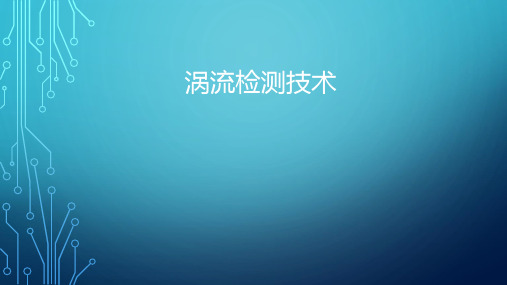
Thank you
涡流检测的主要用途及影响感生涡流的特性的主要因素
目的 探伤
材质试验
厚度及位移 等的测量
检测因素 试件中的裂纹、腐 蚀、凹坑、夹杂、 气泡等
电导率 磁导率
提离效应、厚度效 应、充填效应等
典型应用
管、棒、线、板材等的探伤; 机制件的探伤; 飞机维护及管道系统的维护检查; 疲劳裂纹的监视。
测量金属试件的电磁参数; 金属热处理状态的鉴别; 金属材料的分选; 金属材料成分含量、杂质含量的鉴 别。
金属试件上涂、镀等膜层测量; 板材测厚; 位移、振动测量; 液面位置、压力等的监控; 试件尺寸、形状测量等。
主要应用
• (1)能检测出材料和构件中的缺陷,例如裂纹、折叠、气孔和夹杂等。 • (2)能测量材料的电导率、磁导率、检测晶粒度、热处理状况、材料
的硬度和尺寸等。
• (3)金属材料或零件的混料分选。通过检查其成分、组织和物理性能
当探头从零件的中间部位移动到零件的边缘时,仪器所发生的报警现
象,是由于边缘效应所致,一般不是裂纹信号
当探头扫描移动到局部漆层脱落处,仪器所发出的报警现象,属间隙
效应引起,一般不是裂纹信号
当探头移动到受检部位的形状,或曲率发生变化的区域时,发出的报
警现象,一般不是裂纹信号
在对非磁性材料进行涡流检测过程中,如探头移动到磁性材料附近,
涡流检测的特点
• 优点: • (1)不需耦合剂,对管、棒、线材易于实现自动化。 • (2)对导电材料表面和近表面缺陷的检测灵敏度较高。 • (3)能在高温、高速下进行检测。 • (4)应用范围广,对影响感生涡流特性的各种物理和工艺因素均能实现检测。 • (5)工艺简单、操作容易、检测速度快。
第三章 涡流检测

d Ei dt
此负值表明闭合回路中感应电流所产生的磁场总是阻碍产生 感应电流的磁通的变化,这个方程称为法拉第电磁感应定律。 此方程用于一个绕有N匝的线圈,所得感应电动势表示为
d N d Ei N dt dt
Ei 伏,N-匝, 韦伯,t 秒
2.自感应
其中忽略了容抗,则 (3-1) 当初级线圈与次级线圈(被检对象)相互耦合时,由于互感的 作用,闭合的次级线圈中会产生感应电流,而这个电流反过来又 会影响初级线圈中的电压和电流。这种影响可以用次级线圈电路 阻抗通过互感M反映到初级线圈电路的折合阻抗来体现,设折合 阻抗为。
2 2 XM XM Z e Re jX e 2 R2 j 2 X2 2 2 R2 X 2 R2 X 2
涡流密度及磁场强度的几何分布均相同。
f d f2 2 2 d2
2 1 1 1 1
2
3) 涡流检测相似律 如 , 一 根 d=10cm 、 γ=35s/μm 的 铝 棒 ( fg=1.45Hz )在 f=145Hz 的试验频率下所显示 的有效磁导率、场强分布及涡流密度分布,与 一 根 直 径 d=0.01cm , γ =10s/μm 的 铁 丝 ( fg=50660Hz ),在 f=5.07Mhz 的试验频率下 所显示的结果完全相同。 根据相似定律,可进行对比试验,以此判定 缺陷的深度和大小。
当线圈中通以交变电流I时,其所产生的交变磁通量 也将在本线圈中产生感应电动势,此现象称为自感现象, 产生的感应电动势称为自感电动势EL
dI E L L dt
L-自感系数,单位亨利(H)
3.互感应
当两个线圈相互靠近,线圈中分别流过交变电流I1和I2 的情况下,由线圈1中电流I1所引起的变化的磁场通过线圈2 时会在线圈2中产生感应电动势;同样,线圈2中电流I2所引 起的变化的磁场通过线圈1时会在线圈1中产生感应电动势, 这种两载流线圈相互激起感应电动势的现象称为互感现象, 所产生的感应电动势称为互感电动势。在线圈2和在线圈1中 产生的感应电动势,在两线圈形状、大小、匝数、相对位置 及周围磁介质给定的情况下可给出
涡流检测-第3章
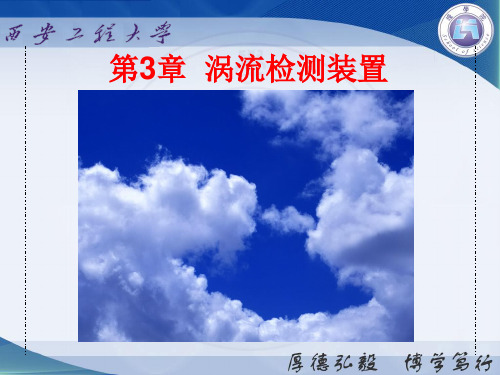
放臵式线圈:对零件的表面和近表面质量的缺陷检测。
外通过式线圈
内穿过式线圈
放置式线圈
3.按比较方式分类 绝对式线圈:针对被检测对象某一位臵的电磁特性直接进 行检测的线圈;
自比式线圈:针对被检测对象两处相邻位臵通过其自身电
磁特性差异的比较进行检测的线圈; 他比式线圈:针对被检测对象某一位臵通过与另一对象电 磁特性差异的比较进行检测的线圈。
按照对检测结果显示方式的不同: 涡流探伤仪可分为阻抗幅值型和阻抗平面型 阻抗幅值型:只在显示终端显示检测结果幅度的相关信息, 不显示检测信号的相位信息, 如:指针式电表、示波器等。 注:该类仪器所指示的结果不一定是最大阻抗值或者阻抗 变化的最大值,而是在最有利抑制干扰信号的想为条件下 的阻抗分量,这一点课通过具有相位调节功能仪器上相位 旋钮的调整,观察电表指针摆动幅度的变化或示波器时基 线上的波形幅度的变化加以确认。 阻抗平面型:不仅给出检测记过幅度的信息,而且同时给出 检测信号的相位信息。当调节相位控制旋钮时,指示显示信 号的相位角发生变化,而幅值不会发生变化。
3.2涡流检测仪器
基本组成部分的工作原理:激励单元的信号发生器产生交
变电流供给检测线圈,放大单元将检测线圈拾取的电压信
号放大并传给处理单元,处理单元抑制或者消除干扰信号, 提取有用信号,最终在显示单元显示出检测结果。
3.2.1检测仪器的分类
根据检测对象和目的的不同:
涡流探伤仪 涡流电导仪 涡流测厚仪
第3章 涡流检测装置
本章内容
3.1涡流检测线圈 3.2涡流检测仪器 3.3涡流检测辅助装臵及使用 3.4标准试样与对比试样 3.5检测仪器(系统)的性能评价
根据应用目的不同,涡流检测仪可分为: 涡流探伤仪 涡流电导仪
涡流检测技术
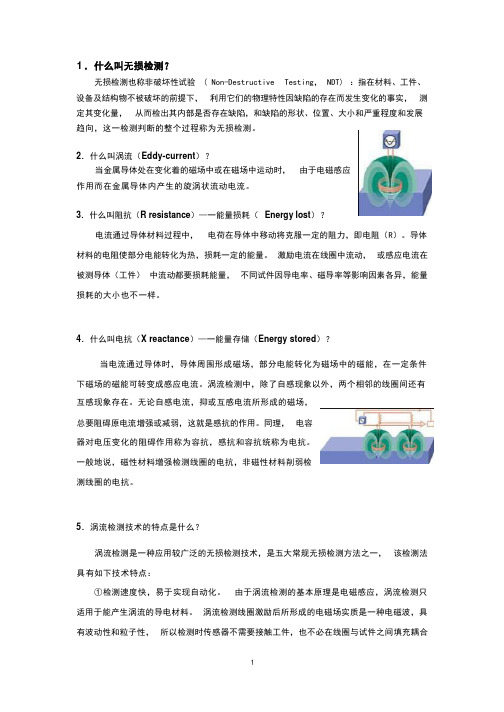
1无损检测也称非破坏性试验( Non-Destructive Testing, NDT) :指在材料、工件、设备及结构物不被破坏的前提下,利用它们的物理特性因缺陷的存在而发生变化的事实,测定其变化量,从而检出其内部是否存在缺陷,和缺陷的形状、位置、大小和严重程度和发展趋向,这一检测判断的整个过程称为无损检测。
2.什么叫涡流(Eddy-current)?当金属导体处在变化着的磁场中或在磁场中运动时,由于电磁感应作用而在金属导体内产生的旋涡状流动电流。
3.什么叫阻抗(R resistance)—一能量损耗(Energy lost)?电流通过导体材料过程中,电荷在导体中移动将克服一定的阻力,即电阻(R)。
导体材料的电阻使部分电能转化为热,损耗一定的能量。
激励电流在线圈中流动,或感应电流在被测导体(工件)中流动都要损耗能量,不同试件因导电率、磁导率等影响因素各异,能量损耗的大小也不一样。
4.什么叫电抗(X reactance)—一能量存储(Energy stored)?当电流通过导体时,导体周围形成磁场,部分电能转化为磁场中的磁能,在一定条件下磁场的磁能可转变成感应电流。
涡流检测中,除了自感现象以外,两个相邻的线圈间还有互感现象存在。
无论自感电流,抑或互感电流所形成的磁场,总要阻碍原电流增强或减弱,这就是感抗的作用。
同理,电容器对电压变化的阻碍作用称为容抗,感抗和容抗统称为电抗。
一般地说,磁性材料增强检测线圈的电抗,非磁性材料削弱检测线圈的电抗。
5.涡流检测技术的特点是什么?涡流检测是一种应用较广泛的无损检测技术,是五大常规无损检测方法之一,该检测法具有如下技术特点:①检测速度快,易于实现自动化。
由于涡流检测的基本原理是电磁感应,涡流检测只适用于能产生涡流的导电材料。
涡流检测线圈激励后所形成的电磁场实质是一种电磁波,具有波动性和粒子性,所以检测时传感器不需要接触工件,也不必在线圈与试件之间填充耦合剂,因此检测速度快,对管、棒材的探伤每分钟可检查几十米;对丝、线材的探伤每分钟可达几百米,甚至上千米,因此,易于实现自动化检测。
第三章 涡流检测

(2) 导电管件的内通式线圈。将线圈插入并通过被检管 材(或管道)内部进行检测的线圈为内通式线圈。 ① 薄壁管件。用内通式线圈检测薄壁管件时,其线圈阻 抗的变化情况可借用穿过式线圈的阻抗图加以分析。
② 厚壁管件。对于非铁磁性材料的厚壁管件,其特征频
率为
fg
式中: di为管件内径。
506606
2 XM
Z 0 R1 jX 1 R1 jL1
R X
2 2
2 2
R2 j
2 XM
R X
2 2
2 2
X2
X M M 互感抗
(3-2)
将次级线圈的折合阻抗与初级线圈自身的阻抗的和称为 初级线圈的视在阻抗Zs,即
Z s Rs jX s R1 Re j( X 1 X e )
E21 M d I1 dt , E12 M
M L1 L 2
d I2 dt
M 为两个线圈的互感系数
耦合系数 K=
, L1和 L 2 线圈1和线圈2的自感系数
3.2 涡流检测的阻抗分析法
线圈耦合电路
一、 检测线圈的阻抗和阻抗归一化
1) 检测线圈的阻抗
设通以交变电流的检测线圈(初级线圈)的自身阻抗为Z0,
(4) 缺陷。 (5)检测频率。
2) 其他常用类型检测线圈的阻抗分析
(1) 内含导电管材的穿过式线圈。
① 薄壁管件。 对非铁磁性材料的薄壁管件,特征频率为
fg 506606
r d i
(3-7)
式中:di为管件内径;δ为管件壁厚。管件的填充系数η=(da/dc)2,
其中,da为管件外径,dc为线圈内径。 ② 厚壁管件。厚壁管穿过式线圈的阻抗曲线位于圆柱体和 薄壁管两者的曲线之间。
涡流检测技术

3.2.2-涡流检测技术原理-3.2.2.1-涡流检测原理-▣3.2.2.2趋肤效应和渗透深度-13.2. 磁导率-☐3.2.2.5-涡流检测相似定律
3.2.2.1涡流检测原理-试件表面缺陷影响涡流-Electrie-Current-·涡流变化导致检测线圈 抗变化-Magnetic Field-Coil-通过测量线圈阻抗变化,检测缺陷。-Conductive-M teral-Eddy Current's-Eddy Currents-难以-Electric-易被-探测泷-工件-Material-图3-1涡流检测示意图-图3一2裂纹垂直于涡流流向易被检测-Surface-F aw-Sub-Surface Flaw
3.2.2.2-趋肤效应和渗透深度-口趋肤效应:-Jx=Joez√-▣涡流集中在靠近激励线圈的材料表面附近 ■交变电流激励磁场强度及涡流密度,-随着深度增加按指数分布规律递减;-■涡流的相位差随着深度增加成比例的增 。-,渗透深度:-6=-√fo-▣涡流密度衰减为其表面密度的1/e36.8%时对应的深度-■渗透深度随被检 料的电导率、磁导率及激励频率的增大而减小。-口涡流探伤能够达到的极限深度:-■涡流密度仅约为其表面密度的5 时的深度--36。
3.2.2.2趋肤效应和渗透深度
3.22.3涡流检测线圈的阻抗分析-1.单线圈的阻抗-2.耦合线圈的阻抗-3.阻抗平面图
1.单线圈的阻抗-Z=√R2+X,tan0=-十-Q3-年锁-实部轴(®)-图3一4祸流检测单线围的等效电 -图3-5复阻抗平面图
2.、耦合线圈的阻抗-Z=R+-@"M2-@'M2-R,+R2+02--E:+R.+joL-joI:R:+ .+@E-=R+jX-Z。=-R2+R2+o2-R2+R-jω L2-e-Z一初级线圈的视在阻抗-Z。一次级 圈对初级线圈作用的等效阻抗-Z=ZO+Ze-图3-6耦合线圈互感电路
第3章涡流检测技术-精选文档
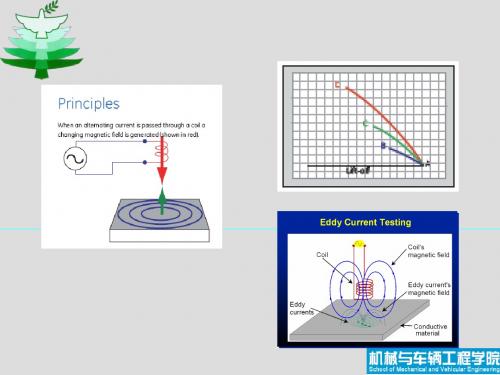
3.1 概 述
3.2 涡流检测基础知识 3.3 涡流检测仪器及设备 3.4 涡流检测方法 3.5 涡流检测诊断常用标准 3.6 涡流检测技术应用
3.1 概 述
3.1.1 涡流检测基本原理 3.1.2 涡流检测的应用
3.1.3 涡流检测的特点
3.1.4 涡流检测的发展过程
3.1.1 涡流检测基本原理
3.1.1 涡流检测基本原理
涡流检测
利用电磁感应原理,通过测定被检工件内感生涡流的变化来无损评定 导电材料及其工件的某些性能,或发现缺陷的无损检测方法称为涡流 检测。 当检测线圈中通有交变电流时,在线圈周围产生交变磁场;当此交变 磁场相对导体作运动时,导体中会感生出涡状流动的电流。 涡流伴生的感应磁场与原磁场叠加,使检测线圈的复阻抗发生变化。 导体内感生涡流的幅值、相位、流动形式及其伴生磁场受导体的物理 特性影响,进而影响检测线圈的复阻抗。 因此通过监测检测线圈的阻抗变化即可非破坏地评价导体的物理和工 艺性能。
顺磁质:
逆磁质:
铁磁质:
磁导率:
相对磁导率:
3.2.1.3 电磁感应
1.电磁感应:
当穿过闭合导电回路所包围面积的磁通量发生变化时,回路中将产生 电流的现象。 法拉第感应定律 感应电动势
2. 自感应:
当线圈中通有交变电流时,
线圈中将产生感应电动势的现象。
3. 互感应:
两载流线圈相互激起感应电动势的现象
涡流探伤能够达到的极限深度:
涡流密度仅约为其表面密度的5%时的深度 - 3δ。
三章涡流检测

▪ 圆柱体直径
– f/fg变化,线圈阻抗沿阻抗曲线切向 变动;
– 填充率η改变,阻抗曲线移位; 结果:阻抗沿弦向移动
常用检测线圈的阻抗分析
内含导电管件的穿过式线圈,特征频率:
fg
506606
r di
f / fg
导电工件的内通式线圈,特征频率:
506606
f g r di2
eff
阻抗变化
阻抗变化
变化的磁场和不变的磁导率由一个虚拟的恒定的磁场强度和变化着的磁导率 所取代。这个变化的磁导率叫有效磁导率。
有效磁导率
eff
2 J1( jr) jr J0( jr)
其中, 2 f J 0 :0阶贝塞尔函数 J 1 :1阶贝塞尔函数
可根据模型试验测得的 e f f 的变化与人工缺陷的深度、宽度及所处
引言
缺点
▪ 对象必须是导电材料,只适用于检测金属表面缺陷。 ▪ 检测深度与检测灵敏度是相互矛盾的,对一种材料进行ET时,
须根据材质、表面状态、检验标准作综合考虑,然后再确定 检测方案与技术参数。 ▪ 采用穿过式线圈进行ET时,对缺陷所处圆周上的具体位置无 法判定。 ▪ 旋转探头式ET可定位,但检测速度慢。
Conductive material
涡流检测的特点
优点
▪ 对表面或近表面缺陷高度灵敏性 ▪ 较高的探测速度 ▪ 表面不需要准备 ▪ 能够探测涂层下缺陷 ▪ 对不同缺陷有较好的区分能力 ▪ 无消耗、无辐射危害、无耦合剂 ▪ 无需污水处理 ▪ 能够进行小和复杂外形结构检测 ▪ 技术易掌握 ▪ 可做超声波检测的补充
3.2 涡流检测的应用
3.2.2 典型仪器介绍
▪ 特殊目的: (AutoSigma 3000型) – 导电性,表层厚度等. – 简单的数字读数; – 易掌握。
- 1、下载文档前请自行甄别文档内容的完整性,平台不提供额外的编辑、内容补充、找答案等附加服务。
- 2、"仅部分预览"的文档,不可在线预览部分如存在完整性等问题,可反馈申请退款(可完整预览的文档不适用该条件!)。
- 3、如文档侵犯您的权益,请联系客服反馈,我们会尽快为您处理(人工客服工作时间:9:00-18:30)。
相对磁导率r的影响
沿阻抗曲线切线变
几何尺寸d的影响
切线、径向同时变
检测频率的影响
沿阻抗曲线切线变
3.3 涡流检测仪器及设备
3.3.1 涡流检测仪
3.3.2 涡流检测探头(检测线圈)
3.3.3 对比试样
3.3 涡流检测仪器及设备
3.3.1 涡流检测仪
LC振荡器:起振容易、调整频率方便,振幅大、频率稳定
2 放大器
要求:低噪声、宽动态范围和低失真
3 抑止电路:通过信号叠加和平均消除干扰
4 检出电路:幅度探测器、相位探测器 5 显示:电流表显示、阻抗图显示、计算机数字处理和显示
3.3.2 涡流检测探头(检测线圈)
3.3.2.1 检测线圈的分类 3.3.2.2 检测线圈的使用方式
2M 2
( R2 Rr ) L
2 2 2 2
( R2 Rr ) j L1 j L2 (
2M 2
( R2 Rr ) L
2 2 2 2
)
Ze
2M 2
( R2 Rr ) L
2 2 2 2
( R2 Rr j L2 )
Z- 初级线圈的视在阻抗 Ze-次级线圈对初级线圈作用的等效阻抗 Z=Z0+Ze
3.2.2.6 填充系数
填充系数
d D
2
d--工件直径 D--线圈直径
线圈归一化视在阻抗:
L L1
L 1 r eff Re L1 R R1 r eff Im L1
3.2.2.7 影响线圈阻抗的因素
电导率的影响:
第三章 涡流检测技术
3.1 概 述
3.2 涡流检测基础知识 3.3 涡流检测仪器及设备 3.4 涡流检测方法 3.5 涡流检测诊断常用标准 3.6 涡流检测技术应用
3.1 概 述
3.1.1 涡流检测基本原理 3.1.2 涡流检测的应用
3.1.3 涡流检测的特点
3.1.4 涡流检测的发展过程
k 2 f
特征频率:使贝塞尔函数变量 jkr的模为1的频率,是工件 的固有特性,取决于工件的电磁特性和几何尺寸。
5066 fg 2 20 r r r d 2
1
3.2.2.4 有效磁导率和特征频率
3.2.2.5 涡流检测相似定律
相似定律:
kr
f / fg
3.1.1 涡流检测基本原理
3.1.1 涡流检测基本原理
涡流检测
利用电磁感应原理,通过测定被检工件内感生涡流的变化来无损评定 导电材料及其工件的某些性能,或发现缺陷的无损检测方法称为涡流 检测。 当检测线圈中通有交变电流时,在线圈周围产生交变磁场;当此交变 磁场相对导体作运动时,导体中会感生出涡状流动的电流。 涡流伴生的感应磁场与原磁场叠加,使检测线圈的复阻抗发生变化。 导体内感生涡流的幅值、相位、流动形式及其伴生磁场受导体的物理 特性影响,进而影响检测线圈的复阻抗。 因此通过监测检测线圈的阻抗变化即可非破坏地评价导体的物理和工 艺性能。
3.2.2 涡流检测技术原理
3.2.2.1 涡流检测原理
3.2.2.2 趋肤效应和渗透深度
3.2.2.3 涡流检测线圈的阻抗分析 3.2.2.4 特征频率和有效磁导率 3.2.2.5 涡流检测相似定律
3.2.2.1 涡流检测原理
试件表面缺陷影响涡流 涡流变化导致检测线圈阻抗变化 通过测量线圈阻抗变化,检测缺陷。
3.3.2.1 检测线圈的分类
1 穿过式线圈: 3 放置式线圈:Βιβλιοθήκη 小直径管材、棒材、线材等检测
2 内通过式线圈:管件、深孔、螺纹孔内壁表面检测。
板材、带材和大直径管材、棒材的表面检测, 形状复杂的工件的特定区域局部检测。
3.3.2.1 检测线圈的分类
3.3.2.2 检测线圈的使用方式
3.3.2.2 检测线圈的使用方式
3.2.1 与涡流检测相关的电学和磁学基本知识
3.2.1.1 金属的导电性
3.2.1.2 金属的磁特性
3.2.1.3 电磁感应
3.2.1.2 金属的磁特性
磁化:
物质在外磁场作用下感生出磁场的物理过程称为磁化。
感生磁场微弱、与外磁场方向相同的物质,如铝。 感生磁场微弱、与外磁场方向相反的物质,如铜。 感生磁场强的物质,如铁,钴、镍及其合金。
涡流探伤能够达到的极限深度:
涡流密度仅约为其表面密度的5%时的深度 - 3δ。
3.2.2.2 趋肤效应和渗透深度
Depth Depth Standard Depth of Penetration
(Skin Depth) 1/e or 37 % of surface density
Eddy Current Density High Frequency High Conductivity High Permeability
Reference Standards (cont.)
Material thickness standards used to help determine such things as material thinning caused by corrosion or erosion.
Reference Standards (cont.)
3.2.2.2 趋肤效应和渗透深度
趋肤效应:
涡流集中在靠近激励线圈的材料表面附近
交变电流激励磁场强度及涡流密度, 随着深度增加按指数分布规律递减;
涡流的相位差随着深度增加成比例的增加。
渗透深度:
涡流密度衰减为其表面密度的 1/e (36.8%) 时对应的深度
渗透深度随被检材料的电导率、磁导率及激励频率的增大而减小。
3.4.3 涡流检测信号分析
相位分析法
1 同步检波法
用于抑制直线状干扰电压的杂波(如棒材直径变化的干扰)
2 不平衡电桥法
用于抑制呈圆弧状电压轨迹变化的杂波(如提离效应的干扰)
频率分析法
振幅分析法
3.4.4 提离效应及其抑制
提离效应:
又称提离干扰,指在涡流检测中,探头晃动引起的
信号变化叠加在缺陷信号中产生的干扰。阻碍对缺 陷的正确判断与识别。
3.阻抗平面图
A点 B点
3.阻抗平面图
3.阻抗平面图
3.2.2.4 有效磁导率和特征频率
有效磁导率:为简化阻抗分析,假定磁场不变磁导率变化, 称为有效磁导率,事实上磁导率不变磁场变化 无限长螺线管,内置导电圆柱体,非铁磁性材料时:
eff
2
J 1 ( jkr )
jkr J 0 ( jkr )
Crack Standards:
Reference Standards (cont.)
ASME Tubing Pit Standard:
Reference Standards (cont.)
Nonconductive coating (paint) standard with various thickness of paint on aluminum substrate.
3.3.3 对比试样
检测和鉴定涡流检测仪的灵敏度、分辨力、端部 不可检测长度等性能,用于:
选择检测条件 调整检测仪器 定期检查仪器 作为整个仪器的标准当量
Reference Standards
Reference Standards (cont.)
•
In order to give the eddy current inspector useful data while conducting an inspection, signals generated from the test specimen must be compared with known values.
频率比 f/fg 相同时,不同试件的有效 磁导率、涡流密度和磁感应强度的几何 分布均相似。 导体内部的涡流分布、磁场分布随 f/fg 变化。 只要频率比相同,几何相似的不连续性 缺陷(例如以圆柱体直径的百分率表示 的一定深度和宽度的裂纹)将引起相同 的涡流效应和相同的有效磁导率变化。
相似条件: f d 2 f d 2 1 1 1 1 2 2 2 2 模型试验的理论基础
顺磁质:
逆磁质:
铁磁质:
磁导率:
相对磁导率:
3.2.1.3 电磁感应
1.电磁感应:
当穿过闭合导电回路所包围面积的磁通量发生变化时,回路中将产生 电流的现象。 法拉第感应定律 感应电动势
2. 自感应:
当线圈中通有交变电流时,
线圈中将产生感应电动势的现象。
3. 互感应:
两载流线圈相互激起感应电动势的现象
•
• •
Reference standards are typically manufactured from the same or very similar material as the test specimen.
Many different types of standards exist for due to the variety of eddy current inspections performed. The following slides provide examples of specific types of standards.