减少钢坯烧损、优化加热工艺的研究
浅谈如何有效降低加热炉钢坯氧化烧损

的 5 % 以上 。这样 既可 充 分 利 用余 热 , 0 降低 排 烟
温度 , 高 热 效 率 , 提 同时 钢 坯 在 预 热 段 可 预 热 到 80 , 0 % 还为高 温快速加热创造 了条件 。均热 段采用 耐热 滑轨 , 重视 炉底 水管 绝 热效果 ,不仅 可缩 短 均 热 时间 , 提高加热质量 , 氧化层厚度也 能得到控制 。
研究 热 工测 试结 果 发 现 , 度越 高 , 位 时 间 温 单
内生成 的氧化 铁皮 量越 多 。随着 钢 坯加 热 温度 的 升 高 , 种成份 的扩 散加 速 , 气 和 钢 的化学 反 应 各 炉
平 衡常 数也有 变化 , 加 速氧 化创 造 了条件 , 钢 为 使
的氧 化 加剧 。在 6 0C以下 时 , 轻 微 氧化 , 成 5 ̄ 有 生 极 少量 的氧 化铁 皮 ; 当温 度 大 于 7 0 时 , 化 而 6% 氧 迅速加 剧 , 氧化铁 皮 量也 急 剧增 加 。一 般 情况 下 , 加热 炉 加 热 段 和 均 热 段 炉 温 控 制 在 1 0 2 0—
c ount m ea ur s. er s e
Ke yW or ds: xd t n p o ri s h r lp ro a c o i ai rpe t ;te ma e fr n e;f co s ou in o e m a t r ;s l to
钢坯 在 加 热 炉加 热 过 程 中 , 由于 加 热 介质 具 有 氧化性 , 在钢 坯表 面会 产 生 氧化 , 不 仅损 害 了 这 钢 的性 能 , 导 致 大 量 的 氧 化 烧 损 。同 时 氧 化 铁 还 皮 掉入并 堆 积 在 均 热段 炉 底 , 炉 底 耐 火 材 料 受 使 到侵蚀 , 时 甚 至 被 迫 停 炉 扒 渣 , 加 了 劳 动 强 有 增
探讨轧钢加热炉节能及降低氧化烧损的途径

探讨轧钢加热炉节能及降低氧化烧损的途径轧钢加热炉是钢铁生产中重要的热处理设备,用于将钢坯加热至一定温度,以便进行下一道工序的加工。
然而,在加热过程中,不可避免地会出现氧化烧损现象,这会导致生产成本的增加和能源浪费。
因此,降低轧钢加热炉的能耗和氧化烧损,成为钢铁生产过程中急需解决的问题之一。
一、节能方面1、采用高效燃料:传统的轧钢加热炉通常采用重油、煤等燃料,这些燃料存在着高能耗、高排放等问题。
采用天然气、生物质燃料等清洁、高效的燃料,是减少能耗、降低碳排放的有效途径。
2、改善炉膛结构:炉膛的结构直接影响了热量的传递效率。
改善炉膛内的结构,增加热量传递面积和热量利用率,能够有效地减少能耗。
3、优化燃烧条件:在炉内达到适当的燃烧条件,通过调节风量、比例阀等工艺参数,可以提高燃烧效率,降低能耗。
4、采用余热回收技术:利用余热回收技术,在加热钢坯的过程中回收废热,供暖、供电等其他用途,从而充分利用能源。
二、降低氧化烧损方面1、采用保护气氛:在加热钢坯的过程中,采用保护气氛,能够有效地防止氧化烧损现象的发生。
通常采用氮气、氩气等惰性气体作为保护气氛。
2、合理调节加热温度:将加热温度控制在合理范围内,能够有效地降低氧化烧损的发生。
通过精准控制加热温度,可以使钢坯表面的氧化膜形成得更薄、更膜稳定,从而减少氧化烧损。
3、控制加热时间:过长的加热时间会增加氧化烧损的风险。
因此,通过控制加热时间,可以降低氧化烧损的发生。
4、优化加热速度:加热速度的快慢也会影响氧化烧损的程度。
适当加快加热速度,降低加热时间,能够减少氧化烧损。
总的来说,轧钢加热炉的能耗和氧化烧损问题是产业升级和环保要求下急需解决的关键问题。
通过采用高效燃料、改善炉膛结构、优化燃烧条件、余热回收技术等措施,可以有效地节能减排。
同时,采用保护气氛、合理控制加热温度、加热时间和速度等手段,可以减少氧化烧损现象的出现,提高生产效率和经济效益。
高棒车间加热制度的优化
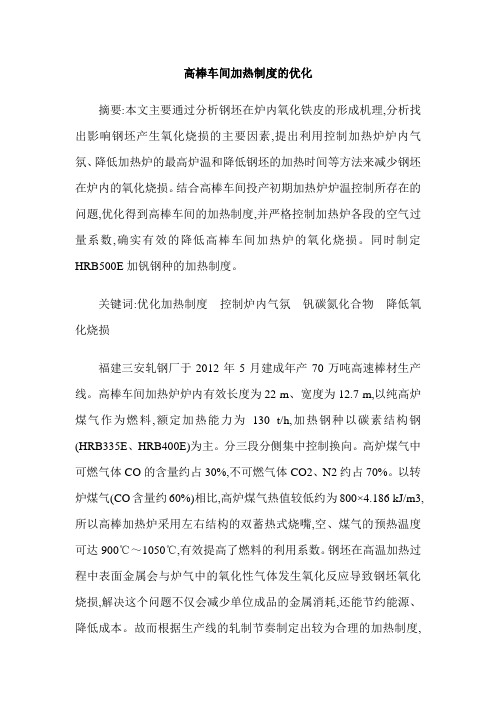
高棒车间加热制度的优化摘要:本文主要通过分析钢坯在炉内氧化铁皮的形成机理,分析找出影响钢坯产生氧化烧损的主要因素,提出利用控制加热炉炉内气氛、降低加热炉的最高炉温和降低钢坯的加热时间等方法来减少钢坯在炉内的氧化烧损。
结合高棒车间投产初期加热炉炉温控制所存在的问题,优化得到高棒车间的加热制度,并严格控制加热炉各段的空气过量系数,确实有效的降低高棒车间加热炉的氧化烧损。
同时制定HRB500E加钒钢种的加热制度。
关键词:优化加热制度控制炉内气氛钒碳氮化合物降低氧化烧损福建三安轧钢厂于2012年5月建成年产70万吨高速棒材生产线。
高棒车间加热炉炉内有效长度为22 m、宽度为12.7 m,以纯高炉煤气作为燃料,额定加热能力为130 t/h,加热钢种以碳素结构钢(HRB335E、HRB400E)为主。
分三段分侧集中控制换向。
高炉煤气中可燃气体CO的含量约占30%,不可燃气体CO2、N2约占70%。
以转炉煤气(CO含量约60%)相比,高炉煤气热值较低约为800×4.186 kJ/m3,所以高棒加热炉采用左右结构的双蓄热式烧嘴,空、煤气的预热温度可达900℃~1050℃,有效提高了燃料的利用系数。
钢坯在高温加热过程中表面金属会与炉气中的氧化性气体发生氧化反应导致钢坯氧化烧损,解决这个问题不仅会减少单位成品的金属消耗,还能节约能源、降低成本。
故而根据生产线的轧制节奏制定出较为合理的加热制度,是降低钢坯在加热炉炉内产生氧化烧损的唯一可行性方案。
根据公司生产高级别钢种要求,对HRB500E加钒钢种的加热制度进行制定。
1 存在的问题高棒车间建成投产半年后,各项经济指标和各种规格的生产节奏趋于稳定。
但是,加热炉在2012年近半年的使用中,逐渐暴露出加热制度不够完善的缺点。
如:各段炉温控制不够合理、钢坯沿长度方向上的温差较大、总体氧化烧损量偏高、面对新的高级别钢种(HRB500E 加钒)需要制定相应的加热等等。
2 优化措施2.1 优化加热制度,降低氧化烧损。
连铸坯热装热送装备的热损失减少与监测改善优化方案

连铸坯热装热送装备的热损失减少与监测改善优化方案连铸坯热装热送装备在钢铁行业中发挥着关键作用,然而,由于热损失的存在,这种装备在运行过程中面临着一些问题。
本文将探讨连铸坯热装热送装备的热损失减少与监测改善的优化方案。
一、热损失减少方案1. 热绝缘材料的使用为了减少连铸坯热装热送装备的热损失,我们可以考虑在关键部位使用热绝缘材料,例如隔热砖、耐火纤维等。
这些材料能够有效地隔离高温与外界环境,降低热能的传导和散失。
2. 温度控制系统的优化连铸坯热装热送装备的温度控制系统对于减少热损失非常关键。
我们可以考虑使用先进的温度传感器和控制器,实时监测和调控温度,以确保热能的最大利用。
3. 隔离与密封性改善装备的隔离和密封性也是减少热损失的重要因素。
我们可以通过优化装备的密封接口、采用高效密封材料等手段,减少热能的泄漏,提高整体装备的热效率。
二、热损失监测改善方案1. 热损失监测系统的建设为了实时监测连铸坯热装热送装备的热损失情况,我们可以建立一个完善的监测系统。
这个系统可以包括热量计和温度计等设备,能够准确测量和记录热能的损失情况,为优化措施的制定提供可靠数据支持。
2. 数据分析与优化通过对热损失监测系统所得到的数据进行分析,我们可以找出热能损失的主要原因和关键节点。
然后,根据这些数据结果,我们可以制定相应的优化方案,针对性地改进装备的设计和运行方式,进一步减少热损失。
3. 定期维护与检查热损失监测改善工作需要定期进行装备的维护与检查。
我们可以制定相应的维护计划,包括清洁设备、更换老化部件、调整温度控制系统等,确保装备的正常运行和最佳性能。
三、优化方案的效益与意义连铸坯热装热送装备的热损失减少与监测改善优化方案的实施,将带来以下效益与意义:1. 提高能源利用效率:通过减少热损失,我们能够最大限度地利用原料中的热能,提高生产效率和能源利用效率。
2. 降低能源消耗:热损失的减少将导致能源消耗的降低,减轻对环境的负面影响。
减少加热炉氧化烧损几种方法讲解
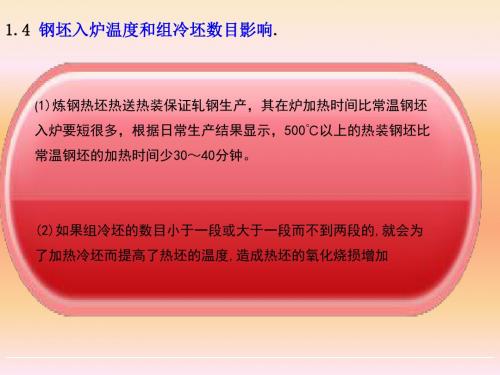
这是组坯30~39根冷钢坯在炉内的情况
图A
加热1段39
进
料 冷坯
端
加热2段33
均热段36
热
坯
出 料
端
这是组冷坯60~69钢坯在加热炉内的情景
图B
加热1段39
进
料
冷
端
加热2段33
均热段36
坯
热
坯
出 料 端
如果在轧钢生产上坯料中由于非计划停车或者是其他原因出 现下图上料情形:
进
加热1段
加热2段
料 冷
1.4 钢坯入炉温度和组冷坯数目影响.
(1)炼钢热坯热送热装保证轧钢生产,其在炉加热时间比常温钢坯 入炉要短很多,根据日常生产结果显示,500℃以上的热装钢坯比 常温钢坯的加热时间少30~40分钟。
(2)如果组冷坯的数目小于一段或大于一段而不到两段的,就会为 了加热冷坯而提高了热坯的温度,造成热坯的氧化烧损增加
优化空燃比:改变各段空燃比相似的烧火操作,将加 热1段的空燃比调整为0.6~0.65。加热2段调整为0. 6~0.65这样可以在加热1、2段快速升温,减少钢坯 在炉内时间,实现快速加热。均热段的空燃比调整为 0.45~0.55呈还原性气氛,可减少钢坯在高温段的氧 化,在加热炉保持微正压换向时即使吸入冷空气也会 减轻了残余氧在高温段对钢坯氧化的程度。
如果出现上诉情况最有效的办法是:关闭热 坯所对应的空煤气烧嘴。这样既能降低热坯 的氧化烧损又能降低热坯钢温,同时降低煤 气消耗,避免出现粘钢的危险! ②在日常3小时以上的检修过程中,进行停炉 控制,停煤气鼓风机、引风机.关闭上料端炉 门和出钢炉门. 减少冷空气的吸入,降低了氧 化铁的产生量。
调整空煤气使用比例
图1
减少钢坯烧损实践

江
西
冶
金
21 0 2年 6月
很致 密的 , 加 上氧化 铁 化 。
2 3 炉 内气 氛 的影响 .
钢坯 热装 过程 中 , 为保证 产量 , 常 将冷 、 坯混 装 , 常 热 但这 样 只能按 照冷 料来 加热 , 容 易造 成热 坯 过烧 , 很 增 加热坯 的氧化烧 损 , 没有 起到 热装 的作 用 。
体形 态 存 在 于 钢 坯 的 表 面 , 溶 点 为 13  ̄ 一 固 3 0C
15  ̄ 。影 响钢 坯 氧 化 的 因 素包 括 加 热 温 度 、 热 30( 2 加
时间 、 内气 氛 和钢 的成分 。 炉
2 1 加热 温度 的影 响 .
直控 制 在 0 8 , 近 年 来 钢 坯 的 氧 化 烧 损 率 逐 .% 但
f ura pe t fr h a ig tm p r t e,r h a ig tme,f r c t s e e a d bi e o o s c so e e tn e e aur e e tn i u na e a mo ph r n l tc mpo iin.The i o e ntme s e r as d l sto mprv me a urs ae r ie an o nd r s l Sa h e e . d s u e uti c i v d
Ke o ds: rd cn y W r e u ig;sa unn os rcie lbb r igls ;p at c
1 前 言
萍钢实 业 股份有 限公 司一轧 厂 高线 蓄 热 式加 热 炉 于 20 0 0年 8月 投产 。前 两 年 钢坯 的 氧化 烧 损 率
一
步 上 升 , 高 达到 12 , 国 内同类 加 热 炉 氧 化 烧 最 .% 而 损 率大 多在 0 9 左 右 。严 重 的 氧化 烧 损 不 但 多 消 .% 耗 能源 , 降低 钢 坯成 材率 , 而且 造 成轧 制 后钢 材 质量
探讨轧钢加热炉节能及降低氧化烧损的途径

探讨轧钢加热炉节能及降低氧化烧损的途径轧钢加热炉是钢铁生产过程中的重要环节,对钢材进行加热热处理,以提高钢材的塑性和韧性,减少体积缩减和内部应力,从而保证钢材的质量。
传统的加热炉存在能源浪费和氧化烧损等问题,为了实现节能和降低氧化烧损,可以采取以下途径:1. 优化炉膛结构:对加热炉的炉膛结构进行优化设计,在保证加热效果的前提下,尽量减少炉膛的内部空气流动,降低燃料的消耗。
改善炉膛内的温度分布,使其更加均匀,减少钢材的温度梯度和应力,提高钢材的质量。
2. 采用先进的燃烧技术:采用高效率和低氮氧化物燃烧技术,如燃烧器预混技术、气液混合燃烧技术等,提高燃料的利用率,降低燃料的消耗。
还可以采用多炉联控技术,实现燃烧系统的精细化调控,进一步提高能效。
3. 循环利用废热:将炉膛的废热进行回收利用,供给其他工艺流程或者热水供暖等用途,减少能源的浪费。
可以通过增加余热锅炉或者蒸汽发生器,将废热转化为热能,提高能源利用效率。
4. 控制氧化烧损:采取有效的技术手段,控制氧化烧损的产生。
可以通过控制燃烧过程中的氧气含量,减少钢材与氧气的接触,从而降低氧化烧损。
还可以采用保护气体或者真空炉等方法,减少氧化烧损的发生。
5. 提高设备的运行效率:定期对加热炉进行维护和保养,确保设备的正常运行。
可以采用有效的清洗、检修和调整措施,保证燃烧器、烟囱和热交换器等设备的效率和稳定性,减少能源的损耗和浪费。
轧钢加热炉节能和降低氧化烧损的途径多种多样,可以通过优化炉膛结构、应用先进的燃烧技术、循环利用废热、控制氧化烧损以及提高设备的运行效率等方法来实现。
这些措施能够有效减少能源的消耗和浪费,提高钢材的质量和产能,对于钢铁生产的可持续发展具有重要意义。
探讨轧钢加热炉节能及降低氧化烧损的途径

探讨轧钢加热炉节能及降低氧化烧损的途径
轧钢加热炉在钢铁行业中是常见的设备之一,其加热效率直接影响到钢材的质量和生
产成本。
节能和降低氧化烧损是轧钢加热炉优化运行的关键目标。
以下是几种节能和降低氧化烧损的途径:
1. 提高炉内温度均匀性:通过改进燃气喷嘴设计、调整燃烧工艺参数等方式,提高
炉内温度均匀性,减少热能浪费和热能损失。
2. 优化燃烧工艺:合理选择燃料和空气的配比,控制燃料的供应和空气的进入速度,提高燃烧效率,减少能源的消耗。
采用先进的燃烧技术,如高效燃烧器、预混合燃烧等,
进一步提高燃烧效率。
3. 合理控制加热温度:根据钢材的性质和要求,合理控制加热温度,避免过热或过冷,减少能源浪费和热能损失。
4. 优化炉内气氛:调整炉内气氛的组成和气体流速,减少氧化烧损的发生。
通过添
加还原剂、调整排烟通风等方式,使炉内气氛保持还原性,减少氧化反应,降低燃料的消
耗和热能的损失。
5. 定期清理炉膛和换热器:炉膛和换热器的积灰会增加热阻,降低换热效率,导致
能源的浪费。
定期清理炉膛和换热器,保持其表面清洁,提高换热效率,减少热能损失。
6. 合理利用余热:通过安装余热回收装置,将废气中的热能回收利用,用于预热燃
料和进料,减少能源的消耗。
7. 加强员工培训和管理:加强对操作人员的培训和管理,提高其专业技能和操作水平,使其能够合理操作设备,提高燃烧效率,避免燃料的浪费。
通过采取上述措施,可以有效地节能和降低氧化烧损,提高轧钢加热炉的运行效率和
产品质量,降低生产成本。
这些措施也符合环保要求,对减少大气污染和保护环境具有积
极意义。
连铸坯热送热装工艺热技术概述

连铸坯热送热装工艺热技术概述蒋扬虎肖坤伟王德仓肖世华丁翠娇(技术中心)摘要简要回顾了连铸坯热送热装工艺的历史,介绍了该项技术的应用现状及可取得的技术经济效果,并重点从“通用高温坯生产技术”和“温度均匀性保证技术”两个方面介绍了连铸坯热送热装工艺的各项“热技术”。
关键词连铸坯热送热装直接轧制加热炉1前言连铸坯热送热装工艺,是一项具有降低热轧加热炉燃耗、减少钢坯氧化烧损和提高热轧产量等多方面经济效益的技术。
该项工艺是连铸技术的一项重大突破,它不仅对节能有重要意义,而且对改革传统的钢铁工业结构有深远的意义,它涉及从炼钢到热轧之间各个生产环节,是一项系统工程。
目前世界许多钢铁企业根据自身的特点不同程度上采用了该项技术。
本文将对该项技术作一个初步的概括。
2连铸坯热送热装技术的历史及现状1968年美国麦克劳斯钢公司将连铸板坯装入感应加热炉,从而迈出了热装技术的第一步。
70年代初期,由于石油危机的冲击,日本钢铁工业面临严重的能源问题,日本钢铁界以此为契机,开始研究和应用连铸坯热送热装工艺,1973年日本钢管公司鹤见厂首先实现连铸坯热装轧制工艺(CC—HCR);1981年6月新日铁土界厂研究成功并在生产中实现了近程(连铸机终点和轧机始点之间距离为130m)连铸—直接轧制工艺(CC—DR);1987年6月新日铁八幡厂在生产中实现了远程CC—DR工艺(连铸机终点和轧机始点之间距离为620m)。
日本在该项技术上的成功,促进了世界各国对该项技术的研究和应用。
经过80年代世界各国钢铁界的努力,连铸坯热装和直接轧制工艺正日趋完善。
按照温度的高低,连铸坯热送工艺可分为三种情况。
(1)热装轧制HCR(Hot Charge Rolling)。
将经过(或不经过)表面处理的热板坯在大约400~700℃装入加热炉。
(2)直接热装轧制DHCR(Direct Hot Charge Rolling)。
按照和连铸同一序号,将经过(或不经过)表面处理的热板坯在大约700~1000℃装入加热炉。
加热炉形成钢坯氧化烧损的成因及措施

加热炉形成钢坯氧化烧损的成因及措施钢坯氧化烧损是钢铁行业生产过程中常见的问题,对产品质量和生产效率都会产生不良影响。
本文将介绍钢坯氧化烧损的成因和相应的措施。
一、成因分析1.高温下氧化反应:在高温下,钢坯表面的铁与空气中的氧发生氧化反应,生成氧化铁。
特别是在钢坯温度较高的情况下,氧化反应速度更快,导致表面氧化层增厚,严重影响钢坯的质量。
2.钢坯表面覆盖物:钢坯在生产过程中会与一些覆盖物接触,如油脂、润滑剂等。
这些覆盖物在高温下易发生分解、氧化等反应,产生氧化物,严重时还会产生灼烧现象。
3.炉气中的氧含量:加热炉中的燃烧气体中氧的含量对钢坯氧化烧损有重要影响。
如果氧含量过高,将加速钢坯表面的氧化反应;反之,氧含量过低,则可能出现不完全燃烧现象,产生有毒气体或出现还原性气氛,也会对钢坯表面造成损害。
4.加热炉的通气不良:加热炉内通风不良会导致炉气中氧含量过高,增加氧化烧损的风险。
二、措施建议1.控制钢坯加热温度:合理控制钢坯的加热温度是减少氧化烧损的关键。
钢坯加热温度不宜过高,以避免高温下氧化反应加速。
根据钢坯的不同材质和加工需求,合理控制加热温度,尽量选择较低的加热温度来加工,有利于减少氧化烧损。
2.清除覆盖物:在钢坯加热前,要对钢坯表面的覆盖物进行清除,如清除油脂、润滑剂等,以减少高温下的分解、氧化等反应。
可以采用机械清洗、酸洗等方法。
3.控制炉气中的氧含量:合理控制加热炉的燃烧条件,降低炉气中的氧含量。
可以通过调整炉内空气与燃气的混合比例或改变燃烧器的工作参数来实现。
同时,还可以采用反应器和转换器等装置,将废炉气中的氧转化为废气排出,以减少炉内氧含量。
4.改善通风条件:加热炉内的通风条件对氧化烧损有较大影响,要保证良好的通风条件,及时排出炉内的废气。
可以采用合理的炉内结构设计和通风系统,确保空气的流动性和通风效果。
5.使用保护措施:可以在钢坯表面涂覆一层保护剂,以防止钢坯与空气接触,减少氧化烧损。
优化加热工艺 提高加热质量
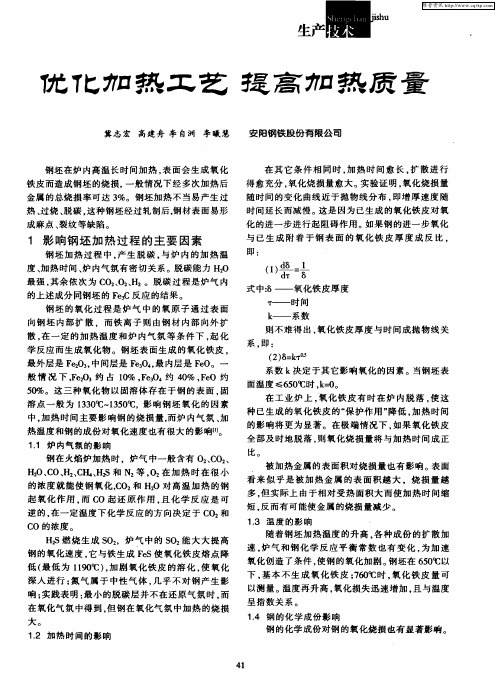
5 %。这 三种 氧化 物 以 固溶体 存 在 于钢 的 表 面 . 0 固
溶 点一 般 为 13  ̄~ 3 0C 3 0C 15  ̄.影 响 钢坯 氧化 的 因素
中, 加热 时 间 主要影 响 钢 的烧 损 量 , 而炉 内气 氛 、 加
热温 度和钢 的成 份对 氧化 速度 也有很 大 的影 响【 l 】 。 11 炉 内气氛 的影 响 . 钢 在火焰 炉加热 时 ,炉气 中一般 含有 O 、 O 、 C H 0、 O、 2C- 、 s和 N 等 , 2 加 热 时 在 很 小 2 C H 、 I H2 I , 2 O在 的浓 度就 能 使 钢氧 化 ,O 和 H o对 高 温 加热 的钢 C 2 起氧化作用 , C 而 O起 还 原 作 用 , 化 学 反 应 是 可 且 逆 的 , 一定 温度 下化 学 反应 的方 向决定 于 C 在 O 和
C 的浓 度 。 O
被 加热 金属 的表 面积对 烧损 量 也有 影响 。表面 看 来 似 乎 是 被加 热 金 属 的表 面 积 越 大 .烧 损 量 越 多 , 实 际上 由 于相对 受 热面 积大 而 使 加热 时 间缩 但 短, 反而 有可 能使 金属 的烧 损量 减少 。
13 温 度 的 影 响 .
14 钢 的 化 学 成 份 影 响 .
在 氧化 气 氛 中得到 , 钢在 氧化 气 氛 中加热 的烧损 但
大。
12 加 热 时 间 的 影 响 .
钢 的化 学成 份对 钢 的氧化烧 损 也有显 著影 响 。
4 1
维普资讯
生
ju i s h
在 其 它 条 件 相 同 时 , 热 时 间 愈长 , 散 进 行 加 扩
得 愈充 分 , 氧化烧 损量 愈 大 。 实验 证 明 , 化烧 损量 氧 随时 间 的变化 曲线 近 于抛 物线 分 布 , 即增 厚 速度 随 时间延 长而 减慢 。这是 因为 已生成 的氧化 铁皮 对 氧 化 的进 一步 进行起 阻 碍作 用 。 如果 钢 的进一 步 氧化 与 已 生成 附 着 于 钢 表 面 的 氧 化 铁 皮 厚 度 成 反 比 ,
轧钢加热炉节能及降低氧化烧损优化措施

轧钢加热炉节能及降低氧化烧损优化措施
一、轧钢加热炉节能措施:
1.优化燃烧系统:通过对燃烧系统进行优化,提高燃烧效率,减少能源的消耗。
可以采用先进的燃烧器、预混燃烧等技术,提高燃烧效率,减少氧化烧损。
2.烟气废热回收利用:将炉内产生的烟气进行回收利用,通过换热器等设备将废热传递给需要加热的物料或热水系统,达到节能的目的。
3.采用高效的隔热材料:对炉体进行隔热处理,减少热量的散失,提高加热效率。
4.控制进料速度和温度:合理控制进料速度和温度,避免过高或过低导致能源的浪费。
5.加强设备维护和管理:定期检查设备运行状况,保持设备的完好,减少能源损失。
二、降低氧化烧损优化措施:
1.优化燃烧工艺:合理控制燃烧条件,避免过多的氧气进入炉内,减少氧化反应的发生,降低氧化烧损。
2.对钢材进行预处理:采用预脱碳、减轻氧化层等措施对钢材进行预处理,减少氧化烧损。
3.优化加热工艺:针对不同的钢材,合理选择加热工艺,控制加热温度和时间,减少氧化烧损。
4.加强操作管理:加强对操作人员的培训,提高操作人员的技能水平,减少人为操作不当导致的氧化烧损。
5.优化设备结构:根据炉型和加热工艺的要求,优化加热炉的结构和
设计,减少氧化烧损。
通过采取上述措施,可以有效的节能并降低氧化烧损,提高加热炉的
加热效率和钢材的质量,减少资源的浪费和环境的污染,实现可持续发展。
探讨轧钢加热炉节能及降低氧化烧损的途径

探讨轧钢加热炉节能及降低氧化烧损的途径轧钢加热炉是钢铁工业中重要的设备之一,利用高温对钢坯进行加热,使其达到轧制温度,进而进行轧制工艺。
轧钢加热炉在工作过程中存在一定的能源消耗和氧化烧损的问题,如何节能降耗已成为轧钢企业亟待解决的问题。
对于轧钢加热炉的节能问题,可以采取以下几种途径。
一是优化设备结构,提高炉子的热效率。
通过对加热炉的结构进行改良,减少热量的散失,提高炉子的热效率。
采用高效节能的燃烧器,提高燃烧效率和热效率;增加加热炉的保温层,减少热量的辐射散失;采用热回收技术,对炉排出的废热进行回收利用等。
二是控制炉温,减少能源的消耗。
通过合理控制炉温,避免过高的加热温度,减少能源的消耗。
可以通过加入合适的燃料和调整氧气的含量,控制炉温的升降。
三是优化运行管理,提高设备的利用率。
通过优化设备的运行管理,如合理安排生产计划,减少设备的空转时间;合理调整设备的工作状态,减少设备的能耗;加强设备的维护与保养,保持设备的正常运行等,可以提高设备的利用率,减少能源的浪费。
在降低氧化烧损方面,可以采取以下几种途径。
一是控制加热速度,避免钢坯在加热过程中过快或过慢。
加热速度过快会导致钢坯表面出现氧化烧损现象,而加热速度过慢则会使加热炉的能源消耗增加。
合理控制加热速度,避免氧化烧损的发生,同时兼顾节能的需要。
二是加强炉内气氛控制,减少氧化烧损。
通过控制加热炉内的气氛,如增加还原性气氛或者采用保护气体,减少氧气与钢坯的接触,从而减少氧化烧损的发生。
三是提高加热炉的炉墙材料和保温效果。
提高加热炉的炉墙材料的抗氧化性能和保温效果,能够有效减少氧化烧损问题。
对于轧钢加热炉的节能与降低氧化烧损问题,需要轧钢企业加强技术研发和创新,引进先进设备和管理经验,加大对员工的培训和教育力度。
只有通过不断的技术革新和管理创新,才能实现轧钢加热炉的节能降耗目标,为企业的可持续发展做出贡献。
减少板坯氧化烧损的措施

p e h e s r o e f c i l o r l t o s o rng f r a e e i e p r t r l b,s o t n n a — os d t e m a u es t f e tve y c nto he l s :l we i u n c x t t m e a u e ofs a h r e i g he t i i e,a d r a o a l on r li g f n c t o p e e,ex e l nte o m i n oc a r ft g t ng tm n e s n b y c to ln ur a e a m s h r cl e c no c a d s i lp o o . i
W a g Li u n y n,Li i u u Cu h a,J n X i i i nx n, M a Xi r n,Ch n A i i o na e m a
( lt Co t .o a gSe l P ae .L d fT n te ,He e rn a d SelGru b iIo n te o p,T n sa a g h n,He e ,0 3 1 ) b i 6 0 6
A b ta t: i ai n b r n os sa mpo tntf co o a f c c o i n e hn c li de si ea t— sr c Ox d to u nig l si n i ra a t rt fe te on m ca d t c i a n xe n m tlho wo ki r ng. S e loxdai u ni l s i ai f r c te i ton b r ng os n he tng u na e woud l m a a e ti c no ia o s t e s l ke c ran e o m c ll s , h cae
不锈钢加热炉实现全部热装的工艺研究
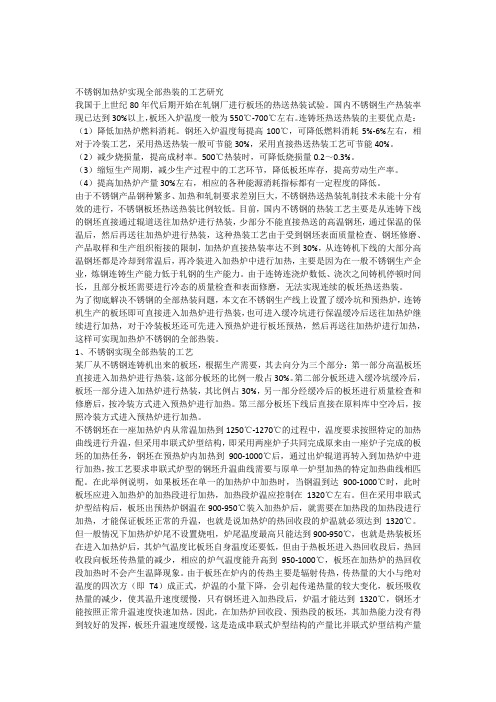
不锈钢加热炉实现全部热装的工艺研究我国于上世纪80年代后期开始在轧钢厂进行板坯的热送热装试验。
国内不锈钢生产热装率现已达到30%以上,板坯入炉温度一般为550℃-700℃左右。
连铸坯热送热装的主要优点是:(1)降低加热炉燃料消耗。
钢坯入炉温度每提高100℃,可降低燃料消耗5%-6%左右,相对于冷装工艺,采用热送热装一般可节能30%,采用直接热送热装工艺可节能40%。
(2)减少烧损量,提高成材率。
500℃热装时,可降低烧损量0.2~0.3%。
(3)缩短生产周期,减少生产过程中的工艺环节,降低板坯库存,提高劳动生产率。
(4)提高加热炉产量30%左右,相应的各种能源消耗指标都有一定程度的降低。
由于不锈钢产品钢种繁多、加热和轧制要求差别巨大,不锈钢热送热装轧制技术未能十分有效的进行,不锈钢板坯热送热装比例较低。
目前,国内不锈钢的热装工艺主要是从连铸下线的钢坯直接通过辊道送往加热炉进行热装,少部分不能直接热送的高温钢坯,通过保温的保温后,然后再送往加热炉进行热装,这种热装工艺由于受到钢坯表面质量检查、钢坯修磨、产品取样和生产组织衔接的限制,加热炉直接热装率达不到30%,从连铸机下线的大部分高温钢坯都是冷却到常温后,再冷装进入加热炉中进行加热,主要是因为在一般不锈钢生产企业,炼钢连铸生产能力低于轧钢的生产能力。
由于连铸连浇炉数低、浇次之间铸机停顿时间长,且部分板坯需要进行冷态的质量检查和表面修磨,无法实现连续的板坯热送热装。
为了彻底解决不锈钢的全部热装问题,本文在不锈钢生产线上设置了缓冷坑和预热炉,连铸机生产的板坯即可直接进入加热炉进行热装,也可进入缓冷坑进行保温缓冷后送往加热炉继续进行加热,对于冷装板坯还可先进入预热炉进行板坯预热,然后再送往加热炉进行加热,这样可实现加热炉不锈钢的全部热装。
1、不锈钢实现全部热装的工艺某厂从不锈钢连铸机出来的板坯,根据生产需要,其去向分为三个部分:第一部分高温板坯直接进入加热炉进行热装,这部分板坯的比例一般占30%。
连铸坯热装热送装备的热损失减少方案

连铸坯热装热送装备的热损失减少方案随着工业化的发展,连铸技术在钢铁行业的应用越来越广泛。
而在连铸过程中,连铸坯的热装热送装备起着至关重要的作用。
然而,由于热能的传导、辐射和对流等多种因素的影响,连铸坯在装热送过程中会发生一定程度的热损失。
本文将针对这一问题,提出一些有效的减少连铸坯热损失的方案。
1. 热损失分析在开始介绍具体的减少热损失方案之前,我们需要先了解连铸坯的热损失原因。
连铸坯热损失主要包括以下几个方面:1.1 传导热损失:连铸坯与容器、输送设备等接触面隔热性能不佳,导致热量通过传导逐渐流失。
1.2 辐射热损失:连铸坯表面存在着辐射传热,高温连铸坯表面会对周围环境辐射热量。
1.3 对流热损失:连铸坯周围的空气在热送装备运输过程中会与连铸坯表面发生对流传热,导致热量散失。
针对以上热损失原因,我们可以采取一系列方案来减少连铸坯热损失。
2. 减少传导热损失为了减少连铸坯与容器及输送设备的传导热损失,可以采取以下方案:2.1 采用高温隔热材料:在连铸装备的接触面使用高温隔热材料,有效地降低传导热损失。
2.2 优化装备接触面:改善连铸坯与容器、输送设备的接触情况,提高密封性能,减少传导热损失。
3. 减少辐射热损失为了减少连铸坯表面的辐射热损失,可以采取以下方案:3.1 表面涂层处理:在连铸坯表面进行涂层处理,增加连铸坯表面的辐射热量反射率,减少热量散失。
3.2 安装热辐射屏蔽板:在连铸坯的热传输路径上安装热辐射屏蔽板,阻挡辐射传热,降低辐射热损失。
4. 减少对流热损失为了减少连铸坯在热送过程中由于对流而造成的热损失,可以采取以下方案:4.1 安装保温罩:对连铸坯进行保温罩加固,减少与外界环境空气的对流传热。
4.2 控制送风速度和温度:在热送过程中合理控制送风速度和温度,避免过大的对流传热。
5. 结束语通过以上几个减少连铸坯热损失的方案,可以有效地提高连铸坯的热装热送效率,减少热能浪费。
在实际应用中,我们需要根据具体的情况,选择合适的方案组合,并全面考虑设备成本和能源效益等因素。
减少钢坯氧化烧损的探讨

减少钢坯氧化烧损的探讨高建舟 徐玉军 冀志宏(安阳钢铁股份有限公司)摘要 通过对钢坯在炉内加热过程中的氧化机理和现象的分析,探讨了炉内气氛、加热时间、加热温度以及钢的化学成份对钢坯氧化过程的影响,并结合生产实际操作给出了若干改善或减少钢坯氧化烧损的方法。
关键词 钢坯 氧化 探讨THE DISCUSSION TO RE DUCE STEE L BI LLET OXI DATION BURNING LOSSG ao Jianzhou Xu Y ujun Ji Zhihong(Anyang Iron&S teel C o.,Ltd)ABSTRACT Through analyzing and researching the oxidizing mechanism,discussed oxidizing law and in fluence of flav ours,heat2 ing time,heating tem perature in furnace and consist of steel billet,it is found s ome ameliorating which probably proposed the oper2 ation or methods to reduce steel billet oxidizing loss.KE Y WOR DS steel billet oxidation discussion0 前言钢在加工过程中,要经过多次加热和冷却。
每次加热和冷却,钢的表面都会生成氧化铁皮而造成钢的烧损。
一般情况下经过多次加热后金属的总烧损率可达3%~5%。
钢的氧化增加了金属的无为损耗,而且还会引起一系列不良后果,如脱碳、气泡显露等,严重影响到钢的加工质量。
1 钢坯在炉内的氧化众所周知,钢坯在炉内的氧化是由两种元素在相反的方向上扩散的结果,即炉气中的氧原子通过钢坯表面向内部扩散,而铁离子则由内部向外扩散,当两元素相遇,在一定的加热温度和炉内气氛等条件下,起化学反应而生成铁的氧化物。
- 1、下载文档前请自行甄别文档内容的完整性,平台不提供额外的编辑、内容补充、找答案等附加服务。
- 2、"仅部分预览"的文档,不可在线预览部分如存在完整性等问题,可反馈申请退款(可完整预览的文档不适用该条件!)。
- 3、如文档侵犯您的权益,请联系客服反馈,我们会尽快为您处理(人工客服工作时间:9:00-18:30)。
应从工 艺 、钢种 、规格 、质量 、产量 、成材率 和节 能降耗等诸 因素综合考 虑,合理选择 加热温度 ,从 低碳 钢 、中高碳钢 及低合金钢 的轧钢加 热实践看,炉子 加热
( a tu i ce gWi o o t. h ae o ayo B o agG o p atu 0 4 1, C i ) B oo a h n r R dC .Ld T eSls mp n f ag n ru ,B oo 1 0 0 hn tn e C a
Ab t a t T i a tc ed s rb s e e t g f r a e i i h s e d wi d l e o ep o l m a eb e n l z d u h a et p f e s r c : h s ri l e c i e h a i u n c h g p e r r i .S m r b e h v e n a ay e ,s c st y eo r — r n n eo n h
h a i g t mp r t r ,r h a i g s se a d t e d c r o ia i n o i e .T e n w i h r c s f e t g f e a ewa u o wo r n e t e e a u e e e tn y t m n e a b n z to fb l t h e r t o e so a i u n c sp t r a d a d n h l g p h n f t e a v n e p r t n me h d wa p l d h d a c d o e a i t o s p i .Th x mi a i n r s l h we a eb l t x d t n b r i g o f n n r y c n u t n o a e ee a n t u t s o d t t h i e i a i u n f d e e g o s mp i o e s h t l o o n a o
we d c d c n mi a e e t wa b i u . ee r r u e ,e o o c l n f s b i so v o s Ke r s t eb l t x d to u ig o f p i z n eh ai g p o e s a en n r y y wo d : h l i ai n b r n f;o t eo n mii g t e t r c s ;s v i g e e g h n
带 木 流 接 交
D : 1.9 9 . s .10 —6 92 1. .1 OI O 6 / i n 0 2 13 .0 1 20 9 3 j s 0
《业 热第O21第 期 工加 4 0年 2 卷1
减 少钢坯 烧损、优 化加热工艺 的研 究
闰和 平 , 闫 磊
( 包头天诚线材有 限公司 包钢集 团销 售公司,内蒙古 包头 0 4 1 ) 10 0
Re e r h OlRe u i g t eS e l l t r i g 0f n tmi i g t eHe t g P o e s sac i d c n h t e l sBu n n f d Op i z n h a i r c s Bi e a n Y AN He p n ,YAN Le — ig i
况进行全 面分析 ,针对 存在 的缺 陷和 问题,提 出了实施
方案 和技术路线 ,通 过试验优化调 整热工参数 ,控制合
理空 、燃 比例, 采用 “ 快速加热” 和 “ 三定” 先进 操作 法达到预期 目标 。于 2 1 0 0年 7月获得 了包钢 ( 团)公 集 司科技进步三等奖 。
1 钢坯加热工艺主要 内容
摘要 :针对包钢高速 线材生产 工艺加热炉中的钢 坯加 热温度 ,加热 时间 ,加热制度,氧化烧损等 问题进行 了分析 。重点对 科研 课题 进行攻关,提 出了新 颖的高线加热生产 的先进操作法。对试验进行 测定对 比,在优化加热工艺研究后,钢坯 氧化烧损 、燃耗 、产量 等取得 了成果和显著经济效益。 关键词 :钢坯烧损 ;优化加热_ ;节能减排 丁艺 中图分 类号 :T 0 7 F 8 文献标 志码 :A 文章 编号 :10 —6 92 1)20 5 —4 0 213 (0 10 —0 70
20 0 9年,对高线 步进梁式 加热炉的科研项 目 减少
钢坯烧 损 、优化加 热工艺的研 究》 进行攻 关,通过对炉
时间 、加热时间 、均热时间的总和|。 l 』
1 钢加热制度是三段式加热制度 , 钢坯的加热分别在预热段 、加热段 、 热段进行 _。 三 均 2在 段式加热 制度 中, 目前包钢 高线是从预 热 、加热到再 加 热的强化加 热方 式,称 为快速加热法 如图 1 所示 ,它 的 优越性是 均热段 的热 负荷 较大,温度偏 高,均热段起着 强化加热的作用 。这种加热方式 中,钢坯 温度一直上 升, 到均热段达到高峰后转入平缓 。 实际调 整闸阀开启度 : 均 上 5 %,均下 5 %,加上 4 %,加下 4 %。热平衡 测试 0 0 0 0
优化制度调 整后基本全部 采用此加热工 艺和 “ 三定” 操 作法,7 ,9 0 ,8 ,1 连续 4个月加热能力均衡,线材产量 为 6 2 .8 46 75 5 27 l l,6 2 . 3 ,达 49 8 ,6 9 .1 ,6 3 _ 3 4903 3 3 7t 历史月产较高 水平 。 成材率为 9 .5 9 . %, 76 %, 77%, 7 5 9 . 8 7