35 制造过程控制110-112
2018年制造业质量体系文件QP1101检验、测量和试验设备控制程序

1.目的
对检验、测量和试验设备的配置、校准、周检、维修和使用进行有效的控制,以确保量值的准确可靠,并与要求的测量能力一致,满足预期的使用要求.
2.适用范围
本程序用于对影响产品质量的所有检验、测量和试验设备包括用作检验手段的各类器具、样板/样架、测量仪器、测量传感器、特殊的检测设备及其所属软件以及影响产品/过程质量工装、检测定位装置、比较基准和过程监控仪器.本程序也适用于顾客提供的测量和售后服务用以及员工自带的测量设备管理.
3. 定义
3.1计量确认――为保证检测设备满足预定使用要求所需的一组操作程序.
3.2计量标准――实现、保持或再现单位一个或多个已知值,并通过比较将它们传递到其它
计量器具的实物量具,计量仪器等.
3.3校准――在规定条件下,为确定计量器具或讲量系统的示值,或实物量具或物质所代表的
值与相对应的由参考(计量)标准获得的量值之间关系的一组操作.
3.4溯源性――通过连续的比较链,使用测量结果能够与有关的计量标准(通常是国际或国
家计量标准)联系起来的特性.
3.5测量不确定度――表征被测量的真值所处的量值范围的评定结果.
3.6检具能力――由检测设备的测量不确定度与检验特性的公差的比例关系确定.
4.职责
4.1质保部负责检验、测量和试验设备(以下简称测量设备)的管理,包括设备的校准、维
修及送检.
4.2采购课负责测量设备的采购.
4.3各部门、车间负责各自使用的测量设备的日常维护和保养工作.
5.工作程序
5.1测量设备的配置。
冷轧和退火if钢板中{111}〈110〉和{111}〈112〉织构的形成
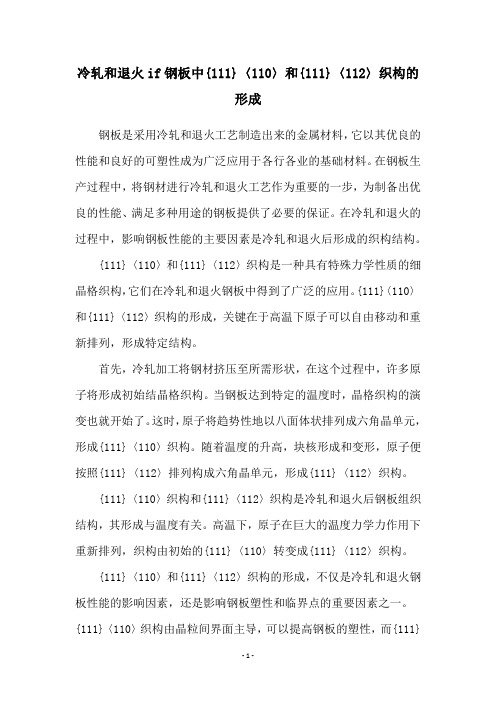
冷轧和退火if钢板中{111}〈110〉和{111}〈112〉织构的形成钢板是采用冷轧和退火工艺制造出来的金属材料,它以其优良的性能和良好的可塑性成为广泛应用于各行各业的基础材料。
在钢板生产过程中,将钢材进行冷轧和退火工艺作为重要的一步,为制备出优良的性能、满足多种用途的钢板提供了必要的保证。
在冷轧和退火的过程中,影响钢板性能的主要因素是冷轧和退火后形成的织构结构。
{111}〈110〉和{111}〈112〉织构是一种具有特殊力学性质的细晶格织构,它们在冷轧和退火钢板中得到了广泛的应用。
{111}〈110〉和{111}〈112〉织构的形成,关键在于高温下原子可以自由移动和重新排列,形成特定结构。
首先,冷轧加工将钢材挤压至所需形状,在这个过程中,许多原子将形成初始结晶格织构。
当钢板达到特定的温度时,晶格织构的演变也就开始了。
这时,原子将趋势性地以八面体状排列成六角晶单元,形成{111}〈110〉织构。
随着温度的升高,块核形成和变形,原子便按照{111}〈112〉排列构成六角晶单元,形成{111}〈112〉织构。
{111}〈110〉织构和{111}〈112〉织构是冷轧和退火后钢板组织结构,其形成与温度有关。
高温下,原子在巨大的温度力学力作用下重新排列,织构由初始的{111}〈110〉转变成{111}〈112〉织构。
{111}〈110〉和{111}〈112〉织构的形成,不仅是冷轧和退火钢板性能的影响因素,还是影响钢板塑性和临界点的重要因素之一。
{111}〈110〉织构由晶粒间界面主导,可以提高钢板的塑性,而{111}〈112〉织构由晶粒内部单元主导,可以提高钢板的临界点。
基于此,在实际的产品应用过程中,将{111}〈110〉和{111}〈112〉织构的形成,与所需的组织结构和力学性能做有效的关联,有助于优化钢板的加工条件,提高钢板的力学性能和使用性能,满足各业应用需求。
从以上可以看出,{111}〈110〉和{111}〈112〉织构的形成,对冷轧和退火钢板性能有着显著的影响,如果能准确控制冷轧和退火工艺,形成合适的织构结构,有利于优化钢板的力学性能和使用性能,提升产品质量。
兵器装备集团制造管理体系之制造工程与过程控制

中国兵器装备集团公司制造管理体系CSPS 制造工程与过程控制当前版本:2.0发布日期:2013年7月实施日期:2013年7月发布单位:中国兵器装备集团公司目录5.0 模块说明 (4)5.1 管理程序 (6)5.2 生产线立项输入 (7)5.3 工程项目立项管理 (7)5.3.1 项目立项管理流程 (7)5.3.2 项目策划 (8)5.3.3 可行性研究 (9)5.3.4 立项审批 (10)5.3.5 记录管理 (10)5.4 生产线精益设计 (11)5.4.1 生产线精益设计原则 (11)5.4.2 生产线精益设计的主要内容 (13)5.4.3 精益设计的主要技术和方法 (14)5.4.4 生产线精益设计的输出 (15)5.4.5 生产线设计的精益评审 (16)5.5 项目实施管理 (16)5.5.1 承包商选择及控制 (17)5.5.2 项目合同管理 (18)5.5.3 项目质量控制 (20)5.5.4 项目进度控制 (22)5.5.5 项目成本控制 (23)5.6 试生产管理及项目验收 (23)5.6.1 试生产管理流程 (23)5.6.2 试生产管理内容 (24)5.6.3 项目评估及验收 (25)5.7 过程控制 (26)5.7.1 生产管理模式的建立 (27)5.7.2 标准化作业 (27)5.7.3 精益工具的运用 (29)5.7.4 异常管理 (32)5.7.5 全员培训 (35)5.7.6 绩效评估 (36)5.0 模块说明(5.0)内涵制造是指企业按照生产计划的安排,采用一定的设备和工具,根据工艺规程,实现从原材料到最终产品的转化,以满足设计技术要求的增值活动过程。
本模块主要包括两部分的内容:制造工程和过程控制,它们相对独立,但又有一定联系。
制造工程指的是对新建、改建、扩建的生产线进行的从立项到投产的所有管理和控制活动,设置制造工程子模块的目的是为企业提供一套规范的流程,实现对工程项目寿命周期进行有效的管理和控制,为实现精益生产打下良好的基础;过程控制指的是在生产现场所进行的一切管理和控制活动,目的是通过对现场的整改和资源优化配置提高生产现场的管理水平,确保准时化生产的可能。
制造质量控制计划

厚度
1件
每个规格
3
外观
无夹渣、划痕、裂纹,平整
目测
每块钢板
自检
5
切割
门式
切割机
1
长度
下料公差技术标准
下料单
卷尺
1件
每规格
自检
调整、隔离
2
宽度
直尺/卷尺
每件
3
切割边缘
自动、半自动气割作业指导书
目测
每件
自检
打磨切割边
4
氧气压力
气割设备仪表
随机
自检
按作业指导书设定参数后无法达到质量要求时,应提请设备部门检修
调整、隔离、返工
2
孔径
直尺
3
孔位
卷尺
切断
冲剪
机构
1
总长
卷尺
2
对接长度
卷尺
质量控制计划
样件 试生产 生产
控制计划编号:GY——35 版本:A
编制/日期:
客户工程批准/日期
零件名称描述:刚架生产线
审核日期:
客户质量批准/日期
供方公司:
批准日期:
其他批准/日期
过程
编号
操作
描述
生产
设备
特 性
特殊
特性
方 法
反应计划
1.2焊接质量控制
工厂上岗操作的焊接人员均具有资质;焊接质量控制人员来自压力容器、船厂和重型钢结构厂家,并从事焊接工作多年;首次使用的板材焊接前均进行了焊接工艺评定。制作时对对接等强焊缝进行超声波检测以控制焊缝内在质量。
1.3流程卡的品质跟踪
主钢构的产品品质采用“质量跟踪流程卡”来进行品质跟踪,做到一件一卡,每卡上既能反映该件产品质量的具体指标和检验结果,而且卡上能反映操作人员和专职检验人员名单。产品检验合格,检验人员用专用颜色记号笔在构件的端板外侧或端头位置写上检字标示,具有该标示的部件才准流入下道工序.
控制系统中的制造过程控制技术

控制系统中的制造过程控制技术控制系统在现代制造过程中扮演着至关重要的角色。
控制系统可以被定义为利用传感器测量来自制造过程的反馈信息,并根据设定目标进行调整的技术。
制造过程控制技术是指在制造过程中使用控制系统来实现生产的系统化管理和优化。
本文将探讨控制系统中的制造过程控制技术,并阐述其在工业生产中的重要性。
一. 控制系统的基本概念控制系统是指通过对输人、处理、输出和反馈等参数进行监控和管理,以实现系统的稳定和控制的系统。
它由输入、处理、输出和反馈四个主要组成部分组成。
1. 输入:控制系统的输入通常来自传感器,可以测量温度、压力、流量等关键参数。
2. 处理:控制系统通过对输入信号的处理,计算出适当的控制操作,并进行下一步操作的决策。
3. 输出:控制系统通过执行控制操作,控制执行机构来改变制造过程的状态。
4. 反馈:控制系统通过采集制造过程的反馈信息,评估当前的系统状态,并根据需要进行调整。
二. 制造过程控制技术的种类制造过程控制技术可以分为开环控制和闭环控制两种。
1. 开环控制:开环控制是指控制系统仅基于预设参数进行操作,而无法实时响应或调整。
这种控制技术适用于制造过程中稳定和可预测的操作。
2. 闭环控制:闭环控制是指控制系统通过使用反馈信息来监控和调整制造过程中产生的偏差。
反馈信息可以帮助控制系统实时调整操作,以确保制造过程的稳定性和一致性。
三. 制造过程控制技术的应用领域制造过程控制技术广泛应用于各个行业的制造过程中,包括汽车制造、电子制造、化工制造等。
1. 汽车制造:在汽车制造中,控制系统可以用于监测和调整生产线上的各种参数,如温度、湿度和压力,以确保生产出高质量的汽车。
2. 电子制造:控制系统在电子制造中的应用主要是通过调节温度、湿度等环境参数,优化电子产品的制造过程,提高产品的一致性和可靠性。
3. 化工制造:化工制造过程中,控制系统可以实时监测和调整反应器温度、压力等参数,以确保化学反应过程的稳定性和安全性。
35号钢加工工艺流程

35号钢加工工艺流程英文回答:Process Flow of 35# Steel Processing.1. Raw Material Preparation.The raw materials for 35# steel processing include iron ore, coke, and limestone. The iron ore is crushed and screened to a desired size, and the coke is used as a fuel to provide heat for the smelting process. The limestone is used as a flux to remove impurities from the molten iron.2. Ironmaking.The raw materials are charged into a blast furnace, where they are heated to a high temperature. The iron oreis reduced to iron, which is then tapped from the furnace as molten iron.3. Steelmaking.The molten iron is charged into a basic oxygen furnace (BOF), where it is refined to remove impurities. Oxygen is blown into the furnace, which oxidizes the impurities and forms a slag. The slag is then removed from the furnace, leaving behind molten steel.4. Casting.The molten steel is cast into slabs, which are then rolled into plates, sheets, or other shapes.5. Heat Treatment.The steel is subjected to a heat treatment process to improve its mechanical properties. The heat treatment process may include annealing, normalizing, or tempering.6. Finishing.The finished steel products are then subjected to afinishing process to improve their surface quality. The finishing process may include grinding, polishing, or coating.中文回答:35号钢加工工艺流程。
机器人制造过程中的质量控制方法
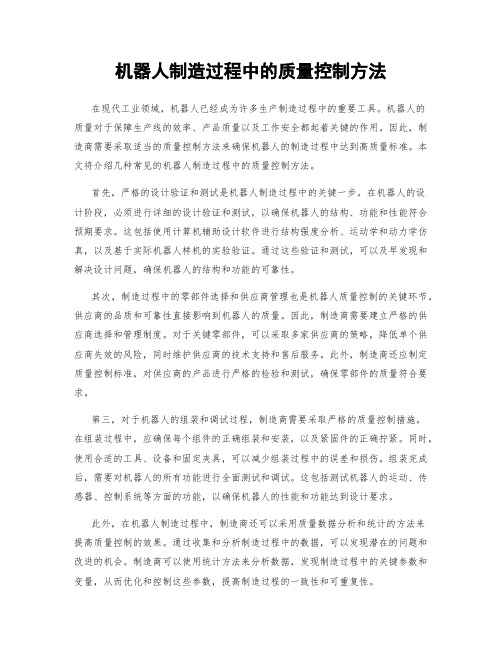
机器人制造过程中的质量控制方法在现代工业领域,机器人已经成为许多生产制造过程中的重要工具。
机器人的质量对于保障生产线的效率、产品质量以及工作安全都起着关键的作用。
因此,制造商需要采取适当的质量控制方法来确保机器人的制造过程中达到高质量标准。
本文将介绍几种常见的机器人制造过程中的质量控制方法。
首先,严格的设计验证和测试是机器人制造过程中的关键一步。
在机器人的设计阶段,必须进行详细的设计验证和测试,以确保机器人的结构、功能和性能符合预期要求。
这包括使用计算机辅助设计软件进行结构强度分析、运动学和动力学仿真,以及基于实际机器人样机的实验验证。
通过这些验证和测试,可以及早发现和解决设计问题,确保机器人的结构和功能的可靠性。
其次,制造过程中的零部件选择和供应商管理也是机器人质量控制的关键环节。
供应商的品质和可靠性直接影响到机器人的质量。
因此,制造商需要建立严格的供应商选择和管理制度。
对于关键零部件,可以采取多家供应商的策略,降低单个供应商失效的风险,同时维护供应商的技术支持和售后服务。
此外,制造商还应制定质量控制标准,对供应商的产品进行严格的检验和测试,确保零部件的质量符合要求。
第三,对于机器人的组装和调试过程,制造商需要采取严格的质量控制措施。
在组装过程中,应确保每个组件的正确组装和安装,以及紧固件的正确拧紧。
同时,使用合适的工具、设备和固定夹具,可以减少组装过程中的误差和损伤。
组装完成后,需要对机器人的所有功能进行全面测试和调试。
这包括测试机器人的运动、传感器、控制系统等方面的功能,以确保机器人的性能和功能达到设计要求。
此外,在机器人制造过程中,制造商还可以采用质量数据分析和统计的方法来提高质量控制的效果。
通过收集和分析制造过程中的数据,可以发现潜在的问题和改进的机会。
制造商可以使用统计方法来分析数据,发现制造过程中的关键参数和变量,从而优化和控制这些参数,提高制造过程的一致性和可重复性。
最后,制造商还应确保机器人的交付过程和售后服务的质量。
控制系统中的制造过程与质量控制

控制系统中的制造过程与质量控制在控制系统中的制造过程与质量控制控制系统在现代工业生产中起着至关重要的作用,它能够有效地监控和调节制造过程,确保产品的质量符合规定的标准。
本文将探讨控制系统在制造过程和质量控制中的应用。
一、控制系统在制造过程中的作用控制系统在制造过程中有以下几个主要作用:1. 监测和测量:控制系统通过传感器和测量设备对制造过程中的各种参数进行实时监测和测量,例如温度、压力、湿度等。
这些监测数据可以帮助生产厂家及时发现和解决制造过程中可能出现的问题,确保产品的质量稳定。
2. 控制和调节:控制系统能够通过操纵执行机构,调整制造过程中的各个参数,使其保持在合理的范围内。
例如,在生产过程中,通过控制温度、流量等参数,可以实现对产品质量的精确控制。
3. 故障预警和安全保护:控制系统通过分析和处理监测数据,能够及时发现制造过程中可能存在的故障和危险,从而采取相应措施确保生产过程的安全和可靠。
二、控制系统在质量控制中的应用控制系统在质量控制中具有以下几个重要应用:1. 过程控制:控制系统通过对制造过程中各个环节进行控制,实现对产品质量的控制。
例如,在汽车制造过程中,控制系统可以通过控制车身焊接的温度和压力,确保焊接质量符合要求。
2. 反馈控制:控制系统通过对产品质量的反馈信息进行处理和分析,调整制造过程中的参数,从而改进产品的质量。
例如,在电子产品制造中,通过检测产品性能参数,控制系统可以实时调整生产线上的参数,提高产品质量。
3. 数据分析和优化:控制系统能够收集和分析大量的制造过程数据,通过数据挖掘和统计分析,找出生产过程中的潜在问题,并提出优化方案。
例如,在食品加工过程中,通过对原材料的质量数据进行分析,控制系统可以调整加工参数,提高产品口感和质量。
三、控制系统在制造过程和质量控制中的挑战与未来发展尽管控制系统在制造过程和质量控制中具有重要的应用,但也面临一些挑战。
例如,制造过程中的复杂性引发了控制系统设计的困难,同时,制造过程中产生的大量数据也对控制系统的性能和存储能力提出了更高的要求。
生产制造控制程序
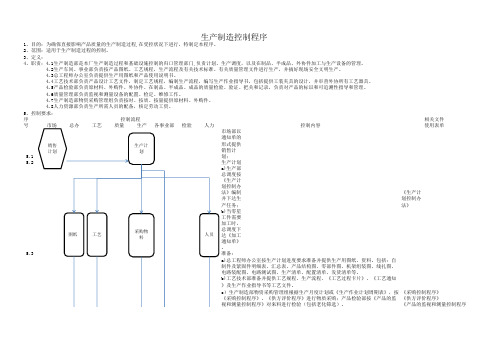
验或验证记录。
量控制程
5.6.2因生产急需,需要紧急放行或例外转序的零部件及产品,由生产制造部填写 《紧急放
《紧急放行、例外转序申请审批单》,经过工艺技术部,产品设计部门确认后, 行、例外
由总工程师审批放行,并抄送产品检验部、工艺技术部。产品检验部应对该批零 转序申请
(部)件及产品作好记录,以便一旦发现不符合规定要求时,能立即追回更换。 审批单》
制;
测量设备
a)应定
的控制程
期对监视
和测量设
备进行鉴
定,保证
其精度满
足质量要
求;
b) 不定
期的巡
检;
c)及时
维修送交
的监视和
测量设备
。
5.6
检验
5.6.1产品检验部负责依据技术指标、工艺要求,对生产制造过程和过程中的产品 《产品的
按《产品的监视和测量控制程序》进行监视和测量或验证,并做好相关的质量检 监视和测
5.5.2产品设计、工艺、车间技术人员应深入生产现场,对生产进行技术指导,按 《工艺纪 《工艺纪律管理规定》监督检查工艺纪律执行情况,解决生产中出现的技术及工艺 律管理规
问题。当出现下列情况之一时,工艺、技术人员应到现场解决问题:
定》
a) 新产品样机试制;
b) 产品首次批量生产; c)既有加工要求及检测方法和工艺规定不能满足要求时; d)产品设计更改后第一次生产。
5.5.5生
《工艺装
5.5.6生
《焊接过
5.5.7生
《环境管
5.5.8生产制造部按《产品标识和可追溯性管理规定》对产品及产品检验状态进行 《产品标
标识和可追溯性管理;
识和可追
5.8.9生
制造过程日常质量控制五种方法
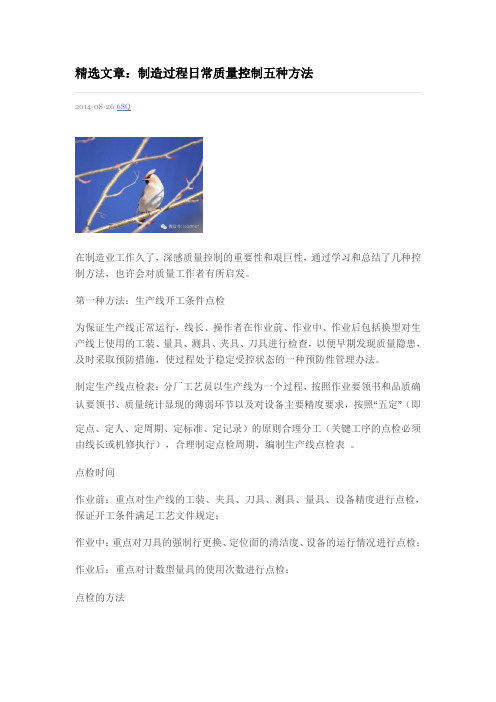
精选文章:制造过程日常质量控制五种方法2014-08-266SQ在制造业工作久了,深感质量控制的重要性和艰巨性,通过学习和总结了几种控制方法,也许会对质量工作者有所启发。
第一种方法:生产线开工条件点检为保证生产线正常运行,线长、操作者在作业前、作业中、作业后包括换型对生产线上使用的工装、量具、测具、夹具、刀具进行检查,以便早期发现质量隐患,及时采取预防措施,使过程处于稳定受控状态的一种预防性管理办法。
制定生产线点检表:分厂工艺员以生产线为一个过程,按照作业要领书和品质确认要领书、质量统计显现的薄弱环节以及对设备主要精度要求,按照“五定”(即定点、定人、定周期、定标准、定记录)的原则合理分工(关键工序的点检必须由线长或机修执行),合理制定点检周期,编制生产线点检表。
点检时间作业前:重点对生产线的工装、夹具、刀具、测具、量具、设备精度进行点检,保证开工条件满足工艺文件规定;作业中:重点对刀具的强制行更换、定位面的清洁度、设备的运行情况进行点检;作业后:重点对计数型量具的使用次数进行点检;点检的方法按照点检清单要求,操作者、线长、机修通过看、听、测判断是否有异常响声、异味、震动、磨损、定位基准有无多余物、刀具该换否等方法进行点检。
生产线长根据点检实际情况提请、制作快速点检的专用测具,提高点检的速度和准确性。
点检中的异常处理※在作业前点检发现的异常,如机床的软爪跳动超差、量具失准等生产线长要及时督促进行调整和更换,经再次点检合格后方可进行正式生产;※某些点检异常(在极限状态或暂不可使用但有其他替代办法)可以继续生产,操作者在异常部位挂黄色警示标牌,以督促线长、分厂快速修复;※作业中、作业后点检发现的异常,如设备故障、量具失准、刀具磨损、夹具定位面(销子、钻套)磨损,生产线线长组织将可疑区间的产品进行复查,将不合格品隔离;车间工艺员、技术主任确定不合格品的类别并提请相应的审理组进行审理,按照审理结论对不合格品进行处置。
制造过程控制

1 目的确保产品质量形成的全过程处于受控状态。
2 范围适用于本公司对所有产品的生产过程的控制。
3 术语无4 控制流程5 程序说明5.1 作业准备控制5.1.1 市场部最迟于周五将下一周的周生产指令下发到生产采购部,以便车间有充足的时间做好生产准备工作。
5.1.2 生产车间必须严格按照周生产指令规定的品种、数量、完成截止时间组织生产,在规定的截止时间前完成。
5.1.3 生产现场使用的作业指导书必须是由产品开发部发放并确认(受控)的,作业指导书中应规定如下事项:a.零件名称/零件号及图纸版次;b.使用设备/工装;c.外观要求;d.操作指导内容:包括原材料要求,设备参数,工艺参数,技术要求,检验要求(方法、量检具、精度、频次等),操作规程,操作要领等。
所有的作业指导书应易于在现场得到,并确保操作者在不中断操作的情况下能得到其所需的作业指导书。
5.1.4 车间按控制计划、过程流程图、设备操作规程以及各工序的作业指导书的要求对制造过程进行控制。
5.1.5 操作者(对装配线:为班组长)每班开始生产前、更换材料、作业改变或生产过程中更换产品时应进行生产起始点检,点检内容包括:a.对照生产计划检查现场工艺文件、原材料与要生产的产品是否一致;b.检查设备参数、工艺参数的设定是否符合工艺文件的要求;c.检查设备/工装状态是否良好,量具是否正确、完好;d.与上批保留的末件进行比较是否符合。
5.1.6 点检内容应填写在生产起始点检记录上,发现问题时应通知有关部门解决,只有确认点检结果不会影响生产时,方可开始生产。
5.1.7 连续作业时(交接班不停机),只须在生产开始时进行点检,生产过程中,操作者应对所生产的产品作自检,以确保产品质量。
5.2 生产过程中的控制5.2.1 车间操作者的过程作业,是以车间检查员对首件认可检验合格后开始的,由检查员填写首件检验记录,在确保生产的产品无任何问题后,进行连续生产。
每一工位经检验合格的首件,放置于本工位的指定位置。
制造过程质量控制

制造过程质量控制制造过程质量控制一、引言本文档旨在规范制造过程中的质量控制,确保产品的质量达到预期标准。
以下是制造过程质量控制的详细内容。
二、质量控制目标1.1 产品质量目标确保产品达到设计要求,并符合国家相关标准及客户需求。
1.2 过程质量目标优化制造过程,降低生产成本,提高生产效率,并持续改进过程控制,以达到质量稳定和一致性。
三、质量控制措施2.1 原材料采购控制要求供应商提供符合国家标准的原材料,并建立合格供应商名单。
对每批原材料进行严格检验,保证原材料质量符合要求。
2.2 过程控制建立严格的制造作业指导书和作业流程,明确每个生产环节的要求和控制点。
通过工艺参数的控制,确保产品在每个制造过程中的稳定性和一致性。
2.3 检测与测试在制造过程中,对关键控制点进行抽样检测和测试,以验证产品质量符合要求。
建立检测记录,并进行记录保存与追溯。
2.4 环境控制制定合理的环境控制标准,确保生产现场温度、湿度等环境条件符合要求,不影响产品质量。
2.5 员工培训与素质管控进行员工技能培训,提高员工对质量控制的认识和操作技能。
建立员工素质管理制度,对员工进行绩效评估和奖惩措施。
四、质量控制流程3.1 产品设计阶段在产品设计阶段,明确产品质量标准和要求,并进行可行性评估和技术可行性分析。
3.2 原材料采购从合格供应商处采购符合要求的原材料,并进行严格检验与监控。
3.3 过程控制通过制造作业指导书和作业流程,实施每个生产环节的控制措施。
3.4 检测与测试在制造过程中,对关键控制点进行抽样检测和测试,确保产品质量符合要求。
3.5 产品验收对生产出的产品进行全面检验,确认产品质量符合要求,方可出货。
五、相关附件1、质量控制记录表格3、员工培训计划表4、检测设备清单六、法律名词及注释1、国家相关标准:指制定和发布由国家相关部门颁布的与产品质量相关的标准。
2、合格供应商名单:经过评估和审核,符合质量要求的供应商名单。
3、抽样检测:从批量生产的产品中随机抽取部分样品进行检测。
飞机制造过程控制

飞机制造过程控制引言飞机制造是一个复杂而精细的过程,涉及到多个环节和各种细节,为了确保飞机的质量和安全性,制造过程必须进行严格的控制和监督。
本文将介绍飞机制造过程中的关键控制点以及相应的措施,旨在提高飞机制造的效率和品质。
飞机制造过程控制关键点设计控制在飞机制造过程中,设计是起点和核心。
设计控制主要包括设计评审和设计变更管理。
通过设计评审,验证和确保设计满足飞机的性能要求,并检查设计的合理性和可制造性。
设计变更管理则确保在设计过程中的任何变更都经过评估和批准,以避免不必要的错误和风险。
材料控制材料控制是飞机制造过程中至关重要的环节。
材料的选择、采购和验收必须按照制定的规范和标准进行。
在材料供应商的选择上,必须对其进行合格评估,并建立长期合作关系,以确保原材料的质量和供应的稳定。
而材料的验收则需要严格的检测和测试,确保其符合飞机的要求和规格。
加工控制加工控制是飞机制造中的关键环节之一。
加工过程包括各种加工工艺和工序,如钣金加工、机械加工、焊接等。
为了确保加工质量,需要制定和执行相应的加工工艺规程和操作规程,并进行过程控制和监测。
此外,加工中的检验和测试也是必不可少的,以确保加工件的尺寸、形状和性能符合要求。
装配控制飞机的装配过程是飞机制造中的最后一道工序,也是最重要的环节之一。
装配控制涉及到各种组件的安装、连接和调整,以确保飞机的结构完整和功能正常。
为了保证装配质量,需要制定严格的装配规程和操作规程,并进行过程控制和检查。
此外,装配后的功能测试和试飞也是必不可少的,以验证飞机的性能和可靠性。
飞机制造过程控制措施建立完善的质量管理体系飞机制造过程中的控制需要建立一个完善的质量管理体系。
该体系包括质量管理手册、程序文件、质量目标和指标等。
同时,还需要制定相应的质量管理和控制措施,如质量计划、质量检验和质量审计等。
通过质量管理体系的建立和执行,可以确保飞机制造过程的全面控制和监督。
建立有效的供应链管理飞机制造涉及到众多供应商和合作伙伴,建立有效的供应链管理是非常关键的。
钢管制造的生产流程和产品质量控制方法

钢管制造的生产流程和产品质量控制方法摘要:为了保证结构钢管制造流程符合工艺设计要求,生产过程得到规范而有效的控制,让完工交付的产品质量达到质量标准。
根据生产流程编制钢管制造流程的下料划线、钢板切割、钢管卷制、钢管焊接、组对接长、产品报验和释放等施工作业。
以指导钢管制造作业具备正确的施工流程,确保满足质量体系、工艺规范标准等专业技术要求。
关键词:作业标准、过程规范、优质高效、安全生产资质确认;焊工资质报批,焊接程序确认,焊接材料确认,焊接工艺环节确认,支持性文件确认,确认机械作业人员资质情况等满足要求方可进入项目。
材料和图纸的确认;技术工程师对设计部门下发的施工图纸、施工方案、施工料单、板材排版图、造管图等进行审核,经过确认无误后将技术文件下发到生产队。
生产队依据板材排版图精确计算下料尺寸并进行复核,待确认无误后后方可进行下料,根据施工方案编制下料优先顺序。
板材划线;施工人员首先准备好划线工具,划线顺序按照施工优先顺序进行。
施工作业人员清理好划线区域后将板材摆放平整,板材表面清理干净,确认板材规格、材质与排版图一致;如发现问题时,及时向技术人员反映,标注杆件号、下料尺寸,要求清晰准确;正确标注切割线、弯曲中心线,下料标记完成后填写报检单,由现场作业人员对接质量控制和检验人员进行报检工作。
接收到升版图纸时;技术工程师应立即核对变更内容是否已经完成,如已经完成,应立即向领班和队长反映情况,等再次确认后再进行施工;如未施工及时替换变更图纸,作废旧版图纸,按新版图纸施工避免发生不合格交付的情况以免影响产品交付质量。
卷制完成点焊完后的钢管内焊口板材切割;下料班长验收合格后的板材运进车间,按优先顺序把板材摆放到切割胎架。
对所有切割工具进行准备、检查。
切割人员检查所要切割杆件的尺寸、坡口形式,与划线所标注一致时方可切割,如有不同及时与下料人员联系。
切割过程中注意轨道摆放精确,调整好适宜的火焰,坡口角度的精度,气焊带的随时调整。
环氧乙烷储罐泄漏环境风险事故探讨

环氧乙烷储罐泄漏环境风险事故探讨摘要:风险评价常称事故(或事故后果)评价,它主要考虑与项目联在一起的突发性灾难事故,包括易燃易爆和有毒物质、放射性物质失控状态下的泄漏,大型技术系统的故障。
发生这种灾难性事故的概率虽然很小,但影响的程度往往是巨大的。
环境风险评价的目的是通过风险(危险)甄别、危害框定、预测项目可能发生的事故及其可能造成的环境(或健康)风险,即对环境产生的物理性、化学性或生物性的作用及其造成的环境变化和对人类健康的可能影响,进行系统的分析和评估,并提出减少这些影响的对策措施。
为此,结合广东某化工企业环氧乙烷储罐具体实例,定量进行环氧乙烷储罐的环境风险分析。
关键字:储罐泄漏;风险评价;探讨Abstract: the risk evaluation is often called accident ( or accident consequence) assessment, it is mainly considered and project linked to the disastrous accident, including flammable explosive and toxic substances, radioactive substances out of control under the condition of leakage, large system fault. The occurrence of these catastrophic accidents very small, but the magnitude of impact is often great. This paper combined with a chemical industry enterprise in Guangdong epoxy ethane tank concrete as examples, analyzes ethylene oxide storage tank quantitative environmental risk.Key words: tank leakage; risk assessment; discussion中图分类号:文献标识码:A 文章编号:1、项目概况:广东某化工企业设环氧乙烷储罐一个,30m3氮封保温,储罐压力0.2MPa,环氧乙烷保存温度10(℃),密度为909.9kg/m3,环氧乙烷储存量为20t,约占储罐容积最大值的73%。
- 1、下载文档前请自行甄别文档内容的完整性,平台不提供额外的编辑、内容补充、找答案等附加服务。
- 2、"仅部分预览"的文档,不可在线预览部分如存在完整性等问题,可反馈申请退款(可完整预览的文档不适用该条件!)。
- 3、如文档侵犯您的权益,请联系客服反馈,我们会尽快为您处理(人工客服工作时间:9:00-18:30)。
1 目的
确保与维持过程产品质量,及时发现过程中产品质量问题,并采取有效改善措施,防止不合格产品流入下道过程。
2 适用范围
适用于本企业所有产品制造加工过程的控制。
3 定义
无
4 职责
4.1生产部是本过程的归口管理部门,负责生产作业计划的制订和组织实施。
4.2质量部负责检验、测量和试验设备的归口管理。
4.3技术部负责生产作业技术指导文件的编制和完善以及监督其实施;负责产品批量生产时有关标准文件制订与修改并交付生产部使用。
4.4供销部负责将销售计划及销售变更计划和发货计划下发至相关部门。
4.5仓库负责原材料数量监控、生产产品库存控制并每月提供库存数据。
4.6供销部负责制定采购计划并对发生物料异常状况立即通知厂商采取必要措施。
4.7综合办公室负责为制造过程提供满足要求的人力资源。
6 相关文件
6.1《设备管理程序》 SYTL-QP-33
6.2《工艺装备管理程序》 SYTL-QP-32
6.3《标识和可追溯性管理程序》 SYTL-QP-17
6.4《交付与支付管理程序》 SYTL-QP-34
6.5《不合格品控制程序》 SYTL-QP-27
6.6《产品审核程序》 SYTL-QP-25
7 附件
过程更改控制:过程中产品的零件号、工程更改状态、制造地点、材料来源和生产过程环境等更改要求事先获得顾客生产件批准部门的批准,并应征询顾客意见以获得对这种更改批准要求的指导,由生产部负责保存更改生效日期的记录。