《金矿石氰化浸出锌粉置换提金工艺回收率计算方法》征求意见稿
从某金矿氰化渣中回收金银的试验研究

路 试验可获得精矿 中金 品位 2 4 . 6 8 、回收率 6 1 . 3 0 %, 银 品位 6 7 . 2 l 、回收率 4 7 . 4 7 %的较好指标 。浮选 精矿产品 的 x
a mmo n i u m b u t y l a e r o f l o a t i s a s c o l l e c t o r ,a n d RB - 3 a s f r o t h e r wa s d e t e r mi n e d ,a n d t h e o p e n - c i r c u i t l f o w s h e e t
( 中南大学 资源加工与生物工程学院,长沙 4 1 0 0 8 3 )
摘 要 :新疆某金矿 的浮选 精矿经生物氧化 、氧化渣 再氰化提金后 ,氰化渣 中金银含量仍较 高。针对该氰化渣进 行
了重选和浮选 试验 ,确定 了碳酸钠 +水玻璃作 组合调整 剂 、硫酸铜作 活化剂 、异戊基黄 药 + 丁基 铵黑药作组 合捕收 剂、
Ag ,t h e c o n c e n ra t t e g r a d i n g 2 4 . 6 8 g / t Au a n d 6 7 . 2 1 % Ag wa s o b t a i n e d b y o p e n - c i r c u i t t e s t ,a t r e c o v e r i e s o f
Ex p e r i me n t a l Re s e a r c h o n Re c o v e r i n g Go l d a n d S i l v e r f r o m Cy a n i d e Re s i d u e o f Go l d Or e
金矿浮选-焙烧-浸出-置换试验研究方案

金矿浮选-焙烧-浸出-置换试验研究方案2009-3-11 11:57:09 中国选矿技术网浏览366 次收藏我来说两句黑龙江乌拉嘎黄金矿业有限责任公司(简称乌拉嘎金矿)选矿厂处理能力为1450t/d,选矿工艺流程为浮选-金精矿氰化-锌粉置换。
随着矿区内东坑矿石供矿量的减少,西坑矿石出矿量的增大,入选矿石性质发生了很大变化,致使浮选回收率、金精矿浸出率逐渐降低。
对西坑矿石进行系统的选矿试验研究,目的是寻求适于该矿石性质的选矿工艺流程,合理利用矿产资源,提高金的总回收率及企业的经济效益。
一、矿石性质西坑矿石为石英黄铁矿型、碳酸盐黄铁矿型和玉髓质石英黄铁矿型。
矿石中有价元素为金,品位为2.86g/t。
主要金属矿物以白铁矿、黄铁矿为主;非金属矿物以石英、长石为主,含一定量的高岭土、云母等黏土矿物。
矿石中金属硫化物嵌布粒度较细,0.037mm以下占64.14%。
白铁矿与黄铁矿关系密切,是金的主要载体矿物。
原矿多元素分析结果见表1,金的粒度测量结果见表2。
*ω(Au),ω(Ag)/10-6金矿物的赋存状态以粒间金为主,占48.42%,裂隙金占1.82%,剩余为包裹金。
其中,脉石包裹金占29.51%,硫化物包裹金占20.25%。
硫化物包裹的金均为次显微金,机械磨矿无法使之解离或裸露。
脉石包裹金也不易完全单体解离。
二、选矿试验(一)浮选工艺流程对比试验验证现场生产工艺原矿浮选-金精矿氰化试验流程及条件见图1,浮选综合条件试验流程见图2,浮选工艺流程对比试验结果见表3。
图1 乌拉嘎金矿现场选矿工艺流程图2 乌拉嘎金矿西坑矿石浮选试验工艺流程磨矿细度-0.074mm占75%,对一次粗选、一次精选、二次扫选浮选生产工艺流程进行的验证试验,获得金精矿产率8.69%、金品位24.87g/t、金浮选回收率75.45%的技术指标,金精矿氰化浸出率71.09%,金的选矿总回收率仅为53.64%,其技术指标与生产指标基本相符。
采用一次粗选、二次精选、三次扫选浮选-中矿氰化工艺流程,金精矿的产率明显降低,品位大幅度提高,金的总回收率提高了4.93%。
广西某金矿石氰化浸出试验研究

该 工 艺具
1 材 料 与 方 法
1 1 试 验 原 料 .
有 工 艺成 熟 、操 作 简 单 且 氰 化 废 水 的处 理 易 达 到 排 放 标 准 等 特点 。对 于 易 处 理 金 矿 石 , 可 首 选 氰 化 法 进 行 提 金
;
试 验 用 的金 矿 石 取 自广 西 平 南 金 矿 山
,
.
垂
05 . 1 15 . 2 25
.
收 稿 日期 :2 0 - 1 - 0 09 1 9
誓 冶 学 硕( 4 , 从 , 南 广 院 …究 主 壮 ) 差研 生 要 事 宁 蒜 1- 9. 广 人 大 用 究 金 耋 士 8 )女(族物 西 喜 , 西 学 研
验 结 果 见 图 1 。
O 0
,
因 此 该 矿
。
采用批次法进行 浸出试验 ,主要考察 了磨 矿细度
氰 用 量 、矿浆 浓 度 、浸 出时 间 和 焙 烧 预 处 理 等 对 金 浸 出
、
蠢- 蓁 . ●
9 o
J
8 8 9 9 0 5 0 5 10 0
,
效果 体 的影 响 。利 用 搅 拌 浸 出 试 验 机 进 行 金 的 氰 化 浸 出 矗
中 图分 类 号 :T 0 ・ 1 F 8 3 2 文 献标 识 码 :A 文章 编 号
: l l一 85 O ( 。l 67 5 2 O) O 3一 。 4一 。2 03
0 引 言
氰 化 浸 出 工艺 是 提 金 工 业 普 遍 采 用 的 方 法
,
可 浸 性 ,为 该 矿 石 的开 发 利 用 提 供 技术 依 据
。
磨矿粒度对金 浸 出率影 响较 大
陕西某黄金冶炼厂焙烧氰化浸渣提金方法研究报告

陕西某黄金冶炼厂焙烧氰化浸渣提金方法研究报告本文研究了陕西某黄金冶炼厂焙烧氰化浸渣提金方法,分析了该方法的优缺点,并从工艺流程、操作技术、设备应用等方面对该方法进行了详细阐述。
一、工艺流程本研究采用的焙烧氰化浸渣提金方法主要由以下几个步骤组成:1. 氰化浸渣焙烧:将氰化浸渣送入焙炉中进行高温处理,使其得到充分焙烧,达到剥离金属的效果。
2. 氰化浸渣破碎:将焙烧后的氰化浸渣进行破碎,得到较小的颗粒状物料。
3. 搅拌:将破碎后的氰化浸渣与水一起搅拌,使其形成悬浮液。
4. 沉淀:将悬浮液静置一段时间,使其沉淀,得到含金泥浆。
5. 过滤:将含金泥浆进行过滤,去除杂质。
6. 洗涤:将过滤后的含金泥浆用水进行洗涤,使其去除残留杂质。
7. 烘干:将洗涤后的含金泥浆放入焙炉中进行烘干,得到金粉末。
二、操作技术1. 焙烧操作温度的选择:在本研究中,焙烧时采用了950℃的高温,能够使氰化浸渣得到充分焙烧,并且可以保证金属与其他杂质迅速分解。
2. 破碎操作:在氰化浸渣破碎时,应采用适当的粉碎机,能够将氰化浸渣破碎成较小的颗粒状物料。
3. 悬浮液搅拌操作:搅拌时间和强度应根据浸出效果进行调整。
4. 沉淀时间的选择:沉淀时间应根据泥浆中悬浮颗粒的大小、颗粒浓度等因素进行调整。
5. 过滤操作:过滤应选用细孔滤纸,过滤时应逐渐加压。
三、设备应用本研究采用了较新的设备,包括高温焙炉、永磁搅拌器、温度控制系统等。
这些设备的应用,不仅能够提高提金效率,而且能够保证产品质量。
四、优缺点分析本研究采用的焙烧氰化浸渣提金方法具有以下优点:1. 提金效率高:在保证产品质量的前提下,可以达到较高的提金效率。
2. 工艺流程简单:焙烧氰化浸渣提金方法的工艺流程相对简单,易于操作。
3. 环保性好:焙烧氰化浸渣提金方法的环保性好,能够减少对环境的影响。
但该方法也存在一些缺点,主要包括:1. 能源消耗大:焙烧氰化浸渣需要较高的温度,因此消耗的能源较大。
难处理金精矿冶炼过程中的废气治理简析

难处理金精矿冶炼过程中的废气治理简析摘要:某金精矿属于含砷(As)、含锑(Sb)等成分高的难处理金精矿。
难处理金精矿中的贵金属一般以显微或次显微甚至晶格金的形式被黄铁矿、毒砂和碳酸盐等矿物包裹,直接氰化浸出率很低,必须对其进行预处理。
如何确定金锑分离工艺,最大限度地回收锑,以及提高金精矿中金的回收率是目前面临的主要问题。
针对矿石性质、金精矿产品成分,最大限度地回收金(Au)、银(Ag)和锑(Sb)等有价金属,金锑分离工艺采用锑金矿湿法碱性条件下浸出锑,含锑富液电积生产阴极锑产品,分离锑后的浸渣送焙烧、氰化浸出回收金银,从而提高金精矿中金的回收率。
关键词:难处理金精矿;冶炼;废气;治理措施1冶炼工艺针对复杂难处理金精矿最终采用碱浸提锑、两段焙烧回收砷硫、水淬酸浸浸铜、氯化挥发提金工艺,在确保金高回收率的情况下,也高效回收了金精矿中的锑、银,经济效益和社会效益明显。
具体工艺如下:含锑金精矿→碱浸电积→浸出渣。
含锑金精矿浸出渣+含砷金精矿→调浆→两段焙烧→水淬浸铜→氰化浸出→氰化尾渣脱水→氯化提金→金银渣返回氰化工艺。
金泥→贵金属冶炼→金、银。
2冶炼废气治理措施冶炼过程产生的主要大气污染源有:焙烧收砷包装粉尘、焙烧烟气经制酸后的尾气、氯化提金干燥废气、物料转运及造粒粉尘、氯化提金焙烧烟气、锅炉烟气、试化验废气等。
结合《黄金行业污染防治技术政策》要求,遵循“源头减量、过程控制、末端治理、资源化利用”结合的原则,积极采用先进、成熟的污染防治技术,提高污染防治水平。
2.1源头削减措施⑴原料储存采用密闭原料棚,并喷雾洒水,确保在装卸料、转运、调浆过程中产尘较少,对转运过程中撒漏的原料及时清理,厂区设置初期雨水收集池并配套沉淀池,雨水返回工艺使用,最大限度消除原料流失及因此带来的环境污染。
⑵锑浸出电积工序的硫化钠、烧碱配置采用破袋机并集气,一是原料颗粒较大,产生的粉尘量较少;二是将集气并入硫化三级吸收塔系统。
⑶水淬过程中采用螺旋、刮板密闭输送,在焙烧车间设置防风抑尘网,并对水淬过程中产生的水雾设置捕尘器喷淋。
金矿石氰化浸出锌粉置换提金工艺回收率计算规范(送审稿)_百度.

ICSH :YS金矿石氰化浸出锌粉置换提金工艺理论回收率计算方法Calculation methods of gold recovery rateOf cyanide leaching and zinc dust precipitation (送审稿中华人民共和国工业和信息化部发布YS/T××× -20××前言本标准由中国黄金协会提出。
本标准由全国黄金标准化技术委员会归口。
本标准由长春黄金研究院负责起草。
本标准主要起草人:XXX 、 XXX 、郑晔、赵明福。
目次前言 (I)1 范围 . (1)2 术语和定义 (1)3 氰化浸出锌粉置换提金工艺理论回收率计算方法 ............ 2 3.1氰化浸出锌粉置换提金原则工艺流程及取样点设置 . ............... 2 3.2回收率计算方法 (5)金矿石氰化浸出锌粉置换提金工艺理论回收率计算方法 1 范围本标准规定了金矿石氰化浸出锌粉置换提金工艺过程理论回收率计算方法。
本标准适用于金矿石、浮选金精矿,或金矿石、浮选金精矿经焙烧、生物氧化及其它工艺预处理后,氰化浸出锌粉置换提金工艺过程。
2 术语和定义下列术语和定义适用于本标准。
2.1 金矿石 Gold ore指含有金的矿石。
2.2 氰原 Gold-bearing material(gold ore or gold concentrates before cyanide leaching进入氰化浸出作业前的含金物料,在本标准中指直接氰化的金矿石、浮选金精矿,或金矿石、浮选金精矿经焙烧、生物氧化及其它工艺预处理后得到的含金物料。
2.3 氰化浸出 Cyanide leaching在含氧的氰化物溶液中溶解金的过程。
2.4 洗涤 Washing使含金溶液与固体分离的过程。
2.5 锌粉置换 Zinc dust precipitation在含金的贵液中加入锌粉,通过锌与金的置换反应使金沉淀的方法。
某低品位金矿氰化浸出试验

SerialNo.598 February.2019
现 代 矿 业
MODERNMINING
总 第 598期 2019年 2月第 2期
某低品位金矿氰化浸出试验
刘 猛 胡杨甲 赵志强 罗思岗
(北京矿冶科技集团有限公司)
摘 要 某低品位金矿石金品位 0.65g/t,可综合回收银。金多以粒间金的形式嵌布于褐铁 矿与脉石矿物中,裸露金占总金的 95.52%,50.75%的载金矿物分布于 40~100μm粒级中。为合 理回收该矿石中的金,采用柱浸—活性炭吸附提金工艺来模拟现场堆浸进行试验。结果表明,在矿 石粒度 -20~-15mm、浸出液喷淋强度 10L/(h·m2)、浸出 35d的条件下,金浸出率可达 75%左 右,说明该金矿石适宜采用柱浸工艺提金。
3。
表 3 不同分布特征的金在共生矿物中的分布率 %
氰化渣综合回收铁、金的工艺研究

氰化渣综合回收铁、金的工艺研究随着我国黄金产业的不断发展,每年相继伴随着大量氰化渣的产生。
这些氰化渣综合回收利用率低,不仅占用大量耕地,而且严重污染环境。
由于这些氰化渣中含有大量可综合回收利用的有价金属,但至今,并未有合理有效的方法将其综合回收利用,因此,寻找一种合理有效的方法综合回收冶金工业废渣中的有价金属显得十分迫切,具有相当可观的经济效益和社会环境效益。
本文以山东招远某氰化渣为研究对象,在系统研究其工艺矿物学特性的基础上,提出了“复合添加剂还原焙烧-水浸-磁选”的新工艺来回收氰化渣中的铁,并利用硫脲法来回收尾渣中的金。
本研究主要包括两大部分:(1)复合添加剂还原焙烧-水浸-磁选法回收氰化渣中铁的工艺研究。
实验过程中研究了还原焙烧温度、焙烧时间、活性炭用量、复合添加剂用量、水浸温度、水浸时间、水浸液固比、激磁电流强度等条件对氰化渣中铁回收的影响,获得了最佳的实验条件:在原矿细磨至粒度小于74μm占85%,焙烧温度750℃,焙烧保温时间60min,氰化渣:活性炭粉:硫酸钠:碳酸钠(重量百分比)=l00:10:10:3,转速20r/min,水浸温度60℃,水浸时间5min,水浸液固比为15:1以及激磁电流为2A的条件下,可获得铁品位59.11%,回收率75.12%的铁精矿,产品基本满足工业生产的要求。
(2)硫脲法回收尾渣中金的工艺研究。
实验过程中研究了硫脲浓度、pH值、浸金液固比、浸出时间对尾渣中金回收的影响,获得了最佳的实验条件:当浸出液固比3:1,浸出温度60℃,浸出时间6h,pH值1-1.5,硫脲浓度2kg/t时,可获得最佳金的浸出率为82.30%。
本文还利用X射线衍射(XRD)、扫描电镜(SEM)、能谱面扫描(EDS)、X射线荧光(xRF)等现代分析测试手段对氰化渣铁回收工艺过程中的物相变化进行分析,表征了还原焙烧-水浸-磁选过程中各主要物相的变化规律:在水浸过程中,经复合添加剂还原焙烧所产生的可溶性物质经水浸后被洗除,而不溶性的非磁性物质经磁选后随之进入非磁性物质,部分的杂质铝、硅矿物等经水浸后被去除,还有部分进入非磁性物质,复合添加剂焙烧只能改变矿物的物相特征,但是通过水浸过程才能有效的实现铁与杂质矿物之间的有效分离,使铁的品位和回收率有所提高。
某金矿石中金浸出率的实验

某金矿石中金浸出率的实验作者:陈梅蓉来源:《中国新技术新产品》2011年第02期摘要:目前,该矿采用全泥氰化炭浆法进行生产。
由于金以超微粒金存在褐铁矿中金的氰化浸出率较低。
试验拟定了一个提高金氰化浸出率的工艺方法,在氰化浸出时,加入一种自行研制的高效助浸剂,可有效地提高金的氰化浸出率,使金的氰化浸出率达93.75%,比现行生产中工艺方法提高14%。
该工艺方法操作简便,药剂成本低,设备投资小,见效快,具有较好的经济效益和社会效益,值得推广。
关键词:氰化浸出试验;金浸出率;氰化纳耗量中图分类号:TF1文献标识码:B1矿石性质。
该金矿石中主要金属矿物为褐铁矿(针铁矿)、铅铁矾、白铅矿、砷铅矿、方铅矿、铅矾等。
金主要为自然金平均粒度为0.018mm,呈星散状、包裹体分布于褐铁矿中,有的分布于胶状褐铁矿中,个别与铅铁矾呈包裹体存在。
褐铁矿中的自然金多具有再生长结构。
自然金表面被铁污染,形成一层氧化铁钝化膜。
银主要以自然银存在平均粒度为0.0054mm,以骸晶树枝状、毛发状以及粒状分布于褐铁矿及铅铁矾矿集合体中。
经分析测定,矿样的主要化学组成见表1。
从表1可见,矿样中的Fe,Cu,Pb含量较高,尤其是铁量较高,含硫较低。
Au,Ag矿物则以微粒、超微粒状态被铁的氢氧化物和铅的次生矿物包裹。
常规氰化很难获得较好指标。
2常规氰化浸出。
采用常规氰化对该矿样进行浸出,其条件为:NaCN质量分数0.05%,液固比3:1,浸出液pH>10,浸出时间48h。
试验结果见表2。
从表2可见,在常规条件下进行氰化浸出Au,Ag的氰化浸出率较低,分别为79.73%和49.27%。
其主要原因是矿样中的铁、铜、铅较高,而Au,Ag的粒度较小,以微粒、超微粒状态被铁的氢氧化物和铅的次生矿物所包裹,且金的表面形成的氢氧化铁钝化膜影响金、银的氰化浸出。
3加助浸剂氰化浸出。
采用“提高金精矿氰化浸出工艺中金、银浸出率的技术方法”对该矿样进行氰化浸出试验。
某金矿全泥氰化锌粉置换厂工艺流程技术改造实践

某金矿全泥氰化锌粉置换厂工艺流程技术改造实践摘要:该矿石属少硫化矿物石英脉含金矿石,金属矿物主要为黄铁矿;脉石矿物主要为石英,其次为长石、方解石、云母等。
矿石中的金元素以自然金的形式产出,并且以裂隙金为主,属于易氰化浸出矿石。
经过现场工业生产调试结果证明,采用全泥氰化—锌粉置换工艺流程代替浮选处理该矿石是正确的,尾矿品位由0.57g/t降到0.20g/t,金的回收率由82.87%提高到92.16%,提高了企业的经济效益。
关键词:全泥氰化-锌粉置换、浮选、代替、回收率、经济效益Abstract: The ore is a sulfide mineral quartz vein ore less, metal minerals is mainly pyrite; major gangue mineral is quartz, feldspar, calcite, followed by mica. Of gold in Ores by natural gold in the form of output elements, and fissure gold, is easy to cyanide leaching of ores. After the industrial production debugging results show that, using the all sliming cyanidation - zinc powder replacement process for flotation treatment of the ore is correct, tailing grade from 0.57g/t to 0.20g/t, the gold recovery rate from 82.87% to92.16%, increasing economic benefits of enterprises.Key words: all slime cyanidation - zinc powder replacement; flotation; replace; recovery rate; economic benefit该金矿自1998年建成投产以来,选矿技术人员围绕着如何提高选矿技术指标和经济效益,对选矿工艺流程进行了多次的变更和革新。
用锌粉从高铜铅含氰贵液中置换金银

用锌粉从高铜铅含氰贵液中置换金银叶跃威杨建国(浙江遂昌金矿有限公司,浙江遂昌323304)摘要:遂昌金矿采用氰化法处理高铜铅锌金精矿,由于浸出液中重金属含量偏高,在用锌置换金和银时置换率下降,最低时金置换率只有12.66%。
后采用预先沉铅—提高氰碱浓度—锌粉置换—酸化除铜—酸化废液调浆—返回浸出的工艺,很好地解决了浸出贵液中重金属含量偏高影响金置换的难题。
关键词:高铜铅锌金精矿;氰化法;贵液;置换;金;银高铜铅锌金精矿一般须经过预处理除铜铅后再氰化,这样可消除重金属的积累及提高金回收率。
遂昌金矿利用现有设备对一批高铜铅锌金精矿直接进行氰化浸出,然后用锌粉置换浸出液中的金和银,取得了一定效果。
1金精矿及氰化浸出液化学成分金精矿多元素分析结果见表1。
表1 高铜铅锌金精矿化学分析结果%浸出条件:矿浆浓度35%,浸液中氧化钙浓度:0.06%;浸液中氰化钠浓度: 0.45%,搅拌浸出24小时,从金精矿中浸出金和银,金银浸出率分别达到96.19%和81.47%,同时,其他金属杂质也被浸出,贵液中杂质积累现象明显[2]。
表2 贵液组成mg/l2 用锌粉从贵液中置换金银过程中存在的问题前期置换过程基本稳定,后期指标急剧恶化。
金置换率随贵液中铜铅含量升高而下降,而银置换率基本上不变,铜置换率极低,铅置换率在90%以上。
各金属置换效果见凑3,金泥成分见表4。
表3 各金属置换率表4 金泥的化学成分生产期间曾发生进液管道严重堵塞现象,使得一些金属沉积在淤泥中。
管道沉积物成分见表5。
表5 管道沉积物成分g/tAu Ag Cu Pb Zn Fe3.15 100340.5 756.85 36.87 33.24 0.113 含金贵液置换工艺为了提高含金贵液的金置换率,进行了如下试验:1)提高贵液pH到12~12.5,结果金置换率变化不大。
2)对贵液进行酸化处理,去除其中大部分铜铅后,再调整回原来的酸度条件,结果金置换率在98%以上。
金精矿焙烧冶炼氰化项目建议书 推荐

2×400t/d金精矿焙烧氰化项目立项建议书河南中原黄金冶炼厂有限责任公司目录一、总论 (2)二、项目建设的必要性和条件 (4)三、建设规模与产品方案 (10)四、工艺流程、设备方案和工程方案 (11)五、投资估算及资金筹措 (18)六、劳动组织与岗位定员 (20)七、效益分析 (22)八、结论 (26)一、总论1、项目名称:2×400t/d金精矿焙烧氰化项目2、承办单位及概况(1)承办单位:河南中原黄金冶炼厂有限责任公司(2)单位概况:河南中原黄金冶炼厂有限责任公司,是国家“七五”重点建设项目,中国最大的专业化黄金冶炼、精炼加工企业之一,是中国黄金集团骨干企业、河南省和三门峡市政府确定的重点企业,2010年产值148亿元,位列河南省工业百强企业第15位。
公司拥有330t/d金精矿焙烧氰化、300t/d高铜金精矿焙烧氰化及100t/d直接氰化流程各一条,年产冶炼金8吨,冶炼银16吨,精炼金100吨,年产优质阴极铜1.5万吨,工业硫酸13万吨,氧化铁颜料4万吨,硫酸铵6万吨,具有年产15吨99.999%的高纯金生产能力。
公司下设冶炼、氰化、综合、精炼、精化、精艺、动力七大分厂和企业管理部、生产技术部、健康安全环保部等17个职能部室及辅助生产部门,其中工程技术研发中心为三门峡市重点实验室。
公司在职员工1300余人,其中高中级专业技术人员380余人,技术工人300余人。
公司建立20年来,始终坚持“以人为本、谋求发展、造福员工、奉献社会”的办厂方针和“精诚所至、金石为开”的企业精神,先后通过ISO9001质量管理体系﹑ISO14001环境管理体系、OHSMS18001职业健康安全管理体系认证和中国合格评定国家认可委员会CNAS认证,是我国黄金行业首家通过伦敦金银市场协会(LBMA)产品认证的企业,“中金”牌金锭因此取得了进军国际市场和参与国际竞争的通行证。
公司以优质的产品和服务赢得了客户的信任,先后与全国百余家矿山、企业建立了稳固的合作关系,并实现了互惠双赢。
氰化锌粉置换规范讲义.
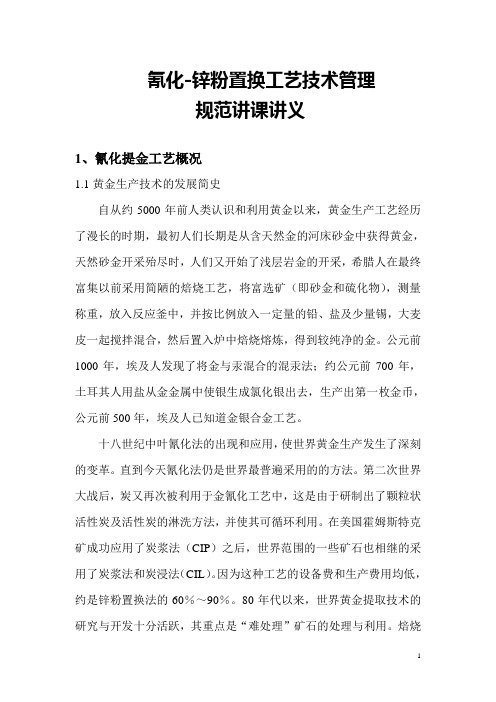
氰化-锌粉置换工艺技术管理规范讲课讲义1、氰化提金工艺概况1.1黄金生产技术的发展简史自从约5000年前人类认识和利用黄金以来,黄金生产工艺经历了漫长的时期,最初人们长期是从含天然金的河床砂金中获得黄金,天然砂金开采殆尽时,人们又开始了浅层岩金的开采,希腊人在最终富集以前采用简陋的焙烧工艺,将富选矿(即砂金和硫化物),测量称重,放入反应釜中,并按比例放入一定量的铅、盐及少量锡,大麦皮一起搅拌混合,然后置入炉中焙烧熔炼,得到较纯净的金。
公元前1000年,埃及人发现了将金与汞混合的混汞法;约公元前700年,土耳其人用盐从金金属中使银生成氯化银出去,生产出第一枚金币,公元前500年,埃及人已知道金银合金工艺。
十八世纪中叶氰化法的出现和应用,使世界黄金生产发生了深刻的变革。
直到今天氰化法仍是世界最普遍采用的的方法。
第二次世界大战后,炭又再次被利用于金氰化工艺中,这是由于研制出了颗粒状活性炭及活性炭的淋洗方法,并使其可循环利用。
在美国霍姆斯特克矿成功应用了炭浆法(CIP)之后,世界范围的一些矿石也相继的采用了炭浆法和炭浸法(CIL)。
因为这种工艺的设备费和生产费用均低,约是锌粉置换法的60%~90%。
80年代以来,世界黄金提取技术的研究与开发十分活跃,其重点是“难处理”矿石的处理与利用。
焙烧法在处理难处理矿的预处理的中普遍得到了应用。
1949年加拿大的大耶洛奈夫首先使用流化床焙烧法焙烧浮选精矿以来,许多国家和地区都建立了金精矿焙烧工厂。
1988年美国默克尔建立了第一座金矿石非酸性加压氧化厂,这种方法适合处理含碳酸盐高的矿石。
更新一代的预氧化技术是微生物湿法化学氧化(细菌氧化)。
随着金矿石难处理性的增大和环保日益严格的要求,人们正寻求能用于酸性介质以避免氧化后产物的碱性氰化处理所需要的高中和费用的浸出剂,以及相应的氰化提金技术。
虽至今仍未实现工业应用,但这毕竟是提金技术的一个重要发展方向。
微生物浸出是利用微生物(细菌)的氧化作用选择性溶解矿石中某组分的工艺过程,既可以用来提取金属,也可以用来除去矿石中的有害干扰组分。
- 1、下载文档前请自行甄别文档内容的完整性,平台不提供额外的编辑、内容补充、找答案等附加服务。
- 2、"仅部分预览"的文档,不可在线预览部分如存在完整性等问题,可反馈申请退款(可完整预览的文档不适用该条件!)。
- 3、如文档侵犯您的权益,请联系客服反馈,我们会尽快为您处理(人工客服工作时间:9:00-18:30)。
ICS H :
YS
金矿石氰化浸出锌粉置换提金工艺
回收率计算方法
Calculation methods of gold recovery rate Of cyanide leaching and zinc dust precipitation
(征求意见稿)
中华人民共和国工业和信息化部 发布
YS/T××× -20××
前言
本标准由中国黄金协会提出。
本标准由全国黄金标准化技术委员会归口。
本标准由长春黄金研究负责起草。
本标准主要起草人:XXX、XXX、郑晔、赵明福。
本标准为首次发布
目录
前言 (I)
1 范围 (1)
2 术语和定义 (1)
2.1 金矿石Gold ore (1)
2.2 氰原Gold-bearing material(gold ore or gold concentrates)
before cyanide leaching (1)
2.3 氰化浸出Cyanide leaching (1)
2.4 洗涤Washing (1)
2.5 锌粉置换Zinc dust precipitation (1)
2.6 贵液Pregnant solution (1)
2.7 贫液Barren liquor (1)
2.8 氰渣cyanide leaching residue (1)
2.9 排液the apocenosis (1)
2.10 金泥Gold mud (1)
2.11 理论回收率Theoretical recovery rate (2)
2.12浸出率Leaching recovery (2)
2.13洗涤率washing rate (2)
2.14置换率precipitate rate (2)
3 氰化浸出锌粉置换工艺流程回收率计算方法 (2)
3.1氰化浸出锌粉置换提金工艺流程及采样点设置 (2)
3.1.1工艺流程及取样点设置 (2)
3.1.2 回收率计算方法 (5)
3.1.2.1浸出率计算方法 (5)
3.1.2.2洗涤率计算方法 (5)
3.1.2.3置换率计算方法 (6)
3.1.2.4氰化理论总回收率计算方法 (6)
金矿石氰化浸出锌粉置换提金工艺回收率计算规范
1 范围
本标准规定了金矿石氰化浸出锌粉置换工艺过程理论回收率和实际回收率的计算方法。
本标准适用于原生金矿、浮选金精矿、金矿石焙烧或采用其它工艺预处理后氰化浸出锌粉置换提金工艺过程。
2 术语和定义
下列术语和定义适用于本标准。
2.1 金矿石Gold ore
指含有金的矿石
2.2 氰原Gold-bearing material(gold ore or gold concentrates) before cyanide leaching
进入氰化浸出作业前的含金物料,在本标准中指直接氰化的金矿石、金矿石的焙烧渣、生物氧化渣或其它工艺预处理后得到的含金物料。
2.3 氰化浸出Cyanide leaching
在含氧的氰化物溶液中溶解金的过程。
2.4 洗涤Washing
使含金溶液与固体分离的过程。
2.5 锌粉置换Zinc dust precipitation
在含金银的贵液中加入锌粉,通过锌与金银的置换反应使金银沉淀的方法。
2.6 贵液Pregnant solution
氰化浸出结束后,经洗涤后得到的富含金的溶液。
2.7 贫液Barren liquor
贵液经锌粉置换后的废液。
2.8 氰渣cyanide leaching residue
金矿石经氰化浸出、洗涤后的固体。
2.9 排液the apocenosis
氰化浸出后洗涤过程中,最后一级压滤(或洗涤作业)中随氰渣排走的液体。
2.10 金泥Gold mud
锌粉置换金银后得到的富含金银的固体。
2.11 理论回收率Theoretical recovery rate
即总回收率,等于浸出率、洗涤率、置换率三大率的乘积。
根据氰原及各产物计量的量和分析品位,按理论公式计算的产品金属量与氰原中的金属的比值。
2.12浸出率Leaching recovery
氰化原矿经过磨矿、浸出、洗涤作业后,固体金总的溶解量与进入氰化厂原矿含金量之比值(%)称为浸出率。
2.13洗涤率washing rate
固体金总溶解量与洗涤作业损失金属量的差值与固体金总溶解量的比值(%),称作洗涤率。
2.14置换率precipitate rate
经置换后,贵液金属量与排出贫液金属量的差值与贵液金属量的比值(%),称作置换率。
3 氰化浸出锌粉置换工艺流程回收率计算方法
3.1氰化浸出锌粉置换提金工艺流程及采样点设置
3.1.1工艺流程及取样点设置
工艺流程及取样点见图1-1。
为计算回收率,首先要确定取样点取得必要的原始数据(图1-1)。
图1-1简单氰化工艺流程及取样点设置
图1-1中:
0P ----------氰化原矿中的含金量,g/d
2P ---------排液含金量,g/d 6P -----------金泥含金量,g/d 7P -----------排出贫液金属量,g/d
为方便工艺流程技术指标计算,假设下列条件: 1).氰化原矿中液体不含金,则液β=0
2).磨矿、浸出、洗涤作业的给矿量和排矿量相等,则21Q Q Q == 3).贵液、贫液、洗水中固体很少,可以忽略不计,则0543===固固固βββ
0543===Q Q Q
4).同一溶液分别进入不同作业,含金品位不变,则
54液液ββ=
5).金泥量很少,可以忽略不计,则06666====液βR W Q 工艺流程及技术指标计算,所取的样品包括:
Q ——————氰化原矿量, t/d;
固β——————氰化原矿金品位,g/t;
1固β——————浸出结束的矿浆,经清水充分洗涤后
g/t;
1R ——————浸出作业矿浆液固比, =
1R 1
W Q
; 2固β——————洗涤作业排矿经清水充分洗涤后固体(氰渣)含金品位,g/t;
2R ——————洗涤作业排矿的液固比;
2液β——————洗涤作业排矿中液体(排液)含金品位,g/m 3
;
3液β——————进入置换作业的液体(贵液)含金品位,g/m 3
; 4液β——————经置换后的液体(贫液)含金品位,g/m 3
; 7液β—贫液品位,g/m 3
;
3W —贵液量, m 3
/d ;
4W ————返回至磨矿作业的贫液量,m 3
/d ; 5W ————洗涤作业洗涤水量,m 3
/d ; 6W ————金泥中液体量,m 3
/d ; 7W ————排出贫液量,m 3/d ;
3.1.2 回收率计算方法 3.1.2.1浸出率计算方法 a)浸出率
ε总浸=
固
固固)βββQ (2-Q =
2
2
固固固βββ-=
氰原
氰渣
氰原-⨯100%
3.1.2.2洗涤率计算方法
a)洗涤率
ε洗=
)
)固固固固22
2((ββββ---Q P Q ⨯100%
式中ε洗——————洗涤率
因 2P =22222W 液液ββQ R = 所以:ε洗=1-2
2
2固固液βββ-R =(1-
氰渣
氰原排液
-2R )⨯100%
3.1.2.3置换率计算方法 a)置换率
=
置ε%1003
37
733⨯⨯⨯-⨯W W W 液液液βββ 式中置ε—————置换率
3.1.2.4氰化理论总回收率计算方法
等于浸出率、洗涤率、置换率三大率的乘积。
ε氰总=
固
液固固ββββQ )
R (222--Q ⨯
%1003
37
733⨯⨯⨯-⨯W W W 液液液βββ
=
%1002⨯⨯⨯-⨯⨯--贵液量
贵液品位贫液排出量
贫液品位贵液量贵液品位氰原排液氰渣氰原R
ε氰总也可以用下述计算式求出:
ε氰总=ε浸⨯ε洗⨯ε置 两种计算方法的结果相同。