课程设计之齿轮啮合有限元分析
齿轮有限元分析

2 ANSYS 准备工作.................................................................................................................- 4 2.1 ANSYS 安装与启动........................................................................................................- 4 2.1.1 许可证服务器安装............................................................................................ - 4 2.1.2 主程序安装.......................................................................................................- 5 2.1.3 启动许可证服务器............................................................................................ - 7 2.1.4 ANSYS 启动与配置............................................................................................. - 8 2.2 设置工作目录............................................................................................................ - 10 2.3 指定作业名与分析标题.............................................................................................. - 10 2.3.1 指定作业名..................................................................................................... - 10 2.3.2 指定分析标题..................................................................................................- 11 2.4 定义图形界面过滤参数....................................................................................... - 11 2.5 ANSYS 单位制...................................................................................................... - 12 2.6 选取和定义单元................................................................................................. - 13 -
汽车主减速器弧齿锥齿轮参数化设计与有限元分析

实验设计方面,首先需要准备相应的材料和设备,包括优质合金钢、数控机 床、滚齿机、测量仪器等。在具体步骤和方法上,首先需要根据图纸要求制定螺 旋锥齿轮的基本参数,如模数、齿数、压力角等,然后利用三维软件进行建模, 并通过有限元分析软件进行静态和动态性能分析。
在进行参数化建模与有限元分析后,我们可以得到一些有关螺旋锥齿轮性能 的关键数据。例如,通过静态分析,可以获得齿轮的应力分布、变形和接触应力 的数值;通过动态分析,可以了解齿轮在各种工况下的振动、噪音和疲劳寿命等 情况。对于这些数据,我们可以通过对比不同参数或不同设计方案的结果,进行 性能评估和优化建议。
参考内容二
基本内容
汽车主减速器是汽车传动系统中的关键部件,其主要功能是减速并增加扭矩, 以提高车辆的驱动力和行驶稳定性。而螺旋锥齿轮作为一种高效率、高承载的齿 轮形式,在汽车主减速器中得到广泛应用。为了优化其设计和性能,本次演示将 探讨汽车主减速器螺旋锥齿轮的参数化建模与有限元分析。
在汽车主减速器螺旋锥齿轮的参数化建模中,首先需要明确建模的目的和方 法。通过借助三维软件,如SolidWorks、CATIA等,可以对螺旋锥齿轮进行几何 建模,并利用有限元分析软件,如ANSYS、Abaqus等,进行性能分析和优化。此 外,参数化建模还可以为后续的优化设计和制造提供方便,缩短产品开发周期。
未来研究方向可以从以下几个方面展开:1)深入研究弧齿锥齿轮的啮合原 理和动力学特性,建立更加精确的数学模型;2)拓展材料库和网格划分方法, 提高分析的精度和效率;3)考虑多学科耦合因素,如热力学、流体动力学等, 以更加全面地评估弧齿锥齿轮的性能;4)开展实验研究,将有限元分析结果与 实验数据进行对比,以验证分析的准确性和有效性。
5、参数化设计流程
ANSYS workbench齿轮啮合瞬态动力学分析

ANSYS workbench齿轮啮合瞬态动力学分析齿轮传动是机械系统传动方式中应用最为广泛的一种,今天给介绍一下如何利用workbench实现齿轮啮合的瞬态动力学分析。
有限元分析流程分为3大步、3小步,如下图所示。
今天将以这种方式介绍使用workbench实现齿轮啮合的分析流程。
图1 有限元分析流程一、前处理1.1 几何模型的构建本文几何模型在SolidWorks中创建,并导入workbench中,如图所示图2 齿轮对几何模型1.2 材料定义材料选用结构钢:密度:7850kg/m3,杨氏模量:2.1e11Pa,泊松比:0.31.3 有限元模型的构建有限元模型的构建包括材料赋予、网格划分以及连接关系的构建1.3.1 材料赋予双击瞬态动力学分析流程中的Model,进入Mechanical界面,单击项目树Geometry 下的两个零件,左下角细节框中,Material处指派steel材料1.3.2 网格划分为便于分析及收敛,对网格进行一个简单的控制:首先在左侧项目树Mesh处插入一个method,选中两个齿轮,划分方法为MultiZone;然后插入两个Size,对几个参与啮合的齿面进行尺寸控制,得到了如图所示的网格模型。
图3 网格模型1.3.3 连接关系的构建连接关系包括两部分:接触和运动副,运动副可以实现齿轮的转动,接触可以实现齿轮的传力。
由于workbench会自动创建向邻近位置之间的接触,但默认接触为绑定接触,不符合实际情况,故直接删除,后续手动创建相应接触。
首先在左侧项目树Connections下插入一个Frictional contact,接触面选择其中一个齿轮参与接触的几个齿面,目标面选择另一个齿轮参与接触的几个齿面。
摩擦系数为0.15,Normal Stiffness为1,Update Stiffness为Each iteration,Time Step Controls为Automatic Bisection。
某变速器斜齿轮的设计与有限元分析

摘要斜齿轮运动作为工业生产中最主要的方式之一,其存在传动效率高、功率大、运动精确、寿命久、安全性能好等特征,它主要用于任何两根轴之间进行运动和作用力的传输。
随着工业和生产技术的高速发展,对工业运动控制的精度有了更高的要求,斜齿轮有限元分析法使用得到了广大学者们的密切注意。
本设计运用Ansys Workbench软件对斜齿轮进行了有限元的分析,包括斜齿轮的静态分析和斜齿轮变形分析。
因为我们拥有现有的斜齿轮的三维模型及斜齿轮啮合时的三维模型,所以只需要在Ansys Workbench中,直接将三维模型依次导入其中;再然后,在Ansys Workbench软件中依次对两种三维模型进行有限元的分析,获得各自的应力分布云图和形变量图;最终,对斜齿轮和啮合的斜齿轮副依次进行静力与变形的答案汇总,并将汇总得出的结论进行分析,并得出最终评价。
关键词:斜齿轮,有限元分析,应力云图,Ansys WorkbenchAbstractOne of the helical gear movement as the main way of sports industry, with large transmission power, high efficiency, precision, long working time, safe and reliable characteristics, it is mainly used for transmission between any two axes of motion and force. With the rapid development of industry and production technology, the accuracy of industrial motion control has been more and more demanding.This design uses the Ansys Workbench software to carry on the finite element analysis of the helical cylindrical gear, including the static analysis of the helical gear and the deformation analysis of the helical gear. Because we have three-dimensional three-dimensional model of helical gear and the helical gear pairs, so only in the Ansys Workbench, will turn into the direct 3D model; then, in the Ansys Workbench software in finite element analysis of two kinds of three-dimensional model, get the stress distribution and deformation diagram each other; finally, the meshing of helical gear and helical gear pair in the static deformation and answer summary, and the summary of the conclusion of the analysis, and draw the final evaluation.Keywords:Helical cylindrical gears,Finite element analysis;,Stress nephogram,Ansys Woekbench目录摘要 (I)Abstract ...................................................................................................................................... I I 1 绪论. (1)1.1论文研究的意义 (1)1.2本论文研究的主要内容和特征 (1)1.3有限元分析介绍 (2)1.3.1有限单元法的发展及应用 (2)1.3.2Anysys Workbench软件特征 (3)1.4本论文研究的主要目的 (4)1.5本章小结 (4)2 变速器和齿轮 (5)2.1汽车变速器的发展 (5)2.2汽车变速器齿轮的作用 (5)2.3齿轮的发展与分析 (6)2.3.1 齿轮的特点及种类 (6)2.3.2 国内外齿轮的分析概况 (7)2.3.3 齿轮有限元分析基本原理 (9)3斜齿轮工况下的失效分析 (10)3.1斜齿轮运动时的特征概述 (10)3.2斜齿轮的主要失效形式 (11)3.3斜齿轮的改进措施 (12)4 斜齿轮的有限元分析 (14)4.1斜齿轮有限元模型的建立 (14)4.2斜齿轮静力分析 (15)4.2.1模型载荷和约束的施加 (15)4.2.2添加材料的属性 (16)4.2.3 网格的划分 (16)4.2.4 Ansys Workbench分析 (17)4.3斜齿轮对变形有限元分析 (20)4.4图形结果分析与对比校核 (22)4.4.1图形结果分析 (22)4.4.2两种疲劳强度校核 (23)4.5本章小结 (23)5 总结 (24)5.1总结 (24)5.2展望 (24)参考文献 (26)致谢 (27)1 绪论1.1论文研究的意义就在目前的工业情形之下,不可否认工业运动中最重要的运动之一就是斜齿轮运动,其应用范围之广包括了工业、冶金、矿业、汽车、及船舶等领域[1]。
齿轮接触的有限元分析
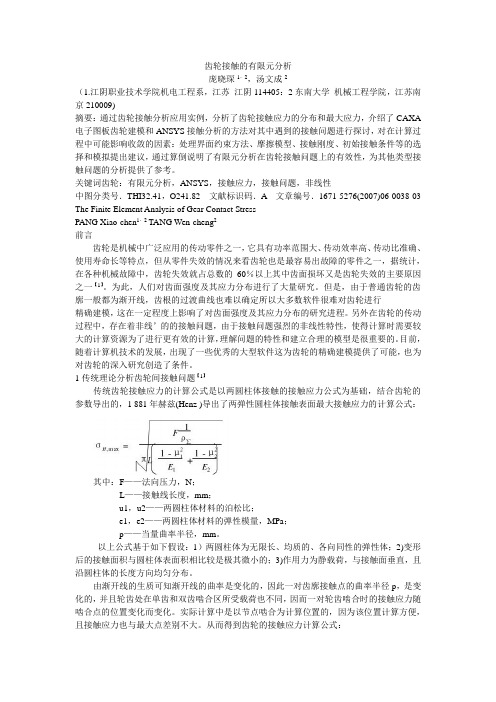
齿轮接触的有限元分析庞晓琛1、2,汤文成2(1.江阴职业技术学院机电工程系,江苏江阴114405:2东南大学机械工程学院,江苏南京210009)摘要:通过齿轮接触分析应用实例,分析了齿轮接触应力的分布和最大应力,介绍了CAXA 电子图板齿轮建模和ANSYS接触分析的方法对其中遇到的接触问题进行探讨,对在计算过程中可能影响收敛的因素:处理界面约束方法、摩擦模型、接触刚度、初始接触条件等的选择和模拟提出建议,通过算倒说明了有限元分析在齿轮接触问题上的有效性,为其他类型接触问题的分析提供了参考。
关键词齿轮:有限元分析,ANSYS,接触应力,接触问题,非线性中图分类号.THI32.41,O241.82 文献标识码.A 文章编号.1671-5276(2007)06-0038-03 The Finite Element Analysis of Gear Contact StressPANG Xiao-chen1、2 TANG Wen-cheng2前言齿轮是机械中广泛应用的传动零件之一,它具有功率范围大、传动效率高、传动比准确、使用寿命长等特点,但从零件失效的情况来看齿轮也是最容易出故障的零件之一,据统计,在各种机械故障中,齿轮失效就占总数的60%以上其中齿面损坏又是齿轮失效的主要原因之一【1】。
为此,人们对齿面强度及其应力分布进行了大量研究。
但是,由于普通齿轮的齿廓一般都为渐开线,齿根的过渡曲线也难以确定所以大多数软件很难对齿轮进行精确建模,这在一定程度上影响了对齿面强度及其应力分布的研究进程。
另外在齿轮的传动过程中,存在着非线’的的接触问题,由于接触问题强烈的非线性特性,使得计算时需要较大的计算资源为了进行更有效的计算,理解问题的特性和建立合理的模型是很重要的。
目前,随着计算机技术的发展,出现了一些优秀的大型软件这为齿轮的精确建模提供了可能,也为对齿轮的深入研究创造了条件。
1传统理论分析齿轮间接触问题【1】传统齿轮接触应力的计算公式是以两圆柱体接触的接触应力公式为基础,结合齿轮的参数导出的,1 881年赫兹(Henz )导出了两弹性圆柱体接触表面最大接触应力的计算公式:其中:F——法向压力,N;L——接触线长度,mm;u1,u2——两圆柱体材料的泊松比;e1,e2——两圆柱体材料的弹性模量,MPa;p——当量曲率半径,mm。
有限元分析法在齿轮设计中的应用

有限元分析法在齿轮设计中的应用————————————————————————————————作者:————————————————————————————————日期:2- 61 -有限元分析法在齿轮设计中的应用宋国岩摘 要:现代机械零件不仅承受各种复杂机械载荷,还可能工作在热、电、磁、流体的环境中,因此零件设计不仅要考虑机械载荷,还应对其它因素的作用进行计算,本文在介绍了有限元分析软件功能,有限元分析软件的静力、动力分析方法基础上,介绍了如何使用有限元分析软件ANSYS 进行有限元分析,完成齿轮设计的方法。
关键词:有限元分析; 模态; 质量矩阵; 等效应力引言有限元分析方法是随计算机发展起来,在计算数学、计算力学和计算工程科学领域的先进计算方法。
其就是将复杂结构假设离散为有限数目的单元组合体,对复杂结构的物理性用离散法进行分析得出的近似结果来代替复杂计算,解决理论分析无法解决的问题。
有限元分析计算法已广泛应用,并开发出通用和专用软件,如ANSYS 、MSC/NASTRAN 等.有限元软件的前处理器,使用计算机视窗、图形技术和交互式操作方式等,建模效率高,特别是非线性问题的求解能力强.有限元软件的后处理器,用户容易获得和处理数值计算结果,并可利用图形功能进行深层次再加工。
一般有限元分析软件支持工业数据/几何模型交换标准,与CAD 设计系统或CAD/CAE/CAM 互留单向或双向接口。
有限元软件有多种操作系统版本,例如Unix 、Windows/NT 操作系统等,同时支持多种硬件平台。
其中ANSYS 功能强、操作方便、硬件适应性较好,与常用的CAD 软件具有良好接口等优点。
1。
ANSYS 有限元分析软件 1。
1 ANSYS 功能介绍ANSYS 的功能包括:结构分析、结作者简介:宋国岩(1964—)辽宁黑山县人,硕士,教授、高级工程师,两项自治区级科研课题主持人、在国家核心期刊发表多篇论文,从事机械电子工程及实践教学.构非线性分析、热分析、电场分析、压电分析、电磁场分析、耦合场分析、流体流动分析、ANSYS的材料与单元库等。
齿轮的精确建模及其接触应力有限元分析

齿轮的精确建模及其接触应力有限元分析齿轮是机械系统中重要的运动元件,其质量和可靠性对产品质量及使用寿命有重要影响,因此齿轮的精确建模及其接触应力的分析显得尤为重要。
齿轮精密建模是实现齿轮精确分析的基础,因此建立精确的齿轮模型是本文的重要内容。
首先,我们利用工程设计软件进行齿轮模型的建模,并使用外圆角,内圆角,基圆角和压力角规划齿轮的几何形状。
然后,利用有限元分析软件对齿轮的接触应力进行模拟分析,判断齿轮的设计是否合理,以保证机械元件的工作可靠性。
在有限元分析之前,我们还需要将齿轮模型网格化,可以计算模型的节点以及每个节点的参数。
有限元分析的原理是,利用有限元法对形状空间内的物体进行离散,将齿轮模型划分成多个元素,每个元素可以用一组有限的方程描述。
对每个元素进行处理,采用雅可比矩阵,将模型的每个单元的变量及参数表示出来,然后根据受力状况求解不同的齿轮模型的接触应力分布和应变能量。
最后,我们利用有限元分析解出齿轮模型的接触应力和应变能量,进而求出质量,强度,寿命等物理量,以检验齿轮的设计性能。
本文通过精确的齿轮建模及其接触应力有限元分析,从而实现对齿轮性能的有效评估。
通过应用有限元方法建立精确的齿轮模型,从而实现对齿轮接触应力的准确分析和衡量,以检验齿轮的设计性能,进而提升设计和制造的质量与可靠性。
此外,利用有限元分析法还可以模拟齿轮的多轴载荷特性,从而更好的理解齿轮的工作过程,从而为优化设计带来有效的参考。
总之,齿轮的精确建模及其接触应力有限元分析在机械零件设计和制造中具有重要作用,而有限元方法是实现齿轮模型精确分析的理想方法。
有限元分析法可以较为精确地模拟齿轮的接触应力,为优化机械零件设计及确保机械元件可靠性提供有力的参考。
齿轮有限元分析

基于ANSYS的齿轮传动有限元分析和优化摘要ANSYS是随着电子计算机的发展而迅速发展起来的一种在计算数学,计算力学和计算工程科学领域最有效的通用有限元分析软件。
它是融结构,热,流体,电磁,声学于一体的大型通用有限元商用分析软件。
利用ANSYS有限元分析,可以对各种机械零件,构件进行应力,应变,变形,疲劳分析,并对某些复杂系统进行仿真,实现虚拟的设计,从而大大节省人力,财力和物力。
由于其方便性、实用性和有效性,ANSYS软件在各个领域,特别是机械工程当中得到了广泛的应用。
齿轮是机械中常用的一种零件,其在工作的过程中会产生应力,应变和变形,为保证其正常工作需要对齿轮的轮齿和整体受力进行分析,保证其刚度和强度的要求。
本论文采用ANSYS软件对齿轮进行静力学分析和优化实现对齿轮的虚拟设计。
齿轮是最重要的零件之一。
它具有功率范围大,传动效率高,传动比正确,使用寿命长等特点,但从零件失效的情况来看,齿轮也是最容易出故障的零件之一。
据统计,在各种机械故障中,齿轮失效就占故障总数的60%以上。
其中轮齿的折断又是齿轮失效的主要原因之一。
齿轮啮合过程作为一种接触行为, 因涉及接触状态的改变而成为一个复杂的非线性问题。
传统的齿轮理论分析是建立在弹性力学基础上的, 对于齿轮的接触强度计算均以两平行圆柱体对压的赫兹公式为基础,在计算过程中存在许多假设,不能准确反映齿轮啮合过程中的应力以及应变分布与变化。
相对于理论分析,有限元法则具有直观、准确、快速方便等优点。
齿廓曲面是渐开线曲面,所以建模的难点和关键在于如何确定精确的渐开线。
通过PDL命令流直接在ANSYS中创建标准直齿圆柱齿轮,学习应用ANSYS软件进行零件的几何建模和网格划分,并进行静力加载和求解,对求解的结果进行查看,分析和优化。
关键词:ANSYS;有限元;齿轮;CAEGear Transmission Of Finite Element Analysis AndOptimizationAbstractANSYS is along with the rapid development of electronic computers and developed a computational mathematics, computational mechanics and engineering science, the most effective general finite element analysis software. It is hot, the fluid, structure, electromagnetic, acoustics integration in the universal finite element analysis software for commercial. Using the ANSYS finite element analysis, all kinds of machine parts, can carry out stress, strain and structural deformation, fatigue analysis of some complex system, and the simulation, the design and realization of virtual human, to save money and material. Due to its convenience, practicability and validity, ANSYS software, especially in the field of mechanical engineering has been widely used.Gear is commonly used in machinery, a part of the work in process of stress, strain and can produce deformation, so as to ensure the normal working of gear teeth and to overall analysis, ensure the stiffness and strength. This thesis of ANSYS software of gear static analysis and optimization of virtual design of gear.Gear is one of the most important parts. It has big power range, high transmission efficiency and transmission ratio correctly, long using life, etc, but from the failure parts, gear is the most vulnerable parts of the fault. According to statistics, in all kinds of mechanical failure, gear failure is accounted for 60% of the total failure. One of the broken tooth gear is one of the main reasons.Gear meshing process as a contact, because involves contact state changes a complex nonlinear problems. The traditional theory of gear analysis was based on the basis of elastic mechanics, the contact strength for gear with two parallel computation formula of the cylinder pressure, based in Hertz calculation process in many assumptions, was not accurate in reflecting gear meshing process of stress and strain distribution and change. Relative to the theoretical analysis, finite element method, the principle is convenient and fast accurate, etc. Involute tooth profile surface is curved, so the difficulties and modeling key lies in how to determine the precise involute. Through PDL coupler, single mode WDMS directly in order to create ANSYS flow standard spur gears, study on parts of ANSYS software, and the meshing geometric modeling and static load and the solving of solving the check, analysis and optimization.Key words: ANSYS; Finite element; Gear; CAE目录1 绪论.................................................................................................................................... - 1 -1.1有限元概述................................................................................................................................. - 1 -1.2选题背景..................................................................................................................................... - 3 -1.3 本文主要工作............................................................................................................................ - 3 -2 ANSYS准备工作................................................................................................................. - 4 -2.1 ANSYS安装与启动..................................................................................................................... - 4 -2.1.1 许可证服务器安装........................................................................................................ - 4 -2.1.2 主程序安装.................................................................................................................... - 5 -2.1.3 启动许可证服务器........................................................................................................ - 7 -2.1.4 ANSYS启动与配置......................................................................................................... - 8 -2.2 设置工作目录.......................................................................................................................... - 10 -2.3 指定作业名与分析标题.......................................................................................................... - 10 -2.3.1 指定作业名.................................................................................................................. - 10 -2.3.2 指定分析标题...............................................................................................................- 11 -2.4 定义图形界面过滤参数...................................................................................................- 11 -2.5 ANSYS单位制................................................................................................................... - 12 -2.6 选取和定义单元.............................................................................................................. - 13 -3 在ANSYS中建立齿轮分析模型...................................................................................... - 15 -3.1 几何模型的建立...................................................................................................................... - 15 -3.1.1 大小齿轮的具体基本参数和尺寸 .............................................................................. - 15 -3.1.2 渐开线的生成原理...................................................................................................... - 16 -3.1.3 创建渐开线曲线.......................................................................................................... - 16 -3.1.4 生成齿根过渡曲线...................................................................................................... - 18 -3.1.5 生成完整齿廓线.......................................................................................................... - 18 -3.1.6 生成完整齿轮的面...................................................................................................... - 19 -3.1.7 生成大齿轮.................................................................................................................. - 20 -3.1.8 生成两齿轮的啮合图.................................................................................................. - 22 -3.2 几何模型的网格划分.............................................................................................................. - 22 -3.2.1 定义单元属性.............................................................................................................. - 23 -3.2.2 定义网格生成控制并生成网格 .................................................................................. - 24 -4 ANSYS静力加载与静力求解........................................................................................... - 27 -4.1创建接触对............................................................................................................................... - 27 -4.2 ANSYS施加边界条件和加载................................................................................................... - 29 -4.3 ANSYS求解............................................................................................................................... - 31 -5 求解结果的分析和优化.................................................................................................. - 32 -5.1 求解结果查看.......................................................................................................................... - 32 -5.2 结果分析及结论...................................................................................................................... - 34 -5.3 对齿轮的优化.......................................................................................................................... - 35 -6 全文总结与展望.............................................................................................................. - 36 -6.1 全文总结.................................................................................................................................. - 36 -6.2 工作展望.................................................................................................................................. - 36 - 参考文献.............................................................................................................................. - 37 -附录...................................................................................................................................... - 38 - 致谢.................................................................................................................................... - 47 -绪论1 绪论1.1有限元概述有限元是随着电子计算机的发展而迅速发展起来的一种现代计算方法。
齿轮有限元分析
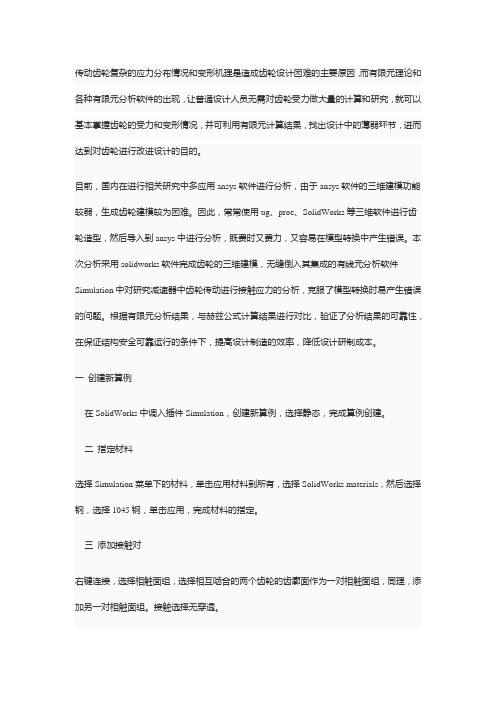
传动齿轮复杂的应力分布情况和变形机理是造成齿轮设计困难的主要原因,而有限元理论和各种有限元分析软件的出现,让普通设计人员无需对齿轮受力做大量的计算和研究,就可以基本掌握齿轮的受力和变形情况,并可利用有限元计算结果,找出设计中的薄弱环节,进而达到对齿轮进行改进设计的目的。
目前,国内在进行相关研究中多应用ansys软件进行分析,由于ansys软件的三维建模功能较弱,生成齿轮建模较为困难。
因此,常常使用ug、proe、SolidWorks等三维软件进行齿轮造型,然后导入到ansys中进行分析,既费时又费力,又容易在模型转换中产生错误。
本次分析采用solidworks软件完成齿轮的三维建模,无缝倒入其集成的有线元分析软件Simulation中对研究减速器中齿轮传动进行接触应力的分析,克服了模型转换时易产生错误的问题。
根据有限元分析结果,与赫兹公式计算结果进行对比,验证了分析结果的可靠性,在保证结构安全可靠运行的条件下,提高设计制造的效率,降低设计研制成本。
一创建新算例在SolidWorks中调入插件Simulation,创建新算例,选择静态,完成算例创建。
二指定材料选择Simulation菜单下的材料,单击应用材料到所有,选择SolidWorks materials,然后选择钢,选择1045钢,单击应用,完成材料的指定。
三添加接触对右键连接,选择相触面组,选择相互啮合的两个齿轮的齿廓面作为一对相触面组,同理,添加另一对相触面组。
接触选择无穿透。
四添加夹具为了完成一个静态算例,模型必须被正确的进行约束,使之无法移动。
在Simulation study 树中,右键单击夹具,并选择固定几何体,将中间齿轮固定。
同样,对高速小轴的轴向、径向移动进行约束,使其只有绕齿轮回转中心轴的转动自由度。
五施加外载荷对小齿轮施加扭矩,选择小齿轮的基准轴,面选择为齿轮的齿廓面上,扭矩载荷大小为25.53Nm六划分网格划分网格时采用网格控制,将啮合处的齿廓细化网格,其余的为默认设置。
齿轮参数化建模及啮合齿轮的有限元分析_解洪江

Z1
Z2
m(mm)
F(N)
α(°)
20
30
2.75
4500
20
图 5 啮合齿模型 图 6 导入 ANSYS 后模型
2.3 啮合齿轮有限元分析过程 2.3.1 定义材料属性 其弹性模量和泊松比分别为 E=2×1011N/m2 及 μ=0.3。 材 料 为 A5 钢 , 可 查 出 其 密 度 为 7800kg/m3。按照要求给出输入以上数据。 2.3.2 网格划分 选用分析精度较高的 PLANE183 单元对两齿 轮进行网格划分;同时,选用 TARGE169 和 CON- TA172 作为接触单元,建立齿对间的接触关系。将 传递的扭矩作用在小齿轮上,约束小齿轮的径向 位移以及大动轮的周向转动和径向移动自由度, 以限制齿轮副的刚体位移,调整初始位置使齿轮 恰好接触。为了使分析更精确,需要对接触区域的 网格进行细化, 网格细化后的实体模型接触部分 局部显示如图 7 所示。
10 技术纵横
轻型汽车技术 2012(11/12)总 279/280
导设置面面接触,程序自动选择面上的目标单元 为 TARGE 170 单元类型,TARGE 170 表示 “目 标”表面,目标表面离散成为一系列目标层单元 (TARGE 170),并通过共享实常数与相关的接触面 配对,对于柔性目标,这些单元覆盖于变形体边界 的实体单元上;程序自动选择接触面上的接触单 元为 CONTA 174 单元类型,此单元位于三维实体 的表面,并与其依附的实体单元有相同的几何特 性,当单元表面穿透指定目标表面上的目标单元 (TARGE170)时,接触状态开始。
1.2.2 建立参数方程 选择 fog 按钮,分别建立 x 与 y 关于参数 t 的 函数,即: x=rb*sin(t*PI*1rad)-rb*r*PI*cos(t*PI*1rad) y=rb*cos(t*PI*1rad)-rb*r*PI*sin(t*PI*1rad) 所建立的齿轮参数和 x、y 函数都可以在结构 树上看出,如图 2 所示。
齿轮系统的有限元分析

西京学院毕业设计(论文)题目:齿轮系统的有限元分析系(院): 机电工程系专业: 数控技术班级: 数控0902姓名: 方荣稳学号: 05指导老师: 李少海日期: 2011年11月摘要齿轮啮合过程作为一种接触行为, 因涉及接触状态的改变而成为一个复杂的非线性问题。
传统的齿轮理论分析是建立在弹性力学基础上的, 对于齿轮的接触强度计算均以两平行圆柱体对压的赫兹公式为基础,在计算过程中存在许多假设,不能准确反映齿轮啮合过程中的应力以及应变分布与变化。
相对于理论分析,有限元法则具有直观、准确、快速方便等优点。
本论文对齿轮系统同利用有限元法进行实验分析实现对齿轮的有限元模态分析。
利用有限元理论和数值分析方法, 对齿轮系统在加载和离心力共同作用下的变形和强度进行了分析, 研究了离心力对该系统的影响和动态响应。
利用三维啮合弹塑性接触有限元方法对齿轮进行了接触强度分析, 并基于热弹耦合进行了轮齿的修形计算, 得到轮齿的理想修形曲线, 为齿轮动态设计提供了一种非常有效的方法。
将齿轮系统划分为传统系统和结构系统两部分, 通过轴承把两者耦合起来。
采用有限元方法, 建立了实际单级齿轮减速器的有限元动力学模型, 在工作站上用I- DEA S 软件研究了该齿轮系统的固有特性, 所得结果既后映了系统的动力学性能, 又为齿轮系统的动态响应计算和分析奠定了基础。
关键词:齿轮;有限元法; 模态分析;接触; 修形;目录第一章绪论 (3)有限元的概念 (3)概述 (4)第二章齿轮系统有限元模型的建立 (6)第三章 I2DEA S 固有特性的计算方法 (8)第四章齿轮系统有限元模态分析结果 (10)结论 (12)致谢 (14)参考文献 (15)第一章绪论有限元的概念有限元分析(FEA,Finite Element Analysis)的基本概念是用较简单的问题代替复杂问题后再求解。
它将求解域看成是由许多称为有限元的小的互连子域组成,对每一单元假定一个合适的(较简单的)近似解,然后推导求解这个域总的满足条件(如结构的平衡条件),从而得到问题的解。
齿轮-轴系耦合系统振动特性有限元分析

( . c o l f Meh nc lEn i ern 1 S h o c a ia g n e i g,Lio i gS i u n v r i o a n n h h a U ie st y,Fu h nL a nn 1 0 1 P. C ia; s u i o ig 1 3 0 , R. h n
关 键 词 : 齿轮 ~ 轴 系耦 合 系统 ; 齿轮 啮 合 ; 动 力 学设 计 ; 有 限 元 法 中 图分 类 号 :TH1 2 4 .1 3 文献标识码 : A d i1 . 6 6 j i n 1 7 — 6 5 . 0 0 0 . 0 o :0 3 9 /.s . 6 2 9 2 2 1 . 2 0 5 s
第3 卷第 2 0 期
21 0 0年 6川
辽
宁
石
汕
化
J 二
火
学
学
报
Vo1 .30
NO.2
J ) RNAI ) AA( NI (U ( F I ) NG HI S HU A UNI VERS Y 1 r
JI . 2 1 D 0 L 0
文 章 编 号 : 6 2 9 2 2 l ) 2 0 1 — 0 1 7 ~6 5 ( O O O — 0 5 4
曲模 态 和 弯扭 耦 合 模 态 进行 了对 比 分 析 , 析 了啮 合 刚度 对耦 合 转 子 临 界 转 速 的影 响 。 在 此 基 础 上 , 未 耦 合 和 耦 分 对 合 齿轮 系统进 行 了不 平 衡 响 应研 究 。 研 究 结 果 为 齿 轮 一 轴 系耦 合 系统 的动 力 学设 计 提 供 了一 定 的 理 论 参 考 。
Fi ie Elm e n l ss o i a i n Cha a t rs i s n t e ntA a y i fV br to r c e itc
齿轮动态啮合有限元分析

齿轮动态啮合有限元分析作者:陕西法士特齿轮有限公司孙春艳郭君宝齿轮传动是机械传动中最重要、应用最广泛的一种传动。
通常齿轮安装于轴上并通过键连接,转矩从驱动轴经键、齿轮体和轮齿最终传递到从动轮的齿轮。
在这一过程中,齿轮承受应力作用。
另外,为了润滑齿轮传动与减少齿轮传动时产生的热量,通常在齿轮轮体上开设润滑油孔(图1)。
油孔的开设位置将影响齿轮的应力及其分布,进而影响齿轮疲劳寿命。
图1中的齿轮A在实际使用过程中,经常发生油孔附近轮齿断裂的现象。
本文的目的在于计算齿轮动态啮合过程的应力分布,得到齿轮轮齿根部应力及接触应力的分布情况,从而为齿轮的结构优化提供理论依据。
传动齿轮在工作中速度高,所受载荷大,引起的应力情况复杂。
传统的齿轮强度分析是建立在经验公式基础上的,其局限性和不确定性日益突出。
有限元方法在齿轮仿真分析中的应用,提高了齿轮设计计算精度。
目前,轮齿接触有限元分析多建立在静力分析基础上,未考虑动力因素的影响。
而在齿轮轮齿啮合过程中,动力因素对轮齿的受力和变形状态会产生较大的影响,尤其在轮齿啮入和啮出时,由于轮齿受力变形,会产生较大的啮合冲击。
本文应用参数化方法首先建立齿轮轮齿的精确几何模型,然后采用动力接触有限元方法,对齿轮轮齿啮合过程中的应力变化情况进行仿真分析,得到轮齿应力在啮合过程中随时间的变化情况。
本文主要针对图1中的齿轮A和与其配对齿轮在运转过程中的应力变化情况进行有限元分析。
其主要参数为:主动齿轮齿数20,从动齿轮齿数19,模数4.5,压力角为20°,齿宽为23mm,从动齿轮上所受扭矩为400N·m。
如图2 所示,首先利用Pro/ENGINEER软件建立四齿对啮合的齿轮轮齿几何模型。
这是因为,对于重合度大于1的齿轮副,需要考虑几对轮齿同时啮合的情况,建立多对轮齿的几何模型,在此基础上划分有限元网格,如图3所示。
由于轮齿接触区域很小,需要对接触齿面的有限元网格加密。
直齿轮啮合疲劳强度的有限元仿真与失效分析_程文冬
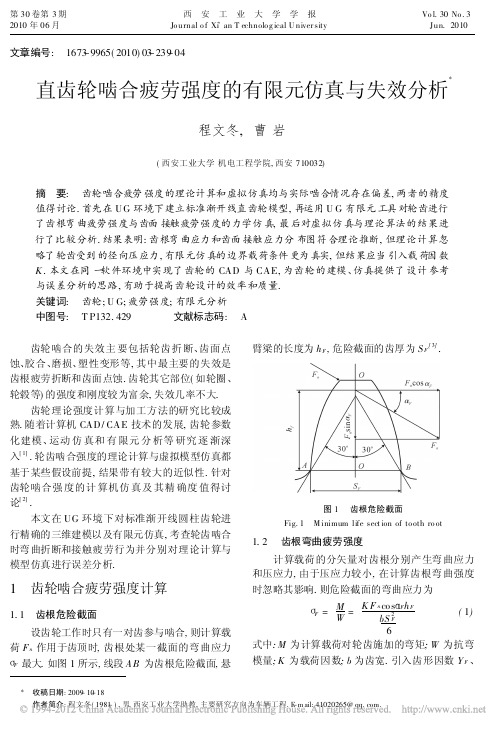
文章编号:1673-9965(2010)03-239-04直齿轮啮合疲劳强度的有限元仿真与失效分析*程文冬,曹岩(西安工业大学机电工程学院,西安710032)摘要:齿轮啮合疲劳强度的理论计算和虚拟仿真均与实际啮合情况存在偏差,两者的精度值得讨论.首先在UG环境下建立标准渐开线直齿轮模型,再运用U G有限元工具对轮齿进行了齿根弯曲疲劳强度与齿面接触疲劳强度的力学仿真,最后对虚拟仿真与理论算法的结果进行了比较分析.结果表明:齿根弯曲应力和齿面接触应力分布图符合理论推断,但理论计算忽略了轮齿受到的径向压应力,有限元仿真的边界载荷条件更为真实,但结果应当引入载荷因数K.本文在同一软件环境中实现了齿轮的CAD与CAE,为齿轮的建模、仿真提供了设计参考与误差分析的思路,有助于提高齿轮设计的效率和质量.关键词:齿轮;U G;疲劳强度;有限元分析中图号:T P132.429文献标志码:A齿轮啮合的失效主要包括轮齿折断、齿面点蚀、胶合、磨损、塑性变形等,其中最主要的失效是齿根疲劳折断和齿面点蚀.齿轮其它部位(如轮圈、轮毂等)的强度和刚度较为富余,失效几率不大.齿轮理论强度计算与加工方法的研究比较成熟.随着计算机CAD/CAE技术的发展,齿轮参数化建模、运动仿真和有限元分析等研究逐渐深入[1].轮齿啮合强度的理论计算与虚拟模型仿真都基于某些假设前提,结果带有较大的近似性.针对齿轮啮合强度的计算机仿真及其精确度值得讨论[2].本文在UG环境下对标准渐开线圆柱齿轮进行精确的三维建模以及有限元仿真,考查轮齿啮合时弯曲折断和接触疲劳行为并分别对理论计算与模型仿真进行误差分析.1齿轮啮合疲劳强度计算1.1齿根危险截面设齿轮工作时只有一对齿参与啮合,则计算载荷F n作用于齿顶时,齿根处某一截面的弯曲应力R F最大.如图1所示,线段AB为齿根危险截面,悬臂梁的长度为h F,危险截面的齿厚为S F[3].图1齿根危险截面Fig.1M inimum life sect ion of to oth ro ot1.2齿根弯曲疲劳强度计算载荷的分矢量对齿根分别产生弯曲应力和压应力,由于压应力较小,在计算齿根弯曲强度时忽略其影响.则危险截面的弯曲应力为R F=MW=K F n co s A F h FbS2F6(1)式中:M为计算载荷对轮齿施加的弯矩;W为抗弯模量;K为载荷因数;b为齿宽.引入齿形因数Y F、第30卷第3期西安工业大学学报Vo l.30No.3 2010年06月Jo urnal o f Xi.an T echnolo g ical U niver sity Jun.2010*收稿日期:2009-10-18作者简介:程文冬(1981-),男,西安工业大学助教,主要研究方向为车辆工程.E-m ail:41020265@.传递转矩T1、齿轮模数m、齿数z1和传动比i,得到轮齿弯曲强度校核公式为R F=2K T1Y Fbm2z1[[R F](2) 1.3齿面接触疲劳强度齿面最大接触应力可以通过近似的齿面法向力进行求解.以齿面靠近分度圆处的接触应力为计算依据.对于标准钢制外啮合齿轮,齿面接触强度校核公式为R F=670(i+1)K Tibm2z21[[R H](3) 2CA D模型以某机床渐开线圆柱直齿轮为研究对象.其材料为40Cr调质钢,传动比i=3.6,模数m=3,齿数z1=50,理论传递转矩T=320N#m,载荷因数K=1.5,齿形因数Y F=2.57,许用弯曲应力[R F]= 185MPa,齿轮组许用接触应力[R H]=491MPa.将齿轮参数代入式(2)、(3),得到齿根弯曲应力与齿面接触应力的理论数值:R F1=60.2MPa[[R F](4)R H1=367.3M Pa[[R H](5)齿轮三维模型创建的关键步骤是渐开线齿廓的生成.笛卡尔直角坐标系中的渐开线方程为x t=r b[cos(s)+rad(s)sin(s)]y t=r b[sin(s)-rad(s)co s(s)]z t=0(6)根据式(4),在UG表达式模块(Ex pression)中编译渐开线表达式如下:a=0;b=180;r b=m*z*cos(20)/2s=(1-t)*a+t*b;t=0x t=r b*sin(s)-r b*s*3.14/180*cos(s)y t=r b*cos(s)-r b*s*3.14/180*sin(s)(7)式中:r b是基圆半径;t为系统变量,取值范围0~1.运用U G规律曲线功能(Law Curve)生成渐开线,建立齿轮基圆、齿根圆、齿顶圆与分度圆,如图2所示.其中,齿根的过渡曲线对齿根弯曲强度影响很大.设齿轮的齿根过渡圆角半径r=1.5m m.最终的齿轮模型如图3所示,齿轮主要参数见表1.表1齿轮主要参数T ab.1Gear par amet er主要参数模数m齿数z1齿宽b/mm分度圆直径d/mm齿高h/mm压力角A 取值350901506.7520b图2渐开线齿廓F ig.2Involut e t ooth pro file图3齿轮模型F ig.3Gear model轮齿的精确建模满足了理论强度计算中齿宽b、齿形因数Y F等几何参数条件,为啮合强度仿真的准确性提供了前提保证.3U G有限元分析[4]通常,建立精确的三维模型与有限元分析分别在不同的软件中完成的.本文在UG-CAD模块中准确建立了三维模型并导入UG-Structure模块中进行有限元分析.利用U G有限元分析(简称U G-FEA)工具可将三维模型直接转化为有限元分析对象而不丢失特征参数,其技术流程如图4所示.图4U G-F EA的技术流程Fig.4K no wledg e flo w o f U G-F EA3.1前置处理1)模型简化.由于标准齿轮啮合传动的连续240西安工业大学学报第30卷性,轮齿载荷的作用力、弯矩等具有重复性,模型可进行简化,提取一个轮齿进行疲劳强度分析.2)网格划分.考虑齿型的复杂程度、精度要求以及求解时间等实际因素,运用MSC 网格生成器对轮齿划分了3D 四节点四面体单元网格.根据受力特点对啮合齿面和齿根部位进行网格细化,结果如图5所示.单元尺寸为1.4mm,共划分节点(nodes)3538个,单元(elements)8460个,网格控制角最小为20b ,最大150b.图5 简化的有限元模型与网格划分F ig.5 Simplified model fo r F EA and g r id meshing3)边界条件.根据啮合力学的矢量关系,进行齿根弯曲强度仿真时齿顶水平分力F n 1=3866.3N,竖直分力F n 2=1802.9N.渐开线曲面的法向载荷决定着齿面接触强度,其中分度圆曲面法向载荷F n =4266N.模型轮心剖切内表面为固定约束.4)材料属性.U G -FEA 内嵌了常用工程材料数据库,用户可以指定分析对象的材料属性.40Cr 调质钢的泊松比为0.28,弹性模量E =206GPa,密度为7.82@106kg/m m 3,布氏硬度为260H BS.3.2 分析求解UG -FEA 模块为配备了四种求解器:结构F.P.E 、Nastran 、AN SYS 和ABAQUS.本文选取结构F.P.E 结算器进行分析运算.分析输出结果中包含了静力分析的多种物理量,如:位移、应力、应变、外施载荷等.选择Vo n-Mises 第四强度理论准则进行应力分析,得到轮齿的等单元轮廓边齿根弯曲应力图和齿面接触应力图,分别如图6~7所示.3.3 比较讨论依据仿真结果得到齿根最大弯曲应力R F 2=66.5M Pa,齿面最大接触应力R H 2=313.6M Pa.齿轮根部受到的弯曲应力最大,最大弯曲应力节点图6 轮齿弯曲应力分布云图Fig.6 N ephog ram o f too th bending st ress图7 齿面接触应力云图Fig.7 N epho gr am of too th sur face str essID 为2737,节点位于图1中理论AB 线下侧0.22mm 处,误差为3.2%.齿面接触应力分布形状为近似矩形,表示齿面易发生疲劳点蚀的分布区域.仿真结果小于材料许用应力值,符合齿轮工作强度需求.仿真的最大弯曲应力与接触应力R F 2、R H 2相对理论计算值R F 2、R H 1的误差分别10.5%与-14.6%.误差分析如下:1)UG -FEA 外施载荷的设定综合了弯曲应力和纵向压应力,符合实际载荷条件.理论计算未考虑外施载荷的纵向压应力,导致弯曲应力计算结果小于仿真值.2)齿面接触强度与齿根弯曲强度仿真未考虑啮合不平稳时冲击载荷的影响.理论计算与计算机仿真均忽略了轮齿渐开线曲面的切向摩擦力[5-6].3)划分网格时应用少量的网格单元数量满足分析精度的要求.精确的网格能够使得仿真结果无限逼近实际情况,运算速度与解算精度是对立统一的矛盾关系.4 结论本文通过理论计算和有限元仿真两种方法研241第3期 程文冬等:直齿轮啮合疲劳强度的有限元仿真与失效分析究了轮齿啮合的疲劳强度,结论如下:1)文中在UG-CAD模块中准确建立了三维模型并导入UG-Structure模块中进行有限元分析.在同一软件环境中实现了CAD与CAE的结合,设计效率较高,仿真精度可靠.2)齿根弯曲强度与齿面接触强度的计算值分别为60.2M Pa和367.3M Pa,仿真结果分别为66.5M Pa和313.6M Pa.各项结果均满足许用强度要求,仿真应力分布符合理论推断,亦符合实际失效情形.3)啮合强度的理论计算忽略了外施载荷径向压应力作用,导致弯曲应力计算结果偏小.有限元仿真的边界条件更接近于实际载荷,但仿真中未考虑工作不平稳的冲击作用,应在仿真结果中引入载荷因数K.4)CAD-CAE的有机结合,实现了产品的精确建模与有限元仿真,产品结构尺寸与力学性能可以得到合理的分析与评估,有助于迅速、准确的实现产品的优化设计.参考文献:[1]孙贤初,党新安.CA D/CA E软件在齿轮结构分析中的联合应用[J].拖拉机与农用运输车,2008,35(3):77.SU N Xian-chu,DA NG Xin-an.CA D/CA E Softw are in Gear M echanical A naly sis[J].T racto r&F armT ranspo rter,2008,35(3):77.(in Chinese)[2]胡爱萍,刘善淑,陈权.标准直齿圆柱齿轮传动接触强度计算的研究[J].机械设计.2008,25(11):45.H U A-i ping,LIU Shan-shu,CH EN Q uan.Study o nthe Co ntact St reng th Calculation of Standard Cylin-drical Spur Gear T ransmission[J].Jo ur nal of M achine Desig n,2008,25(11):45.(in Chinese)[3]马保吉,朱育权,王丽君.机械设计基础[M].西安:西北工业大学出版社,2005.M A Bao-ji,ZH U Yu-quan,W AN G L-i jun.Basics ofM echanical Desig n[M].Xi.an:No rthw ester n Po ly-technical U niver sity P ress,2005.[4]马秋成,韩利芬,罗益宁,等.U G CA E篇[M].北京:机械工业出版社,2002.M A Q iu-cheng,H AN L-i fen,L U O Y-i ning,et al.U G-CA E[M].Beijing:M echanica l Industr y Pr ess,2002.(in Chinese)[5]M ao K.Gear T o oth Co ntact A nalysis and It s A pplica-tio n in the Reduction o f Fatig ue Wear[J].Wear,2007,262(11/12):1281.[6]D ing H,K ahr aman A.Inter act ions Between No nlinearSpur Gear Dynamics and Surface Wear[J].Journal ofSo und and Vibr atio n,2007,307(3/4/5):662.Simulation Study of Meshing FatigueStrength of Involute Cylinder GearCH EN G Wen-dong,CAO Yan(Schoo l o f M echatr onic Eng ineering,X i.an T echno lo gical U niver sity,Xi.an710032,China)Abstract:T here are tw o metho ds to obtain the result of g ear fatig ue streng th:theo retical calculatio n and CAE simulation.Ther e w ill be som e error betw een the result and the actuality.Fir st,the normal invo lute cy linder gear m odel w as built in the UG environment,the gear too th contact fatig ue and bending streng th simulation w as then im plemented.At last the simulation result w as compar ed w ith the theoretical calculation r esult.T he co mparison sho wed that:both theor etical calculation and structural analysis results w as satisfied to the requirement o f adm issible stress.T he radial compressiv e stress influence to the bending str ength w as not considered in the theo retical calculation and the load factor K should co nsider into the sim ulation result.The co mbinatio n o f CAD and CA E w as achieved in one softw ar e background.This paper,w hich is a reference to the gear modeling and simulation as w ell as the er ror analysis,could make a useful effort to increase the efficiency and quality of pr oduct.Key words:g ear;U G;fatigue strength;finite element analysis(责任编辑、校对魏明明) 242西安工业大学学报第30卷。
- 1、下载文档前请自行甄别文档内容的完整性,平台不提供额外的编辑、内容补充、找答案等附加服务。
- 2、"仅部分预览"的文档,不可在线预览部分如存在完整性等问题,可反馈申请退款(可完整预览的文档不适用该条件!)。
- 3、如文档侵犯您的权益,请联系客服反馈,我们会尽快为您处理(人工客服工作时间:9:00-18:30)。
图4.2划分网格后的齿轮面
5
利用ansys中的接触向导创建接触对,选择主菜单中的Preprocessor>Modeling>Cr
eat>Contact Pair命令,弹出Contact Manager对话框,如图5.1所示。
图5.1接触管理对话框
创建步骤如下:
(1)单击对话框中的“ ”创建接触向导(Contact Wizard)按钮,弹出接触向导的对话框,如图5.2所示。
齿轮是最重要的零件之一。它具有功率范围大,传动效率高,传动比正确,使用寿命长等特点,但从零件失效的情况来看,齿轮也是最容易出故障的零件之一。据统计,在各种机械故障中,齿轮失效就占故障总数的60%以上。其中轮齿的折断又是齿轮失效的主要原因之一。
齿轮啮合过程作为一种接触行为,因涉及接触状态的改变而成为一个复杂的非线性问题。传统的齿轮理论分析是建立在弹性力学基础上的,对于齿轮的接触强度计算均以两平行圆柱体对压的赫兹公式为基础,在计算过程中存在许多假设,不能准确反映齿轮啮合过程中的应力以及应变分布与变化。相对于理论分析,有限元法则具有直观、准确、快速方便等优点。
图3.2单元类型库对话框
(2)选择完毕单击【OK】按钮,如果确定了当前选择后还想继续添加单元类型,单击【Apply】按钮。将返回到如图3.3所示的ElementTypes对话框。
(3)如果想改变单元的其他输入选项单击【Options…】按钮。出现如图3.14所示的element type options(单元类型选项)对话框。
图6.1施加边界条件拾取对话框图6.2约束选择
图6.3施加载荷拾取对话框图6.4施加载荷
图6.5施加边界条件和载荷的小齿轮图6.6施加边界条件和载荷的大小齿轮
6.2ANASYS求解
在求解前先对求解控制进行设置单击Preprocessor>Solution>Analysis Type>Sol’n Control出现如图6.7所示的对话框,并按图6.7中的设置进行设置。完成设置后单击OK推出设置。
关键词:有限元法;齿轮;啮合
Abstract
With the development of computer,ANSYS has became one ofthemost effective general-purpose finite element analysis softwarein calculation mathematics, computational mechanics and computational engineering sciences.It isone of the large general-purpose commercial finite element analysis softwarewhich isthe integration of structural, thermal, fluid, electromagnetic, acoustic.By this method,we can make the stress,strain,deformation and fatigue analysis to various mechanical parts、components.Additionally ,it isalsocan be used to make the simulation of certain complex system,to achieve a virtual design with the significant saving in manpower,financial and material.Because of its convenience, practicality and effectiveness,ANSYS software has been widely usedinvarious fields, especially mechanical engineering.
导入anasys中如图2.1所示:
图2.1
3
3.1定义单元属性
定义材料属性中弹性模量206Gpa,泊松比PRXY:0.3,密度为:7.82×103kg/m3,在本文的讨论的问题中,摩擦因数Mu=0.3。具体的操作如下:
3.1.1定义网格单元
单击Main>Preprocessor>Element Type>Add Edit/Delete弹出单元类型选择对话框如图3.1所示,单击Add选择PLANE42,SOLID45。
图3.1
(1)单击【Add】按钮。弹出Library ofElement Types(单元类型库)对话框,如图3.2所示。在图中左边的列表框中选择欲添加的单元类别(有梁、管,壳,实体等),此处选择Solid(实体)类别,然后在右边的列表框中选择具体的单元类型,此处选择四节点四边形单元,Quad 4node 42。
图3.6
图3.7
4
在本论文中,不要求得到很精确的应力值,主要得到相应的应力危险点以及该结构的动力响应过程,因此网格不用划分得很细,在满足求解条件下,可以尽量地减少网格以减少规模。
单击Main>Preprocessor>Meshing>MeshTool弹出如图4.1所示对话框。选中Smart Size 8自由划分网格,单击Mesh出现拾取对话框,拾取大小齿轮处于同向的一面,划分结果如图4.2所示。
图6.7求解控制设置
再单击Main Menu> Preprocessor>Solution>Solve>Current LS出现如图6.8的信息提示框,单击Ok开始求解。当出现“Solution is done”,求解完成。
图6.8信息提示框
7
7.1求解结果的查看
(1)变形图:单击MainMenu>Preprocessor>General Postproc>Plot Results>Deformed Shape,弹出Plot Deformed Shape对话框,选择Def+undf edge,如图7.1,单击OK,变形图如图7.2。
(5)在该对话框中,在Target Surface下选择Areas,单击Pick Contact…按钮,弹出图形拾取对话框,用鼠标在大齿轮上选择接触面。然后单击OK按钮。
(6)单击对话框中的Next按钮,进入接触设置对话框,如图5.4所示。
(7)单击对话框中的Optional settings…按钮,弹出的设置对话框如图5.5所示。
图7.1Plot Deformed Shape对话框
图7.2变形图
(2)节点位移图:
单击MainMenu>Preprocessor>General Postproc>Plot Results>Contour Plot>Nodal Solu,弹出Contour Nodal Solution Data对话框,如图7.3所示。选择DOFSolution/Displacement vector sum,单击OK,节点位移云图如图7.4所示。
(4)确定后单击【OK】按钮,返回到如图3.4所示的对话框后单击【Close】按钮,结束单元类型的添加。
图3.3添加单元类型对话框
图3.4单元类型选项对话框
3.2定义材料属性
单击Main>Preprocessor>Material Props>Material Models弹出定义材料属性对话框如图3.6所示,填入EX:2.06e11、PRXY:0.3,在Structural下单击Friction Coefficient弹出如图3.7所示对话框,填入Mu:0.3,至此材料属性定义完成,下一步进入网格划分。
(2)在对话框Target Type栏中选择Flexible如图5.2所示。
(3)选择目标面,在Target Surface下选择Areas,单击Pick Target…弹出拾取对话框。通过鼠标在大齿轮上选择目标面,然后单击OK按钮。
(4)单击向导对话框中的Next按钮,进入下一步,拾取接触面如图5.3所示。
(8)完成设置,单击对话框中的OK按钮,回到接触向导对话框。
(9)单击对话框中的Create按钮,完成接触向导,创建好一个接触对,并出现如图5.6的信息提示,如果接触对正确单击Finish完成见图5.7所示。
图5.2接触向导图
5.3拾取接触面对话框
齿廓曲面是渐开线曲面,所以建模的难点和关键在于如何确定精确的渐开线。本文先在proe中建立标准直齿圆柱齿轮的三维模型,然后导入ANSYS中,应用ANSYS软件进行网格划分,并进行静力加载和求解,对求解的结果进行查看,分析和优化。
2
鉴于anasys的三维建模能力一般,本文通过在proe中建立标准直齿圆柱齿轮的三维模型,保存副本为PARASOLID(*x_t)格式,然后在anasys中导入:file>import>PARA,
图5.4设置接触参数图5.5设置接触对属性对话框
图5.6提示对话框
图5.7三个接触对
回到接触管理对话框,可以看到所创建的所有接触对,如图5.8所示。
图5.8所创建的接触对
在完成接触对创建后,还可以通过在接触管理对话框中选择该接触对,并单击属性按钮“ ”进入接触属性修改对话框修改其属性,在这里重点介绍下对接触属性的设置,因为接触属性设置的正确与否直接影响到求解的收敛与正确,对三个接触对的接触属性的设置见图5.9。
图5.9对接触属性的设置
选择拉格朗日法的原因是拉格朗日法容易得到良性条件,对接触刚度的敏感性较小。也可以通过设置实常数和关键字来实现,打开CONTA174 element type options菜单如图5.10设置这三个接触对的关键字。
图5.10对关键字的设置
6
6.1边界条件定义