去毛刺作业指导书
去毛刺作业指导书
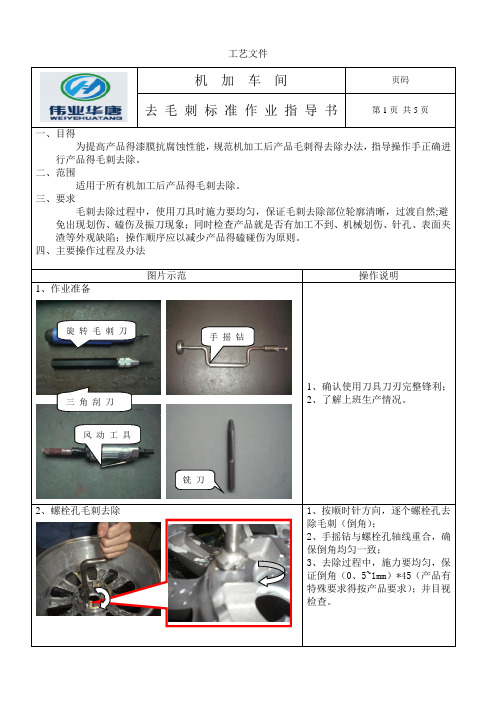
工艺文件
机 加 车 间
页码 去 毛 刺 标 准 作 业 指 导 书
第1页 共5页
一、目得
为提高产品得漆膜抗腐蚀性能,规范机加工后产品毛刺得去除办法,指导操作手正确进行产品得毛刺去除。
二、范围
适用于所有机加工后产品得毛刺去除。
三、要求
毛刺去除过程中,使用刀具时施力要均匀,保证毛刺去除部位轮廓清晰,过渡自然;避免出现划伤、磕伤及振刀现象;同时检查产品就是否有加工不到、机械划伤、针孔、表面夹渣等外观缺陷;操作顺序应以减少产品得磕碰伤为原则。
四、主要操作过程及办法
图片示范
操作说明
1、作业准备
1、确认使用刀具刀刃完整锋利;
2、了解上班生产情况。
2、螺栓孔毛刺去除
1、按顺时针方向,逐个螺栓孔去除毛刺(倒角);
2、手摇钻与螺栓孔轴线重合,确保倒角均匀一致;
3、去除过程中,施力要均匀,保证倒角(0、5~1mm )*45(产品有特殊要求得按产品要求);并目视检查。
旋 转 毛 刺 刀
三 角 刮 刀
手 摇 钻
风 动 工 具
铣 刀
1 2 2)划窝产品背面毛刺去除
3)背面铸窝毛刺去除
4)气门孔沉孔毛刺去除
5、帽口接刀处毛刺去除
6、帽槽毛刺去除
8、正面轮辐毛刺去除
9、窗口毛刺去除1)用风动铣刀铣削窗口
12、正面精车产品正面凹槽毛刺去除
13、正面精车产品螺栓孔沉孔边缘。
去毛刺作业指导书
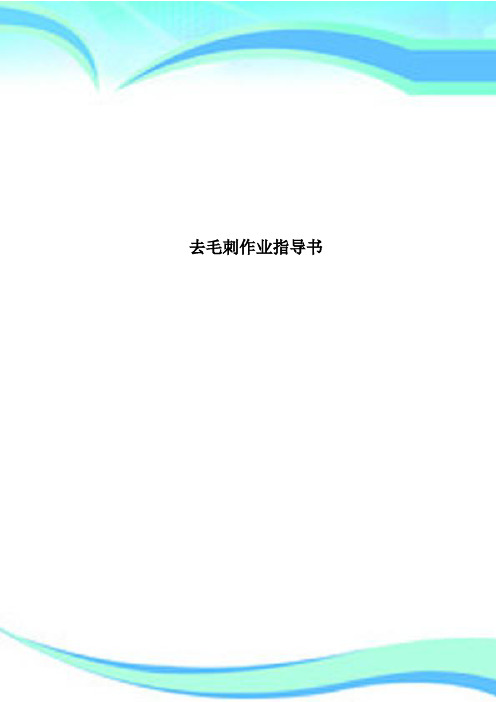
2、了解上班生产情况。
2、螺栓孔毛刺去除
1、按顺时针方向,逐个螺栓孔去除毛刺(倒角);
2、手摇钻与螺栓孔轴线重合,确保倒角均匀一致;
3、去除过程中,施力要均匀,保证倒角(0.5~1mm)*45(产品有特殊要求的按产品要求);并目视检查。
工艺文件
3.气门孔毛刺去除——1)不划窝产品背面毛刺去除
2)用风动砂纸棒对窗口铣削线进行打磨
1、产品窗口铣削合格后,用
风动砂纸棒对窗口铣削线进
行打磨;
2、每个窗口,沿铣削表面打
磨2~3周,打磨方向须与工具
旋转方向相反;
2、操作过程中,要求持稳工
具、施力均匀、动作熟练,不
能损伤窗口周围表面;
3、操作后,目视检查各拐角、
夹角部位的打磨质量。
注:1、砂纸棒使用P150#砂
1、检查气门孔正面毛刺去除
质量;
2、左手托二道轮缘,右手持
三角刮刀,以气门孔逆时针方
向第一根轮辐开始,按逆时针
方向逐个清除轮辐正面毛刺;
3、刀具与加工面夹角控制在
20~30度之间,要求去除过
程排屑均匀连续;
4、过程中避免划伤产品表面,
棱边不能崩漆,过渡要圆滑无
尖角。
注:精车产品去毛刺时,操作
者持刀手不可以带手套且双
背面划窝产生的毛刺,并用
P240#砂纸打磨,保证毛刺去
除干净。
3)背面铸窝毛刺去除
气门孔背面有铸窝的产品,用旋转毛刺刀或三角刮刀清除铸窝周边毛刺,并用P240#砂纸打磨一遍,保证过渡圆滑无尖角。
4)气门孔沉孔毛刺去除
1、将产品平放在工作台上,
左手把住外轮缘,右手用旋转毛刺刀或三角刮刀清除气门孔沉孔周边毛刺,确保去除后轮廓线均匀一致;
去毛刺作业指导书范本
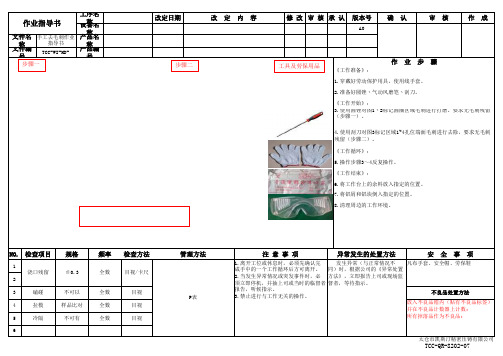
作业指导书工序名称改定日期改 定 内 容修 改设备名称审 核承 认版本号确 认审 核作 成A0文件名称手工去毛刺作业指导书产品名称文件编号TCC-WI-MD-产品编号3.使用圆锉对图1丶2标记圆圈区域毛刺进行打磨。
要求无毛刺残留(步骤一)。
《工作循环》:5.操作步骤3~4反复操作。
《工作结束》:作 业 步 骤《工作准备》:1.穿戴好劳动保护用具,使用线手套。
2.准备好圆锉丶气动风磨笔丶刮刀。
《工作开始》:6.将工作台上的余料放入指定的位置。
7.将铝屑和铝块倒入指定的位置。
8.清理周边的工作环境。
NO.检查项目规格频率检查方法管理方法注 意 事 项异常发生的处置方法安 全 事 项1浇口残留≦0.3全数目视/卡尺P表凡布手套、安全帽、劳保鞋23磕碰不可以全数目视不良品处置方法样品比对全数目视放入不良品箱内(贴有不良品标签)并在不良品计数器上计数;所有掉落品作为不良品;5冷隔不可有全数1.离开工位或休息时,必须先确认完成手中的一个工作循环后方可离开。
2.当发生异常情况或突发事件时,必须立即停机,并抽上司或当时的临督者报告,听候指示。
3.禁止进行与工作无关的操作。
发生异常(与正常情况不同)时,根据公司的《异常处置方法》,立即报告上司或现场监督者,等待指示。
太仓市凯斯汀精密压铸有限公司4.使用刮刀对图3标记区域1~4孔位端面毛刺进行去除,要求无毛刺残留(步骤二)。
目视64拉模工具及劳保用品步骤二步骤一TCC-QR-8202-07。
去毛刺作业指导书

客户名称
产品名称
产品图号
工艺流程 一、工序内容 序 号
1ห้องสมุดไป่ตู้
作业步骤及要点
去毛刺作业指导书
版本
物料编码
模腔数量 设备编号
三、作业视图
工艺装备
标准工时/ 件
版本号:A-0 ;表单编号:XX-QP07-QR-39
工装编号 产品重量 每小时产能 原材料
g
件
2
3
4
5
6
产品按图示要求摆放,盖确认章后转入下道工序 。
二、控制重点
序 号
检测项目
质量要求
检测方 法
检测频率
记录
1
2
3
4
5
6
说 1、符号标识:关键◆ 重要◇ 记录※ 不记录×
明 2、反应计划:停止生产→标识 → 隔离 →上报组长 → 调整
四、产品视图 责任人
编制(日期)
五、摆放视图 审核(日期)
批准(日期)
去毛刺作业指导书

去毛刺作业指导书
1
工艺文件
机 加 车 间
页码 去 毛 刺 标 准 作 业 指 导 书
第1页 共5页
一、目的
为提高产品的漆膜抗腐蚀性能,规范机加工后产品毛刺的去除办法,指导操作手正确进行产品的毛刺去除。
二、范围
适用于所有机加工后产品的毛刺去除。
三、要求
毛刺去除过程中,使用刀具时施力要均匀,保证毛刺去除部位轮廓清晰,过渡自然;避免出现划伤、磕伤及振刀现象;同时检查产品是否有加工不到、机械划伤、针孔、表面夹渣等外观缺陷;操作顺序应以减少产品的磕碰伤为原则。
四、主要操作过程及办法
图片示范
操作说明
1、作业准备
1、确认使用刀具刀刃完整锋利;
2、了解上班生产情况。
2、螺栓孔毛刺去除
1、按顺时针方向,逐个螺栓孔去除毛刺(倒角);
2、手摇钻与螺栓孔轴线重合,确保倒角均匀一致;
3、去除过程中,施力要均匀,保证倒角(0.5~1mm )*45(产品有特殊要求的按产品要求);并目视检查。
旋 转 毛 刺 刀
三 角 刮 刀
手 摇 钻
风 动 工 具
铣 刀
1 2 2)划窝产品背面毛刺去除
3)背面铸窝毛刺去除
4. 背腔法兰盘及轮辐减重窝毛刺去除
5. 帽口接刀处毛刺去除
7. 螺栓孔沉孔毛刺去除
8. 正面轮辐毛刺去除。
去毛刺作业指导书知识分享
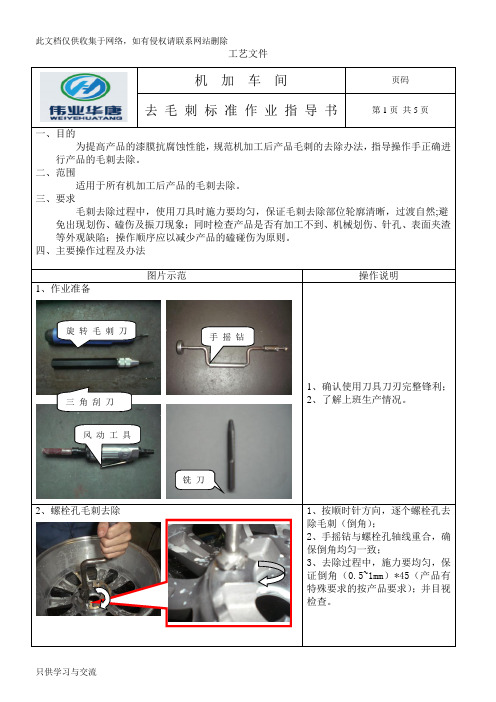
工艺文件
机 加 车 间
页码 去 毛 刺 标 准 作 业 指 导 书
第1页 共5页
一、目的
为提高产品的漆膜抗腐蚀性能,规范机加工后产品毛刺的去除办法,指导操作手正确进行产品的毛刺去除。
二、范围
适用于所有机加工后产品的毛刺去除。
三、要求
毛刺去除过程中,使用刀具时施力要均匀,保证毛刺去除部位轮廓清晰,过渡自然;避免出现划伤、磕伤及振刀现象;同时检查产品是否有加工不到、机械划伤、针孔、表面夹渣等外观缺陷;操作顺序应以减少产品的磕碰伤为原则。
四、主要操作过程及办法
图片示范
操作说明
1、作业准备
1、确认使用刀具刀刃完整锋利;
2、了解上班生产情况。
2、螺栓孔毛刺去除
1、按顺时针方向,逐个螺栓孔去除毛刺(倒角);
2、手摇钻与螺栓孔轴线重合,确保倒角均匀一致;
3、去除过程中,施力要均匀,保证倒角(0.5~1mm )*45(产品有特殊要求的按产品要求);并目视检查。
旋 转 毛 刺 刀
三 角 刮 刀
手 摇 钻
风 动 工 具
铣 刀
1 2 2)划窝产品背面毛刺去除
3)背面铸窝毛刺去除
4)气门孔沉孔毛刺去除
5. 帽口接刀处毛刺去除
6. 帽槽毛刺去除
8. 正面轮辐毛刺去除
9.窗口毛刺去除1)用风动铣刀铣削窗口
12. 正面精车产品正面凹槽毛刺去除
13. 正面精车产品螺栓孔沉孔边缘。
去毛刺作业指导书
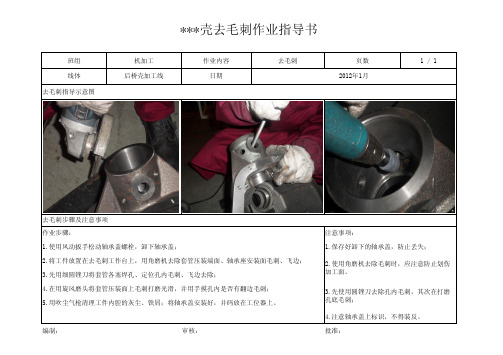
班组机加工作业内容去毛刺页数 1 / 1
线体
后桥壳加工线日期编制:审核:批准:***壳去毛刺作业指导书
去毛刺步骤及注意事项
2012年1月去毛刺指导示意图1.使用风动扳手松动轴承盖螺栓,卸下轴承盖;
2.使用角磨机去除毛刺时,应注意防止划伤加工面。
3.先使用圆锉刀去除孔内毛刺,其次在打磨孔底毛刺;
注意事项:1.保存好卸下的轴承盖,防止丢失;作业步骤:
4.注意轴承盖上标识,不得装反。
2.将工件放置在去毛刺工作台上,用角磨机去除套管压装端面、轴承座安装面毛刺、飞边;
3.先用细圆锉刀将套管各塞焊孔、定位孔内毛刺、飞边去除;
4.在用旋风磨头将套管压装面上毛刺打磨光滑,并用手摸孔内是否有翻边毛刺;
5.用吹尘气枪清理工件内腔的灰尘、铁屑;将轴承盖安装好,并码放在工位器上。
齿轮泵泵体去毛刺作业指导书

操作要领
合格标准目测,边缘无明显大毛刺
目测如果有明显大毛
刺,先用锉刀轻挫边缘
操作
要领
用抛光轮打磨泵体的顶
面
合格
标准
目测,手指抚摸泵体边缘和密
封圈槽,平滑无突起
类型泵体页数1/3
操作要领用抛光轮打磨两侧进出
油口法兰面
操作
要领
将泵体翻面,用抛光轮打
磨泵体底面(如果是两开
泵,此道工序省略)
合格标准目测,手指抚摸泵体侧面油
口,平滑无突起
合格
标准
目测,手指抚摸泵体底面边缘
和密封圈槽,平滑无突起
类型泵体页数2/3
类型泵体页数3/3
合格标准目测,手指抚摸泵体油口内
侧,平滑无突起
合格
标准
目测,无残留碎屑
操作要领用刮刀轻刮泵体进出油
口的内侧毛刺
操作
要领
用气枪将螺栓孔中的碎
屑吹干净。
去毛刺作业指导书(一)2024

去毛刺作业指导书(一)引言概述:去毛刺是一项重要的作业,它能够消除产品表面的毛刺,提高产品的质量和外观。
本文将介绍去毛刺作业的指导步骤和注意事项,帮助操作人员正确进行去毛刺作业,并确保成品的优质。
正文内容:1. 准备工作- 检查毛刺区域:仔细检查产品表面的毛刺,确保标记清晰。
- 准备工具和材料:准备去毛刺所需的工具和材料,如砂纸、砂轮、研磨机等。
- 安全措施:佩戴个人防护装备,如手套、护目镜和口罩,确保操作人员的安全。
2. 毛刺去除步骤- 粗磨:使用砂轮或砂纸对毛刺部位进行粗磨,将明显突出的毛刺磨平。
- 细磨:使用细砂纸或研磨机对粗磨后的部位进行细磨,使表面更加光滑。
- 对比检查:磨磨细磨后,用手轻轻触摸表面,与其他无毛刺区域进行对比,检查是否还有残留毛刺。
- 重新处理:如发现残留毛刺,重复进行粗磨和细磨的步骤,直至完全去除毛刺。
- 清洁表面:用清洁布或刷子清洁表面,确保去除磨剂和杂质。
3. 注意事项- 定期检查工具磨损情况:及时更换磨损严重的砂纸、砂轮等工具,以保证去毛刺效果。
- 控制磨削力度:不可用过大的力度进行磨削,以免损坏产品表面。
- 注意磨削位置:确保只磨削毛刺区域,避免磨损其他无毛刺的表面。
- 避免过度磨削:在去毛刺过程中,适时停止磨削,以免磨损产品。
- 清理作业区域:进行去毛刺作业后,及时清理作业区域,防止残留的研磨粉末造成二次污染。
4. 产品质量检验- 视觉检查:对去毛刺后的产品进行视觉检查,确保表面光滑无毛刺。
- 用手触摸检查:用手轻轻触摸产品表面,检查是否仍有毛刺残留。
- 用量规检测:使用量规对产品尺寸进行检测,确保去毛刺过程中未造成尺寸变化。
5. 总结去毛刺作业是一项重要的工艺,通过准备工作、正确的磨削步骤和注意事项的遵守,能够有效地去除产品表面的毛刺。
正确进行去毛刺作业,不仅能提高产品质量,还能提升产品外观。
操作人员在进行去毛刺作业时,务必遵守安全规定,并定期检查工具的磨损情况。
齿轮泵后盖的去毛刺作业指导书
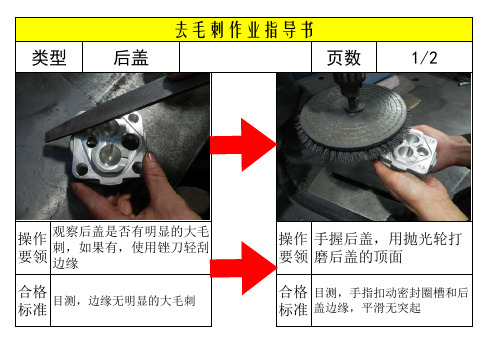
合格 目测,手指抚摸进出油口边 标准 缘,平滑无突起
操作 用气枪将空中产生的碎 要领 屑吹干净
合格 标准
目测,无残留Βιβλιοθήκη 屑去毛刺作业指导书类型 后盖
页数
1/2
操作 要领
观察后盖是否有明显的大毛 刺,如果有,使用锉刀轻刮 边缘
合格 标准
目测,边缘无明显的大毛刺
操作 手握后盖,用抛光轮打 要领 磨后盖的顶面
合格 目测,手指扣动密封圈槽和后 标准 盖边缘,平滑无突起
去毛刺作业指导书
类型 后盖
页数
2/2
操作 要领
将后盖翻面,用抛光轮打磨 后盖的进出油口(侧进出后 盖省略此步)
去毛刺作业指导书

去毛刺作业指导书
一、介绍
去毛刺是一种常见的表面处理方法,用于去除材料表面的毛刺或瑕疵。
它可以改善材料的质量和外观,并提高其使用性能。
本作业指导书将为您介绍去毛刺的基本原理和操作方法。
二、去毛刺原理
去毛刺的原理是利用机械或化学方法去除材料表面的毛刺。
机械方法包括打磨、研磨和抛光,通过磨削和研磨的力量去除表面的毛刺或瑕疵。
化学方法则使用腐蚀剂或溶剂,通过溶解或转化表面的毛刺来实现去毛刺的效果。
三、去毛刺工具和材料
去毛刺所需的工具和材料有:
1. 手工磨具:如砂纸、打磨布等;
2. 机械磨具:如砂轮、切割机等;
3. 清洁剂:如酒精、去油剂等;
4. 防护用品:如手套、护目镜等。
四、去毛刺步骤
1. 准备工作:在进行去毛刺之前,首先要确保工作区域整洁,
且具备良好的通风条件。
同时,戴上防护手套和护目镜,以保护好
自己的安全。
2. 检查材料表面:仔细检查材料表面是否存在毛刺或瑕疵,并
确定需要去除的部位。
3. 选择合适的工具和材料:根据材料的类型和需要去除的毛刺
程度,选择合适的手工磨具或机械磨具。
同时,准备好清洁剂用于
清洁材料表面。
4. 进行去毛刺操作:根据选择的工具和材料,按照操作说明进
行去毛刺。
在手工磨具时,注意使用适当的力度和角度进行磨削。
在机械磨具时,注意调整转速和磨具的角度。
5. 清洁材料表面:在去毛刺完成后,使用清洁剂清洗材料表面,以去除残留的磨削或研磨剂。
去毛刺作业指导书(二)2024

去毛刺作业指导书(二)引言概述:本文档是去毛刺作业的指导书(二),旨在帮助员工更好地完成去毛刺任务。
去毛刺是一项细致而重要的工作,对于提高产品质量和美观度至关重要。
本指导书将详细介绍去毛刺作业的步骤和注意事项,以确保任务的顺利完成。
第一部分:准备工作1. 准备合适的工具和装备:a. 去毛刺刀:选择适当刀头材质和刀身长度,确保能够在不损坏产品的情况下去除毛刺。
b. 个人保护装备:佩戴耳塞、护目镜、手套等必要的个人保护装备,确保工作时的安全。
c. 清洁工具:准备清洁布、刷子或压缩气罐等工具,用于清理去毛刺时产生的碎片和粉尘。
2. 确定去毛刺的方式:a. 手工去毛刺:适用于小尺寸或复杂形状的产品,需使用去毛刺刀进行精确操作。
b. 机械去毛刺:适用于大规模生产的产品,可使用机器进行去毛刺加工,提高效率。
第二部分:去毛刺操作步骤1. 检查产品表面:a. 仔细观察产品表面,寻找可能存在的毛刺和瑕疵。
b. 使用触摸或视觉检测方法,确保产品表面的光滑度和质量。
2. 去除毛刺:a. 对于手工去毛刺,使用去毛刺刀轻轻拖曳在产品表面,去除毛刺。
b. 对于机械去毛刺,将产品放置在机器上,按照设定好的程序进行去毛刺操作。
3. 清洁表面:a. 使用清洁布或刷子清理产品表面,去除去毛刺时产生的碎片和粉尘。
b. 可使用压缩气罐将产品表面吹洗,确保产品表面的清洁度。
第三部分:注意事项1. 注意安全:a. 使用去毛刺刀时,要小心操作,避免刀尖划伤人体。
b. 戴上护目镜,防止去毛刺时产生的碎片击中眼睛。
2. 记录问题和改进:a. 发现产品表面的毛刺或其他质量问题时,及时记录并上报。
b. 对去毛刺过程中出现的问题进行总结和改进,不断提高去毛刺的效率和质量。
3. 维护工具:a. 定期检查和保养去毛刺刀,保持刀刃的锋利度和刀身的整洁。
b. 清洗和储存清洁工具,确保下次使用时的清洁度和完好性。
第四部分:工作环境整理1. 清理工作区域:a. 去除去毛刺时产生的碎片和粉尘。
去毛刺及刷板工艺指导书.doc
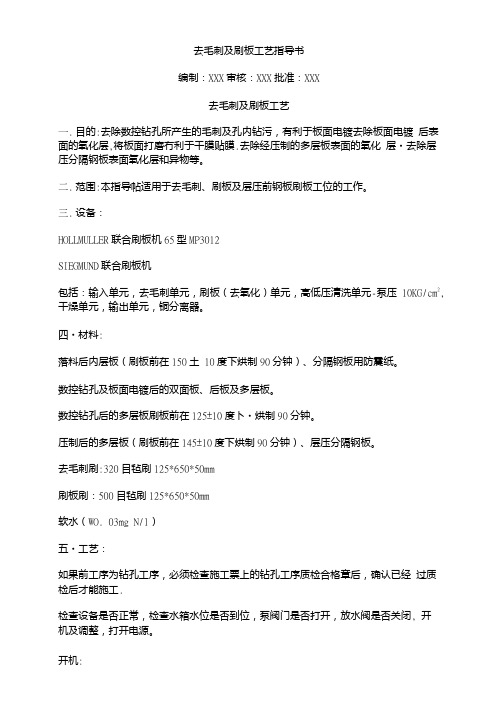
去毛刺及刷板工艺指导书编制:XXX审核:XXX批准:XXX去毛刺及刷板工艺一.目的:去除数控钻孔所产生的毛刺及孔内钻污,有利于板面电镀去除板面电镀后表面的氧化层,将板面打磨冇利于干膜贴膜.去除经压制的多层板表面的氧化层•去除层压分隔钢板表面氧化层和异物等。
二.范围:本指导帖适用于去毛刺、刷板及层压前钢板刷板工位的工作。
三.设备:HOLLMULLER联合刷板机65型MP3012SIEGMUND联合刷板机包括:输入单元,去毛刺单元,刷板(去氧化)单元,高低压清洗单元-泵压 10KG/cm2,干燥单元,输出单元,铜分离器。
四•材料:落料后内层板(刷板前在150土 10度下烘制90分钟)、分隔钢板用防震纸。
数控钻孔及板面电镀后的双面板、后板及多层板。
数控钻孔后的多层板刷板前在125±10度卜•烘制90分钟。
压制后的多层板(刷板前在145±10度下烘制90分钟)、层压分隔钢板。
去毛刺刷:320目毡刷125*650*50mm刷板刷:500目毡刷125*650*50mm软水(WO. 03mg N/l)五•工艺:如果前工序为钻孔工序,必须检查施工票上的钻孔工序质检合格章后,确认已经过质检后才能施工.检查设备是否正常,检查水箱水位是否到位,泵阀门是否打开,放水阀是否关闭, 开机及调整,打开电源。
开机:按顺序开启刷板机,输送马达,振动器,高压泵及干燥器•当工作结束后,关机顺序与开机正好相反.调整:整个刷板机冇两组刷轮,即去毛刺用的粗刷轮和刷板用的细刷轮。
对丁粗刷轮调整,我们使用三组按钮,面板上中间的按钮用來调整压辘与水平抛轮的距离,即线路板厚度,该厚度在数码显示屏上显示,精度为0・1毫米。
在调整中注意距离调节,下限不得超过0.2毫米,上限不得超过5毫米,以防超过记数范围,造成实际距离与显示距离不符。
左右两组按钮用来调节压力•显示屏上的显示灯,表示抛轮所受的压力值0%-90%o开关向上拨至A,为压力自动调节,开关向下拨至0,为手动调节。
【精品文档】去毛刺作业指导书-范文word版 (3页)
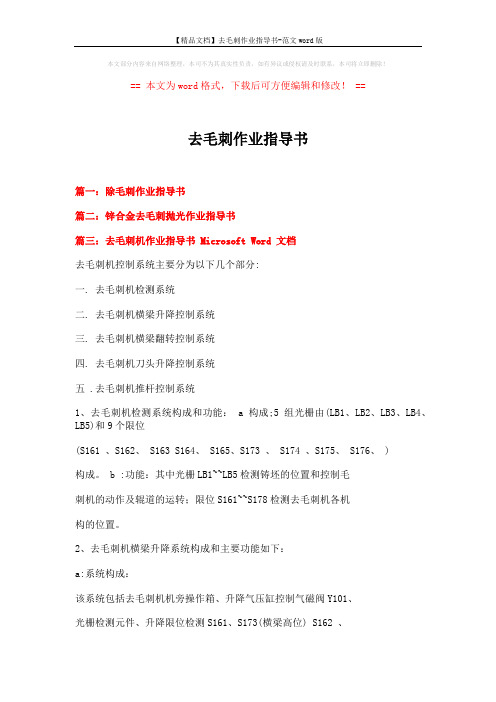
本文部分内容来自网络整理,本司不为其真实性负责,如有异议或侵权请及时联系,本司将立即删除!== 本文为word格式,下载后可方便编辑和修改! ==去毛刺作业指导书篇一:除毛刺作业指导书篇二:锌合金去毛刺抛光作业指导书篇三:去毛刺机作业指导书 Microsoft Word 文档去毛刺机控制系统主要分为以下几个部分:一. 去毛刺机检测系统二. 去毛刺机横梁升降控制系统三. 去毛刺机横梁翻转控制系统四. 去毛刺机刀头升降控制系统五 .去毛刺机推杆控制系统1、去毛刺机检测系统构成和功能: a 构成;5组光栅由(LB1、LB2、LB3、LB4、LB5)和9个限位(S161 、S162、 S163 S164、 S165、S173 、 S174 、S175、 S176、 )构成。
b :功能:其中光栅LB1~~LB5检测铸坯的位置和控制毛刺机的动作及辊道的运转;限位S161~~S178检测去毛刺机各机构的位置。
2、去毛刺机横梁升降系统构成和主要功能如下:a:系统构成:该系统包括去毛刺机机旁操作箱、升降气压缸控制气磁阀Y101、光栅检测元件、升降限位检测S161、S173(横梁高位) S162 、S174(横梁低位)b.主要控制功能:当铸坯挡住1# 、2#、3#光栅,检测铸坯的位置并控制升降气磁阀Y101动作。
使横梁上升到高位S161、S173信号到,气动阀 Y101失电。
3、去毛刺机横梁翻转控制系统的系统构成和主要功能如下: a、系统构成:包括气动阀Y103、 Y104,限位S162(工作位)、S161(清洗位)、光栅。
b.主要控制功能:当去毛刺结束气动阀Y104得电动作横梁翻转到清洗位S164清洗毛刺,由清洗位信号S163后气动阀Y103得电动作横梁翻转到工作位。
4. 去毛刺机刀头升降控制系统的构成和功能:a. 系统构成:包括气动阀Y102b. 主要功能:当铸坯档住1#、2#、3# 、4#光栅时气动阀Y102得电,刀头上升;当铸坯离开4#、3#、2#光栅时,横梁到清洗位气动阀Y102失电动作,刀头下降。
去毛刺文档

客户
产品名称产品图号制定日期图示说明:二、注意事项
三、使用工具
图三
余姚市光立车件有限公司
1.作业五金件产品必须佩戴手套(手指套)
2.所有产品必须全数逐一检验去除毛刺,确保无毛刺残留。
3.去除毛刺作业过程不可伤及产品,不可刮伤、划伤
图一图二核准: 审核: 拟定: 作业指导书-去毛刺
之残留的痕迹。
4.手工去除毛刺品经研磨全数检验,出货产品不可有任何
残留毛刺之不良。
一、作业步骤
1.左手带上手套(或手指套),把五金件拿在手上(如
图)。
2.右手拿上刀具、刀头插入¢4的横孔外(内)转一圈(视
图),使孔角毛刺去尽。
旋转式手工毛刺刀。
修毛刺作业指导书
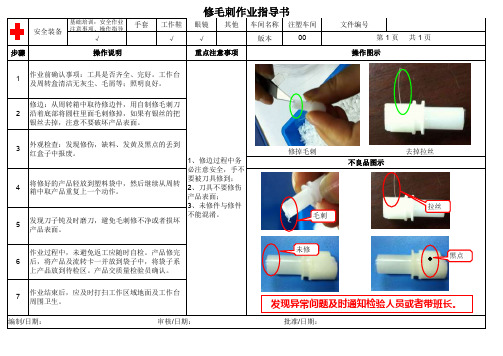
基础培训:安全作业注意事项、操作指导
手套工作鞋眼镜其他车间名称注塑车间文件编号
√√
√
版本
00
步骤
1
2
修掉毛刺
去掉拉丝
4
5
6
编制/日期:审核/日期:
批准/日期:
将修好的产品轻放到塑料袋中,然后继续从周转箱中取产品重复上一个动作。
发现刀子钝及时磨刀,避免毛刺修不净或者损坏产品表面。
安全装备
第 1 页 共 1 页
操作说明
重点注意事项
操作图示
3
外观检查:发现修伤,缺料、发黄及黑点的丢到红盒子中报废。
不良品图示
7
作业结束后,应及时打扫工作区域地面及工作台周围卫生。
1、修边过程中务必注意安全,手不要被刀具修到;
2、刀具不要修伤产品表面;
3、未修件与修件不能混淆。
作业前确认事项:工具是否齐全、完好。
工作台及周转盒清洁无灰尘、毛屑等;照明良好。
修边:从周转箱中取待修边件,用自制修毛刺刀沿着底部将圆柱里面毛刺修掉,如果有银丝的把银丝去掉,注意不要破坏产品表面。
作业过程中,未避免返工应随时自检。
产品修完后,将产品及流转卡一并放到袋子中,将袋子系上产品放到待检区。
产品交质量检验员确认。
毛刺
拉丝
未修
黑点
发现异常问题及时通知检验人员或者带班长。
毛刺整修作业指导书
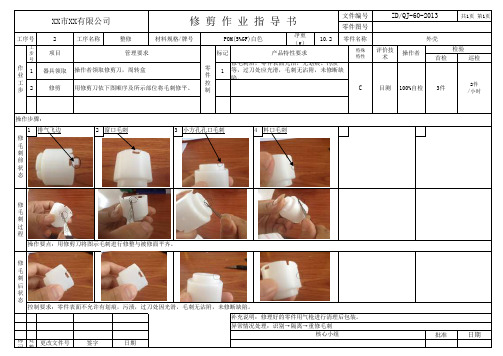
共1页 第1页
2净重(g)10.2
首检
巡检
1器具领取1
2
修剪
1234
批准日期
标记处数更改文件号
日期
控制要求:零件表面不允许有划痕,污渍,过刀处因光滑,毛刺无沾附,未修断缺陷。
修毛刺后状态
C 100%自检3件
2件/小时
修毛刺过程
操作要点:用修剪刀将图示毛刺进行修整与被修面平齐。
作业工步
检验特殊特性
评价技术操作者
目测窗口毛刺
排气飞边
项目工序名称
整修材料规格/牌号
料口毛刺
小方孔孔口毛刺
零件控制
操作者领取修剪刀,周转盒
用修剪刀依下图顺序及所示部位将毛刺修平。
签字
补充说明:修理好的零件用气枪进行清理后包装。
异常情况处理:识别→隔离→重修毛刺
核心小组
修毛刺前状态
产品特性要求
修毛刺后,零件表面光洁,无划痕、污渍等,过刀处应光滑,毛刺无沾附,未修断缺陷。
管理要求
操作步骤:
标记工步号
外壳
零件名称
修 剪 作 业 指 导 书
XX市XX有限公司
ZD/QJ-60-2013
文件编号零件图号
工序号
POM(5%GF)白色。
去毛刺作业规程
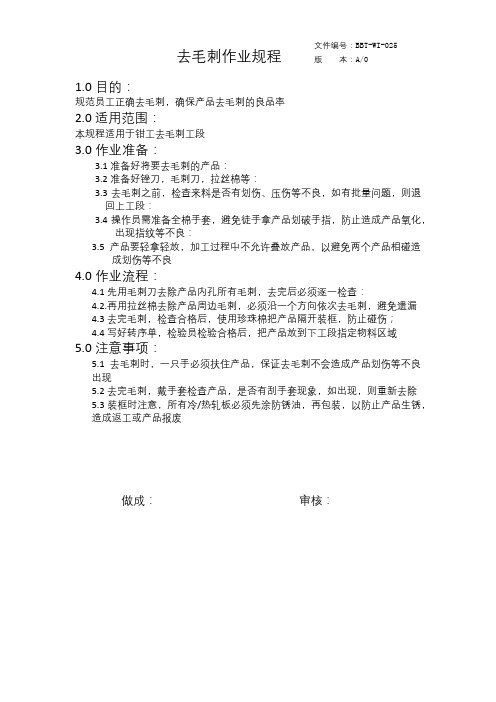
去毛刺作业规程文件编号:BBT-WI-025
版本:A/0
1.0目的:
规范员工正确去毛刺,确保产品去毛刺的良品率
2.0 适用范围:
本规程适用于钳工去毛刺工段
3.0作业准备:
3.1准备好将要去毛刺的产品:
3.2准备好锉刀,毛刺刀,拉丝棉等:
3.3去毛刺之前,检查来料是否有划伤、压伤等不良,如有批量问题,则退
回上工段:
3.4操作员需准备全棉手套,避免徒手拿产品划破手指,防止造成产品氧化,
出现指纹等不良:
3.5产品要轻拿轻放,加工过程中不允许叠放产品,以避免两个产品相碰造
成划伤等不良
4.0作业流程:
4.1先用毛刺刀去除产品内孔所有毛刺,去完后必须逐一检查:
4.2.再用拉丝棉去除产品周边毛刺,必须沿一个方向依次去毛刺,避免遗漏
4.3去完毛刺,检查合格后,使用珍珠棉把产品隔开装框,防止碰伤;
4.4写好转序单,检验员检验合格后,把产品放到下工段指定物料区域
5.0注意事项:
5.1去毛刺时,一只手必须扶住产品,保证去毛刺不会造成产品划伤等不良
出现
5.2去完毛刺,戴手套检查产品,是否有刮手套现象,如出现,则重新去除
5.3装框时注意,所有冷/热轧板必须先涂防锈油,再包装,以防止产品生锈,
造成返工或产品报废
做成:审核:。
- 1、下载文档前请自行甄别文档内容的完整性,平台不提供额外的编辑、内容补充、找答案等附加服务。
- 2、"仅部分预览"的文档,不可在线预览部分如存在完整性等问题,可反馈申请退款(可完整预览的文档不适用该条件!)。
- 3、如文档侵犯您的权益,请联系客服反馈,我们会尽快为您处理(人工客服工作时间:9:00-18:30)。
工艺文件
第 1 页
机 加 车 间
页码
去 毛 刺 标 准 作 业 指 导 书
第 1 页 共 5 页
一、目的
为提高产品的漆膜抗腐蚀性能,规范机加工后产品毛刺的去除办法,指导操作手正确 进行产品的毛刺去除。
二、范围
适用于所有机加工后产品的毛刺去除。
三、要求
毛刺去除过程中,使用刀具时施力要均匀,保证毛刺去除部位轮廓清晰,过渡自然;避 免出现划伤、磕伤及振刀现象;同时检查产品是否有加工不到、机械划伤、针孔、表面夹 渣等外观缺陷;操作顺序应以减少产品的磕碰伤为原则。
四、主要操作过程及办法
图片示范
操作说明
1、作业准备
旋 转 毛 刺 刀
手 摇 钻
三 角 刮 刀
风 动 工 具
铣 刀
1、确认使用刀具刀刃完整锋利;
2、了解上班生产情况。
2、螺栓孔毛刺去除
1、按顺时针方向,逐个螺栓孔 去除毛刺(倒角);
2、手摇钻与螺栓孔轴线重合, 确保倒角均匀一致;
3、去除过程中,施力要均匀, 保证倒角(0.5~1mm )*45(产品 有特殊要求的按产品要求);并 目视检查。
3.气门孔毛刺去除——1)不划窝产品背面毛刺去除121、选用合适的手摇钻操作,
避免因钻头过大划伤轮辋;
2、操作时手摇钻与气门孔轴
线重合;
3、去除过程中均匀施力,确
保倒角轮廓线均匀一致,倒角
0.5mm×450(产品有特殊要求
的按产品要求);去除后用P240#砂纸打磨,保证过渡圆
滑无尖角。
2)划窝产品背面毛刺去除
1、检查气门孔是否划窝;
2、用旋转毛刺刀去除气门
孔
背面划窝产生的毛刺,并用
P240#砂纸打磨,保证毛刺
去
除干净。
3)背面铸窝毛刺去除
气门孔背面有铸窝的产品,
用旋转毛刺刀或三角刮刀清
除铸窝周边毛刺,并用
P240#砂纸打磨一遍,保证
过渡圆滑无尖角。
4)气门孔沉孔毛刺去除
1、将产品平放在工作台上,
左手把住外轮缘,右手用旋
转毛刺刀或三角刮刀清除气
门孔沉孔周边毛刺,确保去
除后轮廓线均匀一致;
2、倒角尺寸:0.5mm×45°,
无尖角现象。
4.背腔法兰盘及轮辐减重窝毛刺去除1、操作者首先确认气门孔
毛
刺去除质量,并检查气门
孔是
否划窝(需要划窝产品);
2、右手持旋转毛刺刀按顺
序
清除毛刺:每个法兰面减
重窝
→排水槽→轮辐减重窝;
3、操作过程中,毛刺去除
部
位要轮廓线均匀一致,无
尖角
现象;
4、操作完成后应再次确认
气
门孔位置(气门孔应回到
开始
位置),避免操作漏项。
5.帽口接刀处毛刺去除1、左手持产品内轮缘,右
手
持旋转毛刺刀置于帽口接
刀
处,连续逆时针转动产品2
周,清除毛刺;
2、倒角尺寸:(0.5~1.0)
mm
×45°。
注:操作过程中,应避免
划伤
帽口。
6.帽槽毛刺去除
1、左手持产品内轮缘,右
手
持旋转毛刺刀清除帽槽毛
刺;
确保去除后轮廓线均匀一
致,
无尖角现象;
2、倒角尺寸:
0.5mm×45°。
7.螺栓孔沉孔毛刺去除
1、左手持产品内轮缘,右手
持旋转毛刺刀或三角刮刀清
除螺栓孔沉孔毛刺,确保去
除
后轮廓线均匀一致。
注:不要划伤螺栓孔表面。
8.正面轮辐毛刺去除1、左手持产品内轮缘,右手
持三角刮刀,以气门孔逆时
针
方向第一根轮辐开始,按逆
时
针方向逐个清除轮辐正表面
毛刺;
2、刀具与加工面夹角控制
在
20~30度,操作过程中不能
划伤铸造表面,必要时对刀
具
进行防护;
3、去除部位要圆滑过渡,无
尖角现象。
注:正面精车产品在粗车时
正
面毛刺也应去除。
9.窗口毛刺去除1)用风动铣刀铣削窗口1、将产品斜架于工作台上,
用风动铣刀以气门孔所在窗
口开始,逆时针依次去除窗
口
周围毛刺;
2、操作过程中,要求持稳工
具、施力均匀、动作熟练,
走
刀方向须与刀具旋转方向相
反,不能损伤窗口周围表面;
3、清理标准:窗口部位要求
过渡圆滑,铣削加工线要求
均
匀一致;(轮辐背腔不加工
的
产品铣削线宽度在1~2mm之
间,加工的产品铣削线宽度
在
0.4~0.8mm之间)。
2)用风动砂纸棒对窗口铣削线进行打磨2)用风动砂纸棒对窗口铣削
线进行打磨
1、产品窗口铣削合格后,用
风动砂纸棒对窗口铣削线进
行打磨;
2、每个窗口,沿铣削表面打
磨2~3周,打磨方向须与工
具
旋转方向相反;
2、操作过程中,要求持稳工
具、施力均匀、动作熟练,
不
能损伤窗口周围表面;
3、操作后,目视检查各拐角、
夹角部位的打磨质量。
注:1、砂纸棒使用P150#砂
纸,2、直径应小于10mm。
、窗口用风动砂纸棒打磨后,、过程中避免划伤产品表面,
1
将产品竖起,用砂纸板对背 腔
窗口处残留毛刺进行清理; 2、动作要领:砂纸打磨面与 背腔打磨面平行接触,打磨 2~3 周,注意拐角处要清除 干净;
3、打磨后过渡要圆滑不许有 尖角。
注:砂纸板采用木板或竹板 做
成,厚度不要大于10mm ;用 P240#砂纸。
11.正面精车产品轮辐毛刺去除
1、检查气门孔正面毛刺去除 质量;
2、左手托二道轮缘,右手持 三角刮刀,以气门孔逆时针 方
向第一根轮辐开始,按逆时 针
方向逐个清除轮辐正面毛刺;
3、刀具与加工面夹角控制在 20~30 度之间,要求去除过 程排屑均匀连续;
4
棱边不能崩漆,过渡要圆滑 无
尖角。
注:精车产品去毛刺时,操 作
者持刀手不可以带手套且双 手不可以接触精车表面。
12.正面精车产品正面凹槽毛刺去除1、用三角刮刀清除正面凹槽
毛刺,刀具与加工面夹角控
制
在20~30度之间,要求去除
过程中排屑均匀连续;
2、过程中,避免划伤喷漆表
面,棱边不能崩漆,过渡要
圆
滑,去除后不许有尖角产生。
13.正面精车产品螺栓孔沉孔边缘毛刺去除1、用三角刮刀清除正面精车
后螺栓孔沉孔边缘毛刺;
2、过程中不能碰伤喷漆面,
要求去除过程中无停顿,保
证
毛刺去除干净,棱边不能掉
漆,去除后不许有尖角产生。