新产品型检流程及方法
成品检验流程图

成品检验流程图在生产过程中,成品检验是一个至关重要的环节。
它确保了产品的质量,并防止不合格的产品流入市场。
下面是一个成品检验流程图的示例,它概述了成品检验的主要步骤。
1、准备检验设备在开始成品检验之前,需要准备必要的检验设备,包括测量仪器、检测工具、实验室设备等。
这些设备应按照相关规定进行校准和维护,以确保其准确性和可靠性。
2、接收产品从生产线上接收待检验的产品,并将其放在指定的检验区域。
同时,应记录产品的信息,如型号、规格、批次等。
3、检查外观对产品的外观进行检查,包括是否有划痕、瑕疵、变形等问题。
同时,检查产品的完整性,确保没有明显的缺陷或损坏。
4、检查尺寸和形状使用测量仪器对产品的尺寸和形状进行检测,确保其符合设计要求和规格。
对于关键尺寸和形状,应进行详细的测量和记录。
5、检查材料质量对产品的材料质量进行检查,包括材料的硬度、韧性、耐久性等指标。
对于关键材料,应进行实验室测试和分析。
6、检查功能性能对产品的功能性能进行检查,包括开关、按钮、指示灯等部件的功能测试。
确保产品能够在正常条件下运行,并满足设计要求。
7、审核质量文件查阅产品质量文件,包括生产记录、检测报告、合格证明等。
确保产品质量符合相关标准和客户要求。
8、填写检验报告根据检验结果填写检验报告,记录产品的信息、检测数据和评价结果。
检验报告应准确、完整地反映检验过程和结果。
9、审核检验报告对检验报告进行审核,确认检验结果是否符合要求。
如有不合格的产品,应进行返工或报废处理。
10、交付合格产品将合格的产品交付给下一道工序或客户,确保产品质量符合要求并满足市场需求。
成品检验流程是产品质量控制的关键环节之一。
通过实施严格的成品检验流程,可以确保产品的质量符合标准要求,提高产品的可靠性和安全性。
及时发现并处理潜在问题,有助于降低生产成本和减少质量损失。
成品检验流程图的推广和应用有助于提高企业生产效率和产品质量水平,提升企业的市场竞争力。
在任何生产或制造过程中,原材料的检验都是至关重要的环节。
新产品试制管理规定
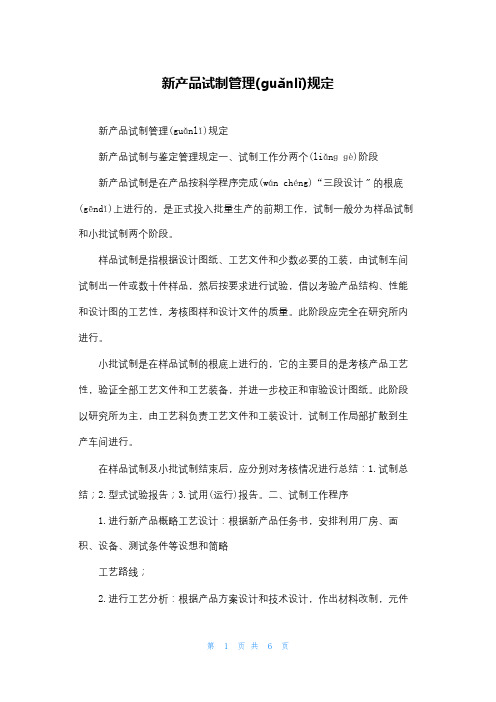
新产品试制管理(guǎnlǐ)规定新产品试制管理(guǎnlǐ)规定新产品试制与鉴定管理规定一、试制工作分两个(liǎnɡ ɡè)阶段新产品试制是在产品按科学程序完成(wán chéng)“三段设计〞的根底(gēndǐ)上进行的,是正式投入批量生产的前期工作,试制一般分为样品试制和小批试制两个阶段。
样品试制是指根据设计图纸、工艺文件和少数必要的工装,由试制车间试制出一件或数十件样品,然后按要求进行试验,借以考验产品结构、性能和设计图的工艺性,考核图样和设计文件的质量。
此阶段应完全在研究所内进行。
小批试制是在样品试制的根底上进行的,它的主要目的是考核产品工艺性,验证全部工艺文件和工艺装备,并进一步校正和审验设计图纸。
此阶段以研究所为主,由工艺科负责工艺文件和工装设计,试制工作局部扩散到生产车间进行。
在样品试制及小批试制结束后,应分别对考核情况进行总结:1.试制总结;2.型式试验报告;3.试用(运行)报告。
二、试制工作程序1.进行新产品概略工艺设计:根据新产品任务书,安排利用厂房、面积、设备、测试条件等设想和简略工艺路线;2.进行工艺分析:根据产品方案设计和技术设计,作出材料改制,元件改装,选配复杂自制件加工等项工艺分析;3.产品工作图的工艺性审查;4.编制试制用工艺卡片:(1)工艺过程卡片(路线卡);(2)关键工序卡片(工序卡);(3)装配工艺过程卡(装配卡);(4)特殊工艺、专业工艺守那么。
5.根据产品试验的需要,设计必不可少的工装,本着经济可靠,保证产品质量要求的原那么,充分利用现有工装、通用工装、组合工装、简易工装、过渡工装等。
6.制定试制用材料消耗工艺定额和加工工时定额。
7.零部件制造、总装配中应按质量保证方案,加强质量管理和信息反应,并做好试制记录,编制新产品质量保证要求和文件。
此项工作在批试阶段由全质办牵头组织工艺科、检验科进行。
8.编写试制总结:着重总结图样和设计文件验证情况,以及在装配和调试中所反映出的有关产品结构、工艺及产品性能方面的问题及其解决过程,并附上各种反映技术内容的原始记录。
江苏省新产品新技术鉴定实施细则
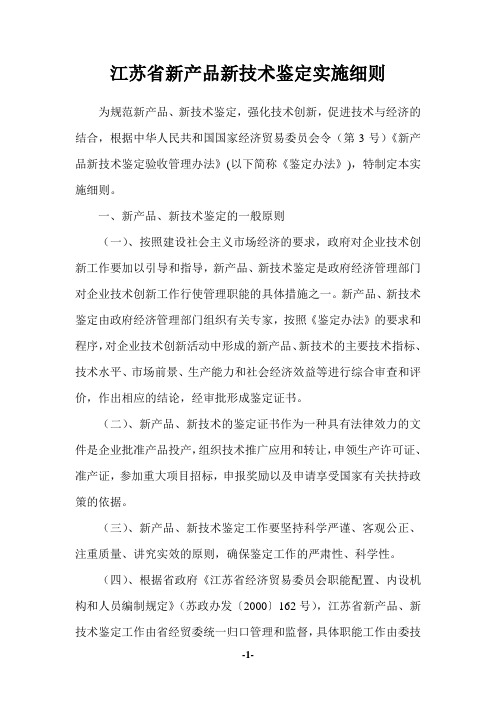
江苏省新产品新技术鉴定实施细则为规范新产品、新技术鉴定,强化技术创新,促进技术与经济的结合,根据中华人民共和国国家经济贸易委员会令(第3号)《新产品新技术鉴定验收管理办法》(以下简称《鉴定办法》),特制定本实施细则。
一、新产品、新技术鉴定的一般原则(一)、按照建设社会主义市场经济的要求,政府对企业技术创新工作要加以引导和指导,新产品、新技术鉴定是政府经济管理部门对企业技术创新工作行使管理职能的具体措施之一。
新产品、新技术鉴定由政府经济管理部门组织有关专家,按照《鉴定办法》的要求和程序,对企业技术创新活动中形成的新产品、新技术的主要技术指标、技术水平、市场前景、生产能力和社会经济效益等进行综合审查和评价,作出相应的结论,经审批形成鉴定证书。
(二)、新产品、新技术的鉴定证书作为一种具有法律效力的文件是企业批准产品投产,组织技术推广应用和转让,申领生产许可证、准产证,参加重大项目招标,申报奖励以及申请享受国家有关扶持政策的依据。
(三)、新产品、新技术鉴定工作要坚持科学严谨、客观公正、注重质量、讲究实效的原则,确保鉴定工作的严肃性、科学性。
(四)、根据省政府《江苏省经济贸易委员会职能配置、内设机构和人员编制规定》(苏政办发〔2000〕162号),江苏省新产品、新技术鉴定工作由省经贸委统一归口管理和监督,具体职能工作由委技术进步与装备处负责。
各市(含部分享有省辖市管理权限的计划单列市)经贸委(经委)归口管理各市的新产品、新技术鉴定工作。
二、鉴定类别及内容(一)、根据《鉴定办法》的规定,新产品、新技术的鉴定范围是指列入国家和省项目计划的新产品、新技术,以及企业自行开发,提出鉴定申请的重大新产品、新技术。
具体分为新产品投产鉴定、新产品样机(样品)鉴定、新技术鉴定。
(二)、上文所称的“列入国家和省项目计划的新产品、新技术”主要是指列入国家和省技术创新项目计划和新产品试产计划的新产品、新技术以及实施项目计划过程中研究开发的新产品、新技术。
产品验证标准程序
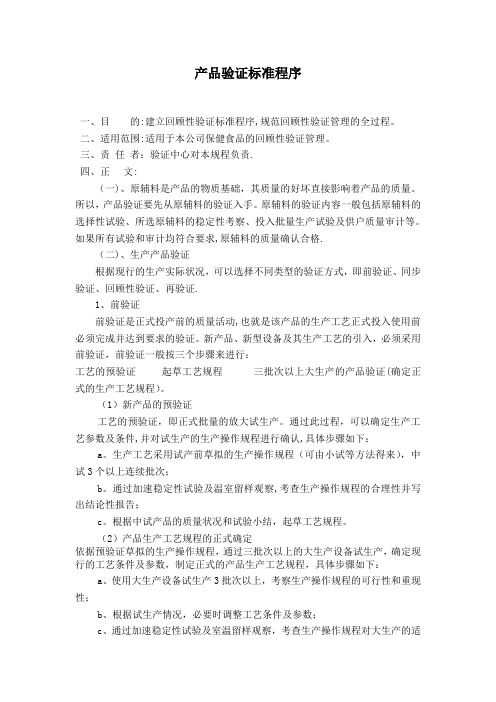
产品验证标准程序一、目的:建立回顾性验证标准程序,规范回顾性验证管理的全过程。
二、适用范围:适用于本公司保健食品的回顾性验证管理。
三、责任者:验证中心对本规程负责.四、正文:(一)、原辅料是产品的物质基础,其质量的好坏直接影响着产品的质量。
所以,产品验证要先从原辅料的验证入手。
原辅料的验证内容一般包括原辅料的选择性试验、所选原辅料的稳定性考察、投入批量生产试验及供户质量审计等。
如果所有试验和审计均符合要求,原辅料的质量确认合格.(二)、生产产品验证根据现行的生产实际状况,可以选择不同类型的验证方式,即前验证、同步验证、回顾性验证、再验证.1、前验证前验证是正式投产前的质量活动,也就是该产品的生产工艺正式投入使用前必须完成并达到要求的验证。
新产品、新型设备及其生产工艺的引入,必须采用前验证,前验证一般按三个步骤来进行:工艺的预验证起草工艺规程三批次以上大生产的产品验证(确定正式的生产工艺规程)。
(1)新产品的预验证工艺的预验证,即正式批量的放大试生产。
通过此过程,可以确定生产工艺参数及条件,并对试生产的生产操作规程进行确认,具体步骤如下:a。
生产工艺采用试产前草拟的生产操作规程(可由小试等方法得来),中试3个以上连续批次;b。
通过加速稳定性试验及温室留样观察,考查生产操作规程的合理性并写出结论性报告;c。
根据中试产品的质量状况和试验小结,起草工艺规程。
(2)产品生产工艺规程的正式确定依据预验证草拟的生产操作规程,通过三批次以上的大生产设备试生产,确定现行的工艺条件及参数,制定正式的产品生产工艺规程,具体步骤如下:a、使用大生产设备试生产3批次以上,考察生产操作规程的可行性和重现性;b、根据试生产情况,必要时调整工艺条件及参数;c、通过加速稳定性试验及室温留样观察,考查生产操作规程对大生产的适应性并写出报告;d、制定切实可行的生产操作规程,确定正式的产品生产工艺规程.(3)使用大生产设备试生产,以验证生产操作规程的可行性和重现性,应采用生产工艺的运行验证来进行。
产品质量检验程序

产品质量检验程序在生产过程中,产品质量检验是确保产品符合质量标准的重要环节。
本文将介绍产品质量检验的程序,包括质量检验的目的、流程、方法和结果评估等方面。
一、质量检验的目的质量检验的主要目的是确保产品的合格率和可靠性。
通过检验,我们可以及时发现并纠正产品制造过程中的问题,提高产品质量,满足客户的需求和期望。
同时,质量检验也可以帮助企业降低成本、增强竞争力。
二、质量检验的流程质量检验的流程一般包括取样、测试、评估和记录等步骤。
1. 取样:根据检验标准和要求,从生产线上随机选取代表性样品。
2. 测试:对取样的产品进行相关的物理、化学、机械等测试,以评估其质量和性能。
3. 评估:根据测试结果和预设的质量标准,判断产品的合格性,并记录合格或不合格的结论。
4. 记录:将检验过程中的相关数据和结果进行记录,包括样品信息、检验结果、检验员等。
三、质量检验的方法产品质量检验可以采用各种方法和工具,下面介绍两种常用的方法:1. 外观检验:通过肉眼观察产品的外观,检查是否有瑕疵、变色、变形等表面缺陷。
2. 功能性检验:根据产品的设计要求,进行相应的功能测试,如电器产品的电流、电压测试,机械产品的运转试验等。
除了以上方法,还可以根据产品的特点和要求,采用其他专业的检验方法,如X射线检测、声波检测、拉力测试等。
四、质量检验结果评估在质量检验中,根据检验结果的合格与否,可以分为合格品和不合格品。
1. 合格品:符合质量标准和要求,可以正常出货或投入市场。
2. 不合格品:不符合质量标准和要求,需要进行相应的处理,如修复、重新制造或报废等。
对于不合格品,企业需要追溯其原因,采取相应的纠正措施,确保类似问题不再发生,并承担相应的责任。
五、质量检验的重要性质量检验在产品生产中具有重要的作用:1. 保证产品质量:通过检验,可以发现和排除产品生产过程中的缺陷和问题,确保产品的质量稳定和一致性。
2. 提高客户满意度:优质的产品可以满足客户的需求和期望,提高客户对企业的信任和满意度。
产品检测流程

产品检测流程产品检测是确保产品质量和安全的重要环节,它涉及到从原材料采购到成品出厂的全过程。
一个完善的产品检测流程能够有效地保障产品的质量,避免因质量问题带来的损失和风险。
下面将介绍一种常见的产品检测流程,以供参考。
1. 制定检测计划。
首先,需要根据产品的特点和要求,制定相应的检测计划。
检测计划应包括检测的内容、标准、方法、频次等,确保全面、系统地对产品进行检测。
2. 原材料检测。
在产品生产过程中,原材料的质量直接影响着最终产品的质量。
因此,对原材料进行严格的检测是至关重要的。
原材料检测的内容包括外观、尺寸、化学成分、力学性能等。
3. 在线检测。
在产品生产的各个环节,需要进行相应的在线检测,以及时发现和解决生产过程中的质量问题。
在线检测可以通过自动化设备、传感器等实现,对产品的尺寸、外观、工艺参数等进行监测和控制。
4. 成品检测。
成品检测是产品质量的最后一道关卡,也是最为重要的一环。
成品检测的内容包括外观质量、功能性能、安全性能等。
通过对成品进行全面的检测,可以确保产品的质量达到标准要求。
5. 抽样检验。
除了对所有产品进行全面检测外,还需要进行抽样检验。
通过抽样检验,可以对产品的质量状况进行评估,及时发现和解决质量问题。
6. 数据分析和处理。
在产品检测过程中产生的大量数据需要进行分析和处理。
通过对检测数据的分析,可以了解产品质量的整体状况,及时发现问题并采取相应的改进措施。
7. 记录和归档。
对产品检测过程中的各项数据和结果进行记录和归档是非常重要的。
这些记录和归档不仅可以为产品质量的追溯提供依据,还可以为今后的改进和优化提供参考。
8. 完善反馈。
产品检测流程的最后一步是完善反馈。
通过对检测结果的分析和总结,及时向相关部门反馈问题和改进建议,以确保产品质量的持续改进和提升。
总结。
产品检测流程是保障产品质量的重要环节,一个完善的产品检测流程能够有效地提高产品质量,降低质量风险。
通过制定检测计划、严格把控原材料质量、进行在线和成品检测、抽样检验、数据分析和处理、记录归档以及完善反馈等环节,可以构建一个完整的产品检测流程,为产品质量的稳定提供有力保障。
商品检验的程序
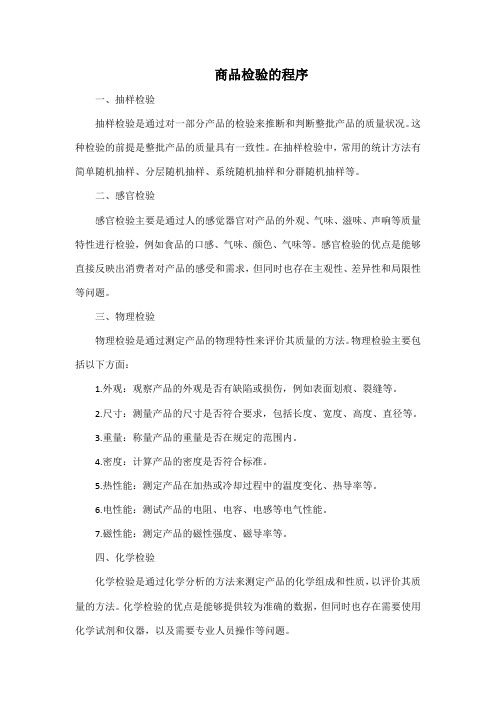
商品检验的程序
一、抽样检验
抽样检验是通过对一部分产品的检验来推断和判断整批产品的质量状况。
这种检验的前提是整批产品的质量具有一致性。
在抽样检验中,常用的统计方法有简单随机抽样、分层随机抽样、系统随机抽样和分群随机抽样等。
二、感官检验
感官检验主要是通过人的感觉器官对产品的外观、气味、滋味、声响等质量特性进行检验,例如食品的口感、气味、颜色、气味等。
感官检验的优点是能够直接反映出消费者对产品的感受和需求,但同时也存在主观性、差异性和局限性等问题。
三、物理检验
物理检验是通过测定产品的物理特性来评价其质量的方法。
物理检验主要包括以下方面:
1.外观:观察产品的外观是否有缺陷或损伤,例如表面划痕、裂缝等。
2.尺寸:测量产品的尺寸是否符合要求,包括长度、宽度、高度、直径等。
3.重量:称量产品的重量是否在规定的范围内。
4.密度:计算产品的密度是否符合标准。
5.热性能:测定产品在加热或冷却过程中的温度变化、热导率等。
6.电性能:测试产品的电阻、电容、电感等电气性能。
7.磁性能:测定产品的磁性强度、磁导率等。
四、化学检验
化学检验是通过化学分析的方法来测定产品的化学组成和性质,以评价其质量的方法。
化学检验的优点是能够提供较为准确的数据,但同时也存在需要使用化学试剂和仪器,以及需要专业人员操作等问题。
五、微生物检验
微生物检验是通过检测产品中的微生物种类和数量来评价其卫生状况和质量的方法。
微生物检验通常用于食品、饮料、化妆品等领域,以确保产品在使用或消费过程中的安全性。
首件检验方法指导书

首件检验方法指导书1. 背景介绍首件检验是指在新产品设计或生产过程中,对首批生产产品进行全面、系统的检验,以保证产品的质量和性能达到设计要求,并对生产过程进行规范。
首件检验是产品质量管理的重要环节之一,能够及时发现和解决生产过程中的问题,确保产品质量稳定。
2. 首件检验目的首件检验的主要目的是验证产品样品的工艺性能是否达标,产品质量是否符合设计要求,以及生产过程的可行性和稳定性。
首件检验的具体目标包括:- 确定产品性能和规格是否符合设计要求;- 检查产品的外观品质,确保符合美观和卫生要求;- 验证产品的功能和可靠性,以保证产品能够正常运行;- 分析生产过程中出现的问题,并提出改进建议。
3. 首件检验流程首件检验的流程可以分为以下几个步骤:3.1 准备工作在进行首件检验之前,需要完成以下准备工作:- 收集相关产品设计和规格文件;- 准备检验设备和工具;- 建立检验记录表格。
3.2 样品抽取根据产品的设计要求和生产数量,从生产批次中抽取符合要求的样品,确保样品的代表性和有效性。
3.3 样品检测对抽取的样品进行检测,包括外观检查、尺寸测量、功能测试、寿命测试等,根据产品的不同特性进行相应的测试。
3.4 检验结果分析根据检测结果,对样品进行分析,评估样品的质量和性能是否符合要求,记录并反馈不合格的情况,找出问题的原因。
3.5 改进建议根据检验结果和问题原因,提出具体的改进建议,包括调整生产工艺、改进产品设计、优化生产流程等。
4. 首件检验要点在进行首件检验时,需要注意以下要点:- 检验人员应具备专业的产品知识和检验技能;- 严格按照检验标准和流程进行检验操作;- 确保检验设备和工具的准确性和可靠性;- 对不合格的产品和问题进行详细记录,并及时反馈给相关部门;- 在处理问题时,注重问题根源的查找和解决,避免问题的反复发生。
5. 总结首件检验是保障产品质量和生产流程稳定性的重要环节,能够帮助企业及时发现和解决问题,确保产品符合设计要求。
成品检验作业指导书
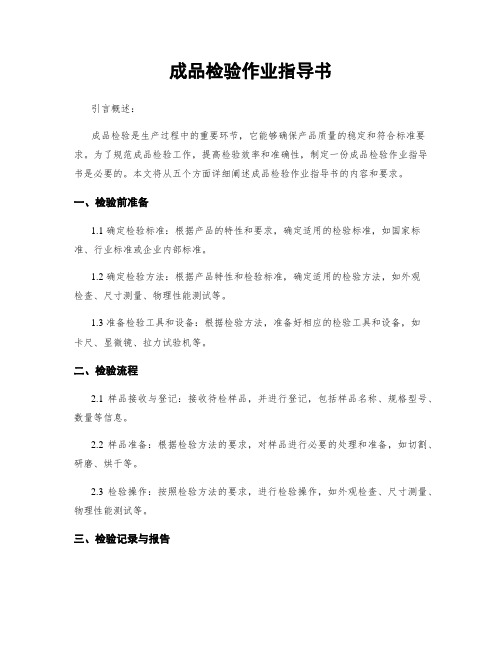
成品检验作业指导书引言概述:成品检验是生产过程中的重要环节,它能够确保产品质量的稳定和符合标准要求。
为了规范成品检验工作,提高检验效率和准确性,制定一份成品检验作业指导书是必要的。
本文将从五个方面详细阐述成品检验作业指导书的内容和要求。
一、检验前准备1.1 确定检验标准:根据产品的特性和要求,确定适用的检验标准,如国家标准、行业标准或企业内部标准。
1.2 确定检验方法:根据产品特性和检验标准,确定适用的检验方法,如外观检查、尺寸测量、物理性能测试等。
1.3 准备检验工具和设备:根据检验方法,准备好相应的检验工具和设备,如卡尺、显微镜、拉力试验机等。
二、检验流程2.1 样品接收与登记:接收待检样品,并进行登记,包括样品名称、规格型号、数量等信息。
2.2 样品准备:根据检验方法的要求,对样品进行必要的处理和准备,如切割、研磨、烘干等。
2.3 检验操作:按照检验方法的要求,进行检验操作,如外观检查、尺寸测量、物理性能测试等。
三、检验记录与报告3.1 记录检验数据:在检验过程中,准确记录检验数据,包括样品信息、检验结果、检验时间等。
3.2 分析检验结果:根据检验数据,进行结果分析,判断样品是否符合标准要求。
3.3 编制检验报告:根据检验结果,编制检验报告,包括样品信息、检验结果、分析结论等,并进行归档保存。
四、异常处理4.1 发现异常情况:在检验过程中,如发现样品存在异常情况,如破损、缺陷等,应及时记录并报告相关人员。
4.2 分析异常原因:对于发现的异常情况,进行原因分析,找出异常的根本原因。
4.3 采取措施:根据异常原因,采取相应的措施,如修复、更换、返工等,确保产品质量符合要求。
五、持续改进5.1 定期评估:定期对成品检验作业指导书进行评估,检查是否需要进行修订和更新。
5.2 收集反馈意见:定期收集相关人员的意见和建议,了解检验工作的实际情况和需求。
5.3 更新改进指导书:根据评估和反馈意见,及时更新和改进成品检验作业指导书,确保其符合实际需求和最新标准。
新材料、新产品试验流程
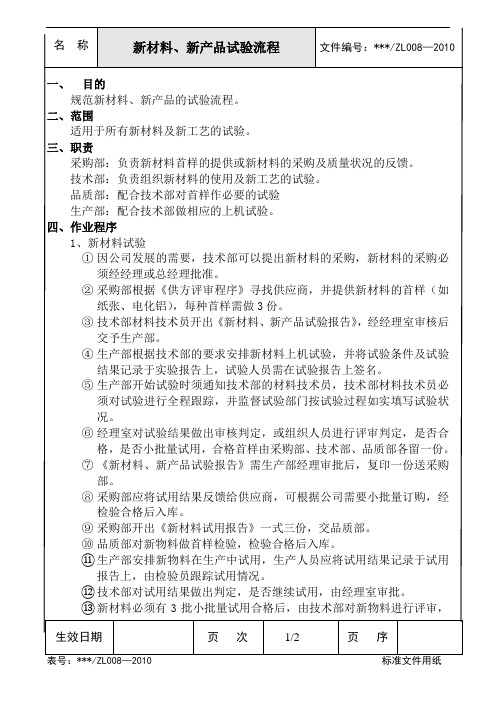
7《新材料、新产品试验报告》需生产部经理审批后,复印一份送采购部。
8采购部应将试用结果反馈给供应商,可根据公司需要小批量订购,经检验合格后入库。
9采购部开出《新材料试用报告》一式三份,交品质部。
5技术部组织试验人员对试验结果进行评审,并判定是否成功。
6如试验成功,由经理室批准,技术部、品质部、生产部各保存一份试验报告,技术部制定该工艺的工艺标准,由经理室批准后方可用于生产,《新工艺工艺标准》由技术部、生产部、品质部各保存一份。
五、相关文件
《供应商评审程序》六、来自关记录《新材料、新产品试验报告》《新材料试用报告》《新工艺工艺标准》
10品质部对新物料做首样检验,检验合格后入库。
11生产部安排新物料在生产中试用,生产人员应将试用结果记录于试用报告上,由检验员跟踪试用情况。
12技术部对试用结果做出判定,是否继续试用,由经理室审批。
13新材料必须有3批小批量试用合格后,由技术部对新物料进行评审,确定为认可物料,该供应商也就成为合格供应商,并将物料编号列入《合格供应商》名录。采购部可以根据生产情况进行大批量采购。
一、目的
规范新材料、新产品的试验流程。
二、范围
适用于所有新材料及新工艺的试验。
三、职责
采购部:负责新材料首样的提供或新材料的采购及质量状况的反馈。
技术部:负责组织新材料的使用及新工艺的试验。
品质部:配合技术部对首样作必要的试验
生产部:配合技术部做相应的上机试验。
四、作业程序
1、新材料试验
1因公司发展的需要,技术部可以提出新材料的采购,新材料的采购必须经经理或总经理批准。
《型式检验报告》
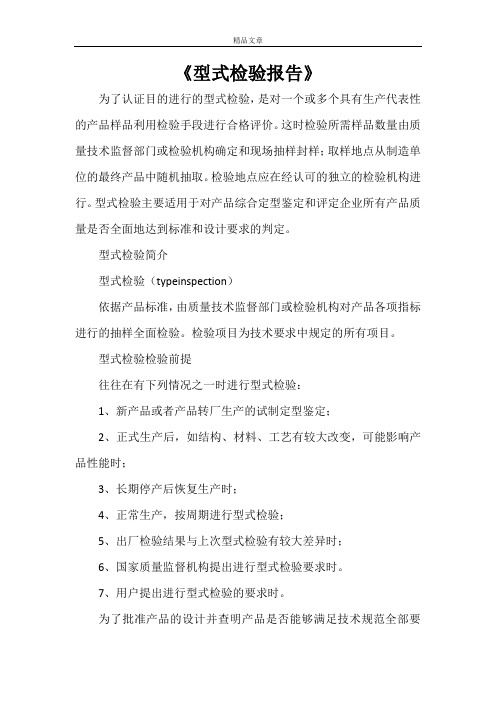
《型式检验报告》为了认证目的进行的型式检验,是对一个或多个具有生产代表性的产品样品利用检验手段进行合格评价。
这时检验所需样品数量由质量技术监督部门或检验机构确定和现场抽样封样;取样地点从制造单位的最终产品中随机抽取。
检验地点应在经认可的独立的检验机构进行。
型式检验主要适用于对产品综合定型鉴定和评定企业所有产品质量是否全面地达到标准和设计要求的判定。
型式检验简介型式检验(typeinspection)依据产品标准,由质量技术监督部门或检验机构对产品各项指标进行的抽样全面检验。
检验项目为技术要求中规定的所有项目。
型式检验检验前提往往在有下列情况之一时进行型式检验:1、新产品或者产品转厂生产的试制定型鉴定;2、正式生产后,如结构、材料、工艺有较大改变,可能影响产品性能时;3、长期停产后恢复生产时;4、正常生产,按周期进行型式检验;5、出厂检验结果与上次型式检验有较大差异时;6、国家质量监督机构提出进行型式检验要求时。
7、用户提出进行型式检验的要求时。
为了批准产品的设计并查明产品是否能够满足技术规范全部要求所进行的型式检验,是新产品鉴定中必不可少的一个组成部分。
只有型式检验通过以后,该产品才能正式投入生产。
对于批量生产的定型产品,为检查其质量稳定性,往往要质量技术监督部门或检验机构进行定期抽样检验(在某些行业该抽样检验又叫做确认检验)。
型式检验的依据是产品标准,为了认证目的所进行的型式检验必须依据产品国家标准。
型式检验流程1.约请型式检验机构。
申请产品制造许可的单位,在获得受理通知后,应按相关管理办法向有型式检验资格的机构提出申请制造许可的产品型式检验意向委托书,同时提交制造许可受理通知书(复印件)。
型式检验机构根据受理通知书中申请制造许可的产品类别、品种进行型式检验。
2.型式检验机构在接到申请单位的约请后,按双方应约定的时间,派出2~4名检验检测人员组成型式检验组,由一名具有评审资格的评审员担任组长,到制造单位进行产品抽样、并完成相关检查等工作。
新产品开发及检验流程
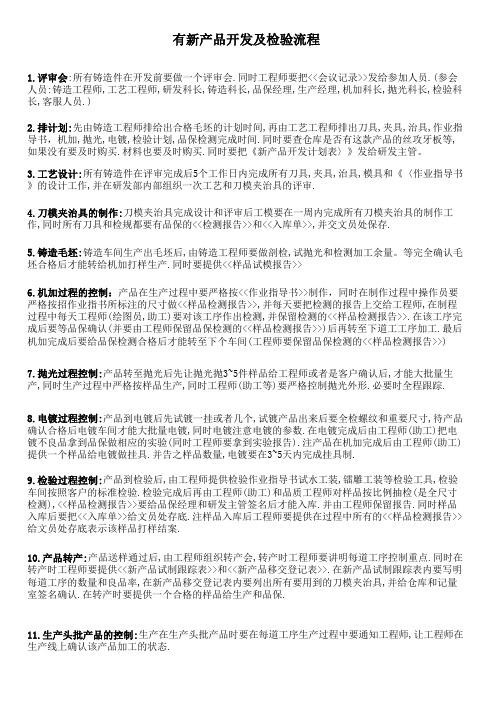
有新产品开发及检验流程1.评审会:所有铸造件在开发前要做一个评审会.同时工程师要把<<会议记录>>发给参加人员.(参会人员:铸造工程师,工艺工程师,研发科长,铸造科长,品保经理,生产经理,机加科长,抛光科长,检验科长,客服人员.)2.排计划:先由铸造工程师排给出合格毛坯的计划时间,再由工艺工程师排出刀具,夹具,治具,作业指导书,机加,抛光,电镀,检验计划,品保检测完成时间.同时要查仓库是否有这款产品的丝攻牙板等,如果没有要及时购买.材料也要及时购买.同时要把《新产品开发计划表〉》发给研发主管。
3.工艺设计:所有铸造件在评审完成后5个工作日内完成所有刀具,夹具,治具,模具和《〈作业指导书》的设计工作,并在研发部内部组织一次工艺和刀模夹治具的评审.4.刀模夹治具的制作:刀模夹治具完成设计和评审后工模要在一周内完成所有刀模夹治具的制作工作,同时所有刀具和检规都要有品保的<<检测报告>>和<<入库单>>,并交文员处保存.5.铸造毛坯:铸造车间生产出毛坯后,由铸造工程师要做剖检,试抛光和检测加工余量。
等完全确认毛坯合格后才能转给机加打样生产.同时要提供<<样品试模报告>>6.机加过程的控制:产品在生产过程中要严格按<<作业指导书>>制作,同时在制作过程中操作员要严格按招作业指书所标注的尺寸做<<样品检测报告>>,并每天要把检测的报告上交给工程师,在制程过程中每天工程师(绘图员,助工)要对该工序作出检测,并保留检测的<<样品检测报告>>.在该工序完成后要等品保确认(并要由工程师保留品保检测的<<样品检测报告>>)后再转至下道工工序加工.最后机加完成后要给品保检测合格后才能转至下个车间(工程师要保留品保检测的<<样品检测报告>>)7.抛光过程控制:产品转至抛光后先让抛光抛3~5件样品给工程师或者是客户确认后,才能大批量生产,同时生产过程中严格按样品生产,同时工程师(助工等)要严格控制抛光外形.必要时全程跟踪.8.电镀过程控制:产品到电镀后先试镀一挂或者几个,试镀产品出来后要全检螺纹和重要尺寸,待产品确认合格后电镀车间才能大批量电镀,同时电镀注意电镀的参数.在电镀完成后由工程师(助工)把电镀不良品拿到品保做相应的实验(同时工程师要拿到实验报告).注产品在机加完成后由工程师(助工)提供一个样品给电镀做挂具.并告之样品数量,电镀要在3~5天内完成挂具制.9.检验过程控制:产品到检验后,由工程师提供检验作业指导书试水工装,镭雕工装等检验工具,检验车间按照客户的标准检验.检验完成后再由工程师(助工)和品质工程师对样品按比例抽检(是全尺寸检测),<<样品检测报告>>要给品保经理和研发主管签名后才能入库.并由工程师保留报告.同时样品入库后要把<<入库单>>给文员处存底.注样品入库后工程师要提供在过程中所有的<<样品检测报告>>给文员处存底表示该样品打样结案.10.产品转产:产品送样通过后,由工程师组织转产会,转产时工程师要讲明每道工序控制重点.同时在转产时工程师要提供<<新产品试制跟踪表>>和<<新产品移交登记表>>.在新产品试制跟踪表内要写明每道工序的数量和良品率,在新产品移交登记表内要列出所有要用到的刀模夹治具,并给仓库和记量室签名确认.在转产时要提供一个合格的样品给生产和品保.11.生产头批产品的控制:生产在生产头批产品时要在每道工序生产过程中要通知工程师,让工程师在生产线上确认该产品加工的状态.。
产品质量检验流程
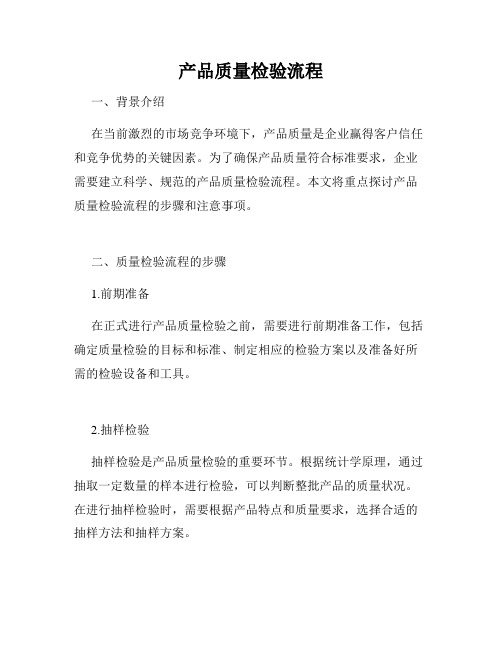
产品质量检验流程一、背景介绍在当前激烈的市场竞争环境下,产品质量是企业赢得客户信任和竞争优势的关键因素。
为了确保产品质量符合标准要求,企业需要建立科学、规范的产品质量检验流程。
本文将重点探讨产品质量检验流程的步骤和注意事项。
二、质量检验流程的步骤1.前期准备在正式进行产品质量检验之前,需要进行前期准备工作,包括确定质量检验的目标和标准、制定相应的检验方案以及准备好所需的检验设备和工具。
2.抽样检验抽样检验是产品质量检验的重要环节。
根据统计学原理,通过抽取一定数量的样本进行检验,可以判断整批产品的质量状况。
在进行抽样检验时,需要根据产品特点和质量要求,选择合适的抽样方法和抽样方案。
3.质量检测根据抽样得到的样品,进行质量检测是产品质量检验流程中的核心环节。
质量检测的方法和指标应根据产品的特性和行业标准来确定,可以包括外观检查、物理性能测试、化学成分分析等多个方面。
4.数据分析与判断在质量检验完成后,需要对检测结果进行数据分析和判断。
通过对数据的比较和统计分析,判断产品是否符合质量要求。
如果发现产品存在质量问题,需要及时采取相应的纠正措施,确保产品质量符合标准要求。
5.记录和报告产品质量检验流程的最后一步是进行记录和报告。
记录检验过程中的关键信息、数据和处理结果,以便日后追溯和查证。
同时,对检验结果进行详细的报告,包括产品质量状况、存在的问题以及改进措施建议等,以供相关部门和管理层参考。
三、产品质量检验流程的注意事项1.标准和方法的选择在制定产品质量检验流程时,需要根据产品的特点和行业标准来选择适合的检验标准和方法。
合理选择标准和方法,能够保证检验结果的准确性和可靠性。
2.检验设备和工具的维护产品质量检验过程中使用的检验设备和工具需要定期进行维护和校准,以确保其测量精度和准确性。
同时,需要保持检验环境的干净整洁,避免外界因素对检验结果的干扰。
3.抽样方法的科学性抽样检验是产品质量检验的关键环节,抽样方法的科学性直接影响到检验结果的可靠性。
产品质量检验方案编制工作流程及方法
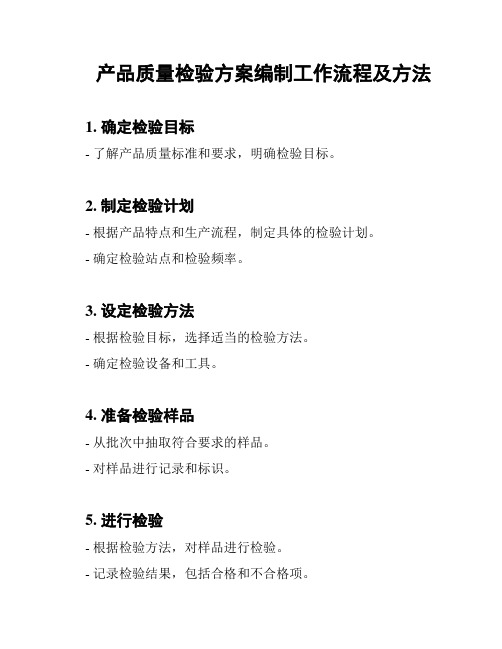
产品质量检验方案编制工作流程及方法
1. 确定检验目标
- 了解产品质量标准和要求,明确检验目标。
2. 制定检验计划
- 根据产品特点和生产流程,制定具体的检验计划。
- 确定检验站点和检验频率。
3. 设定检验方法
- 根据检验目标,选择适当的检验方法。
- 确定检验设备和工具。
4. 准备检验样品
- 从批次中抽取符合要求的样品。
- 对样品进行记录和标识。
5. 进行检验
- 根据检验方法,对样品进行检验。
- 记录检验结果,包括合格和不合格项。
6. 处理不合格项
- 对不合格项进行分析和评估。
- 制定纠正措施,确保产品质量。
7. 完善检验方案
- 根据实际情况对检验方案进行完善。
- 不断优化和改进检验方法和流程。
8. 审核和培训
- 对检验方案进行审核和评估。
- 向相关人员进行培训,确保检验方案的有效实施。
9. 监督和维护
- 建立监督机制,确保检验方案的执行和效果。
- 定期评估和更新检验方案。
以上是产品质量检验方案编制的工作流程及方法。
通过科学合理的步骤和方法,我们可以确保产品质量符合标准和要求,提升客户满意度,提升企业竞争力。
- 1、下载文档前请自行甄别文档内容的完整性,平台不提供额外的编辑、内容补充、找答案等附加服务。
- 2、"仅部分预览"的文档,不可在线预览部分如存在完整性等问题,可反馈申请退款(可完整预览的文档不适用该条件!)。
- 3、如文档侵犯您的权益,请联系客服反馈,我们会尽快为您处理(人工客服工作时间:9:00-18:30)。
新规部品型检业务基准
1、适用范围:
本基准适用于在MWIC新产品开发中新规部品的型检(精密型式检查),包括新模具塑料件、金属件、橡胶件和重要安全部品(如电子电器元部件)。
2、职责:
2.1产品技术课负责提供图纸、部品仕样书、产品规格书等一切技术资料,必要时进行技术支持和变更.
2.2资材课和模具系负责联系供应商进行新规部品的送样和改善
2.3品管课负责新规部品的检查判定,及改善方案的提供。
2.4生产管理课负责新产品开发日程的制定推进。
3、管理内容:
3.1 产品技术课根据新产品开发日程及时制作提供图纸、部品纳入仕样书、色板及部品名细和材料一览等技术资料,并及时发给相应部门。
3.2 资材课和模具系担当根据新产品开发日程及时联系供应商开发模具试做样品,并将样品送至品质管理课判定。
3.3 品质管理课型检担当依据产品技术课提供的图纸等相关技术资料对样品的各技术规格进行精密检查,并将检查结果及时通知相关人员。
3.4 检查内容和方法按附表《新产品检查方法》、并填写相应的检查成绩表。
3.5 如果检查发现不良,担当应及时反馈给资材课或模具系,由各担当将信息反馈给供应商并督促及时改善,并再次送样评价;如有必要可以与产品技术课协商是否要设计变更。
3.6 如果检查结果OK,由型检担当和其他相应担当办理采用手续,出具合格的型检报告或签板确认。
并办好与IQC的工作交接。
3.7 如果发生变更,由产品技术课立即发设计变更通知书给相关部门,各部门担当负责履行各自的职责。
3.8 检查结果要求得到型检组长、品管课长的确认
新产品印刷/新色新材料/新规包装材料型检确认流程
1、范围
适用于MWIC所有新产品印刷/新色新材料/新规包装材料的型检
2、职责
2.1 产品技术课负责提供图纸、菲林、色板和部品明细及设计变更等技术资料
2.2 资产课负责新规部品的试作品送样
2.3 品质管理课型检担当负责印刷和新色的检查、判定
3、管理内容
3.1 产品技术课根据新产品开发日程及时制作提供图纸、菲林、色板及部品名细和材料一览等技术资料,并及时发给资材课、品质管理课、部品制造课和生产制造课。
3.2 资材课根据新产品开发日程督促外协厂按期试作样品,并将样品送至品质管理课判定。
3.3 品质管理课型检担当依据产品技术课提供的图纸、菲林和色板检查试作样品,并将判定结果反馈给资材课。
3.4 检查内容和方法按附表《新产品印刷检查方法》、《新色新材料检查方法》和《包装材料检查方法》,并填写相应的检查成绩表。
3.5 如果检查发现不良,担当应及时反馈给资材课,由资材课担当将信息反馈给供应商及时改善,并再次送样评价。
3.6 如果检查结果OK,由型检担当在样品适当位置签写:印刷/颜色/样板OK,并注明机种、担当者和日期,并将样板交给资材课和进货检查担当各一个。
3.7 如果发生变更,由产品技术课立即发设计变更通知书给相关部门,各部门担当负责履行各自的职责。
3.8 检查结果要求得到型检组长、品管课长的确认
4、附录
4.1 《新产品印刷检查方法》、《新产品印刷检查成绩表》
4.2 〈新色新材料检查方法〉、〈新色新材料检查成绩表〉
新产品
检
查
方
法
松下·万宝(广州)电熨斗有限公司
新产品印刷检查方法
本办法规定了MWIC新产品印刷型检时的检查内容、方法及注意事项。
检查步骤及方法:
1、内容及排版式样:依据设计图纸和菲林检查样品的印刷内容和式样,如符合,则判定为OK,
否则NG
2、油墨颜色:依据设计图纸、部品明细或其他技术资料确定油墨颜色,并将样品和标准色板(纸
质)相对照,如符合,则判定为OK,否则NG;其偏差范围参考旧机种印刷样。
3、外观效果:印刷文字、线条、图案清晰明确,油墨均匀一致,无毛刺、模糊、漏墨、扭曲、
偏移等不良,否则NG;其偏差范围参考旧机种印刷样或限度样板。
4、油墨粘性:(A)将透明胶布粘住印刷部位,用拇指轻轻抹4次,提起一端与印刷成90度迅
速剥离,如此连续剥离三次无脱墨现象即为OK(注:连续剥离均在同一处,且胶布不许重复使用)。
(B)用软质棉布把1000克的钢质圆磙包住沾少许洗洁精,在印刷处来回檫拭100次无明显脱墨即为OK(注:檫拭和剥离不在同一处)。
5、位置尺寸:依据设计图纸检查印刷位置尺寸,样品实物尺寸在公差范围之内即为OK;水量表
示位置。
注意事项:
(1)检查位置尺寸时根据印刷的部位和设计意图不同分为重点尺寸和非重点尺寸,重点尺寸必须保证在公差范围之内,不符则必须修正,如水量表示印刷;非重点尺寸则在不
影响美观、使用的前提下可适当放宽,如商标表示印刷。
(2)检查外观效果时,发现不良要通知担当部门及时改善;如确实因为技术或其它原因无法改善时,可以考虑做限度样板管理或特采处理
新色新材料部品检查方法
本办法规定了MWIC新色新材料部品型检时的检查内容、方法及注意事项。
检查内容及步骤:
1、材料:依据产品技术课提供的新产品材料一览表、部品明细等标准资料检查样品的颜
色材料是否符合规定要求,如符合即判定为OK,否则NG;
2、颜色:依据产品技术课提供的标准色板判定样品的颜色是否有偏差,与相关部品的颜
色搭配是否协调一致,如无明显偏差即判为OK,偏差较大即判定为NG;
3、外观:参考旧机种的限度样板检查外观有无不良,如流纹、气泡、混色、光洁度不够、
飞边等。
注意事项:
1、由于塑料件的颜色受材料和成型条件的影响较大,模温、成型压力等成型条件稍有变
化都会直接导致颜色变化,有可能型检时的试做样品和正式量产品颜色有较大偏差,
所以新色型检时要确认样品的成型条件是否稳定,不能把初始试模时的部品用做新色
型检样品。
2、将结果填写在〈〈新色新材料检查成绩表〉〉上,并将结果通知资材课,如结果OK,
即可在样品适当位置签写:颜色OK,并注明机种、材料、颜色、担当、日期;如结
果NG,则通知资材课改善后重新送样果
3、将颜色OK的新色新材料部品通知担当人员可以进行新色新材料的耐光实验
新型模具塑料件的检查方法
本办法适用于MWIC所有新型新规模具的塑料件的精密型式检查(不包括组件的印刷、颜色)。
塑料件在所有部品中是结构最复杂、品质最不稳定、工艺难度最大的一种,受材料、模具、成型、储藏和运输等诸多因素的影响,控制起来难度大。
所以在型检时要考虑多方面的因素,特别是要照顾到与其他部品的配合。
检查方法:
1、对照设计图纸检查样品的各个尺寸是否在公差之内,是否有材料刻印、模号等其他标
识,外观颜色是否符合要求.
2、与相关部品组装评价其嵌合性能,级差、间隙是否符合要求,装配有无困难,其嵌合
状态能否满足设计要求等
3、成型的稳定性如何,是否存在脱模困难、颜色变异、顶针易断、冷却后收缩变形等不
良现象
4、使用的材料是否为规定材料,因为不同的材料其收缩率不同,成型的样品在颜色、尺
寸、形状方面也会不同。
5、将检查结果记录在“试作品检查成绩表”上
6、精密型式检查完成后要联系模具系、产品技术课一起合议确定最终修正方案。
对于一
些不符合项目,如果影响嵌合、性能、外观则必须修正,否则可以考虑特采。
注意事项:
1、由于图纸上的尺寸较多,很多是空间尺寸,检查困难,要全检需花费很长时间,因此
有选择的检查,对于重点的、影响嵌合装配的尺寸重点检查,而对于一些参考尺寸可
以少检或不检,可以根据嵌合状态决定是否进行模具修正。
其中图中标“﹡”、“☆”
的尺寸为设计参考尺寸,必要时可以调整。
2、提出改善方案时要充分考虑到与相关部品的嵌合性能,修模的合理性和难易性。
一般
常识是:加胶容易减胶难。
改模时分型面一般避免改动,复杂的嵌合一定要先有一个
基准在此基础上改善其他部品或其他尺寸。
确定方案前要考虑全面仔细,搞清嵌合的
内部结构状态,比要时作样板验证方案的可行性。
此时要多与模具系、产品技术课沟
通。
3、由于成型塑料件受各种因素如成型、材料、模具的影响变形较大,材料不同收缩率也
差别很大,同时生产的同一模部品其尺寸可能差别都很大,组装起来间隙、级差都会
不同,所以在确定修正尺寸时一定要多收集数据,充分验证,尤其是不同模号之间的
嵌合状态。
4、塑料件部品最不稳定的尺寸大致在:各种孔的内径和孔深,模具结构中是镶件、顶针
划块等能活动的部位,较大成型面的轮廓尺寸,模具尖锐处,距离水口较远处的结构尺
寸和外观等,特别是用PP材料做的部品的外形尺寸。
5、如果部品有外观方面的不良,如:流纹、混色、收缩、飞边、级差等,在模具改善困
难、并且不影响嵌合的情况下可以参考现行品的基准判定是否可以特采,必要时做限度样板。