精馏塔单元仿真培训系统
精馏塔单元操作手册

文档编号:TSS_C4.DOC精馏塔单元仿真培训系统操作说明书北京东方仿真软件技术有限公司二〇〇六年十月目录一、工艺流程说明 (2)1、工艺说明 (2)2、本单元复杂控制方案说明 (2)3、设备一览 (3)二、精馏单元操作规程 (3)1、冷态开车操作规程 (3)2、正常操作规程 (4)3、停车操作规程 (5)4、仪表一览表 (6)三、事故设置一览 (7)四、仿真界面 (9)附:思考题 (11)一、工艺流程说明1、工艺说明本流程是利用精馏方法,在脱丁烷塔中将丁烷从脱丙烷塔釜混合物中分离出来。
精馏是将液体混合物部分气化,利用其中各组分相对挥发度的不同,通过液相和气相间的质量传递来实现对混合物分离。
本装置中将脱丙烷塔釜混合物部分气化,由于丁烷的沸点较低,即其挥发度较高,故丁烷易于从液相中气化出来,再将气化的蒸汽冷凝,可得到丁烷组成高于原料的混合物,经过多次气化冷凝,即可达到分离混合物中丁烷的目的。
原料为67.8℃脱丙烷塔的釜液(主要有C4、C5、C6、C7等),由脱丁烷塔(DA-405)的第16块板进料(全塔共32块板),进料量由流量控制器FIC101控制。
灵敏板温度由调节器TC101通过调节再沸器加热蒸汽的流量,来控制提馏段灵敏板温度,从而控制丁烷的分离质量。
脱丁烷塔塔釜液(主要为C5以上馏分)一部分作为产品采出,一部分经再沸器(EA-418A、B)部分汽化为蒸汽从塔底上升。
塔釜的液位和塔釜产品采出量由LC101和FC102组成的串级控制器控制。
再沸器采用低压蒸汽加热。
塔釜蒸汽缓冲罐(FA-414)液位由液位控制器LC102调节底部采出量控制。
塔顶的上升蒸汽(C4馏分和少量C5馏分)经塔顶冷凝器(EA-419)全部冷凝成液体,该冷凝液靠位差流入回流罐(FA-408)。
塔顶压力PC102采用分程控制:在正常的压力波动下,通过调节塔顶冷凝器的冷却水量来调节压力,当压力超高时,压力报警系统发出报警信号,PC102调节塔顶至回流罐的排气量来控制塔顶压力调节气相出料。
罐区单元仿真系统操作手册
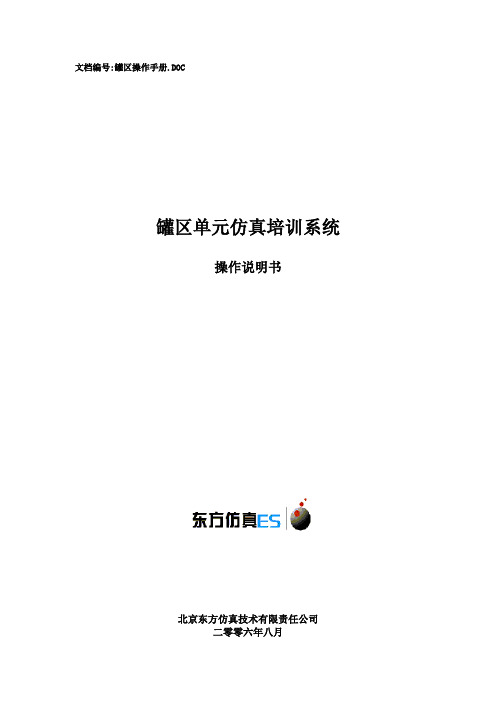
文档编号:罐区操作手册.DOC罐区单元仿真培训系统操作说明书北京东方仿真技术有限责任公司二零零六年八月一、工艺流程说明1.罐区的工作原理:罐区是化工原料,中间产品及成品的集散地,是大型化工企业的重要组成部分,也是化工安全生产的关键环节之一。
大型石油化工企业罐区储存的化学品之多,是任何生产装置都无法比拟的。
罐区的安全操作关系到整个工厂的正常生产,所以,罐区的设计、生产操作及管理都特别重要。
罐区的工作原理如下:产品从上一生产单元中被送到产品罐,经过换热器冷却后用离心泵打入产品罐中,进行进一步冷却,再用离心泵打入包装设备。
2.罐区的工艺流程:本工艺为单独培训罐区操作而设计,其工艺流程(参考流程仿真界面)如下:来自上一生产设备的约35℃的带压液体,经过阀门MV101进入产品罐T01,由温度传感器TI101显示T01罐底温度,压力传感器PI101显示T01罐内压力,液位传感器LI101显示T01的液位。
由离心泵P101将产品罐T01的产品打出,控制阀FIC101控制回流量。
回流的物流通过换热器E01,被冷却水逐渐冷却到33℃左右。
温度传感器TI102显示被冷却后产品的温度,温度传感器TI103显示冷却水冷却后温度。
由泵打出的少部分产品由阀门MV102打回生产系统。
当产品罐T01液位达到80%后,阀门MV101和阀门MV102自动关断。
产品罐T01打出的产品经过T01的出口阀MV103和T03的进口阀进入产品罐T03,由温度传感器TI103显示T03罐底温度,压力传感器PI103显示T03罐内压力,液位传感器LI103显示T03的液位。
由离心泵P103将产品罐T03的产品打出,控制阀FIC103控制回流量。
回流的物流通过换热器E03,被冷却水逐渐冷却到30℃左右。
温度传感器TI302显示被冷却后产品的温度,温度传感器TI303显示冷却水冷却后温度。
少部分回流物料不经换热器E03直接打回产品罐T03;从包装设备来的产品经过阀门MV302打回产品罐T03,控制阀FIC302控制这两股物流混合后的流量。
基于MATLAB的精馏控制系统开发与仿真

过程控制三级项目说明书题目:精馏控制系统学院(系):电气工程学院年级专业: 13级仪表一班小组:第一组指导教师:摘要精馏塔是化工、石油化工、炼油生产过程中应用极为广泛的传质传热过程设备。
精馏过程的实质就是利用混合物中各组分具有不同的挥发度,实现各组分的分离。
精馏塔是一个多输入多输出的多变量过程,内在机理较复杂,动态响应迟缓,变量之间相互关联,在线测量困难,不同的塔工艺结构差别很大,而工艺对控制提出的要求又较高,所以确定精馆塔的控制方案是一个极为重要的课题。
此外,在全球金融危机的压力下,国内众多过程工业企业不仅面临着同行的竞争压力,同时也面临着来自国际间的市场挑战.在当前经济并不景气的大环境下,积极的开发和应用先进过程控制技术来提高企业的经济效益,增强企业自身的竞争力是过程工业迎接挑战的主要途径。
随着控制理论与计算机技术的发展,不仅为先进控制技术的应用奠定了理论基础,同样也提供了良好的软硬件平台。
近些年来,先进控制技术在实际工业过程中也取得了较好的成效,具有十分广泛的应用前景。
精馏过程因其大时滞、变量藕合、动态特性分析复杂、约束条件复杂且难以进行变量配对等特性成为过程控制界多年来理论研究和实践的热点。
本文针对工程训练任务书中给出的系统辨识函数,搭建了仿真框图,调整PID参数,最终使系统在较好的指标内达到稳定。
关键词:精馏塔仿真框图 PID参数目录1.精馏控制系统................................................3 1.1精馏工艺概述..............................................3 1.2精馏工艺的基本要求......................................4 2。
系统分析及方案选择..........................................43.控制对象的数学模型..........................................64.系统稳定性分析.......................................65.控制系统的参数整定..........................................8 6。
UniSim OTS操作员仿真培训系统应用

25 Honeywell Proprietary
/ps
UniSim Design煤气化模型与应用
• 煤的分析数据
– 输入工业分析、元素分析、灰分性质 – 计算煤的高/低热值、密度、比热等性质
• 气化炉
– 计算煤的热解、气化、激冷过程 – 采用动力学反应,内置反应动力学参数,可以通过现场数据校正 – 输出结果
换热网络夹点 分析与 能量优化软件
工艺/控制 设备
公用工程与能耗
UniSim Flare 火炬系统设计软件
安全
16 Honeywell Proprietary
/ps
UniSim Design 流程行业解决方案
油气开采/集输 天然气处理 炼油石化
化工
UniSim Design Suite
UniSim DCS Interface Experion Server
UniSim Safety Manager UniSim / Experion Control Environment Control Environment
7 Honeywell Proprietary
/ps
• 神华宁煤煤制烯烃OTS • 大唐电力煤制烯烃OTS • 航天煤化工煤制甲醇OTS • 神华集团煤制油壳牌煤气化OTS • 中石化岳阳/湖北大化/安庆油改煤项目煤气化OTS • 中海油富岛合成氨/甲醇OTS
• 广东/上海/大连 LNG OTS • BP珠海PTA OTS
新建大型石油化工装置进行操作工仿真培训在国外已成标配, 在国内也已成为大势所趋。
工艺仿真
工艺单元 外操
模型服务器
现场站 现场操作员
5 Honeywell Proprietary
仿真软件系统总体介绍

中国仿真教学网
朱素娟
18618347261
sjzhu@
2.1.6 2.1.7 2.1.8 2.1.9 2.1.10 2.1.11 2.1.12 2.2 2.2.1
操作员站软 件模块 场景设计器 软件模块 接口机软件 模块 模拟服务器 软件模块
和解冻学员仿真模型的运行,支持设置学员联系。支持对教师参 数的监控,支持向学员站发送教师信息。 支持用户登陆,可接收来自教师机的信息,可连接接口机并和模 拟服务器进行通讯。 自由配置教师、 学员和模型之间的操作关系, 可将学员进行编组。 支持教师、学员的用户管理,支持特定时刻点的模型场景设置, 验证配置关系。 支持 OPC DA 和 DCS 接口,并支持学员站流程软件和仿真服务器 的连接 运行所有学员、教师和模型。支持故障、考评、回放等功能。支 持用户管理、信息管理、和模型管理,支持对系统日志,报警和 调试信息的管理和显示
中国仿真教学网
朱素娟
18618347261
sjzhu@
1
设计原则
从培养高职院校的实践能力及职业培训需求出发, 本着实用性与前瞻性相结
合、职业技能培训鉴定与技能训练仿真软件相结合的思想,对工艺过程、动态操 作、正在使用的国内外先进的 DCS 控制系统进行仿真模拟,以培养能够适应当 前及未来化工企业所需要的各类技术人员,满足化工工业建设与生产的需要。 系统性原则: 流程仿真软件系统, 应在真实完整体现实际工业流程的基础上, 利用操作员培训系统(OTS)仿真软件和 DCS 模拟环境进行全流程模拟培训, 使受训人员可感受操控真实工厂和 DCS 般“身临其境”的强大体验。 真实性原则:流程仿真软件系统按照工业现场设备和流程进行模拟仿真,同 时对重点设备的内部结构、 工作原理深入的剖析。 通过机理建模建立 “虚拟工厂” , 可自上而下地实现对工厂过程和控制逻辑的动态模拟。OTS 仿真软件的动态模 型真实再现实际工业流程状态和行为, 实时准确的模拟工艺现场, 模拟真实故障。 全面性原则: 既能使学员了解和掌握正常工况下各个相关流程的操作和维护, 能进行化工工艺的冷态开车、热态开车、正常运行、正常停车、紧急停车、设备 维护等方面的技能操作训练、 工艺指标控制操作技能训练;又能通过安全手段设 置各类故障,使学员能够处理各类紧急状况,进行生产过程操作、分析、排除工 业生产过程故障。
信息化大赛蒸馏仿真教学设计说课稿

精馏塔单元仿真操作教学设计说课稿一、教学分析1.教学内容本单元内容选自应用化工技术专业的《化工单元操作技术》课程,依据人才培养方案,立足于企业对于化工专业人才的技术需求,结合学院现有设备优势,将课程内容确定为单元仿真操作练习。
本次课是单元仿真操作练习里的一项内容,即精馏塔单元仿真操作实训。
2.教学对象课程教学对象为:高职应用化工技术专业二年级学生,前置课程为《化学基础》、《化工仪表及自动化》、《化工设备操作维护与使用》。
学生对前置课程的学习,已掌握化工生产中的基本理论知识,及化工生产中精馏分离的理论知识和基本工艺流程、主要设备的大致构造,和化工生产过程中常用的仪表和控制方法的基础理论知识。
3.教学目标根据岗位要求和人才培养计划的要求,确定本单元的技能目标和知识目标,并把培养学生的安全操作意识和团队合作精神贯穿其中。
4.重点难点根据课程标准和学生已有知识的掌握能力,确定本单元重点是熟练掌握冷态开车操作及事故处理,难点是操作中各参数的协调配合关系。
二、信息化手段及素材准备本次课程在仿真实训室进行,不仅制作了讲课用的PPT幻灯片方便讲解,同时在讲授及练习期间利用手机与学生进行互动,来调动学习积极性。
课前准备的素材及资料有:(1)利用录屏软件录制好操作视频,编制好操作说明书,并将这些资源发布到蓝墨云班课的资源库里;(2)备课期间,制作好讲授理论知识方面的PPT幻灯片及教案,幻灯片配备图片及操作截图,重点进行讲解;并提前设置好在蓝墨云班课上的头脑风暴问题及随堂测试题库;(3)利用东方仿真的教师站设置好培训策略,并编辑考核试卷,建立培训室和考核室;(4)课程结束后,在蓝墨云班课上进行作业点评,并在讨论区对学生的问题进行答疑解惑。
三、设计思路依据职业教育教学改革要求,基于翻转课堂教学理念,采用任务驱动教学放,以精馏单元仿真操作的冷态开车和事故处理任务为载体进行教学设计,完成从精馏塔冷态开车操作到事故分析处理的完整工作过程。
技能训练二 精馏塔操作仿真训练

技能训练二精馏塔操作仿真训练●训练目标能利用仿真系统操作精馏塔。
●训练准备熟悉工艺流程及原理。
本单元是一种加压精馏操作,原料液为脱丙烷塔塔釜的混合液,分离后馏出液为高纯度的C4产品,残液主要是C5以上组分。
67.8℃的原料液经流量调节器FICl01控制流量(14056kg/h)后,从精馏塔DA405的第16块塔板(全塔共32块塔板)进料。
塔顶蒸气经全凝器EA419冷凝为液体后进入回流罐FA408;回流罐FA408的液体由泵GA412A/B抽出,一部分作为回流液由调节器FCl04控制流量(9664kgm)送回DA405第32层塔板;另一部分则作为产品,其流量由调节器FCl03控制(6707kg/h)。
回流罐的液位由调节器LCl03与FCl03构成的串级控制回路控制。
DA405操作压力由调节器PCI02分程控制为5.0kg/m2,其分程动作如图3-34所示。
同时调节器PCI01将调节回流罐的气相出料,保证系统的安全和稳定。
图3-34调节阀PVl02分程动作示意图塔釜液体的一部分经再沸器EA408A/B回精馏塔,另一部分由调节器FCl02控制流量(7349kg/h),作为塔底采出产品。
调节器LCl01和FCl02构成串级控制回路,调节精馏塔的液位。
再沸器用低压蒸汽加热,加热蒸汽流量由调节器TCl01控制,其冷凝液送FA414。
FA414的液位由调节器LCl02调节。
其工艺流程如图3-35所示。
图3-58 精馏塔单元带控制点工艺流程图●训练步骤(要领)(一)冷态开车进料前确认装置冷态开工状态为精馏塔单元处于常温、常压、氮气吹扫完毕的氮封状态,所有阀门、机泵处于关停状态、所有调节器置于手动状态。
1.进料及排放不凝气(1)打开PVl01(开度>5%)排放塔内不凝气;(2)打开FVl01(开度>40%),向精馏塔进料;(3)进料后,塔内温度略升、压力升高;当压力升高至0.5atm(表)时(4)控制塔顶压力大于1.0atm(表),不超过4.25atm(表)。
精馏塔单元仿真工艺流程及控制方案说明

精馏塔单元仿真工艺流程及控制方案说明嘿,朋友们!今天咱就来好好聊聊精馏塔单元仿真工艺流程及控制方案。
你看啊,这精馏塔就好比是一个神奇的魔法塔!原料就像是一群五花八门的小精灵,它们一股脑地涌进塔里面。
在塔里面呀,经过层层的折腾和分离,就像小精灵们找到了自己的专属领地一样。
先来说说这工艺流程吧。
原料从塔底进入,然后就开始了它们的奇妙之旅。
热气腾腾地往上跑,各种成分在不同的高度被分离开来。
这就像是一场盛大的赛跑,跑得快的成分就率先冲出来啦。
而那些跑得慢的呢,就乖乖地留在后面,等待合适的时机。
再讲讲控制方案,这可太重要啦!就好比是给这个魔法塔装上了智能的大脑。
温度、压力、流量这些参数都得好好把控着。
温度高了不行,低了也不行,这不就跟咱炒菜似的,火候得恰到好处嘛!压力也是,得保持在一个合适的范围,不然这魔法塔可就要闹脾气啦。
流量呢,就像是给小精灵们安排的通道,不能太拥挤,也不能太空旷呀。
要是控制不好会咋样?那可就乱套啦!就好像做饭的时候盐放多了或者火太大了,做出来的菜能好吃吗?所以啊,这控制方案可得精心设计,仔细调整。
想象一下,如果温度乱来,一会儿高得离谱,一会儿又低得吓人,那里面的成分还不得晕头转向呀?压力要是不稳定,这魔法塔会不会也跟着摇摇晃晃的?流量要是出了问题,那整个流程不就都乱套啦?咱可得把这个魔法塔照顾好,让它稳稳当当地工作。
这不仅需要我们有精湛的技术,还得有足够的耐心和细心呢。
这可不是一件轻松的事儿,但一旦做好了,那成果可是相当可观的呀!总之,精馏塔单元仿真工艺流程及控制方案就像是一场精彩的演出,我们就是导演,得把每一个细节都安排得妥妥当当,才能让这场演出圆满成功!大家说是不是这个理儿呀?。
双塔精馏单元仿真实训报告

双塔精馏单元仿真实训报告实验目的:1.学习双塔精馏单元的基本原理和工作原理。
2.了解双塔精馏单元的操作过程和优化方法。
3.通过仿真实训,提高学生的实际操作能力和问题解决能力。
实验装置:我们使用了一套虚拟化工厂仿真软件,该软件可以模拟真实的化工装置和操作过程。
双塔精馏单元仿真装置由两个塔和一台加热炉组成。
其中,塔1为粗提塔,塔2为精提塔。
实验步骤:1.设定进料组分和流量,并开启加热炉,使进料加热到所需温度。
2.将加热后的进料引入粗提塔顶部,通过粗提塔内的塔盘进行分离。
塔盘上的液相会向下流动,与上升的蒸汽相进行传质传热,从而实现分离。
3.从粗提塔底部收集出塔床液相产物,以及从塔顶收集出的气相产物。
通过调整收集温度和流量,获取理想的产物组分。
4.将从塔顶收集出的气相产物引入精提塔,进行进一步分离。
精提塔的塔盘和粗提塔相似,但操作条件和设定略有不同。
5.最后,从精提塔底部收集出塔床液相产物和从塔顶收集出的气相产物。
根据实验要求,验证分离效果和产物组分。
实验结果:通过模拟实验,我们成功地实现了双塔精馏单元的分离过程。
在不同的操作条件下,我们获得了不同的产物组分。
通过对产物组分的分析,我们发现随着操作条件的改变,产物组分也发生变化。
在实验过程中,我们还发现了一些问题,如温度的控制、流量的调节等。
通过调整操作条件,我们解决了这些问题,并获得了较好的分离效果。
实验总结:通过该次仿真实训,我们深入了解了双塔精馏单元的原理和操作过程。
同时,我们也发现了一些需要改进的地方。
在以后的学习和实践中,我们将加强对于操作条件和工艺参数的掌握,以实现更好的分离效果。
另外,我们还发现了化工仿真实训的重要性和优势。
通过虚拟仿真实验,我们能够快速理解和掌握复杂的操作过程,大大提高了学习效率。
因此,我们将继续积极参与各类实训,以提升自己的实践能力和问题解决能力。
精馏塔仿DCS图
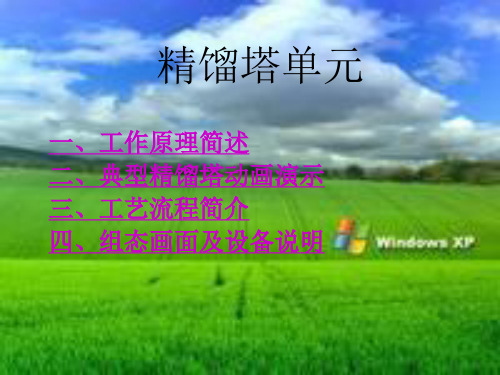
精馏塔单元一、工作原理简述二、典型精馏塔动画演示三、工艺流程简介四、组态画面及设备说明一、工作原理简述精馏是化工生产中分离互溶液体混合物的典型单元操作,其实质是多级蒸馏,即在一定压力下,利用互溶液体混合物各组分的沸点或饱和蒸汽压不同,使轻组分(沸点较低或饱和蒸汽压较高的组分)汽化,经多次部分液相汽化和部分气相冷凝,使气相中的轻组分和液相中的重组分浓度逐渐升高,从而实现分离。
精馏过程的主要设备有:精馏塔、再沸器、冷凝器、回流罐和输送设备等。
精馏塔以进料板为界,上部为精馏段,下部为提留段。
一定温度和压力的料液进入精馏塔后,轻组分在精馏段逐渐浓缩,离开塔顶后全部冷凝进入回流罐,一部分作为塔顶产品(也叫馏出液),另一部分被送入塔内作为回流液。
回流液的目的是补充塔板上的轻组分,使塔板上的液体组成保持稳定,保证精馏操作连续稳定地进行。
而重组分在提留段中浓缩后,一部分作为塔釜产品(也叫残液),一部分则经再沸器加热后送回塔中,为精馏操作提供一定量连续上升的蒸气气流。
二、精馏塔动画演示1.板式塔结构2.板式塔工作原理3.精馏塔实观4.精馏塔剖面图5.板式精馏塔1.板式塔结构2.板式塔工作原理3精馏塔实观4精馏塔剖面图5.板式精馏塔三、工艺流程简介本单元是一种加压精馏操作,原料液为脱丙烷塔塔釜的混合液,分离后馏出液为高纯度的C4产品,残液要是C5以上组分。
67.80C的原料液经流量调节器FIC101控制流量(14056Kg/h)后,从精馏塔DA405的第16块塔板(全塔共32块塔版)进料。
塔顶蒸气经全凝器EA419冷凝为液体后进入回流罐FA408;回流罐FA408的液体由泵GA412A/B抽出,一部分作为回流液由调节器FC104控制流量(9664KG/H)送回DA405第32层塔板;另一部分则作为产品,其流量由调节器FC103控制(6707Kg/h)。
回流罐的液位由调节器LC103与FC103构成的串级控制回路控制。
东方仿真--精馏塔单元
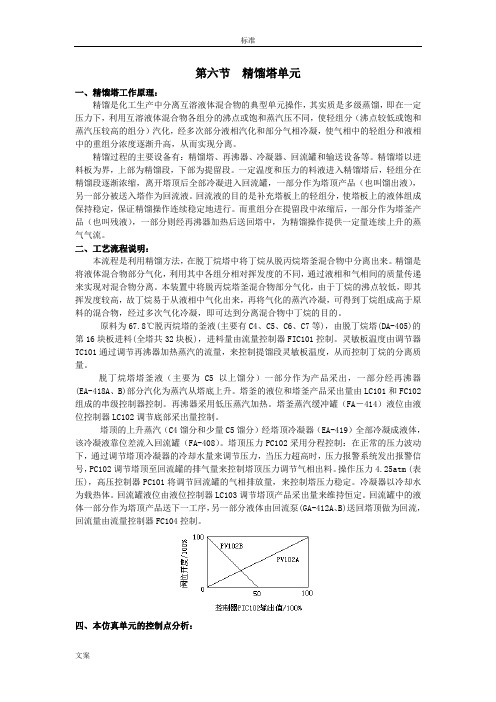
第六节精馏塔单元一、精馏塔工作原理:精馏是化工生产中分离互溶液体混合物的典型单元操作,其实质是多级蒸馏,即在一定压力下,利用互溶液体混合物各组分的沸点或饱和蒸汽压不同,使轻组分(沸点较低或饱和蒸汽压较高的组分)汽化,经多次部分液相汽化和部分气相冷凝,使气相中的轻组分和液相中的重组分浓度逐渐升高,从而实现分离。
精馏过程的主要设备有:精馏塔、再沸器、冷凝器、回流罐和输送设备等。
精馏塔以进料板为界,上部为精馏段,下部为提留段。
一定温度和压力的料液进入精馏塔后,轻组分在精馏段逐渐浓缩,离开塔顶后全部冷凝进入回流罐,一部分作为塔顶产品(也叫馏出液),另一部分被送入塔作为回流液。
回流液的目的是补充塔板上的轻组分,使塔板上的液体组成保持稳定,保证精馏操作连续稳定地进行。
而重组分在提留段中浓缩后,一部分作为塔釜产品(也叫残液),一部分则经再沸器加热后送回塔中,为精馏操作提供一定量连续上升的蒸气气流。
二、工艺流程说明:本流程是利用精馏方法,在脱丁烷塔中将丁烷从脱丙烷塔釜混合物中分离出来。
精馏是将液体混合物部分气化,利用其中各组分相对挥发度的不同,通过液相和气相间的质量传递来实现对混合物分离。
本装置中将脱丙烷塔釜混合物部分气化,由于丁烷的沸点较低,即其挥发度较高,故丁烷易于从液相中气化出来,再将气化的蒸汽冷凝,可得到丁烷组成高于原料的混合物,经过多次气化冷凝,即可达到分离混合物中丁烷的目的。
原料为67.8℃脱丙烷塔的釜液(主要有C4、C5、C6、C7等),由脱丁烷塔(DA-405)的第16块板进料(全塔共32块板),进料量由流量控制器FIC101控制。
灵敏板温度由调节器TC101通过调节再沸器加热蒸汽的流量,来控制提馏段灵敏板温度,从而控制丁烷的分离质量。
脱丁烷塔塔釜液(主要为C5以上馏分)一部分作为产品采出,一部分经再沸器(EA-418A、B)部分汽化为蒸汽从塔底上升。
塔釜的液位和塔釜产品采出量由LC101和FC102组成的串级控制器控制。
精馏塔单元仿真培训 操作说明书

精馏塔单元仿真培训操作说明书欧倍尔北京欧倍尔软件开发有限公司2013年4月地址:北京海淀区清河强佑新城甲一号楼14层1431室邮编:100085I目录一、工艺流程简介 (1)1、工艺原理........................................................................................................................................12、工艺流程........................................................................................................................................1二、工艺卡片. (1)1、设备列表........................................................................................................................................12、现场阀门........................................................................................................................................23、仪表列表........................................................................................................................................34、物流平衡数据................................................................................................................................3三、复杂控制说明.. (3)1、分程控制........................................................................................................................................32、串级控制系统................................................................................................................................4四、控制规程. (4)1、冷态开车 (4)1.1、开工准备.............................................................................................................................41.2、进料过程.............................................................................................................................41.3、启动再沸器.........................................................................................................................41.4、建立回流.............................................................................................................................41.5、调整至正常.........................................................................................................................42、停车操作规程.. (5)2.1、降负荷.................................................................................................................................52.2、停进料和再沸器.................................................................................................................52.3、停回流.................................................................................................................................52.4降压、降温...........................................................................................................................53、事故设置. (6)3.1、停电.....................................................................................................................................63.2、冷却水中断.........................................................................................................................63.3、热蒸汽压力过高.................................................................................................................63.4、热蒸汽压力过低.................................................................................................................73.5、回流泵故障.........................................................................................................................73.6、回流控制阀FV304阀卡. (7)五、PID 图...................................................................................................................................................8六、仿真画面. (8)一、工艺流程简介1、工艺原理精馏是将液体混合物部分汽化,利用其中各组分相对挥发度的不同,通过液相和气相相同的质量传递来实现对混合物的分离。
ZSDZB2018-064化工仿真实训软件技术参数

1、认识实习,真实再现炼油化工过程的设备,并配合matrix系统,可进行设备结构、工艺原理的深度学习;
2、生产实习,可进行装置开工、停工,重演工业级生产过程;
3、事故处理,还原工厂中真实事故状况,如蒸汽中断、炉管破裂…培养学生应变、解决问题能力;
(2)调节阀门模块:主要用于现场和DCS操作中,对现场阀和控制阀的操作,根据阀门开度大小,仪表显示不同,要求每个单元至少有20个阀门可以进行调节。
(3)查找阀门模块:显示需要查找阀门方向与距离阀门距离,用多少米显示。
(4)知识点模块:每个单元有不少于5个动画或视频的知识点。
(5)报警模块:每个单元有不少于3个报警点,发生警报时有警报声,并且在发生事故点有汉字提示报警原因。
5、主要软件工况要求
(1)CO2压缩机工艺3D仿真软件包含冷态开车工况,正常操作工况,正常停工工况,事故处理不少于10个。
(2)固定床反应器工艺3D仿真软件包含冷态开车,正常停车,正常运行,事故处理不少于7个。
(3)管式加热炉单元3D虚拟现实仿真软件包含冷态开车工况,冷态开车,正常停车,正常操作,事故处理不少于8个。
3、联合操作3D场景中可以观察到同组参与培训人员操作的角色。
4、支持学员操作总成绩、细化步骤得分情况的浏览、保存、排版打印等功能。
(五)化工单元CSTS仿真(3D)
1、主要内容
(1)CO2压缩机工艺3D仿真软件
(2)固定床反应器工艺3D仿真软件
(3)管式加热炉单元3D虚拟现实仿真软件
(4)间歇釜反应单元3D虚拟现实仿真软件
3、设备
至少包含沉降室、再生器、提升管反应器、冷催化剂罐、热催化剂罐、催化裂化新鲜原料缓冲罐、回炼油罐、外取热器、余热锅炉、油浆-裂化原料换热器等10种主要设备,要求详细列出。
精馏塔的仿真操作讲解

当塔釜液位无法维持时(>35%),逐渐打开fc102 当塔釜产品采出量稳定在7349kg/h,将fc102设置为自动 设定fc102为7349kg/h 将lc101设置为自动 设定lc101为50% 将fc102设置为串级 塔釜产品采出量稳定在7349kg/h 打开fv103前截止阀v41 打开fv103后截止阀v42 当回流罐液位无法维持时,逐渐打开fv103,采出塔顶产品 待产出稳定在6707kg/h,将fc103设置为自动 设定fc103为6707kg/h 将lc103设置为自动 设定lc103为50% 将fc103设置为串级
停电的操作规程编制
将pc101设置为手动 打开回流罐放空阀pv101 将fic101设置为手动 关闭fic101,停止进料 关闭fv101前截止阀v31 关闭fv101后截止阀v32 将tc101设置为手动 关闭tc101,停止加热蒸汽 关闭tv101前截止阀v33 关闭tv101后截止阀v34 将fc102设置为手动 关闭fc102,停止产品产出 关闭fv102前截止阀v39 关闭fv102后截止阀v40
冷态开车建立
打开回流泵GA412A入口阀V19 启动泵 打开泵出口阀V17 打开FV104前截止阀V43 打开FV104后截止阀V44 手动打开调节阀FV104(开度>40%),维持回流罐液位升至40%以上
冷态开车
待塔压稳定后,将PC101设为自动 设定PC101为4.25atm 塔压完全稳定后,将PC101设置为5.0atm 待进料量稳定在14056kg/h,将FIC101设置为自动 设定FIC101为14056kg/h 热敏版温度稳定在89.3度,塔釜温度TI102稳定在109.3度 进料量稳定在14056kg/h 灵敏板温度tc101 塔釜温度稳定在109.3度 将调节阀fv104开至50% 当fc104流量稳定在9664kg/h将其设为自动 设定fc104为9664Kg/h 打开fv102前截止阀v39 打开fv102后截止阀v40
东方仿真_精馏塔单元

第六节精馏塔单元一、精馏塔工作原理:精馏是化工生产中分离互溶液体混合物的典型单元操作,其实质是多级蒸馏,即在一定压力下,利用互溶液体混合物各组分的沸点或饱和蒸汽压不同,使轻组分(沸点较低或饱和蒸汽压较高的组分)汽化,经多次部分液相汽化和部分气相冷凝,使气相中的轻组分和液相中的重组分浓度逐渐升高,从而实现分离。
精馏过程的主要设备有:精馏塔、再沸器、冷凝器、回流罐和输送设备等。
精馏塔以进料板为界,上部为精馏段,下部为提留段。
一定温度和压力的料液进入精馏塔后,轻组分在精馏段逐渐浓缩,离开塔顶后全部冷凝进入回流罐,一部分作为塔顶产品(也叫馏出液),另一部分被送入塔内作为回流液。
回流液的目的是补充塔板上的轻组分,使塔板上的液体组成保持稳定,保证精馏操作连续稳定地进行。
而重组分在提留段中浓缩后,一部分作为塔釜产品(也叫残液),一部分则经再沸器加热后送回塔中,为精馏操作提供一定量连续上升的蒸气气流。
二、工艺流程说明:本流程是利用精馏方法,在脱丁烷塔中将丁烷从脱丙烷塔釜混合物中分离出来。
精馏是将液体混合物部分气化,利用其中各组分相对挥发度的不同,通过液相和气相间的质量传递来实现对混合物分离。
本装置中将脱丙烷塔釜混合物部分气化,由于丁烷的沸点较低,即其挥发度较高,故丁烷易于从液相中气化出来,再将气化的蒸汽冷凝,可得到丁烷组成高于原料的混合物,经过多次气化冷凝,即可达到分离混合物中丁烷的目的。
原料为67.8℃脱丙烷塔的釜液(主要有C4、C5、C6、C7等),由脱丁烷塔(DA-405)的第16块板进料(全塔共32块板),进料量由流量控制器FIC101控制。
灵敏板温度由调节器TC101通过调节再沸器加热蒸汽的流量,来控制提馏段灵敏板温度,从而控制丁烷的分离质量。
脱丁烷塔塔釜液(主要为C5以上馏分)一部分作为产品采出,一部分经再沸器(EA-418A、B)部分汽化为蒸汽从塔底上升。
塔釜的液位和塔釜产品采出量由LC101和FC102组成的串级控制器控制。
煤化工仿真实训指导书

仿真培训系统操作说明书目录第一章甲醇合成一、甲醇概述甲醇(分子式:CH3OH)又名木醇或木酒精,是一种透明、无色、易燃、有毒的液体,略带酒精味。
熔点-97.8℃,沸点64.8℃,闪点12.22℃,自燃点47℃,相对密度0.7915,爆炸极限下限6%,上限36.5%,能与水、乙醇、乙醚、苯、丙酮和大多数有机溶剂相混溶。
它是重要有机化工原料和优质燃料。
主要用于制造甲醛、醋酸、氯甲烷、甲氨、硫酸二甲脂等多种有机产品,也是农药、医药的重要原料之一。
甲醇亦可代替汽油作燃料使用。
生产甲醇的方法有多种,早期用木材或木质素干馏法制甲醇的方法,今天在工业上已经被淘汰了。
氯甲烷水解法也可以生产甲醇,但因水解法价格昂贵,没有得到工业上的应用。
甲烷部分氧化法可以生产甲醇,这种制甲醇的方法工艺流程简单,建设投资节省,但是,这种氧化过程不易控制,常因深度氧化生成碳的氧化物和水,而使原料和产品受到很大损失,因此甲烷部分氧化法制甲醇的方法仍未实现工业化。
目前工业上几乎都是采用一氧化碳、二氧化碳加压催化氢化法合成甲醇。
典型的流程包括原料气制造、原料气净化、甲醇合成、粗甲醇精馏等工序。
天然气、石脑油、重油、煤及其加工产品(焦炭、焦炉煤气)、乙炔尾气等均可作为生产甲醇合成气的原料。
天然气是制造甲醇的主要原料,主要组分是甲烷,还含有少量的其他烷烃、烯烃与氮气。
以天然气生产甲醇原料气有蒸汽转化、催化部分氧化、非催化部分氧化等方法,其中蒸汽转化法应用得最广泛,它是在管式炉中常压或加压下进行的。
由于反应吸热必须从外部供热以保持所要求的转化温度,一般是在管间燃烧某种燃料气来实现,转化用的蒸汽直接在装置上靠烟道气和转化气的热量制取。
由于天然气蒸汽转化法制的合成气中,氢过量而一氧化碳与二氧化碳量不足,工业上解决这个问题的方法一是采用添加二氧化碳的蒸汽转化法,以达到合适的配比,二氧化碳可以外部供应,也可以由转化炉烟道气中回收。
另一种方法是以天然气为原料的二段转化法,即在第一段转化中进行天然气的蒸汽转化,只有约1/4的甲烷进行反应;第二段进行天然气的部分氧化,不仅所得合成气配比合适而且由于第二段反应温度提高到800℃以上,残留的甲烷量可以减少,增加了合成甲醇的有效气体组分。
化工单元操作仿真实训总结
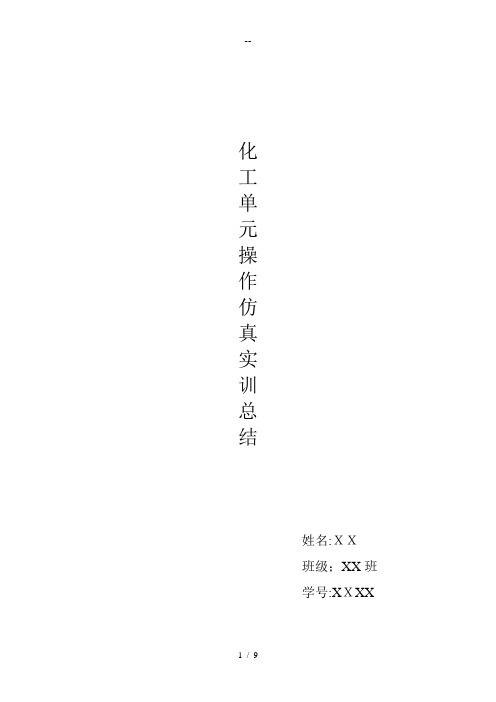
化工单元操作仿真实训总结姓名:XX班级;XX班学号:XXXX目录一、实训内容1、精馏塔仿真2、液位控制仿真3、吸收解吸仿真4、萃取仿真5、灌区仿真6、真空仿真二、仿真总结一、实训内容1、精馏塔仿真1.1操作原理:精馏原理精馏操作迫使混合物的气、液两相在精馏塔体中作逆向流动,在互相接触过程中,液相中的轻组分逐渐转入气相,而气相中的重组分则逐渐进入液相。
精馏过程本质上是一种传质过程,也伴随着传热。
在恒定压力下,对单组分液体在沸腾时继续加热,其温度保持不变。
但对于多组分的理想溶液来说, 在恒定压力下,沸腾溶液的温度却是可变的。
一般而言,在恒定压力下,溶液气液相平衡与其组分有关。
高沸点组分的浓度越高,溶液平衡温度越高。
与纯物质的气液平衡相比较,溶液气液平衡的一个特点是:在平衡态下,气相浓度与液相浓度是不相同的。
一般情况下,气相中的低沸点组分的浓度高于它在液相中的数值.对于纯组分的气液相平衡,把恒定压力下的平衡温度称为该压力下的沸点或冷凝点。
但对于处在相平衡的溶液,则把平衡温度称为在该压力下某气相浓度的露点温度或对应的液相浓度的泡点温度。
对于同一气相和液相来说,露点温度与泡点一般是不相等的,前者比后者高。
1.2工艺流程:进料及排放不凝气启动再沸器建立回流调整至正常1.3仿真图:2、液位控制仿真2.1操作原理:缓冲罐V101仅一股来料,8Kg/cm2压力的液体通过调节产供阀FIC101向罐V101充液,此罐压力由调节阀PIC101分程控制,缓冲罐压力高于分程点(5.0Kg/cm2)时,PV101B自动打开泄压,压力低于分程点时,PV101B自动关闭,PV101A自动打开给罐充压,使V101压力控制在5Kg/cm2。
缓冲罐V101液位调节器LIC101和流量调节阀FIC102串级调节,一般液位正常控制在50%左右,自V101底抽出液体通过泵P101A或P101B(备用泵)打入罐V102,该泵出口压力一般控制在9Kg/cm2,FIC102流量正常控制在20000Kg/hr。
精馏塔

文档编号:TSS_C4.DOC精馏塔单元仿真培训系统操作说明书北京东方仿真软件技术有限公司二〇〇六年十月目录一、工艺流程说明 21、工艺说明 22、本单元复杂控制方案说明 23、设备一览 3二、精馏单元操作规程 31、冷态开车操作规程 32、正常操作规程 43、停车操作规程 54、仪表一览表 6三、事故设置一览7四、仿真界面9附:思考题11一、工艺流程说明1、工艺说明本流程是利用精馏方法,在脱丁烷塔中将丁烷从脱丙烷塔釜混合物中分离出来。
精馏是将液体混合物部分气化,利用其中各组分相对挥发度的不同,通过液相和气相间的质量传递来实现对混合物分离。
本装置中将脱丙烷塔釜混合物部分气化,由于丁烷的沸点较低,即其挥发度较高,故丁烷易于从液相中气化出来,再将气化的蒸汽冷凝,可得到丁烷组成高于原料的混合物,经过多次气化冷凝,即可达到分离混合物中丁烷的目的。
原料为67.8℃脱丙烷塔的釜液(主要有C4、C5、C6、C7等),由脱丁烷塔(DA-405)的第16块板进料(全塔共32块板),进料量由流量控制器FIC101控制。
灵敏板温度由调节器TC101通过调节再沸器加热蒸汽的流量,来控制提馏段灵敏板温度,从而控制丁烷的分离质量。
脱丁烷塔塔釜液(主要为C5以上馏分)一部分作为产品采出,一部分经再沸器(EA-418A、B)部分汽化为蒸汽从塔底上升。
塔釜的液位和塔釜产品采出量由LC101和FC102组成的串级控制器控制。
再沸器采用低压蒸汽加热。
塔釜蒸汽缓冲罐(FA-414)液位由液位控制器LC102调节底部采出量控制。
塔顶的上升蒸汽(C4馏分和少量C5馏分)经塔顶冷凝器(EA-419)全部冷凝成液体,该冷凝液靠位差流入回流罐(FA-408)。
塔顶压力PC102采用分程控制:在正常的压力波动下,通过调节塔顶冷凝器的冷却水量来调节压力,当压力超高时,压力报警系统发出报警信号,PC102调节塔顶至回流罐的排气量来控制塔顶压力调节气相出料。
精馏分离的仿真设计
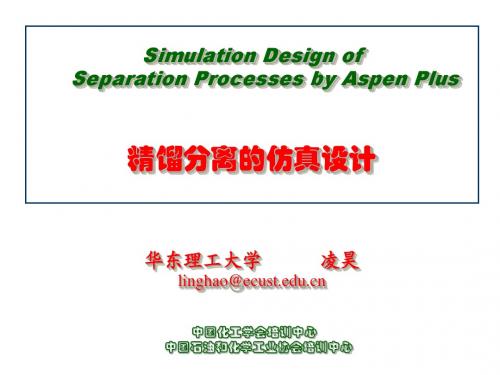
(5) 操作设定
操作设定从十个选项中选择:
1、回流比(Reflux Ratio)
2、回流速率(Reflux Rate)
3、馏出物速率(Distillate Rate)
4、塔底物速率(Bottoms Rate) 5、上升蒸汽速率(Boilup Rate)
操作设定从十个选项中选择:
6、上升蒸汽比(Boilup Ratio) 7、上升蒸汽/进料比(Boilup to Feed Ratio)
(Both reflux and liquid distillate are subcooled)
/仅仅回流物过冷 (Only reflux is subcooled) 2)过冷指标(Subcooling specification) 过冷物温度 (Subcooled temperature) /过冷度 (Degrees of subcoo:
4、冷凝器设定 ( Condenser specifications) (1) 全凝器 ( Total condenser) (2) 带汽相馏出物的部分冷凝器 ( Partial condenser with vapor distillate) (3) 带汽、液相馏出物的部分冷凝器 ( Partial condenser with vapor and liquid distillate)
(8) 冷凝器
冷凝器设定有两组参数:
1、冷凝器指标(Condenser Specification) 仅仅应用于部分冷凝器。只需指定冷凝温度 (Temperature)和蒸汽分率(Vapor Fraction)两个参数之一。
冷凝器设定有两组参数:
2、过冷态(Subcooling) 1)过冷选项(Subcooling option) 回流物和馏出物都过冷
[练习]操作员培训仿真系统OTS技术知识
![[练习]操作员培训仿真系统OTS技术知识](https://img.taocdn.com/s3/m/098e85253868011ca300a6c30c2259010202f386.png)
仿真培训OTS系统知识操作员培训系统(Operator Training System,OTS)在国内还不是特别普及,只是一些大的化工/石化/炼油企业在用,比如使用国外品牌的OTS包括Honywell,Invensys和Y okogawa等。
总体的认知度在企业界还是不高的。
但是在国外,工厂建厂之初都是需要OTS系统的,相信这块以后会越来越普及,市场前景也会越来越好。
OTS的核心是仿真模拟技术,即在计算机上仿真模拟真实生产过程,建立对应的“虚拟工厂”,包含其生产过程及其控制逻辑。
在此基础上,实现对工厂过程和控制逻辑的模拟、调整和培训。
仿真相关的知识相信很多人是大牛,就不详述了。
只是想提醒一点,OTS中的模拟与平时大家所用的ASPEN PLUS等设计软件中的模拟不同,前者是动态模拟过程,后者是稳态模拟过程。
从数学建模的角度讲,它们的区别在于,前者内部建立的是微分+代数方程,后者建立的则是代数方程。
为什么OTS需要动态模拟呢?因为OTS需要模拟开车、停车等岗位操作过程,因此必然需要关注时间这一维的影响。
因此OTS仿真与ASPEN PLUS类的软件不同,前者更注重动态的变化过程,后者更关注稳态的精度。
OTS操作员培训系统有三方参与者:教师(教师大厅)、虚拟工厂(仿真服务器)、操作员(操作员站)。
教师大厅上可以监控每位操作员的情况。
而仿真服务器作用是运行作为“虚拟工厂”的仿真模型,仿真模型是在建模平台(比如奥秘仿真®)上建立的基于严格机理的动态模型,能高精度地模拟工厂的生产流程,并模拟开车、停车、各种故障处理过程。
仿真服务器能够自动运行仿真模型,最终用户不需要关心任何建模的过程和形式。
关于操作员站,一般为客户提供两类产品选择:一类是真实的DCS 操作员站软件,另一类是仿DCS的HMI组态软件。
前者的优势是操作员站能够真实再现工厂中控室的情形,让学员有身临其境的真实感觉。
后者一般需要符合工业标准OPC协议。
- 1、下载文档前请自行甄别文档内容的完整性,平台不提供额外的编辑、内容补充、找答案等附加服务。
- 2、"仅部分预览"的文档,不可在线预览部分如存在完整性等问题,可反馈申请退款(可完整预览的文档不适用该条件!)。
- 3、如文档侵犯您的权益,请联系客服反馈,我们会尽快为您处理(人工客服工作时间:9:00-18:30)。
精馏塔单元仿真培训系统操作说明书目录一、工艺流程说明 (2)1、工艺说明 (2)2、本单元复杂控制方案说明 (2)3、设备一览 (3)二、精馏单元操作规程 (3)1、冷态开车操作规程 (3)2、正常操作规程 (4)3、停车操作规程 (5)4、仪表一览表 (6)三、事故设置一览 (7)四、仿真界面 (9)附:思考题 (11)一、工艺流程说明1、工艺说明本流程是利用精馏方法,在脱丁烷塔中将丁烷从脱丙烷塔釜混合物中分离出来。
精馏是将液体混合物部分气化,利用其中各组分相对挥发度的不同,通过液相和气相间的质量传递来实现对混合物分离。
本装置中将脱丙烷塔釜混合物部分气化,由于丁烷的沸点较低,即其挥发度较高,故丁烷易于从液相中气化出来,再将气化的蒸汽冷凝,可得到丁烷组成高于原料的混合物,经过多次气化冷凝,即可达到分离混合物中丁烷的目的。
原料为67.8℃脱丙烷塔的釜液(主要有C4、C5、C6、C7等),由脱丁烷塔(DA-405)的第16块板进料(全塔共32块板),进料量由流量控制器FIC101控制。
灵敏板温度由调节器TC101通过调节再沸器加热蒸汽的流量,来控制提馏段灵敏板温度,从而控制丁烷的分离质量。
脱丁烷塔塔釜液(主要为C5以上馏分)一部分作为产品采出,一部分经再沸器(EA-418A、B)部分汽化为蒸汽从塔底上升。
塔釜的液位和塔釜产品采出量由LC101和FC102组成的串级控制器控制。
再沸器采用低压蒸汽加热。
塔釜蒸汽缓冲罐(FA-414)液位由液位控制器LC102调节底部采出量控制。
塔顶的上升蒸汽(C4馏分和少量C5馏分)经塔顶冷凝器(EA-419)全部冷凝成液体,该冷凝液靠位差流入回流罐(FA-408)。
塔顶压力PC102采用分程控制:在正常的压力波动下,通过调节塔顶冷凝器的冷却水量来调节压力,当压力超高时,压力报警系统发出报警信号,PC102调节塔顶至回流罐的排气量来控制塔顶压力调节气相出料。
操作压力 4.25atm (表压),高压控制器PC101将调节回流罐的气相排放量,来控制塔内压力稳定。
冷凝器以冷却水为载热体。
回流罐液位由液位控制器LC103调节塔顶产品采出量来维持恒定。
回流罐中的液体一部分作为塔顶产品送下一工序,另一部分液体由回流泵(GA-412A、B)送回塔顶做为回流,回流量由流量控制器FC104控制。
2、本单元复杂控制方案说明吸收解吸单元复杂控制回路主要是串级回路的使用,在吸收塔、解吸塔和产品罐中都使用了液位与流量串级回路。
串级回路:是在简单调节系统基础上发展起来的。
在结构上,串级回路调节系统有两个闭合回路。
主、副调节器串联,主调节器的输出为副调节器的给定值,系统通过副调节器的输出操纵调节阀动作,实现对主参数的定值调节。
所以在串级回路调节系统中,主回路是定值调节系统,副回路是随动系统。
分程控制:就是由一只调节器的输出信号控制两只或更多的调节阀,每只调节阀在调节器的输出信号的某段范围中工作。
具体实例:DA405的塔釜液位控制LC101和和塔釜出料FC102构成一串级回路。
FC102.SP随LC101.OP的改变而变化。
PIC102为一分程控制器,分别控制PV102A和PV102B,当PC102.OP逐渐开大时,PV102A从0逐渐开大到100;而PV102B从100逐渐关小至0。
3、设备一览DA-405:脱丁烷塔EA-419:塔顶冷凝器FA-408:塔顶回流罐GA-412A、B:回流泵EA-418A、B:塔釜再沸器FA-414:塔釜蒸汽缓冲罐二、精馏单元操作规程1、冷态开车操作规程本操作规程仅供参考,详细操作以评分系统为准。
装置冷态开工状态为精馏塔单元处于常温、常压氮吹扫完毕后的氮封状态,所有阀门、机泵处于关停状态。
1.1、进料过程(1)开FA-408顶放空阀PC101排放不凝气,稍开FIC101调节阀(不超过20%),向精馏塔进料。
(2)进料后,塔内温度略升,压力升高。
当压力PC101升至0.5atm时,关闭PC101调节阀投自动,并控制塔压不超过4.25atm(如果塔内压力大幅波动,改回手动调节稳定压力)。
1.2、启动再沸器(1)当压力PC101升至0.5atm时,打开冷凝水PC102调节阀至50%;塔压基本稳定在4.25atm后,可加大塔进料(FIC101开至50%左右)。
(2)待塔釜液位LC101升至20%以上时,开加热蒸汽入口阀V13,再稍开TC101调节阀,给再沸器缓慢加热,并调节TC101阀开度使塔釜液位LC101维持在40%-60%。
待FA-414液位LC102升至50%时,并投自动,设定值为50%。
1.3、建立回流随着塔进料增加和再沸器、冷凝器投用,塔压会有所升高。
回流罐逐渐积液。
(1)塔压升高时,通过开大PC102的输出,改变塔顶冷凝器冷却水量和旁路量来控制塔压稳定。
(2)当回流罐液位LC103升至20%以上时,先开回流泵GA412A/B的入口阀V19,再启动泵,再开出口阀V17,启动回流泵。
(3)通过FC104的阀开度控制回流量,维持回流罐液位不超高,同时逐渐关闭进料,全回流操作。
1.4、调整至正常(1)当各项操作指标趋近正常值时,打开进料阀FIC101。
(2)逐步调整进料量FIC101至正常值。
(3)通过TC101调节再沸器加热量使灵敏板温度TC101达到正常值。
(4)逐步调整回流量FC104至正常值。
(5)开FC103和FC102出料,注意塔釜、回流罐液位。
(6)将各控制回路投自动,各参数稳定并与工艺设计值吻合后,投产品采出串级。
2、正常操作规程2.1、正常工况下的工艺参数(1)进料流量FIC101设为自动,设定值为14056 kg/hr。
(2)塔釜采出量FC102设为串级,设定值为7349 kg/hr,LC101设自动,设定值为50%。
(3)塔顶采出量FC103设为串级,设定值为6707 kg/hr。
(4)塔顶回流量FC104设为自动,设定值为9664 kg/hr。
(5)塔顶压力PC102设为自动,设定值为4.25atm,PC101设自动,设定值为5.0atm。
(6)灵敏板温度TC101设为自动,设定值为89.3 ℃。
(7)FA-414液位LC102设为自动,设定值为50%。
(8)回流罐液位LC103设为自动,设定值为50%。
2.2、主要工艺生产指标的调整方法(1)质量调节:本系统的质量调节采用以提馏段灵敏板温度作为主参数,以再沸器和加热蒸汽流量的调节系统,以实现对塔的分离质量控制。
(2)压力控制:在正常的压力情况下,由塔顶冷凝器的冷却水量来调节压力,当压力高于操作压力4.25atm(表压)时,压力报警系统发出报警信号,同时调节器PC101将调节回流罐的气相出料,为了保持同气相出料的相对平衡,该系统采用压力分程调节。
(3)液位调节:塔釜液位由调节塔釜的产品采出量来维持恒定。
设有高低液位报警。
回流罐液位由调节塔顶产品采出量来维持恒定。
设有高低液位报警。
(4)流量调节:进料量和回流量都采用单回路的流量控制;再沸器加热介质流量,由灵敏板温度调节。
3、停车操作规程本操作规程仅供参考,详细操作以评分系统为准。
3.1、降负荷(1)逐步关小FIC101调节阀,降低进料至正常进料量的70%。
(2)在降负荷过程中,保持灵敏板温度TC101的稳定性和塔压PC102的稳定,使精馏塔分离出合格产品。
(3)在降负荷过程中,尽量通过FC103排出回流罐中的液体产品,至回流罐液位LC104在20%左右。
(4)在降负荷过程中,尽量通过FC102排出塔釜产品,使LC101降至30%左右。
3.2、停进料和再沸器在负荷降至正常的70%,且产品已大部采出后,停进料和再沸器。
(1)关FIC101调节阀,停精馏塔进料。
(2)关TC101调节阀和V13或V16阀,停再沸器的加热蒸汽。
(3)关FC102调节阀和FC103调节阀,停止产品采出。
(4)打开塔釜泄液阀V10,排不合格产品,并控制塔釜降低液位。
(5)手动打开LC102调节阀,对FA-114泄液。
3.3、停回流(1)停进料和再沸器后,回流罐中的液体全部通过回流泵打入塔,以降低塔内温度。
(2)当回流罐液位至0时,关FC104调节阀,关泵出口阀V17(或V18),停泵GA412A(或GA412B),关入口阀V19(或V20),停回流。
(3)开泄液阀V10排净塔内液体。
3.4 降压、降温(1)打开PC101调节阀,将塔压降至接近常压后,关PC101调节阀。
(2)全塔温度降至50℃左右时,关塔顶冷凝器的冷却水(PC102的输出至0)。
精馏塔单元仿真培训系统操作说明书4、仪表一览表6三、事故设置一览下列事故处理操作仅供参考,详细操作以评分系统为准。
1、热蒸汽压力过高原因:热蒸汽压力过高。
现象:加热蒸汽的流量增大,塔釜温度持续上升。
处理:适当减小TC101的阀门开度。
2、热蒸汽压力过低原因:热蒸汽压力过低。
现象:加热蒸汽的流量减小,塔釜温度持续下降。
处理:适当增大TC101的开度。
3.冷凝水中断原因:停冷凝水。
现象:塔顶温度上升,塔顶压力升高。
处理:(1)开回流罐放空阀PC101保压。
(2)手动关闭FC101,停止进料。
(3)手动关闭TC101,停加热蒸汽。
(4)手动关闭FC103和FC102,停止产品采出。
(5)开塔釜排液阀V10,排不合格产品。
(6)手动打开LIC102,对FA114泄液。
(7)当回流罐液位为0时,关闭FIC104。
(8)关闭回流泵出口阀V17/V18。
(9)关闭回流泵GA424A/GA424B。
(10)关闭回流泵入口阀V19/V20。
(11)待塔釜液位为0时,关闭泄液阀V10。
(12)待塔顶压力降为常压后,关闭冷凝器。
4.停电原因:停电。
现象:回流泵GA412A停止,回流中断。
处理:(1)手动开回流罐放空阀PC101泄压。
(2)手动关进料阀FIC101。
(3)手动关出料阀FC102和FC103。
(4)手动关加热蒸汽阀TC101。
(5)开塔釜排液阀V10和回流罐泄液阀V23,排不合格产品。
(6)手动打开LIC102,对FA114泄液。
(7)当回流罐液位为0时,关闭V23。
(8)关闭回流泵出口阀V17/V18。
(9)关闭回流泵GA424A/GA424B。
(10)关闭回流泵入口阀V19/V20。
(11)待塔釜液位为0时,关闭泄液阀V10。
(12)待塔顶压力降为常压后,关闭冷凝器。
5.回流泵故障原因:回流泵GA-412A泵坏。
现象:GA-412A断电,回流中断,塔顶压力、温度上升。
处理:(1)开备用泵入口阀V20。
(2)启动备用泵GA412B。
(3)开备用泵出口阀V18。
(4)关闭运行泵出口阀V17。
(5)停运行泵GA412A。
(6)关闭运行泵入口阀V19。
6.回流控制阀FC104阀卡原因:回流控制阀FC104阀卡。