浅析我国氨(NH3)合成化工技术工艺
合成氨的工艺流程
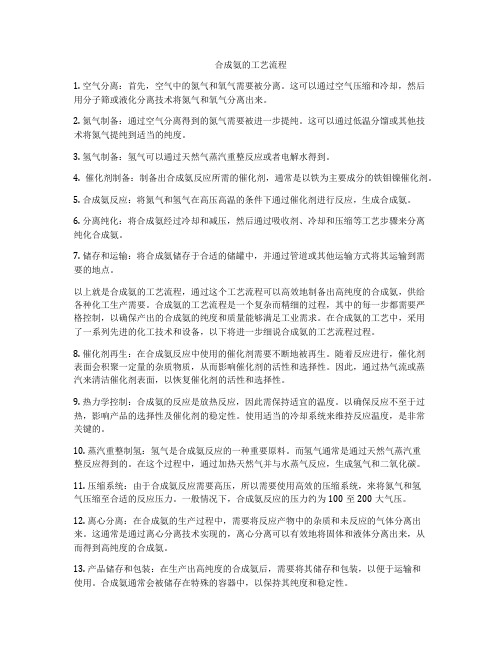
合成氨的工艺流程1. 空气分离:首先,空气中的氮气和氧气需要被分离。
这可以通过空气压缩和冷却,然后用分子筛或液化分离技术将氮气和氧气分离出来。
2. 氮气制备:通过空气分离得到的氮气需要被进一步提纯。
这可以通过低温分馏或其他技术将氮气提纯到适当的纯度。
3. 氢气制备:氢气可以通过天然气蒸汽重整反应或者电解水得到。
4. 催化剂制备:制备出合成氨反应所需的催化剂,通常是以铁为主要成分的铁钼镍催化剂。
5. 合成氨反应:将氮气和氢气在高压高温的条件下通过催化剂进行反应,生成合成氨。
6. 分离纯化:将合成氨经过冷却和减压,然后通过吸收剂、冷却和压缩等工艺步骤来分离纯化合成氨。
7. 储存和运输:将合成氨储存于合适的储罐中,并通过管道或其他运输方式将其运输到需要的地点。
以上就是合成氨的工艺流程,通过这个工艺流程可以高效地制备出高纯度的合成氨,供给各种化工生产需要。
合成氨的工艺流程是一个复杂而精细的过程,其中的每一步都需要严格控制,以确保产出的合成氨的纯度和质量能够满足工业需求。
在合成氨的工艺中,采用了一系列先进的化工技术和设备,以下将进一步细说合成氨的工艺流程过程。
8. 催化剂再生:在合成氨反应中使用的催化剂需要不断地被再生。
随着反应进行,催化剂表面会积聚一定量的杂质物质,从而影响催化剂的活性和选择性。
因此,通过热气流或蒸汽来清洁催化剂表面,以恢复催化剂的活性和选择性。
9. 热力学控制:合成氨的反应是放热反应,因此需保持适宜的温度。
以确保反应不至于过热,影响产品的选择性及催化剂的稳定性。
使用适当的冷却系统来维持反应温度,是非常关键的。
10. 蒸汽重整制氢:氢气是合成氨反应的一种重要原料。
而氢气通常是通过天然气蒸汽重整反应得到的。
在这个过程中,通过加热天然气并与水蒸气反应,生成氢气和二氧化碳。
11. 压缩系统:由于合成氨反应需要高压,所以需要使用高效的压缩系统,来将氮气和氢气压缩至合适的反应压力。
一般情况下,合成氨反应的压力约为100至200大气压。
合成氨的生产工艺流程
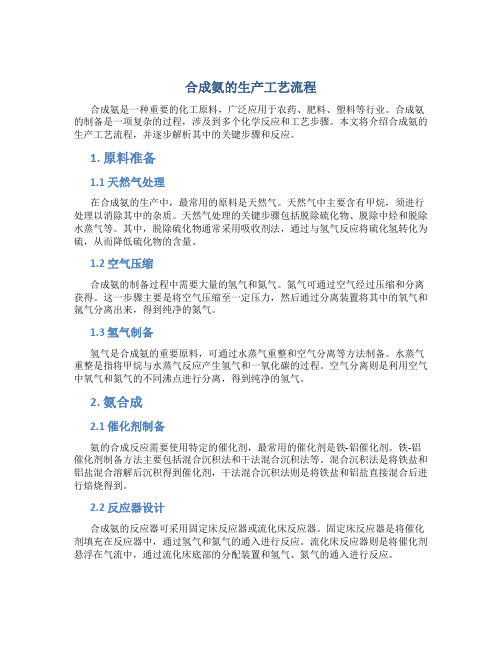
合成氨的生产工艺流程合成氨是一种重要的化工原料,广泛应用于农药、肥料、塑料等行业。
合成氨的制备是一项复杂的过程,涉及到多个化学反应和工艺步骤。
本文将介绍合成氨的生产工艺流程,并逐步解析其中的关键步骤和反应。
1. 原料准备1.1 天然气处理在合成氨的生产中,最常用的原料是天然气。
天然气中主要含有甲烷,须进行处理以消除其中的杂质。
天然气处理的关键步骤包括脱除硫化物、脱除中烃和脱除水蒸气等。
其中,脱除硫化物通常采用吸收剂法,通过与氢气反应将硫化氢转化为硫,从而降低硫化物的含量。
1.2 空气压缩合成氨的制备过程中需要大量的氢气和氮气。
氮气可通过空气经过压缩和分离获得。
这一步骤主要是将空气压缩至一定压力,然后通过分离装置将其中的氧气和氩气分离出来,得到纯净的氮气。
1.3 氢气制备氢气是合成氨的重要原料,可通过水蒸气重整和空气分离等方法制备。
水蒸气重整是指将甲烷与水蒸气反应产生氢气和一氧化碳的过程。
空气分离则是利用空气中氧气和氮气的不同沸点进行分离,得到纯净的氢气。
2. 氨合成2.1 催化剂制备氨的合成反应需要使用特定的催化剂,最常用的催化剂是铁-铝催化剂。
铁-铝催化剂制备方法主要包括混合沉积法和干法混合沉积法等。
混合沉积法是将铁盐和铝盐混合溶解后沉积得到催化剂,干法混合沉积法则是将铁盐和铝盐直接混合后进行焙烧得到。
2.2 反应器设计合成氨的反应器可采用固定床反应器或流化床反应器。
固定床反应器是将催化剂填充在反应器中,通过氢气和氮气的通入进行反应。
流化床反应器则是将催化剂悬浮在气流中,通过流化床底部的分配装置和氢气、氮气的通入进行反应。
2.3 反应条件合成氨的合成反应需要在一定的温度、压力和催化剂的存在下进行。
通常情况下,合成氨反应的温度约为350-450°C,压力约为200-300atm。
此外,还需要在反应器中加入适量的惰性气体(如氦气)以稀释氢气和氮气,以减少反应的热量和危险性。
2.4 反应过程合成氨的合成反应是一个多步骤的复杂过程。
合成氨合成工艺流程
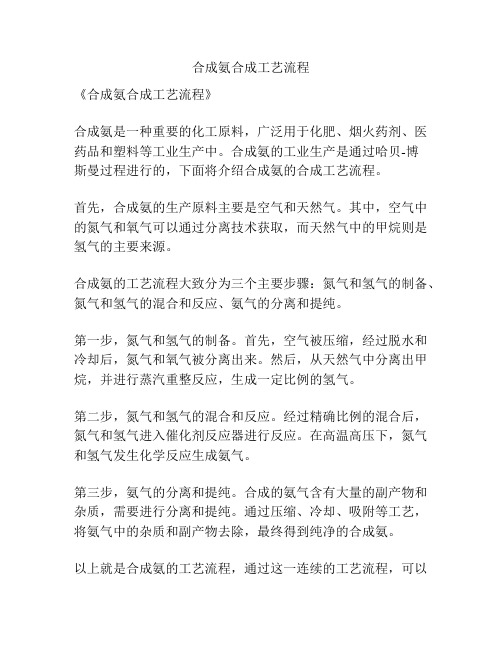
合成氨合成工艺流程
《合成氨合成工艺流程》
合成氨是一种重要的化工原料,广泛用于化肥、烟火药剂、医药品和塑料等工业生产中。
合成氨的工业生产是通过哈贝-博
斯曼过程进行的,下面将介绍合成氨的合成工艺流程。
首先,合成氨的生产原料主要是空气和天然气。
其中,空气中的氮气和氧气可以通过分离技术获取,而天然气中的甲烷则是氢气的主要来源。
合成氨的工艺流程大致分为三个主要步骤:氮气和氢气的制备、氮气和氢气的混合和反应、氨气的分离和提纯。
第一步,氮气和氢气的制备。
首先,空气被压缩,经过脱水和冷却后,氮气和氧气被分离出来。
然后,从天然气中分离出甲烷,并进行蒸汽重整反应,生成一定比例的氢气。
第二步,氮气和氢气的混合和反应。
经过精确比例的混合后,氮气和氢气进入催化剂反应器进行反应。
在高温高压下,氮气和氢气发生化学反应生成氨气。
第三步,氨气的分离和提纯。
合成的氨气含有大量的副产物和杂质,需要进行分离和提纯。
通过压缩、冷却、吸附等工艺,将氨气中的杂质和副产物去除,最终得到纯净的合成氨。
以上就是合成氨的工艺流程,通过这一连续的工艺流程,可以
高效地生产出合成氨,满足工业生产的需求。
合成氨的工艺流程是化学工程领域的重要研究课题,对于提高生产效率和减少能源消耗具有重要意义。
氨合成工艺技术方案

氨合成工艺技术方案氨合成是一种重要的化学反应,在工业生产中广泛应用于化肥、塑料、燃料等领域。
本文将介绍氨合成的工艺流程、反应机理、催化剂选择、工艺优化及安全措施等方面的技术方案。
一、工艺流程氨合成的工艺流程包括氮气和氢气的预处理、气体的混合、催化反应、分离和纯化等步骤。
具体的工艺流程如下:1.氮气和氢气的预处理氮气和氢气的纯度对合成氨的质量有重要影响,因此需要进行预处理。
氮气通过膜分离或吸附分离去除O2等杂质,然后通过压缩机提高压力。
氢气需要进行硫化处理,以去除有毒物质并防止催化剂中的中毒。
2.气体的混合氮气和氢气以一定比例混合,通常为1:3或1:2。
混合后的气体需要通过精密控制,在进入反应器前进行混合和压力调整。
3.催化反应混合后的气体通过加热和压力升高进入反应器,在特定的温度和催化剂作用下,发生化学反应,生成氨。
反应原理如下:N2(g) + 3H2(g) → 2NH3(g)该反应是一个放热反应,需要在适当的温度范围内进行,一般为350℃~550℃。
催化剂是反应中不可或缺的因素,常用的有铁、铝、钯等,通过特定的制造工艺调整催化剂的特性,以提高反应效率和选择性。
4.分离和纯化反应后的气体包含氨、氢气和氮气等组成部分,需要进行分离和纯化。
通常采用冷凝法和脱吸附法进行分离,日产量可达数百吨至几千吨不等。
二、反应机理氮气是一种非常稳定的分子,与氢气发生反应需要高能量折算,因此氨合成反应需要催化作用。
反应过程大致分为以下几个步骤:1.催化剂吸附催化剂表面存在一种特殊的吸附态,当氢气通过催化剂时,会对催化剂表面的活性位点发生吸附。
吸附后的氢分子变得容易分解,形成游离氢原子。
2.氢原子吸附催化剂表面活性位点上的游离氢原子会被氮气吸附,形成氢化氮离子。
3.合成氨生成两个氢化氮离子会发生反应,形成氨分子和游离氢原子,氨分子随即从催化剂表面解离。
N2 + 3H2 → 2NH34.游离氢原子再次吸附游离氢原子在催化剂表面进行再次吸附,形成新的反应循环。
合成氨的工艺流程
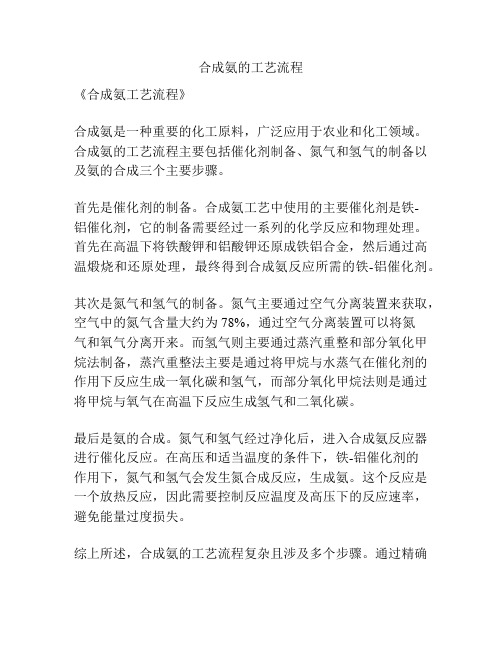
合成氨的工艺流程
《合成氨工艺流程》
合成氨是一种重要的化工原料,广泛应用于农业和化工领域。
合成氨的工艺流程主要包括催化剂制备、氮气和氢气的制备以及氨的合成三个主要步骤。
首先是催化剂的制备。
合成氨工艺中使用的主要催化剂是铁-
铝催化剂,它的制备需要经过一系列的化学反应和物理处理。
首先在高温下将铁酸钾和铝酸钾还原成铁铝合金,然后通过高温煅烧和还原处理,最终得到合成氨反应所需的铁-铝催化剂。
其次是氮气和氢气的制备。
氮气主要通过空气分离装置来获取,空气中的氮气含量大约为78%,通过空气分离装置可以将氮
气和氧气分离开来。
而氢气则主要通过蒸汽重整和部分氧化甲烷法制备,蒸汽重整法主要是通过将甲烷与水蒸气在催化剂的作用下反应生成一氧化碳和氢气,而部分氧化甲烷法则是通过将甲烷与氧气在高温下反应生成氢气和二氧化碳。
最后是氨的合成。
氮气和氢气经过净化后,进入合成氨反应器进行催化反应。
在高压和适当温度的条件下,铁-铝催化剂的
作用下,氮气和氢气会发生氮合成反应,生成氨。
这个反应是一个放热反应,因此需要控制反应温度及高压下的反应速率,避免能量过度损失。
综上所述,合成氨的工艺流程复杂且涉及多个步骤。
通过精确
控制每个步骤的条件和参数,可以确保生产安全高效地进行,从而满足氨的需求并为化工及农业领域提供丰富的原料。
合成氨工艺流程
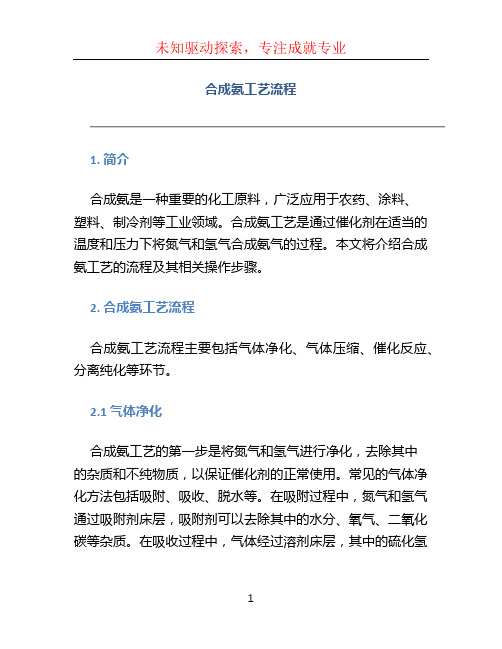
合成氨工艺流程1. 简介合成氨是一种重要的化工原料,广泛应用于农药、涂料、塑料、制冷剂等工业领域。
合成氨工艺是通过催化剂在适当的温度和压力下将氮气和氢气合成氨气的过程。
本文将介绍合成氨工艺的流程及其相关操作步骤。
2. 合成氨工艺流程合成氨工艺流程主要包括气体净化、气体压缩、催化反应、分离纯化等环节。
2.1 气体净化合成氨工艺的第一步是将氮气和氢气进行净化,去除其中的杂质和不纯物质,以保证催化剂的正常使用。
常见的气体净化方法包括吸附、吸收、脱水等。
在吸附过程中,氮气和氢气通过吸附剂床层,吸附剂可以去除其中的水分、氧气、二氧化碳等杂质。
在吸收过程中,气体经过溶剂床层,其中的硫化氢等有毒气体被吸收掉。
同时,还可以使用脱水剂去除气体中的水分。
2.2 气体压缩在气体净化后,将净化后的氮气和氢气进行压缩,提高其压力,以便后续的催化反应。
氮气和氢气分别进入压缩机进行压缩,压缩机通常采用多级压缩,保证气体压力的稳定和可控。
2.3 催化反应经过气体压缩后的氮气和氢气进入催化剂床层,进行合成氨的催化反应。
催化剂通常采用铁、钼或镍等金属催化剂,催化剂在适当的温度和压力下,使氮气和氢气发生反应,生成合成氨气。
催化反应是一个放热反应,需要控制温度以避免过高的温度导致副反应的发生。
2.4 分离纯化经过催化反应生成的合成氨气含有大量的副产物和未反应的氮气、氢气等杂质。
在分离纯化环节中,需要进行吸附、压缩、蒸馏等操作,将合成氨气中的杂质去除,提高纯度。
常见的分离纯化方法包括低温吸附法、压缩法和蒸馏法。
3. 工艺条件和参数合成氨工艺的实施需要满足一定的工艺条件和参数,以确保反应的进行和产出的质量。
常见的工艺条件和参数包括温度、压力、催化剂种类和配比、气体流速等。
3.1 温度催化反应的温度是合成氨工艺中的关键参数之一。
温度过高会导致副反应的发生,影响合成氨气的产量和纯度;温度过低则会降低反应速率。
一般情况下,催化反应的温度在300-500°C之间控制。
氨合成的工艺流程

氨合成的工艺流程氨合成是指通过水气变换反应将氮气和氢气直接合成氨的工艺过程。
氨合成的工艺流程主要包括气体净化、反应器的热力学和动力学模型、反应器的设计和操作、催化剂的选择和再生以及产物的分离等环节。
首先,进料气中的杂质如二氧化碳、一氧化碳等需要通过气体净化装置进行除去。
常用的净化方法有吸附除油、吸附水和活性炭掺混除气中杂质的方法。
其次,将经过净化的氮气和氢气按照一定的比例送入反应器中。
反应器的热力学和动力学模型是指根据反应的热力学特性和动力学特性,建立合理的模型来描述反应过程。
根据热力学平衡,氨的生成反应需要在高温高压下进行,通常温度在350-550℃,压力在10-30MPa,较高的温度和压力有利于催化剂的活性,但也会增加设备的成本和能耗。
在氨合成反应器的设计和操作中,需考虑到催化剂选择、反应器的结构和冷却方式等因素。
常用的催化剂是铁-铝催化剂或铁-铝-钾催化剂。
同时,为了确保反应器的正常运行,需进行恒定的循环气体流动来提高反应的速率和产物的收率,并通过合适的冷却方式控制反应的温度。
另外,为了提高氨的产率,需要定期检查和维护反应器的状况。
催化剂的选择和再生是氨合成过程中的重要环节。
催化剂的活性可通过添加助催化剂、改变催化剂的物理状态来提高。
在催化剂失活后,常常需要将催化剂送入再生热气体中进行再生,以恢复催化剂的活性。
最后,产物的分离是氨合成工艺流程的最后一步。
氨合成反应产生的主要产物是氨、氮气和未反应的氮气和氢气。
通过合理的工艺设计,可采用吸附分离、压力变化法等方法将氨和氮气进行分离,再通过压缩和冷凝等方式进行进一步分离,并进行储存和使用。
总之,氨合成是一种重要的化学工艺过程,其工艺流程包括净化、反应器的热力学和动力学模型、反应器的设计和操作、催化剂的选择和再生以及产物的分离等环节。
只有在每个环节都进行合理设计和操作,才能保证氨合成反应的高效率、高产出和高质量。
合成氨工艺流程详解
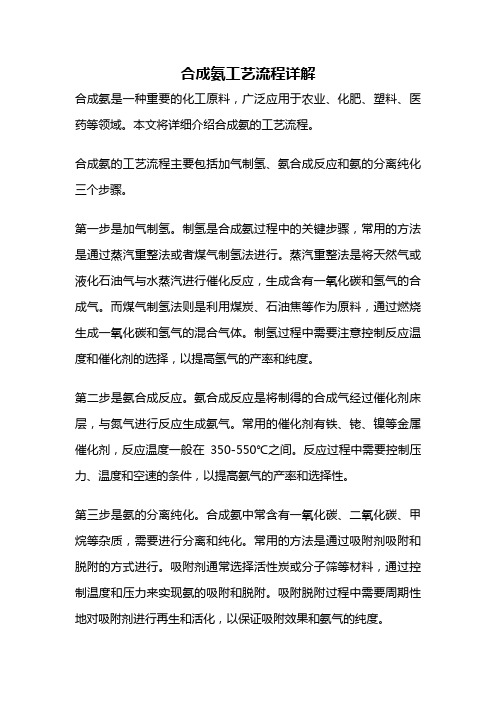
合成氨工艺流程详解
合成氨是一种重要的化工原料,广泛应用于农业、化肥、塑料、医药等领域。
本文将详细介绍合成氨的工艺流程。
合成氨的工艺流程主要包括加气制氢、氨合成反应和氨的分离纯化三个步骤。
第一步是加气制氢。
制氢是合成氨过程中的关键步骤,常用的方法是通过蒸汽重整法或者煤气制氢法进行。
蒸汽重整法是将天然气或液化石油气与水蒸汽进行催化反应,生成含有一氧化碳和氢气的合成气。
而煤气制氢法则是利用煤炭、石油焦等作为原料,通过燃烧生成一氧化碳和氢气的混合气体。
制氢过程中需要注意控制反应温度和催化剂的选择,以提高氢气的产率和纯度。
第二步是氨合成反应。
氨合成反应是将制得的合成气经过催化剂床层,与氮气进行反应生成氨气。
常用的催化剂有铁、铑、镍等金属催化剂,反应温度一般在350-550℃之间。
反应过程中需要控制压力、温度和空速的条件,以提高氨气的产率和选择性。
第三步是氨的分离纯化。
合成氨中常含有一氧化碳、二氧化碳、甲烷等杂质,需要进行分离和纯化。
常用的方法是通过吸附剂吸附和脱附的方式进行。
吸附剂通常选择活性炭或分子筛等材料,通过控制温度和压力来实现氨的吸附和脱附。
吸附脱附过程中需要周期性地对吸附剂进行再生和活化,以保证吸附效果和氨气的纯度。
合成氨的工艺流程包括加气制氢、氨合成反应和氨的分离纯化三个步骤。
通过合理控制各个步骤的条件和催化剂的选择,可以提高氨气的产率和纯度,满足不同领域的需求。
合成氨工艺的优化和改进,对于提高工业生产效率和减少能源消耗具有重要意义。
希望本文对读者了解合成氨的工艺流程有所帮助。
浅析我国氨(NH_3)合成化工技术工艺

关键 词 : 合成氨
生产工艺
尿素
技术
节能
发 展趋 势
然气 与水蒸 汽在 氧化 催化 剂作 用下 进行部 分 氧化 。 进 料气 与 水 蒸 汽 先 混 合 预 热 、 与 氧 化 剂 燃 烧 ,然 后在 1 7 9 0 o C
艺流 程 图如下 :
造 气一 半 水 煤 气脱 硫一 压 缩 机 1 , 2段一 变 换一 变换 气 脱 硫一 压 缩 机 3段一 脱 碳一 精 脱 硫一 甲烷 化一 压缩 机
洁 生 产 技 术 等 几个 方面 进 行 了论 述 。
1 9 2 0 o C反应 温 度 下 通 过 催 化 剂 床 层 进 行水 蒸 汽 与 甲烷 1 合成 氨 工艺净 化 转化生 成合 成气 ) 是最 适合 大型化 制 氨工 艺技术 。 T e x a c o 、 合 成 氨 指 由氨 和 氢在 高温 高 压和 催 化 剂 存 在 下 直 接 s h e l l 和 中 国工 程 公司 则研 发 非催 化 部 分氧 化 技 术 ,为 合 合 成 的氨。 别名 氨 气 , 化 学分子 式 为 NH 。 。 世 界上 的氨 除少 成气制 备工 艺 的大型 化进行 技术 ; 隹备 。 量 从 焦炉 气 中 回收外 , 绝 大部 分是 合 成 的氨。 合成 氨造 气 ② 合 成 气 净 化 技术 。 目前 广 泛 使 用 的 B A S F公 司 的 废 水 悬浮 物高 , 含 有 氰化物 、 硫 化 物、 挥 发酚 和 氨氮 等 。其 MDE A工艺, 完 全适用 于 大型化 装置 : 以低 温 甲醇 洗、 低 温 处理 方法 多采 用沉淀 、 冷 却、 生化工 艺。选用 一体 化净 水器 液氮 洗 为代表 的低 温 净化 工 艺 , 也 有可 能在 合 成气 净 化大 和双 层 曝气 生物 滤 池 处理 造 气 废水 ,不 但 可 提 高 回 用水 型化 装置 中得 以应 用。 质, 达 到 了《 污水综合排放标准》 ( GB 8 9 7 8 — 1 9 9 6 ) 的 一 级 3 低 能耗 合成 氨工 艺技 术 标; 隹: 还 能减 少 处理 运行 能耗和 工程 占地 。 为老企 业 合 成 合成 氨典 型 的节 能流 程 。目前新建 的以天 然气 为原 料 氨造 气 废水 的 处理 改造 提供 了新 途径 。 的合成 氨 装 置 的综合 能 耗 已降到 2 9 . 3 G J / t氨 以下 。 世界 以无烟煤 为原 料 生成合 成 氨常见 过程 是 : 上 具 有 竞 争 能 力 的低 能 耗 合 成 氨 技术 有 : K B R公 司 的 技 造 气一 半水 煤 气 脱硫一 压 缩机 1 , 2工段一 变 换一 变 术、 l Cl 公 司 的 AMV技 术 、 U h d e公 司 的技 术 和 T o p s ①e 换 气 脱 硫一 压缩 机 3段一 脱 硫一 压 缩 机 4, 5工段一 铜 洗 公 司 的技术 。 各公 司依 据其 拥 有 的专利 技术 , 组 合 了 四种 一 压缩 机 6段一 氨合成一 产 品 N H 。 典 型 的节 能流程 。其 中具 有代表 性 的是 K B R工 艺。 采用 甲烷 化法脱 硫 除原 料 气 中 C O、 C O, 时, 合 成 氨工 现 已开 发成功 的 合成 氨各 工序 的节 能 工艺还 有 许 多 ,
合成氨工作原理与工艺流程
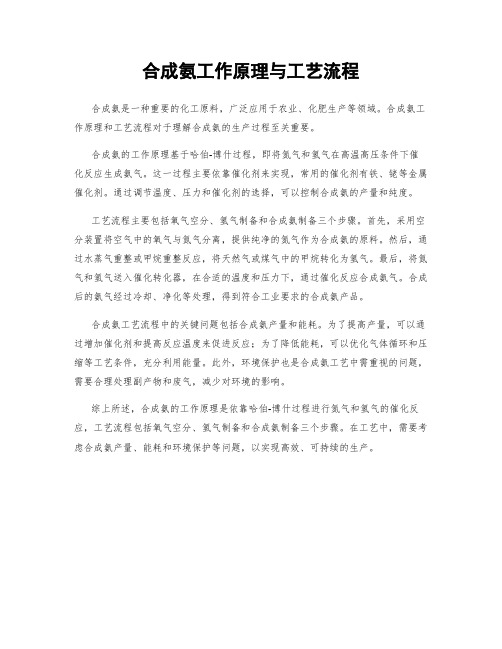
合成氨工作原理与工艺流程
合成氨是一种重要的化工原料,广泛应用于农业、化肥生产等领域。
合成氨工作原理和工艺流程对于理解合成氨的生产过程至关重要。
合成氨的工作原理基于哈伯-博什过程,即将氮气和氢气在高温高压条件下催化反应生成氨气。
这一过程主要依靠催化剂来实现,常用的催化剂有铁、铑等金属催化剂。
通过调节温度、压力和催化剂的选择,可以控制合成氨的产量和纯度。
工艺流程主要包括氧气空分、氢气制备和合成氨制备三个步骤。
首先,采用空分装置将空气中的氧气与氮气分离,提供纯净的氮气作为合成氨的原料。
然后,通过水蒸气重整或甲烷重整反应,将天然气或煤气中的甲烷转化为氢气。
最后,将氮气和氢气送入催化转化器,在合适的温度和压力下,通过催化反应合成氨气。
合成后的氨气经过冷却、净化等处理,得到符合工业要求的合成氨产品。
合成氨工艺流程中的关键问题包括合成氨产量和能耗。
为了提高产量,可以通过增加催化剂和提高反应温度来促进反应;为了降低能耗,可以优化气体循环和压缩等工艺条件,充分利用能量。
此外,环境保护也是合成氨工艺中需重视的问题,需要合理处理副产物和废气,减少对环境的影响。
综上所述,合成氨的工作原理是依靠哈伯-博什过程进行氮气和氢气的催化反应,工艺流程包括氧气空分、氢气制备和合成氨制备三个步骤。
在工艺中,需要考虑合成氨产量、能耗和环境保护等问题,以实现高效、可持续的生产。
氨合成工艺流程中
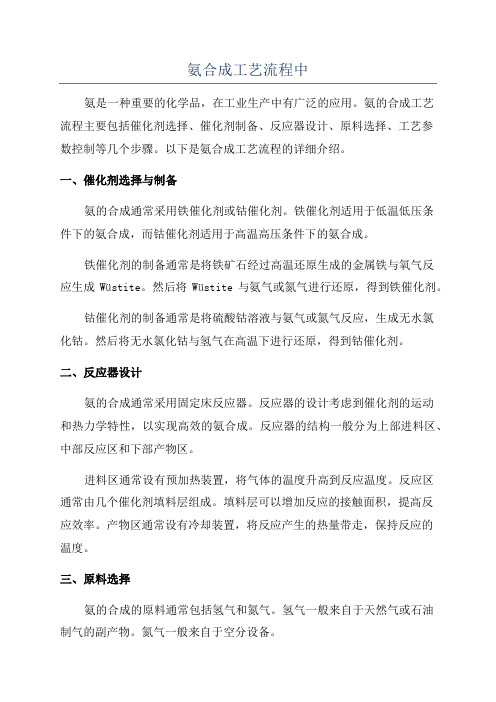
氨合成工艺流程中氨是一种重要的化学品,在工业生产中有广泛的应用。
氨的合成工艺流程主要包括催化剂选择、催化剂制备、反应器设计、原料选择、工艺参数控制等几个步骤。
以下是氨合成工艺流程的详细介绍。
一、催化剂选择与制备氨的合成通常采用铁催化剂或钴催化剂。
铁催化剂适用于低温低压条件下的氨合成,而钴催化剂适用于高温高压条件下的氨合成。
铁催化剂的制备通常是将铁矿石经过高温还原生成的金属铁与氧气反应生成Wüstite。
然后将Wüstite与氨气或氮气进行还原,得到铁催化剂。
钴催化剂的制备通常是将硫酸钴溶液与氨气或氮气反应,生成无水氯化钴。
然后将无水氯化钴与氢气在高温下进行还原,得到钴催化剂。
二、反应器设计氨的合成通常采用固定床反应器。
反应器的设计考虑到催化剂的运动和热力学特性,以实现高效的氨合成。
反应器的结构一般分为上部进料区、中部反应区和下部产物区。
进料区通常设有预加热装置,将气体的温度升高到反应温度。
反应区通常由几个催化剂填料层组成。
填料层可以增加反应的接触面积,提高反应效率。
产物区通常设有冷却装置,将反应产生的热量带走,保持反应的温度。
三、原料选择氨的合成的原料通常包括氢气和氮气。
氢气一般来自于天然气或石油制气的副产物。
氮气一般来自于空分设备。
四、工艺参数控制氨的合成的工艺参数主要包括温度、压力和气体比例等。
温度影响氨的生成速度和催化剂的寿命,通常保持在200-500°C之间。
压力影响氨的产率和催化剂的活性,通常保持在100-300atm之间。
氢气和氮气的比例影响氨的选择性和氨的产率,通常保持在1:3-3:1之间。
五、氨的分离与精制氨合成反应产生的气体混合物中含有大量的惰性气体和杂质。
因此需要对气体进行分离和精制。
通常采用液气分离和吸附分离的方法。
液气分离通常采用吸附剂或凝析剂将气体中的氨吸附或凝形成液体,然后通过蒸馏或吸附解吸将氨分离出来。
吸附分离通常采用活性碳吸附剂,通过气体分子的表面吸附来分离氨。
合成氨工艺流程详解

合成氨工艺流程详解合成氨是一种重要的化工原料,在农药、肥料、塑料、纤维等方面都有广泛应用。
下面我们就来详细解析一下合成氨的工艺流程。
合成氨的工艺流程主要包括气体净化、气体压缩、气体循环、气体转化及气体分离等环节。
首先是气体净化。
合成氨的原料主要是天然气和空气,其中天然气中含有杂质,需要进行净化。
常用的净化方法有吸附、干燥和过滤等。
吸附是利用吸附材料对杂质进行吸附,干燥是将天然气中的水分去除,过滤是通过过滤器过滤掉颗粒杂质。
经过这些处理后,能够得到纯净的原料气体。
接下来是气体压缩。
原料气体需要进行压缩,提高其进入合成反应器的压力。
通常使用压缩机进行气体的压缩,将其压缩到所需的工作压力。
然后是气体循环。
合成氨反应是连续进行的,需要循环利用气体,提高反应的效率。
在循环过程中,气体需要经过冷却、减压和再压缩等处理,以保持合适的温度和压力。
接下来是气体转化。
气体转化是合成氨工艺的核心环节。
主要是通过催化剂催化,将氮气和氢气在一定的温度和压力下,进行化学反应生成氨气。
这个过程中,需要控制好反应的温度、压力、催化剂的选择和反应时间等条件,以提高氨气的产率和质量。
最后是气体分离。
合成氨反应生成的气体中还包括一些未反应的氮气、氢气和其他副产物,需要对其进行分离和回收。
通常使用吸附法、吸收法和膜分离等方法进行气体分离。
吸附法是利用吸附剂对气体进行吸附,吸收法是将气体溶解到溶剂中,膜分离是利用半透膜对气体进行分离。
通过这些分离技术,能够得到纯度较高的合成氨。
总的来说,合成氨的工艺流程包括气体净化、气体压缩、气体循环、气体转化和气体分离等环节。
在每个环节中,都需要进行相应的操作和控制,以确保合成氨的生产过程稳定、高效和安全。
化工合成氨工艺原理及流程分析

化工合成氨工艺原理及流程分析合成氨是一种重要的化工原料,广泛用于制造化肥、塑料、炸药等工业产品。
化工合成氨的工艺原理及流程分析包括以下几个方面:氨合成反应原理、催化剂选择、反应器类型、反应条件等。
氨合成反应原理:合成氨的反应原理是通过氮气与氢气在适宜的温度、压力和催化剂条件下发生氨合成反应。
反应的化学方程式为:N2 + 3H2 → 2NH3、该反应是一个放热反应,反应热释放为-92 kJ/mol。
催化剂选择:在氨合成中,催化剂起到提高反应速率的作用。
常用的催化剂有铁、铑及铂铑合金等。
其中,铁是最常用的催化剂,它在常压、常温下较容易活化氮分子直接反应生成NH3反应器类型:氨合成反应器主要分为固定床反应器和流化床反应器两种。
固定床反应器是将氨合成催化剂装填在固定的反应器床层中,氮气和氢气在催化剂上发生反应。
流化床反应器则是将催化剂悬浮在气流中,气体通过床层时与催化剂接触反应。
反应条件:氨合成反应需要控制的反应条件包括合适的温度、压力和气体物质的配比。
一般来说,较高温度有利于增加反应速率,但过高会使催化剂失活。
常用的反应温度在300-550摄氏度之间。
反应压力的选择要保证合理的反应速率,一般在100-300atm之间。
氮气和氢气的配比一般为1:3,即1 mol氮气需要3 mol氢气参与反应。
1.氮气和氢气的净化:通过气体净化系统处理供应的氮气和氢气,去除其中的杂质,保证进入反应器的气体纯度。
2.反应器:将纯化后的氮气和氢气以合适的压力和比例输入反应器。
反应器内设置催化剂床层,使氮气和氢气在催化剂上发生反应生成氨。
3.冷却器:反应结束后,将反应后的气体通过冷却器冷却,使氨气在较低温度下凝结成液态。
4.分离器:将液态的氨与未反应的氢气和氮气通过分离器分离,以得到干净的合成氨。
5.回收和再利用:未反应的氢气和氮气可经再循环回收,以减少原料的消耗和降低生产成本。
总结:化工合成氨工艺原理及流程分析包括了氨合成反应原理、催化剂选择、反应器类型、反应条件等。
合成氨的工艺流程

合成氨的工艺流程
合成氨是一种重要的化工原料,广泛应用于化肥、合成树脂、
医药等领域。
其工艺流程主要包括氮气和氢气的合成反应,以及合
成氨的分离和提纯过程。
下面将详细介绍合成氨的工艺流程。
首先,氮气和氢气通过压缩机分别被压缩至一定压力,然后经
过冷凝器降温至所需温度。
接着,氮气和氢气进入合成反应器,在
催化剂的作用下发生合成反应,生成氨气。
合成反应的温度、压力
和催化剂的选择对反应效果有着至关重要的影响,需要严格控制。
随后,合成氨气通过冷凝器冷却至液态,然后进入分离塔进行
分离。
在分离塔内,通过控制温度和压力,将未反应的氮气和氢气
重新回收利用,而将得到的合成氨气进行提纯。
提纯过程主要包括
吸附、脱附和冷凝等步骤,最终得到高纯度的合成氨。
在整个工艺流程中,需要严格控制反应温度、压力和催化剂的
选择,以确保合成氨的产率和纯度。
同时,还需要对氮气和氢气进
行预处理,去除其中的杂质和水分,以保证反应的顺利进行。
此外,对于合成氨的分离和提纯过程,也需要精密的设备和严格的操作,
确保产品的质量符合要求。
总的来说,合成氨的工艺流程包括氮气和氢气的合成反应,以及合成氨的分离和提纯过程。
在整个过程中,需要严格控制各项操作参数,保证反应的高效进行,最终得到高品质的合成氨产品。
这些工艺流程的细节和技术要点,对于合成氨生产工艺的优化和改进具有重要的指导意义。
氨合成的工艺流程

氨合成的工艺流程
《氨合成工艺流程》
氨合成是一种重要的化工工艺,用于生产氨气,它是肥料生产和化工工业中的重要原料。
氨气可以用于制造化肥、合成硝酸和其他化学品。
以下是氨合成的基本工艺流程。
首先,氨合成使用的原料主要是氮气和氢气。
氮气可以从空气中提取出来,而氢气可以从天然气或其他石油化工产品中提取出来。
其次,氨合成的工艺流程主要有三个步骤:合成气制备、氨的合成和氨的精制。
首先是合成气制备,合成气是一种混合物,主要由氢气和一氧化碳组成。
这一步骤通常是在催化剂的作用下,将氮气和水蒸气一起加热至高温,然后再经过催化剂的作用,生成合成气。
接下来是氨的合成,这一步骤是将合成气在高压和高温下经过催化剂的作用,使其转化为氨气。
这一步骤通常使用铁催化剂或其他金属催化剂来促进反应的进行。
最后是氨的精制,氨气经过合成后,通常会含有一定量的杂质,所以需要进行精制。
这一步骤通常是通过冷凝和吸附等工艺来进行,从而得到纯净的氨气。
总的来说,氨合成的工艺流程是一个复杂的化学反应过程,需
要通过合成气制备、氨的合成和氨的精制等步骤来进行。
只有严格控制每一个步骤,才能够得到高纯度的氨气,从而满足工业生产和农业生产的需要。
对合成氨工艺的认识和理解
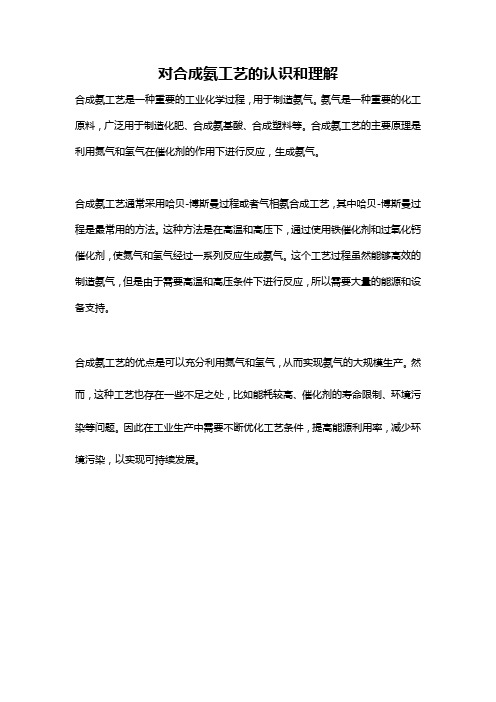
对合成氨工艺的认识和理解
合成氨工艺是一种重要的工业化学过程,用于制造氨气。
氨气是一种重要的化工原料,广泛用于制造化肥、合成氨基酸、合成塑料等。
合成氨工艺的主要原理是利用氮气和氢气在催化剂的作用下进行反应,生成氨气。
合成氨工艺通常采用哈贝-博斯曼过程或者气相氨合成工艺,其中哈贝-博斯曼过程是最常用的方法。
这种方法是在高温和高压下,通过使用铁催化剂和过氧化钙催化剂,使氮气和氢气经过一系列反应生成氨气。
这个工艺过程虽然能够高效的制造氨气,但是由于需要高温和高压条件下进行反应,所以需要大量的能源和设备支持。
合成氨工艺的优点是可以充分利用氮气和氢气,从而实现氨气的大规模生产。
然而,这种工艺也存在一些不足之处,比如能耗较高、催化剂的寿命限制、环境污染等问题。
因此在工业生产中需要不断优化工艺条件,提高能源利用率,减少环境污染,以实现可持续发展。
氨合成工艺技术
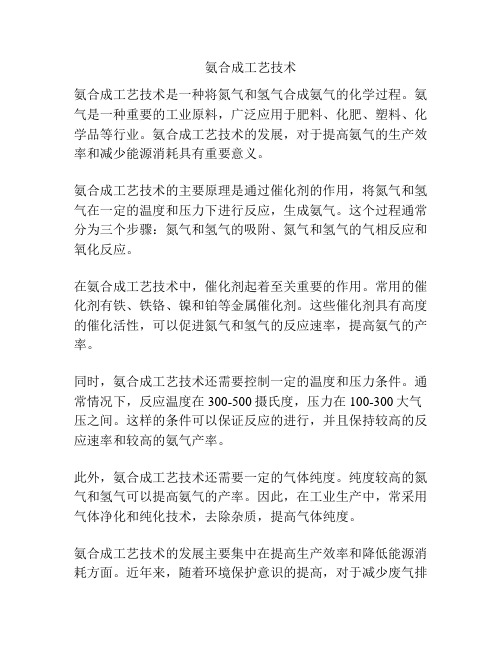
氨合成工艺技术
氨合成工艺技术是一种将氮气和氢气合成氨气的化学过程。
氨气是一种重要的工业原料,广泛应用于肥料、化肥、塑料、化学品等行业。
氨合成工艺技术的发展,对于提高氨气的生产效率和减少能源消耗具有重要意义。
氨合成工艺技术的主要原理是通过催化剂的作用,将氮气和氢气在一定的温度和压力下进行反应,生成氨气。
这个过程通常分为三个步骤:氮气和氢气的吸附、氮气和氢气的气相反应和氧化反应。
在氨合成工艺技术中,催化剂起着至关重要的作用。
常用的催化剂有铁、铁铬、镍和铂等金属催化剂。
这些催化剂具有高度的催化活性,可以促进氮气和氢气的反应速率,提高氨气的产率。
同时,氨合成工艺技术还需要控制一定的温度和压力条件。
通常情况下,反应温度在300-500摄氏度,压力在100-300大气压之间。
这样的条件可以保证反应的进行,并且保持较高的反应速率和较高的氨气产率。
此外,氨合成工艺技术还需要一定的气体纯度。
纯度较高的氮气和氢气可以提高氨气的产率。
因此,在工业生产中,常采用气体净化和纯化技术,去除杂质,提高气体纯度。
氨合成工艺技术的发展主要集中在提高生产效率和降低能源消耗方面。
近年来,随着环境保护意识的提高,对于减少废气排
放和减少能源消耗的要求越来越高。
因此,通过改进催化剂、减少副反应和提高反应选择性等手段,可以提高氨合成的生产效率和减少能源消耗。
总的来说,氨合成工艺技术是一种将氮气和氢气合成氨气的重要化学工艺。
通过控制温度、压力和气体纯度,以及改进催化剂和反应条件,可以提高氨气的产率和生产效率,减少能源消耗,符合环保要求。
氨合成 工艺流程

氨合成工艺流程
《氨合成工艺流程》
氨是一种重要的化工产品,广泛应用于肥料、化肥、石油化工和医药等领域。
氨合成是一种重要的工业化学过程,其工艺流程包括催化剂的选择、反应条件的控制和产品精制等步骤。
氨合成的工艺流程主要包括合成氨的催化反应、氨的分离和净化过程。
在合成氨的催化反应中,通常采用哈勃-博斯曼法,
通过在高温高压条件下,将氢气和氮气在铁催化剂的作用下进行反应,生成氨。
此过程需要严格控制反应条件,如温度、压力和催化剂活性等参数,以确保高效率和高选择性的产物生成。
在氨的分离和净化过程中,通常采用氨冷凝和吸收、压缩和脱水等步骤,以获得高纯度的合成氨产品。
此外,氨合成的工艺流程还需要考虑能源消耗、环境保护和安全生产等方面的问题。
因此,在工艺流程中通常会考虑能量回收、废气治理和安全设施等方面的设计和应用,以降低能耗、减少污染和保障生产安全。
总的来说,氨合成的工艺流程是一个复杂而重要的过程,需要综合考虑催化剂选择、反应条件控制和产品精制等方面,以确保高效率、高选择性和高品质的合成氨产品。
同时,还需要重视能源消耗、环境保护和安全生产等方面,以推动氨合成工艺的可持续发展。
氨合成工艺技术方案
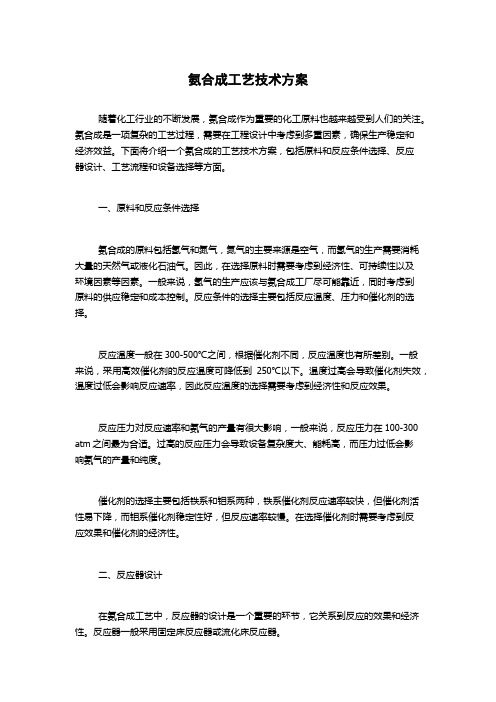
氨合成工艺技术方案随着化工行业的不断发展,氨合成作为重要的化工原料也越来越受到人们的关注。
氨合成是一项复杂的工艺过程,需要在工程设计中考虑到多重因素,确保生产稳定和经济效益。
下面将介绍一个氨合成的工艺技术方案,包括原料和反应条件选择、反应器设计、工艺流程和设备选择等方面。
一、原料和反应条件选择氨合成的原料包括氢气和氮气,氮气的主要来源是空气,而氢气的生产需要消耗大量的天然气或液化石油气。
因此,在选择原料时需要考虑到经济性、可持续性以及环境因素等因素。
一般来说,氢气的生产应该与氨合成工厂尽可能靠近,同时考虑到原料的供应稳定和成本控制。
反应条件的选择主要包括反应温度、压力和催化剂的选择。
反应温度一般在300-500℃之间,根据催化剂不同,反应温度也有所差别。
一般来说,采用高效催化剂的反应温度可降低到250℃以下。
温度过高会导致催化剂失效,温度过低会影响反应速率,因此反应温度的选择需要考虑到经济性和反应效果。
反应压力对反应速率和氨气的产量有很大影响,一般来说,反应压力在100-300 atm之间最为合适。
过高的反应压力会导致设备复杂度大、能耗高,而压力过低会影响氨气的产量和纯度。
催化剂的选择主要包括铁系和钼系两种,铁系催化剂反应速率较快,但催化剂活性易下降,而钼系催化剂稳定性好,但反应速率较慢。
在选择催化剂时需要考虑到反应效果和催化剂的经济性。
二、反应器设计在氨合成工艺中,反应器的设计是一个重要的环节,它关系到反应的效果和经济性。
反应器一般采用固定床反应器或流化床反应器。
固定床反应器:反应器由一定数量的催化剂组成,原料在催化剂上通过反应后产生氨气。
固定床反应器具有结构简单、操作方便、稳定性好等优点,但清洗困难,会产生空间流动沉积物等问题。
流化床反应器:原料气体和催化剂混合后形成类似于流体的状态进行反应,具有反应速率快、流量调节性能好、热量均匀等优点。
但由于流化床内流速快、颗粒更易磨损或流失,反应器运行中噪音大、操作难度大等问题也需重视。
- 1、下载文档前请自行甄别文档内容的完整性,平台不提供额外的编辑、内容补充、找答案等附加服务。
- 2、"仅部分预览"的文档,不可在线预览部分如存在完整性等问题,可反馈申请退款(可完整预览的文档不适用该条件!)。
- 3、如文档侵犯您的权益,请联系客服反馈,我们会尽快为您处理(人工客服工作时间:9:00-18:30)。
浅析我国氨(NH3)合成化工技术工艺
作者:李红涛等
来源:《中小企业管理与科技·下旬刊》2014年第07期
摘要:合成氨指由氮和氢在高温高压和催化剂存在下直接合成的氨。
别名氨气,化学分子式为NH3。
本文综述了合成氨生产工艺的发展趋势,重点从装置大型化、节能降耗结构调整以及长周期运转和清洁生产技术等几个方面进行了论述。
关键词:合成氨生产工艺尿素技术节能发展趋势
1 合成氨工艺净化
合成氨指由氮和氢在高温高压和催化剂存在下直接合成的氨。
别名氨气,化学分子式为NH3。
世界上的氨除少量从焦炉气中回收外,绝大部分是合成的氨。
合成氨造气废水悬浮物高,含有氰化物、硫化物、挥发酚和氨氮等。
其处理方法多采用沉淀、冷却、生化工艺。
选用一体化净水器和双层曝气生物滤池处理造气废水,不但可提高回用水质,达到了《污水综合排放标准》(GB8978-1996)的一级标准;还能减少处理运行能耗和工程占地。
为老企业合成氨造气废水的处理改造提供了新途径。
以无烟煤为原料生成合成氨常见过程是:
造气→半水煤气脱硫→压缩机1,2工段→变换→变换气脱硫→压缩机3段→脱硫→压缩机4,5工段→铜洗→压缩机6段→氨合成→产品NH3
采用甲烷化法脱硫除原料气中CO、CO2时,合成氨工艺流程图如下:
造气→半水煤气脱硫→压缩机1,2段→变换→变换气脱硫→压缩机3段→脱碳→精脱硫→甲烷化→压缩机4,5,6段→氨合成→产品NH3
2 氨合成装置大型化技术
中国石油和化学工业联合会于2013年在北京组织专家对湖南安淳高新技术有限公司开发完成的“日产千吨级新型(ⅢJD)氨合成技术”项目进行科技成果鉴定。
鉴定委员会的结果显示,该氨合成塔及系统是一项新的自主知识产权,具有优异的工业运行综合性能,已经打破了我国在这项技术上长期依赖国外技术的尴尬局面,不仅在我国处于领先地位,在世界上也是先进的水平,应该进行大力的推广应用。
该系统不仅具有操作简单,装置运行安全稳定、年运转率高、能耗低等优势,还能够在高惰气情况下,保证其主要指标都优于设计值,这在国际上还是首例。
有关专家指出,该技术的十大创新点都是原始创新,其中还包括计算方法、径向筐气分布装置等重大创新。
工业合成氨在高压合成塔中完成,由于合成氨需要加压、催化,所以合成塔中有催化室。
由于合成氨的过程释放大量热量,所以合成塔中还有热交换室,用于预热反应气体。
未来,单系列合成氨装置生产能力将从2000t/d提高至4000~5000t/d,在合成氨装置大型化的技术开发过程中,其焦点主要集中在关键性的工序和设备。
世界级合成氨、尿素装置的规模越来越大,采用斯塔米卡帮CO2汽提工艺新建尿素装置中规模最大已达3250t/d。
①合成气制备。
天然气自热转化技术和非催化部分氧化技术将会在合成气制备工艺的大型化方面发挥重要的作用,而To psΦe公司和Lurgi公司均认为ATR技术(天然气与水蒸汽在氧化催化剂作用下进行部分氧化。
进料气与水蒸汽先混合预热、与氧化剂燃烧,然后在1790℃-1920℃反应温度下通过催化剂床层进行水蒸汽与甲烷转化生成合成气)是最适合大型化制氨工艺技术。
Texaco、shell和中国工程公司则研发非催化部分氧化技术,为合成气制备工艺的大型化进行技术准备。
②合成气净化技术。
目前广泛使用的BASF公司的MDEA工艺,完全适用于大型化装置;以低温甲醇洗、低温液氮洗为代表的低温净化工艺,也有可能在合成气净化大型化装置中得以应用。
3 低能耗合成氨工艺技术
合成氨典型的节能流程。
目前新建的以天然气为原料的合成氨装置的综合能耗已降到29.3GJ/t氨以下。
世界上具有竞争能力的低能耗合成氨技术有:KBR公司的技术、ICI公司的AMV技术、Uhde公司的技术和TopsΦe公司的技术。
各公司依据其拥有的专利技术,组合了四种典型的节能流程。
其中具有代表性的是KBR工艺。
现已开发成功的合成氨各工序的节能工艺还有许多,主要有:
①合成气制备工艺单元。
节能降耗的主要技术有:预转化技术、低水碳比转化技术、换热式转化技术。
②CO变换工艺单元。
等温CO变换技术,实现低水碳比变换反应。
③CO2脱除工艺单元。
Linde公司LAC工艺的制氢单元中采用了简单的PSA装置,即可完成传统流程中氢气的精制和CO2脱除两个工序的任务。
程控操作、没有转动设备,维护工作量少。
含有CO、CH4和H2的排放气可以作为燃料,回收热量。
④氨合成工艺单元。
采用新型氨合成塔和低压高活性催化剂,开发气体分布更均匀、阻力更小、结构更合理的合成塔及其内件,实现“等压合成”。
其中以钌基催化剂为核心的KAAP工艺为代表。
4 结束语
随着石油化工和天然气化工的发展,氨合成工艺技术越来越先进,真正简化了流程、降低了系统阻力、提高了变换率和有效能的利用率、减少了系统投资,实现了变换工艺历史性的新突破,能满足大型化肥生产节能与环保的要求,推广应用社会经济效益显著。
参考文献:
[1]鲍卫娜,祝亚荣.新型四喷嘴气化炉技术的发展现状[J].广州化工,2011(18).
[2]徐红东,门长贵.多元料浆气化工艺过程模拟[J].化肥设计,2008(02).
[3]汪家铭.BGL碎煤熔渣气化技术及其工业应用[J].化学工业,2011(07).。