典型表面加工工艺共37页
SMT工艺介绍

第一页,共37页。
Page 1 of 58
1.SMT整休介绍(jièshào) 2.锡膏印刷的介绍(jièshào) 3.锡膏,刮刀,钢网 4.SMT贴片机介绍(jièshào) 5.AOI介绍(jièshào) 6.回流焊 7.underfill点胶
壁粗糙度
三球定律: 至少有三個最大直徑的錫珠能垂直排在钢网的厚度(hòudù)
方向上 至少有三個最大直徑的錫珠能水平排在钢网的最小孔 的寬度方向上
第二十二页,共37页。
Page 22 of 58
三.锡膏,刮刀(ɡuā dāo),钢网
钢网开孔: 面积(miàn jī)比
宽厚比
化学蚀刻
激光+电抛光
电铸(diàn zhù)成 形
Page 32 of 58
五.AOI介绍 (jièshào)
AOI系统用可见光(激光)或不可见光(X射线)作为检测光源,光 学部分采集需要检测的电路板图形,由图像处理软件对数据进 行处理、分析和判断。AOI只能以设定好的标准为基准进行判。
如果标准设定太严,则误判太多。标准设定太宽,又会漏检。
第三十三页,共37页。
Page 20 of 58
第二十页,共37页。
三.锡膏,刮刀(ɡuā dāo), 钢网
钢网(GERBER文件(wénjiàn))
SMT印刷机,通过钢网将锡膏印刷到PCB 焊盘上
钢网
第二十一页,共37页。
钢网开孔区 Page 21 of 58
三.锡膏,刮刀(ɡuā dāo), 钢网
钢网好坏: 开孔位置(wèi zhi),开孔形状,开孔尺寸,孔壁形状,孔
Page 29 of 58
典型表面加工工艺
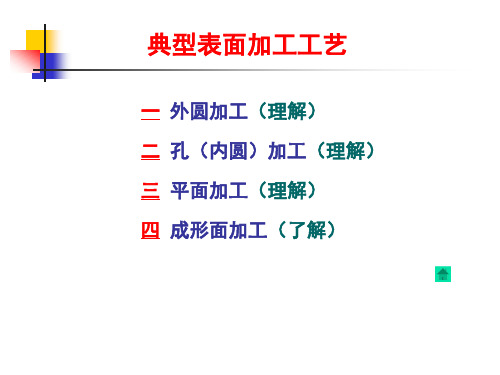
2)平面研磨
一般在磨削之后进行。 尺寸精度可达IT5~IT3, Ra可达0.1~0.008μm。
应用:直尺、块规等。 单件小批生产中常用手工研磨, 大批量生产常用机械研磨。
7. 平面加工方法的选择
粗车—精车 粗铣或粗刨
粗铣—精铣 粗刨—精刨
粗拉—精拉
粗铣(车、刨)—精 铣(车、刨)—磨
粗铣(刨)—精铣 (刨)—磨—研磨 粗刨—精刨—宽刃 细刨
交叉网纹利于贮存润滑油耐磨性好3超精加工11粗车it14it1250125各种金属和部分非金属材料淬火钢除外22粗车半精车it11it9633233粗车半精车精车it8it7512544粗车半精车精车抛光it7it6080455粗车半精车磨削it7it60804黑色金属66粗车半精车粗精磨it6it5040277粗车半精车粗磨精磨超精加工it6it401001288粗车半精车精车金刚石精细车it6it50802主要用于非铁金属99粗车半精车粗磨精磨高精度磨削it5it3010008极高精度的外圆加工10粗车半精车粗磨精磨研磨it5it3010008加工方案经济精度rraam适用范围工序工序名称工序内容的要求11下料用热轧圆钢按尺寸35mmx215mm切断22车削车两端面钻中心孔保证长度尺寸210mm33车削32外圆留磨削余量04mm其余达图样尺寸55热处理保证渗碳层深度0812mm硬度5862hrc66研中心孔研两端中心孔77磨外圆磨32mm外圆32h6留研磨余量001mm88研磨研磨32h6表面达设计要求抛光圆角99检验材料
周铣
端铣
逆
顺
铣
铣
端铣
a) 对称端铣 b) 不对称逆铣 c) 不对称顺铣 对称铣削铣刀耐用度高。 不对称逆铣切入厚度小,适于硬度高的材料。 不对称顺铣切出厚度小,适于塑性大的材料。
第一章 典型表面的加工工艺

深孔加工示意图
平面加工方案框图
1.1.3平面的加工方法
• 1.平面的车削加工 • 2.平面的铣削加工 • (1)粗铣平面 • (2)精铣平面 3.平面的刨削加工和拉削加工 (1)粗刨平面 (2)精刨平面 4 平面的磨削加工 (1)端面磨削 (2)圆周磨削 5.平面的光整加工 (1)平面的研磨 (2)平面的刮研 (3)平面抛光 6 电解磨削平面、线切割平面
•
•
•
内孔表面加工方案框图
1.3.3 内孔表面的加工方法
• • • • • • • • 1. 钻孔 2. 扩孔 3. 铰孔 4. 镗孔 5. 磨孔 6. 深孔加工 7. 内孔的精密加工 8. 箱体的孔系加工
1. 钻孔
• 钻孔是采用钻头在实心材料上加工孔的一种方法。 • 钻孔时钻头容易产生偏斜,从而导致被加工孔的轴心线歪 斜。为防止和减少钻头的偏斜,工艺上常采用下列措施: • 1) 钻孔前先加工孔的端面,以保证端面与钻头轴心线垂直。 • 2) 先采用90˚顶角直径大而且长度较短的钻头预钻一个凹 坑,以引导钻头钻削,此方法多用于转塔车床和自动车床, 防止钻偏。 • 3) 仔细刃磨钻头,使其切削刃对称。 • 4) 钻小孔或深孔时应采用较小的进给量。 • 5) 采用工件回转的钻削方式,注意排屑和切削液的合理使 用。
5. 磨孔
• 采用磨头对淬火孔进行孔的精加工方法, 一般在内圆磨床上进行。
内圆磨削工艺范围
行星式内圆磨削原理图
无心内圆磨削原理图
6. 深孔加工
• 一般将孔的长度L与孔径D之比(L/D)大于5的孔称为深孔。 • (1)深孔加工的工艺特点 • 由于零件较长,工件安装常用“一夹一托”方式,孔的粗加工多选用 深孔钻削或镗削,对要求较高的孔则采用铰削、珩磨或滚压等工艺方 法。 • 深孔加工存在的问题: • 1) 由于深孔刀具一般都比较细长,强度和刚性较差,从而将导致加工 的孔轴心线歪斜,加工中也容易发生引偏和振动。 • 2) 刀具的冷却散热条件差,切削温度升高会使刀具的耐用度降低。 • 3) 切屑排出困难,不仅会划伤已加工表面,严重时会引起刀具崩刃甚 至折断。 • 针对上述三方面问题,工艺上常采用如下措施: • 1) 为解决刀具引偏,宜采取工件旋转的方式及改进刀具导向结构。 • 2) 为解决散热和排屑,采用压力输送切削液以冷却刀具和排出切屑; 同时改进刀具结构,使其既能有一定压力的切削液输入和断屑,又有 利于切屑的顺利排出。
第5章典型表面的加工ppt课件

半和精加工,后用外圆磨床精加工。
3)850.011和 700.009外5 圆表面,
采用车削和磨削两种加工方法(要分粗、半、精车加工,留磨 削余量)。先用卧式车床进行粗、半和精加工,后用外圆磨床 精加工。
ppt精选版
21
4)M 8 326h 和 M 7 026h外圆面,采用车削方法加工即 可(分粗、半、和精加工)。采用卧式车床加工可达到图 纸要求。
分齿运动 使插齿刀与工件间保持啮合关系的运动
径向进给运动 插齿时,刀具渐切至齿的全深,为 此插齿刀应有径向进给运动。
3、插齿的特点
插齿的特点与滚齿相比,插齿有以下特点:
插齿刀制造、刃磨比滚齿刀方便,可制造得较精确。
由于插齿时插齿刀沿齿面全长连续切下切屑,故齿 面粗糙度值较小。
插齿可方便地加工滚齿难以加工的内齿轮、多联齿 轮和齿条。但加工斜齿圆柱齿轮不如滚齿方便。
5、精密内孔表面的加工( IT6以上, Ra0.4~0.025µm )
视情况分别用手铰,精细铰,精拉,精磨,研磨,珩磨,挤压或 滚压等精细加工方法加工
ppt精选版
16
ppt精选版
17
ppt精选版
18
轴承位
ppt精选版
19
Ф142
9000.0 2 2
850.011 M 8 326h
80
700.0095 M 7 026h
ppt精选版
28
(二)成形表面加工方法
1、利用成形刀具加工
即用切削刃形状与工件廓形相符合的刀具,直接加工出 成形面。
(1)车削成形表面 (2)刨削成形表面
(3)铣削成形表面
(4)拉削成形表面 (5)磨削成形表面
2、利用刀具与工件间特定的相对运动加工
典型表面加工工艺
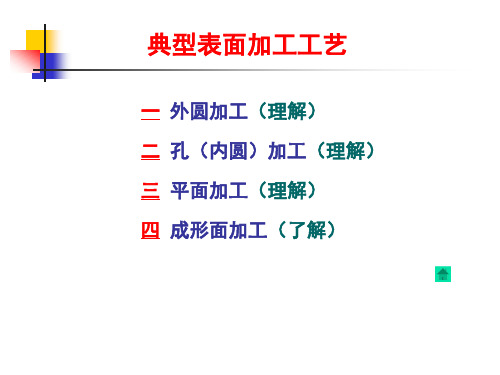
IT7~IT6 IT14~IT12
IT9~IT7 IT9~IT7 IT7~IT6 IT6~IT5
IT5~IT3
IT8~IT7
IT7~IT6
3.2~1.6 50~12.5 3.2~1.6 3.2~1.6 0.8~0.4
淬火钢外的金 属件
刨削用于单件 小批
拉削用于大批 大量
小批;
10-
细长小孔。
80mm
成批、30~80铸锻孔
非淬硬大量中小通孔
单件小批的金属件 (淬火钢除外)。
用于钢及铸铁件
不宜加工韧性大、硬 度低的非铁金属件
三 、平面加工
1、端面车削
一次装夹可完成外圆、内孔和端面,可保证这些 零件的相互位置精度。 精度IT7~IT6,Ra12.5~1.6μm。
2、铣平面
铰孔
在半精加工基础上进行的一种孔的精加工方法。 铰刀应与机床主轴浮动连接床、车床上进行。 对于大尺寸孔,镗孔几乎是唯一的加工方法。 镗孔精度IT11~IT7,Ra0.8-6.3m。
3、磨孔
一般仅适用于淬硬工件的精加工
a) 内圆磨削 b) 行星磨削 c) 无心内圆磨削
1)按划线加工成形面 2)手动控制进给加工曲面
回转曲面:卧式车削 直线曲面:立式铣床 立体曲面:不采用
2)靠模装置加工曲面
1.工件; 2.车刀; 3.拉板; 4.紧固件; 5.滚柱
机械靠模
随动系统靠模
3)数控机床加工曲面
二轴联动:数控车削 二轴半: 二轴数控插补
第三轴周期进刀 三座标联动: 四五轴数控:
IT14~IT12 50~12.5 IT11~IT9 6.3~3.2 IT8~IT7 5~1.25 IT7~IT6 0.8~0.4
《常用表面加工方法》课件

铣削加工
总结词
通过铣床对工件进行切削加工,实现工件表面形状和尺寸的改变。
详细描述
铣削加工是利用铣床对工件进行切削加工的方法,通过刀具的旋转和进给,实现 工件表面形状和尺寸的改变。铣削加工广泛应用于平面、沟槽、齿轮等零件的加 工。
磨削加工
总结词
通过磨床对工件进行研磨加工,实现工件表面粗糙度的降低 和形状精度的提高。
详细描述
磨削加工是利用磨床对工件进行研磨加工的方法,通过砂轮 的高速旋转和进给,实现工件表面粗糙度的降低和形状精度 的提高。磨削加工广泛应用于各种材料的表面精加工。
钻削加工
总结词
通过钻床对工件进行钻孔加工,实现 工件孔洞的形成。
详细描述
钻削加工是利用钻床对工件进行钻孔 加工的方法,通过钻头的旋转和进给 ,实现工件孔洞的形成。钻削加工广 泛应用于各种材料的钻孔加工。
高能束加工
高能束加工是指利用高能电子束 、激光束或离子束等高能束流对 工件表面进行扫描、熔融或烧蚀
等加工的工艺方法。
高能束加工具有高精度、高效率 、非接触等优点,广泛应用于材 料表面改性、微纳结构制备等领
域。
高能束加工的缺点是设备成本较 高,对工件的热影响较大,容易
造成工件变形。
05
其他加工方法
机械工业
提高零件耐磨性、抗腐蚀性、 密封性等。
化工行业
制造高效能催化剂、功能涂层 等。
其他领域
医疗器械、珠宝首饰、艺术品 等领域的表面处理和精饰。
02
机械加工方法
车削加工
总结词
通过车床对工件进行旋转加工,实现工件表面形状和尺寸的改变。
详细描述
车削加工是利用车床对工件进行旋转加工的方法,通过刀具的进给和切削,实 现工件表面形状和尺寸的改变。车削加工广泛应用于轴类、盘类等旋转体零件 的加工。
典型表面加工方法ppt课件

内圆加工方案四
拉削类
Ra25-12.5 IT 12-11
钻孔
粗车 粗镗
粗拉
Ra1.6-0.8 IT 8-7
Ra25-12.5
IT 12-11 调质
精拉
Ra0.8-0.4 IT 7-6
应用:大批量生产的、除淬硬钢以外的、结构适宜拉削的孔
内圆加工方案五
特种加工
Ra3.2-0.4
电火花穿孔
Ra1.6—0.1
4.材料热处理要求决定加工方案
5.生产批量决定加工方案
生产类型
单件生产
批量 生产
小批 中批 大批
大量生产
零件的年产量(生产纲领)(件)
重型零件 中型零件 轻型零件
<5
<10
<100
5~100
10~200
100~500
100~300 200~500 500~5000
300~1000 500~5000 5000~50000
典型表面的加工方法
表面加工方案的选择原则 常见表面的加工方案
外圆、孔、平面
典型成形面-齿轮
加工方法 加工方案
一、表面加工方案的选择原则
1.零件/型面类型(结构形状和尺寸)
外圆、内圆、平面、特殊表面(齿轮) 回转体、非回转体
2.加工精度(IT、Ra)
粗糙、中等、精度较高、精密、超精密
Ra0.2-0.1 IT5
Ra0.8-0.2 IT5
超精 Ra0.1-0.05 加工 IT5
砂带 Ra0.4-0.1 磨削 IT6-5
应用: 1. 除有色金属零件的外圆; 2. 零件结构适宜磨削的外圆;特别适合淬火处理的外圆
外圆加工方案三
典型表面加工工艺共39页文档

60、生活的道路一旦选定,就要勇敢地 走到底工艺
11、战争满足了,或曾经满足过人的 好斗的 本能, 但它同 时还满 足了人 对掠夺 ,破坏 以及残 酷的纪 律和专 制力的 欲望。 ——查·埃利奥 特 12、不应把纪律仅仅看成教育的手段 。纪律 是教育 过程的 结果, 首先是 学生集 体表现 在一切 生活领 域—— 生产、 日常生 活、学 校、文 化等领 域中努 力的结 果。— —马卡 连柯(名 言网)
13、遵守纪律的风气的培养,只有领 导者本 身在这 方面以 身作则 才能收 到成效 。—— 马卡连 柯 14、劳动者的组织性、纪律性、坚毅 精神以 及同全 世界劳 动者的 团结一 致,是 取得最 后胜利 的保证 。—— 列宁 摘自名言网
15、机会是不守纪律的。——雨果
56、书不仅是生活,而且是现在、过 去和未 来文化 生活的 源泉。 ——库 法耶夫 57、生命不可能有两次,但许多人连一 次也不 善于度 过。— —吕凯 特 58、问渠哪得清如许,为有源头活水来 。—— 朱熹 59、我的努力求学没有得到别的好处, 只不过 是愈来 愈发觉 自己的 无知。 ——笛 卡儿
典型表面的加工工艺

圆 周 磨 削
§1.2 外圆表面加工
外圆表面是轴、套、盘等类零件的主 要表面或辅助表面。不同零件上的外圆表 面或同一零件上不同部位的外圆表面,由 于所起作用不同,技术要求也不一样。加 工时,需要拟定合理的加工方案。 外圆表面的技术要求 外圆表面加工方案分析 外圆表面的加工方法
一. 外圆表面的技术要求
非配合平面:不与任何零件相配合,一般无加工精 度要求(低精度平面)。 配合平面:这种平面多数用于零部件的连接面,一 般要求精度和表面质量均较高。 导向平面:如各类机床的导轨面,这种平面的精度 和表面质量要求很高。 端平面:指各种轴类、盘套类零件上与其旋转中心 线相垂直的平面,多起定位作用。这类平面往往对 垂直度、端面间的平行度和表面粗糙度有较高的要 求。 精密量具表面:如钳工的平台、平尺的测量面和计 量用量块的测量平面等。这种平面精度和表面质量 要求均很高。
IT5
Ra0.2~0.006μm
IT5
Ra0.08~0.008μm
Ra1.25~0.008μm
外圆表面加工方案
三. 外圆表面加工方法
外圆表面的车削加工
外圆表面的加工余量主要是由车削切除的。
粗车:尽快切除多余材料,使之接近工件的 形状和尺寸; 半精车:粗车后进一步提高外圆表面的精度 和表面质量; 精车:一般情况下可达到高精度外圆表面的 加工要求; 精细车:属光整加工(常用于有色金属零件 高精度外圆表面的最终加工);
超精加工 超精加工是采用细粒度的磨条以较低的 压力和切削速度对工件表面进行精密加工的 方法。 四个加工阶段—— 强烈切削阶段
自动停止切削
超 精 加 工 的 运 动
正常切削阶段 微弱切削阶段
超 精 加 工 的 轨 迹
表面加工工艺

表面加工工艺表面加工工艺是指对材料表面进行处理以改变其外观、性能或使用寿命的过程。
在制造业中,表面加工工艺被广泛应用于各种材料的加工和生产过程中。
本文将介绍几种常见的表面加工工艺,包括镀层技术、喷涂技术和机械加工技术。
一、镀层技术镀层技术是一种通过将一层金属或其他物质覆盖在材料表面以改变其性能的方法。
镀层可以提高材料的硬度、耐腐蚀性和光泽度。
常见的镀层技术包括电镀、热镀和镀膜等。
1. 电镀电镀是将材料浸入含有金属离子的电解液中,并通过外加电流使离子在材料表面析出形成金属层的过程。
电镀可以提供均匀的镀层,并且可以镀制各种金属,如铬、镍、铜等。
2. 热镀热镀是将材料加热至金属熔点,然后将金属块涂在材料表面,待金属冷却后形成镀层的过程。
热镀在特殊材料的加工中应用广泛,可以提供更坚固的镀层。
3. 镀膜镀膜是将材料浸入含有特殊材料的液体中,让材料表面形成一层薄膜的过程。
镀膜可以提供不同颜色和质感的外观效果,并且可以增加材料的耐磨性和耐腐蚀性。
二、喷涂技术喷涂技术是将液体或粉末状的材料喷射到材料表面形成薄膜的过程。
喷涂技术可以应用于各种材料的加工和装饰,常见的喷涂技术包括喷漆、喷粉和喷砂等。
1. 喷漆喷漆是将液体状的漆料通过喷枪喷射到材料表面形成薄膜的过程。
喷漆可以提供各种颜色和光泽度的外观效果,并且可以保护材料表面免受氧化和腐蚀。
2. 喷粉喷粉是将粉末状的涂料通过喷枪喷射到材料表面形成均匀的薄膜的过程。
喷粉可以提供高耐用性和抗腐蚀性的涂层,并且可以应用于各种复杂形状的材料表面。
3. 喷砂喷砂是通过喷射高压气流中的砂粒使其撞击材料表面,从而改变材料表面的形貌和光泽度的过程。
喷砂可以提供粗糙或纹理的外观效果,并且可以去除材料表面的污渍和氧化层。
三、机械加工技术机械加工技术是通过对材料表面进行物理或化学的加工以改变其形状和光洁度的方法。
常见的机械加工技术包括抛光、研磨和切削等。
1. 抛光抛光是通过机械设备和磨料对材料表面进行研磨,以去除表面的瑕疵和提高光洁度的过程。