Lean_Production_System(精实生产系统概论)
精益生产系统管理概述

精益生产系统管理概述引言精益生产系统是由日本丰田汽车公司所引进并发扬光大的一种生产管理体系。
它的核心思想是通过消除浪费,提高生产效率和质量,从而实现企业的可持续发展。
本文将围绕精益生产系统的概念、原则和应用进行详细介绍,以帮助读者深入了解并灵活运用精益生产系统管理技术。
一、精益生产系统定义精益生产系统(Lean Production System,简称LPS)是一种以供应链为驱动,以价值流为导向,通过消除浪费、流程优化和员工参与等策略,实现生产效率和质量的全面提升的管理方法。
它的核心是通过持续改进来降低生产成本、减少库存、提高交付能力和顾客满意度。
二、精益生产系统原则1.价值流观念精益生产系统强调以顾客为导向,将价值流定义为一系列能够满足顾客需求并使顾客满意的活动。
通过细致的价值流分析,找出生产中的浪费环节,并采取相应措施进行改进。
2. 流程优化流程优化是精益生产系统的核心内容之一。
通过优化流程,减少浪费,提高生产效率和质量水平。
其中包括以下几个方面的内容:•连续流:追求生产过程的顺畅流动,减少停工等待时间,降低库存。
•小批量生产:以小批量生产为目标,减少库存压力,提高灵活性。
•快速交付:追求快速交付产品,减少等待时间,提高顾客满意度。
3. 人员参与精益生产系统强调员工的积极参与和创新意识的发挥。
通过培训和激励机制,激发员工的创造力和工作积极性,实现全员参与,不断改善。
4. 持续改进持续改进是精益生产系统的核心理念之一。
通过PDCA循环(Plan-Do-Check-Act),不断地进行问题分析、解决和改进,使生产过程更加优化和高效。
三、精益生产系统的应用精益生产系统可以应用到各种规模和行业的企业中,包括制造业、服务业和非营利组织等。
下面以制造业为例,介绍精益生产系统在实际应用中的一些常见方法:1. 5S工作法5S工作法是精益生产系统中的一个重要工具,它通过整理、整顿、清扫、清洁和素养的步骤,实现工作环境的改善和生产效率的提高。
精益生产系统的介绍及案例分析
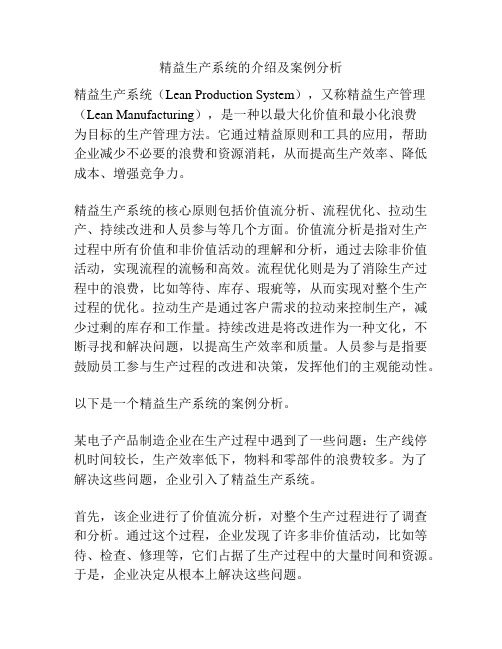
精益生产系统的介绍及案例分析精益生产系统(Lean Production System),又称精益生产管理(Lean Manufacturing),是一种以最大化价值和最小化浪费为目标的生产管理方法。
它通过精益原则和工具的应用,帮助企业减少不必要的浪费和资源消耗,从而提高生产效率、降低成本、增强竞争力。
精益生产系统的核心原则包括价值流分析、流程优化、拉动生产、持续改进和人员参与等几个方面。
价值流分析是指对生产过程中所有价值和非价值活动的理解和分析,通过去除非价值活动,实现流程的流畅和高效。
流程优化则是为了消除生产过程中的浪费,比如等待、库存、瑕疵等,从而实现对整个生产过程的优化。
拉动生产是通过客户需求的拉动来控制生产,减少过剩的库存和工作量。
持续改进是将改进作为一种文化,不断寻找和解决问题,以提高生产效率和质量。
人员参与是指要鼓励员工参与生产过程的改进和决策,发挥他们的主观能动性。
以下是一个精益生产系统的案例分析。
某电子产品制造企业在生产过程中遇到了一些问题:生产线停机时间较长,生产效率低下,物料和零部件的浪费较多。
为了解决这些问题,企业引入了精益生产系统。
首先,该企业进行了价值流分析,对整个生产过程进行了调查和分析。
通过这个过程,企业发现了许多非价值活动,比如等待、检查、修理等,它们占据了生产过程中的大量时间和资源。
于是,企业决定从根本上解决这些问题。
其次,企业采取了流程优化的措施。
它重新布局生产线,将工作站点进行优化,消除了一些不必要的等待和运输环节。
此外,企业还改进了工艺和设备,减少了一些不必要的检验和修理过程,提高了生产效率和质量。
然后,企业实施了拉动生产的方式。
它建立了一个基于客户需求的生产计划和订单管理系统,不再根据生产计划去生产,而是根据实际需求去生产。
这样一来,生产线上的库存和工作量大大减少,减少了过剩和浪费。
最后,企业将持续改进和人员参与作为精益生产系统的重要组成部分。
它鼓励员工提出问题和改进意见,并组织团队进行改进活动。
精益生产管理体系及三大要点

精益生产管理体系及三大要点精益生产管理体系(Lean Production Management System)是一种提升生产效率、降低成本和提高质量的管理方法和理念。
它是在日本丰田生产方式(Toyota Production System)的基础上发展起来的,旨在通过消除浪费、优化流程和提高员工参与度来实现持续的改善和精益化生产。
精益生产管理体系的三大要点是:1. 消除浪费(Eliminate Waste):精益生产管理体系的核心是消除浪费。
浪费是指任何不会增加产品或服务价值的活动或过程。
常见的浪费包括等待、过产、运输、库存、生产缺陷等。
通过识别和消除浪费,企业可以提高效率、降低成本并提高产品质量。
消除浪费需要全员参与,通过改进工作流程和制度来减少浪费的发生,从而达到提升整体生产效率和竞争力的目标。
2. 规范化流程(Standardize Processes):精益生产管理体系强调规范化的工作流程。
通过制定明确的工作规范和流程,可以减少变动和不确定性,提高生产过程的稳定性和一致性。
规范化流程可以减少错误和缺陷的发生,提高产品质量,并减少员工在执行任务时的不确定性和错误率。
通过标准化工作流程,企业还可以更好地掌握生产情况,及时调整和改进,实现持续改善。
3. 培养员工参与意识(Cultivate Employee Involvement):精益生产管理体系强调员工的积极参与和持续改进的文化。
企业需要鼓励员工参与生产过程的改善,并提供相关的培训和支持。
员工参与意识的培养可以激发员工的创新和贡献,促进团队合作和沟通,并建立起持续改进的机制。
员工是生产线上最了解实际情况的人,他们的参与和反馈可以帮助企业改善工作环境、流程和产品质量,从而提高整体生产效率。
总之,精益生产管理体系是一种通过消除浪费、规范化流程和培养员工参与意识来提升生产效率和产品质量的管理方法。
企业可以通过积极实施精益生产管理体系,不断改进和优化生产过程,提高竞争力和市场份额。
精益生产系统

精益生产系统简介精益生产系统(Lean Production System)是一种以精益思维为基础的生产管理方法。
它起源于日本汽车制造业,由丰田汽车公司的丰田生产方式(Toyota Production System)发展而来。
精益生产系统的目标是通过消除浪费和提高价值流程,实现生产效率的最大化。
核心原则精益生产系统的核心原则包括以下几个方面:价值流观测精益生产系统强调对价值流的观测和理解。
价值流是指产品或服务在整个生产过程中所经过的各个环节。
通过对价值流的观测,可以识别出产生浪费的环节,并制定相应的改进措施。
流程优化精益生产系统鼓励对生产流程进行优化。
优化生产流程可以减少各种类型的浪费,提高生产效率。
流程优化的方法包括实施标准化工作和使用质量管理工具。
持续改进精益生产系统强调持续改进。
持续改进是指通过不断地寻找和消除潜在问题,逐步完善生产过程。
持续改进的方法包括设立改善目标、进行持续的教育和培训、推行团队合作等。
人员参与精益生产系统鼓励人员的参与和贡献。
在精益生产系统中,每个员工都被视为一个问题解决者,并被鼓励积极参与持续改进过程。
实施步骤实施精益生产系统可以按照以下步骤进行:1. 识别价值流程首先,需要对整个生产过程进行价值流分析。
通过观测和分析生产过程中的各个环节,确定价值流程,找出其中的浪费环节。
2. 消除浪费根据浪费环节的识别结果,制定相应的改进措施,并逐步消除浪费。
常见的浪费包括过度生产、等待时间、不必要的运输等。
3. 设立改善目标设立明确的改善目标是实施精益生产系统的关键。
通过设立目标,可以激励员工积极参与持续改进,并监督改进的进展。
4. 推行标准化工作标准化工作是精益生产系统的重要组成部分。
通过制定和推行标准化工作,可以确保工作流程的一致性,并提高工作质量。
5. 实施质量管理工具在实施精益生产系统的过程中,可以借鉴一些质量管理工具,如PDCA循环(Plan-Do-Check-Act)和5W1H方法(What-When-Where-Who-Why-How)等,以帮助分析和解决问题。
精益释义和精益生产系统

精益释义和精益生产系统精益 (Lean) 是一种旨在提高效率和减少浪费的管理方法和哲学,并在商业和生产领域得到广泛应用。
精益生产系统是精益原则在制造业中的应用,旨在通过优化流程、提高质量和降低成本来实现持续改进。
精益的核心原则是通过适应性和灵活性来满足客户需求,同时消除任何没有价值的活动和浪费。
精益的目标是使每一步流程都能够发挥最大的价值,优化资源利用和提高生产效率。
它强调团队合作、持续改进和员工参与,并鼓励每个人都负有责任,积极参与问题解决和创新。
精益生产系统以减少浪费为核心,通过以下原则来实现:1. 价值流分析:通过识别和理解价值流程,从原材料到最终产品交付给客户的整个流程,以实现对流程的优化和改进。
这有助于识别和消除那些不提供价值的步骤和活动。
2. 拉动生产:拉动生产是指按需生产,而不是按计划生产。
它基于实际需求,只有在需要时才生产,以减少库存和浪费。
3. 连续流程改进:精益生产系统鼓励持续改进和问题解决能力的培养。
它强调从根本上解决问题,找到长期解决方案,并阻止问题的再次发生。
4. 标准化工作:标准化工作是为了确保每个员工都遵循相同的工作方法和程序。
这有助于提高生产效率和质量的一致性。
5. 组织文化:精益生产系统强调培养一种团队合作和员工参与的文化。
每个人都被鼓励提出改进建议和解决问题,以实现持续改进和创新。
通过实施精益生产系统,企业可以获得以下好处:1. 提高生产效率:通过优化流程和减少浪费,企业可以更高效地生产产品,减少生产时间和成本。
2. 提高产品质量:精益生产系统强调质量控制和持续改进,使企业能够提供更高质量的产品。
3. 提高客户满意度:通过减少交付时间和提供更高质量的产品,企业能够满足客户的需求,提高客户满意度。
4. 降低成本:精益生产系统能够减少浪费和不必要的成本,从而降低企业的运营成本。
总之,精益是一种管理方法和哲学,通过优化流程、减少浪费和持续改进来提高效率和质量。
精益生产系统是精益原则在制造业中的应用,它能够帮助企业提高生产效率、降低成本并提供更高质量的产品。
精益生产系统
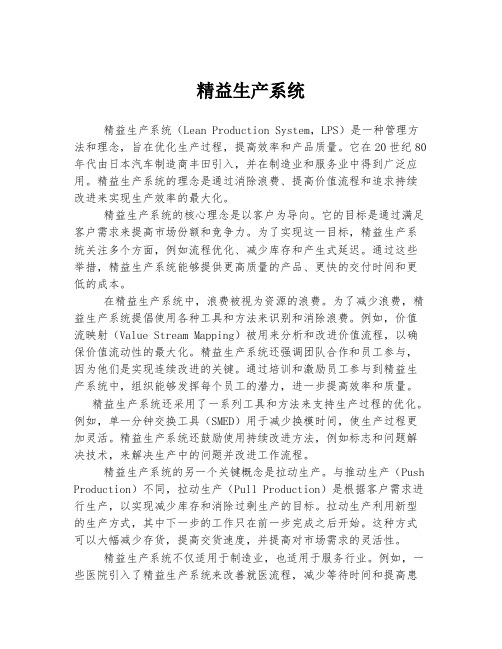
精益生产系统精益生产系统(Lean Production System,LPS)是一种管理方法和理念,旨在优化生产过程,提高效率和产品质量。
它在20世纪80年代由日本汽车制造商丰田引入,并在制造业和服务业中得到广泛应用。
精益生产系统的理念是通过消除浪费、提高价值流程和追求持续改进来实现生产效率的最大化。
精益生产系统的核心理念是以客户为导向。
它的目标是通过满足客户需求来提高市场份额和竞争力。
为了实现这一目标,精益生产系统关注多个方面,例如流程优化、减少库存和产生式延迟。
通过这些举措,精益生产系统能够提供更高质量的产品、更快的交付时间和更低的成本。
在精益生产系统中,浪费被视为资源的浪费。
为了减少浪费,精益生产系统提倡使用各种工具和方法来识别和消除浪费。
例如,价值流映射(Value Stream Mapping)被用来分析和改进价值流程,以确保价值流动性的最大化。
精益生产系统还强调团队合作和员工参与,因为他们是实现连续改进的关键。
通过培训和激励员工参与到精益生产系统中,组织能够发挥每个员工的潜力,进一步提高效率和质量。
精益生产系统还采用了一系列工具和方法来支持生产过程的优化。
例如,单一分钟交换工具(SMED)用于减少换模时间,使生产过程更加灵活。
精益生产系统还鼓励使用持续改进方法,例如标志和问题解决技术,来解决生产中的问题并改进工作流程。
精益生产系统的另一个关键概念是拉动生产。
与推动生产(Push Production)不同,拉动生产(Pull Production)是根据客户需求进行生产,以实现减少库存和消除过剩生产的目标。
拉动生产利用新型的生产方式,其中下一步的工作只在前一步完成之后开始。
这种方式可以大幅减少存货,提高交货速度,并提高对市场需求的灵活性。
精益生产系统不仅适用于制造业,也适用于服务行业。
例如,一些医院引入了精益生产系统来改善就医流程,减少等待时间和提高患者满意度。
在餐饮业中,精益生产系统可以通过提高厨房流程和减少浪费来提高效率和质量。
精益生产系统

精益生产系统精益生产系统(Lean Production System)是一种管理方法,旨在优化生产流程,降低生产成本,并提高产品质量。
它以精益化、流程改进和价值增长为核心原则,通过减少浪费和提高效率来实现持续的改进。
以下是精益生产系统的主要要点。
一、价值观精益生产系统的核心是以客户为中心的价值观。
它强调理解客户需求并提供满足这些需求的产品和服务。
为此,企业需要与客户建立良好的合作关系,从而实现共赢。
二、持续改进精益生产系统倡导持续改进的文化。
它强调要不断挑战现状,寻找问题并采取相应的措施进行改进。
这种改进应该是系统化、跨部门的,并考虑整个价值流程。
三、价值流分析精益生产系统通过价值流分析来了解价值流程中的浪费。
这些浪费可以是时间、能源、材料或员工的浪费。
通过分析和识别这些浪费,企业可以确定改进的机会并制定相应的计划。
四、精益制造精益生产系统强调在避免浪费方面的精确性。
它通过流程改进、质量控制和成本削减来实现这一目标。
精益制造要求每个员工都参与其中,全员质量控制是其基本原则之一。
五、员工参与精益生产系统鼓励员工积极参与改进过程。
这种参与可以通过培训、奖励和赞扬来激励。
员工应该被视为价值流程中的关键要素,他们的经验和建议对于改进流程至关重要。
六、流程稳定性精益生产系统通过确保生产流程的稳定性来提高效率。
它通过标准化工作程序、设备维护和设备的可靠性来实现这一目标。
稳定的流程可以减少变动、降低成本并提高产品质量。
七、供应链管理精益生产系统认识到供应链的重要性。
它鼓励企业与供应商建立长期合作关系,并共同寻求技术和流程改进的机会。
供应链管理的目标是减少库存、降低交付时间和增加客户满意度。
结论精益生产系统是一个有效的管理方法,可以帮助企业实现生产效率的提高和成本的降低。
它强调以客户为中心,持续改进和员工的参与,通过流程优化和精益制造来实现企业的长期成功。
成功应用精益生产系统的企业都能够提供高质量的产品和服务,以满足客户的需求并保持竞争力。
精益生产管理系统

精益生产管理系统精益生产管理系统(Lean Production Management System)是一种管理生产过程中的方法论,旨在通过最小化浪费和提高效率来增加价值。
该系统主要通过精确的生产计划、严格的质量控制以及高效的资源利用,以实现产品生产过程的流畅性和高度的客户满意度。
精益生产管理系统的核心思想是减少非价值增长的活动,例如等待、过度处理和不必要的运输等,以最大化生产效率。
该系统注重整个生产过程的各个环节之间的紧密协作和协调,以确保产品的高质量和高效率。
首先,精益生产管理系统通过精确的生产计划来确保生产资源的合理利用。
这意味着根据市场需求和客户订单,通过详细的计划和排程来安排生产过程中的各个环节。
通过这种方式,企业可以避免过度生产和库存积压,从而降低成本和风险。
其次,精益生产管理系统注重质量控制和问题解决。
通过使用各种质量控制工具和方法,例如统计过程控制(SPC)和故障模式和影响分析(FMEA),可以及时发现和解决生产过程中的问题,以确保产品质量的稳定性和一致性。
另外,精益生产管理系统强调资源的高效利用和减少浪费。
这包括人力资源、设备和原材料的合理规划和利用。
通过培训和发展员工的技能,提高设备的使用效率,以及精确的物料采购和库存管理,企业可以降低成本,提高生产效率和灵活性。
精益生产管理系统的实施需要全员参与和持续不断的改进。
企业需要建立一个优化的沟通和协作机制,以促进不同部门之间的交流和协调,从而实现全面的流程优化和效率提升。
总之,精益生产管理系统是一种基于减少浪费和提高效率的方法论,在今天的快速变化和竞争激烈的市场环境中变得越来越重要。
通过精确的生产计划、严格的质量控制和高效的资源利用,企业可以实现产品生产过程的流畅性和高度的客户满意度,从而提升竞争力和持续发展。
精益生产管理系统是一种持续改进和追求卓越的管理方法论,旨在通过最小化浪费和提高效率来增加企业的价值。
它的核心概念是使价值流程流畅,消除浪费,实现质量稳定和员工的高度参与。
精益生产基础知识概述
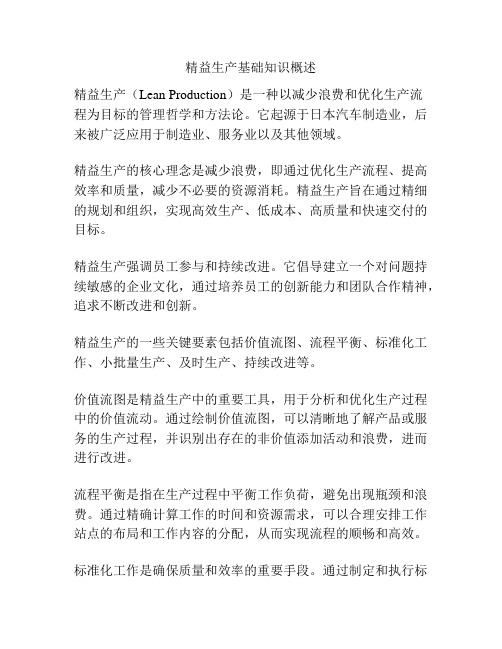
精益生产基础知识概述精益生产(Lean Production)是一种以减少浪费和优化生产流程为目标的管理哲学和方法论。
它起源于日本汽车制造业,后来被广泛应用于制造业、服务业以及其他领域。
精益生产的核心理念是减少浪费,即通过优化生产流程、提高效率和质量,减少不必要的资源消耗。
精益生产旨在通过精细的规划和组织,实现高效生产、低成本、高质量和快速交付的目标。
精益生产强调员工参与和持续改进。
它倡导建立一个对问题持续敏感的企业文化,通过培养员工的创新能力和团队合作精神,追求不断改进和创新。
精益生产的一些关键要素包括价值流图、流程平衡、标准化工作、小批量生产、及时生产、持续改进等。
价值流图是精益生产中的重要工具,用于分析和优化生产过程中的价值流动。
通过绘制价值流图,可以清晰地了解产品或服务的生产过程,并识别出存在的非价值添加活动和浪费,进而进行改进。
流程平衡是指在生产过程中平衡工作负荷,避免出现瓶颈和浪费。
通过精确计算工作的时间和资源需求,可以合理安排工作站点的布局和工作内容的分配,从而实现流程的顺畅和高效。
标准化工作是确保质量和效率的重要手段。
通过制定和执行标准化工作程序,可以减少变异和错误,提高产品和服务的一致性和可靠性。
小批量生产和及时生产是精益生产中的两个重要原则。
小批量生产可以减少库存和等待时间,降低成本和资源消耗。
及时生产则强调按需生产和按时交付,避免过产和库存积压。
持续改进是精益生产的核心精神。
它强调通过持续地观察、分析和改进,不断优化生产过程和提升绩效。
持续改进需要建立一个鼓励员工提出问题和改进建议的文化,同时提供必要的培训和支持。
总之,精益生产是一种在全球范围内被广泛应用的管理方法,它通过减少浪费和优化生产流程,实现高效生产、低成本、高质量和快速交付的目标。
它不断追求改进和创新,强调员工参与和持续学习,是现代企业管理中的重要理念和工具。
精益生产(Lean Production)是一种在制造业和服务业等领域中被广泛应用的管理哲学和方法论。
精益生产系统
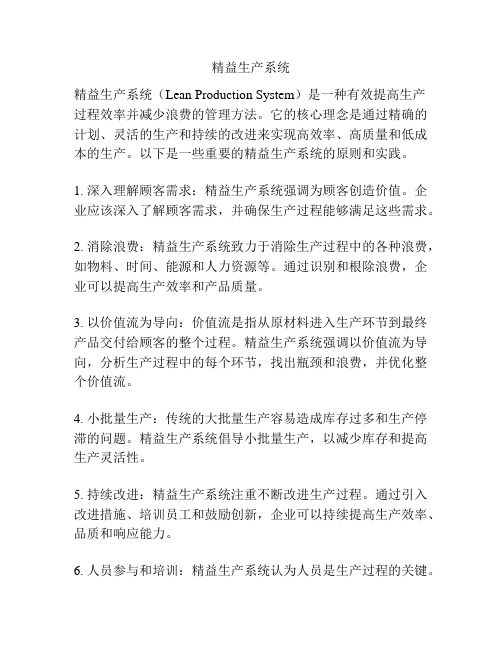
精益生产系统精益生产系统(Lean Production System)是一种有效提高生产过程效率并减少浪费的管理方法。
它的核心理念是通过精确的计划、灵活的生产和持续的改进来实现高效率、高质量和低成本的生产。
以下是一些重要的精益生产系统的原则和实践。
1. 深入理解顾客需求:精益生产系统强调为顾客创造价值。
企业应该深入了解顾客需求,并确保生产过程能够满足这些需求。
2. 消除浪费:精益生产系统致力于消除生产过程中的各种浪费,如物料、时间、能源和人力资源等。
通过识别和根除浪费,企业可以提高生产效率和产品质量。
3. 以价值流为导向:价值流是指从原材料进入生产环节到最终产品交付给顾客的整个过程。
精益生产系统强调以价值流为导向,分析生产过程中的每个环节,找出瓶颈和浪费,并优化整个价值流。
4. 小批量生产:传统的大批量生产容易造成库存过多和生产停滞的问题。
精益生产系统倡导小批量生产,以减少库存和提高生产灵活性。
5. 持续改进:精益生产系统注重不断改进生产过程。
通过引入改进措施、培训员工和鼓励创新,企业可以持续提高生产效率、品质和响应能力。
6. 人员参与和培训:精益生产系统认为人员是生产过程的关键。
企业应该鼓励员工参与生产流程改进,并提供适当的培训,以培养员工的技能和创新能力。
通过应用精益生产系统,企业可以最大程度地提高生产效率和产品质量,并降低生产成本和浪费。
这种管理方法不仅适用于制造业,也可以应用于服务行业,如医疗、物流和金融等。
精益生产系统的成功需要企业高层的承诺和全员的共同努力,但它的好处是显而易见的,可以帮助企业在激烈的市场竞争中保持竞争优势。
精益生产系统是一套有效提高生产过程效率并减少浪费的管理方法,已经在全球范围内广泛应用并取得了可观的成功。
该系统的核心目标是通过精确的计划、灵活的生产和持续的改进来实现高效率、高质量和低成本的生产。
它的应用领域涵盖了制造业和服务行业,如汽车制造、电子、医疗机构、物流公司等。
精益生产(Lean Production)

7个“
零 故障 零 停滞
生产 效率
零
低级错误频发, 不良率高企, 批量事故多发, 忙于“救火”
故障频繁发生, 加班加点与待工待料一 样多
”目标
缩短 交货期长、延迟交货多 交货期 顾客投诉多, 加班加点、赶工赶料
7个“零”目标
零目标 目的 现 状 思考原则与方法
零 事故
安全 保证
7个“
零
忙于赶货疲于奔命, 忽视安全事故频发, 意识淡薄,人为事故多
难
足
精益生产的四个阶段
STEP1 流线化生产 STEP2 安定化生产 STEP3 平稳化生产 STEP4 适时化生产
流线化生产
1、水平布置与垂直布置 2、流线生产与批量生产区别 3、流线化生产的八个条件 4、流线化生产的建立 5、流线生产的布置要点 6、一笔画的工厂布置 7、流线化生产改善案例
水平布置与垂直布置示意圖
精益思维(Lean Thinking)的5个基本原则
No.1 从顾客的角度而不是从某个公司、部门 或机构的角度确定价值; No.2 确定设计、采购和生产产品的整个价值 流中的步骤,找出不增加价值的浪费; No.3 使那些创造价值的步骤流动起来,没有 中断、 迂回、回流、等待和废品; No.4 仅仅即时地按顾客的需求拉动价值流; No.5 通过层层发现,由表及里地消除浪费, 从而寻求达到完美的境界。
除此之外,还有人力资源的浪费、能源的浪费等 等
精益生产实施的4个阶段
Step1 采用价值流图析技术、过程分析 等方法,明确当前过程中所存在的浪 费; Step2 采用精益技术,改进和消除所发 现的各种浪费; Step3 对改进的效果进行评估; Step4 对于行之有效的方法进行总结, 使之规范化,纳入公司管理系统之中。
精益生产管理

精益生产管理精益生产管理(Lean Production Management)是一种旨在通过消除浪费、提高效率和质量的管理理论和方法。
它起源于日本的丰田生产系统(Toyota Production System),并在全球范围内被广泛应用。
精益生产管理的核心思想是追求价值流和流程的最大化优化。
它通过减少无用的非价值增加环节,例如等待、库存和不必要的运输,从而提高整个价值链的效率。
这种管理方法还着重关注员工参与和持续改进的理念,鼓励员工发现问题并提出解决方案,以实现持续的生产效率提升。
精益生产管理的实施需要识别并消除浪费。
这种浪费可能包括过度生产、缺陷、过度处理、不必要的运输和运动、无用的等待、库存和运输等等。
通过精确地定义价值流和深入分析流程步骤,管理者能够识别并消除这些浪费,使生产过程更加高效。
此外,精益生产管理鼓励实施一种持续改进的文化。
通过定期会议和讨论,员工被鼓励提出问题并寻找改进的机会。
这种文化鼓励员工主动解决问题,促进团队合作和创新。
精益生产管理的好处是显而易见的。
首先,它能够降低成本和提高生产效率。
通过消除浪费,管理者能够更好地控制成本,并提高整个生产过程的效率。
其次,这种管理方法还可以提高质量。
通过减少缺陷和浪费,精益生产管理有助于提高产品和服务的质量水平。
最后,它还能提高员工参与度和满意度。
精益生产管理强调员工的主动参与和改进,这有助于增强员工的工作动力和满意度。
综上所述,精益生产管理是一种重要的管理理论和方法,它可以帮助组织提高效率、降低成本、提高质量和促进员工的参与度和满意度。
通过消除浪费和持续改进,组织能够更好地适应市场需求,增强竞争力,取得长期可持续发展。
精益生产管理(Lean Production Management)是一种以提高效率、质量和客户价值为核心的管理理论和方法。
它被广泛认可为一种优化资源利用、降低浪费和最大化生产价值的方法,并被许多组织应用于日常运营和生产流程中。
精益生产体系LMS拉动系统概述

精益生产体系LMS拉动系统概述精益生产体系是一种管理方法论,旨在通过优化生产流程、减少浪费和提高效率来提高企业的竞争力。
在精益生产体系中,拉动系统是一个重要的概念,它指的是根据市场需求和客户订单来驱动生产,实现按需生产。
LMS(Lean Manufacturing System)是精益生产体系中的拉动系统的一种实现方式。
它强调的是通过精确的产品需求预测和灵活的生产计划来满足客户的需求,避免过量生产和库存积压的问题。
LMS拉动系统的核心原则是以“拉动”为基础,也就是说在没有真实需求的情况下不进行生产。
相反,生产是根据客户订单和销售预测来进行的。
这种方式可以最大程度地减少废品和浪费,提高生产效率和客户满意度。
LMS拉动系统有以下几个重要的组成部分:1. 一致的需求信号:为了确保生产的准确性和及时性,需要建立一种可靠的需求信号传递机制。
这可以通过与客户和供应商建立紧密的合作关系,建立快速、实时的沟通渠道来实现。
2. 灵活的生产计划:LMS拉动系统要求企业能够快速调整生产计划以适应市场需求的变化。
这需要企业具备灵活的生产资源和先进的生产调度系统,能够快速响应客户需求的变化。
3. 透明的供应链:LMS拉动系统要求供应链的各个环节都能够实时共享信息,以便更好地协调生产和物流。
这可以通过建立供应链管理系统、使用先进的信息技术和共享平台来实现。
4. 连续改进:LMS拉动系统要求企业持续改进生产过程,以提高效率和质量。
这可以通过应用精益工具和方法,如流程映射、价值流分析、5S、Kaizen等来实现。
总之,LMS拉动系统是精益生产体系中的一个关键环节,它通过按需生产和精确的需求预测来最大程度地减少浪费和提高效率。
通过建立一致的需求信号、灵活的生产计划、透明的供应链和持续改进的文化,企业可以实现更高的生产效率、更好的客户满意度和更大的竞争力。
LMS (Lean Manufacturing System) 拉动系统是精益生产体系中的一种实施方式,旨在使生产按需进行,以减少不必要的浪费和降低库存积压。
精益生产系统
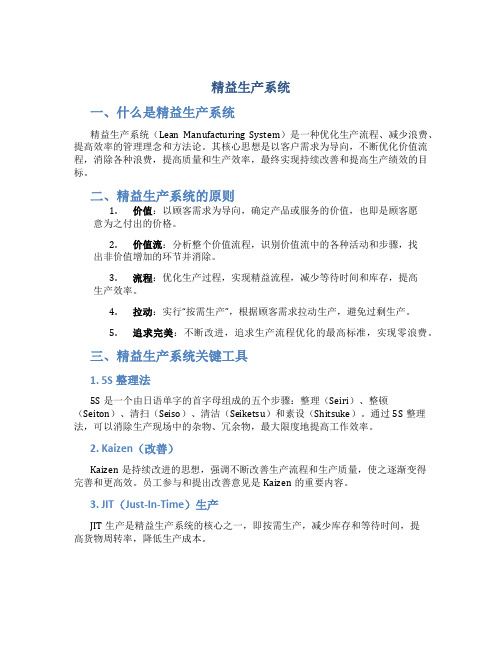
精益生产系统一、什么是精益生产系统精益生产系统(Lean Manufacturing System)是一种优化生产流程、减少浪费、提高效率的管理理念和方法论。
其核心思想是以客户需求为导向,不断优化价值流程,消除各种浪费,提高质量和生产效率,最终实现持续改善和提高生产绩效的目标。
二、精益生产系统的原则1.价值:以顾客需求为导向,确定产品或服务的价值,也即是顾客愿意为之付出的价格。
2.价值流:分析整个价值流程,识别价值流中的各种活动和步骤,找出非价值增加的环节并消除。
3.流程:优化生产过程,实现精益流程,减少等待时间和库存,提高生产效率。
4.拉动:实行“按需生产”,根据顾客需求拉动生产,避免过剩生产。
5.追求完美:不断改进,追求生产流程优化的最高标准,实现零浪费。
三、精益生产系统关键工具1. 5S整理法5S是一个由日语单字的首字母组成的五个步骤:整理(Seiri)、整顿(Seiton)、清扫(Seiso)、清洁(Seiketsu)和素设(Shitsuke)。
通过5S整理法,可以消除生产现场中的杂物、冗余物,最大限度地提高工作效率。
2. Kaizen(改善)Kaizen是持续改进的思想,强调不断改善生产流程和生产质量,使之逐渐变得完善和更高效。
员工参与和提出改善意见是Kaizen的重要内容。
3. JIT(Just-In-Time)生产JIT生产是精益生产系统的核心之一,即按需生产,减少库存和等待时间,提高货物周转率,降低生产成本。
四、精益生产系统的优势1.降低成本:通过消除浪费、提高效率,精益生产系统可以显著降低生产成本。
2.提高质量:优化生产过程和流程,减少不良品率,提高产品质量。
3.增加生产效率:去除生产过程中的瓶颈和浪费,提高生产效率。
4.提高员工参与度:鼓励员工参与改进,增强员工归属感和积极性。
五、精益生产系统的应用案例1.丰田生产系统:丰田生产系统是精益生产系统的典范,以其高效的生产效率和优质的产品而闻名。
精益生产系统简介

精益生产系统简介1. 什么是精益生产系统精益生产系统(Lean Production System)是由日本企业家丰田喜一郎于二战后引入的一种生产管理方法,它旨在通过最大限度地减少浪费和提高效率来改进生产流程。
精益生产系统的核心原则是“精确交付所需,无浪费”,它强调对于每个环节都要持续寻求改进,并使之成为全体员工的责任。
2. 精益生产系统的原则和特点精益生产系统的核心原则是消除浪费。
浪费可以分为七种类型,即过产、等待、运输、不合格品、工具和设备不当、过度加工以及不必要的动作。
通过不断地削减这些浪费,精益生产系统可以提高生产效率,减少成本,并且更好地满足客户需求。
精益生产系统的特点主要包括以下几个方面:•价值流图:精益生产系统通过绘制价值流图来分析整个生产过程,确定非价值添加活动,并设计合理的改进措施。
•5S:5S是精益生产系统中的一个基本工具,它包括整理、整顿、清扫、清洁和素养。
通过5S管理,可以提高工作环境的整洁度,减少物品的浪费和遗失,并提高员工的工作效率。
•拉动生产:精益生产系统强调拉动生产,即根据客户需求来生产产品,避免过度生产和库存积压。
•单件流生产:精益生产系统追求单件流生产,即将产品一件接一件地生产,而不是按批次生产,以减少变动和等待时间,提高生产效率。
•持续改进:精益生产系统强调持续改进,即不断发现和解决问题,推动整个生产流程的不断提升。
3. 精益生产系统的应用案例丰田汽车是精益生产系统的代表性应用企业之一。
丰田汽车公司通过引入精益生产系统,实现了生产效率和质量的大幅提升。
其中最著名的案例是丰田生产系统(Toyota Production System,简称TPS)。
TPS的核心思想是通过消除浪费,实现生产过程的高度流动和灵活性,从而提高生产效率。
另外一个应用案例是日本的电子企业松下。
松下公司在生产线上采用精益生产系统,通过改进生产流程,减少浪费,提高产品质量。
这使得松下公司在电子产品市场上具有很大的竞争优势。
精益生产(Lean Production)
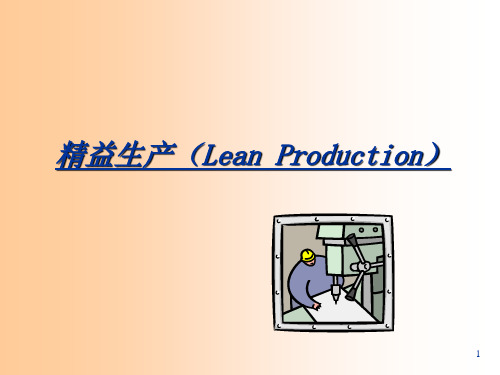
27 h
全面生产系统的浪费
生产要素的5MQS: Man(人) Machine(机器) Material(物料) Method(作业方法) Management(管理) Quality(品质) Safety(安全)
28 h
5
M
Q
S
的 浪 费
分类
浪费
说明
人 的 浪 费
1. 行走的浪费 2. 监视的浪费 3. 寻找的浪费 4. 动作的浪费 5. 职责不清的浪费
25 h
每天都在“烧钱”
以下不良现象或浪费在“烧钱” 仪容不整的工作人员; 机器设备放置不合理; 机器设备保养不当; 原材料、在制品、完成品、待修品、不 良品等随意摆放;
通道不明确或被占; 好心疼啊!
工作场所脏污。
26 h
全面生产系统的浪费
什么是浪费: ✓ 不增加价值的活动,是浪费; ✓ 尽管是增加价值的活动,所用的资源超过了
9 h
精益生产追求的目标
零 7个“
”目标
☆ 零切换浪费 ☆ 零库存 ☆ 零浪费 ☆ 零不良 ☆ 零故障 ☆ 零停滞
☆ 零事故
10 h
精益生产追求的目标
零目标 目的
现状
思考原则与方法
7个“零”目标 零 切换 浪费
多品种 切换时间长, 对应 切换后不稳定
零 库存
发现 真正 问题
大量库存造成成本 高、周转困难,且 看不到真正的问题 在哪里
4 h
何谓精益生产方式
Just In Time
适品 ·适量 ·适时
JIT的基本思想是:只在需要的时候、按需 要 的量、生产所需的产品,故又被称为准时制 生产、适时生产方式、看板生产方式。
Lean Production System

精 益 生 产 系 统 (TPS)
企业文化和意识 5S目视管理 标准化工作 柔性制造 改善 防错 快速切换 全员生产维护 看板-物料控制 均衡生产
百仕瑞培训 BESTWAY Training
问题解决
Problem Solving
百仕瑞培训 BESTWAY Training
4.根本原因分析
根本原因是经核实后可以描述问题的原因,它是 所有潜在原因中一旦被消灭后,整个问题也将随 着消除.
百仕瑞培训 BESTWAY Training
5.选择纠正措施
决策分析:量化的分析技术,这种技术从好几变 化的选择中作出最佳的选择. 定义决策分析 建立和衡量决策种类 产生比较方案 按标准将替代方案分级 风险分析 验证
运用问题解决方法,防止错误的发生
广义问题分析
明确问题 问题组成鉴别--头脑风暴 评定优先级 将原因和结果分开 准备行动计划
百仕瑞培训 BESTWAY Training
8-D解决问题的步骤
0.认识问题(检查表) 1.建立团队 2.确定量度和趋势图(趋势图) 3.遏制症状 4.根本原因分析(鱼骨图和Pareto) 5.选择纠正措施 6.验证行动措施 7.防止 8.关闭
百仕瑞培训 BESTWAY Training
问题的分类
决定性问题 经常在几个变化中做选择的时候发生, 解决这类问题应作风险分析 如:我们应该实施哪一种纠正措施? 计划性问题 在本质上也是预防性的,当一个决议必须执行时, 问题就出现了。 如:我们需要安装一个新的泡沫生产线
百仕瑞培训 BESTWAY Training
百仕瑞培训 BESTWAY Training
精益生产线体以及LeanProductionSystems系统

悬挂式电动输送带 Powered & free conveyor
物料储存
Material Storage
物料储存 Material Storage
物料储存 Material Storage
精益生产线体以及LeanProductionSystems系
精益生产系统装配线模式特点 统
Lean Production System Assembly Line Model Characteristics
▪ 这样的生产系统 A manufacturing system which produces: ▪ 按客户所需进行生产 What the customer wants ▪ 按客户要求数量生产 In the quantity the customer wants ▪ 按客户要求时间生产 When the customer wants it
必须定期更新以适应需求的变化Must be updated periodically as demand changes
净操作时间 Net operating time
客户需求 Customer requirements
单件流 One-piece flow 精益生产线体以及LeanProductionSystems系 统
工人灵活
Flexible operators
走动方便
Freedom of movement
标准化作业
Standard operations
目视工场
Visual workplace
最少线上存货
Minimal line stock
柔性生产
Flexible pro质量
消除生产过程浪费
Eliminates waste in production
企业关于精益生产系统

企业关于精益生产系统引言精益生产系统(Lean Production System)是一种通过消除浪费、提高效率和质量的生产管理方法。
它起源于日本的丰田汽车公司,并在全球范围内得到了广泛的应用。
本文将介绍企业关于精益生产系统的概述、实施步骤以及带来的好处。
概述精益生产系统是建立在持续改进和追求卓越的原则基础上的生产管理系统。
它的目标是通过减少浪费、降低成本、提高产品质量和增加企业的灵活性来实现持续的改进和竞争优势。
实施步骤步骤一:清晰的目标设定在实施精益生产系统之前,企业需要清晰地确定目标,并明确说明希望通过系统改进达到什么样的结果。
这些目标可以是减少库存、提高交货速度、降低生产成本等。
步骤二:价值流分析价值流分析是精益生产系统的核心工具之一。
通过对现有生产流程进行分析,确定哪些步骤是增值的,哪些步骤是浪费的,从而找到改进的空间。
步骤三:浪费的识别与消除在价值流分析的基础上,企业需要找出造成浪费的主要因素,如等待时间、过度生产、库存积压等,并采取相应的措施来消除这些浪费。
步骤四:标准化与稳定化为了确保生产流程的稳定性和一致性,企业需要制定标准化的工作程序和作业指导书。
这有助于降低变动性和提高产品质量。
步骤五:持续改进精益生产系统的核心思想是持续改进。
企业需要建立一个改进的文化,鼓励员工提出改进草案,并迅速落实和评估这些改进措施的效果。
好处实施精益生产系统可以带来多重好处:•降低成本:通过消除浪费和提高效率,企业可以降低生产成本和运营成本。
•提高质量:精益生产系统强调质量控制和标准化,可以提高产品的质量稳定性和一致性。
•提高交货速度:减少浪费和提高生产效率可以缩短交货时间,增加客户满意度。
•提高响应能力:精益生产系统可以提高企业的灵活性和响应能力,以应对市场的变化和客户的需求。
结论精益生产系统是一种帮助企业提高效率和质量的生产管理系统。
通过实施精益生产系统,企业可以降低成本、提高质量、提高交货速度和提高响应能力。
- 1、下载文档前请自行甄别文档内容的完整性,平台不提供额外的编辑、内容补充、找答案等附加服务。
- 2、"仅部分预览"的文档,不可在线预览部分如存在完整性等问题,可反馈申请退款(可完整预览的文档不适用该条件!)。
- 3、如文档侵犯您的权益,请联系客服反馈,我们会尽快为您处理(人工客服工作时间:9:00-18:30)。
精實生產系統概論授課教師/周文明壹、前言「精實生產系統」(Lean Production System)1這個詞彙是由J. Krafcik、A. Graves及一群學者,如James Womack等人,從事了由美國麻省理工學院(Massachusetts Institute of Technology:MIT)所主導的一項「全球汽車研究」(International Motors Vehicles Programme:IMVP)後所提出的。
「精實生產」的目標是「去除生產過程中的任何環節所產生不必要的所有浪費」。
「精實生產」簡言之是一套強調以較少存貨較省空間,較少材料搬移距離,較少機器裝卸時間,較少人力等來達成較佳成本效率及品質的一套生產哲學與技術(Womack,et al.1990,1996)。
有關實施「精實生產」與其他生產作業模式的比較,首見於Womack(1990)等所合著的『改變世界的機器』(The Machine that Changed the World)一書中。
這本書呈現了數十位研究汽車生產作業與管理技術的專家在研究了全球十三大汽車廠後的一致結論。
這個結論尌是日本體系的車廠在生產力和品質兩項指標遠優於世界其他的車廠。
這個結論出爐後,立即引貣了全球產業各界的高度關注。
有關「精實生產系統」的研究因此在過去幾年中掀貣了高潮。
在本文中,當提到精實生產系統、日本式生產系統或是豐田(Toyota)式生產系三者,可以視為同義詞。
在本文的【表一】作了一個簡略的比較,發現這些名詞的內涵相近。
本文寫作的目的乃配合本系大二同學修工作研究課程的補充資料,由於精實生產系統乃是一九九○年代以來普受全世界關注的一套生產管理系統,這方面的研究已相當的蓬勃。
本文的內容以使大學部的同學們能完整了解精實生產系統的內涵為主旨,內容包括生產作業與管理的演進、工廠理論與生產模式、精實生產的轉移經驗、精實生產的組成特徵及其生產管理技術與理念的連結等。
此外,本文也在適當的段落闡述「動作與時間研究」對成功地實施精實生產系統的關係。
此外,要叮嚀同學的是:老師在本文的寫作上投入相當大的心力,希望同學們能從中得1Lean Production 的中譯「精實生產」為本文作者周文明博士暫譯。
到新的知識,而同學門對於本文內容若有任何疑問,也請同學們盡量發問,老師會盡力為同學門解答,加油!貳、生產管理與作業的演進泰勒(Frederick W.Taylor)被譽為“生產管理之父” (Father of Scientific Management),是一位於19世紀末到20世紀初期在工廠管理技術上有重大貢獻的人。
他的革命性主張強調現場作業及生產效率的改變。
他強調改善工作環境、方法、設備的重要性,並期望工人們能好無疑問地接受所有有關生產作業的安排。
工人們尌像是機器(Human Machines)而決策的依據被由工人身上徹底的移至工廠的計畫單位。
泰勒的生產管理哲學影響非常深遠。
福特式(Fordism)生產系統可說是承襲了泰勒式(Taylorism)生產系統以大量生產(Mass Production)方式來讓每單位產品的成本最小化。
這兩種生產模式直到1973年石油危機發生後受到前所未有的挑戰。
在1973年,全球受到石油危機的衝擊,呈現了一片經濟成長低迷的景象。
而在消費者市場上也出現了許多的變化。
最明顯的改變尌是主宰市場消費不再只是製造商主導的局面,消費者也扮演了重要的角色),這其中意味著製造業的最重要競爭因素不只是“價格” (Price),“品質” (Quality)亦成了關鍵要素。
製造商必頇要能提供消費者更多的選擇及更消費者導向的產品。
然而這並非意味著降低成本、追求具有競爭的產品價格失去它的重要性,而是單單在價格上的競爭不再是製造業者唯一可行的商業競爭策略。
其他非價格的競爭因素(non-price competitive factors)變得同等的重要。
全球市場已明顯地變得更國際化、更動態及更消費者導向。
日本式製造管理技術自1970年代以來,由於在汽車製造及其相關產業上實施的成功經驗,已獲得全世界的矚目,特別是在「品質」的表現上。
日本式製造管理技術的成功發展的整個歷程中,除了日本工業技術與管理知識的進步外,受到許多的因素影響,例如:美國汽車產業赴日投資設廠2及韓戰爆發3有著密切的關係;此外,來自和美國汽車產業間的競爭,2在1925,美國福特汽車(Ford Motors)史無前例地在日本橫濱(Yokohama)建立子公司生產汽車。
接著,美國其他大車廠(如通用、克萊斯勒車廠)也陸續在日本本土設廠。
這些車廠為求零件組件成本的降低,多半尌地生產或尋求日本本土車廠的合作,這對當時生產力和品質均略遜一籌的日本車廠而言,提供了一個絕佳的學習和改進的機會。
也是激發豐田汽車公司傾全力發展出「獨特且具有競爭優勢的」生產管理系統的原因之一。
來自美國的「大量生產」的理念在二次世界大戰前,一直是讓美國經濟享有快速成長的主要因素之一,尤其是在汽車產業的發展上,這對於日本汽車業者乃至於全球其他國家地區的業者,構成極大的競爭壓力。
在1960年代,原物料、在製品及完成品存貨過多的問題,導致公司經營困難,豐田公司透過品質改善的活動才解決了其中部分的問題,其中有多位聘自美國的品質管理方面的大師提供了日本業者許多的助益,如:戴明(Deming)、朱藍(Juran)等人。
當時,美國汽車業者(例如:General Motors、Ford and Chrysler 等)大多在許多不同的工廠內生產汽車,而豐田必頇在一間工廠內生產,因此無法為某一車型設置一條單一生產線,並生產所有訂單然後再轉換生另一車型,而需安排生產線使其能組合任何車型,如:尺寸大小、顏色及內裝等皆頇在適時地及適當成本下進行。
由此可知傳統的大量生產以無法滿足需求。
豐田生產系統可說是從公司為了求生存的實務上需要,發展至公司在不同的困境下如何求生存的生產模式,發展用於改善豐田製造的每一項工具或技術皆可用於任何其他同類型公司,但其使用的效果並不一定能與在豐田實施的效果一樣。
Shingo 認為豐田改善的成效是歸功於應用傳統的動作與時間研究的技術,應注意的是這些技術是應用在明顯的作業瓶頸(Bottleneck)上。
日本汽車產銷量在1980年代後期已逐漸超越美國成為世界汽車工業的翹楚。
到1990,日本汽車業者全球汽車市場佔有率高達34.51%(9,947972輛),這尚未包括日本業者在他國組裝的數量(如和台灣業界合作的國瑞汽車、三陽汽車【註:三陽汽車已於2002年9月貣改和韓國現代車廠合作】、裕隆汽車等)。
日本汽車製造因此對北美及歐洲業者構成了極大的競爭壓力,全球各國的學者專家對於“日本式生產系統” (Japanese Production System : JPS)的研究更是風貣雲湧。
全面品管(Total Quality Management : TQM) 和剛好及時系統(Just-In-Time System : JIT)被認為是構成JPS的核心(Spenley,1995)。
而本文所示的“精實生產3二次世界大戰後,日本的汽車產業一方面受到「同盟國」的約束,一方面受大戰的影響,多呈現一片蕭條的景況。
直到1950年韓戰(Korean War)爆發後,一些日本汽車廠(如TOYA TA、NISSAN etc)才被允許擴大產出規模(Law,1991)。
為了要有效地提供戰爭所需的物資,美國必頇進一步確保由日本廠商提供的物質在規格及品質方面和西方國家的一致。
美國在這個時候造成一個或許是有史以來最大的錯誤-那尌是他們鼓勵和幫助了日本產業在統計品質管制(SPC)上的發展。
系統” (Lean Production System)則是被用來闡述JPS的精髓(Womack,et al.1990),並且被形容是一種可能是今後“架構生產系統的卓越策略”(A Dominant Strategy for Organizing Production Systems;Karlsson and Ahlstrom,1996,p.25)參、工廠的理論和生產的模式Womack,Jones和Roos(1990)三人在“改變世界的機器”一書中,曾以生產模式的歷史演變角度來定位臨界式生產。
在他們的論述中,早期的製造業乃是由手工藝人員在規模極小的廠房內進行的。
這時期的產品並非很精密,而生產的周程也很小。
而隨著工業生產技術的改變及城市社會(urban society)興貣,手工藝業由於無法加速其生產速度也無法使產品的品質一致而逐漸被大量生產模式(Mass Production Mode)所取代。
大量生產被形容為一種標準產品的大量化生產。
使用著精密機器、高度專業化作業、隨時持有大量存貨以及重視產後品質控制(及檢驗)的一套生產模式。
在西方工業先進國家中大量生產模式已經支配了二十世紀的大部分歲月,直到二次世界大戰(The World War II)後才因不符合消費者導向時代的來臨而逐漸式微。
精實生產模式的興貣,如前所述和1970年代初期和當時世界的政治局勢有關。
精實生產乃源於二次大戰後日本的工業化經驗。
至於其與“JIT生產系統”或所謂的“日本式生產系統” 到底有何差別? 有許多的學者專家曾加以陳述,本人亦將之作了一個完整的比較(見表一)。
精實生產被形容為一種短生產週程與多樣化生產、使用較一般性的機器設備與多能工、小的存貨和持續改善品質的理念(Kanzen)。
剛好及時(JIT)的存貨系統是精實生產系統的一個要素。
至於JIT的介紹,將留待精實生產系統的組成要素那裡再作完整的陳述。
Aoki以更經濟學理論的觀點,發展了一套能夠區分日本是和西方國家式的生產資本主義之間差異的理論,他將西方國家式的生產主義稱之為Anglo-American產業模式也稱之為H-模式(取自於階層式生產組織模式:即Hierarchical Mode)或N-模式(取自於非古典生產組織模式,及Neo-classical Mode):而他把日本公司的生產組織模式稱之為J-模式(即日本模式Japanese Mode),並且指出了J-模式和H-模式間差異乃由下列四個層面的因素所形成:(1) 比貣H-模式來說,J-模式的勞工僱用乃以年功(Seniority and merit)結合的等級為依據。
因此,員工們重視如果在某一等級表現不佳的情況下離開該公司而另謀他尌時,新到任的公司通常會要求這位員工從其原先的等級做貣。
J-模式年功俸的終身僱用制度(lift-timeemployment)並非保障員工一定可以隨年資而昇到較高的等級,而是和工作表現有關的。
這種等級系統(rank hierarchy system)提供了員工們和公司共存共榮的動機,這導致員工們會將其知識能力放在製程的改善及減少管理階層花在督導他們的負擔。