§10—7渐开线变位齿轮简介
机械加工 机械原理 齿轮8

(2)传动比
i12 =r2 / r1=z2 / z1
渐开线直齿圆柱齿轮的啮合传动(3/6)
(3)啮合角 渐开线齿轮传动的啮合角α′就等于其节圆压力角。 当两轮按标准中心距安装时,则实际中心距 a′= a; 当两轮实际中心距 a′与标准中心距 a 不同时,则: 若 a′>a 时, r1′>r1,r2′>r2; c′>0,c>c*m;α′>α。 若 a′<a 时,两轮将无法安装。 (4)齿轮传动的中心距与啮合角的关系 a′cosα′= a cosα
齿轮传动的中心距与啮合角的关系 a′cosα′= a cosα 一对轮齿的啮合过程 实际啮合线段B1B2 理论啮合线段N1N2 连续传动条件 通常把 B1B2与 pb的比值εα称为齿轮的重合度, 故齿轮连续传 动的条件为
εα = B1B2 /pb ≥1
εα= [z1(tanαa1 - tanα′) +z2(tanαa2 - tanα′)]/(2π)
渐开线齿轮的变位修正(3/6)
2、标准齿轮的加工原理 1)齿轮与刀具的相对位臵 ①用范成法切制标准齿轮 时,刀具的分度线与齿轮的 分度圆相切。 ②被切齿轮的的模数、压 力角取决于刀具的模数、 压力角,齿轮的齿数取决 于刀具与齿轮的相对位臵
渐开线齿轮的变位修正(3/6)
2)渐开线齿廓的根切现象 发生根切的根本原因在 于刀具的齿顶线超过了极限 啮合点N1,即当时,就会发生 根切。 为了避免产生根切现象, 则刀具齿顶线必须位于啮合极 限点N1之下。
渐开线直齿圆柱齿轮的啮合传动(6/6)
课堂练习:已知一对标准直齿圆柱齿轮的参数如下:
求这对齿轮作无侧隙啮合时的中心距、分度圆半径、节圆半径、齿 顶圆半径、基圆半径、分度圆曲率半径及啮合角和重合度. 解:由于这对齿轮为标准齿轮,所以当它们作无侧隙啮合传动时, 其中心距等于标准中心距。则 :
渐开线齿轮传动
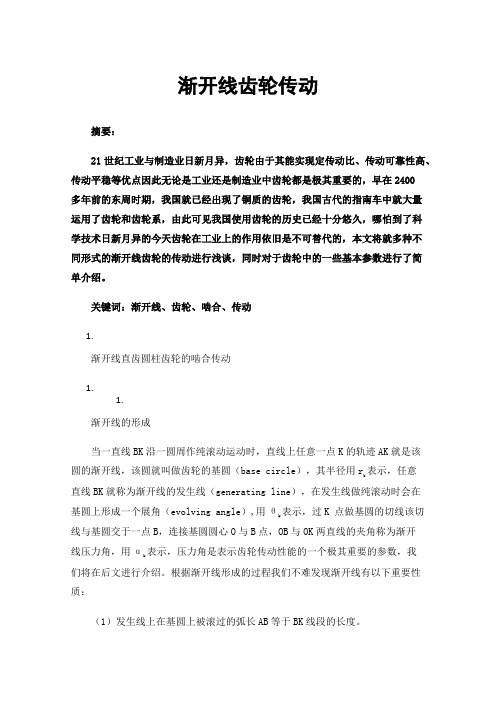
渐开线齿轮传动摘要:21世纪工业与制造业日新月异,齿轮由于其能实现定传动比、传动可靠性高、传动平稳等优点因此无论是工业还是制造业中齿轮都是极其重要的,早在2400多年前的东周时期,我国就已经出现了铜质的齿轮,我国古代的指南车中就大量运用了齿轮和齿轮系,由此可见我国使用齿轮的历史已经十分悠久,哪怕到了科学技术日新月异的今天齿轮在工业上的作用依旧是不可替代的,本文将就多种不同形式的渐开线齿轮的传动进行浅谈,同时对于齿轮中的一些基本参数进行了简单介绍。
关键词:渐开线、齿轮、啮合、传动1.渐开线直齿圆柱齿轮的啮合传动1.1.渐开线的形成当一直线BK沿一圆周作纯滚动运动时,直线上任意一点K的轨迹AK就是该圆的渐开线,该圆就叫做齿轮的基圆(base circle),其半径用r表示,任意b直线BK就称为渐开线的发生线(generating line),在发生线做纯滚动时会在表示,过K 点做基圆的切线该切基圆上形成一个展角(evolving angle),用θk线与基圆交于一点B,连接基圆圆心O与B点,OB与OK两直线的夹角称为渐开表示,压力角是表示齿轮传动性能的一个极其重要的参数,我线压力角,用αk们将在后文进行介绍。
根据渐开线形成的过程我们不难发现渐开线有以下重要性质:(1)发生线上在基圆上被滚过的弧长AB等于BK线段的长度。
(2)渐开线的曲率半径取决于基圆的大小,当基圆半径趋于无穷大时,此时齿轮将演化为齿条。
(3)基圆内部没有渐开线。
以上的性质在研究渐开线传动过程中十分重要,正因为渐开线具有这些重要性质,渐开线齿轮才在今天任是使用最普遍的齿轮形式,可以说对于渐开线齿轮的研究极大地推动了工业和制造业的发展。
1.2 渐开线直齿圆柱齿轮的啮合渐开线齿廓最大的优点就是能够满足定传动比传动。
但是两齿轮要想正确啮合还必须满足正确啮合条件。
一对渐开线齿轮在传动时,它们的齿廓啮合点都应位于啮合线N1,N2上,因此要使齿轮能正确啮合传动,应使处于啮合线上的各对轮齿都能同时进入啮合,为此两齿轮的法向齿距用pb表示,两齿轮法向齿距应相等,即式中,m1、m2及α1,α2分别为两齿轮的模数和压力角。
认识渐开线齿轮
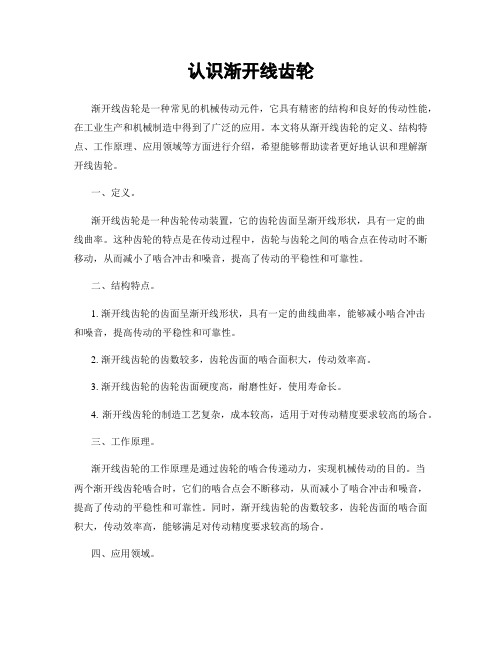
认识渐开线齿轮渐开线齿轮是一种常见的机械传动元件,它具有精密的结构和良好的传动性能,在工业生产和机械制造中得到了广泛的应用。
本文将从渐开线齿轮的定义、结构特点、工作原理、应用领域等方面进行介绍,希望能够帮助读者更好地认识和理解渐开线齿轮。
一、定义。
渐开线齿轮是一种齿轮传动装置,它的齿轮齿面呈渐开线形状,具有一定的曲线曲率。
这种齿轮的特点是在传动过程中,齿轮与齿轮之间的啮合点在传动时不断移动,从而减小了啮合冲击和噪音,提高了传动的平稳性和可靠性。
二、结构特点。
1. 渐开线齿轮的齿面呈渐开线形状,具有一定的曲线曲率,能够减小啮合冲击和噪音,提高传动的平稳性和可靠性。
2. 渐开线齿轮的齿数较多,齿轮齿面的啮合面积大,传动效率高。
3. 渐开线齿轮的齿轮齿面硬度高,耐磨性好,使用寿命长。
4. 渐开线齿轮的制造工艺复杂,成本较高,适用于对传动精度要求较高的场合。
三、工作原理。
渐开线齿轮的工作原理是通过齿轮的啮合传递动力,实现机械传动的目的。
当两个渐开线齿轮啮合时,它们的啮合点会不断移动,从而减小了啮合冲击和噪音,提高了传动的平稳性和可靠性。
同时,渐开线齿轮的齿数较多,齿轮齿面的啮合面积大,传动效率高,能够满足对传动精度要求较高的场合。
四、应用领域。
渐开线齿轮广泛应用于各种机械传动系统中,特别是在对传动精度和可靠性要求较高的场合。
例如,汽车变速箱、工程机械、风力发电机、船舶设备等领域都需要使用渐开线齿轮进行传动。
此外,渐开线齿轮还常用于精密仪器、航空航天等领域,满足了对传动精度和可靠性要求较高的场合。
总之,渐开线齿轮作为一种重要的机械传动元件,具有精密的结构和良好的传动性能,在工业生产和机械制造中得到了广泛的应用。
通过本文的介绍,相信读者对渐开线齿轮有了更深入的认识和理解,希望能够为相关领域的工程师和技术人员提供一些参考和帮助。
渐开线齿轮原理

渐开线齿轮原理一、引言渐开线齿轮是一种常见的机械传动元件,它通过齿轮的啮合来传递动力和运动。
渐开线齿轮原理的理解对于机械工程师和设计师来说至关重要。
本文将介绍渐开线齿轮的原理及其应用。
二、渐开线齿轮的定义渐开线齿轮是一种特殊形状的齿轮,其齿廓曲线为渐开线。
渐开线齿轮的齿廓曲线具有独特的性质,使得齿轮的啮合更加平稳,传动效率更高。
三、渐开线齿轮的原理1. 渐开线的定义:渐开线是一种特殊的曲线,其特点是在任意一点处的切线与该点到一个固定点的距离成正比。
在渐开线齿轮中,齿廓曲线正是由这样的渐开线构成。
2. 渐开线齿轮的齿廓曲线:渐开线齿轮的齿廓曲线是由渐开线与圆弧段组成的。
渐开线部分使得齿轮的啮合过程更加平稳,而圆弧段则用来实现齿轮的啮合。
四、渐开线齿轮的特点1. 平稳的啮合:由于渐开线齿轮的齿廓曲线特殊,使得齿轮的啮合过程更加平稳,减小了齿轮的噪声和振动。
2. 高效的传动:渐开线齿轮的齿廓曲线使得齿轮的传动效率更高,能够减小能量损失,提高传动效率。
3. 大扭矩传递能力:渐开线齿轮由于齿廓曲线的特殊性质,使得齿轮的接触面积更大,从而增加了齿轮的扭矩传递能力。
五、渐开线齿轮的应用1. 机械传动:渐开线齿轮广泛应用于各种机械传动系统中,如汽车变速器、工业机械等。
其平稳的啮合特性和高效的传动性能使其成为理想的传动元件。
2. 纺织机械:渐开线齿轮在纺织机械中的应用也非常广泛。
纺织机械中需要传递大扭矩和保持稳定的运动,渐开线齿轮能够满足这些要求。
3. 风力发电:在风力发电机组中,渐开线齿轮用于传递风力发电机的转动力和转速,保证风能转化为电能的高效率和稳定性。
六、总结渐开线齿轮作为一种常见的机械传动元件,具有平稳的啮合特性、高效的传动性能和大扭矩传递能力。
它在各种机械传动系统中得到广泛应用,如汽车变速器、工业机械、纺织机械和风力发电等领域。
了解渐开线齿轮的原理和特点对于机械工程师和设计师来说非常重要,能够帮助他们设计出更加高效和稳定的机械传动系统。
齿轮的设计
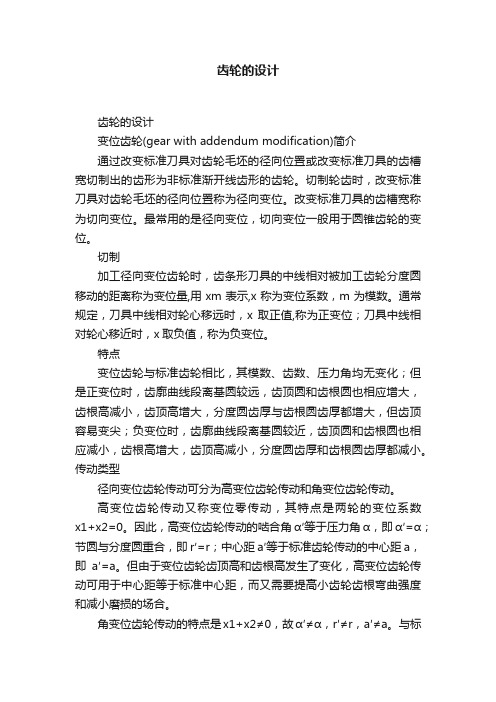
齿轮的设计齿轮的设计变位齿轮(gear with addendum modification)简介通过改变标准刀具对齿轮毛坯的径向位置或改变标准刀具的齿槽宽切制出的齿形为非标准渐开线齿形的齿轮。
切制轮齿时,改变标准刀具对齿轮毛坯的径向位置称为径向变位。
改变标准刀具的齿槽宽称为切向变位。
最常用的是径向变位,切向变位一般用于圆锥齿轮的变位。
切制加工径向变位齿轮时,齿条形刀具的中线相对被加工齿轮分度圆移动的距离称为变位量,用xm表示,x称为变位系数,m为模数。
通常规定,刀具中线相对轮心移远时,x 取正值,称为正变位;刀具中线相对轮心移近时,x取负值,称为负变位。
特点变位齿轮与标准齿轮相比,其模数、齿数、压力角均无变化;但是正变位时,齿廓曲线段离基圆较远,齿顶圆和齿根圆也相应增大,齿根高减小,齿顶高增大,分度圆齿厚与齿根圆齿厚都增大,但齿顶容易变尖;负变位时,齿廓曲线段离基圆较近,齿顶圆和齿根圆也相应减小,齿根高增大,齿顶高减小,分度圆齿厚和齿根圆齿厚都减小。
传动类型径向变位齿轮传动可分为高变位齿轮传动和角变位齿轮传动。
高变位齿轮传动又称变位零传动,其特点是两轮的变位系数x1+x2=0。
因此,高变位齿轮传动的啮合角α′等于压力角α,即α′=α;节圆与分度圆重合,即r′=r;中心距a′等于标准齿轮传动的中心距a,即a′=a。
但由于变位齿轮齿顶高和齿根高发生了变化,高变位齿轮传动可用于中心距等于标准中心距,而又需要提高小齿轮齿根弯曲强度和减小磨损的场合。
角变位齿轮传动的特点是x1+x2≠0,故α′≠α,r′≠r,a′≠a。
与标准齿轮传动相比,其啮合角发生了变化。
当x1+x2>0 时,称为正传动,此时α′>α,r′>r,a′>a。
采用正传动可以提高轮齿的接触强度和弯曲强度,改善轮齿的磨损,凑配中心距,但重合度有所减小。
当x1+x2<0 时,称为负传动,此时α′<α,r′<r,a′<a。
渐开线变位齿轮渐开线变位齿轮
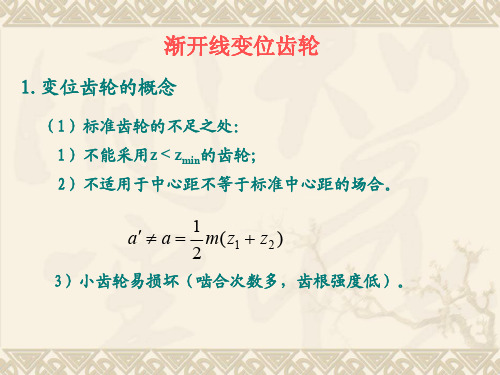
(3)变位齿轮传动的类型及特点 变位齿轮传动的类型及特点 1)标准齿轮传动
x1 + x , 且 x 2 = 0 1 = x 2 = 0
2)等变位齿轮传动(高度变位齿轮传动 高度变位齿轮传动)
x , 且 x x ¹ 0 1 + x 2 = 0 1 = - x 2
3.变位齿轮传动
(1)变位齿轮传动的正确啮合条件和连续传动条件与标准齿 变位齿轮传动的正确啮合条件和连续传动条件与标准齿 轮相同。 (2)变位齿轮传动的中心距
m ( z + z ) 1 2 + ym 保证无侧隙啮合中心距: a ' = a + ym = 2
a ' ' = r + r x m 保证标准顶隙啮合中心距: : a1 + c m f 2 = a + ( 1 + x 2 )
当x>0时,称为正变位,所加工的齿轮称为 所加工的齿轮称为正变位齿轮; 当x<0时,称为负变位,所加工的齿轮称为 所加工的齿轮称为负变位齿轮。
2.变位齿轮的几何尺寸
比较标准齿轮和变位齿轮几何尺寸 (1)分度圆及基圆尺寸不变
d = mz d b = mz cos a
(2)齿顶圆和齿根圆变化
小齿轮是正变位齿轮,大齿轮是负变位齿轮 大齿轮是负变位齿轮。
a = a ', a = a ' , y = 0 , Dy = 0
3)不等变位齿轮传动(角度变位齿轮传动 角度变位齿轮传动)
x1 + x 2 ¹ 0
x1 + x 2 > 0 正传动
x 1 + x 2 < 0 负传动
* h a = h a m + xm * h f = h a m + c * m -
(完整word版)渐开线齿轮
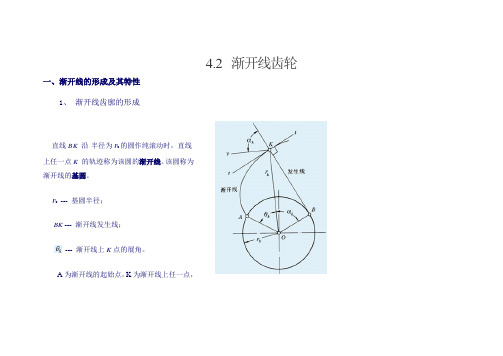
4.2 渐开线齿轮一、渐开线的形成及其特性1、渐开线齿廓的形成直线BK沿半径为r b的圆作纯滚动时,直线上任一点K 的轨迹称为该圆的渐开线。
该圆称为渐开线的基圆。
r b--- 基圆半径;BK --- 渐开线发生线;--- 渐开线上K点的展角。
A为渐开线的起始点,K为渐开线上任一点,其向径用r k表示。
渐开线齿轮的齿廓曲线是渐开线。
2、渐开线的特性1)发生线沿基圆滚过的长度,等于基圆上被滚过的圆弧长度。
由于发生线BK在基圆上作纯滚动,故2)渐开线上任一点的法线恒与基圆相切。
发生线BK沿基圆作纯滚动,它与基圆的切点B即为其速度瞬心,所以发生线BK即为渐开线在K点的法线。
又由于发生线恒切于基圆,故渐开线上任一点的法线恒与基圆相切。
3)渐开线上离基圆愈远的部分,其曲率半径愈大,渐开线愈平直。
发生线BK与基圆的切点B是渐开线在点K的曲率中心,而线段KB是相应的曲率半径,故渐开线上离基圆愈远的部分,其曲率半径愈大,渐开线愈平直;渐开线初始点A处的曲率半径为零。
4)基圆内无渐开线。
5)渐开线的形状取决于基圆的大小。
基圆愈小,渐开线愈弯曲;基圆愈大,渐开线愈平直。
当基圆半径为无穷大时,其渐开线将成为一条直线。
二、渐开线齿廓的啮合特点一对齿轮传动,是依靠主动轮的齿廓依次推动从动轮的齿廓来实现的。
因此,要能实现预定的传动比,一个齿轮最关键的部位是轮齿的齿廓曲线。
图示为一对分别属于齿轮1和齿轮2的两条齿廓曲线G1、G2在点K 啮合接触的情况。
齿廓曲线G1绕O1点转动,G2绕O2 转动。
过K点所作的两齿廓的公法线nn与连心线O1O2 相交于点C。
由三心定理知,点C是两齿廓的相对速度瞬心,齿廓曲线G1和齿廓曲线G2在该点有相同的速度:由此可得我们称点C为两齿廓的啮合节点,简称节点。
齿廓啮合基本定律:两齿廓在任一位置啮合接触时,过接触点所作的两齿廓的公法线必通过节点C,它们的传动比等于连心线O1O2被节点C所分成的两条线段的反比。
渐开线标准齿轮的基本参数和几何尺寸

渐开线标准齿轮的基本参数和⼏何尺⼨(1)斜齿轮的基本参数1)螺旋⾓,斜齿轮的齿廓曲⾯与其分度圆柱⾯相交的螺旋线的切线与齿轮轴线之间所夹的锐⾓,⼜称为斜齿轮分度圆柱的螺旋⾓,有左右旋之分,也有正负之别。
2)法⾯模数与端⾯模数的关系m n = m t cosβ3)法⾯压⼒⾓与端⾯压⼒⾓的关系tanα n = tanαt cosβ(2)斜齿轮的⼏何尺⼨计算斜齿轮的⼏何尺⼨是按其端⾯参数来进⾏计算的。
(表10-5 斜齿圆柱齿轮的参数和⼏何尺⼨的计算公式)。
2.⼀对斜齿轮的啮合传动(1)正确啮合的条件⼀对斜齿轮的正确啮合的条件,除两个轮的模数及压⼒⾓应分别相等外,它们的螺旋⾓还必须相匹配,以保证两轮在啮合处的齿廓螺旋⾓相切。
因此,⼀对斜齿轮正确啮合的条件为:1)两轮的螺旋⾓对于外啮合,应⼤⼩相等,⽅向相反,即β1=-β2;对于内啮合,应⼤⼩相等,⽅向相同,即β1=β2。
2)两轮的法⾯模数及压⼒⾓应分别相等,m n1 = m n2,αn1 = αn2。
⼜因相互啮合的两轮的螺旋⾓的绝对值相等,故其端⾯模数及压⼒⾓也分别相等,即m t1= m t2,αt1=αt2。
(2)斜齿轮传动的中⼼距a = r1+ r2 = m n(z1 + z1)/(2cosβ)(3)斜齿轮传动的重合度斜齿轮传动的总重合度εγ为其端⾯重合度εα与轴⾯重合度εβ的两部分之和,即εγ = εα + εβ其中:εα是⽤其端⾯参数并按直齿轮重合度的计算公式来计算的;⽽εβ = B sinβ/(πm n) 。
3.斜齿轮的当量齿轮和当量齿数(1)斜齿轮的当量齿轮,是指与斜齿轮法⾯齿形相当的直齿轮。
即以斜齿轮的法⾯参数m n、α n、h an*及c n*为参数,以z v ( z v = z/cos3β)为齿数所构造的直齿轮。
该直齿轮的齿形就是相当该斜齿轮的法⾯齿形。
(2)斜齿轮的当量齿数:z v = z/cos3β。
4.斜齿轮传动的主要优缺点优点:1)啮合性能好。
齿轮参数详解
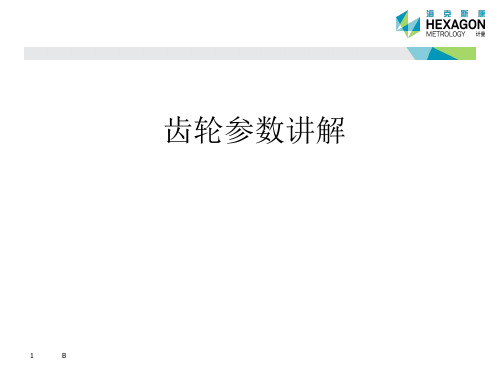
7
B
a) 内齿轮 1.齿顶圆 2.上齿面 3.节柱 4.下齿面
R b)外L齿轮
5.齿根圆 6.基准面
法面模数和端面模数
法面模数是斜齿轮法面齿形的模数;端面模数是斜齿轮端面齿形的模数。 法面模数(法面压力角,等)用于齿轮制造、强度校核。端面模数(端面压力角 ,等)用于结构尺寸计算。
对于斜齿轮,端面模数 mt 和 法面模数mn的的换算公式:
d=mz da=d±2 ha df=d±2 hf db=dcosa=mzcosa a=m(Z2±Z1)/2
ቤተ መጻሕፍቲ ባይዱ
齿数和齿面
齿数:从基准面看下去,若顺时针测量,则齿或槽定义齿/槽号为1,2…,Z为总 齿数。
齿面:如何判断一个齿面是左面还是右面?有2种方法: 1、站在齿轮外面,看齿,左手即为左齿面,右手则为右齿面 2、站在齿轮中心,看齿槽,左手即为左齿面,右手则为右齿面 对于一个齿面,不管用哪种方法,结果都是一样的。
3
B
齿轮各部分名称和基本参数
端面──垂直于齿轮轴线的平面 法面──垂直于轮齿齿线的平面 齿线──齿面与分度圆柱面的交线
基圆──形成渐开线的发生线在其上作纯 滚动的圆
齿宽b ──轮齿沿轴向的尺寸
基准齿条 ──依其标准齿轮规格所切削出来 之齿条称为基准齿条
节圆(Pitch Circle) ──两齿轮连心线上咬 合接触点各齿轮上留下轨迹称为节圆
与标准齿轮相比,由于基圆未变,所
以齿廓曲线为相同的渐开线,只是正变位
齿轮应用曲率半径较大的一段渐开线,而
负变位齿轮应用曲率半径较小的一段渐开
线。
9
B
变位齿轮
变位齿轮与标准齿轮相比,其模数、齿数、压力角均无变化; 正常非变位齿轮在分度圆处:轮齿厚度=齿槽宽度;变位齿轮,在加工时改变刀具的位置( 比正常的位置向外或向内),这样:轮齿厚度≠齿槽宽度。 正变位时,齿廓曲线段离基圆较远,齿顶圆和齿根圆也相应增大,齿根高减小,齿顶高增大 ,分度圆齿厚与齿根圆齿厚都增大,但齿顶容易变尖; 负变位时,齿廓曲线段离基圆较近,齿顶圆和齿根圆也相应减小,齿根高增大,齿顶高减小 ,分度圆齿厚和齿根圆齿厚都减小。
变位齿轮知识点总结

变位齿轮知识点总结一、变位齿轮的定义变位齿轮是一种适用于传动小功率,传递大扭矩,高速或低速的齿轮传动,由于它在传动方向上有无级变速的优点,被广泛应用在机床、纺织、工程机械及农业机械等领域。
二、变位齿轮的种类1、锥齿轮: 锥齿轮是一种圆柱齿轮的修改形式,以斜齿轮和圆锥齿轮的方式相互咬合。
2、直齿轮: 直齿轮是圆柱形齿轮的两种平行轴相互咬合,实现传动作用。
3、蜗杆齿轮: 蜗杆齿轮是由蜗杆与齿轮配对构成的一种高效率和大传动比的齿轮传动。
三、变位齿轮的优点1、传动平稳: 由于使用了多齿齿轮及齿形更弧齿形式,可以有效降低啮合冲击,使传动更平稳。
2、传动效率高: 由于采用了多齿齿轮和齿形改进设计,使其传动效率大幅提高。
3、传动扭矩大: 由于变位齿轮采用了多齿齿轮,使其传动扭矩更大,能够满足更大功率的传动需求。
四、变位齿轮的结构变位齿轮由齿轮、齿轮轴、齿轮壳体及其相关传动零件组成。
其中齿轮包括主动齿轮和从动齿轮,齿轮轴为承载齿轮的传动轴,并通过轴承支撑使齿轮能够旋转不变。
齿轮壳体为包围齿轮及其传动零件的外壳。
五、变位齿轮的应用领域1、机床: 变位齿轮广泛应用于机床的主轴驱动系统,以满足高速、大扭矩、低噪音等要求。
2、纺织: 变位齿轮在纺织机械上的应用,可以有效提高传动效率,延长设备使用寿命。
3、工程机械: 工程机械的传动系统中常常采用变位齿轮传动,以满足其高扭矩、高速、平稳等要求。
4、农业机械: 在农业机械的传动系统中,变位齿轮也被广泛应用,以适应各种不同的工作环境和工作条件。
六、变位齿轮的制造工艺1、铣削: 变位齿轮的制造过程中,铣削是其中一项重要的工艺,通过数控铣床进行齿轮齿面的精密加工,以保证齿轮的质量。
2、热处理: 在变位齿轮制造工艺中,热处理是不可或缺的一道工序,通过热处理可以有效提高齿轮的硬度、耐磨性,增强其使用寿命。
3、组装: 在变位齿轮制造的最后一个环节是齿轮的组装,通过精密的组装工艺,使得齿轮能够实现顺畅的传动。
齿数,模数和压力角相同的渐开线标准齿轮与变位齿轮
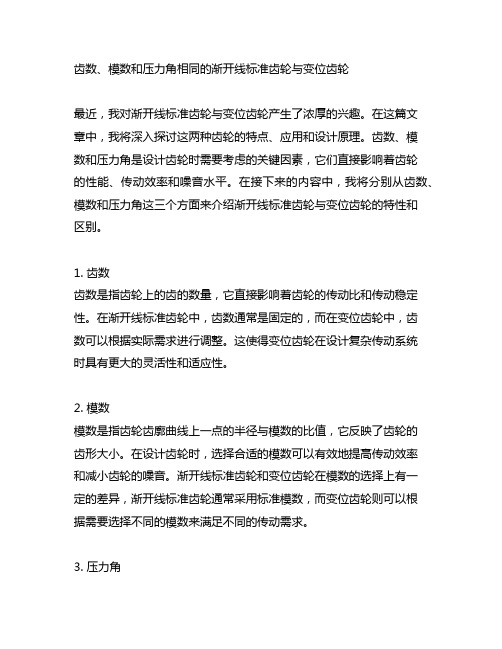
齿数、模数和压力角相同的渐开线标准齿轮与变位齿轮最近,我对渐开线标准齿轮与变位齿轮产生了浓厚的兴趣。
在这篇文章中,我将深入探讨这两种齿轮的特点、应用和设计原理。
齿数、模数和压力角是设计齿轮时需要考虑的关键因素,它们直接影响着齿轮的性能、传动效率和噪音水平。
在接下来的内容中,我将分别从齿数、模数和压力角这三个方面来介绍渐开线标准齿轮与变位齿轮的特性和区别。
1. 齿数齿数是指齿轮上的齿的数量,它直接影响着齿轮的传动比和传动稳定性。
在渐开线标准齿轮中,齿数通常是固定的,而在变位齿轮中,齿数可以根据实际需求进行调整。
这使得变位齿轮在设计复杂传动系统时具有更大的灵活性和适应性。
2. 模数模数是指齿轮齿廓曲线上一点的半径与模数的比值,它反映了齿轮的齿形大小。
在设计齿轮时,选择合适的模数可以有效地提高传动效率和减小齿轮的噪音。
渐开线标准齿轮和变位齿轮在模数的选择上有一定的差异,渐开线标准齿轮通常采用标准模数,而变位齿轮则可以根据需要选择不同的模数来满足不同的传动需求。
3. 压力角压力角是指在齿轮齿廓上两个相邻齿面的交线与径向的夹角,它直接影响着齿轮的传动容量和接触应力。
在渐开线标准齿轮中,压力角通常是固定的,而在变位齿轮中,可以根据需要选择不同的压力角来调整齿轮的传动性能。
通过合理选择压力角,可以有效地提高齿轮的传动效率和使用寿命。
齿数、模数和压力角是影响齿轮设计和性能的重要因素,它们直接关系着齿轮的传动效率、噪音特性和使用寿命。
渐开线标准齿轮和变位齿轮在这三个方面都有各自的特点和优势,设计人员应该根据具体的传动需求来选择合适的齿轮类型和参数。
个人观点和理解:在工程设计中,齿轮作为一种常见的传动元件,其设计和选择直接关系着整个传动系统的性能和可靠性。
通过深入了解齿数、模数和压力角这三个因素,可以更好地理解渐开线标准齿轮与变位齿轮的特性和适用范围,进而更加灵活地应用于实际工程中。
在撰写本文的过程中,我深刻体会到了这三个因素对齿轮设计和选择的重要性,以及渐开线标准齿轮与变位齿轮在这三个方面的差异和优势。
§10—7渐开线变位齿轮简介
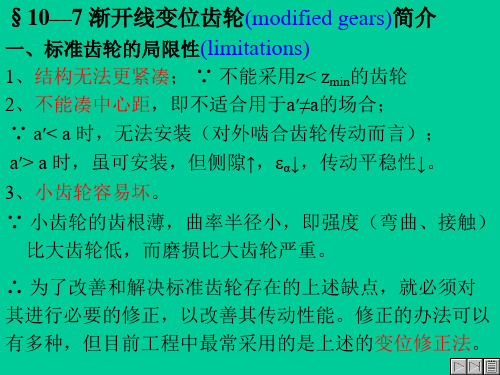
∴ 正传动优点较多,传动质量较高,而负传动缺点较多。 所以在一般情况下,应多采用正传动,负传动除了凑中 心距之外一般不采用。在中心距等于标准中心距时,为 了提高传动质量,可采用等变位传动来代替标准齿轮传 动。 ▲ 传动类型选择的大原则: 传动类型选择的大原则: ① 要求互换性较高(即易坏、易磨损),同时z >17,采 用标准齿轮传动。 ② a ′= a 时,采用标准齿轮传动、等变位传动; a ′> a 时,必须采用正传动; a ′< a 时,必须采用负传动。
2、变位齿轮传动类型 、 按一对齿轮变位系数和x1+ x2的不同来分: 1)零传动:x1 + x2 = 0 ① x1 = x2 = 0——标准齿轮传动(零变位传动) 齿数条件:z 齿数条件 1≥zmin 、z2≥zmin; 啮合特点:a ′= a、α′=α、y = 0、△y = 0。 啮合特点
② x1 = -x2(x1>0、x2<0且x1 = |x2|) ——等变位传动(又称为高度变位齿轮传动) 齿数条件:z 齿数条件 1+ z2≥2zmin;(条件较宽,∵z2都比较大) 啮合特点:a ′= a(分度圆与节圆重合)、α′=α、 啮合特点 = 0、 △y = 0。 优点:结构紧凑(∵允许z1< zmin); 优点 两轮的抗弯能力接近,相对地提高了承载能力 (∵x1>0,sf1↑;x2<0,sf2↓); 可成对替换标准齿轮,可修复旧齿轮(∵a ′= a)。 缺点:互换性差;εα↓;sa1↓(齿顶易变尖,∵x1>0); 缺点 齿面接触强度没有提高。 y
(2)标准顶隙时的中心距a″ a″= ra1 + c + rf2 = m ( z1+z2 ) / 2 + ( x1+ x2 ) m 一般情况下,a″≠a′,并且可以证明a″> a′。 ∴ 对变位齿轮传动,无法同时满足无侧隙和标准顶隙。 实际设计时解决的办法是: 两轮按中心距a ′安装,并将两轮的齿顶削短一些,来保 证标准顶隙。 设齿顶的削短量为△y m, △y称为齿顶高变动系数 齿顶高变动系数。 齿顶高变动系数 △y m = ( x1 + x2 ) m – y m ∴ △y = ( x1 + x2 ) – y > 0 这时齿顶高 ha = ( ha*+ x - △y ) m ,齿全高h减少了△y m。
机械原理第十章 标准齿轮与渐开线齿轮
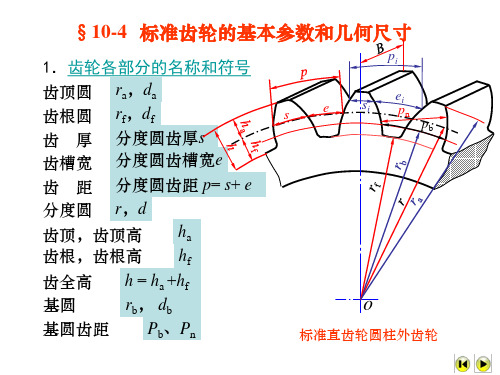
h 1 或 h 0.8 基准
ha c ha m c m 顶隙系数 c 0.25 或 c 0.3
h ha hf 6. 齿顶圆直径 d a d 2ha 7. 齿根圆直径 d f d 2hf
8. 齿距
p m m 9. 齿厚 s 2 m 10.齿槽宽 e 2
标准齿轮 m、、h*a、c* (15或20)为标准值 且 e = s 几何尺寸计算公式 (P307表10-2)
si ri [(s r ) 2(invi inv )]
齿轮与齿条比较
4.标准齿条和内齿轮的尺寸 1、渐开线齿条的几何特点 (1)同侧齿廓为互相平行的直线。
(2)齿条齿廓上各点的压力角均相等,且数值上等
1渐开线齿条的几何特点分度线齿根线一渐开线齿轮的啮合过程理论啮合线段n齿廓工作段二正确啮合的条件保证前后两对轮齿有可能同时在啮合线上相切接触
§10-4 标准齿轮的基本参数和几何尺寸
1.齿轮各部分的名称和符号 齿顶圆 ra,da 齿根圆 rf,df 分度圆齿厚s 齿 厚 任意圆齿厚 si 分度圆齿槽宽e ei 齿槽宽 任意圆齿槽宽 分度圆齿距 p pi= s+ ei 齿 距 任意圆齿距 i+e 分度圆 r,d ha 齿顶,齿顶高 hf 齿根,齿根高
o1
' r1
c
用C 表示。
上述参数即为渐开线齿轮的五个基本参数。
r2' o2
'
* ) 3.渐开线齿轮各部分几何尺寸 (基本参数为 m、Z、 和 h * 、 c a
1.分度圆直径 d mz 2.基圆直径 d b d cos 3.齿顶高 ha ha m 齿顶高系数
正常齿制 4.齿根高 hf 5.齿全高
渐开线齿轮几何参数学习总结

渐开线齿轮几何参数学习总结一.渐开线1.1 渐开线的形成一条动直线(发生线)沿着一个固定圆(基圆)作纯滚动时,和该动直线固连点的轨迹线称渐开线。
由图一可知,固连点在动直线上的位置可分为A ,B ,C 三种情况。
A 点的轨迹线称缩短渐开线;C 点的渐开线称延伸渐开线;若C 点与基圆圆心重合,则延伸渐开线演变成了阿基米德螺旋线;B 点的轨迹线称圆的渐开线,简称渐开线。
三种渐开线总称广义渐开线。
A BC发生线基圆图一 基圆的形成现在工业上常用的渐开线齿轮齿形是圆的渐开线。
如未特别说明,下面提到的渐开线均指此类渐开线。
1.2 与渐开线有关的各种名称(1) 基圆—直线在其上滚动的定圆称为渐开线的基圆。
基圆的半径与直径分别用b r ,b d 表示。
(2) 发生线—沿基圆作纯滚动的直线称为渐开线的发生线(3) 压力角—渐开线齿形上任意一点K 的受力方向线与速度方向线之间的夹角称为K 点的压力角(4) 渐开角—渐开线上任意一点K 的向量半径与渐开线的起点的向量半径之间的夹角1.3 渐开线的性质(1) 发生线沿基圆滚过的长度,等于基圆上被滚过的圆弧长度。
即:⌒AN KN(2) 渐开线上任一点的法线一定是基圆的切线。
(3) 同一基圆所生成的任意两条反向渐开线间的公法线处处相等。
(4) 发生线与基圆的切点N 是渐开线K 点曲率中心,而发生线NK 是渐开线上K 点的曲率半径。
渐开线离基圆越圆的部分,其曲率越小,即渐开线越平直,渐开线越靠近基圆,其曲率越大,即渐开线越弯曲,曲率半径越小。
(5) 渐开线的形状与基圆大小有关。
基圆半径相等则渐开线完全相同,基圆半径越小,则渐开线越弯曲,基圆半径越大,则渐开线越平直,基圆半径为无穷大时,则渐开线变为一条直线。
(6) 基圆内无渐开线。
A1A2B1B2N1N212图二 渐开线的公法线 1.4 渐开线的方程 (1) 渐开线的极坐标方程k k k inv k kb r kαααθα-===tan cos r(2)渐开线的直角坐标方程αθααθcos cos cos sin x b r kinv y b r ===图三1.5 基于MATLAB 的渐开线齿轮齿廓建模 (1)程序流程图:输入ra,m,z,x,alpha将每个齿形视为三部分求出每部分极角范围采用极坐标分别绘制每段齿形采用循环绘制Z个齿(2)源程序function y=getinvolute(ra,m,z,x,alpha)rb=m*z*cosd(alpha)/2;for theta=0:0.1:2*pipolar(theta,rb);endhold onalpha1=acos(rb/ra);theta1=tan(alpha1)-alpha1;for i=0:zfor alpha2=0:0.01:alpha1theta2=tan(alpha2)-alpha2;rx=rb/cos(alpha2);polar(theta2+2*i*pi/z,rx);endendhold onfaib=(pi+4*x*tand(alpha))/z+2*(tand(alpha)-alpha/180*pi); x1=ra*cos(theta1);y1=ra*sin(theta1);x2=ra*cos(faib-theta1);y2=ra*sin(faib-theta1);k=(y2-y1)/(x2-x1);b=y1-k*x1;for i=0:zfor theta3=theta1:0.001:(faib-theta1)rzx=b/(sin(theta3)-k*cos(theta3));polar(theta3+2*i*pi/z,rzx);hold onendendfor i=0:zfor alpha4=0:0.01:alpha1theta4=faib-(tan(alpha4)-alpha4);rx2=rb/cos(alpha4);polar(theta4+2*i*pi/z,rx2);endendhold onaxis tightend(3)渐开线生成实例利用程序绘制的齿数为20,齿顶圆半径为22,模数为2,变位系数为0,20的齿轮齿廓曲线如下:压力角为二.渐开线标准直齿圆柱齿轮的基本参数及几何计算2.1 齿轮的基本参数h,径向间隙齿轮的基本参数为:齿数Z,模数m,压力角α,齿顶高系数*a系数*c,根据上述基本参数可推算出齿轮的几何尺寸。
机械基础——渐开线变位直齿圆柱齿轮与 齿轮结构及工作图(教学教案)
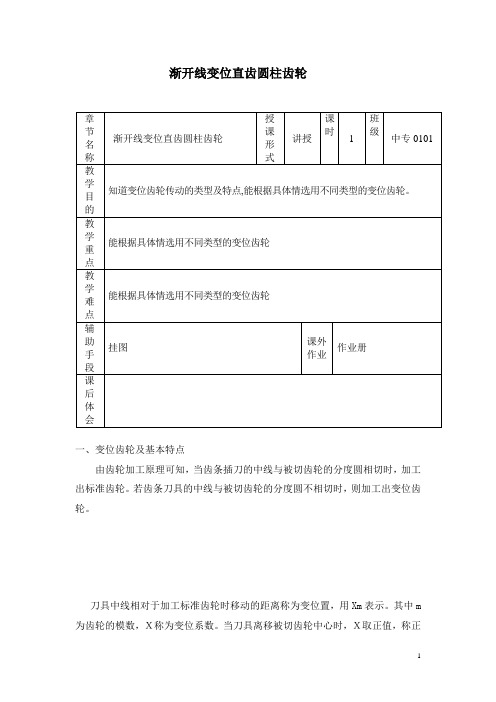
渐开线变位直齿圆柱齿轮一、变位齿轮及基本特点由齿轮加工原理可知,当齿条插刀的中线与被切齿轮的分度圆相切时,加工出标准齿轮。
若齿条刀具的中线与被切齿轮的分度圆不相切时,则加工出变位齿轮。
刀具中线相对于加工标准齿轮时移动的距离称为变位置,用Xm表示。
其中m 为齿轮的模数,X称为变位系数。
当刀具离移被切齿轮中心时,X取正值,称正图11变位,当刀具移近被切齿轮中心时,X为负值,称为负变位。
两个特点:1.不论是正变位还是负变位,刀具变位后的节线与齿轮的分度圆相切作纯滚动。
因为刀具上任一条节线的齿距P ,模数m 以及齿形角都相等,故被加工出的变位齿轮的齿距、模数、压力角并不改变,与标准直齿轮相同。
2.正变位齿轮的齿顶圆、齿根圆、齿顶高和齿根厚度均增大,而齿根高、齿顶厚度则减小,齿轮强度提高,还可以避免根切。
负变位齿轮的齿顶圆、齿根圆、齿顶高和齿根厚度均减小,而齿根高和齿顶厚度则增加,齿轮抗弯强度降低。
二、变位加工后应用在一对大小齿轮传动中,通常小齿轮采用正变位,齿顶高增大,齿根高减小,齿根变厚,强度和寿命提高,还可避免根切;大齿轮采用负变位,齿顶高减小,齿根高增大,齿根强度有所减弱。
由于大齿轮强度较高,选择适当的变位系数后,可以使一对大小齿轮的强度和使用寿命相近。
齿轮结构和工作图章节名齿轮结构和工作图授课形讲授课时1班级 中专0101一、齿轮结构根据强度条件和传动比要求可以确定齿轮的模数、齿数等基本参数,并计算出齿轮传动的主要尺寸。
在确定齿轮尺寸的基础上,考虑材料制造工艺等因素,确定齿轮的结构形状。
齿轮结构可分为齿轮轴、实心式、腹板式、轮辐式等。
1.齿轮轴直径较小的钢质齿轮,当齿根圆直径与轴径接近时,可将齿轮和轴做成整体的,称为齿轮轴。
齿轮轴刚度较好,但齿轴磨损后,轴也同时报废,对直径较大的齿轮应分开制造。
2.实心式齿轮齿顶圆直径da≤160mm时,可采用锻造毛坯的实心式结构,•当齿顶圆直径da<100mm时,单件或小批量生产的齿轮,•可直接用轧制圆钢作齿轮毛坯。
- 1、下载文档前请自行甄别文档内容的完整性,平台不提供额外的编辑、内容补充、找答案等附加服务。
- 2、"仅部分预览"的文档,不可在线预览部分如存在完整性等问题,可反馈申请退款(可完整预览的文档不适用该条件!)。
- 3、如文档侵犯您的权益,请联系客服反馈,我们会尽快为您处理(人工客服工作时间:9:00-18:30)。
1、结构无法更紧凑; ∵ 不能采用z< zmin的齿轮 2、不能凑中心距,即不适合用于a′≠a的场合; ∵ a′< a 时,无法安装(对外啮合齿轮传动而言); a′> a 时,虽可安装,但侧隙↑,εα↓,传动平稳性↓。 3、小齿轮容易坏。 ∵ 小齿轮的齿根薄,曲率半径小,即强度(弯曲、接触) 比大齿轮低,而磨损比大齿轮严重。 ∴ 为了改善和解决标准齿轮存在的上述缺点,就必须对 其进行必要的修正,以改善其传动性能。修正的办法可以 有多种,但目前工程中最常采用的是上述的变位修正法。
图10-25
∵ 变位前后基圆半径 rb不变 ∴ 变位齿轮与标准齿轮的齿 廓是由同一基圆所形成的 渐开线。但它们所不同的 是采用了渐开线上的不同 部位:(如图10-26)
图10-26
正变位:截取了离基圆较远的渐开线部位; 负变位:截取了离基圆较近的渐开线部位。 ∴ 正变位时,渐开线越平直,曲率半径↑,接触强度↑; 而且基圆的齿厚↑,弯曲强一对齿轮变位系数和x1+ x2的不同来分: 1)零传动:x1 + x2 = 0 ① x1 = x2 = 0——标准齿轮传动(零变位传动) 齿数条件:z 齿数条件 1≥zmin 、z2≥zmin; 啮合特点:a ′= a、α′=α、y = 0、△y = 0。 啮合特点
② x1 = -x2(x1>0、x2<0且x1 = |x2|) ——等变位传动(又称为高度变位齿轮传动) 齿数条件:z 齿数条件 1+ z2≥2zmin;(条件较宽,∵z2都比较大) 啮合特点:a ′= a(分度圆与节圆重合)、α′=α、 啮合特点 = 0、 △y = 0。 优点:结构紧凑(∵允许z1< zmin); 优点 两轮的抗弯能力接近,相对地提高了承载能力 (∵x1>0,sf1↑;x2<0,sf2↓); 可成对替换标准齿轮,可修复旧齿轮(∵a ′= a)。 缺点:互换性差;εα↓;sa1↓(齿顶易变尖,∵x1>0); 缺点 齿面接触强度没有提高。 y
2)中心距 ) 与标准齿轮传动一样,确定变位齿轮传动的中心距时, 也需满足两个条件: ①无侧隙(△=0);②两轮的顶隙c为标准值。 (1)无侧隙时的中心距a′ a ′ = a cosα/ cosα' 设a′- a = y m,y称为两轮的中心距变动系数 中心距变动系数。则 中心距变动系数 y = ( z1+ z2 )(cosα/ cosα′-1)/ 2 讨论:① 如α′=α → y = 0 → a ′ = a → 两分度圆相切; ② 如α′>α → y > 0 → a ′ > a → 两分度圆分离; ③ 如α′<α → y < 0 → a ′ < a → 两分度圆相交。 ∴ y的物理意义 表示两个分度圆的位置(相切、分离、相交)。 物理意义: 物理意义
2)正传动:x1 + x2>0(① x1>0,x2>0;② x1>0,x2=0; ③ x1>0,x2<0且x1>|x2|) 齿数条件:不受限制,允许可以采用z1 + z2< 2 zmin; 齿数条件 啮合特点:a ′ > a(分度圆小于节圆,两分度圆分离)、α′ 啮合特点 >α、y > 0、 △y >0。 优点: 结构紧凑(∵允许z1< zmin、 z2< zmin ); 优点 齿面接触强度↑(∵α′↑,综合曲率半径↑); 抗弯强度↑(∵x1>0,sf1↑); 缺点:ε 缺点 α↓(较多)。
3、变位齿轮传动的设计步骤 、 1)已知中心距的设计 已知中心距的设计:(已知z1、z2、m、 α、 a′) 已知中心距的设计 ①确定啮合角:cosα′= a cosα/ a′; ②确定变位系数和:x1+x2=(invα ′-invα)(z1+z2)/(2tanα); ③确定中心距变动系数:y = ( a ′- a ) / m; ④确定齿顶高变动系数:△y = ( x1+ x2 ) - y ; ⑤分配变位系数x1、x2,按表10-4计算齿轮的几何尺寸; ⑥检验重合度εα≥[εα],及正变位齿轮的齿顶圆齿厚 sa≥[sa]=(0.25~0.4)m。
二、变位原理 径向变位法,即改变刀具与 采用径向变位法 径向变位法 被加工齿轮的相对位置,使刀具的加 工节线与齿轮的分度圆相切。则这样 加工出来的齿轮便是变位齿轮 变位齿轮。 变位齿轮 变位量 x m——齿条刀具分度线与齿 轮分度圆之间的距离, 其中m为模数 模数。即刀具 模数 从切制标准齿轮的位置 沿径向移动的距离。 x ——径向变位系数 径向变位系数(简称变位系数 变位系数)。 径向变位系数 变位系数
(2)标准顶隙时的中心距a″ a″= ra1 + c + rf2 = m ( z1+z2 ) / 2 + ( x1+ x2 ) m 一般情况下,a″≠a′,并且可以证明a″> a′。 ∴ 对变位齿轮传动,无法同时满足无侧隙和标准顶隙。 实际设计时解决的办法是: 两轮按中心距a ′安装,并将两轮的齿顶削短一些,来保 证标准顶隙。 设齿顶的削短量为△y m, △y称为齿顶高变动系数 齿顶高变动系数。 齿顶高变动系数 △y m = ( x1 + x2 ) m – y m ∴ △y = ( x1 + x2 ) – y > 0 这时齿顶高 ha = ( ha*+ x - △y ) m ,齿全高h减少了△y m。
x=0 ——零变位 零变位,切制标准齿轮 零变位 (必要条件); x>0 ——正变位 正变位,切制正变位齿轮, 正变位 刀具远离齿轮中心;(z< zmin时必须采用) x<0 ——负变位 负变位,切制负变位齿轮, 负变位 刀具靠近齿轮中心。 三、(被切齿轮刚好无根切时刀具的)最小变位系数 、(被切齿轮刚好无根切时刀具的) 被切齿轮刚好无根切时刀具的 xmin= ha*( zmin- z ) / zmin=(17- z)/ 17 ∴ 对齿轮进行变位时,必须保证: x≥xmin 。
2、变位齿轮的尺寸计算 、 正变位: s =πm / 2 +2 x m tanα e =πm / 2 –2 x m tanα ra = r + ha*m + x m rf = r -(ha* +c*)m + x m ha= ha*m + x m hf =(ha*+ c*)m – x m 负变位:同正变位,但公式中的x为负值。
3)负传动:x1+ x2<0(①x1>0,x2<0且x1<|x2|; ②x1<0,x2<0;③x1=0,x2<0) 齿数条件:z 齿数条件 1 + z2 ≥2 zmin; 啮合特点:a ′< a(分度圆大于节圆,两分度圆相交)、 啮合特点 α′<α、y < 0、 △y > 0。 优点:允许a ′< a ; εα↑。 优点 缺点:与正传动的优点相反。 缺点
四、变位齿轮的几何尺寸 1、几何尺寸的变化情况(图10-25) 、几何尺寸的变化情况 变位齿轮与标准齿轮相比: 1)不变的参数及尺寸有: m、 z 、α、ha*、c*、p、r、 rb、h; 2)正变位时尺寸变化情况: s↑、e↓、ra↑、rf↑ 、ha↑、 hf↓,齿轮的强度↑ 3)负变位时尺寸变化情况: 与正变位时相反。
2)已知变位系数的设计 已知变位系数的设计(已知z1、z2、m、 α、 x1、x2) 已知变位系数的设计 ①确定啮合角:invα′=2 tanα( x1+ x2 ) / (z1+ z2) + invα; ②确定中心距:a′= a cosα/ cosα′; ③确定中心距变动系数:y = ( a ′- a ) / m; ④确定齿顶高变动系数:△y = ( x1 + x2 ) - y ; ⑤按表10-4 计算齿轮的几何尺寸。
∴ 正传动优点较多,传动质量较高,而负传动缺点较多。 所以在一般情况下,应多采用正传动,负传动除了凑中 心距之外一般不采用。在中心距等于标准中心距时,为 了提高传动质量,可采用等变位传动来代替标准齿轮传 动。 ▲ 传动类型选择的大原则: 传动类型选择的大原则: ① 要求互换性较高(即易坏、易磨损),同时z >17,采 用标准齿轮传动。 ② a ′= a 时,采用标准齿轮传动、等变位传动; a ′> a 时,必须采用正传动; a ′< a 时,必须采用负传动。
五、变位齿轮传动简介 1、变位齿轮的啮合传动 、 变位齿轮传动的正确啮合条件及连续传动条件——与 标准齿轮传动相同。 1 )无侧隙啮合方程 一对齿轮为了实现无侧隙啮合,必须满足下列条件: e2 ′ = s1 ′及e1 ′ = s2 ′ 根据上式,再结合其它公式可推导出无侧隙啮合方程式 无侧隙啮合方程式: 无侧隙啮合方程式 invα′=2 tanα( x1 + x2 ) / ( z1+ z2 ) + invα 上式和a ′cosα ′= a cosα—变位齿轮传动设计的基本关系式。 上式表明:x1+ x2≠0时,则α′≠α,a′≠a , 两轮 的节圆与分度圆不重合(要么分离要么相交)。