贵冶硫酸尾气有机胺法脱硫工艺的试验与应用
氨法脱硫技术装备在硫酸厂尾气处理中的应用分析

氨法脱硫技术装备在硫酸厂尾气处理中的应用分析尾气处理是硫酸厂关注的重要环节。
随着环境保护要求的不断提高和硫酸厂规模的扩大,传统的催化剂脱硫技术已经不能满足尾气处理的需求。
因此,氨法脱硫技术装备作为一种新型的尾气处理技术,被越来越多的硫酸厂应用。
本文将对氨法脱硫技术装备在硫酸厂尾气处理中的应用进行详细的分析。
一、氨法脱硫技术基本原理氨法脱硫技术是利用氨水作为脱硫剂,与硫酸厂尾气中的SO2反应生成硫酸铵,进而实现脱硫的技术。
该技术的基本原理是先将尾气中的SO2通过吸收剂与氨水反应生成硫酸铵,然后通过脱水、浓缩、结晶等工艺步骤来提取和回收硫酸铵,最终得到高纯度的硫酸产品。
二、氨法脱硫技术装备的优势1. 高效性能:氨法脱硫技术装备能够高效地去除尾气中的SO2,并且具有较高的脱硫效率和脱硫率。
经过该装备处理后的尾气达到环保标准,大大减少了对环境的污染。
2. 节能环保:相比传统的催化剂脱硫技术,氨法脱硫技术装备具有较低的能耗,并且无需使用酸性催化剂,从而减少了对环境的二次污染。
3. 硫酸产品回收:氨法脱硫技术装备能够将脱硫过程中生成的硫酸铵进行回收,再利用于硫酸生产过程中。
这既减少了硫酸厂的原材料消耗,也提升了硫酸产品的质量和经济效益。
4. 操作简单:氨法脱硫技术装备的操作相对简单,不需要复杂的设备和大量的人力投入。
硫酸厂可以通过简化工艺流程,节省人力成本,提高生产效率。
5. 适应性强:氨法脱硫技术装备适用于各种硫酸厂的尾气处理,无论是新建厂还是既有厂,都可以进行改造和更新,减少硫酸厂改造的成本和工期。
三、氨法脱硫技术装备在硫酸厂尾气处理中的应用案例1. 某硫酸厂采用氨法脱硫技术装备进行尾气处理。
经过一段时间的运行,该装备的脱硫效率达到了90%以上,远高于环保要求。
硫酸厂不仅获得了环保部门的认可,还提升了企业形象和产品竞争力。
2. 另一家硫酸厂利用氨法脱硫技术装备成功回收了大量的硫酸铵,再利用于硫酸制造过程中。
浅议制酸尾气脱硫工艺建设及实践应用

1 制酸 尾 气 脱 硫 建 设
某公司于 1 9 9 5年 建 设 投 产 运 行 , 当 时 生 产 规 模 为 粗铜 1 0 k t / a ,硫 酸 2 8 k t / a ,硫 酸 采 用 净 化 稀 酸
洗 涤 ,一转 一 吸 的制 酸工 艺 。经过 几 次 改 造及 环
3 双 氧 水 脱 硫 的 基 本 原 理
2 01 7年 5 月
云 南 化 工
Yun n an Ch e mi c a l Te c h no l o g y
Ma v . 2 01 7 V0 1 . 4 4. No. 5
第4 4卷 第 5期
d o i : 1 0 . 3 9 6 9 / j . i s s n . 1 0 0 4 - 2 7 5 X. 2 0 1 7 . 0 5 . 0 3 1
表 1 几 种脱 硫 工 艺 的 比较
收 稿 日期 :2 0 1 7 — 0 4 — 21
作 者 简 介 :戚永 辉 ,云 南 易 门铜 业 有 限 公 司 。
2 0 1 7年 第 5期
戚永辉等 : 浅议 制 酸尾 气 脱硫 工 艺建 设 及 实践 应 用
・ 1 1 3・
二 氧 化 硫 质 量 分 数 从 几 千 到 上 万 mg / m。 ,都 能 实 现 处 理后 气 体 中二氧 化 硫 本 质达 标 排 放 ,吸收 率 在 9 8 % 以上 ,具 有 生 产 弹 性 大 ,调 整 及 时 有 效
高 ,生 产 控 制稀 酸 浓 度 低 ,产 生 的 稀 酸量 大 ; 反
之 亦 然 。公 司 底 吹 炉 冶 炼 工 艺 脱 硫 率 达 7 4 % 左 右 ,产 生 烟 气 中 二 氧 化 硫 浓 度 高 , 通 过 配 气 、 混 烟进 入 制 酸 系 统 烟 气 中二 氧 化硫 浓 度 可 达 8 % 以
氨法脱硫工艺流程
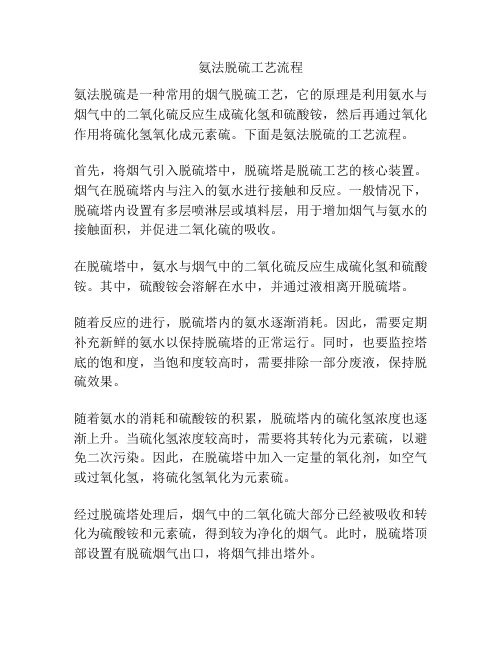
氨法脱硫工艺流程
氨法脱硫是一种常用的烟气脱硫工艺,它的原理是利用氨水与烟气中的二氧化硫反应生成硫化氢和硫酸铵,然后再通过氧化作用将硫化氢氧化成元素硫。
下面是氨法脱硫的工艺流程。
首先,将烟气引入脱硫塔中,脱硫塔是脱硫工艺的核心装置。
烟气在脱硫塔内与注入的氨水进行接触和反应。
一般情况下,脱硫塔内设置有多层喷淋层或填料层,用于增加烟气与氨水的接触面积,并促进二氧化硫的吸收。
在脱硫塔中,氨水与烟气中的二氧化硫反应生成硫化氢和硫酸铵。
其中,硫酸铵会溶解在水中,并通过液相离开脱硫塔。
随着反应的进行,脱硫塔内的氨水逐渐消耗。
因此,需要定期补充新鲜的氨水以保持脱硫塔的正常运行。
同时,也要监控塔底的饱和度,当饱和度较高时,需要排除一部分废液,保持脱硫效果。
随着氨水的消耗和硫酸铵的积累,脱硫塔内的硫化氢浓度也逐渐上升。
当硫化氢浓度较高时,需要将其转化为元素硫,以避免二次污染。
因此,在脱硫塔中加入一定量的氧化剂,如空气或过氧化氢,将硫化氢氧化为元素硫。
经过脱硫塔处理后,烟气中的二氧化硫大部分已经被吸收和转化为硫酸铵和元素硫,得到较为净化的烟气。
此时,脱硫塔顶部设置有脱硫烟气出口,将烟气排出塔外。
最后,脱硫塔底部的废液经过处理后可回收利用。
一般来说,废液中含有一定的硫酸铵,在经过脱水处理后可以得到硫酸铵结晶,作为化肥的原料。
总之,氨法脱硫工艺是一种有效的烟气脱硫方法。
通过脱硫塔中的反应和氧化过程,能够将二氧化硫转化为硫酸铵和元素硫,达到环保净化烟气的目的。
与此同时,也能够回收和利用废液中的硫酸铵,实现资源的循环利用。
贵溪冶炼厂硫酸尾气脱硫实践

分活性焦含水量过大,在再生塔内产生绝热蒸发,再 生塔中部热量转变为水蒸气潜热,因此再生塔中部 温度出现下降,由于再生气管道内水蒸气处于饱和 状态,再生气出口温度无法提高,再生塔底部为排料 段,温度较低,水蒸气从 300℃ 下降到 130℃ 时,出现 过饱和,部分蒸汽形成了液态水。对尾气增湿工艺 进行调整后,各个温度点均达到设计值,再生塔下料 段未出现滴水现象,再生塔底部未出现结垢,再生气 出口管道腐蚀问题得到了解决。工艺调整后再生塔
Total 110 No. 4 2011
铜业工程 COPPER ENGINEERING
总第 110 期 2011 年第 4 期
贵溪冶炼厂硫酸尾气脱硫实践
胡滔
( 江西铜业集团公司贵溪冶炼厂,江西 贵溪 335424)
摘 要:根据国家节能减排的规划要求,贵溪冶炼厂硫酸车间采用活性焦干法烟气脱硫装置对尾气进行处理, 产生的副产品能有效利用和完全处置。本文主要介绍活性焦干法脱硫工艺特点,装置运行中存在的主要问题及改 进措施。
( 5) 再生塔下部活性焦循环量小,部分活性焦 在卸料器间循环,造成卸料器故障不动作。
5 原因分析及改进措施
( 1) 装置活性焦添加正值雨季,部分活性焦含 水量大,在物料循环过程中,产生的粉尘粘结在下料 处。硫酸尾气含水量少,尾气内水含量处于不饱和 状态,具有吸水性能。新添加的活性焦用尾气干燥 后,再进行循环,保证了物料循环系统的正常运行。
2 活性焦脱硫原理
活性焦烟气脱硫是利用具有比表面积大的微孔 活性焦对烟气中的 SO2 进行选择性吸附,吸附态的 SO2 在烟气和水蒸气存在的条件下被氧化为 H2 SO4 并被存储在活性焦微孔内。吸附 SO2 后的活性焦被
带入再 生 系 统,在 高 温 加 热 下,活 性 焦 中 吸 附 的 H2 SO4 与活性焦发生反应,还原为 SO2 气体,活性焦 微孔表面恢复吸附性能,循环使用。活性焦的加热 再生反应相当于对活性焦进行再次活化。随着活性 焦与 H2 SO4 的化学反应,比表面积得到增加,活性 焦的脱硫效果会有进一步提高[1]。
氨法脱硫技术装备在废气资源化利用过程中的应用案例分析

氨法脱硫技术装备在废气资源化利用过程中的应用案例分析引言:随着工业化的进展,大量的废气排放给环境带来了严重的污染问题。
废气中的二氧化硫(SO2)是一种常见的污染物,对环境和人类健康造成严重威胁。
为了降低废气中的SO2含量,氨法脱硫技术被广泛应用于工业生产中,并逐渐成为废气资源化利用的重要手段。
氨法脱硫技术概述:氨法脱硫技术是一种利用氨水与废气中的SO2反应生成硫酸盐的方法。
氨气与SO2在催化剂参与下反应生成氨硫酸氢铵,然后通过各种分离设备将生成的氨硫酸氢铵提取并加热脱水得到硫酸。
该技术具有高效、经济、环保等优点,被广泛应用于电力、钢铁、化工等工业领域。
应用案例分析:1. 电力行业氨法脱硫技术在电力行业中的应用是最为广泛的。
以某电力厂为例,该厂使用燃煤锅炉发电,废气中含有大量的SO2。
为了达到国家排放标准,该电力厂引进了氨法脱硫装备。
通过氨法脱硫技术,厂内的SO2排放浓度明显降低,达到了环保要求。
与传统的石膏湿法脱硫相比,氨法脱硫不仅具有更高的脱硫效率,还能实现废气中SO2的资源化利用,生产出高纯度的硫酸,为企业带来了经济效益。
2. 钢铁行业钢铁行业是一个大量排放废气的行业,其中SO2是主要的污染物之一。
某钢铁公司引进了氨法脱硫技术装备,用于减少废气中的SO2含量。
通过一系列的装置,废气中的SO2与氨水反应并生成氨硫酸氢铵。
该氨法脱硫系统具有多级SO2吸收、催化剂再生和氨水循环等功能,提高了脱硫效率和设备的稳定性。
同时,该装备还能够调节氨水的投加量,使得废气的排放达到国家规定的标准要求。
3. 化工行业化工行业中的一些生产过程也会产生大量的SO2废气。
以某化工企业为例,该企业使用氨法脱硫技术装备对废气中的SO2进行处理。
通过氨法脱硫技术,废气中的SO2与富氨水反应生成高浓度的氨硫酸氢铵溶液。
该溶液可以进一步提纯,得到高纯度的硫酸,并用于企业的生产过程。
这种废气资源化利用方法不仅降低了企业的环境污染,还提高了资源利用的效率。
贵冶硫酸两套尾气脱硫装置工艺及比较

斗 机 、 选设 备 等 活 性 焦 循 环 系统 后 ,活 性 焦 粉 末 筛 及 吸 附的灰 尘被 分 离 , 部 分 活 性 焦 则返 回脱 硫 塔 大
进行 循 环 。此 过 程 中损 失 的 活 性 焦 需 定 期 进 行 补
充 。再 生过 程所 产 生 的较 高浓 度 的 S O 气体 经 再生
Toa 0 t l1 4
铜
业
工
程
总 第 14期 0
ቤተ መጻሕፍቲ ባይዱ
No 2 2 0 . 01
C P 0P ER NGI ER NG E NE I
21 0 0年第 2期
责诲硫酸霹聋展 朦骧紫羲 工. 誊
乔 彦 强 ,江 红 卫
(. 1 中南大 学化 学化工学院 , 湖南 长沙 摘 4 0 8 ;. 10 3 2 江西铜业集 团公司贵溪冶炼厂 , 江西 贵溪
镶
3 52 ) 34 4
要: 介绍了江西铜业集 团公 司贵溪冶炼厂硫酸 车间两套 尾气脱硫装置 的概 况 、 艺流程 和技术控制 , 工 重点
阐述 两 套 装 置 工 艺 上 的异 同及 在 实 际 生 产 中 遇 到 的 一 些 问题 及 处 理 措 施 。 关键词 : 酸 ; 气脱硫 ; 艺 ; 制 尾 工 问题 ; 施 措 中图 分 类 号 : 7 13 文 献 标 识 码 : 文 章 编 号 :0 9—34 ( 0 0 0 0 4 0 X 0 . B 10 8 2 2 1 ) 2— 07— 3
贵溪冶炼厂硫酸尾气脱硫实践

铜
业
工
程
总第 10期 1
21 0 1年第 4期
C P 0P ER ENG N RI I EE NG
贵 溪冶 厂 燎
( 江西铜业集 团公司贵溪冶炼厂 , 西 贵溪 江
摘
践
352) 344
要: 根据 国家节能减排 的规划要求 , 贵溪冶炼厂硫酸车间采用活性焦干 法烟气脱硫装 置对尾气 进行处理 ,
Ab t a t c o d n o t e r q i me t o ain l e e g e u t n p o r m ,s l rc a i l n f G iis l r u e ci e s r c :A c r i g t h e u r e n s fn to a n ry r d ci r g a o uf i c d p a to u x met s s a t u e v c k e u p u iain t r a e t i g s n h n t e b o e d s l h r t o te t h al a ,a d t e h y—p o u tc n b t ie f ciey a d t ae o ltl . T i at l z o t rd c a e ui z d e e t l n r td c mp eey l v e h s ri e c ma ny i t d c st ec aa trsiso ci ec k e up u i t n o i g s t e man p o lmse i e h p l ain a d t ei i l nr u e h r c e t f t o e d s l h rz i f al a , h i r be xs d i t e a p i t n m— o h i c a v ao t t n c o h
氨法脱硫工程技术方案

氨法脱硫工程技术方案1. 概述氨法脱硫是目前使用最为广泛的脱硫技术之一,它主要通过将烟气与一定浓度的氨气在催化剂的作用下反应,使二氧化硫被还原为硫化氢,再通过催化剂的吸附、氧化等作用,将硫化氢转化为硫酸铵,最终达到脱除烟气中二氧化硫的目的。
氨法脱硫技术具有具有脱硫效果好、适应范围广、可靠性高、后处理技术简单等特点,广泛应用于煤电、石化、钢铁、化工等行业的大型烟气脱硫工程中。
2. 工艺流程(1)烟气净化烟气经过除尘器和脱硝装置处理后进入氨法脱硫系统,保证烟气中杂质的净化和氨气的使用效率。
(2)预处理预处理包括水分加热、氧气除去、烟气温度控制和氧化铵的制备等环节,确保烟气的物理、化学参数在合适的范围内,为之后的催化反应和吸附提供良好的条件。
(3)催化反应催化反应是氨法脱硫的核心,其主要包括二氧化硫与氨气的催化还原、产生硫化氢和其他副产物等环节。
其中催化剂的种类、用量、活性等因素对催化反应的效果具有重要的影响。
(4)吸附换热在催化反应后,烟气中仍存在少量的硫化氢等有害物质,需要通过吸附换热的方式将其与烟气分离,同时回收热量提高系统能量效率。
(5)逆反应为了提高催化剂的长期使用效果,氨法脱硫系统中还需要进行逆反应环节,即用硫酸铵溶液对催化剂进行再生,去除其中硫化物沉积,保证催化剂的活性和可持续使用性。
3. 设备配置氨法脱硫系统的设备包括废气处理设备、预处理设备、催化反应器、吸附换热器、脉冲喷吹器、逆流吸附器、再生器等。
其中催化反应器和再生器是氨法脱硫的核心设备,其设计和运行对脱硫效果和系统稳定性具有重要影响。
4. 工程实例以某电厂2×300MW燃煤发电机组的氨法脱硫工程为例,其主要设备及参数如下表所示:设备名称数量容量/规格预处理系统 2 1200m3/h、800℃催化反应器 3 3200 m3/h吸附换热器 3 9600 m3/h逆流吸附器 1 800 m3/h再生器 1 1200 m3/h氨气供应系统 1 1500 m3/h该工程于2010年正式投运,经过多年的运行,脱硫效果稳定,系统稳定运行。
硫酸尾气处理工程上催化法脱硫技术的应用

硫酸尾气处理工程上催化法脱硫技术的应用本文介绍了一种用于硫酸尾气处理的新型催化脱硫技术,探讨了硫资源回收的工艺流程与基本原理,以工程实例加以论述。
标签:硫酸尾气;催化法;脱硫技术;应用硫酸作为工业化学品架构中的重要构成,在各个工业部门中广泛应用。
但硫酸行业乃属高污染行业,因制酸工艺的不同,在生产过程中均会产生程度差异性的重金属、酸雾、SO2等污染,其中最为常见且最严重的污染即为SO2,此乃大气中的主要有害成分。
在全国SO2排放量当中,尽管硫酸工业的排放量占据较小比例,但却严重影响着区域环境。
至此,本文特介绍了一种新型的催化法脱硫技术,此技术运用低温非钒系催化剂,具有良好的应用效能。
1 新型催化法脱硫技术1.1 新型催化法脱硫原理分析当前,国内在处理硫酸尾气的方法上,主要有活性焦法、氨-酸法、石灰石-石膏法、柠檬酸钠法及氨法等,其中最为常用的有活性焦法、石灰石-石膏法等,而本文则运用一种较新型的催化法。
此新型的催化法脫硫技术选用的是低温非钒系催化剂,烟气当中的O2、H2O、SO2以被吸附的方式固定在催化剂的孔隙中,基于活性组分所持有的催化作用下,能够转变为带有活性的分子,另外,经反应还能生成H2SO4,而经过催化反应而最终生成的硫酸,会在催化剂孔隙内大量富集,经一段时间的脱硫后,即硫酸饱和后,孔隙能再生,从而将催化剂的活性位释放出来,此时催化剂便能恢复其脱硫能力。
所生成的H2SO4,便会以各种浓度形式重返工艺系统,制得硫酸溶液,无有害物质排入环境。
其脱硫反应的原理为:SO2(g)→SO2*;O2(g)→O2*;H2O(g)→H2O*;SO2*+1/2 O2*→SO3*;SO3*+H2O*→H2SO4*(*表示吸附态)。
1.2 工艺流程新型催化法脱硫的主要工艺流程:控制硫酸尾气温度,使之适宜反应,且不可含尘,此外,控制二氧化硫濃度,使之维持在催化剂可处理的范围内,即体积分数<3%,因此,仅需对水分进行调节便可。
氨法脱硫系统工艺优化分析与应用

氨法脱硫系统工艺优化分析与应用
氨法脱硫是一种常用的烟气脱硫技术,其基本原理是利用溶液中的氨气与烟气中的二
氧化硫发生反应生成硫酸铵,进而达到脱除烟气中的二氧化硫的目的。
在实际的工业应用中,氨法脱硫系统存在一些问题和不足,需要进行优化分析和改进。
对氨法脱硫系统进行工艺优化分析是非常必要的。
优化分析可以从多个方面对系统进
行改进,提高系统的脱硫效率和经济效益。
其中一个重要的方面是优化溶液配比,控制氨
气和二氧化硫的摩尔比,以达到最佳的反应条件。
还可以考虑对脱硫剂的质量要求和进料
温度等参数进行控制,以提高系统的稳定性和可靠性。
对氨法脱硫系统进行工艺优化分析还可以从设备结构和操作条件等方面进行改进。
针
对系统中可能存在的溶液泵、喷雾器、反应器等设备的问题,可以进行合理的设计和选型,提高设备的工作效率和稳定性。
还可以通过调整反应温度、保持适宜的液气比和控制氨气
流量等操作条件,使系统在不同的工况下都能够保持较高的脱硫效率。
在氨法脱硫系统的优化分析中,还可以考虑与其他脱硫技术的结合应用。
可以将氨法
脱硫与湿法脱硫技术相结合,形成混合脱硫工艺,以提高系统的脱硫效率和适应性。
还可
以考虑将氨法脱硫与其他污染物处理技术结合应用,实现废气污染物的综合治理和资源化
利用。
氨法脱硫系统的工艺优化分析是提高系统性能和效益的重要手段。
通过优化分析和应
用改进,可以提高系统的脱硫效率和稳定性,减少能耗和化学品的使用量,并与其他脱硫
技术相结合,实现更好的污染物治理效果。
有机胺法脱硫工艺在石化行业的应用
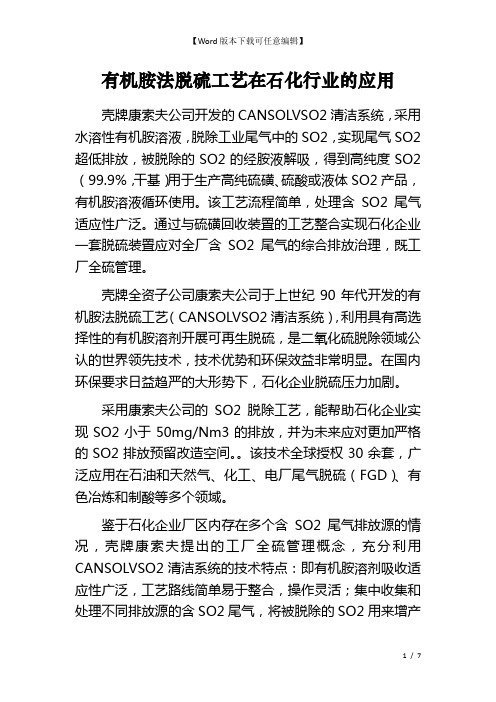
有机胺法脱硫工艺在石化行业的应用壳牌康索夫公司开发的CANSOLVSO2清洁系统,采用水溶性有机胺溶液,脱除工业尾气中的SO2,实现尾气SO2超低排放,被脱除的SO2的经胺液解吸,得到高纯度SO2(99.9%,干基)用于生产高纯硫磺、硫酸或液体SO2产品,有机胺溶液循环使用。
该工艺流程简单,处理含SO2尾气适应性广泛。
通过与硫磺回收装置的工艺整合实现石化企业一套脱硫装置应对全厂含SO2尾气的综合排放治理,既工厂全硫管理。
壳牌全资子公司康索夫公司于上世纪90年代开发的有机胺法脱硫工艺(CANSOLVSO2清洁系统),利用具有高选择性的有机胺溶剂开展可再生脱硫,是二氧化硫脱除领域公认的世界领先技术,技术优势和环保效益非常明显。
在国内环保要求日益趋严的大形势下,石化企业脱硫压力加剧。
采用康索夫公司的SO2脱除工艺,能帮助石化企业实现SO2小于50mg/Nm3的排放,并为未来应对更加严格的SO2排放预留改造空间。
该技术全球授权30余套,广泛应用在石油和天然气、化工、电厂尾气脱硫(FGD)、有色冶炼和制酸等多个领域。
鉴于石化企业厂区内存在多个含SO2尾气排放源的情况,壳牌康索夫提出的工厂全硫管理概念,充分利用CANSOLVSO2清洁系统的技术特点:即有机胺溶剂吸收适应性广泛,工艺路线简单易于整合,操作灵活;集中收集和处理不同排放源的含SO2尾气,将被脱除的SO2用来增产硫磺、生产硫酸或制备液态SO2等高附加值产品,变废为宝。
帮助石化企业在尾气排放环保达标的同时,实现循环经济。
1、CANSOLVSO2清洁系统壳牌康索夫开发的有机胺对于SO2具有极高的选择性,在脱硫过程中起到弱碱性基团的功能,并有效平衡吸收和解吸过程,最大限度降低能耗。
在与尾气接触时起到弱碱性基团的功能,与尾气中的SO2发生如下反应:该反应为放热反应,尾气进气温度低,有利于吸收反应的开展。
对SO2的高选择性决定了CANSOLVSO2清洁系统的胺液循环量低,这降低了原胺液填充量和系统运行能耗。
氨法脱硫技术装备在石化行业乙脱硫过程中的应用优化

氨法脱硫技术装备在石化行业乙脱硫过程中的应用优化近年来,随着环境保护政策的加强和对大气污染物排放的限制,石化行业面临着更严格的气体脱硫要求。
氨法脱硫技术作为一种常用的脱硫方法,在石化行业中得到了广泛应用。
本文将探讨氨法脱硫技术装备在石化行业乙脱硫过程中的应用优化策略,并分析其在环境保护和经济效益方面的优势。
首先,氨法脱硫技术是一种基于氨与二氧化硫气体反应生成硫酸盐的方法。
在石化行业的乙脱硫过程中,氨法脱硫技术被广泛应用于高硫含量燃料气体的脱硫处理。
其主要装备包括氨喷射器、吸收塔、反应塔和尾气处理系统等。
这些装备的优化设计可以进一步提高脱硫效率,降低运营成本。
在氨法脱硫过程中,氨喷射器是关键设备之一。
合理设计和布置氨喷射器,能够实现均匀的氨的喷射,提高氨与二氧化硫的反应效率。
通过调整喷射器的角度、喷孔的大小和布置,可以确保氨气均匀分布于吸收塔中,从而提高脱硫效率。
吸收塔是氨法脱硫技术中另一个重要的装备。
其功能是将待处理的燃料气体与喷入的氨气充分接触,使二氧化硫在溶液中溶解并与氨反应生成硫酸盐。
在吸收塔的设计中,需要考虑溶液流动性、气液接触效果和负荷均衡等因素。
通过增加塔板数量、合理设置塔板间隔和优化溶液循环,可以提高吸收塔的脱硫效率。
在反应塔中,英超开场时间固液分离是一个重要的步骤。
在脱硫过程中,氨和硫酸盐溶液会与产生的固体颗粒一起沉积在反应塔底部。
合理设计反应塔的结构,提高固液分离效果,可以有效减少氨的损失和废水的排放,以及提高硫酸盐的回收率。
尾气处理系统是氨法脱硫技术中必不可少的一部分。
其主要功能是对处理后的尾气进行处理和排放。
在尾气处理系统中,可采用一系列装置如洗涤塔、吸附器和除霜装置来去除残余的氨气和其他污染物。
这些装置的优化设计将有助于减少二次污染和废气排放,提高环境保护效果。
氨法脱硫技术装备在石化行业乙脱硫过程中的应用优化不仅能够提高脱硫效率,还可以降低运营成本和对环境的负面影响。
采用先进的氨喷射器设计和布局,合理设计吸收塔和反应塔的结构,优化尾气处理系统等措施,能够最大程度地提高硫酸盐的回收率,减少废水排放和氨的损失。
贵冶30万吨熔炼脱硫系统节能减排实践
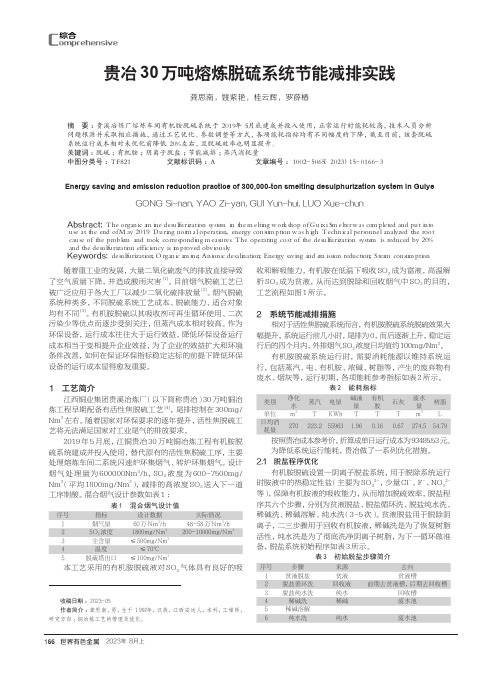
166贵冶30万吨熔炼脱硫系统节能减排实践龚思南,姚紫艳,桂云辉,罗薛椿(江西铜业集团贵溪冶炼厂,江西 贵溪 335400)摘 要:贵溪冶炼厂熔炼车间有机胺脱硫系统于2019年5月底建成并投入使用,正常运行时能耗较高,技术人员分析问题根源并采取相应措施,通过工艺优化、参数调整等方式,各项能耗指标均有不同幅度的下降,截至目前,该套脱硫系统运行成本相对未优化前降低20%左右,且脱硫效率也明显提升。
关键词:脱硫;有机胺;阴离子脱盐;节能减排;蒸汽消耗量中图分类号:TF821 文献标识码:A 文章编号:1002-5065(2023)15-0166-3Energy saving and emission reduction practice of 300,000-ton smelting desulphurization system in GuiyeGONG Si-nan, YAO Zi-yan, GUI Yun-hui, LUO Xue-chun(Guixi Smelter,Jiangxi Copper Group,Guixi 335400,China)Abstract: The organic amine desulfurization system in the melting workshop of Guixi Smelter was completed and put into use at the end of May 2019. During normal operation, energy consumption was high. Technical personnel analyzed the root cause of the problem and took corresponding measures. The operating cost of the desulfurization system is reduced by 20% and the desulfurization efficiency is improved obviously.Keywords: desulfurization; Organic amine; Anionic desalination; Energy saving and emission reduction; Steam consumption收稿日期:2023-05作者简介:龚思南,男,生于1992年,汉族,江西安远人,本科,工程师,研究方向:铜冶炼工艺的管理及优化。
冶金尾气氨法脱硫工艺的应用
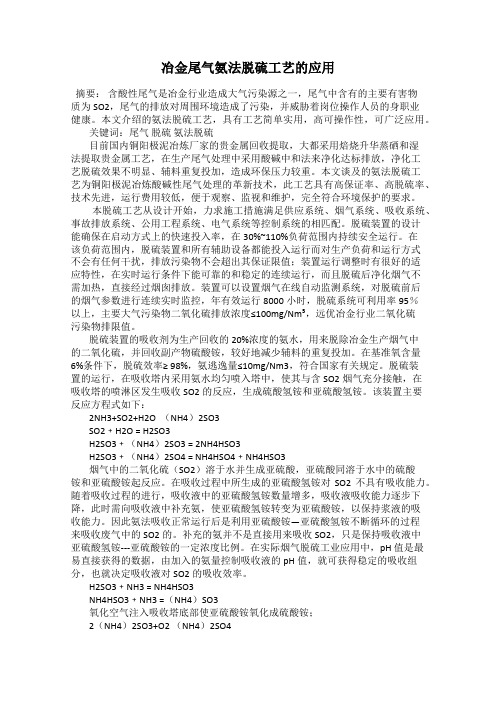
冶金尾气氨法脱硫工艺的应用摘要:含酸性尾气是冶金行业造成大气污染源之一,尾气中含有的主要有害物质为SO2,尾气的排放对周围环境造成了污染,并威胁着岗位操作人员的身职业健康。
本文介绍的氨法脱硫工艺,具有工艺简单实用,高可操作性,可广泛应用。
关键词:尾气脱硫氨法脱硫目前国内铜阳极泥冶炼厂家的贵金属回收提取,大都采用焙烧升华蒸硒和湿法提取贵金属工艺,在生产尾气处理中采用酸碱中和法来净化达标排放,净化工艺脱硫效果不明显、辅料重复投加,造成环保压力较重。
本文谈及的氨法脱硫工艺为铜阳极泥冶炼酸碱性尾气处理的革新技术,此工艺具有高保证率、高脱硫率、技术先进,运行费用较低,便于观察、监视和维护,完全符合环境保护的要求。
本脱硫工艺从设计开始,力求施工措施满足供应系统、烟气系统、吸收系统、事故排放系统、公用工程系统、电气系统等控制系统的相匹配。
脱硫装置的设计能确保在启动方式上的快速投入率,在30%~110%负荷范围内持续安全运行。
在该负荷范围内,脱硫装置和所有辅助设备都能投入运行而对生产负荷和运行方式不会有任何干扰,排放污染物不会超出其保证限值;装置运行调整时有很好的适应特性,在实时运行条件下能可靠的和稳定的连续运行,而且脱硫后净化烟气不需加热,直接经过烟囱排放。
装置可以设置烟气在线自动监测系统,对脱硫前后的烟气参数进行连续实时监控,年有效运行8000小时,脱硫系统可利用率95%以上,主要大气污染物二氧化硫排放浓度≤100mg/Nm³,远优冶金行业二氧化硫污染物排限值。
脱硫装置的吸收剂为生产回收的20%浓度的氨水,用来脱除冶金生产烟气中的二氧化硫,并回收副产物硫酸铵,较好地减少辅料的重复投加。
在基准氧含量6%条件下,脱硫效率≥ 98%,氨逃逸量≤10mg/Nm3,符合国家有关规定。
脱硫装置的运行,在吸收塔内采用氨水均匀喷入塔中,使其与含SO2烟气充分接触,在吸收塔的喷淋区发生吸收SO2的反应,生成硫酸氢铵和亚硫酸氢铵。
氨法脱硫在硫磺制酸装置尾气处理中的应用

前较成熟的并已实现工业化的氨法脱硫工艺, 该工 艺既脱硫又脱氮。其工艺过程一般分成脱硫吸收、 [ 1] 中间产品处理、 副产品制造三大步骤 。根据过程 和副产品的不同, 湿式氨法又可分为氨 - 酸法、 氨硫铵肥法、 氨 - 磷铵肥法、 氨 - 亚硫酸铵法等 , 其吸 收的原理和过程是相同的, 不同之处仅在于对吸收液 处理的方法和工艺技术路线及副产品制造的区别。
目前我国超微粉碎设备行业尚无统一的行业标准和国家标准生产企业依据各自的企业标准组织生产为改变这一状况提升行业竞争力和方便用户进行设备选型浙江丰利粉碎设备有限公司向国家标准化管理委员会报批成立了超微粉碎设备工作组该工作组由来自高等院校科研单位生产企业标准管理等机构的10多名行业专家企业家组本次活动期间到会的超微粉碎设备工作组的专家们分析了目前现状提出了解决急需逐步推进的工作策略首先将拟订目前行业急需的一批标准并落实了第一牵头起草单他们是
nes ite for w et desu lfu rization of flue gases [ J ] . I b id, 1988 , ( 362) : 113 ~ 136 . [ 30] S Satoh , M N akam ura , Y O h ira , et a.l Ch aracteristics of desu lfu rizat ion by m agn es ite [ J] . K ogaku K ogaku R onbun shu , 2004 , 30 ( 5 ) : 661~ 667. [ 31] Tong Shanghu,i H e Jiafu , L iu Jingm ing , et a. l In tegrated apparatus and m ethod for treat ing flue gas by recovering heat , dedust ing , and magnes ia desu lfurizing [ P]. CN: 101073744 , 2007- 11- 21. [ 32] Z T aborsky, F M arka lou r , J Beranek, et a.l M agnesium su lfate from m agnesiu m m inerals and su lfu r d ioxide contained in flu e ga ses [ P] . CZ: 159575, 1975- 08 - 15 . [ 33] [ 34] 金 明焕 . 利用 水镁 石浆 液脱 硫方 法 [ P] . CN: 101058053 , 2007 - 10- 24 . 张 强 , 许世森 , 郭振锁 , 等 . 湿 法氧化 镁烟气 脱硫技 术在我 国的发展前景 [ J] . 热力发电 , 2005( 8) :Байду номын сангаас9~ 11 . [ 35] [ 36] 张大全 , 刘丽佳 , 辛志玲 , 等 . 氧 化镁湿 法烟气 脱硫结 垢性能 的研究 [ J] . 电力环境保护 , 2007 , 23( 6 ): 20~ 22 . 姚洪猛 , 崔爱臻 . 镁法烟气脱硫技术的应 用 [ J] . 山 东电力技 术 , 2007( 2) : 57 ~ 59 .
氨法脱硫在硫酸尾气中的成功应用及母液的氧化回收
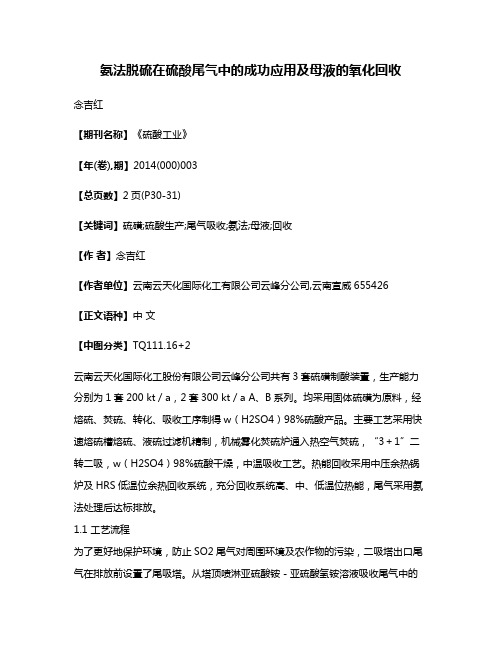
氨法脱硫在硫酸尾气中的成功应用及母液的氧化回收念吉红【期刊名称】《硫酸工业》【年(卷),期】2014(000)003【总页数】2页(P30-31)【关键词】硫磺;硫酸生产;尾气吸收;氨法;母液;回收【作者】念吉红【作者单位】云南云天化国际化工有限公司云峰分公司,云南宣威655426【正文语种】中文【中图分类】TQ111.16+2云南云天化国际化工股份有限公司云峰分公司共有3套硫磺制酸装置,生产能力分别为1套200 kt/a,2套300 kt/a A、B系列。
均采用固体硫磺为原料,经熔硫、焚硫、转化、吸收工序制得w(H2SO4)98%硫酸产品。
主要工艺采用快速熔硫槽熔硫、液硫过滤机精制,机械雾化焚硫炉通入热空气焚硫,“3+1”二转二吸,w(H2SO4)98%硫酸干燥,中温吸收工艺。
热能回收采用中压余热锅炉及HRS低温位余热回收系统,充分回收系统高、中、低温位热能,尾气采用氨法处理后达标排放。
1.1 工艺流程为了更好地保护环境,防止SO2尾气对周围环境及农作物的污染,二吸塔出口尾气在排放前设置了尾吸塔。
从塔顶喷淋亚硫酸铵-亚硫酸氢铵溶液吸收尾气中的SO2和SO3,使尾气达到国家排放标准后,再经高80 m烟囱排入大气。
吸收母液自塔底进入母液循环槽,通过加入w(NH4OH)为12%稀氨水使吸收液中(NH4)2SO3与NH4HSO3质量比保持恒定。
吸收反应方程式为:氨法尾气吸收工艺流程如图1,图中虚线为改造后增加的部分。
1.2 过程控制尾气回收塔系泡沫塔,共有3层塔板。
塔内喷淋的亚硫酸铵与SO2反应后生成亚硫酸氢铵,自塔底流到尾吸循环槽,加氨后再生为能与SO2反应的亚硫酸铵溶液,再由尾吸循环泵送至尾吸塔循环使用。
吸收液循环使用一定时间后,密度会升高,为维持密度稳定,循环液要定期加水维持。
用加稀氨水和加水来调节母液的碱度和密度。
多余母液送至母液氧化槽氧化,以控制尾吸循环槽液位。
亚硫酸铵对SO2有很好的吸收能力,是主要吸收剂。
- 1、下载文档前请自行甄别文档内容的完整性,平台不提供额外的编辑、内容补充、找答案等附加服务。
- 2、"仅部分预览"的文档,不可在线预览部分如存在完整性等问题,可反馈申请退款(可完整预览的文档不适用该条件!)。
- 3、如文档侵犯您的权益,请联系客服反馈,我们会尽快为您处理(人工客服工作时间:9:00-18:30)。
贵冶硫酸尾气有机胺法脱硫工艺的试验与应用
江铜集团贵溪冶炼厂硫酸车间江红卫
摘要:本文介绍了江铜集团贵溪冶炼厂硫酸车间硫酸尾气有机胺法脱硫试验装置的概况、工艺流程、工艺特点、设备规格和生产控制,同时介绍了在实际生产应用中遇到的一些问题及处理措施。
关键词:硫酸尾气有机胺脱硫工艺设备运行问题措施
1 前言
贵溪冶炼厂是全国环保先进企业,各种污染排放达到国家环保要求,2007年,贵冶新30万吨冶炼工程投产,分别建于熔炼环集烟气和硫酸尾气的活性焦脱硫系统同时投入使用。
2010年,一系统环集和硫酸一系列尾气活性焦脱硫系统建成并投入使用。
2012年,新的《铜、镍、钴工业污染物排放标准》开始执行,污染物排放要求越来越高,废气排放的二氧化硫浓度必须达到400mg/Nm3以下。
2015年,新环保法的实施,对SO2排放提出更高要求,贵冶硫酸车间不断摸索硫酸尾气脱硫新工艺,对有机胺法脱硫进行试验。
本次试验装置选择建在硫酸四系列,将其一半负荷(烟气量为35000Nm3/h)作为有机胺法脱硫试验,一方面可适当降低硫酸二系统尾气总排放SO2浓度,另一方面通过与活性焦脱硫的比较,为今后贵冶在脱硫工艺的选择上提供可靠依据。
2 工艺流程及特点介绍
2.1 工艺流程
本烟气脱硫装置采用湿法有机胺脱硫工艺,装置采用有机胺浓液稀释到一定浓度后作为脱硫剂。
该工艺主要分为4个过程,即烟气的预处理、SO2的吸收、SO2的再生和胺液的净化。
烟气预处理的目的是降低进入脱硫塔烟气温度和洗涤烟气中的酸雾及粉尘等杂质,为烟气在脱硫塔采用有机胺脱硫剂高效脱硫奠定基础。
烟气预处理设置洗涤塔一座,采用空塔喷雾洗涤降温除尘。
二氧化硫吸收系统是烟气脱硫系统的核心。
在吸收装置中吸收剂与烟气相接触,吸收剂与SO2发生可逆性反应。
为了达到最大的吸收效果, 采用高效耐腐蚀规整填料塔和空喷吸收相结合的形式。
烟气经过洗涤塔洗涤降温净化后,将烟气中的粉尘和部分SO3等杂质洗涤下来,烟气温度被降低至约40℃,进入脱硫塔下段,与从喷头处循环喷淋的脱硫液逆流接触,气体中60%的SO2被吸收。
未被吸收的烟气进入脱硫塔中部,在两段分布的规整填料中实现气液的逆流接触和SO2的高效吸收,吸收液为再生塔再生后温度35~45℃的贫液。
未被吸收的净化气进入脱硫塔上部,经回收液回收夹带的溶液后,从塔顶引出,经塔顶烟囱送至硫酸
尾气总管。
SO2再生装置包含一个再沸器、一座再生塔及二氧化硫、蒸汽冷凝冷却系统和二氧化硫真空系统,将吸收了SO2的富液从吸收装置通过换热后进入再生装置,减压再生后返回脱硫塔。
从脱硫塔底部出来的吸收液温度约43~45℃,经富液泵打入再生塔一级冷凝器、贫富液换热器升温至约60~65℃,进入再生塔上部,塔釜经再沸器加热至75~85℃再生。
从再生塔底部出来的溶液经贫液泵加压,进入贫富液换热器换热、贫液冷却器冷却后,大部分进入脱硫塔吸收SO2,小部分送溶液净化装置,以除去溶液中的热稳定性盐。
贫液经脱盐前冷却器冷却后,进入脱硫液净化系统除去系统中的SO42-和Cl-。
净化后的脱硫液进入系统继续使用。
有机胺法脱硫工艺流程如下图:
2.2 工艺原理
有机胺湿法烟气脱硫技术是一种新兴的烟气脱硫技术、具有处理二氧化硫浓度低、脱硫效率高、吸收剂可以循环利用、不产生二次污染、能有效解决烟气制酸的稳定性问题等优点。
有机胺脱硫化学原理为:在水溶液中, 溶解的SO2会发生式(1) 、(2) 所示的可逆水合和电离过程:
在水中加入有机胺缓冲剂,通过和水中的氢离子发生反应,形成胺盐,反应(1)、(2) 方
程式向右发生反应, 增大了SO2的溶解量如反应(3),可以增加SO2的溶解量。
采用蒸汽加热, 可以逆转( 1) ~ ( 3) 的方程式,再生吸收剂,得到高浓度的SO2气体,对SO2进行回收利用。
一元胺的吸收功能过于稳定, 以至于无法通过改变温度再生SO2,一旦一元胺与SO2或其他的强酸发生化学反应便永久的生成一种非常稳定的胺盐。
二元胺在烟气脱硫上具有更大优势, 二元胺在工艺过程中首先与一种发生反应:
R1 R2N - R3 - NR4R5 + HX = R1 R2NH+ - R3- NR4 R5 +X- (4)
式(4) 中X-为强酸根离子, 反应式右边的单质子胺基是一种非常稳定的盐,不能通过改变温度再生, 另一个胺基是强基胺, 其化学性能不稳定, 能与SO2发生化学反应, 在不同的温度下可以再生, 反应式如式(5) :
化学平衡和再生之间的关系是有机胺烟气脱硫的精华之所在。
2.3 工艺特点
有机胺法烟气脱硫技术是利用复合有机胺液作为脱硫剂,对烟气中SO2进行吸收脱除的一种技术。
有机胺是良好的SO2吸收剂,其溶解度远高于钙基等吸收剂。
用其吸收烟气中的SO2是气-液或气-气相反应,反应速度快,脫硫效率最高可达99.5%,吸收剂效率高,满足日益提高的环保要求。
工艺适应性较强,脱硫剂对二氧化硫有较大的吸收量和对二氧化硫有较高的选择性,在烟气量、SO2浓度大幅波动时,仍能保证稳定的脱硫效率。
由于解吸塔采用负压再生,不但提高了解吸效率,降低了再生温度,有效减缓了设备腐蚀和脱硫液老化,为脱硫系统高效低耗长周期运行奠定了基础,而且将真空泵替代二氧化硫尾气加压风机,大幅度降低了系统能耗。
系统运行可靠、简便,系统装置开停方便,运行和维修费用较低。
3主要性能指标如下表:
项目单位指标
装置处理烟气能力Nm3/h 35000
脱硫效率%≥97
净化烟气中SO2mg/Nm3≤50
循环水用量m3/h≤80
电耗(有功功率)kW•h/h≤135
蒸汽消耗t/h ≤2.0
装置操作弹性% 60~120
除尘能力% ≥50
4 主要设备明细表如下:
名称数量型号规格
洗涤塔 1 园筒型 DN2800 H=6261 V=35.42m3
洗涤泵 1 IHF80-50-200 流量50m3/h;扬程50m
脱硫塔 1 园筒型 DN2400 H=23250 V=93.59m3
富液泵 1 80HFM-II 流量40m3/h;扬程70m
脱硫塔下段循环泵 1 IHF100-80-160 流量100m3/h;扬程32m
再生塔 1 园筒型 DN1200 H=23325
贫液泵 1 80HFM-II 流量40m3/h;扬程70m
回收液槽 1 园筒型 DN1850 H=3900 VN10m3
溶液槽 1 园筒型 DN2800 H=4600 VN30m3
气液分离器 1 园筒型 DN1400 L=3870 VN5m3
再沸器 1 管式 FN100 m2
液环式真空泵 2 2BV5131 流量385m3/h;进口压力:3KPa;出口压力:115KPa 5 性能测试
根据该套装置的试运行情况,车间于2014年11月进行了为期15天的性能考核,考核情况如下表:
项目单位设计数据实际数据
烟气量 Nm3/H 35000 35000
入口浓度 mg/Nm3 600-700 401.9
出口浓度 mg/Nm3≤50 26.8
温度℃≤70 60
酸雾 mg/Nm3 400 257
阻力降 KPa ≤2 3.3
入口压力 KPa 2.5 3.6
含尘浓度 mg/Nm3≤50 无监测
氟氯量 mg/Nm3≤5 3.5
烟道直径 mm 1120 1120
6 问题与措施
在试生产运行过程中,出现过一些问题,通过及时采取措施,弥补了设计上的一些不足。
6.1 作业率虽然较高,达到95.77%,但仍没有达到我们制酸系统作业率(99.96%)的要求。
后续需在设备和材料选型上有所改进,减少设备故障和跑、冒、滴、漏,以保证高作业率。
6.2 本套装置设备故障率较高。
本套装置为了节约成本,设备选型主要以修旧利废为主,由于高温及稀酸腐蚀等因素,设备故障率居高不下,这也是影响作业率和脱硫效率的主要因素。
6.3 自动化程度较低。
如一些必要的监视数据和脱盐自动化等都没有设计,离子交换柱等设备需要改进。
6.4 高温下的有机胺对再生塔及其填料是否有腐蚀还需要进一步的试验观察。
7 结束语
通过半年时间的试运行,硫酸四系列尾气有机胺脱硫装置各项指标基本正常,主要是针对一些未解决的问题需进一步摸索研究,在生产过程中不断完善,同时下一步进行本套装置扩建,进一步降低尾气排放的SO2浓度。