烧结烟气中二氧化硫地脱除技术
烧结烟气脱硫工艺流程简介

烧结烟气脱硫工艺流程简介发表时间:2019-07-18T09:00:03.323Z 来源:《科技尚品》2019年第3期作者:孙雅文[导读] 文章济钢集团国际工程技术有限公司1、烧结烟气中SO2的生成机理及排放规律由于烧结过程中物理化学反应的复杂性,导致了烧结过程中硫元素存在的形态的多样性和含硫物质分布的不均匀性。
二氧化硫经历了析出、被吸收和再析出的复杂物化过程,呈现出烧结工艺特有的二氧化硫及其他硫化物的分布特性。
1.1 烧结烟气中SO2的生成机理按物料的烧结形态、烧结料层从上到下分成烧成区、燃烧烧融带、干燥预热带及湿润带。
热量从烧结料层的上层向下层传递。
湿润带上平面温度小于100℃,且含有自由水,此处距离燃烧熔融带底面(1000℃以上)仅有几厘米。
处于上述两个带之间的干燥预热带自上而下流动的高温烟气急速加热。
干燥预热带的停留时间约2min左右。
在干燥预热带之后,燃烧颗粒开始燃烧,通过燃烧放出的热进一步加热物料,使温度达到1300℃左右,部分物料熔融流动。
停止燃烧后床层开始冷却,熔融五再次固化,从而完成烧结过程。
若按照烧结烟气中二氧化硫的行为来区分,整个烧结过程自上而下可以分为二氧化硫扩散析出区、二氧化硫燃烧析出区和二氧化硫析出区三个区域。
二氧化硫燃烧析出区是产生二氧化硫的主要区域,它与干燥预热带和燃烧熔融带相对应。
以单质和硫化物形式存在的硫在干燥预热带发生的氧化反应中以气态硫化物的形式释放。
大部分二氧化硫直接扩散到烟气中去,少部分被液相或固体颗粒包纳或被碱性助剂再吸收形成稳定的物质(如CaS,CaSO4)。
二氧化硫扩散区对应于烧成区,该区域不存在生产的二氧化硫的化学反应,主要是烧结矿块中已形成的二氧化硫向烟气中的扩散。
二氧化硫吸收区与湿润带相对应,在该区域由于烧结原料中碱性物质和液态水的存在,大部分二氧化硫被吸收,但随着烧结过程的推进,该区域的上端面下移,使其吸收能力和容纳能力逐步下降,在烧结末期该区域消失。
燃煤烟气脱硫技术

近年来,我国越来越重视环境污染问题,相关环保政策和大气污染物排放标准的相继出台,对烟气排放的要求更加严格。
在超低排放的背景下,降低燃煤烟气中的硫含量排放势在必行。
目前,我国燃煤烟气脱硫工艺快速进展,也引进了很多国外先进的脱硫技术并实现了外乡化。
常见的脱硫技术以燃烧阶段为根底可以分为三大类,即燃烧前脱硫、燃烧中脱硫、燃烧后脱硫。
目前,燃烧后脱硫技术以其成熟的技术优势在世界范围内广泛应用,尤其是在兴旺国家内更是占有最高的市场比例,取得的效果显著。
1燃烧前脱硫在煤炭燃烧前将硫分从煤炭中脱离出来,以削减最终排放烟气中二氧化硫含量的技术称为燃烧前脱硫。
这种技术不仅能够提高煤炭自身的燃烧效率,使煤炭充分燃烧,还可以将硫元素对后续存在的工艺设备造成的损害和影响降至最低。
依据脱硫根本原理燃烧前脱硫可分为物理法脱硫、化学法脱硫和微生物法脱硫。
1.1物理法脱硫物理法脱硫利用煤中硫分和煤基体的密度、导电性、悬浮性等物理性质之间的差异而在洗选煤过程中脱除存在于煤中的无机硫,是我国目前较为常用的燃烧前脱硫方法。
该法的优点是工艺简洁,投资少;缺点是只能脱除煤中的无机硫,对于煤中的有机硫没有脱除效果,并且脱硫效率也不高。
目前常用的工艺有:重选法、浮选法、磁选法、电选法。
重选法常用的脱硫设备有水力旋流机、摇床等。
该方法的优点是本钱低、处理量大、污染小,但局限性也比较大,几乎不能脱除有机硫,对颗粒较细的煤炭脱除效果也不好。
浮选法利用矿物的疏水性,通过较多气泡黏附在其外表而上浮在浮选液之上,形成一种矿化泡沫层,刮除该层泡沫层从而实现煤炭与矿物杂质的分别。
磁选法首先将煤与含硫矿物经过强磁场,然后进入磁选,利用它们磁性的差异来分别煤中的含硫矿物。
但该方法只能脱除局部无机硫,对有机硫无脱除作用。
1.2化学法脱硫化学法脱硫是在高温、高压、氧化剂等作用下,将煤中的硫氧化或者置换,最终实现脱硫目的。
该法的优点是能够脱除无机硫和大局部有机硫,但所用设备简单,能耗大,本钱较高,并且脱硫试剂对设备具有肯定的腐蚀性,会破坏煤炭构造,难以工业化利用。
烟道气脱氧技术-概述说明以及解释

烟道气脱氧技术-概述说明以及解释1.引言1.1 概述概述部分的内容可以介绍烟道气脱氧技术的基本概念和背景信息。
可以按照以下内容来撰写:烟道气脱氧技术是一种通过去除烟道气中的二氧化硫和氮氧化物等有害气体,减少大气污染的环境保护技术。
随着工业化和城市化的发展,大量二氧化硫和氮氧化物等有害气体的排放对环境和人体健康带来了严重影响。
烟道气脱氧技术的出现,为解决这一问题提供了有效手段。
烟道气脱氧技术主要通过化学或物理方法,将燃烧过程中产生的有害气体转化为其他相对无害或可利用的物质,以达到减少污染物排放的目的。
在烟道气脱氧技术中,常见的方法包括湿法脱硫、选择性催化还原(SCR)、选择性非催化还原(SNCR)等。
烟道气脱氧技术的应用领域广泛,包括发电厂、钢铁冶炼厂、化工厂、水泥厂等大型工业生产单位。
这些生产单位的燃烧过程中排放的烟道气中含有大量的有害气体,对周围环境和生态系统造成了严重威胁。
烟道气脱氧技术的应用可以有效降低这些有害气体的排放量,实现减少污染物对环境的影响,保护环境和人类健康的目标。
然而,烟道气脱氧技术也面临着一些挑战。
首先,技术的成本相对较高,需要投入较大的资金和资源。
此外,烟道气脱氧技术对设备和技术要求较高,需要具备先进的脱氧设备和专业的操作人员。
此外,烟道气脱氧技术的运行过程中也会产生一些副产物,对环境可能造成新的影响。
尽管存在挑战,烟道气脱氧技术依然具有重要意义。
它能够显著减少大气中的有害气体排放,改善空气质量,保护人类健康。
未来,研发更有效、低成本的烟道气脱氧技术将成为环境保护领域的重要课题。
通过持续创新和技术进步,我们有望更好地应对环境污染问题,实现可持续的发展。
文章结构部分的内容:1.2 文章结构本文共分为三个主要部分:引言、正文和结论。
在引言部分,将对烟道气脱氧技术进行概述,包括其定义和原理。
同时介绍文章的结构和目的。
在正文部分,将详细讨论烟道气脱氧技术的应用领域。
探讨该技术在环境保护、工业生产等方面的实际应用情况。
氨法脱硫技术在烧结烟气治理领域的应用
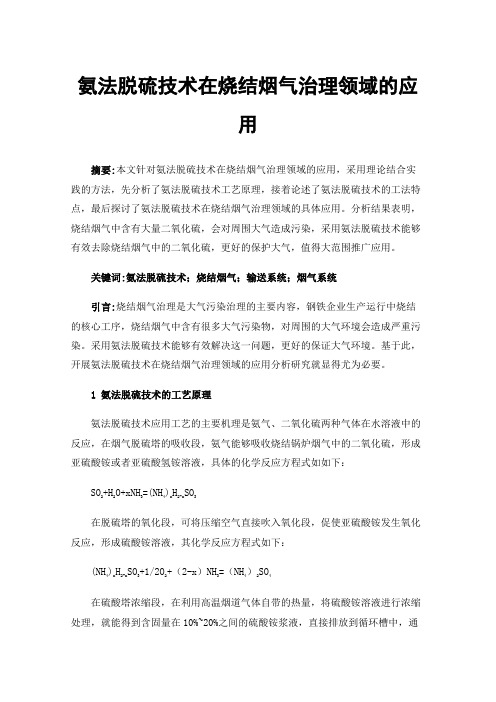
氨法脱硫技术在烧结烟气治理领域的应用摘要:本文针对氨法脱硫技术在烧结烟气治理领域的应用,采用理论结合实践的方法,先分析了氨法脱硫技术工艺原理,接着论述了氨法脱硫技术的工法特点,最后探讨了氨法脱硫技术在烧结烟气治理领域的具体应用。
分析结果表明,烧结烟气中含有大量二氧化硫,会对周围大气造成污染,采用氨法脱硫技术能够有效去除烧结烟气中的二氧化硫,更好的保护大气,值得大范围推广应用。
关键词:氨法脱硫技术;烧结烟气;输送系统;烟气系统引言:烧结烟气治理是大气污染治理的主要内容,钢铁企业生产运行中烧结的核心工序,烧结烟气中含有很多大气污染物,对周围的大气环境会造成严重污染。
采用氨法脱硫技术能够有效解决这一问题,更好的保证大气环境。
基于此,开展氨法脱硫技术在烧结烟气治理领域的应用分析研究就显得尤为必要。
1氨法脱硫技术的工艺原理氨法脱硫技术应用工艺的主要机理是氨气、二氧化硫两种气体在水溶液中的反应,在烟气脱硫塔的吸收段,氨气能够吸收烧结锅炉烟气中的二氧化硫,形成亚硫酸铵或者亚硫酸氢铵溶液,具体的化学反应方程式如如下:SO2+H2O+xNH3=(NH4)xH2-xSO3在脱硫塔的氧化段,可将压缩空气直接吹入氧化段,促使亚硫酸铵发生氧化反应,形成硫酸铵溶液,其化学反应方程式如下:(NH4)xH2-xSO3+1/2O2+(2-x)NH3=(NH4)2SO4在硫酸塔浓缩段,在利用高温烟道气体自带的热量,将硫酸铵溶液进行浓缩处理,就能得到含固量在10%~20%之间的硫酸铵浆液,直接排放到循环槽中,通过旋流器进行分离后,再用离心机进行脱水处理,再经过干燥处理之后,就能得到硫铵产物。
2氨法脱硫技术的工法特点2.1完全资源化在烧结烟气治理中应用氨法脱硫技术能够将回收到的二氧化硫和氨全部转化为化肥,不会产生废水、废气、废渣等,也就没有不存在二次污染,实现了完全资源化,符合绿色、环保、循环经济的发展要求【1】。
2.2副产物价值高应用氨法脱硫技术每吸收1t液氨,可脱除2t二氧化硫,形成4t硫酸钠,按照市场价格算,液氨每吨2000元,硫酸铵每吨700元,烧结烟气中每吨二氧化硫能够体现400元的价值,应用成本比较小。
烧结烟气脱硫脱硝处理技术

烧结烟气脱硫脱硝处理技术摘要:近些年,我国经济发展迅速,钢铁企业为我国经济发展做出了很大贡献。
随着环保要求的日益严格,冶金行业烟气协同脱硫脱硝将是烟气气态污染物治理的主流方向,本文分析了目前主流的烟气脱硫和脱硝工艺技术的原理、分类,同时简述了脱硫脱硝的新技术。
为脱硫脱硝工艺及其改进提供理论依据与指导。
关键词:烧结;烟气;脱硫脱硝;处理技术引言近些年来,在可持续发展理念逐步落实的时代背景下,各行各业都在积极转变生产观念和方式,以达到经济效益和生态效益同步发展的目的。
但从目前来看,部分钢铁厂在烧结烟气脱硫脱硝处理方面仍存在一定的不利因素,基于此,有必要对其展开更加深层次的探索。
1烧结烟气特点阐释第一,烧结烟气所产生的烟气量比较大。
一般情况下,1t烧结矿会产生1.5立方千米至6立方千米的烧结烟气量,由于不同类型的烧结燃料具有不同的透气性,同时所使用的的辅助材料也不均匀,导致烧结烟气系统所出现的阻力发生明显变化,从而提高了烧结矿的烧结烟气量。
第二,烧结烟气所产生的SO2和NOX浓度出现变化。
一般情况下,烧结烟气所生成的SO2浓度一般在300至800mg/Nm3范围内,然而当SO2浓度较高时,其浓度会高于2000至4000mg/Nm3范围。
而烧结烟气所生成的NOX浓度范围为0.15至0.3g/Nm3,若NOX浓度较高时,其浓度将会达到0.5至0.6g/Nm3。
第三,烧结烟气所包含的成分较为复杂。
在烧结烟气中,其包含了许多不同类别的污染物,在这些污染物中,氧化碳、氯化氢、多环芬烃和HF等为主要成分,但是二噁英和重金属等则是烟尘的主要成分。
在烧结生产工业中所产生的二噁英排放量仅低于垃圾焚烧业,位居排放量第二位。
第四,烧结行业所产生的烟气温度容易出现变化,并且温度的变化范围比较大。
一般情况下,烧结烟气的温度处于120到180℃之间,如果运用低温烧结技术,其所生成的烟气温度则在80摄氏度到180摄氏度范围内。
2烧结烟气脱硫脱硝处理技术2.1 SCR脱硝脱硝系统采用选择性催化还原技术(SCR),在催化剂的作用下将20%氨水作为还原剂与烟气中NO x进行反应,达到去除NOx的目的。
我国烧结烟气脱硫现状及脱硝技术研究

我国烧结烟气脱硫现状及脱硝技术研究随着全世界经济的快速发展,环境问题已经成为了我们人类所面临的最严峻的问题之一。
而其中大气环境又是人类赖以生存的最基本的要素之一,如今人们还是主要利用煤、石油和天然气等能源作为燃料,它们的燃烧会产生大量的二氧化硫、氮氧化合物和烟尘颗粒物等,而其中SO2和NOx又是主要的大气污染物,对大气环境造成了严重的污染。
大气污染造成的自然灾害也在我们的身边频繁發生,酸雨泛滥、气候异常、光化学烟雾等严重影响了我们的生活、健康,可以预见,如果随着大气环境的不断恶化,最终会导致地球生态环境和平衡遭到严重破坏,人类以及动植物的生存将会面临严重威胁。
标签:烟气烧结;脱硫技术;脱硝技术一、烟气脱硫脱硝技术现状目前,人们为了减少二氧化硫排放到大气中去,主要采用的控制方法是燃烧一些低硫燃料、对燃料进行前期脱硫、燃料燃烧过程脱硫以及末端尾气处理。
燃烧前脱硫主要是利用一些特定的方法对煤等燃料进行净化,以去除原来燃料中的硫分、灰分等杂质。
燃烧过程中脱硫主要是指当煤等燃料在炉内燃烧时,同时向炉内恰当的位置喷入脱硫剂(常用的有石灰石、熟石灰、生石灰等),脱硫剂在炉内较高温度下受热分解成CaO和MgO等,然后与燃烧过程中产生的SO2和SO3发生反应,生成硫酸盐和亚硫酸盐,最后以灰渣的形式排出,从而达到脱硫的目的。
而目前世界上应用比较成熟的技术主要是燃烧后脱硫,即烟气脱硫技术。
其中,又以一些湿法、干法以及其他典型的方法应用最为广泛。
二、烟气脱硫技术(一)湿法烟气脱硫技术(1)石灰石/石灰法石灰石/石灰法烟气脱硫是采用石灰石或者石灰浆液脱除烟气中二氧化硫的方法。
石灰石/石灰法开发比较早,工艺成熟,吸收剂价格便宜而且容易得到,应用比较广泛。
其主要工艺参数为:浆液pH在5.6-7.5之间,浆液固体含量:1.0%-15%,液气比:大于5.3L/m3钙硫比为1.05-1.1之间,碳酸钙粒度90%通过325目,纯度大于90%脱硫率大于90%。
烟气脱硫脱硝 技术方案

1、化学反应原理任意浓度的硫酸、硝酸,都能够跟烟气当中细颗粒物的酸、碱性氧化物产生化学反应,生成某酸盐和水,也能够跟其它酸的盐类发生复分解反应、氧化还原反应,生成新酸和新盐,通过应用高精尖微分捕获微分净化处理技术产生的巨大量水膜,极大程度的提高烟气与循环工质接触、混合效率,缩短工艺流程,在将具有连续性气、固、液多项流连续进行三次微分捕获的同时,连续进行三次全面的综合性高精度微分净化处理.2、串联叠加法工作原理现有技术装备以及烟气治理工艺流程的效率都是比较偏低,例如脱硫效率一般都在98%左右甚至更低,那么,如果将三个这样工作原理的吸收塔原型进行串联叠加性应用,脱硫效率一定会更高,例如99.9999%以上。
工艺流程工作原理传统技术整治大气环境污染,例如脱硫都是采用一种循环工质,那么,如果依次采用三种化学性质截然不同的循环工质,例如稀酸溶液、水溶液和稀碱溶液进行净化处理,当然可以十分明显的提高脱除效率,达到极其接近于百分百无毒害性彻底整治目标。
1、整治大气环境污染,除尘、脱硫、脱氮、脱汞,进行烟气治理,当然最好是一体化一步到位,当然首选脱除效率最高,效价比最高,安全投运率最高,脱除污染因子最全面,运行操作最直观可靠,运行费用最低的,高效除尘、脱硫、脱氮、脱汞一体化高精尖技术装备。
2、高效除尘、脱硫、脱氮、脱汞一体化高精尖技术装备,采用最先进湿式捕获大化学处理技术非选择性催化还原法,拥有原创性、核心性、完全自主知识产权,完全国产化,发明专利名称《一种高效除尘、脱硫、脱氮一体化装置》,发明专利号.3、吸收塔的使用寿命大于30年,保修三年,耐酸、耐碱、耐摩擦工质循环泵,以及其它标准件的保修期,按其相应行业标准执行。
4、30年以内,极少、甚至可以说不会有跑、冒、滴、漏、渗、堵现象的发生。
5、将补充水引进到3#稀碱池入口,根据实际燃煤含硫量和烟气含硝量调整好钠碱量以及相应补充水即可正常运行。
6、工艺流程:三个工质循环系统的循环工质,分别经过三台循环泵进行加压、喷淋。
钙基循环流化床烧结烟气同时脱硫脱硝技术
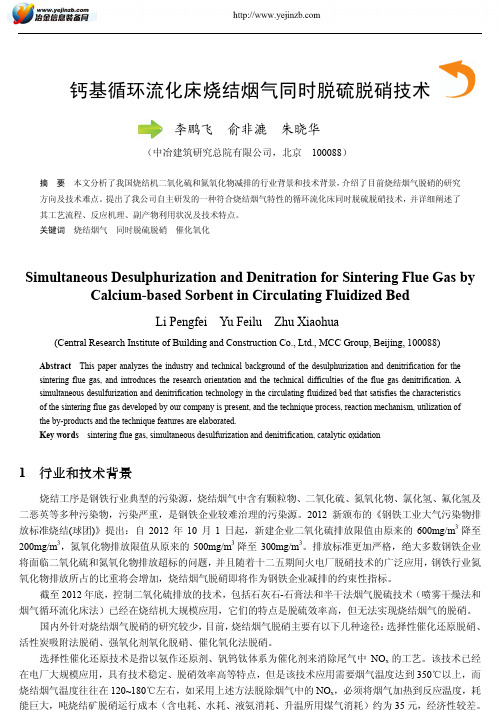
钙基循环流化床烧结烟气同时脱硫脱硝技术李鹏飞俞非漉朱晓华(中冶建筑研究总院有限公司,北京 100088)摘 要 本文分析了我国烧结机二氧化硫和氮氧化物减排的行业背景和技术背景,介绍了目前烧结烟气脱硝的研究方向及技术难点。
提出了我公司自主研发的一种符合烧结烟气特性的循环流化床同时脱硫脱硝技术,并详细阐述了其工艺流程、反应机理、副产物利用状况及技术特点。
关键词 烧结烟气 同时脱硫脱硝 催化氧化Simultaneous Desulphurization and Denitration for Sintering Flue Gas by Calcium-based Sorbent in Circulating Fluidized BedLi Pengfei Yu Feilu Zhu Xiaohua(Central Research Institute of Building and Construction Co., Ltd., MCC Group, Beijing, 100088)Abstract This paper analyzes the industry and technical background of the desulphurization and denitrification for the sintering flue gas, and introduces the research orientation and the technical difficulties of the flue gas denitrification. A simultaneous desulfurization and denitrification technology in the circulating fluidized bed that satisfies the characteristics of the sintering flue gas developed by our company is present, and the technique process, reaction mechanism, utilization of the by-products and the technique features are elaborated.Key words sintering flue gas, simultaneous desulfurization and denitrification, catalytic oxidation1 行业和技术背景烧结工序是钢铁行业典型的污染源,烧结烟气中含有颗粒物、二氧化硫、氮氧化物、氯化氢、氟化氢及二恶英等多种污染物,污染严重,是钢铁企业较难治理的污染源。
常见烟气脱硫脱硝技术介绍

常见烟气脱硫脱硝技术介绍1、磷铵肥法(PAFP)烟气脱硫技术磷铵肥法(Phosphate Ammoniate Fertilizer Process,简称PAFP),此技术的特点是将烟气中的SO2脱除并针对我国硫资源短缺的现状,回收SO2取代硫酸生产肥料,在解决污染的同时,又综合利用硫资源,是一项化害为利的烟气脱硫新方法。
2、活性炭纤维法(ACFP)烟气脱硫技术活性炭纤维法(Activated Carbon Fiber Process,简称ACFP)烟气脱硫技术是采用新材料脱硫活性炭纤维催化剂(DSACF)脱除烟气中SO2并回收利用硫资源生产硫酸或硫酸盐的一项新型脱硫技术。
该技术脱硫率可达95%以上,单位脱硫剂处理能力会高于活性炭脱硫一个数量级以上(一般GAC处理能力为102Nm3/h.t,而ACF可达104Nm3/h.t)。
由于工艺过程简单,设备少,操作简单。
投资和运行成本低,且能在消除SO2污染同时回收利用硫资源,因而可在电厂锅炉烟气、有色冶炼烟气、钢铁厂烧结烟气及各种大中型工业锅炉的烟气SO2污染控制中采用,改善目前烟气脱硫技术装置“勉强上得起,但运行不起”的状况。
该烟气脱硫技术按10万KW机组锅炉机组烟气计,装置投资费用3500万,年产硫酸3万~4万吨。
仅用于全国高硫煤电厂脱硫每年约可减少SO2排放240万吨,副产硫酸360万吨,产值可达数十亿元。
3、软锰矿法烟气脱硫资源化技术MnO2是一种良好的脱硫剂。
在水溶液中,MnO2与SO2发生氧化还原发应,生成了MnSO4。
软锰矿法烟气脱硫正是利用这一原理,采用软锰矿浆作为吸收剂,气液固湍动剧烈,矿浆与含SO2烟气充分接触吸收,生成副产品工业硫酸锰。
该工艺的脱硫率可达90%,锰矿浸出率为80%,产品硫酸锰达到工业硫酸锰要求(GB1622-86)。
常规生产工业硫酸锰方法是:软锰矿粉与硫酸和硫精沙混合反应,产品净化得到工业硫酸锰。
由于我国软锰矿品位不高,硫酸耗量增大,成本上升。
浅谈烟气脱硫技术及脱硫脱硝除尘与环保措施
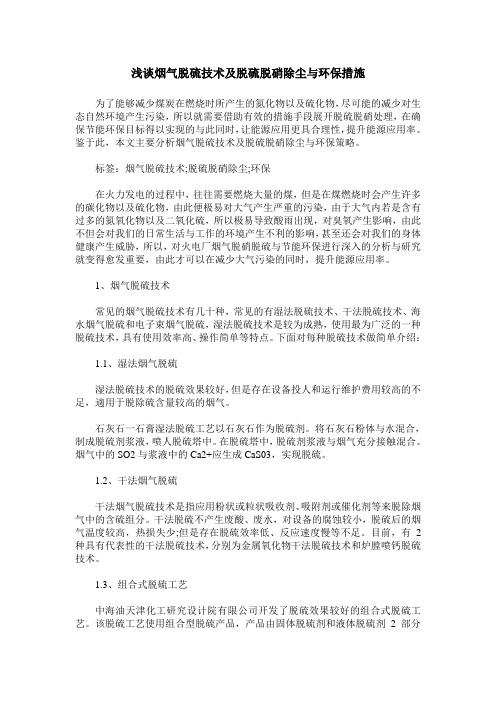
浅谈烟气脱硫技术及脱硫脱硝除尘与环保措施为了能够减少煤炭在燃烧时所产生的氮化物以及硫化物,尽可能的减少对生态自然环境产生污染,所以就需要借助有效的措施手段展开脱硫脱硝处理,在确保节能环保目标得以实现的与此同时,让能源应用更具合理性,提升能源应用率。
鉴于此,本文主要分析烟气脱硫技术及脱硫脱硝除尘与环保策略。
标签:烟气脱硫技术;脱硫脱硝除尘;环保在火力发电的过程中,往往需要燃烧大量的煤,但是在煤燃烧时会产生许多的碳化物以及硫化物,由此便极易对大气产生严重的污染,由于大气内若是含有过多的氮氧化物以及二氧化硫,所以极易导致酸雨出现,对臭氧产生影响,由此不但会对我们的日常生活与工作的环境产生不利的影响,甚至还会对我们的身体健康产生威胁,所以,对火电厂烟气脱硝脱硫与节能环保进行深入的分析与研究就变得愈发重要,由此才可以在减少大气污染的同时,提升能源应用率。
1、烟气脱硫技术常见的烟气脱硫技术有几十种,常见的有湿法脱硫技术、干法脱硫技术、海水烟气脱硫和电子束烟气脱硫,湿法脱硫技术是较为成熟,使用最为广泛的一种脱硫技术,具有使用效率高、操作简单等特点。
下面对每种脱硫技术做简单介绍:1.1、湿法烟气脱硫湿法脱硫技术的脱硫效果较好,但是存在设备投人和运行维护费用较高的不足,適用于脱除硫含量较高的烟气。
石灰石一石膏湿法脱硫工艺以石灰石作为脱硫剂。
将石灰石粉体与水混合,制成脱硫剂浆液,喷人脱硫塔中。
在脱硫塔中,脱硫剂浆液与烟气充分接触混合。
烟气中的SO2与浆液中的Ca2+应生成CaS03,实现脱硫。
1.2、干法烟气脱硫干法烟气脱硫技术是指应用粉状或粒状吸收剂、吸附剂或催化剂等来脱除烟气中的含硫组分。
干法脱硫不产生废酸、废水,对设备的腐蚀较小,脱硫后的烟气温度较高,热损失少;但是存在脱硫效率低、反应速度慢等不足。
目前,有2种具有代表性的干法脱硫技术,分别为金属氧化物干法脱硫技术和炉膛喷钙脱硫技术。
1.3、组合式脱硫工艺中海油天津化工研究设计院有限公司开发了脱硫效果较好的组合式脱硫工艺。
烧结烟气臭氧氧化-半干法吸收脱硫脱硝实践

烧结烟气臭氧氧化-半干法吸收脱硫脱硝实践一、前言烧结烟气中的二氧化硫和氮氧化物是大气污染物的主要来源之一。
针对这一问题,人们研究出了许多脱硫脱硝的方法。
本文将介绍一种烧结烟气脱硫脱硝的实践方法——烧结烟气臭氧氧化-半干法吸收脱硫脱硝。
二、烧结烟气臭氧氧化-半干法吸收脱硫脱硝实践方法1. 烧结烟气臭氧氧化烧结烟气脱硝的第一步是臭氧氧化。
臭氧可以将氮氧化物(NOx)和二氧化硫(SO2)氧化为更易于吸收的氧化物。
臭氧氧化反应可以表示为:NO + O3 → NO2 + O2SO2 + O3 → SO3 + O2SO3 + H2O → H2SO4在实践中,臭氧通常通过紫外线灯生成。
2. 半干法吸收脱硫脱硝烧结烟气经过臭氧氧化后,进入半干法吸收脱硫脱硝系统。
半干法吸收脱硫脱硝分为两个阶段:半干法脱硫和半干法脱硝。
2.1 半干法脱硫半干法脱硫使用硫酸铁线(FeSO4.7H2O)吸收烧结烟气中的二氧化硫。
硫酸铁线在吸收过程中不需要添加水,因此被称为“半干法”。
半干法脱硫的反应可以表示为:SO2 + FeSO4 + O2 + H2O → FeSO4.7H2O + H2SO42.2 半干法脱硝半干法脱硝使用异丙醇胺(IPA)作为还原剂,将烧结烟气中的氮氧化物(NOx)还原为氮气(N2)。
半干法脱硝的反应可以表示为:4NO + 4NH3 + O2 → 4N2 + 6H2O3. 优势烧结烟气臭氧氧化-半干法吸收脱硫脱硝方法具有以下优势:1.同时脱硫和脱硝:这种方法可以一次性脱除烟气中的二氧化硫和氮氧化物,不需要分别进行脱硫和脱硝。
2.高效:经过臭氧氧化后,二氧化硫和氮氧化物都被氧化成了更易于吸收的氧化物,半干法吸收效率更高。
3.低耗能:半干法脱硫不需要添加水,而半干法脱硝所需的异丙醇胺量较少,因此整个系统的能耗较低。
三、结论烧结烟气臭氧氧化-半干法吸收脱硫脱硝是一种高效、低耗能的脱硫脱硝方法。
该方法可以将烟气中的二氧化硫和氮氧化物一次性脱除,同时具有较高的脱硫和脱硝效率,在实际应用中具有较广泛的应用前景。
天然气燃烧的烟气脱硫脱硝技术

天然气燃烧的烟气脱硫脱硝技术在当前环境保护和空气质量改善的背景下,天然气燃烧的烟气脱硫脱硝技术的研究和应用日益受到关注。
天然气燃烧产生的烟能源烟气中的氮氧化物(NOx)和二氧化硫(SO2)是对环境和人体健康危害最大的污染物之一,因此有效地脱除烟气中的NOx和SO2成为了急需解决的问题。
本文将从脱硫、脱硝两个方面介绍天然气燃烧的烟气脱硫脱硝技术的研究进展和应用情况。
一、天然气燃烧烟气脱硫技术1.湿法脱硫技术湿法脱硫技术是目前应用最为广泛的烟气脱硫技术之一,其原理是利用含有碱性氧化剂的溶液与烟气中的SO2进行反应,生成易于去除的硫酸盐。
常用的湿法脱硫工艺包括石膏法、氧化吸收法和氨法等。
(1)石膏法石膏法是一种成熟的湿法脱硫技术,其核心是利用石膏颗粒与烟气中的SO2进行反应,生成硫酸钙,最终生成石膏。
该技术具有投资和操作成本较低的优势,广泛应用于燃煤电厂中,但其对高温烟气中的SO2去除效果有限。
(2)氧化吸收法氧化吸收法是一种高效的湿法脱硫技术,其核心是通过将烟气中的SO2氧化为亚硫酸氢钠,再与氢氧化钠溶液反应生成硫代硫酸钠,并最终沉淀为硫酸钠。
该技术对烟气中的SO2去除效果较好,但操作复杂且投资成本较高。
(3)氨法氨法是一种新兴的湿法脱硫技术,其核心是将氨气引入烟气中,与SO2反应生成亚硫酸氨盐,再通过氧化反应生成硫酸铵。
该技术对烟气中的SO2去除效果较好,且适用于高温和高硫煤气的脱硫,但对运行和维护要求较高。
2.干法脱硫技术干法脱硫技术是一种较为成熟的烟气脱硫技术,其核心是利用固体吸收剂吸附烟气中的SO2,达到脱硫的目的。
常用的干法脱硫工艺包括固体氧化物法、活性炭法和氧化剂法等。
(1)固体氧化物法固体氧化物法是一种常用的干法脱硫技术,其主要原理是将固体吸附剂喷入烟气中,与SO2发生化学反应生成易于去除的硫酸盐。
常用的固体吸附剂包括石灰石和活性系煤灰等。
该技术具有较高的脱硫效率和成本效益,但对烟气颗粒物的去除效果较差。
烟气脱硫技术方案

烟气脱硫技术方案烟气脱硫技术是一种用于减少燃煤和发电厂产生的二氧化硫(SO2)的技术。
根据国家大气污染控制要求,烟气中的二氧化硫的排放浓度必须控制在一定范围之内。
下面将提供一种烟气脱硫技术方案,它是利用湿法氧化吸收法进行二氧化硫的脱除。
该技术基于湿法氧化吸收法,具体步骤如下:1.烟气预处理:首先,将原始烟气进行预处理,去除颗粒物和其他固体杂质。
这可以通过采用旋风除尘器或电除尘器等设备来实现。
2.安装吸收塔:在炉固废焚烧炉或发电厂的烟囱底部,安装一个吸收塔。
吸收塔是一个具有多层喷嘴的塔状装置,用于接收排放的烟气并进行湿法脱硫处理。
3.准备吸收液:准备一种含有氧化剂和碱性成分的吸收液。
通常,常用的氧化剂是过氧化氢或二氧化氯,而碱性成分可以是石灰石或氨水。
4.硫化物的氧化:烟气进入吸收塔中后,与吸收液接触并反应。
氧化剂中的氧气与二氧化硫发生反应,形成硫酸。
这个过程是一个氧化反应。
5.硫酸的吸收:生成的硫酸溶液会与吸收液中的碱性成分反应,形成硫酸盐。
这个过程是一个吸收反应。
6.脱硫产物的处理:硫酸盐会沉淀下来,通过设备进行分离。
可以采用沉淀池和旋流器等设备将沉淀的硫酸盐分离出来。
7.循环利用吸收液:将分离出来的硫酸盐进行处理,使其恢复为吸收液,并循环利用。
8.烟气的释放:经过脱硫处理的烟气会在吸收塔顶部被释放到大气中。
根据国家规定的排放标准,烟气中的二氧化硫浓度必须控制在合理范围内。
这种湿法氧化吸收法具有以下优点:-高效:该技术可以高效地去除烟气中的二氧化硫,降低环境污染。
-可靠:该技术成熟且运行稳定,具有良好的稳定性和可靠性。
-灵活:可以根据烟气中二氧化硫的浓度和其他因素进行调节和优化,以实现最佳效果。
-环保:该技术可以使烟气中的二氧化硫大幅降低,减少污染物排放对环境的影响。
尽管该技术具有一些优点,但仍有一些挑战和限制。
例如,技术的投资成本较高,需要占用一定的场地,并对废水和废渣进行处理和处置。
此外,硫酸盐的回收和处理也需要专门的设备和操作。
太钢炼铁厂烧结烟气脱硫脱硝技术

5、入口氮氧化物
吸附塔入口 NOX ppm 200.0 150.0 100.0 50.0 0.0 0 500 1000 1500 2000 2500 3000 3500 4000
入口氮氧化物浓度平均102mg/Nm3。
21
6、出口氮氧化物
吸附塔出口 NOX ppm 80.0 60.0 40.0 20.0 0.0 0 500 1000 1500 2000 2500 3000 3500 4000
脱硝效率平均:39.9%,
24
9、保证性能与实测值如下表所示
各性能指标为投运4个月后(2011年1月)经市环保局检测的结果。所有项 目均超过保证性能。 另外,生产的硫酸达到了工业硫酸一等品质,在太钢轧钢系统进行了有效 利用。
保证项目
SO2(脱硫)
保证值 mg/m3N-dry
% mg/m3N-dry %
三烧 硫酸产量(T)
2)、硫酸产量
从2010年9月到2012年6月产酸13001吨,平均每月590吨。
27
3)、液氨用量
300 250 200 150 100 50 0 三烧 液氨用量(T)
20 10 年 20 11 10 月 年 20 12月 11 年 20 1月 11 年 20 2月 11 年 20 3月 11 年 20 4月 11 年 20 5月 11 年 20 6月 11 年 20 7月 11 年 20 8月 11 20 年9 11 月 年 20 10 11 月 年 20 11 11 月 年 20 12月 12 年 20 1月 12 年 20 2月 12 年 20 3月 12 年 20 4月 12 年 20 5月 12 年 6月
太钢炼铁厂烧结烟气脱硫脱硝
技术及应用
烧结烟气脱硫脱硝处理技术的比较分析
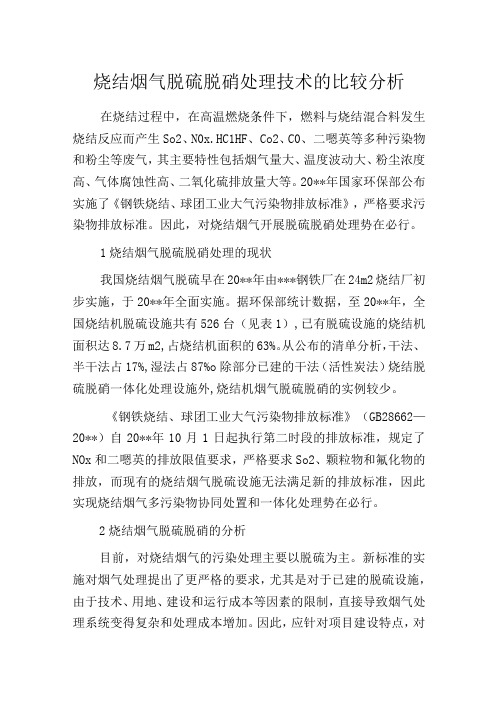
烧结烟气脱硫脱硝处理技术的比较分析在烧结过程中,在高温燃烧条件下,燃料与烧结混合料发生烧结反应而产生So2、N0x.HC1HF、Co2、C0、二嗯英等多种污染物和粉尘等废气,其主要特性包括烟气量大、温度波动大、粉尘浓度高、气体腐蚀性高、二氧化硫排放量大等。
20**年国家环保部公布实施了《钢铁烧结、球团工业大气污染物排放标准》,严格要求污染物排放标准。
因此,对烧结烟气开展脱硫脱硝处理势在必行。
1烧结烟气脱硫脱硝处理的现状我国烧结烟气脱硫早在20**年由***钢铁厂在24m2烧结厂初步实施,于20**年全面实施。
据环保部统计数据,至20**年,全国烧结机脱硫设施共有526台(见表1),已有脱硫设施的烧结机面积达8.7万m2,占烧结机面积的63%。
从公布的清单分析,干法、半干法占17%,湿法占87%o除部分已建的干法(活性炭法)烧结脱硫脱硝一体化处理设施外,烧结机烟气脱硫脱硝的实例较少。
《钢铁烧结、球团工业大气污染物排放标准》(GB28662—20**)自20**年10月1日起执行第二时段的排放标准,规定了NOx和二嗯英的排放限值要求,严格要求So2、颗粒物和氟化物的排放,而现有的烧结烟气脱硫设施无法满足新的排放标准,因此实现烧结烟气多污染物协同处置和一体化处理势在必行。
2烧结烟气脱硫脱硝的分析目前,对烧结烟气的污染处理主要以脱硫为主。
新标准的实施对烟气处理提出了更严格的要求,尤其是对于已建的脱硫设施,由于技术、用地、建设和运行成本等因素的限制,直接导致烟气处理系统变得复杂和处理成本增加。
因此,应针对项目建设特点,对新建烧结机、已建成的脱硫设施区别对待,综合考虑一种一体化的处理技术。
由于现有的烧结烟气脱硫工艺主要集中于传统的干法、半干法、湿法,因此分别选取干法、半干法、湿法脱硫脱硝一体化等技术开展分析比照。
2.1活性炭烟气净化技术20世纪50年代德国开始研发活性炭吸附工艺,20世纪60年代日本也开始研发。
双碱脱硫工艺流程

双碱脱硫工艺流程一、引言。
随着工业化进程的加快,大气污染问题日益严重,其中二氧化硫是造成酸雨的主要污染源之一。
因此,对二氧化硫进行有效的脱除成为环保工作的重要任务之一。
双碱脱硫工艺是目前比较成熟的脱硫技术之一,其工艺流程简单,效果显著,被广泛应用于电力、冶金、化工等行业。
本文将对双碱脱硫工艺流程进行详细介绍。
二、双碱脱硫工艺原理。
双碱脱硫工艺是利用氢氧化钙和氢氧化钠共同脱除烟气中的二氧化硫。
其原理主要包括以下几个方面:1. 氢氧化钙(Ca(OH)2)与二氧化硫(SO2)发生化学反应生成硫化钙(CaSO3)和水(H2O)。
2. 氢氧化钠(NaOH)与二氧化硫(SO2)发生化学反应生成硫代硫酸钠(Na2S2O3)和水(H2O)。
通过上述两个反应,可以将烟气中的二氧化硫有效地转化为硫化物和硫代硫酸盐,从而实现脱硫的目的。
三、双碱脱硫工艺流程。
双碱脱硫工艺流程主要包括石灰石破碎、石灰石浆液制备、石灰石浆液喷射、氧化钠溶液制备、氧化钠溶液喷射、吸收塔、脱硫液处理等环节。
1. 石灰石破碎,将石灰石破碎成适当的颗粒大小,以便后续制备石灰石浆液。
2. 石灰石浆液制备,将破碎后的石灰石与水混合搅拌,制备成石灰石浆液。
3. 石灰石浆液喷射,将制备好的石灰石浆液喷射到吸收塔中,与烟气进行接触反应。
4. 氧化钠溶液制备,制备氢氧化钠溶液,以备后续喷射到吸收塔中。
5. 氧化钠溶液喷射,将制备好的氢氧化钠溶液喷射到吸收塔中,与烟气中的二氧化硫进行反应。
6. 吸收塔,烟气在吸收塔中与石灰石浆液和氢氧化钠溶液接触,二氧化硫被有效地吸收和转化。
7. 脱硫液处理,对吸收后的脱硫液进行处理,将其中的硫化物和硫代硫酸盐沉淀出来,使脱硫液得以再生循环使用,同时产生的废渣进行处理。
四、双碱脱硫工艺优缺点。
双碱脱硫工艺相比其他脱硫工艺具有以下优点:1. 脱硫效果好,双碱脱硫工艺可以将烟气中的二氧化硫脱除率达到90%以上。
2. 适用范围广,双碱脱硫工艺适用于高硫煤和低硫煤的脱硫处理。
- 1、下载文档前请自行甄别文档内容的完整性,平台不提供额外的编辑、内容补充、找答案等附加服务。
- 2、"仅部分预览"的文档,不可在线预览部分如存在完整性等问题,可反馈申请退款(可完整预览的文档不适用该条件!)。
- 3、如文档侵犯您的权益,请联系客服反馈,我们会尽快为您处理(人工客服工作时间:9:00-18:30)。
烧结烟气中二氧化硫的脱除技术摘要:烧结烟气脱硫是钢铁行业污染减排的重点,减排形势日趋严峻。
而烧结工序是二氧化硫的主要排放源,因此也是烟气脱硫技术研发的主要领域。
本文主要介绍了石灰-石膏法、循环流化床法、密相干塔法三种脱硫技术原理及优缺点,并论述了烧结烟气脱硫技术的选定原则与发展方向。
关键字:烧结烟气,二氧化硫,脱硫Abstract:Sintering gas desulfurization is emphasized in iron and steel industry.SO2 emission reduction was serious. The main origin of the sulfur dioxide was sinter process, so it is the main research field of flue gas desulfurization technology.This paper mainly introduces the process principles, advantage and disadvantage of some sintering gas desulphurization technologies such as limestone/lime-plaster, CFB, dense flow absorber.And the select principle and development trend of sintering flue gas desulphurization technology are demonstrated.Key words:sintering flue gas,sulfur dioxide,desulfurization1 引言众所周知钢铁企业作为国家的支柱性产业,为国家建设做出了突出的贡献。
但同时其产生的污染也是不可忽视的,钢铁行业在其生产和加工过程中消耗大量的燃料和矿石,同时排放出大量的空气污染物。
统计表明我国钢铁行业SO2排放量仅次于电力行业居第2位。
钢铁生产包括焦化、烧结、炼铁和轧钢等工艺过程,其中烧结工序是钢铁生产中SO2减排的重点工序。
烧结过程排放的SO2占钢铁工业年排放量的60%以上[1]。
因此,烧结烟气脱硫已成为SO2污染控制的重点。
目前国家已经从排放总量与排放浓度两个方面对烧结烟气SO2排放进行了控制,标准非常严格,无论是现有企业还是新建企业都应建设烟气脱硫装置,才能达到SO2排放国家标准。
由于烧结烟气具有自身的特殊性,烧结烟气脱硫技术发展缓慢。
目前世界上烧结烟气脱硫应用的主要技术有石灰石-石膏法、硫酸铵法、旋转喷雾干法、循环流化床半干法等[2]。
我国在这方面已投入运行的烧结烟气脱硫装置采用的主要工艺有石灰-石膏法、密相干塔法、循环流化床法半干法、ENS半干法等。
但投入运行中还存在诸多问题需要进一步研究改善。
2 烧结烟气的来源及特点2.1 烧结烟气的来源以攀钢烧结原料来代表说明,攀钢炼铁厂烧结机烧结混合料由29种原料组成,其中铁精矿5种、富矿9种、熔剂6种、燃料3种、辅料4种,其它铁料2种[3]。
其组分见表2.1表2.1烧结混合料组成及原料含硫量名称占烧结混合料质量百分(%)含硫量(%)精矿粉58.9 0.67石灰石粉9.0 0.038澳矿 4.8 0.11外购白灰 4.5 —焦炭粉 4.3 0.51高加粉 4.3 0.51无烟煤粉 2.8 0.52钢渣粉 2.2 0.27中加粉 1.6 0.082 由表2.1中可以看出钢铁企业烧结烟气中SO2主要来源于含硫量较高的铁精矿,其他原料如焦炭粉、高加粉也对烟气中SO2的产生有一定贡献。
除了表中的来源燃料中硫的氧化反应也会产生不少的SO2。
除了铁矿石和固体燃料中硫含量的影响,烧结过程中SO2的产生还受铁矿石粒度和品位、烧结矿碱度和添加物性质、燃料及返矿的用量的影响。
可见从源头控制使用含硫量低的铁矿石和燃料能有效的减少SO2的产生,但是由于受到资源、成本等多种条件的限制。
就目前原料短缺的现状来看,此法难以全面推广应用。
2.2 烧结烟气的特点①产生的烟气量大:每生产1 t烧结矿大约产生4000~6000 m3烟气。
②不稳定性:由于烧结工况波动烟气量、烟气温度、SO2浓度等经常发生变化阵发性强。
③烟气温度较高:随烧结工况变化烟气温度一般在120~180℃。
④含湿量大。
为了提高烧结料层的透气性混合料在烧结前加水制粒,因此,致使烟气中含湿量较大,按体积比计算水分含量一般在10%左右。
⑤烟气粉尘浓度高:粉尘主要以铁及其化合物为主,由于使用不同的原料还可能含有微量重金属元素。
⑥含有害气体:烟气中含有一定量的SOx、NOx、HCl和HF等,它们遇水后将形成酸雨腐蚀金属构件。
此外,还含有对人体健康危害极大的二噁英和呋喃等[4]。
⑦含SO2浓度相对较低:随原料硫负荷等因素的变化而变化国企业一般在1000~3000 mg/m3。
3 烧结烟气的脱硫方法上面已经分析从源头上控制SO2的排放很难推广,事实上从烧结过程中控制减少SO2的产生也不大容易进行。
因为在原料、燃料结构一定的前提下,硫的脱除和烟气中SO2的生成主要受烧结温度、烧结时间、空气中氧浓度、焦粉粒度等因素的影响。
但通过控制烧结过程减少SO2排放的方法应同时考虑过程控制不影响烧结矿质量,减少的SO2排放以硫的化合物形式进入高炉,减排SO2要不影响高炉顺行和不增加高炉生产成本等因素。
所以过程中控制减少SO2现实也很难实施[5]。
那么最好的方法也就是末端治理即过程后脱硫了,下面介绍几种比较可行的主流的脱硫方法。
3.1 石灰-石膏法石灰石-石膏法是一种典型的湿法脱硫技术,在20世纪70年代就已成为一种应用较广的烟气脱硫工艺,约占已建成投产的烟气脱硫装置的84%。
其原理是利用冷却塔对烧结烟气进行冷却增湿,然后进入吸收塔与石灰浆液进行脱硫反应,同时将吸收塔中的浆液鼓入空气,氧化后的浆液再经浓缩、脱水生成纯度90%以上的石膏[6]。
石灰石-石膏法烟气脱硫的过程包括以下两步:首先,气液传质和水合过程。
即烟气中SO2分子与水接触时溶解在水中并与水分子水合为亚硫酸;其次,H2SO3与溶解在水中的碱性脱硫剂作用。
该工艺采用的脱硫剂是石灰,其主要成分是氧化钙。
石灰-石膏法烟气脱硫系统采用5%~10%的浆液脱硫以保证烟气脱硫效率。
主要反应过程如下:CaCO3+SO2+1/2H2O→CaSO3·1/2H2O+CO2Ca(OH)2+SO2→CaSO3·1/2H2O+1/2H2OCaSO3·1/2H2O+1/2O2+3/2H2O→CaSO4·2H2O烧结烟气经烟道进入烟气换热器,与从吸收塔排出的低温烟气换热降温后进入吸收塔,经过均流孔板上行,与多层雾化喷淋下来的洗涤液进行充分混合,SO2被吸收液洗涤吸收。
含有细液滴水气的烟气经过水幕式喷淋洗涤液时,烟气中的细小液滴被较大液滴吸收分离,再经过上部多层脱水除雾装置进一步除雾后经管道排出吸收塔外,进入烟气换热器,与进口高温烟气换热升温后经引风机进入烟囱高空排放。
洗涤液吸收烟气中的SO2后落入吸收塔下部的氧化池,SO2与石灰反应生成亚硫酸钙,被均布在池底的氧化装置送入的空气进一步氧化成稳定的硫酸钙。
石灰-石膏法脱硫效率高,在Ca/S比小于1.1的时候,脱硫效率可高达90%以上;吸收剂利用率高,可达到90%;吸收剂资源广泛,价格低廉;适用于高硫燃料,尤其适用于大容量烧结烟气处理;副产品为石膏,高品位石膏可用于建筑材料。
但该工艺的缺点是:系统复杂,占地面积大;造价高,一次性投资大;运行问题较多副产品CaSO4易沉积和粘结,所以,容易造成系统积垢,堵塞和磨损;运行费用高,高液气比所带来的电、水循环和耗量非常大。
3.2 循环流化床法循环流化床法是在循环流化床反应器,以钙基物质或其它碱性物质作为吸收剂和循环床料脱除二氧化硫的方法。
其将生石灰消化后引入脱硫塔,在流化状态下与通入的烟气进行脱硫反应。
烟气脱硫后进入布袋除尘器除尘,再由引风机经烟囱排出,布袋除尘器除下的物料大部分经吸收剂循环输送槽返回流化床循环使用。
由于循环流化使脱硫剂整体形成较大反应表面,脱硫剂与烟气中的SO2充分接触,脱硫效率较高[7]。
主要有以下化学反应:CaO+H2O→Ca(OH)2SO2+H2O→H2SO3Ca(OH)2+H2SO3→CaSO3·H2O+H2OCaSO·3H2O+O2+H2O→CaSO4·2H2O循环流化床法的脱硫剂是石灰,副产物是亚硫酸钙和硫酸钙的混合干粉。
优点是系统阻力低、水耗、电耗小、运行费用相对较低,吸收塔占地面积小,不需要考虑防腐,投资相对较小。
缺点是脱硫效率相对低于湿法脱硫工艺,脱硫副产物成分复杂,特别是脱硫灰中的亚硫酸钙含量过高不好利用,基本采用抛弃、堆存处理。
3.3 密相干塔法密相干塔法是利用干粉状的钙基脱硫剂,与布袋除尘器除下的大量循环灰一起进入加湿器进行增湿消化,使混合灰的水分体积分数保持在3%~5%之间,然后循环灰由密相塔上部进料口进入反应塔。
大量循环灰进入塔后,与由塔上部进入的含SO2烟气进行反应。
含水分的循环灰有极好的反应活性和流动性,另外塔设有搅拌器,不仅克服了粘壁问题而且增强了传质,使脱硫效率可达90%以上。
脱硫剂不断循环使用,有效利用率达98%以上。
最终脱硫产物由灰仓排出循环系统,通过气力输送装置送入存储仓[8]-[9]。
主要有以下化学反应:CaO+H2O→Ca(OH)2Ca(OH)2+SO2→CaSO3·H2O密相干塔法脱硫剂是石灰,副产物是亚硫酸钙和硫酸钙的混合干粉。
优点是系统阻力低,水耗、电耗小,运行费用相对较低,吸收塔占地面积小,不需要考虑防腐,投资相对较小。
缺点是脱硫效率相对低于湿法脱硫工艺,脱硫副产物成分复杂,脱硫剂在运行过程中可能不能完全与烟气进行反应,造成部分活性灰外排,对后部的除尘器要求较高[10]。
特别是脱硫灰中的亚硫酸钙含量过高不好利用,基本采用抛弃、堆存处理。
4 结论在众多脱硫方法如何做出最佳的选择,理想的烧结烟气脱硫技术是技术成熟可靠,投资省,脱硫剂来源广泛,副产品易于处理不产生二次污染,能回收高质量有广阔应用前景的脱硫副产品,运行成本低,占地面积小的符合循环经济理念要求的脱硫工艺。
符合高效化、资源化、综合化的要求,以达到烟气脱硫成本经济化的目的。
从有效性、经济性、安全性等方面综合评价烟气脱硫技术。
现有的各种脱硫方法各有优缺点。
石灰-石膏法脱硫是目前技术最成熟,运行状况最稳定的脱硫工艺。
而具有中国自主知识产权的密相干塔法,投资节省,脱硫效率高,运行成本低,副产物可利用,也是是一种较好的烧结烟气脱硫技术值得大力推广。