尺寸公差、形位公差、粗糙度数值关系
尺寸公差 形位公差关系
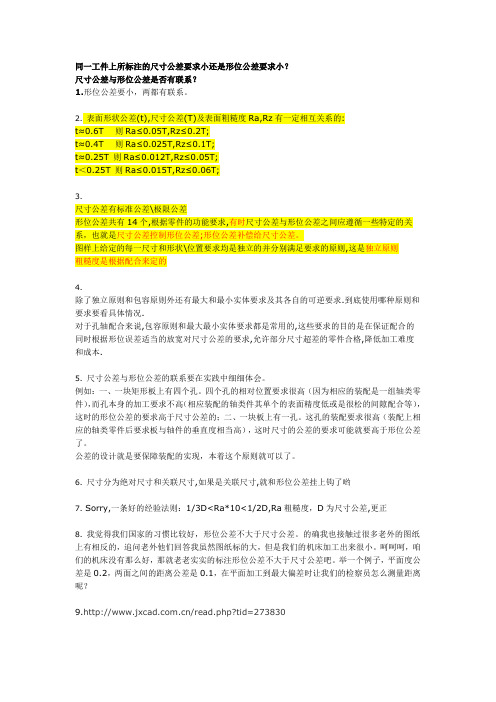
同一工件上所标注的尺寸公差要求小还是形位公差要求小?尺寸公差与形位公差是否有联系?1.形位公差要小,两都有联系。
2.表面形状公差(t),尺寸公差(T)及表面粗糙度Ra,Rz有一定相互关系的:t≈0.6T 则Ra≤0.05T,Rz≤0.2T;t≈0.4T 则Ra≤0.025T,Rz≤0.1T;t≈0.25T 则Ra≤0.012T,Rz≤0.05T;t<0.25T 则Ra≤0.015T,Rz≤0.06T;3.尺寸公差有标准公差\极限公差形位公差共有14个,根据零件的功能要求,有时尺寸公差与形位公差之间应遵循一些特定的关系,也就是尺寸公差控制形位公差;形位公差补偿给尺寸公差。
图样上给定的每一尺寸和形状\位置要求均是独立的并分别满足要求的原则,这是独立原则粗糙度是根据配合来定的4.除了独立原则和包容原则外还有最大和最小实体要求及其各自的可逆要求.到底使用哪种原则和要求要看具体情况.对于孔轴配合来说,包容原则和最大最小实体要求都是常用的,这些要求的目的是在保证配合的同时根据形位误差适当的放宽对尺寸公差的要求,允许部分尺寸超差的零件合格,降低加工难度和成本.5.尺寸公差与形位公差的联系要在实践中细细体会。
例如:一、一块矩形板上有四个孔。
四个孔的相对位置要求很高(因为相应的装配是一组轴类零件),而孔本身的加工要求不高(相应装配的轴类件其单个的表面精度低或是很松的间隙配合等),这时的形位公差的要求高于尺寸公差的;二、一块板上有一孔。
这孔的装配要求很高(装配上相应的轴类零件后要求板与轴件的垂直度相当高),这时尺寸的公差的要求可能就要高于形位公差了。
公差的设计就是要保障装配的实现,本着这个原则就可以了。
6.尺寸分为绝对尺寸和关联尺寸,如果是关联尺寸,就和形位公差挂上钩了哟7. Sorry,一条好的经验法则:1/3D<Ra*10<1/2D,Ra粗糙度,D为尺寸公差,更正8.我觉得我们国家的习惯比较好,形位公差不大于尺寸公差。
公差 形位公差与尺寸公差的关系

Dfe Dfe Dfe DM
+0.025
+
H7
0
-
h6Leabharlann φ40-0.016
最大实体边界
dfe dfe dfe dM
为保证配合性质,用最大实体尺寸控制体外作用尺寸 的公差原则——包容原则
第三章 形位公差与尺寸公差的关系
包容原则
含义—用最大实体边界控制被测要素的实际轮廓 应用—保证配合性质的场合 标注—无形位公差,尺寸公差后加 E
最大实体边界(MMB)
等于最大实体尺寸的边界
第三章 形位公差与尺寸公差的关系
最小实体状态(LMC)
处于极限尺寸 具有最小实体 ——材料最少
最小实体尺寸(LMS) ——保证材料最少极限尺寸
对孔: 最大极限尺寸 DL = Dmax 对轴: 最小极限尺寸 dL = dmin
dfe da da da
0.013
当零件与其他零件配合时,起作用 的尺寸不再是局部实际尺寸,而是 体外作用尺寸
第三章 形位公差与尺寸公差的关系
体外作用尺寸
被测要素的给定长度上,与实际内表面体外相接的最大理想面 或与实际外表面体外相接的最小理想面的直径或宽度
装配过程中起作用的尺寸 实际尺寸与形位误差综合作用的结果 存在于零件上,而不是图纸上
检测合格条件:
⎧⎨⎩dmifn形≤位d≤a
≤ dmax t形位
⎧ ⎨ ⎩
Dmin ≤ Da f形位 ≤
≤ Dmax t形位
0.02
检测方法:—两点法测量
小批量:卡尺、千分尺 大批量: 卡规、塞规
0 -0.033
20
第三章 形位公差与尺寸公差的关系
尺寸公差、形位公差、粗糙度数值关系

一、尺寸公差、形位公差、表面粗糙度数值上的关系1、形状公差与尺寸公差的数值关系当尺寸公差精度确定后,形状公差有一个适当的数值相对应,即一般约以50%尺寸公差值作为形状公差值;仪表行业约20%尺寸公差值作为形状公差值;重型行业约以70%尺寸公差值作为形状公差值。
由此可见.尺寸公差精度愈高,形状公差占尺寸公差比例愈小所以,在设计标注尺寸和形状公差要求时,除特殊情况外,当尺寸精度确定后,一般以50%尺寸公差值作为形状公差值,这既有利于制造也有利于确保质量。
2、形状公差与位置公差间的数值关系形状公差与位置公差间也存在着一定的关系。
从误差的形成原因看,形状误差是由机床振动、刀具振动、主轴跳动等原因造成;而位置误差则是由于机床导轨的不平行,工具装夹不平行或不垂直、夹紧力作用等原因造成,再从公差带定义看,位置误差是含被测表面的形状误差的,如平行度误差中就含有平面度误差,故位置误差比形状误差要大得多。
因此,在一般情况下、在无进一步要求时,给了位置公差,就不再给形状公差。
当有特殊要求时可同时标注形状和位置公差要求,但标注的形状公差值应小于所标注的位置公差值,否则,生产时无法按设计要求制造零件。
3、形状公差与表面粗糙度的关系形状误差与表面粗糙度之间在数值和测量上尽管没有直接联系,但在一定的加工条件下两者也存在着一定的比例关系,据实验研究,在一般精度时,表面粗糙度占形状公差的1/5~1/4。
由此可知,为确保形状公差,应适当限制相应的表面粗糙度高度参数的最大允许值。
在一般情况下,尺寸公差、形状公差、位置公差、表面粗糙度之间的公差值具有下述关系式:尺寸公差>位置公差>形状公差>表面粗糙度高度参数从尺寸、形位与表面粗糙度的数值关系式不难看出,设计时要协调处理好三者的数值关系,在图样上标注公差值时应遵循:给定同一表面的粗糙度数值应小于其形状公差值;而形状公差值应小于其位置公差值;位置各差值应小于其尺寸公差值。
尺寸公差、形位公差、表面粗糙度三者的关系
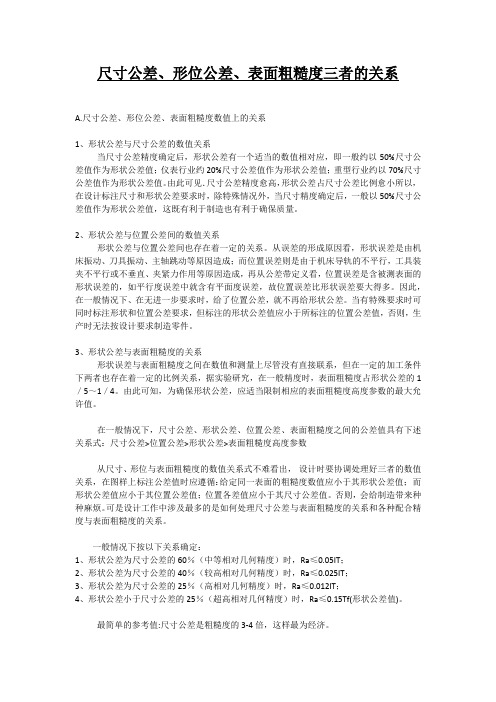
尺寸公差、形位公差、表面粗糙度三者的关系A.尺寸公差、形位公差、表面粗糙度数值上的关系1、形状公差与尺寸公差的数值关系当尺寸公差精度确定后,形状公差有一个适当的数值相对应,即一般约以50%尺寸公差值作为形状公差值;仪表行业约20%尺寸公差值作为形状公差值;重型行业约以70%尺寸公差值作为形状公差值。
由此可见.尺寸公差精度愈高,形状公差占尺寸公差比例愈小所以,在设计标注尺寸和形状公差要求时,除特殊情况外,当尺寸精度确定后,一般以50%尺寸公差值作为形状公差值,这既有利于制造也有利于确保质量。
2、形状公差与位置公差间的数值关系形状公差与位置公差间也存在着一定的关系。
从误差的形成原因看,形状误差是由机床振动、刀具振动、主轴跳动等原因造成;而位置误差则是由于机床导轨的不平行,工具装夹不平行或不垂直、夹紧力作用等原因造成,再从公差带定义看,位置误差是含被测表面的形状误差的,如平行度误差中就含有平面度误差,故位置误差比形状误差要大得多。
因此,在一般情况下、在无进一步要求时,给了位置公差,就不再给形状公差。
当有特殊要求时可同时标注形状和位置公差要求,但标注的形状公差值应小于所标注的位置公差值,否则,生产时无法按设计要求制造零件。
3、形状公差与表面粗糙度的关系形状误差与表面粗糙度之间在数值和测量上尽管没有直接联系,但在一定的加工条件下两者也存在着一定的比例关系,据实验研究,在一般精度时,表面粗糙度占形状公差的1/5~1/4。
由此可知,为确保形状公差,应适当限制相应的表面粗糙度高度参数的最大允许值。
在一般情况下,尺寸公差、形状公差、位置公差、表面粗糙度之间的公差值具有下述关系式:尺寸公差>位置公差>形状公差>表面粗糙度高度参数从尺寸、形位与表面粗糙度的数值关系式不难看出,设计时要协调处理好三者的数值关系,在图样上标注公差值时应遵循:给定同一表面的粗糙度数值应小于其形状公差值;而形状公差值应小于其位置公差值;位置各差值应小于其尺寸公差值。
形尺表面三者关系GG
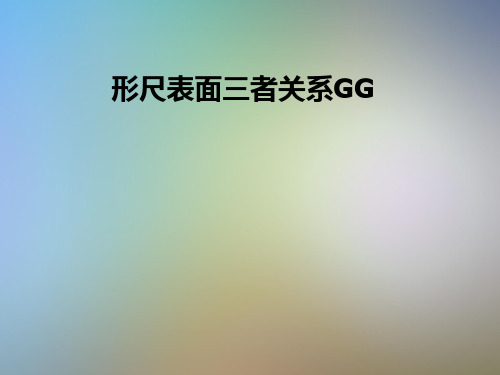
的包容要求。对最大实体要求和最小实体要求只作了概括性说 明。
GB/T 16671-1996对最大实体要求和最小实体要求(包括它们的 可逆要求)作了详细的规定,并对GB/T 4249-1996使用的术语 、定义作了规定。
3.公差原则类术语
(3)图样标注无“隐含”要求
泰勒原则使形状公差的允许值自然地”与尺寸公差相关联,而采用独立原则 时,设计人员必须另行确定形状公差。
泰勒原则是指遵守包容要求的单一要素,孔或轴的实际尺寸和形状误差综合形成的体外作用尺寸不 允许超越最大实体尺寸,在孔或轴的任何位置上的实际尺寸不允许超越最小实体尺寸。简单地讲, 泰勒原则就是有配合要求的孔、轴,其局部实际尺寸与形状误差都要控制在尺寸公差带以内。
从图控制实际尺寸就能控制该零件的 形状和位置误差9一2(b)中1图看出: ,也可以说形状和位置误差完全反映 到了实际尺寸中。
2)形位误差不影响实际尺寸 形位误差中的大多数情况都与尺寸无关,如零件平表面的平面
度、直线度、轴线的直线度,圆形零件的奇数棱误差,轴线的同 轴度,对称中心面的对称度等。
图9-3为圆形零件在正截面内,轮廓 产生三棱形的误差(由无心磨磨削造成)。 此时,两对应点之间距离可以处处相等, 在实际直径的测量中却反映不出实际存 在的圆形误差f。
在实际生产中,由于功能的要求,形位公差与尺寸公差需要存 在不同的相互关系,即尺寸控制形位误差,尺寸允许补偿给形位 误差,从而形成双向补偿。此时,控制零件要素的是一个控制边 界。这种尺寸公差与形位公差有一定关系的要求称为“相关要求” 。
相关要求按尺寸与形位两者之间的关系分为包容要求、最大 实体要求、最小实体要求和可逆要求。这些相关要求必须在图样 上明确标注。
尺寸公差形位公差、表面粗糙度数值上的关系
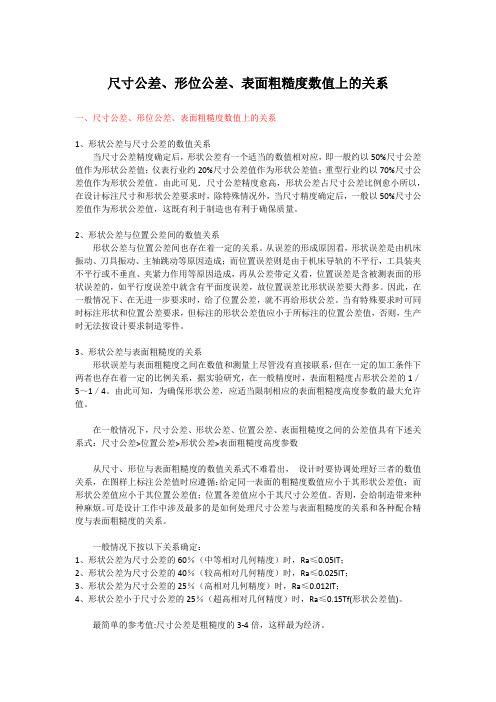
尺寸公差、形位公差、表面粗糙度数值上的关系一、尺寸公差、形位公差、表面粗糙度数值上的关系1、形状公差与尺寸公差的数值关系当尺寸公差精度确定后,形状公差有一个适当的数值相对应,即一般约以50%尺寸公差值作为形状公差值;仪表行业约20%尺寸公差值作为形状公差值;重型行业约以70%尺寸公差值作为形状公差值。
由此可见.尺寸公差精度愈高,形状公差占尺寸公差比例愈小所以,在设计标注尺寸和形状公差要求时,除特殊情况外,当尺寸精度确定后,一般以50%尺寸公差值作为形状公差值,这既有利于制造也有利于确保质量。
2、形状公差与位置公差间的数值关系形状公差与位置公差间也存在着一定的关系。
从误差的形成原因看,形状误差是由机床振动、刀具振动、主轴跳动等原因造成;而位置误差则是由于机床导轨的不平行,工具装夹不平行或不垂直、夹紧力作用等原因造成,再从公差带定义看,位置误差是含被测表面的形状误差的,如平行度误差中就含有平面度误差,故位置误差比形状误差要大得多。
因此,在一般情况下、在无进一步要求时,给了位置公差,就不再给形状公差。
当有特殊要求时可同时标注形状和位置公差要求,但标注的形状公差值应小于所标注的位置公差值,否则,生产时无法按设计要求制造零件。
3、形状公差与表面粗糙度的关系形状误差与表面粗糙度之间在数值和测量上尽管没有直接联系,但在一定的加工条件下两者也存在着一定的比例关系,据实验研究,在一般精度时,表面粗糙度占形状公差的1/5~1/4。
由此可知,为确保形状公差,应适当限制相应的表面粗糙度高度参数的最大允许值。
在一般情况下,尺寸公差、形状公差、位置公差、表面粗糙度之间的公差值具有下述关系式:尺寸公差>位置公差>形状公差>表面粗糙度高度参数从尺寸、形位与表面粗糙度的数值关系式不难看出,设计时要协调处理好三者的数值关系,在图样上标注公差值时应遵循:给定同一表面的粗糙度数值应小于其形状公差值;而形状公差值应小于其位置公差值;位置各差值应小于其尺寸公差值。
形位公差与尺寸公差的关系

形位公差与尺寸公差的关系一、基本概念公差原则的定义定义:处理尺寸公差和形位公差关系的规定。
分类:1、体外作用尺寸单一要素的作用尺寸简称作用尺寸MS。
是实际尺寸和形状误差的综合结果。
在被测要素的给定长度上,与实际内表面(孔)体外相接的最大理想面,或与实际外表面(轴)体外相接的最小理想面的直径或宽度,称为体外作用尺寸,即通常所称作用尺寸。
图例局部实际尺寸和单一要素的体外作用尺寸2、关联要素的体外作用尺寸是局部实际尺寸与位置误差综合的结果。
是指结合面全长上,与实际孔内接(或与实际轴外接)的最大(或最小)的理想轴(或孔)的尺寸。
而该理想轴(或孔)必须与基准要素保持图样上给定的功能关系。
图例关联体外作用尺寸3、体内作用尺寸在被测要素的给定长度上,与实际内表面(孔)体内相接的最小理想面,或与实际外表面(轴)体内相接的最大理想面的直径或宽度,称为体内作用尺寸。
4、最大实体状态(尺寸、边界)最大实体状态(MMC):实际要素在给定长度上具有最大实体时的状态。
最大实体尺寸(MMS):实际要素在最大实体状态下的极限尺寸。
(轴的最大极限尺寸dmax,孔的最小极限尺寸Dmin)边界:由设计给定的具有理想形状的极限包容面。
最大实体边界:尺寸为最大实体尺寸的边界。
5、最大实体实效状态(尺寸、边界)MMVC:在给定长度上,实际要素处于最大实体状态且其中心要素的形状或位置误差等于给出的形位公差值时的综合极限状态。
MMVS:最大实体实效状态下的体外作用尺寸。
MMVS=MMS±t形·位其中:对外表面取“+”;对内表面取“-”dMV =dfe=da+f =dM + t =dmax + tDMV=Dfe=Da-f =DM–t =Dmin- t最大实体实效边界:尺寸为最大实体实效尺寸的边界。
最大实体实效尺寸(单一要素)最大实体实效尺寸(关联要素)6、最小实体实效状态(尺寸、边界)LMVC:在给定长度上,实际要素处于最小实体状态且其中心要素的形状或位置误差等于给出的形位公差值时的综合极限状态,称为最小实体实效状态。
形位公差与尺寸公差的关系
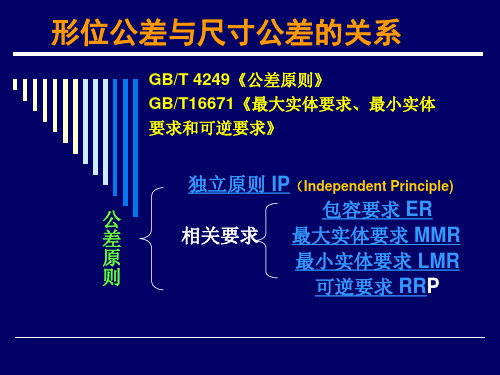
轴类零件形位公差项目的选择
➢ 与支承件结合部位
a、轴颈的圆度或圆柱度。 b、对公共轴线的圆跳动或同
轴度。 c、轴肩对轴线的端面圆跳动
(或垂直度)。
➢与传动件结合部位
a、表面的圆度或圆柱度 b、对公共轴线的圆跳动或同 轴度 c、轴肩对其轴线的垂直度( 或端面圆跳动) d、键槽对其轴线的对称度。
➢形位公差各项目的应用示例:见表2-9~表2-12 ➢形位公差值的选用原则
1、总的原则是在满足零件功能的前提下,选取最经济的公差 值。
形位公差值的确定
2、根据零件的功能要求,考虑加工的经济性和零件的结构、 刚性,按表中数系确定要素的公差值。并考虑以下因素: a)在同一要素上给出的t形状≤t位置。如要求平行的两个表面, 其平面度公差值应小于平行度公差值;
轴类零件形位公差值的确定
齿轮形位公差值的确定
箱体类零件形位公差值的确定
形位公差的未注公差值(GB/T 1184-1996)
为简化制图,对一般机床加工就能保证的形位精度,不必 在图样上注出形位公差,形位未注公差按以下规定执行:
➢ 未注直线度、平面度、垂直度、对称度和圆跳动(表213~表2-16)各规定了H、K、L三个公差等级,在标题栏 或技术要求中注出标准及等级代号。如:“GB/T1184—
➢其它
齿轮类零件形位公差项目的选择
GB10095-1988《齿轮公差》有专门规定:
➢齿轮孔(或轴)的圆度 或圆柱度
➢齿轮键槽对其轴线的对 称度
➢齿轮基准端面对轴线的 垂直度 ➢齿顶圆对轴线的圆跳动
箱体类零件形位公差项目的选择
轴承座孔的圆度或 圆柱度
轴承座孔轴线的同 轴度
尺寸精度与粗糙度

表面粗糙度的测量方法
• 1、比较法:将被测表面与粗糙度标准样块进行比较, 用目测或抚摸、指甲划动等感触判断表面粗糙度的大 小。 • 2、测量仪器:比较显微镜、双管显微镜、干涉显微镜 和轮廓仪等。
6.3 12.5
25
25
25
50 (▽)
50 100
100
计算标准为 4Ra = Ry = Rz
表面粗糙度对零件质量的影响 • • • • 对耐磨性的影响 对疲劳强度的影响 对腐蚀性的影响 对配合性质的影响
•
设计零件时,要根据具体条件选择适当的 表面粗糙度,取值越小,加工越困难成本越高。
表面粗糙度的选用原则
零件的表面质量
零件表面上微小峰谷的高低程度和间距状况, 称为表面粗糙度,也称为微观不平度。 • 基本的表面粗糙度符号: • 切削加工获得的表面: • 用不去除方法获得的表面:
• 表面粗糙度的评定参数 • 1)轮廓算术平均偏差Ra:在取样长度内轮廓偏距绝对值的算术平均值; • 2)微观不平度十点高度Rz:在取样长度内5个最大的轮廓峰高的平均值与5 个 最大的轮廓谷深的平均值之和; • 3)轮廓最大高度Ry:在取样长度内轮廓峰顶线和轮廓谷底线之间的距离。
位置精度 • 指零件的点线面要素 的实际位置相对于理想 位置的准确程度。用位 置公差来控制。国标中 规定了八项位置公差: 平行度、垂直度、倾斜 度、同轴度、对称度、 位置度、圆跳动和全跳 动。
尺寸公差、形位公差、表面粗糙度数值上的关系
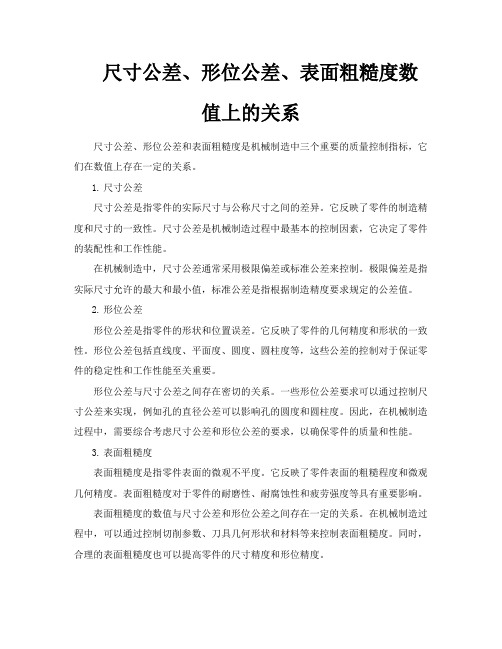
尺寸公差、形位公差、表面粗糙度数值上的关系尺寸公差、形位公差和表面粗糙度是机械制造中三个重要的质量控制指标,它们在数值上存在一定的关系。
1.尺寸公差尺寸公差是指零件的实际尺寸与公称尺寸之间的差异。
它反映了零件的制造精度和尺寸的一致性。
尺寸公差是机械制造过程中最基本的控制因素,它决定了零件的装配性和工作性能。
在机械制造中,尺寸公差通常采用极限偏差或标准公差来控制。
极限偏差是指实际尺寸允许的最大和最小值,标准公差是指根据制造精度要求规定的公差值。
2.形位公差形位公差是指零件的形状和位置误差。
它反映了零件的几何精度和形状的一致性。
形位公差包括直线度、平面度、圆度、圆柱度等,这些公差的控制对于保证零件的稳定性和工作性能至关重要。
形位公差与尺寸公差之间存在密切的关系。
一些形位公差要求可以通过控制尺寸公差来实现,例如孔的直径公差可以影响孔的圆度和圆柱度。
因此,在机械制造过程中,需要综合考虑尺寸公差和形位公差的要求,以确保零件的质量和性能。
3.表面粗糙度表面粗糙度是指零件表面的微观不平度。
它反映了零件表面的粗糙程度和微观几何精度。
表面粗糙度对于零件的耐磨性、耐腐蚀性和疲劳强度等具有重要影响。
表面粗糙度的数值与尺寸公差和形位公差之间存在一定的关系。
在机械制造过程中,可以通过控制切削参数、刀具几何形状和材料等来控制表面粗糙度。
同时,合理的表面粗糙度也可以提高零件的尺寸精度和形位精度。
综上所述,尺寸公差、形位公差和表面粗糙度之间存在密切的关系。
在机械制造过程中,需要综合考虑这些因素,制定合理的制造工艺和质量控制方案,以确保零件的质量和性能。
同时,对于不同的应用场合和工作条件,需要根据实际情况选择合适的控制方法和要求,以达到最佳的经济效益和技术效果。
尺寸公差与表面粗糙度

05 总结与展望
总结
尺寸公差与表面粗糙度是机械加工中的重要参数,它 们对产品的性能和可靠性有着显著的影响。
随着科技的不断发展,对尺寸公差与表面粗糙度的要 求也越来越高,这需要我们不断探索新的加工方法和
测量技术,以提高产品的质量和性能。
在实际应用中,应综合考虑尺寸公差与表面粗糙度的 关系,以及它们对产品性能的影响,以制定合理的加
工和测量方案。
展望
随着数字化和智能化技术的不断发展,未来的机械加工将更加依赖于先进的测量技术和数据分析方法。
新的加工方法和材料将对尺寸公差与表面粗糙度提出更高的要求,需要我们不断探索和创新,以适应新 的市场需求。
在未来,尺寸公差与表面粗糙度的研究将更加注重跨学科的合作和交流,以推动相关领域的发展和进步。
测量精度
测量精度对结果的影响很大,因此需要选择精度 合适的测量工具和正确的测量方法,以获得准确 的测量结果。
03 尺寸公差与表面粗糙度的 控制方法
加工工艺控制
加工方法选择
根据零件材料、结构、精度要求等选择合适的加工方 法,如车削、铣削、磨削等。
加工余量分配
合理分配各工序的加工余量,确保最终加工尺寸的精 度。
02
表面粗糙度越高,摩擦系数越大,磨损速度越快,从而影响零
件的耐磨性。
表面粗糙度对零件疲劳强度的影响
03
表面粗糙度越高,应力集中越严重,疲劳裂纹容易形成和扩展,
降低零件的疲劳强度。
尺寸公差对表面粗糙度的影响
尺寸公差越小,表面粗糙度越低
在加工过程中,尺寸公差越小,切削深度、进给量等工艺参数越小,从而减小 表面粗糙度。
热处理工艺
控制零件的热处理工艺,以减小变形和组织不均匀性 对尺寸精度的影响。
尺寸公差,形状公差与表面粗糙度的关系
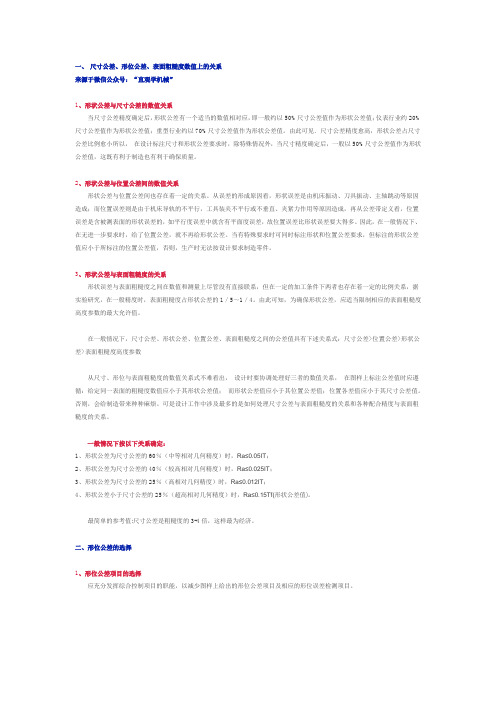
一、尺寸公差、形位公差、表面粗糙度数值上的关系来源于微信公众号:“直观学机械”1、形状公差与尺寸公差的数值关系当尺寸公差精度确定后,形状公差有一个适当的数值相对应,即一般约以50%尺寸公差值作为形状公差值;仪表行业约20%尺寸公差值作为形状公差值;重型行业约以70%尺寸公差值作为形状公差值。
由此可见.尺寸公差精度愈高,形状公差占尺寸公差比例愈小所以,在设计标注尺寸和形状公差要求时,除特殊情况外,当尺寸精度确定后,一般以50%尺寸公差值作为形状公差值,这既有利于制造也有利于确保质量。
2、形状公差与位置公差间的数值关系形状公差与位置公差间也存在着一定的关系。
从误差的形成原因看,形状误差是由机床振动、刀具振动、主轴跳动等原因造成;而位置误差则是由于机床导轨的不平行,工具装夹不平行或不垂直、夹紧力作用等原因造成,再从公差带定义看,位置误差是含被测表面的形状误差的,如平行度误差中就含有平面度误差,故位置误差比形状误差要大得多。
因此,在一般情况下、在无进一步要求时,给了位置公差,就不再给形状公差。
当有特殊要求时可同时标注形状和位置公差要求,但标注的形状公差值应小于所标注的位置公差值,否则,生产时无法按设计要求制造零件。
3、形状公差与表面粗糙度的关系形状误差与表面粗糙度之间在数值和测量上尽管没有直接联系,但在一定的加工条件下两者也存在着一定的比例关系,据实验研究,在一般精度时,表面粗糙度占形状公差的1/5~1/4。
由此可知,为确保形状公差,应适当限制相应的表面粗糙度高度参数的最大允许值。
在一般情况下,尺寸公差、形状公差、位置公差、表面粗糙度之间的公差值具有下述关系式:尺寸公差>位置公差>形状公差>表面粗糙度高度参数从尺寸、形位与表面粗糙度的数值关系式不难看出,设计时要协调处理好三者的数值关系,在图样上标注公差值时应遵循:给定同一表面的粗糙度数值应小于其形状公差值;而形状公差值应小于其位置公差值;位置各差值应小于其尺寸公差值。
尺寸公差、形位公差、表面粗糙度的区别和联系及选择方法
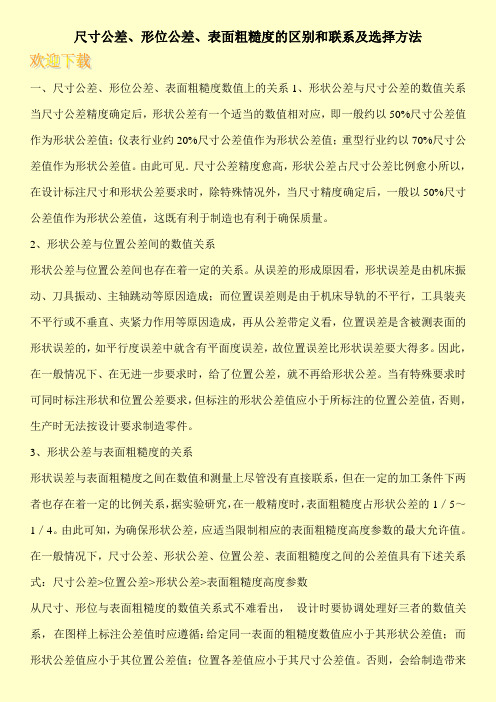
尺寸公差、形位公差、表面粗糙度的区别和联系及选择方法一、尺寸公差、形位公差、表面粗糙度数值上的关系1、形状公差与尺寸公差的数值关系当尺寸公差精度确定后,形状公差有一个适当的数值相对应,即一般约以50%尺寸公差值作为形状公差值;仪表行业约20%尺寸公差值作为形状公差值;重型行业约以70%尺寸公差值作为形状公差值。
由此可见.尺寸公差精度愈高,形状公差占尺寸公差比例愈小所以,在设计标注尺寸和形状公差要求时,除特殊情况外,当尺寸精度确定后,一般以50%尺寸公差值作为形状公差值,这既有利于制造也有利于确保质量。
2、形状公差与位置公差间的数值关系形状公差与位置公差间也存在着一定的关系。
从误差的形成原因看,形状误差是由机床振动、刀具振动、主轴跳动等原因造成;而位置误差则是由于机床导轨的不平行,工具装夹不平行或不垂直、夹紧力作用等原因造成,再从公差带定义看,位置误差是含被测表面的形状误差的,如平行度误差中就含有平面度误差,故位置误差比形状误差要大得多。
因此,在一般情况下、在无进一步要求时,给了位置公差,就不再给形状公差。
当有特殊要求时可同时标注形状和位置公差要求,但标注的形状公差值应小于所标注的位置公差值,否则,生产时无法按设计要求制造零件。
3、形状公差与表面粗糙度的关系形状误差与表面粗糙度之间在数值和测量上尽管没有直接联系,但在一定的加工条件下两者也存在着一定的比例关系,据实验研究,在一般精度时,表面粗糙度占形状公差的1/5~1/4。
由此可知,为确保形状公差,应适当限制相应的表面粗糙度高度参数的最大允许值。
在一般情况下,尺寸公差、形状公差、位置公差、表面粗糙度之间的公差值具有下述关系式:尺寸公差>位置公差>形状公差>表面粗糙度高度参数从尺寸、形位与表面粗糙度的数值关系式不难看出,设计时要协调处理好三者的数值关系,在图样上标注公差值时应遵循:给定同一表面的粗糙度数值应小于其形状公差值;而形状公差值应小于其位置公差值;位置各差值应小于其尺寸公差值。
形位公差、尺寸公差以及表面粗糙度三者之间关系

形位公差、尺寸公差以及表面粗糙度三 者之间关系
要合理标注各项公差值, 首先就要了解和充 分考虑各项公差值的相互关系。
检验时,轴的实际圆柱轮廓都通过按最大实 体实效边界尺寸Ф20.01mm制成的位置量规。 且用两点法测量局部实际尺寸在最大与最大 小实体尺寸内,则可判为合格。
从公差带动态图可见,随着实际尺寸偏离最 大实体状态Ф20mm而减小时,其允许的直 线度误差f值允许相应增大,但最大增加量不 超过尺寸公差,从而实现了尺寸公差向形位 公差的转化。
形位公差、尺寸公差以及表面粗糙度三 者之间关系
当直线度误差为零时,其实际尺寸可以达到 最大值,即等于其最大实体实效边界尺寸 Ф20.1mm,从而实现了形位公差转化为尺 寸公差的可逆要求。图c为上述关系的公差 带动态图。
检验时,轴的实际轮廓通过按最大实体实效 边界尺寸Ф20.1mm设计的综合位置量规; 同时用两点法测得实际尺寸大于其最小实体 尺寸19.7mm时,则该零件判为合格。
一、形位公差的分类 形状公差——直线度、平面度、圆度、圆柱度 形状或位置公差——线轮廓度、面轮廓度 定向位置公差——平行度、垂直度、倾斜度 定位位置公差——同轴度、对称度、位置度 跳动——径向、斜向、端面圆跳动,径向、端
面全跳动
形位公差、尺寸公差以及表面粗糙度三 者之间关系
二、尺寸公差和形位公差关系的公差原则 公差原则就是对尺寸公差与形位公差相互可否
形位公差、尺寸公差以及表面粗糙度三 者之间关系
(2)可逆要求用于最大实体要求 可逆要求用于最大实体要求时,被测要素的
形位公差值的选择或确定
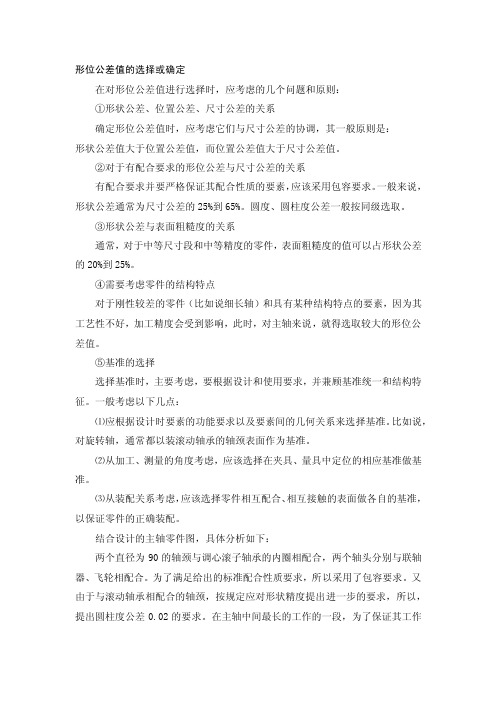
形位公差值的选择或确定在对形位公差值进行选择时,应考虑的几个问题和原则:①形状公差、位置公差、尺寸公差的关系确定形位公差值时,应考虑它们与尺寸公差的协调,其一般原则是:形状公差值大于位置公差值,而位置公差值大于尺寸公差值。
②对于有配合要求的形位公差与尺寸公差的关系有配合要求并要严格保证其配合性质的要素,应该采用包容要求。
一般来说,形状公差通常为尺寸公差的25%到65%。
圆度、圆柱度公差一般按同级选取。
③形状公差与表面粗糙度的关系通常,对于中等尺寸段和中等精度的零件,表面粗糙度的值可以占形状公差的20%到25%。
④需要考虑零件的结构特点对于刚性较差的零件(比如说细长轴)和具有某种结构特点的要素,因为其工艺性不好,加工精度会受到影响,此时,对主轴来说,就得选取较大的形位公差值。
⑤基准的选择选择基准时,主要考虑,要根据设计和使用要求,并兼顾基准统一和结构特征。
一般考虑以下几点:⑴应根据设计时要素的功能要求以及要素间的几何关系来选择基准。
比如说,对旋转轴,通常都以装滚动轴承的轴颈表面作为基准。
⑵从加工、测量的角度考虑,应该选择在夹具、量具中定位的相应基准做基准。
⑶从装配关系考虑,应该选择零件相互配合、相互接触的表面做各自的基准,以保证零件的正确装配。
结合设计的主轴零件图,具体分析如下:两个直径为90的轴颈与调心滚子轴承的内圈相配合,两个轴头分别与联轴器、飞轮相配合。
为了满足给出的标准配合性质要求,所以采用了包容要求。
又由于与滚动轴承相配合的轴颈,按规定应对形状精度提出进一步的要求,所以,提出圆柱度公差0.02的要求。
在主轴中间最长的工作的一段,为了保证其工作的准确性,对该段轴颈相对与两个直径为90的轴颈公共基准轴线给出了径向圆跳动公差0.025毫米。
尺寸公差和形位公差相互关系遵循的基本原则是

尺寸公差和形位公差相互关系遵循的基本原则一、引言尺寸公差和形位公差是机械工程中非常重要的概念,它们在零件制造和装配过程中起着关键的作用。
尺寸公差用于确定零件尺寸的允许范围,形位公差则用于描述零件之间的相对位置关系。
本文将深入探讨尺寸公差和形位公差之间的相互关系,并阐述它们遵循的基本原则。
二、尺寸公差的基本原则尺寸公差是指零件所允许的尺寸范围,它反映了零件尺寸的精度要求。
尺寸公差的基本原则如下:1. 公差选择原则在确定尺寸公差时,应根据零件的功能需求、制造工艺和经济因素等综合考虑,选择合适的公差等级。
一般来说,零部件的功能越关键,公差等级应该越高。
2. 逐级公差原则在整个产品的设计过程中,应采用逐级公差的原则。
即将公差分配到各个特征面或特征尺寸上,确保各个零件之间的相对位置关系和功能要求的实现。
3. 公差配合原则在配合设计中,应根据零件之间的相对运动形式及其所处的工作条件,选择合适的配合公差。
例如,对于需要灵活运动的配合,公差应较大;对于需要高精度的配合,公差应较小。
4. 公差传递原则在零件装配过程中,尺寸公差会通过零件之间的相对位置传递。
因此,在设计过程中应充分考虑公差传递的影响,避免公差堆积导致装配不良。
三、形位公差的基本原则形位公差是指零件之间的相对位置关系的精度要求,它反映了零件的几何要求。
形位公差的基本原则如下:1. 统一基准原则在确定形位公差时,应选择合适的基准面或基准轴线作为参考,通过基准的统一来确定零件之间的相对位置。
2. 逐级公差原则与尺寸公差类似,形位公差也应按照逐级公差的原则进行分配。
通过形位公差的逐级分配,确保产品在各个层次上的形位要求得以实现。
3. 相对优先原则在多个形位公差共同作用于一个特征时,应根据设计要求和制造工艺的可行性,确定各个形位公差的优先次序。
一般来说,越高级的形位公差优先级越高。
4. 形位公差的传递原则形位公差也会在零件装配过程中传递,因此在设计中要充分考虑形位公差的传递规律,避免传递过程中的误差积累,影响产品的装配质量和性能。
形位公差与尺寸公差的关系
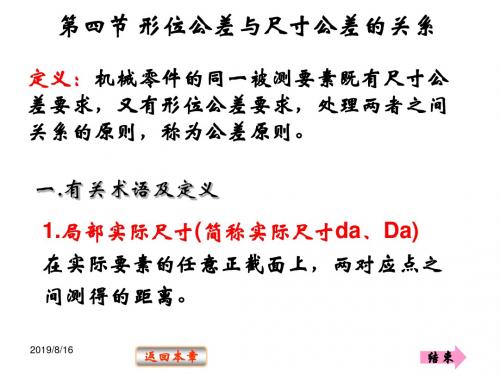
19.97(d-L0).03 -0.02-0.010 20(dM) 20.05(dMV)
da/mm
4)实际尺寸必须在最大实体尺寸和最小实体尺寸之间
变化。
2019/8/16
Hale Waihona Puke 返回本章结束3.合格条件:
Da f D fe DMV Dmin t 孔:
Dmin DM Da DL Dmax
(1) 最小实体实效状态(LMVB) 在给定长度上, 实际要素处于最小实体状态且其中心要素 的形状或位置误差等于给出的形位公差值 时的综合极限状态。
(2) 最小实体实效尺寸(dLV、DLV) 最小实体实
效状态下的体内作用尺寸。
dLV =dL – t =dmin-t
DLV=DL + t =Dmax+t
dL dmin es d DL Dmax ES D
2019/8/16
返回本章
结束
2019/8/16
返回本章
结束
3. 最大实体实效状态、尺寸
(1) 最大实体实效状态(MMVC) 在给定长度上,实际要 素处于最大实体状态且其中心要素的形状或位置误差 等于给出的形位公差值时的综合极限状态。
a) 外表面(轴)
返回本章
b) 内表面(孔)
实际尺寸和作用尺寸
结束
(2) 体内作用尺寸(dfi、Dfi )
在被测要素的给定长度上,与实际外表面体内 相接的最大理想面或与实际内表面体内相接的 最小理想面的直径或宽度。对于关联要素,该 理想面的轴线或中心平面必须保持图样给定的 几何关系。
作用尺寸是由实际尺寸和形位误差综合形成的, 对于每个零件不尽相同。
da f d fe d MV dmax t 轴:
- 1、下载文档前请自行甄别文档内容的完整性,平台不提供额外的编辑、内容补充、找答案等附加服务。
- 2、"仅部分预览"的文档,不可在线预览部分如存在完整性等问题,可反馈申请退款(可完整预览的文档不适用该条件!)。
- 3、如文档侵犯您的权益,请联系客服反馈,我们会尽快为您处理(人工客服工作时间:9:00-18:30)。
一、尺寸公差、形位公差、表面粗糙度数值上的关系
1、形状公差与尺寸公差的数值关系
当尺寸公差精度确定后,形状公差有一个适当的数值相对应,即一般约以50%尺寸公差值作为形状公差值;仪表行业约20%尺寸公差值作为形状公差值;重型行业约以70%尺寸公差值作为形状公差值。
由此可见.尺寸公差精度愈高,形状公差占尺寸公差比例愈小所以,在设计标注尺寸和形状公差要求时,除特殊情况外,当尺寸精度确定后,一般以50%尺寸公差值作为形状公差值,这既有利于制造也有利于确保质量。
2、形状公差与位置公差间的数值关系
形状公差与位置公差间也存在着一定的关系。
从误差的形成原因看,形状误差是由机床振动、刀具振动、主轴跳动等原因造成;而位置误差则是由于机床导轨的不平行,工具装夹不平行或不垂直、夹紧力作用等原因造成,再从公差带定义看,位置误差是含被测表面的形状误差的,如平行度误差中就含有平面度误差,故位置误差比形状误差要大得多。
因此,在一般情况下、在无进一步要求时,给了位置公差,就不再给形状公差。
当有特殊要求时可同时标注形状和位置公差要求,但标注的形状公差值应小于所标注的位置公差值,否则,生产时无法按设计要求制造零件。
3、形状公差与表面粗糙度的关系
形状误差与表面粗糙度之间在数值和测量上尽管没有直接联系,但在一定的加工条件下两者也存在着一定的比例关系,据实验研究,在一般精度时,表面粗糙度占形状公差的1/5~1/4。
由此可知,为确保形状公差,应适当限制相应的表面粗糙度高度参数的最大允许值。
在一般情况下,尺寸公差、形状公差、位置公差、表面粗糙度之间的公差值具有下述关系式:尺寸公差>位置公差>形状公差>表面粗糙度高度参数
从尺寸、形位与表面粗糙度的数值关系式不难看出,设计时要协调处理好三者的数值关系,在图样上标注公差值时应遵循:给定同一表面的粗糙度数值应小于其形状公差值;而形状公差值应小于其位置公差值;位置各差值应小于其尺寸公差值。
否则,会给制造带来种种麻烦。
可是设计工作中涉及最多的是如何处理尺寸公差与表面粗糙度的关系和各种配合精度与表面粗糙度的关系。
一般情况下按以下关系确定:
1、形状公差为尺寸公差的60%(中等相对几何精度)时,Ra≤0.05IT;
2、形状公差为尺寸公差的40%(较高相对几何精度)时,Ra≤0.025IT;
3、形状公差为尺寸公差的25%(高相对几何精度)时,Ra≤0.012IT;
4、形状公差小于尺寸公差的25%(超高相对几何精度)时,Ra≤0.15Tf(形状
公差值)。
最简单的参考值:尺寸公差是粗糙度的3-4倍,这样最为经济。
二、形位公差的选择
1、形位公差项目的选择
应充分发挥综合控制项目的职能,以减少图样上给出的形位公差项目及相应的形位误差检测项目。
在满足功能要求的前提下,应选用测量简便的项目。
如:同轴度公差常常用径向圆跳动公差或径向圆跳动公差代替。
不过应注意,径向圆跳动是同轴度误差与圆柱面形状误差的综合,故代替时,给出的跳动公差值应略大于同轴度公差值,否则就会要求过严。
2、公差原则的选择
应根据被测要素的功能要求,充分发挥公差的职能和采取该公差原则的可行性、经济性。
独立原则用于尺寸精度与形位精度精度要求相差较大,需分别满足要求,或两者无联系,保证运动精度、密封性,未注公差等场合。
包容要求主要用于需要严格保证配合性质的场合。
最大实体要求用于中心要素,一般用于配件要求为可装配性(无配合性质要求)的场合。
最小实体要求主要用于需要保证零件强度和最小壁厚等场合。
可逆要求与最大(最小)实体要求联用,能充分利用公差带,扩大了被测要素实际尺寸的范围,提高了效益。
在不影响使用性能的前提下可以选用。
3、基准要素的选择
3.1 基准部位的选择
选用零件在机器中定位的结合面作为基准部位。
例如箱体的底平面和侧面、盘类零件的轴线、回转零件的支承轴颈或支承孔等。
基准要素应具有足够的大小和刚度,以保证定位稳定可靠。
例如,用两条或两条以上相距较远的轴线组合成公共基准轴线比一条基准轴线要稳定。
选用加工比较精确的表面作为基准部位。
尽量使装配、加工和检测基准统一。
这样,既可以消除因基准不统一而产生的误差;也可以简化夹具、量具的设计与制造,测量方便。
3.2 基准数量的确定
一般来说,应根据公差项目的定向、定位几何功能要求来确定基准的数量。
定向公差大多只要一个基准,而定位公差则需要一个或多个基准。
例如,对于平行度、垂直度、同轴度公差项目,一般只用一个平面或一条轴线做基准要素;对于位置
度公差项目,需要确定孔系的位置精度,就可能要用到两个或三个基准要素。
3.3 基准顺序的安排
当选用两个以上基准要素时,就要明确基准要素的次序,并按第一、第二、第三的顺序写在公差框格中,第一基准要素是主要的,第二基准要素次之。
4、形位公差值的选择
总的原则:在满足零件功能的前提下,选取最经济的公差值。
根据零件的功能要求,考虑加工的经济性和零件的结构、刚性,按表确定要素的公差值。
并考虑以下因素:
同一要素给出的形状公差应小于位置公差值;
圆柱形零件的形状公差值(轴线的直线度除外)应小于其尺寸公差值;如同一平面上,平面度公差值应小于该平面对基准的平行度公差值。
平行度公差值应小于其相应的距离公差值。
表面粗糙度与形状公差的大概的比例关系:通常,表面粗糙度的Ra值可取为形状公差值的(20%~25%)。
对于以下情况,考虑到加工的难易程度和除主参数以外的其它因素的影响,在满足零件功能的要求下,适当降低1~2级选用:
孔相对于轴;
细长比较大的轴和孔;距离较大的轴和孔;
宽度较大(大于1/2长度)的零件表面;
线对线和线对面的相对于面对面的平行度、垂直度公差。
5、形位未注公差的规定
为简化制图,对一般机床加工就能保证的形位精度,不必在图样上注出形位公差,形位未注公差按GB/T1184-1996的规定执行。
大致内容如下:
对未注直线度、平面度、垂直度、对称度和圆跳动各规定了H、K、L三个公差等级.
未注圆度公差值等于直径公差值,但不能大于径向圆跳动的未注公差值。
未注圆柱度公差值不作规定,由要素的圆度公差、素线直线度和相对素线平行度的注出或未注公差控制。
未注平行度公差值等于被测要素和基准要素间的尺寸公差和被测要素的形状公差(直线度或平面度)的未注公差值中的较大者,并取两要素中较长者作为基准。
未注同轴度公差值未作规定。
必要时,可取同轴度的未注公差值等于圆跳动的未注公差。
未注线轮廓度、面轮廓度、倾斜度、位置度的公差值均由各要素的注出或未注线性尺寸公差或角度公差控制。
未注全跳动公差值未作规定。
6、形位未注公差值的图样表示
若采用GB/T1184-1996规定的未注公差值,应在标题栏或技术要求中注出标准及等级代号。
“GB/T1184—K”。
图样上未标注“公差原则按GB/T 4249”的工作公差,应按“GB/T1800.2-1998”的要求执行。