高炉生产的理想烧结料
烧结及高炉炼铁基本原理及工艺课件

03
烧结及高炉炼铁的能耗 与环保
能耗分析
烧结过程的能耗
烧结过程是钢铁生产中能耗最高的环节之一,其主要能耗来自于点火燃料、电力消耗和工艺用水。其中,点火燃 料是烧结过程最主要的能源,占整个烧结过程能耗的60%以上。
高炉炼铁的能耗
高炉炼铁的能耗主要包括煤炭、电力、焦炭和氧气等,其中煤炭和焦炭是最主要的能耗来源。在炼铁过程中,需 要将这些能源转化为化学能以还原铁矿石中的铁元素。
环保措施与减排技术
烧结过程的环保措施
在烧结过程中,采取一系列环保措施以减少环境污染,例如使用低硫燃料、安装除尘设备、进行烟气 脱硫等。此外,还可以通过提高烧结矿的质量和利用率来减少废渣的产生。
碳捕获和储存技术
利用该技术可以有效地减少高炉炼铁过程中的碳排放,提高环保 水平。
氢还原技术
利用氢气作为还原剂,替代焦炭,以减少碳排放和环境污染。
自动化和智能化设备
应用先进的自动化和智能化设备,可以提高生产效率、降低劳动成 本,并确保产品质量。
05
烧结及高炉炼铁生产过 程中的问题与解决方案
烧结生产过程中的问题与解决方案
高炉炼铁的环保措施
高炉炼铁过程中产生的废气和废水对环境造成的影响较大。为了减少环境污染,需要采取一系列环保 措施,例如使用高效除尘设备、进行废气脱硫、废水处理等。此外,还可以通过提高炼铁效率来减少 废渣的产生。
可持续发展的方向和前景
烧结及高炉炼铁的可持续 发展方向
为了实现烧结及高炉炼铁的可持续发展,需 要从能源消耗和环境保护两个方面入手。一 方面,需要研发和推广低能耗技术和设备, 提高能源利用效率;另一方面,需要加强环 保措施和技术的研究和应用,减少环境污染 和排放。
高炉炼铁技术简介
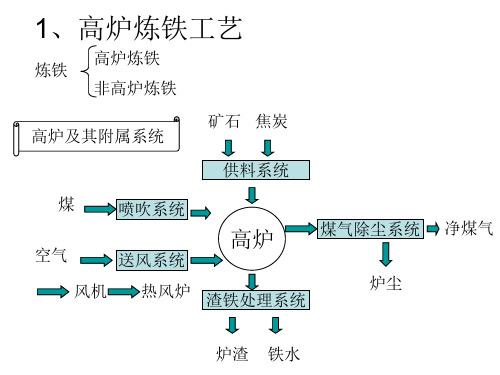
烧结 工艺 流程
精矿、粉矿 (0~10mm)
石灰石、白云石 (80~0mm)
碎焦、无烟煤 (25~0mm)
破碎
>3mm
• 炉渣中氧化物的种类:碱性氧化物、酸性氧化物 和中性氧化物。以碱性氧化物为主的炉渣称碱性 炉渣;以酸性氧化物为主的炉渣称酸性炉渣。
• 炉渣的碱度(R):炉渣中碱性氧化物和酸性氧化 物的质量百分数之比表示炉渣碱度:
• 高炉炉渣碱度一般表示式:R=w(CaO)/w (SiO2)
• 炉渣的碱度根据高炉原料和冶炼产品的不同,一 般在1.0~1.25之间。
消耗的(干)焦炭量(焦比一定的情况 下)
高炉每天消耗的焦炭量 I=
高炉的有效容积
• 生铁合格率:生铁化学成分符合国家标准的总量 占生铁总量的指标。
• 休风率:高炉休风时间(不包括计划大、中、小 修)占日历工作时间的百分数。
规定的日历作业时间=日历时间-计划大中修及
封炉时间
休风率=
高炉休风时间 规定的日历作业时间 ×100%
高炉炉渣与脱硫
• 高炉炉渣是铁矿石中的脉石和焦炭(燃料)中 的灰分等与熔剂相互作用生成低熔点的化 合物,形成非金属的液相。
– 高炉炉渣的成分 – 高炉炉渣作用 – 成渣过程 – 生铁去硫
• 高炉炉渣的来源:矿石中的脉石、焦炭(燃料)中 的灰分、熔剂中的氧化物、被侵蚀的炉衬等。
• 高炉炉渣的成分:氧化物为主,且含量最多的是 SiO2、CaO、Al2O3、MgO。
② 物理性能 包括机械强度和粒度组成等。高炉要求烧结矿机械 强度高,粉末少,粒度均匀。 烧结矿粒度小于5mm的称之为粉末。粉末含量对高 炉料柱透气性影响很大。粉末含量高,高炉透气性差, 导致炉况不顺,可能引起崩料或悬料。 反应机械强度的指标为:转鼓指数、抗磨指数、筛 分指数。 目前武钢烧结矿的转鼓强度大约在79%~80%左右。
高炉配吃落地烧结矿的实际操作

高炉配吃落地烧结矿的实际操作摘要:我国钢铁工业得到了前所未有的发展,而钢材是现代建筑工程最主要的结构材料和工程材料,其质量直接关系到工程的结构质量和安全。
烧结矿是高炉炼铁的主要原料之一,其质量直接影响到钢铁的质量。
烧结原料、烧结性能不同,烧结矿中矿物的组成和结构也不同,而烧结矿的组成和结构是影响其质量的最主要因素。
因此,研究烧结矿的组成和结构对其质量的影响具有非常重要的现实意义。
关键词:高炉;配吃落地烧结矿;实际操作1 前言邯钢西区1号高炉炉容3200m3,设有32个风口,4个出铁场,于2008年4月18日点火开炉。
主要工艺如下:(1)设置独立的矿槽和焦槽,并列式布置;烧结矿分级入炉,采用焦丁回收入炉技术;(2)采用PW型并罐无钟炉顶;(3)冷却系统采用软水密闭循环,实现全软水冷却;(4)采用INBA渣处理装置;(5)采用改进型高温内燃式热风炉;(6)TRT炉顶余压回收装置。
邯钢西区1号高炉是邯钢首个开炉的大型高炉,投产初期各项经济技术指标与国内同类型高炉有很大的差距。
09年10月后,1号高炉去除中心焦,采用平台+漏斗布料模式。
历经近一年时间,摸索出适应自身炉况的操作制度,炉缸工作状态逐渐改善,各方面技术指标不断进步。
尤其在进入2012年以后,通过实施加强入炉原燃料管理、优化高炉操作制度、稳定高炉操作炉型、强化炉前生产管理、降低高炉休慢风率、四班统一稳定操作等有效措施,实现了高炉长期稳定生产,燃料比长期保持在500kg/t以下。
2 高炉配吃落地烧结矿的原料烧结矿作为高炉炼铁的主要原料,直接影响着高炉冶炼过程的经济技术指标,除要求其具有较高的品位外,还需对其中脉石成分进行分析。
现在广泛为各实验室采用的方法为以碳酸钠熔融法进行SiO2-CaO-MgO-Al2O3的系统分析,由于贵金属铂坩埚的使用,不仅提高了分析成本,同时对日常管理提出了更高的要求,完成上述系统分析约需2小时左右。
近年来发展起来的X荧光分析技术,初步实现了烧结矿试样分析的仪器化,但因该方法所用设备昂贵,对标样的依赖性强等因素,不仅使分析成本大大提高,同时试样成分的差异性造成的制备条件限制,使其广泛应用受到一定的局限。
烧结原料介绍
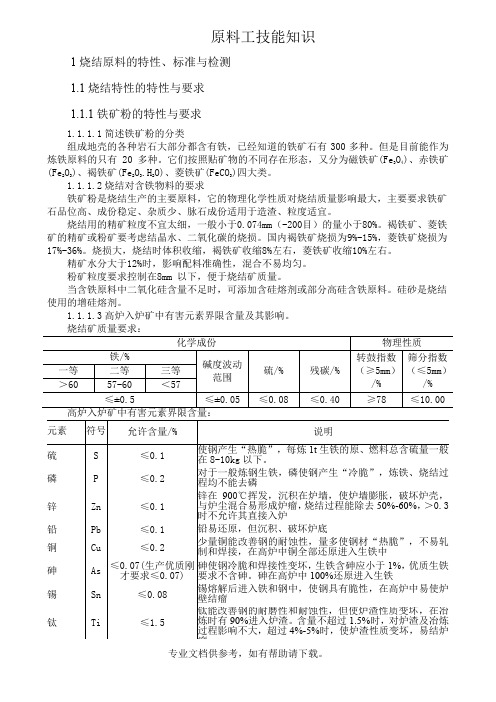
原料工技能知识1烧结原料的特性、标准与检测1.1烧结特性的特性与要求1.1.1铁矿粉的特性与要求1.1.1.1简述铁矿粉的分类组成地壳的各种岩石大部分都含有铁,已经知道的铁矿石有300多种。
但是目前能作为炼铁原料的只有20多种。
它们按照贴矿物的不同存在形态,又分为磁铁矿(Fe3O4)、赤铁矿(Fe2O3)、褐铁矿(Fe2O3.H2O)、菱铁矿(FeCO3)四大类。
1.1.1.2烧结对含铁物料的要求铁矿粉是烧结生产的主要原料,它的物理化学性质对烧结质量影响最大,主要要求铁矿石品位高、成份稳定、杂质少、脉石成份适用于造渣、粒度适宜。
烧结用的精矿粒度不宜太细,一般小于0.074mm(-200目)的量小于80%。
褐铁矿、菱铁矿的精矿或粉矿要考虑结晶水、二氧化碳的烧损。
国内褐铁矿烧损为9%-15%,菱铁矿烧损为17%-36%。
烧损大,烧结时体积收缩,褐铁矿收缩8%左右,菱铁矿收缩10%左右。
精矿水分大于12%时,影响配料准确性,混合不易均匀。
粉矿粒度要求控制在8mm 以下,便于烧结矿质量。
当含铁原料中二氧化硅含量不足时,可添加含硅熔剂或部分高硅含铁原料。
硅砂是烧结使用的增硅熔剂。
1.1.1.3高炉入炉矿中有害元素界限含量及其影响。
1.1.2熔剂的特性与要求1.1.2.1熔剂的分类熔剂可分为碱性熔剂、酸性熔剂和中性熔剂三类。
我国铁矿的脉石多以SiO2为主,所以普遍使用碱性熔剂。
碱性熔剂即含CaO和MgO高的熔剂。
常用的熔剂有:石灰石(CaCO3)生石灰(CaO)、消石灰(Ca(OH)2)和白云石(主要是CaCO3和MgCO3)。
1.1.2.2熔剂的要求碱性氧化物含量要高;S、P杂质要少;酸性氧化物含(SiO2+Al2O3) 越低越好;粒度和水分适宜。
①有效熔剂性高:即碱性氧化物CaO+MgO含量要高,而酸性氧化物SiO2含量要低。
评价熔剂品质的重要标准,是根据烧结矿碱度要求,扣除本身酸性氧化物所消耗的碱性氧化物成分,所剩余的碱性氧化物的含量而确定的。
烧结技术

烧结生产0概述全世界的矿石储量2500亿吨,富矿20%我国矿石储量500亿吨,富矿5%随着钢铁工业的发展,天然富矿从产量和质量上都不能满足高炉冶炼的要求。
而且精矿粉和富矿粉都不能直接入炉冶炼。
为了解决这一难题,将粉矿制成块状人造富矿。
方法:烧结法和球团法。
一、现代高炉对原料的要求1、节焦上(1)、铁矿石品位高,杂质少。
首钢经验:品位提高1%,焦比下降2%,产量提高3%。
产量提高,单位热损失减少,加入熔剂少,减少热量支出。
(2)、熟料比高。
不用或少加熔剂,减少热量支出,冶金性能好。
(3)碱度高。
可以不加石灰石,减少热量支出。
C a C O=CaO+CO2 吸热32、透气性(1)粒度均匀大小不均造成小块填到大块中间破块透气性上限40~50mm下限5~10mm。
(2)粉末少(3)强度高3、冶炼性能(1)还原性好有利于铁氧化物还原,有利于煤气利用的改善与焦比的下降(2)低温还原粉化率低粉化率高粉末多影响透气性(3)软熔性能软化温度高软化区间窄使成渣带下移变薄改善透气性二、人工富矿的方法1、烧结法烧结是将各种粉状含铁原料,配入一定数量的燃料和熔剂,混匀后,进行燃烧,进行一系列的物化反应,产生一定数量的液相,冷凝后粘结起来的块状产品叫做烧结矿,这个过程叫烧结。
2球团法球团矿:把润湿的铁精矿粉和少量的添加剂混合,再造球设备中滚动成9~16mm左右的圆球,在经过干燥,预热,焙烧、均热、冷却、发生一系列的物化反映,使生球固结,成为高炉需要的球团矿。
三、烧结矿在钢铁工业中的重要地位1、扩大矿石来源贫矿经过选矿、造块、烧结制成烧结矿,供高炉使用。
富矿粉经过造块后,供高炉使用。
2、可以改善高炉技术经济指标改善了原料的物理化学性能。
孔隙率高,反应面积增大,加速冶炼过程。
粒度均匀,透气性好。
机械强度高还原性好。
低温还原粉化率低,高温还原软化性好,提高冶炼效果。
3、能够充分利用冶金工业和化学工业的废品。
烧结可以利用高炉炉灰,轧钢皮,硫酸渣、转炉尘作为原料,合理利用资源,降低生产成本。
项目三 烧结配料
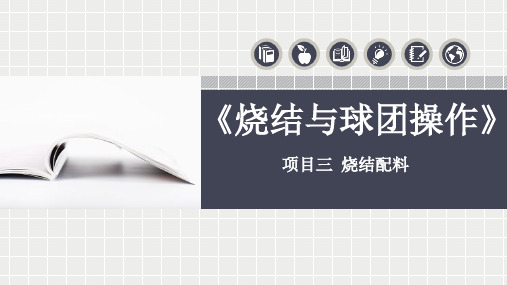
用熔剂、返矿粉等配料,但不适用水分含量较大的精矿粉;
1— 电 动 机 ;2— 减
直筒式套筒采用刮刀排料,堵料现象较蜗牛式套筒轻,但
速器;3—圆盘;4—
下料量波动大。故当精矿或粉矿用量较大时,宜用带活动
套筒;5—闸门
刮刀的套筒;当熔剂或燃料用量少,而且要求精确性高时,
宜用闸门式套筒。
相关知识
一、配料设备
设混合矿减重ax =0.084%×0.9+1.06%=1.14%;
石灰石减重a =42.25%;
炉尘减重a尘
=10.87%+0.102%×0.9=10.96%;
焦粉减重a焦 =80.9%+0.8%×0.9+2.17%=83.7%;
总减重a=Xax +Ya +8a尘 +8a焦 =0.0114X+0.4225Y+0.88+6.7=0.0114X+0.4225Y+7.58
偏大,因此,应根据干料量的变化来进行必要的调整。
4.同一品种原料下料量过大时,最好用两台给料机给料,可减少下料量的波动。
5.应十分注意下料量少的物料品种的下料量。由于影响下料量的因素较多,在人工操作
时要严格配料操作,班与班统一操作,要勤称量勤校正。铁料每15min校正一次,根据
具体情况规定各种下料量的波动范围。
掌握影响配料准确的因素,熟悉实际烧结矿成分与配料计算值发生偏差
的原因及调整措施。
任务
描述
配料操作是根据配料单准确配料,使用圆盘给料机给料,电子皮带秤称
量依次按配比加入混匀矿、返矿、熔剂、燃料等原料,通过皮带运输到烧结
混匀系统。配料必须按配料单准确配料,使配合料的化学成分合乎规定;配碳
炼铁生产基本问答
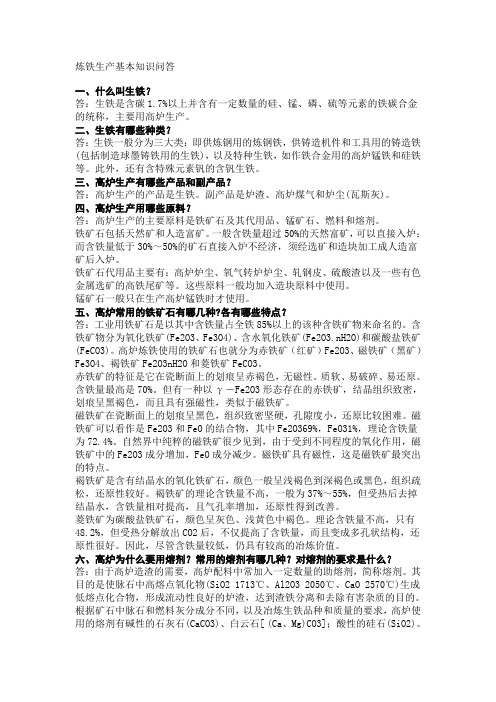
炼铁生产基本知识问答一、什么叫生铁?答:生铁是含碳1.7%以上并含有一定数量的硅、锰、磷、硫等元素的铁碳合金的统称,主要用高炉生产。
二、生铁有哪些种类?答:生铁一般分为三大类:即供炼钢用的炼钢铁,供铸造机件和工具用的铸造铁(包括制造球墨铸铁用的生铁),以及特种生铁,如作铁合金用的高炉锰铁和硅铁等。
此外,还有含特殊元素钒的含钒生铁。
三、高炉生产有哪些产品和副产品?答:高炉生产的产品是生铁。
副产品是炉渣、高炉煤气和炉尘(瓦斯灰)。
四、高炉生产用哪些原料?答:高炉生产的主要原料是铁矿石及其代用品、锰矿石、燃料和熔剂。
铁矿石包括天然矿和人造富矿。
一般含铁量超过50%的天然富矿,可以直接入炉;而含铁量低于30%~50%的矿石直接入炉不经济,须经选矿和造块加工成人造富矿后入炉。
铁矿石代用品主要有:高炉炉尘、氧气转炉炉尘、轧钢皮、硫酸渣以及一些有色金属选矿的高铁尾矿等。
这些原料一般均加入造块原料中使用。
锰矿石一般只在生产高炉锰铁时才使用。
五、高炉常用的铁矿石有哪几种?各有哪些特点?答:工业用铁矿石是以其中含铁量占全铁85%以上的该种含铁矿物来命名的。
含铁矿物分为氧化铁矿(Fe2O3、Fe3O4)、含水氧化铁矿(Fe2O3.nH2O)和碳酸盐铁矿(FeCO3)。
高炉炼铁使用的铁矿石也就分为赤铁矿(红矿)Fe2O3、磁铁矿(黑矿)Fe3O4、褐铁矿Fe2O3nH2O和菱铁矿FeCO3。
赤铁矿的特征是它在瓷断面上的划痕呈赤褐色,无磁性。
质软、易破碎、易还原。
含铁量最高是70%。
但有一种以γ-Fe2O3形态存在的赤铁矿,结晶组织致密,划痕呈黑褐色,而且具有强磁性,类似于磁铁矿。
磁铁矿在瓷断面上的划痕呈黑色,组织致密坚硬,孔隙度小,还原比较困难。
磁铁矿可以看作是Fe2O3和FeO的结合物,其中Fe2O369%,FeO31%,理论含铁量为72.4%。
自然界中纯粹的磁铁矿很少见到,由于受到不同程度的氧化作用,磁铁矿中的Fe2O3成分增加,FeO成分减少。
高炉冶炼用原料
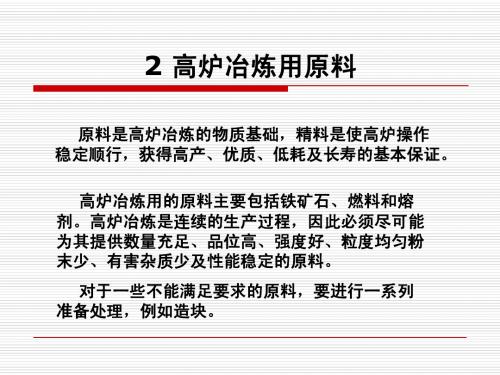
2.2.1 铁矿粉烧结
4、烧结生产工艺
1)烧结配料 采用重量法配料,根据配料计算。
2)混匀与制粒 一混的主要作用是混匀;二混的主要作用是造球制粒。 影响混匀和制粒的因素: (1)原料性质:粘性大,比重相差小,粒度差别小有利于混 匀和造球。 (2)水分含量和加水方法:适量、雾状有利于混匀和造球。 (3)工艺因素:倾角、转速、填充率,混匀时间长有利于混 匀和造球。
S、P低;常温强度高;
高炉中70%S来自于焦碳。焦碳中S:0.5-1.5%,主要以S化物、硫 酸盐的形式存在。没有有机硫。
高温强度高;稳定性好。
2.1 高炉冶炼用原料
2.1.5 煤粉
(1)喷吹煤粉的作用:发热、还原 (2)质量要求: ①灰分低,C高; ②S、P低,K、Na低;发热值高;可磨性好;燃 烧性和反应性好;安全性高
2.2.2 球团矿生产
3、造球设备
圆盘造球机、圆筒机 4、工艺操作: 加水加料原则:滴水成球,雾水长大,无水压紧。 造球时间: 3至10分钟 设备指标:圆盘造球机的转速和倾角(倾角45至50度),圆 盘边高和填充率适宜,底料和刮板要适宜。 物料温度:预热混合料,50℃为宜。
2.2.2 球团矿生产
2 .2 铁矿粉造块
一、定义:铁矿粉造块是将不能直接入炉的金属矿
粉经配料后用人工方法造成符合冶炼要求的矿块。 二、意义:扩大了冶炼原料的来源,同时又改善了原 料的质量。 三、目的:将粉料制成具有高温强度的块状料;改善铁矿 石的冶金性能,使高炉冶炼指标得到改善;去除某些有害 杂质,回收有益元素,达到综合利用资源和扩大铁矿石原 料资源。
提供C用于直接还原金属氧化物,尤其是FeO的还原提供相应数量 的CO,用于间接还原
作为铁的增碳剂,焦碳中的晶型碳及石墨溶解在液态铁中起增碳作 用 保证高炉料体的透气性和透液性。使炉料在高炉内自上而下自如运 动
烧结矿质量对高炉冶炼的影响 精品

吉林电子信息职业技术学院毕业论文烧结矿质量对高炉冶炼的影响摘要烧结矿是高炉炼铁生产的主要原料之一,烧结矿的性能和质量直接影响高炉冶炼的顺行、操作制度和技术经济指标。
本论文通过对烧结矿的还原,滴落实验,验证不同粒度的半焦、无烟煤代替焦粉作燃料的铁矿烧结技术的比较优势。
以及改变其粒度等方面对烧结进行分析、研究。
本项研究内容包括:原、燃料的物理化学性质、燃料的性能及反应性、烧结矿质量指标的评价;在不同原料配比条件下改变燃料粒度的烧结实验;烧结矿的物理化学性能和冶金性能等检测;对燃料种类和配比对烧结矿生产指标、烧结矿化学成分、矿物组成、还原性能、还原粉化性能、软熔滴落性能的影响进行评价,实验结果及其分析。
实验结果证明:半焦在>5mm粒级控制在15%的粒度下是很好的烧结燃料。
无烟煤相对做烧结燃料效果不好;<3mm粒级控制在70%左右为宜。
关键词:烧结矿,无烟煤,焦粉,半焦,矿物组成,烧结矿冶金性能,改变粒度I吉林电子信息职业技术学院毕业论文目录第一章绪论·············································································································· - 6 -1.1烧结生产的目的·············································································································- 6 -1.2烧结用原料条件·············································································································- 7 -1.3燃料的粒度 ······················································································································- 7 -1.4燃料的基本性质·············································································································- 8 -1.4.1燃料的工业分析、元素分析 ......................................................................... - 8 -1.4.2燃料的灰成分和灰熔点·······························································································- 10 -第二章烧结的作用·································································································- 11 -2.1烧结矿的作用 ···············································································································- 11 -2.2烧结机的作用 ···············································································································- 12 -2.3烧结矿中MgO 作用机理 ····························································································- 12 -第三章烧结生成工艺及生产的工艺流程·························································- 13 -3.1烧结生成工艺 ···············································································································- 13 -3.2烧结生产的工艺流程··································································································- 13 -3.2.1烧结原料的准备 ..................................................................................... - 14 -3.2.2配料与混合............................................................................................... - 14 -3.2.3烧结生产 ................................................................................................... - 15 -第四章烧结矿对高炉冶炼的影响·····································································- 18 -4.1烧结矿指标对高炉冶炼过程的影响·······································································- 18 -4.2烧结矿指标和冶金性能的影响因素·······································································- 20 -第五章结论·········································································································- 24 -参考文献·················································································································- 25 -致谢·································································································错误!未定义书签。
烧结配矿优化及高炉生产应对实践

M etallurgical smelting冶金冶炼烧结配矿优化及高炉生产应对实践张利波摘要:近些年,高炉炼铁一直是冶炼生铁过程中应用的最重要的技术,居于主导地位。
最近几年,全球的学者即使研究出许多高炉炼铁技术,不过在制作成本的经济性方面,依旧不能和以往的高炉制造技术进行比较。
国内,因为历史条件与制造成本的干预,非高炉炼铁技术的发展速度较慢,超过百分之九十五的生铁依旧借助高炉进行制作。
高炉生产期间,入炉原料重点是烧结矿、球团矿和块矿,而且烧结矿的比例高于百分之八十。
所以,烧结矿的品质高低在高炉生产过程中占据着主导作用,提升烧结矿品质对于缩减制作成本、保证高炉良好的运行具备着较高的作用。
关键词:烧结配矿优化;高炉生产;应对实践对策现如今使用的矿粉、矿石以及含铁工业物料等,使得烧结原料逐渐繁杂,如何通过原料的优化搭配实现品质最优、成本最优是钢铁生产重点关注的问题。
烧结矿是高炉的主要“口粮”,其质量的好坏直接影响高炉生产稳定和各项经济技术指标的完成。
为了确保烧结矿质量稳定,工作人员运用智能化手段,提升烧结配料精度,改善烧结矿质量,为高炉高效生产筑牢保障。
1 研究背景1.1 铁矿粉市场行情在我国环保政策高效实施的环境下,钢铁公司开始限制产量,铁矿石的需求数目逐渐下降。
不过在2017年~2018年鉴因为钢铁利润空间的变化,个别产能被释放,导致铁矿石的需求数目逐渐提升。
身为铁矿石的出产地澳大利亚与巴西境内铁矿石的出产量也随之增加,不过市场依然处于供需不平衡的状态,导致铁矿石的流通价格较高。
并且,因为持续的挖掘与应用优质资源,导致地球上的优质铁矿石数量逐步的减少,铁矿石供需框架的调节会是后期国际上需要一起面临与开展的工作。
我国铁矿石的存储数量位于世界前列,大约为整体存储量的百分之十二,整体的应用潜力较高。
由于铁矿的开采、加工工艺的提升,铁矿资源的整体应用会呈现出良好的经济性。
1.2 烧结配矿结构优化的理论基础低品矿粉为减少烧结资金投入最为重要的方式,不过品味下降可能导致非铁元素的高效提升,造成烧结矿品质降低,为后续高炉生产留下隐藏的危害,科学的应用铁矿粉高温特性展开烧结配矿,能够提升烧结配矿的效果。
烧结工艺介绍

烧结工艺的简单介绍目前,随着市场竞争的加剧,钢铁工业设备向大型化发展,对原料的要求日益提高,而高炉炼铁生产技术指标的提高,主要依靠入炉原料性质的改善,烧结矿是我国高炉的主要入炉料,因此,保证和提高烧结矿的质量,是保证钢铁工业稳定发展的重要手段。
一、烧结的概念烧结是钢铁生产工艺中的一个重要环节,它是将各种粉状含铁原料,配入适量的燃料和熔剂,加入适量的水,经混合和造球后在烧结设备上使物料发生一系列物理化学变化,将矿粉颗粒黏结成块的过程。
二、烧结矿的来源以及意义铁矿粉造块目前主要有两种方法:烧结法和球团法。
两种方法所获得的块矿分别为烧结矿和球团矿。
球团法通常在选贫矿的地区采用,尤其是北美地区。
而在有天然富矿可以开采使用的地方,烧结法则是一种成本较低的方法,在世界的其它地区被广泛采用。
虽然新的炼铁方法会不断出现,但是烧结矿的需求在很长一段时间内仍将保持在较高的水平。
在我国,高炉入炉的炉料90%^上都是靠烧结法提供的。
因此,铁矿石烧结对我国的钢铁工业有重大的意义。
三、烧结工艺流程介绍经烧结而成的有足够强度和粒度的烧结矿可作为炼铁的熟料。
利用烧结熟料炼铁对于提高高炉利用系数、降低焦比、提高高炉透气性保证高炉运行均有一定意义。
烧结生产的工艺流程如下图所示。
主要包括烧结料的准备,配料与混合, 烧结和产品处理等工序。
[警_1水I ~Sri~ —»j _|~点火: *%结礦辟rwv ~~iI讨烧站矿上鹿炉旷棺1、烧结的原材料准备:含铁原料:含铁量较高、粒度<5mm 的矿粉,铁精矿,高炉炉尘,轧钢皮, 钢渣等。
一般要求含铁原料品位高,成分稳定,杂质少。
熔剂:要求熔剂中有效CaO 含量高,杂质少,成分稳定,含水3%左右,粒 度小于3mm 的占90%以上。
在烧结料中加入一定量的白云石,使烧结矿含有适 当的MgQ 对烧结过程有良好的作用,可以提高烧结矿的质量。
燃料:主要为焦粉和无烟煤。
对燃料的要求是固定碳含量高,灰分低,挥 发分低,含硫低,成分稳定,含水小于 10%,粒度小于3mm 勺占95%以上。
烧结生产工艺
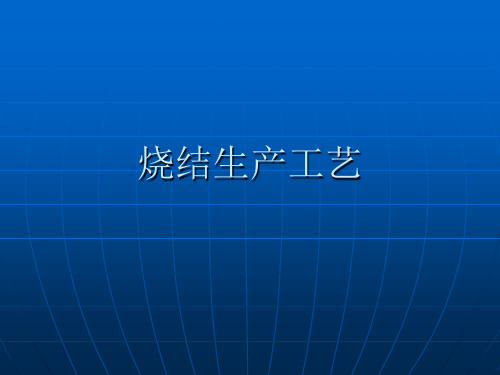
8)、烧结矿整粒
主要设备: 1、一次冷矿筛(椭圆振动筛) 2000×6000、筛孔20mm 2、二次冷矿筛(直线振动筛) 2000×6000、筛孔5mm; 10mm。 整粒分级为: 1、大成品≥20mm; 2、铺底料:10-20mm; 3、小成品:5-10mm; 4、冷返矿:≤5mm。 我厂大小成品分后又混供。
4)、烧结配料
一、主要设备: 1、配料圆盘; 2、拉式皮带机; 3、配消器及湿 式除尘器; 4、配料矿槽; 5、称量设备;
二、配料的目的: 1、使烧结料化学成份和物理性质稳定,符合烧结生 产需要; 2、使烧结料有一定的原始透气性,提高烧结生产率; 3、使烧结料化学成份稳定,符合高炉冶炼需要; 4、实现烧结和炼铁的物料平衡、资源利用和效益最 大化。 三、配料方法: 1、容积配料法; 2、重量配料法;
2、水分的蒸发、冷凝与结晶水分解
一、水的作用: 1、利用水的表面张力,将烧结料制成具有 一定强度的颗粒和小球; 2、在料层自动蓄热过程中将温度压缩在一 个较窄的区间内。 二、蒸发与冷凝: H2O(液)=H2O(气) 三、露点 四:结晶水的分解:
3、碳酸盐的分解和氧化钙的化合
9、烧结矿贮存与转运
1、成品矿槽:360m3×6; 2、SW系列皮带机; 3、S系列皮带机。
10、抽风与除尘
1、主抽风机;额定风量9000m3/min;匹 配电机3200KW;大烟道直径3600mm; 2、机头除尘器:198m2(4电场);多管除尘 器824管; 3、成品电除尘器50m2(3电场);燃料电除 尘器30m2(3电场);1#、2#机尾电除尘器 40m2(3电场);配料电除尘器40m2(3电 场)。
4、铁氧化物分解、氧化和还原
1、铁氧化物主要有三种形态:FeO、Fe2O3、 Fe3O4 2、分解:3Fe2O3=2Fe3O4+1/2O2。 3、氧化和还原: Fe FeO Fe3O4 Fe2O3 从左至右为氧化过程,放热;从右至左为还 原过程,吸热。 4、烧结过程总体上是氧化气氛,局部存在还 原气氛。
耐火材料用烧结镁橄榄石-概述说明以及解释
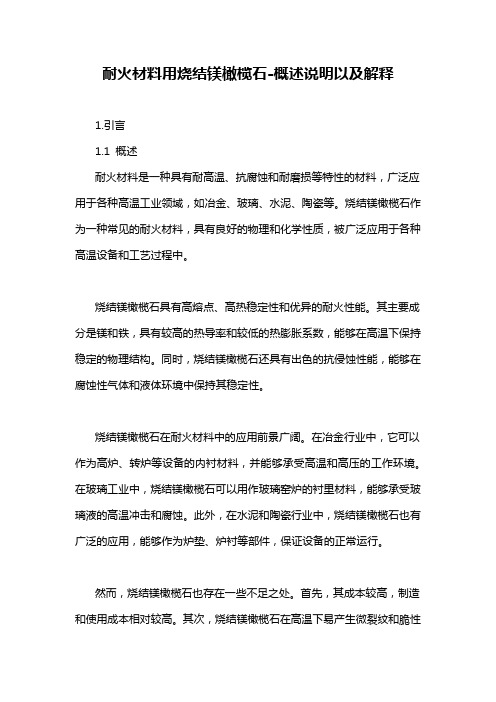
耐火材料用烧结镁橄榄石-概述说明以及解释1.引言1.1 概述耐火材料是一种具有耐高温、抗腐蚀和耐磨损等特性的材料,广泛应用于各种高温工业领域,如冶金、玻璃、水泥、陶瓷等。
烧结镁橄榄石作为一种常见的耐火材料,具有良好的物理和化学性质,被广泛应用于各种高温设备和工艺过程中。
烧结镁橄榄石具有高熔点、高热稳定性和优异的耐火性能。
其主要成分是镁和铁,具有较高的热导率和较低的热膨胀系数,能够在高温下保持稳定的物理结构。
同时,烧结镁橄榄石还具有出色的抗侵蚀性能,能够在腐蚀性气体和液体环境中保持其稳定性。
烧结镁橄榄石在耐火材料中的应用前景广阔。
在冶金行业中,它可以作为高炉、转炉等设备的内衬材料,并能够承受高温和高压的工作环境。
在玻璃工业中,烧结镁橄榄石可以用作玻璃窑炉的衬里材料,能够承受玻璃液的高温冲击和腐蚀。
此外,在水泥和陶瓷行业中,烧结镁橄榄石也有广泛的应用,能够作为炉垫、炉衬等部件,保证设备的正常运行。
然而,烧结镁橄榄石也存在一些不足之处。
首先,其成本较高,制造和使用成本相对较高。
其次,烧结镁橄榄石在高温下易产生微裂纹和脆性断裂现象,降低了其寿命和耐久性。
此外,烧结镁橄榄石对环境的影响也需要关注,因为其生产过程中会产生大量的气体和固体废物。
综上所述,烧结镁橄榄石作为一种耐火材料,在高温工业领域具有广泛的应用前景。
然而,为了进一步提高烧结镁橄榄石的性能和降低其成本,还需要进行更多的研究和创新。
通过改进制备工艺和材料结构,可以提高烧结镁橄榄石的耐火性能和稳定性,推动其在高温工业中的应用发展。
1.2 文章结构文章结构部分的内容可以如下所示:2. 正文2.1 耐火材料的定义和应用2.2 烧结镁橄榄石的特性和性能在本文中,我们将探讨耐火材料的应用领域以及烧结镁橄榄石在其中的特性和性能。
首先,我们将介绍耐火材料的定义和广泛应用的背景知识。
随后,在2.2部分,我们将重点讨论烧结镁橄榄石这一种常用的耐火材料,包括其特性、性能以及应用范围。
烧结矿配料目的、要求以及配料方法

为了使烧结矿的化学成分和物理性质稳定,符合高炉冶炼的要求,并使烧结料具有足够的透气性以获得较高的烧结生产率,必须把各种不同成分的含铁原料、熔剂和燃料根据烧结过程的要求和烧结矿质量的要求进行精确的配料。
烧结生产实践证明:烧结配料发生偏差会影响烧结过程的进行和烧结矿质量。
例如在某厂的条件下,灰石配比误差1%就影响烧结矿的碱度0.04;燃料波动1%,影响烧结矿中FeO变化2~3,使烧结矿的还原性及强度受到影响。
烧结原料的品种多,成分的波动大,进入配料室前必须经过破碎筛分、中和混匀处理,然后根据炼铁对烧结矿化学成份的要求进行配料计算,以保证烧结矿的含铁量、碱度、含硫量、FeO含量等主要成分控制在规定范围内,并为设备选择,矿槽设计以及运输系统提供设计数据。
配料的精确性在很大的程度上决定于所采用的配料方法。
目前配料方法有容积配料及质量(重量)配料。
目前各厂广泛使用的圆盘给矿机是容积配料的一种。
它是假定物料堆积密度一定的情况下,借套筒的闸门控制配料的容积。
为了增加其准确性必须定期检查。
由于各种原料的堆积密度随料粒和湿度不同而发生波动,致使配料量产生较大的误差,一般在5%以上。
在增加圆盘配料的准确性方面,各烧结厂积累了丰富的经验,如圆盘给矿机安装时应使给料圆盘中心与料仓中心相吻合,保持料仓中一定高度的料面,并使物料在料仓中分布均匀,防止物料堆集于一边。
保持圆盘盘面沿各方面具有相同的粗糙度。
有些烧结厂配料室为了保证混合矿化学成分及粒度均匀采用梯形给料法,即四个混合矿仓使用三个,一个是满仓,一个是半仓,一个是下仓,另一个在输料,输满后即送样化验成分。
一般来说满仓时给料的粒度细、量大。
底仓时给料的粒度粗、重量轻。
另外,为了正确地检查料量,采用三点一线的方法:即圆盘上的红线,称盘的中心点,皮带的中心点在一条线上。
圆盘上的红线是根据事先测定具有代表性的一点。
由于容积配料法设备简单,便于操作,因此目前还广泛地、特别是在中小企业中被采用。
高炉炼铁基本原理及工艺
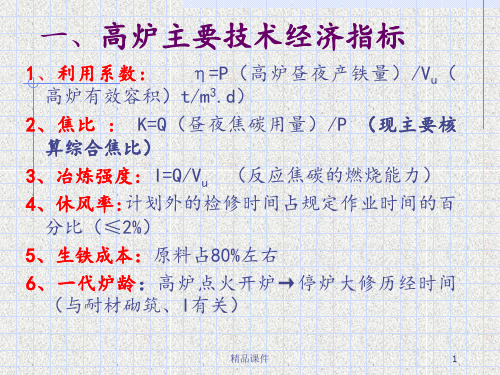
30
P ↑易还原
菱
FeCO3
48.2
30~40
25
P,S↓熔烧
后易还原
精品课件
2
各类铁矿石图
磁铁矿
褐铁矿
赤铁矿
精品课件
菱铁矿
3
⑴品位:含铁量,理论上品位↑1%,焦
比↓2%,产量↑ 3%
⑵脉石成分:SiO2、Al2O3↓越好(须重
视Al2O3 ),MgO ↑越好
⑶有害杂质:S、P、Cu、Pb、Zn、As、K
(1)合理布料的意义: ①影响料柱的空隙度 ②不人为调整将产生偏析,煤气自动边缘分布
(2)影响因素: ①布料设备 ②装料制度: 包括:料线、批重、装料次序
精品课件
33
(五)高炉能量利用 1.评价方法:
(1)燃料比 (2)rd (3)C的利用程度ηco 2.煤气上升过程中的变化
精品课件
34
五、高炉强化冶炼手段与方法
②气化脱S(一定值)
③适宜的渣量
(3)炉渣脱S基本反应:
[FeS]+(CaO)=(CaS)+(FeO)
提高炉渣脱S能力的因素:
①↑温度
精品课件 ②↑还原气氛
28
(三)风口前C的燃烧
1.风口前C燃烧的意义
占总C量的70%,其它碳用于:
直接还原:(FeO)+C=[Fe]+CO
(MnO)+C=[Mn]+CO
①C的燃烧速度(一般认为影响不大)
②布料状态(中心堆积,燃烧带小;中心疏 松,燃烧带大)
③鼓风动能EK的大小 (2)影响EK的因素:
①风量↑,EK ↑ ②风温↑,体积膨胀,质量流量↓ ,EK ↓
风温↑ ,速度↑ , EK ↑ 总体EK 略有变化 ③风压↑ , EK ↓ ④风口截面积S ↓, EK ↑
高炉炼铁对入炉含铁原料的质量要求

高炉炼铁对入炉含铁原料的质量要求,随着炼铁技术的进步不断提高。
在20世纪50年代,为了保证高炉炼铁有一个一般水平的指标,中国就制订了一条规范:入炉铁矿石品位应≥50%。
并提出“高炉是炼铁,不是炼渣”的说法。
和其他产业一样,对使用的原材料都有一定的质量要求,这也是高炉炼铁最原始的“精料”概念。
随着富块矿资源的越来越少,大量采用粉矿烧结时,作为人造富矿的烧结矿比生料块矿给高炉带来了更多好处。
同时为了高炉生产的“增铁节焦”和改善烧结矿性能,开始在烧结料中配加石灰石和白云石,从而减少高炉中因碳酸钙分解的热量耗损和改善炉料性能而生产自熔性烧结矿、熔剂性烧结矿和高碱度烧结矿。
为了达到增铁节焦的最大效果,在中国开始了100%“自熔性烧结矿”的高炉炼铁时代。
但根据米列尔博士和中国孔令坛老师的大量试验研究和生产实践的经验:当满足高炉冶炼炉渣碱度时,烧结矿的碱度(CaO/SiO2)应为1.4~1.6左右。
但此时烧结矿的强度处于最低点,烧结矿极易粉化,对高炉内的透气性和气流分布极为不利。
因此提出了精料和合理的炉料结构问题。
高炉炼铁“合理的炉料结构”这一理论概念和实践,在20世纪80年代的宝钢建设开始就十分重视。
日本在70年代钢铁工业崛起,钢铁生产技术达到世界领先的水平,对高炉炼铁不但实现了大型化,而且对合理炉料结构的研究取得了成功经验。
在采用进口澳大利亚矿的原料供应条件下,根据新日铁的经验确定了:80%烧结矿+15%球团矿+5%富块矿的炉料结构,并进入了工业性试验研究。
这一模式的优点是:100%的粉矿烧结生产烧结矿,同时烧结矿碱度为高碱度熔剂性(R=l.8),以生产优质铁酸钙为黏结相的烧结矿,避免了采用自熔性烧结矿强度低,不能满足大型高炉的要求。
为了满足高炉冶炼炉渣碱度的要求,另配加进口酸性球团矿和高品位块矿。
高质量的烧结矿、优质的巴西球团矿和高品位的块矿,实现了合理的炉料结构,为宝钢炼铁技术的先进性打下了坚实的基础,后来在国内得到广泛的模仿和推广。
炼铁学复习资料
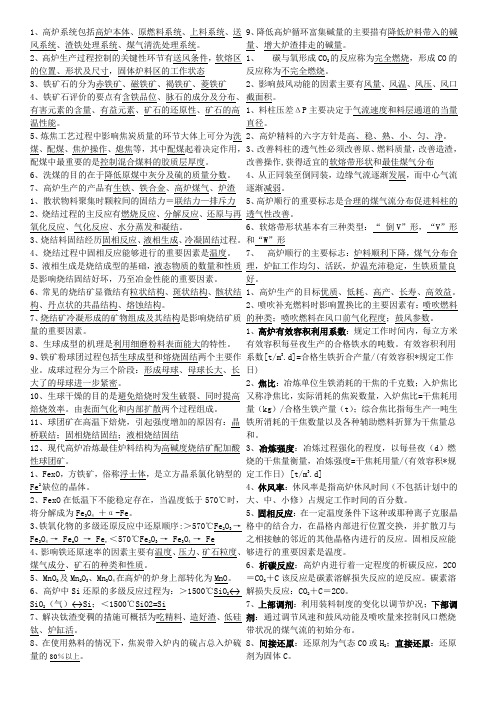
1、高炉系统包括高炉本体、原燃料系统、上料系统、送风系统、渣铁处理系统、煤气清洗处理系统。
2、高炉生产过程控制的关键性环节有送风条件,软熔区的位置、形状及尺寸,固体炉料区的工作状态3、铁矿石的分为赤铁矿、磁铁矿、褐铁矿、菱铁矿4、铁矿石评价的要点有含铁品位、脉石的成分及分布、有害元素的含量、有益元素、矿石的还原性、矿石的高温性能。
5、炼焦工艺过程中影响焦炭质量的环节大体上可分为洗煤、配煤、焦炉操作、熄焦等,其中配煤起着决定作用,配煤中最重要的是控制混合煤料的胶质层厚度。
6、洗煤的目的在于降低原煤中灰分及硫的质量分数。
7、高炉生产的产品有生铁、铁合金、高炉煤气、炉渣1、散状物料聚集时颗粒间的固结力=联结力—排斥力2、烧结过程的主反应有燃烧反应、分解反应、还原与再氧化反应、气化反应、水分蒸发和凝结。
3、烧结料固结经历固相反应、液相生成、冷凝固结过程。
4、烧结过程中固相反应能够进行的重要因素是温度。
5、液相生成是烧结成型的基础,液态物质的数量和性质是影响烧结固结好坏,乃至冶金性能的重要因素。
6、常见的烧结矿显微结有粒状结构、斑状结构、骸状结构、丹点状的共晶结构、熔蚀结构。
7、烧结矿冷凝形成的矿物组成及其结构是影响烧结矿质量的重要因素。
8、生球成型的机理是利用细磨粉料表面能大的特性。
9、铁矿粉球团过程包括生球成型和熔烧固结两个主要作业。
成球过程分为三个阶段:形成母球、母球长大、长大了的母球进一步紧密。
10、生球干燥的目的是避免焙烧时发生破裂、同时提高焙烧效率。
由表面气化和内部扩散两个过程组成。
11、球团矿在高温下焙烧,引起强度增加的原因有:晶桥联结;固相烧结固结;液相烧结固结12、现代高炉冶炼最佳炉料结构为高碱度烧结矿配加酸性球团矿。
1、FexO,方铁矿,俗称浮士体,是立方晶系氯化钠型的Fe2缺位的晶体。
2、FexO在低温下不能稳定存在,当温度低于570℃时,将分解成为Fe3O4+α-Fe。
3、铁氧化物的多级还原反应中还原顺序:>570℃Fe2O3 → Fe3O4 → Fe x O → Fe,<570℃Fe2O3 → Fe3O4 → Fe4、影响铁还原速率的因素主要有温度、压力、矿石粒度、煤气成分、矿石的种类和性质。
烧结配料知识
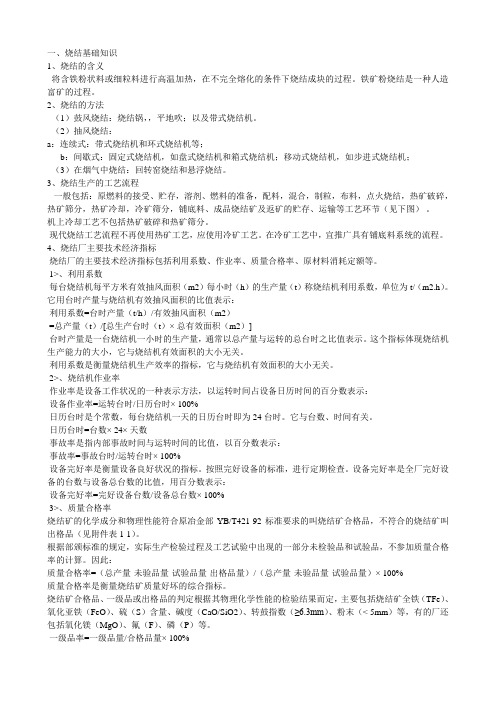
一、烧结基础知识1、烧结的含义将含铁粉状料或细粒料进行高温加热,在不完全熔化的条件下烧结成块的过程。
铁矿粉烧结是一种人造富矿的过程。
2、烧结的方法(1)鼓风烧结:烧结锅,,平地吹;以及带式烧结机。
(2)抽风烧结:a:连续式:带式烧结机和环式烧结机等;b:间歇式:固定式烧结机,如盘式烧结机和箱式烧结机;移动式烧结机,如步进式烧结机;(3)在烟气中烧结:回转窑烧结和悬浮烧结。
3、烧结生产的工艺流程一般包括:原燃料的接受、贮存,溶剂、燃料的准备,配料,混合,制粒,布料,点火烧结,热矿破碎,热矿筛分,热矿冷却,冷矿筛分,铺底料、成品烧结矿及返矿的贮存、运输等工艺环节(见下图)。
机上冷却工艺不包括热矿破碎和热矿筛分。
现代烧结工艺流程不再使用热矿工艺,应使用冷矿工艺。
在冷矿工艺中,宜推广具有铺底料系统的流程。
4、烧结厂主要技术经济指标烧结厂的主要技术经济指标包括利用系数、作业率、质量合格率、原材料消耗定额等。
1>、利用系数每台烧结机每平方米有效抽风面积(m2)每小时(h)的生产量(t)称烧结机利用系数,单位为t/(m2.h)。
它用台时产量与烧结机有效抽风面积的比值表示:利用系数=台时产量(t/h)/有效抽风面积(m2)=总产量(t)/[总生产台时(t)×总有效面积(m2)]台时产量是一台烧结机一小时的生产量,通常以总产量与运转的总台时之比值表示。
这个指标体现烧结机生产能力的大小,它与烧结机有效面积的大小无关。
利用系数是衡量烧结机生产效率的指标,它与烧结机有效面积的大小无关。
2>、烧结机作业率作业率是设备工作状况的一种表示方法,以运转时间占设备日历时间的百分数表示:设备作业率=运转台时/日历台时× 100%日历台时是个常数,每台烧结机一天的日历台时即为24台时。
它与台数、时间有关。
日历台时=台数× 24×天数事故率是指内部事故时间与运转时间的比值,以百分数表示:事故率=事故台时/运转台时× 100%设备完好率是衡量设备良好状况的指标。
- 1、下载文档前请自行甄别文档内容的完整性,平台不提供额外的编辑、内容补充、找答案等附加服务。
- 2、"仅部分预览"的文档,不可在线预览部分如存在完整性等问题,可反馈申请退款(可完整预览的文档不适用该条件!)。
- 3、如文档侵犯您的权益,请联系客服反馈,我们会尽快为您处理(人工客服工作时间:9:00-18:30)。
高炉生产的理想烧结料
1、前言
现代高炉生产只有在使用性能均匀稳定的炉料的情况下才能达到高生产率和高喷煤率。
因此,生产优质烧结矿,是确保高炉以高水平运行,同时降低还原剂消耗的决定性因素。
高炉的性能、生产率、能耗等不仅取决于炉料的质量,也同设备的设计特点、条件和所使用的过程控制系统密切相关。
2、优质烧结矿
使用如下指标的优质烧结矿,高炉能够达到生产率高、还原剂消耗低、铁水质量稳定等理想的性能:
(1)优化的粒度分布:约5~50mm,平均直径≥10mm;
(2)高强度:落下指数(SI)≥92%;
(3)高还原性:还原指数(RI)>65%,还原粉化指数(RDI<3.15mm):<20%;
(4)高孔隙度;
(5)软化温度高于1250℃(具体同高炉炉料总配比有关);
(6)软熔区温度范围窄;
(7)FeO含量稳定在7%左右;
(8)碱度B2和B4稳定在最适合高炉炉料总配比的指标。
另一个需要考虑的方面是,大多数高炉混和使用烧结矿、球团和块矿。
市场上的球团和块矿一般都有特定的化学成分和品位等级,而使用烧结矿的好处则在于可根据其他炉料成分的情况相应调节烧结矿的等级和加入量,从而优化炉料配比。
2.1原料对烧结矿质量的影响
生产优质烧结矿在很大程度上取决于原料成分,特别是脉石(SiO2、MgO、A 12O3)含量、间隙水和烧结原料的CaO/SiO2比。
颗粒度是至关重要的。
调查表明,烧结厂燃料消耗和烧结矿中FeO含量都随着原料中0.1mm以下和8mm以上的粒度所占的比例而增加。
2.2烧结厂操作参数对烧结矿质量的影响
生产优质烧结矿的一个决定性的前提条件是,烧结原料具有均匀的高透气性,所有成分应均匀分布。
透气性高而且均匀,就可以增大烧结床的高度,相应降低烧结工艺的燃料消耗。
这样能够避免烧结温度过高,对烧结矿的强度和还原性十分有利,间接地也有助于控制FeO含量。
FeO含量低于7%的烧结矿只能在烧结床高度约为600lnnl时得到。
还要提到的重要一点是,必须安装合适的设备来保证从烧结料床顶部到底部燃料浓度连续降低,以防止烧结温度过高。
延长烧结时间也对烧结矿的平均直径有利。
烧结时间受原料的透气性和负压影响。
降低负压会降低烧结床的生产率。
从烧透点位置到烧结机加料端的距离对烧结机能力、烧结矿平均FeO含量和平均直径有直接影响。
理想的烧透点位置是生产率和质量目标折衷的结果,而对
高炉生产来说烧结矿的质量总是最重要的。
如果为了保证烧结矿的质量而造成其数量的不足,可以用相对较低的投资方案来应对这一局面。
2.3烧结厂设备对烧结矿质量和数量的影响
优质烧结矿的生产在混料床就已开始了,一直延续到储料仓和配料仓。
在设计这些设备时必须特别注意,防止出现不利的物料偏析。
为获得理想结果,储料仓的配料、计量和称重系统必须由计算机进行实时控制。
控制向烧结机的加料可以获得以下改善:
(1)烧结料床透气性高而均匀,能够以低电耗生产优质烧结矿;
(2)可以控制烧结原料的偏析,从而保证烧结床从顶部到底部有期望的粒度分布;
(3)烧结床从顶部到底部燃料浓度降低,从而避免烧结温度过高。
烧结机台车的设计要使漏气吸人减少到最低程度,因而应当在边缘带加罩,以保证沿侧面的烧结矿也达到高质量。
3、高效高炉操作
3.1高炉炉料
现代高炉生产只有在使用性能均匀稳定的炉料的情况下才能达到高生产率水平。
从高炉操作人员角度来说,对炉料要求的主要关注点是:
(1)在高炉的整个温度范围和反应区域内有高透气性和均匀性;
(2)还原性高以缩短停留时间;
(3)Zn、Pb、碱金属等杂质元素含量低,避免对工艺造成扰动。
3.2高炉设备
3.2.1料仓和炉顶
料仓和高炉加料系统是获得期望的炉料分布的关键设施。
料仓的设计应当能够筛分多种粒度的烧结矿和焦炭(包括筛过的或未筛过的细料)并灵活配比各种不同粒度的这些原料。
这是有效利用作为如今高炉先进生产前提条件的无料钟加料系统的基础。
3.2.2风口喷吹设施
准确控制风口喷吹率(特别是煤的喷吹),对获得炉膛内均匀的温度分布和全面稳定的工艺条件具有决定性意义。
在良好的喷吹操作中,不同风口喷煤率的标准偏差不应超过2%。
中等富氧热鼓风是控制循环区火焰温度达到目标值的基本条件。
3.2.3出铁操作
认真监测炉壁温度、炉膛排放情况和出铁速度(最好使用专用工艺模型)对防止炉膛破损加剧和保证炉况稳定非常重要,特别是在喷煤率高、生产率高的情况下。
一些操作人员报告说在高生产率时对出铁口长度的控制存在问题。
使用高速液压钻口机和改进堵口泥,可以显著改善出铁口的条件。
3.3过程控制和自动化
综合控制系统方便了各级自动化系统与操作人员工作站和冶金工程师工作站相互之间有组织的、统一协调的数据交换。
为优化高炉运行,奥钢联开发了V Airon高炉自动化系统,包括3个不同的级别。
工艺信息管理级收集、处理和储存所有相关数据供随后使用;工艺模型级由一系列标准数学模型组成,分为物料
和热平衡模型、专用模型和动态模型等类别;闭环专家系统级全自动控制关键的操作参数。
4、结论
大多数高炉在增大生产率、降低能耗、延长炉役寿命和提高铁水质量等方面有很大改进余地。
高炉性能直接取决于炉料质量和高炉条件。
在现代烧结厂认真调整烧结矿的质量,在相当大程度上能够为高炉提供理想的炉料。
必须指出,只有在所有的高炉设施(包括料仓、加料系统、喷吹系统、出铁系统和过程控制系统)都高效运行时,优化炉料的优点才能充分发挥出来。
先进的工艺模型和专家系统可以确保稳定而精确地控制高炉的运行,同时实现所有质量、生产率和成本目标。