不锈钢外圆表面车削加工的总结与探索
外圆表面车削质量的提高方法
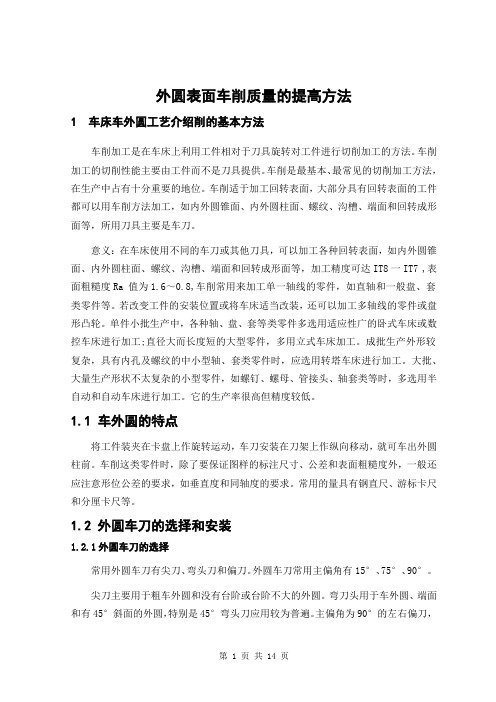
外圆表面车削质量的提高方法1 车床车外圆工艺介绍削的基本方法车削加工是在车床上利用工件相对于刀具旋转对工件进行切削加工的方法。
车削加工的切削性能主要由工件而不是刀具提供。
车削是最基本、最常见的切削加工方法,在生产中占有十分重要的地位。
车削适于加工回转表面,大部分具有回转表面的工件都可以用车削方法加工,如内外圆锥面、内外圆柱面、螺纹、沟槽、端面和回转成形面等,所用刀具主要是车刀。
意义:在车床使用不同的车刀或其他刀具,可以加工各种回转表面,如内外圆锥面、内外圆柱面、螺纹、沟槽、端面和回转成形面等,加工精度可达IT8一IT7 ,表面粗糙度Ra 值为1.6~0.8,车削常用来加工单一轴线的零件,如直轴和一般盘、套类零件等。
若改变工件的安装位置或将车床适当改装,还可以加工多轴线的零件或盘形凸轮。
单件小批生产中,各种轴、盘、套等类零件多选用适应性广的卧式车床或数控车床进行加工;直径大而长度短的大型零件,多用立式车床加工。
成批生产外形较复杂,具有内孔及螺纹的中小型轴、套类零件时,应选用转塔车床进行加工。
大批、大量生产形状不太复杂的小型零件,如螺钉、螺母、管接头、轴套类等时,多选用半自动和自动车床进行加工。
它的生产率很高但精度较低。
1.1 车外圆的特点将工件装夹在卡盘上作旋转运动,车刀安装在刀架上作纵向移动,就可车出外圆柱前。
车削这类零件时,除了要保证图样的标注尺寸、公差和表面粗糙度外,一般还应注意形位公差的要求,如垂直度和同轴度的要求。
常用的量具有钢直尺、游标卡尺和分厘卡尺等。
1.2 外圆车刀的选择和安装1.2.1外圆车刀的选择常用外圆车刀有尖刀、弯头刀和偏刀。
外圆车刀常用主偏角有15°、75°、90°。
尖刀主要用于粗车外圆和没有台阶或台阶不大的外圆。
弯刀头用于车外圆、端面和有45°斜面的外圆,特别是45°弯头刀应用较为普遍。
主偏角为90°的左右偏刀,车外圆时,径向力很小,常用来车削细长轴的外圆。
不锈钢车削方法
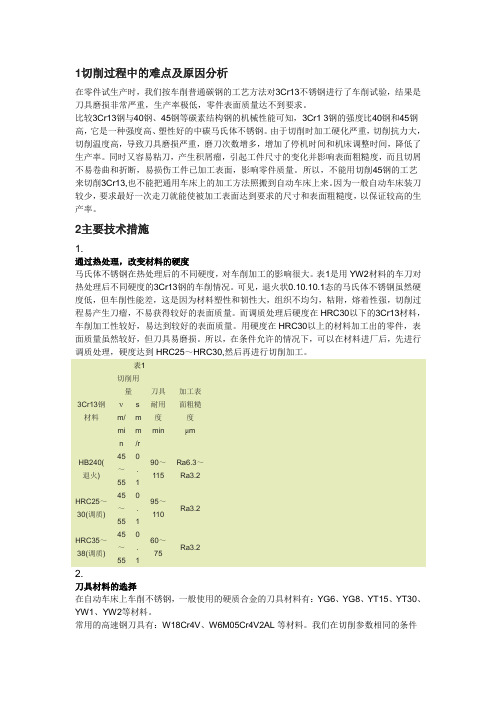
复合
°°
°
5 1 185
涂层
用) Ra~
刀片
5
Ra1.6
3.
刀具的几何角度和结构的选取
对于良好的刀具材料,选择合理的几何角度则显得尤为重要。
• 前角 γ:一般车削马氏体不锈钢刀具前角取10°~20°较为适宜。 • 后角 α:一般取5°~8°较合适,最大不过10°。 • 刃倾角 λ:一般选取 λ 为-10°~30°。 • 主偏角 Kr 应根据工件的形状、加工部位和装刀情况来选择。 • 刃口表面粗糙度应不大于 Ra0.4~Ra0.2。 • 在结构上,我们对外圆车刀采用外斜式圆弧断屑槽,靠刀尖处切屑卷曲半径大,靠 外缘处切屑卷曲半径小,切屑将翻向待加工表面而折断,断屑情况好。而对切断刀,我
5.
选用适当的冷却润滑液 车削不锈钢用的冷却润滑液,应该具有以下几个特点:
• 高的冷却性能,保证能带走大量的切削热。 • 不锈钢韧性大,切削时易产生刀瘤,恶化加工表面,这就要求冷却润滑液有高的润 滑性能,能起到较好的润滑作用。 • 渗透性好,对不易被切离的切屑,能起到较好的楔裂、扩散和内润滑作用。 常用的加工不锈钢的冷却润滑液有如下几种:硫化油、硫化豆油,煤油加油酸或植物油、四 氯化碳加矿物油、乳化液等。 考虑到硫对机床有一定的腐蚀作用,植物油(如豆油)容易附在机床上结痂和变质,我们选用 了四氯化碳与机油按重量比为1:9的混合物。其中四氧化碳渗透性好,机油的润滑性好。试 验证明,这种冷却润滑液适用于表面粗糙度要求小的不锈钢零件的半精加工和精加工工序, 特别适合于马氏体类不锈钢零件的车加工。
3结论
由于采取了一系列措施,我们对 3Cr13 不锈钢材料的加工已完全处于正常状态。磨刀次数 只有试生产时的 1/3,提高了生产效率,零件质量完全达到设计要求。
浅谈不锈钢材料的车削加工
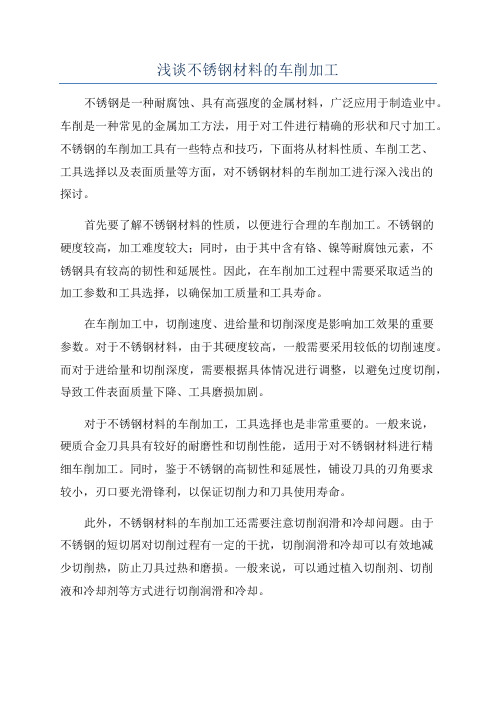
浅谈不锈钢材料的车削加工不锈钢是一种耐腐蚀、具有高强度的金属材料,广泛应用于制造业中。
车削是一种常见的金属加工方法,用于对工件进行精确的形状和尺寸加工。
不锈钢的车削加工具有一些特点和技巧,下面将从材料性质、车削工艺、工具选择以及表面质量等方面,对不锈钢材料的车削加工进行深入浅出的探讨。
首先要了解不锈钢材料的性质,以便进行合理的车削加工。
不锈钢的硬度较高,加工难度较大;同时,由于其中含有铬、镍等耐腐蚀元素,不锈钢具有较高的韧性和延展性。
因此,在车削加工过程中需要采取适当的加工参数和工具选择,以确保加工质量和工具寿命。
在车削加工中,切削速度、进给量和切削深度是影响加工效果的重要参数。
对于不锈钢材料,由于其硬度较高,一般需要采用较低的切削速度。
而对于进给量和切削深度,需要根据具体情况进行调整,以避免过度切削,导致工件表面质量下降、工具磨损加剧。
对于不锈钢材料的车削加工,工具选择也是非常重要的。
一般来说,硬质合金刀具具有较好的耐磨性和切削性能,适用于对不锈钢材料进行精细车削加工。
同时,鉴于不锈钢的高韧性和延展性,铺设刀具的刃角要求较小,刃口要光滑锋利,以保证切削力和刀具使用寿命。
此外,不锈钢材料的车削加工还需要注意切削润滑和冷却问题。
由于不锈钢的短切屑对切削过程有一定的干扰,切削润滑和冷却可以有效地减少切削热,防止刀具过热和磨损。
一般来说,可以通过植入切削剂、切削液和冷却剂等方式进行切削润滑和冷却。
最后,不锈钢材料的车削加工后还需要进行相应的表面处理,以提高工件的表面质量和防锈性能。
一般可以采用研磨、抛光等方式进行表面处理,以增加工件的光洁度和美观度。
总之,不锈钢材料的车削加工是一项综合性的任务,需要考虑材料性质、车削工艺、工具选择以及表面质量等多个方面的因素。
只有合理选择加工参数和工具,严格控制加工过程,才能获得满意的加工效果和产品质量。
同时,注重切削润滑和冷却、以及后续表面处理,也是保证不锈钢材料车削加工成功的关键。
不锈钢的车削技巧

不锈钢的车削技巧主要包括以下几个方面:1.刀具选择:选择适合不锈钢车削的刀具非常重要。
通常,选择具有较高耐热性、耐磨性和与不锈钢亲和作用小的刀具材料,如高碳、高钒或钼系的高速钢。
此外,刀具的几何形状和角度也需要根据具体加工要求进行选择。
2.切削用量选择:切削用量包括切削速度、进给量和切削深度。
对于不锈钢的车削,切削速度通常较低,一般为普通碳钢切削速度的40%~60%。
进给量和切削深度也需要根据具体情况进行选择,以避免刀具过度磨损和工件表面质量下降。
3.冷却液选择:使用合适的冷却液可以有效降低切削温度,减少刀具磨损和提高工件表面质量。
对于不锈钢的车削,通常选择具有较好冷却和润滑性能的冷却液。
4.操作技巧:在车削不锈钢时,需要注意以下几点操作技巧:首先,保持刀具的锋利,及时更换磨损的刀具;其次,避免使用过大的切削用量,以减少刀具的受力;最后,注意工件的装夹方式和切削力的方向,以避免工件变形或振动。
此外,还需要注意以下几点:1.由于不锈钢的塑性大、韧性高,车削时容易产生积屑瘤和鳞刺,这不仅影响工件的表面粗糙度,还会使刀具的磨损加快。
因此,需要选择合适的刀具材料和几何角度,以及合理的切削用量来避免这些问题的产生。
2.不锈钢的导热性差,导致切削热无法及时散出,使刀具的刃口温度升高,加剧刀具磨损。
为了降低切削温度,可以采用浇注冷却液的方法。
3.在车削过程中,应随时注意观察切削情况,如发现异常现象(如振动、噪声、温度升高等),应及时采取措施进行调整。
4.对于不同种类和规格的不锈钢材料,其车削性能也会有所不同。
因此,在实际加工前,最好先进行一些试验性切削,以确定最佳的切削参数和工艺方案。
总之,掌握不锈钢的车削技巧需要综合考虑多个因素,包括刀具选择、切削用量、冷却液和操作技巧等。
通过合理的选择和调整这些参数,可以提高加工效率、降低生产成本并获得高质量的工件。
车削外圆注意事项

车削外圆注意事项车削是一种常见的金属加工工艺,用于加工外圆的车削操作在制造业中应用广泛。
在进行车削外圆时,需要注意一些重要事项,以确保加工质量和安全。
本文将介绍一些车削外圆的注意事项。
1. 选择合适的车削刀具在车削外圆时,选择合适的车削刀具至关重要。
根据加工材料和加工要求,选择适合的切削刀具。
常见的车削刀具有硬质合金刀具、高速钢刀具等。
刀具的选择应考虑刀具材料的硬度、耐磨性和切削性能等因素。
2. 确定合适的切削速度切削速度是车削外圆过程中的重要参数之一。
它直接影响到加工效率和刀具寿命。
合理的切削速度可提高生产效率,减少刀具磨损。
切削速度的选择应根据材料的硬度、刀具材料和刀具结构等因素进行合理确定。
3. 控制进给量进给量是指切削刀具每转一圈在进给方向上移动的距离。
进给量的大小直接影响到加工表面的粗糙度和加工效率。
进给量过大会导致切削刀具过度磨损,加工表面粗糙度增加;进给量过小则会降低加工效率。
因此,在车削外圆时需要根据加工要求和材料特性合理确定进给量。
4. 控制切削深度切削深度是指切削刀具在一次切削中与工件接触的最大深度。
切削深度的选择应根据工件材料、刀具结构和切削稳定性等因素进行合理确定。
切削深度过大会导致切削刀具振动和工件变形,加工质量下降;切削深度过小则会降低加工效率。
5. 确保切削刀具的刃口质量切削刀具的刃口质量直接影响到加工表面的精度和光洁度。
在车削外圆前,应对切削刀具的刃口进行检查和修整。
刃口磨损严重或有缺口的刀具应及时更换或修整,以确保加工质量。
6. 控制切削液的使用切削液在车削外圆过程中起到冷却、润滑和清洁的作用。
适当的切削液可以降低切削温度,减少切削力,提高加工质量。
但切削液的过多或过少都会影响加工效果。
因此,在使用切削液时,应根据切削情况合理调节切削液的用量。
7. 加强安全防护在进行车削外圆操作时,应加强安全防护措施。
操作人员应穿戴好防护设备,保持操作区域整洁,避免工件和切削刀具的碰撞。
论述不锈钢材料切削加工的难点分析与解决方法

论述不锈钢材料切削加工的难点分析与解决方法摘要:结合实际,对不锈钢材料切削加工的难点分析与解决方法进行研究。
首先对不锈钢材料切削难点内容进行论述,其次在难点问题提出的基础上,给出了相关的解决方法。
关键词:不锈钢;材料切削;加工难点;解决方法1.引言和碳素钢进行对比分析,不锈钢中包含Cr、Ni、N、Nb、Mo等合金元素。
这些元素的存在使得不锈钢具备一定的耐腐蚀性,同时使得其性能得到了很大的提升。
比如马氏体不锈钢4Cr13与45号中碳钢进行对比分析,虽然含碳量是相同的,但是切削加工特性仅有45钢的58%。
2.不锈钢材料切削难点分析在金属加工的过程中,切削不锈钢环节,容易存在断刀、粘刀等问题。
这是因为不锈钢切削环节存在塑性变形过大的问题,导致切屑不易折断,粘连到主材上,造成切削环节的硬化比较严重,每次进刀都会给下一次切削产生硬化层,经过层层积累,不锈钢的切削硬度在大幅增大,切削力也要随之增加。
正式因为不锈钢切削环节存在上述的问题,会造成刀具和工件的摩擦力增大,切削温度也会相对较高,同时不锈钢的热传导系数比较小,散热性能不足,刀具和工具之间存在比较大的温度差,造成加工表面质量比较差。
此外,切削温度的上升会导致刀具磨损严重,刀具前刀面存在月牙洼,导致表面质量比较差,不仅使得加工效率下降,还会造成加工成本的增加。
3.提高不锈钢加工质量的方法3.1 刀具材料的选择刀具的选择对于加工来说是非常重要的,刀具是促进加工质量提升的关键性因素。
刀具如果质量比较差,就无法保证加工零件的合格;选择比较好的刀具,能够促进零件加工质量的提升,如果过高,则会导致资源浪费、成本的增加。
综合考虑到不锈钢材料的散热性比较差、产生硬化层、粘刀严重等特性,在刀具的选择过程中,需要达到耐热性强、耐磨性高、与不锈钢亲和力小等要求,从而可以保证加工可以顺利的进行。
3.1.1 高速钢高速钢中含有W、Mo、Cr、V、Go等合金元素,属于高合金工具钢的类型,工艺性能比较好,强度和韧性非常高,抗冲击振动效果都比较高。
不锈钢切削工作总结

不锈钢切削工作总结
不锈钢由于其自身特性,在切削加工过程中难度较大,容易产生磨损。
经过这次切削工作,我总结几点经验:
1. 使用正确的工具材料。
不锈钢最好使用陶瓷或超级陶瓷的刀具,降低磨损。
使用碳钢或高速钢的刀具在切削不锈钢时寿命较短。
2. 选择合适的切削参数。
切削速度和进给率不能太大,否则容易造成刀具断裂。
速度一般控制在100-150/之间,进给率控制在0.1-0.2/转之间。
3. 减小切屑厚度。
一次切除厚度控制在0.2以下,多次切削完成整个形状,减轻单次切削的负担。
4. 切削材料预热。
将不锈钢材料预热到150-200°,可以减少切削时的力量和延展冷缩应力,有利于延长刀具使用寿命。
5. 增大切削液流量。
合理使用切削液冷却和清洗作用,有效减少风化和磨损。
通过这次总结,下次切削不锈钢时能选择更合适的工具和参数,操作过程更顺利,也为日后不锈钢加工积累经验。
不锈钢材料的车削加工

不锈钢材料的车削加工摘要:随着现代工业的日益发达,不锈钢材质也在生产加工中被广泛应用,因此合理选用不锈钢材质加工刀具,是确保正确高效切割不锈钢的关键条件。
针对不锈钢切削特点,一般要求刀具材质应具备耐热性好、耐磨性高、与不锈钢材质的亲和性影响小等优点。
关键词:不锈钢材料车削加工不锈钢,是在空气中或化学腐蚀介质中都可以抗侵蚀的一类高温合金钢,不锈钢是指拥有漂亮的表层和耐腐蚀性能良好,而且无须经过镀色等表层处理过程,而发挥了不锈钢所存在的表层特点,应用在多种多样的钢材的一类,也常简称为不锈耐酸钢材。
一:不锈钢车削加工的弊端1、加工硬化严重。
2、塑性变形大,热硬度高,切削抗力大,刀具卷曲折断难。
3、由于切屑和工作物之间的磨擦大,所形成的剪切热较多。
4、切削刀具表面容易粘附,易生成积屑瘤,使切削刀具表面出现粘附、扩大损坏,造成前刃面出现月牙洼,切削后刃生成较小的剥落和缺陷;不锈耐酸钢的碳化物微粒硬度很高,在切割时会直接和菜刀接触,从而损坏菜刀,使菜刀的磨损程度加大。
不锈耐酸钢材质的加热强度高、加工韧性大对数控车高速切削并不适用,相较而言,不锈钢材质在高温下的加工硬度下降较小,但实践已证明,在相同切削高温的作用下,不锈钢车削用量远较于一般的碳素钢更难以加工,其中加热强度高是个至关重要的原因。
加工质量硬化趋势强,对数控车削用量影响大在数字控制高速切削的过程中,由于刃刃对工件材料挤出的效果使车削用量区的金属材料形成了变化,晶内出现滑移,晶体畸变,组织致密,加工力学性能也随之改变,而一般的车削用量硬度也可提高2~3倍。
数控切割后的机械加工生硬层深入可能从数十微米至数百微米之间,所以前一次性走刀所形成的机械加工生硬状态,也阻碍了下一次性走刀时的切割,同时加工生硬层的高硬度也使得刀具非常易于损坏,而且岩屑的粘着性强、导热差对数控技术切割也有一定危害。
此外,刀由于受剥肋断面宽度形状的影响,再加上本身硬度不够,加工中易形成振动,刃刃也易在切削过程中因为内部温度过高而烧坏或由于其震动太大而崩裂。
车削不锈钢零件的工艺分析与加工方法

车削不锈钢零件的工艺分析与加工方法摘要:不锈钢是机械装备制造领域的重要材料,因为其具有抗腐蚀性强、耐磨性佳的优势,所以以其为材料制作的零件韧性大、强度高、使用寿命长。
但受材料本身的影响,车削不锈钢零件时常会对刀具的切削性能、加工效率造成影响。
由于不锈钢零件加工对于机械装备而言有着重要意义,所以相关工作人员需采用科学合理的手段解决当下存在的问题,进一步提高车削效果。
本文就车削不锈钢零件的工艺与加工进行研究,以期为相关工作人员进行不锈钢零件的切削以及为研发人员改进切削加工技术提供参考。
关键词:车削;不锈钢零件;加工工艺;机械制造引言:目前,如何进行不锈钢零件的车削加工成为相关工作人员需要深入探讨的课题。
因为不锈钢零件的抗腐蚀性、机械性能较高,在进行车削加工时容易受到一些因素的影响,导致刀具出现磨损、“刀瘤”,不仅影响了刀具的切削性能,还引起了不锈钢零件加工效果与理想不符的情况。
为解决这些问题,下列进行了深入研究,以期解决上述存在的问题,进一步提高不锈钢零件的车削加工效率、质量,并为切削加工技术的不断改进提供参考。
1.不锈钢的车削特性以化学成分为依据,可以将不锈钢划分两个大类,一为铬不锈钢,二为镍不锈钢。
前者一般视情况而定选择含铬量,常见的为12%、17%、27%等。
含铬量通常与其靠腐蚀性能成正比。
铬镍不锈钢的含铬量、含镍量分别在17%~20%之间,8%~11%之间。
不锈钢的机械性能可直接影响其切削加工。
首先,在切削过程中会受到导热性的影响。
具体表现为:不锈钢本身的导热性越差,那么在车削过程中,热量会聚集于刀具上,而不是切屑中,所以刀具的切削性能会受到一定的影响,导致工作效率相对较低。
其次,不锈钢中含有碳化物杂质,其具有较强的磨蚀性,所以在切削时很容易出现磨损问题。
再次,不锈钢可在高温条件下保持较高强度和硬度,而刀具不能。
一旦超过其极限,便会产生塑性变形。
第四,不锈钢具有较强的粘附性,如果其黏附至刀具上时,便会产生“刀瘤”,导致车削工作的开展受到影响。
车削外圆的常见问题及解决方法

车削外圆的常见问题及解决方法车削是机械加工中一种常见的加工方式,它包括车削内圆、车削外圆、车削孔等多种加工形式。
其中,车削外圆是较为常见的一种。
在进行车削外圆的加工时,经常会出现一些问题或者难点,这些问题将影响到整个加工过程的质量和效率。
因此,本文将分析并总结车削外圆加工中的常见问题以及对应的解决方法。
常见问题1. 车削外圆圆度不精确车削外圆圆度不精确是车削加工中最为常见的问题之一。
在进行车削外圆加工时,由于车刀和工件夹紧不均匀或夹具靠板磨损等原因,会导致车削出的外圆不圆或者圆度不精确。
此外,由于车床本身及刀具刃口磨损或变形等原因也会导致圆度不精确。
2. 车削外圆表面粗糙车削外圆表面粗糙是车削外圆加工中常见的质量问题。
外圆表面的粗糙度受到许多因素的影响,例如车刀磨损、刀具倾角不合适、工件硬度等。
3. 车削外圆尺寸不正确车削外圆加工不仅需要满足圆度、表面粗糙度的要求,还要符合指定的尺寸要求。
但是,在实际加工中,经常会出现尺寸不正确的情况。
这主要和工件夹紧方式不正确、工件变形、车床导轨磨损等因素有关。
4. 车削外圆阴影部分过深车削外圆阴影部分过深是车削外圆加工中的一种瑕疵问题。
阴影部分是指车削后工件表面周围与车刀接触不良的部分,此部分与其它表面形成的交界处,如不加以处理,将对工件的美观度产生影响。
当工件硬度过高、刀具尖角过大、过渡角不合适等原因时,都很容易导致阴影部分过深。
解决方法1. 车削外圆圆度不精确的解决方法要解决车削外圆圆度不精确的问题,可以采用以下的方法:•对车刀的刀具倾角进行调整,保证车刀的刀尖与工件的中心线处于同一平面上。
•对车床的主轴及夹紧机构进行校准和调整,确保夹紧力均匀、准确。
•当工件过硬或者过长时,可以采用多次轮切或顺切的方法进行加工。
2. 车削外圆表面粗糙的解决方法要解决车削外圆表面粗糙的问题,可以采用以下的方法:•适当调整车刀的进给量,减小车削表面粗糙度。
•选用合适的刀具材料,提高切削质量,减小表面残留的毛刺。
车削外圆的常见问题及解决方法

车削外圆的常见问题及解决方法1出现波纹1.1振动引起的原因及解决方法工件表面有时出现波纹,主要是由于振动引起的,在车削中出现振动有以下几种原因后角。
例如:加工45#钢粗车时取后角5°—7°。
精车时取6°—8°A:电动机转动时产生振动。
解决方法:发现电动机转动时有振动应及时坚固电动机的螺栓螺母,同时检查机床底脚螺栓是否拧紧。
有条件时,更换带有橡胶垫圈的调整垫块。
B:车床主轴承松动或不圆,主轴上的齿轮啮合不好,主轴后轴承松动或不圆。
解决方法:用直径20毫米、1米长的钢元撬抬卡盘,发现卡盘有明显上抬间隙时,应打开床头箱,调整前轴承的松紧度,消除主轴的径向跳动。
同时检查后轴承的松紧度,调整控制后轴承的并帽螺母。
手盘动卡盘,使主轴转动松紧适度,消除主轴的轴向窜动,这样即可解决在车削中发生的工件表面跳动和工件轴向窜支所产生的波纹。
如发现床头箱内的齿轮发生严重磨损,啮合不好,必须更换齿轮。
使齿轮啮合状态良好,消除齿轮传动时产生的冲击,减轻产生振动给车削带来的波纹。
C:工件空心或伸出太长。
解决方法:安装工件要牢固,加工空心零件不能伸出过长,车刀要刃磨锋利,这样可避免工件表面出现波纹。
D:刀架松动。
解决方法:检查刀架是否锁紧,检查清除刀架底接触面的铁屑,增强刀架的锁紧力。
E:车刀伸出过长或刀刃已用钝。
解决方法:车刀伸出长度不宜过长。
刀刃用钝,要将刀具刃磨出合理角度。
刃磨好车刀的前角、后角、主偏角、副偏角、刃倾角。
前角:增大前角可以减少切削变形和切削力。
使切削轻快,提高加工精度和降低表面粗糙度。
工件材料的强度、硬度高,前角应选小一些,工件材料的强度硬度低前角应大一些。
一般硬质合金刀具前角为15°—20°为宜。
后角:要求切削刃强固,应取较小的后角。
精加工时应取较大的。
1.2辐射状波纹产生原因及消除方法用车床车削端面,有时会产生辐射状波纹。
用不同材料的刀具加工不同材料工件的端面,波纹深浅程度也不尽相同。
不锈钢的表面加工总结
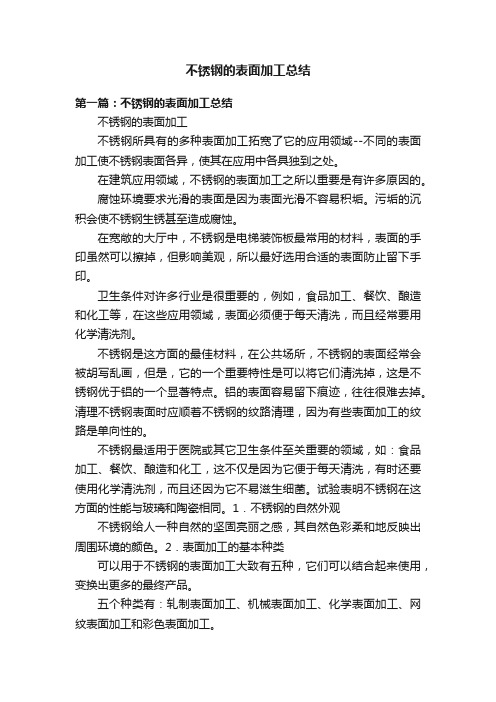
不锈钢的表面加工总结第一篇:不锈钢的表面加工总结不锈钢的表面加工不锈钢所具有的多种表面加工拓宽了它的应用领域--不同的表面加工使不锈钢表面各异,使其在应用中各具独到之处。
在建筑应用领域,不锈钢的表面加工之所以重要是有许多原因的。
腐蚀环境要求光滑的表面是因为表面光滑不容易积垢。
污垢的沉积会使不锈钢生锈甚至造成腐蚀。
在宽敞的大厅中,不锈钢是电梯装饰板最常用的材料,表面的手印虽然可以擦掉,但影响美观,所以最好选用合适的表面防止留下手印。
卫生条件对许多行业是很重要的,例如,食品加工、餐饮、酿造和化工等,在这些应用领域,表面必须便于每天清洗,而且经常要用化学清洗剂。
不锈钢是这方面的最佳材料,在公共场所,不锈钢的表面经常会被胡写乱画,但是,它的一个重要特性是可以将它们清洗掉,这是不锈钢优于铝的一个显著特点。
铝的表面容易留下痕迹,往往很难去掉。
清理不锈钢表面时应顺着不锈钢的纹路清理,因为有些表面加工的纹路是单向性的。
不锈钢最适用于医院或其它卫生条件至关重要的领域,如:食品加工、餐饮、酿造和化工,这不仅是因为它便于每天清洗,有时还要使用化学清洗剂,而且还因为它不易滋生细菌。
试验表明不锈钢在这方面的性能与玻璃和陶瓷相同。
1.不锈钢的自然外观不锈钢给人一种自然的坚固亮丽之感,其自然色彩柔和地反映出周围环境的颜色。
2.表面加工的基本种类可以用于不锈钢的表面加工大致有五种,它们可以结合起来使用,变换出更多的最终产品。
五个种类有:轧制表面加工、机械表面加工、化学表面加工、网纹表面加工和彩色表面加工。
还有一些专用的表面加工,不过无论指定哪一种表面加工,都应遵循以下步骤:①与制造厂家一起商定需要的表面加工,最好准备一个样品,作为今后批量生产的标准。
②大面积使用时(如复合板,必须保证所用的基底卷板或卷材采用的是同一批次。
③在许多建筑应用中,如:电梯内部,尽管手印可以擦掉,但很不美观。
如果选用布纹表面,就不那么明显了。
在这些敏感的地方一定不能使用镜面不锈钢。
不锈钢车削浅谈
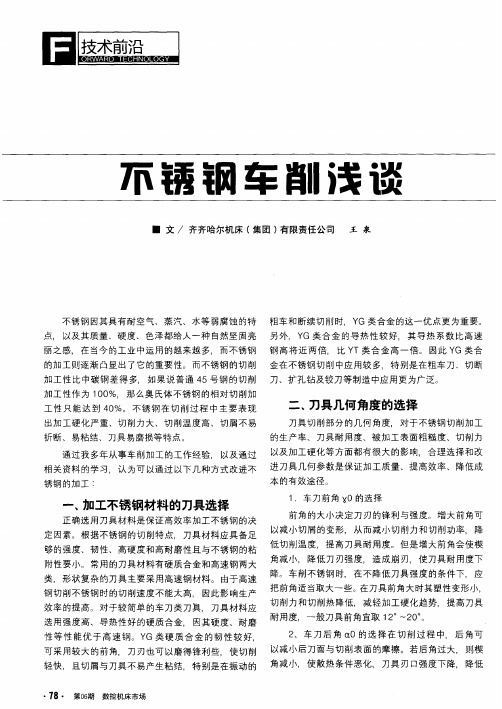
10
。 。
精车: 粗车:
0 05
.
—
0 10
.
4
4 4 4 5
.
0 10
.
~
0 20
.
车 刀 主 偏 角 K r 的选 择 当切 削 深 度
,
a
p
和进给
4
,
量 f 不 变时
减 小 主 偏 角 K r 可 使散 热 条件 得 到 改善
,
30 30
30 27 27
> 4
0
~
减少 刀 具 损坏
使刀 具切入
径
(舢 )
Rn 1
1
。
钝
一
,
增大切 削力
,
增 高 切 削温 度
,
加剧 刀 具 磨损
一
外 圆 车 刀 断 (卷 ) 屑槽 尺 寸 前角
g
0
般情况 下
,
后 角变化 不 大
但必 须有
。
个 合 理 的数
,
宽度
Bn
值
以 利 于 提 高 刀 具 的耐 用 度
车 削不 锈钢 时
,
由于
倒棱 尺 寸 b
(IIIⅡ1)
・
7 第0期 数控机床市场 8・ 6
f]
.. . . . .
. . . . . . . . . . . . . . . . . . . . . . . .
__J
刀具耐用度
:若 后
,
角过 小
,
摩擦 严 重
,
,
则 会使 刃
口
。变Biblioteka 在工外 圆 车 刀 断 ( 卷 ) 屑 槽 尺 寸选 择 见 表
外圆车削工艺与技巧
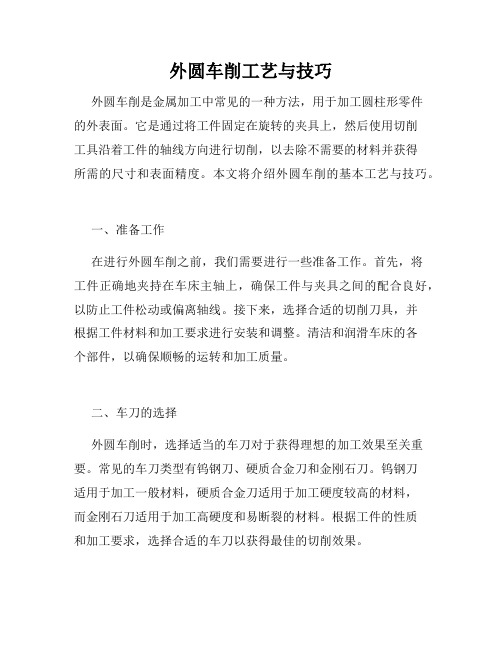
外圆车削工艺与技巧外圆车削是金属加工中常见的一种方法,用于加工圆柱形零件的外表面。
它是通过将工件固定在旋转的夹具上,然后使用切削工具沿着工件的轴线方向进行切削,以去除不需要的材料并获得所需的尺寸和表面精度。
本文将介绍外圆车削的基本工艺与技巧。
一、准备工作在进行外圆车削之前,我们需要进行一些准备工作。
首先,将工件正确地夹持在车床主轴上,确保工件与夹具之间的配合良好,以防止工件松动或偏离轴线。
接下来,选择合适的切削刀具,并根据工件材料和加工要求进行安装和调整。
清洁和润滑车床的各个部件,以确保顺畅的运转和加工质量。
二、车刀的选择外圆车削时,选择适当的车刀对于获得理想的加工效果至关重要。
常见的车刀类型有钨钢刀、硬质合金刀和金刚石刀。
钨钢刀适用于加工一般材料,硬质合金刀适用于加工硬度较高的材料,而金刚石刀适用于加工高硬度和易断裂的材料。
根据工件的性质和加工要求,选择合适的车刀以获得最佳的切削效果。
三、进给量和切削速度控制在进行外圆车削时,我们需要合理地控制进给量和切削速度。
进给量是指车刀在与工件接触的同时,沿着工件轴向前进的距离。
进给量的选择应考虑工件材料、硬度、尺寸等因素。
通常情况下,进给量越小,加工表面的质量越好。
切削速度是指切削刀具和工件相对旋转的速度,通常以转速来表示。
切削速度的选择应根据工件材料和车刀类型来确定,以保证切削效率和刀具寿命。
四、切削液的使用在外圆车削过程中,切削液的使用可以降低切削温度,减少摩擦和磨损,提高加工效率和表面质量。
适当的切削液应根据工件材料和加工要求来选择,并正确地润滑和冷却切削区域。
同时,切削液的使用应符合环保要求,合理回收和处理。
五、刀具的磨损检查与更换在进行外圆车削过程中,定期检查和更换刀具是保证加工质量和工具寿命的重要措施。
刀具的磨损会导致切削力增加、加工表面质量下降等问题。
因此,及时检查刀具的磨损情况,并根据需要进行修磨或更换,以保持刀具的锋利度和切削性能。
六、表面质量与精度要求外圆车削的目的之一是获得良好的表面质量和尺寸精度。
浅谈不锈钢材料的车削加工

浅谈不锈钢材料的车削加工不锈钢是一种耐腐蚀、耐热、耐高温的材料,广泛应用于机械制造、汽车制造、航空航天、建筑装饰等行业。
在不锈钢的车削加工中,需要特别注意材料的性质、工艺参数以及切削工具的选择。
不锈钢的性质决定了它的车削加工相对复杂。
首先,不锈钢的硬度较高,所以切削力比较大,对车削刀具的耐磨性提出了更高的要求。
其次,由于不锈钢具有较好的导热性,切削时容易产生热量,导致刀具快速磨损和加工表面产生尺寸偏差,因此需要采取合理的降温和冷却措施。
此外,不锈钢还具有较好的韧性和塑性,容易产生切削硬化,使切削加工更加困难。
在不锈钢的车削加工中,选择合适的车削工艺参数非常重要。
首先,应根据不锈钢的成分和硬度,选择合适的切削速度、进给速度和切削深度。
一般来说,低硬度的不锈钢适合选择较高的切削速度和进给速度,以提高生产效率;而高硬度的不锈钢则需要选择较低的切削速度和进给速度,以避免过度切削或切削过热。
此外,还需根据加工的具体要求和工件的尺寸,选择合适的刀具和切削方式。
切削工具的选择也对不锈钢的车削加工起着至关重要的作用。
不锈钢的硬度和耐热性,要求使用高强度、高耐磨性的刀具。
一般来说,硬质合金刀具可以满足这些要求,但也需要根据具体的加工情况选择合适的刀具材料和刀具几何形状。
此外,应根据切削参数和加工要求,合理选择切削润滑剂和冷却液,以降低切削温度、延长刀具使用寿命和提高加工质量。
总之,不锈钢材料的车削加工相对复杂,需要注意材料的性质、工艺参数和切削工具的选择。
在实际生产中,需要根据不锈钢的具体类型和加工要求,采取合适的加工工艺和切削方式,以提高加工效率和加工质量。
此外,还需加强刀具的研发和刀具涂层技术的应用,以适应不锈钢材料的车削加工需求。
车削外圆的常见问题及解决方法
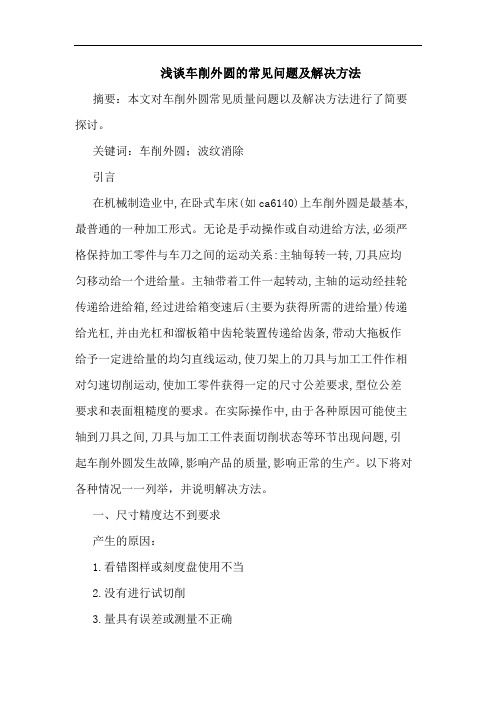
浅谈车削外圆的常见问题及解决方法摘要:本文对车削外圆常见质量问题以及解决方法进行了简要探讨。
关键词:车削外圆;波纹消除引言在机械制造业中,在卧式车床(如ca6140)上车削外圆是最基本,最普通的一种加工形式。
无论是手动操作或自动进给方法,必须严格保持加工零件与车刀之间的运动关系:主轴每转一转,刀具应均匀移动给一个进给量。
主轴带着工件一起转动,主轴的运动经挂轮传递给进给箱,经过进给箱变速后(主要为获得所需的进给量)传递给光杠,并由光杠和溜板箱中齿轮装置传递给齿条,带动大拖板作给予一定进给量的均匀直线运动,使刀架上的刀具与加工工件作相对匀速切削运动,使加工零件获得一定的尺寸公差要求,型位公差要求和表面粗糙度的要求。
在实际操作中,由于各种原因可能使主轴到刀具之间,刀具与加工工件表面切削状态等环节出现问题,引起车削外圆发生故障,影响产品的质量,影响正常的生产。
以下将对各种情况一一列举,并说明解决方法。
一、尺寸精度达不到要求产生的原因:1.看错图样或刻度盘使用不当2.没有进行试切削3.量具有误差或测量不正确4.由于切削热影响,使工件尺寸发生变化5.机动进给没及时关闭使车刀进给超过台阶长度6.车槽时车槽刀主切削刃太宽或太狭使槽宽不正确7.尺寸计算错误,使槽深度不正确预防方法:必须看清图纸尺寸要求,正确使用刻度盘,看清刻度值。
根据加工余量算出背吃刀量,进行试切削,然后修正背吃刀量。
量具使用前,必须检查和调整零位,正确掌握测量方法。
不能在工件温度高时测量,如测量应掌握工件的收缩情况,或浇注切削液,降低工件温度。
注意及时关闭机动进给或提前关闭机动进给用手动到长度尺寸。
根据槽宽刃磨车槽刀主切削刃宽度。
二、产生锥度:产生的原因:1.用一顶一夹或两顶尖装卡工件时,由于后顶尖轴线不在主轴线上2.用小滑板车外圆时产生锥度是由于小滑板的位置不正确3.用卡盘装卡工件纵向进给车削时产生锥度是由于车床床身导轨跟主轴轴线不平行4.工件装卡时伸出较长,车削时因切削力影响使前端让开,产生锥度5.车刀中途逐渐磨损预防方法:车削时必须找正锥度、必须事先检查小滑板的刻线是否与中滑板刻线的“0”线对准。
车削外圆的常见问题及解决方法
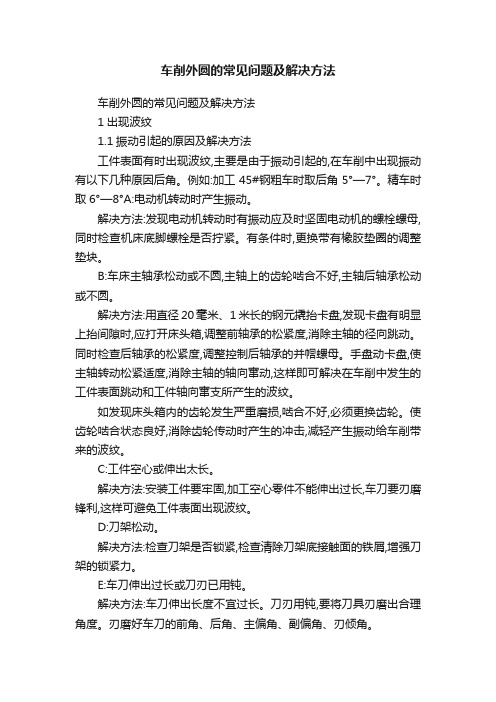
车削外圆的常见问题及解决方法车削外圆的常见问题及解决方法1出现波纹1.1振动引起的原因及解决方法工件表面有时出现波纹,主要是由于振动引起的,在车削中出现振动有以下几种原因后角。
例如:加工45#钢粗车时取后角5°—7°。
精车时取6°—8°A:电动机转动时产生振动。
解决方法:发现电动机转动时有振动应及时坚固电动机的螺栓螺母,同时检查机床底脚螺栓是否拧紧。
有条件时,更换带有橡胶垫圈的调整垫块。
B:车床主轴承松动或不圆,主轴上的齿轮啮合不好,主轴后轴承松动或不圆。
解决方法:用直径20毫米、1米长的钢元撬抬卡盘,发现卡盘有明显上抬间隙时,应打开床头箱,调整前轴承的松紧度,消除主轴的径向跳动。
同时检查后轴承的松紧度,调整控制后轴承的并帽螺母。
手盘动卡盘,使主轴转动松紧适度,消除主轴的轴向窜动,这样即可解决在车削中发生的工件表面跳动和工件轴向窜支所产生的波纹。
如发现床头箱内的齿轮发生严重磨损,啮合不好,必须更换齿轮。
使齿轮啮合状态良好,消除齿轮传动时产生的冲击,减轻产生振动给车削带来的波纹。
C:工件空心或伸出太长。
解决方法:安装工件要牢固,加工空心零件不能伸出过长,车刀要刃磨锋利,这样可避免工件表面出现波纹。
D:刀架松动。
解决方法:检查刀架是否锁紧,检查清除刀架底接触面的铁屑,增强刀架的锁紧力。
E:车刀伸出过长或刀刃已用钝。
解决方法:车刀伸出长度不宜过长。
刀刃用钝,要将刀具刃磨出合理角度。
刃磨好车刀的前角、后角、主偏角、副偏角、刃倾角。
前角:增大前角可以减少切削变形和切削力。
使切削轻快,提高加工精度和降低表面粗糙度。
工件材料的强度、硬度高,前角应选小一些,工件材料的强度硬度低前角应大一些。
一般硬质合金刀具前角为15°—20°为宜。
后角:要求切削刃强固,应取较小的后角。
精加工时应取较大的。
1.2辐射状波纹产生原因及消除方法用车床车削端面,有时会产生辐射状波纹。
车削加工实践总结

车削加工实践总结引言车削加工是常见的金属加工工艺之一,广泛应用于制造业中。
本文将总结车削加工的实践经验,包括工艺准备、加工操作、常见问题及解决方案等方面。
通过对车削加工实践的总结,可以提高加工效率,降低成本,提升产品质量。
工艺准备在进行车削加工之前,需要进行一系列的工艺准备工作,以确保加工的顺利进行。
材料准备首先要准备好待加工的金属材料,根据加工要求选择合适的材料。
常见的车削材料有铝合金、不锈钢、黄铜等。
不同的材料具有不同的切削性能和热膨胀系数,需要根据实际情况进行选择。
工件夹持将待加工的工件固定在车床上,保证工件的稳定性和安全性。
夹紧方式有多种,如三爪卡盘、四爪卡盘、弹簧卡盘等,选择夹紧方式要根据工件的形状和加工要求进行选择。
刀具选择选择合适的刀具是保证车削加工质量的关键。
刀具的选择要考虑刀具材料、刀片形状、刃口清晰度等因素。
根据加工材料的硬度和耐磨性选择合适的刀具,同时要考虑刀具的寿命和经济效益。
工艺流程设计在进行车削加工前,需要设计和规划好加工的工艺流程。
包括确定车削顺序、切削参数、切削速度等。
合理的工艺流程设计可以提高加工效率和保证加工质量。
加工操作车削加工的操作过程需要经过以下几个步骤:1. 上机操作操作人员首先要按照规定程序进行上机操作。
包括启动车床、调整主轴转速、调整进给速度等。
在上机操作过程中要注意安全,确保自身和周围人员的安全。
2. 确定零点和起始点在进行车削加工前,需要确定零点和起始点。
零点是指车床主轴和工件相对位置的参考点,起始点是加工的起始位置。
操作人员需要根据工件的要求,在车床上标出零点和起始点。
3. 开始车削加工根据工艺流程,启动切削刀具,进行车削加工。
在车削过程中,要保持稳定切削速度和进给速度,确保加工质量。
同时要注意观察加工过程中的异常情况,如切屑形态、切削力等,及时调整切削参数。
4. 进行切削检测在车削加工完成后,需要进行切削检测。
通过测量工件的尺寸、表面粗糙度等参数,判断加工质量是否符合要求。
- 1、下载文档前请自行甄别文档内容的完整性,平台不提供额外的编辑、内容补充、找答案等附加服务。
- 2、"仅部分预览"的文档,不可在线预览部分如存在完整性等问题,可反馈申请退款(可完整预览的文档不适用该条件!)。
- 3、如文档侵犯您的权益,请联系客服反馈,我们会尽快为您处理(人工客服工作时间:9:00-18:30)。
j £旖要】结合不锈钢的特性,根据生产实践确定出合理的刀具角度,达到矗好断屑和提高刀冥寿命的目的。 j 巨.键词] 不锈钢;性能;车71;切削角度;断屑
含铬量达10~12%以上的合金钢 称为不锈钢。按其化学成分不同 可分为两大类:铬不锈钒和镍铬不锈钢。它们在大气、水、碱和其他的 介质中具有良好的抗腐蚀性能。在工业生产中应用非常广泛。
此外在实践中我还摸索到利用普通高速钢刀具可刃磨的非常锋利这一特点用锋利的高速钢刀具在较低的切削速度下车削不锈钢外圆表面切削过程轻快切削变形小表面硬化现象不明显加工过程与普通中碳钢类似
不 锈钢 外 圆 表面 车 削加 工 的总 结 与 探索
郝德成邢健 ( 东北电力大学工程训练教学中心,吉林吉林132012)
通中碳钢类似。并目这类刀具尤其适合于加工工件刚性较差、直径较细
较长的 不锈钢工 件。
在使用不锈钢刀具时应注意的是,在刃磨刀具时,刀具的各种角
度均与切削普通中碳钢类似,但刃磨的表面要尽可能光滑,刃磨次数要 勤,并不要用油石研磨刃口,保持刃口锋利。刀具的圆角要适当加大修
圆,以增加刀尖强度,提高高速钢刀具的耐用度。切削速度应控制在 20m/mi n以下,并且用切削液充分冷却,控制温度,保持切屑呈银白
廖河
车刀前角影响刃口的锋利程度和强 度,影响切削变形和切削力。 车削不锈钢时,车刀必须采用较大的前角。这里亦采用较大前角 ( 1酽<y<2伊) ,增加刃口锋利性,减少切屑变形,从而减小切削 力,降f 氏切哨Ⅱ温度,减少加工硬化趋势,从而减小刀刃磨损,延长刀具 寿命 。
后角 也选择较 大角度眵 <a o<1伊) ,使车刀后刀面磨损减少, 寿命较长。
1车削不锈 钢外圆 表面的特 点 由于不锈钢的物理机械性能,车削 加工不锈钢外圆表面相对于加 工普通碳钢比较困难。如果不掌握加工要点,在切削过程中不容易得到 理想的表面粗糙度,且刀具寿命较低。这是因为: 1) 不锈钢的高温强度和高温硬度高,所以切削力大。 2)不锈钢的塑性大、韧性高,切削 变形大,相应的切削力和切削 熟也,大。 3)不锈 钢的导热率低 ,仅为碳钢 的033~0.5倍,由 切屑带走的 热量很少,因此车刀上的切削温度较高,使车刀磨损加快。 4)不锈钢的粘附性强,在切削过程 中,切屑容易粘附在刀具上而 产生积屑瘤,不易获得理想的表面粗糙度,刀刃容易磨损。 5) 不锈钢在加工中产生加工硬化的趋势强,加剧车刀的磨损。 6) 不锈钢的韧性大,切屑不易折断,容易破坏已扫凸工表面质量。 2车肖q 不锈钢外圆提高表面质量和刀具寿命的刀具改进方案 在长期 车削1 Cr l 8Ni 9 11、2 Cr l 3等不锈钢零件的生产实 践中,摸 索出一 种,j o- v不锈 钢的外圆车 刀( 见 示意图) 。车刀刀块 采用YG8、 Y\/v 1、Ⅵ/v2硬质合金,它们具有较大的韧性,能承受较大的冲击力和 切削力,而目抗切屑粘附性能也较好,更适合加工不锈钢。
为增强刃口强度,切削刃倒棱宽度b o, 一Q1 5mm,倒棱 前角y。,* 伊。
刀具 主偏角K y=750以减少切削抗力 ,不易产生振动。 刀尖部位修磨成圆弧状,其圆角半 径的大小对车刀耐用度有很大 的影响。圆角半径 R太小,散热条件 差,刀尖很容易被磨损:R过大, 切削过程中容易引起振动,因而也会加速刀尖的磨损。这里我选择圆弧 半径R==O.5mmo并使用圆弧型断屑 槽,刀具留有足够的容屑 空间,使
色。切忌用钝的已经磨损的高速钢刀具加工工件,在加工过程中一旦出
现切屑变色发黄的现象及工件表面硬化现象,应立即重新刃磨或更换刀
具。
在掌握以上要点后,利用锋利的高速钢刀具合理地车削加工不锈
钢工 件 外圆表 面 也可以 获 得满意 的 效果。
3 在条件允许的情况下采取以下措施可进一步提高车削不锈钢外
圆表面的质■和刀具寿命
2003.
210 2009年10月 (f )
排屑流畅。
?j
? i | }i
f j f .i
i I?
一 ? /j
,?
实践 证明 使用 该刀具 加工 不锈 钢轴类 零件 时,当 加工 直径 在
中30一中 60mm之间时切削 轻快、断屑良好、 表面质量高,刀 具寿命
明显提高。
此外在实践中我还摸索到利用普通高速钢刀具可刃磨的非常锋利
这—特点,用锋利的高速钢刀具在较低的切削速度下车削不,力o- r - 过程与普
1) 尽可能选用功率大的机床,提高机来——工件——刀具系统的
刚性 。
2) 选用抗粘附和散热性能好的切削液,如硫化由或硫化油加四氯 化碳,以刚氏切削熟和切削力,提高刀具耐用度。
3) 在技术要求允许的条件下,进行适当的热处理,以改善不锈钢
材料的 切削加工 性。
[ 参考文献】 f l l 陈宏钧.车工操作技能手册fM埘E束觏械工业出版被.2004. 1212郑文虎.机械加工实用经验【M1.北京:围防工业出版争} =,2003. f 31孙东升.不锈钢材料的车削加工o】科技情报开发与经济.2002. f 4】张文周.谭承晦.不锈钢加工对刀具材质和几何参数的要求l 『1.机械制造