汽车部件产品确认流程阶段
汽车零部件的技术开发过程
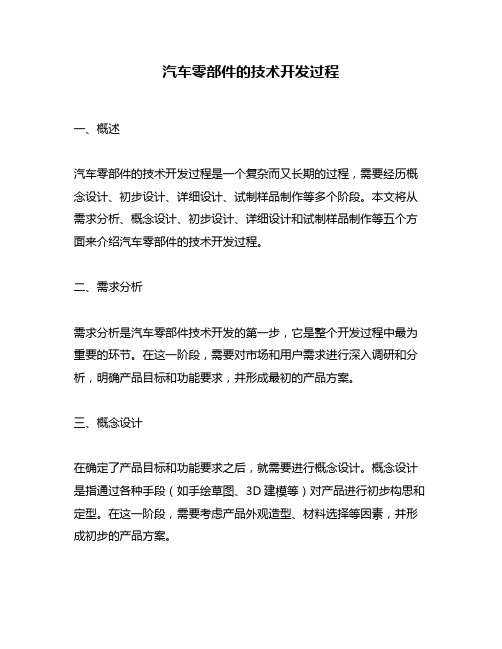
汽车零部件的技术开发过程一、概述汽车零部件的技术开发过程是一个复杂而又长期的过程,需要经历概念设计、初步设计、详细设计、试制样品制作等多个阶段。
本文将从需求分析、概念设计、初步设计、详细设计和试制样品制作等五个方面来介绍汽车零部件的技术开发过程。
二、需求分析需求分析是汽车零部件技术开发的第一步,它是整个开发过程中最为重要的环节。
在这一阶段,需要对市场和用户需求进行深入调研和分析,明确产品目标和功能要求,并形成最初的产品方案。
三、概念设计在确定了产品目标和功能要求之后,就需要进行概念设计。
概念设计是指通过各种手段(如手绘草图、3D建模等)对产品进行初步构思和定型。
在这一阶段,需要考虑产品外观造型、材料选择等因素,并形成初步的产品方案。
四、初步设计在完成了概念设计之后,就需要进入到初步设计阶段。
在这一阶段,需要对产品进行更加详细的构思和规划,并确定具体的技术路线和工艺流程。
同时,还需要进行各种仿真和试验,以验证产品的可行性和性能指标。
五、详细设计在完成了初步设计之后,就需要进入到详细设计阶段。
在这一阶段,需要对产品的各个细节进行更加精细的设计和规划,并确定具体的零部件尺寸、材料等要素。
同时,还需要对产品进行各种仿真和试验,以验证产品的可行性和性能指标。
六、试制样品制作在完成了详细设计之后,就需要进入到试制样品制作阶段。
在这一阶段,需要根据详细设计图纸进行零部件加工和组装,并对整个产品进行测试和调试。
如果测试结果符合预期,则可以进入到批量生产阶段。
七、总结汽车零部件技术开发是一个复杂而又长期的过程,在这个过程中需要经历需求分析、概念设计、初步设计、详细设计和试制样品制作等多个阶段。
每个阶段都有其独特的任务和重要性,在整个过程中都需要高度重视质量控制和技术创新,以确保最终产品的质量和竞争力。
汽车零部件产品开发流程

汽车零部件产品开发流程1.需求分析:在汽车零部件产品开发过程中,首先需要进行市场调研和需求分析。
通过了解市场需求和竞争对手的产品情况,确定产品的需求和定位,明确产品的功能、性能、质量标准、成本限制以及安全要求等。
2.概念设计:根据需求分析的结果,进行概念设计。
这一阶段包括以下内容:a.设计思路的确定:确定产品的总体设计思路,包括外观、结构、材料等。
b.执行评估:通过计算和仿真等手段,评估产品的可行性和性能。
3.详细设计:在概念设计阶段确定后,需要进行详细设计。
这一阶段包括以下内容:a.零部件的结构设计:确定零部件的具体结构,包括尺寸、形状、连接方式等。
b.零部件的材料选择:选择合适的材料,满足产品的性能和质量要求。
c.零部件的装配设计:确定零部件之间的装配方式和工艺。
4.原型制作:通过三维打印、模具制作等方式制作产品的原型。
原型通常用于测试验证产品的可行性、性能和质量。
5.测试验证:进行产品的各种测试验证,包括性能测试、可靠性测试、安全性测试等。
根据测试结果进行产品的优化和改进。
6.生产制造:根据产品设计和测试验证的结果,进行产品的生产制造。
这包括制定生产计划、采购零部件、生产装配、质量控制等。
7.市场推广:产品生产完成后,进行市场推广。
这包括制定市场营销策略、推广产品特点、与销售渠道合作等方式。
8.售后服务:对于汽车零部件产品来说,售后服务非常重要。
提供及时的售后服务可以增加客户对产品的满意度和忠诚度,同时也可以收集用户的反馈信息,为产品的改进提供参考。
汽车零部件产品开发流程是一个复杂的过程,需要涉及到多个专业领域的知识和技术,包括市场调研、设计、工程制图、材料选择、制造工艺、测试验证等。
以上是汽车零部件产品开发的主要流程,但实际情况可能因不同的企业、产品和市场需求而有所不同。
汽车产品开发流程

汽车产品开发流程汽车产品开发是一个复杂的过程,需要经过多个阶段的设计、测试和验证。
这个过程需要涉及到多个部门和团队的协作,包括设计师、工程师、测试人员和市场营销人员等。
下面将介绍汽车产品开发的流程。
第一阶段:概念设计概念设计是汽车产品开发的第一阶段,这个阶段的目的是确定产品的基本设计方向和特点。
在这个阶段,设计师和工程师会进行大量的市场调研和用户需求分析,以确定产品的定位和目标用户。
然后,他们会进行初步的设计和模型制作,以便在后续的阶段进行测试和验证。
第二阶段:详细设计在概念设计阶段确定了产品的基本方向和特点之后,就需要进入详细设计阶段。
在这个阶段,设计师和工程师会进行更加详细的设计和模型制作,以便进行更加精确的测试和验证。
这个阶段需要涉及到多个方面的设计,包括外观设计、内饰设计、底盘设计、动力系统设计等。
第三阶段:工程开发在详细设计阶段完成之后,就需要进入工程开发阶段。
在这个阶段,工程师会进行更加深入的设计和制造,以便进行更加精确的测试和验证。
这个阶段需要涉及到多个方面的工程开发,包括零部件制造、装配、测试和验证等。
第四阶段:测试和验证在工程开发阶段完成之后,就需要进行测试和验证。
在这个阶段,测试人员会对汽车进行各种测试和验证,以确保汽车的性能和安全性能符合要求。
这个阶段需要涉及到多个方面的测试和验证,包括性能测试、安全测试、耐久性测试等。
第五阶段:生产和销售在测试和验证阶段完成之后,就需要进入生产和销售阶段。
在这个阶段,汽车制造商会进行汽车的生产和销售,以满足市场需求。
这个阶段需要涉及到多个方面的生产和销售,包括零部件制造、装配、销售和售后服务等。
总结汽车产品开发是一个复杂的过程,需要经过多个阶段的设计、测试和验证。
这个过程需要涉及到多个部门和团队的协作,包括设计师、工程师、测试人员和市场营销人员等。
只有经过严格的测试和验证,才能确保汽车的性能和安全性能符合要求,从而满足市场需求。
汽车行业产品开发流程
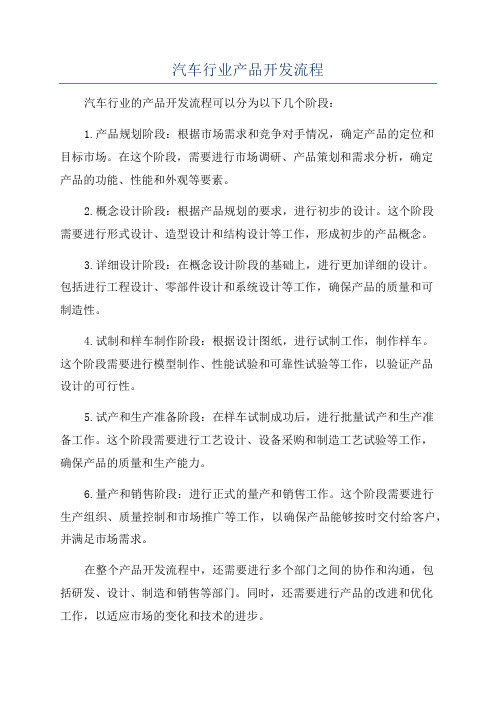
汽车行业产品开发流程汽车行业的产品开发流程可以分为以下几个阶段:1.产品规划阶段:根据市场需求和竞争对手情况,确定产品的定位和目标市场。
在这个阶段,需要进行市场调研、产品策划和需求分析,确定产品的功能、性能和外观等要素。
2.概念设计阶段:根据产品规划的要求,进行初步的设计。
这个阶段需要进行形式设计、造型设计和结构设计等工作,形成初步的产品概念。
3.详细设计阶段:在概念设计阶段的基础上,进行更加详细的设计。
包括进行工程设计、零部件设计和系统设计等工作,确保产品的质量和可制造性。
4.试制和样车制作阶段:根据设计图纸,进行试制工作,制作样车。
这个阶段需要进行模型制作、性能试验和可靠性试验等工作,以验证产品设计的可行性。
5.试产和生产准备阶段:在样车试制成功后,进行批量试产和生产准备工作。
这个阶段需要进行工艺设计、设备采购和制造工艺试验等工作,确保产品的质量和生产能力。
6.量产和销售阶段:进行正式的量产和销售工作。
这个阶段需要进行生产组织、质量控制和市场推广等工作,以确保产品能够按时交付给客户,并满足市场需求。
在整个产品开发流程中,还需要进行多个部门之间的协作和沟通,包括研发、设计、制造和销售等部门。
同时,还需要进行产品的改进和优化工作,以适应市场的变化和技术的进步。
在汽车行业,产品开发流程一般较为复杂和漫长,涉及到多个方面的知识和技能。
因此,汽车制造商通常会投入大量的人力、物力和财力,以保证产品的质量和竞争力。
总体而言,汽车行业的产品开发流程包括产品规划、概念设计、详细设计、试制和样车制作、试产和生产准备、量产和销售等阶段,其中每个阶段都有具体的工作内容和任务。
通过科学的产品开发流程,汽车制造商能够有效地开发出具有竞争力的产品,满足市场的需求。
汽车零部件和材料进货检验验证及定期确认管理程序

汽车零部件和材料进货检验验证及定期确认管理程序一、引言汽车制造过程需要大量的零部件和材料,这些零部件和材料质量的好坏将直接影响汽车的质量和性能。
为了确保汽车零部件和材料的质量、可靠性和稳定性,本文将介绍汽车零部件和材料进货检验、验证及定期确认的管理程序。
二、进货检验1.进货前准备在进货之前,企业应根据产品的技术要求和质量标准,制定进货检验的标准和相关要求,明确进货检验的流程和程序。
2.检验项目进货检验主要包括外观检验、尺寸检验、材料检验、性能检验、包装检验等项目。
根据不同的零部件和材料的特点,制定相应的检验项目和标准。
3.检验方法进货检验可以采用抽样检验的方法。
根据进货批次和批量确定抽样数量和检验方法。
同时,可以采用第三方检测机构来进行检验,确保检验结果的客观性和准确性。
4.检验记录和处理进货检验的结果需要进行记录,并进行适当的处理。
对于不合格的零部件和材料,需要及时返工或者退货,并对相关供应商进行评估和处理。
三、验证1.验证目标验证是通过试验和实际使用来判断零部件和材料是否满足产品的技术要求和质量标准。
验证的目标是为了评估零部件和材料的可靠性、耐久性和稳定性。
2.验证方法验证可以采用实验室试验、原理验证、试制样车验证等方法。
根据验证的目标和要求,制定相应的验证方案和试验计划。
3.验证记录和处理验证结果需要进行记录,并根据验证结果进行适当的处理。
对于不合格的零部件和材料,需要及时进行改进和调整。
四、定期确认1.定期确认的目的定期确认是为了评估已经在使用中的零部件和材料的性能和质量,以确保汽车的安全和可靠性。
定期确认的目的是发现零部件和材料的老化、磨损、变形等问题,并采取相应的措施进行处理。
2.定期确认的频率和方法根据不同零部件和材料的特点和使用环境,制定相应的定期确认频率和方法。
定期确认可以通过检测、试验、分析等方法进行。
3.定期确认记录和处理定期确认的结果需要进行记录,并根据确认结果进行适当的处理。
简述汽车零部件物流的主要运作流程
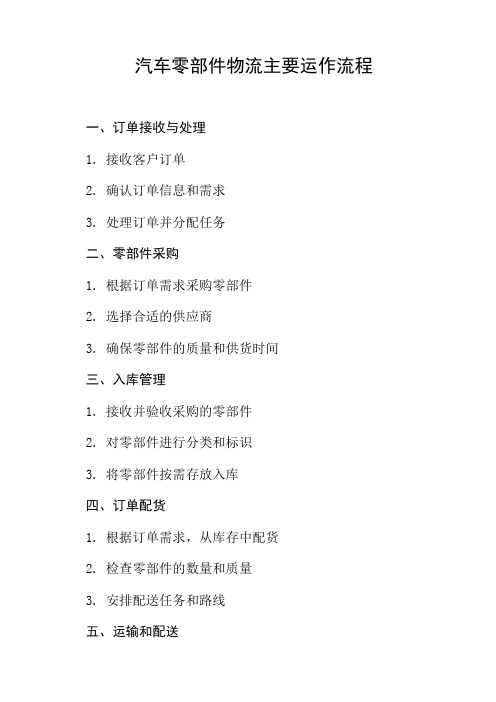
汽车零部件物流主要运作流程
一、订单接收与处理
1. 接收客户订单
2. 确认订单信息和需求
3. 处理订单并分配任务
二、零部件采购
1. 根据订单需求采购零部件
2. 选择合适的供应商
3. 确保零部件的质量和供货时间
三、入库管理
1. 接收并验收采购的零部件
2. 对零部件进行分类和标识
3. 将零部件按需存放入库
四、订单配货
1. 根据订单需求,从库存中配货
2. 检查零部件的数量和质量
3. 安排配送任务和路线
五、运输和配送
1. 将配货的零部件装车运输
2. 选择合适的运输方式和车辆
3. 按时将零部件送达客户指定地点
六、客户签收与反馈
1. 客户签收零部件并确认收货
2. 收集客户反馈和意见
3. 处理客户投诉和问题
七、库存管理与优化
1. 定期盘点和管理库存
2. 分析库存情况和动态
3. 优化库存结构和管理策略
八、供应链协调
1. 与供应商和客户进行有效沟通
2. 协调供应链各环节的运作
3. 解决供应链中的问题和瓶颈
九、数据分析与优化
1. 收集并分析物流数据
2. 识别和优化物流流程
3. 提高物流效率和服务水平。
TS汽车零部件项目开发流程
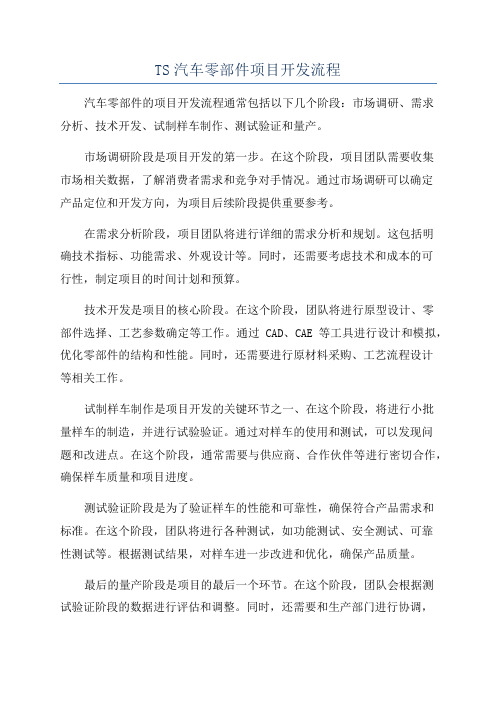
TS汽车零部件项目开发流程汽车零部件的项目开发流程通常包括以下几个阶段:市场调研、需求分析、技术开发、试制样车制作、测试验证和量产。
市场调研阶段是项目开发的第一步。
在这个阶段,项目团队需要收集市场相关数据,了解消费者需求和竞争对手情况。
通过市场调研可以确定产品定位和开发方向,为项目后续阶段提供重要参考。
在需求分析阶段,项目团队将进行详细的需求分析和规划。
这包括明确技术指标、功能需求、外观设计等。
同时,还需要考虑技术和成本的可行性,制定项目的时间计划和预算。
技术开发是项目的核心阶段。
在这个阶段,团队将进行原型设计、零部件选择、工艺参数确定等工作。
通过CAD、CAE等工具进行设计和模拟,优化零部件的结构和性能。
同时,还需要进行原材料采购、工艺流程设计等相关工作。
试制样车制作是项目开发的关键环节之一、在这个阶段,将进行小批量样车的制造,并进行试验验证。
通过对样车的使用和测试,可以发现问题和改进点。
在这个阶段,通常需要与供应商、合作伙伴等进行密切合作,确保样车质量和项目进度。
测试验证阶段是为了验证样车的性能和可靠性,确保符合产品需求和标准。
在这个阶段,团队将进行各种测试,如功能测试、安全测试、可靠性测试等。
根据测试结果,对样车进一步改进和优化,确保产品质量。
最后的量产阶段是项目的最后一个环节。
在这个阶段,团队会根据测试验证阶段的数据进行评估和调整。
同时,还需要和生产部门进行协调,确保量产的顺利进行。
在量产阶段,也需要对生产过程进行质量控制和监控,确保产品质量的稳定性。
总之,汽车零部件项目的开发流程是一个系统而复杂的过程,需要团队成员的密切合作和各个环节的有序衔接。
通过科学合理的流程管理,可以提高项目的效率和质量,推动整个项目的顺利完成。
PPAP、APQP、ESER、PSW等汽车行业产品认证体系资料

VAPQP
Supplier Program Development
SOSPOP
报价单
EPR
30天内通知
DV
APQP
APQP 启动
LRR
(within +/- 30 days from PSW)
PV
SLP( Part B)
分供方APQP 过程验证
PTR
试生产
模具生产
AP供QP方APQP
SOP
SLP (Part C)
要求。 PDS 1994.8年第一版;1995.2第二版。1998.3第三版
参考手册有:
AP QP
① 生产件批准程序(PPAP)。
② 质量体系评审 (QSA)
③ 产品质量的先期策划的控制计划 (APQP) PP ④ 测量系统分析 (MSA) AP ⑤ 失效模式和效果分析(FMEA)
⑥ 统计过程式控制 (SPC) 回顾
VISTEON CONFIDENTIAL – 2 April 2003
目录 B.VDA6:
体系
德国汽车工业联合会(VDA)在 ISO 9001及ISO
9004基础上增加了很多汽车行业特有要求制定了
PD VDA6.1。
CA 1991年第一版;1992.12第二版。1996.1第三版,
1999年4月1日第四版。
回顾 VISTEON CONFIDENTIAL – 2 April 2003
目录
3、ISO/TS16949:2002
体系
PD CA
PDS
AP QP
PP AP
IATF是国际汽车行动组织,是由美.德.法.意.英等国 家的汽车公司和汽车行业组织组成的协会性组织,主要协 调汽车行业质量管理体系要求。
汽车新零部件开发的主要阶段和程序

汽车新零部件开辟的主要阶段和程序汽车新零部件开辟的主要阶段和程序可以分为以下几个步骤:
1. 需求分析阶段:在这个阶段,研发团队会与市场部门和客户进行沟通,了解市场需求和客户需求。
根据需求分析,确定新零部件的功能、性能、质量和成本等要求。
2. 概念设计阶段:在这个阶段,研发团队会进行初步的概念设计,包括制定产品的整体架构和功能模块,进行初步的性能分析和评估,制定产品的技术路线和开辟计划。
3. 详细设计阶段:在这个阶段,研发团队会对概念设计进行详细设计,包括制定产品的详细设计方案、绘制产品的详细图纸和工艺流程,进行材料选型和工艺选择等。
4. 零部件创造阶段:在这个阶段,研发团队会根据详细设计方案进行零部件的创造,包括原材料采购、零部件加工和组装等。
5. 零部件测试阶段:在这个阶段,研发团队会对创造完成的零部件进行各种测试,包括功能测试、性能测试、可靠性测试和安全性测试等。
6. 验证和认证阶段:在这个阶段,研发团队会对测试通过的零部件进行验证和认证,确保其符合相关的技术标准和法规要求。
7. 量产和市场推广阶段:在这个阶段,研发团队会将验证和认证通过的零部件进行量产,并进行市场推广和销售。
需要注意的是,汽车新零部件的开辟过程可能会因公司和产品的不同而有所差异,上述步骤仅为普通性的描述。
汽车零部件产品开发流程

汽车零部件产品开发流程一、需求分析阶段1.1 确定产品需求:确定新产品的类型、性能、规格等基本要求,以及市场需求和竞争对手情况。
1.2 市场调研:通过市场调研和用户反馈,收集相关信息,了解用户需求和市场趋势。
1.3 技术分析:对技术可行性进行评估,确定技术路线和方案。
二、设计阶段2.1 概念设计:根据需求分析结果,进行创意构思和方案设计,并绘制草图或模型。
2.2 详细设计:在概念设计的基础上,进行更加详细的设计工作,包括结构设计、材料选择等。
2.3 仿真验证:利用计算机辅助工具进行仿真验证,评估产品性能和可靠性。
三、开发阶段3.1 零部件制造:根据设计图纸或模型制造零部件,并进行质量检测。
3.2 组装调试:将零部件组装成整体产品,并进行调试和测试。
3.3 样品制作:制作样品并进行测试验证。
四、试产阶段4.1 试产准备:准备试产所需的设备、工具和人员等资源。
4.2 试产生产:进行试产生产,并进行质量检测和性能测试。
4.3 试产改进:根据试产结果,对产品进行改进和优化。
五、批量生产阶段5.1 工艺规程编制:制定产品的加工工艺规程,确保产品的一致性和稳定性。
5.2 生产准备:准备生产所需的设备、材料和人员等资源。
5.3 批量生产:进行批量生产,并进行质量检测和性能测试。
六、售后服务阶段6.1 售后服务准备:准备售后服务所需的设备、工具和人员等资源。
6.2 售后服务实施:对用户提出的问题进行解答和处理,并提供维修、保养等服务。
6.3 用户反馈收集:收集用户反馈意见,不断改进产品设计和售后服务。
七、总结汽车零部件产品开发流程是一个复杂而又漫长的过程,需要团队成员之间密切合作,充分利用各种技术手段,不断改进和优化产品设计。
通过以上流程可以使得汽车零部件产品开发更加科学化、规范化,从而提高产品质量和市场竞争力。
汽车零部件研发流程及APQP表单输出
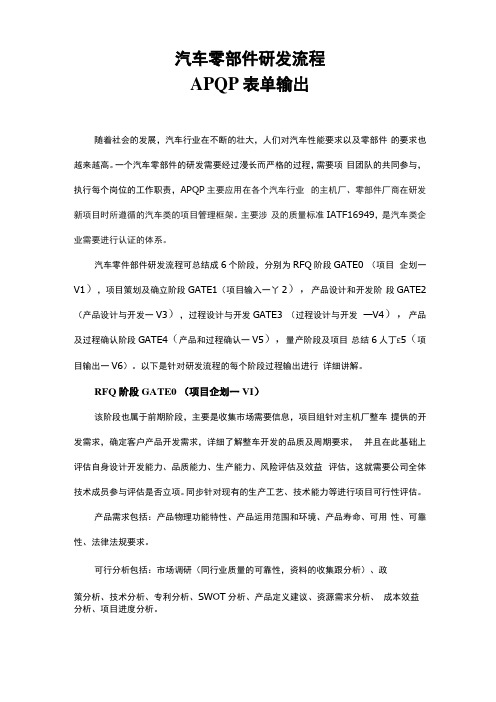
汽车零部件研发流程APQP表单输出随着社会的发展,汽车行业在不断的壮大,人们对汽车性能要求以及零部件的要求也越来越高。
一个汽车零部件的研发需要经过漫长而严格的过程,需要项目团队的共同参与,执行每个岗位的工作职责,APQP主要应用在各个汽车行业的主机厂、零部件厂商在研发新项目时所遵循的汽车类的项目管理框架。
主要涉及的质量标准IATF16949,是汽车类企业需要进行认证的体系。
汽车零件部件研发流程可总结成6个阶段,分别为RFQ阶段GATE0 (项目企划一V1),项目策划及确立阶段GATE1(项目输入一丫2),产品设计和开发阶段GATE2 (产品设计与开发一V3),过程设计与开发GATE3 (过程设计与开发—V4),产品及过程确认阶段GATE4(产品和过程确认一V5),量产阶段及项目总结6人丁£5(项目输出一V6)。
以下是针对研发流程的每个阶段过程输出进行详细讲解。
RFQ阶段GATE0 (项目企划一VI)该阶段也属于前期阶段,主要是收集市场需要信息,项目组针对主机厂整车提供的开发需求,确定客户产品开发需求,详细了解整车开发的品质及周期要求,并且在此基础上评估自身设计开发能力、品质能力、生产能力、风险评估及效益评估,这就需要公司全体技术成员参与评估是否立项。
同步针对现有的生产工艺、技术能力等进行项目可行性评估。
产品需求包括:产品物理功能特性、产品运用范围和环境、产品寿命、可用性、可靠性、法律法规要求。
可行分析包括:市场调研(同行业质量的可靠性,资料的收集跟分析)、政策分析、技术分析、专利分析、SWOT分析、产品定义建议、资源需求分析、成本效益分析、项目进度分析。
关键输出物:《客户项目信息表》、《客户技术资料》、《客户样件》、《客户需求表》、《成本策划分析表》、《项目可行性分析报告》项目策划及确立阶段GATE1(项目输入一丫2 )根据客户的整车开发需求,如产品物理和功能特性、产品应用范围和环境、产品寿命、可靠性、可用性、产品法规要求、试验要求、性能要求等制定产品开发计划表、新产品的需求定义表来明确产品在设计开发过程的输入整车或系统及参数需求。
汽车部件新产品开发流程

工艺工程师
车间主任
质量工程师
模具工程师
39
Flow Chart
团队
参加部门:技术、质保、生 产、市场、采购
1、配光要求 2、零部件间的配合 3、生产治具与产品 的配合 4、检具的作用 5、生产条件的合理性
工作定时 汇报
评审怎么样?有哪些方面的问题( 成本、资金、时间、人力……)需
要我来沟通?
Flow Chart
OK
依据公司之前类似产品 开发经验、技术能力
NG
形成书面文档
可行性评估报告 产品建议书
初使零部件清单
初使过程流程图
采购文件草案
初使产品/过程特殊特性清单
Flow Chart
5
风险评估
开发时间
效益评估
设计能力 开发能力
生产能力
品质能力
工作定时 汇报
评审怎么样?有哪些方面的问题( 成本、资金、时间、人力……)需
PROJECT
12
Flow Chart
Customer
项目小组成立
星宇车灯
R&D
R&D
Q.C.
Project manager
Project Project manager Leader
Q.C.
Purchase
Purchase
正向设计
形成书面文档
设计不良模式分析
产品试验大纲
Flow Chart
要我来沟通?
Flow Chart
7
供应商
FOURNISSEUR
开发周期 产品价格
产品质量
报价
主 机 厂 采购部
CONSTRUCTEUR 分析&选择
(精确版)汽车零部件进货检验验收流程

(精确版)汽车零部件进货检验验收流程精确版汽车零部件进货检验验收流程1. 验收准备1.1 确认采购订单和供应商信息,确保零部件的规格、型号、数量等与订单一致。
1.2 查阅相关技术文件,包括零部件的图纸、技术要求、检验标准等。
1.3 准备必要的验收工具和设备,如卡尺、千分尺、显微镜等。
2. 外观检查2.1 检查零部件的外包装是否完好无损,确认包装上的标识是否清晰可见。
2.2 拆开包装,检查零部件的外观质量,包括表面是否有划痕、变形、锈蚀等缺陷。
2.3 对有特殊要求的零部件进行尺寸测量,确保其符合技术文件规定的要求。
3. 功能检验3.1 对具有功能的零部件进行功能测试,如汽车发动机的运行性能、刹车的制动效果等。
3.2 记录测试结果,与技术文件中的要求进行对比,确保零部件的功能正常。
4. 尺寸检验4.1 使用卡尺、千分尺等工具对零部件的尺寸进行测量,包括长度、宽度、厚度等。
4.2 记录测量结果,与技术文件中的要求进行对比,确保零部件的尺寸符合规定。
5. 材质检验5.1 对零部件的材质进行检验,如钢铁、塑料、橡胶等。
5.2 采用光谱分析、硬度测试等方法对材质进行检测,确保零部件的材质符合技术文件要求。
6. 包装检验6.1 检查包装是否符合规定的要求,包括包装材料、包装方式、标识等。
6.2 确认包装内的零部件数量是否与订单一致。
7. 记录与反馈7.1 将验收过程中的各项检验结果进行记录,填写在验收记录表中。
7.2 对验收不合格的零部件进行标记,并及时反馈给供应商,要求其进行处理。
8. 合格判定8.1 根据验收记录,对零部件进行合格判定,符合所有检验要求的零部件视为合格。
8.2 对合格的零部件进行入库或发货处理。
9. 持续改进9.1 对验收过程中发现的问题进行总结,分析原因,并提出改进措施。
9.2 定期对验收流程进行审核,确保其有效性和可靠性。
以上是精确版汽车零部件进货检验验收流程,供您参考。
汽车零部件产品开发流程

汽车零部件产品开发流程一、市场调研:在进行零部件产品开发之前,首先需要进行市场调研,了解市场需求和竞争对手的产品情况。
通过市场调研,可以收集到与产品相关的信息,为后续的产品设计和开发提供参考。
二、产品规划:根据市场调研的结果,制定产品规划,明确产品的定位、功能、性能等要求。
同时,还需考虑到成本、工艺、适用车型等方面的因素。
三、产品设计:在产品设计阶段,需要进行结构设计、工艺设计、材料选择等工作。
结构设计是指确定产品的整体结构和各个零部件的布置方式,工艺设计是指确定产品的加工工艺和制造流程,材料选择是根据产品的要求选择适合的材料。
四、工程开发:在产品设计确定后,需要进行工程开发工作。
工程开发包括制造工艺开发、生产设备选型、生产工艺设计等工作。
这些工作是为了保证产品能够顺利投产,达到设计要求。
五、样品试制:完成工程开发后,需要进行样品试制。
样品试制是为了验证产品的设计和工程开发是否符合要求。
在样品试制过程中,需要对样品进行测试和调试,以确保产品的质量和性能。
六、测试验证:在样品试制完成后,需要进行测试验证。
测试验证主要包括性能测试、可靠性测试、耐久性测试等。
通过测试验证,可以评估产品的性能和质量,并对产品进行改进和优化。
七、小批量生产:测试验证通过后,可以进入小批量生产阶段。
小批量生产是为了进一步验证产品的生产能力和质量控制能力。
在小批量生产过程中,需要对生产工艺进行调整和优化,并进行生产检验和质量控制。
八、大规模生产:小批量生产通过后,可以进入大规模生产阶段。
大规模生产需要建立起完善的供应链体系和生产管理体系,以保证产品的稳定性和交货能力。
九、产品投产:在经过大规模生产验证后,产品可以正式投产。
产品投产需要进行生产计划制定、生产组织和调度等工作。
经过产品投产后,产品将进入市场供应阶段。
综上所述,汽车零部件产品开发流程是一个较为复杂的过程,需要经历市场调研、产品设计、工程开发、样品试制、测试验证、小批量生产等多个环节。
汽车部件产品确认流程阶段

汽车部件产品确认流程阶段汽车部件产品确认流程是指在汽车制造过程中,对汽车部件进行确认和验证的一系列流程和步骤。
这个流程的目的是确保汽车部件的质量和性能符合设计要求,并在车辆生产前得到验证和确认。
本文将详细介绍汽车部件产品确认流程的各个阶段。
第一阶段,设计确认汽车部件产品确认流程的第一阶段是设计确认阶段。
在这个阶段,汽车部件的设计师和工程师会根据汽车制造商的需求和规范进行设计和开发。
设计确认阶段的目标是确保汽车部件的设计满足设计要求和标准。
设计师和工程师会进行详细的设计评审和仿真分析,以确保部件在使用过程中的可靠性和耐久性。
他们还会进行实验室测试和原型验证,以验证设计的正确性和性能。
一旦设计被确认,产品开发团队将进入下一个阶段。
第二阶段,原型制造和验证在设计确认阶段完成后,汽车部件的原型制造和验证阶段开始。
在这个阶段,制造商会根据设计图纸和规范制造汽车部件的原型。
制造过程严格遵循相关的质量控制标准和制造工艺。
制造的原型将经过一系列的实验室测试和验证。
这些测试包括材料测试、功能测试和性能测试。
目的是验证原型的质量和性能是否满足要求。
一旦原型通过验证,制造商将进入下一个阶段。
第三阶段,小批量生产和评估原型通过验证后,汽车部件进入小批量生产和评估阶段。
在这个阶段,制造商将制造一定数量的部件进行实际的车辆安装和使用测试。
这些部件将安装到预生产车辆中,以检查其在实际工作条件下的性能和可靠性。
制造商还会进行一些额外的测试和评估,包括耐久性测试、遗忘性测试和可靠性评估。
目的是进一步验证部件的质量和性能,并确定是否需要进行进一步的改进和调整。
第四阶段,大规模生产和验证在小批量生产和评估阶段验证通过后,汽车部件将进入大规模生产和验证阶段。
在这个阶段,制造商将大量生产汽车部件,以供车辆生产线使用。
在生产过程中,制造商会严格遵守质量管理体系和标准操作程序,确保产品的一致性和质量。
制造商还会进行一系列的验证和审核,包括外观审核、尺寸检测、功能测试和寿命测试等。
汽车零部件开发流程5个阶段

汽车零部件开发流程5个阶段1 研发需求分析汽车零部件开发的前期阶段是研发需求分析,主要包括了客户需求分析、市场研究分析以及本次零部件开发项目工作计划的制定。
首先,进行客户需求分析时,主要研究汽车零部件在使用中的工作特征,掌握零部件在使用时的特殊要求,筛选适合的材料以及成型方法;其次,根据市场信息对汽车零部件已有的发展状况进行全面分析,发现市场空白、竞争者已有的解决方案以及国外相关产品,从而帮助开发者更好地把握研发方向;最后,根据研发进度安排信息,建立好研发项目的时间管理表,此外,还需制定本次零部件开发项目的实施和进度细则,为整个研发流程提供指导。
2 设计方案拟定研发需求分析完成之后,可以进入设计方案的拟定,主要根据零部件的技术参数和表面上的要求,进行模具设计方案的拟定,形成设计图纸以及主要的画板设计元素模式,同时,还要对本次模具设计的操作工艺进行分析,制定设计操作方式以及判断设计所需要达到的标准要求。
拟定完设计方案后,即可进行投资计算,根据设计后面的制作、使用以及维修成本进行分析,以确立设计方案的可行性。
3 模具设计拟定好设计方案之后,可以进入模具设计阶段,根据设计方案,开始进行模具三维设计,使用可视化设计软件来实现一系列的设计,从而最终得出本次模具的设计图纸。
考虑到模具开发的复杂性,在设计过程中,要进行多次的模拟,使用模拟软件来进行模具行为记录。
模具设计完成之后,还要结合生产工艺,做出本次模具的操作说明书,为后期的实际生产提供参考指导。
4 模具验证模具设计完成之后,可以进入模具验证,这一阶段一般采用节点及全局验证的方式分别验证零部件以及模具的输出结果,并对零部件的尺寸、精度以及形状等进行检验,以确认模具的高效能与精度。
在模具验证阶段,还要对模具的工作效率、生产质量以及使用寿命等做出分析,以保证成品中不会存在质量问题。
5 模具制作模具最后的步骤为模具制作,模具制作主要包括模具三维样板制作、零部件金属加工等项目。
汽车零件新产品导入流程

汽车零件新产品导入流程英文回答:The process of introducing new automotive parts involves several steps, and it is crucial to ensure a smooth and efficient flow. Here, I will outline the general process for importing new car parts.Firstly, the process begins with identifying the need for a new car part. This could be due to a market demandfor a specific feature or an improvement in the existing component. For example, if there is a growing demand for electric vehicles, the need for advanced battery technology may arise.Once the need is identified, the next step is to conduct thorough research and development. This involves designing and testing the new part to ensure its compatibility, performance, and safety. For instance, if a car manufacturer wants to introduce a new type of brakesystem, extensive testing will be conducted to ensure its reliability.After the research and development phase, the next step is to find suitable suppliers for the new car part. This involves sourcing and evaluating potential suppliers based on their quality, cost, and delivery capabilities. Negotiations and contracts will be established with the chosen supplier to ensure a steady supply of the new part.Once the supplier is finalized, the next step is to integrate the new part into the existing manufacturing process. This requires coordination between the supplier and the car manufacturer to ensure a seamless integration of the new part. For example, if a new engine component needs to be integrated, the manufacturing process may need to be adjusted accordingly.Following the integration, the new car part will undergo rigorous testing and quality control to ensure its performance meets the required standards. This includes conducting various tests such as durability, reliability,and safety tests. Only after passing these tests will the new part be approved for mass production.The final step in the process is the mass productionand distribution of the new car part. This involves setting up the necessary production lines and ensuring a smooth supply chain to deliver the new part to the car assembly plants. The new part will then be installed in the vehicles during the manufacturing process.In conclusion, the process of introducing newautomotive parts involves identifying the need, conducting research and development, sourcing suitable suppliers, integrating the new part, testing and quality control, and finally, mass production and distribution. This process ensures that the new car part meets the required standards and is seamlessly integrated into the manufacturing process.中文回答:汽车零件新产品导入流程涉及多个步骤,确保流程的顺畅和高效非常重要。
汽车制造PPAP认可流程
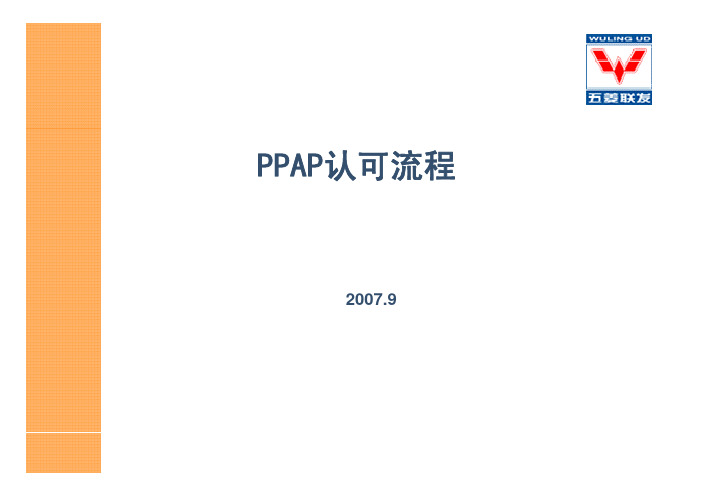
人事处
二00七年四月
PFMEA
2121
供方必须按照QS-9000第三版制定PFMEA 同一份PFMEA可以适用于相似的零件或材料的工艺过程
人事处
表格
二00七年四月
控制计划
2222
供方必须按照QS-9000第三版的要求制定控制计划
控制计划必须与过程流程图、PFMEA一一对应
如果对新零件的共通性以及通过评审,可以使用类似
人事处
表格
二00七年四月
零件尺寸检验计划
1717
z尺寸检验计划应事前获得我司SQE、PE的认可;
z对于适用一般量具用的检验计划,各尺寸都需标明公差,量具标明类别 型号,附图必须清晰;
z如果采用一个以上的型腔、铸模、冲模、工装或加工设备、生产单元、 生产线的过程设计,必须从每一部分的PPAP产品都需要提交一份测量计 划(需要时)
概括:验证供应商的生产过程是否具有能力来生产满足顾 客要求的产品
人事处
二00七年四月
适用范围
44
必须进行PPAP认可:
一种新的零件或产品(如:以前从未提供给指定顾客 的特殊零件、材料,或颜QE根据实际情况决定是否需要供方通过PPAP:
a.对与以前不合格处进行修正提交的零件; b.由于工程设计、设计规范或材料的改变而发生的产品变化。 c.和以前批准的零件或产品相比,使用了其它不同的结构或材料; d.使用新的或改进的工装(不包括易损工装)、模具、铸模、模型等,包括附加的或替换用的工装; e.在对现有的工装或设备进行翻新或重新布置之后进行生产 f.生产是在工装和设备转移到不同的工厂或在一个新增的厂址进行的; g.分承包方对零件、非等效材料或服务(如热处理、电镀)的更改,从而影响顾客的装配、成型、功能、耐久性
- 1、下载文档前请自行甄别文档内容的完整性,平台不提供额外的编辑、内容补充、找答案等附加服务。
- 2、"仅部分预览"的文档,不可在线预览部分如存在完整性等问题,可反馈申请退款(可完整预览的文档不适用该条件!)。
- 3、如文档侵犯您的权益,请联系客服反馈,我们会尽快为您处理(人工客服工作时间:9:00-18:30)。
T1: 1.设备程序的设计确认 2.部品外观外形评价
T2: 1.部品尺寸精度确认,检 具配合确认 2.全制造工程确认评价
T3: 1.部品表面处理确认评价 2.全部量产设备制作评价 3.生产线制作的确认评价 4.部品品质综合评价 对应设备: 1.量产设备 2.量产发泡模具 3.量产生产线
LOT1: 1.正式生产线小批量试 作的部品品质评价 2.正式生产线的生产设 备的评价
T3: 1.量产设备模具试作评价 2.量产设备工艺确定 3.部品品质综合评价
LOT1: 1.正式生产线小批量试 作的部品品质评价 2.正式生产线的生产设 备的评价
使用道具
对应设备: 1.量产模具 2.临时发泡设备
对应设备: 1.量产模具 2.临时发泡设备 3.实验测试设备
对应设备: 1.量产设备 2.量产发泡模具 3.量产生产线
T3: 1.部品表面处理确认评价 2.量产冲压焊接设备评价 3.量产模具夹具综合评价 4.部品品质综合评价 对应设备: 1.量产冲压和焊接设备 2.所有量产模具 3.检具和量产焊接夹具 使用资料: 1.图纸和3D、DATA 2.品质安定化表 3.检查成绩表
量产生 产线综 合评价
LOT1: 1.正式生产线的量产模 具夹具评价 2.正式生产线的部品品 质确认评价
T2
·非正式生产线制作 ·量产的生产工序 ·临时检查设备 ·可手工修正(树脂、焊接) ·无手工修正(电气部品) ·场所-模具厂/供应商 1. 部品尺寸精度确认,检具 配合确认 2. 成型工艺确定
T3
·生产线上制作/人工在生 产线上制作 ·量产检查设备 ·无手工修正 ·线上组装 ·场所-模具厂/供应商 1. 部品蚀纹前评价 2. 量产设备成型综合评价
使用资料: 1.图纸和3D、DATA
使用资料: 1.图纸和3D、DATA 2.品质安定化表 3.检查成绩表 4.失效模式分析表
海绵部品确认方法
评价阶段 制作日程
认证 E段 段确
段确对应
品确
品确对应
量确
量产
设定开 发部品
规格发放
图纸规 格确认
模具日本日 本设计制作
T0品
E段T1 品
T2品
T3品
LOTI
品确对应
量确
量产
设定开发 部品
规格发放
图纸规 格确认
模具日本日 本设计制作
T0品
E段T1品
T2品
T3品
T4品 LOT1
量产水平 部品确认
评价项目
模具设 计确认 组立治具 功能确认 全部组立 工序确认 组立工具和 工序确认
卓纹评价或 小批量评价
具体内容
T0: 1.模具的设计确认 2.组立设计构想确认
T1: 1.组立治具的功能确认 2.QA 机器的设计确认
对应设备: 1.量产设备 2.正式量产生产线
使用资料: 1.图纸 2.品质安定化表 3.失效模式分析表
使用资料: 1.图纸 2.品质安定化表 3.检查成绩表 4.失效模式分析表
使用资料: 1.图纸 2.品质安定化表 3.检查成绩表
使用资料: 1.国产化部品确认报告
管、线材品确Байду номын сангаас方法
评价阶段 制作日程
具体内容
T0: 1.表皮材的仕样设计确认
T1: 1.表皮材的车缝性能确认 2.座椅总成评价表皮的色 调、外观、毛向(纹理) 3.材料物理性能确定
T2: 1.表皮材的车缝性能确认 2.座椅总成评价表皮的色 调、外观、毛向(纹理) 3.材料物理性能确定 对应设备: 1.量产设备 2.临时生产线(现地) 3.评价用座椅(现地试作)
使用道具
对应设备: 1.量产设备(切断和折弯) 2.临时设备(接合及组立 治具)
对应设备: 1.量产模具 2.临时发泡设备 3.实验测试设备
对应设备: 1.量产模具 2.量产发泡设备
对应设备: 1.量产设备 2.量产模具 3.正式量产生产线
使用资料: 1.图纸和3D、DATA
使用资料: 1.图纸和3D、DATA 2.品质安定化表 3.失效模式分析表
T2: 1.部品尺寸精度确认评 价 2.部品的功能确认评价 3.QA机器的功能确认 4.部品制造的工序确认 对应设备: 1.量产治具和设备 2.量产模具 3.量产3QA机器 使用资料: 1.图纸和3D、DATA 2.品质安定化表 3.检查成绩表 4.失效模式分析表
T3: 1.需蚀纹部品蚀纹前评价 2.量产的组立工具和工序的 确认评价 3.组立人员的培训确认 对应设备: 1.量产治具、设备和QA 机 2.量产模具 3.量产的组立工具 使用资料: 1.图纸和3D、DATA 2.品质安定化表 3.检查成绩表 4.皮纹CD指示书
设定开 发部品
规格发放
认证
E段
段确
段确对应
品确
品确对应
量确
量产
图纸规 格确认
模具日本日 本设计制作
T0品
E段T1 品
T2品
T3品
LOTI
量产水平 部品确认
评价项目
设备程 序设计 确认 程序对 制造工 程确认 尺寸精 度和组 立效果 正式产线 综合品质 评价 小批量 生产综 合评价
具体内容
T0: 1.设备程序的设计确认
部品各阶段素性
评价阶段 模具熟成 水平 评价项目
认证 段确 品确 量确 量产
T0品
T1品
T2品
T3品
T4品
模具配合及 成形性
样品外观 尺寸
装配性确认
复合品 质确认
最终效 果确认
安全宣言
品熟水平
T0
·非正式生产线制作 ·临时生产工序 ·临时检查设备 ·允许手工修正 ·场所-模具厂/供应商
T1
·非正式生产线制作 ·临时生产工序 ·临时检查设备 ·场所-模具厂/供应商
冲压件
1. 模具的结构设计确认2. 落料模具为制作 3. 采用线切割进行落料
1. 部品尺寸精度确认,检具 配合确认 2. 落料模具完成并平静 3. 全制造工程确认评价
1. 部品表面处理确认评价 2. 量产冲压焊接设备评价 3. 量产模具夹具综合评价 4. 部品品质综合评价
1. 正式生产线的量产模 具夹具评价 2. 正式生产线的部品品 质确认评价
对应设备: 1.量产设备 2.量产模具 3.正式量产生产线
使用资料: 1.图纸和3D、DATA
使用资料: 1.图纸和3D、DATA 2.品质安定化表 3.失效模式分析表
使用资料: 1.图纸和3D、DATA 2.品质安定化表 3.检查成绩表 4.失效模式分析表
使用资料: 1.图纸和3D、DATA 2.品质安定化表 3.检查成绩表
量产水平 部品确认
评价项目
模具的 配合性 确认 部品的 外观外 形评价 尺寸精 度和组 立效果 正式产线 综合品质 评价 小批量 生产综 合评价
具体内容
T0: 1.模具的配合性确认
T1: 1.部品的断面尺寸确认 2.部品的外观外形评价 3.部品材料的SPEC确认
T2: 1.部品尺寸精度确认评价 2.发泡工艺设定确认 3.组立性以及座椅总成外 观评价 对应设备: 1.量产模具 2.量产发泡设备
使用道具
对应设备: 1.临时成型机 2.量产模具
对应设备: 1.临时成型机 2.量产模具 3.检具和夹具 使用资料: 1.图纸和3D、DATA 2.品质安定化表 3.检查成绩表 4.失效模式分析表
对应设备: 1.量产成型机 2.量产模具 3.检具和夹具 使用资料: 1.图纸和3D、DATA 2.品质安定化表 3.检查成绩表 4.皮纹CD指示书
对应设备: 1.量产成型机 2.量产模具
使用资料: 1.图纸和3D、DATA
使用资料: 1.图纸和3D、DATA 2.品质安定化表 3.检查成绩表 4.失效模式分析表
使用资料: 1.皮纹标准版 2.皮纹CD报告书 3.国产化部品确认报 告
电气部品确认方法
评价阶段 制作日程
认证 E段 段确
段确对应
品确
使用资料: 1.国产化部品确认报告
冲压部品确认方法
评价阶段 制作日程
认证 E段 段确
段确对应
品确
品确对应
量确
量产
设定开 发部品
规格发放
图纸规 格确认
模具日本日 本设计制作
T0品
E段T1品
T2品
T3品
LOT1
量产水平 部品确认
评价项目
模具的 结构设 计确认 生产制 造工程 确认 尺寸精 度和组 立效果 试作品 综合品 质评价
使用资料: 1.图纸和3D、DATA 2.品质安定化表 3.检查成绩表 4.失效模式分析表
使用资料: 1.图纸和3D、DATA 2.品质安定化表 3.检查成绩表
使用资料: 1.国产化部品确认报告
树脂部品确认方法
评价阶段 制作日程
认证 E段 段确
段确对应
品确
品确对应
量确
量产
设定开发 部品
规格发放
图纸规 格确认
模具日本日 本设计制作
T0品
E段T1 品
T2品
T3品
T4品
量产水平 部品确认
评价项目
模具配合及 成型性 样品外 观尺寸 同制造确 立组立性 同品质课确 认整体性能
T3: 1.部品蚀纹前评价 2.量产设备成型综合评价
T4/LOT1: 1.蚀纹部品蚀纹后评 价并得到客户承认 2.小批量试作部品品 质的综合评价
使用道具
对应设备: 1.临时治具 2.量产模具 3.临时设备
对应设备: 1.临时治具和设备 2.量产模具 3.临时治具
对应设备: 1.量产治具、设备和 QA 机 2.量产模具 3.量产的组立工具 使用资料: 1.皮纹标准版 2.皮纹CD报告书 3.国产化部品确认报 告