精益改善报告
精益生产项目改善报告模板

时间
% 完成
备注
Note: • 请包括改善项目在研讨会结束后需要跟踪的行动措施. • 工厂精益领导对此表的行动措施担负追踪推动责任. • 精益领导从此表中选择需要在其他工厂/生产线推广的措施,并推动实施。
25% Complete 50% Complete
75% Complete 100% Complete
责任人
目标完成日期
时间 计划
结束
% 完成百分比
备注
25% Complete 50% Complete
75% Complete 100% Complete
改善活动中学到的经验教训和知识工具
序号 1 2 3 4 5 6
知识工具/经验教训
描述
改善日志 – 持续推广的提案
持续推广提案I
责任人
目标完成日 期
运营单元 / 工位
问题
措施
指标/(单位) 改善前
结果
改善后
% 提高
客户
节约
持续保持的 方法
硬节约(金 额/每月)
软节约(金 额/每月)
照片-改善前
照片-改善后
标题:
子标题3:XXXX (该改善项目包含的独立子改善项目)
运营单元 / 工位
问题
措施
指标/(单位) 改善前
结果
改善后
% 提高
客户
节约
持续保持的 方法
标准化作业表 – 改善前:
标准化作业表 – 改善后
标准化作业表 – 改善后:
作业员平衡图 – 改善前
作业员平衡图 – 改善前:
作业员平衡图 – 改善后
作业员平衡图 – 改善后:
设备平衡图 – 改善前
设备平衡图 – 改善前:
精益改善报告完整版PPT课件
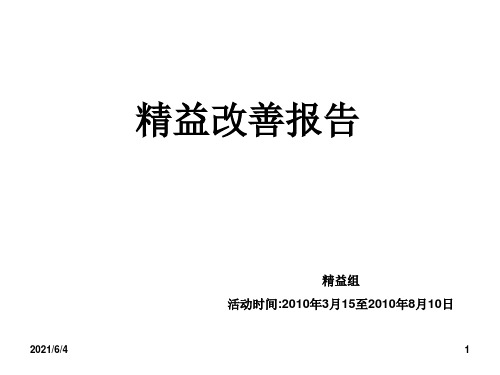
珠海市俊凯机械有限公司
改善前物料摆放
两种产 品混料
成品摆 放混乱
产品上 还有废
屑
2021/6/4
报废品 无指定 摆放区
域
物料 放置 不清
晰
不良品 放置在 成品架
上
不良品 放置在 产品放 置盒中
35
珠海市俊凯机械有限公司
产品摆 整齐 能很快 找到物
料
2021/6/4
时间:秒u
节拍:180
150
100
50
0
1
2
改善前生产一个产品所需的 时间为1233秒
2021/6/4
改善前生产一个产品所需的 时间为180秒
21
珠海市广浩捷精密机械有限公司
序号
1 2 3 4 5
6
改善内容
46302011ACG生产线 岗位及人员的确定 员工技能表的建立 现场的目视化管理建立
生产周期提升了50% 生产效率提升了50%
目标 50%
改善前 60分钟
207
1319 13 10
改善后 40分钟
138
2400 2 2
总提升 33%
33%
82% 85% 80%
2021/6/4
11
珠海博杰电子有限公司
• 改善中出现的问题:
• 1.物料难以找到 • 2.没有管理者关注生产线 • 3.员工的心态没有人引导 • 4.线内管理者缺失 • 5.物料关注的问题少 • 6.员工的工具没有地方存放,导致工具丢失 • 7.专门物料员没有配置给生产线 • 8.出现品质问题,四处找人,没有品管巡线
2021/6/4
效果确认:生产工序严格按单件流,从而使 物流间/工序间库存是零,减少库存浪费等 问题,异常情况下,使问题立即暴露,把问 题立即解决…
仓库精益改善亮点总结汇报

仓库精益改善亮点总结汇报仓库精益改善亮点总结汇报一、引言近年来,仓储行业竞争加剧,仓库企业面临着提高运营效率和降低成本的挑战。
为了应对这一挑战,本公司积极推行精益改善,通过优化流程和提升员工技能,取得了显著的改善效果。
本报告将总结仓库精益改善的亮点,并展示改善效果。
二、精益改善亮点1. 价值流图优化本公司通过制作价值流图,全面梳理了仓库各项流程。
我们发现了诸多非价值增加的环节和浪费,例如库存过多、物料堆放不合理等。
在此基础上,我们制定了一系列改善措施:调整物料放置位置,优化放货和拣货流程,减少重复工序等。
通过这些措施,我们降低了仓库运营成本,提高了效率。
2. 5S管理实施本公司引入了5S管理方法,通过整理、整顿、清扫、清洁、素养五个步骤,使仓库环境整洁有序。
我们建立了标准化的储物位置、标识和标牌,使得物料存放更加规范,员工可以快速找到所需物料。
通过5S管理,我们提高了工作效率,减少了错误率。
3. Kaizen活动推行我们积极推行Kaizen(改善活动),通过员工的创新意识和改善能力,不断寻找和解决问题。
我们建立了一个改善建议箱,鼓励员工积极提出改善意见,并给予相应的奖励。
通过这些改善活动,我们解决了许多小问题,优化了工作流程,提高了工作质量。
4. 人员培训提升为了提升员工的职业素养和技能水平,我们定期组织培训,并加强岗位责任意识培养。
我们鼓励员工参与外部培训,并为取得认证的员工提供晋升机会。
通过这些培训措施,我们增强了员工的综合素质,减少了人力资源浪费,提高了工作效率。
5. 数据驱动改进我们引入了数据分析工具,对仓库的运营情况进行全面的监测和分析。
通过对数据的持续分析,我们发现了许多潜在的问题和改进点,并制定了相应的改进措施。
通过数据驱动的改进,我们能够更加准确地评估改进效果,并及时调整措施。
三、改善效果展示在精益改善的推行下,本公司取得了显著的改善效果。
以下是一些具体数据的展示:1. 准时交货率提高了10%通过优化放货、拣货流程和减少重复工序等措施,我们的准时交货率提高了10%,有效地提升了客户满意度。
精益改善案例提案改善报告

精益改善案例提案改善报告一、背景我们所处的公司是一家生产化妆品的企业,由于市场竞争激烈和内部管理不足等多种原因,导致生产效率低下,产品质量不稳定,在市场上的竞争力较弱。
为此,我们决定通过精益管理的方法来对生产过程进行改善,提高生产效率和产品质量,以增强企业的市场竞争力。
二、问题定义通过对企业生产过程的分析,我们发现以下问题:1. 生产过程中存在大量浪费,如原料浪费、等待时间浪费、生产线下停机时间浪费等,导致生产效率低下;2. 生产线某些工站出现了制造不良品的情况,存在质量问题;3. 生产过程中缺乏可视化管理,员工难以及时发现和解决问题。
三、改善方案针对上述问题,我们提出以下改善方案:1. 实施6S管理6S管理是指整理、整顿、清洁、清点、标准化和维护的管理方法,通过对现场进行整理、清理、标识等操作,去除生产过程中的浪费,提高生产效率。
同时,开展6S培训,增强员工的职业素养和安全意识,营造整洁有序的工作环境,提高工作效率和生产质量。
2. 引入可视化管理针对生产过程中缺乏可视化管理的问题,我们将引入可视化管理技术,将生产过程中的各项数据实时呈现在生产线上方的显示屏上,让员工随时了解生产状况,更好地发现和解决问题。
3. 实施质量管理和问题解决在生产过程中,存在不良品生成的情况,我们将加强质量管理,对生产过程中的各项质量参数进行监控和检测,及时发现和解决问题。
同时,我们将建立定期例会和工作汇报机制,及时解决员工工作中遇到的问题,为员工提供更好的工作支持。
四、实施计划通过培训,将6S管理理念传递至员工,开展整理、整顿、清洁等活动,打造整洁有序的生产环境,提高生产效率和产品质量。
引入并实施可视化管理系统,打造实时监控的全新生产模式,加强员工生产意识和工作效率,实现生产流程信息和数据的可视化和透明化。
五、效果预期通过精益管理的方法,我们期望实现以下效果:1. 生产效率提高:通过实施6S管理和改善流程,去除浪费,提高生产效率,降低生产成本。
精益生产:公司生产效率提升改善项目报告

4.18-4.24
17715 2722 15.4% 1652 6.04% 1071
4.25-5.1
11144 2123 19.0% 1514 5.46% 608
前加工中心
5月份
65031.5 8077.16 12.42% 5793.27 3.51% 2283.89
6.1-6.12
18645 2479 13.3% 1907 3.07% 572
54229.5
线外人员出勤
3298 457 488 1528 3595.5 9366.5
UPPH 151.98 35.15 39.78 76.96
2.70 345.67
数据分析 基准值 129.30 29.97 35.21 66.33
2.30
提升比率 17.54% 17.28% 12.98% 16.02% 17.56%
328538.52
37209.5
8.83
7.8
1088694.42 841336.91 509796.65
81991 64921.4 41975.5
13.28 12.96 12.15
11.01 11.97 10.62
3654017.88
310486.4
11.77
10.4
提升比例
8.71% 7.41% 13.20% 20.60% 8.26% 14.36%
5.下阶段工作计划
编号
工作计划
1
AGV小车的具体导入实施方案
2
异性插件机的导入实施方案
3
筒灯自动化线方案确认
4
二分厂细胞拉效率持续提升
5
环保生物科技燃料导入
6
披锋自动化设备导入
生产改善报告

生产改善报告过去一年,我公司致力于提高生产效率和质量,通过一系列的改进措施和创新实践,取得了显著的成果。
以下是我们的生产改善报告,向大家介绍我们在不同方面所取得的进展和成就。
1. 制造流程优化为了提高产品的制造效率和质量,我们对制造流程进行了全面的优化。
首先,我们进行了价值流映射,通过识别和消除浪费,缩短了生产周期。
我们实施了精益生产,并优化了供应链管理,使原材料供应和产品出货更加快捷和准确。
此外,引入了自动化技术和先进的设备,提高了生产线的效率和灵活性。
2. 品质管理提升质量是我们公司的核心竞争力之一。
为了提升产品的质量水平,我们采取了一系列的措施。
首先,我们建立了严格的品质控制体系,从原材料的采购到成品的出货,每个环节都有相应的检查和测试。
我们还加强了员工的质量意识培养,每个员工都参与到质量管理中来,形成了全员参与的质量文化。
同时,我们与供应商进行了密切合作,确保原材料的质量和稳定供应。
3. 环境友好型生产在推动生产改善的同时,我们坚持了环保可持续发展的理念。
我们实施了清洁生产,减少了废品和废水的产生,采用了环保的生产工艺和材料。
我们优化了能源利用,提高了资源的利用效率,降低了能源消耗和碳排放。
此外,我们加强了对员工环境意识的培养,提供了安全和健康的工作环境。
4. 创新与研发为了保持市场竞争力,我们不断进行创新和研发。
我们成立了研发中心,招募了一批高素质的研发人员,开展了一系列的研究项目。
在产品研发方面,我们引入了最新的技术和材料,改进了产品的性能和功能。
在工艺研发方面,我们开发了新的生产工艺和装备,实现了产品制造的高效和灵活。
我们还与国内外的科研机构和大学合作,共同推动技术创新。
5. 绩效评价和持续改进为了评估生产改善的效果和推动持续改进,我们建立了绩效评价体系。
我们通过设置关键绩效指标和目标,对各个环节的表现进行定量化评估和分析。
我们每月举行生产改善会议,收集员工的改进建议和意见。
根据评估结果和反馈意见,我们制定了相应的改进计划,并不断优化和调整。
精益管理改善总结报告

精益管理改善总结报告精益管理的核心内容是:减少浪费、降低成本、提高效率、持续改善、提升满意度。
精益管理不同于如绩效管理、目标管理,精细管理等其它的管理理论和方式,它以识别管理中的浪费并持续地减少浪费为核心思想,通过一系列的方法和工具来定义管理中的问题,测量浪费,分析浪费产生的时间、区域、过程和原因,进而获得系统的减少浪费的方法,并使改进措施标准化来实现管理效率的提高。
精益改善遵从以下基本原则:1、打破固有观念以前正确的,现在未必正确;现在正确的,未来未必正确。
所谓“当局者迷,旁观者清”,从原有的工作观念中跳出来,用旁观者的眼光、站在高处审视自己的工作理念和工作流程,也许就会发现不合理之处,也就有了改善的切入点。
2、寻找可行的方法有了改善的切入点后,接下来就是如何开展改善活动。
在自己面前也许有多种方法和理念,但是通过全面分析以后要选择一条可行的路径,开展改善。
3、不要分辨,要否定现状“吾日三省吾身”,没有人提建议,也要每日自省。
如果有他人给自己提出了改善的建议,更要尽量接受,不要去分辨,要先审视自身工作理念、方法、流程,找出问题所在,即使没有问题,对自己做一次全面检查也无害。
4、不要力求完美,50分也好,立即实施想到了对自身工作有利的改善点后就要立即实施,哪怕实施后效果并不那么完美,但是只有实施了,才知道方法是否可行,才知道向何方改善。
5、错了马上改善如果确实是自身工作理念、方法、流程出现了问题和错误,那就要马上改善,耽误一秒钟就要产生一秒钟的浪费。
6、先从不花钱的改善做起改善的最终目的是减少浪费、提升企业竞争力,毋庸置疑,改善方法本身也一定要“够节俭”,尽量不花钱,否则改善获得的成果就会被改善方法的浪费无情地削减。
7、穷则变,变则通“山穷水尽疑无路,柳暗花明又一村”,当我们面前只有两条路:死亡或者改变,无疑,聪明的人会毫无迟疑地选择改变,因为改变了才有生存下去的希望和可能。
当我们在谷底时,无论往哪一个方向走,只要走,我们的高度都比谷底要高,只要改变了,往往就会获得意想不到的收益,8、最求根源,反复五次为什么改善要立即实施,也要追求问题的根本原因,正所谓“有的放矢”,排除假因获得真因,才能够以最高的效率获得改善预期的效果。
精益示范线项目计划与改善报告

精益示范线项目计划与改善报告1. 项目简介本项目旨在利用精益生产方法,改善公司生产线的效率和质量,减少浪费,提高客户满意度。
1.1 项目背景公司生产线的效率和质量一直是公司的瓶颈,同时也限制了公司的发展。
为了提高公司的竞争力,我们决定采用精益生产方法,对生产线进行改善。
通过优化生产线流程,减少浪费,提高质量和效率,最终达到增加产能和提高客户满意度的目标。
1.2 项目目标本项目通过引入精益生产方法,旨在实现以下目标:•减少生产线上的浪费:通过精益方法,减少生产线上的浪费,包括时间、人力、材料和能源等方面的浪费,提高生产线的效率。
•提高生产线的质量:通过精益方法,改善生产线的流程和质量控制系统,减少次品率,提高产品质量和客户满意度。
•提高公司的竞争力:通过提高生产线的效率和质量,提高公司产能并降低成本,增强公司的竞争力。
2. 项目计划2.1 项目组织为了保证项目的顺利推进和实现项目目标,我们组成了一个专门的项目组,包括以下人员:•项目负责人:负责项目的整体规划、组织、协调和监督。
•精益专家:负责精益方法的引入和指导。
•生产线主管:负责生产线的日常管理和生产绩效的改善。
•质量控制主管:负责生产线的质量控制和质量指标的改善。
•信息技术主管:负责建立和维护信息系统。
2.2 项目流程本项目分为以下几个主要流程:1.项目启动:成立项目组,确定项目计划和目标,建立项目管理机制。
2.流程分析:通过对生产流程的分析,确定当前存在的问题和改进机会。
3.改进方案制定:制定改进方案,并进行评估,确定最终方案。
4.方案实施:实施改进方案,并进行效果评估。
5.持续改进:持续监测并改进生产线的流程和效果,保证项目的持续改进。
2.3 项目计划表步骤时间负责人备注项目启动第1周项目负责人成立项目组,确定项目计划和目标,建立项目管理机制。
流程分析第2-3周生产线主管通过对生产流程的分析,确定当前存在的问题和改进机会。
改进方案制定第4-5周精益专家制定改进方案,并进行评估,确定最终方案。
精益生产改善总结报告
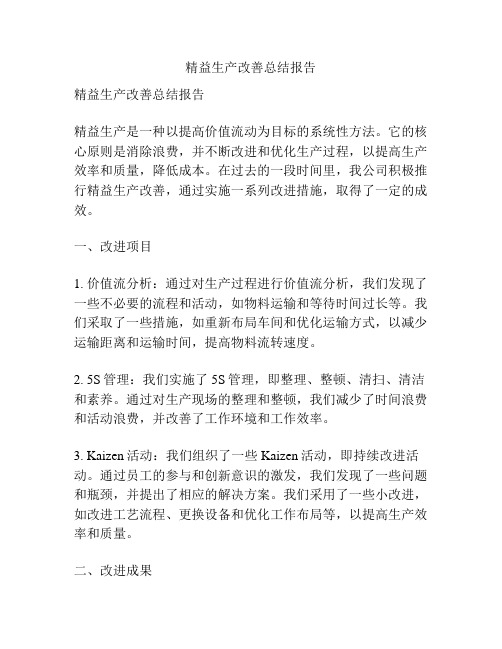
精益生产改善总结报告精益生产改善总结报告精益生产是一种以提高价值流动为目标的系统性方法。
它的核心原则是消除浪费,并不断改进和优化生产过程,以提高生产效率和质量,降低成本。
在过去的一段时间里,我公司积极推行精益生产改善,通过实施一系列改进措施,取得了一定的成效。
一、改进项目1. 价值流分析:通过对生产过程进行价值流分析,我们发现了一些不必要的流程和活动,如物料运输和等待时间过长等。
我们采取了一些措施,如重新布局车间和优化运输方式,以减少运输距离和运输时间,提高物料流转速度。
2. 5S管理:我们实施了5S管理,即整理、整顿、清扫、清洁和素养。
通过对生产现场的整理和整顿,我们减少了时间浪费和活动浪费,并改善了工作环境和工作效率。
3. Kaizen活动:我们组织了一些Kaizen活动,即持续改进活动。
通过员工的参与和创新意识的激发,我们发现了一些问题和瓶颈,并提出了相应的解决方案。
我们采用了一些小改进,如改进工艺流程、更换设备和优化工作布局等,以提高生产效率和质量。
二、改进成果经过一段时间的改进工作,我们取得了以下一些成果:1. 生产效率提高:通过消除浪费和优化流程,我们的生产效率提高了20%。
生产时间缩短,生产速度提升,产量增加。
这使我们能够更好地满足客户需求,并提高竞争力。
2. 质量改善:通过改进工艺和优化设备,我们的产品质量得到了提高。
产品合格率提高了10%,不良品率降低了20%。
这不仅降低了生产成本,还增强了顾客对我们产品的信任和满意度。
3. 成本降低:通过消除浪费和减少不必要的活动,我们的生产成本得到了一定的降低。
这使我们能够更好地控制成本,并提高利润空间。
4. 员工参与度提高:通过推行精益生产改善活动,我们激发了员工的参与意愿和创新意识。
员工参与度提高了,他们对工作更加积极主动,提出了很多有价值的改进意见和建议。
三、改进方向虽然我们在精益生产改善方面取得了一些成果,但仍然存在一些问题和挑战。
精益生产改善成果报告表

实施者事业部最高主管审批:
推动委员会组长批准:
备注
1-3星级提案要签批到实施者所在事业部推动干事及最高主管; 4-5星级要签批到事业部最高主管及推行委员会组长批准;
表单编号:
*提案主题 *提案编号
*提案实施组 长
*员工编号 *XXX有限公司
提案改善成果报告表
版 本:
A01
*实施开始日 期
*实施部门
*受益部门
职责
员工卡号
保存期 限:
3年
*实施完成日期
*实现部门负责人签字 日期
*受益部门负责人签字 日期
姓名
职责
*改善团队分 工
(主要原因及现状说明) *原因分析
(采取什么对策来改善,必要时可以附图说明) *改善对策
*改善区域
*改善前图文展示
*改善对象
*改善后图文展示
成果说明
*(改善后效果及收益说明)
(实际效果核对情况、成果计算) 推动委员会
成果复审
IE课&财务部 直接收益核实
推动干事复评 定级:
奖励金额:
核实者 推动干事:
核实日期 复评日期:
提出者事业部最高主管审批:
精益生产目视化样板线改善成果报告

精益生产目视化样板线改善成果报告1. 引言精益生产是一种以最大限度地提高价值流程效率为目标的生产管理方法。
其中,目视化样板线是精益生产中的关键工具,用于实时显示生产线的运行状况,帮助管理者及时发现问题并采取措施改善生产效率。
本报告将介绍我们在实施目视化样板线改善项目中的具体成果和收获。
2. 背景分析在传统生产管理中,往往很难及时了解生产线的运行状况,以及各项指标的实时数据。
这导致了问题的迅速积累,给生产效率带来不良影响。
为了解决这一问题,我们决定采用精益生产的方法,借助目视化样板线来实现对生产线的实时监控。
3. 目视化样板线改善项目3.1 项目目标本项目的目标是通过引入目视化样板线,提高生产线的效率和透明度,减少生产过程中的浪费,最终实现生产线的精益化管理。
3.2 项目计划•第一阶段:需求分析,确定目视化样板线的设计和功能•第二阶段:系统开发和部署,包括硬件设备的安装和软件系统的开发•第三阶段:培训和推广,教育工厂员工正确使用和理解目视化样板线•第四阶段:持续改进,根据实际使用情况不断优化目视化样板线的设计和功能3.3 实施成果在实施目视化样板线改善项目的过程中,我们取得了以下成果:•实时监控:通过目视化样板线,我们可以实时了解生产线上各个环节的运行状况,包括生产量、质量指标、故障情况等,从而及时采取措施解决问题。
•流程优化:通过对目视化样板线的数据分析,我们发现了生产线上的瓶颈环节和潜在浪费,进而进行了相应的流程优化,提高了生产效率和质量。
•管理可视化:通过目视化样板线的展示,我们改善了管理者对生产线的监控能力,能够随时了解生产线的状态,并及时做出决策。
•故障预警:目视化样板线可以实时监测设备的状态和运行情况,一旦出现故障,系统会自动发出警报,提醒维修人员及时处理,避免生产过程中的停机和延误。
4. 结论通过目视化样板线的实施,我们成功实现了对生产线的实时监控和精益化管理。
经过一段时间的应用后,我们发现生产效率明显提高,生产线的运行稳定性和质量得到了有效控制。
精益5S管理之1S管理向后作业报告
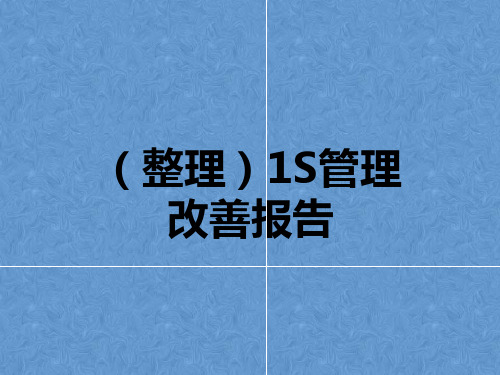
目录
一、1S管理改善实施过程照片(5-10张)
二、改善前后对比(1-5组对比图)越多越好
三、收获及感悟(个人及团队) 四、下一步计划
1
一、1S管理改善实施过程照片(9张)
2
二、改善前后对比(1-5组对比图)
二、改善前后对比(1-5组对比图)
3
二、改善前后对比(1-5组对比图)
• 跟着乐老师的脚步,一步一步将焊接车间 的5S工作做好,打造公司5S样板间,要 求全厂干部学习,从面推动全厂的5S工作 有序进行,提升公司效率与形象!
3
二、改善前后对比(1-5组对比图)
3
三、收获及感悟(个人及团队)
看到我们开心的笑容了吧!通过本次实际演练,我跟焊接的主管都切 身感到的通过自身的努力产生的变化,我要把我所学的5S知识传授给 每一个努力配合的部门主管,一个S一个S的去做好,相信公司产生
的变化是巨大的,效率一定会提升!
四、下一步计划
精益改善报告完整版

建议引入先进的流程管理工具和方法,以支持流程持续改进 。
对未来工作的建议与展望
建议三:强化员工培训与激励
建议加强员工培训,特别是 针对精益管理理念和工具的
培训。
建议建立激励机制,鼓励员工 积极参与精益改善活动,并对
优秀成果给予奖励。
对未来工作的建议与展望
01
建议四:加强与客户沟通与合作
02 建议企业加强与客户的沟通,深入了解客户需求, 以便更好地满足客户期望。
03 建议寻求与客户的长期合作,共同推进精益改善, 实现互利共赢。
THANKS FOR WATCHING
感谢您的观看
对改善效果进行评估,确认改 善成果是否达到预期目标。
改善过程中的挑战与解决方案
挑战一
团队协作问题
解决方案
加强团队沟通与协作,明确各成员职责,建立有效的协作机制。
改善过程中的挑战与解决方案
挑战二:资源不足
1
2
解决方案:合理分配资源,优化资源配置,提高 资源使用效率。
挑战三:技术难题
3
改善过程中的挑战与解决方案
社会效益
精益改善不仅提高了企业的经济效益 ,同时也为社会创造了更多的就业机 会和税收。
持续改进的建议与展望
持续改进的建议
1. 深化员工培训,提高全员精益意识。
2. 定期对生产流程进行审查和优化,确保持续 改进。
持续改进的建议与展望
• 加强与供应商和客户的沟通与合作,共同推进精益管理。
持续改进的建议与展望
对改善效果进行了评估,收集 了员工和相关方的反馈意见。
阶段性成果与反馈
01
反馈一:员工参与度提 高
02
员工对精益改善的参与 度有所提高,团队协作 意识增强。
精益改善报告
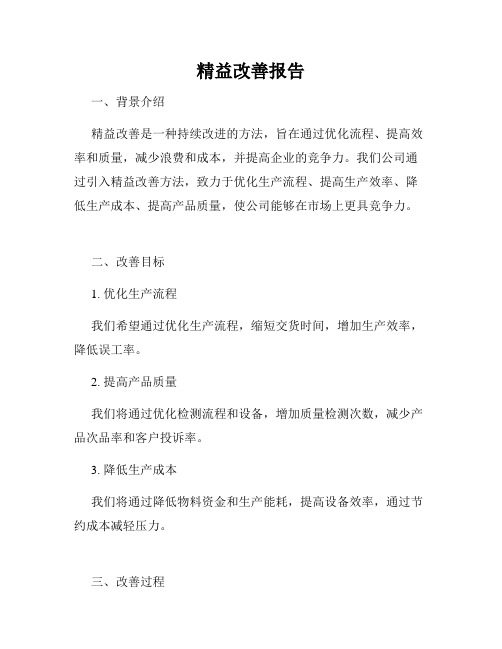
精益改善报告一、背景介绍精益改善是一种持续改进的方法,旨在通过优化流程、提高效率和质量,减少浪费和成本,并提高企业的竞争力。
我们公司通过引入精益改善方法,致力于优化生产流程、提高生产效率、降低生产成本、提高产品质量,使公司能够在市场上更具竞争力。
二、改善目标1. 优化生产流程我们希望通过优化生产流程,缩短交货时间,增加生产效率,降低误工率。
2. 提高产品质量我们将通过优化检测流程和设备,增加质量检测次数,减少产品次品率和客户投诉率。
3. 降低生产成本我们将通过降低物料资金和生产能耗,提高设备效率,通过节约成本减轻压力。
三、改善过程1. 流程优化(1)工艺图纸数字化首先,我们将对工艺图纸进行数字化处理,以便更好地进行管理和存储。
通过数字化,我们可以更好地控制生产流程,并及时发现不符合要求的工艺图纸。
(2)根据生产流程制作流程图我们将不断地监督生产流程,并根据生产情况制作生产流程图,并对流程图进行优化调整。
这将为我们提供一个更好的生产管理平台,并优化生产流程。
2. 检测设备升级我们将引进先进的机器视觉和检测设备,更准确地检测产品质量,增加质量检测次数和准确性,并进一步降低产品次品率。
3. 预防性维护我们将实施预防性维护计划,根据设备的使用情况定期进行检查,及早发现和解决设备问题,提高设备可靠性和使用寿命。
四、改善效果1. 生产效率提高40%通过优化生产流程和设备升级,我们的生产效率提高了40%,交货时间大大缩短,生产效益明显提高。
2. 产品质量提高30%通过加强质量检测和设备升级,我们的产品质量提高了30%,次品率大幅降低,得到了客户的认可。
3. 生产成本降低20%通过精细化生产管理,设备维护计划的实施等方式,我们的生产成本减少了20%,大大提升了公司的盈利能力。
五、改善展望我们将不断改进,不断创新,引进新技术,提高管理水平,降低成本,提高质量,推进企业的可持续发展。
超越自我,走在行业的前列,展现我们公司的优势和实力。
某公司车间精益生产改善总结报告

某公司车间精益生产改善总结报告一、引言车间精益生产改善是某公司持续提高生产效率的关键举措之一。
为了进一步提升生产效能和降低生产成本,本次改善活动对车间的生产流程和生产设备进行了分析和改进。
本文将对改善活动的实施过程和取得的成果进行总结和分析。
二、改善目标本次改善活动的目标主要包括以下几点: 1. 提高生产效率,实现生产能力的最大化利用。
2. 缩短生产周期,满足客户需求的快速响应。
3. 降低生产成本,提高公司的竞争力。
三、改善过程1. 生产流程分析首先,我们对车间的生产流程进行了详细的分析。
通过对产品生命周期进行大致划分,我们确定了关键的生产环节和可能存在的瓶颈。
同时,我们还对每个生产环节的工序进行了时间测定和产能评估。
2. 团队协作为了顺利实施改善活动,我们成立了一个专门的改善团队。
团队由不同领域的专家组成,包括生产工程师、生产运营经理、质量控制专员等。
团队协作是本次改善活动的关键,通过大家的努力和协同工作,我们才能更好地实现改善目标。
3. 改善方案制定基于对生产流程的分析和团队的讨论,我们制定了一系列改善方案。
每个方案都明确了改进目标、实施步骤和预期效果。
我们将这些方案进行了优先级排序,并制定了详细的实施计划。
4. 实施和改进根据制定的实施计划,我们开始逐步实施改善方案。
在每个环节的改进过程中,我们及时收集和分析了数据,并不断进行评估和调整。
通过持续的改进和优化,我们逐步取得了显著的改善效果。
四、改善成果通过本次改善活动,我们取得了以下一系列显著的成果: 1. 生产效率提升:经过改善后,车间整体生产效率提高了20%,产能得到了充分的释放,公司的生产需求得到了快速响应。
2. 生产周期缩短:改善后,产品的生产周期减少了30%,使公司能够更快地交付产品给客户,提升了客户满意度。
3. 成本降低:通过对生产流程的优化和设备的改进,我们成功地降低了生产成本。
这不仅提升了公司的竞争力,还增加了公司的盈利空间。
精益活动推动的进度报告

精益活动推动的进度报告引言精益活动是一种持续改进的管理方法,旨在通过消除浪费、提高效率和质量,实现企业的长期可持续发展。
本文旨在汇报我们团队在精益活动推动方面的进展情况,并简要介绍已实施的措施和取得的成果。
一、活动开展情况自精益活动启动以来,我们团队紧密配合,积极投入工作。
在活动的推动下,我们制定了详细的计划和目标,并逐步实施。
1. 初步调研我们首先进行了企业内部的初步调研,了解了现有的生产流程、管理方式以及存在的问题和瓶颈。
通过调研,明确了我们需要改进和优化的方向。
2. 流程分析基于对现有流程的认知,我们进行了详细的流程分析。
通过流程图、价值流图等工具,我们深入剖析了每个工序的价值和浪费,找出了存在的问题和不必要的环节。
3. 消除浪费根据流程分析的结果,我们确定了主要的浪费点,并制定了相应的改进措施。
我们采取了精益生产、质量管理、5S管理等方法,通过减少不必要的操作、提高生产效率等方式,实现了浪费的降低。
4. 持续改进我们明确了持续改进的重要性,并建立了改进的机制和流程。
每个团队成员都被鼓励积极提出改进建议,并参与改进活动。
我们定期进行改进成果的评估和效果跟踪,确保改进措施的落地和持续。
二、取得的成果经过团队的共同努力,我们取得了一些初步的成果,主要表现在以下几个方面:1. 生产效率提升通过消除浪费和优化流程,我们成功提升了生产效率。
以往需要花费一天完成的任务,现在只需要半天甚至更短的时间。
这不仅节约了人力资源,还提高了客户的满意度。
2. 品质改善通过强化质量管理和加强培训,我们成功提高了产品的质量。
不合格品率明显下降,产品问题的投诉和退换货率也得到有效控制。
3. 节约成本通过深入分析流程和消除浪费,我们有效地降低了成本。
不必要的环节和操作被取消或优化,节约了原材料的使用和人力资源的开支。
4. 满意度提升通过持续改进和优化,我们成功提高了员工和客户的满意度。
员工参与改进过程的积极性提高,客户对产品和服务的评价反馈也明显改善。
精益生产改善总结报告

精益生产改善总结报告精益生产改善总结报告篇一:精益生产示范区经验总结报告十五分厂精益示范区建设工作报告尊敬的各位领导、同志们:大家上午好,今天十分荣幸能在此代表公司精益试点单位与大家分享精益示范区建设成果,下面由我代表单位向在座各位汇报精益生产前期工作开展情况,不到之处请批评指正。
为全面贯彻落实集团公司和公司关于精益生产的总体要求,作为试点单位,在整个推进过程中,我们坚持“立足岗位、人人参与、消除浪费、创造效益”的总体方针和“理论联系实际,学以致用”的原则,边学边干,全力推进精益生产工作并取得阶段性成果。
第一部分前期工作总结一、广泛宣传发动,全面导入精益生产理念。
“精益生产”在我们广大干部职工的思想意识里并不陌生,但是在单位内部全面导入精益生产理念,并利用精益生产工具解决生产过程中的系列问题,实现精益生产示范区建设的总体目标,这是我们面临的一项新课题。
为确保精益生产工作深入开展,我们利用横幅、板报、看板等各种宣传手段广泛开展宣传发动工作,营造浓厚的精益文化氛围,让广大干部职工进一步明确精益生产的任务和目标,并深刻领会精益生产重要意义,实现广大干部职工在意识层面上由被动接受到主动作为的根本性转变。
其次,为使精益生产理念和工具在实际工作中得到充分应用,由班子成员亲自授课,和全体干部职工一起学精益、讲精益,使得精益理念和知识深入人心,并运用于生产的各个环节。
二、结合自身特点,对标查找问题与不足。
谈起精益生产,大家首先想到的就是高效的“丰田模式”,但是我们毕竟不是“丰田”,无论是生产组织模式还是日常管理,我们与之相比有太多的不一样,如果一味的照搬照抄,我们的精益生产无从下手。
为确保精益生产工作有序开展,我们必须立足自身特点,对照标准、对标兄弟企业,找出问题与不足加以改善。
在生产效率方面,存在辅助时间的浪费,无法形成高效的定向物流加工;在产品质量方面,存在品种多、换产频繁的浪费,无法通过标准化作业来控制产品质量;在物流改善和管理方面,存在提前计划、提前投料,在制品积压的浪费,同时导致物流紊乱,搬运频繁;在现场管理方面,因为现场设备布局、计划以及人员素养问题的影响,致使现场管理和5S活动推进困难。
精益生产目视化样板线改善成果报告

确定实施范围:根据企业实际情况,选择合适的生产线进行实施
资源投入:包括人力、物力、财力等方面的投入,确保实施过程的顺利进行
制定实施计划:根据实施范围和资源投入,制定详细的实施计划,明确各阶段的任务和 目标
实施过程中的监控和调整:在实施过程中,对实施情况进行监控,发现问题及时调整, 确保实施效果达到预期。
PART THREE
确定目标:明确精益生产目视化样板线的目 标和要求
分析现状:分析现有生产线存在的问题和瓶 颈
制定方案:制定具体的实施计划和方案,包 括时间节点、责任人、实施步骤等
培训和宣传:对相关人员进行培训和宣传, 确保方案的顺利实施
实施跟踪:对实施过程进行跟踪和监控,确 保方案的实施效果
总结和改进:总结实施过程中的经验和教训, 不断优化和完善方案,提高实施效果。
成就感增强
员工满意度提 高:员工对改 善项目的满意 度和幸福感增
强
员工工作效率 提升:员工在 改善项目中的 协作和沟通能 力增强,工作
效率提高
PART FIVE
推广效果:提高生产效率、 降低成本、提高产品质量等
推广方式:培训、宣传、现 场指导等
推广难点:员工接受程度、 实施难度、资金投入等
推广建议:制定推广计划、 分阶段实施、持续改进等
背景:企业面临生产效率低、成本高、质量不稳定等问题
目的:提高生产效率、降低成本、提高产品质量
原因:市场竞争激烈,需要提高企业竞争力
实施方法:引入精益生产理念,建立目视化样板线,实现生产过程的可视化、标准化和 持续改进。
提高生产效率:通过目视化管理,提高生产效率,降低生产成本 提高产品质量:通过目视化管理,提高产品质量,减少不良品率 提高员工满意度:通过目视化管理,提高员工满意度,降低员工流失率 提高企业形象:通过目视化管理,提高企业形象,增强企业竞争力
某重机有限公司精益计划管理改善项目评审报告

某重机有限公司精益计划管理改善项目评审报告引言本评审报告对某重机有限公司进行的精益计划管理改善项目进行了评估和总结。
该项目的目标是通过精益管理方法,提高公司的生产效率和质量水平。
在本报告中,我们将讨论项目的背景、目标、实施过程、结果和推荐措施。
项目背景某重机有限公司是一家重型机械制造公司。
在过去几年中,公司面临着生产效率低下、质量问题频发等挑战。
为了解决这些问题,公司决定实施精益计划管理改善项目。
项目目标该项目的主要目标是提高公司的生产效率和质量水平。
具体目标包括: - 减少生产周期时间 - 提高产品质量 - 降低成本项目实施过程为了实现项目目标,公司采用了以下步骤进行项目实施:1. 项目准备在项目准备阶段,公司确定了项目的范围、目标和可行性。
同时,制定了项目计划和资源需求,为项目的顺利实施打下基础。
2. 流程分析公司对目前的生产流程进行了详细的分析,找出了存在的问题和瓶颈。
通过流程分析,公司识别了可以进行改进的关键环节和优化点。
3. 流程优化基于流程分析的结果,公司进行了流程优化的工作。
通过引入精益管理方法,公司优化了生产流程,并实施了相应的改进措施。
4. 培训和教育为了确保项目的顺利实施,公司对员工进行了培训和教育。
培训内容包括精益管理方法的基本概念、工具和技巧。
5. 实施和监控在项目实施阶段,公司根据项目计划执行了各项改进措施,并对项目进行了监控和评估。
在此过程中,公司识别和解决了一些问题,并进行了实时调整。
6. 结果总结项目的最后阶段是结果总结。
公司评估了项目的成果和效果,并对项目进行了总结和反思。
项目结果通过精益计划管理改善项目的实施,某重机有限公司实现了以下成果: - 生产周期时间减少了20% - 产品质量得到了显著提高,缺陷率减少了30% - 成本降低了15%推荐措施基于对项目实施过程和结果的评估,我们向某重机有限公司推荐以下措施: 1. 持续改进:公司应将精益管理作为持续改进的理念,不断寻求进一步的优化和提升。
精益管理推进情况汇报

精益管理推进情况汇报自去年开始,我公司着手推进精益管理,旨在通过优化流程、提高效率、降低成本,实现持续改善和增强竞争力。
经过一年多的努力,现将精益管理推进情况进行汇报。
首先,我们在全公司范围内开展了精益管理知识的培训和普及工作。
通过内部培训讲座、外部专家指导等形式,使全体员工对精益管理理念有了更深入的了解。
同时,我们还建立了精益管理工作小组,负责具体的推进工作,并将精益管理理念融入到公司的日常经营中。
其次,我们在生产制造环节进行了精益改善。
通过价值流图分析、5S现场管理、设备保养改善等手段,我们成功优化了生产流程,提高了生产效率,降低了生产成本。
在产品质量方面,我们引入了精益质量管理方法,大幅提升了产品合格率和客户满意度。
另外,在供应链管理方面,我们加强了与供应商的沟通与合作,优化了供应商管理流程,降低了采购成本,缩短了供应周期,提高了供应链的稳定性和灵活性。
同时,我们还加强了对库存的管理,通过精益库存管理方法,有效降低了库存占用成本,提高了资金周转效率。
此外,我们还在管理层面进行了精益管理的推进。
通过制定KPI指标体系、建立绩效考核机制、推行精益报告制度等方式,加强了对各项工作的监督和管理,提高了管理效率和透明度,推动了公司整体绩效的持续改善。
总的来看,精益管理在我公司的推进取得了一定的成效,但也面临着一些挑战和问题。
比如,一些员工对精益管理理念的理解和认同还不够深入,需要加强宣传和教育;一些流程改善和管理机制的落实还存在一定的难度,需要进一步加强执行力和监督力。
未来,我们将继续深化精益管理,进一步推进各项工作。
我们将加强对员工的培训和引导,营造良好的精益管理氛围;加强对各项工作的执行和落实,确保精益管理取得实质性成效;加强对各项工作的监督和考核,推动精益管理持续改进和持续发展。
通过精益管理的持续推进,我们相信能够进一步提高公司的竞争力和持续发展能力,实现公司的可持续发展目标。
感谢各位领导和同事们对精益管理工作的支持和配合,让我们携手共进,共同开创美好的未来!。
- 1、下载文档前请自行甄别文档内容的完整性,平台不提供额外的编辑、内容补充、找答案等附加服务。
- 2、"仅部分预览"的文档,不可在线预览部分如存在完整性等问题,可反馈申请退款(可完整预览的文档不适用该条件!)。
- 3、如文档侵犯您的权益,请联系客服反馈,我们会尽快为您处理(人工客服工作时间:9:00-18:30)。
559610员工负荷表 559610 员工负荷表
650 600 550 500 450 400 350 300 513 250 200 150 100 50 71 0 CNC2 工人总时间 72
珠海市俊凯机械有限公司
改善前 改善后
558880员工负荷表 558880 员工负荷表
600 550 500 450 400 350 28 300 531 250 200 316 150 100 115 50 0 CNC1 CNC3 工人总时间 37
珠海市俊凯机械有限公司
改善前生产现场 改善后生产现场
传统的一类设备直线分区摆放
建立的U型生产线 建立的 型生产线
珠海市俊凯机械有限公司
改善前工具柜里的物品摆放 改善后工作台的物品摆放
工具摆放混乱,没有标示, 工具摆放混乱,没有标示,经常用工 具时需要到处寻找工具浪费时间
工具摆放整齐、标示清楚明了, 工具摆放整齐、标示清楚明了, 员工不需要再寻找工具。 员工不需要再寻找工具。
珠海市俊凯机械有限公司
改善前物料摆放
报废品 无指定 摆放区 域
两种产 品混料
物料 放置 不清 晰
不良品 放置在 产品放 置盒中
成品摆 放混乱
产品上 还有废 屑
不良品 放置在 成品架 上
珠海市俊凯机械有限公司
改善后物料摆放
原材料标示 产品摆 放整齐
物料摆 放整齐 能很快 找到物 料
珠海市俊凯机械有限公司
生产效率提升50% 一、生产效率提升 建立小批量生产线,岗位及人员的确定。 二、建立小批量生产线,岗位及人员的确定。
活动时间: 月 日 月 日 活动时间:6月3日-6月10日
珠海市俊凯机械有限公司
•
改善范围: 改善范围:
– 观测小批量产品族的生产过程. 观测小批量产品族的生产过程 生产过程.
•
所做的工作: 所做的工作:
珠海市俊凯机械有限公司
改善前 改善后
557526员工负荷表 557526 员工负荷表
500
450 41 400
350 46 300
250 417 200 150
296
100 162 50
0 CNC1 CNC3 工人总时间
珠海市俊凯机械有限公司
改善前的生产现场 改善后的生产现场
设备上随处可见的油污和垃圾 设备焕然一新
+
质量检验 安全预防 半品
+
半品数量 接拍时间/U秒 周期时间/u秒
+
46302011生产线员工技能表 46302011 生产线员工技能表
一级:(能培训员工,并且使他们能达到二级水平) 二级:(单独熟练操作)
3
120
289
操作负荷表
4630211操作负荷表 操作负荷表
62 时间:秒u 节拍:120
150
108 150
100
120 108 50
0 CNC2 工人总时间
珠海市俊凯机械有限公司
改善前 改善后
543784员工负荷表 543784 员工负荷表
400
350 67 54 300
250
200
318 310 150 299
100
50
0 CNC1 CNC2 人工总时间
珠海市俊凯机械有限公司
改善前 改善后
改善目的:
建立PCBA组装生产线,实现定岗定人,达到单件 组装生产线,实现定岗定人, 建立 组装生产线 流生产
活动时间:3月26日-4月24日 活动时间: 月 日 月 日
珠海博杰电子有限公司
改善范围: 改善范围:
PCBA 组装产品族的生产过程 生产过程. 生产过程
所做的工作: 所做的工作:
1.作现场时间观测 作现场时间观测 2.确定了存在的浪费 确定了存在的浪费 3.布置 布置PCBA组装产品族生产布局 (u形拉) 布置 组装产品族生产布局 4.做了物料摆放布置及目视化标签 做了物料摆放布置及目视化标签 5.生产线尾部看板 生产线尾部看板
珠海市广浩捷精密机械有限公司
改善前生产现场 改善后生产现场
主要问题点:生产布局排序虽按 型序 型序, 主要问题点:生产布局排序虽按U型序,但 未按单件流程生产, 未按单件流程生产,造成各工序半成品积 从而引过设备过剩,库存过剩, 压,从而引过设备过剩,库存过剩,人员过 剩…最后导致制造成本增加,许多问题未及 最后导致制造成本增加, 最后导致制造成本增加 时暴露
U型布局 型布局 定岗定人 已建立 已建立
生产周期提升了50% 生产周期提升了50% 生产效率提升了50% 生产效率提升了50%
618m 12PCS/h/2人 12PCS/h/2人
407m 24/h2人 24/h2人
提高了51.8% 提高了51.8% 提高了100% 提高了100%
6
珠海市俊凯机械有限公司 活动目标:
改善后各工序标准工时
机器 人标准工时 机器标准工时
1
下料
卧铣
15
5
1
下料
卧铣
10
3
2
飞底面
立铣
35
15
2
飞底面
立铣
30
15
3
铣长度
哈斯机
15
60
3
铣长度
哈斯机
10
64
4
铣内腔
起亚机
15
270
4
铣内腔
起亚机
10
110
5
铣外宽
哈斯机
15
80
5
铣外宽及沉孔
哈斯机
15
80
6
反面沉孔
佳铁
15
18
7
自检
60
6
自检
珠海市俊凯机械有限公司
改善前 改善后
557559员工负荷表 557559 员工负荷表
500 450 61 400 350 300
250 200 150 100 50 61 0 CNC2 工人总时间 406
珠海市俊凯机械有限公司
改善前 改善后
550316员工负荷表 550316 员工负荷表
250
200
改善前生产一个产品所需的 时间为1233秒
改善前生产一个产品所需的 时间为180秒
珠海市广浩捷精密机械有限公司
改善结果
序号
1 2 3 4 5
改善内容
46302011ACG生产线 46302011ACG生产线 岗位及人员的确定 员工技能表的建立 现场的目视化管理建立
改善前
不清晰 不清晰 无 无
改善后
60
8
研磨去毛刺
振动研磨
7
研磨去毛刺
9
检验出货
8
检验出货
合计
170
448
135
272
珠海市广浩捷精密机械有限公司
改善后的生产现场 改善前的生产现场 防护 罩制 作
开 关 移 位 限 位 制 作
主要问题: ① 操作机器不方便,不安全 ② 粉尘大 ③ 机器来回行程未定化
改善后效果确认: (1)粉尘大大减少 (2)操作安全方便 (3)单件可节约时间:5 S
目视化管理板
珠海市俊凯机械有限公司
改善结果
产品 改善内容 改善前
135 生产力( 100人工 小时) 人工/ 559610 生产力(每100人工/小时) 生产力( 100人工 小时) 人工/ 557559 生产力(每100人工/小时) 生产力( 100人工 小时) 人工/ 543784 生产力(每100人工/小时) 生产力( 100人工 小时) 人工/ 543666 生产力(每100人工/小时) 生产力( 100人工 小时) 人工/ 558880 生产力(每100人工/小时) 生产力( 100人工 小时) 人工/ 557526 生产力(每100人工/小时) 531759 生产力(每100人工/小时) 人工/ 生产力( 100人工 小时) 47 52 18 83 31 42 20 •
珠海博杰电子有限公司
改善前时间观测( 为例) 改善前时间观测(以X-BOX为例) 为例 装针: 分钟 装针:53分钟 装气缸,拉手,合页,及其他附件: 分钟 装气缸,拉手,合页,及其他附件:60分钟 压针套: 分钟 压针套:45分钟 框架组装: 分钟 框架组装:40分钟
70 60 50 40 30 20 10 0 装针 装气缸 压针套 框架
珠海博杰电子有限公司
改善结果
序号 节拍时间 每天出货数量 Productivity 生产力 Operators 操作人员 Inventory- WIP 在线半成品
目标
改善前 60分钟 分钟 207
改善后 40分钟 分钟 138 2400 2 2
总提升 33% 33% 82% 85% 80%
50%
– – 1.现场时间的观测 1.现场时间的观测 2.确定了存在的浪费 2.确定了存在 确定了存在的浪费
• •
– –
3.小批量产品生产布局 3.小批量产品生产布局 (U形生产线) 4.小批量生产线日常管理看板的制作 4.小批量生产线日常管理看板的制作
5.工作台的制作 5.工作台的制作 6.5S检点表及作业指导书的改进 6.5S检点表及作业指导书的改进
工具 标签
工具摆放不整齐,没有标示, 工具摆放不整齐,没有标示,经常用 工具时需要到处寻找工具浪费时间
工具摆放整齐、标示清楚明了, 工具摆放整齐、标示清楚明了, 员工不需要再寻找工具。 员工不需要再寻找工具。
珠海市广浩捷精密机械有限公司
改善后标准工作表及负荷表
标准工作表
北 哈斯 机 起亚机
+ +
哈斯 机 品 检
•
所做的工作: 所做的工作: