大面积风口区流态化焙烧炉组合炉衬研究
气态悬浮焙烧炉炉顶内衬的优化
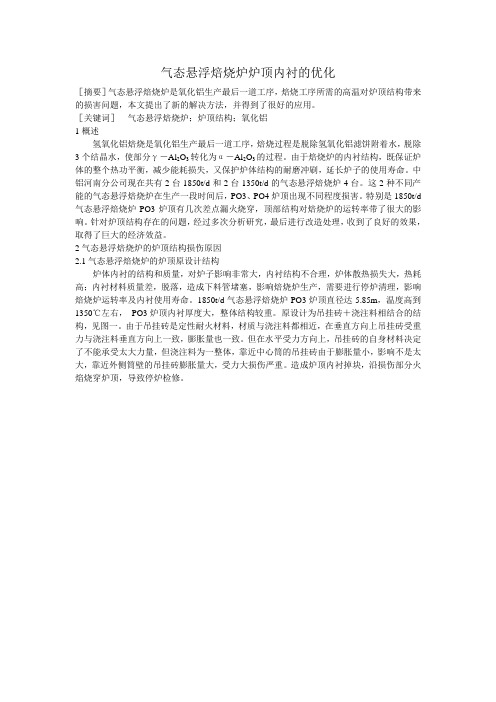
气态悬浮焙烧炉炉顶内衬的优化[摘要]气态悬浮焙烧炉是氧化铝生产最后一道工序,焙烧工序所需的高温对炉顶结构带来的损害问题,本文提出了新的解决方法,并得到了很好的应用。
[关键词]气态悬浮焙烧炉;炉顶结构;氧化铝1概述氢氧化铝焙烧是氧化铝生产最后一道工序,焙烧过程是脱除氢氧化铝滤饼附着水,脱除3个结晶水,使部分γ-Al2O3转化为α-Al2O3的过程。
由于焙烧炉的内衬结构,既保证炉体的整个热功平衡,减少能耗损失,又保护炉体结构的耐磨冲刷,延长炉子的使用寿命。
中铝河南分公司现在共有2台1850t/d和2台1350t/d的气态悬浮焙烧炉4台。
这2种不同产能的气态悬浮焙烧炉在生产一段时间后,PO3、PO4炉顶出现不同程度损害。
特别是1850t/d 气态悬浮焙烧炉PO3炉顶有几次差点漏火烧穿,顶部结构对焙烧炉的运转率带了很大的影响。
针对炉顶结构存在的问题,经过多次分析研究,最后进行改造处理,收到了良好的效果,取得了巨大的经济效益。
2气态悬浮焙烧炉的炉顶结构损伤原因2.1气态悬浮焙烧炉的炉顶原设计结构炉体内衬的结构和质量,对炉子影响非常大,内衬结构不合理,炉体散热损失大,热耗高;内衬材料质量差,脱落,造成下料管堵塞,影响焙烧炉生产,需要进行停炉清理,影响焙烧炉运转率及内衬使用寿命。
1850t/d气态悬浮焙烧炉PO3炉顶直径达5.85m,温度高到1350℃左右,PO3炉顶内衬厚度大,整体结构较重。
原设计为吊挂砖+浇注料相结合的结构,见图一。
由于吊挂砖是定性耐火材料,材质与浇注料都相近,在垂直方向上吊挂砖受重力与浇注料垂直方向上一致,膨胀量也一致。
但在水平受力方向上,吊挂砖的自身材料决定了不能承受太大力量,但浇注料为一整体,靠近中心筒的吊挂砖由于膨胀量小,影响不是太大,靠近外侧筒壁的吊挂砖膨胀量大,受力大损伤严重。
造成炉顶内衬掉块,沿损伤部分火焰烧穿炉顶,导致停炉检修。
焙烧炉的工作原理

焙烧炉的工作原理
焙烧炉是一种用于将物料进行高温热处理的设备,其工作原理如下:
1. 待处理物料进入焙烧炉的进料口,通常会经过预处理,例如破碎、筛分等。
2. 焙烧炉内的燃料(如煤、天然气或重油)被点火,产生高温火焰。
3. 火焰通过燃烧室或燃烧器喷嘴进入焙烧炉的焙烧区域。
4. 焙烧炉内有一个内衬(通常是耐火材料制成)来承受高温和化学腐蚀。
物料被放置在焙烧炉内部,并随着焙烧区域内的火焰移动。
5. 高温火焰加热物料,引起其内部化学反应,产生所需的热解、脱水、焙烧或煅烧效果。
6. 焙烧炉内设有出料口,处理过的物料从该口流出焙烧炉。
7. 排出的废气由烟囱或其他排气系统排出。
总之,焙烧炉通过高温火焰加热物料,在控制的气氛下实现物料的热处理,从而实现所需的化学反应和产品变化。
浅谈三种氢氧化铝焙烧炉的应用
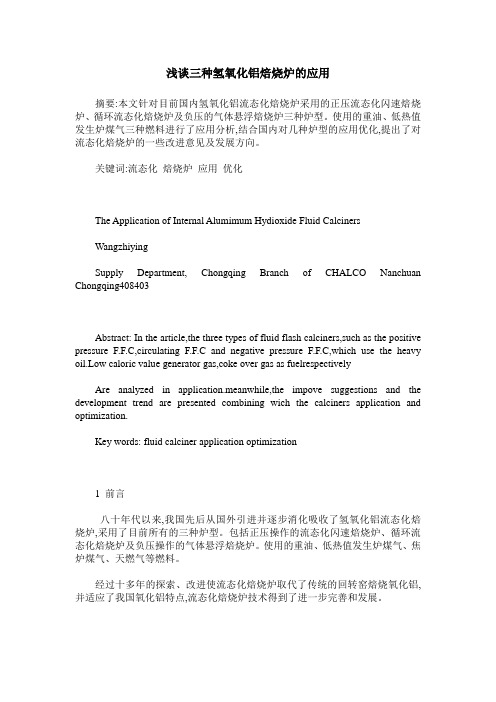
浅谈三种氢氧化铝焙烧炉的应用摘要:本文针对目前国内氢氧化铝流态化焙烧炉采用的正压流态化闪速焙烧炉、循环流态化焙烧炉及负压的气体悬浮焙烧炉三种炉型。
使用的重油、低热值发生炉煤气三种燃料进行了应用分析,结合国内对几种炉型的应用优化,提出了对流态化焙烧炉的一些改进意见及发展方向。
关键词:流态化焙烧炉应用优化The Application of Internal Alumimum Hydioxide Fluid CalcinersWangzhiyingSupply Department, Chongqing Branch of CHALCO Nanchuan Chongqing408403Abstract: In the article,the three types of fluid flash calciners,such as the positive pressure F.F.C,circulating F.F.C and negative pressure F.F.C,which use the heavy oil.Low caloric value generator gas,coke over gas as fuelrespectivelyAre analyzed in application.meanwhile,the impove suggestions and the development trend are presented combining wich the calciners application and optimization.Key words: fluid calciner application optimization1 前言八十年代以来,我国先后从国外引进并逐步消化吸收了氢氧化铝流态化焙烧炉,采用了目前所有的三种炉型。
包括正压操作的流态化闪速焙烧炉、循环流态化焙烧炉及负压操作的气体悬浮焙烧炉。
109m 2锌精矿流态化焙烧炉及制酸系统的生产实践

间 的两 台余 热 锅炉 所 产 饱 和蒸 汽 合 并 , 入两 级余 进 热饱 和 蒸 汽发 电机组 , 中一 级 发 电后 抽 出部 分 低 其 压 蒸 汽 供 湿法 炼锌 工艺 加 热 和冬 季 采 暖使 用 , 代 替
况 。该 系统 开 车一 次成 功 , 产 半 年 来 运 行 稳 定 , 要 生 产 技 术 经 济指 标 均 达到 了设 计值 。 目前 制 酸 转 试 主
化率稳定在 9 .%, 97 吸收率达到 9 . %, 气达标排放。 99 尾 6 【 关键词】 锌精矿 ; 流态化焙烧炉 ; 焙烧 ; 制酸装 置 ; 试产
・
3 ・ 0
中 固 有
色 冶 金
A卷生产实践篇 . 重金属
19d 精 矿 流 态 化 焙 烧 炉及 制 酸 系 统 的生 产 实 践 0 锌 r
岳 凤 洲 , 兴 龙 , 西 民 柳 戴
( 陕西锌业有限公司商 洛炼 锌厂 , 陕西 商 州 760) 2 0 7
【 摘
要l 介绍 了商洛炼锌 厂 19i 锌精矿 流态化焙 烧炉及制 酸 系统 的工 艺、 0 n 主要 设备及试 产运行 情
冲吹灰装置 , 清灰效果好 。余热锅炉 自 试产投入运
行 后 , 口烟气 温 度一 直稳 定 在 3 0o以 内 , 出 5 C 临时检 修 未发 现锅 炉 内部有 明显 粘结 结块 现象 。 余 热锅 炉烟 气 出 口处 紧接 恩菲 的专 利设 备两级 四管 式旋 风收 尘 器 , 电收尘 器 采 用 卧式 单 室 四 电场
胀 和烟气 泄漏 的 问题 。
溢 流焙砂 通过 流态 化冷 却器 和 高效冷 却 圆筒冷 却 , 气 经余 热 锅 炉 、 风 收尘 器 、 烟 旋 电收尘 器 收 尘 降
焙烧炉简介
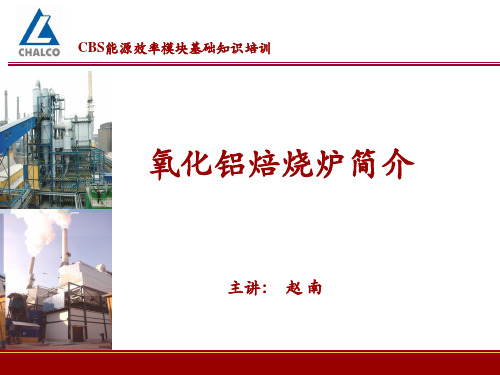
-8-
介绍完毕
焙烧小组 2011年11月
-9-
工艺特点 焙烧温度/℃ 焙烧时间 系统压力/MPa 控制水平 热耗/(GJ/t) 电耗/(kwh/t) 废气/(mg/m3)
— 1200 45min — 低 4.50 — —
产能调节范围/%
30~100
46~100
60~100
—
-3-
焙烧炉工艺流程图
-4-
焙烧炉结构图
-5-
焙烧系统物料和热量平衡模型
AH
AH
AO
焙 烧 系 统 废气 系统散热 冷却水
重油
蒸汽 空气
焙 烧 系 统
AO 废气
重油 蒸汽 空气 冷却水
物料平衡模型
热量平衡模型
-Байду номын сангаас-
氢氧化铝的焙烧机理
-7-
焙烧炉主要工艺技术指标
焙烧炉主要工艺技术指标及控制范围 指标名称 重油单耗(kg/t-AO) AO灼减(%) AO -45μm (%) 破损率(%) 焙烧铝氧SiO2增值(%) 电收尘出口含尘量(mg/Nm3) 控制范围 < 82 0.70~1.00 ≤18 ≤14 ≤0.003 ≤80
与回转窑相比,流态化焙烧炉①热效率高、热耗低;②产品质量好;③ 投资少;④设备简单、寿命长、维修费用低。 20世纪80年代以来,国外新建氧化铝厂基本上都采用了流态化焙烧炉。 我国1984年从德国引进第一台1300t/d的美铝闪速焙烧装置,相继又引 进丹麦史密斯公司的五套气态悬浮焙烧装置、两套德国鲁奇公司的循环 焙烧装置。
-2-
焙烧炉的种类和历史
各种类型焙烧装置性能比较
炉 型 流程及设备 闪速焙烧炉 文丘里和流化床干燥 脱水,载流预热闪速 焙烧,流化停留槽保 温,三级载流冷却加 流化床冷却 闪速焙烧加停留槽 980~1050 15~30min 0.18~0.21 高 3.096 20 <50 循环焙烧炉 一级文丘里干燥脱 水,一级载流预热 ,循环流化床焙烧 ,一级载流冷却加 流化床冷却 循环焙烧 950~1000 20~30min 约0.3 高 3.075 20 <50 悬浮焙烧炉 文丘里和一级载流 干燥脱水,悬浮焙 烧,四级载流冷却 加流化床冷却 稀相悬浮焙烧 1150~1200 1~2s -0.055~0.065 高 3.075 <18 <50 回转窑 窑内集干燥、脱 水、焙烧、冷却 、加冷却机冷却
科技成果——流态化焙烧高效节能炉窑技术
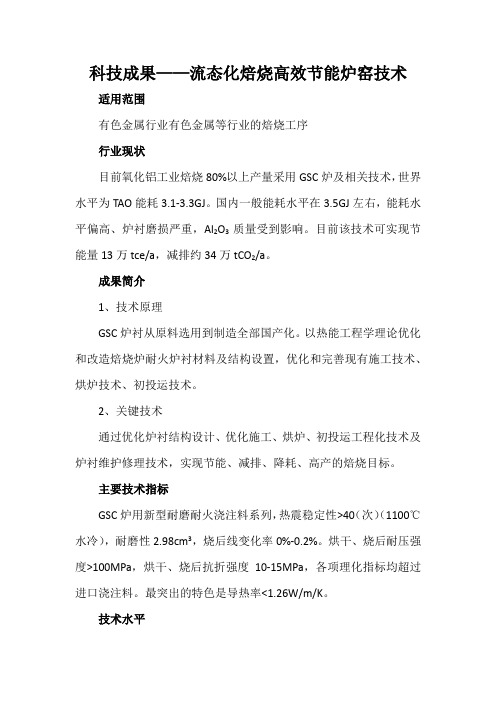
科技成果——流态化焙烧高效节能炉窑技术适用范围有色金属行业有色金属等行业的焙烧工序行业现状目前氧化铝工业焙烧80%以上产量采用GSC炉及相关技术,世界水平为TAO能耗3.1-3.3GJ。
国内一般能耗水平在3.5GJ左右,能耗水平偏高、炉衬磨损严重,Al2O3质量受到影响。
目前该技术可实现节能量13万tce/a,减排约34万tCO2/a。
成果简介1、技术原理GSC炉衬从原料选用到制造全部国产化。
以热能工程学理论优化和改造焙烧炉耐火炉衬材料及结构设置,优化和完善现有施工技术、烘炉技术、初投运技术。
2、关键技术通过优化炉衬结构设计、优化施工、烘炉、初投运工程化技术及炉衬维护修理技术,实现节能、减排、降耗、高产的焙烧目标。
主要技术指标GSC炉用新型耐磨耐火浇注料系列,热震稳定性>40(次)(1100℃水冷),耐磨性2.98cm3,烧后线变化率0%-0.2%。
烘干、烧后耐压强度>100MPa,烘干、烧后抗折强度10-15MPa,各项理化指标均超过进口浇注料。
最突出的特色是导热率<1.26W/m/K。
技术水平该技术通过中国有色金属工业协会鉴定,已先后在我国最大的1850t/d及1400t/d、1300t/d、180t/d等不同类型的GSC炉推广。
典型案例典型用户:中国铝业河南分公司、洛阳香江万基铝业公司、中铝中州分公司、广西分公司、贵州黄果树铝业有限公司等。
典型案例1:中铝河南分公司建设规模:年产65万tAl2O3(1850t/d)气态悬浮焙烧炉。
主要改造内容:(1)国产化GSC炉耐火材料设置(定型、不定形、保温耐火材料);(2)GSC炉炉衬耐火材料结构设计;(3)优化工程施工、烘炉、初投运、维护工程技术及标准化。
节能技改投资额约740万元,建设期约2个月。
项目年节能22162tce,取得节能经济效益2550万元,提高产能11万tAl2O3,增加产值4.18亿元(07年不变价),投资回收期约4个月。
第八章氢氧化铝的焙烧

第八章氢氧化铝的焙烧第一节概述氧化铝生产采用流态化焙烧技术的试验研究开始于20世纪40年代,近40年来,流态化焙烧在工业生产中显示出其优质、低耗的强大优势,技术发展十分迅速。
目前广泛应用于氧化铝生产的焙烧技术为美国的闪速焙烧、德国的循环焙烧、丹麦的气态悬浮焙烧三种,其中气态悬浮焙烧技术起步最晚,但技术先进,代表着最新流态化焙烧水平,号称“第三代”。
然而,因其在工业生产中应用较晚,实际运行中,仍然存在许多问题,若能很好地解决,进一步完善其工艺,则气态悬浮焙烧技术无疑是氧化铝生产的最佳选择。
我国自1987年山西铝厂引进第一台美铝闪速焙烧炉以后,十多年来,相继又引进了德国鲁奇循环流态化焙烧炉、丹麦史密斯气态悬浮焙烧炉,其中以气态悬浮焙烧炉为主,占到总数的70%。
目前国内氧化铝几乎全部采用流态化焙烧。
流态化焙烧与回转窑比有其明显优点:(1)、热效率高、热耗低。
热耗3.1~3.2GJ/t,流态化焙烧炉中燃料燃烧稳定,温度分布均匀,氢氧化铝和燃烧产物以及高温氧化铝和助燃空气间接触密切,换热迅速,空气预热温度高,过剩空气系数低,燃料燃烧温度提高,系统热效率大大提高,废气量则随之减少,加之散热损失只有回转窑的30%,流态化焙烧炉的热效率可达75~80%,而回转窑最好情况下的热效率也低于60%,流态化焙烧炉单位产品热耗比回转窑降低约1/3。
国外回转窑热耗先进水平约为4.186GJ/t-Al2O3,而国内回转窑焙烧热耗约为5.032GJ/t- Al2O3。
(2)、产品质量好。
这是由于炉衬磨损少,德国循环流态化焙烧产品中SiO2含量比回转窑产品约低0.006%,不同粒级氢氧化铝焙烧均匀,相同比表面积的氧化铝中α-Al2O3含量低,与回转窑比,流态化焙烧的产品中小于45μm粒级增加约4%,而小于15μm的粒级没有改变。
各类型流态化焙烧炉都能制取砂状氧化铝。
(3)、投资少:流化床焙烧炉单位面积产能高、设备紧凑、占地少。
它的机电设备重量仅为回转窑的1/2,建筑面积仅为1/3~2/3,投资比回转窑低40~60%(以1983年国内价格计),国外发表数据,美国少50~70%,西德少20%,法国少15~20%。
19国家重点节能技术推广目录(第二批)
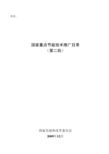
附件:国家重点节能技术推广目录(第二批)国家发展和改革委员会2009年12月典型项目预计2015年序号节能技术名称适用范围主要技术内容技术条件投资额单位节能量项目节能量目前推广比例(%)该技术在行业能推广到的比例(%)总投入(万元)节能能力(万t ce)1煤炭储运减损抑尘技术煤炭等行业粉料运输及露天堆放通过喷洒减损抑尘剂,使煤炭或粉状物料表面形成固化层,以达到降低损耗、防治扬尘的目的。
煤炭运输量1000万t/a以上300万元70t煤炭/万t煤炭运输量50000t ce/a 14%左右(铁路煤炭运输部分)>50%(铁路煤炭运输)20%~30%(公路煤炭运输)350005002 电除尘器节能提效控制技术电力、冶金、建材等行业电除尘器改造通过采用优化控制的高频脉冲供电波形,提高设备的电能利用效率,大幅度降低设备运行电耗,减少粉尘污染物排放,达到节能减排目的。
1台300MW发电机组用大型电除尘器270万元 电除尘器节电70%以上1400t ce/a <1% 25% 90000 503 纯凝汽轮机组改造实现热电联产技术电力行业125~600MW纯凝汽轮机组纯凝汽轮机组的导汽管打孔抽汽,实现热电联产。
2台200MW三缸三排汽纯凝机组,抽汽参数可调1600万元改造后每供1GJ热节能28kg ce14000t ce/a(按1个采暖期供热500000GJ)<10% 20% 160000 4004电站锅炉空气预热器柔性接触式密封技术电力行业火力发电锅炉空气预热器采用柔性金属密封组件,直接与空预器的密封板进行接触,从而降低运行电耗,提高除尘效率。
2台1000MW火力发电机组,采用回转式空气预热器600万元漏风率减少2%15700t ce/a<5% 20% 37500 801典型项目预计2015年序号节能技术名称适用范围主要技术内容技术条件投资额单位节能量项目节能量目前推广比例(%)该技术在行业能推广到的比例(%)总投入(万元)节能能力(万t ce)5锅炉智能吹灰优化与在线结焦预警系统技术电力、钢铁、化工等行业工业锅炉在锅炉各受热面污染在线监测的基础上,实现系统开环运行操作指导与闭环反馈监测控制相结合的智能吹灰运行模式,从而减少吹灰蒸汽用量,降低排烟温度,提高锅炉效率。
多级循环流态化焙烧炉的两相流模拟
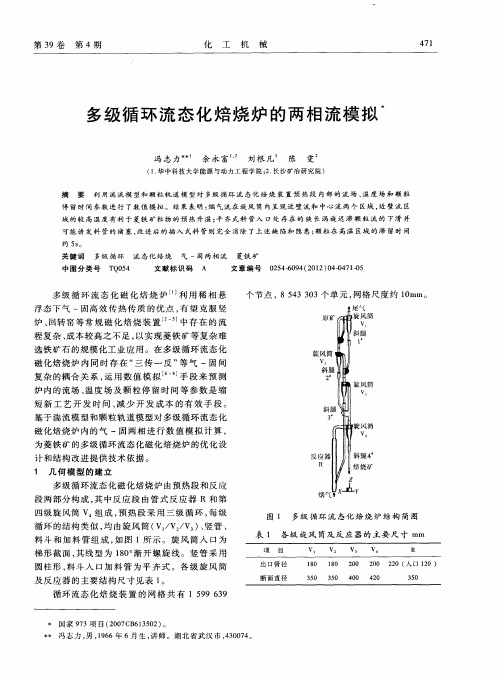
第 4期
化 [ 机
械 Leabharlann 41 7 多 级 循 环 流 态 化 焙 烧 炉 的 两 相 流 模 拟
冯 志 力 余 永 富 刘 根 凡 陈 雯 ,
( . 中科 技 大 学 能 源 与 动 力 工 程 学 院 ;. 沙 矿 冶 研 究 院 ) 1华 2长
摘 要 利 用 湍 流 模 型 和 颗 粒 轨 道 模 型 对 多 级 循 环 流 态化 焙 烧 装 置 预 热段 内部 的 流 场 、 度 场 和 颗 粒 温
将预热 段 和反应段 内烟气视 为不 可压缩 定 常
界条 件 , 口速 度 为 7 7 5 / , 度 9 0 , 入 .7 m s温 0 ℃ 烟气 出 口( 第一级 旋 风筒 ) 为压 力 边界 条 件 , 表压 设 取
为零 。各级 的 其他 进/ 口边 界条 件 经 由界 面耦 出
流动 , 其控 制方 程包括 连续性 方 程 、 动量 方程 和能
速■■ 二 二 二
烟气 按 混 合 气 体 处 理 , 主 要 组 分 为 : O 其 C,
( 2 7 % ) H, 1 . 8 ) C 5 ) N 。烟 1 .6 、 0( 5 6 % 、 O( % 和 ,
对流 及辐 射换 热系数 设定 为 1 W/ m K) 2 ( ・ 。
表 2 烟 气 与 壁 面 的 对 流 换 热 系数
多 级 循 环 流 态 化 磁 化 焙 烧 炉 … 利 用 稀 相 悬
浮 态下 气 一固高 效 传 热 传 质 的 优 点 , 望 克 服竖 有 炉、 回转 窑 等常 规 磁 化 焙 烧 装 置 中存 在 的流
程 复杂 、 成本 较 高之不 足 , 以实 现菱 铁矿 等复 杂难
焙烧炉原理

焙烧炉原理
焙烧炉是一种用于矿石、煤炭和其他原材料的热处理设备,其原理主要包括燃烧、传热和传质三个方面。
在焙烧炉内,矿石或煤炭等原料经过一系列的物理化学变化,最终得到所需的产品。
下面将详细介绍焙烧炉的原理。
首先,焙烧炉的燃烧原理是其能够提供热能的基础。
在焙烧炉内,燃料经过点火后产生燃烧,释放出大量的热能。
这些热能可以提供给焙烧炉内的物料,使其达到所需的温度。
同时,燃烧过程中产生的燃烧产物也会对物料的性质产生影响,例如氧化反应会使物料中的有害元素得到去除。
其次,传热是焙烧炉原理中的重要环节。
燃烧产生的热能需要通过传热的方式传递给焙烧炉内的物料。
传热的方式包括传导、对流和辐射。
在焙烧炉内,通过燃烧产生的高温气体和固体物料之间的热量传递,使得物料的温度逐渐升高,从而实现所需的热处理效果。
最后,传质是焙烧炉原理中的另一个重要环节。
在焙烧炉内,除了温度的影响外,气体、液体和固体之间的物质传递也是至关重要的。
例如,氧气在燃烧过程中与物料发生氧化反应,从而影响物料的化学成分。
另外,焙烧炉内的气氛对物料的热处理效果也有重要影响,通过控制气氛的成分和流动速度,可以实现对物料的精确控制。
总的来说,焙烧炉的原理涉及燃烧、传热和传质三个方面,通过这些过程,可以实现对原料的热处理和改性。
了解焙烧炉的原理对于提高生产效率、优化产品质量具有重要意义,同时也为焙烧炉的设计和改进提供了理论依据。
希望本文能够帮助读者更好地理解焙烧炉的工作原理,为相关领域的研究和应用提供参考。
循环流态化焙烧技术在复杂难处理金矿矿石预脱硫中的应用研究
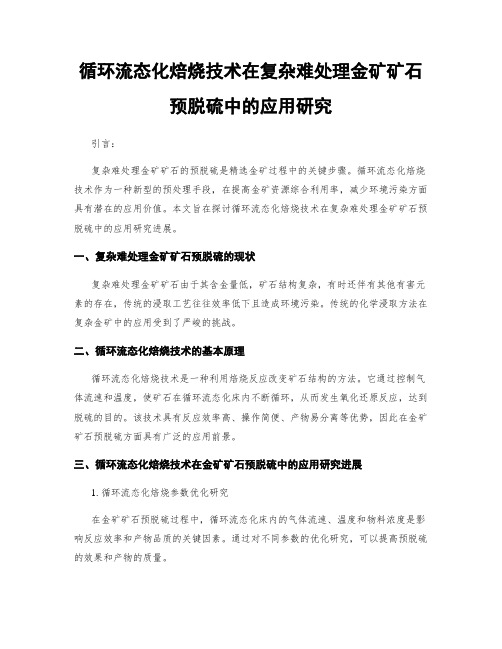
循环流态化焙烧技术在复杂难处理金矿矿石预脱硫中的应用研究引言:复杂难处理金矿矿石的预脱硫是精选金矿过程中的关键步骤。
循环流态化焙烧技术作为一种新型的预处理手段,在提高金矿资源综合利用率,减少环境污染方面具有潜在的应用价值。
本文旨在探讨循环流态化焙烧技术在复杂难处理金矿矿石预脱硫中的应用研究进展。
一、复杂难处理金矿矿石预脱硫的现状复杂难处理金矿矿石由于其含金量低,矿石结构复杂,有时还伴有其他有害元素的存在,传统的浸取工艺往往效率低下且造成环境污染。
传统的化学浸取方法在复杂金矿中的应用受到了严峻的挑战。
二、循环流态化焙烧技术的基本原理循环流态化焙烧技术是一种利用焙烧反应改变矿石结构的方法。
它通过控制气体流速和温度,使矿石在循环流态化床内不断循环,从而发生氧化还原反应,达到脱硫的目的。
该技术具有反应效率高、操作简便、产物易分离等优势,因此在金矿矿石预脱硫方面具有广泛的应用前景。
三、循环流态化焙烧技术在金矿矿石预脱硫中的应用研究进展1. 循环流态化焙烧参数优化研究在金矿矿石预脱硫过程中,循环流态化床内的气体流速、温度和物料浓度是影响反应效率和产物品质的关键因素。
通过对不同参数的优化研究,可以提高预脱硫的效果和产物的质量。
2. 循环流态化焙烧与其他技术的联合应用研究循环流态化焙烧技术与其他技术的联合应用可以进一步提高预脱硫效果。
例如,与化学浸取技术相结合,可以同时去除金矿矿石中的硫和其他有害元素,提高金的回收率。
与氧化技术相结合,可以使难处理金矿矿石中的金更易于溶解,提高金的提取效率。
3. 循环流态化焙烧床内反应机理研究研究循环流态化床内的反应机理有助于进一步优化循环流态化焙烧技术的参数和工艺。
通过微观和宏观的实验和模拟研究,可以深入了解焙烧反应的速率和热力学特性,为工业应用提供理论依据。
4. 循环流态化焙烧技术的工程应用研究循环流态化焙烧技术的工程应用是将其推广应用于实际生产中的关键。
通过建设大规模的循环流态化焙烧装置,并进行工艺优化和经济分析,可以验证该技术的可行性和经济效益,以促进其在金矿矿石预脱硫中的应用。
焙烧炉技术参数

招标编号:2009-03-S-3-1内蒙古大唐国际鄂尔多斯综合利用高铝粉煤灰生产铝硅钛合金项目焙烧炉招标文件第三卷招标人:内蒙古大唐国际鄂尔多斯硅铝科技项目筹备处二00九年十月中国·沈阳目录附件1技术规范 (2)附件2供货范围................................................................................................... 错误!未定义书签。
附件3技术资料和交付进度............................................................................... 错误!未定义书签。
附件4交货进度................................................................................................... 错误!未定义书签。
附件5监造(检验)和性能验收试验 .............................................................. 错误!未定义书签。
附件6技术服务和设计联络............................................................................... 错误!未定义书签。
附件7分包与外购............................................................................................... 错误!未定义书签。
附件8设备性能违约金的计算........................................................................... 错误!未定义书签。
气体悬浮焙烧炉教材

一、回转窑(d e)描述:氢氧化铝焙烧是氧化铝生产工艺中最后一道工序,焙烧(de)目(de)是在1000℃左右(de)高温下把氢氧化铝(de)附着水和结晶水脱除后,从而生产出符合电解要求和其他用途(de)氧化铝.自1856—1892年以来,分别由法国萨林德厂和奥地利人拜耳研究发明碱-石灰烧结法和利用苛性碱溶液直接浸出铝兔矿生产氧化铝(de)拜耳法以来,已有100多年(de)历史了,截止到1963年,世界各国氧化铝厂基本上都采用回转窑焙烧氢氧化铝来生产氧化铝(de)工艺流程.回转焙烧窑(de)长度一般都在100米左右,直径在3米左右,有2%左右(de)斜度.在开始下料前,首先要点燃安装在窑前(de)油枪,把窑内(de)温度加热到1000℃以上后,开始下料,入窑后(de)湿氢氧化铝随窑体(de)旋转由窑尾被送到窑头,而热气流从窑头向窑尾流动,使湿氢氧化铝在窑内经过烘干、脱水、晶型转变等物理化学变化而焙烧成氧化铝.根据物料在窑内发生(de)物理化学变化,可以将窑从窑尾起划分为以下四个带:1、烘干带:此带(de)主要作用是去除附着水,入窑后(de)湿氢氧化铝并参和电收尘来(de)窑灰由30℃左右被加热到200℃左右,附着水全部被蒸发,烘干带(de)热气则由600℃左右降低到250—350℃左右出窑,经旋风收尘器至电收尘后排入大气层.2、脱水带:此带(de)主要作用是去除结晶水,氢氧化铝由200℃左右继续被加热到900℃左右,全部脱除结晶水变为嘎马氧化铝(γ—氧化铝),而此带(de)温度由1050℃左右降到600℃左右.3、煅烧带:此带(de)主要作用是进行晶型转变,火焰温度可达1500℃左右,嘎马氧化铝(γ—氧化铝)转变为阿尔法氧化铝(α—氧化铝),焙烧温度在1100—1200℃左右,物料在窑内停留40—45分钟左右.4、冷却带:氧化铝在此带冷却到900—800℃左右,然后进入冷却机即生产出产品氧化铝.用回转窑生产氧化铝有几大缺点:1、设备投资大;2、占地面积大;3、热耗高:理论热耗万千卡/吨=t,实际热耗130万千卡/吨= GJ/t左右;4、设备运转周期短,维修强度大,费用高.5、对环境污染严重;6、产品质量不好掌握,波动性较大.焙烧氧化铝(de)主要质量指标是灼减(de)控制,必须控制在%以下,超过%为等外品,回转焙烧窑灼减(de)判断是靠眼来观察高温下氧化铝(de)颜色及流动性来判断(de).用一长把铁勺从窑头舀出一勺氧化铝,如为红色并且流动性很快,这种料一般都不合格,如为杏黄色,灼减一般在—%左右,如为金黄色并发亮,灼减一般在%左右,如为金黄色且有少许结块,灼减一般在—%,如有10毫米以内(de)结块,灼减一般在—%,质量正好(de)氧化铝,其颜色应是杏黄色到黄金色之间,勺子斜放时流动较慢,表面出现凹凸不平(de)痕迹.二、新型氧化铝焙烧窑炉(de)发展和应用:当今世界各国氧化铝厂采用(de)新型焙烧炉主要有三种类型:1、美国铝业公司(de)流态化闪速焙烧炉:美国铝业公司从1946年开始进行流态化焙烧(de)实验和半工业化试验,到1963年第一座300t/d氧化铝(de)流态闪速焙烧炉诞生,用了17年(de)时间,至今美国铝业公司(de)F.F.C装置已发展为五种规格型号,产能最大可达到2400吨以上.2、德国鲁奇公司和联合铝业公司(de)循环流态焙烧炉,鲁奇公司从1958年开始研究氢氧化铝沸腾焙烧,1963年第一座25t/d(de)试验装置成功.1970年在利泊厂建成一台500t/d循环沸腾焙烧炉,从研究到产业化共用了12年时间,最大设计产能3000t/d.3、丹麦史密斯公司(de)气体悬浮焙烧炉:丹麦史密斯公司(de)气体悬浮焙烧是从水泥窑(de)气体悬浮窑处分解装置移植而来,史密斯公司从1975年立项开始进行氢氧化铝气体悬浮焙烧试验,到1979年进入半工业化试验,进行了三个月(de)试验比较成功.1984年在印度(de)享达尔阔厂设计安装了一台850t/d(de)气态悬浮焙烧炉(G..S.C),1986年投产,从研究到产业化共用10年时间.4、法国F.C.B公司(de)气体悬浮焙烧炉:在法国,流态化焙烧炉原先由尤仁辛尔曼公司和西德(de)K.H.D公司所属(de)加丹氧化铝厂内建成一台30t/d 氧化铝(de)闪速焙烧炉,进行了6个月(de)焙烧—铝电解系统(de)联合试验,试验结果非常好,于是F.C.B公司和希腊铝业公司在1981年6月决定在圣.尼古拉斯厂建设一套日产900吨氧化铝(de)气体悬浮焙烧炉,1984年建成投产.三、流态化焙烧技术及装置(de)优缺点:目前,世界上四个国家研制开发(de)三种类型(de)焙烧炉虽各有特点和略有优劣之别,但均具有共同(de)技术经济(de)先进性,与回转焙烧窑相比,流态化焙烧具有以下显着优点:1、焙烧氧化铝理论热耗约为T —AL 2O 3,其余热量主要是出窑废气和焙烧后(de)氧化铝带走或通过窑体散失,而流态化或气态化焙烧(de)热耗约为—kg —AL 2O 3,可节煤气约为300m 3.2、产品质量好:⑴产品中有害杂质SiO 2基本不受焙烧过程(de)影响,只取决于它在氢氧化铝中(de)含量;⑵流态化焙烧产品中不同粒级氧化铝(de)焙烧程度均匀,相同比表面积(de)氧化铝中阿尔法氧化铝(α—氧化铝)含量低,在铝电解中溶解速度较快,可提高铝电解(de)电流效率;⑶流态化焙烧(de)破碎指数不高;⑷三种类型(de)流化焙烧炉均能满足生产砂状氧化铝要求.3.投资少: 流态化焙烧(de)投资比回转窑焙烧(de)投资少,国外各公司发表(de)数据为:(1)美国F .F .C 少50%左右;(2)西德G..S .C 少20%左右;(3)法国G..S .C 少15-20%左右,国内于是1983年,以日产800吨氧化铝(de)焙烧装置为例,根据实物工作量按当时(de)国内价格计算,流态化焙烧装置(de)投资比回转窑少40—60%左右.4.占地面积小:流态化焙烧装置(de)占地面积小,以日产800吨氧化铝(de)焙烧设备为例,仅是回转窑焙烧装置(de)五分之一,而建筑面积约为三分之一至三分之二.5.设备简单,使用寿命长,维修难度低,费用低流态化焙烧系统除了引风机、给料设备之外,没有大型(de)转动设备.炉衬使用寿命可长达10年左右,因而维修费用低,据有关厂家提供(de)数据:流态化焙烧炉(de)维修费用只是回转窑(de)35%左右.6.对环境(de)污染轻由于流态化焙烧炉燃烧完全,过剩空气系数低,废气中氧(de)含量低(de)生成量均要比回转窑低;排入大气(de)烟含尘(1-2%),废气中(de)SO3量均小于50mg/nm3,因此对环境(de)污染轻.四、流态化和气态化焙烧技术和设备在我国应用(de)状况:流态化焙烧炉和气态悬浮焙烧是二十世纪八十年代以来,我国开始引进(de)具有世界先进水平(de)氢氧化铝焙烧技术和设备,该炉型装置具有热耗低、投资少、设备简单、使用寿命长、维修费用低、自动化程度高、有利于环境保护等特点,截止到2005年,我国已投入使用和正在建设中(de)流态化和气态悬浮焙烧炉大约有27台之多,如:山西正在使用(de)6台,山东正在使用(de)2台,郑铝正在使用(de)3台,中州铝正在使用(de)4台,平果铝正在使用(de)2台,桂西正在建(de)2台,贵铝正在使用(de)2台,重庆正在建(de)1台,义马正在使用(de)1台,山东茨平正在建(de)2台,东方希望正在使用(de)一台,开曼即将建成(de)一台.五、三种炉型(de)优劣分析:流态化焙烧炉虽具有共同(de)优点,但认真分析比较,无论从技术经济指标,还是炉型(de)设计成熟性与生产稳定性,不同炉型具有各自(de)特点与不足,比较分析如下:1、美铝流态闪速焙烧炉(F.F.C)美铝流态闪速焙烧炉属正在作业,采用稀相换热和浓相保温相结合(de)技术,相对另两种炉型有其特点:其一:由于采用了调节焙烧温度和停留保温槽料位(控制反应时间)这一双重控制方式,产品质量能得到可靠(de)保障,同时可根据用户(de)要求获得不同灼减、比表面积及α—氧化铝含量(de)焙烧产品.其二:由于整套装置设计了预热炉、流化干燥器、停留保温槽、流化冷却器这四个缓冲器,若焙烧炉(de)干燥段、焙烧段和冷却段中任何一段出现短时故障(或因进出料外部系统影响),另外三段仍能维持运行,整个系统不会产生热工制度(de)大波动,对焙烧炉(de)使用寿命及生产(de)恢复有利,因此整个焙烧炉运行稳定可靠,并且承受各种事故(de)能力强,其三:炉内衬及养护(烘炉)过程设计合理,因此运转率可达95%左右.美铝流态闪速焙烧炉也有其本身(de)不足:一、此套装置适应低水分(de)氢氧化铝物料(6—8%),若氢氧化铝附着水较高时,必需通过增加过剩空气,使热量从焙烧段带入干燥段,以增强干燥能力,相对来说,使焙烧(de)热耗和电耗增加;二、整套装置流化板多,大小床板等多达7块,这样维修时工作量相对增加;三、控制回路多,控制软件设计复杂,相应对操作人员和计控人员提出了较高(de)要求;四、由于系统是正压作业,整个焙烧炉体(de)密封检测点(de)密封及容器回料封系统要求严格.2、鲁奇循环流态焙烧炉(C.F.C)鲁奇循环流态焙烧炉是采用正压作业浓相流态化技术,其炉型有独特之处.其一,流态化循环炉依靠大量(de)物料循环(为产量(de)12—30倍),焙烧停留时间6分钟左右,这样可降低焙烧温度,有利于降低焙烧氧化铝(de)热耗,同时确保焙烧氧化铝产品质量,此外,大量循环物料(de)热仿量、热冲击,维持系统(de)热稳定性,对提高炉内衬(de)使用寿命极为有利,炉子运转率可达90—94%;其二,整个装置无高电压、大型设备,设备简单,投资省,生产控制灵活,事故率低;其三,控制回路简单,流态悬浮焙烧自动控制回路仅有6条.循环流态化也有焙烧炉对颗粒破损率大,究其原因如下:一、气体在喷射口、旋风筒入口及弯头处(de)流速大;二、颗粒在循环炉内发生颗粒之间、颗粒与器壁(de)撞击与摩擦,尽管鲁奇公司对该装置不断地进行改造与完善,使破损率大幅度降低,但目前,焙烧产品45μm粒极(de)破损率仍高达3—6%,其二,循环焙烧炉有4个流化床,不仅在冷却系统设计有流化床,而且在高温段也设有流化床,增加了维修工作量;其三,循环流态焙烧炉与流态闪速焙烧炉一样,亦不适应氢氧化铝附着水高(de)物料.3、丹麦气体悬浮焙烧炉(G..S.C)丹麦气体悬浮焙烧炉是流态化焙烧(de)后起之秀,整个装置采用负压作业、稀相流态化技术,相对比,上述两种炉型具有明显(de)优势.其一,此炉型采用了在干燥段设计安装了热发生器这一新颖措施,当供料氢氧化铝附水含量增加时,不需象其他炉型那样,采取增加过剩空气(de)方式来增加干燥能力,而只需启动干燥热发生器来增加干燥段(de)热量,从而避免了废气量大增而大量热能损失.因此,与前两种炉型相比,气体悬浮焙烧炉热耗和电耗略低一些;其二,整套装置设计简单,一是物料自上而下流动,可避免事故停炉时(de)炉内积料和计划停炉时(de)排料;二是设备简单,除流化冷却器外无任何流化床,没有物料控制阀,方便了设备维修;三是负压作业对焙烧炉(de)问题诊断和事故处理有利.这些都是有利于发生故障后快速恢复生产,给生产带来方便.其三,控制回路简单,气体悬浮焙烧炉虽有12条自动控制回路,但在生产中起主要作用(de)仅有2条,一条是主燃烧系统(de)主炉温度回路,另一条是氧气含量控制回路.气态悬浮焙烧炉是20世纪80年代发展起来(de)(de)气态悬浮焙烧装置,90年代,我国开始引进这一技术,通过近10年来国内各氧化铝厂(de)消化吸收、改进完善,基本上已经定型,目前,它已是国内大部分氧化铝厂焙烧氧化铝设备(de)首选.其主要缺点是:一、烘炉设计不太完美,二、由于各悬浮焙烧炉容器部下料管改用了翻板阀,生产中不能低产运行,即便是刚开始下料,也必须迅速提高产量,其目(de)是避免气流反窜(走短路)或焙烧炉系统内料流形成回流现象,因此,G..S.C 产能(de)可调范围窄,一般要求在设计能力(de)50%以上调节.三、气体悬浮焙烧炉设计(de)检修、清理、观察孔较多,易造成系统漏风隐患,四、电收尘`粉料输送系统和文丘里烟道降温系统(de)设计尚未定型,各氧化铝厂各有千秋.五、各旋风器下料腿结构简单,料封性能差,料腿高,因此气态悬浮焙烧炉(de)炉体高,造成投资增大.国外各公司(de)主要技术经济指标从国外各公司(de)主要技术经济指标和近年来国内各氧化铝厂(de)使用情况来看,一致认为,丹麦(de)气体悬浮焙烧炉(G、S、C)有以下明显(de)优势:①运转率高;②热耗低;③电耗低;④维修方便;⑤生产环境卫生条件好;⑥提产幅度大等优势已被国内外氧化铝厂认可.气体悬浮焙烧炉(de)炉型,是其它二种炉型(de)佼佼者.六、气态悬浮焙烧炉工艺过程描述1、目前国内使用(de)气态悬浮焙烧炉(de)规格有:1850T/D、1400T/D、1300T/D、1200T/D、 850T/D几种规格,但都有相当大(de)提产幅度,焙烧炉(de)热能所需燃料有:一是重油,二是煤气,三是天然气;氢氧化铝(de)焙烧过程是一种固体颗粒与热气流直接混合接触并均匀分布于其中,强化了传质、传热(de)过程,其热效利用率可达80%,回转窑热利用率在40%左右,气态悬浮焙烧炉热效利用率比回转焙烧窑提高了35%以上,它采用(de)是一级载流干燥脱水,一级载流预热,气态悬浮焙烧,四级载流冷却以及流态化床冷却等技术,属于稀相载流焙烧工艺.其固体氢氧化铝颗粒在炉内始终处于悬浮运动状态,在悬浮运动过程中与载流热气进行传质、传热,完成干燥脱水和晶型转变等一系列物理化学演变过程,它具有结构紧凑、产能大、热耗低、焙烧时间短(约秒左右)、系统阻力小和运转率高等优点.2、一级载流干燥脱水是在AO2文丘里干燥器内完成(de),由螺旋给料机把湿氢氧化铝(含水率10%以下)送至AO2文丘里干燥器内,和来自预热旋风筒PO2(de)热气流(约320—400℃左右)进行载流传质、传热,脱除氢氧化铝(de)附着水. 3、一级载流预热是在PO2预热旋风筒内完成(de),来自分离旋风筒(de)氢氧化铝和来自PO3分离旋风筒(de)热气流(约1000—1150℃左右)在PO2旋风筒内进行载流预热,将氢氧化铝加热到300℃左右,脱除氢氧化铝中(de)大部分结晶水.4、气态悬浮焙烧是在PO4主炉内完成(de),来自PO2(de)物料和来自V19主燃烧器所产生(de)1100℃左右(de)高温气流相混合,最终在PO4、PO3筒体内脱除结晶水和完成晶型转变(de)全过程,生产出一种由α—氧化铝和γ—氧化铝混合物料构成(de)且物理化学性质符合电解要求(de)氧化铝产品.5、四级载流冷却是在四个串联(de)旋风筒(CO1、 CO2、CO3、CO4)组成(de)载流冷却装置内完成(de).来自PO3(de)1050℃左右(de)物料和来自冷风进口和流化床冷却器(de)空气进行载流热交换,物料被空气冷却达到250℃左右,而空气被预热到700℃左右后,进入PO4主炉下部,供V19主燃烧器煤气所需(de)助燃气体之用.冷却旋风筒(de)作用:在冷却物料(de)同时回收物料(de)热量,借此提高助燃空气(de)温度,从而提高整个气态悬浮焙烧炉(de)热效率.6、流化床冷却器KO1、KO2是氧化铝物料(de)最终冷却器,来自CO4锥体下部分料阀(de)物料,在流化床内被来自罗茨鼓风机(de)空气流态化,流化床内装有管道冷却器,管内是流动(de)冷却水,流态化(de)物料通过管壁进行热交换,物料从250℃左右被冷却到80℃以下,从流态化冷却器出来(de)氧化铝经输送设施被送到氧化铝大仓.7、气态悬浮焙烧炉内(de)气体流动(de)动力来自炉子尾部(de)排风机,整个炉子处于负压下状态下工作,排风机前面还装有控制风量(de)可调(de)电动风门和净化焙烧炉尾气(de)电收尘,PO1预热旋风筒出来(de)含尘烟气在电收尘器内进行除尘,除尘后(de)气体含尘量要求在50mg/NM3以下,除尘后(de)气体通过烟囱排入大气.整个气态悬浮焙烧炉错落布置,结构紧凑,形成一个完整(de)统一体.气体悬浮焙烧炉(de)主要工作参数:①主炉温度PO4T1 1020—1060℃②CO%<%③O2控制在%—%④文丘里出口温度:140℃⑤电收尘入口温度P11T1:140℃⑥流化床出水温度:≤55℃⑦冷却水进口温度:≤35℃⑧流化床出料温度:≤80℃⑨入炉水份:<10%三、主要设备及构造1、主要设备及构造:⑴喂料螺旋:φ630×3200mm减速电机:YTC-280⑵文丘里闪速干燥器AO2φ3750 mm H=9047 mm材质:δ=6 mm低碳钢:φ3950×9625mm⑶旋风筒PO1材质:δ=6 mm低碳钢⑷旋风筒PO:φ4800×11161mm2材质:δ=6 mm低碳钢⑸旋风筒PO:φ5700×14223mm3材质:δ=6 mm低碳钢:φ5750×17020mm⑹旋风筒PO4材质:δ=6 mm低碳钢:φ4200×9666mm⑺旋风冷却器CO1材质:δ=6 mm低碳钢:φ3450×8307mm⑻旋风冷却器CO2材质:δ=6 mm低碳钢:φ3000×7094mm⑼旋风筒CO3材质:δ=6 mm低碳钢:φ2250×5523mm⑽旋风筒CO4材质:δ=6 mm低碳钢⑾流化床冷却器:1900×1900×10300mm⑿ID风机2150S1BB50流量:Q=240000M3/h电机:YPTQ500-4 P=900KW IP44 690V⒀启动燃烧器T12:SO-1000-GO正常燃油:400kg/h 进口压力:8—25×105Pa 附风机:MT50S 电机:P=15KW⒁燃烧器V19:流量25000Nm3/h⒂点火燃烧器:PG-100作用:内衬养护和焙烧炉主燃烧器点火流量:1000Nm3/h进口压力:250mba电机:KQF-40/44-N风量:15—42M3/min压差:350mba电机: n=2980rpm⒃干燥器加热器:HG-G-63作用:控制干燥器出口温度流量:0—5000Nm3/h风机:MT-50S Q=130M3/min P=15KW3、气体悬浮焙烧炉(de)工艺流程介绍工艺流程图(见附图).①氢氧化铝给料系统由平盘过滤机生产(de)氢氧化铝滤饼经皮带运至皮带称FO1上(de)氢氧化铝小仓中,从皮带秤下来(de)物料经AH小皮带FO3送至螺旋给料机AO1,螺旋给料机把物料送入文丘里闪速干燥器.②文丘里闪速干燥器A02含自由水分≤10%(de)湿氢氧化铝通过螺旋输送机AO1,以50℃温度进入闪速干燥器.在干燥器中干燥了(de)物料由烟气及水蒸气(de)气流带入上部预热旋风筒.闪速干燥器出口(de)温度大约为135℃.给料螺旋(de)出口设计确保滤饼很容易分散到热气流中去.③干燥热发生器T11干燥器AO2出口(de)温度维持在135℃左右,以防止电收尘受到酸腐蚀.为控制因氢氧化铝水分波动而引起干燥器出口温度变化所需要(de)热量由干燥热发生器T11提供.④预热旋风系统烟气和干氢氧化铝(de)混合物在干燥器之后(de)预热旋风筒P01中得以分离.干燥(de)氢氧化铝卸入第二级预热旋风筒PO2(de)上升管,在此与热旋风筒来(de)1050℃左右(de)热气体混合.氢氧化铝在上升管中同时得以预热和分解.物料与气体之间(de)温度实际上已达到完全平衡.预焙烧(de)氧化铝在第二级预热旋风筒PO2中与废气分离后大约以320℃进入焙烧炉.由于经过焙烧(de)物料具有良好(de)流动性和较高(de)温度,通常焙烧辅炉PO3向第一级冷却旋风筒(de)下料管上都不设翻板锁气阀和阀门.然而,第一、二级预热旋风筒和冷却旋风筒(de)下料管都设有翻板锁气阀,以消除反向气流并改善热效率和旋风筒(de)分离效率.⑤焙烧炉PO4气态悬浮焙烧炉和热旋风筒组成为一个反应器—分离器联合系统.焙烧炉是一个有内衬耐火材料且带有锥形底部(de)圆柱形容器.助燃空气在氧化铝冷却器中被预热到600~700℃,并从焙烧炉底部引入.预焙烧后(de)氧化铝平行地加入到炉子(de)锥形底部,在这里,物料同预热(de)空气、燃料充分混合.焙烧炉入口处空气/烟气(de)速度选定以保证正常及部分产能下,在整个反应器断面上颗粒物料都能良好悬浮.反应器合理(de)空气/烟气入口管尺寸可以是任何形式(de)分布板或高压喷嘴得以取消.(这一点是气态悬浮焙烧炉与其他炉型不同(de)关键之处,也是悬浮炉得以命名(de)依据).在热旋风筒PO3中,焙烧好(de)氧化铝从热气流中分离并卸入上部(de)冷却旋风筒CO1(de)上升管.⑥CO1、CO2、CO3和CO4初级冷却器初级冷却在四级旋风筒冷却器组中进行,旋风筒组以紧凑(de)设计垂直布置.氧化铝冷却用空气主要取自大气及第二流态冷却机.空气和热氧化铝之间(de)热交换是在每一个冷却器旋风筒(de)上升管中顺流进行,空气和氧化铝在进入旋风筒中分离之前,其温度已经在上升管中达到了完全平衡.由于旋风多级配置,氧化铝与焙烧炉所需(de)助燃空气之间可以达到完全(de)逆流热交换.离开初级旋风筒冷却器(de)氧化铝约为240℃,再进入第二级流态化冷却机进一步冷却.⑦第二级冷却机KO1和KO2第二级流化床冷却机将旋风筒冷却器来约240℃(de)氧化铝降至80℃以下.流化床中氧化铝通过一组管束换热器用水流反向间接冷却,这种形式(de)冷却机要求(de)空气量受氧化铝流态所限制.流态化所用(de)空气由罗茨鼓风机提供,并通过一块分布板分配到整个流态化床断面上.流态化空气通过一套排风管连接到初级冷却器(de)空气入口管上.⑧除尘系统从顶部预热旋风筒PO1出来(de)含尘废气在电收尘P11中得以净化,两条空气斜槽把收下(de)粉尘卸入返灰系统.除尘后(de)废气通过装有控制风量(de)百叶风门(de)排风机送入大气当中.收下(de)粉尘在一个密闭循环系统中完全回收.。
大型循环流化床锅炉风室与布风板联合布风均匀性数值模拟与试验研究
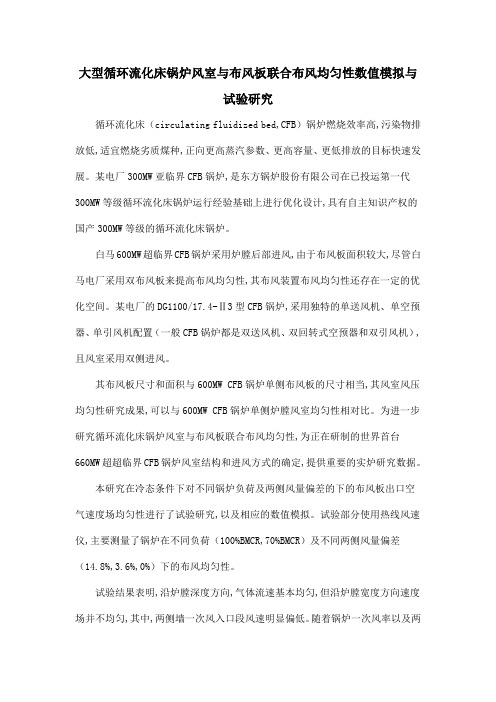
大型循环流化床锅炉风室与布风板联合布风均匀性数值模拟与试验研究循环流化床(circulating fluidized bed,CFB)锅炉燃烧效率高,污染物排放低,适宜燃烧劣质煤种,正向更高蒸汽参数、更高容量、更低排放的目标快速发展。
某电厂300MW亚临界CFB锅炉,是东方锅炉股份有限公司在已投运第一代300MW等级循环流化床锅炉运行经验基础上进行优化设计,具有自主知识产权的国产300MW等级的循环流化床锅炉。
白马600MW超临界CFB锅炉采用炉膛后部进风,由于布风板面积较大,尽管白马电厂采用双布风板来提高布风均匀性,其布风装置布风均匀性还存在一定的优化空间。
某电厂的DG1100/17.4-Ⅱ3型CFB锅炉,采用独特的单送风机、单空预器、单引风机配置(一般CFB锅炉都是双送风机、双回转式空预器和双引风机),且风室采用双侧进风。
其布风板尺寸和面积与600MW CFB锅炉单侧布风板的尺寸相当,其风室风压均匀性研究成果,可以与600MW CFB锅炉单侧炉膛风室均匀性相对比。
为进一步研究循环流化床锅炉风室与布风板联合布风均匀性,为正在研制的世界首台660MW超超临界CFB锅炉风室结构和进风方式的确定,提供重要的实炉研究数据。
本研究在冷态条件下对不同锅炉负荷及两侧风量偏差的下的布风板出口空气速度场均匀性进行了试验研究,以及相应的数值模拟。
试验部分使用热线风速仪,主要测量了锅炉在不同负荷(100%BMCR,70%BMCR)及不同两侧风量偏差(14.8%,3.6%,0%)下的布风均匀性。
试验结果表明,沿炉膛深度方向,气体流速基本均匀,但沿炉膛宽度方向速度场并不均匀,其中,两侧墙一次风入口段风速明显偏低。
随着锅炉一次风率以及两侧风量偏差的提升,风室内气流湍流度增加,布风的不均匀性也随之增强,此外由于一次风管射流在风室入口段造成强烈回流效应,风室入口处的若干风帽出口风速总是要低于其他不受影响的风帽的出口风速。
将模拟结果与试验结果进行对比分析,发现模拟结果与试验结果基本吻合。