27齿轮
齿轮精度等级
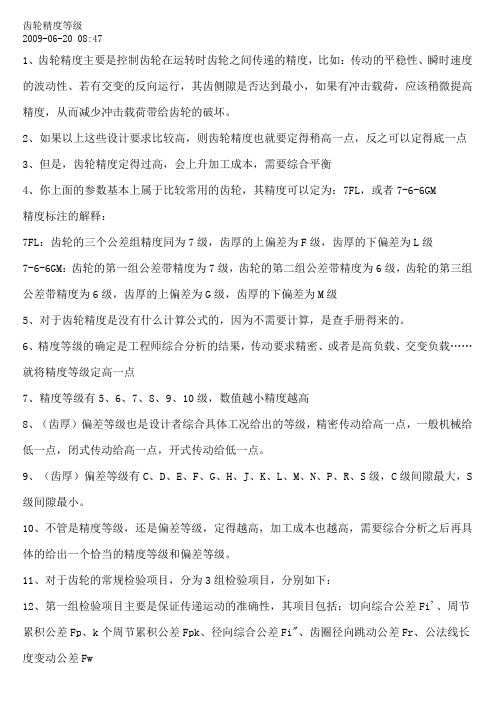
齿轮精度等级2009-06-20 08:471、齿轮精度主要是控制齿轮在运转时齿轮之间传递的精度,比如:传动的平稳性、瞬时速度的波动性、若有交变的反向运行,其齿侧隙是否达到最小,如果有冲击载荷,应该稍微提高精度,从而减少冲击载荷带给齿轮的破坏。
2、如果以上这些设计要求比较高,则齿轮精度也就要定得稍高一点,反之可以定得底一点3、但是,齿轮精度定得过高,会上升加工成本,需要综合平衡4、你上面的参数基本上属于比较常用的齿轮,其精度可以定为:7FL,或者7-6-6GM精度标注的解释:7FL:齿轮的三个公差组精度同为7级,齿厚的上偏差为F级,齿厚的下偏差为L级7-6-6GM:齿轮的第一组公差带精度为7级,齿轮的第二组公差带精度为6级,齿轮的第三组公差带精度为6级,齿厚的上偏差为G级,齿厚的下偏差为M级5、对于齿轮精度是没有什么计算公式的,因为不需要计算,是查手册得来的。
6、精度等级的确定是工程师综合分析的结果,传动要求精密、或者是高负载、交变负载……就将精度等级定高一点7、精度等级有5、6、7、8、9、10级,数值越小精度越高8、(齿厚)偏差等级也是设计者综合具体工况给出的等级,精密传动给高一点,一般机械给低一点,闭式传动给高一点,开式传动给低一点。
9、(齿厚)偏差等级有C、D、E、F、G、H、J、K、L、M、N、P、R、S级,C级间隙最大,S 级间隙最小。
10、不管是精度等级,还是偏差等级,定得越高,加工成本也越高,需要综合分析之后再具体的给出一个恰当的精度等级和偏差等级。
11、对于齿轮的常规检验项目,分为3组检验项目,分别如下:12、第一组检验项目主要是保证传递运动的准确性,其项目包括:切向综合公差Fi'、周节累积公差Fp、k个周节累积公差Fpk、径向综合公差Fi"、齿圈径向跳动公差Fr、公法线长度变动公差Fw13、第二组检验项目主要是保证传递运动的平稳性、噪声、振动,其项目包括:切向一齿综合公差fi'、基节极限偏差fpb、周节极限偏差fpt、径向一齿综合公差fi"14、第三组检验项目主要是保证载荷分布的均匀性,其项目包括:齿向公差Fβ、接触线公差Fb、轴向齿距极限偏差Fpx15、齿轮的齿坯公差的精度等级为:5、6、7、8、9、10级16、齿轮中间的孔公差、及其形位公差:IT5、IT6、IT7、IT8级17、齿轮轴的尺寸公差、及其形位公差:IT5、IT6、IT718、顶圆直径公差:IT7、IT8、IT919、基准面的径向跳动、基准面的端面跳动:根据直径的大小,按照5、6、7、8、9、10级查表20、需要说明一下:我给出的·第一组、第二组、第三组检验项目是比较全的,但是,在实际中,在实际的图纸上,我们列出的检验项目没有这么多,太多了不但给检验带来麻烦,还增加制造成本,所以,在图纸上只检验其中的几项即可,你可以参看一下专业的齿轮图纸,也可以在《机械设计手册》上看看例题,在此给你列出常规要检查的、在图纸上要列出来的项目:21、小齿轮的检验项目:21、根据你上面给出的参数,小齿轮的精度等级可以定为7FL,接下来级,就是按照精度等级差手册:22、周节积累公差Fp:0.06323、周节极限偏差fpt:0.01824、在图纸上标注的齿坯公差:内孔按照IT7级:在手册上按照孔径大小查《标准公差表》25、顶圆的径向跳动:按照外径尺寸大小查《标准公差表》26、大齿轮的检验项目:27、周节积累公差Fp:0.09028、周节极限偏差fpt:0.02029、在图纸上标注的齿坯公差:内孔按照IT7级:在手册上按照孔径大小查《标准公差表》30、顶圆的径向跳动:按照外径尺寸大小查《标准公差表》本网络手册中的圆柱齿轮精度摘自(GB10095—88),现将有关规定和定义简要说明如下:(1) 精度等级齿轮及齿轮副规定了12个精度等级,第1级的精度最高,第12级的精度最低。
齿轮参数中英文对照表
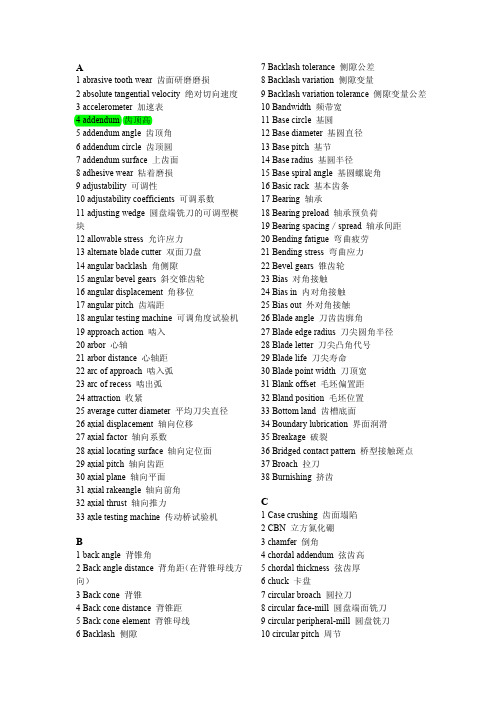
A1 abrasive tooth wear 齿面研磨磨损2 absolute tangential velocity 绝对切向速度3 accelerometer 加速表4 addendum 齿顶高5 addendum angle 齿顶角6 addendum circle 齿顶圆7 addendum surface 上齿面8 adhesive wear 粘着磨损9 adjustability 可调性10 adjustability coefficients 可调系数11 adjusting wedge 圆盘端铣刀的可调型楔块12 allowable stress 允许应力13 alternate blade cutter 双面刀盘14 angular backlash 角侧隙15 angular bevel gears 斜交锥齿轮16 angular displacement 角移位17 angular pitch 齿端距18 angular testing machine 可调角度试验机19 approach action 啮入20 arbor 心轴21 arbor distance 心轴距22 arc of approach 啮入弧23 arc of recess 啮出弧24 attraction 收紧25 average cutter diameter 平均刀尖直径26 axial displacement 轴向位移27 axial factor 轴向系数28 axial locating surface 轴向定位面29 axial pitch 轴向齿距30 axial plane 轴向平面31 axial rakeangle 轴向前角32 axial thrust 轴向推力33 axle testing machine 传动桥试验机B1 back angle 背锥角2 Back angle distance 背角距(在背锥母线方向)3 Back cone 背锥4 Back cone distance 背锥距5 Back cone element 背锥母线6 Backlash 侧隙7 Backlash tolerance 侧隙公差8 Backlash variation 侧隙变量9 Backlash variation tolerance 侧隙变量公差10 Bandwidth 频带宽11 Base circle 基圆12 Base diameter 基圆直径13 Base pitch 基节14 Base radius 基圆半径15 Base spiral angle 基圆螺旋角16 Basic rack 基本齿条17 Bearing 轴承18 Bearing preload 轴承预负荷19 Bearing spacing/spread 轴承间距20 Bending fatigue 弯曲疲劳21 Bending stress 弯曲应力22 Bevel gears 锥齿轮23 Bias 对角接触24 Bias in 内对角接触25 Bias out 外对角接触26 Blade angle 刀齿齿廓角27 Blade edge radius 刀尖圆角半径28 Blade letter 刀尖凸角代号29 Blade life 刀尖寿命30 Blade point width 刀顶宽31 Blank offset 毛坯偏置距32 Bland position 毛坯位置33 Bottom land 齿槽底面34 Boundary lubrication 界面润滑35 Breakage 破裂36 Bridged contact pattern 桥型接触斑点37 Broach 拉刀38 Burnishing 挤齿C1 Case crushing 齿面塌陷2 CBN 立方氮化硼3 chamfer 倒角4 chordal addendum 弦齿高5 chordal thickness 弦齿厚6 chuck 卡盘7 circular broach 圆拉刀8 circular face-mill 圆盘端面铣刀9 circular peripheral-mill 圆盘铣刀10 circular pitch 周节11 circular thickness 弧齿厚12 circular thickness factor 弧齿厚系数13 clearance 顶隙14 clearance angle 后角15 coarse pitch 大节距16 coast side 不工作齿侧17 combination 组合18 combined preload 综合预负荷19 complementary crown gears 互补冠状齿轮20 completing cycle 全工序循环21 composite action 双面啮合综合检验误差22 compressive stress 压应力23 concave side 凹面24 concentricity 同心度25 concentricity tester 同心度检查仪26 cone distance 锥距27 cone element 锥面母线28 conformal surfaces 共型表面29 coniskoid 斜锥齿轮30 conjugate gears 共轭齿轮31 conjugate racks 共轭齿条32 contact fatigue 接触疲劳33 contact norma 接触点法线34 contact pattern (tooth contact pattern) 轮齿接触斑点35 contact ratio 重合度36 contact stress 接触应力37 continuous index 连续分度38 control gear 标准齿轮,检验用齿轮39 convex side 凸面40 coolant 冷却液41 corrosive wear 腐蚀性磨损42 corrugated tool 阶梯刨刀43 counter forma surfaces 反法向表面44 cradle 摇台45 cradle test roll 摇台角46 cross 大小端接触47 crossing point 交错点48 crown 齿冠49 crown circle 锥齿轮冠圆50 crowned teeth 鼓形齿51 crown gear 冠轮52 crown to back (轮冠距)轮冠至安装定位面距离53 crown to crossing point 轮冠至相错点距离54 cutter 刀盘55 cutter axial 刀盘的轴向位置56 cutter axial plane 刀盘轴向平面57 cutter axis 刀盘轴线58 cutter diameter 刀盘直径59 cutter edge radius 刀刃圆角半径60 cutter head 刀盘体61 cutter number 刀号62 cutter parallel 刀盘平垫片63 cutter point diameter 刀尖直径64 cutter point radius 刀尖半径65 cutter point width 刀顶距66 cutter spindle 刀盘主轴67 cutter spindle rotation angle 刀盘主轴转角68 cutting distance 切齿安装距69 CV testing mashing 常速试验机70 cyclex 格里森粗铣精拉法圆盘端铣刀71 cylindrical gears 圆柱齿轮D1 Datum tooth 基准齿2 Debur 去毛刺3 Decibel (CB) (噪音)分贝4 Decimal ratio 挂轮比值5 Dedendum 齿根高6 Dendendum angle 齿根角7 Dedendum surface 下齿面8 Deflection 挠曲9 Deflection test 挠曲试验10 Deflection testing machine 挠曲试验机11 Depthwise taper 齿高收缩12 Design data sheet 设计数据表13 Destructive pitting 破坏性点蚀14 Destructive wear 破坏性磨损15 Developed setting 试切调整16 Dial indicator 度盘式指示表17 Diametral pitch 径节18 Diamond 菱形接触19 Dinging ball check 钢球敲击检查20 Disc-mill cuter 盘铣刀21 Dish angle 凹角22 Displacement 位移23 Displacement error 位移误差24 Double index 双分度25 Double roll 双向滚动26 Down roll 向下滚动27 Drive side 工作齿侧28 Duplete 双刃刀29 Duplex 双重双面法30 Duplex helical 双重螺旋法(加工方法之一)31 Duplex spread blade 双重双面刀齿(加工/磨齿方法)32 Duplex taper 双重收缩齿33 Durability factor 耐久系数34 Dynamic factor 动载荷系数E1 Ease-off 修正、失配2 Eccentric 偏心3 Eccentric angle 偏心角4 Eccentricity 偏心度5 Edge radius 刀尖圆角半径6 Effective bearing spacing 轴承有效间距7 Effective face width 有效宽度(有效齿宽)8 Elastic coefficient 弹性系数9 Elastic deformation 弹性变形10 Elastic limit 弹性极限11 Elastohydrodynamic lubrication 弹性液压润滑12 Element 母线、要素13 End movement 轴向移动14 Endrem 修内端凸轮、导程凸轮15 Endurance life 耐久寿命16 Endurance limit 耐久极限17 Engine torque 发动机扭矩18 Enveloping 包络19 EP lubricant, EP 极压润滑剂20 EPG check, “EPG” 检查21 Equal addendum teeth 等齿顶高齿22 Equicurv 等高齿大轮成形法23 Equidep 等高齿24 Equiside 等边25 Equivalent fear ratio 当量传动比26 Equivalent number of teeth 当量齿数27 Equivalent pitch radius 当量节圆半径28 Equivalent rack 当量齿条29 Expander 涨胎30 Expanding arbor 可张心轴31 Extreme pressure lubricant 极压润滑剂F1 Face acvance 斜齿轮扭曲量2 Face angle 顶锥角(面锥角)3 Face angle distance 顶锥角距4 Face apex 顶锥顶5 Face apex beyond crossing point 顶锥顶至相错点距离6 Face cone 顶锥7 Face cone element 齿顶圆锥母线,面锥母线8 Face contact ratio 齿长重合度,轴向重合度(圆柱齿轮)9 Face line 齿面与轴面交线10 Face width 齿宽11 Factor of safety 安全系数12 Fatigue breakage 疲劳破裂13 Fatigue failure 疲劳失效14 Fatigue test 疲劳测试15 Feed cam 进给凸轮16 Feed gears 进给齿轮17 Fillet 齿根圆角18 Fillet curve 齿根过渡曲线19 Fillet radius 齿根圆角半径20 Film strength 液膜强度21 Filter (electronic) (电子的)滤波器22 Filter (mechanical) (机械的)滤波器23 Fine pitch (小模数)细径节24 Finisher 精切机床25 Fishtail 鱼尾形26 Fixed setting 固定安装法27 Flank 下齿面28 Flanking 下齿面加工29 Formarc 加工齿轮用的曲线齿廓刀具30 Formate 成形法31 Former 齿廓样板,靠模32 Forming 成型,在磨具内挤压成型33 Form tool 成形刀34 Fourier analysis 傅里叶分析35 Frequency 频率36 Friction load 摩擦负荷37 Front angle 前角38 Front cone 前锥39 Front crown 前锥齿冠40 Front crown to crossing point 前锥齿冠至交错点41 Full-depth teeth 全齿高齿42 Fundametal 基频G1 Gable 山形齿沟底面2 Gear 齿轮3 Gear axial displacement 齿轮轴向位移4 Gear axial plane 齿轮轴向平面5 Gear axis 齿轮轴线6 Gear center 齿轮中心7 Gear combination 齿轮组合8 Gear cone 大轮锥距9 Geared index 齿轮系分度10 Gear finisher 成形法齿轮精切机床11 Gear manufacturing summary 齿轮加工调整卡12 Gear marking compound 检查齿轮啮合涂色剂13 Gear member 大轮14 Gear planer 成型刨齿机15 Gear ratio 齿数比16 Gear rougher 齿轮粗切机床17 Gears 齿轮组18 Gear tipping 齿轮倾斜19 Generated gear 展成法齿轮20 Generating cam 展成凸轮21 Generating gear 展成齿轮22 Generating pressure angle 产形轮压力角23 Generating train 展成传动键24 Generation 展成25 Generator 展成齿轮加工机床26 Geneva index 星形轮分度,槽轮分度27 Geometry factor-durability 齿面接触强度几何系数28 Geometry factor0-strength 强度几何系数29 G-flow 格里森制金属件的商标,采用冷挤压成形法30 G-form 采用热锻成形法制造31 GLE-sine 砂轮内外压力角正弦波进行修整用机构32 G-plete 全工序法33 Gradeability 托曳力34 Grinding cracks 磨削裂纹35 G-spin 精密主轴的机床36 G-trac 圆柱齿轮的无端链式机床的商标H1 Hand of cutter 刀盘方向2 Hand of spiral 螺旋方向3 Hand-rolling tester 手动滚动试验机4 Hardac 镶篇淬硬刀体精切刀盘5 Hard finishing 硬齿面精加工6 Hardness ratio factor 硬度比系数7 Harmonic 谐振8 Harmonic search 谐振追踪9 Harmonic sweep 谐振扫描10 Heel 轮齿大端11 Heel pattern 大端接触12 Helical duplex 双重螺旋法13 Helical motion 螺旋运动14 Helixact 螺旋运动法15 Helixform 螺旋成形法16 Hertz (Hz) 赫兹17 Hook angle 断面前角18 Horizontal displacement 水平位移19 Horizontal offset 水平偏置20 HRH 高减速比准双曲面齿轮(大于10:1的减速比)21 Hunting tooth combination 大小齿轮齿数无公因数的齿轮副22 Hudrodynamic lubrication 液压润滑23 Hupermesh 超配合24 Hypoid gears 准双曲面齿轮25 Hypoid offset 准双曲面齿轮偏置距I1 Imaginary generating gear 假想成形法2 Incremental index 逐齿分度3 Index gears 分度齿轮4 Index interval 分度跳跃齿齿数5 Index plate 分度盘6 Index tolerance 分度公差7 Index variation 分度变化量8 Indicator anchorage 指示表支撑座9 Inertia factor 惯量系数10 Initial pitting 初期点蚀11 Inner addendum 小端齿顶高12 Inner cone distance 小端锥距13 Inner dedendum 小端齿根高14 Inner slot width 小端槽宽15 Inner spiral angle 小端螺旋角16 Inserted blade cutter 镶片刀盘17 Inside blade 内切刀齿18 Inside point diameter 内切刀尖直径19 Instantaneous contact pattern 瞬时接触斑点20 Interference 干涉21 Interference point 干涉点22 Interlocking disc-mill cutters 交错齿盘形铣刀23 Intermittent index 间断分度24 Internal bevel gear 内锥齿轮25 Inverse gear ratio 反齿数比26 Involute 渐开线27 Involute gear 渐开线齿轮28 Involute interference point 渐开线干涉点29 Involute spiral angle 渐开线螺旋角30 Involute teeth 渐开线齿J1 Jet lubrication 喷射润滑L1 Lame 顶根接触2 Lapping 研磨3 Lead cam 导程凸轮4 Length of action 啮合长度5 Lengthwise bridge 纵向桥型接触6 Lengthwise mismatch 纵向失配7 Lengthwise sliding velocity 纵向滑动速度8 Life factor 寿命系数9 Lift 垂直位移10 Limit point width 极限刀顶距11 Limit pressure angle 极限压力角12 Linear displacement transducer 线性位移传感器13 Line of action 啮合线14 Line of centers 中心线15 Line of contact 接触线16 Load sharing ratio 负荷分配比17 Localized tooth contact 齿局部接触18 Locating surface 定位表面19 Long-and-short-addendum teeth 高变位齿轮20 Long-toe-short-heel 小端长,大端短接触21 Lubricant 润滑剂22 Lubrication 润滑23 Lubricity 润滑性M1 Machine center 基床中心点2 Machine center to back 机床中心至工件安装基准面3 Machine plane 机床切削平面4 Machine root angle 毛坯安装角5 Marking compound 检查齿轮啮合型情况使用的涂色剂6 Master blade 标准刀齿7 Master gear 标准齿轮8 Mean addendum 中点齿顶高9 Mean cone distance 中点锥距10 Mean dedendum 中点齿根高11 Mean diametral pitch 中点径节12 Mean measuring addendum 中点测量齿顶高13 Mean measuring depth 中点测量齿高14 Mean measuring thickness 中点测量厚度15 Mean normal base pitch 中点法向基节16 Mean normal diameter pitch 中点法向径节17 Mean normal module 中点法向模数18 Mean point 中点,平均点19 Mean radius 中点半径20 Mean section 中点截面21 Mean slot width 中点齿槽宽22 Mean spiral angle 中点螺旋角23 Measuring addendum 测量齿顶高24 Measuring tooth thickness 测量齿厚25 Member 齿轮,元件26 Mesh point 啮合点27 Minimum slot width 最小槽宽28 Mismatch 失配29 Miter gears 等齿数整角锥齿轮副30 Mixed lubrication 混合润滑31 Modified contact ratio 修正总重合度32 Modified roll 滚修正比33 Module 模数34 Motion curves 运动曲线35 Motor torque 电机扭矩36 Mounting distance 安装距37 Mounting surface 安装面N1 Narrow-tow-wide-heel 小端窄大端宽接触2 No load 空载3 Nominal 名义4 Non-generated gear 非展成大轮5 Normal 法向,法线,法面6 Normal backlash 法向侧隙7 Normal backlash tolerance 法向侧隙公差8 Normal base pitch 法向基节9 Normal chordal addendum 法向弦齿高10 Normal chordal thickness 法向弦齿厚11 Normal circular pitch 法向周节12 Normal circular thickness 法向弧齿厚13 Normal contact ratio 法向重合度14 Normal diametral pitch 法向径节15 Normal direction 法线方向16 Normal (perpendicular) load 法向(垂直)负载17 Normal module 法向模数18 Normal plane 法向平面19 Normal pressure angle 法向压力角20 Normal section 法向截面21 Normal space-width taper 正常齿槽宽收缩22 Normal thickness taper 正常齿厚收缩23 Normal tilt 法向刀倾24 Normal wear 正常磨损25 No-roll roughing 无滚动粗切26 Number of teeth 齿数O1 Octoid teeth 锥齿轮的“8”字啮合2 Offset 偏置距3 Operating load 工作负荷4 Operating pressure angle 工作压力角5 Operating torque 工作扭矩6 Outer addendum 大端齿顶高7 Outer cone distance 外锥距8 Outer dedendum 大端齿根高9 Outer slot width 大端槽宽10 Outer spiral angle 大端螺旋角11 Outside blade 外切刃点12 Outside diameter 外径,大端直径13 Outside point diameter 外切刀尖直径14 Outside radius 齿顶圆半径15 Outside surface 外表面16 Overhung mounting 双支承安装17 Overload breakage 超负荷破裂18 Overload factor 超负荷系数P1 Path of action 啮合点轨迹2 Path of contact 接触迹3 Peak load 峰值负荷4 Peak torque 峰值扭矩5 Pedestal bearings 安装差速器壳的架座轴承6 Performance torque 性能扭矩7 Perim-mate 研磨锥齿轮和准双面齿轮用的全齿面研磨法8 Pinion 小轮9 Pinion axial displacement 小轮轴向位移10 Pinion cone 小轮锥距11 Pinion front bearing 小轮前端轴承12 Pinion head bearing 小轮后端前轴承13 Pinion rear bearing 小轮后端后轴承14 Pinion rougher 小轮粗切机15 Pinion offset 小轮偏置距16 Pitch 节距,齿距17 Pitch angle 节锥角18 Pitch apex 节锥顶19 Pitch apex beyond crossing point 节锥顶超出至相错点20 Pitch apex to back 节锥顶至安装端面21 Pitch apex to crown 节锥顶至轮冠22 Pitch circle 节圆23 Pitch cone 节锥24 Pitch curve 节面曲线25 Pitch diameter 节径26 Pitch element 节面母线27 Pitch line 节线28 Pitch-line chuck 节圆夹具29 Pitch-line runout 节线跳动30 Pitch plane 节面31 Pitch point 节点32 Pitch radius 节圆半径33 Pitch surfaces 节曲面34 Pitch tolerance 齿距公差35 Pitch trace 节线36 Pitch variation 齿距变化量37 Pitting 点蚀38 Plane of action 啮合平面39 Plane of rotation 旋转平面40 Planning generator 展成法刨齿机41 Plastic deformation 塑性变形42 Plastic flow 塑性流动43 Plate index 分度盘44 Point diameter 刀尖直径45 Point of contact 接触点46 Point radius 刀尖半径47 Point width 刀顶距48 Point width taper 刀顶距收缩49 Pressure lubrication 压力润滑50 Prime mover torque 原动机扭矩51 Profile angle 齿廓角52 Profile bridge 齿廓桥形接触53 Profile contact ratio 齿廓重合度54 Profile mismatch 齿廓啮合失配55 Profile radius of curvature 齿廓曲率半径56 Proof surface 检测基准面Q1 Quality measurement system 质量检测系统2 Quenching cracks 淬火裂纹3 Quenching die 淬火压模4 Quenching press 淬火压床R1 Rack 齿条2 Radial 径向刀位3 Radial load 径向负荷4 Radial locating surface 径向定位表面5 Radial rake angle 径向前角6 Ratio control roughing 变滚比粗切7 Ratio gears 滚比挂轮8 Ratio of roll 滚比9 Ratio of roll gears 滚比挂轮10 Recess action 啮出11 Relative displacement 相对位移12 Relative movement 相对运动13 Relative radius of curvature 相对曲率半径14 Residual stress 残余应力15 Revacycle 直齿锥齿轮圆拉法用机床及刀具16 Revex 直齿锥齿轮粗拉法17 Ridg-AC 镶片圆盘端面粗铣刀18 Ridging 沟条变形19 Ring gear 大轮,环形齿轮20 Rippling 振纹21 Roll centering 滚动定心22 Roll queching 滚动式淬火压床23 Roll gears 摆角挂轮24 Rolling 滚轧25 Rolling velocity 滚动速度26 Root angle 根锥角27 Root angle tilt 齿根角倾斜28 Root apex 根锥顶29 Root apex beyond crossing point 根锥顶至相错点的距离30 Root apex to back 根锥顶至安装基准面距离31 Root circle 齿根圆32 Root cone 根锥33 Root diameter 根圆直径34 Root line 齿根线35 Root radius 根圆半径36 Root surface 齿根曲面37 Roughac 弧齿锥齿轮粗切刀38 Rougher 粗切机39 RSR 弧齿锥齿轮条形刀齿铣刀盘40 Runout 径向跳动41 Runout tolerance 径向跳动公差S1 Scoring 胶合2 Scoring index 胶合指数3 Scuffing 胶合4 Sector 扇形齿/齿弧5 Segment 扇形齿/体6 Segmental-blade cutter 大轮精切刀7 Separation 分离间隙8 Separating factor 分离系数9 Separating force 分离力10 Set-in 补充切入,进刀11 Set-over 补充转角,调整转换12 Shaft angle 轴转角13 Shot peening 喷丸强化14 Sidebank 边频15 Side movement 侧向位移16 Side rake angle 侧前角17 Single cycle 单循环法18 Single roll 单滚动19 Single setting 单面调整法20 Single side 单面精切法21 Single-side taper 齿槽收缩22 Size factor 尺寸系数23 Skew bevel gears 斜直齿锥齿轮24 Skip index 跳齿分度25 Slide-roll ratio 单位滑滚比,比滑26 Sliding base 床鞍,滑座27 Sliding base setting 床鞍调整,滑座调整28 Sliding velocity 滑动速度29 Slip-chip 直齿锥齿轮一次成形刀30 Slip torque 滑移扭矩31 Slotting tool 切槽刀32 Slot width 槽宽33 Slot-width taper 槽宽收缩34 Small cutter development 小刀盘试切,能产生接近渐开线的刀具35 Solid cutter 整体刀盘36 Sound test 噪声试验37 Space-width taper 齿距收缩38 Spacing tolerance 齿距公差39 Spacing variation 齿距变动量40 Spalling 剥落41 Specific sliding 单位滑动比42 Speed gears 速度挂轮43 Spherical involute teeth 球面渐开线齿44 Spherica limacon teeth 球面钳线齿45 Spindle rotation angle 主轴旋转角46 Spiral angle 螺旋角47 Spiral bevel gears 弧齿锥齿轮48 Splash lubrication 飞溅润滑49 Split profile 齿型中断50 Spread blade 双面刀51 Spread blade 双面刀渐缩52 Standard depthwise taper 标准深锥度53 Standard taper 正常收缩54 Standard thickness 正常齿厚收缩55 Stock allowance 毛坯加工流量56 Straddle cutter 双列刀齿刀盘57 Straddle mounting 跨装58 Straight bevel gears 直齿锥齿轮59 Strength factor 强度系数60 Stress concentration factor 应力集中系数61 Stub teeth 短齿62 Subsurface initiated fatigue breakage 金属表面斜层初始疲劳破裂63 Summary of machine settings 机床调整卡64 Sump lubrication 油槽润滑65 Sum velocity 总速度66 Surface asperities 表面粗糙度67 Surface condition factor 表面条件系数68 Surface deformation 表面变形69 Surface durability 表面耐久度70 Surface fatigue 表面疲劳71 Surface initiated fatigue breakage 表面初始疲劳破裂72 Surface of action 啮合面73 Surface of revolution 回转面74 Surface treatment 表面处理75 Swinging base 回转底座76 Swing pinion cone 摆动小轮节锥法77 Swivel 刀转78 Swivel angle 刀转角79 Symmetrical rack 对称齿条80 Symmetrical rack proportions 对称齿条比例T1 Tangential load 切向负荷2 Tangent plane 切平面3 Tanline 小轮夹具4 Tanruf 双联粗切刀,85模数一下5 Tan-tru 用在加工1016-2540mm的锥齿刀具6 Taper roughing 具有刀顶距收缩的大小轮粗切过程7 Temperature factor 温度系数8 Testing machine 试验机9 Thickness taper 齿厚收缩10 Tilt 刀倾11 Tilt angle 刀倾角12 Tilted rootline taper 倾斜齿根收缩13 Tip radius 齿顶圆角半径14 Toe 轮齿小端15 Toe pattern 小端接触16 Tool 刀具17 Tool advance 刀具进刀18 Tool edge radius 刀刃圆角半径19 Tool point width 刀顶距20 Tooth angle 齿角21 Tooth bearing 齿支撑面,轮齿接触面22 Tooth contact analysis 轮齿接触分析23 Tooth contact pattern 轮齿接触斑点24 Tooth horizontal 齿水平面25 Tooth layout 轮齿剖面图26 Tooth-mesh frequency 齿啮合频率27 Tooth number 齿数28 Tooth profile 齿形,齿廓29 Tooth spacing testing 齿距检查仪30 Tooth spiral 齿螺旋线31 Tooth surface 轮齿表面32 Tooth taper 轮齿收缩33 Tooth-to-tooth composite tolerance 一齿度量中心距公差34 Tooth-to- Tooth composite variation 一齿度量中心距变量35 Tooth trace 齿线36 Tooth vertical 齿垂直面37 Top 齿顶38 Topland 齿顶面39 Topland width 齿顶面宽度40 Topping 修顶41 Top relief angle 顶刃后角42 Toprem 修根刀片43 Toprem angle 刀齿突角角度44 Top slope angle 刀齿顶刃倾角45 Total composite tolerance 总综合公差46 Total composite variation 总度量中心距变动量47 Total contact ratio 总重合度48 Total index tolerance 总分度公差49 Total index variation 总分度变动量50 Tractive effort torque 牵引力扭矩51 Transverse circular pitch 端面周节52 Transverse circular thickness 端面弧齿厚53 Transverse contact ratio 端面重合度54 Transverse diametral pitch 端面径节55 Transverse module 端面模数56 Transverse plane 端平面57 Transverse pressure angle 端面压力角58 Transverse space-width taper 端面槽宽收缩59 Transverse thickness taper 端面齿厚收缩60 Tredgold’s approximation 背锥近似法61 Tribology 润滑与磨损学62 Triplex 三面刃圆盘端铣刀63 Two-tool generator 双刀展成加工机床U1 Undercut 根切2 Undeveloped settings 试切前调整3 Uniform roll 匀速滚动4 Uniform velocity tester 匀速试验机5 Uni-spand 大轮心轴6 Unit load 单位负荷7 Unitool 曲面镶片刀8 Up-roll 向上滚动V1 V and H check 锥齿轮啮合的VH检查2 Variable roll 变滚动3 Velocity factor 速度系数4 Versacut 弧齿锥齿轮加工多用刀盘5 Vers-grip 卡紧小齿轮用的卡盘(商标名称)6 Vertical direction 垂直方向7 Vertical displacement 垂直位移8 Vertical factor 垂直系数9 Vertical force 垂直力10 Vertical offset 垂直偏置距11 Vertical plane 垂直面12 Virtual number of teeth 当量齿数13 Virtual pitch radius 当量节圆半径14 Viscosity 粘度15 V-tool V型刀具W1 Waveform 波形2 Wear 磨损3 Webless-type gear 无幅板式齿轮4 Web-type gear 幅板式齿轮5 Wheel slip torque 车轮打滑扭矩6 Whole depth 齿全高7 Workhead 工件头座8 Workhead offset 垂直轮位9 Workholding equipment 工件夹具10 Working depth 工作齿高11 Working stress 工作允许应力12 Work tests roll 检验工件主轴转角X1X-pandisk 大轮蝶形,涨胎心轴Z1 Zero depthwise taper 等齿高2 Zerol 零度锥齿轮。
齿轮各项公差表
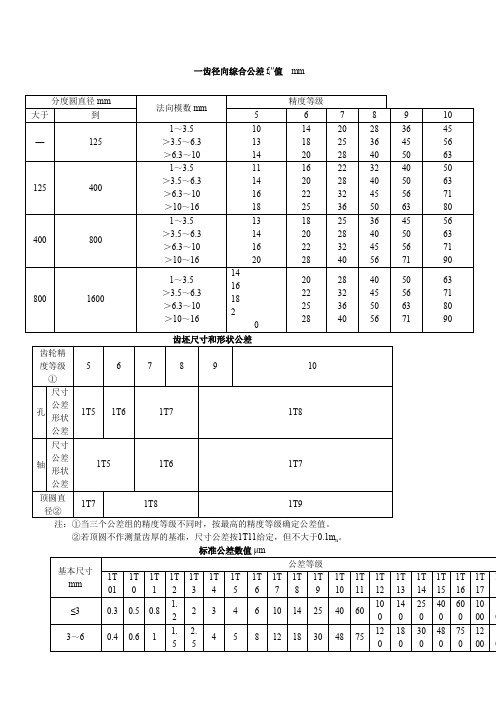
一齿径向综合公差f i″值m m分度圆直径mm法向模数mm 精度等级大于到 5 6 7 8 9 10—1251~3.5>3.5~6.3>6.3~10101314141820202528283640364550455663125 4001~3.5>3.5~6.3>6.3~10>10~16111416181620222522283236324045504050566350637180400 8001~3.5>3.5~6.3>6.3~10>10~16131416201820222825283240364045564550567156637190800 16001~3.5>3.5~6.3>6.3~10>10~1614161822022252828323640404550565056637163718090齿坯尺寸和形状公差齿轮精度等级①5 6 7 8 9 10孔尺寸公差形状公差1T5 1T6 1T7 1T8轴尺寸公差形状公差1T5 1T6 1T7顶圆直径②1T7 1T8 1T9 注:①当三个公差组的精度等级不同时,按最高的精度等级确定公差值。
②若顶圆不作测量齿厚的基准,尺寸公差按1T11给定,但不大于0.1m n 。
标准公差数值μm基本尺寸mm公差等级1T011T1T11T21T31T41T51T61T71T81T91T101T111T121T131T141T151T161T1711≤30.3 0.5 0.8 1.22 3 4 6 10 14 25 40 601014254060100013~6 0.4 0.6 1 1.52.54 5 8 12 18 30 48 751218304875120016~10 0.4 0.6 1 1.52.54 6 9 15 22 36 58 9015223658901500210~18 0.5 0.8 1.2 2 3 5 8 11 18 27 43 70 111827437011001800218~30 0.6 1 1.5 2.54 6 9 13 21 33 52 84132133528413002100330~50 0.6 1 1.5 2.54 7 11 16 25 39 621016253962100016002500350~80 0.8 1.2 2 3 5 8 13 19 30 46 74 1219304674120019003000480~120 1 1.5 2.5 4 6 10 15 22 35 54 87 14223554871400220035005120~180 1.2 2 3.5 5 8 12 18 25 40 63 101625406310001600250040006180~250 2 3 4.5 7 10 14 20 29 46 72 11518529467211501850290046007250~315 2.5 4 6 8 12 16 23 32 52 81 132132528113002100320052008315~400 3 5 7 9 13 18 25 36 57 89 142336578914002300360057008400~500 4 6 8 10 15 20 27 40 63 97 1552540639715502500400063009500~630 4.5 6 9 11 16 22 30 44 70 11175284470110017502800440070001630~800 5 7 10 13 18 25 35 50 80 125203250801250200032005000800015齿坯基准面径向跳动*和端面圆跳动公差m m 直径(mm)精度等级到5、6 7、89、10125 400 800 1600 111420281822324528365071注:*当以顶圆作基准面时,本栏就指顶圆的径向跳动。
齿轮各项公差表
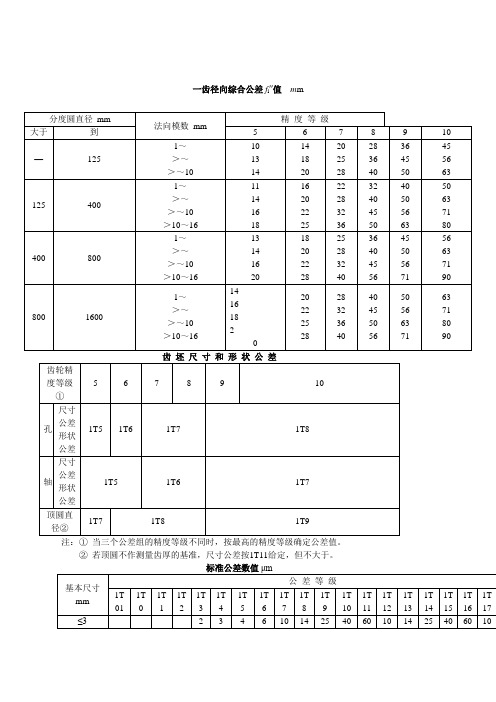
一齿径向综合公差f i″值m m
注:①当三个公差组的精度等级不同时,按最高的精度等级确定公差值。
②若顶圆不作测量齿厚的基准,尺寸公差按1T11给定,但不大于。
标准公差数值μm
齿坯基准面径向跳动*和端面圆跳动公差m m
注:*当以顶圆作基准面时,本栏就指顶圆的径向跳动。
齿轮的表面粗糙度(R
注:本表不属GB10095-88,供参考。
非变位直齿圆柱齿轮分度圆上弦齿厚及弦齿高
(a*
注:1. 用成形铣刀加工齿轮时,标注和测量分度圆弦齿厚和弦齿高;
用范成法加工时,可以标注或测量固定弦厚和弦齿高。
2. 对于斜齿圆柱齿轮和圆锥齿轮,使用本表时,应以当量齿数z d代替z(斜齿轮:z d=z/cos3b b;
锥齿轮:z d=z/cosd)。
z d非整数时,可用插值法求出。
3. 本表不属GB10095-88,供参考。
27其它常用齿轮及其传动的选择和应用

《机械基础》教案(2009~ 2010学年第二学期)学院山西省工贸学校系(部)机电系教研室教师梁少宁山西省工贸学校③学生学案课题名称:接触器联锁电动机正反转控制电路的安装与调试班级:姓名:(一)、工作任务:某工厂自制一台简易机床,要求能实现主轴的“正转—停止—反转”功能,该机床采用三相笼型异步电动机拖动,电压380V,功率3kW。
工作过程如下:1、按下正转按钮,电动机带动机床主轴正转运行;2、按下停止按钮,电动机停止运行;3、按下反转按钮,电动机带动机床主轴反转运行。
要求电路有必要的电气保护。
为防止意外发生,还必须设有急停按钮。
试设计该电路,并安装调试合格。
(二)、学习目标:在前面已经学习点动、单向连续控制电路安装与调试的基础上:1、掌握接触器常闭辅助触点联锁的特点;2、掌握接触器联锁电动机正反转控制电路的工作原理;3、掌握电路正确的接线与调试方法;4、掌握该电路中电工元器材的选择方法。
(三)、回答问题1、原来正转的电动机,如何改变主电路的接线才能实现电动机的反转功能?2、该电路中如果二只交流接触器线圈同时通电吸合,会产生什么后果?你在该电路中是如何避免这种情况发生的?(四)、分析该资料,完成下列项目任务: 【新授】一、斜齿圆柱齿轮及其传动1、斜齿圆柱齿轮齿线为螺旋线的圆柱齿轮称为斜齿圆柱齿轮,简称斜齿轮。
2、斜齿圆柱齿轮传动的特点 (1)传动平稳,承载能力高。
(2)传动时产生轴向力。
(3)不能用作变速滑移齿轮.3、标准斜齿圆柱齿轮几何尺寸的计算法向截面内的模数n m 采用标准模数,齿形角采用标准齿形角,齿顶高等于模数,全齿高等于m 25.2的斜齿圆柱齿轮称为标准斜齿圆柱齿轮, 简称标准斜齿轮。
斜齿轮只在垂直于齿轮轴线的平面(端平面)内具有渐开线齿形。
所以有关齿形的尺寸应在端平面内进行计算。
βcos n t m m =4、斜齿圆柱齿轮用于平行轴传动时的正确啮合条件 (1)两齿轮法向模数相等。
齿轮各部分名称及标准齿轮的基本尺寸

最常用
齿轮加 工方法
铣削 拉削 插齿 滚齿 范成法 (展成法共 剃齿 轭法 磨齿
包络法)
一、成形法铣削
盘铣刀
指状铣刀
14
ω
分度 进给
铣刀旋转,工件进给 分度、断续切削。
切削
适用于加工大模数 m>20 的齿轮和人字 齿轮。 切削 进给
ω
盘铣刀加工 由db=mzcosα可知,渐 开线形状随齿数变化。 要想获得精确的齿廓, 加工一种齿数的齿轮, 就需要一把刀具。这在 工程上是不现实的。
γ
进给 t
为什么滚刀要倾斜一个角度呢?
V=ωr=ωmz/2
ω
v
19
t
t
γ
t
t
范成法加工的特点: 一种模数只需要一把刀具连续切削,生产效率 高,精度高,用于批量生产。
20
c*m h*amh*am c*m
4.用标准齿条型刀具加工标准齿轮 α=20° πm/2 πm/2 4.1标准齿条型刀具 GB1356-88规定了标准齿条 型刀具的基准齿形。
ha=h*am
s
e
21
§4-7 根切现象、最少齿数及变位齿轮 一、根切现象 图示现象称为轮齿的根切。
根切的后果: ①削弱轮齿的抗弯强度; ②使重合度ε下降。
以下分析产生根切的原因: 当B2落在N1点的下方: PB2<PN1 刀具在位置1开始切削齿间; 在位置2开始切削渐开线齿廓; 在位置3切削完全部齿廓;
让刀运动
ω0
ω
ω
i=ω0 /ω=z/z0
齿轮插刀加工
17
2. 齿条插刀 切削 v
范成
让刀
行星齿轮传动的配齿方法及常用齿数组合表

NGW型传动的配齿方法及齿数组合表
对于一般动力传动用行星传动,不要求十分精确的传动比,在已知要求的传动比的情况下,可按以下步骤选配齿数
①根据,按表行星轮数目与传动比范围中表选取行星轮数目C s,通常选C s=3~4
②根据齿轮强度及传动平稳性等要求确定太阳轮齿数z A
③根据下列条件试凑Y值:
(a) Y=z A——传动比条件;
(b) Y/C s=整数——装配条件;
(c) Y应为偶数——同心条件。
但当采用不等啮合角的角变位传动时,Y值也可以是奇数
④计算内齿圈及行星轮齿数z B和z C
z B=Y-z A
对非角变位传动
对角变位齿轮传动
式中,Δz C为行星轮齿数减少值,由角变位要求确定,可为整数,也可以为非整数,Δz C=0.5~2 下表为NGW型行星齿轮传动的常用传动比,常用行星轮数对应的齿轮齿数组合表
NGW型行星齿轮传动的齿数组合
i=2.8
i=3.15
i=3.55
i=4.0
注:1.表中齿数满足装配条件、同心条件(带“”者除外)和邻接条件,且无公因数(带“*”者除外),以提高传动平稳性。
2.本表除带“”者外,可直接用于非变位、高变位和等角变位传动(α'tAC=α'tCB)。
表中各齿数组合当采用不等角角变位(α'tAC>α'tCB)时,应将表中z C 值适当减少1~2齿,以适应变位需要。
3.带“”者必须进行不等角角变位,以满足同心条件。
4.当齿数少于17且不允许根切时,应进行变位。
5.表中i为名义传动比,其所对应的不同齿数组合应根据齿轮强度条件选择;为实际传动比。
齿轮精度等级定义与比较
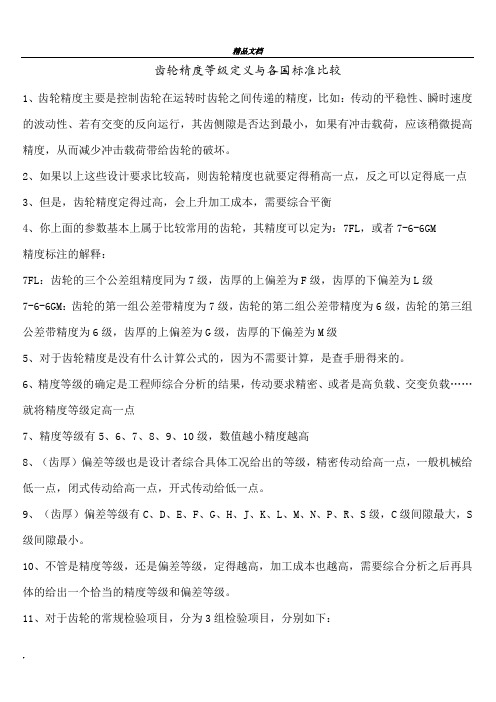
齿轮精度等级定义与各国标准比较1、齿轮精度主要是控制齿轮在运转时齿轮之间传递的精度,比如:传动的平稳性、瞬时速度的波动性、若有交变的反向运行,其齿侧隙是否达到最小,如果有冲击载荷,应该稍微提高精度,从而减少冲击载荷带给齿轮的破坏。
2、如果以上这些设计要求比较高,则齿轮精度也就要定得稍高一点,反之可以定得底一点3、但是,齿轮精度定得过高,会上升加工成本,需要综合平衡4、你上面的参数基本上属于比较常用的齿轮,其精度可以定为:7FL,或者7-6-6GM精度标注的解释:7FL:齿轮的三个公差组精度同为7级,齿厚的上偏差为F级,齿厚的下偏差为L级7-6-6GM:齿轮的第一组公差带精度为7级,齿轮的第二组公差带精度为6级,齿轮的第三组公差带精度为6级,齿厚的上偏差为G级,齿厚的下偏差为M级5、对于齿轮精度是没有什么计算公式的,因为不需要计算,是查手册得来的。
6、精度等级的确定是工程师综合分析的结果,传动要求精密、或者是高负载、交变负载……就将精度等级定高一点7、精度等级有5、6、7、8、9、10级,数值越小精度越高8、(齿厚)偏差等级也是设计者综合具体工况给出的等级,精密传动给高一点,一般机械给低一点,闭式传动给高一点,开式传动给低一点。
9、(齿厚)偏差等级有C、D、E、F、G、H、J、K、L、M、N、P、R、S级,C级间隙最大,S 级间隙最小。
10、不管是精度等级,还是偏差等级,定得越高,加工成本也越高,需要综合分析之后再具体的给出一个恰当的精度等级和偏差等级。
11、对于齿轮的常规检验项目,分为3组检验项目,分别如下:12、第一组检验项目主要是保证传递运动的准确性,其项目包括:切向综合公差Fi'、周节累积公差Fp、k个周节累积公差Fpk、径向综合公差Fi"、齿圈径向跳动公差Fr、公法线长度变动公差Fw13、第二组检验项目主要是保证传递运动的平稳性、噪声、振动,其项目包括:切向一齿综合公差fi'、基节极限偏差fpb、周节极限偏差fpt、径向一齿综合公差fi"14、第三组检验项目主要是保证载荷分布的均匀性,其项目包括:齿向公差Fβ、接触线公差Fb、轴向齿距极限偏差Fpx15、齿轮的齿坯公差的精度等级为:5、6、7、8、9、10级16、齿轮中间的孔公差、及其形位公差:IT5、IT6、IT7、IT8级17、齿轮轴的尺寸公差、及其形位公差:IT5、IT6、IT718、顶圆直径公差:IT7、IT8、IT919、基准面的径向跳动、基准面的端面跳动:根据直径的大小,按照5、6、7、8、9、10级查表20、需要说明一下:我给出的·第一组、第二组、第三组检验项目是比较全的,但是,在实际中,在实际的图纸上,我们列出的检验项目没有这么多,太多了不但给检验带来麻烦,还增加制造成本,所以,在图纸上只检验其中的几项即可,你可以参看一下专业的齿轮图纸,也可以在《机械设计手册》上看看例题,在此给你列出常规要检查的、在图纸上要列出来的项目:21、小齿轮的检验项目:21、根据你上面给出的参数,小齿轮的精度等级可以定为7FL,接下来级,就是按照精度等级差手册:22、周节积累公差Fp:0.06323、周节极限偏差fpt:0.01824、在图纸上标注的齿坯公差:内孔按照IT7级:在手册上按照孔径大小查《标准公差表》25、顶圆的径向跳动:按照外径尺寸大小查《标准公差表》26、大齿轮的检验项目:27、周节积累公差Fp:0.09028、周节极限偏差fpt:0.02029、在图纸上标注的齿坯公差:内孔按照IT7级:在手册上按照孔径大小查《标准公差表》30、顶圆的径向跳动:按照外径尺寸大小查《标准公差表》本网络手册中的圆柱齿轮精度摘自(GB10095—88),现将有关规定和定义简要说明如下:(1) 精度等级齿轮及齿轮副规定了12个精度等级,第1级的精度最高,第12级的精度最低。
齿轮主要术语图解及英文翻译

•齿轮的主要术语轮齿(齿)——齿轮上的每一个用于啮合的凸起部分。
一般说来,这些凸起部分呈辐射状排列。
配对齿轮上轮齿互相接触,导致齿轮的持续啮合运转。
齿槽——齿轮上两相邻轮齿之间的空间。
端面——在圆柱齿轮或圆柱蜗杆上垂直于齿轮或蜗杆轴线的平面。
法面——在齿轮上,法面指的是垂直于轮齿齿线的平面。
齿顶圆——齿顶端所在的圆。
齿根圆——槽底所在的圆。
基圆——形成渐开线的发生线在其上作纯滚动的圆。
分度圆——在端面内计算齿轮几何尺寸的基准圆,对于直齿轮,在分度圆上模数和压力角均为标准值。
齿面——轮齿上位于齿顶圆柱面和齿根圆柱面之间的侧表面。
齿廓——齿面被一指定曲面(对圆柱齿轮是平面)所截的截线。
齿线——齿面与分度圆柱面的交线。
端面齿距——相邻两同侧端面齿廓之间的分度圆弧长。
模数m——齿距除以圆周率π所得到的商,以毫米计。
径节p——模数的倒数,以英寸计。
齿厚s ——在端面上一个轮齿两侧齿廓之间的分度圆弧长。
槽宽e——在端面上一个齿槽的两侧齿廓之间的分度圆弧长。
齿顶高hɑ──齿顶圆与分度圆之间的径向距离。
齿根高hf──分度圆与齿根圆之间的径向距离。
全齿高h──齿顶圆与齿根圆之间的径向距离。
齿宽b──轮齿沿轴向的尺寸。
端面压力角ɑt──过端面齿廓与分度圆的交点的径向线与过该点的齿廓切线所夹的锐角。
基准齿条(Standard Rack) ——只基圆之尺寸,齿形,全齿高,齿冠高及齿厚等尺寸均合乎标准正齿轮规格之齿条,依其标准齿轮规格所切削出来之齿条称为基准齿条.基准节圆(Standard Pitch Circle) ——用来决定齿轮各部尺寸基准圆.为齿数x模数基准节线(Standard Pitch Line) ——齿条上一条特定节线或沿此线测定之齿厚,为节距二分之一.作用节圆(Action Pitch Circle) ——一对正齿轮咬合作用时,各有一相切做滚动圆.基准节距(Standard Pitch) ——以选定标准节距做基准者,与基准齿条节距相等.节圆(Pitch Circle) ——两齿轮连心线上咬合接触点各齿轮上留下轨迹称为节圆.节径(Pitch Diameter) ——节圆直径.有效齿高(Working Depth) ——一对正齿轮齿冠高和.又称工作齿高.齿冠高(Addendum) ——齿顶圆与节圆半径差.齿隙(Backlash) ——两齿咬合时,齿面与齿面间隙.齿顶隙(Clearance) ——两齿咬合时,一齿轮齿顶圆与另一齿轮底间空隙.节点(Pitch Point) ——一对齿轮咬合与节圆相切点.节距(Pitch) ——相邻两齿间相对应点弧线距离.法向节距(Normal Pitch) ——渐开线齿轮沿特定断面同一垂线所测节距.A.1. abrasive tooth wear 齿面研磨磨损2. absolute tangential velocity 绝对切向速度3. accelerometer 加速表4. addendum 齿顶高5. addendum angle 齿顶角6. addendum circle 齿顶圆7. addendum surface 上齿面8. adhesive wear 粘着磨损9. adjustability 可调性10. adjustability coefficients 可调系数11. adjusting wedge 圆盘端铣刀的可调型楔块12. allowable stress 允许应力13. alternate blade cutter 双面刀盘14. angular backlash 角侧隙15. angular bevel gears 斜交锥齿轮16. angular displacement 角移位17. angular pitch 齿端距18. angular testing machine 可调角度试验机19. approach action 啮入20. arbor 心轴21. arbor distance 心轴距22. arc of approach 啮入弧23. arc of recess 啮出弧24. attraction 收紧25. average cutter diameter 平均刀尖直径26. axial displacement 轴向位移27. axial factor 轴向系数28. axial locating surface 轴向定位面29. axial pitch 轴向齿距30. axial plane 轴向平面31. axial rakeangle 轴向前角32. axial thrust 轴向推力33. axle testing machine 传动桥试验机B.1.back angle 背锥角2.Back angle distance 背角距(在背锥母线方向)3.Back cone 背锥4.Back cone distance 背锥距5.Back cone element 背锥母线6.Backlash 侧隙7.Backlash tolerance 侧隙公差8.Backlash variation 侧隙变量9.Backlash variation tolerance 侧隙变量公差10.Bandwidth 频带宽11.Base circle 基圆12.Base diameter 基圆直径13.Base pitch 基节14.Base radius 基圆半径15.Base spiral angle 基圆螺旋角16.Basic rack 基本齿条17.Bearing 轴承18.Bearing preload 轴承预负荷19.Bearing spacing/spread 轴承间距20.Bending fatigue 弯曲疲劳21.Bending stress 弯曲应力22.Bevel gears 锥齿轮23.Bias 对角接触24.Bias in 内对角接触25.Bias out 外对角接触26.Blade angle 刀齿齿廓角27.Blade edge radius 刀尖圆角半径28.Blade letter 刀尖凸角代号29.Blade life 刀尖寿命30.Blade point width 刀顶宽31.Blank offset 毛坯偏置距32.Bland position 毛坯位置33.Bottom land 齿槽底面34.Boundary lubrication 界面润滑35.Breakage 破裂36.Bridged contact pattern 桥型接触斑点37.Broach 拉刀38.Burnishing 挤齿C.1. Case crushing 齿面塌陷2. CBN 立方氮化硼3. chamfer 倒角4. chordal addendum 弦齿高5. chordal thickness 弦齿厚6. chuck 卡盘7. circular broach 圆拉刀8. circular face-mill 圆盘端面铣刀9. circular peripheral-mill 圆盘铣刀10. circular pitch 周节11. circular thickness 弧齿厚12. circular thickness factor 弧齿厚系数13. clearance 顶隙14. clearance angle 后角15. coarse pitch 大节距16. coast side 不工作齿侧17. combination 组合18. combined preload 综合预负荷19. complementary crown gears 互补冠状齿轮20. completing cycle 全工序循环21. composite action 双面啮合综合检验误差22. compressive stress 压应力23. concave side 凹面24. concentricity 同心度25. concentricity tester 同心度检查仪26. cone distance 锥距27. cone element 锥面母线28. conformal surfaces 共型表面29. coniskoid 斜锥齿轮30. conjugate gears 共轭齿轮31. conjugate racks 共轭齿条32. contact fatigue 接触疲劳33. contact norma 接触点法线34. contact pattern (tooth contact pattern) 轮齿接触斑点35. contact ratio 重合度36. contact stress 接触应力37. continuous index 连续分度38. control gear 标准齿轮,检验用齿轮39. convex side 凸面40. coolant 冷却液41. corrosive wear 腐蚀性磨损42. corrugated tool 阶梯刨刀43. counter forma surfaces 反法向表面44. cradle 摇台45. cradle test roll 摇台角46. cross 大小端接触47. crossing point 交错点48. crown 齿冠49. crown circle 锥齿轮冠圆50. crowned teeth 鼓形齿51. crown gear 冠轮52. crown to back (轮冠距)轮冠至安装定位面距离53. crown to crossing point 轮冠至相错点距离54. cutter 刀盘55. cutter axial 刀盘的轴向位置56. cutter axial plane 刀盘轴向平面57. cutter axis 刀盘轴线58. cutter diameter 刀盘直径59. cutter edge radius 刀刃圆角半径60. cutter head 刀盘体61. cutter number 刀号62. cutter parallel 刀盘平垫片63. cutter point diameter 刀尖直径64. cutter point radius 刀尖半径65. cutter point width 刀顶距66. cutter spindle 刀盘主轴67. cutter spindle rotation angle 刀盘主轴转角68. cutting distance 切齿安装距69. C.V. testing mashing 常速试验机70. cyclex 格里森粗铣精拉法圆盘端铣刀71. cylindrical gears 圆柱齿轮D.1.Datum tooth 基准齿2.Debur 去毛刺3.Decibel (CB) (噪音)分贝4.Decimal ratio 挂轮比值5.Dedendum 齿根高6.Dendendum angle 齿根角7.Dedendum surface 下齿面8.Deflection 挠曲9.Deflection test 挠曲试验10.Deflection testing machine 挠曲试验机11.Depthwise taper 齿高收缩12.Design data sheet 设计数据表13.Destructive pitting 破坏性点蚀14.Destructive wear 破坏性磨损15.Developed setting 试切调整16.Dial indicator 度盘式指示表17.Diametral pitch 径节18.Diamond 菱形接触19.Dinging ball check 钢球敲击检查20.Disc-mill cuter 盘铣刀21.Dish angle 凹角22.Displacement 位移23.Displacement error 位移误差24.Double index 双分度25.Double roll 双向滚动26.Down roll 向下滚动27.Drive side 工作齿侧28.Duplete 双刃刀29.Duplex 双重双面法30.Duplex helical 双重螺旋法(加工方法之一)31.Duplex spread blade 双重双面刀齿(加工/磨齿方法)32.Duplex taper 双重收缩齿33.Durability factor 耐久系数34.Dynamic factor 动载荷系数E1.Ease-off 修正、失配2.Eccentric 偏心3.Eccentric angle 偏心角4.Eccentricity 偏心度5.Edge radius 刀尖圆角半径6.Effective bearing spacing 轴承有效间距7.Effective face width 有效宽度(有效齿宽)8.Elastic coefficient 弹性系数9.Elastic deformation 弹性变形10.Elastic limit 弹性极限11.Elastohydrodynamic lubrication 弹性液压润滑12.Element 母线、要素13.End movement 轴向移动14.Endrem 修内端凸轮、导程凸轮15.Endurance life 耐久寿命16.Endurance limit 耐久极限17.Engine torque 发动机扭矩18.Enveloping 包络19.EP lubricant, EP 极压润滑剂20.EPG check, “EPG”检查21.Equal addendum teeth 等齿顶高齿22.Equicurv 等高齿大轮成形法23.Equidep 等高齿24.Equiside 等边25.Equivalent fear ratio 当量传动比26.Equivalent number of teeth 当量齿数27.Equivalent pitch radius 当量节圆半径28.Equivalent rack 当量齿条29.Expander 涨胎30.Expanding arbor 可张心轴31.Extreme pressure lubricant 极压润滑剂F.1.Face acvance 斜齿轮扭曲量2.Face angle 顶锥角(面锥角)3.Face angle distance 顶锥角距4.Face apex 顶锥顶5.Face apex beyond crossing point 顶锥顶至相错点距离6.Face cone 顶锥7.Face cone element 齿顶圆锥母线,面锥母线8.Face contact ratio 齿长重合度,轴向重合度(圆柱齿轮)9.Face line 齿面与轴面交线10.Face width 齿宽11.Factor of safety 安全系数12.Fatigue breakage 疲劳破裂13.Fatigue failure 疲劳失效14.Fatigue test 疲劳测试15.Feed cam 进给凸轮16.Feed gears 进给齿轮17.Fillet 齿根圆角18.Fillet curve 齿根过渡曲线19.Fillet radius 齿根圆角半径20.Film strength 液膜强度21.Filter (electronic) (电子的)滤波器22.Filter (mechanical) (机械的)滤波器23.Fine pitch (小模数)细径节24.Finisher 精切机床25.Fishtail 鱼尾形26.Fixed setting 固定安装法27.Flank 下齿面28.Flanking 下齿面加工29.Formarc 加工齿轮用的曲线齿廓刀具30.Formate 成形法31.Former 齿廓样板,靠模32.Forming 成型,在磨具内挤压成型33.Form tool 成形刀34.Fourier analysis 傅里叶分析35.Frequency 频率36.Friction load 摩擦负荷37.Front angle 前角38.Front cone 前锥39.Front crown 前锥齿冠40.Front crown to crossing point 前锥齿冠至交错点41.Full-depth teeth 全齿高齿42.Fundametal 基频G.1.Gable 山形齿沟底面2.Gear 齿轮3.Gear axial displacement 齿轮轴向位移4.Gear axial plane 齿轮轴向平面5.Gear axis 齿轮轴线6.Gear center 齿轮中心7.Gear combination 齿轮组合8.Gear cone 大轮锥距9.Geared index 齿轮系分度10.Gear finisher 成形法齿轮精切机床11.Gear manufacturing summary 齿轮加工调整卡12.Gear marking compound 检查齿轮啮合涂色剂13.Gear member 大轮14.Gear planer 成型刨齿机15.Gear ratio 齿数比16.Gear rougher 齿轮粗切机床17.Gears 齿轮组18.Gear tipping 齿轮倾斜@U UlsC|3. 19.Generated gear 展成法齿轮20.Generating cam 展成凸轮21.Generating gear 展成齿轮22.Generating pressure angle 产形轮压力角23.Generating train 展成传动键24.Generation 展成25.Generator 展成齿轮加工机床26.Geneva index 星形轮分度,槽轮分度27.Geometry factor-durability 齿面接触强度几何系数28.Geometry factor0-strength 强度几何系数29.G-flow 格里森制金属件的商标,采用冷挤压成形法30.G-form 采用热锻成形法制造31.GLE-sine 砂轮内外压力角正弦波进行修整用机构32.G-plete 全工序法33.Gradeability 托曳力34.Grinding cracks 磨削裂纹35.G-spin 精密主轴的机床36.G-trac 圆柱齿轮的无端链式机床的商标H.1.Hand of cutter 刀盘方向2.Hand of spiral 螺旋方向3.Hand-rolling tester 手动滚动试验机4.Hardac 镶篇淬硬刀体精切刀盘5.Hard finishing 硬齿面精加工6.Hardness ratio factor 硬度比系数7.Harmonic 谐振8.Harmonic search 谐振追踪9.Harmonic sweep 谐振扫描10.Heel 轮齿大端11.Heel pattern 大端接触12.Helical duplex 双重螺旋法13.Helical motion 螺旋运动14.Helixact 螺旋运动法15.Helixform 螺旋成形法16.Hertz (Hz) 赫兹17.Hook angle 断面前角18.Horizontal displacement 水平位移19.Horizontal offset 水平偏置20.HRH 高减速比准双曲面齿轮(大于10:1的减速比)21.Hunting tooth combination 大小齿轮齿数无公因数的齿轮副22.Hudrodynamic lubrication 液压润滑23.Hupermesh 超配合24.Hypoid gears 准双曲面齿轮25.Hypoid offset 准双曲面齿轮偏置距I.1.Imaginary generating gear 假想成形法2.Incremental index 逐齿分度3.Index gears 分度齿轮4.Index interval 分度跳跃齿齿数5.Index plate 分度盘6.Index tolerance 分度公差7.Index variation 分度变化量8.Indicator anchorage 指示表支撑座9.Inertia factor 惯量系数10.Initial pitting 初期点蚀11.Inner addendum 小端齿顶高12.Inner cone distance 小端锥距13.Inner dedendum 小端齿根高14.Inner slot width 小端槽宽15.Inner spiral angle 小端螺旋角16.Inserted blade cutter 镶片刀盘17.Inside blade 内切刀齿18.Inside point diameter 内切刀尖直径19.Instantaneous contact pattern 瞬时接触斑点20.Interference 干涉21.Interference point 干涉点22.Interlocking disc-mill cutters 交错齿盘形铣刀23.Intermittent index 间断分度24.Internal bevel gear 内锥齿轮25.Inverse gear ratio 反齿数比26.Involute 渐开线27.Involute gear 渐开线齿轮28.Involute interference point 渐开线干涉点29.Involute spiral angle 渐开线螺旋角30.Involute teeth 渐开线齿J.1.Jet lubrication 喷射润滑L.1.Lame 顶根接触2.Lapping 研磨3.Lead cam 导程凸轮4.Length of action 啮合长度5.Lengthwise bridge 纵向桥型接触6.Lengthwise mismatch 纵向失配7.Lengthwise sliding velocity 纵向滑动速度8.Life factor 寿命系数9.Lift 垂直位移10.Limit point width 极限刀顶距11.Limit pressure angle 极限压力角12.Linear displacement transducer 线性位移传感器13.Line of action 啮合线14.Line of centers 中心线15.Line of contact 接触线16.Load sharing ratio 负荷分配比17.Localized tooth contact 齿局部接触18.Locating surface 定位表面19.Long-and-short-addendum teeth 高变位齿轮20.Long-toe-short-heel 小端长,大端短接触21.Lubricant 润滑剂22.Lubrication 润滑23.Lubricity 润滑性M.1.Machine center 基床中心点2.Machine center to back 机床中心至工件安装基准面3.Machine plane 机床切削平面4.Machine root angle 毛坯安装角5.Marking compound 检查齿轮啮合型情况使用的涂色剂6.Master blade 标准刀齿7.Master gear 标准齿轮8.Mean addendum 中点齿顶高9.Mean cone distance 中点锥距10.Mean dedendum 中点齿根高11.Mean diametral pitch 中点径节12.Mean measuring addendum 中点测量齿顶高13.Mean measuring depth 中点测量齿高14.Mean measuring thickness 中点测量厚度15.Mean normal base pitch 中点法向基节16.Mean normal diameter pitch 中点法向径节17.Mean normal module 中点法向模数18.Mean point 中点,平均点19.Mean radius 中点半径20.Mean section 中点截面21.Mean slot width 中点齿槽宽22.Mean spiral angle 中点螺旋角23.Measuring addendum 测量齿顶高24.Measuring tooth thickness 测量齿厚25.Member 齿轮,元件26.Mesh point 啮合点27.Minimum slot width 最小槽宽28.Mismatch 失配29.Miter gears 等齿数整角锥齿轮副30.Mixed lubrication 混合润滑31.Modified contact ratio 修正总重合度32.Modified roll 滚修正比33.Module 模数34.Motion curves 运动曲线35.Motor torque 电机扭矩36.Mounting distance 安装距37.Mounting surface 安装面英语站N.1.Narrow-tow-wide-heel 小端窄大端宽接触2.No load 空载3.Nominal 名义4.Non-generated gear 非展成大轮5.Normal 法向,法线,法面6.Normal backlash 法向侧隙7.Normal backlash tolerance 法向侧隙公差8.Normal base pitch 法向基节9.Normal chordal addendum 法向弦齿高10.Normal chordal thickness 法向弦齿厚11.Normal circular pitch 法向周节12.Normal circular thickness 法向弧齿厚13.Normal contact ratio 法向重合度14.Normal diametral pitch 法向径节15.Normal direction 法线方向16.Normal (perpendicular) load 法向(垂直)负载17.Normal module 法向模数18.Normal plane 法向平面19.Normal pressure angle 法向压力角20.Normal section 法向截面21.Normal space-width taper 正常齿槽宽收缩22.Normal thickness taper 正常齿厚收缩23.Normal tilt 法向刀倾24.Normal wear 正常磨损25.No-roll roughing 无滚动粗切26.Number of teeth 齿数英语站O.1.Octoid teeth 锥齿轮的“8”字啮合2.Offset 偏置距3.Operating load 工作负荷4.Operating pressure angle 工作压力角5.Operating torque 工作扭矩6.Outer addendum 大端齿顶高7.Outer cone distance 外锥距8.Outer dedendum 大端齿根高9.Outer slot width 大端槽宽10.Outer spiral angle 大端螺旋角11.Outside blade 外切刃点12.Outside diameter 外径,大端直径14.Outside radius 齿顶圆半径15.Outside surface 外表面16.Overhung mounting 双支承安装17.Overload breakage 超负荷破裂18.Overload factor 超负荷系数英语站P.1.Path of action 啮合点轨迹2.Path of contact 接触迹3.Peak load 峰值负荷4.Peak torque 峰值扭矩5.Pedestal bearings 安装差速器壳的架座轴承6.Performance torque 性能扭矩7.Perim-mate 研磨锥齿轮和准双面齿轮用的全齿面研磨法8.Pinion 小轮9.Pinion axial displacement 小轮轴向位移10.Pinion cone 小轮锥距11.Pinion front bearing 小轮前端轴承12.Pinion head bearing 小轮后端前轴承13.Pinion rear bearing 小轮后端后轴承14.Pinion rougher 小轮粗切机15.Pinion offset 小轮偏置距16.Pitch 节距,齿距17.Pitch angle 节锥角18.Pitch apex 节锥顶19.Pitch apex beyond crossing point 节锥顶超出至相错点20.Pitch apex to back 节锥顶至安装端面21.Pitch apex to crown 节锥顶至轮冠22.Pitch circle 节圆23.Pitch cone 节锥24.Pitch curve 节面曲线25.Pitch diameter 节径26.Pitch element 节面母线27.Pitch line 节线28.Pitch-line chuck 节圆夹具u< ` da E29.Pitch-line runout 节线跳动30.Pitch plane 节面31.Pitch point 节点32.Pitch radius 节圆半径33.Pitch surfaces 节曲面34.Pitch tolerance 齿距公差35.Pitch trace 节线36.Pitch variation 齿距变化量37.Pitting 点蚀38.Plane of action 啮合平面39.Plane of rotation 旋转平面40.Planning generator 展成法刨齿机41.Plastic deformation 塑性变形42.Plastic flow 塑性流动43.Plate index 分度盘44.Point diameter 刀尖直径45.Point of contact 接触点46.Point radius 刀尖半径47.Point width 刀顶距48.Point width taper 刀顶距收缩49.Pressure lubrication 压力润滑50.Prime mover torque 原动机扭矩51.Profile angle 齿廓角52.Profile bridge 齿廓桥形接触53.Profile contact ratio 齿廓重合度54.Profile mismatch 齿廓啮合失配55.Profile radius of curvature 齿廓曲率半径56.Proof surface 检测基准面Q.1.Quality measurement system 质量检测系统2.Quenching cracks 淬火裂纹3.Quenching die 淬火压模4.Quenching press 淬火压床英语站R.1.Rack 齿条2.Radial 径向刀位3.Radial load 径向负荷4.Radial locating surface 径向定位表面5.Radial rake angle 径向前角6.Ratio control roughing 变滚比粗切7.Ratio gears 滚比挂轮8.Ratio of roll 滚比9.Ratio of roll gears 滚比挂轮10.Recess action 啮出11.Relative displacement 相对位移12.Relative movement 相对运动13.Relative radius of curvature 相对曲率半径14.Residual stress 残余应力15.Revacycle 直齿锥齿轮圆拉法用机床及刀具16.Revex 直齿锥齿轮粗拉法17.Ridg-AC 镶片圆盘端面粗铣刀18.Ridging 沟条变形19.Ring gear 大轮,环形齿轮20.Rippling 振纹21.Roll centering 滚动定心22.Roll queching 滚动式淬火压床23.Roll gears 摆角挂轮24.Rolling 滚轧25.Rolling velocity 滚动速度26.Root angle 根锥角27.Root angle tilt 齿根角倾斜28.Root apex 根锥顶29.Root apex beyond crossing point 根锥顶至相错点的距离30.Root apex to back 根锥顶至安装基准面距离31.Root circle 齿根圆32.Root cone 根锥33.Root diameter 根圆直径34.Root line 齿根线35.Root radius 根圆半径36.Root surface 齿根曲面37.Roughac 弧齿锥齿轮粗切刀38.Rougher 粗切机39.RSR 弧齿锥齿轮条形刀齿铣刀盘40.Runout 径向跳动41.Runout tolerance 径向跳动公差S.1.Scoring 胶合2.Scoring index 胶合指数3.Scuffing 胶合4.Sector 扇形齿/齿弧5.Segment 扇形齿/体6.Segmental-blade cutter 大轮精切刀7.Separation 分离间隙8.Separating factor 分离系数9.Separating force 分离力10.Set-in 补充切入,进刀11.Set-over 补充转角,调整转换12.Shaft angle 轴转角13.Shot peening 喷丸强化14.Sidebank 边频15.Side movement 侧向位移16.Side rake angle 侧前角17.Single cycle 单循环法18.Single roll 单滚动19.Single setting 单面调整法20.Single side 单面精切法21.Single-side taper 齿槽收缩22.Size factor 尺寸系数23.Skew bevel gears 斜直齿锥齿轮24.Skip index 跳齿分度25.Slide-roll ratio 单位滑滚比,比滑26.Sliding base 床鞍,滑座27.Sliding base setting 床鞍调整,滑座调整28.Sliding velocity 滑动速度29.Slip-chip 直齿锥齿轮一次成形刀30.Slip torque 滑移扭矩31.Slotting tool 切槽刀32.Slot width 槽宽33.Slot-width taper 槽宽收缩34.Small cutter development 小刀盘试切,能产生接近渐开线的刀具35.Solid cutter 整体刀盘36.Sound test 噪声试验37.Space-width taper 齿距收缩38.Spacing tolerance 齿距公差39.Spacing variation 齿距变动量40.Spalling 剥落41.Specific sliding 单位滑动比42.Speed gears 速度挂轮43.Spherical involute teeth 球面渐开线齿44.Spherica limacon teeth 球面钳线齿45.Spindle rotation angle 主轴旋转角46.Spiral angle 螺旋角47.Spiral bevel gears 弧齿锥齿轮48.Splash lubrication 飞溅润滑49.Split profile 齿型中断50.Spread blade 双面刀51.Spread blade 双面刀渐缩52.Standard depthwise taper 标准深锥度53.Standard taper 正常收缩54.Standard thickness 正常齿厚收缩55.Stock allowance 毛坯加工流量56.Straddle cutter 双列刀齿刀盘57.Straddle mounting 跨装58.Straight bevel gears 直齿锥齿轮59.Strength factor 强度系数英语站60.Stress concentration factor 应力集中系数61.Stub teeth 短齿62.Subsurface initiated fatigue breakage 金属表面斜层初始疲劳破裂63.Summary of machine settings 机床调整卡64.Sump lubrication 油槽润滑65.Sum velocity 总速度66.Surface asperities 表面粗糙度67.Surface condition factor 表面条件系数68.Surface deformation 表面变形69.Surface durability 表面耐久度70.Surface fatigue 表面疲劳71.Surface initiated fatigue breakage 表面初始疲劳破裂72.Surface of action 啮合面73.Surface of revolution 回转面74.Surface treatment 表面处理75.Swinging base 回转底座76.Swing pinion cone 摆动小轮节锥法77.Swivel 刀转78.Swivel angle 刀转角79.Symmetrical rack 对称齿条80.Symmetrical rack proportions 对称齿条比例T.1.Tangential load 切向负荷2.Tangent plane 切平面3.Tanline 小轮夹具4.Tanruf 双联粗切刀,8.5模数一下5.Tan-tru 用在加工1016-2540mm的锥齿刀具6.Taper roughing 具有刀顶距收缩的大小轮粗切过程7.Temperature factor 温度系数8.Testing machine 试验机9.Thickness taper 齿厚收缩10.Tilt 刀倾11.Tilt angle 刀倾角12.Tilted rootline taper 倾斜齿根收缩13.Tip radius 齿顶圆角半径14.Toe 轮齿小端15.Toe pattern 小端接触16.Tool 刀具17.Tool advance 刀具进刀18.Tool edge radius 刀刃圆角半径19.Tool point width 刀顶距20.Tooth angle 齿角21.Tooth bearing 齿支撑面,轮齿接触面22.Tooth contact analysis 轮齿接触分析23.Tooth contact pattern 轮齿接触斑点24.Tooth horizontal 齿水平面25.Tooth layout 轮齿剖面图26.Tooth-mesh frequency 齿啮合频率27.Tooth number 齿数28.Tooth profile 齿形,齿廓29.Tooth spacing testing 齿距检查仪30.Tooth spiral 齿螺旋线31.Tooth surface 轮齿表面32.Tooth taper 轮齿收缩33.Tooth-to-tooth composite tolerance 一齿度量中心距公差34.Tooth-to- Tooth composite variation 一齿度量中心距变量35.Tooth trace 齿线36.Tooth vertical 齿垂直面37.Top 齿顶38.Topland 齿顶面39.Topland width 齿顶面宽度40.Topping 修顶41.Top relief angle 顶刃后角42.Toprem 修根刀片43.Toprem angle 刀齿突角角度44.Top slope angle 刀齿顶刃倾角45.Total composite tolerance 总综合公差46.Total composite variation 总度量中心距变动量47.Total contact ratio 总重合度48.Total index tolerance 总分度公差49.Total index variation 总分度变动量50.Tractive effort torque 牵引力扭矩51.Transverse circular pitch 端面周节52.Transverse circular thickness 端面弧齿厚53.Transverse contact ratio 端面重合度54.Transverse diametral pitch 端面径节55.Transverse module 端面模数56.Transverse plane 端平面57.Transverse pressure angle 端面压力角58.Transverse space-width taper 端面槽宽收缩59.Transverse thickness taper 端面齿厚收缩60.Tredgold’s approximation 背锥近似法61.Tribology 润滑与磨损学62.Triplex 三面刃圆盘端铣刀63.Two-tool generator 双刀展成加工机床U.1.Undercut 根切2.Undeveloped settings 试切前调整3.Uniform roll 匀速滚动4.Uniform velocity tester 匀速试验机5.Uni-spand 大轮心轴6.Unit load 单位负荷7.Unitool 曲面镶片刀8.Up-roll 向上滚动V.1.V and H check 锥齿轮啮合的VH检查2.Variable roll 变滚动3.Velocity factor 速度系数4.Versacut 弧齿锥齿轮加工多用刀盘5.Vers-grip 卡紧小齿轮用的卡盘(商标名称)6.Vertical direction 垂直方向7.Vertical displacement 垂直位移8.Vertical factor 垂直系数9.Vertical force 垂直力10.Vertical offset 垂直偏置距11.Vertical plane 垂直面12.Virtual number of teeth 当量齿数13.Virtual pitch radius 当量节圆半径14.Viscosity 粘度15.V-tool V型刀具W.1.Waveform 波形2.Wear 磨损3.Webless-type gear 无幅板式齿轮4.Web-type gear 幅板式齿轮5.Wheel slip torque 车轮打滑扭矩6.Whole depth 齿全高7.Workhead 工件头座8.Workhead offset 垂直轮位9.Workholding equipment 工件夹具10.Working depth 工作齿高11.Working stress 工作允许应力12.Work tests roll 检验工件主轴转角X.1.X-pandisk 大轮蝶形,涨胎心轴Z.1.Zero depthwise taper 等齿高2.Zerol 零度锥齿轮。
齿轮各项公差表

一齿径向综合公差f i″值m m
齿坯尺寸和形状公差
注:① 当三个公差组的精度等级不同时,按最高的精度等级确定公差值。
② 若顶圆不作测量齿厚的基准,尺寸公差按1T11给定,但不大于。
标准公差数值μm
齿坯基准面径向跳动*和端面圆跳动公差m m
注:*当以顶圆作基准面时,本栏就指顶圆的径向跳动。
齿轮的表面粗糙度(R a)推荐值m m
注:本表不属GB10095-88,供参考。
非变位直齿圆柱齿轮分度圆上弦齿厚及弦齿高(a0=20°,h a*=1)
注:1. 用成形铣刀加工齿轮时,标注和测量分度圆弦齿厚和弦齿高;
用范成法加工时,可以标注或测量固定弦厚和弦齿高。
2. 对于斜齿圆柱齿轮和圆锥齿轮,使用本表时,应以当量齿数z d代替z(斜齿轮:z d=z/cos3b b;
锥齿轮:z d=z/cosd)。
z d非整数时,可用插值法求出。
3. 本表不属GB10095-88,供参考。
齿轮公差
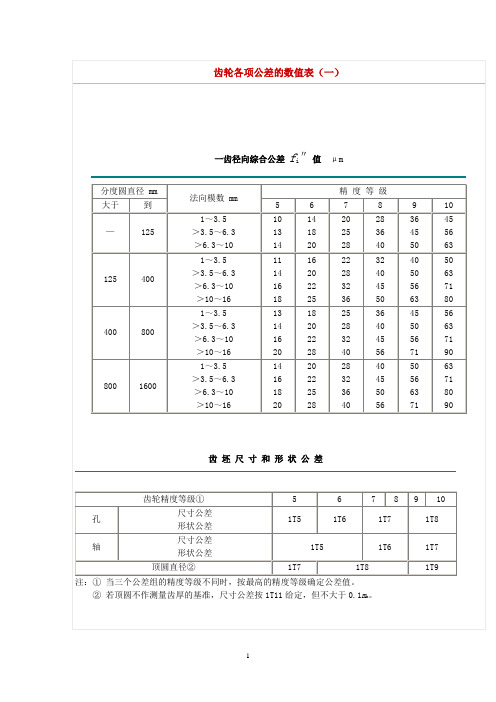
1.0134
1.0131
1.0128
1.0126
1.0123
1.0121
131
132
133
134
135
140
145
150
齿条
1.5708
1.0047
1.0047
1.0047
1.0046
1.0046
1.0044
1.0042
1.0041
1.0000
注:1.用成形铣刀加工齿轮时,标注和测量分度圆弦齿厚和弦齿高;
0.8
1.2
2
3
5
8
13
19
30
46
74
120
190
300
460
740
1200
1900
3000
4600
80~120
1
1.5
2.5
4
6
10
15
22
35
54
87
140
220
350
540
870
1400
2200
3500
5400
120~180
1.2
2
3.5
5
8
12
18
25
40
63
100
160
250
400
630
锥齿轮:zd=z/cosd)。zd非整数时,可用插值法求出。
3.本表不属GB10095-88,供参考。
齿轮各项公差的数值表(三)
中心距极限偏差(±fa)值μm
第Ⅱ公差组精度等级
5~6
7~8
9~10
齿轮副的中心距mm
标准齿轮齿数规格表
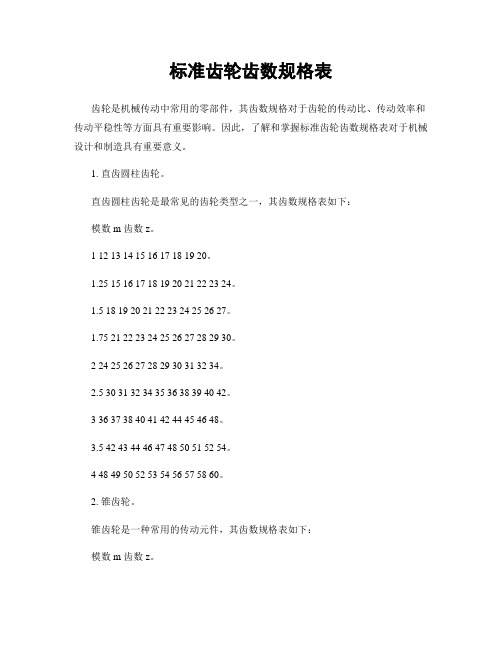
标准齿轮齿数规格表齿轮是机械传动中常用的零部件,其齿数规格对于齿轮的传动比、传动效率和传动平稳性等方面具有重要影响。
因此,了解和掌握标准齿轮齿数规格表对于机械设计和制造具有重要意义。
1. 直齿圆柱齿轮。
直齿圆柱齿轮是最常见的齿轮类型之一,其齿数规格表如下:模数 m 齿数 z。
1 12 13 14 15 16 17 18 19 20。
1.25 15 16 17 18 19 20 21 22 23 24。
1.5 18 19 20 21 22 23 24 25 26 27。
1.75 21 22 23 24 25 26 27 28 29 30。
2 24 25 26 27 28 29 30 31 32 34。
2.5 30 31 32 34 35 36 38 39 40 42。
3 36 37 38 40 41 42 44 45 46 48。
3.5 42 43 44 46 47 48 50 51 52 54。
4 48 49 50 52 53 54 56 57 58 60。
2. 锥齿轮。
锥齿轮是一种常用的传动元件,其齿数规格表如下:模数 m 齿数 z。
1.25 15 16 17 18 19 20 21 22 23 24。
1.5 18 19 20 21 22 23 24 25 26 27。
1.75 21 22 23 24 25 26 27 28 29 30。
2 24 25 26 27 28 29 30 31 32 34。
2.5 30 31 32 34 35 36 38 39 40 42。
3 36 37 38 40 41 42 44 45 46 48。
3.5 42 43 44 46 47 48 50 51 52 54。
4 48 49 50 52 53 54 56 57 58 60。
3. 细齿圆柱齿轮。
细齿圆柱齿轮常用于高速、高精度传动系统中,其齿数规格表如下:模数 m 齿数 z。
0.5 12 13 14 15 16 17 18 19 20。
齿轮基本参数

齿轮基本参数:1、齿数Z闭式齿轮传动一般转速较高,为了提高传动的平稳性,减小冲击振动,以齿数多一些为好,小一些为好,小齿轮的齿数可取为z1=20~40。
开式(半开式)齿轮传动,由于轮齿主要为磨损失效,为使齿轮不致过小,故小齿轮不亦选用过多的齿数,一般可取z1=17~20。
为使齿轮免于根切,对于α=20o的标准支持圆柱齿轮,应取z1≥17。
Z2=u·z1。
2、压力角α rb=rcosα=1/2mzcosα在两齿轮节圆相切点P处,两齿廓曲线的公法线(即齿廓的受力方向)与两节圆的公切线(即P点处的瞬时运动方向)所夹的锐角称为压力角,也称啮合角。
对单个齿轮即为齿形角。
标准齿轮的压力角一般为20‖。
在某些场合也有采用α=14.5°、15°、22.50°及25°等情况。
3、模数m=p/ π齿轮的分度圆是设计、计算齿轮各部分尺寸的基准,而齿轮分度圆的周长=πd =z p模数m是决定齿轮尺寸的一个基本参数。
齿数相同的齿轮模数大,则其尺寸也大。
4、齿顶高系数和顶隙系数—h*a 、C*两齿轮啮合时,总是一个齿轮的齿顶进入另一个齿轮的齿根,为了防止热膨胀顶死和具有储成润滑油的空间,要求齿根高大于齿顶高。
为次引入了齿顶高系数和顶隙系数。
正常齿:h*a =1;C*=0.25 短齿:h*a =0.8;C*=0.3一般的直齿圆柱齿轮,啮合的条件是:模数相等,压力角相等一、60°牙型的外螺纹中径计算及公差(国标GB 197/196)a. 中径基本尺寸计算:螺纹中径的基本尺寸=螺纹大径-螺距×系数值公式表示:d/D-P×0.6495例:外螺纹M8螺纹中径的计算8-1.25×0.6495=8-0.8119≈7.188b.常用的6h外螺纹中径公差(以螺距为基准)上限值为‖0‖下限值为P0.8-0.095 P1.00-0.112 P1.25-0.118P1.5-0.132 P1.75-0.150 P2.0-0.16P2.5-0.17上限计算公式即基本尺寸,下限值计算公式d2-hes-Td2即中径基本尺寸-偏差-公差M8的6h级中径公差值:上限值7.188 下限值:7.188-0.118=7.07C常用的6g级外螺纹中径基本偏差: (以螺距为基准)P 0.80-0.024 P 1.00-0.026 P1.25-0.028 P1.5-0.032P1.75-0.034 P2-0.038 P2.5-0.042上限值计算公式d2-ges即基本尺寸-偏差下限值计算公式d2-ges-Td2即基本尺寸-偏差-公差例M8的6g级中径公差值:上限值7.188-0.028=7.16下限值:7.188-0.028-0.118=7.042注:①以上的螺纹公差是以粗牙为准,对细牙的螺纹公差相应有些变化,但均只是公差变大,所以按此控制不会越出规范界限,故在上述中未一一标出.②螺纹的光杆坯径尺寸在生产实际中根据设计要求的精度和螺纹加工设备的挤压力的不同而相应比设计螺纹中径尺寸加大0.04—0.08之间,为螺纹光杆坯径值,例我们公司的M8外螺纹6g级的螺纹光杆坯径实在7.08—7.13即在此范围.③考虑到生产过程的需要外螺纹在实际生产的未进行热处理和表面处理的中径控制下限应尽量保持在6h级为准二、60°内螺纹中径计算及公差(GB 197 /196)a. 6H级螺纹中径公差(以螺距为基准)上限值:P0.8+0.125 P1.00+0.150 P1.25+0.16 P1.5+0.180P1.25+0.00 P2.0+0.212 P2.5+0.224下限值为‖0‖,上限值计算公式2+TD2即基本尺寸+公差例:M8-6H内螺纹中径为:7.188+0.160=7.348 上限值:7.188为下限值b. 内螺纹的中径基本尺寸计算公式与外螺纹相同即D2=D-P×0.6495即内螺纹中径螺纹大径-螺距×系数值c. 6G级螺纹中径基本偏差E1(以螺距为基准)P0.8+0.024 P1.00+0.026 P1.25+0.028 P1.5+0.032P1.75+0.034 P1.00+0.026 P2.5+0.042例:M8 6G级内螺纹中径上限值:7.188+0.026+0.16=7.374下限值:7.188+0.026=7.214上限值公式2+GE1+TD2即中径基本尺寸+偏差+公差下限值公式2+GE1即中径尺寸+偏差三、外螺纹大径的计算及公差(GB 197/196)a. 外螺纹的6h大径上限值即螺纹直径值例M8为φ8.00上限值公差为‖0‖b. 外螺纹的6h级大径下限值公差(以螺距为基准)P0.8-0.15 P1.00-0.18 P1.25-0.212 P1.5-0.236 P1.75-0.265P2.0-0.28 P2.5-0.335大径下限计算公式:d-Td 即螺纹大径基本尺寸-公差例:M8外螺纹6h大径尺寸:上限为φ8,下限为φ8-0.212=φ7.788c. 外螺纹6g级大径的计算与公差6g级外螺纹的基准偏差(以螺距为基准)P0.8-0.024 P1.00-0.026 P1.25-0.028 P1.5-0.032 P1.25-0.024 P1.75 –0.034 P2.0-0.038 P2.5-0.042上限计算公式d-ges 即螺纹大径基本尺寸-基准偏差下限计算公式d-ges-Td 即螺纹大径基本尺寸-基准偏差-公差例: M8 外螺纹6g级大径上限值φ8-0.028=φ7.972下限值φ8-0.028-0.212=φ7.76注:①螺纹的大径是由螺纹光杆坯径及搓丝板/滚丝轮的牙型磨损程度来决定的,而且其数值在同样毛坯及螺纹加工工具的基础上与螺纹中径成反比出现即中径小则大径大,反之中径大则大径小.②对需进行热处理和表面处理等加工的零件,考虑到加工过程的关系实际生产时应将螺纹大径控制在6h级的下限值加0.04mm以上,如M8的外螺纹在搓(滚)丝的大径应保证在φ7.83以上和7.95以下为宜.四、内螺纹小径的计算与公差a. 内螺纹小径的基本尺寸计算(D1)径基本尺寸=内螺纹基本尺寸-螺距×系数例:内螺纹M8的小径基本尺寸8-1.25×1.0825=6.646875≈6.647b. 内螺纹6H级的小径公差(以螺距为基准)及小径值计算P0.8 +0. 2 P1.0 +0. 236 P1.25 +0.265 P1.5 +0.3 P1.75 +0.335P2.0 +0.375 P2.5 +0.48内螺纹6H级的下限偏差公式D1+HE1即内螺纹小径基本尺寸+偏差注:6H级的下偏值为―0‖内螺纹6H级的上限值计算公式=D1+HE1+TD1即内螺纹小径基本尺寸+偏差+公差例:6H级M8内螺纹小径的上限值6.647+0=6.6476H级M8内螺纹小径的下限值6.647+0+0.265=6.912c. 内螺纹6G级的小径基本偏差(以螺距为基准)及小径值计算P0.8 +0.024 P1.0 +0.026 P1.25 +0.028 P1.5 +0.032 P1.75 +0.034P2.0 +0.038 P2.5 +0.042内螺纹6G级的小径下限值公式=D1+GE1即内螺纹基本尺寸+偏差例: 6G级M8内螺纹小径的下限值6.647+0.028=6.6756G级M8内螺纹小径的上限值公式D1+GE1+TD1即内螺纹基本尺寸+偏差+公差例: 6G级M8内螺纹小径的上限值是6.647+0.028+0.265=6.94注:①内螺纹的牙高直接关系到内螺纹的承载力矩的大小,故在毛坯生产中应尽量在其6H级上限值以内②在内螺纹的加工过程中,内螺纹小径越小会给加工具——丝锥的使用效益有所影响.从使用的角度讲是小径越小越好,但综合考虑时一般采用小径的在中限至上限值之间,如果是铸铁或铝件时应采用小径的下限值至中限值之间③内螺纹6G级的小径在毛坯生产中可按6H级执行,其精度等级主要考虑螺纹中径的镀层,故只在螺纹加工时考虑丝锥的中径尺寸而不必考虑光孔的小径。
标准齿轮齿数

标准齿轮齿数齿轮是一种常见的机械传动装置,它通过齿轮之间的啮合传递动力,被广泛应用于各种机械设备中。
而齿轮的齿数是其重要的参数之一,不同的齿数会直接影响到齿轮的传动比、速比等性能指标。
因此,了解标准齿轮齿数的相关知识对于正确选择和设计齿轮传动至关重要。
标准齿轮齿数是指在一定模数范围内,经过统一规定的齿轮齿数。
在实际应用中,标准齿轮齿数能够有效地减少齿轮的制造成本,提高齿轮的互换性和通用性。
常见的标准齿轮齿数有以下几种:1. 等距齿数,等距齿数是指齿轮齿数按照等差数列排列,常见的等距齿数有20、25、30等。
等距齿数的齿轮制造工艺简单,适用于一般的传动要求。
2. 法向齿数,法向齿数是指齿轮齿数按照等比数列排列,常见的法向齿数有12、24、48等。
法向齿数的齿轮传动效率高,适用于高速、大功率传动。
3. 组合齿数,组合齿数是指齿轮齿数由等距齿数和法向齿数组合而成,常见的组合齿数有21、27、35等。
组合齿数的齿轮传动具有较好的综合性能,适用于特殊传动要求。
标准齿轮齿数的选择应根据具体的传动要求和工况条件来确定。
在实际应用中,需要考虑齿轮传动的传动比、速比、工作环境、工作温度、载荷大小等因素,综合分析确定最合适的齿数类型和数值范围。
除了上述的常见标准齿轮齿数外,还有一些特殊的齿数类型,如非整数齿数、修形齿数等,它们通常用于特殊传动要求或特定机械设备中。
这些特殊齿数类型的应用需要更加严格的设计和制造要求,通常需要进行专门的计算和分析。
总之,标准齿轮齿数是齿轮传动设计和制造中的重要参数,正确选择合适的齿数类型和数值范围对于保证齿轮传动的性能和可靠性具有重要意义。
在实际应用中,需要充分考虑传动要求和工况条件,综合分析确定最佳的齿数方案,以确保齿轮传动的正常运行和长期稳定性。
KISSSOFT操作与齿轮设计培训教程
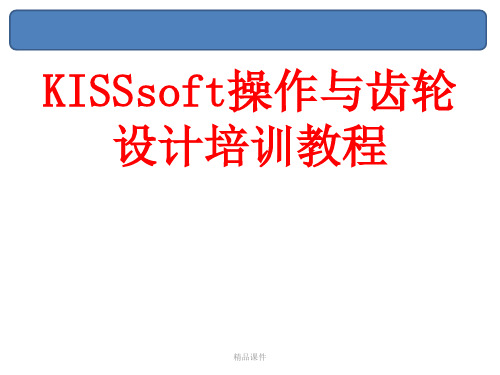
KISSsoft软件齿轮基本模块介绍
二、单对齿轮模块介绍
2.4 齿轮的修形参数(Modifications)
对于使用模具工艺加工齿形,齿顶必须倒圆角,因为尖角在注塑时是不可能很精确的 完成的。最好将齿轮1和齿轮2的这个参数同时在一个界面控制。这样可以确保所有重要的 参数(例如重合度等)计算时可以同时考虑齿顶倒圆角的影响。齿轮的齿顶、齿廓倒角、 倒圆,并无标准计算公式,一般依据各公司的经验。但不宜过大,从而影响齿轮重合度和 强度,一般齿轮倒角如下:
基本齿条型式的应用 1、A型标准基本齿条齿廓推荐用于传递大转矩的齿轮。 2、B型和C型基本齿条齿廓推荐用于通常的使用场合。用一些标准滚刀加工时,可以用C型。 3、D型基本齿条齿廓的齿根圆角为单圆弧齿根圆角。当保持最大齿根圆角半径时,增大的齿根高
=1.4m,齿根圆角半径=0.39m使得精加工刀具能在没有干涉的情况下工作。这种齿廓推荐用于高精度、 传递大转矩的齿轮,因此,齿廓精加工用磨齿或剃齿。在精加工时,要小心避免齿根圆角处产生凹痕 凹痕会导致应力集中。 几种类型基本齿条齿廓的几何参数见下表。
13比在固定传动比的情况下不同齿数搭出来的滑动比数值结果会不同调整齿数kisssoft软件齿轮基本模块介绍二单对齿轮模块介绍26滑动比优化总结修改变位系数可以优化滑动比合理增加齿顶修圆可以优化滑动比选择合适齿数配合可以优化滑动比在kisssoft软件几何设置过程中应用最为广泛的一个功能就是对啮合齿轮副滑动比的优化以上几点优化方法并不是任何情况都通用具体情况还的根据实际产品设计需求来调试kisssoft软件齿轮基本模块介绍二单对齿轮模块介绍27齿轮的重合度contactratio单对齿轮啮合重合度尽量大于1否则会有撞击影响噪音和强度
精品课件
齿轮参数附表

齿 轮
14
«a14
24.719°
16
重合度
Z
1.65
项目
代号
计算公式及计算结果
齿数
齿 轮
26
乙6
102
齿轮22
Z27
17
模数
m
2
压力角
a
200
齿顶咼系数
ha
1
顶隙系数
c*
0.25
标准中心距
a
119
实际中心距
1
a
119
啮合角
1
a
200
变位系数
齿 轮
26
X26
0
齿 轮
27
X27
0
齿顶咼
齿 轮
29
齿 轮
12
df 1:
!113
15
齿顶圆压力 角
齿 轮
11
%
32.778°
齿 轮
12
%
24.649°
16
重合度
1.65
定轴齿轮传动13与定轴齿轮14齿轮对
序 号
项目
代号
计算公式及计算结果
1
齿数
齿 轮
13
Z13
17
齿 轮
14
Z14
58
2
模数
m
数
ha
1
5
顶隙系数
c*
0.25
6
标准中心距
a
75
7
实际中心距
1
a
75
8
啮合角
1
Ct
200
9
变位系数
齿 轮
13
机械设计基础知识大全

机械设计基础知识大全引导语:有关机械设计的基础知识哪里有哪?接下来是小编为你带来收集整理的文章,欢迎阅读!1机械零件常用材料:普通碳素结构钢(Q屈服强度)优质碳素结构钢(20平均碳的质量分数为万分之20)、合金结构钢(20Mn2锰的平均质量分数约为2%)、铸钢(ZG230-450屈服点不小于230,抗拉强度不小于450)、铸铁(HT200灰铸铁抗拉强度).2常用的热处理方法:退火(随炉缓冷)、正火(在空气中冷却)、淬火(在水或油中迅速冷却)、回火(吧淬火后的零件再次加热到低于临界温度的一定温度,保温一段时间后在空气中冷却)、调质(淬火+高温回火的过程)、化学热处理(渗碳、渗氮、碳氮共渗).3机械零件的结构工艺性:便于零件毛坯的制造、便于零件的机械加工、便于零件的装卸和可靠定位 .4机械零件常见的失效形式:因强度不足而断裂;过大的弹性变形或塑性变形;摩擦表面的过度磨损、打滑或过热;连接松动;容器、管道等的泄露;运动精度达不到设计要求 .5应力的分类:分为静应力和变应力。
最基本的变应力为稳定循环变应力,稳定循环变应力有非对称循环变应力、脉动循环变应力和对称循环变应力三种.6疲劳破坏及其特点:变应力作用下的破坏称为疲劳破坏。
特点:在某类变应力多次作用后突然断裂;断裂时变应力的最大应力远小于材料的屈服极限;即使是塑性材料,断裂时也无明显的塑性变形。
确定疲劳极限时,应考虑应力的大小、循环次数和循环特征.7接触疲劳破坏的特点:零件在接触应力的反复作用下,首先在表面或表层产生初始疲劳裂纹,然后再滚动接触过程中,由于润滑油被基金裂纹内而造成高压,使裂纹扩展,最后使表层金属呈小片状剥落下来,在零件表面形成一个个小坑,即疲劳点蚀。
疲劳点蚀危害:减小了接触面积,损坏了零件的光滑表面,使其承载能力降低,并引起振动和噪声。
疲劳点蚀使齿轮。
滚动轴承等零件的主要失效形式.8引入虚约束的原因:为了改善构件的受力情况(多个行星轮)、增强机构的刚度(轴与轴承)、保证机械运转性能.9螺纹的种类:普通螺纹、管螺纹、矩形螺纹、梯形螺纹、锯齿形螺纹.10自锁条件:λ≤ψ即螺旋升角小于等于当量摩擦角.11螺旋机构传动与连接:普通螺纹由于牙斜角β大,自锁性好,故常用于连接;矩形螺纹梯形螺纹锯齿形螺纹因β小,传动效率高,故常用于传动.12螺旋副的效率:η=有效功/输入功=tanλ/tan(λ+ψv)一般螺旋升角不宜大于40°。
- 1、下载文档前请自行甄别文档内容的完整性,平台不提供额外的编辑、内容补充、找答案等附加服务。
- 2、"仅部分预览"的文档,不可在线预览部分如存在完整性等问题,可反馈申请退款(可完整预览的文档不适用该条件!)。
- 3、如文档侵犯您的权益,请联系客服反馈,我们会尽快为您处理(人工客服工作时间:9:00-18:30)。
第27章齿轮传动27.1 概述齿轮机构是各种机器中应用最广泛的一种传动机构.功率——几万千瓦,圆周速度——300 m /s ,直径范围——1毫米~ 20米。
传动精度高,效率高(99%),寿命长。
★常用齿廓曲线:渐开线、摆线、圆弧。
★齿轮的分类:按齿向分—直齿、斜齿、人字齿、螺旋齿。
按轴向位置分—平行、相交、交错。
按工作条件分—闭式传动,开式传动。
按齿面硬度分—软齿面(HB≤350)硬齿面(HB>350)齿轮传动的设计:一.齿轮的运动应准确、平稳.(几何学)二.在一定的工作条件下,齿轮应具有一定的工作寿命及可靠性。
27.2渐开线齿轮传动参数直齿圆柱齿轮正确啮合条件:m1 = m2 = m α 1 = α 2 = α齿轮连续传动条件:重合度ε>11、传动比、齿数比传动比:齿数比: u=Z 2/Z 12、齿轮传动的精度国标规定了12个精度等级,1级最高。
1. 运动精度—— 一周内运转速度不均匀.2. 平稳性精度—— 一齿内运转速度不均匀.3. 接触精度—— 一对轮齿齿面沿轴线方向的接触情况.4. 齿侧间隙—— 轮齿非工作表面所具有的间隙.D ——零间隙; D b ——较小间隙;D c ——标准间隙; D e ——较大间隙;齿轮精度标注:7-7-8- Dc3、模数、中心距、变位齿轮传动(1)模数m :表征齿厚的参数,齿轮抗弯能力的标志。
设:在e = s 处做一圆,其直径为d ,有:d ×π= P ×Z ; d =(P /π)Z令:m = P /π(2)中心距a标准中心距两齿轮分度圆相切时的中心距:a = r 1 + r 2 = 0.5 m (Z 1 + Z 2)齿轮按标准中心距安装时: r ’ = r α’=α(3)变位齿轮传动1)高度变位齿轮传动(等变位传动)两齿轮的变位系数的绝对值相等,但一个为正变位,另一个为负变位。
ΣX=X 1+X 2=01b 2b 1221r r r r i =''==ωω两轮的分度圆相切,分度圆与节圆重合,中心距仍为标准中心距。
只是齿顶高和齿根高发生了变化。
2)角度变位齿轮传动两齿轮的变位系数之和不为零,ΣX=X1+X2≠0ΣX>0 :正传动;ΣX<0 :负传动。
在角度变位齿轮传动中,两轮的分度圆不再相切,分度圆与节圆不重合,中心距不等于标准中心距。
27.3渐开线齿轮传动几何计算1、外啮合圆柱齿轮传动几何计算齿轮基本尺寸计算d = m Z ; m = P /π; α = 20°;h a* =1; c* = 0.25h a = h a* m = m d a =d + 2 h a = (Z + 2) mh f =(h a* + c*)m =1. 25 m d f =d - 2 h f = (Z – 2.5 ) mh = h a + h f = 2. 25 m d b= d cos α = m Z cos αs = e = P / 2 =πm / 2 a = 0.5 (d1 + d2) = 0.5 m (Z1 + Z2 )2、锥齿轮传动(1)锥齿轮传动的特点两相交轴之间的传动。
(2)直齿圆锥齿轮传动的参数圆锥齿轮传动相当一对节圆锥作纯滚动。
其齿分布在圆锥体上,因此圆柱齿轮的有关参数都变为圆锥。
齿廓的形成:一个半径为R 的圆平面在锥距为R 基圆锥上做纯滚动,平面边缘上任一点在空间展开一条渐开线,且该线落在以R 为半径的球面上,因此是一条球面渐开线。
圆锥齿轮几何尺寸:δ— 分度圆锥角; ∑— 齿轮轴线夹角;∑=δ1 +δ212121221sin sin r r Z Z i δδωω====以大端的m 、α为标准值,齿轮各参数按大端尺寸计算.圆锥齿轮正确啮合条件:两齿轮大端模数、压力角相等。
(3)当量齿轮球面无法展平,给齿轮的设计和制造带来困难。
用与球体相切的圆锥面近似代替球面,此圆锥即称为背锥。
因此将背锥上的齿廓曲线作为圆锥齿轮大端的实际齿廓曲线。
将背锥展成平面,圆锥齿轮即成为平面扇形齿轮,将其补足为一个完整的圆柱齿轮,称为当量齿轮。
此当量齿轮的齿数称为该圆锥齿轮的当量齿数。
圆锥齿轮的当量齿数:圆锥齿轮不发生根切的最少齿数: Z m i n = Z V cos δ=17 cos δ< 1727.4齿轮传动的失效分析1.轮齿折断单向传动按脉动循环处理,δδcos Z cos 2m mZ 2m r 2m d Z v v V ====双向传动按对称循环处理.过载折断:ζ>ζB疲劳折断:ζ>[ζ-1]2.齿面失效(1)点蚀:在接触应力作用下,齿面产生裂纹和凹坑。
齿面硬度越高,抗点蚀能力越强.(2)齿面胶合高速传动中,局部高温使金属熔化.(3)齿面磨损破坏齿形,严重时使齿厚减薄.(4)齿面塑性变形:低速重载时,金属表面产生滑移.3、设计计算准则1.闭式传动:齿轮在齿轮箱内工作,且润滑密封情况良好。
软齿面——失效形式为点蚀,用式(2)计算主要参数,用式(3)进行弯曲应力校核。
硬齿面——不易产生点蚀,失效形式主要为断齿,用式(4)计算主要参数,用式(1)进行接触应力校核。
2. 开式传动:齿轮外露,无防尘润滑设施或润滑情况不好。
硬、软齿面失效形式均为摩损,导致断齿。
为将m适当放大用式(4)计算时取[ζF ]= 0.7 ζF l i m/ S F (P169)因开式传动基本来不及产生点蚀,故可不做接触应力验算。
要求有精确瞬时传动比的传动,必须采用闭式传动。
27.5齿轮常用材料和热处理1、常用材料对齿轮材料的要求: 齿面有足够的硬度,心部有足够的强度和韧性.按齿面硬度分为:1. 软齿面——HBS ≤350 正火、调质.2. 硬齿面——HBS >350 渗碳淬火、表面淬火。
3. HBS 1 = HBS 2+(20~50)小齿轮硬度高于大齿轮。
布氏硬度HBS ——用淬火钢球压入被测材料测量压痕面积。
用于软材料. (HBS <400)洛氏硬度HRC ——用圆锥形金刚石做压头,测量压痕深度。
用于较硬材料.2、齿轮的热处理钢的热处理——将金属在固态下,通过加热、保温和不同的冷却方式,改变金属内部组织结构的工艺. 常用热处理工艺:退火——加热、保温,随炉冷却.正火——加热、保温,空气冷却.作用:消除冷热加工后产生的内应力,降底硬度,细化晶粒。
淬火——加热、保温,水或油冷却.作用:提高硬度及耐磨性。
回火——加热、保温,空气或水冷却.作用:消除淬火内应力,降低脆性,提高塑性。
调质——淬火+高温回火.得到较好的综合机械性能.表面热处理工艺:表面淬火——改变表层组织,不改变化学成分.化学热处理——表层组织及化学成分均改变.渗碳、渗氮、氰化(碳氮共渗)齿轮常用热处理工艺正火、调质、表面淬火、渗碳、渗氮.27.6齿轮传动的载荷和应力1、齿轮传动的载荷计算(1)直齿圆柱齿轮传动的受力分析设:两齿轮为标准安装。
齿轮1为主动,齿轮2为被动。
T1为小齿轮上的工作扭矩。
在节点处进行受力分析。
轮齿上作用力的数值法线方向作用力Fn可分解为:圆周力:Ft = 2T1 /d1(d1—小齿轮分度圆直径)径向力:Fr=Ft×tgαα—啮合角。
标准安装时,啮合角=压力角=20°法向力与圆周力的关系:Fn = Ft / cosα轮齿上作用力的方向圆周力:主动齿轮,Ft与ω反向。
被动齿轮,Ft与ω同向。
径向力:两齿轮均指向各自圆心。
(2)斜齿圆柱齿轮传动一.轮齿上的作用力各作用力的数值圆周力:Ft = 2T /d1在齿轮端面内,与分度圆相切.径向力:Fr = Ft×tgαn / cosβ(αn= 20°)轴向力:Fa = Ft×tgβ在轴剖面内各作用力的方向圆周力:主动齿轮Ft 与转向相反;被动齿轮Ft 与转向相同。
径向力:两齿轮均指向各自圆心,且垂直于轴线。
轴向力:沿齿轮轴线方向,其指向与齿轮旋向β、齿轮转向ω有关。
轴向力Fa的判断方法:1)根据转向及主、从动轮确定出圆周力Ft 的指向;2)由旋向β做出齿向的法线,此线可看作Fa 与Ft 的合力方向线。
3)由Ft 的指向及法线方向确定Fa的指向。
(3)直齿圆锥齿轮传动一.轮齿的受力分析1. 各作用力的数值圆周力:Ft = 2T1 /d m1与分度圆锥相切。
径向力:Fr = Ft×tgαCosδα= 20°轴向力:Fa = Ft×tgαSinδ∵δ1 +δ2 = 90°∴Sinδ1 = Cosδ 2则有Fr1 = - Fa2Fa1 = - Fr2(4)齿轮传动的计算载荷Ftc = K Ft (K — 载荷系数,表11—3)K = K A K V K αK β式中 K A — 使用系数(外部附加动载荷系数)。
K V — 动载系数(内部附加动载荷系数)。
K α— 齿间载荷分配系数,与重合度有关。
K β—齿向载荷分配系数,沿齿宽分布不均匀。
2、齿轮传动应力分析齿轮承载能力的计算依据1. 防止断齿——齿根弯曲强度计算2. 防止齿面接触疲劳(点蚀)——齿面接触疲劳强度计算 (其他失效形式,尚无成熟的计算方法)(1)齿面接触强度计算齿面接触应力ζH根据Hertz 公式,设载荷由一对轮齿承担,(ε=1)计算节点处的接触应力。
接触强度计算公式:HP t H H V A E H H u u b d F K K K K Z Z Z Z σσαββε≤±=11接触强度参数设计公式: 2311)(12HPE H d H H V A Z Z Z Z u u T K K K K d σεψβαβ±≥式中 Z H----点区域系数。
Z E----弹性系数. 与弹性模量E和泊松比μ有关;Zε----重合度系数。
Zβ----螺旋角系数。
K A—使用系数。
K V—动载系数。
Kα—齿间载荷分配系数。
Kβ—齿向载荷分配系数。
ψa----齿宽度系数ψa = b /d1u----齿数比。
许用接触应力的确定:[σH]=σH l i m Z/ S HminζH l i m ——实验齿轮接触疲劳极限,与材料的齿面硬度有关。
S Hmin ——接触应力最小安全系数,与齿面硬度有关。
Z=Z NT Z L Z V Z R Z W Z XZ NT—寿命系数。
Z L、Z V 、Z R—润滑油膜影响系数Z W—齿面工作硬化系数。
Z X—尺寸系数。
(2)齿根弯曲应力ζF设:法向力沿齿宽均匀分布,且载荷作用齿顶。
径向力对齿产生压力,计算时可忽略。
圆周力Ft对齿根产生弯曲应力:ζF = M / WM = Ftc×h F = K Ft h F W = b S2 / 6引入模数m,并将Ft1 = 2T1 / d1 = 2T1 / m Z1 代入得弯曲应力计算公式:FP S F n t F F V A F Y Y Y Y bm F K K K K σσβεαααβ≤=弯曲强度参数设计公式:βεαααβσψβY Y Y Y Z COS T K K K K m S F FP d F F V A n 321212≥式中K α— 齿间载荷分配系数。