EPS树脂生产关键工艺技术的研究
聚苯乙烯发泡成型工艺研究

目录1关于EPS的概述 (3)1.1化学与性能 (3)1.2发展 (4)1.3制备工艺 (6)1.4成型工艺 (6)1.5再生利用 (7)2聚苯乙烯泡沫板生产工艺流程 (8)2.1工艺流程 (8)2.2发泡原理 (8)2.3原材料配方及预加工 (8)3聚苯乙烯挤出发泡片材生产工艺 (10)3.1工艺过程 (10)3.2原料、辅料、发泡剂的使用 (10)3.3聚苯乙烯发泡片材工艺条件分析讨论 (12)3.3.1温度、压力和冷却 (12)3.3.2生产量及厚度和发泡倍率 (13)4EPS的应用 (16)聚苯乙烯发泡成型工艺研究摘要:可发性聚苯乙烯(EPS)通称聚苯乙烯和苯乙烯系共聚物,是一种树脂与物理性发泡剂和其它添加剂的混合物。
可发性PS可被加工成低密度(0.7—10.0ib/ft3)的泡沫塑料剂品。
最常见的可发性聚苯乙烯是含有作为发泡剂的戊烷的透明PS粒料。
由可发性聚苯乙烯制出泡沫塑料制品有几个专门步骤,这也是许多塑料树脂(包括可成型泡沫的聚烯烃及其共聚物)的一种特性。
可发性PS可用来制造各种制品如咖啡杯、吸收能量的汽车用减震器或300 ft3大的泡沫塑料块。
EPS的主要用途是一次性饮料杯、抗震包装以及隔热材料。
本文主要介绍了聚苯乙烯发泡的基本信息,然后引入到其发泡成型工艺中,最后总结了其在生活中的应用[1]。
关键词:EPS 发泡树脂工艺1关于EPS的概述可发性聚苯乙烯(expandable polystyrene)是一种加入了发泡剂的聚苯乙烯制品。
缩写代号“EPS”。
外观为无色透明珠状颗粒。
常用发泡剂为低沸点烃(如石油醚、丁烷、戊烷等),制备时以苯乙烯单体在高压釜中一次反应完成,称一步法;也可聚合后加发泡剂,使其逐步渗入聚合物本体,称二步法。
一步法产品发泡后泡孔均匀细小,制品弹性好,但聚合物分子量低,质量差;二步法产品聚合物分子量高,制成泡沫塑料强度好,但操作复杂。
在一定条件下加热起泡,即成泡沫塑料。
浅述不饱和聚酯成型技术
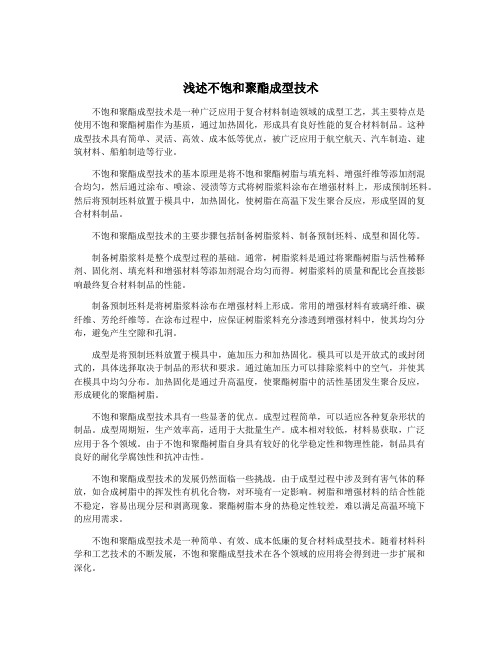
浅述不饱和聚酯成型技术不饱和聚酯成型技术是一种广泛应用于复合材料制造领域的成型工艺,其主要特点是使用不饱和聚酯树脂作为基质,通过加热固化,形成具有良好性能的复合材料制品。
这种成型技术具有简单、灵活、高效、成本低等优点,被广泛应用于航空航天、汽车制造、建筑材料、船舶制造等行业。
不饱和聚酯成型技术的基本原理是将不饱和聚酯树脂与填充料、增强纤维等添加剂混合均匀,然后通过涂布、喷涂、浸渍等方式将树脂浆料涂布在增强材料上,形成预制坯料。
然后将预制坯料放置于模具中,加热固化,使树脂在高温下发生聚合反应,形成坚固的复合材料制品。
不饱和聚酯成型技术的主要步骤包括制备树脂浆料、制备预制坯料、成型和固化等。
制备树脂浆料是整个成型过程的基础。
通常,树脂浆料是通过将聚酯树脂与活性稀释剂、固化剂、填充料和增强材料等添加剂混合均匀而得。
树脂浆料的质量和配比会直接影响最终复合材料制品的性能。
制备预制坯料是将树脂浆料涂布在增强材料上形成。
常用的增强材料有玻璃纤维、碳纤维、芳纶纤维等。
在涂布过程中,应保证树脂浆料充分渗透到增强材料中,使其均匀分布,避免产生空隙和孔洞。
成型是将预制坯料放置于模具中,施加压力和加热固化。
模具可以是开放式的或封闭式的,具体选择取决于制品的形状和要求。
通过施加压力可以排除浆料中的空气,并使其在模具中均匀分布。
加热固化是通过升高温度,使聚酯树脂中的活性基团发生聚合反应,形成硬化的聚酯树脂。
不饱和聚酯成型技术具有一些显著的优点。
成型过程简单,可以适应各种复杂形状的制品。
成型周期短,生产效率高,适用于大批量生产。
成本相对较低,材料易获取,广泛应用于各个领域。
由于不饱和聚酯树脂自身具有较好的化学稳定性和物理性能,制品具有良好的耐化学腐蚀性和抗冲击性。
不饱和聚酯成型技术的发展仍然面临一些挑战。
由于成型过程中涉及到有害气体的释放,如合成树脂中的挥发性有机化合物,对环境有一定影响。
树脂和增强材料的结合性能不稳定,容易出现分层和剥离现象。
可发性聚苯乙烯生产工艺

可发性聚苯乙烯生产工艺
可发性聚苯乙烯(EPS)是一种重要的泡沫塑料材料,广泛应
用于建筑、包装、电子等领域。
以下是可发性聚苯乙烯的生产工艺。
1. 原料准备:可发性聚苯乙烯的主要原料是苯乙烯单体、发泡剂和催化剂。
苯乙烯单体用于制备聚苯乙烯树脂,发泡剂用于实现泡孔结构,催化剂用于促进发泡反应。
2. 聚合反应:苯乙烯单体通过聚合反应聚合成聚苯乙烯树脂。
这一步骤通常在聚合釜中完成,加入合适的溶剂和催化剂,并控制反应温度和时间,使得聚合反应能够正常进行。
3. 发泡剂的添加:聚合得到的聚苯乙烯树脂需要添加发泡剂,常用的发泡剂有丙烯腈-丁二烯橡胶共聚物(NBR)、氟利昂等。
发泡剂的添加可以通过溶解在溶剂中,或者分散到树脂中的方式实现。
4. 发泡成型:将添加发泡剂的聚苯乙烯树脂放入具有一定形状的模具中,加热至熔化状态。
发泡剂在热熔的聚苯乙烯中分解产生气体,形成封闭的泡孔结构。
随着树脂的熔化,气体逐渐扩散,使得泡孔可发性聚苯乙烯形成。
5. 冷却固化:待发泡过程完成后,将模具中的可发性聚苯乙烯冷却至常温,使其固化。
固化过程中,泡孔内的气体冷却收缩,形成微小的孔洞。
6. 加工制品:将冷却固化的可发性聚苯乙烯取出模具,进行后续的加工,如切割、打磨等。
最终得到符合要求的可发性聚苯乙烯制品。
以上是可发性聚苯乙烯的主要生产工艺。
在实际应用中,还需要根据具体需求,对原料和工艺进行优化和调整,以达到更高的生产效率和产品质量。
eps成型工艺技术

eps成型工艺技术EPS(聚苯乙烯)是一种可塑性极好的材料,广泛应用于建筑、包装和运输等领域。
EPS成型工艺技术是指将EPS颗粒通过加热融化,注入空气后进行成型的过程。
本文将对EPS成型工艺技术进行详细介绍。
首先,EPS成型工艺技术的第一步是将EPS颗粒从原料中获取。
EPS颗粒通常由聚苯乙烯树脂通过物理或化学方法制得,成型前需要经过筛选和预处理,以确保颗粒的均匀性和质量。
接下来,EPS颗粒被送至注塑机。
注塑机是一台可以将EPS颗粒加热融化并注入空气的设备。
在注塑机中,EPS颗粒首先被加热,使其逐渐融化。
然后,通过喷射压缩空气的方式,将融化的EPS颗粒吹入模具中。
喷射压缩空气的强度和角度可以根据需要进行调整,以控制成型件的质量和形状。
在注塑成型的过程中,还有一项关键的工艺技术是温度控制。
EPS颗粒的加热温度和模具的温度都需要精确控制,以确保EPS颗粒能够充分融化并均匀注入模具中。
同时,模具的温度也会影响成型件的表面质量和尺寸稳定性,因此需要在整个成型过程中严格控制。
在EPS成型工艺技术中,模具的设计和制造也是至关重要的一环。
模具的设计需要考虑到成型件的形状和尺寸要求,以及EPS颗粒加热和注入的特点。
模具的制造需要使用优质材料,并经过精密加工,以确保精准的成型尺寸和光滑的表面质量。
最后,成型后的EPS产品需要进行冷却和固化。
冷却的方法通常是通过冷却水或冷却器对成型件进行迅速降温,以使EPS 颗粒能够凝固固化。
在固化过程中,成型件会逐渐变得坚固和稳定,从而可在后续的加工和使用中保持其形状和性能。
总体而言,EPS成型工艺技术是一项复杂而精密的工艺,需要掌握一系列关键的参数和操作技巧。
通过合理的EPS成型工艺技术,可以获得高质量的EPS产品,满足各种应用领域的需求。
未来,随着技术的不断进步,EPS成型工艺技术也将不断演变和创新,为人们提供更多样化和高性能的EPS产品。
可发性聚苯乙烯一步法生产悬浮工艺简介

一、前言(一)可发性聚苯乙烯简介可发性聚苯乙烯树脂,英文简称(EPS),通称聚苯乙烯和苯乙烯系共聚物。
其是由苯乙烯单体在一定量的纯水中,在一定温度下加入引发剂、分散剂、稳定剂、发泡剂后进行悬浮聚合制得的一种新型高分子材料。
主要分为普通型、高倍型和阻燃型三种类型。
经预发、熟化和模塑成形即可制得泡沫塑料制品。
具有质轻、价廉、导热率低、吸水性小、电绝缘性能好、隔音、防潮、成型工艺简单等优点,广泛用作包装、保温、隔热建筑装磺等方面的材料[1]。
(二)可发性聚苯乙烯生产工艺发展概况在国外,可发性聚苯乙烯(EPS)的生产开始于40年代,其制备工艺现有一步浸渍法(一步法)和二步浸渍法(二步法)。
自50年代由德国BASF公司开发EPS 珠粒生产工艺后, 泡沫塑料由于成型工艺及设备简易可行, 并可制成各种形状、不同密度的产品, 因而发展迅速。
70年代以来,国外一步法工艺开发的主要类型如下:聚合后期加发泡剂法,以日本日立化成公司为例,以在聚合转化率80%-85%时压入发泡剂最好。
“一锅煮法”,以德国BASF公司为代表,将包括发泡剂在内的所有物料一次加入,采用较好的配方设计和控制技术,可制得粒径分布窄的珠粒产品。
种子聚合选用可发性聚苯乙烯(EPS)、聚苯乙烯(PS)、聚氯乙烯(PVC)等作为聚合种子,得到合乎要求的可发性聚苯乙烯珠粒。
以日本钟渊化学公司为例,将离心收集的一定规格可发性聚苯乙烯细颗粒作为聚合的种子,分散在分散介质中,然后进行悬浮聚合。
在实际生产中,国外大量采用的仍是聚合后期加发泡剂法。
在国内,60年代才开始可发性聚苯乙烯技术的开发工作,随后实现工业化,但采用的方法为二步法,且规模都很小,只有千吨级水平。
80年代以前国内一直用传统的二步法工艺。
90年代初先后引进荷兰Shell公司一步法生产工艺在上海高桥化工厂和金陵石化公司塑料厂投产, 开创了我国一步法工艺的先河。
在该工艺中,PS珠粒的浸渍是在聚合过程中一起完成的。
可发性聚苯乙烯生产工艺介绍

可发性聚苯乙烯生产工艺介绍
EPS粒子的制备工艺主要有两种:
一步浸渍工艺(简称一步法)。
一步法是将苯乙烯单体、引发剂、分散剂、水、发泡剂(常见发泡剂有戊烷和丁烷)和其他助剂一起加入反应釜内,聚合后得含发泡剂的树脂颗粒,经洗涤、离心分离和干燥,制得可发性聚苯乙烯珠粒产品;
两步浸渍工艺(简称两步法)。
是将苯乙烯单体先聚合成粒度的聚苯乙烯珠粒,经分级过筛,再重新加水、乳化剂、发泡剂和其他助剂于反应釜内,加热浸渍,制得可发性聚苯乙烯珠粒产品,此法也称为后浸渍法。
一步法工艺的特点是工艺简单,投资费用低,在降低消耗和节约能耗方面也优于二步法。
目前,国外生产可发性聚苯乙烯的工艺主要为一步法是用悬浮法。
EPS成型的工艺也主要有两种:
一步挤出路线,在EPS粒子起泡之后被直接热挤出成型,这方法多用于制造板材和薄膜;
模塑路线,首先将EPS粒子用100℃的空气(或者水蒸气)进行30~50倍的预发泡,然后放置24小时使其熟化,再将已经熟化的预发泡料放置于铝或者铸件制造的模具中,用115~120℃的空气(或者水蒸气)加热,在材料膨胀同时,粒子表面相互由热的作用融合成泡塑件。
eps泡沫塑料生产工艺
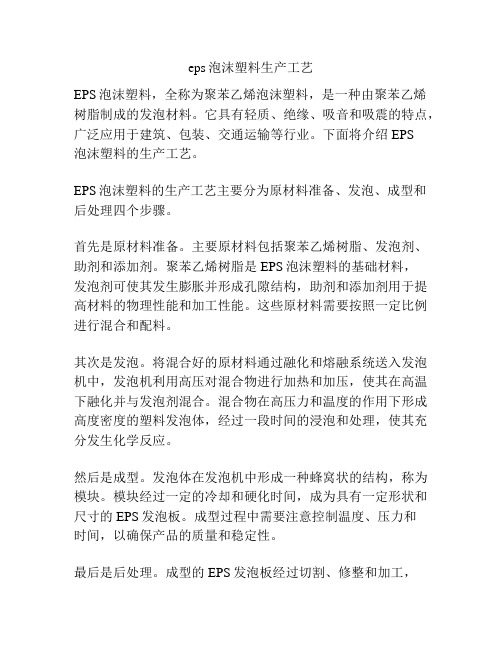
eps泡沫塑料生产工艺EPS泡沫塑料,全称为聚苯乙烯泡沫塑料,是一种由聚苯乙烯树脂制成的发泡材料。
它具有轻质、绝缘、吸音和吸震的特点,广泛应用于建筑、包装、交通运输等行业。
下面将介绍EPS泡沫塑料的生产工艺。
EPS泡沫塑料的生产工艺主要分为原材料准备、发泡、成型和后处理四个步骤。
首先是原材料准备。
主要原材料包括聚苯乙烯树脂、发泡剂、助剂和添加剂。
聚苯乙烯树脂是EPS泡沫塑料的基础材料,发泡剂可使其发生膨胀并形成孔隙结构,助剂和添加剂用于提高材料的物理性能和加工性能。
这些原材料需要按照一定比例进行混合和配料。
其次是发泡。
将混合好的原材料通过融化和熔融系统送入发泡机中,发泡机利用高压对混合物进行加热和加压,使其在高温下融化并与发泡剂混合。
混合物在高压力和温度的作用下形成高度密度的塑料发泡体,经过一段时间的浸泡和处理,使其充分发生化学反应。
然后是成型。
发泡体在发泡机中形成一种蜂窝状的结构,称为模块。
模块经过一定的冷却和硬化时间,成为具有一定形状和尺寸的EPS发泡板。
成型过程中需要注意控制温度、压力和时间,以确保产品的质量和稳定性。
最后是后处理。
成型的EPS发泡板经过切割、修整和加工,制成符合要求的产品。
切割可以使用封闭式切割机,修整可以使用电锯或砂轮机,加工可以使用开槽、热压等方法。
后处理过程还包括对产品外观进行检查、均匀分装和存储等。
整个生产过程中需要严格控制原材料比例、温度、压力和时间等参数,以确保产品的质量和性能。
此外,还要注意安全操作,避免塑料燃烧和有害气体的产生。
以上就是EPS泡沫塑料的生产工艺,通过合理的工艺流程和严格的操作控制,可以生产出质量稳定的EPS泡沫塑料产品。
EPS树脂生产工艺
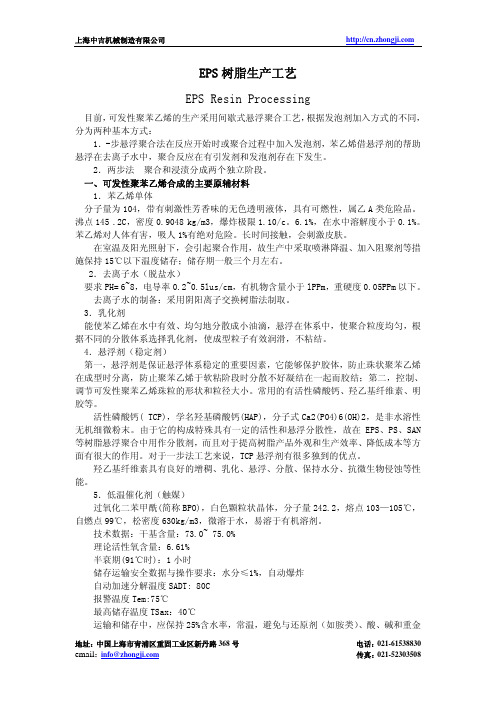
序号
名称
配比
加料量
备注
1 苯乙烯
100
2000
2 去离子水
120
2400
3 过氧化苯甲酰( BPO)
0.3~0.5
6
100%
4 过苯甲酸叔丁酯(T- BPB) 0.04~ 0.08
1
5 羟乙基纤维素(HEC)
0.05~0.1 0.5+0.25+0.25
分三次
6 磷酸三钙(TCP)
0.3—0.5
4+2+2
苯乙烯
100
水
160
BPO
0.35
t- BPB
0.07
活性磷酸钙( TCP) 0.05~ 0.15 羟乙基纤维索 0.1~ 0.2
拉开粉(皂粉) 2~ 8
消化剂 0.1
发泡剂
7~ 12
(2)阻燃型 FPS 配方
苯乙烯
100
水
160
BPO
0.35
t – BPB
0.07
过氧化二异丙苯 0.2~0.3
聚乙烯醇
2.两步法 聚合和浸渍分成两个独立阶段。 一、可发性聚苯乙烯合成的主要原辅材料
1.苯乙烯单体 分子量为 104,带有刺激性芳香味的无色透明液体,具有可燃性,属乙 A 类危险品。 沸点 145 .2C,密度 0.9048 kg/m3,爆炸极限 1.10/c。6.1%,在水中溶解度小于 0.1%。 苯乙烯对人体有害,吸人 1%有绝对危险。长时间接触,会刺激皮肤。
普通型可发性聚苯乙烯浸渍操作规程如表 2-3 所示。 阻燃型可发性聚苯乙烯浸渍操作规程如表 2-4 所示。
图 2-3 可发性聚苯乙烯树脂生产流程图 1-发泡剂贮槽;2-往复泵;3-高位计量槽;4-分散剂溶解锅;5-离心泵;6-鼓风 机;7-加料斗;8-旋风加料器;9-反应釜;10 -活动洗料车;11-送料鼓风机;12 一加 料斗;13 -吹干鼓风机;14 -吹予器;15 -装料筒
EPS生产工艺(新材料发展科)

一、可发性聚苯乙烯树脂
聚苯乙烯的珠粒中加入低沸点的液体发泡剂,在加温加压的条件下,渗透到聚苯乙烯珠粒中,使其溶胀,制成可发性聚苯乙烯树脂(珠粒)。
二、预发机理
预发过程中,含有发泡剂的珠粒缓慢加热至80C°以上,开始软化,珠粒内的发泡剂受热汽化产生压力,而使珠粒膨胀,并形成互不连通的泡孔,预发后气泡的直径为80~150微米,每立方厘米约有0.55万个小气泡。
同时,蒸汽也渗透到已膨胀的泡孔中,增加了泡孔的总压力。
随着蒸汽的不断渗入,压力也不断增大,珠粒内的体积也不断增大。
这一过程一直持续下去,体积膨胀可一直持续到泡孔壁破裂为止。
三、熟化机理
熟化处理过程中,珠粒经过空气冷却,泡孔内气孔的发泡剂和水蒸汽被冷凝成液体,使泡孔内形成了真空。
同时,空气通过泡孔膜渗透到泡孔内部,使泡孔内的压力与外界压力平衡。
这样会使预发后的珠粒具有弹性。
熟化贮存过程中发泡剂也同时向外扩散,所以预发后的珠粒贮存期不要过长。
四、成型机理
成型包括二个阶段,蒸汽加热和冷却定型。
熟化后的预发珠粒通过蒸汽进行加热,约10~50s的时间内,空气来不及逸出,受热膨胀后产生压力,此时聚合物软化,发泡剂汽化后产生的压力和泡孔内空
气产生的压力之和大于外界蒸汽压力,珠粒又再度膨胀,并胀满珠粒间隙而结成整块,形成与模具形状相同的泡沫塑料制品,通过水或风冷却便可使其定型。
EPS生产工艺解析
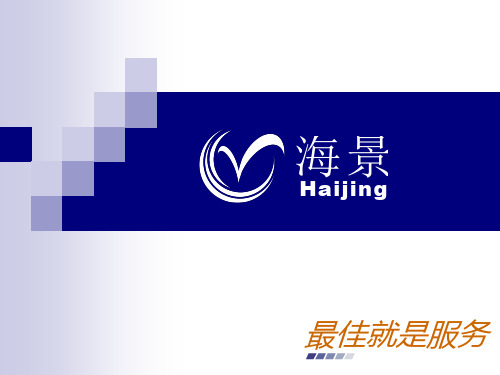
最佳就是服务
首先感谢贵集团各事 业部相关领导,长期 以来对我司工作上的 大力支持和指导!
EPS工艺培训内容
一、EPS原料性能 二、预发工艺技术
三、成型工艺技术
EPS原料性能
现原料型号主要有龙王料、兴达料 及BASF料。
EPS原料性能
EPS原料性能
EPS原料性能
快速料:分子量、挥发份低,主要用于自动机,也可用于土机方面。 标准料:分子量、挥发份高,主要用于土机方面,较少用于自动机。 快速料:它本身含发泡剂少,熟化时间短。操作时,加热时间短,冷却短,成型周期短,提高生产效率。 1. 一般情况下,因为发泡剂少,必须在最短的时间内加热,充分利用少量的发泡剂使泡粒粘结,加热 时间短,节省时间。采用高压,短时间加热。 2. 能节省能耗,提高效率,采用高温脱模,成型模温与脱模温之差距少,所以能节省蒸汽。 模具成型温度115-130℃——经过水冷却90 ℃ —— 经过抽真空,产品表面膨胀率减少到一定值——85 ℃ —— 才能脱模。 1. 快速料类型:巴斯夫CP303、龙王B-SB、兴达303、诚达PK303等。 快速料特性: 冷却速度快导致成型周期快,一般能够比普通料快20-30% 快速料的脱模温度高,达到80-85º C 传统料的脱模温度低,为60-65º C 因此,快速料可节省蒸气最高达30% 快速料成型时产品结合性宜控制在6-8成,更能体现其快速性。 快速料控制技术:采取高压短时间加热。 2. 普通料类型:巴斯夫CP203、龙王E-SB、兴达302、诚达PK302等。 普通料控制技术:因其分子量大、挥发份高。生产时易出现发胀现象。 宜采用低压较长时间加热。
成型工艺技术
成型工艺技术
12. 脱模 脱模原理(一次脱模): 移模脱模气 移排水阀关闭 固排水阀开 压 边吹边顶 影响脱模不良的因素: 1) 加热过火,粘模,发胀,冷却不够。 2) 模具脱模斜度不够,模具表面粗糙。 3) 顶针布置不当,不平衡。 4) 空气压力不足。 5) 气冷压力不够,模具升压不够。 6) 模具密封性不好,真空效果不好。 7) 模具水冷系统很差,产品局部没有水冷。
聚苯乙烯工艺设计
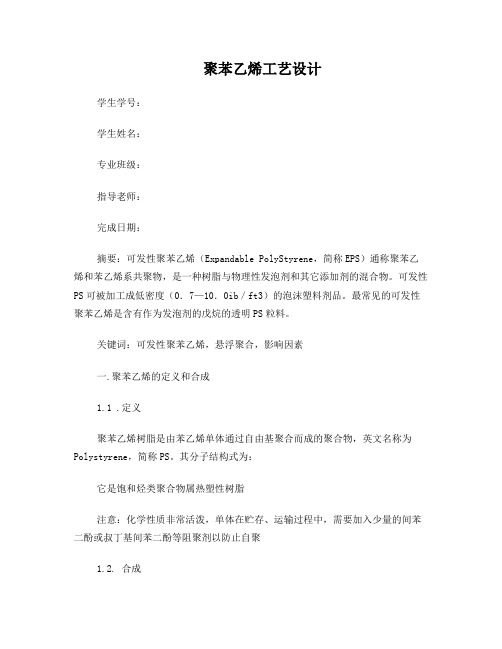
聚苯乙烯工艺设计学生学号:学生姓名:专业班级:指导老师:完成日期:摘要:可发性聚苯乙烯(Expandable PolyStyrene,简称EPS)通称聚苯乙烯和苯乙烯系共聚物,是一种树脂与物理性发泡剂和其它添加剂的混合物。
可发性PS可被加工成低密度(0.7—10.0ib/ft3)的泡沫塑料剂品。
最常见的可发性聚苯乙烯是含有作为发泡剂的戊烷的透明PS粒料。
关键词:可发性聚苯乙烯,悬浮聚合,影响因素一.聚苯乙烯的定义和合成1.1 .定义聚苯乙烯树脂是由苯乙烯单体通过自由基聚合而成的聚合物,英文名称为Polystyrene,简称PS。
其分子结构式为:它是饱和烃类聚合物属热塑性树脂注意:化学性质非常活泼,单体在贮存、运输过程中,需要加入少量的间苯二酚或叔丁基间苯二酚等阻聚剂以防止自聚1.2. 合成●本体聚合——获得的PS纯净度高,主要用来制造对电性能要求高的制品。
●悬浮聚合——获得的PS分子量高分布窄但纯度不如本体聚合PS,可用来制造一般日用和工业用品、和PS泡沫塑料。
乳液聚合——主要用于涂料和PS泡沫塑料。
溶液聚合——主要用于配制清漆。
各种生产方法制得的PS在性能上略有不同。
我国PS的工业化生产主要采用悬浮聚合和本体聚合,其中以悬浮法为主。
1.3.聚苯乙烯的结构聚苯乙烯的分子链上交替连接着侧苯基。
由于侧苯基的体积较大,有较大的位阻效应,而使聚苯乙烯的分子链变得刚硬,因此,玻璃化温度比聚乙烯、聚丙烯都高,且刚性脆性较大,制品易产生内应力。
由于侧苯基在空间的排列为无规结构,因此聚苯乙烯为无定形聚合物,具有很高的透明性。
侧苯基具有很大的空间位阻,造成PS分子链很僵硬,Tg在80℃。
侧苯基的存在使聚苯乙烯的化学活性要大一些,苯环所能进行的特征反应如氯化、硝化、磺化等聚苯乙烯都可以进行。
此外,侧苯基可以使主链上a 氢原子活化,在空气中易氧化生成过氧化物,并引起降解,因此制品长期在户外使用易变黄、变脆。
但由于苯环为共扼体系,使得聚合物耐辐射性较好,在较强辐射的条件下,其性能变化较小。
EPS制造工艺
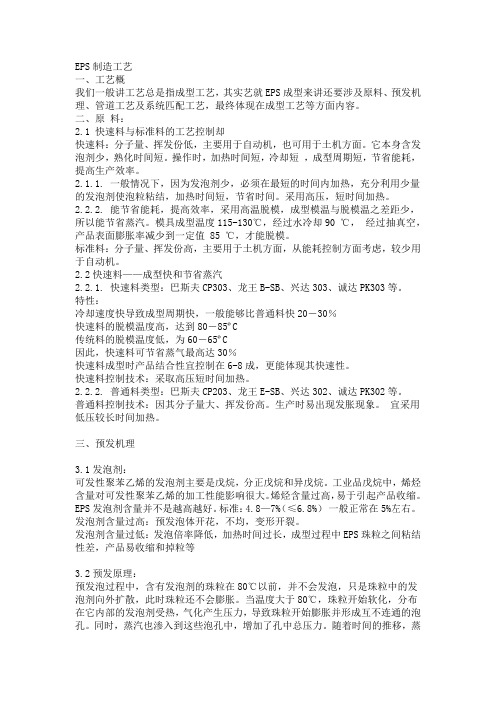
EPS制造工艺一、工艺概我们一般讲工艺总是指成型工艺,其实艺就EPS成型来讲还要涉及原料、预发机理、管道工艺及系统匹配工艺,最终体现在成型工艺等方面内容。
二、原料:2.1 快速料与标准料的工艺控制却快速料:分子量、挥发份低,主要用于自动机,也可用于土机方面。
它本身含发泡剂少,熟化时间短。
操作时,加热时间短,冷却短,成型周期短,节省能耗,提高生产效率。
2.1.1. 一般情况下,因为发泡剂少,必须在最短的时间内加热,充分利用少量的发泡剂使泡粒粘结,加热时间短,节省时间。
采用高压,短时间加热。
2.2.2. 能节省能耗,提高效率,采用高温脱模,成型模温与脱模温之差距少,所以能节省蒸汽。
模具成型温度115-130℃,经过水冷却90 ℃,经过抽真空,产品表面膨胀率减少到一定值85 ℃,才能脱模。
标准料:分子量、挥发份高,主要用于土机方面,从能耗控制方面考虑,较少用于自动机。
2.2快速料——成型快和节省蒸汽2.2.1. 快速料类型:巴斯夫CP303、龙王B-SB、兴达303、诚达PK303等。
特性:冷却速度快导致成型周期快,一般能够比普通料快20-30%快速料的脱模温度高,达到80-85ºC传统料的脱模温度低,为60-65ºC因此,快速料可节省蒸气最高达30%快速料成型时产品结合性宜控制在6-8成,更能体现其快速性。
快速料控制技术:采取高压短时间加热。
2.2.2. 普通料类型:巴斯夫CP203、龙王E-SB、兴达302、诚达PK302等。
普通料控制技术:因其分子量大、挥发份高。
生产时易出现发胀现象。
宜采用低压较长时间加热。
三、预发机理3.1发泡剂:可发性聚苯乙烯的发泡剂主要是戊烷,分正戊烷和异戊烷。
工业品戊烷中,烯烃含量对可发性聚苯乙烯的加工性能影响很大。
烯烃含量过高,易于引起产品收缩。
EPS发泡剂含量并不是越高越好。
标准:4.8—7%(≤6.8%)一般正常在5%左右。
发泡剂含量过高:预发泡体开花,不均,变形开裂。
EPS原料生产工艺及主要用途
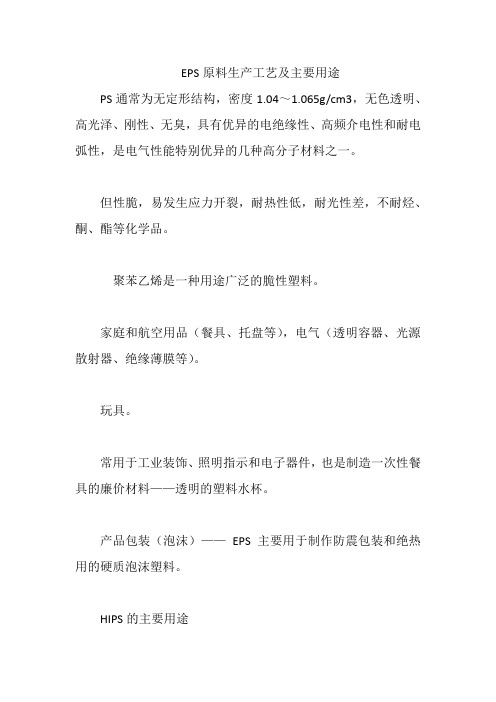
EPS原料生产工艺及主要用途PS通常为无定形结构,密度1.04~1.065g/cm3,无色透明、高光泽、刚性、无臭,具有优异的电绝缘性、高频介电性和耐电弧性,是电气性能特别优异的几种高分子材料之一。
但性脆,易发生应力开裂,耐热性低,耐光性差,不耐烃、酮、酯等化学品。
聚苯乙烯是一种用途广泛的脆性塑料。
家庭和航空用品(餐具、托盘等),电气(透明容器、光源散射器、绝缘薄膜等)。
玩具。
常用于工业装饰、照明指示和电子器件,也是制造一次性餐具的廉价材料——透明的塑料水杯。
产品包装(泡沫)——EPS主要用于制作防震包装和绝热用的硬质泡沫塑料。
HIPS的主要用途现在正在广泛使用的电视机、空调器的外壳就是聚苯乙烯的。
也适于制作包装材料、容器和家具等。
聚苯乙烯(PS)类塑料是一种比较古老的塑料,生产工艺也已经较为完善。
与其它塑料相比ps具有的特点是有良好的透明性(透光率88%-92%)和表面光泽、容易染色、硬度高、刚性好,此外,还有良好的耐水性,耐化学腐蚀和加工流动性。
其主要缺点有:性脆、冲击强度低、易出现应力开裂、耐热性差等。
市场上出售的常有HIPS和GDPS两种,其中HIPS为改性的高抗冲击性聚苯乙烯,它具有很好的抗冲击性能。
GPPS为普通聚苯乙烯。
聚苯乙烯的主要用途:电子电器:可用于制造电视机、录音机以及各种电器仪表零件、壳体、高频电容器等建筑方面:用于公用建筑透明部件、光学仪器和透明模型的生产,如灯罩,仪器罩壳,包装容器等。
日常用品:梳子、盒子、牙刷柄、圆珠笔杆、学习用品、儿童玩具等其它方面:可用于发泡制作防震、隔音、保温、夹芯结构材料,电冰箱、火车、飞机等也用它们来作为隔热、隔音,还可用来做救生圈等。
PS是一种热塑性非结晶性的树脂,主要分为:通用级聚苯乙烯(GPPS、俗称透苯),使用于日常用品、玩具、塑料板等方面;抗冲击级聚苯乙烯(HIPS、俗称改苯)是添加了BR或SBR等橡胶的PS产品,主要用于汽机车零配件、电气外壳等;和发泡级聚苯乙烯(EPS)是添加丁烷、戊烷等挥发性液体作为发泡剂的预发泡粒,依发泡程度,可用于生产包装材、隔热材、缓冲材等。
可发性聚苯乙烯EPS的生产工艺修订版
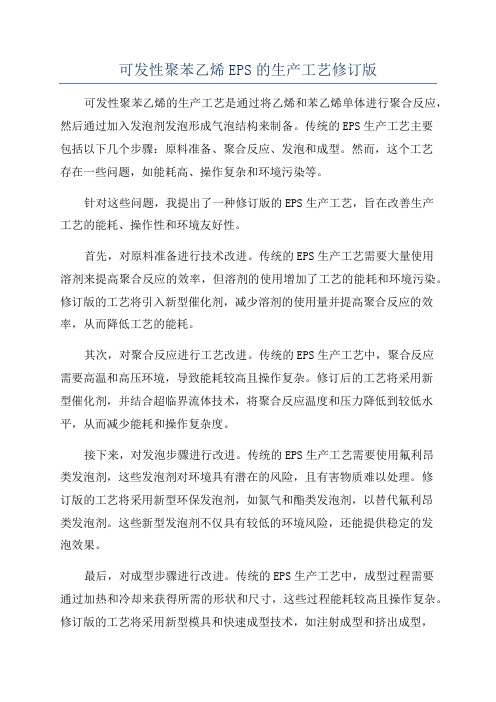
可发性聚苯乙烯EPS的生产工艺修订版可发性聚苯乙烯的生产工艺是通过将乙烯和苯乙烯单体进行聚合反应,然后通过加入发泡剂发泡形成气泡结构来制备。
传统的EPS生产工艺主要包括以下几个步骤:原料准备、聚合反应、发泡和成型。
然而,这个工艺存在一些问题,如能耗高、操作复杂和环境污染等。
针对这些问题,我提出了一种修订版的EPS生产工艺,旨在改善生产工艺的能耗、操作性和环境友好性。
首先,对原料准备进行技术改进。
传统的EPS生产工艺需要大量使用溶剂来提高聚合反应的效率,但溶剂的使用增加了工艺的能耗和环境污染。
修订版的工艺将引入新型催化剂,减少溶剂的使用量并提高聚合反应的效率,从而降低工艺的能耗。
其次,对聚合反应进行工艺改进。
传统的EPS生产工艺中,聚合反应需要高温和高压环境,导致能耗较高且操作复杂。
修订后的工艺将采用新型催化剂,并结合超临界流体技术,将聚合反应温度和压力降低到较低水平,从而减少能耗和操作复杂度。
接下来,对发泡步骤进行改进。
传统的EPS生产工艺需要使用氟利昂类发泡剂,这些发泡剂对环境具有潜在的风险,且有害物质难以处理。
修订版的工艺将采用新型环保发泡剂,如氮气和酯类发泡剂,以替代氟利昂类发泡剂。
这些新型发泡剂不仅具有较低的环境风险,还能提供稳定的发泡效果。
最后,对成型步骤进行改进。
传统的EPS生产工艺中,成型过程需要通过加热和冷却来获得所需的形状和尺寸,这些过程能耗较高且操作复杂。
修订版的工艺将采用新型模具和快速成型技术,如注射成型和挤出成型,以替代传统的加热和冷却成型方法。
这些新型成型技术能够提供更高的效率和更精确的成型结果,从而减少能耗和操作复杂度。
修订版的EPS生产工艺通过改进原料准备、聚合反应、发泡和成型步骤,实现了能耗的降低、操作的简化和环境友好性的提高。
这将有助于推动可发性聚苯乙烯的产业发展,并减少对环境的影响。
年产3000吨eps生产工艺初步设计方案

年产3000吨eps生产工艺初步设计方案年产3000吨EPS生产工艺初步设计方案引言:EPS(聚苯乙烯)是一种轻质、耐用、隔热和吸震材料,广泛应用于建筑、包装、航空航天等领域。
本文将介绍一种年产3000吨EPS的生产工艺初步设计方案,旨在提供一种高效、可靠的生产工艺流程。
一、原材料准备1. 聚苯乙烯颗粒:选择高质量的聚苯乙烯颗粒作为原材料,确保产品质量稳定。
2. 发泡剂:选用合适的发泡剂,根据产品要求确定添加量。
二、预发泡和成型工艺1. 预发泡:将聚苯乙烯颗粒和发泡剂加入预发泡机中,在一定温度和压力下进行预发泡处理,使颗粒膨胀。
2. 成型:将预发泡后的颗粒放入模具中,施加一定的温度和压力,使颗粒粘合成型。
三、热处理工艺1. 烘烤:将成型后的EPS产品放入烘炉中进行烘烤,使其内部的气泡膨胀均匀,并提高产品的物理性能。
2. 冷却:将烘烤后的EPS产品进行冷却处理,使其固化并保持形状。
四、切割和包装工艺1. 切割:根据产品要求,采用自动或手动切割设备,将成品EPS产品切割成所需尺寸。
2. 包装:将切割后的EPS产品进行包装,以防止产品在运输和储存过程中受到损坏。
五、质量控制1. 原材料检测:对进货的聚苯乙烯颗粒进行质量检测,确保原材料符合标准要求。
2. 工艺控制:严格控制预发泡、成型、热处理等工艺参数,确保产品质量稳定。
3. 产品检测:对成品EPS产品进行物理性能测试和外观检查,确保产品符合要求。
六、环保措施1. 废水处理:对生产过程中产生的废水进行处理,确保排放达到环保标准。
2. 废料回收:对生产过程中产生的废料进行回收利用,减少资源浪费。
3. 能源节约:采用节能型设备,并合理控制能源的使用,降低能源消耗。
七、安全生产1. 培训与防护:对生产工人进行相关培训,提高其安全意识,配备必要的个人防护用品。
2. 安全设施:配备消防设备、安全警示标识等,确保生产过程安全可靠。
总结:本文介绍了一种年产3000吨EPS的生产工艺初步设计方案。
eps生产工艺比选
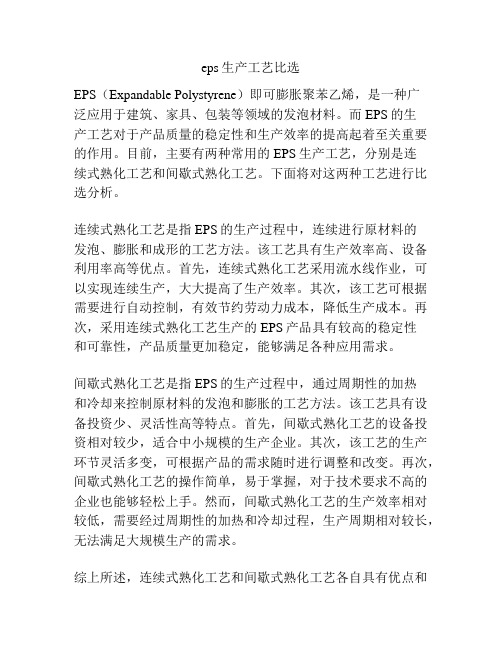
eps生产工艺比选EPS(Expandable Polystyrene)即可膨胀聚苯乙烯,是一种广泛应用于建筑、家具、包装等领域的发泡材料。
而EPS的生产工艺对于产品质量的稳定性和生产效率的提高起着至关重要的作用。
目前,主要有两种常用的EPS生产工艺,分别是连续式熟化工艺和间歇式熟化工艺。
下面将对这两种工艺进行比选分析。
连续式熟化工艺是指EPS的生产过程中,连续进行原材料的发泡、膨胀和成形的工艺方法。
该工艺具有生产效率高、设备利用率高等优点。
首先,连续式熟化工艺采用流水线作业,可以实现连续生产,大大提高了生产效率。
其次,该工艺可根据需要进行自动控制,有效节约劳动力成本,降低生产成本。
再次,采用连续式熟化工艺生产的EPS产品具有较高的稳定性和可靠性,产品质量更加稳定,能够满足各种应用需求。
间歇式熟化工艺是指EPS的生产过程中,通过周期性的加热和冷却来控制原材料的发泡和膨胀的工艺方法。
该工艺具有设备投资少、灵活性高等特点。
首先,间歇式熟化工艺的设备投资相对较少,适合中小规模的生产企业。
其次,该工艺的生产环节灵活多变,可根据产品的需求随时进行调整和改变。
再次,间歇式熟化工艺的操作简单,易于掌握,对于技术要求不高的企业也能够轻松上手。
然而,间歇式熟化工艺的生产效率相对较低,需要经过周期性的加热和冷却过程,生产周期相对较长,无法满足大规模生产的需求。
综上所述,连续式熟化工艺和间歇式熟化工艺各自具有优点和缺点。
若企业追求生产效率和产品质量的稳定性,且有较高的技术实力和资金支持,可选择连续式熟化工艺。
若企业规模较小,资金有限,但追求生产灵活性和设备投资少的情况下,可选择间歇式熟化工艺。
当然,具体选择哪种生产工艺还需根据企业自身的情况和需求进行综合考量。
最后,无论选择哪种EPS生产工艺,企业应注重技术研发和人才培养,不断提高生产工艺的稳定性和效率,以满足市场需求,实现企业的可持续发展。
《可发性聚苯乙烯(EPS)的生产工艺》
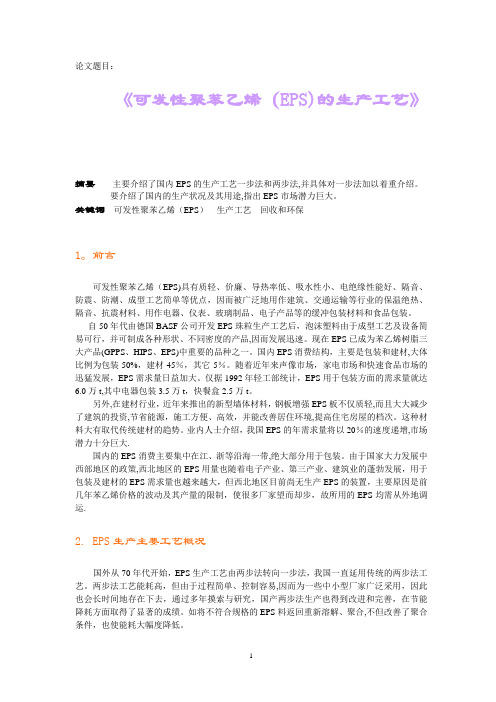
论文题目:《可发性聚苯乙烯(EPS)的生产工艺》摘要主要介绍了国内EPS的生产工艺一步法和两步法,并具体对一步法加以着重介绍。
要介绍了国内的生产状况及其用途,指出EPS市场潜力巨大。
关键词可发性聚苯乙烯(EPS)生产工艺回收和环保1。
前言可发性聚苯乙烯(EPS)具有质轻、价廉、导热率低、吸水性小、电绝缘性能好、隔音、防震、防潮、成型工艺简单等优点,因而被广泛地用作建筑、交通运输等行业的保温绝热、隔音、抗震材料、用作电器、仪表、玻璃制品、电子产品等的缓冲包装材料和食品包装。
自50年代由德国BASF公司开发EPS珠粒生产工艺后,泡沫塑料由于成型工艺及设备简易可行,并可制成各种形状、不同密度的产品,因而发展迅速。
现在EPS已成为苯乙烯树脂三大产品(GPPS、HIPS、EPS)中重要的品种之一。
国内EPS消费结构,主要是包装和建材,大体比例为包装50%,建材45%,其它5%。
随着近年来声像市场,家电市场和快速食品市场的迅猛发展,EPS需求量日益加大。
仅据1992年轻工部统计,EPS用于包装方面的需求量就达6.0万t,其中电器包装3.5万t,快餐盒2.5万t。
另外,在建材行业,近年来推出的新型墙体材料,钢板增强EPS板不仅质轻,而且大大减少了建筑的投资,节省能源,施工方便、高效,并能改善居住环境,提高住宅房屋的档次。
这种材料大有取代传统建材的趋势。
业内人士介绍,我国EPS的年需求量将以20%的速度递增,市场潜力十分巨大.国内的EPS消费主要集中在江、浙等沿海一带,绝大部分用于包装。
由于国家大力发展中西部地区的政策,西北地区的EPS用量也随着电子产业、第三产业、建筑业的蓬勃发展,用于包装及建材的EPS需求量也越来越大,但西北地区目前尚无生产EPS的装置,主要原因是前几年苯乙烯价格的波动及其产量的限制,使很多厂家望而却步,故所用的EPS均需从外地调运.2. EPS生产主要工艺概况国外从70年代开始,EPS生产工艺由两步法转向一步法,我国一直延用传统的两步法工艺。
EPS生产工艺解析
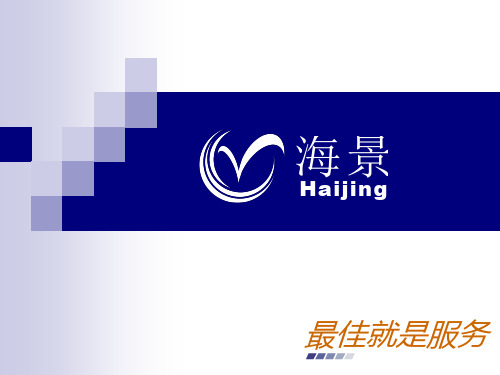
成型工艺技术
影响入料因素:
⑴ 风管、料管损坏出现漏气现象而导致进料不畅。 ⑵ 产品结构薄、窄。 ⑶ 料桶、料管、料枪中出现结块现象。 ⑷ 料枪数量不够。 ⑸ 空气压力不够,入料时间短。 ⑹ 料枪互相干扰 ⑺ 料枪出现故障(因密封或润滑性差导致不开枪或不打 料)。
4. 合模加压 在正常情况下,尽量缩短时间一般在1.5 S—2.5 S 。 5. 预热 蒸汽进入固移模内,对模具进行预热,使模具得到预热的同时,将存留期间的冷凝水 与冷空气排出。作用:提高模具温度,加强产品表观熔结度。 6. 穿透加热(固模加热;移模加热) 作用:提高制品芯部、内部熔结性。穿透加热耗、浪费蒸汽较严重。 7. 双方加热 作用:进一步增强加热效果,提高产品表面质量。 8. 回温(保温) 所有阀关闭,充分利用模具的余热,使产品进行保温加热。有利于产品表面熔结性,能 较好节约能源(蒸汽)。 9. 预冷 水冷阀打开,排水阀关闭。合理延长预冷,产品冷却较快,缩短冷却时间,提高成型速 度。 10. 水冷 水冷却时,水冷阀打开,排水阀打开。水与空气共同进行冷却效果较好。 11. 真空冷却 真空阀打开,真空泵抽真空。 作用:使模具和制品内的余热与水分全部排空,抽掉部分发泡剂,避免产品发胀。使模内 形成负压,有利于产品进行脱模。
预发工艺技术 发泡剂: 可发性聚苯乙烯的发泡剂主要是戊烷,分正戊烷和异戊 烷。工业品戊烷中,烯烃含量对可发性聚苯乙烯的加工 性能影响很大。烯烃含量过高,易于引起产品收缩。 EPS发泡剂含量并不是越高越好。标准:4.8—7%(≤6.8%) 一般正常在5%左右。 发泡剂含量过高:预发泡体开花,不均,变形开裂。 发泡剂含量过低:发泡倍率降低,加热时间过长,成型过程 中EPS珠粒之间粘结性差,产品易收缩和掉粒等。
聚苯乙烯生产技术及其进展

聚苯乙烯生产技术及其进展聚苯乙烯(PS)是产量仅次于聚乙烯、聚氯乙烯和聚丙烯的通用树脂,分为通用聚苯乙烯(GPPS)、抗冲聚苯乙烯(HIPS)和发泡聚苯乙烯(EPS)3种。
聚苯乙烯树脂在丄业上主要采用本体法和悬浮法制得,其中稀释剂本体法最为常用。
聚苯乙烯树脂是一种热塑性树脂,易加工、价格低,被广泛应用于一次性用品、包装、玩具、建筑、电子和家具器械等方面。
1主要工艺技术工业上聚苯乙烯主要采用本体法及悬浮法两种生产工艺,本体法是最主要的生产方法,目前世界上85%以上的GPPS和HIPS是采用连续本体法工艺生产的。
连续本体法生产装置一般有一条或儿条生产线,生产能力为2万-16万吨/年。
通过改进反应器设计、分子量和橡胶粒径控制以及脱挥发分技术,可以使本体法工艺生产线的规模更大、效率更高。
H前已有单线能力9万-13.8万吨/年的大型本体法生产装置投入工业运转,但一般来说单反应器能力3万-5万吨/年。
悬浮法是第二种聚苯乙烯基本生产工艺,悬浮法工艺的装置规模一般小于本体法,间歇操作,牌号切换时清洗时间很短。
对于某些高耐热和高分子量的牌号只能用间歇悬浮聚合工艺生产,但在相同的生产能力下采用连续本体法的工厂固定资产投资及生产成本比悬浮法低,因此对大多数PS牌号来说用本体法生产更为经济。
LI前悬浮法一般已被本体法代替,主要还用于生产EPSo(1)本体聚合工艺技术。
目前全世界工业化的本体法PS生产装置采用的专利技术在12种以上,这些工艺基本步骤相同,仅在反应器及工艺配置方面有所不同,如反应器的撤热方式、轴向混合程度、径向混合程度、串联的反应器数(包括预聚合) 以及反应器的构型(如立式或卧式)等。
PS稀释剂本体聚合反应主要采用两种类型的反应器:线性流反应器(LFR)和连续搅拌槽式反应器(CSTR) o前者与理想情况下的柱塞流反应器类似,后者的组成和温度具有比较理想的各向同性。
美国大多数GSPS(即未改性)采用这类装置生产。
- 1、下载文档前请自行甄别文档内容的完整性,平台不提供额外的编辑、内容补充、找答案等附加服务。
- 2、"仅部分预览"的文档,不可在线预览部分如存在完整性等问题,可反馈申请退款(可完整预览的文档不适用该条件!)。
- 3、如文档侵犯您的权益,请联系客服反馈,我们会尽快为您处理(人工客服工作时间:9:00-18:30)。
EPS树脂生产关键工艺技术的研究
【摘要】本课题以苯乙烯、戊烷、甲苯等和其他辅助化学品为原料,使用国际先进水平的“一步法”TCP悬浮聚合工艺,对关键工艺技术进行研究,开发出不同类型的可发性聚苯乙烯树脂产品。
【关键词】EPS;聚合浸渍;悬浮体系
1 前言
可发性聚苯乙烯是苯乙烯和其他的一些辅料经过聚合生产成聚苯乙烯,是很好的保温材料。
EPS产品具有优异持久的保温隔热性、独特的缓冲抗震性、抗老化性和防水性,且其质轻、价廉、导热率低、吸水性小、电绝缘性能好、隔音、防潮、成型工艺简单等优点。
主要用在板材、大型的包装制品以及特殊用品的产品件。
2 实验部分
2.1 试验材料
苯乙烯、纯水、发泡剂(戊烷)、低温引发剂1:BPO 、低温引发剂2:CP-02 、分散剂1:硫酸钠、分散剂2:磷酸钙、分散剂3:活性磷酸钙、稳定剂1:轻质碳酸钙、稳定剂2:硬脂酸锌、增塑剂1:甲苯、增塑剂2:二甲苯、乳化剂:GMS 、成核剂、聚乙烯蜡。
2.2 试验过程与结果
采用正交试验方法进行配比优选试验,从中选取最佳基本配方。
通过调整不同比例以满足系列产品不同的功能、性质等性能需求。
以阻燃型EPS为例阐述试验过程与结果:
(1)正交实验设计:根据产品本身的性质,结合生产实际,工艺研究中选定配方比例、熟化温度、反应时间为考虑因素,以产品的特性:密度、压缩强度、导热系数、断裂弯曲负荷、氧指数作为考察指标。
选用L9(34)正交表进行试验,根据预试验情况,因素水平安排见表1。
2)产品特性的考察
产品最大的特性是适应多数消费者的需求,这里只考察了阻燃型可发性聚苯乙烯的内在品质特性,密度、压缩强度、导热系数、断裂弯曲负荷、氧指数,不包含商业运作中包装及价格等因素。
考察结果采用了市场评价评分方法统计取得。
(3)实验过程及数据处理
试验及实验结果见表2,方差分析见表3、表4、表5、表6。
注:除导热系数评分为数值越小越好外,其它均为评分值越大越好。
从实验结果直观分析,最好的实验条件为:密度A2B1C2,压缩强度A2B1C2或者A3B1C3,导热系数A2B3C1,氧指数A3B2C1。
对实验结果影响最大的因素从表中极差R值分析可知,密度B、C素均影响大,压缩强度A、B因素均影响大,导热系数B、C因素影响大,氧指数C因素影响大。
F0.9(2,2)=9.0,从方差分析表中可知,A、C因素即水油比,阻燃剂对压缩强度指标在显著性水平0.1上显露,压缩强度优选A2、C2。
F0.9(2,2)=9.0,FA =FB<FC,因此,水油比和悬浮聚合分散剂对导热系数特性在显著水平0.1上是最显著的,在导热系数上上优选A2、B3。
F0.9(2,2)=9.0 ,从方差分析表中可知,B、C对氧指数指标在0.1上显著,氧指数优选B、C即P悬浮分散剂、阻燃剂为显著因素,选择B2C1。
(4)实验结果
通过正交试验设计,结合生产实际,证明在可发性聚苯乙烯生产中,水油比为1.05,悬浮分散剂为0.16,阻燃剂为0.075为最佳工艺参数。
以正交试验分析同样选择出目前条件下最佳的配方范围为苯乙烯:92—95份;去离子水100—150份;发泡剂(戊烷)6.5—7.5份。
通过正交试验设计分析同样得到可发性聚苯乙烯生产最佳工艺参数为水油比为1.05,悬浮分散剂为0.16,阻燃剂为0.075。
2.3 不同分散体系的影响
本课题研究过程中采用常温常压下合成的TCP粉末,反应过程中不断有副产物C02从TCP中逸出,留下气体通道,使得TCP分散剂微粒具有多孔结构、高比表面积,粒度适中且分布均匀。
这种工艺生产的TCP具有良好的悬浮聚合分散性和稳定性,并解决了生产过程中的团聚问题。