10分钟详细了解TPE注塑成型容易出现的问题及解决方法
注塑过程中常见的问题及解决方案

注塑过程中常见的问题及解决方案一、飞边(披锋)1. 问题描述- 这飞边就像塑料偷偷长出来的小翅膀,在注塑件的边缘或者分型面那里冒出来,看着可闹心了。
就像好好的一块蛋糕,边缘突然多出了一些不规则的奶油坨坨。
2. 解决方案- 首先得检查模具的合模力。
要是合模力不够,那塑料就会像调皮的小孩从门缝里挤出来。
适当增加合模力,把模具紧紧抱住,让塑料乖乖待在该待的地方。
- 模具的磨损也会导致飞边。
就像穿破了的鞋子会漏脚指头一样,磨损的模具缝隙变大了。
这时候就得修模啦,把那些磨损的地方补一补或者磨平。
- 注塑压力也不能太大。
如果压力太大,塑料就像被大力士猛推的水,到处乱流。
降低注塑压力,找到一个合适的值,既能把模具填满,又不会让塑料溢出来。
二、短射(缺料)1. 问题描述- 短射就像给一个杯子倒水,结果没倒满一样。
注塑件看着不完整,有些地方该有塑料的却空着,就像一个没发育好的小怪物。
2. 解决方案- 先看看注塑压力是不是太小。
压力小的话,塑料就像没力气的小蚂蚁,爬不到模具的每个角落。
增加注塑压力,让塑料充满整个模具型腔。
- 塑料的流动性也很关键。
如果塑料太黏,就像浓稠的糨糊,很难流到模具的远端。
这时候可以提高料筒温度,让塑料变得稀一点,流动性更好,就像把糨糊加热变成稀粥一样,能顺利流到各个地方。
- 浇口尺寸也可能有问题。
要是浇口太小,就像一个小得可怜的水龙头,水流不出来多少。
适当扩大浇口尺寸,让塑料能畅快地流进模具。
三、气泡(气穴)1. 问题描述2. 解决方案- 注塑速度可能太快了。
塑料像一阵风呼呼地冲进模具,把空气都裹在里面了。
降低注塑速度,让塑料慢慢流进去,就像散步一样,这样空气就有机会跑出来了。
- 模具的排气也很重要。
如果模具没有排气孔或者排气不良,空气就被困在里面出不来。
在模具上开排气槽或者使用透气钢材料,给空气一条逃跑的路。
- 塑料干燥不彻底也会产生气泡。
如果塑料里有水份,加热的时候就会变成水蒸气,形成气泡。
TPE常见问题
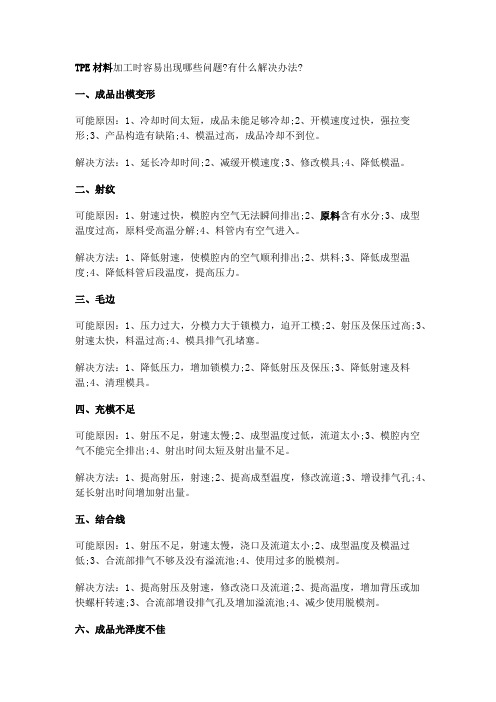
TPE材料加工时容易出现哪些问题?有什么解决办法?一、成品出模变形可能原因:1、冷却时间太短,成品未能足够冷却;2、开模速度过快,强拉变形;3、产品构造有缺陷;4、模温过高,成品冷却不到位。
解决方法:1、延长冷却时间;2、减缓开模速度;3、修改模具;4、降低模温。
二、射纹可能原因:1、射速过快,模腔内空气无法瞬间排出;2、原料含有水分;3、成型温度过高,原料受高温分解;4、料管内有空气进入。
解决方法:1、降低射速,使模腔内的空气顺利排出;2、烘料;3、降低成型温度;4、降低料管后段温度,提高压力。
三、毛边可能原因:1、压力过大,分模力大于锁模力,迫开工模;2、射压及保压过高;3、射速太快,料温过高;4、模具排气孔堵塞。
解决方法:1、降低压力,增加锁模力;2、降低射压及保压;3、降低射速及料温;4、清理模具。
四、充模不足可能原因:1、射压不足,射速太慢;2、成型温度过低,流道太小;3、模腔内空气不能完全排出;4、射出时间太短及射出量不足。
解决方法:1、提高射压,射速;2、提高成型温度,修改流道;3、增设排气孔;4、延长射出时间增加射出量。
五、结合线可能原因:1、射压不足,射速太慢,浇口及流道太小;2、成型温度及模温过低;3、合流部排气不够及没有溢流池;4、使用过多的脱模剂。
解决方法:1、提高射压及射速,修改浇口及流道;2、提高温度,增加背压或加快螺杆转速;3、合流部增设排气孔及增加溢流池;4、减少使用脱模剂。
六、成品光泽度不佳可能原因:1、射速过慢,射压不足,模温过低;2、模腔内有水气或有油脂污染;3、模具表面研磨不佳或浇口及流道太小;4、射出量不足或原料中含有水分。
解决方法:1、提高射速、射压、模温;2、擦拭干净;3、修改模具;4、提高射压、射速、延长射出时间或烘料。
七、流纹可能原因:1、射压太高或太低,射速太快或太慢;2、保压时间太短或浇口太小;3、模温及浇口温度太低4材料熔融不佳。
解决方法:1、调整适当的射压及射速;2、增加保压时间或加大浇口;3、提高温度;4、提高温度,提高背压或加快螺杆转速。
注塑成型常见不良现象及处理措施

注塑成型常见不良现象及处理措施在注塑成型过程中,常常会出现一些不良现象,这些现象可能会导致产品的质量下降,甚至无法使用。
因此,及时发现并解决这些问题是非常重要的。
下面将介绍一些常见的注塑成型不良现象及处理措施。
1. 短射短射是指注塑制品在填充过程中未能充满模具腔体,导致制品出现不完整的现象。
短射的原因可能有:- 注塑机温度设置过低,导致熔融物质无法充分流动;- 模具温度过低,使得熔融物质凝固速度过快;- 注射压力过低,无法将熔融物质充分填充到模具腔体中。
处理措施:- 调整注塑机温度,确保熔融物质能够充分流动;- 提高模具温度,延缓熔融物质的凝固速度;- 增加注射压力,确保熔融物质能够充分填充到模具腔体中。
2. 气泡气泡是指制品内部或表面出现的气体聚集现象,给产品的外观和性能带来负面影响。
气泡的原因可能有:- 熔融物质中含有过多的挥发性物质;- 注射速度过快,导致气体无法及时排出;- 模具中存在气体积聚的死角。
处理措施:- 选择低挥发性的熔融物质;- 控制注射速度,避免气体无法及时排出;- 优化模具结构,减少气体积聚的死角。
3. 热胀冷缩热胀冷缩是指注塑制品在冷却过程中由于热胀冷缩系数不一致而导致尺寸变化的现象。
热胀冷缩的原因可能有:- 注塑机温度和模具温度不匹配;- 熔融物质的热胀冷缩系数不一致。
处理措施:- 调整注塑机温度和模具温度的匹配度;- 选择热胀冷缩系数相近的熔融物质。
4. 毛刺毛刺是指制品表面出现的细小突起,给产品的外观和触感带来不良影响。
毛刺的原因可能有:- 模具中存在不平整的表面;- 注塑机压力过高,使得熔融物质溢出模具腔体。
处理措施:- 修复模具表面,保持其光滑平整;- 调整注塑机压力,避免熔融物质溢出模具腔体。
5. 缩水缩水是指注塑制品在冷却过程中由于体积收缩而导致尺寸变小的现象。
缩水的原因可能有:- 熔融物质中含有过多的收缩剂;- 注塑机温度和模具温度不匹配。
处理措施:- 选择低含量的收缩剂;- 调整注塑机温度和模具温度的匹配度。
TPE注塑成型缺陷分析及解决方法

TPE注塑成型缺陷分析及解决方法1、成品出模变型1、冷却时间太短,成品未能足够冷却;解决方法:延长冷却时间;2、开模速度过快,强拉变型;解决方法:减缓开模速度;3、成品构造有缺陷;解决方法:修改模具;4、模温过高,成品冷却不到位。
解决方法:降低模温。
2、成品出模易破裂1、料温过低或模温过低;解决方法:提高炮筒温度和模具温度;2、脱模斜度不够或顶出顶出方式不当;解决方法:修改模具;3、浇口太小,解决方法:修改模具;4、脱模角不足,解决方法:修改模具。
3、成品出模后有射纹1、射速过快,模腔内空气无法瞬间排出;解决方法:降低射速,使模腔内空气顺利排出;2、原料含有水份;解决方法:烘料;3、成型温度过高,脱粒受高温分解;解决方法:降低成型温度;4、料筒内有空气进入。
解决方法:降低料管后段温度,提高压力。
4、成品出模后有毛边1、压力过大,分模力大于锁模力,迫开工模;解决方法:降低压力,飞一下模,增加锁模力;2、射压及保压过大;解决方法:降低射压及保压;3、射度过快,料温高;解决方法:降低射速及料温;4、模具排气孔堵塞。
解决方法:清理模具。
5、制品充模不足1、射压不足、射速太慢或模口有杂物;解决方法:加大射压、提高射速及清理模口射嘴;2、成型温度过低,浇口流道太小;解决方法:提高成型温度,修改流道;3、模腔内空气不能完全排出;解决方法:增设或加大排气孔;4、射出时间太短,射量不足。
解决方法:延长射出时间,增加射出量。
6、制品有结合线1、射压不足,射速太慢,浇口及流道太小;解决方法:提高射压、射速,修改浇口流道;另:喷嘴温度低,成型周期长,色母钛白粉太多,色母分散不好也是其其中原因之一。
2、成型温度及模温过低;解决方法:提高成型温度和模具温度,增加背压或加速螺杆转速;3、合流部位排气不畅或没有溢流池(冷料井);解决方法:合流部增加排气孔或增加溢流池;4、使用过多的脱模剂。
解决方法:减少脱模剂的使用量。
7、制品光泽度不佳1、射速过慢,射压过低,模温低;解决方法:提高射压、射速、模温;2、模腔内有水份或油脂污染;解决方法:擦拭干净;3、模具表面研磨不佳或浇口及流道太小;解决方法:修改模具;4、射出量不足或原料含有水份。
注塑模成型过程中的常见缺陷及解决方法

注塑模成型过程中的常见缺陷及解决方法
1 注塑模成型过程中的缺陷
注塑模是指将塑料以液体状态注入模具内,并承受模具内设计好的形状而成型的加工工艺。
这种加工工艺的缺陷主要体现在:(1)内应力
由于冷凝和冻结等原因,塑料在冷却期内会形成一定的内应力,这些内应力会折断或变形塑料制品,影响其成型的精度和尺寸的准确性;
(2)开裂
由于注塑模具的温度失去平衡,容易引起塑料表面开裂,影响塑料制品的外观质量;
(3)射脂
由于过大的模具压力,塑料在冷却过程中产生弹性变形,导致部分塑料夹在模具内,出现射脂现象,从而影响塑料制品的精度;
(4)易燃体
一些易燃物质在注塑模具成型过程中,受到热源的热量,容易引发火灾。
2 注塑模成型过程中的解决方法
(1)改善冷凝条件
合理设计模具内的冷凝段,增加冷却水的循环流量,加快冷却速度,降低内应力,减少变形现象;
(2)模具润滑
模具润滑能有效减少注塑模具生产过程中开裂的几率;
(3)改变模具温度
根据注塑塑料特性,采取合理的模具温度,确保合理的射出压力,有效减少射脂;
(4)加强安全防护
增强环境湿度,禁止一切产生火花的设备进入生产现场,防止火灾。
总之,正确处理注塑模具成型过程中的缺陷和解决方法,能有效
改善塑料制品的成型精度,改善它们的外观、可靠性和使用寿命,能
为有效利用注塑技术提供有效援力。
注塑成型各种缺陷的现象及解决方法
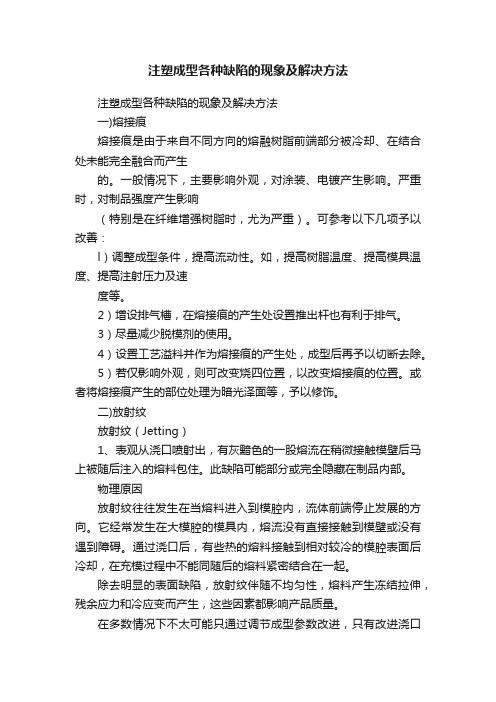
注塑成型各种缺陷的现象及解决方法注塑成型各种缺陷的现象及解决方法一)熔接痕熔接痕是由于来自不同方向的熔融树脂前端部分被冷却、在结合处未能完全融合而产生的。
一般情况下,主要影响外观,对涂装、电镀产生影响。
严重时,对制品强度产生影响(特别是在纤维增强树脂时,尤为严重)。
可参考以下几项予以改善:l)调整成型条件,提高流动性。
如,提高树脂温度、提高模具温度、提高注射压力及速度等。
2)增设排气槽,在熔接痕的产生处设置推出杆也有利于排气。
3)尽量减少脱模剂的使用。
4)设置工艺溢料并作为熔接痕的产生处,成型后再予以切断去除。
5)若仅影响外观,则可改变烧四位置,以改变熔接痕的位置。
或者将熔接痕产生的部位处理为暗光泽面等,予以修饰。
二)放射纹放射纹(Jetting)1、表观从浇口喷射出,有灰黯色的一股熔流在稍微接触模壁后马上被随后注入的熔料包住。
此缺陷可能部分或完全隐藏在制品内部。
物理原因放射纹往往发生在当熔料进入到模腔内,流体前端停止发展的方向。
它经常发生在大模腔的模具内,熔流没有直接接触到模壁或没有遇到障碍。
通过浇口后,有些热的熔料接触到相对较冷的模腔表面后冷却,在充模过程中不能同随后的熔料紧密结合在一起。
除去明显的表面缺陷,放射纹伴随不均匀性,熔料产生冻结拉伸,残余应力和冷应变而产生,这些因素都影响产品质量。
在多数情况下不太可能只通过调节成型参数改进,只有改进浇口位置和几何形状尺寸才可以避免。
与加工参数有关的原因与改良措施见下表:1、注射速度太快降低注射速度2、注射速度单级采用多级注射速度:慢-快3、熔料温度太低提高料筒温度(对热敏性材料只在计量区)。
增加低螺杆背压与设计有关的原因与改良措施见下表:1、浇口和模壁之间过渡不好提供圆弧过渡2、浇口太小增加浇口3、浇口位于截面厚度的中心浇口重定位,采用障碍注射、工艺溢料是指用手工在模具上開一條深一些的排气槽,在生產時此槽產生出來的(批峰),又叫工藝批峰,主要是用來改善燒膠或熔接痕,可將燒膠或熔接痕調整到此批峰上,生產后將其切除。
注塑成型常见不良现象及处理措施

注塑成型常见不良现象及处理措施注塑成型常见的不良现象有以下几种:
1. 短射:指注塑料进模型中未充满模腔,导致产品缺陷。
处理措施:增加注射
压力、延长注射时间、增加料缸温度、增加模具温度、增加模具出料口直径等。
2. 气泡:指产品表面或者内部浮现气泡,影响产品质量。
处理措施:增加注射
压力、延长注射时间、增加模具温度、增加料缸温度、增加模具出料口直径、增加模具排气孔等。
3. 热熔线:指产品表面浮现细小的线状缺陷,通常是由于注射速度过快导致的。
处理措施:减小注射速度、增加模具温度、增加模具出料口直径等。
4. 毛刺:指产品表面浮现细小的凸起,通常是由于模具设计不合理或者模具磨
损导致的。
处理措施:修复模具、修改模具设计、增加模具温度、增加模具出料口直径等。
5. 缩水:指产品尺寸缩小,通常是由于注射压力不足或者冷却时间不足导致的。
处理措施:增加注射压力、延长冷却时间、增加模具温度等。
6. 毛洞:指产品表面或者内部浮现凹陷,通常是由于注射速度过快或者模具设
计不合理导致的。
处理措施:减小注射速度、修改模具设计、增加模具温度等。
处理不良现象的关键是找到问题的根源,然后针对性地采取相应的处理措施。
同时,注塑成型过程中的参数控制和模具维护也是关键的因素,需要进行定期检查和调整。
注塑成型常见不良现象及处理措施

注塑成形常见不良现象产生原因分析及对策(一)缺料(1)缺料(不饱模):即是溶融塑料未能完全填充填满成型空间(模穴)各个角落的现象(2)原因及改善对策(见下表)原因改善对策1、料温,模温太低提高料管温度和模具温度2、喷嘴,主流道及灌点尺寸太小适当加大喷嘴,主流道及灌点尺寸3、模具排气不良模面保持洁净,增开排气孔4、喷嘴冷头或堵塞清除射嘴杂物,适当提高射嘴温度5、料管﹑止逆阀磨损,内泄更换止逆阀﹑料管6、射出速度,压力不够提高射速,射压7、塑料颗粒大小不一造成溶化不均调整背压与螺杆转速,使塑料混合均匀(二)毛边(1)毛边:即是在分模面﹑流道周围及模仁镶块间隙内出现的膜状或毛刺状的多余胶料(2)原因及改善对策(见下表)原因改善对策1、模具锁模力不足,射胶时模具被撑开提高机台锁模压力或调较大型机台2、分模面不吻合或有杂物清理模面,重新配模使公母模吻合3、模具镶块有间隙镶块重配至无间隙4、模温太高调整模温5、料温太高降低料管温度6、射出压力过大降低射压7、射出速度太快减慢射速8、保压时间,压力设定不当调整保压压力及时间9、背压太大,螺杆转速太快降低背压及螺杆转速改用较大机台,改正灌点位置,数量10、成品面积太大或灌点位置,数量设计不当*注:成型时间过长,模温过低而采用高压,高速射出也是产生毛边的常见原因(三)银线(1)银条(银线)即是在成型产品表面或表面附近,沿塑料流动方向,呈放射状的银白色条纹。
(2)原因及改善对策(见下表)原因改善对策1、塑料中含水份太多成型前充分干燥成型材料2、材料中有易挥发性成份或杂质原料尽量少用挥发性强的添加济保证材料纯度3、模具温度过低适当提高模温4、模具排气不良疏通排气沟或增设排气孔5、模穴内有油﹑水或脱模剂清理模穴内水,油及脱模剂6、横浇道﹑进浇口过小加大横浇道及进浇口7、射出压力过大,射速太快降低射压及减缓射速8、料管中余料过火减少料管余料及降低射嘴温度缩短成型周期9、材料在料管中分解过火降低料管后段温度,适当增加背压,减慢螺杆转速(四)成品光泽度低(1)成品光泽度低是指成品表面光泽达不到质量要求,表面无折光度。
TPE注塑件11种表面问题缺陷及解决方法

1、白化现象:指稳定剂等配合剂迁移至成型品表面,其表面像喷上粉一样呈现出一种白色现象。
原因:主要是由于稳定剂过量配合或与聚合物不相容而引起的,不相容则可以加入南京塑泰相关的相容剂来解决。
应选择与聚合物相容性良好的稳定剂或将稳定剂的用量控制在最佳的范围。
其次,更换成相对分子质量高的稳定剂也是十分有效的。
另外,也有通过迁移至成型品表面发挥其功能的稳定剂。
例如,抗静电剂、润滑剂等。
对这种稳定剂来讲,选择即使迁移也难以出现白化的稳定剂是非常必要的。
热塑性弹性体在一般的环境下使用时很少会出现白化的问题,但在高温、潮湿、户外长期使用的场合,为提高耐久性在配合上追加耐热稳定剂(防老剂)、耐侯稳定剂是十分必要的。
特别是高温下,因其极易引起迁移,所以稳定剂的选择也是相当重要的。
2.发粘现象:与树脂相比,软质热塑性弹性体表面更容易产生发粘的现象。
原因:主要是因老化而生成低相对分子质量聚合物和增塑剂、稳定剂迁移至表面而引起的。
但无论属哪种情况,采用红外光谱法(IR)等分析手段,通过分析发粘成分便能够比较容易地确定出与此相关的物质。
发粘主要是成型温度过高,聚合物因热分解而形成低相对分子质量物质的缘故。
尽管成型机的设定温度本身未达到热分解温度,但在成型工艺中的剪切生热有时也会使其暂时达到高温。
解决方案:作为其对策,降低成型温度、低剪切化,用氮气净化成型机液压缸体内部都是十分有效的。
另外,在成型机暂停时,胶料长时间以熔融状态置留在成型机的模腔内,有时也会因热老化而发粘。
另外,在高温下使用的制品很容易出现发粘的现象。
因此,稳定剂、软化剂种类的选择和用量的确定是非常重要的。
3、老化现象:制品机械性能明显降低,外观质量变差。
原因:与无机材料和金属材料相比,高分子材料的耐热、耐紫外线性较差引起制品老化。
多数制品因老化而使其机械特性明显降低,外观质量变差。
解决方案:通过配合耐热、耐候性等稳定剂,通过添加紫外线吸收剂、光稳定剂的方法,在一定程度上可以抑制老化现象的产生。
注射成型中常见缺陷及解决方法

注射成型中常见缺陷及解决方法注塑成型过程中,很容易发生一些异常现象,比如说:裂纹、制品表面有波纹、制品脆性强度下降、脱模难、制品尺寸不稳定、制品尺寸不稳定、制件脱皮分层、熔接痕、注射不满等,这些现象都会影响到成型模具的具体使用效果,因此我们需要找出相关因素以及解决方法。
裂纹1.模具太冷,调整模具温度。
2.冷却时间太长,降低冷却时间。
3.塑料和金属嵌件收缩不一样,对金属嵌件预热。
4.顶出装置倾斜不平衡,顶出截面积小或分布不当,调整顶出装置或合理安排顶杆数量及其位置。
5.制作斜度不够,脱模难,正确设计脱模斜度。
制品表面有波纹1.物料温度低,拈度大提高料温。
2.注射压力,料温高,可减少注射压力,反之则加大注射压力。
3.模具温度低,提高模具温度或增大注射压力。
4.注射速度太慢提高注射速度。
5.浇口太小,适当扩展浇口。
制品脆性强度下降1.料温太高,塑料分解,降低料温,控制物料在料筒内滞留时间。
2.塑料和嵌件处内应力过大,对嵌件预热,保证嵌件周围有一定厚度的塑料。
3.塑料回用次数多控制回料配比。
4.塑料含水,原料预热干燥。
脱模难1.模具顶出装置结构不良,改进顶出设计。
2.模腔脱模斜度不够,正确设计模具。
3.模腔温度不合适,适当控制模温。
4.模腔有接缝或存料,清理模具。
5.成型周期太短或太长,适当控制注塑周期6.模芯无进气孔,修改模具。
制品尺寸不稳定1.机器电路或油路系统不稳,修正电器或油压系统。
2.成型周期不一样,控制成型周期,使一致。
3.温度。
时间。
压力变化,调节,控制基本一致。
4.塑料颗粒大小不一,使用均一塑料。
5.回收下脚料与新料混合比例不均,控制混合比例,使均匀。
6.加料不均控制或调节加料均匀。
制件脱皮分层1.不同塑料混杂,采用单一品种的塑料。
2.同一塑料不同牌号混杂,采用同牌号的塑料。
3.塑化不良,提高成型温度。
4.混入异物,清理原材料,出去杂质。
熔接痕1.塑料温度太低提高机筒。
喷嘴及模具温度。
2.浇口太多减少浇口或改变浇口位置。
注塑过程中存在的问题及解决办法

注塑过程中存在的问题及解决办法在注塑过程中,可能会出现一些问题,影响产品的质量和生产效率。
下面列举一些常见的问题及解决办法:1. 热熔物质不充分:热熔物质的充填不充分可能会导致制品的短射或缩水等问题。
解决办法是检查喂料系统,确保熔料能够充分填充模具的所有空间,同时调整熔融温度和压力以适应具体材料和模具的要求。
2. 热熔物质的脱模性差:脱模性差可能导致产品拉伸、变形、形状不完整等问题。
解决办法是优化注塑工艺参数、或改进模具设计,增加脱模剂的使用量,确保热熔物质能顺利脱模。
3. 模具磨损严重:在长时间使用后,模具可能会出现磨损,导致制品尺寸偏差增大、质量下降。
解决办法是定期检查模具状态,必要时进行维护和修复,并妥善保养模具,延长使用寿命。
4. 模内气泡和气体线:模具填充时,可能会产生气泡或气体线,这会对产品的外观和性能造成影响。
解决办法是优化注塑压力和速度,以减少气体产生;在设计模具时,合理设置通气口和冷却系统,以排除气泡。
5. 温度控制不准确:温度是影响注塑过程和产品性能的重要因素,如果温度控制不准确,可能导致产品变形、气泡、表面瑕疵等问题。
解决办法是使用高质量的注塑机和热控系统,严格控制加热和冷却时间,确保温度分布均匀。
注塑过程中存在的问题多种多样,解决办法也需因情况而异。
因此,对于每个具体问题,需要仔细分析原因并采取相应的措施,以确保最终生产出符合要求的产品。
注塑过程中存在的问题及解决办法可以从多个方面展开,下面将深入探讨一些常见的问题,并提供相应的解决办法。
1. 模具设计问题:模具是注塑过程中至关重要的部分,如果设计不合理,就会导致一系列问题。
常见的问题包括产品尺寸偏差大、表面粗糙、开裂等。
解决办法是优化模具的进料系统和冷却系统,确保充填均匀,并增加冷却时间和加热时间。
2. 注塑机参数调节不当:注塑机的温度、压力和速度等参数设置不当,会导致产品质量问题。
例如,温度过高或过低会导致材料熔化不完全或固化不充分;压力过高或过低会影响产品的密度和强度。
注塑成型常见问题及解决方法

注塑成型常见问题及解决方法:注射模塑缺点和反常现象最终集中在注塑制品的质量上反映出来。
注塑制品缺点可分成下列几点:(1)产品注射不足;(2)产品溢边;(3)产品凹痕和气泡;(4)产品有接痕;(5)产品发脆;(6)塑料变色;(7)产品有银丝、斑纹和流痕;(8)产品浇口处混浊;(9)产品翘曲和收缩;(10)产品尺寸不准;(11)产品粘贴模内;(12)物料粘贴流道;(13)喷嘴流涎。
下面一一叙述其产生的原因及克服的办法。
1.怎样克服产品注射不足产品注料不足往往由于物料在未充满型腔之前即已固化,当然还有其他多种的原因。
⑴设备原因:①料斗中断料;②料斗缩颈部分或全部堵塞;③加料量不够;④加料控制系统操作不正常;⑤注压机塑化容量太小;⑥设备造成的注射周期反常。
⑵注塑条件原因:①注射压力太低;②在注射周期中注射压力损失太大;③注射时间太短;④注射全压时间太短;⑤注射速率太慢;⑥模腔内料流中断;⑦充模速率不等;⑧操作条件造成的注射周期反常。
⑶温度原因:①提高料筒温度;②提高喷嘴温度;③检查毫伏计、热电偶、电阻电热圈(或远红外加热装置)和加热系统;④提高模温;⑤检查模温控制装置。
⑷模具原因①流道太小;②浇口太小;③喷嘴孔太小;④浇口位置不合理;⑤浇口数不足;⑥冷料穴太小;⑦排气不足;⑧模具造成的注射周期反常;⑸物料原因:物料流动性太差。
2.怎样克服产品飞边溢料:产品溢边往往由于模子的缺陷造成,其他原因有:注射力大于锁模力、物料温度太高、排气不足、加料过量、模子上沾有异物等。
⑴模具问题:①型腔和型芯未闭紧;②型腔和型芯偏移;③模板不平行;④模板变形;⑤模子平面落入异物;⑥排气不足;⑦排气孔太大;⑧模具造成的注射周期反常。
⑵设备问题:①制品的投影面积超过了注压机的最大注射面积;②注压机模板安装调节不正确;③模具安装不正确;④锁模力不能保持恒定;⑤注压机模板不平行;⑥拉杆变形不均;⑦设备造成的注射周期反常⑶注塑条件问题:①锁模力太低;②注射压力太大;③注射时间太长;④注射全压力时间太长;⑤注射速率太快;⑥充模速率不等;⑦模腔内料流中断;⑧加料量控制太大;⑨操作条件造成的注射周期反常。
注塑制品容易出现的品质缺陷成因分析及解决方法

注塑制品品质缺陷成因分析与解决方法注塑成型技术系统培训教材SANSEI精密注塑成形欠注(缺胶):形成原因及解决办法1.设备选型不当。
选用注射量适当的注塑机。
塑件重量一般为理论注射量的85%以下。
2.熔胶料量不足。
给足够的熔融塑料。
(加大熔胶量)。
3.料斗下料不充分。
检查料的颗粒大小,使用颗粒均匀的原料。
4.原料的流动性太差。
检查水口料量的比例多少,添加增塑助剂。
或更换流动性好的材料。
5.冷料杂质堵塞流道。
清理喷咀,加大唧咀直径,加大冷料井或流道截面。
6.浇注系统设计不合理。
多腔模具浇道不平衡,浇口大小不一致,流道细小而长。
改良流道设计。
7.模具排气不良。
加强模具排气。
在模具上开排气孔或0.02-0.04MM,宽度为5-10MM的槽在最终充模处。
8.模具温度太低。
节制模内冷却流量,提高模具温度或使用模温机。
9.熔料温度太低。
料筒温度太低使塑料流动性差,应适量提高温度设定。
检查发热圈是否正常发热。
10.喷咀温度太低。
喷咀温度太低致射出熔料时阻力增大,压力损失大,检查发热圈是否正常发热。
模具冷料穴小或没有时冷料堵塞,故应提高喷咀温度。
11.注射压力不足。
适当提高注射压力。
12.注射及保压时间不足。
适当延长注射时间。
厚壁制件需较长的保压时间。
13.保压压力不足。
适当提高保压压力。
14.注射速度太慢或太快。
注射速度太慢制品难以充填,太快可能模具排气不良. 同时太慢可能使制品出现流纹,太快使制品出现熔体破裂而形成银纹。
15.注射设定位置不合理。
对于壁厚薄不一致的制品,注射时分段设定的切换位置不合理及压力速度不协调时,会造成壁薄位置难以充填,壁厚部分承受过大注射压力形成披锋。
16.模具结构设计不合理。
制件壁薄,投影面积大,或制件壁厚薄极不均匀。
薄壁时太薄使之难以充填。
改变其结构壁厚。
17.背压太低。
对于发泡性材料或某些干燥不充分的成形材料,有背压太低也会导致欠注现象发生,故调较应有适量背压。
18.机器螺杆磨损。
注塑常见不良原因和改善对策

注塑常见不良原因和改善对策注塑是一种常见的塑料制造技术,广泛应用于各个行业中。
然而,在注塑过程中,常常会出现一些不良现象,其中包括缺陷、变形、色差等问题。
本文将介绍注塑常见的不良原因,并提出相应的改善对策。
首先,缺陷是注塑过程中最常见的不良现象之一、缺陷可能是由于模具或注塑机的设计不合理导致的,也可能是由于操作人员的疏忽或技术不足造成的。
另外,材料的选择和质量也会影响缺陷的产生。
为了改善缺陷问题,我们可以采取以下对策:1.优化模具设计:对模具进行合理的设计和优化,确保注塑产品的几何尺寸、表面质量和力学性能符合要求。
另外,采用一些特殊的模具结构,如针阀模具、气动顶出模具等,可以进一步减少缺陷的产生。
2.提升操作技术:培训操作人员,提高其注塑技术水平和操作技能,确保注塑过程的稳定性和一致性。
另外,建立严格的操作规程和品质控制流程,规范操作行为,减少人为因素的影响。
3.加强材料质量控制:选择优质的注塑原料,定期对原料进行检验和筛查,确保其符合产品要求。
另外,在注塑过程中,通过控制注射速度、温度和压力等参数,有效控制材料的熔融和流动,减少缺陷的产生。
其次,变形是另一个常见的注塑不良现象。
变形可能是由于材料的热胀冷缩引起的,也可能是由于模具设计不合理或注塑工艺参数设置不当导致的。
为了减少变形问题,我们可以采取以下对策:1.优化模具设计:改善模具的冷却系统,通过增加冷却道的数量和位置,提高材料的冷却速度,减少变形的产生。
此外,采用一些特殊的模具结构,如加厚或加固构件,可以增加产品的刚度,防止变形的发生。
2.优化注塑工艺:通过调整注射速度、温度和压力等参数,控制材料的熔融和流动,减少热胀冷缩引起的变形。
另外,选择合适的注塑工艺,如预热模具或采用热流道系统等,可以进一步减少变形的产生。
最后,色差是注塑过程中常见的外观缺陷之一、色差可能是由于原料的质量问题导致的,也可能是由于注塑工艺参数设置不当或模具表面处理不良造成的。
TPR.TPR注塑成型制品易出现缺陷,原因,解决全方案

TPR/TPE注塑成型制品易出现缺陷,原因,解决方案1. TPR/TPE等注塑成型的制品易出现飞边注塑零件飞边又称溢边或者披锋,大多发生在模具上模块相结合的位置。
如:分型面、顶针的孔隙、滑块的配合部位、镶件的缝隙、顶针的孔隙等处。
飞边不及时修正可能会影响产品外观或影响充模过程中的排气;若飞边过大,脱模过程中产生的碎屑可能会残留在模具内部,导致产品出现冷料,严重的还会使模具产生永久性压痕,如果碎屑残留在运动部件,如滑块、顶针等处,还可能导致模具运动不畅。
第一、设备方面(1)成型机合模力不足。
如果成型机的额定合模力小与成型过程中制品从像投影面积上的张力,将会导致分型面间隙,造成飞边。
TPR/TPE注塑缺陷问题解决方案:增大锁模力(2)成型机合模形成不足。
如果成型机合模的最小间隙大于模具的厚度,制品的投影面积超过了注压机的最大注射面积,注压机模板安装调节不正确,模具安装不正确,锁模力不能保持恒定,注压机模板不平行,拉杆变形不均将会导致模具合模不紧密造成飞边。
TPR/TPE注塑缺陷问题解决方案:改进注塑机缺陷第二、模具方面(1)模具本身精度差,如分型面配合不严密;分型面有压痕或疲劳塌陷;分型面间隙过大;TPR/TPE注塑缺陷问题解决方案:改进模具设计(2) 设计不合理,如型腔分布不对称,导致成型时张力不均容易产生分型面飞边;顶出机构不对称,导致顶出时顶针受到扭力,也会产生飞边;排气间隙过大;型腔和型芯对插结构过多;型腔和型芯偏移;模板不平行;模板变形;模子平面落入异物;排气不足;排气孔太大;第三、工艺方面(1) 注射压力过高或速度过快,产生高速高压熔体,导致模具接合部位出现弹性变形,从而产生飞边。
TPR/TPE注塑缺陷问题解决方案:降低注塑速度(2) 温度过高:无论是料筒温度、喷嘴温度还使模具温度过高,都将使塑料熔体黏度下降,流动性增强从而在模块接合部位产生飞边。
TPR/TPE注塑缺陷问题解决方案:降低温度(3)计量过大,会使模具内产生局部高压,如果发生在模块接合部位,将产生飞边。
TPE材料加工常见问题及解决方法
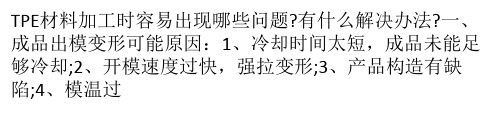
头温度;降低螺杆转速;2、调整限料装置。十三、挤出时 产生大量气体可能原因:1、融体温度过高;2、料管内有 杂物。解决方法:1、降低融体温度;2、清理料管。十四、 挤出成品有凹
点可能原因:1、原料含有水分;2、融体温度过高,螺杆 转速过快。解决方法:1、烘料;2、降低融体温度及螺杆 转速。
skfjejwn 原油返佣网 原油返佣是什么 原油返佣高 百利原油返佣网/
;3、降低射速及料温;4、清理模具。四、充模不足可能原 因:1、射压不足,射速太慢;2、成型温度过低,流道太 小;3、模腔内空气不能完全排出;4、射出时间太短及射出 量不足。解
Hale Waihona Puke 决方法:1、提高射压,射速;2、提高成型温度,修改流 道;3、增设排气孔;4、延长射出时间增加射出量。五、结 合线可能原因:1、射压不足,射速太慢,浇口及流道太 小;2、成型温
TPE材料加工时容易出现哪些问题?有什么解决办法?一、 成品出模变形可能原因:1、冷却时间太短,成品未能足 够冷却;2、开模速度过快,强拉变形;3、产品构造有缺 陷;4、模温过
高,成品冷却不到位。解决方法:1、延长冷却时间;2、 减缓开模速度;3、修改模具;4、降低模温。二、射纹可能 原因:1、射速过快,模腔内空气无法瞬间排出;2、原料 含有水分;3
状可能原因:1、料管未清理干净,有杂物;2、添加物如 色母的载体未按要求。解决方法:1、清理料管;2、找出 相应的色母。十一、挤出量不够可能原因:1、料管温度 不够;2、模口有
杂物或螺杆速率过低。解决方法:1、提高模头;2、清理 模口或提高螺杆转速。十二、挤出成品出模膨胀可能原 因:1、模头温度过低或螺杆转速过快;2、限料过快。解 决方法:1、提高模
度,提高背压或加快螺杆转速。八、成品出模破裂可能 原因:1、料温过低或模温过低;2、脱模斜度不够或顶出 方式不当;3、浇口太小;4、脱模角不足。解决方法:1、 提高温度;2、修
注射成型常见故障的产生原因及排除方法

注射成型常见故障的产生原因及排除方法一、欠注故障分析及排除方法:1.设备选型不当在选用注射设备时,注射机的最大注射量必须大于塑件重量,在验核时,注射总量(包括塑件、浇道和飞边)不能超出注射机塑化量的85%。
2.供料不足目前常用的控制加料的办法是定体积加料法,其加料量与原料的颗粒形状、加料口温度及背压等因素有关。
当出现欠注时,应检查原料粒径是否均一,加料口底部有无“架桥”现象。
若加料口处温度过高,也会引起落料不畅。
对此,应疏通和冷却加料口。
如果注射机塑化行程尚有剩余,可适当加大注射行程,增加供料量,检查止回阀位置是否适当。
3.原料流动性能太差原料的熔体流动性能太差时,模具的结构参数是影响欠注的主要原因。
因此,应设法改善模具浇注系统的滞流缺陷,如合理设置浇道位置、扩大浇口、流道和注料口尺寸以及采用较大的喷嘴等。
同时,可在原料配方中增加适量助剂,改善树脂的流动性能。
此外,还应检查原料中再生料是否超量,适当减少其用量。
4.润滑剂超量如果原料配方中润滑剂用量太多,且螺杆、杆与料筒磨损间隙较大时,熔料在料筒中回流严重会引起供料不足,导致欠注。
对此,应减少润滑剂用量及调整料筒与螺杆间隙,修复设备。
5.冷料杂质阻塞料道当熔料内的杂质堵塞喷嘴或冷料阻塞浇口及流道时,应将喷嘴拆卸清理或扩大模具冷料穴和流道截面。
6.浇注系统设计不合理一模多腔时,往往因浇口和浇道平衡设计不合理导致塑件外观缺陷。
设计浇注系统时,要注意浇口平衡,各型腔内塑件的重量要与浇口大小成正比,使各型腔能同时充满,浇口位置要选择在厚壁部位,也可采用分流道平衡布置的设计方案。
若浇口或流道小、薄、长,熔料的压力在流动过程中沿程损失太大,流动受阻,容易产生填充不良。
对此,应扩大流道截面和浇口面积,必要时可采取多点进料的方法。
7.模具排气不良当模具内因排气不良而残留的大量气体受到流料挤压,产生大于注射压力的高压时,就会阻碍熔料充满型腔造成欠注。
对此,应检查有无设置冷料穴或其位置是否正确,对于型腔较深的模具,应在欠注的部位增设排气槽或排气孔;在合模面上,可开设深度为0.02~0.04mm,宽度为5~10mm的排气槽,排气孔应设置在型腔的最终充模处。
TPE注塑常见的问题及处理方法

TPE注塑常见的问题及处理方法注塑前需要清洗料筒新购进的注塑机初用之前,或者在生产中需要改变产品、更换原料、调换颜色或发现塑料中有分解现象时,都需要对注塑机机筒进行清洗或拆洗。
清洗机筒一般采用加热机筒清洗法。
清洗料一般用塑料原料(或塑料回收料)。
对于TPR材料,可用所加工的新料置换出过渡清洗料。
TPR的成型温度在加工注塑过程中,温度的设定是否准确是制品外观和性能好坏的关键。
下面是进行TPR加工注塑时温度设定的一些建议。
进料区域的温度应设定得相当低,以避免进料口堵塞并让夹带的空气逸出。
当使用色母料时为了改善混合状态,应将过渡区域的温度设定在色母料的熔点以上。
离注塑喷嘴近区域的温度应该设定得接近于所需的熔体温度。
所以,经过测试,通常TPR产品在各个区域温度的设定范围分别是:料筒为160摄氏度到210摄氏度,喷嘴为180摄氏度到230摄氏度。
模具温度应该设定高与注塑区的冷凝温度,这将能避免水分对模具的污染以致制品表面出现的条纹。
较高的模具温度通常会导致较长的循环周期,但它能改进焊接线和制品的外观效果,所以,模具温度的范围应设计定在30到40之间。
注塑工艺条件的影响1塑料成型不完整(1)进料调节不当,缺料或多料。
(2)注射压力太低,注射时间短,柱塞或螺杆退回太早。
(3)注射速度慢。
(4)料温过低。
2溢料(飞边)(1)注射压力过高或注射速度过快。
(2)加料量过大造成飞边。
(3)机筒、喷嘴温度太高或模具温度太高都会使塑料黏度下降,流动性增大,在流畅进模的情况下造成飞边3银纹、气泡和气孔(1)料温太高,造成分解(2)注射压力小,保压时间短,使熔料与型腔表面不密贴。
(3)注射速度太快,使熔融塑料受大剪切作用而分解,产生分解气;注射速度太慢,不能及时充满型腔造成制品表面密度不足产生银纹。
(4)料量不足、加料缓冲垫过大、料温太低或模温太低都会影响熔料的流动和成型压力,产生气泡。
(5)螺杆预塑时背压太低、转速太高,使螺杆退回太快,空气容易随料一起推向机筒前端。
注塑成型制品易出现缺陷原因解决全方案
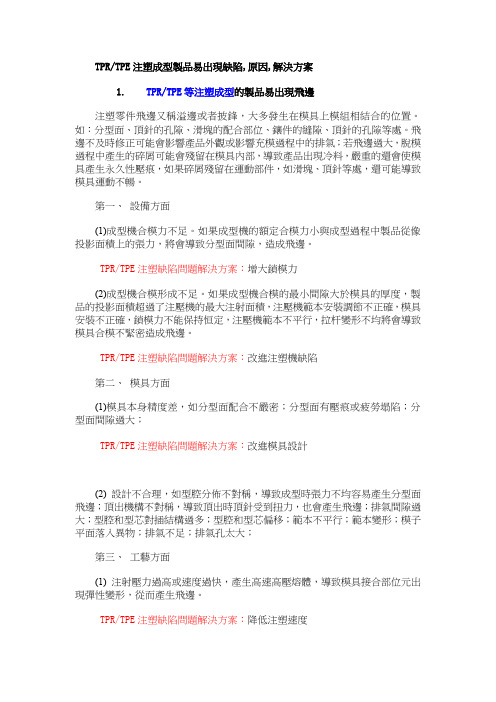
TPR/TPE注塑成型製品易出現缺陷,原因,解決方案1.TPR/TPE等注塑成型的製品易出現飛邊注塑零件飛邊又稱溢邊或者披鋒,大多發生在模具上模組相結合的位置。
如:分型面、頂針的孔隙、滑塊的配合部位、鑲件的縫隙、頂針的孔隙等處。
飛邊不及時修正可能會影響產品外觀或影響充模過程中的排氣;若飛邊過大,脫模過程中產生的碎屑可能會殘留在模具內部,導致產品出現冷料,嚴重的還會使模具產生永久性壓痕,如果碎屑殘留在運動部件,如滑塊、頂針等處,還可能導致模具運動不暢。
第一、設備方面(1)成型機合模力不足。
如果成型機的額定合模力小與成型過程中製品從像投影面積上的張力,將會導致分型面間隙,造成飛邊。
TPR/TPE注塑缺陷問題解決方案:增大鎖模力(2)成型機合模形成不足。
如果成型機合模的最小間隙大於模具的厚度,製品的投影面積超過了注壓機的最大注射面積,注壓機範本安裝調節不正確,模具安裝不正確,鎖模力不能保持恒定,注壓機範本不平行,拉杆變形不均將會導致模具合模不緊密造成飛邊。
TPR/TPE注塑缺陷問題解決方案:改進注塑機缺陷第二、模具方面(1)模具本身精度差,如分型面配合不嚴密;分型面有壓痕或疲勞塌陷;分型面間隙過大;TPR/TPE注塑缺陷問題解決方案:改進模具設計(2) 設計不合理,如型腔分佈不對稱,導致成型時張力不均容易產生分型面飛邊;頂出機構不對稱,導致頂出時頂針受到扭力,也會產生飛邊;排氣間隙過大;型腔和型芯對插結構過多;型腔和型芯偏移;範本不平行;範本變形;模子平面落入異物;排氣不足;排氣孔太大;第三、工藝方面(1) 注射壓力過高或速度過快,產生高速高壓熔體,導致模具接合部位元出現彈性變形,從而產生飛邊。
TPR/TPE注塑缺陷問題解決方案:降低注塑速度(2) 溫度過高:無論是料筒溫度、噴嘴溫度還使模具溫度過高,都將使塑膠熔體黏度下降,流動性增強從而在模組接合部位元產生飛邊。
TPR/TPE注塑缺陷問題解決方案:降低溫度(3)計量過大,會使模具內產生局部高壓,如果發生在模組接合部位元,將產生飛邊。
注射成型塑件常见缺陷问题及改善措施
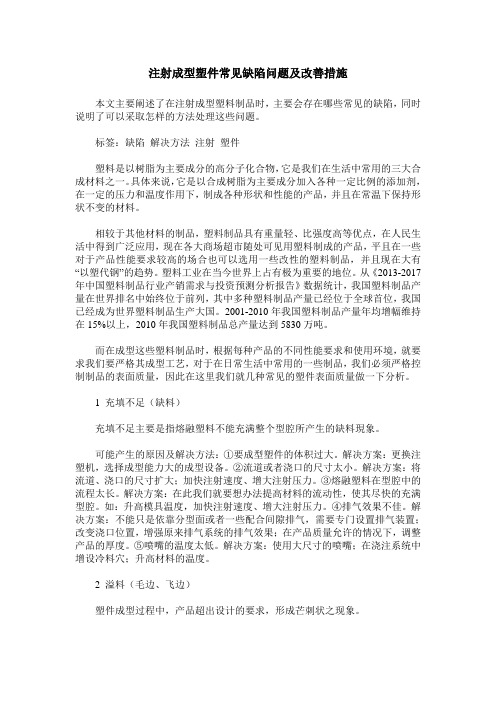
注射成型塑件常见缺陷问题及改善措施本文主要阐述了在注射成型塑料制品时,主要会存在哪些常见的缺陷,同时说明了可以采取怎样的方法处理这些问题。
标签:缺陷解决方法注射塑件塑料是以树脂为主要成分的高分子化合物,它是我们在生活中常用的三大合成材料之一。
具体来说,它是以合成树脂为主要成分加入各种一定比例的添加剂,在一定的压力和温度作用下,制成各种形状和性能的产品,并且在常温下保持形状不变的材料。
相较于其他材料的制品,塑料制品具有重量轻、比强度高等优点,在人民生活中得到广泛应用,现在各大商场超市随处可见用塑料制成的产品,平且在一些对于产品性能要求较高的场合也可以选用一些改性的塑料制品,并且现在大有“以塑代钢”的趋势。
塑料工业在当今世界上占有极为重要的地位。
从《2013-2017年中国塑料制品行业产销需求与投资预测分析报告》数据统计,我国塑料制品产量在世界排名中始终位于前列,其中多种塑料制品产量已经位于全球首位,我国已经成为世界塑料制品生产大国。
2001-2010年我国塑料制品产量年均增幅维持在15%以上,2010年我国塑料制品总产量达到5830万吨。
而在成型这些塑料制品时,根据每种产品的不同性能要求和使用环境,就要求我们要严格其成型工艺,对于在日常生活中常用的一些制品,我们必须严格控制制品的表面质量,因此在这里我们就几种常见的塑件表面质量做一下分析。
1 充填不足(缺料)充填不足主要是指熔融塑料不能充满整个型腔所产生的缺料現象。
可能产生的原因及解决方法:①要成型塑件的体积过大。
解决方案:更换注塑机,选择成型能力大的成型设备。
②流道或者浇口的尺寸太小。
解决方案:将流道、浇口的尺寸扩大;加快注射速度、增大注射压力。
③熔融塑料在型腔中的流程太长。
解决方案:在此我们就要想办法提高材料的流动性,使其尽快的充满型腔。
如:升高模具温度,加快注射速度、增大注射压力。
④排气效果不佳。
解决方案:不能只是依靠分型面或者一些配合间隙排气,需要专门设置排气装置;改变浇口位置,增强原来排气系统的排气效果;在产品质量允许的情况下,调整产品的厚度。
- 1、下载文档前请自行甄别文档内容的完整性,平台不提供额外的编辑、内容补充、找答案等附加服务。
- 2、"仅部分预览"的文档,不可在线预览部分如存在完整性等问题,可反馈申请退款(可完整预览的文档不适用该条件!)。
- 3、如文档侵犯您的权益,请联系客服反馈,我们会尽快为您处理(人工客服工作时间:9:00-18:30)。
10分钟详细了解TPE注塑成型容易出现的问题及解决方法
TPE可以通过多种方法成型,市面上较长见到的有挤出、注塑、模塑等方法,下面详细为大家解答TPE注塑过程中容易出现的问题及解决方法。
注塑成型又称注射模塑成型,它是一种注射兼模塑的成型方法。
注塑成型方法的优点有很多,注塑成型生产速度快、效率高,操作可实现自动化,花色品种多,形状可以由简到繁,尺寸可以由大到小,而且制品尺寸精确,产品易更新换代,能成形状复杂的制件,注塑成型适用于大量生产与形状复杂产品等成型加工领域。
下面是TPE注塑成型中容易出现的问题:
1.出现银色条纹
以注胶口为中心出现放射状条纹的现象,是材料中的水分或挥发成分气化引起的。
其中,在塑化过程中卷入或模具内存留的空气也会导致这一现象的产生。
因此,对吸潮性材料在成型前进行充分地干燥及降低易产生分解性气体材料的成型温度都是非常必要的。
2.注塑出现缺胶
未充满模腔端部的现象称之为缺胶。
这主要是因填胶量不足等成型条件不适而引起的,但成型时排气不充分或流胶道不均衡(多腔模具)也会导致这一现象的产生。
3.注塑产生气孔
在注塑成型品中出现塌陷孔现象,主要是成型品在模具内的冷却过程中因收缩而引起的。
除要求材料必须充满模腔外,快速冷却也是十分必要的。
具体地来讲,就是提高保压(二次压力),降低热塑性弹性体材料加工温度和模具冷却温度。
另外,对注塑成型品的形状也有很大的依赖性。
由于在厚的部位极易出现气孔,所以对这样的制品来说,应采用在其周围设有注胶口或流胶道。
4.注塑产生毛边(飞边)
这是热塑性弹性体材料从模腔溢出造成的。
对橡胶的注射成型来讲,出现毛边是正常的,但对树脂或热塑性弹性体是不正常的。
其理由是:(1)与橡胶胶料相比,熔融的树脂或热塑性弹性体的流动性较高,注射压力也比较低;(2)与模具接触、冷却,在瞬间即可固化、终止流动。
因此,树脂或热塑性弹性体通常是不易出现毛边的现象。
作为对策,首先必须降低填充量、降低保压和缩短保压时间。
另外,对尺寸精度差、分型面有间隙的模具来讲,其修理是非常必要的。