干法除尘技术
干法除尘工安全技术操作规程模版

干法除尘工安全技术操作规程模版第一章总则第一条各单位及工作人员在进行干法除尘工作时,应严格按照本操作规程进行操作,确保操作安全。
第二条干法除尘工作人员必须经过相应的培训合格后方可上岗,且需持有合法操作证书。
第三条干法除尘工作人员应具备一定的技术知识和操作经验,了解除尘设备的工作原理和操作规程。
第四条干法除尘工作人员应严格遵守相关的安全生产法律法规,操作时必须保证人身安全和设备安全。
第二章设备操作第五条干法除尘设备操作前,必须检查设备的各项部件是否完好,确保设备能够正常运行。
第六条进行干法除尘操作时,必须戴好个人防护用品,包括安全帽、防护眼镜、口罩、耳塞等。
第七条在进行干法除尘操作时,必须确保设备与电源正常连接,避免因电气故障引发意外事故。
第八条在操作干法除尘设备过程中,严禁随意触摸设备的运转部件,以免发生危险。
第九条在操作干法除尘设备过程中,必须注意设备周围的通风情况,确保操作环境的安全。
第十条在操作干法除尘设备时,必须按照设备的工作原理和操作规程进行操作,严禁违章操作。
第三章作业流程第十一条进行干法除尘作业前,必须对作业区域进行环境检测,确保作业环境符合要求。
第十二条干法除尘作业前,必须清理作业区域的杂物,确保作业区域整洁无障碍。
第十三条进行干法除尘作业时,必须按照作业计划和操作规程进行作业,严禁擅自改变作业流程。
第十四条干法除尘作业时,必须保持设备运行平稳,严禁随意调整设备参数,以免影响除尘效果。
第十五条干法除尘作业结束后,必须对设备进行及时维护保养,确保设备可以正常使用。
第四章应急措施第十六条在干法除尘作业过程中,如发生设备故障或其他意外情况,必须立即停止作业并采取应急措施。
第十七条干法除尘作业现场必须设置明显的应急出口标志,确保作业人员在发生事故时能够及时疏散。
第十八条干法除尘作业人员必须熟悉本单位的应急预案,能够正确、迅速地处置各类事故。
第五章事故处理第十九条在干法除尘作业中,如发生事故或其他不安全事件,必须立即向上级汇报,并采取措施进行事故处理。
干法除尘的工艺流程及工作原理(精)
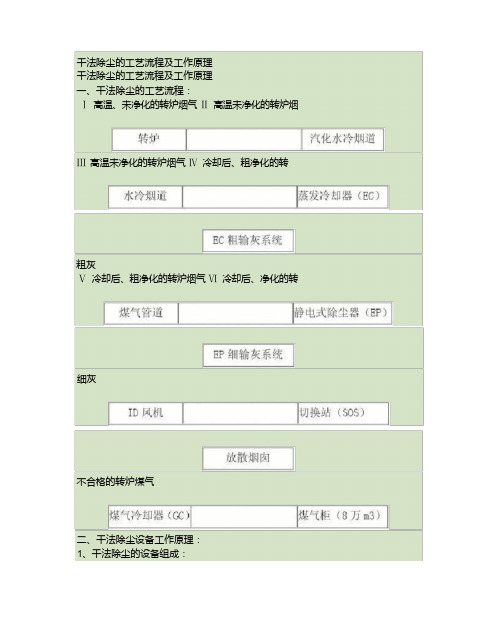
干法除尘的工艺流程及工作原理干法除尘的工艺流程及工作原理一、干法除尘的工艺流程:Ⅰ 高温、未净化的转炉烟气Ⅱ 高温未净化的转炉烟Ⅲ 高温未净化的转炉烟气Ⅳ 冷却后、粗净化的转粗灰Ⅴ 冷却后、粗净化的转炉烟气Ⅵ 冷却后、净化的转细灰不合格的转炉煤气二、干法除尘设备工作原理:1、干法除尘的设备组成:通过对干法除尘设备的功能来看,干法除尘的设备主要分成五大块,分别为转炉烟气的冷却设备(即EC 系统)、转炉烟气的净化设备(即EP 系统)、转炉烟气的动力设备(即ID 风机)、转炉煤气的回收和排放设备(切换站和煤气冷却器)、粉尘排放设备(即EC 粗输灰系统和EP 细输灰系统)。
2、转炉烟气冷却设备(EC 系统)转炉冶炼时,含有大量CO的高温烟气冷却后才干满足干法除尘系统的运行条件。
蒸发冷却器入口的烟气温度为800 ~ 1200C,出口温度的控制应根据静电式除尘器的入口温度而定,普通EC 的出口温度控制在200 ~ 300C,才干达到静电除尘器的要求。
为此,EC 系统采用14 杆喷枪进行转炉烟气的冷却,喷枪通过双流喷嘴对蒸汽和冷却水进行混合,达到冷却水的雾化效果,提高冷却水与气流的接触面积,使得转炉烟气得到良好、均匀的冷却。
喷射水与转炉烟气在运行的过程中,水滴受烟气加热被蒸发,在汽化过程中吸收烟气的热量,从而降低烟气温度。
蒸发冷却器除了冷却烟气外,还可依靠气流的减速以及进口处水滴对烟尘的润湿将粗颗粒的烟尘分离出去,达到一次除尘的目的。
灰尘聚积在蒸发冷却器底部由链式输送机排出。
蒸发冷却器还有对烟气进行调节改善的功能,即在降低气体温度的同时提高其露点,改变粉尘比电阻,有利于在静电除尘器中将粉尘分离出来。
除了烟气冷却和调节以外,占烟气中灰尘总含量约15%的粗灰也在蒸发冷却器中进行采集、排放。
此外,通过对喷射水流量的控制(水调节阀),可控制EC 的出口温度,使之达到静电式除尘器所需要的温度。
3、转炉烟气净化设备(EP 系统)静电除尘器为圆筒形静电除尘器,它是转炉烟气干法除尘系统中的关键除尘设备,其主要技术特点为:①优异的极配形式。
干法除尘工安全技术操作规程

干法除尘工安全技术操作规程第一章总则第一条为保障干法除尘工作的安全进行,规范干法除尘工作操作,防范事故发生,制定本安全技术操作规程。
第二条本安全技术操作规程适用于干法除尘工作的操作人员。
第三条干法除尘工作应遵循安全第一的原则,严格执行本安全技术操作规程,做到安全生产、环境保护、预防为主。
第四条干法除尘工作操作人员应具备相应的操作技能,并接受相应的安全培训。
第五条干法除尘工作操作人员应持有效的操作证件,定期进行健康检查,确保身体健康。
第六条干法除尘工作操作人员应在施工前,对设备进行检查,确保设备处于良好的工作状态。
第七条干法除尘工作操作人员在进行操作前,应对工作区域进行清理,以防降低事故发生的概率。
第八条干法除尘工作操作人员不得在行车道上工作,并按照要求佩戴个人防护装备。
第二章作业前的准备工作第九条干法除尘工作操作人员在进行作业前,应熟悉设备的使用说明书,并根据要求进行设备的调试。
第十条干法除尘工作操作人员应在进行作业前,对工作区域进行清理,包括清理杂物和障碍物,以防影响作业。
第十一条干法除尘工作操作人员应根据施工计划,确定设备的布置位置,并确认设备与其他设备之间的合理距离。
第十二条干法除尘工作操作人员应对设备的电源进行检查,确保电源的稳定。
第十三条干法除尘工作操作人员应根据工作区域的具体情况,选取合适的工作方式和工具。
第十四条干法除尘工作操作人员应对设备进行检查,包括检查设备是否处于正常工作状态,设备各个部分是否完好。
第三章作业中的安全技术操作第十五条干法除尘工作操作人员应按照正常的作业程序,进行作业。
第十六条干法除尘工作操作人员在进行作业前,应按照要求进行个人防护,包括佩戴防护眼镜、防护口罩和防护手套等。
第十七条干法除尘工作操作人员应按照设备的使用说明书进行操作,并注意设备的运行状况,如有异常情况应及时停机。
第十八条干法除尘工作操作人员应注意作业区域的通风情况,确保空气流通畅通,以防气体中毒。
干法除尘工艺流程及功能介绍
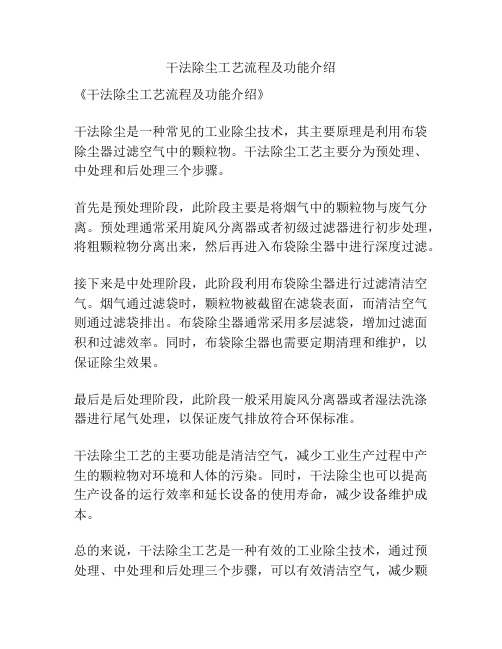
干法除尘工艺流程及功能介绍
《干法除尘工艺流程及功能介绍》
干法除尘是一种常见的工业除尘技术,其主要原理是利用布袋除尘器过滤空气中的颗粒物。
干法除尘工艺主要分为预处理、中处理和后处理三个步骤。
首先是预处理阶段,此阶段主要是将烟气中的颗粒物与废气分离。
预处理通常采用旋风分离器或者初级过滤器进行初步处理,将粗颗粒物分离出来,然后再进入布袋除尘器中进行深度过滤。
接下来是中处理阶段,此阶段利用布袋除尘器进行过滤清洁空气。
烟气通过滤袋时,颗粒物被截留在滤袋表面,而清洁空气则通过滤袋排出。
布袋除尘器通常采用多层滤袋,增加过滤面积和过滤效率。
同时,布袋除尘器也需要定期清理和维护,以保证除尘效果。
最后是后处理阶段,此阶段一般采用旋风分离器或者湿法洗涤器进行尾气处理,以保证废气排放符合环保标准。
干法除尘工艺的主要功能是清洁空气,减少工业生产过程中产生的颗粒物对环境和人体的污染。
同时,干法除尘也可以提高生产设备的运行效率和延长设备的使用寿命,减少设备维护成本。
总的来说,干法除尘工艺是一种有效的工业除尘技术,通过预处理、中处理和后处理三个步骤,可以有效清洁空气,减少颗
粒物对环境和设备的影响,是目前工业领域常用的除尘技术之一。
干式除尘原理

干式除尘原理干式除尘是一种常见的工业除尘方式,它通过物理方法将粉尘颗粒从气体中分离出来,从而净化气体。
干式除尘原理主要包括离心力、惯性力、重力沉降和静电作用等多种物理机制。
下面将详细介绍这些原理及其作用。
首先,离心力是干式除尘中起着重要作用的一种力。
当含有粉尘的气体通过旋转设备时,由于离心力的作用,粉尘颗粒会沿着旋转方向迅速移动,从而被分离出来。
这种原理主要适用于粒径较大的粉尘颗粒。
其次,惯性力也是干式除尘中的重要原理之一。
当气体流经弯曲管道或旋转设备时,由于惯性力的作用,粉尘颗粒会受到惯性力的影响而偏离气流方向,最终被分离出来。
惯性力主要适用于粒径较小的粉尘颗粒。
重力沉降是干式除尘中最常见的原理之一。
根据粉尘颗粒的密度和大小不同,通过设置合适的沉降室或沉降器,粉尘颗粒在气流中会因重力作用而沉降下来,从而实现除尘效果。
静电作用也是干式除尘中的重要原理之一。
通过在除尘设备内部设置静电场,可以使粉尘颗粒带上静电荷,从而与带有相反电荷的集尘板或集尘袋发生静电吸附,达到除尘的效果。
除了以上几种主要原理外,干式除尘还可以通过筛分、过滤等方式将粉尘颗粒从气体中分离出来。
筛分通过设置不同孔径的筛网,使粉尘颗粒在气流中被筛除;过滤则是通过设置过滤材料,使气体通过过滤材料时,粉尘颗粒被截留在过滤材料上。
综上所述,干式除尘原理主要包括离心力、惯性力、重力沉降、静电作用、筛分和过滤等多种物理机制。
这些原理相互作用,共同发挥作用,最终实现对气体中粉尘颗粒的有效分离和除尘,从而达到净化气体的目的。
在工业生产中,合理应用干式除尘原理,可以有效改善生产环境,保护工人健康,实现清洁生产。
干法除尘工安全技术操作规程模版

干法除尘工安全技术操作规程模版一、工作概述本操作规程适用于XX公司干法除尘工作的安全技术操作,目的是确保操作人员在进行干法除尘工作时能够遵守相关安全规定,保证工作的安全进行。
二、安全准备1. 操作人员在进行干法除尘工作前必须穿戴好相应的个人防护装备,包括防护服、安全帽、护目镜、防尘口罩、耐酸碱手套等,确保自身的安全。
2. 对工作现场进行安全检查,确保设备完好无损,没有任何安全隐患。
如发现异常情况,应立即上报相关负责人,由专业人员进行排除故障。
3. 确保所需工艺设备已经得到良好的维护和保养,使用前进行检查,并按照操作手册上的操作步骤进行操作。
三、操作流程1. 开始工作前,操作人员应仔细阅读相关操作手册,了解干法除尘工作的基本原理和操作流程。
2. 在工作开始前,确保干法除尘设备处于停机状态,并对控制柜和电源进行断电处理,以免发生触电事故。
3. 操作人员应使用干净的工具和设备进行工作,避免引入任何杂质和污染物。
4. 当进行设备检修和维护时,操作人员应使用专用工具,绝不允许使用金属工具接触电气设备内部,以免引发电弧故障。
5. 在操作过程中,操作人员应按照相关安全规定进行操作,并根据情况随时调整操作方式。
如发现设备异常,应及时报告,并由专业人员进行处理。
6. 在操作过程中尽量减少设备的开启和关闭次数,以避免设备运行不稳定导致的操作风险。
7. 操作人员应时刻注意自身的安全,避免被尘埃和粉尘触及眼睛、口鼻等部位,必要时应及时更换防尘口罩。
8. 完成工作后,操作人员应对工作现场进行清理,确保不留下任何杂物和污染物。
四、安全预防措施1. 操作人员在进行干法除尘工作前应接受相应的培训,熟悉操作规程和相关安全知识,提高自身的安全意识和应急处理能力。
2. 所有设备必须经过定期的维护和保养,确保设备处于良好的工作状态。
3. 在进行维护和检修操作时,必须先停机,并在断电情况下进行,确保操作人员的人身安全。
4. 严禁擅自更改设备操作参数,如需要进行修改,必须由专业人员进行,并经过相关负责人审批。
干法除尘的工艺流程及工作原理(精)(精选五篇)

干法除尘的工艺流程及工作原理(精)(精选五篇)第一篇:干法除尘的工艺流程及工作原理(精)干法除尘的工艺流程及工作原理干法除尘的工艺流程及工作原理一、干法除尘的工艺流程:Ⅰ 高温、未净化的转炉烟气Ⅱ 高温未净化的转炉烟Ⅲ 高温未净化的转炉烟气Ⅳ 冷却后、粗净化的转粗灰Ⅴ 冷却后、粗净化的转炉烟气Ⅵ 冷却后、净化的转细灰不合格的转炉煤气二、干法除尘设备工作原理:1、干法除尘的设备组成:通过对干法除尘设备的功能来看,干法除尘的设备主要分成五大块,分别为转炉烟气的冷却设备(即EC系统)、转炉烟气的净化设备(即EP系统)、转炉烟气的动力设备(即ID风机)、转炉煤气的回收和排放设备(切换站和煤气冷却器)、粉尘排放设备(即EC粗输灰系统和EP细输灰系统)。
2、转炉烟气冷却设备(EC系统)转炉冶炼时,含有大量CO的高温烟气冷却后才能满足干法除尘系统的运行条件。
蒸发冷却器入口的烟气温度为800~1200C,出口温度的控制应根据静电式除尘器的入口温度而定,一般EC的出口温度控制在200~300C,才能达到静电除尘器的要求。
为此,EC系统采用14杆喷枪进行转炉烟气的冷却,喷枪通过双流喷嘴对蒸汽和冷却水进行混合,达到冷却水的雾化效果,提高冷却水与气流的接触面积,使得转炉烟气得到良好、均匀的冷却。
喷射水与转炉烟气在运行的过程中,水滴受烟气加热被蒸发,在汽化过程中吸收烟气的热量,从而降低烟气温度。
蒸发冷却器除了冷却烟气外,还可依靠气流的减速以及进口处水滴对烟尘的润湿将粗颗粒的烟尘分离出去,达到一次除尘的目的。
灰尘聚积在蒸发冷却器底部由链式输送机排出。
蒸发冷却器还有对烟气进行调节改善的功能,即在降低气体温度的同时提高其露点,改变粉尘比电阻,有利于在静电除尘器中将粉尘分离出来。
除了烟气冷却和调节以外,占烟气中灰尘总含量约15%的粗灰也在蒸发冷却器中进行收集、排放。
另外,通过对喷射水流量的控制(水调节阀),可控制EC的出口温度,使之达到静电式除尘器所需要的温度。
干法除尘技术123.ppt

干法除尘与湿法除尘的效益比较分析
210t转炉干法除尘 序号 项目 吨钢费 用(元) 全年费用 (万元) 210t转炉湿法除尘 吨钢 耗量 吨钢 费用 (元) 0.54 全年费 (万元) 干法与湿法 比较(万元)
吨钢耗量
1
备件(折旧 费4%计)
0.74
-180
-132
-48
2
水耗(m3)
0.05
0.25
阀 极线 极板
高压变 压器、 绝缘子、 加热器
四、转炉干法除尘的主要设备构成、功能
3)内部刮灰和振打 两套刮板机:是专门极板振打 装置 为圆形电除尘器开发研 制的,AB、CD电场各一 套。 振打系统:入口分布 扇形挂灰 器 板振打;出口分布板振 打;阴极线振打;阳极 板振打。
链式刮灰 装置 吊挂 装置
四、转炉干法除尘的主要设备构成、功能
3)粗粉尘捕集系统 蒸发冷却器内部捕集 的大颗粒粉尘集中到 下部,由链式刮灰输送 机输送到外部的灰仓。 包括链条、紧急卸灰阀 和插板阀等构成。见图)
四、转炉干法除尘的主要设备构成、功能
2、电除尘器 电除尘器由1)电除尘器本体;2)四个高压电 场;3)内部刮灰和振打;4)细粉尘捕集系统;5) 卸爆阀。
二、转炉干法除尘与湿法的比较
粉尘利用率高 干法除尘系统吨钢粉尘回收量可达到20-25kg/吨钢 全部可以通过罐车直接送烧结厂重复利用。
占地面积少 干法除尘系统设备之间的配置灵活简单,而且占地面 积少,整个占地约为湿法的1/2,可节省征地费用。
二、转炉干法除尘与湿法的比较 2、效益比较
以包钢薄板厂 210 吨转炉数据统计的对比表(见下页 表) 从表中可以看出,干法系统较湿法系统仅在节省运 行费用和多回收煤气方面,每年效益就达到1200多万元。 该表未统计节约征地费用与多回收粉尘中含铁量成 本。
干法除尘工安全技术操作规程

干法除尘工安全技术操作规程一、前言干法除尘工作是指利用物理方法去除工业生产过程中产生的粉尘污染。
为了确保干法除尘工作的安全性,特制定本操作规程,以指导操作人员进行安全操作。
二、操作人员要求1. 操作人员必须经过相关培训,掌握干法除尘工作的基本原理、操作流程和安全规范。
2. 操作人员必须具备良好的身体健康状况,不得有残疾、眩晕等不适宜从事此项工作的疾病。
3. 操作人员必须佩戴个人防护装备,包括防尘口罩、防护眼镜、防护服等。
4. 操作人员必须定期进行体检,确保身体健康状态。
三、设备及工具检查1. 操作人员在开始工作之前,必须对干法除尘设备及配套工具进行检查,确保设备及工具完好无损。
2. 发现设备及工具有缺陷或损坏的情况,应立即上报并修复或更换。
3. 检查设备及工具时,应切断电源,避免意外触电风险。
四、操作流程1. 在进行干法除尘操作前,必须确保工作区域内无可燃材料和易燃气体。
2. 操作人员在开始操作前,应佩戴个人防护装备,并确保周围环境通风良好。
3. 操作人员应根据工作现场情况选择合适的除尘工艺和工具。
4. 操作人员在操作过程中,应严格按照操作流程进行,不得擅自更改设备参数或操作步骤。
5. 操作人员在操作过程中,应注意安全距离,避免设备运转时被卷入或碰伤。
五、安全预防措施1. 操作人员在进行干法除尘操作时,应避免短路、过载等电气故障,确保设备工作正常。
2. 操作人员应注意操作过程中的火源和静电积聚,避免引发火灾或爆炸。
3. 操作人员应定期清理除尘设备,防止积尘堆积引发事故。
4. 操作人员应注意设备操作温度的监控,避免因温度过高造成设备损坏或安全隐患。
5. 操作人员应妥善保管好操作工具,避免被他人非法使用。
六、事故处理1. 发生事故时,操作人员应立即停止操作,采取紧急救援措施。
2. 发生火灾时,应迅速切断电源,并使用灭火器等器材进行灭火。
3. 发生人员伤害事故时,应及时拨打急救电话或进行紧急救治。
七、操作记录与汇报1. 每次干法除尘操作结束后,操作人员应做好操作记录,包括操作时间、操作流程、设备工作情况等内容。
干法除尘工安全技术操作规程范文

干法除尘工安全技术操作规程范文一、概述干法除尘工是一种常见的工业粉尘处理工艺,其作用是通过粉尘的湿化和捕捉,将空气中的固体颗粒物去除。
为了确保干法除尘工作的安全和高效进行,制定以下安全技术操作规程。
二、操作前准备1. 检查干法除尘设备的工作状态,确保设备正常运行。
2. 检查设备周围的安全环境,确保没有易燃、易爆物品存在。
3. 穿戴个人防护装备,包括头盔、防护眼镜、防护口罩、防护手套等。
三、操作流程1. 根据工作需求,启动干法除尘设备,并确保设备处于正常工作状态。
2. 调整干法除尘设备的湿化参数,确保粉尘能够被湿化并捕捉。
3. 定期监测干法除尘设备的运行情况,包括设备的工作温度、湿化效果等,及时进行调整和维护。
4. 定期清理干法除尘设备的滤袋,确保其正常工作。
5. 严禁在设备运行期间进行维修和更换零部件,必要时需要停机并采取相应安全措施。
6. 在干法除尘设备工作期间,严格控制粉尘的扬尘源,采取封闭操作和湿法作业等措施,防止二次污染和粉尘爆炸。
四、应急措施1. 在发生设备故障或事故时,及时停机,并采取相应安全措施,防止事故扩大。
2. 在发生粉尘爆炸或火灾时,立即启动灭火器材进行灭火,并报警求助。
3. 在发生人员伤害事故时,立即停止工作,向上级报告,并及时进行紧急救援。
五、安全管理要求1. 学习和掌握干法除尘工的操作技术和安全知识,定期进行安全培训和考核。
2. 严格遵守操作规程,不得违章操作,确保自身和他人的安全。
3. 配备完善的应急救援设备和器材,定期检查和维护。
4. 定期进行设备的维护和检修,确保其可靠运行。
5. 建立健全的安全管理制度,包括安全奖惩制度和安全监督机制等。
六、操作注意事项1. 在操作过程中,严禁将手或其他物品伸入干法除尘设备,以防止意外事故的发生。
2. 注意观察设备运行情况,如有异常情况及时报告上级并采取相应措施。
3. 学习和熟悉设备的操作手册和说明书,正确操作设备。
4. 在操作过程中,保持设备周围的环境整洁,防止杂物堆积。
干法除尘工安全技术操作规程范本

干法除尘工安全技术操作规程范本一、操作准备1. 工作人员应事先进行足够的安全培训和技术操作培训。
2. 在进行任何操作之前,必须佩戴个人防护设备,包括安全帽、耳塞、防护眼镜、防尘口罩和防滑鞋等。
3. 确保工作区域的通风良好,并清理工作区域的杂物和障碍物。
二、设备检查1. 在操作前,对干法除尘设备进行检查,确保设备正常运行。
2. 检查设备电源及连接线路是否正常,防止电器设备故障引发安全问题。
3. 检查设备的旋转部件和传动部件是否正常,及时更换损坏的配件。
4. 检查除尘装置是否存在堵塞情况,及时清理。
三、操作流程1. 在进行操作前,确保设备处于停机状态,并拉下电源总开关。
2. 佩戴好个人防护装备后,按照操作手册的要求,启动设备。
3. 在开启设备后,使用清洁工具将灰尘和杂质清理干净,确保设备正常工作。
4. 操作设备时,应保持注意力集中,不得分心、嬉闹或讲话。
5. 在设备运行中,要时刻关注设备的工作状态,如有异常情况应立即报告上级并采取措施停机检修。
6. 操作完成后,应将设备归位并关闭设备电源,进行设备的维护和保养。
四、操作注意事项1. 禁止在设备运行时随意触摸设备的旋转部件,防止发生伤害事故。
2. 禁止将手指或其他物体伸入设备内部,以免发生夹伤或撞伤事故。
3. 禁止在设备运行时拆卸或更换设备的关键部件,所有维修保养应由专人负责。
4. 禁止在设备周围堆放杂物,保持设备周边的通风和安全通道。
5. 在操作设备时,如遇到紧急情况,应立即停止设备运行,并按照应急预案进行处理。
五、事故处理1. 在发生设备故障、事故或人员受伤时,立即停止设备运行,进行紧急救援。
2. 报告现场负责人,并及时通知公司相关部门,保护现场并进行安全隔离。
3. 根据应急预案进行事故调查、记录和报告,提出事故原因和改进措施。
六、个人防护措施1. 切勿在设备运行过程中解开个人防护装备,以免引发安全事故。
2. 在操作设备过程中,不得将个人防护装备借给其他人使用。
2024年干法除尘工安全技术操作规程
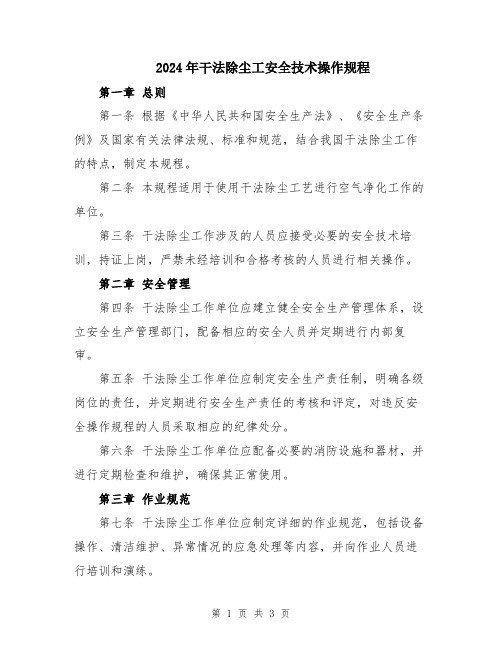
2024年干法除尘工安全技术操作规程第一章总则第一条根据《中华人民共和国安全生产法》、《安全生产条例》及国家有关法律法规、标准和规范,结合我国干法除尘工作的特点,制定本规程。
第二条本规程适用于使用干法除尘工艺进行空气净化工作的单位。
第三条干法除尘工作涉及的人员应接受必要的安全技术培训,持证上岗,严禁未经培训和合格考核的人员进行相关操作。
第二章安全管理第四条干法除尘工作单位应建立健全安全生产管理体系,设立安全生产管理部门,配备相应的安全人员并定期进行内部复审。
第五条干法除尘工作单位应制定安全生产责任制,明确各级岗位的责任,并定期进行安全生产责任的考核和评定,对违反安全操作规程的人员采取相应的纪律处分。
第六条干法除尘工作单位应配备必要的消防设施和器材,并进行定期检查和维护,确保其正常使用。
第三章作业规范第七条干法除尘工作单位应制定详细的作业规范,包括设备操作、清洁维护、异常情况的应急处理等内容,并向作业人员进行培训和演练。
第八条干法除尘设备操作前,应进行全面检查,确保设备的正常运行,并按照作业规范的要求进行操作。
第九条干法除尘设备运行过程中,严禁未经许可私自停机、操作和维护设备。
第十条干法除尘设备的清洁维护应定期进行,清理过程中应停机,并且由具备相关培训和技能的人员进行操作。
第十一条干法除尘设备发生故障时,操作人员应立即采取措施停止设备的运行,并报告相关负责人进行处理。
第四章特殊环境安全防护第十二条干法除尘工作可能存在的特殊环境,如高温、低温、有毒有害物质等,必须严格按照相关标准和规范进行安全防护。
第十三条对于工作环境存在高温、低温情况下的作业人员,应制定相应的防护措施和应急预案,并提供必要的防暑、防寒用具和设备。
第十四条对于工作环境存在有毒有害物质的情况下的作业人员,应进行必要的防护措施,配备必要的个人防护用具,严禁直接接触和吸入有毒有害物质。
第五章废弃物处理第十五条干法除尘工作产生的废弃物和污染物,应按照相关法律法规的要求进行分类、储存、运输和处置,严禁乱倒、乱丢和乱排放。
炼铁厂干法除尘工作原理
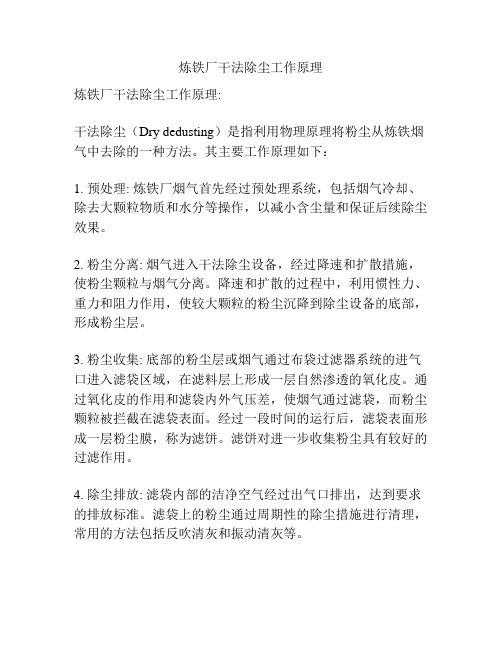
炼铁厂干法除尘工作原理
炼铁厂干法除尘工作原理:
干法除尘(Dry dedusting)是指利用物理原理将粉尘从炼铁烟气中去除的一种方法。
其主要工作原理如下:
1. 预处理: 炼铁厂烟气首先经过预处理系统,包括烟气冷却、除去大颗粒物质和水分等操作,以减小含尘量和保证后续除尘效果。
2. 粉尘分离: 烟气进入干法除尘设备,经过降速和扩散措施,使粉尘颗粒与烟气分离。
降速和扩散的过程中,利用惯性力、重力和阻力作用,使较大颗粒的粉尘沉降到除尘设备的底部,形成粉尘层。
3. 粉尘收集: 底部的粉尘层或烟气通过布袋过滤器系统的进气口进入滤袋区域,在滤料层上形成一层自然渗透的氧化皮。
通过氧化皮的作用和滤袋内外气压差,使烟气通过滤袋,而粉尘颗粒被拦截在滤袋表面。
经过一段时间的运行后,滤袋表面形成一层粉尘膜,称为滤饼。
滤饼对进一步收集粉尘具有较好的过滤作用。
4. 除尘排放: 滤袋内部的洁净空气经过出气口排出,达到要求的排放标准。
滤袋上的粉尘通过周期性的除尘措施进行清理,常用的方法包括反吹清灰和振动清灰等。
通过以上过程,炼铁厂干法除尘设备可以有效地去除烟气中的粉尘,从而达到净化环境和保护员工健康的目的。
干法除尘工安全技术操作规程

干法除尘工安全技术操作规程第一章总则第一条为了确保干法除尘工作的安全和顺利进行,保障操作人员的生命财产安全,制定本规程。
第二条本规程适用于所有从事干法除尘工作的操作人员。
第三条干法除尘工作是指利用各种除尘设备,通过风力或振动等方式将粉尘从气体中分离出来的工作。
第四条操作人员应按照本规程进行工作,并参照相关安全法规、操作规范和标准。
第五条本规程应定期进行检查和修订,以适应工作需要。
第二章职责与权限第六条操作人员的主要职责是根据工艺流程和生产计划,进行干法除尘工作,并保证操作过程的安全和有效。
第七条操作人员应具备必要的操作技能,严格遵守操作规程和操作流程。
第八条操作人员应严格按照作业票的要求进行工作,不得超越自己的权限进行操作。
第九条操作人员对自己的操作行为负责,应及时上报并报告操作中的问题或异常情况。
第三章安全措施第十条操作人员进行干法除尘工作前,应首先进行必要的安全检查,确保设备和工具的运行状态良好,并检查环境是否安全。
第十一条操作人员应按照规定佩戴并正确使用个人防护装备,包括安全帽、防护眼镜、口罩、耳塞等。
第十二条操作人员在工作现场应保持整洁,不得乱堆放杂物,确保通道畅通,减少跌倒和碰撞等安全隐患。
第十三条操作人员在作业期间应严禁吸烟、喧哗和嬉闹,确保作业现场的安静和秩序。
第十四条操作人员在进行设备维护、清洗等操作时,应确保设备电源已切断,防止事故的发生。
第十五条操作人员在进行高处作业时,应使用安全绳或安全防护网,在确保自身安全的前提下进行作业。
第四章应急处理第十六条操作人员在发现危险情况或突发事件时,应立即采取措施进行紧急处理,并及时上报上级领导。
第十七条操作人员应熟悉应急救援设备,如灭火器、防毒面具等,并进行必要的应急演练。
第十八条操作人员在发生火灾、泄漏等事故时,应迅速撤离现场,并按照应急预案进行紧急处理。
第十九条操作人员受伤或发生事故时,应立即寻求医疗救助,并保持现场不动,等待救援人员的到来。
干法除尘工安全技术操作规程

干法除尘工安全技术操作规程前言干法除尘工是一项重要的环保工作,主要用于对工业排放中的灰尘进行去除。
在进行干法除尘操作时,需要遵守一些安全技术操作规程,以保证操作的安全性和高效性。
本文将详细介绍干法除尘工安全技术操作规程,旨在提高操作人员的安全意识和技术水平,确保干法除尘工的正常运行。
工作场所安全环境要求干法除尘工需要在无风、较为封闭的环境中进行,以确保灰尘可以被完全吸收,不影响正常生产和工作。
在进行操作前,需要对工作场所进行必要的安全性检查,确保操作的安全。
安全设施在干法除尘工场所中,需要设立必要的安全设施,包括防爆、防电触及、防火等安全设施,以确保操作人员的身体安全和设备的正常运行。
作业人员素质要求干法除尘工是一项技术比较高的工作,在进行工作时,需要操作人员具备一定的技术素质。
操作人员需要经过专门的培训,并具有相关证书,具体要求如下:•具备一定的机械、化工、电气等方面的知识;•具备一定的电机安装、维护技术;•具备一定的电气设备和控制技术。
工作流程安全设备检查在进行干法除尘工作之前,需要对设备进行必要的检查,确保设备的正常运行。
具体要求如下:•检查一次性飞灰除尘器、刮板输送机、振动筛等设备是否处于良好的工作状态,如有异常情况需要及时处理;•检查电器控制系统的正常运行;•检查风机、电机、进风口、气体出口等设备的密封性和可靠性,并进行必要的维护和加固。
操作流程在进行干法除尘工作时,需要严格按照操作规程进行操作,保证操作的安全性和高效性。
具体流程如下:•在开动设备之前,需要对设备进行预热,以确保设备的正常运行;•操作人员应该进行必要的身体检查,确保身体状况良好,不影响操作;•进行干法除尘作业期间,需要随时关注设备的运行状态,并观察灰尘的排放情况;•在操作结束后,需要对设备进行必要的清理和维护工作,确保下一次操作的顺利进行。
总结干法除尘工是一项重要的环保工作,对于保护人类和环境的健康发挥了重要作用。
为确保干法除尘工的正常运行,避免安全事故的发生,必须加强操作人员的安全意识和技术水平,严格按照干法除尘工安全技术操作规程进行操作,确保操作的安全性和高效性。
干法除尘工安全技术操作规程范本

干法除尘工安全技术操作规程范本安全技术操作规程范本一、目的和范围为保证干法除尘工安全运行,维护工人的身体健康,制定本操作规程。
本规程适用于干法除尘工操作过程中的安全技术管理。
二、责任和义务1. 生产经营单位必须建立健全干法除尘工的安全技术管理制度,并指派负责人负责实施。
2. 干法除尘工操作负责人必须具备相应的技术培训和持证上岗。
3. 操作人员必须严格遵守操作规程,不得违反安全规定,确保本人和他人的安全。
三、干法除尘工操作安全规定1. 操作人员必须穿戴符合个人防护要求的工装,佩戴安全帽、防护眼镜、防护口罩等个人防护用品。
2. 操作前必须对设备进行检查,确保设备完好无损。
3. 操作人员必须按照操作要求进行操作,不得擅自改变设备参数。
4. 操作人员必须掌握设备的安全操作方法,不得违章操作。
5. 遇到设备异常情况,操作人员应立即停机检查,排除故障后方可继续操作。
6. 加装、更换设备配件时必须在设备关机状态下进行,防止发生意外。
四、劳动保护1. 长时间在灰尘环境下工作的人员,应定期进行身体健康检查。
2. 操作人员应注意个人卫生,经常洗手、洗脸,保持身体清洁。
3. 操作人员长时间暴露在灰尘下工作,需定期更换防护用品,如口罩、防护面罩等。
五、事故应急处理1. 发生事故时,操作人员应立即切断设备电源,并向负责人汇报。
2. 发生意外事故时,负责人应及时组织现场救援,并报告相关部门。
六、安全培训和教育1. 生产经营单位应定期开展安全培训和教育,提高操作人员的安全意识。
2. 定期组织安全知识考核,确保操作人员掌握必要的安全知识。
七、违反规定的处理1. 违反安全规定者,由负责人进行批评教育,并记录违规情况。
2. 严重违反安全规定者,负责人有权停止其操作工作,并书面向上级报告。
3. 造成严重事故或伤亡的,依法追究相关责任。
计划如何深入学习干法除尘
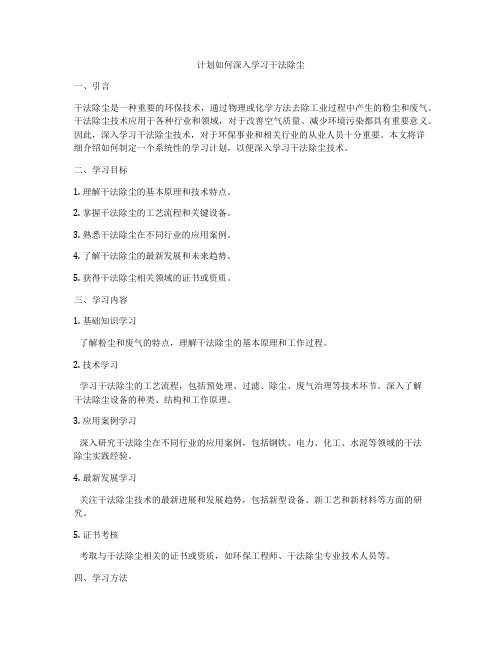
计划如何深入学习干法除尘一、引言干法除尘是一种重要的环保技术,通过物理或化学方法去除工业过程中产生的粉尘和废气。
干法除尘技术应用于各种行业和领域,对于改善空气质量、减少环境污染都具有重要意义。
因此,深入学习干法除尘技术,对于环保事业和相关行业的从业人员十分重要。
本文将详细介绍如何制定一个系统性的学习计划,以便深入学习干法除尘技术。
二、学习目标1. 理解干法除尘的基本原理和技术特点。
2. 掌握干法除尘的工艺流程和关键设备。
3. 熟悉干法除尘在不同行业的应用案例。
4. 了解干法除尘的最新发展和未来趋势。
5. 获得干法除尘相关领域的证书或资质。
三、学习内容1. 基础知识学习了解粉尘和废气的特点,理解干法除尘的基本原理和工作过程。
2. 技术学习学习干法除尘的工艺流程,包括预处理、过滤、除尘、废气治理等技术环节。
深入了解干法除尘设备的种类、结构和工作原理。
3. 应用案例学习深入研究干法除尘在不同行业的应用案例,包括钢铁、电力、化工、水泥等领域的干法除尘实践经验。
4. 最新发展学习关注干法除尘技术的最新进展和发展趋势,包括新型设备、新工艺和新材料等方面的研究。
5. 证书考核考取与干法除尘相关的证书或资质,如环保工程师、干法除尘专业技术人员等。
四、学习方法1. 理论学习通过阅读相关教材、论文和专业书籍,学习干法除尘的理论知识和技术原理。
2. 实践学习参与实际项目,亲身体验干法除尘设备的安装、调试和运行。
通过实践掌握干法除尘技术的实际操作技能。
3. 学习交流参加干法除尘相关的学术会议、研讨会和培训班,与专业人士进行学习交流和经验分享。
4. 自主学习利用互联网资源,参与在线课程、讨论社区和专业论坛,获取最新的干法除尘技术信息。
五、学习计划1. 第一阶段(1-2个月)了解干法除尘的基本原理和技术特点,学习相关的基础理论知识。
2. 第二阶段(3-6个月)深入学习干法除尘的工艺流程和关键设备,掌握干法除尘技术的操作和维护。
干法除尘工安全技术操作规程
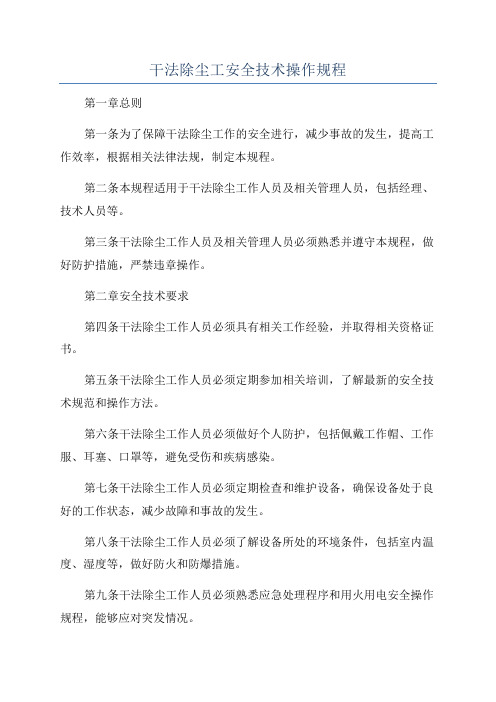
干法除尘工安全技术操作规程第一章总则第一条为了保障干法除尘工作的安全进行,减少事故的发生,提高工作效率,根据相关法律法规,制定本规程。
第二条本规程适用于干法除尘工作人员及相关管理人员,包括经理、技术人员等。
第三条干法除尘工作人员及相关管理人员必须熟悉并遵守本规程,做好防护措施,严禁违章操作。
第二章安全技术要求第四条干法除尘工作人员必须具有相关工作经验,并取得相关资格证书。
第五条干法除尘工作人员必须定期参加相关培训,了解最新的安全技术规范和操作方法。
第六条干法除尘工作人员必须做好个人防护,包括佩戴工作帽、工作服、耳塞、口罩等,避免受伤和疾病感染。
第七条干法除尘工作人员必须定期检查和维护设备,确保设备处于良好的工作状态,减少故障和事故的发生。
第八条干法除尘工作人员必须了解设备所处的环境条件,包括室内温度、湿度等,做好防火和防爆措施。
第九条干法除尘工作人员必须熟悉应急处理程序和用火用电安全操作规程,能够应对突发情况。
第十条干法除尘工作人员必须具备清理污染物的技术方法,避免二次污染和污染物的扩散。
第三章操作规范第十一条干法除尘工作人员在进行工作前,必须对设备进行检查,确保设备处于正常工作状态,准备好相应的工具和材料。
第十二条干法除尘工作人员必须严格按照作业指导书和操作规范进行操作,不得擅自修改操作方法或放松操作要求。
第十三条在进行干法除尘工作前,必须对工作区域进行清洁,避免杂物和垃圾对设备正常运转造成影响。
第十四条在进行干法除尘工作时,必须严格按照操作规程进行操作,操作人员必须全程戴好防护用品,避免受伤和疾病感染。
第十五条在干法除尘工作中,如发生异常情况,操作人员必须立即采取止步措施,并及时报告相关负责人,经批准后再进行处理。
第十六条干法除尘工作完成后,必须对设备进行清理和消毒,确保设备处于良好的工作状态。
第四章突发事故处理第十七条干法除尘工作中如发生火灾、爆炸等突发情况,操作人员必须立即采取相应的紧急措施,确保自身安全和设备的正常运行,同时及时报告相关负责人。
炼钢干法除尘工艺流程

炼钢干法除尘工艺流程嘿,你知道炼钢的时候会产生很多烟尘吧?那这些烟尘可不能就这么放任不管呀,得有个除尘的办法才行呢。
今天呀,我就来给你讲讲炼钢干法除尘工艺流程,这可有趣着呢!我有个朋友叫小李,他就在炼钢厂工作。
有一次我去他们厂参观,就看到了这个干法除尘的设备在运转。
那场面,就像是一场有条不紊的战斗。
先来说说这个干法除尘的第一步,那就是烟气收集。
就好像我们扫地的时候得先用扫帚把灰尘扫到一起一样。
在炼钢的过程中,会产生大量高温的含尘烟气,这些烟气从转炉里出来后,得通过一个管道系统把它们收集起来。
这个管道就像是一个超级大的吸管,把那些带着灰尘的烟气一股脑儿地吸走。
我当时就问小李:“这管道不会被热气烤坏吧?”小李笑着说:“这管道可是特制的呢,能承受高温的。
”接下来,就是冷却环节啦。
收集起来的烟气温度特别高,就像刚从火炉里冒出来的热气一样。
这时候就需要给它降降温,就像我们喝热水的时候要吹一吹让它凉下来一样。
这里采用的是一种特殊的冷却方式,比如说通过一些冷却设备,让烟气的温度快速降下来。
这一步可重要了,如果温度降不下来,后面的除尘工作就不好开展啦。
我又好奇地问小李:“这温度得降到多少才合适呢?”小李回答说:“一般要降到一定的范围,这样才能保证后面设备的正常运行呢。
”再往后呀,就是最关键的除尘部分了。
这就好比是把混在沙子里的小石子挑出来一样。
在干法除尘里,有一种很神奇的设备,叫做静电除尘器。
你可以把它想象成一个超级大的磁铁,不过它吸引的不是铁,而是灰尘颗粒。
当烟气通过这个静电除尘器的时候,灰尘颗粒就会被吸附在电极上,这样干净的气体就和灰尘分离开来啦。
我当时看着那个大大的静电除尘器,就像看到了一个神奇的魔法盒,忍不住感叹:“哇,这么厉害呀!”小李在旁边说:“这还只是一部分呢,后面还有呢。
”经过静电除尘器之后,虽然大部分灰尘已经被除掉了,但是可能还会有一些细小的灰尘残留。
这时候就需要再进行一次过滤,就像我们筛面粉的时候,要多筛几遍才能把面粉筛得更精细一样。
干式除尘原理
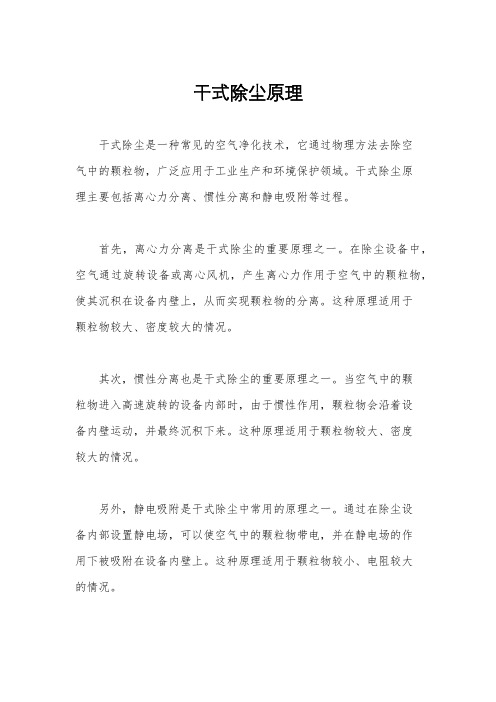
干式除尘原理
干式除尘是一种常见的空气净化技术,它通过物理方法去除空
气中的颗粒物,广泛应用于工业生产和环境保护领域。
干式除尘原
理主要包括离心力分离、惯性分离和静电吸附等过程。
首先,离心力分离是干式除尘的重要原理之一。
在除尘设备中,空气通过旋转设备或离心风机,产生离心力作用于空气中的颗粒物,使其沉积在设备内壁上,从而实现颗粒物的分离。
这种原理适用于
颗粒物较大、密度较大的情况。
其次,惯性分离也是干式除尘的重要原理之一。
当空气中的颗
粒物进入高速旋转的设备内部时,由于惯性作用,颗粒物会沿着设
备内壁运动,并最终沉积下来。
这种原理适用于颗粒物较大、密度
较大的情况。
另外,静电吸附是干式除尘中常用的原理之一。
通过在除尘设
备内部设置静电场,可以使空气中的颗粒物带电,并在静电场的作
用下被吸附在设备内壁上。
这种原理适用于颗粒物较小、电阻较大
的情况。
综上所述,干式除尘原理主要包括离心力分离、惯性分离和静
电吸附等过程。
这些原理通过物理方法有效地去除空气中的颗粒物,达到净化空气的目的。
在实际应用中,可以根据颗粒物的性质和工
作环境的要求,选择合适的干式除尘原理,以实现高效、可靠的除
尘效果。
总的来说,干式除尘原理是一种重要的空气净化技术,通过离
心力分离、惯性分离和静电吸附等原理,可以有效去除空气中的颗
粒物,保障工作环境的清洁和生产设备的正常运行。
希望本文对干
式除尘原理有所帮助,谢谢阅读!。
- 1、下载文档前请自行甄别文档内容的完整性,平台不提供额外的编辑、内容补充、找答案等附加服务。
- 2、"仅部分预览"的文档,不可在线预览部分如存在完整性等问题,可反馈申请退款(可完整预览的文档不适用该条件!)。
- 3、如文档侵犯您的权益,请联系客服反馈,我们会尽快为您处理(人工客服工作时间:9:00-18:30)。
莱钢3#高炉(750 m3)全干式煤气布袋除尘已顺利运行近4年,相比较湿法除尘各项指标效果明显。表2为莱钢3#高炉煤气除尘改造前后的指标对比。
国外应用
据调查,日本在役的大型高炉中,采用了全干法除尘11座、干湿两用的有29座,湿法除尘的有18座。据了解,在日本住友金属工业公司鹿岛厂2# 4800 m3高炉、神户制钢公司加古川厂3# 4500 m3高炉、JFE千叶厂6# 5153 m3高炉均已采用干法除尘。
高炉煤气干法除尘技术优点
更新时间:09-7-31 11:35
高炉煤气干法除尘主要应用技术
更新时间:09-7-30 高炉上的高炉煤气布袋除尘的箱体的直径一般在φ2.6m~φ3.2m之间,个别高炉的箱体的直径做到φ4.0m,在大高炉煤气布袋除尘的箱体基本上采用φ5.2m直径的箱体,在唐钢3200m3高炉上采用了φ6.0m直径的箱体。大直径箱体的应用具有减少投资、节省占地、简化操作等优点,但也带来如下问题:
5)采用气体输送技术,输灰效果好,成本低,且不产生二次污染。
高炉煤气干法除尘工艺流程
更新时间:09-7-30 18:21
目前各高炉采用干式煤气布袋除尘技术的工艺主要有2种:①外滤式脉冲小布袋除尘;②干式煤气布袋除尘。干式煤气布袋除尘采用的是内滤式加压反吹大布袋除尘,该系统在运行中存在对滤袋质量要求较高(目前滤料均为进口) ,系统设备繁多、操作复杂、清灰效果差、反吹时影响高炉顶压等不利因素,后经多年技术改进,现在基本可以满足运行需要,但在全国范围使用较少。而外滤式脉冲小布袋除尘是近几年才发展起来的成熟技术,也是目前国内煤气除尘采用的主流技术,该技术操作简单、除尘效率高、运行稳定安全,图1为该系统工艺。
但是,由于大型高炉煤气发生量多,势必要成倍增加箱体数量,而每个箱体上均有阀门、补偿器、一次仪表等,这使得整个干法除尘器的故障点大量增多,同时占地面积也大大增加。为解决大高炉干法除尘器箱体数量多、可靠性低的缺点,瑞帆企业在干法除尘工艺、设备、关键配套件、输灰系统等方面做了系统深入的研究。通过大量的论证,瑞帆企业对小型高炉干法除尘进行了大量的技术改进,并通过包钢6座高炉、宝钢2500m3、唐钢3200m3高炉干法除尘应用实践证明,在大高炉上采用干法除尘完全是可行的。
6可充分利用煤气显热:净煤气温度比湿法提高约100℃;
7干式TRT可多发电30%以上
8降低焦比,由于干法除尘后的煤气温度较高,供给热风炉后,风温提高50℃以上,可降低焦比;
9环保,由于不需要污水处理系统,可减少污染。
高炉煤气干法除尘原理
更新时间:09-7-30 18:17
1概述
高炉煤气干法布袋除尘装置主要由除尘器箱体(净煤气室、荒煤气室、灰斗组成,荒煤气室、净煤气室之间用花板隔离)、脉冲反吹系统、卸输灰系统、阀门、膨胀节、电气、仪表及自动化控制系统等组成。
但是,在推动大型高炉煤气干式除尘的具体实施过程中,必须以科学态度认真对待。不同钢铁厂原料不同,冶炼强度不同;各地气侯条件不同,产生的高炉煤气含灰含尘性质不同,对干式除尘工艺要求也不尽相同,不能生搬硬套,工艺设计人员必须按不同条件认真区别对待,针对性设计才能使工艺逐步完善。目前高炉煤气干式除尘技术尚存在一些薄弱环节,有待各方面技术人员去研究、逐步完善。
高炉煤气经重力除尘和旋风除尘后,由荒煤气主管分配到布袋除尘器各箱体中,并进入荒煤气室,颗粒较大的粉尘由于重力作用自然沉降而进入灰斗,颗粒较小的粉尘随煤气上升。经过滤袋时,粉尘被阻留在滤袋的外表面,煤气得到净化。净化后的煤气进入净煤气室,由净煤气总管输入煤气管网。
当荒煤气温度过高或过低时,系统将自动关闭荒煤气进气总管蝶阀,同时打开荒煤气放散阀组,进行荒煤气放散,荒煤气放散阀组亦可有效控制高炉炉顶压力。
与传统湿法除尘比较,高炉煤气全干法除尘技术主要优点如下:
1投资省:干法投资仅为湿法投资的70%;
2占地少:面积不到湿法的50%;
3不耗水,少污染:吨铁节水0.7~0.8 m3;
4动力消耗少,节电效果明显,采用干法除尘后,没有冷却水,也就不需要污水处理系统,可降低电耗;
5煤气净化效果好:煤气含尘低于3 mg/m3;
工艺流程
图中干式煤气布袋除尘技术主要工艺系统由以下几部分组成。
1过滤系统
该系统工艺过程为高炉煤气在符合运行条件下进入干式除尘,经滤袋过滤产生净煤气后通过调压阀组或TRT发电后进入煤气管网供用户使用。在此系统中采用的滤料主要是玻璃纤维针刺毡或氟美斯针刺毡,它以5. 5μm的玻璃纤维为主体,配以一定量的高温纤维(P84 ,美塔斯,PPS)制成,具有三维微孔结构,运行阻力低,特别是P84纤维截面呈不规则叶片状,纤维表面积增加了80 %左右,因此具有较强的阻尘与捕尘能力。
2结构特点
1)高炉煤气干法布袋除尘装置是由数除尘器箱体并联组合而成,并由过滤、清灰、粉尘输送、自动控制组成的一个系统。
2)滤袋采用耐高温、高负荷、高强度的特种滤袋,使用寿命长。
3)采用外滤过滤形式,滤袋从箱体上部更换,换袋方便。
4)采用脉冲喷吹清灰技术,清灰能力强,除尘效率高,能耗少,钢耗小,占地面积小,运行稳定可靠,运行成本低,经济效益好。
在大型高炉煤气干法布袋除尘技术中有这样几个关键技术:一是荒煤气高低温对策,采用高炉炉顶喷雾打水和荒煤气放散系统相结合的工艺方式。二是采用大直径箱体,减少占地面积,降低配套阀门、仪表电器等设备的一次投资及维护成本,以便维护。三是双向电磁脉冲喷吹技术。四是采用压力可调式正压气力输送装置,具有投资小、运行费用低、故障少、密封性好、输灰过程无二次污染等优点。五是除尘内部结构优化,在气流分布和安全方面做了大量工作。六是滤料选择合理,选用了耐高温、抗折性、抗拉性较好的P84复合针刺毡滤料。七是在选用的阀门内喷涂了耐磨的涂层,密封圈选用了耐高温、高强度的材料。八是补偿器的不锈钢材质选用耐氯、硫、耐酸腐蚀强的材质。九是系统采用了PLC或DCS自动控制,工艺控制更加可靠。
1)箱体直径加大后,单排布袋数量增多,脉冲阀的能力难以进行有效的反吹清灰。
2)箱体直径加大后,使箱体内的气流均匀分布更难。
3)箱体直径加大后,使灰斗排灰的难度加大。
针对以上问题采取了以下技术措施
1)箱体设双气包,从两侧对布袋进行反吹清灰。
2)箱体出口设在上部椭圆封头的中央,箱体进口上部设有气流分配板。
3)箱体下部灰斗设计加大排灰角度,加强保温伴热,同时还设有氮气炮和舱壁震动器。
2气力输灰技术的应用
传统应用在小型高炉上的高炉煤气布袋除尘的输灰系统均采用螺旋输送机或埋刮板机等设施进行输灰,在大高炉煤气布袋除尘的设计中采用气力输灰技术,与传统的机械输灰相比具有以下优点:
1)设备数量大幅度减少,使输灰系统的投资降低。
干法布袋除尘技术的发展
干法布袋除尘器在我国发展较早,20世纪70年代初期就用于中小型高炉,取得了很好的效果。首座干法布袋除尘器于1974年11月在涉县铁厂13m3高炉上建成;1981年5月在临钢3号高炉上建成第一座100m3高炉煤气干法布袋除尘器,效果显著。到了20世纪90年代末期,电磁脉冲阀的采用,使得布袋清灰方式由反吹风改为脉冲喷吹清灰,过滤方式由内滤式改为外滤式,并采用玻纤针刺毡等新滤料,使高炉煤气干法布袋除尘工艺由大布袋反吹风方式发展为固定列管式喷吹清灰方式。干法除尘技术获得了新生,进入了新的发展阶段。
2清灰系统
目前,本系统使用的反吹清灰方式为氮气脉冲反吹,主要设备由贮气罐、喷吹管、脉冲阀、分气包等组成;低压氮气通过脉冲膜片阀产生脉冲气流,振落滤袋外表面附着的积灰而达到清灰的目的。此套系统自动化程度高、效果显著,当设备发生故障或不符合反吹条件时,PLC可自动发出指令封锁一切现行的操作,以此来杜绝较大事故的发生。
2)与传统的机械输灰相比,气力输灰使整个除尘设施降低3m左右,减少了投资。
3输卸灰系统
该系统流程为“上灰仓→中间灰仓→埋刮板机→斗式提升机→高位灰仓→加湿机→下灰仓→外运”。此系统流程太长,运行中不可避免地出现二次扬尘现象,目前国内还无较好的解决办法。包钢、济钢采用新开发的高炉煤气除尘罐车输灰装置克服了上述缺点,但在应用上还需进一步完善。
4煤气调温系统
干法除尘所选用的滤袋能承受的最高温度大概为280℃左右,而进入滤袋除尘器的煤气温度下限应高于露点30℃,因此,为防止温度超高烧损滤袋或因温度低而粘结滤袋,有效地控制进入箱体的煤气温度对布袋除尘器的正常运行是极为重要的。大中型高炉在操作中正常煤气温度在120- 210℃之间,如出现炉况不顺时煤气温度偏高的情况多于偏低的情况,目前国内通常采用调温系统来控制煤气温度以利除尘系统的运行,其工艺流程如图2。
当煤气温度在正常情况下(炉顶上升管煤气温度低于300℃时)煤气走旁通管,进入布袋可正常工作。当炉顶上升管煤气温度达300 - 350℃时,马上切换到调温系统,启动风机吸入冷风进行热交换降温,以保证布袋除尘器煤气温度控制在300℃以下。当炉顶上升管煤气温度高于350℃时(这种情况出现几率较小,由于炉顶设有喷水降温设施)必须进行炉顶打水或其他高炉操作手段进行煤气降温;当温度低的时候,启动风机吸入热风炉废气进行升温,此系统升、降温的能力是正负40℃之间,基本能满足高炉操作的要求。
高炉煤气干法除尘技术国内外应用情况
更新时间:09-7-31 11:17
国内应用
高炉干法除尘是中国钢铁工业协会重点推荐应用的高炉煤气净化技术,已经采用全干法除尘的大中型高炉主要有:莱钢两座2218 m3、通钢1086m3、韶关2500 m3、柳钢1080 m3、攀钢1350 m3。与湿法除尘相比,不仅简化了工艺系统,从根本上解决二次水污染及污泥的处理问题,而且配合干式TRT可合理利用煤气显热,显著提高发电水平。