杜邦全液相加氢技术
液相加氢技术的应用现状

C-NUM 液相加氢技术的应用对象也是航煤原料,这种原 料本身的性质和状态比常规的柴油等油料更好,加氢效果更 佳,整个精制过程的对循环系统、反应环境的要求比较小。在面 对航煤原料时,C-NUM 技术应用装置取消了循环油系统,有效 降低了循环泵可能带来的安全风险和成本、动力消耗;反应温 度为 245 ℃,压力为 3.5 MPa,氢油比在 12~13 范围内,属于较 为理想的反应过程。但如果面对的是原料性质、状态更差一些 的焦化柴油等柴油种类时,C-NUM 技术装置能否顺利加氢,能 否顺利完成精制反应获得符合标准的产品油,还需要进一步的 实践和验证分析。
目前来看,液相加氢技术始终存在氢气消耗量高、循环加 氢能耗较高、循环泵安全风险较高、催化剂使用寿命较低等问 题。想要改善这些问题需要通过特殊的设备装置,提高氢气与 原料油的混合程度,实现原料油中的氢气饱和状态[3]。想要达 到氢气饱和的理想状态,可能需要超重力、微米气泡等类型的 装置,使原料油中的氢气溶解量远超于实际需求量。如果能够 解决溶氢过程中的氢气饱和问题,就能够真正节约掉循环加氢 的装置和能耗,并且规避掉循环泵可能带来的安全风险和泄露 风险。这是液相加氢技术未来发展的主要方向,突破这一难题 就能够促进液相加氢技术的有效发展,扩大液相加氢技术的应 用范围。目前的液相加氢技术还不能代替气相滴流等技术的应 用,在原料油精制反应中还不能占据更大的主动性[4]。
LI Nong, LI Hai-feng, ZHAO Xin-quan, LI Guo-qi (Sinochem Changhe Technology Co., Ltd., Dongying 257335, China)
Abstract: Liquid phase hydrogenation technology is a process to maintain high hydrogen-oil ratio, which can effectively improve the heat transfer effect between phases, can improve the reaction eff iciency of oil, reduce the power consumption in the application process of diesel oil, kerosene and other feedstock oils, and produce more environmentally friendly clean oil. In the process of liquid phase hydrogenation, the amount of hydrogen dissolved in oil is the key problem, which affects the energy consumption and production eff iciency of the technology. This paper mainly analyzes the application status and application prospect of this technology.
烷基化介绍
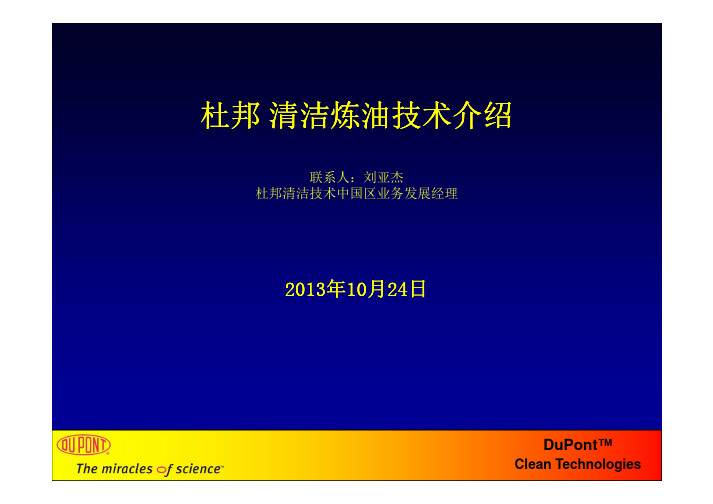
FC-2
C
中间酸 ~ 95 WT%
FC-3
C
中间酸 ~ 93-92 WT%
废酸 90 WT%
M
接触反应器
M
接触反应器
M
接触反应器
烯烃和异丁烷
DuPont™
Clean Technologies
中海油16万吨/年烷基化装置
DuPont™
Clean Technologies
配套的废硫酸再生装置
DuPont™
7- 9 比 1
DuPont Environmental Solutions
Confidential
STRATCO®
DUPONT REFINERY SOLUTIONS
异丁烷消耗 (BBL/BBL烯烃)
丙烯
1.27-1.32
丁烯
1.10-1.16
戊烯
0.96-1.14
DuPont Environmental Solutions
STRATCO®
DUPONT REFINERY SOLUTIONS
STRAห้องสมุดไป่ตู้CO®反应部分
FC-1
新鲜酸
酸沉降罐 NC
FC-2
中间酸
酸沉降罐 NC
FC-3
废酸
M
接触反应器
M
接触反应器
DuPont Environmental Solutions
Confidential
STRATCO®
DUPONT REFINERY SOLUTIONS
• 世界范围
DuPont™
Clean Technologies
4
杜邦公司的14个业务部门
• 先锋良种 • 植物保护 • 营养与健康
硝基苯液相催化加氢制苯胺技术进展
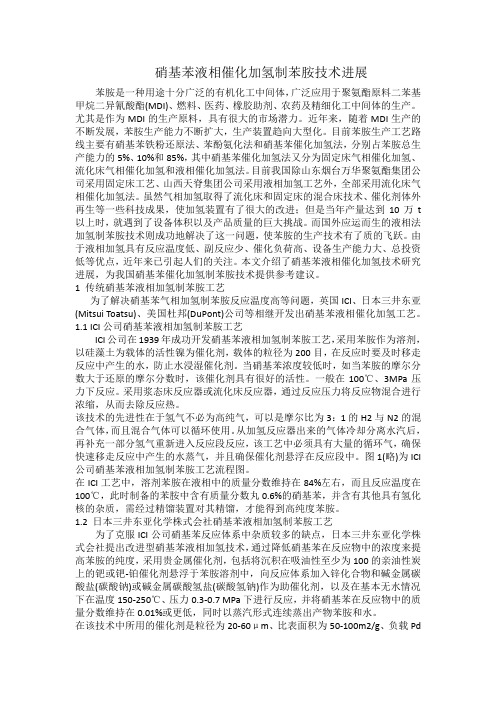
硝基苯液相催化加氢制苯胺技术进展苯胺是一种用途十分广泛的有机化工中间体,广泛应用于聚氨酯原料二苯基甲烷二异氰酸酯(MDI)、燃料、医药、橡胶助剂、农药及精细化工中间体的生产。
尤其是作为MDI的生产原料,具有很大的市场潜力。
近年来,随着MDI生产的不断发展,苯胺生产能力不断扩大,生产装置趋向大型化。
目前苯胺生产工艺路线主要有硝基苯铁粉还原法、苯酚氨化法和硝基苯催化加氢法,分别占苯胺总生产能力的5%、10%和85%,其中硝基苯催化加氢法又分为固定床气相催化加氢、流化床气相催化加氢和液相催化加氢法。
目前我国除山东烟台万华聚氨酯集团公司采用固定床工艺、山西天脊集团公司采用液相加氢工艺外,全部采用流化床气相催化加氢法。
虽然气相加氢取得了流化床和固定床的混合床技术、催化剂体外再生等一些科技成果,使加氢装置有了很大的改进;但是当年产量达到10万t 以上时,就遇到了设备体积以及产品质量的巨大挑战。
而国外应运而生的液相法加氢制苯胺技术则成功地解决了这一问题,使苯胺的生产技术有了质的飞跃。
由于液相加氢具有反应温度低、副反应少、催化负荷高、设备生产能力大、总投资低等优点,近年来已引起人们的关注。
本文介绍了硝基苯液相催化加氢技术研究进展,为我国硝基苯催化加氢制苯胺技术提供参考建议。
1 传统硝基苯液相加氢制苯胺工艺为了解决硝基苯气相加氢制苯胺反应温度高等问题,英国ICI、日本三井东亚(Mitsui Toatsu)、美国杜邦(DuPont)公司等相继开发出硝基苯液相催化加氢工艺。
1.1 ICI公司硝基苯液相加氢制苯胺工艺ICI公司在1939年成功开发硝基苯液相加氢制苯胺工艺,采用苯胺作为溶剂,以硅藻土为载体的活性镍为催化剂,载体的粒径为200目,在反应时要及时移走反应中产生的水,防止水浸湿催化剂。
当硝基苯浓度较低时,如当苯胺的摩尔分数大于还原的摩尔分数时,该催化剂具有很好的活性。
一般在100℃、3MPa压力下反应。
采用浆态床反应器或流化床反应器,通过反应压力将反应物混合进行浓缩,从而去除反应热。
蜡油全液相加氢技术的工业应用

加工工艺石 油 炼 制 与 化 工PETROLEUMPROCESSINGANDPETROCHEMICALS2021年4月 第52卷第4期 收稿日期:2020 10 15;修改稿收到日期:2021 01 10。
作者简介:徐秋鹏,大学本科,工程师,从事加氢裂化、液相加氢、渣油加氢装置的生产管理工作。
通讯联系人:徐秋鹏,E mail:xuqp2@cnooc.com.cn。
¡>¢ £./vw4XYDE徐 秋 鹏(中海油惠州石化有限公司,广东惠州516086)摘 要:中海油惠州石化有限公司二期项目2.6Mt?a蜡油全液相加氢装置于2017年建成投产。
该装置采用杜邦公司的IsoTherming全液相加氢技术设计,是国内首套采用全液相加氢技术的蜡油加氢装置。
经过两年多的运转,该装置虽然经历多次开停工,但仍表现出较好的操作便利性和经济性。
装置运行2年多后的标定结果表明:对于硫质量分数大于2.7%、氮质量分数大于500 g?g的沙特中质原油减压蜡油原料,加氢蜡油产品的硫质量分数小于1000 g?g、氮质量分数小于100 g?g,均满足催化裂化装置对进料的要求;装置标定期间的综合能耗为274.63MJ?t,不但低于传统滴流床蜡油加氢装置,而且优于装置设计指标;装置整体运行情况达到设计要求。
关键词:全液相 蜡油 加氢 IsoTherming 循环油泵 综合能耗在现代炼油行业,加氢处理装置往往由于操作条件较为苛刻,所以装置投资很大。
为生产满足环保要求的清洁石油产品,世界各国炼油技术人员开发了很多加氢技术,以降低装置的投资和能耗。
其中液相加氢技术是近几年发展起来的一种突破性加氢技术。
在液相加氢技术中,反应是以液相进行的。
传统滴流床加氢技术需要大量的富氢气循环气与进料一起进入反应器,以确保反应所需的氢气被充分溶解至液相中。
液相加氢工艺技术反应部分不设置氢气循环系统,依靠液相产品循环以溶解足量的氢气,满足加氢反应的需要[1 2]。
液相加氢技术

学习资料1、杜邦公司Iso Therming 加氢技术杜邦公司Iso Therming 加氢技术特点是不使用喷淋床反应器,而采用液相填充床反应器。
反应中使用的氢溶解在液体中,而不是作为气体进行循环。
(见下图)液相反应器在杜邦公司内的商业运行时间已有几十年的时间。
液相反应器设计中的一项技术要求为溶解在反应器进料中的氢的量应该高于反应所需氢的量。
在大多数炼油厂中,氢的数量只是高于新鲜原料中氢的溶解度。
在Iso Therming 加氢技术中,产品液体进行再循环,以便溶解在混合原料中的氢量远高于反应所需的氢量。
正确的再循环率通过中试装置使用实际进料及反应工程模型进行测试来确定。
装置中不需要设置价格昂贵的氢气循环压缩机。
补充氢压缩机与喷淋床反应器相比,液相填充床反应器在设计及提高产能方面更加简单。
在喷淋床反应器中,气体及液体的最佳分布状态非常关键,并且再分布格栅需要仔细设计以防止分布状态不佳,与此相比,填充床反应器中液体流量的分布并不是一个关键设计问题。
在反应器设计中未考虑与多相流相关的其它问题,如压力降及流动状态。
在Iso Therming 加氢技术中,催化剂是全湿的。
这一点与喷淋床反应器形成对比,在该反应器中充满大量气体,而液体向下喷淋到催化剂床上。
在催化剂中以及催化剂周围存在液体可以尽可能降低减少催化剂活性部位的热点。
由于溶解于液体中氢的量远远超过反应中所需氢的量,催化剂活性部位即有氢的存在。
这些因素可以将结焦造成的催化剂减活作用降至最低程度。
Iso Therming反应器中的绝热温度远低于喷淋反应器中的温度,因为充满液体的反应器中的热质量较高。
这种低温升的特点可以在工艺设计中降低对中间冷却的依赖。
Iso Therming反应器的最大温升受到溶解于液体中氢的数量限制。
而在Iso Therming反应器中没有大量的热偏移或者温度超出控制范围的现象,这一点与喷淋反应器不同,在喷淋床反应器气体持续流动,且气体循环流率比反应所需的流率高几倍。
1,3-丙二醇的合成方法及技术进展
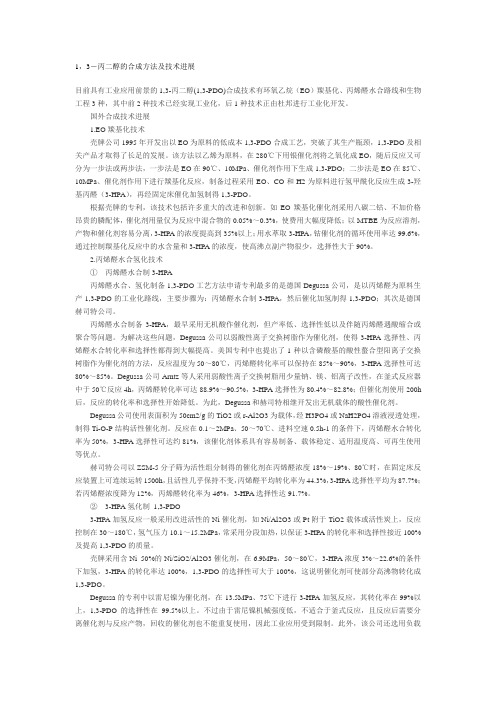
1,3-丙二醇的合成方法及技术进展目前具有工业应用前景的1,3-丙二醇(1,3-PDO)合成技术有环氧乙烷(EO)羰基化、丙烯醛水合路线和生物工程3种,其中前2种技术已经实现工业化,后1种技术正由杜邦进行工业化开发。
国外合成技术进展1.EO羰基化技术壳牌公司1995年开发出以EO为原料的低成本1,3-PDO合成工艺,突破了其生产瓶颈,1,3-PDO及相关产品才取得了长足的发展。
该方法以乙烯为原料,在280℃下用银催化剂将之氧化成EO,随后反应又可分为一步法或两步法,一步法是EO在90℃、10MPa、催化剂作用下生成1,3-PDO;二步法是EO在85℃、10MPa、催化剂作用下进行羰基化反应,制备过程采用EO、CO和H2为原料进行氢甲酰化反应生成3-羟基丙醛(3-HPA),再经固定床催化加氢制得1,3-PDO。
根据壳牌的专利,该技术包括许多重大的改进和创新。
如EO羰基化催化剂采用八碳二钴、不加价格昂贵的膦配体,催化剂用量仅为反应中混合物的0.05%~0.3%,使费用大幅度降低;以MTBE为反应溶剂,产物和催化剂容易分离,3-HPA的浓度提高到35%以上;用水萃取3-HPA,钴催化剂的循环使用率达99.6%,通过控制羰基化反应中的水含量和3-HPA的浓度,使高沸点副产物很少,选择性大于90%。
2.丙烯醛水合氢化技术①丙烯醛水合制3-HPA丙烯醛水合、氢化制备1,3-PDO工艺方法申请专利最多的是德国Degussa公司,是以丙烯醛为原料生产1,3-PDO的工业化路线,主要步骤为:丙烯醛水合制3-HPA,然后催化加氢制得1,3-PDO;其次是德国赫司特公司。
丙烯醛水合制备3-HPA,最早采用无机酸作催化剂,但产率低、选择性低以及伴随丙烯醛遇酸缩合或聚合等问题。
为解决这些问题,Degussa公司以弱酸性离子交换树脂作为催化剂,使得3-HPA选择性、丙烯醛水合转化率和选择性都得到大幅提高。
美国专利中也提出了1种以含磷酸基的酸性螯合型阳离子交换树脂作为催化剂的方法,反应温度为50~80℃,丙烯醛转化率可以保持在85%~90%,3-HPA选择性可达80%~85%。
简述全液相蜡油加氢技术的操作要点
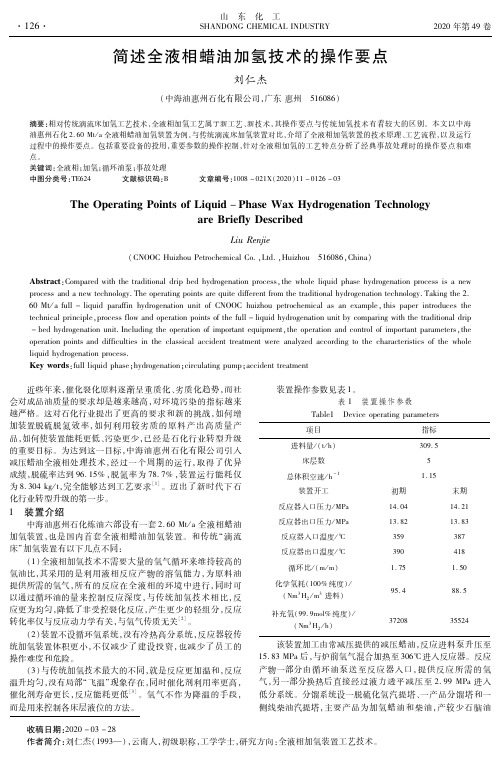
山 东 化 工 收稿日期:2020-03-28作者简介:刘仁杰(1993—),云南人,初级职称,工学学士,研究方向:全液相加氢装置工艺技术。
简述全液相蜡油加氢技术的操作要点刘仁杰(中海油惠州石化有限公司,广东惠州 516086)摘要:相对传统滴流床加氢工艺技术,全液相加氢工艺属于新工艺、新技术,其操作要点与传统加氢技术有着较大的区别。
本文以中海油惠州石化2.60Mt/a全液相蜡油加氢装置为例,与传统滴流床加氢装置对比,介绍了全液相加氢装置的技术原理、工艺流程,以及运行过程中的操作要点。
包括重要设备的投用,重要参数的操作控制,针对全液相加氢的工艺特点分析了经典事故处理时的操作要点和难点。
关键词:全液相;加氢;循环油泵;事故处理中图分类号:TE624 文献标识码:B 文章编号:1008-021X(2020)11-0126-03TheOperatingPointsofLiquid-PhaseWaxHydrogenationTechnologyareBrieflyDescribedLiuRenjie(CNOOCHuizhouPetrochemicalCo.,Ltd.,Huizhou 516086,China)Abstract:Comparedwiththetraditionaldripbedhydrogenationprocess,thewholeliquidphasehydrogenationprocessisanewprocessandanewtechnology.Theoperatingpointsarequitedifferentfromthetraditionalhydrogenationtechnology.Takingthe2.60Mt/afull-liquidparaffinhydrogenationunitofCNOOChuizhoupetrochemicalasanexample,thispaperintroducesthetechnicalprinciple,processflowandoperationpointsofthefull-liquidhydrogenationunitbycomparingwiththetraditionaldrip-bedhydrogenationunit.Includingtheoperationofimportantequipment,theoperationandcontrolofimportantparameters,theoperationpointsanddifficultiesintheclassicalaccidenttreatmentwereanalyzedaccordingtothecharacteristicsofthewholeliquidhydrogenationprocess.Keywords:fullliquidphase;hydrogenation;circulatingpump;accidenttreatment 近些年来,催化裂化原料逐渐呈重质化、劣质化趋势,而社会对成品油质量的要求却是越来越高,对环境污染的指标越来越严格。
二硝基甲苯液相加氢催化剂研究进展
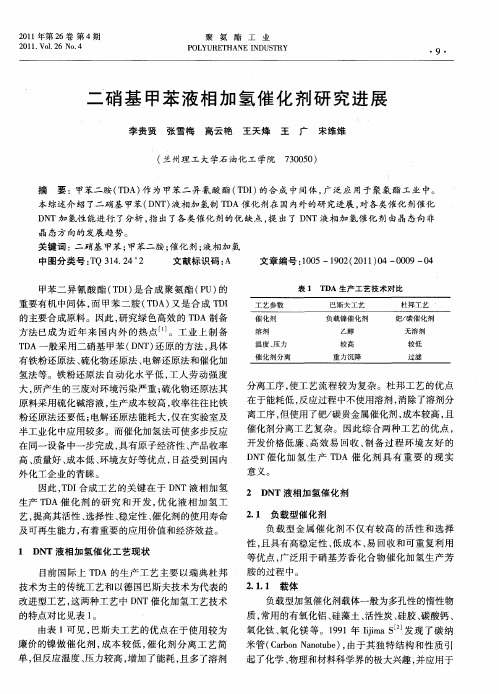
技术为主的传统工艺和以德国巴斯夫技术为代表的
改进 型工 艺 , 这两 种工 艺 中 D T催 化加 氢 工 艺技 术 N 的特 点对 比见 表 1 。
2 11 载体 ..
负载型加氢催化剂载体一般为多孔性的惰性物 质, 常用的有氧化铝 、 硅藻土、 活性炭 、 硅胶 、 碳酸钙 、 氧化钛 、 氧化镁等。19 9 1年 IiaS2 i _ 发现 了碳 纳 j m 米管( a o ao b ) 由于其独特结构和性质 引 C r nN nt e , b u
( 兰州理 工大 学石 油化 工 学院
705 ) 300
摘 要 :甲苯二胺 ( D 作 为 甲苯 二 异 氰 酸 酯 ( D ) T A) T I 的合 成 中 间体 , 广泛 应 用 于聚 氨 酯 工业 中。 本 综 述介 绍 了二硝 基 甲苯 ( N ) D T 液相加 氢 制 T A催化 剂在 国 内外 的研 究进 展 , D 对各 类催 化剂 催化 D T加 氢性 能进行 了分析 , 出了各类催 化 剂 的优 缺 点 , 出了 D T液相 加 氢催 化 剂 由晶 态向 非 N 指 提 N
负 载 型 金 属 催 化 剂 不 仅 有 较 高 的活 性 和 选 择 性 , 具有 高稳 定 性 、 成本 、 回收 和 可 重复 利 用 且 低 易 等优 点 , 泛用 于 硝基 芳 香 化 合 物催 化 加 氢生 产 芳 广
胺 的过程 中。
目前 国际上 T A 的生 产 工 艺 主要 以 瑞典 杜 邦 D
1 0・
聚氨酯工业
第2 6卷
无 机载 体 领 域 中。房 永 彬 将 铂 锡 催 化 剂 分 别 负 载于碳 纳米 管 、 i 和 - 1 上 , SO A O 通过 对 硝基 甲苯 液 相加 氢制 备对 甲基苯 胺 的反应 对催 化剂 进行 活性 评价 , 结果 表 明 , 用碳 纳米 管负载 的铂 锡催 化剂 可使
航煤液相加氢技术的研究及应用

航煤液相加氢技术的研究及应用近年来航煤的价格不断上涨,让航空公司对机务维修保养成本的减少产生了极大的重视。
由于航空发动机的供油系统是其中一个重要的物料,液相加氢技术的研究就变得尤为重要。
航空发动机的飞行依赖于发动机供油系统的高效供油,如果由于污染而影响油性能,则会影响飞行安全并使发动机失效。
因此,航空公司开始采用液相加氢技术来维护和保养发动机供油系统,既可以减少成本,又可以降低机载污染物的排放。
液相加氢技术是一种清洁维护技术,可以清除沾染在油系统内壁上的污物,并以温和的方式改善发动机的供油,使油质得到改善。
液相加氢技术可以对航空燃料油系统中的污垢、油膜、油泥、沉积物和污水等进行去除,从而保持系统清洁,提高系统运行效率。
液相加氢技术利用一些特殊的添加剂,可以有效提高油膜的溶解度,降低油膜的粘度,使发动机的冷却更加有效,有利于延长发动机寿命。
液相加氢技术也可以消除因机载污染物排放而导致的空气污染,减少对环境的影响。
值得一提的是,液相加氢技术的成本并不高,其可以有效降低航空公司的机务维修保养成本,同时也可以有效改善发动机性能,延长发动机寿命,降低机载污染物排放,减少对环境的影响。
随着社会对于环境保护的重视度越来越高,国家开始加强对航空行业的管理,对航空污染的治理更加严格。
液相加氢技术作为一种低污染、高效、经济的机务维修技术,可以有效支撑航空发动机飞行安全,有利于减轻环境负担,在保障航空安全的同时也有利于航空公司的节约成本。
因此,对液相加氢技术的研究将会更加深入,并且必然会更好地应用在航空发动机的清洁维护上,为航空公司和国家免除污染带来的风险,提高安全系数,进一步优化航空发动机的飞行安全性。
基于上述分析,航空发动机液相加氢技术的研究与应用对于提高发动机效率,降低机务维修保养成本,减少机载污染物排放,减少对环境的影响具有重要意义,因此,其未来发展前景广阔,有望给航空公司带来更大的经济效益。
连续液相循环加氢技术(SLHT)的工业应用
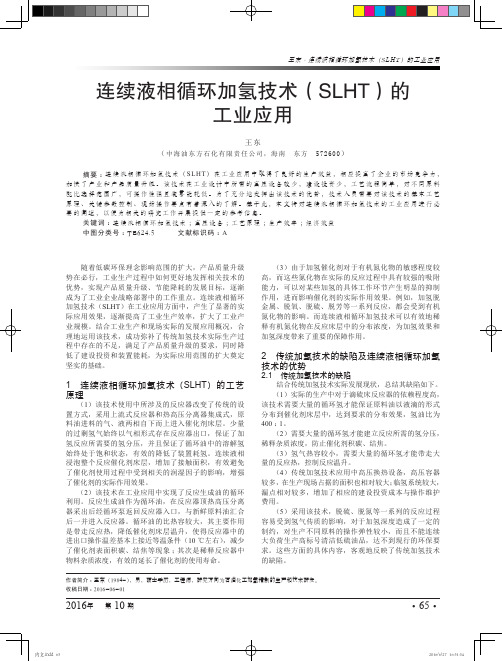
目前,美国杜邦 Iso-therming、中石化 SRH 和 SLHT 等液相加氢技术分别应用于实际生产,优势各异。但是, SLHT 技术无论在理论体系方面,还是实际的应用方面, 都取得了许多重要的成果,相关企业也在该技术的适用 性方面进行了充分地论证,发现它在柴油生产方面具有 低成本、高效率、节能环保的优势,客观地说明了这项
现阶段,随着电气工程及其自动化应用范围不断扩 大,对其进行不断的完善与改进具有非常重要的作用。 因此,加强电气工程及其自动化是发展的首要任务,需 要不断强化电气工程及其自动化的节能设计、加强对电 气工程及其自动化系统的管理、加强电气工程及其自动 化系统进程及提高系统集成化水平,以此促进我国经济 的稳定增长。
王东·连续液相循环加氢技术(SLHT)的工业应用
连续液相循环加氢技术(SLHT)的 工业应用
王东 (中海油东方石化有限责任公司,海南 东方 572600)
摘 要 :连 续 液 相 循 环 加 氢 技 术 ( S LH T )在工业应用中取得了良好的生产效益,相应提高了企 业的市场竞争力, 加 快 了 产 业 和 产 品 质 量 升 级 。 该 技 术 在 工 业 设 计 中 所 需 的 高 压 设 备 较 少 , 建 设 投 资 少, 工 艺 流 程 简 单 , 对 不 同 原 料 配 比 选 择 范 围 广 , 可 操 作 性 强 且 装 置 能 耗 低。 为 了 充 分 地 发 挥 出 该 技 术 的 优 势, 技 术 人 员 需 要 对 该 技 术 的 基 本 工 艺 原 理、 关 键 参 数 控 制 、 现 场 操 作 要 点 有 着 深 入 的 了 解。 基 于 此, 本 文 将 对 连 续 液 相 循 环 加 氢 技 术 的 工 业 应 用 进 行 必 要 的 阐 述 ,以 便 为 相 关 的 研 究 工 作 开 展 提供一定的参考信息。 关 键词 :连 续 液 相 循 环 加 氢 技 术 ;高压设备 ;工艺原理 ;生产效率 ;经济效益 中 图分 类 号 :T E 6 2 4 . 5 文 献标识码 :A
气相加氢和液相加氢
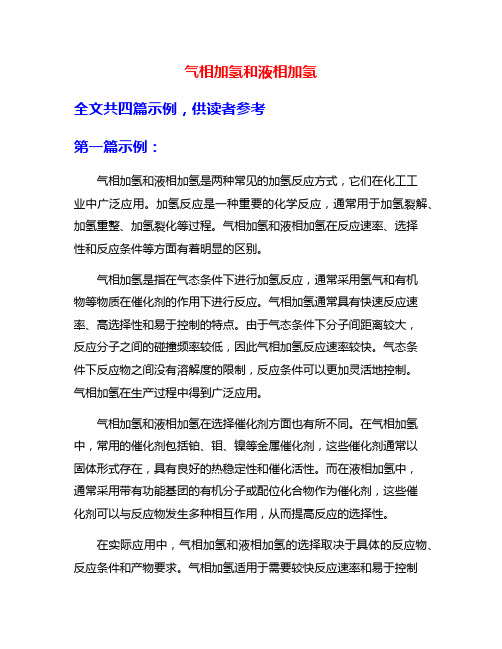
气相加氢和液相加氢全文共四篇示例,供读者参考第一篇示例:气相加氢和液相加氢是两种常见的加氢反应方式,它们在化工工业中广泛应用。
加氢反应是一种重要的化学反应,通常用于加氢裂解、加氢重整、加氢裂化等过程。
气相加氢和液相加氢在反应速率、选择性和反应条件等方面有着明显的区别。
气相加氢是指在气态条件下进行加氢反应,通常采用氢气和有机物等物质在催化剂的作用下进行反应。
气相加氢通常具有快速反应速率、高选择性和易于控制的特点。
由于气态条件下分子间距离较大,反应分子之间的碰撞频率较低,因此气相加氢反应速率较快。
气态条件下反应物之间没有溶解度的限制,反应条件可以更加灵活地控制。
气相加氢在生产过程中得到广泛应用。
气相加氢和液相加氢在选择催化剂方面也有所不同。
在气相加氢中,常用的催化剂包括铂、钼、镍等金属催化剂,这些催化剂通常以固体形式存在,具有良好的热稳定性和催化活性。
而在液相加氢中,通常采用带有功能基团的有机分子或配位化合物作为催化剂,这些催化剂可以与反应物发生多种相互作用,从而提高反应的选择性。
在实际应用中,气相加氢和液相加氢的选择取决于具体的反应物、反应条件和产物要求。
气相加氢适用于需要较快反应速率和易于控制的生产过程,而液相加氢适用于需要提高反应选择性和增加反应条件的情况。
在某些情况下,可以将气相加氢和液相加氢进行组合应用,以充分发挥两种反应方式的优势。
气相加氢和液相加氢是两种重要的加氢反应方式,它们在化工工业中扮演着重要角色。
通过深入研究和比较两种反应方式的特点和应用,可以更好地指导实际生产中的加氢反应设计和优化,为化工产业的发展做出贡献。
【已达到2000字要求,如有需要可继续添加内容】。
第二篇示例:气相加氢和液相加氢是两种常见的加氢反应方式,广泛应用于化工工业中。
气相加氢指的是将氢气与其他物质在气相条件下反应生成加氢产物,液相加氢则是指在液相条件下进行加氢反应。
两种加氢方式各有优缺点,本文将就气相加氢和液相加氢进行详细的介绍。
杜邦硝基苯液相加氢技术副产物研究
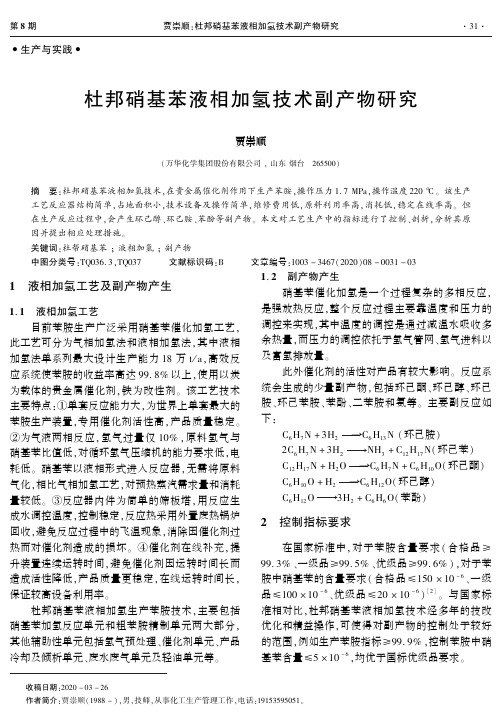
•生产与实践•杜邦硝基苯液相加氢技术副产物研究贾崇顺(万华化学集团股份有限公司ꎬ山东烟台㊀265500)摘㊀要:杜邦硝基苯液相加氢技术ꎬ在贵金属催化剂作用下生产苯胺ꎬ操作压力1.7MPaꎬ操作温度220ħꎮ该生产工艺反应器结构简单ꎬ占地面积小ꎬ技术设备及操作简单ꎬ维修费用低ꎬ原料利用率高ꎬ消耗低ꎬ稳定在线率高ꎮ但在生产反应过程中ꎬ会产生环己醇㊁环己胺㊁苯酚等副产物ꎮ本文对工艺生产中的指标进行了控制㊁剖析ꎬ分析其原因并提出相应处理措施ꎮ关键词:杜帮硝基苯ꎻ液相加氢ꎻ副产物中图分类号:TQ036.3ꎬTQ037㊀㊀㊀文献标识码:B㊀㊀㊀文章编号:1003-3467(2020)08-0031-031㊀液相加氢工艺及副产物产生1.1㊀液相加氢工艺目前苯胺生产广泛采用硝基苯催化加氢工艺ꎬ此工艺可分为气相加氢法和液相加氢法ꎬ其中液相加氢法单系列最大设计生产能力18万t/aꎬ高效反应系统使苯胺的收益率高达99.8%以上ꎬ使用以炭为载体的贵金属催化剂ꎬ铁为改性剂ꎮ该工艺技术主要特点:①单套反应能力大ꎬ为世界上单套最大的苯胺生产装置ꎬ专用催化剂活性高ꎬ产品质量稳定ꎮ②为气液两相反应ꎬ氢气过量仅10%ꎬ原料氢气与硝基苯比值低ꎬ对循环氢气压缩机的能力要求低ꎬ电耗低ꎮ硝基苯以液相形式进入反应器ꎬ无需将原料气化ꎬ相比气相加氢工艺ꎬ对预热蒸汽需求量和消耗量较低ꎮ③反应器内件为简单的筛板塔ꎬ用反应生成水调控温度ꎬ控制稳定ꎬ反应热采用外置废热锅炉回收ꎬ避免反应过程中的飞温现象ꎬ消除因催化剂过热而对催化剂造成的损坏ꎮ④催化剂在线补充ꎬ提升装置连续运转时间ꎬ避免催化剂因运转时间长而造成活性降低ꎬ产品质量更稳定ꎬ在线运转时间长ꎬ保证较高设备利用率ꎮ杜邦硝基苯液相加氢生产苯胺技术ꎬ主要包括硝基苯加氢反应单元和粗苯胺精制单元两大部分ꎬ其他辅助性单元包括氢气预处理㊁催化剂单元㊁产品冷却及倾析单元㊁废水废气单元及轻油单元等ꎮ1.2㊀副产物产生硝基苯催化加氢是一个过程复杂的多相反应ꎬ是强放热反应ꎬ整个反应过程主要靠温度和压力的调控来实现ꎬ其中温度的调控是通过减温水吸收多余热量ꎬ而压力的调控依托于氢气管网㊁氢气进料以及富氢排放量ꎮ此外催化剂的活性对产品有较大影响ꎮ反应系统会生成的少量副产物ꎬ包括环己酮㊁环己醇㊁环己胺㊁环己苯胺㊁苯酚㊁二苯胺和氨等ꎮ主要副反应如下:C6H7N+3H2ңC6H13N(环己胺)2C6H7N+3H2ңNH3+C12H17N(环己苯)C12H17N+H2OңC6H7N+C6H10O(环己酮)C6H10O+H2ңC6H12O(环己醇)C6H12Oң3H2+C6H6O(苯酚)2㊀控制指标要求在国家标准中ꎬ对于苯胺含量要求(合格品ȡ99.3%㊁一级品ȡ99.5%㊁优级品ȡ99.6%)ꎬ对于苯胺中硝基苯的含量要求(合格品ɤ150ˑ10-6㊁一级品ɤ100ˑ10-6㊁优级品ɤ20ˑ10-6)[2]ꎮ与国家标准相对比ꎬ杜邦硝基苯液相加氢技术经多年的技改优化和精益操作ꎬ可使得对副产物的控制处于较好的范围ꎬ例如生产苯胺指标ȡ99.9%ꎬ控制苯胺中硝基苯含量ɤ5ˑ10-6ꎬ均优于国标优级品要求ꎮ㊀㊀收稿日期:2020-03-26㊀㊀作者简介:贾崇顺(1988-)ꎬ男ꎬ技师ꎬ从事化工生产管理工作ꎬ电话:19153595051ꎮ 13第8期㊀㊀㊀㊀㊀㊀㊀㊀㊀㊀㊀㊀㊀㊀贾崇顺:杜邦硝基苯液相加氢技术副产物研究3㊀产品指标分析调控及解决方案当精苯胺产品中分析指标出现异常超标时ꎬ即硝基苯㊁环己胺㊁环己酮㊁苯酚㊁环己醇超标以及各指标异常富集等ꎬ应立即将产品采出切循环操作ꎬ并组织排查原因ꎮ①确认反应单元出现异常ꎬ粗苯胺与精苯胺产品均不合格ꎬ则需根据不合格指标ꎬ开展相对应调整ꎬ即通过反应单元新鲜催化剂㊁氢油比(原料氢气与硝基苯比值)㊁激冷水以及精制单元回流比㊁焦油采出㊁蒸汽用量等手段调控ꎮ②确认反应单元正常ꎬ反应粗苯胺产品合格ꎬ只是单纯的精苯胺产品不合格ꎬ可通过精制单元回流比㊁焦油采出㊁蒸汽用量等手段调控ꎮ3.1㊀硝基苯异常分析调控反应单元温度控制偏低ꎬ导致粗苯胺产品和精产品中硝基苯超标ꎮ反应器内通过减温水来吸收多余热量ꎬ达到调控温度目的ꎬ当温度偏低反应不充分ꎬ硝基苯转化率低ꎬ从而导致反应器顶部粗苯胺产品和侧线循环催化剂采出中硝基苯超标ꎮ解决方案:首先将粗苯胺产品切至不合格罐ꎬ避免影响精制单元ꎬ然后依据反应单元生产情况ꎬ微调激冷水ꎬ将反应核心温度调高ꎬ氢油比调高ꎬ新鲜催化剂和循环催化剂调高等手段ꎮ反应单元催化剂活性降低或失活ꎬ导致粗苯胺产品和精产品中硝基苯超标ꎮ催化剂直接参与反应进行ꎬ加快反应速率ꎬ其活性直接影响主反应和副反应的进程ꎬ当催化剂活性低时ꎬ主副反应均减弱ꎬ反应不完全ꎬ硝基苯转化率低ꎬ从而导致反应器顶部粗苯胺产品和侧线循环催化剂中硝基苯超标ꎮ解决方案:当发生催化剂活性降低时ꎬ第一时间确定原因ꎮ①循环催化剂中焦油含量高ꎬ会堵塞催化剂表面积以及内部通道ꎬ造成催化剂活性被抑制ꎬ影响催化剂和反应物的接触ꎬ严重时造成失活ꎮ解决方案是定期检测焦油含量ꎬ并对焦油净化过滤分离ꎬ使其维持在较低的浓度(1%~2%)ꎮ②原料硝基苯中杂质(长链烷烃)含量高ꎬ使催化剂中毒失活ꎬ同时也会延长粗苯胺的分层时间(1min延长至13min)ꎬ造成苯胺泛白乳化和生产系统紊乱ꎮ解决方案是控制原料中长链烷烃的含量(<400ˑ10-6)ꎬ当含量较高时需调和后使用ꎮ③原料氢气中杂质(CO/CO2/S)含量高ꎬ会对催化剂造成不可恢复性中毒而失活ꎮ解决方案是加强氢气指标的监控ꎬ并对原料氢气及循环氢气进行甲烷化预处理ꎮ④新鲜催化剂添加量持续偏少ꎬ反应单元内催化剂浓度不足ꎬ导致硝基苯转化率低ꎬ解决方案是在线补充损失的催化剂ꎮ3.2㊀环己胺异常分析调控反应过程氢气过量10%ꎬ且在液相苯胺中会溶解氢气7ˑ10-6~12ˑ10-6ꎬ在反应器温度过高时ꎬ会导致苯胺氢化生成环己胺ꎬ造成氢气单耗的增加和副产物环己胺的超标ꎮ解决方案:控制在反应器内生成是重点ꎬ根据反应器各项运行参数㊁微调激冷水㊁新鲜催化剂和循环催化剂㊁控制反应核心温度以及调整氢油比等手段ꎬ严重时可将精致单元脱水塔填料层温度调高(145ħ)ꎬ加大塔顶轻组分采出ꎬ储存富集的轻油ꎬ启用轻油单元脱除环己胺ꎮ3.3㊀环己酮异常分析调控苯胺反应单元高负荷运行中ꎬ若氢油比控制持续较高ꎬ反应器逐步偏离正常调控ꎬ导致粗苯胺产品环己酮异常超标ꎬ而超出后续精制单元处理能力ꎬ最终也会使精产品中苯酚超标ꎮ解决方案:首先将反应单元氢油比控制降低ꎬ微调反应各项参数ꎬ核心是要控制环己酮在反应单元的生成ꎮ其次确认后续精致单元处理环己酮是否异常ꎬ环己酮与苯胺在真空㊁高温㊁干燥特定条件下ꎬ会转化为重组分席夫碱和水ꎬ该反应为可逆反应ꎻ排查精制单元换热器/水冷器是否存在列管泄漏ꎬ使水分进入ꎬ导致席夫碱水解(水分300ˑ10-6ꎬ环己酮转化率96.5%ꎻ水分600ˑ10-6ꎬ环己酮转化率94.7%ꎻ水分1000ˑ10-6ꎬ环己酮转化率93.1%)ꎬ致使环己酮超标ꎻ排查精制单元物料温度㊁压力㊁停留时间等运行参数是否异常ꎬ导致环己酮的转化受抑制ꎮ最后排查其他单元泥浆型屏蔽泵外漏情况ꎬ使不合格苯胺通过泵补苯胺管线反窜补苯胺储罐ꎬ然后经精致单元的泥浆型屏蔽泵内漏至系统内部ꎬ严重时可检修泵ꎬ并将泵补苯胺储罐排液置换清洗ꎮ3.4㊀苯酚异常分析调控粗苯胺产品中苯酚超标ꎬ导致精产品中苯酚超标ꎮ苯胺反应单元持续长时间高负荷运行ꎬ若氢油比控制持续较低ꎬ则导致氢气过量相对不足ꎬ此时添加催化剂量过多ꎬ会使催化剂活性偏高ꎬ副产物苯酚的含量将会升高ꎬ导致粗苯胺产品苯酚异常超标ꎮ解决方案:根据反应单元的不同负荷ꎬ合理控制反应器的氢油比ꎬ通过对反应器的微调ꎬ从源头上控制减少苯酚含量ꎮ反应单元负荷频繁调整ꎬ导致苯酚超标ꎮ若频繁的调整反应负荷ꎬ会影响苯胺生产的优化运行ꎬ导23 河南化工HENANCHEMICALINDUSTRY㊀㊀㊀㊀㊀㊀㊀㊀㊀㊀㊀㊀㊀2020年㊀第37卷致氢气单耗增加(影响成本节约指标)ꎬ能耗变高ꎮ副产物含量增加ꎬ影响苯胺产品指标质量ꎬ主要体现在精制单元苯酚㊁环己胺㊁环己酮的波动超标ꎮ解决方案:减少反应单元㊁精制单元负荷的频繁调整ꎬ保证 安稳长满优 运行ꎮ精制单元升降负荷操作速度过快ꎬ导致底部温度波动ꎮ精制单元升降负荷速度较快ꎬ塔底蒸汽流量调节不同步ꎬ造成塔底温度升高ꎬ部分苯酚随苯胺至塔顶采出ꎬ此外塔釜液位出现大幅度降低时ꎬ也会造成底部物料浓缩ꎬ焦油浓度和苯酚浓度快速增长ꎬ苯酚也会被大量蒸出ꎮ精制塔控制参数有温度㊁压力㊁液位㊁流量ꎬ压力对塔的影响也比较大ꎬ正常情况下ꎬ由于精制塔体积大ꎬ压力变化缓慢ꎬ不会出现突增突减的情况ꎬ压力变动往往发生在改变负荷的情况下ꎮ在精制单元提升高负荷时ꎬ精制塔压力上涨ꎬ塔压增高ꎬ塔内物料沸点高于设定值ꎬ塔间及塔底蒸汽使用量增加ꎬ导致底部温度升高ꎬ从而造成苯酚上蒸量增大ꎬ进入精馏段随顶部产品一起采出ꎬ导致精苯胺产品中苯酚超标ꎮ解决方案:精制单元调整负荷过程中ꎬ严格按照操作规程ꎬ精细升降负荷ꎬ注意脱水塔填料层平均温度ꎬ同步调节精制塔回流比及塔底蒸汽用量ꎬ严密监视温度参数的变化ꎬ焦油采出可适当高于正常负荷匹配值ꎬ待负荷稳定后再根据样品指标ꎬ焦油采出逐步与负荷匹配ꎬ避免塔器出现波动ꎬ保证产品合格ꎮ此外当产品指标异常时ꎬ塔回流比可适当增加ꎬ提高精馏效果ꎬ但会使蒸汽用量增大㊁单耗升高ꎬ不宜长时间维持ꎮ精制单元焦油采出量持续偏少ꎮ在精制单元正常稳定运行时ꎬ焦油采出量长时间低于正常负荷采出量ꎬ会造成精制塔塔底温度持续缓慢升高ꎬ底部物料被浓缩ꎬ苯酚持续累积ꎬ部分苯酚随苯胺蒸出至塔顶采出ꎮ解决方案:在精制单元平稳运行期间ꎬ焦油采出量不易长时间偏低ꎬ保持正常负荷采出量ꎬ对于精制单元不同的负荷ꎬ应合理控制焦油采出ꎮ精制单元精制塔蒸汽量控制偏离正常值ꎬ导致苯酚上蒸至产品中ꎮ若精制塔塔间及塔底再沸器蒸汽分配不均ꎬ底部蒸汽量过高ꎬ塔间蒸汽量偏少ꎬ会导致底部温度偏高ꎬ底部物料被浓缩ꎬ焦油浓度和苯酚浓度持续增长ꎬ部分苯酚随苯胺蒸出至塔顶采出ꎮ解决方案:对于精制塔控制ꎬ在落实回流比和蒸汽分配优化的基础上ꎬ要结合粗苯胺和精苯胺指标中苯酚含量ꎬ调节平衡塔间和塔底的蒸汽量及回流比ꎮ精制单元脱水塔和精制塔内填料损坏ꎬ导致苯酚脱出效果差ꎮ精制单元操作不当或者塔内填料质量问题ꎬ存在脱水塔和精制塔内填料损坏问题ꎬ会使苯酚脱出效果不佳ꎬ导致精苯胺产品中苯酚超标ꎮ解决方案:工艺人员要操作平稳ꎬ持续关注塔内压差变化ꎬ若确定为塔内填料损坏ꎬ则将装置停车处理ꎬ对塔清洗㊁置换㊁隔离ꎬ联系设备专业人员拆开人孔ꎬ进一步检查㊁检修或更换ꎮ3.5㊀环己醇异常分析调控苯胺反应单元持续长时间高负荷运行中ꎬ若氢油比控制持续较低ꎬ则导致氢气过量相对不足ꎬ此时添加催化剂量过多ꎬ会使反应器内催化剂的活性偏高ꎬ副产物苯酚升高ꎮ苯酚在催化剂的作用下ꎬ与氢气反应生成环己醇(可逆)ꎬ致使环己醇含量随之升高ꎮ而后续又无法除去环己醇ꎬ环己醇在系统内持续累积ꎬ最终导致精苯胺产品中环己醇超标ꎮ解决方案:在本工艺的选择中ꎬ环己醇的生成量很少ꎬ可根据反应单元的不同负荷ꎬ合理控制氢油比ꎬ通过对反应器的微调ꎬ从反应源头上控制减少环己醇生成ꎮ3.6㊀产品各指标超标富集处理在装置生产运行中ꎬ若通过各控制手段调节后ꎬ产品指标持续异常且有恶化现象ꎬ说明苯胺生产各单元内富集较多的副产物ꎬ造成生产紊乱ꎬ威胁装置的正常生产和产品指标ꎬ可采取积极妥善的应对措施ꎬ从精制单元脱水塔塔顶采出富集的轻组分ꎬ启用轻油单元处理ꎬ用来分离含有苯胺㊁水㊁环己胺㊁环己醇㊁苯等ꎬ以回收其中的重组分苯胺ꎬ降低不必要的苯胺浪费ꎬ外排环己胺㊁环己醇㊁苯等轻组分ꎬ维持工艺平稳运转ꎮ4㊀结论目前世界上最先进杜邦液相加氢技术ꎬ在运行生产中ꎬ会出现产品指标异常超控现象ꎬ要综合考虑ꎬ统筹调控ꎬ兼顾粗苯胺中副产物和硝基苯异常的相应措施ꎮ任何一个运行参数都不能单独进行分析调整ꎬ特别注意反应单元氢油比的控制ꎬ存在过加氢和转化率的矛盾点ꎮ只有反应单元控制稳定ꎬ调控关联所有的运行参数ꎬ才能从根源上消除隐患ꎬ保证精苯胺产品的合格稳定ꎮ本文研究硝基苯液相加氢技术副产物ꎬ分析异常情况及相应调控措施ꎬ使得产品更稳定㊁高质量和低成本ꎬ保证了生产 安稳长满优 的运行ꎮ33第8期㊀㊀㊀㊀㊀㊀㊀㊀㊀㊀㊀㊀㊀㊀贾崇顺:杜邦硝基苯液相加氢技术副产物研究。
增产航煤工艺改造及优化方案
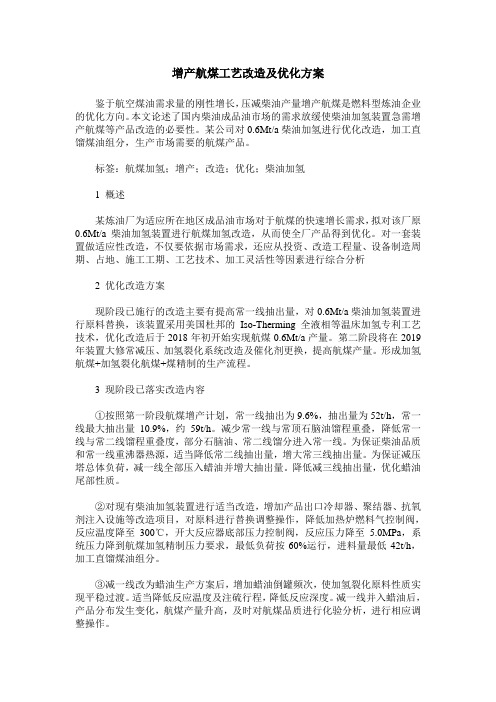
增产航煤工艺改造及优化方案鉴于航空煤油需求量的刚性增长,压减柴油产量增产航煤是燃料型炼油企业的优化方向。
本文论述了国内柴油成品油市场的需求放缓使柴油加氢装置急需增产航煤等产品改造的必要性。
某公司对0.6Mt/a柴油加氢进行优化改造,加工直馏煤油组分,生产市场需要的航煤产品。
标签:航煤加氢;增产;改造;优化;柴油加氢1 概述某炼油厂为适应所在地区成品油市场对于航煤的快速增长需求,拟对该厂原0.6Mt/a柴油加氢装置进行航煤加氢改造,从而使全厂产品得到优化。
对一套装置做适应性改造,不仅要依据市场需求,还应从投资、改造工程量、设备制造周期、占地、施工工期、工艺技术、加工灵活性等因素进行综合分析2 优化改造方案现阶段已施行的改造主要有提高常一线抽出量,对0.6Mt/a柴油加氢装置进行原料替换,该装置采用美国杜邦的Iso-Therming 全液相等温床加氢专利工艺技术,优化改造后于2018年初开始实现航煤0.6Mt/a产量。
第二阶段将在2019年装置大修常减压、加氢裂化系统改造及催化剂更换,提高航煤产量。
形成加氢航煤+加氢裂化航煤+煤精制的生产流程。
3 现阶段已落实改造内容①按照第一阶段航煤增产计划,常一线抽出为9.6%,抽出量为52t/h,常一线最大抽出量10.9%,约59t/h。
减少常一线与常顶石脑油馏程重叠,降低常一线与常二线馏程重叠度,部分石脑油、常二线馏分进入常一线。
为保证柴油品质和常一线重沸器热源,适当降低常二线抽出量,增大常三线抽出量。
为保证减压塔总体负荷,减一线全部压入蜡油并增大抽出量。
降低减三线抽出量,优化蜡油尾部性质。
②对现有柴油加氢装置进行适当改造,增加产品出口冷却器、聚结器、抗氧剂注入设施等改造项目,对原料进行替换调整操作,降低加热炉燃料气控制阀,反应温度降至300℃,开大反应器底部压力控制阀,反应压力降至5.0MPa,系统压力降到航煤加氢精制压力要求,最低负荷按60%运行,进料量最低42t/h,加工直馏煤油组分。
液相加氢系统运行控制策略

液相加氢系统运行控制策略摘要:在辛烯醛气相加氢催化剂运行至末期,反应热点位置会进一步上移,可能会出现辛烯醛加氢饱和不完全、辛醇产品的硫酸色度增高现象,此时需要增开液相加氢系统,保证辛烯醛加氢反应完全,以保证辛醇产品质量,延长装置运行周期。
本文探讨液相加氢系统运行控制策略,保证辛醇产品合格。
关键词:液相加氢运行控制辛醇1液相加氢系统工艺流程自液相加氢进料泵打出的粗辛醇流经辛醇液相加氢加热器进入液相加氢反应器,液相加氢反应器将产品中任何未饱和的物质进行加氢反应,到加热器的蒸汽流量由液相加氢反应器进料管线上的温度控制器控制。
高压氢气在压力控制器控制下进入液相加氢反应器与粗辛醇一起通过催化剂床层,液体产品流经辛醇过滤器过滤出任何催化剂颗粒,然后进入液相加氢分离器,过量的高压氢气在流量控制器的控制下从液相加氢反应器底部进入液相加氢分离器。
粗辛醇由液相加氢分离器液位与流量的串级调节进行控制,液相加氢分离器顶部出来的闪蒸气体进入辛烯醛气相加氢蒸发器的底部。
2 液相加氢系统运行控制辛烯醛气相加氢系统的操作是以连续运行为基础的。
装置负荷的变化系统流量随之调整。
通过观察每班操作的基础上进行控制,在不造成催化剂损坏的前提下,尽可能有效地进行调节和维持产量。
辛烯醛转化器中催化剂的性能和寿命取决于管程内从下到上的温度分布,这也依次取决于各种控制参数和这些变量为达到最佳性能而进行的正确组合。
2.1循环气流循环气流一方面作为蒸发有机物的载体,另一方面作为反应氢气,同时它还用于控制热点温度。
正常情况下,热点温度必须控制在200‑240℃的范围内。
循环气流量应加以调节使热点温度控制在上述范围内,同时随着进料流量的变化相应进行调节。
2.2辛烯醛转化器入口温度转化器的进料温度要保持在进料气体的露点温度以上,提高入口温度可以提高热点温度(入口温度升高10℃,相应热点温度也会升高10℃) 。
辛醇的硫酸色度主要由不饱和化合物的存在所致,例如2-乙基己醛(EHA),它是辛烯醛EPA只有一个双键加氢的产物,它是在低温条件下形成的,为避免这种情况,热点温度最好保持在200℃以上,并尽可能地接近辛烯醛转化器的入口温度。
1,4-丁二醇.doc

目前已工业化的1,4-丁二醇生产路线主要有以下几种:(1)雷珀法:以乙炔和甲醛为原料经合成和加氢二步生成1,4-丁二醇。
此法为生产1,4-丁二醇的传统方法。
经改良后采用硅酸铝为载体的乙炔铜催化剂,还加入了铋,以抑制聚合反应,这样克服了原有工艺的不足,反应温度均匀、质量稳定,安全性有了保证。
(2)丁二烯法:以丁二烯为原料生产1,4-丁二醇,已建成的生产装置有丁二烯乙酰氧基化法和丁二烯氯化法,但以前者为主。
二烯乙酰氧基化法于1970年由日本三菱化成公司首先实现工业化,生产工艺复杂,投资大,催化剂昂贵,水解过程蒸汽消耗量大,但原料易得,反应选择性高,1,4-丁二醇和四氢呋喃比例易调节。
(3)可乐丽法:以环氧丙烷为原料,先将环氧丙烷催化异构化成烯丙醇,在有机膦配位体催化剂作用下,进行氢甲酰化反应生成主产物4-羟基丁醛,然后进行萃取、加氢、精制得到1,4-丁二醇。
该反应投资低,流程简单,副产物利用价值高,铑系催化剂可循环使用,寿命长,1,4-丁二醇收率较高,蒸汽消耗低,氢甲酰化及加氢为液相反应,改变工艺负荷容易,可根据市场需求调节1,4-丁二醇产量。
(4)顺酐酯化加氢法:该工艺由英国戴维公司开发成功,通过调节工艺条件,可以改变1,4-丁二醇、γ-丁内酯、四氢呋喃比例。
工业装置中如要设计1,4-丁二醇产量达最大值,可依据1,4-丁二醇和γ-丁内酯之间的化学平衡,采取将γ-丁内酯循环,直至γ-丁内酯耗尽的方法,以使1,4-丁二醇产量达最大值。
其优点是酯的转化率较高,反应条件温和,设备材质要求不高,催化剂价格低,寿命长,投资和生产成本均较低,1,4-丁二醇和四氢呋喃比例调节范围宽。
(5)正丁烷-顺酐-1,4-丁二醇联合法:该工艺将正丁烷转化为顺酐的气相氧化法和顺酐加氢技术结合起来,仍以C4馏分为原料,整个流程包括顺酐生产、马来酸加氢及1,4-丁二醇精制。
该工艺只需要经过加氢和精制就能得到1,4-丁二醇,不需酯化工序,缩短了整个流程,减少了设备台数,相应降低了投资和操作维修费用,对顺酐纯度要求比较低。
投资和操作费用减少的加氢新工艺
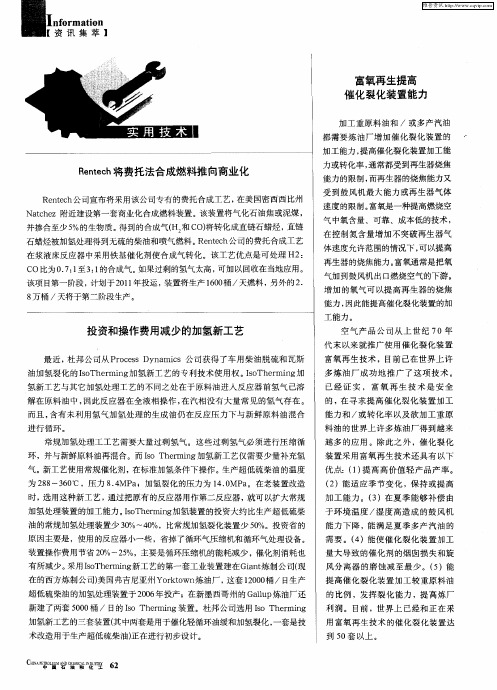
于环境温度 / 湿度高造成的鼓风机
能 力 下 降 , 满 足 夏 季 多 产 汽 油 的 能 需 要 。( ) 使 催 化 裂 化 装 置 加 工 4 能 量 大 导 致 的催 化 剂 的 烟 囱损 失和 旋
R neh e tc 公司 宣布将 采 用该 公司 专有 的费托 合成 工艺 , 在美 国密 西西 比州
力或转化率 , 通常都受到再生器烧焦
能力 的限 制 , 而再 生器 的烧 焦能 力又
受到鼓风机最大 能力或再生器气体 速度的限制。 富氧是一种提高燃烧空
气 中氧含 量 、可靠 、成 本低 的技 术 ,
8 桶 /天将于 第二 阶段 生产 。 万
在控制氮含量增加不突破再生器气
体速度允许范围的情况下 , 以提高 可
再 生器 的烧 焦能 力 。 氧通 常是把 氧 富
气加到鼓风机出口燃烧空气的下游。
增加 的氧 气 可 以提 高 再 生 器 的烧 焦 能力 , 因此 能提高 催化 裂化 装置 的加
油的常规加氢处理装置少 3 %~4 %,比常规加氢裂化装置少 5%。投资省的 0 0 0
原 因主 要是 ,使用 的反 应器小 一 些 ,省 掉 了循环 气压 缩机 和循 环气 处理 设备 。 装置操 作费 用 节省 2% 2%, 0 5 主要 是循 环压 缩机 的能 耗减 少 , 催化 剂消 耗也 有所 减少 。 采用 I T emig 工艺 的第一 套 工业 装置 建在 G a t 制公 司( s hr n 新 o i 炼 n 现 在的 西方 炼制 公 司) 国弗吉 尼亚 州 Y r twn 油厂 , 套 10 0 /日生产 美 oko 炼 这 20 桶
苯胺生产技术及国内苯胺装置概况
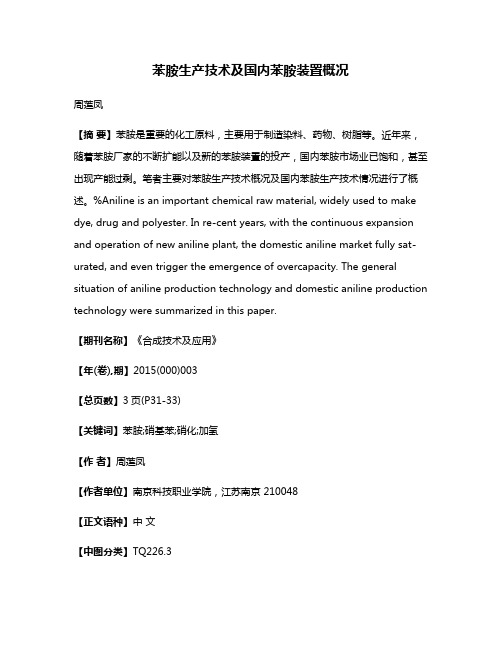
苯胺生产技术及国内苯胺装置概况周莲凤【摘要】苯胺是重要的化工原料,主要用于制造染料、药物、树脂等。
近年来,随着苯胺厂家的不断扩能以及新的苯胺装置的投产,国内苯胺市场业已饱和,甚至出现产能过剩。
笔者主要对苯胺生产技术概况及国内苯胺生产技术情况进行了概述。
%Aniline is an important chemical raw material, widely used to make dye, drug and polyester. In re-cent years, with the continuous expansion and operation of new aniline plant, the domestic aniline market fully sat-urated, and even trigger the emergence of overcapacity. The general situation of aniline production technology and domestic aniline production technology were summarized in this paper.【期刊名称】《合成技术及应用》【年(卷),期】2015(000)003【总页数】3页(P31-33)【关键词】苯胺;硝基苯;硝化;加氢【作者】周莲凤【作者单位】南京科技职业学院,江苏南京 210048【正文语种】中文【中图分类】TQ226.3苯胺是重要的化工原料,主要用于制造染料、药物、树脂,还可以用作橡胶硫化促进剂等,也可作为黑色染料使用。
苯胺制得的化工产品和中间体有300多种,是作为生产聚氨脂产品主要原料MDI(二苯基甲基二异氰酸脂)的重要原料,随着MDI的快速发展,使苯胺需求增长很快。
近年来,随着苯胺厂家的不断扩能以及新的苯胺装置的投产,国内苯胺的市场业已饱和,甚至产能过剩,国内商品苯胺市场呈现严酷的竞争[1],冲击最大的将是规模较小、原材料配套不足尤其是氢气成本较高、没有下游产业链的装置,因此不断更新生产技术,降低物耗、能耗,才能立足市场。