耐热混凝土配合比设计及性能检验规程
混凝土原材料及配合比检验质量标准和检验方法

混凝土原材料及配合比检验质量标准和检验方法注:1、将所取样品充分混合后通过0。
9mm方孔篩,均分为试验样和封存样,封存样加封条,密封保管3个月。
2、安定性:体积安定性不良主要是指水泥硬化和产生不均匀的体积变化。
一般是由于熟料中所含的游离氧化钙、游离氧化镁、或掺入的石膏过多。
3、不合格品和废品:凡氧化镁、三氧化硫、初凝时间、安定性中任一项不符合标准规定时,均为废品;凡细度、终凝时间中的任一项不符合标准规定或混合材料掺加量超过最大限和强度低于商品强度等级的指标时为不合格品.水泥包装标志中水泥品种、强度等级、生产者名称和出厂编号不全的也属于不合格品。
4、混凝土的取样:每100盘,且不超过100m3的同配合比的混凝土,取样次数不得少于一次;每一工作班拌制的同配合比的混凝土不足100盘时,其取样次数不得少于一次;一次浇筑1000m3以上同配合比的混凝土,每200m3取样次数不得少于一次;每层楼或每工作台班浇筑浇筑同配合比的混凝土时,其取样次数不得少于一次.混凝土抽样在浇筑地点随机抽取。
混凝土施工工程质量检验标准及检验方法现浇混凝土结构外观质量和尺寸偏差检验标准及检测方法现浇结构外观质量缺陷注:用于检查结构构件混凝土强度的试件,应在混凝土的浇筑地点随机取样,取样与留置应符合下列规定:①每拌制100盘且不超过100m3的同配合比混凝土,取样不得少于一次。
②每工作班拌制的同一配合比混凝土不足100盘时,取样不得少于一次。
③每一次浇筑超过1000m3时,同一配合比的混凝土每200m3取样不得少于一次.④每一楼层、同配合比的混凝土,取样不得少于一次。
⑤每次取样至少留置一组标准养护试件,同条件养护试件的留置组数应根据实际需要确定。
预应力原材料质量检验标准和检查方法预应力筋制作与安装工程质量检验标准和检测方法预应力张拉、放张、灌浆及封锚工程质量检验标准与检查方法。
普通混凝土配合比设计规程JGJ_55-2011_
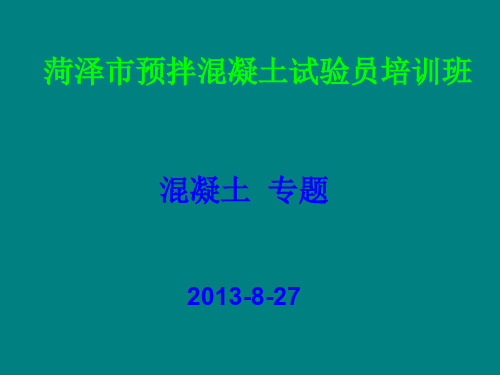
混凝土的耐久性
• 耐久性的概念:砼抵抗所处环境的 作用破坏的能力,如温度、湿度, 化学侵蚀介质等。 • 环境对砼的作用: • ①物理作用如冻融、渗透以及磨蚀, 空蚀等; • ②化学作用,如各种酸、碱、侵蚀, 碳化、碱集料反应以及砼中的钢筋 锈蚀等。
耐久性类型
–1)混凝土的抗渗性 –2)混凝土的抗冻性 –3)混凝土抗侵蚀性 –4)混凝土的碳化 –5)混凝土的碱---骨料反应
–混凝土按功能及用途分类
»如结构混凝土、防水混 凝土、耐热混凝土、耐 酸混凝土、纤维混凝土 和聚合物混凝土。
混凝土的优点
一、作为主要的建筑材料之一,混凝土 的原料丰富,经久耐用,节约能源,价格 较金属、木材和塑料便宜。
二、其它长处: 1、因需配制;2、因需成形;
水泥选择
• (1)水泥品种选择 • 根据砼所要求的性能指标及所处的环
• 砂浆是由胶凝材料、细骨料加水拌 和后,经一定时间硬化而成的人造 复合固体材料,又称无粗骨料混凝 土。
分类
混凝土按照表观密度大小分为三类: • (1)重混凝土(0>2500Kg/M3) • (2)普通混凝土 (0=1900~2500Kg/M3) • (3)轻混凝土(0<1900Kg/M3) »①轻骨料混凝土 »②多孔混凝土(泡沫混凝土、 加气混凝土) »③无砂大孔混凝土
——按流动性分类:
干硬性混凝土 流动性混凝土 自流平(自密实)混凝土 泵送混凝土
混凝土按强度等级可分为:
»①普通混凝土:强度等级为 C7.5-C60;
»②高强混凝土:强度等级为 C60-000;
»③超高强混凝土:强度等级大 于C100。
——按胶凝材料分类:
水泥混凝土、石膏混凝土、沥青 混凝土、水玻璃混凝土、碱矿渣 混凝土、聚合物混凝土。
混凝土配合比和砂浆配合比检测方案
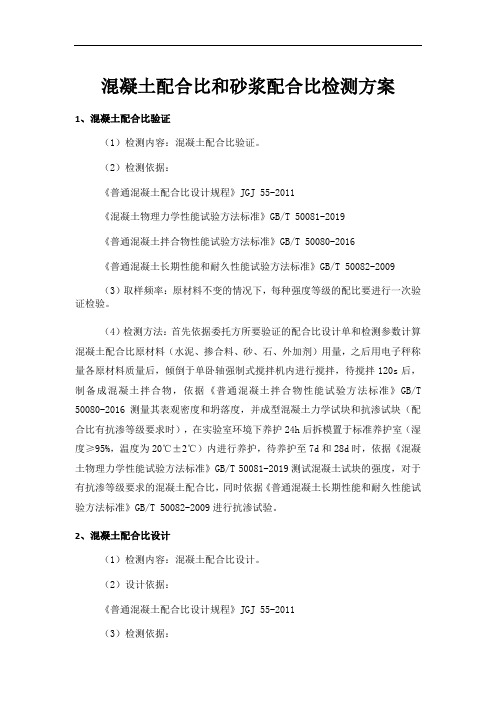
混凝土配合比和砂浆配合比检测方案1、混凝土配合比验证(1)检测内容:混凝土配合比验证。
(2)检测依据:《普通混凝土配合比设计规程》JGJ 55-2011《混凝土物理力学性能试验方法标准》GB/T 50081-2019《普通混凝土拌合物性能试验方法标准》GB/T 50080-2016《普通混凝土长期性能和耐久性能试验方法标准》GB/T 50082-2009(3)取样频率:原材料不变的情况下,每种强度等级的配比要进行一次验证检验。
(4)检测方法:首先依据委托方所要验证的配合比设计单和检测参数计算混凝土配合比原材料(水泥、掺合料、砂、石、外加剂)用量,之后用电子秤称量各原材料质量后,倾倒于单卧轴强制式搅拌机内进行搅拌,待搅拌120s后,制备成混凝土拌合物,依据《普通混凝土拌合物性能试验方法标准》GB/T 50080-2016测量其表观密度和坍落度,并成型混凝土力学试块和抗渗试块(配合比有抗渗等级要求时),在实验室环境下养护24h后拆模置于标准养护室(湿度≥95%,温度为20℃±2℃)内进行养护,待养护至7d和28d时,依据《混凝土物理力学性能试验方法标准》GB/T 50081-2019测试混凝土试块的强度,对于有抗渗等级要求的混凝土配合比,同时依据《普通混凝土长期性能和耐久性能试验方法标准》GB/T 50082-2009进行抗渗试验。
2、混凝土配合比设计(1)检测内容:混凝土配合比设计。
(2)设计依据:《普通混凝土配合比设计规程》JGJ 55-2011(3)检测依据:《混凝土物理力学性能试验方法标准》GB/T 50081-2019《普通混凝土拌合物性能试验方法标准》GB/T 50080-2016《普通混凝土长期性能和耐久性能试验方法标准》GB/T 50082-2009(4)设计和检测方法:a.配合比设计的基本资料:明确配合比设计所要求的技术指标,如强度、工作性、耐久性等;明确所用原材料的品质及技术性能指标,如水泥品种及强度等级、密度等,砂的细度模数及级配,石子种类、最大粒径及级配,掺合料品种和活性,外加剂种类和减水率。
钢渣热泼中耐热混凝土的应用
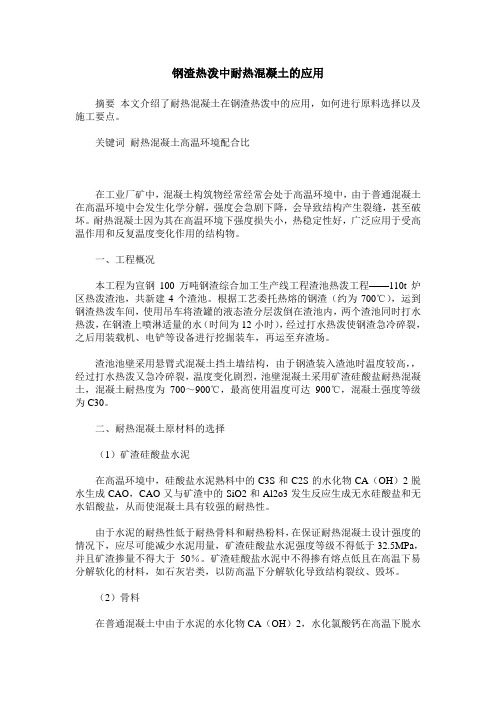
钢渣热泼中耐热混凝土的应用摘要本文介绍了耐热混凝土在钢渣热泼中的应用,如何进行原料选择以及施工要点。
关键词耐热混凝土高温环境配合比在工业厂矿中,混凝土构筑物经常经常会处于高温环境中,由于普通混凝土在高温环境中会发生化学分解,强度会急剧下降,会导致结构产生裂缝,甚至破坏。
耐热混凝土因为其在高温环境下强度损失小,热稳定性好,广泛应用于受高温作用和反复温度变化作用的结构物。
一、工程概况本工程为宣钢100万吨钢渣综合加工生产线工程渣池热泼工程——110t炉区热泼渣池,共新建4个渣池。
根据工艺委托热熔的钢渣(约为700℃),运到钢渣热泼车间,使用吊车将渣罐的液态渣分层泼倒在渣池内,两个渣池同时打水热泼,在钢渣上喷淋适量的水(时间为12小时),经过打水热泼使钢渣急冷碎裂,之后用装载机、电铲等设备进行挖掘装车,再运至弃渣场。
渣池池壁采用悬臂式混凝土挡土墙结构,由于钢渣装入渣池时温度较高,,经过打水热泼又急冷碎裂,温度变化剧烈,池壁混凝土采用矿渣硅酸盐耐热混凝土,混凝土耐热度为700~900℃,最高使用温度可达900℃,混凝土强度等级为C30。
二、耐热混凝土原材料的选择(1)矿渣硅酸盐水泥在高温环境中,硅酸盐水泥熟料中的C3S和C2S的水化物CA(OH)2脱水生成CAO,CAO又与矿渣中的SiO2和Al2o3发生反应生成无水硅酸盐和无水铝酸盐,从而使混凝土具有较强的耐热性。
由于水泥的耐热性低于耐热骨料和耐热粉料,在保证耐热混凝土设计强度的情况下,应尽可能减少水泥用量,矿渣硅酸盐水泥强度等级不得低于32.5MPa,并且矿渣掺量不得大于50%。
矿渣硅酸盐水泥中不得掺有熔点低且在高温下易分解软化的材料,如石灰岩类,以防高温下分解软化导致结构裂纹、毁坏。
(2)骨料在普通混凝土中由于水泥的水化物CA(OH)2,水化氯酸钙在高温下脱水导致混凝土碎裂;并且骨料中的石灰石、石英砂在高温环境下体积变形较大,会导致混凝土结构破坏或强度降低。
c35耐热混凝土配合比优化设计
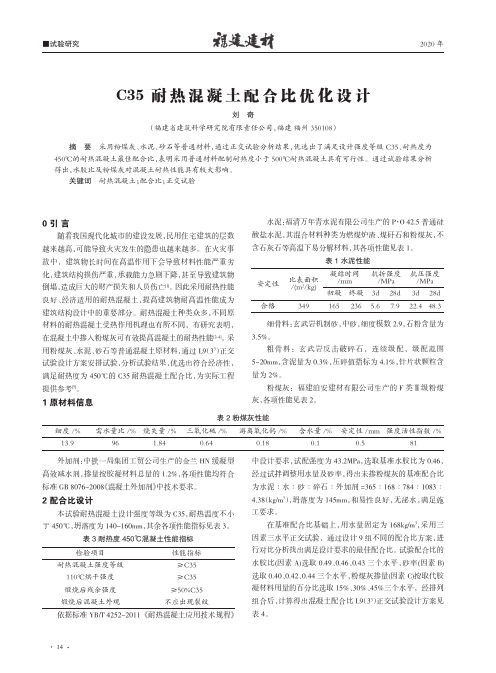
合格
349 165 236 5.6 7.9 22.4 48.3
细骨料:玄武岩机制砂,中砂,细度模数 2.9,石粉含量为 3.5%。
粗骨料:玄武岩反击破碎石,连续级配,级配范围 5~20mm,含泥量为 0.3%,压碎值指标为 4.1%,针片状颗粒含 量为 2%。
粉煤灰:福建泊安建材有限公司生产的 F类Ⅱ级粉煤 灰,各项性能见表 2。
Hale Waihona Puke 第 3期(总第 227期)
试验研究■
编号
1 2 3 4 5 6 7 8 9
水胶比 砂率 /%
(A1)0.49 (A1)0.49 (A1)0.49 (A2)0.46 (A2)0.46 (A2)0.46 (A3)0.43 (A3)0.43 (A3)0.43
(B1)40 (B2)42 (B3)44 (B1)40 (B2)42 (B3)44 (B1)40 (B2)42 (B3)44
中设计要求,试配强度为 43.2MPa,选取基准水胶比为 0.46, 经过试拌调整用水量及砂率,得出未掺粉煤灰的基准配合比 为水泥∶水∶砂∶碎石∶外加剂 =365∶168∶784∶1083∶ 4.38(kg/m3),坍落度为 145mm,和易性良好,无泌水,满足施 工要求。
在基准配合比基础上,用水量固定为 168kg/m3,采用三 因素三水平正交试验,通过设计 9组不同的配合比方案,进 行对比分析找出满足设计要求的最佳配合比。试验配合比的 水胶比(因素 A)选取 0.49、0.46、0.43三个水平,砂率(因素 B) 选取 0.40、0.42、0.44三个水平,粉煤灰掺量(因素 C)按取代胶 凝材料用量的百分比选取 15%、30%、45%三个水平,经排列 组合后,计算得出混凝土配合比 L9(33)正交试验设计方案见 表 4。
耐高温混凝土配合比设计

耐高温混凝土配合比设计一、混凝土材料受热后作用机理大量研究表明混凝土在高温受热下的退化主要表现在:混凝土表观密度降低;形成大量的孔和和裂缝以及强度和弹性模量的下降。
受热作用主要分为两个方面:1、水泥水化产物受热作用机理;2、骨料受热作用机理;3、水泥石和骨料界面受热作用机理。
水泥水化产物受热作用具体过程如下:100℃时毛细孔开始失水;100-150℃时由于水蒸气蒸发促进熟料逐步水化使混凝土抗压强度增加;200-300℃水泥水化产物水化硅酸钙凝体脱水导致组织硬化;300℃以上由于脱水加剧混凝土收缩开始出现裂纹,强度开始下降;575℃氢氧化钙脱水使水泥组织破坏,900℃混凝土中的碳酸钙分解。
普通硅酸盐水泥配制的混凝土在900℃时游离水、结晶水及水化物的脱水基本结束,混凝土强度几乎丧失。
同时必须注意由于氢氧化钙的脱水,碳酸钙的分解,混凝土中生成了氧化钙,氧化钙会吸收空气中的水分,再次水化导致体积膨胀产生混凝土表面酥松剥落现象,此外高温改变了钙矾石的形成机理,使混凝土内部形成粗大的孔结构。
各种岩石成分的骨料,受热变形也不相同。
含有石英岩的骨料(如石英砂、砂岩等石英质骨料),在575℃以下,体积逐渐膨胀,而在575℃时,突然膨胀;含有石灰岩的材料,在750─900℃条件下分解成氧化钙,强度显著降低故普通混凝土不宜在高温环境下使用,其使用温度一般也不超过250℃。
300℃时混凝土中的骨料开始膨胀,随着温度的继续升高,水泥收缩和骨料膨胀加剧,两者结合被破坏产生界面破坏,伴随着水泥水化产物的受热破坏以及骨料的晶型转换,界面破坏加剧。
同时由于混凝土表面温度升高比内部快得多以及骨料和水泥石之间的热不相容造成的内外温差和应力差也会引起混凝土开裂和强度下降。
二、耐热混凝土配合比设计要点依据上述混凝土材料受热后作用机理可以得出配合比设计要点:1、水泥品种的选择按照设计目标,本次混凝土耐热度在700℃,为确保安全实际研究过程中提高至750℃,基本已经达到了硅酸盐水泥耐热混凝土温度上限。
M新标准:TB10424-2010(砼耐久性 及 配合比设计 摘要 与160号对比)

表 D.0.2 氯盐环境下混凝土抗氯离子渗透性能
评价指标
环境作用等级
100 年
60 年
L1
混凝土氯离子扩散系数(56d)
DRCM (×10-12m2/s)
L2
L3
≤7
≤10
≤5
≤8
≤3Leabharlann ≤4(原标准铁建设[2005]160 号规定)氯盐环境下混凝土的电通量
设计使用年限级别
一(100 年)
二(60 年)、三(30 年)
环境下,素混凝土最大水胶比不应超过 0.55,最小胶凝材料用量不应低于 280kg/m3。
注:(盐类结晶 破坏环境)为新增加的环境类别
检验数量:施工单位对每一混凝土配合比进行一次计算;监理单
位全部检查。
检验方法:施工单位计算;监理单位检查计算单。
6
表 6.4.9-1 不同混凝土潮湿养护的最低期限
大气潮湿(RH ≥50%), 大气干燥(20%≤RH <50%), 大气极端干燥(RH<20%),
11
56d 抗硫酸盐结晶 《普通混凝土长期性能和耐久性 仅对盐类结晶破坏环境的
破坏等级
能试验方法标准》(GB/T 50082) 混凝土
12 胶凝材料抗蚀系数
见附录 F
仅对硫酸盐化学侵蚀环境 的混凝土
13
抗渗等级
仅对隧道衬砌混凝土
仅对无砟轨道底座板混凝
14
收缩
《普通混凝土长期性能和耐久性 土、双块式轨枕道床板混凝 能试验方法标准》(GB/T 50082) 土、自密实混凝土和预应力
铁路混凝土工程施工质量验收标准 TB10424-2010(摘要 与 对比)
附录 D 混凝土的耐久性指标
混凝土配合比配置比例及调配办法
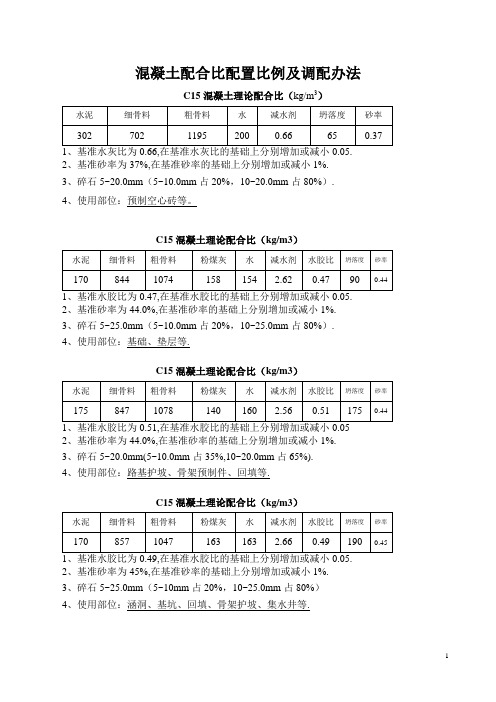
混凝土配合比配置比例及调配办法C15混凝土理论配合比(kg/m3)2、基准砂率为37%,在基准砂率的基础上分别增加或减小1%.3、碎石5~20.0mm(5~10.0mm占20%,10~20.0mm占80%).4、使用部位:预制空心砖等。
C15混凝土理论配合比(kg/m3)2、基准砂率为44.0%,在基准砂率的基础上分别增加或减小1%.3、碎石5~25.0mm(5~10.0mm占20%,10~25.0mm占80%).4、使用部位:基础、垫层等.C15混凝土理论配合比(kg/m3)2、基准砂率为44.0%,在基准砂率的基础上分别增加或减小1%.3、碎石5~20.0mm(5~10.0mm占35%,10~20.0mm占65%).4、使用部位:路基护坡、骨架预制件、回填等.C15混凝土理论配合比(kg/m3)2、基准砂率为45%,在基准砂率的基础上分别增加或减小1%.3、碎石5~25.0mm(5~10mm占20%,10~25.0mm占80%)4、使用部位:涵洞、基坑、回填、骨架护坡、集水井等.CFG桩C20混凝土理论配合比(kg/m3)2、基准砂率为44%,在基准砂率的基础上分别增加或减小1%.3、碎石5~25.0mm(5~10.0mm占20%,10~25.0mm占80%).4、使用部位:CFG桩.CFG桩C20混凝土理论配合比(kg/m3)2、基准砂率为44%,在基准砂率的基础上分别增加或减小1%.3、碎石5~25.0mm(5~10.0mm占20%,10~25.0mm占80%). F类粉煤灰.4、使用部位:CFG桩.32、基准砂率为49%,在基准砂率的基础上分别增加或减小1%.3、碎石5~20.0mm(5~10.0mm占20%,10~20.0mm占80%).4、使用部位:CFG桩.C20混凝土理论配合比(kg/m3)2、基准砂率为37%,在基准砂率的基础上分别增加或减小1%.3、碎石5~20.0mm(5~10mm占20%,10~20.0mm占80%)4、使用部位:侧沟、预制盖板等.2、基准砂率为44.0%,在基准砂率的基础上分别增加或减小1%.3、碎石5~25.0mm(5~10mm占20%,10~25.0mm占80%)4、使用部位:涵洞、垫层、翼墙、侧沟等.C20混凝土理论配合比(kg/m3)2、基准砂率为44.0%,在基准砂率的基础上分别增加或减小1%.3、碎石5~25.0mm(5~10mm占20%,10~25.0mm占80%)4、使用部位:箱涵框架基础等.C20 混凝土理论配合比(kg/m3)2、基准砂率为43.5%,在基准砂率的基础上分别增加或减小1%.3、碎石5~20.0mm(5~10.0mm占35%,10~20.0mm占65%).4、使用部位:基础、侧沟、回填等.C20 混凝土理论配合比(kg/m3)2、基准砂率为44.0%,在基准砂率的基础上分别增加或减小1%.3、碎石5~25.0mm(5~10mm占20%,10~25.0mm占80%).4、使用部位:涵洞、垫层、翼墙、侧沟等.2、基准砂率为45.0%,在基准砂率的基础上分别增加或减小1%.3、碎石5~25.0mm(5~10mm占20%,10~25.0mm占80%).4、使用部位:水沟、盖板、挖孔桩护壁、填充等.高性能混凝土(C25)配合比(kg/m3)2、基准砂率为47.0%.3、碎石5~10.0mm.4、使用部位:预制防护栅栏等.5、只调掺合料比例.C25 混凝土理论配合比(kg/m3)2、基准砂率为43.5%,在基准砂率的基础上分别增加或减小1%.3、碎石5~25.0mm(5~10mm占20%,10~25.0mm占80%).4、使用部位:基础、垫层等.C25 混凝土理论配合比(kg/m3)2、基准砂率为44.0%,在基准砂率的基础上分别增加或减小1%.3、碎石5~20.0mm(5~10.0mm占35%,10~20.0mm占65%).4、使用部位:路基面找平、挡墙、侧沟及盖板、基础回填等.31、基准砂率为50.0%,在基准砂率的基础上分别增加或减小1%.2、基准水胶比为0.40,在基准水胶比的基础上分别增加或减小0.05.3、碎石5~10.0mm.4、使用部位:仰拱﹑初期支护等.C25混凝土理论配合比(kg/m3)2、基准砂率为45.0%,在基准砂率的基础上分别增加或减小1%.3、碎石5~25.0mm(5~10mm占20%,10~25.0mm占80%). 粉煤灰:Ⅰ级.4、使用部位:水沟、盖板、挖孔桩护壁、填充等.高性能混凝土(C30)配合比(kg/m3)2、基准砂率为42.0%.3、碎石5~25.0mm(5~10mm占20%,10~25.0mm占80%).4、使用部位:承台、涵洞.5、只调胶凝材料比例.水下混凝土高性能混凝土(C30)配合比(kg/m3)1、基准水胶比为0.38.2、基准砂率为42.0%.3、碎石5~25.0mm(5~10mm占20%,10~25.0mm占80%).4、使用部位:桩基.5、只调胶凝材料比例.6、水下混凝土配制强度需要提高10%~20%,取15%.例:C30:fcu,0=(30.0+1.645×4.5)×(1+0.15)=43.0MPa.高性能混凝土(C30)配合比(kg/m3)1、基准水胶比为0.41.2、基准砂率为43.0%.3、碎石5~25.0mm(5~10mm占20%,10~25.0mm占80%).4、使用部位:承台.5、只调胶凝材料比例.水下混凝土高性能混凝土(C30)配合比(kg/m3)1、基准水胶比为0.41.2、基准砂率为45.0%.3、碎石5~25.0mm(5~10mm占20%,10~25.0mm占80%).4、使用部位:桩基.5、只调胶凝材料比例.6、水下混凝土配制强度需要提高10%~20%,取15%.例:C30:fcu,0=(30.0+1.645×4.5)×(1+0.15)=43.0MPa. 水下混凝土高性能混凝土(C30)配合比(kg/m3)1、基准水胶比为0.40.2、基准砂率为44.0%.3、碎石5~25.0mm(5~10mm占20%,10~25.0mm占80%).4、使用部位:桩基.5、只调胶凝材料比例.6、水下混凝土配制强度需要提高10%~20%,取15%.例:C30:fcu,0=(30.0+1.645×4.5)×(1+0.15)=43.0MPa.高性能混凝土(C30)配合比(kg/m3)1、基准水胶比为0.41.2、基准砂率为43.0%.3、碎石5~25.0mm(5~10mm占20%,10~25.0mm占80%).4、使用部位:承台.5、只调胶凝材料比例.高性能混凝土(C30)配合比(kg/m3)1、基准水胶比为0.38.2、基准砂率为47.0%.3、碎石5~10.0mm..4、使用部位:预制电缆槽、栅栏、声屏障等.5、只调胶凝材料比例.高性能混凝土(C30)配合比(kg/m3)1、基准水胶比为0.38.2、基准砂率为43.0%.3、碎石5~25.0mm(5~10mm占20%,10~25.0mm占80%).4、使用部位:承台.5、只调胶凝材料比例.水下混凝土高性能混凝土(C30)配合比(kg/m3)1、基准水胶比为0.38.2、基准砂率为44.0%.3、碎石5~25.0mm(5~10mm占20%,10~25.0mm占80%).4、使用部位:桩基、明挖基础.5、只调胶凝材料比例.6、水下混凝土配制强度需要提高10%~20%,取15%.例:C30:fcu,0=(30.0+1.645×4.5)×(1+0.15)=43.0MPa.高性能混凝土(C30)配合比(kg/m3)1、基准水胶比为0.38.2、基准砂率为42.0%.3、碎石5~20.0mm(5~10.0mm占35%,10~20.0mm占65%).4、使用部位:承台、基础等.5、只调胶凝材料比例.水下混凝土高性能混凝土(C30)配合比(kg/m3)1、基准水胶比为0.37.2、基准砂率为43.0%.3、碎石5~20.0mm(5~10.0mm占35%,10~20.0mm占65%).4、使用部位:承台、基础等.5、水下混凝土配制强度需要提高10%~20%,取15%.例:C30:fcu,0=(30.0+1.645×4.5)×(1+0.15)=43.0MPa.高性能混凝土(C30)配合比(kg/m3)1、基准水胶比为0.38.2、基准砂率为42.0%.3、碎石5~25.0mm(5~10mm占20%,10~25.0mm占80%).4、使用部位:承台、涵洞.5、只调胶凝材料比例.水下混凝土高性能混凝土(C30)配合比(kg/m3)1、基准水胶比为0.38.2、基准砂率为44.0%.3、碎石5~25.0mm(5~10mm占20%,10~25.0mm占80%).4、使用部位:桩基..5、水下混凝土配制强度需要提高10%~20%,取15%.例:C30:fcu,0=(30.0+1.645×4.5)×(1+0.15)=43.0MPa.高性能混凝土(C35)配合比(kg/m3)1、基准水胶比为0.38.2、基准砂率为42.0%.3、碎石5~25.0mm(5~10mm占20%,10~25.0mm占80%).4、使用部位:承台、墩身、顶帽、托盘、涵洞.5、只调胶凝材料比例.高性能混凝土(C35)配合比(kg/m3)1、基准水胶比为0.39. 环境作用等级为T2.2、基准砂率为43.0%.3、碎石5~25.0mm(5~10mm占20%,10~25.0mm占80%).4、使用部位:承台、墩身、顶帽、托盘、支承垫石.5、只调胶凝材料比例. *:外掺料.防腐承台高性能混凝土(C35)配合比(kg/m3)1、基准水胶比为0.38. 环境作用等级为H1(二氧化碳侵蚀).2、基准砂率为45.0%. *:内掺料属胶凝材料.3、碎石5~25.0mm(5~10mm占20%,10~25.0mm占80%).4、使用部位:承台、墩身、顶帽、托盘等.5、只调胶凝材料比例. *:内掺料,属胶凝材料.水下混凝土高性能混凝土(C35)配合比(kg/m3)1、基准水胶比为0.38. 环境作用等级为H1.2、基准砂率为44.0%. *:内掺料属胶凝材料.3、碎石5~25.0mm(5~10mm占20%,10~25.0mm占80%).4、使用部位:桩基.5、只调胶凝材料比例. *:内掺料,属胶凝材料.6、水下混凝土配制强度需要提高10%~20%,取15%.例:C35:fcu,0=(35.0+1.645×4.5)×(1+0.15)=48.8MPa.高性能混凝土(C35)配合比(kg/m3)1、基准水胶比为0.40. 环境作用等级为T2.2、基准砂率为43.0%.3、碎石5~25.0mm(5~10mm占20%,10~25.0mm占80%).4、使用部位:承台、墩身、顶帽、托盘、支承垫石.5、只调胶凝材料比例.防腐承台高性能混凝土(C35)配合比(kg/m3)1、基准水胶比为0.39. 环境作用等级为H1(二氧化碳侵蚀).2、基准砂率为43.0%. *:内掺料,属胶凝材料.3、碎石5~25.0mm(5~10mm占20%,10~25.0mm占80%).4、使用部位:承台、墩身、顶帽、托盘等.5、只调胶凝材料比例. 水下混凝土高性能混凝土(C35)配合比(kg/m3)1、基准水胶比为0.39. 环境作用等级为H1.2、基准砂率为44.0%. *:内掺料属胶凝材料.3、碎石5~25.0mm(5~10mm占20%,10~25.0mm占80%).4、使用部位:桩基.5、只调胶凝材料比例.6、水下混凝土配制强度需要提高10%~20%,取15%.例:C35:fcu,0=(35.0+1.645×4.5)×(1+0.15)=48.8MPa.防腐承台高性能混凝土(C35)配合比(kg/m3)1、基准水胶比为0.38. 环境作用等级为H1(二氧化碳侵蚀).2、基准砂率为42.0%. *:内掺料属胶凝材料.3、碎石5~25.0mm(5~10mm占20%,10~25.0mm占80%).4、使用部位:承台、墩身、顶帽、托盘.5、只调胶凝材料比例.高性能混凝土(C35)配合比(kg/m3)1、基准水胶比为0.38. 环境作用等级为T2.2、基准砂率为43.0%.3、碎石5~25.0mm(5~10mm占20%,10~25.0mm占80%).4、使用部位:墩台身、顶帽、托盘.5、只调胶凝材料比例.高性能混凝土(C35)配合比(kg/m3)1、基准水胶比为0.37. 环境作用等级为T2.2、基准砂率为43.0%.3、碎石5~20.0mm(5~10.0mm占35%,10~20.0mm占65%).4、使用部位:基础、墩台身、顶帽、托盘等.5、只调胶凝材料比例.防水混凝土高性能混凝土(C35)配合比(kg/m3)1、基准水胶比为0.38,在基准水胶比的基础上分别增加或减小0.2。
JGJ55-2011普通混凝土配合比设计规程2012

试
配
1、 试配时应采用与工程现场相同的原 材料和搅拌方法,且每盘最小搅拌量 不少于搅拌机额定量的25%; 2、按理论配合比试拌,并根据拌合物性 能作出调整(保证水胶比不变,调整 用水量或砂率),使混凝土拌合物性 能符合设计和施工要求,得出强度试 验用的试拌配合比;
3、应采用三个水胶比进行试配,水胶比在试拌 配合比基础上±0.05,用水量相同,砂率可相 应增减1%; (A) 试拌配合比(B) (C) W/B+0.05 W/B W/B-0.05 w w w βs+1% βs βs-1%
计算水胶比W/B
近年来水泥中多加入不同的掺合料, 有效胶凝材料含量不确定性较大,故配 合比设计的水灰比难以反映有效成分的 影响。因此改用胶凝材料总量作水胶比 及各种含量的控制。
计算水胶比W/B
当混凝土强度等级小于C60时 W/B=( αa · fb)/(fcu.0+ αa ·αb · f b)
砼强度与胶水比成正比(fcu=A×B/W+C ), 大等于 C60 时由于胶凝材料的水化程度不同, 强度与胶水比的关系不能再延伸,即线性关系较 差,分散性较大,故该公式仅适用于强度等级 小于C60的混凝土。
计算每立方米混凝土胶凝材料、矿物 掺合料和水泥用量 1、胶凝材料用量 mb0=
mw0/(W/B)
考虑混凝土满足耐久性要求所必要 的最小胶凝材料用量,除C15及其以 下等级外,应符合本标准中表3.0.4的 规定。
2、矿物掺合料用量mf0= mb0 βf
βf—矿物掺合料掺量(%),可按表 3.0.5确定
1、fb为胶凝材料28天胶砂抗压强度实测值或 按式5.1.3计算 fb=γf · γs· fce γf 、γs分别为粉煤灰和矿渣粉影响系数,按 表5.1.3选用 2、 fce为28天抗压强度实测值或富余系数乘 以水泥抗压强度标准值 ,富余系数按表 5.1.4选用。
耐热混凝土

耐热混凝土配合比设计及性能检验规程1总则针对****钢冶金建筑工程的需要,编制该规程。
本规程中的耐热混凝土指用普通硅酸盐水泥(或硅酸盐水泥、矿渣硅酸盐水泥、铝酸盐水泥)、耐热粗细骨料、耐热掺和料、水以及根据需要选用合适混凝土外加剂搅拌均匀后采用振动成型的混凝土,它能够长时间承受200~1300℃温度作用,并在高温下保持需要的物理力学性能。
该混凝土不能使用于酸、碱侵蚀的部位。
2原材料要求根据耐热温度高低,温度变化的剧烈程度选用原材料的品种。
2.1水泥2.1.1硅酸盐水泥、普通硅酸盐水泥、矿渣硅酸盐水泥、铝酸盐水泥应相应符合国标GB175-1999、GB1344-1999、GB201-2000的要求。
对于高炉基础耐热混凝土使用的水泥,应压蒸安定性合格。
2.1.2对耐热温度高于700℃的混凝土,水泥中不能掺石灰岩类混合材。
低于700℃时,掺量亦不能超过5%。
2.1.3硅酸盐水泥,普通硅酸盐水泥的最高使用温度为1200℃,矿渣水泥的最高使用温度为700℃,且磨细水淬矿渣含量不大于50%,铝酸盐水泥最高使用温度为1400℃。
2.1.4每立方米耐热砼中的水泥用量不应超过450kg。
2.2掺和料2.2.1使用温度大于350℃的耐热砼,应掺加耐热掺和料。
2.2.2常用的耐热掺和料有粘土熟料、铝矾土熟料、粘土砖粉、粉煤灰(不低于Ⅱ级)等。
其技术要求见表1:表1 耐热砼用掺和料技术要求注:掺和料含水率不得大于1.5%。
2.3粗细骨料2.3.1耐热砼不宜采用石英质骨料。
如砂岩、石英等。
应选用粘土熟料、铝矾土熟料、耐火砖碎料、粘土砖碎料、高炉重矿渣碎石、安山岩、玄武岩、辉绿岩等。
且高炉重矿渣碎石、安山岩、玄武岩、辉绿岩仅限于温度变化不剧烈的部位。
2.3.2骨料的燃烧温度不低于1350~1450℃。
2.3.3对于已用过的粘土砖,应除去表面熔渣和杂质,且强度应大于10MPa 。
高炉重矿渣应具有良好的安定性,不允许有大于25mm 的玻璃质颗粒。
耐热混凝土配合比设计及介绍

以下内容均来自于网络,郑广伟整理。
耐热混凝土是一种能长期承受高温作用( 200 C 以上),并在高温作用下保持所需的物理力学性能的特种混凝土。
而代替耐火砖用于工业窑炉内衬的耐热混凝土也称为耐火混凝土。
根据所用胶结料的不同,耐热混凝土可分为:硅酸盐耐热混凝土;铝酸盐耐热混凝土; 磷酸盐耐热混凝土;硫酸盐耐热混凝土;水玻璃耐热混凝土;镁质水泥耐热混凝土;其他胶结料耐热混凝土。
根据硬化条件可分为:水硬性耐热混凝土;气硬性耐热混凝土;热硬性耐热混凝土。
耐热混凝土已广泛地用于冶金、化工、石油、轻工和建材等工业的热工设备和长期受高温作用的构筑物,如工业烟囱或烟道的内衬、工业窑炉的耐火内衬、高温锅炉的基础及外耐热混凝土与传统耐火砖相比,具有下列特点:1 、生产工艺简单,通常仅需搅拌机和振动成型机械即可;2 、施工简单,并易于机械化;3 、可以建造任何结构形式的窑炉,采用耐热混凝土可根据生产工艺要求建造复杂的窑炉形式;4 、耐热混凝土窑衬整体性强,气密性好,使用得当,可提高窑炉的使用寿命;5 、建造窑炉的造价比耐火砖低;6 、可充分利用工业废渣、废旧耐火砖以及某些地方材料和天然材料。
1. 硅酸盐耐热混凝土硅酸盐耐热混凝土所用的材料主要有硅酸盐水泥、耐热骨料、掺合料以及外加剂等。
1 、原材料要求(1) 硅酸盐水泥可以用矿渣硅酸盐水泥和普通硅酸盐水泥作为其胶结材料。
一般应优先选用矿渣硅酸盐水泥,并且矿渣掺量不得大于20 %。
如选用普通硅酸盐水泥,水泥中所掺的混合材料不得含有石灰石等易在高温下分解和软化或熔点较低的材料。
此外,因为水泥的耐热性远远低于耐热骨料及耐热粉料,在保证耐热混凝土设计强度的情况下,应尽可能减少水泥的用量,为此,要求水泥的强度等级不得低于42.5MPa 。
用上述两种水泥配制的耐热混凝土最高使用温度可以达到700〜800 C。
其耐热机理是:硅酸盐水泥熟料中的 C 3 S和 C 2 S的水化产物Ca(OH) 2在高温下脱水,生成的CaO与矿渣及掺合料中的活性SiO 2和A1 2 O 3又反应生成具有较强耐热性的无水硅酸钙和无水铝酸钙,使混凝土具有一定的耐热性。
混凝土配合比设计方法及标准
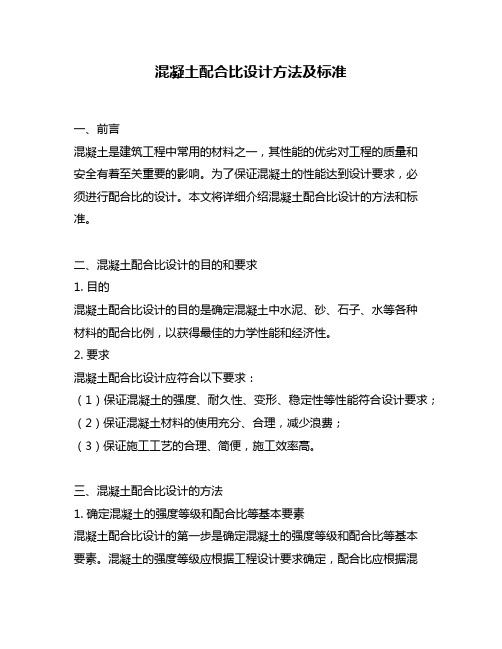
混凝土配合比设计方法及标准一、前言混凝土是建筑工程中常用的材料之一,其性能的优劣对工程的质量和安全有着至关重要的影响。
为了保证混凝土的性能达到设计要求,必须进行配合比的设计。
本文将详细介绍混凝土配合比设计的方法和标准。
二、混凝土配合比设计的目的和要求1. 目的混凝土配合比设计的目的是确定混凝土中水泥、砂、石子、水等各种材料的配合比例,以获得最佳的力学性能和经济性。
2. 要求混凝土配合比设计应符合以下要求:(1)保证混凝土的强度、耐久性、变形、稳定性等性能符合设计要求;(2)保证混凝土材料的使用充分、合理,减少浪费;(3)保证施工工艺的合理、简便,施工效率高。
三、混凝土配合比设计的方法1. 确定混凝土的强度等级和配合比等基本要素混凝土配合比设计的第一步是确定混凝土的强度等级和配合比等基本要素。
混凝土的强度等级应根据工程设计要求确定,配合比应根据混凝土强度等级、施工条件、材料性能等因素确定。
2. 确定各材料的用量混凝土配合比设计的第二步是确定各材料的用量。
混凝土中的材料包括水泥、砂、石子和水。
其中,水泥的用量应根据混凝土的强度等级、水泥的强度等级、材料的相对密度等因素确定;砂、石子的用量应根据混凝土的配合比确定;水的用量应根据混凝土的配合比、砂、石子的含水率、气温、风速等因素确定。
3. 进行配合比的计算混凝土配合比设计的第三步是进行配合比的计算。
配合比的计算应根据混凝土的强度等级、材料的用量等因素确定。
一般来说,可以采用试配和理论配合比两种方法。
试配法是指通过实验确定最佳的配合比;理论配合比是指根据混凝土材料的性能参数,采用数学模型计算出的配合比。
四、混凝土配合比设计的标准1. GB 50015-2003《混凝土结构设计规范》GB 50015-2003《混凝土结构设计规范》是混凝土配合比设计的主要标准之一。
该标准规定了混凝土配合比设计的基本原则、配合比的计算方法、材料的选择和使用等内容,对混凝土配合比设计具有指导意义。
普通配合比设计规程

普通配合比设计规程一、原材料及配合比设计要求1. 原材料:普通混凝土的主要原材料包括水泥、砂、石、水等。
其中,水泥应符合国家相关标准,砂、石应满足混凝土强度等级和耐久性的要求,水应清洁无污染。
2. 配合比设计要求:配合比设计应满足混凝土强度等级、工作性、耐久性等方面的要求。
同时,应考虑原材料的性能、质量、成本等因素,以选定经济合理的配合比。
二、混凝土配合比设计流程1. 了解工程需求:了解工程的设计要求、结构形式、混凝土强度等级等基本信息。
2. 确定混凝土强度等级:根据工程需求和设计要求,确定混凝土的强度等级。
3. 确定水泥品种和标号:根据强度等级和工程特点,选择合适的水泥品种和标号。
4. 确定砂、石规格及质量:根据强度等级、工程要求和原材料性能,选择合适的砂、石规格和质量。
5. 计算配合比:根据强度等级、工作性要求和原材料性能,计算出理论配合比。
6. 试配与调整:进行试配实验,根据实验结果对理论配合比进行调整,以确定实际配合比。
7. 配合比选定与公布:选定经济合理的配合比,并将其公布供生产使用。
三、配合比计算方法1. 理论配合比:根据混凝土强度等级、工作性要求和原材料性能,通过理论计算得出理论配合比。
2. 试配实验:按照理论配合比进行试配实验,以检验混凝土的工作性和强度等级是否满足要求。
根据实验结果对理论配合比进行调整。
3. 实际配合比:根据试配实验结果,调整理论配合比,得出实际配合比。
四、试配与调整1. 试配实验应使用标准化的设备和实验室条件,确保实验结果的准确性。
2. 根据实验结果对理论配合比进行调整,主要包括调整砂率、用水量等,以获得满足工程要求的混凝土工作性和强度等级。
3. 根据调整后的配合比进行再次试配实验,以确保混凝土性能的稳定性和可靠性。
五、配合比选定与公布1. 综合考虑混凝土性能、质量、成本等因素,选定经济合理的配合比。
2. 将选定的配合比公布供生产使用,并建立相应的记录和档案。
混凝土配合比设计及混凝土性能试验方案及措施

第9章混凝土配合比设计及混凝土性能试验方案及措施在混凝土工程开工前84天内,承包人提交现场试验室的设置、材料试验计划报送监理人审批,其内容包括材料试验计划、试验资质、现场试验室的规模、试验设备和项目、试验机构设置和人员配备等。
现场试验室按国家相关规定建立,并定期按国家实验室计量认证规定进行资质评审,评审报告报送发包人中心试验室和监理工程师。
9.1试验室配置及机构设置现场实验室配备足够的人员和设备,试验室人员的能力配置必须满足现场试验的要求,试验室主任由具有丰富的大型工程实践经验的工程师担任。
设备的率定按国家规定进行定期复验具备按合同规定和监理指示,对工程所有原材料按相关的规范进行试验及检验,对各混凝土进行配合比试验,并确定最优配合比。
具备进行工艺试验及对施工现场进行质量检测及取样试验和试验资料整理分析的能力。
施工项目部中心试验室监理工程师现场试验室办公室9.IT现场试验室组织机构图9.2试验室资源配置9.2.1试验室办公、试验用房配置试验室建筑面积约180ιΛ由办公室、水泥试验间、砂石试验间、力学试验问、抗冻抗渗间、碎拌和间、养护间、资料室等组成。
详见表9.2T试验室设置面积一览表9.2.2.仪器设备及器具配置试验室的设备及器具配置以满足本标试验内容要求为原则。
配置见表9.2-2 表9.2-2 试验室主要设备及器具配置表《水工混凝土配合比设计规程》DL/T5330-2005《水工混凝土砂石骨料试验规程》DL/T5151-2001《水工混凝土试验规程》DL/T5150-2001《水工混凝土外加剂技术规程》DL/T5100-1999《水工混凝建筑物抗冲磨防空蚀混凝土技术规程》DL/T5207-2005 《水工混凝土硅粉品质标准暂时规定》1992.3《水工混凝土施工规范》DL/T5144-2001《钢纤维混凝土结构设计与施工规程》CECS38:1992《低热微膨胀水泥》GB2938-2008《通用硅酸盐水泥》GB175-2007《混凝土拌合用水标准》JGJ63-2006《水工建筑物抗冰冻设计规范》DL/T5082-1998《水工混凝土掺用粉煤灰技术规范》DL/T5055-2007《水电水利工程锚喷支护施工规范》DL/5181-2003《水工混凝土水质分析试验规程》DL/T5152-2001《水下不分散混凝土试验规程》DL/T5117-2000《钢筋焊接接头试验方法标准》JGJ/T27-2001《钢筋焊接及验收规程》JGJ18-2003《钢筋混凝土用钢》GB1499.2-2007《钢筋混凝土用钢》GB1499.1-2008《钢纤维混凝土》JGJ/T3064-1999《水利水电工程混凝土防渗墙施工规范》DL/T5199-2004《预应力混凝土用钢丝》GB/T5223-2002《混凝土结构工程施工及验收规范》GB50204-2002;《混凝土质量控制标准》GB50164-92;《混凝土强度检验评定标准》GBJ107-87;《公路土工试验规程》JTGE40-2007;《土工试验规程》SL237-1999;各专项施工技术涉及的其它引用现行最新的标准和规程规范9.4混凝土配合比设计及混凝土性能、原材料的试验9.4.1混凝土配合比设计原则混凝土配合比的设计根据各种不同类型结构物的混凝土配合比必须通过试验选定,其试验方法应遵循DL/T5330-2005规范和工程设计、图纸提供设计指标要求进行配合比设计。
高性能混凝土的配合比设计及应用技术规程

高性能混凝土的配合比设计及应用技术规程一、背景介绍高性能混凝土(High Performance Concrete,简称HPC)是一种具有高强度、高耐久性、高流动性和高可塑性的混凝土,其强度等级一般在C50以上。
HPC具有优异的力学性能和耐久性能,广泛应用于大型桥梁、高层建筑、核电站等重要工程领域。
二、配合比设计1.确定混凝土强度等级HPC的强度等级一般在C50以上,根据工程实际需要和设计要求,确定HPC的强度等级。
2.选择适宜的水泥和掺合料选择优质的水泥和掺合料,以保证混凝土的强度和耐久性。
掺合料包括粉煤灰、硅灰、矿渣粉等。
3.确定水灰比水灰比是混凝土中水和水泥重量比值,水灰比过大会影响混凝土的强度和耐久性,过小则会影响混凝土的可塑性和流动性。
一般HPC的水灰比在0.25-0.35之间。
4.确定骨料配合比HPC的骨料一般采用细骨料和粗骨料的组合,细骨料的粒径一般小于5mm,粗骨料的粒径一般大于5mm。
骨料配合比的确定需要考虑骨料的种类、粒径和比重等因素,以保证混凝土的强度和流动性。
三、应用技术规程1.混凝土搅拌HPC的搅拌需要采用高效的混凝土搅拌设备,以保证混凝土的均匀性和流动性。
在搅拌前,应将水泥、掺合料和骨料充分拌和,再逐步加入适量的水进行搅拌。
2.混凝土浇筑HPC的浇筑需要采用高效的混凝土输送设备和浇筑工艺,以保证混凝土的均匀性和流动性。
在浇筑前,应对模板进行充分的清理和润湿处理。
3.混凝土养护HPC的养护需要采用专业的养护设备和养护工艺,以保证混凝土的强度和耐久性。
在养护期间,应对混凝土进行适当的保温和湿润处理,以促进混凝土的早期强度发展。
四、案例应用某高层建筑工程中,采用了HPC作为结构混凝土,其配合比如下:1.水泥:P.O42.52.粉煤灰:20%(水泥用量的20%)3.矿渣粉:10%(水泥用量的10%)4.细骨料:0-5mm的机制砂5.粗骨料:5-20mm的鹅卵石6.水灰比:0.3根据配合比设计,采用高效的混凝土搅拌设备和浇筑工艺,对混凝土进行了充分的养护。
普通混凝土配合比设计规程《JGJ55_2011》
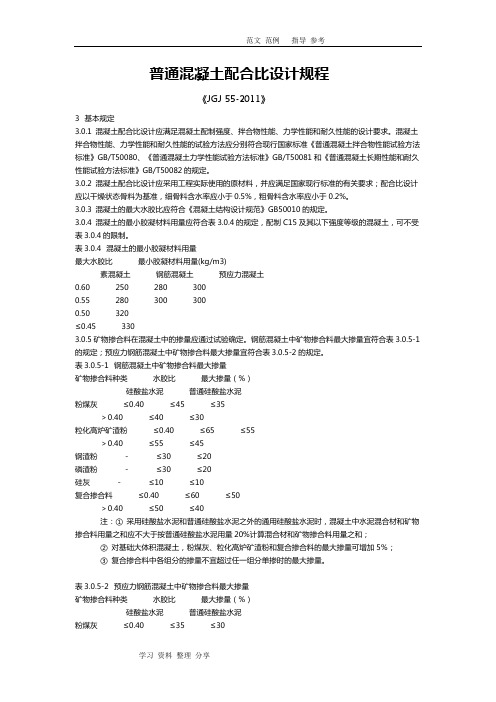
普通混凝土配合比设计规程《JGJ 55-2011》3基本规定3.0.1 混凝土配合比设计应满足混凝土配制强度、拌合物性能、力学性能和耐久性能的设计要求。
混凝土拌合物性能、力学性能和耐久性能的试验方法应分别符合现行国家标准《普通混凝土拌合物性能试验方法标准》GB/T50080、《普通混凝土力学性能试验方法标准》GB/T50081和《普通混凝土长期性能和耐久性能试验方法标准》GB/T50082的规定。
3.0.2 混凝土配合比设计应采用工程实际使用的原材料,并应满足国家现行标准的有关要求;配合比设计应以干燥状态骨料为基准,细骨料含水率应小于0.5%,粗骨料含水率应小于0.2%。
3.0.3 混凝土的最大水胶比应符合《混凝土结构设计规范》GB50010的规定。
3.0.4 混凝土的最小胶凝材料用量应符合表3.0.4的规定,配制C15及其以下强度等级的混凝土,可不受表3.0.4的限制。
表3.0.4混凝土的最小胶凝材料用量最大水胶比最小胶凝材料用量(kg/m3)素混凝土钢筋混凝土预应力混凝土0.602502803000.552803003000.50320≤0.453303.0.5矿物掺合料在混凝土中的掺量应通过试验确定。
钢筋混凝土中矿物掺合料最大掺量宜符合表3.0.5-1的规定;预应力钢筋混凝土中矿物掺合料最大掺量宜符合表3.0.5-2的规定。
表3.0.5-1钢筋混凝土中矿物掺合料最大掺量矿物掺合料种类水胶比最大掺量(%)硅酸盐水泥普通硅酸盐水泥粉煤灰≤0.40≤45≤35>0.40≤40≤30粒化高炉矿渣粉≤0.40≤65≤55>0.40≤55≤45钢渣粉-≤30≤20磷渣粉-≤30≤20硅灰-≤10≤10复合掺合料≤0.40≤60≤50>0.40≤50≤40注:①采用硅酸盐水泥和普通硅酸盐水泥之外的通用硅酸盐水泥时,混凝土中水泥混合材和矿物掺合料用量之和应不大于按普通硅酸盐水泥用量20%计算混合材和矿物掺合料用量之和;②对基础大体积混凝土,粉煤灰、粒化高炉矿渣粉和复合掺合料的最大掺量可增加5%;③复合掺合料中各组分的掺量不宜超过任一组分单掺时的最大掺量。
混凝土配合比设计

3、施工配合比 考虑骨料的含水率,对单位用水量进行调整。
假定砂含水率为a(%),石含水率为b(%) 施工配合比为: m'c mc
m's ms (1 0.01a) m'g mg (1 0.01b)
m'w mw ms 0.01a mg 0.01b
m'c : m's : m'g : m'w
解:1、初步计算配合比
(1)确定配制强度(fcu.o) 据统计资料,标准差σ=6 MP,则
fcu.o = fcu.k+1.645σ=25 +1.645×6=34.87 MP
(2)确定水灰比(
W C
)
因水泥无实测强度,按书上75页,取水泥富余系数γc
=1.13, fce =γc ×fce.k=1.13 ×42.5=48.03 MP
mco mgo mso mwo 0.01 1 c g s w
s
mso mso mgo
100 %
296 3100
mgo 2700
mso 2650
160 1000
0.011 1
s
mso mso mgo
100 %
32%
由两式可解得砂和石的用量:
mso mgo
631kg 1340kg
4.5 普通混凝土的配合比设计
混凝土的配合比是指混凝土中四种树料水泥、水、 砂及石子用量之间的比例关系,有时还注明外加剂的 用量。
配合比表示方法: (1)以每M3混凝土所用水泥重量C、水重量W、砂子 重量S、石子重量G表示(一般情况下多采用此法) 如:C=300kg、W=180kg、S=720kg、G=1200kg
1
水灰比(
高温混凝土材料应用技术规程

高温混凝土材料应用技术规程一、前言高温混凝土是一种应用在高温环境下的特殊混凝土材料,其具有较高的抗温性、耐热性和耐火性。
本技术规程旨在规范高温混凝土材料的应用,以确保其在高温环境下有较好的性能表现。
二、材料选择1.水泥:优先选择矿渣水泥、高铝酸盐水泥或硅酸盐水泥,其强度和耐火性能较好。
2.细集料:应选择粒径小、表面积大、抗高温性能好的细集料,如石英砂、特种陶粒等。
3.粗集料:应选择抗高温性能好的粗集料,如陶粒、熟料等。
4.掺合料:可选用矿渣粉、粉煤灰等,以提高混凝土的耐火性能。
5.外加剂:可选用高温混凝土专用的外加剂,如耐火剂、增强剂等。
三、混凝土配合比设计1.设计原则:应根据施工条件、工程要求和材料性能等因素制定合理的配合比设计方案。
2.水灰比:水灰比应控制在0.3-0.4之间,以保证混凝土的抗温性能。
3.细集料含量:应根据混凝土的用途和工作环境确定细集料含量,一般不超过60%。
4.粗集料含量:应根据混凝土的用途和工作环境确定粗集料含量,一般不超过40%。
5.掺合料控制:掺合料的控制应根据混凝土的用途和工作环境确定,一般不超过20%。
6.外加剂使用量:外加剂的使用量应根据混凝土的用途和工作环境确定,一般不超过5%。
四、混凝土制备1.原材料配比:应按照混凝土配合比设计方案准确配比,严格控制材料的质量。
2.搅拌:应采用搅拌机进行混凝土的搅拌,搅拌时间应不少于3min,以确保混凝土均匀。
3.加水:应根据混凝土的干湿度调整适量的水量,以保证混凝土的流动性和坍落度。
4.施工:应根据混凝土的用途和工作环境选择适当的施工方式,如浇注、振捣等。
五、混凝土养护1.初期养护:混凝土浇筑后,应在24h内进行初期养护,包括覆盖保湿等。
2.中期养护:混凝土在初期养护后,应在7天内进行中期养护,包括覆盖保湿等。
3.后期养护:混凝土在中期养护后,应在28天内进行后期养护,包括覆盖保湿等。
六、混凝土检验1.强度检验:混凝土的强度检验应按照相关标准进行,以保证混凝土的强度符合要求。
耐热混凝土应用技术规程

耐热混凝土应用技术规程引言:耐热混凝土是一种特殊的建筑材料,具有出色的耐高温性能,广泛应用于高温工业领域。
为了确保耐热混凝土的施工质量和使用效果,制定了一系列的应用技术规程。
本文将详细介绍耐热混凝土应用技术规程的相关内容。
一、材料选择1.1 水泥:应选用高温水泥,具有较高的耐热性能和抗渗透性能。
1.2 骨料:骨料应选用高温稳定性好的材料,如高铝骨料、硅酸盐骨料等。
1.3 控制剂:应选用适宜的控制剂,以提高混凝土的耐热性能和抗裂性能。
二、施工工艺2.1 配合比设计:根据工程要求和材料性能,合理设计混凝土的配合比,确保混凝土的强度和耐热性能。
2.2 搅拌:搅拌时间应充分,确保混凝土的均匀性和稳定性。
2.3 浇筑:在浇筑过程中,应采取适当的措施,防止混凝土的温度过高或过低,避免产生裂缝。
2.4 养护:混凝土浇筑后,应及时进行养护,保持适宜的湿度和温度,以提高混凝土的强度和耐热性能。
三、施工注意事项3.1 温度控制:在施工过程中,应控制混凝土的温度,避免过高或过低的温度对混凝土的性能产生不利影响。
3.2 防止裂缝:在施工过程中,应采取措施防止混凝土产生裂缝,如使用适当的控制剂、合理安排浇筑顺序等。
3.3 施工环境:施工环境应保持适宜的湿度和温度,避免对混凝土的施工和养护产生不利影响。
3.4 质量检验:应定期对施工过程进行质量检验,确保混凝土的质量符合要求。
四、施工质量控制4.1 施工方案:应制定详细的施工方案,明确施工过程中的各项控制措施和要求。
4.2 质量检验:应定期进行混凝土的质量检验,包括强度、耐热性能等指标的检测。
4.3 施工记录:应做好施工记录,记录施工过程中的关键参数和控制措施,以备查证。
结论:耐热混凝土应用技术规程是确保耐热混凝土施工质量和使用效果的重要依据。
通过合理选择材料、严格控制施工工艺和质量控制,可以提高耐热混凝土的耐高温性能和使用寿命。
在实际施工中,应严格按照规程要求进行操作,确保施工质量和工程安全。
混凝土配合比设计规范

混凝土配合比设计规范普通混凝土配合比设计包括:普通混凝土配合比设计、混凝土配合比的试配、混凝土配合比的调整与确定、特殊要求混凝土配合比设计。
1、适用范围本作业指导书适用于工业与民用建筑及一般构筑物所采用的普通混凝土配合比设计以及其拌合物性能 (稠度、容重)试验。
2、执行标准《普通混凝土配合比设计规程》JGJ55—2011 《普通混凝土拌合物性能试验方法》GB/T50080—20023、混凝土配合比设计3.1配合比计算步骤3.1.1计算出要求的试配强度f cu ,0; 3.1.2按f cu ,0计算出所要求的水灰比值;3.1.3选取每立方体混凝土的用水量,并计算出混凝土的单位水泥用量; 3.1.4选取合理的砂率值;3.1.5计算出粗、细骨料的用量,提供出试配用的混凝土配合比。
3.2混凝土试配强度3.2.1混凝土配制强度按下式计算:0.cu f ≥k cu f .+1.645σ式中:0.cu f ——混凝土配制强度(MPa );k cu f .——混凝土立方体抗压强度标准值(MPa );σ——混凝土强度标准差(MPa )。
3.2.2混凝土强度标准差的确定(1) 混凝土强度标准差采用公式进行计算,确定该值的强度试件组数不应少于30组。
(2) 当混凝土强度等级不大于C30的混凝土,其强度标准差计算值小于3.0MPa 时,标准差应取用3.0MPa ,当强度等级大于C30且小于C60的混凝土,其强度标准差计算值低于4.0MPa 时,标准差应取用4.0MPa 。
3 当无统计资料和经验时,可参考下表取值。
表3.2.2 标准差取值表3.3 计算水胶比按下列公式计算要求的水胶比值:W/B =bcu bf ab f af 0.式中 W/B ——混凝土所要求的水灰比值;a 、b ——回归系数;当不具备试验资料时,对碎石混凝土可取a =0.53,b =0.20; 对卵石混凝土可取a =0.49,b =0.13。
b f —胶凝材料28d 天胶砂抗压强度(MPa ),可实测,也可根据下式计算: b f =ce s f f r r式中f r 、s r ——粉煤灰和矿渣粉的影响系数ce f ——水泥28天胶砂抗压强度,可实测,也可根据下表取值计算 粉煤灰和矿渣粉的影响系数按下表取值:3.4 用水量选定3.4.1水灰比在0.4~0.8范围内,按骨料品种、规格及施工要求的塌落度值选择每立方米混凝土的用水量(m ω0)按表3.4.1选用。
- 1、下载文档前请自行甄别文档内容的完整性,平台不提供额外的编辑、内容补充、找答案等附加服务。
- 2、"仅部分预览"的文档,不可在线预览部分如存在完整性等问题,可反馈申请退款(可完整预览的文档不适用该条件!)。
- 3、如文档侵犯您的权益,请联系客服反馈,我们会尽快为您处理(人工客服工作时间:9:00-18:30)。
耐热混凝土配合比设计及性能检验规程1总则针对武钢冶金建筑工程的需要,编制该规程。
本规程中的耐热混凝土指用普通硅酸盐水泥(或硅酸盐水泥、矿渣硅酸盐水泥、铝酸盐水泥)、耐热粗细骨料、耐热掺和料、水以及根据需要选用合适混凝土外加剂搅拌均匀后采用振动成型的混凝土,它能够长时间承受200~1300℃温度作用,并在高温下保持需要的物理力学性能。
该混凝土不能使用于酸、碱侵蚀的部位。
2原材料要求根据耐热温度高低,温度变化的剧烈程度选用原材料的品种。
2.1水泥2.1.1硅酸盐水泥、普通硅酸盐水泥、矿渣硅酸盐水泥、铝酸盐水泥应相应符合国标GB175-1999、GB1344-1999、GB201-2000的要求。
对于高炉基础耐热混凝土使用的水泥,应压蒸安定性合格。
2.1.2对耐热温度高于700℃的混凝土,水泥中不能掺石灰岩类混合材。
低于700℃时,掺量亦不能超过5%。
2.1.3硅酸盐水泥,普通硅酸盐水泥的最高使用温度为1200℃,矿渣水泥的最高使用温度为700℃,且磨细水淬矿渣含量不大于50%,铝酸盐水泥最高使用温度为1400℃。
2.1.4每立方米耐热砼中的水泥用量不应超过450kg。
2.2掺和料2.2.1使用温度大于350℃的耐热砼,应掺加耐热掺和料。
2.2.2常用的耐热掺和料有粘土熟料、铝矾土熟料、粘土砖粉、粉煤灰(不低于Ⅱ级)等。
其技术要求见表1:表1 耐热砼用掺和料技术要求注:掺和料含水率不得大于1.5%。
2.3粗细骨料2.3.1耐热砼不宜采用石英质骨料。
如砂岩、石英等。
应选用粘土熟料、铝矾土熟料、耐火砖碎料、粘土砖碎料、高炉重矿渣碎石、安山岩、玄武岩、辉绿岩等。
且高炉重矿渣碎石、安山岩、玄武岩、辉绿岩仅限于温度变化不剧烈的部位。
2.3.2骨料的燃烧温度不低于1350~1450℃。
2.3.3对于已用过的粘土砖,应除去表面熔渣和杂质,且强度应大于10MPa。
高炉重矿渣应具有良好的安定性,不允许有大于25mm的玻璃质颗粒。
2.3.4一般粗骨料粒径不得大于20mm,在钢筋不密的厚大结构中不应大于40mm。
2.3.5骨料中严禁混有有害杂质,特别是石灰岩类碎块等。
2.3.6对于温度低于350℃,可使用河砂。
低于700℃,温度变化不剧烈时,优先选用高炉重矿渣骨料。
2.3.7高炉重矿渣碎石、安山岩、玄武岩、辉绿岩粗细骨料的级配应符合GB/T14684-2001《建筑用砂》、GB/T14685-2001《建筑用卵石、碎石要求》。
高炉重矿渣碎石还应符合YBJ205-84《混凝土用高炉矿渣碎石技术标准》的要求。
粗骨料最大粒径不宜超过31.5mm,最佳不超过25mm。
粘土质及高铝质骨料的颗粒粒级,级配及化学成分要求见下表:表2 耐热砼骨料的技术性质2.4拌合水符合JGJ63-89《普通砼拌合用水标准》。
2.5外加剂2.5.1符合GB8076-1997《普通砼用外加剂》2.5.2应通过试配符合耐热砼的各种指标要求。
3耐热砼配合比设计和试配耐热砼的配合比不但要满足耐热性能的要求,同时必须满足强度和施工和易性的要求。
在设计耐热砼配合比时,应根据极限使用温度和使用条件,选定合适的原材料,然后在参考经验配合比的前提下通过调整胶结材的用量、水灰比、骨料级配、掺和料及外加剂,并经过试验,从而优选出保证砼耐久性的经济、可靠配合比。
3.1胶结材的用量一般情况下,骨料的耐热性能比胶结料好,当胶结料的用量超过一定范围时,随着胶结料用量的增加耐热性能将降低,因此在满足施工和易性和常温强度的要求下,尽可能减少胶结料的用量。
水泥用量一般可控制在砼总重量10~20%范围内。
对荷重软化点和耐热度要求较高,而常温强度要求不高的水泥耐热砼,水泥用量可控制在10~15%以内。
3.2水灰比水灰比的增减对强度和残余变形的影响较显著。
在施工条件允许的前提下,应尽量减少用水量,降低水灰比,一般坍落度应小于20mm。
对于坍落度要求较大的耐热混凝土,必须掺用高效减水剂等外加剂。
3.3掺和料用量掺和料可以改善砼的耐高温性能,提高施工和易性,同时还可以减少水泥用量。
因此,对常温要求强度不高的耐热砼,掺和料用量可多些。
一般为水泥用量的30~100%。
3.4骨料级配及砂率骨料级配应满足2.3.7的要求,细骨料占骨料总量的40~60%。
3.5以经验配合比为初始配合比,进行试配,调整确定基准配合比。
3.6经验配合比见表3。
表3 耐热砼经验配合比3.7耐热砼试配3.7.1原材料称量及成型应符合GB/T50081-2002《普通砼力学性能试验方法标准》的要求。
3.7.2拌制水泥耐热砼时,水泥和掺和料必须预先拌合均匀,约拌2min。
3.7.3耐热砼的养护应遵守以下规定:成型完后应在15~25℃的潮湿环境中养护,其中普通水泥(硅酸盐水泥)耐热砼养护不少于7d,矿渣水泥耐热砼不少于14d;铝酸盐水泥耐热砼不少于3d。
4耐热砼的检验项目和技术要求。
用于检验耐热砼质量的试件,应在砼的浇筑地点随机抽取。
取样与试件留置应符合下列规定:1>每拌制100盘且不超过50m3的同配合比的砼取样不得少于一次;2>每工作班拌制的同一配合比的砼不足100盘时,取样不得少于一次;3>一次连续浇筑超过500m3时,同一配合比的砼每100m3取样不得少于1次;4>取样组数见表4。
表4 耐热砼的检验项目和技术要求注:试件尺寸见耐热砼性能检验相关要求。
5耐热砼性能检验5.1烘干耐压强度检验5.1.1目的及适用范围检验耐热砼在标准养护n d后的烘干耐压强度作为耐热砼强度等级。
(普通水泥、矿渣水泥、铝酸盐水泥分别养护7d、14d、3d)。
适用于测定耐热砼的烘干耐压强度。
5.1.2检验设备5.1.2.1材料试验机符合JGJ70-90中关于试验机的要求。
5.1.2.2电热干燥箱(300℃±1℃)。
5.1.2.3钢板尺,最小刻度0.05cm。
5.1.2.4试模70.7×70.7×70.7mm符合JGJ70-90第7.0.2条要求。
5.1.3试样制备。
在与生产工艺相同条件下,直接成型棱长为70.7±0.5mm的立方体试样3件。
当骨料最大粒径大于25mm时,直接成型棱长为100±1mm的立方体试样。
5.1.4检验步骤5.1.4.1养护龄期到达后及时在110±5℃条件下烘干8h以上,(烘干升温速度为20~30℃/h),然后自然冷却至室温后进行检验。
5.1.4.2用钢板尺分别测量并记录立方体试样上、下受压面的长度,准确至0.1mm。
5.1.4.3将试样受压面对准试验机上、下压板中心,以0.5~1MPa/s 的加压速度均匀地施压于试样,至试样破坏,并记录最大压力值。
5.1.5结果计算将测量数据代入下列公式,计算各个试样的烘干耐压强度,以三个试样的平均值为代表值,并精确至0.1 MPa。
A1=a1×a2A2=b1×b2A=(A1+A2)/2S=P÷A式中,A1、A2—试样上、下受压面的面积(mm2)a1、a2—试样上受压面的两维长度(mm)b1、b2—试样下受压面的两维长度(mm)A—试样受压面积(mm2)P—试样破坏时荷载(N)S—试样烘干耐压强度(MPa)5.2烧后抗压强度、残余抗压强度检验5.2.1目的及适用范围检验耐热砼在经过一定时间的高温加热后的耐压强度。
检验耐热砼在经过一定时间的高温加热后,随炉冷却到室温,放在干燥空气中养护10d后的耐压强度。
适用于检验耐热砼的烧后抗压强度和残余抗压强度。
5.2.2检验设备5.2.2.1箱式加热炉5.2.2.2电热干燥箱(300℃±1℃)。
5.2.2.3材料试验机同5.1.2.1。
5.2.2.4钢板尺,最小刻度0.05cm。
5.2.3试样制备:同5.1.3。
5.2.4检验步骤5.2.4.1养护龄期到达后及时在110±5℃条件下烘干8h以上(烘干升温速度为20~30℃/h)。
5.2.4.2放在加热炉中以每小时不超过150℃的升温速度,升温至指定温度,恒温3h(残余强度恒温4h),随炉冷却至室温。
5.2.4.3取出经过恒温3h的冷却试样作烧后抗压强度检验。
5.2.4.4取出经过恒温4h的冷却试样,放在干燥空气中养护10d后,作残余抗压强度检验。
5.2.4.5用钢板尺分别测量并记录立方体试件上、下受压面的两维长度,准确至0.5mm。
5.2.4.6加压速度同烘干耐压强度检验。
5.2.5结果计算同5.1.5。
5.3烧后线变化检验5.3.1目的及适用范围测定耐热砼加热至高温后的长度增减变化。
适用于耐热砼的烧后线变化检验。
5.3.2试验设备5.3.2.1千分尺:量程50~75mm,精度0.01mm。
若试件尺寸为100mm 时,量程应为75~100 mm或100~125 mm。
5.3.2.2加热炉;应满足极限温度的要求。
且计量检定合格。
5.3.3试样制备5.3.3.1试样的检验数量为3个。
Y5.3.3.2同5.1.3。
5.3.3.3用氧化铬在试样成型面上编号。
5.3.4试验步骤5.3.4.1测量试样长度时,将试样成型面向上,并在试样的四个侧面划出对角线,在每个侧面上按图定出四个测点,加以标记,然后用螺旋百分尺测量试样在两个方向(X,Y)上的各对应点之间的距离。
每次测量应重复两遍,以平均值记录。
要保持加热前后所有测量操作条件的一致。
5.3.4.2装样5.3.4.2.1将试样成型面向上,放置在炉膛内的均温带,距发热体30mm 以上。
试样间至少应保持10mm的间距。
炉膛装样区的温差不得大于20℃.5.3.4.2.2试样可交错迭放两层。
试样之间及试样与炉底的接触面应用在高温下不与试样发生作用的细砂(如电熔刚玉砂,一等高铝矾土熟料砂等)垫平。
5.3.4.3升温速度:低于检验温度200℃前5~10℃/min。
然后以3~5℃/min升温至检验温度。
5.3.4.4到达检验温度后保温4 h,保温期间温差不可超过±10℃。
5.3.4.5应保持炉内为中性气氛或氧化气氛,不可使用还原气氛。
5.3.4.6保温结束后,试样随炉自然冷却至室温,然后进行测量。
允许在200℃以下装、出炉。
5.3.5结果计算5.3.5.1每个试样的烧后线变化百分率按下式计算:△L=((L1-L0)×100)/L0式中△L—试样烧后线变化(%)L0—加热前试样的平均长度(mm)L1—加热后试样的平均长度(mm)5.3.5.2试样烧后收缩以“-”号表示,烧后膨胀以“+”号表示。
“+”、“-”号均写在数字的前面。
5.3.5.3耐热砼烧后线变化的检验结果,以三个试样的平均值为代表值,精确至0.1%。
报告中应列出每个试样的测定值。
5.3.5.4加热后的试样当发现有熔洞、剥落、鼓凸等现象时,应在报告中注明。