金属镁熔盐炉、连续精炼炉温度现场大屏显示方案(DOC)
熔盐炉烘炉方案
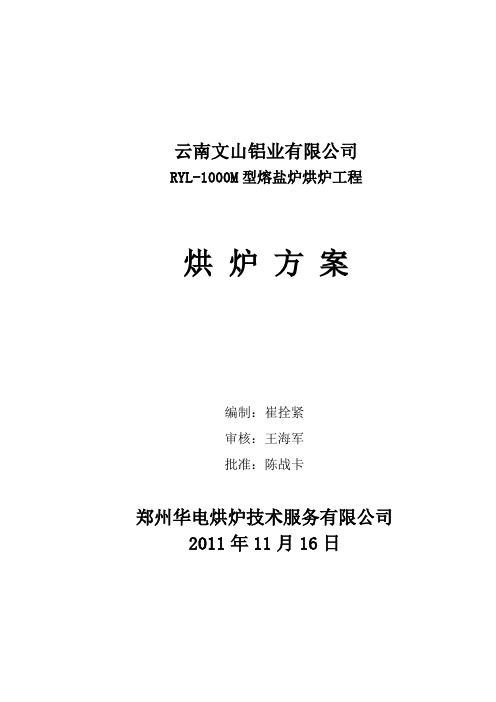
云南文山铝业有限公司RYL-1000M型熔盐炉烘炉工程烘炉方案编制:崔拴紧审核:王海军批准:陈战卡郑州华电烘炉技术服务有限公司2011年11月16日目录1.概述2.炉衬材料结构3.烘炉目的4.烘炉具备的条件5.拟定烘炉制度6.烘炉技术措施7.烘炉质量保证体系及措施8.烘炉安全保证体系及措施9.文明施工、标准化管理措施10.烘炉施工组织及网络图11.其他事项12.设备安装示意图13.烘炉升温曲线图1.概述云南文山铝业有限公司安装三杰实业生产的RYL-1000M型熔盐炉12台,采用排式链条炉,以煤为燃料。
窑炉炉顶呈前高后低形式,形成前拱与后拱,由前拱给燃料、后拱排渣的工作方式。
炉体为立式圆筒三层炉管加顶盘管、四回程烟道结构;内、中、外三层炉管支承在炉底支架上。
燃烧产生的高温烟气由下而上与炉管内侧、顶炉管辐射换热后,再从内层炉管顶部由上而下进入内、中、外三层炉管之间构成第一、二对流换热区,经对流换热后,从外层炉管下部进入外层炉管与壳体之间所构成的第三对流换热区,由下而上对流换热后,由壳体上部排烟口排出。
排面工作温度700℃左右,燃烧室工作温度600-1100℃,溶盐最高温度450℃。
依据现场实际情况,结合我公司的烘炉施工经验和三杰实业提供的烘炉升温曲线,特提供以下用热烟气烘炉机中低烘炉的实施方案。
熔盐炉燃烧室空间约为22立方。
2.炉衬材料结构炉衬材料结构实际具体分布如下:熔盐炉侧墙衬里465mm。
其中高强耐火浇注料400mm;保温砖45mm;保温棉20mm;熔盐炉炉顶衬里465mm。
其中高强耐火浇注料400mm;保温砖45mm;保温棉20mm;熔盐炉炉膛采用耐高温混凝土浇筑完成,炉拱采用大块预制、现场拼装、局部浇注的方式,炉外壁采用多层复合优质保温材料。
3.烘炉目的根据熔盐炉的主体结构、衬里材料施工加水情况和施工环境条件,施工结束后应严格根据材料的特性进行烘干,若烘干不能按程序进行或缩短烘干时间,必然会使材料内部蒸汽胀力过大,造成材料结构的剥落或材料内部结构的损伤,影响熔盐炉的使用寿命。
金属镁蓄热式还原炉燃烧系统方案

北京佳德昌科技有限责任公司
蓄热式金属镁还原炉燃烧系统技术协议
(2)喷嘴设计优化,适用于热脏煤气,调节比大,不回火,不脱火,燃烧 稳定,使用寿命长。 (3)火焰长度可控性好,热流分布合理,炉温差小于±10℃。 (4)采用专门设计的适用于热脏煤气的蓄热体,该蓄热体比表面极大,蓄 热能力强,抗结焦,质量稳定,使用周期长。 (5)蓄热式烧嘴即可满足热脏煤气,又能适用洁净冷煤气的燃烧。 (6)控制系统安全可靠,可实现换向—切换自动控制。 (7)燃料在贫氧状态下燃烧,(烟气中含氧量在 2%~20%)炉内 NOX 生成物 大大减少,NOX 排放量低至 100PPm 以下,完全达到国家级排放标准。 3、烧嘴主要技术参数 名称 烧嘴名称 烧嘴型号 烧嘴额定流量 燃料 燃气热值 燃气压力 燃气温度 助燃风 助燃风机量 助燃风压 助燃风温 火焰长度 烧嘴调节比 火焰形状 节能指标
一、项目内容:
鹤壁某集团本年度计划扩建 6000 吨产量,新建 6 台金属镁还原炉, 为达到节约燃料、提高还原炉能源利用率的目的,将采用北京佳德昌蓄热式 燃烧技术。 该方案是遵循“1 (鹤壁) 镁基材料有限公司”提供的设计意向、 技术参数、 要求等来设计的。 二、技术创新与关键技术 针对热脏煤气的特点,着重考虑煤气中的焦油、粉尘、水等在燃烧过程
北京佳德昌科技有限责任公司 8 010-62952899
北京佳德昌科技有限责任公司
蓄热式金属镁还原炉燃烧系统技术协议
G、排烟系统 排烟系统是由蓄热式燃烧主排烟系统及辅助烟道所组成。 主排烟系统由空气与烟气三通换向阀、烟气流量手动调节阀、排烟管道 和引风机构成,耐温为 200C。引风机根据我公司专利技术设计而选用。 辅助排烟管路排烟量只占总烟量的 20%—30%, 主要起到调节炉压得作 用。 H、压缩空气管道 压缩空气系统由空压机、空气储气罐、空气三联件、调压阀、压力表、 手动球阀等组成。该管路系统由需方自行负责。 I、控制系统 本控制系统由西门子 S7-200 系列 PLC(可编程控制器)控制煤气快速 切断阀、空气-烟气三通换向阀,实现换向自动控制和定温强制换向、排烟 超温报警功能。换向控制及鼓、引风机启停、炉膛温度的显示均集中在一台 控制柜内。 当系统投入运行后,系统工作过程均可实现自动及手动控制,为便于系 统的调整及检修,本方案考虑了人工操作方式和必要的参数显示仪表。 ⅰ、主要检测内容及机构: (1) 炉膛温度 6 个检测、显示点。 (2) 蓄热式烧嘴后排烟温度 12 个检测、 显示点; 三通换向阀后 2 个 测、显示点,当温度超过 180C 时,系统强制换向。 (3) 炉膛压力检测、显示、报警(炉中一个测点) 。 (4) 燃气压力显示、超低压报警(压力 U 型管电子式) 。 (5) 空气压力检测、显示、超低压报警。 (6) 换向阀换向到位指示,及不到位报警。 (7) 鼓风、引风机停运、燃气快断阀联锁功能。 ⅱ、控制原理: 当系统确定接到“打开切断阀”和“启动系统”指令后进入运行准备状态, 当确认点火工作正常,按设定温度要求,通过手动调节控制温度。
镁合金压铸熔炉操作规程(三篇)

镁合金压铸熔炉操作规程第一章总则第一条为规范镁合金压铸熔炉的操作,保证生产安全和生产效率,制定本操作规程。
第二条本操作规程适用于所有从事镁合金压铸熔炉操作的工作人员。
第三条熔炉操作人员必须经过相关的培训合格并持有操作证书方可从事此项操作。
第四条在各个操作环节中,应严格遵守相关的安全操作规定,不得擅自进行操作或改动熔炉。
第五条应定期对熔炉进行维护保养,并做好相应的记录。
第六条对于已经损坏的熔炉设备,应及时进行维修或更换。
第二章操作程序第一节熔炉操作前准备第七条操作人员应严格按照操作流程进行准备工作。
第八条清理操作区域,确保周围环境清洁。
第九条检查熔炉设备的运行状态,包括电源、温度计、压力表等,保证设备正常运行。
第十条检查熔炉操作平台及操作工具的完好情况。
第十一条检查熔炉内是否有异物或有害物质,确保熔炉为空。
第十二条熔炉操作人员应穿戴好相关的劳动防护用品,包括手套、护目镜、口罩等。
第二节熔炉操作流程第十三条操作人员应按照以下顺序进行熔炉操作:(一)开启电源,并确认电源指示灯正常。
(二)按照设备要求设定熔炉的工作参数,包括温度、时间等。
(三)将待熔的镁合金材料放入熔炉内。
(四)关闭熔炉门,并确保门锁好。
(五)根据熔炉类型和要求选择相应的加热方式,并启动加热设备。
(六)观察熔炉的运行状态,确保温度和压力的控制在安全范围内。
(七)在熔炉工作完成之后,关闭加热设备,待熔炉温度降低后再打开熔炉门。
(八)将熔炉内的熔铸液倒出,并进行后续的处理。
(九)关闭电源,清理熔炉及周围环境,并做好相关记录。
第十四条在熔炉操作过程中,操作人员应密切关注熔炉的运行状态,如发现异常情况应立即停止操作,并上报相关人员处理。
第十五条操作结束后,应及时对熔炉进行清洗和维护保养。
第三章安全防护措施第十六条熔炉操作人员必须严格遵守相关的安全操作规程,加强安全意识和防护意识。
第十七条操作人员应穿戴齐全的劳动防护用品,包括头盔、防护眼镜、耳塞、防护服等。
镁合金压铸熔炉操作规程范文(二篇)

镁合金压铸熔炉操作规程范文1. 动态平衡处理为保证镁合金压铸熔炉的正常操作,首先需要进行动态平衡处理。
对于各类材料的熔炼,应根据铸件大小和产量确定合适的铸件计量方式。
在维护熔炼设备稳定性的同时,还要注意控制原料的质量,确保每次熔炼过程中的成品质量。
2. 准备工作2.1 检查设备在进行镁合金压铸熔炉操作之前,需要仔细检查设备的各项参数,包括炉膛温度、燃烧器状态、电机运转情况等。
确保设备处于正常工作状态,并进行必要的维护和修理。
2.2 清洁设备在开始操作之前,需要彻底清洁熔炉的内外部设备。
清理熔炉内部的杂质可以提高铸件的质量,并防止熔炉故障。
清洁外部设备可以提高工作环境的整洁度和操作的安全性。
3. 热风炉燃烧操作3.1 打开熔炼炉首先,打开熔炼炉门并确认内部没有残留物。
然后,逐步加热熔炼室,直到达到所需的工作温度。
在过程中,需要注意观察燃烧情况,对于燃烧不良的情况及时采取措施。
3.2 加入原料当熔炼室达到所需温度时,需要按照预定的参数加入原料,同时根据炉子的容量限制确定铸件的数量。
加入原料时要注意均匀分布,避免原料堆积过多导致不均匀熔炼。
3.3 燃烧调整根据熔炉内部温度的变化,调整燃烧器的工作状态,以保持熔炉内部的温度稳定。
需要根据实际情况进行燃烧器的升降、开启或关闭等操作,以达到最佳燃烧效果和节约燃料的目的。
4. 熔炼操作4.1 搅拌熔炼熔炼过程中,需要定期进行搅拌操作,以保证熔炼均匀度。
搅拌时要注意力度的适中,并注意防止底部杂质的植入。
4.2 测温和采样根据需要,定期进行温度测量和取样,以确保熔炼过程的控制和成品质量的保证。
测温和采样时要小心操作,避免烫伤。
4.3 脱硅和添加剂根据需要,定期进行脱硅和添加剂的操作。
脱硅时要注意操作温度和时间,以确保脱硅效果。
添加剂时要根据铸件要求和材料特性进行控制,确保添加剂的准确性和合理性。
5. 浇注操作5.1 炉渣处理在进行浇注操作之前,需要对炉渣进行处理。
发生炉煤气镁还原炉技术方案
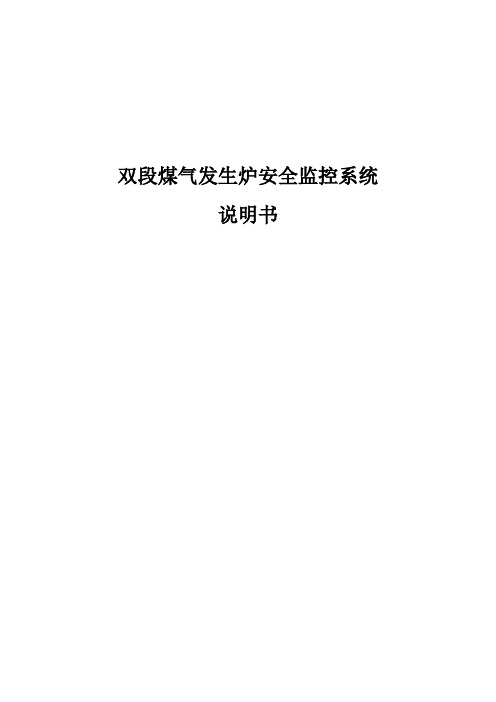
双段煤气发生炉安全监控系统说明书一.蓄热式镁还原炉技术简介1.蓄热式镁还原炉技术蓄热式高温空气燃烧技术(HTAC),是20世纪90年代以来在发达国家开始普遍推广应用的一种全新燃烧技术,它具有高效烟气余热回收和高温预热空煤气以及低污染排放等多重优越性。
我公司首次将HTAC蓄热式燃烧技术与金属镁冶炼相结合,从根本上克服传统金属镁还原炉燃烧效率低下、热量浪费严重、炉内温度不均一、炉内温度不好控制、污染严重的缺点,提供一种能耗低、炉内温度均一、利于控制炉温、提高生产效率及产品品质的高效节能环保型金属镁还原炉.新型的蓄热式镁还原炉技术在各个方面都有着无可比拟的优势,现已成功应用于宁夏华源镁业集团,投产后节能效果非常显著.其优点主要表现为:●采用高效蓄热回收技术,空、煤气双(单)预热到1000℃;●蓄热燃烧技术可应用于各种气体燃料;●炉内温度均匀,无局部高温点、低氧化烧损,延长还原罐的使用寿命;●比目前通用金属镁还原炉可节约能源达50%以上;●具有专利技术的换向和燃烧系统;●采用灵活的PLC控制方式;●提高反应速度,增加产量;●系统排烟温度:≤150℃;●降低NOx物和CO等有害气体的排放,可明显改善现场生产环境;●投资回收周期短,效益高;传统金属镁还原炉一般采用返热加热还原罐的结构。
这种传统结构的还原炉中的火焰和烟气翻过挡火墙进入炉膛,自上而下经过还原罐,很快的由过火孔排出炉膛,排烟温度可以高达1200℃左右,不能很好的回收利用,能源浪费严重。
此外,传统的金属镁还原炉使用原煤作为燃料,燃烧效率低下,污染严重.而且这种燃烧方式导致金属镁还原炉炉膛内部温度不均,燃烧温度控制不灵活,造成了还原罐寿命普遍太短,生产出的成品金属镁品质不高。
蓄热式镁还原炉克服了传统金属镁还原炉燃烧效率低下、热量浪费严重、炉内温度不均匀、炉内温度不好控制、污染严重的缺点。
提供一种能耗低、炉内温度均匀、利于控制炉温、提高生产效率及产品品质的新型高效的金属镁还原炉.可以说,蓄热式镁还原炉技术是金属镁还原炉的一次革命,必将成为金属镁还原炉系统改进的方向.蓄热式镁还原炉简单示意原理图见下图.其特征在于蓄热室(II)和蓄热室(I)中填充蓄热体——陶瓷蜂窝体或者陶瓷小球.炉外设置换向系统。
金属镁生产技术操作规程

煅烧车间四、回转窑操作规程(一)点火1、点火前检查各仪表是否正常,阀门是否开关到位。
电气设备是否完好,余热锅炉安全阀、放空阀、液位计等是否安装或调剂到位,准备好点火用具,余热锅炉按规定加好水。
2、提起烟道闸板,启动鼓风机对回转窑进行置换,放十分钟后关阀。
3、点燃点火用具,从窑头入孔探入到烧嘴出口部位,点火工要站在入孔侧面。
4、煤气水封放水,打开煤气水封进口阀门,然后徐徐开启煤气出口阀。
5、待烧嘴煤气充分燃烧后,撤出点火棍,徐徐开启风阀,正常火焰颜色为透明、淡青色,火焰过于发亮且刺眼说明风量大,火焰颜色浑浊黄色有烟说明配风不足。
6、如果点火没有成功,应立即关闭煤气,按点火顺序重新空气装置。
(二)升温、烘窑1、点火后,启动调速电机,开始转动窑体。
2、回转窑升温烘窑必须按照升温曲线进行操作。
3、随着窑温的不断上升观察窑体内衬得变化的情况。
4、窑壁温度上升至1120℃左右,开始下料。
(三)正常生产操作要求1、回转窑操作的宗旨:以最低的操作温度,生产出优质合格,满足下工段生产要求的段白。
2、根据下工段段白生产需求调节、窑温、转速、下料量。
3、控制窑头温度不超过1250℃,积尘室温度不超过700℃.若窑头温度偏高,可适当调整电机转速或适当关小煤气阀门;若窑头温度偏低,可适当降低调速电机转速,或调整煤气及阀门,但在提温的过程,窑头温度最高不可超过1300℃,根据窑头煅烧带温度高低可进行下料量和窑转速的适度调整。
4、调整烟道闸板,使回转窑处于微负压下操作。
5、以煅白外观颜色及化验数据综合分析判断煅白质量,控制煅烧温度,煅白颜色称焦黄并伴有大量黑斑视为过烧,发白视为欠烧,以外观淡黄色为合格。
6、下料工要服从窑温工的指挥,根据窑温工的指示调节下料量,严禁大幅度调节下料量。
7、回转窑、冷却机每班串窑不低于两次,每班上串、下串不低于30分钟。
8、拖轮轴承每星期加油一次,回转窑大齿圈及减速机变速箱等根据说明书定期加油或换油。
工业熔盐炉技术方案

云南文山铝业有限公司40万吨/年氧化铝工程熔盐炉设备第一部分RYL-1000M型熔盐炉技术简介一、前言根据云南文山铝业有限公司40万吨/年氧化铝工程项目中熔盐炉对物料加热的工艺要求,所设计的熔盐炉设备系统应满足在安全、可靠、稳定、高效运行的前提下,实现热媒系统供热温度的稳定性及可靠性。
为此,我们结合已有的成功范例,针对技术要求,分别就熔盐炉结构设计、供热工艺、燃烧室设计、控制方案及系统安全性进行阐述。
二、RYL-1000M型熔盐炉技术数据表三、执行标准Q/320281ARZ01-2001 熔盐炉GB/T17410-1998 有机热载体炉有机热载体炉安全技术监察规程蒸汽锅炉安全技术监察规程GB13271-2001 锅炉大气污染排放标准GB9222-88 水管锅炉受压元件强度计算GB5310-1995 高压锅炉用无缝钢管GB3323-87 钢熔化焊对接接头射线照相和质量分级`JB/T1610-93 锅炉集箱技术条件JB/T1611-93 锅炉管子技术条件JB/T4735-1997 钢制焊接常压容器GBJ211-1987 工业炉砌筑工程施工及验收规范GB150-1998 钢制压力容器GB151-1999 钢制管壳式换热器参照规范:HG20541-1992 化学工业炉结构设计规定HG20545-1992 化学工业炉受压元件制造技术条件HG/T20567-1994 热油炉技术条件HG/T20525-1992 化学工业管式炉传热计算规定HG/T20589-1996 化学工业炉受压元件强度计算规定HG/T20648-1990 化学工业炉耐火、隔热材料设计选用规定HG/T20682-1996 化学工业炉燃料燃烧设计计算规定GB50058-92 爆炸和火灾危险环境电力装置设计规范四、技术特点1、RYL-1000M型熔盐炉技术特点1.1 热效率比同类产品高3~5%,余热回收达1.2-1.5t/h(0.6MPa),每台全年可节约运行成本约30-38万元。
大型蓄热式金属镁还原炉炉内热过程的模拟与应用
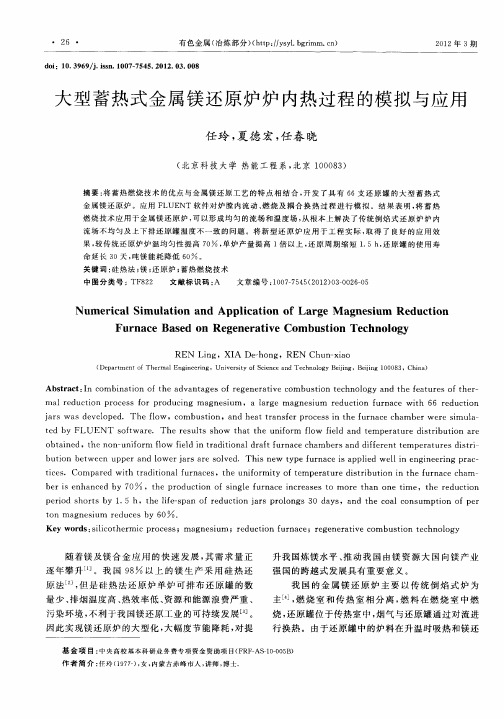
大 型 蓄 热式 金 属 镁 还 原 炉 炉 内热 过 程 的模 拟 与 应用
任 玲 , 德 宏 , 春 晓 夏 任
( 京科技 大 学 热 能工 程系 , 京 1 0 8 ) 北 北 0 0 3
摘 要 : 蓄热 燃 烧 技 术 的优 点 与 金 属 镁 还 原 工 艺 的特 点 相 结 合 , 发 了 具 有 6 将 开 6支 还 原 罐 的 大 型 蓄 热 式 金 属 镁 还 原 炉 。应 用 F UE L NT软 件 对 炉 膛 内流 动 、 烧 及 耦 合 换 热 过 程 进 行 模 拟 。结 果 表 明 , 蓄 热 燃 将
・
2 - 6
有色金属 ( 冶炼 部分 )ht : y y b r ( t / s1 g i p / . mm.n c)
21 0 2年 3 期
d i 1 . 9 9 J i n 1 0 —5 5 2 1 . 3 0 8 o : 0 3 6 ・ .s . 0 7 7 4 . 0 2 0 . 0 / s
REN n Li g,XI De h ng,REN A — o Chun x a — io
( p rme to e ma g n e ig,U nv riyo ce c n c n lg in De a t n fTh r lEn i e rn iest fS in ea d Te h o o y Bej g,Bejn 0 0 3,Chia i i g1 0 8 i n)
金属镁还原生产窑炉温度检测系统

—、热电偶的工作原理热电偶是一种感温元件,是一种仪表。
它直接测量温度,并把温度信号转热电偶换成热电动势信号,通过电气仪表(二次仪表)转换成被测介质的温度。
热电偶测温的大体原理是两种不同成份的材质导体组成闭合回路,当两头存在温度梯度时,回路中就会有电流通过,此时两头之间就存在电动势--热电动势,这就是所谓的塞贝克效应。
两种不同成份的均质导体为热电极,温度较高的一端为工作端,温度较低的一端为自由端,自由端通常处于某个恒定的温度下。
按照热电动势与温度的函数关系,制成热电偶分度表;分度表是自由端温度在o°c时的条件下取得的,不同的热电偶具有不同的分度表。
热电偶测温大体原理:将两种不同材料的导体或半导体A和B焊接起来,组成一个闭合回路。
当导体A和B的两个执着点1和2之间存在温差时,二者之间便产生电动势因此在回路中形成一个大小的电流,这种现象称为热电效应。
热电偶就是利用这一效应来工作的。
二、热电偶工作原理什么叫热电偶?这就要从热电偶测温原理提及,热电偶是一种感温元件,是一次仪表,它直接测量温度,并把温度信号转换成热电动势信号,通过电气仪表(二次仪表)转换成被测介质的温度。
热电偶测温的大体原理是两种不同成份的材质导体(称为热电偶丝材或热电极)组成闭合回路,当接合点两头的温度不同,存在温度梯度时,回路中就会有电流通过,此时两头之间就存在电动势——热电动势,这就是所谓的塞贝克效应。
两种不同成份的均质导体为热电极,温度较高的一端为工作端(也称为测量端),温度较低的一端为自由端(也称为补偿端),自由端通常处于某个恒定的温度下。
按照热电动势与温度的函数关系,制成热电偶分度表;分度表是自由端温度在°C时的条件下取得的,不同的热电偶具有不同的分度表。
在热电偶回路中接入第三种金属材料时,只要该材料两个接点的温度相同,热电偶所产生的热电势将维持不变,即不受第三种金属接入回路中的影响。
因此,在热电偶测温时,可接入测量仪表,测得热电动势后,即可知道被测介质的温度。
镁合金熔化安全技术操作规程

镁合金熔化安全技术操作规程清理炉膛—检查电阻丝—清理炉丝处氧化杂物—检查热电偶位置—检查托砖—检查电气元件—启动风机—检查坩埚—搅拌器、样勺、漏勺、浇包要在熔剂锅内预热并清洗干净。
油炉生产要检查输油管路是否畅通,开关是否正常。
2、装料熔化当坩埚预热至暗红色后,在坩埚底部撒入适量熔剂,清洗2次,用行车将坩埚吊出放在专用铁架上使其倾斜后用勺子将锅壁的残渣清理干净,吊回锅内,送电加温。
——将镁锭逐渐加入坩埚,升温熔化。
同时撒入部分熔剂预防燃烧, 决不允许一次加满坩埚,防止镁液燃烧时灭火不彻底。
——在熔化过程中,炉温应控制在900℃以下,不能过高,防止烧坏坩埚发生危险。
应有专人看护以便全面掌握炉料熔化情况,并适量撒入干燥熔剂防止镁液燃烧。
——镁锭加入前要预热,加镁锭应直立加入,严禁横搭或搭料疏松,以防熔化时塌陷,引起镁液飞溅。
——加入量不宜过多,合金液面应低于坩埚口20cm以下,在熔化过程中,要盖好炉盖,以减少热量损失。
熔化完全后升温至合金化或精炼。
3、合金化——按照温度要求必须将经过预热的中间合金依次加入镁液中,用搅拌器均匀搅拌,使之全部熔化。
将搅拌器缓慢伸入到合金液4/5深处,并按向下→向前→向上→向后的顺序作循环运动搅拌合金液,并在坩埚三个方向搅拌,使之均匀,搅拌速度在每分钟80次左右适宜,搅拌力度要伴有使液面浪花翻滚,直至液面呈银白色光亮如镜为止。
同时用漏筒向合金液中撒入已准备好的2#精炼剂,使用量按工艺参数执行,直到精炼结束。
精炼结束后,合金液面应呈银白色光亮如镜;用铁勺扒去熔液表面的附渣,并撒入适量精炼剂进行覆盖,镁锰合金液静置10分钟后,如有熔剂上冒现象应该重新精炼。
——精炼人员穿戴好工作服、防毒口罩、防护面屏等劳保用品。
——精炼时翻滚浪花不宜过大,以免溅出伤人和容易燃烧氧化。
——用氩气进行排气或精炼操作时应先使管中有少量气流,将通气管迅速插入熔液中、下部,避免熔液飞溅,气流量以保证熔液翻滚而不剧烈为宜。
镁合金熔化炉安全操作规程
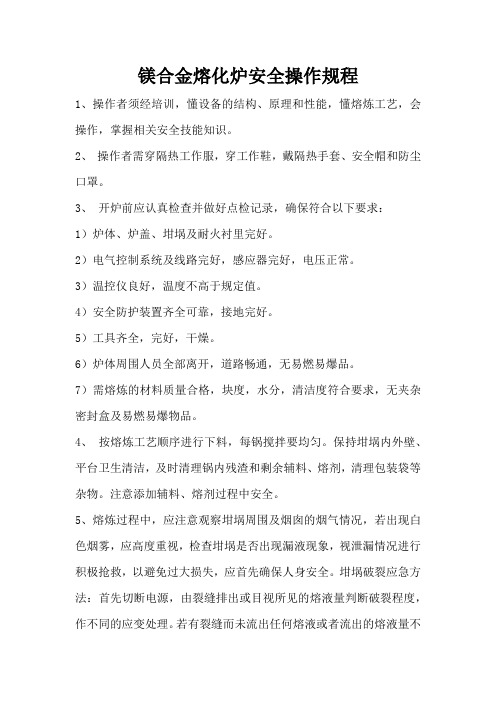
镁合金熔化炉安全操作规程1、操作者须经培训,懂设备的结构、原理和性能,懂熔炼工艺,会操作,掌握相关安全技能知识。
2、操作者需穿隔热工作服,穿工作鞋,戴隔热手套、安全帽和防尘口罩。
3、开炉前应认真检查并做好点检记录,确保符合以下要求:1)炉体、炉盖、坩埚及耐火衬里完好。
2)电气控制系统及线路完好,感应器完好,电压正常。
3)温控仪良好,温度不高于规定值。
4)安全防护装置齐全可靠,接地完好。
5)工具齐全,完好,干燥。
6)炉体周围人员全部离开,道路畅通,无易燃易爆品。
7)需熔炼的材料质量合格,块度,水分,清洁度符合要求,无夹杂密封盒及易燃易爆物品。
4、按熔炼工艺顺序进行下料,每锅搅拌要均匀。
保持坩埚内外壁、平台卫生清洁,及时清理锅内残渣和剩余辅料、熔剂,清理包装袋等杂物。
注意添加辅料、熔剂过程中安全。
5、熔炼过程中,应注意观察坩埚周围及烟囱的烟气情况,若出现白色烟雾,应高度重视,检查坩埚是否出现漏液现象,视泄漏情况进行积极抢救,以避免过大损失,应首先确保人身安全。
坩埚破裂应急方法:首先切断电源,由裂缝排出或目视所见的熔液量判断破裂程度,作不同的应变处理。
若有裂缝而未流出任何熔液或者流出的熔液量不多,呈绢丝状,应尽快用干燥的杓子将炉内的熔液舀出,倒至完好的坩埚内;若裂缝流出的熔液量大,如同倒水,这时要立即去切断电源,接着离开现场,从远处监视其动静。
6、最高熔炼温度和熔炼量不许超过炉的规定值,在熔炼过程中,应每2小时巡视一次炉底,如发现积水,应立即排水。
如有发现漏炉,应立即停电,停止熔炼。
7、熔炼过程中如发生短时停电,应做好保温;如停电较长时间,应会同其他作业人员将炉内熔化的金属液倒至其他完好坩埚。
8、记录坩埚使用次数和使用情况(温度、氧化程度等),应定期坩埚将按固定的方向依次转动,确保坩埚不在局部高温情况下工作,作好定期更换和检修。
9、每运行1-2周,应将坩埚吊出,检查炉体和坩埚安全状况。
停炉前作好准备工作,停炉后负责组织锅底清渣工作。
镁合金熔炼操作规范

镁合金熔炼操作法律规范预备工作:1.将所需熔炼的材料:AZ91D镁锭、熔解剂、精炼剂、掩盖剂根据生产支配进行配备,并且清除镁合金锭及回炉料表面的氧化物,保持炉料洁净、干燥。
2.熔解剂、精炼剂按熔炼100Kg镁锭使用IKg配备,掩盖剂按3Kg配备。
提前将镁合金熔炼过程中所需的化学熔剂进行加热,去除水分,一般预热温度选定在160℃,烘干30分钟。
3.选取浇注模具,表面喷涂395涂料,加热至350℃左右,等待浇注。
4.选取熔炼生烟,镁合金熔炼通常选用钢制蛆烟。
熔化前须将用期内的氧化皮清理洁净。
熔炼过程:1、熔化将用锅预热至暗红色(400-500C),在用锅内壁及底部匀称地撒上一层掩盖剂。
炉料预热至150℃以上加入,并在炉料上撤一层掩盖剂,装料时熔剂用量约占炉料重量的「2%,升温熔炼。
在装料及熔炼过程中,一旦发觉熔液露出,冒火星并燃烧,应马上补撒掩盖剂剂。
整个熔炼过程(不包括精炼)熔剂消耗约占炉料总重量的3%〜5%。
2、精炼处理将合金液升温至740〜760℃精炼10分钟,精炼过程中精炼剂的加入量为炉料量的L 5-2.0%左右,加入后充分搅拌,使熔液自下而上翻滚,不得飞溅,并不断在熔液的波峰上撒以精炼剂。
精炼结束后,清除合金液表面、用锅壁上的氧化渣,然后撒上掩盖剂。
随后静置15分钟。
浇注断口试样,检查断口,以呈致密、银白色为合格。
否则,需重新变质和精炼。
3、浇注使熔液的温度降至720〜740℃时,预备浇注。
浇注前必需对熔液进行扒渣处理,除去熔液表面的氧化物。
浇注完,在取液液面部位,匀称的撒一层掩盖剂,不使表面冒火星、启燃。
熔炼好的熔液静置结束后应在lh内浇注完,否则需重新浇注试样,检查断口,检查合格方可连续浇注,不合格需要重新精炼。
平安防护:1、生产现场必需清洁,不允许有任何积水、油污存在,并要有良好的通风、排气条件。
2、用于镁合金的灭火剂有干沙、掩盖剂,这些灭火器材应放置在醒目的地方,便于现场紧急使用,干沙及掩盖剂要存放在容器内防止潮湿,并要常常检查。
- 1、下载文档前请自行甄别文档内容的完整性,平台不提供额外的编辑、内容补充、找答案等附加服务。
- 2、"仅部分预览"的文档,不可在线预览部分如存在完整性等问题,可反馈申请退款(可完整预览的文档不适用该条件!)。
- 3、如文档侵犯您的权益,请联系客服反馈,我们会尽快为您处理(人工客服工作时间:9:00-18:30)。
青海盐湖工业股份有限公司镁业公司金属镁项目铸造车间温度大屏显示方案项目指挥部:根据生产实际需要,需在金属镁厂铸造车间厂房安装大屏监视融盐炉、连续精炼炉各四台共计144个温度数据(详细点位见附件联络函)。
我项目提出以下三种技术方案。
一、软件组态利用DP通讯实现现场大屏显示1、软件及系统通讯:在铸造车间机柜间增加一台操作员站,利用ABB的800XA组态软件将上位机里面的需要的温度参数分别提出动态链接成EXCEL表格画面,按照16:9的比例传输到现场大屏实时显示。
2、监视屏参数:监视屏采用led双基色显示屏,全屏显示以上144个温度的设备位号、点位及实时动态参数。
大屏尺寸采用16:9的比例拼接Φ 3.75mm双基色256级灰度LED视频屏技术参数指标:◆像素尺寸:Φ 3.75mm◆象素组成:1红◆单元板规格:306MM*153MM◆单元板点数: 64点*32点◆整屏点数:(横向×纵向)◆分辨率: 43800点/平米◆显示灰度: 256级灰度◆显示色彩: 256色◆视角: (阳光不直接的情况下)≥±45度◆屏体倾角: (参照水平面) 视要求而定◆屏体视距: 在2----30米内各种字体点阵文字清晰可见◆最佳视距: 5----20米◆连续显示: 大于24小时◆显示寿命: 大于10万小时◆通讯距离:大于300米(无间断)◆显示性能: 无拖边,无毛刺,画面无闪烁,无抖动◆单元重量:(含结构及电源件)小于50公斤/平方米◆总体尺寸:长 7 米,高 1.5 米◆总体面积:计 10.5 平方米◆通讯方式并行通讯(24对双绞通讯线)3、优点:现场操作工检视清楚,直观、投资成本较小。
4、缺点:占用操作员站、软件组态需增加费用。
二、智能移动终端访问过程数据在工作区范围内通过现场WIFI网络实现生产线设备状态的无线监控,使用智能手机或ipad等移动终端访问铸造车间上位机实时数据、图形及画面。
系统架构设备清单:名称型号单价RMB 数量发布服务器DELL R6 27000 1路由器TP-L 450 1室外天线TP-L 1500 1SIEC通讯软件SIEC 32502.75SIEC现场通讯调试6500 1人现场数据组态调试7500 1人IIS网站安全证书0系统特点:基于WEB架构,所需的仅仅是支持HTML5的网页浏览器,无线接入快,稳定,从不死机。
发展后劲大,系统预留通讯接口及计算机容量,方便以后其他工厂,销售,客户订单等数据服务器的接入及访问,无需额外硬件费用支出。
通讯原理:通过把原系统DCS数据实时传送到发布服务器,客户端可通过浏览器访问上位服务,通过预设的身份安全验证后,可对工厂实时数据情况进行远程监视,远程用户可以通过浏览器直接通过网页上的链接打开上位应用画面。
系统优点:不直接访问原有系统服务器,不影响原有服务器软件的运行,不增加原DCS 服务器负担,系统发展后劲大,方便扩展其他数据继续接入。
三、炉旁温度仪表接线箱改装无纸记录仪同步显示大屏1、实现方法:将现有炉旁温度仪表变送器模拟量接线箱改装成单色32通道无纸记录仪,拆除原有的温度变送器留作备件,实现现场操作员工实时察看炉内温度。
并可利用无纸记录仪485通讯接口同步至大屏显示温度数据、曲线和棒状图。
2、优点:无需加装操作员站和动用原程序,不影响系统正常运行。
就地和大屏都能显示、醒目、直观。
可节约温度变送器144台。
3、缺点:无纸记录仪需采购4台,直接投资成本较大。
以上三种方案,我项目部建议采用第一种方案。
具体涉及的硬件和软件清单见附表:请项目指挥部领导审定!青海盐湖镁业公司金属镁项目部 2016年6月14日大屏显示技术方案一、软件组态利用DP通讯实现现场大屏显示1、软件及系统通讯:在铸造车间机柜间增加一台操作员站,利用ABB的800XA组态软件自带的VBA脚本编程把原有上位机里面的144个温度参数读出来送到数据库或EXCEL表格里,再利用大屏幕自带的数据包软件将数据库或EXCEL表格里的数据传输到现场大屏幕实时同步显示。
2、监视屏参数:监视屏采用LED双基色显示屏,全屏显示以上144个温度的设备位号、点位及实时动态参数。
3、LED视频屏技术参数指标:P4.75SMD二合一技术参数采用SMD-LED材料工艺制造2.1像素点结构图A:结构示意图结构说明:每像素点采用SMD2121三合一发光管B:专业分析分析项目专业分析内容配色分析为使配色达到最佳的白平衡效果,配色对LED 发光的亮度有严格要求,其中红绿色亮度的配色比例为 R:G =4:62.2 像素点指标灯管颜色灯芯厂家指标(典型值,具体与所选灯有关)R(红) 台湾晶元波长:620~625nm,亮度210~280mcd G(绿) 台湾晶元波长:524~528nm,亮度520~610mcd2.3技术参数名称技术参数1、像素管像素点间距:4.75mm晶片产地:(红绿管)台湾晶元基色:红色+绿色发光点颜色组合:1R1G物理密度:44321点/m22、单单元板分辨率:宽64点×高32点单元板尺寸: 304mm×152mm元板单元板像素数:2048点/单元板3、显示屏整屏屏体显示面积:9.9㎡单元板数量:207件(23个长*9个高)物理分辨率: 1408*288点视角: 110°存贮温度: -40℃~ +85℃工作温度:-30℃~ +60℃相对湿度:10%~95%4、供电工作电压: 220V±15%平均功耗: 580W/m2最大功耗: 1700W/m25、控制系统控制主机:联想开天主机或同档次计算机以上操作系统:WIN 98/ 2000/ XP控制方式:同步控制显卡:DVI独立显卡6、主要技术参数1)驱动器件:恒流2)驱动方式:1/16扫3)刷新频率:≥600Hz4)帧频:≥60Hz5)灰度/颜色:4K/显示红绿黄三种颜色6)亮度:≥2500cd/m27)亮度调节方式:软件256级可调8)视频信号:RF、S-Video、RGB、RGBHV、YUV、YC、COMPOSITION等9)控制系统采用:PCTV卡(可选)+DVI显卡+主控卡+光纤传输(可选)10)平均无故障时间:7000小时11)寿命:10万小时12)平整度:任意相邻像素间≤0.5mm;单元板拼接间隙<1mm13)均匀性:像素光强、单元板亮度均匀14)杂点率:<0.000115)开关电源负荷:5V/40A、5V/30A16)计算机显示模式:1920*108017)有效通讯距离:网线100m(无中继),多模光纤500m,单模光纤20km7、软件LED播放软件包4、主要设备明细表:品名规格数量单位备注P4.75贰合SMD(6.778*1.458 m) 9.9 M2台湾晶元芯片一室内双基色显示屏电源5V、40A 以上包含同步系统发送卡 1 张数据发送接收(高刷新)接收卡 1 张LED播放软件 1 套外围设备控制主机(独立显卡) 1 套服务器DELL R640A空气开关 1 套路由器组态与通讯SIEC通讯软件 1 套ABBSIEC现场通讯调试 1 人现场数据组态调试 1 人ABB 800XA5、LED监控屏系统描述:本方案中显示屏幕墙显示部分由多面LED显示屏按照拼接方式排列组成,把上位机采集到的144个温度信号的画面,经过图像拼接处理器处理后输出,完成高分辨率拼接显示。
本显示屏系统具有高亮度、可全天候显示、显示内容和方式可根据实际情况进行修改、显示功能强大、功耗小寿命长等特点。
整套显示屏系统主要由以下及部分组成:1)拼接框架;由铝合金构成内框架,搭载显示板等各种电路板以及开关电源,外边框采用铝合金方管,或者铝合金包不锈钢,或钣金一体化制成。
2)显示单元:是显示屏的主体部分,由发光材料及驱动电路构成。
3)图像拼接处理器;可以灵活配置显示墙的输入信号数量,轻松将一个或者多个计算机的信号在大屏幕上进行显示,超高分辨率图形的全屏显示。
4)控制软件;控制软件对所有显示信号和显示模式进行各种灵活控制,可以进行单屏显示、跨屏显示、分区显示和整屏显示,也可以根据用户的需要设定不同的显示区域,并在指定区域内显示各种信号。
本项目中,大屏幕的信号源为上位机采集的现场数据,大屏幕显示的内容跟上位机显示的内容实时保持一致。
在大屏幕上完美展示现场工艺实际运行状态、技术参数。
当现场温度过高或者过低出现异常的时候,都可以很直观地在大屏幕上显示,及时提醒监控人员或者调度人员采取防预措施。
附件:其他显示方案性能比较55寸DID(液晶拼接)显示系统超窄边标亮高分辨率(2X5)技术方案西安晶安电子科技有限公司2016年6月我公司为此拼接显示墙设计的液晶屏是选用韩国三星电子双边拼缝 3.5mm最新生产的液晶拼接LED背光源面板,具有高亮度、高对比度、高像素等特点。
其发热量非常小。
液晶独特的显示原理、全数字化的驱动系统,以及散热设计方案,确保显示屏的高可靠性和稳定性,同时高强度拼接结构架和美观外型设计,使拼接显示屏既可靠实用又美观大方。
1.工程概况主体工程:55寸2×5液晶拼接屏的安装,实现高清视频,文件或图片展示、监控画面播放;配套工程:液晶拼接屏工程、综合布线工程,音响系统,装修包边。
工程流程:首先由甲方备好大屏供电电源,再由我们厂家安装人员进行安装壁挂式支架固定,施工人员把屏装好并调试好之后,由承包方按照用户方的要求装修包边。
2.系统组成1、拼接屏幕显示系统:55"液晶拼接显示单元(三星液晶屏面板)单屏图像拼接处理器应用管理软件包线材及配件HDMI矩阵专业壁挂式支架3.系统规格本方案采用的液晶拼接墙由晶安的LCD拼接显示单元拼接而成,选择如下方式:2x5 55″拼接,总共10个单元,尺寸规格如下:单屏面积:1213.5mm(宽) X 684.3mm (高)整屏面积:6067.5 mm (宽) X1368.6mm(高)安装结构图终端设备组成1、单屏图像控制器2、液晶屏拼接墙使用三星超窄边专业液晶屏,并经过技术处理,使其符合拼接墙的要求。
首创的液晶挂装设计。
通过对液晶屏进行结构技术处理,改变传统的液晶屏安装形式,使液晶单元装拆变得非常方便。
3、控制计算机拼接墙系统控制提供一个软件包,可安装于任何品牌的PC机,在windows环境下,运行软件并通过RS232串行通信,用于对拼接墙的信号和各种功能的控制。
4、各类线材各类线材将按实地安装数量及高度等数据进行定制。
5、HDMI矩阵晶安自主研发生产的控制器。
可靠性更好普通液晶屏为电视,PC显示器设计,不支持日夜连续使用;液晶屏为监视器、广告牌设计,支持在公众场合日夜连续使用。
接入信号可开多模式窗口每台液晶显示单元可同时接入多路外部信号,。
产品参数项目参数型号JA-553MA50面板类型三星超窄边面板尺寸55寸显示模式16:9背光类型LED亮度500cd/㎡对比度3500:1响应时间8ms分辨率1920×1080幕墙分辨率1920×1080或向下兼容显示色彩16.7M可视角度(左右/上178°/178°下)拼接边缝 3.5mm视频PAL/NTSC使用寿命60000~80000小时外形尺寸1213.5×684.3mm场频50Hz、60Hz、70Hz菜单语言English 中文;(需多种语言可选)拼接单元重量25kg面板控制按键+遥控器拼接墙安装方式落地机柜(电视墙)/墙体壁挂/移动钢架/吊挂壁挂厚度≤200mm壁挂材料铝合金型材支架电源内置电源输入和输出VGA 模拟RGB: 15PiMD-SUBDVI、HDMI 1YPbPr 1组S端子 1串口输入 1串口输出 1BNC输入 1BNC输出 1功率输入电压AC110-250V(50/60Hz)正常工作功耗≤380W待机功耗<3W工作环境温度0℃~60℃湿度10%~90%服务承诺保证其提供的设备是全新的、未使用过的,采用的是最佳材料和第一流的工艺,并在各个方面符合合同规定的质量、规格和性能要求。