主蒸汽温度控制系统
蒸汽温度自动控制系统

WT1S
1
1
时,1
21K
1
2.21K
;Ti1
T1K 1.2
WT1S
1
1
1
1 Ti1S
时,
(3)主、副回路投入后再作适当调整。
能源与动力工程学院 (二)衰减曲线法
步骤与临界曲线法略同,不同之处要注意!
串级控制系统产生共振效应的条件是:
1.副回路的工作频率ω2接近于共振频率ω; 2.主回路的工作频率ω1接近于副回路的工作频率ω2,即 T1P≈3T2P 。
实际生产中,通常把两种过热器结合使用,对流方式下吸收 的热量比辐射方式下吸收的热量要多,因此综合而言,过热器出 口汽温是随流量D的增加而升高的。
能源与动力工程学院
(2)动态特性 影响汽温变化的扰动因素很多,例如蒸汽负荷,烟气温度和
流速,给水温度,炉膛热负荷,送风量,给水母管压力和减温 水量。
归纳: 蒸汽流量,烟气传热量和减温水三个方面的扰动。 1)蒸汽流量扰动
能源与动力工程学院
(二)现场试验整定法
1、边界稳定法(临界曲线法) (1)先决定副调节器的比例带
主、副回路全部投入闭环,主调节器的参数设置:δ1置于较大位 置,Ti1=∞,Td1=0,副调节器的δ2 置于较大位置,且Ti2=∞,Td2=0, 而后便将副调节器的比例带由大往小调,使副回路产生不衰减振荡 (同时观察2),并记下此时的δ2K(临界比例带),T2K(振荡周 期),则副调节器的参数设置为:
2、锅炉过热汽温串级控制系统原理图
温度定值
主P调I1
副P调I2 执行器
内扰 阀门
θ2
减 导温前器区
过惰热性器区
θ1
变送器
变送器
主蒸汽温度控制系统

主蒸汽温度控制系统本机组的锅炉为单汽包、单炉膛、再热式自然循环锅炉。
由汽包分离分离出的蒸汽依次流过顶棚、热回收包覆面、初级过热器、屏式过热器和未级过热器,最后达到一定的温度离开锅炉。
两级喷水减温器分别布置于初过出口、屏过入口处和屏过出口、未级过热器入口处,如图1所示。
主蒸汽温度控制系统,通过这两级喷水减温,将未级过热器出口主蒸汽温度控制在某个定值上,并且保护整个过热器管路乃至主蒸汽管道及汽机金属不被高温损坏。
该系统分两级喷水控制,每级喷水又分左右两侧控制,如图1所示,同一级的两侧减温控制设计思想是相同的。
一、二级减温水控制系统是相互独立的,现分别予以剖析。
1.1 一级减温水控制一级减温水的作用,简单地说是将一级减温器出口温度即屏过入口温度控制在某个定值上。
图2为原理性框图。
这个温度定值通常是锅炉负荷(用汽机第一级压力P1代表),主汽压力P ,主汽压偏差△P 的函数(P1、P 、△P )。
其中,定值与负荷的关系,如图2中的曲线所示,而与压力的关系待定。
但在特殊工况下,这个定值还要受最小减温水量和最大减温水量的限制。
① 最小一级减温水量限制限制最小减温水量的目的是为了防止屏式过热器被高温烧坏,因屏过接受炉内高温火焰辐射,防止屏过内蒸汽温度过高尤为重要,因此最小一级减温水量限制又可理解成屏过出口最高蒸汽温度限制。
图2中,A1为屏过出口所允许的最高汽温值。
当屏过出口汽温高于这个最高值后,PID 1将逐渐减小输出,最后在小值选择器之后,将取代通常的定值(P1、P ,高过 屏过 初过 左侧 右侧 左侧 右侧 关断阀 调节阀 调节阀 关断阀 给泵 高加 给水截止阀和逆止阀 压力调节阀 汽包图 1 逆止阀隔离阀△P ),即去降低一级减温器出口温度定值,PID 0将去增加一级减温水量,从而降低整个屏过段的蒸汽温度。
② 最大一级减温水量限制限制最大一级减温水量目的是为了防止屏过入口汽温过低以致低于此处当前压力下水蒸汽的饱和点,所以又可将最大一级减温水量限制理解成屏过入口最低温度限制。
利用DCS的过热汽温系统控制系统设计

利用DCS的过热汽温系统控制系统设计一、集散控制系统分析集散控制系统是以微处理器为基础的集中分散控制系统。
自70年代中期第一套集散控制系统问世以来,集散控制系统己经在工业控制领域得到广泛的应用,越来越多的仪表和控制工程师已经认识到集散控制系统必将成为过程工业自动控制的主流。
集散控制系统的主要特性是它的集中管理和分散控制,而且,随着计算机技术的发展,网络技术己经使集散控制系统不仅主要用于分散控制,而且向着集成管理的方向发展。
系统的开放不仅使不同制造厂商的集散控制系统产品可以互相连接,而且使得它们可以方便地进行数据交换。
DCS集散式温度控制系统图二、DCS系统主要技术指标调研(1)操作员站及工程师站:CPU PⅢ850以上内存128M以上硬盘40G以上软驱 1.44M以太网卡INTEL 100M×2块加密锁组态王加密锁鼠标轨迹球键盘工业薄膜键盘显示器21寸显示器分辨率1280×1024过程控制站:CPU PⅢ850以上内存128M以上硬盘40G以上电子盘8M以上软驱 1.44M以太网卡INTEL 100M×1块串行通讯卡485卡×1块(可选)(2)I/O站技术指标1)EF4000网络EF-4000网络是多主站、双冗余高速网络,通信波特率为312.5K和1.25M可编程;EF4000网络配合EF4000系列测控站(前端),可以完成工业现场各类信号的采集、处理和各类现场对象的控制任务。
EF4000网络的主要技术指标如下:挂网主站数≤31挂网模块数≤100(不带网络中继器),最多240通讯速率 1.25MBPS和312.5KBPS可编程基本传输距离 1.2MBPS时≥500m,312.5KBPS时≥1600m允许中继级数≤4级双网冗余具备两个通信口互为冗余的功能网络通讯方式半双工同步传输介质聚乙稀双绞线网络隔离度≥500Vrms通信物理层全隔离、全浮空、平衡差动传输方式有效传输字节不小于34K字节/S(1.25MBPS通讯速率)2)通讯网卡主要技术参数型号EF-4000网络─ EF4001安装方式计算机PC总线扩展插槽插卡安装尺寸160×75mm宿主计算机具有AT插槽的IBM-PC及其兼容机I/O地址硬件任选100、120、140、160、180、1A0、1C0七种中断向量软件任意设定IRQ3、5、7、10、11、12、15或不使用耗电不大于1W工作方式连续可靠性指标MTBF80000Hr运行环境温度0~60C°,相对湿度≤80%3)模拟量输入前端模块型号EF4101输入通道数16路通道隔离电压400V(峰—峰值)网络隔离度≥500Vrms通道采样时间80mSA/D分辨率17位测量精度〈0.2%被测信号类型T/C、RTD、mV、mA4)模拟量输出前端模块型号EF4601输出通道数6路(全隔离)通道隔离电压500V网络隔离度≥500Vrms电压输出范围-10V ~ +10V电流输出范围0 ~ 20 mA控制精度0.2级5)数字量输入前端模块型号EF4201输入通道数28路通道隔离电压350V网络隔离度≥500Vrms计数速率≤500次/秒(低频通道)计数速率≤8000次/秒(高频通道)事件分辨率1mS(低频通道)计数长度24位(三字节)测频范围0 Hz ~ 8000 Hz(高频通道)6)数字量输出前端模块型号EF4203输出通道数16路(EF4203)通道隔离电压350V网络隔离度≥500Vrms结点开关电流≤100 mA结点开关电压≤350 V结点隔离电压≤350 V结点闭合时间≤0.6 mS结点断开时间≤0.15 ms7)执行器脉冲控制单元输出结点电压≤380 V输出结点电流≤5A系统网络采用国际上通用的Ethernet 网,通信速率为100Mbps,遵循IEEE 802.3协议。
热工控制系统第八章 汽温控制系统PPT课件

W X 1 S x y 1 1 S S 1 W T 1 S W W T 1 T S 2 W S T W 2 D S 1 W S D W 1 D S 2 W S D 2 W m S 1 S W Z S
(8-2) (8-3)
对于一个定值系统,扰动造成的影响应该越小越好,而定值部分应尽量保持恒定,因
1 WB 1
W0(s)
θ2
γθ2
上图中对应的主回路广义调节器的传递函数为:
W T2
sW 2B
1
2
1T1isTds
则主回路广义调节器的等效比例带为:
2
2 1 1 2
此时主回路广义调节器中各参数可以通过试验得到的等效被
控对象W0(s)的输出端过热汽温θ2在减温水量WB扰动下的阶跃响 应曲线,按单回路控制系统整定方法进行计算:(P175表6-6)
(8-5)
则有:
W b 2SK zK T 2K fK 2 1 K T 2K fK 2K m 2K z
T 2 1 K T 2K fK 2K m 2K z S 1
令: K b 2 1 K K T z2 K K T 2 fK K 2 fK K m 2 2K z,T b 2 1 K T 2K T f2 K 2K m 2K z
Iθ 2 -
I 2 1 1
内回路
γθ2
W2(s) θ2
主回路原理方框图 如果主调节器为PID调节器,其传递函数为:
WT2
s
1
2
1T1is
Tds
忽略导前区的惯性和迟延,则简化后导前区传递函数为:
W1
s
1
WB
1
1
此时主回路原理方框图可以简化为:
主蒸汽温度控制系统前馈的优化_康静秋

1 主蒸汽温度串级控制回路的前馈 控制器设计及仿真
由于火电机组的主蒸汽温度控制系统具有大延 且在不能够 完 全 使 用 一 阶 惯 性 环 节 代 替 串 迟特性 , 级控制系统干扰通 道 模 型 以 及 调 节 通 道 模 型 时 , 仅 利用近似的一阶惯性模型对前馈补偿器进行工程整
3] , 补偿效果差 , 不能完全消除主蒸汽温度的动态 定[
O t i m i z a t i o n o n f e e d f o r w a r d c o n t r o l l e r i n m a i n s t e a m t e m e r a t u r e - p p c o n t r o l s s t e m y
由于主蒸汽温 度 控 制 系 统 一 般 选 用 P I D- P I控 制器作为反馈控制器 , 因此将主蒸汽温度前馈 -串级 ) 。 控制系统简化为单回路前馈 -反馈控制系统 ( 图3
。
为了减少 “ 两个细则 ” 实施下快速变动负荷等对 主蒸汽温度的扰动 , 本文针对机组运行中具有不同 提出了在闭环辨 前馈回路的主蒸汽 温 度 系 统 模 型 , 识中对前馈回路的预处理方案和前馈动态配比整定 的原则及算法 。
1 1 2 , KANG J i n i u YANG Z h e n o n L I W e i h u a 1, Z HU k e g q y g,
, , 1. N o r t h C h i n a E l e c t r i c P o w e r R e s e a r c h I n s t i t u t e C o . L t d . B e i i n 1 0 0 0 4 5, C h i n a j g , , G u o h u a J i n i e E n e r C o . L t d . S h e n m u 7 1 9 3 1 9, S h a a n x i P r o v i n c e C h i n a 2. S h a a n x i j g y
660MW超临界机组过热蒸汽温度的控制系统及运行调整
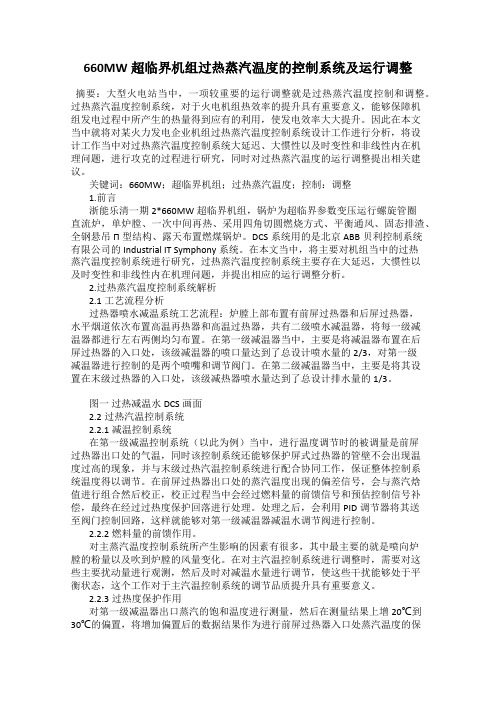
660MW超临界机组过热蒸汽温度的控制系统及运行调整摘要:大型火电站当中,一项较重要的运行调整就是过热蒸汽温度控制和调整。
过热蒸汽温度控制系统,对于火电机组热效率的提升具有重要意义,能够保障机组发电过程中所产生的热量得到应有的利用,使发电效率大大提升。
因此在本文当中就将对某火力发电企业机组过热蒸汽温度控制系统设计工作进行分析,将设计工作当中对过热蒸汽温度控制系统大延迟、大惯性以及时变性和非线性内在机理问题,进行攻克的过程进行研究,同时对过热蒸汽温度的运行调整提出相关建议。
关键词:660MW;超临界机组;过热蒸汽温度;控制:调整1.前言浙能乐清一期2*660MW超临界机组,锅炉为超临界参数变压运行螺旋管圈直流炉,单炉膛、一次中间再热、采用四角切圆燃烧方式、平衡通风、固态排渣、全钢悬吊Π型结构、露天布置燃煤锅炉。
DCS系统用的是北京ABB贝利控制系统有限公司的Industrial IT Symphony 系统。
在本文当中,将主要对机组当中的过热蒸汽温度控制系统进行研究,过热蒸汽温度控制系统主要存在大延迟,大惯性以及时变性和非线性内在机理问题,并提出相应的运行调整分析。
2.过热蒸汽温度控制系统解析2.1工艺流程分析过热器喷水减温系统工艺流程:炉膛上部布置有前屏过热器和后屏过热器,水平烟道依次布置高温再热器和高温过热器,共有二级喷水减温器,将每一级减温器都进行左右两侧均匀布置。
在第一级减温器当中,主要是将减温器布置在后屏过热器的入口处,该级减温器的喷口量达到了总设计喷水量的2/3,对第一级减温器进行控制的是两个喷嘴和调节阀门。
在第二级减温器当中,主要是将其设置在末级过热器的入口处,该级减热器喷水量达到了总设计排水量的1/3。
图一过热减温水DCS画面2.2过热汽温控制系统2.2.1减温控制系统在第一级减温控制系统(以此为例)当中,进行温度调节时的被调量是前屏过热器出口处的气温,同时该控制系统还能够保护屏式过热器的管壁不会出现温度过高的现象,并与末级过热汽温控制系统进行配合协同工作,保证整体控制系统温度得以调节。
锅炉主蒸汽温度模糊PID控制系统的研究

图1 模糊控制 的基本原理 图 模 糊控制基本 原理如 图 1 示 , 所 虚线 内为模糊 控制器 , 其控制 规律 由计 算机程 序实现 。当变送器 测到系统 的被 调量值后 , 与给定值进 行 比较得 到偏差信 号 E E , 是一 个精确 的模拟量 , A D 经 / 转换 后作用 到模 糊 控制器 的输入 。进入模糊控 制器后 , 先经过量化 处理将基本论 域 首 中的 偏差值 E变 成模糊 集论 域中 的值然后 进行 模糊化 处理 变成模 糊 量, 可用相应 的模糊 语言来描述 。这 样 , 就得到 了误差 E的模糊语 言集 合 的一个子集 旦 。再 由 £和模糊控制规 则 墨 根据推理 的合 成规 则进 行模糊决 策 , 然后 得到模糊 控制量 旦 , : =旦 ・ , 即 旦 笪 而施加在 被控 对象上的量需要 的是精确量 , 以还需要将模糊控制量 旦 转换 成精确 所 量, 即进行非模糊 化处理得到实 际的精确控制数字量 , DA转换 后通 经 / 过执行 机构施加在被控对象上 。 三 、 糊 PI 制 系 统 结构 原 理 模 D控 模 糊 PD控制 器 以传统 PD控制 器 为基础 , I I 引入模 糊 集合 论 , 将 P D参数根据偏差 和偏 差变化值 的大小而动态变化 , I 这样显然更符合被 控对象真实 的控制 规律 。模糊 控制器将主汽温偏差 和偏差 变化率转换 为模 糊量, 经过模糊控制规则 的处理得到模糊输 出量 , 最后将模糊 变量 去模糊化 处理得 到精确值 , 作为副调节 器 PD 的参考 输入信号 。模 糊 I 控制系统 的结构 主要由模糊控 制器和被控 制对象两部分 组成 , 结构 其 如图 2 所示 。经过主蒸汽流量修 正的输 人 r 为系统设定值( 确量) = 精 。e rY _ 为系统误差, C d/ 为误差变化率( e- e t d 精确量) Y , 为系统的输 出量 ( 精 确量) 。误差 e 和误 差变化率 e 作 为输入信号进入模 糊控制器 。u c 作为 模糊 控制器的输 出, 经过反模糊化去控制被控对象 。
锅炉蒸汽温度控制系统 2讲解

21
实际运行中,用改变燃烧器的倾角来调节再热汽 温的方法存在一些问题: 1)有较大的延迟性; 2 )由于锅炉燃用灰熔点较低的煤,燃烧器周围 容易结渣,摆动式燃烧器易卡住而不能正常调节; 3 )如燃烧器下倾角度过大,会使冷灰斗处温度 上升,结渣加剧;严重时曾造成人孔门烧红,整个冷 灰斗封住,锅炉被迫停用的局面。
锅炉蒸汽温度控制系统
§1 概 述
§2 过热蒸汽温度控制策略
§3 过热蒸汽温度控制系统实例 §4 再热蒸汽温度控制策略 §5 再热蒸汽温度控制系统实例
1
§1
概
述
2
一、蒸汽温度控制的任务 1. 过热蒸汽温度控制的任务 维持过热器出口温度在允许的范围之内,并保护过热 器,使其管壁温度不超过允许的工作温度。 过热蒸汽温度是锅炉汽水系统中的温度最高点,蒸汽 温度过高会使过热器管壁金属强度下降,以至烧坏过热器 的高温段,严重影响安全。 过热蒸汽温度偏低,则会降低发电机组能量转换效率, 据分析,汽温每降低5℃,热经济性将下降1%;且汽温偏 低会使汽轮机尾部蒸汽湿度增大,甚至使之带水,严重影 响汽轮机的安全运行。一般规定大容量高参数火力发电机 +5 o 540 组都要求保持过热蒸汽温在 的范围内。 - 10 C
10
三、蒸汽温度控制对象的动态特性 1. 过热蒸汽温度对象的动态特性 主要为蒸汽流量、烟气传热量和减温水扰动。 (1)蒸汽扰动下对象的动态特性 引起蒸汽流量变化的原因有二:一是蒸汽母管的压力 变化,二是汽轮机调节汽门的开度变化。结构形式不同的 过热器,在相同蒸汽流量D的扰动下,汽温变化的静态特 性是不同的。对于对流式过热器的出口温度,随着蒸汽流 量D的增加,通过过热器的烟气量也增加,导致汽温升高; 对于辐射式过热器,蒸汽流量D增加时,炉膛温度升高较 少,炉膛辐射给过热器受热面的热量比蒸汽流量的增加所 需的热量要少,因此辐射式过热器的出口汽温反而下降, 对流式过热器和辐射式过热器的出口汽温对负荷变化的反 应是相反的,其静态特性如下。
- 1、下载文档前请自行甄别文档内容的完整性,平台不提供额外的编辑、内容补充、找答案等附加服务。
- 2、"仅部分预览"的文档,不可在线预览部分如存在完整性等问题,可反馈申请退款(可完整预览的文档不适用该条件!)。
- 3、如文档侵犯您的权益,请联系客服反馈,我们会尽快为您处理(人工客服工作时间:9:00-18:30)。
主蒸汽温度控制系统
本机组的锅炉为单汽包、单炉膛、再热式自然循环锅炉。
由汽包分离分离出的蒸汽依次流过顶棚、热回收包覆面、初级过热器、屏式过热器和未级过热器,最后达到一定的温度离开锅炉。
两级喷水减温器分别布置于初过出口、屏过入口处和屏过出口、未级过热器入口处,如图1所示。
主蒸汽温度控制系统,通过这两级喷水减温,将未级过热器出口主蒸汽温度控制在某个定值上,并且保护整个过热器管路乃至主蒸汽管道及汽机金属不被高温损坏。
该系统分两级喷水控制,每级喷水又分左右两侧控制,如图1所示,同一级的两侧减温控制设计思想是相同的。
一、二级减温水控制系统是相互独立的,现分别予以剖析。
1.1一级减温水控制
一级减温水的作用,简单地说是将一级减温器出口温度即屏过入口温度控制在某个定值上。
图2为原理性框图。
这个温度定值通常是锅炉负荷(用汽机第一级压力P1代表),主汽压力P,主汽压偏差△P的函数(P1、P、△P)。
其中,定值与负荷的关系,如图2中的曲线所示,而与压力的关系待定。
但在特殊工况下,这个定值还要受最小减温水量和最大减温水量的限制。
①最小一级减温水量限制
限制最小减温水量的目的是为了防止屏式过热器被高温烧坏,因屏过接受炉内高温火焰辐射,防止屏过内蒸汽温度过高尤为重要,因此最小一级减温水量限制又可理解成屏过出口最高蒸汽温度限制。
图2中,A1为屏过出口所允许的最高汽温值。
当屏过出口汽温高于这个最高值后,PID1将逐渐减小输出,最后在小值选择器之后,将取代通常的定值(P1、P,
△P),即去降低一级减温器出口温度定值,PID0将去增加一级减温水量,从而降低整个屏过段的蒸汽温度。
②最大一级减温水量限制
限制最大一级减温水量目的是为了防止屏过入口汽温过低以致低于此处当前压力下水蒸汽的饱和点,所以又可将最大一级减温水量限制理解成屏过入口最低温度限制。
图2中,f(x)输出为相应压力下屏过入口蒸汽的饱和温度,在此基础上再加上A2(约11℃)的过热度,这个和值在大值选择器中与前级的小选输出进行比较,取大值输出。
这样就可限制屏过入口蒸汽温度定值,使其不致低于饱和点,从而防止了屏过入口蒸汽带水。
如果不出现两种极端情况,即屏过出口汽温过高或屏过入口汽温过低,定值将是f(P1、P、△P)。
实际屏过入口温度与其定值求偏差后,经PID0调节器运算,其输出去调节一级减温水量最终使屏过入口实际汽温与其定值相等。
由此可见,一级减温水控制回路只是一个单回路调节系统,虽然虽然在框图中有两个PID调节器“串联”在一起,但并不是串级控制系统。
1.2二级减温水控制
二级减温水的主要任务是将未级过热器出口蒸汽温度控制在某个定值上,原理框图见图3。
这个温度定值是锅炉蒸汽负荷的函数,如图4。
该控制回路是一个典型的带导前信号的串级汽温控制回路。
调节器PID0的输出作为PID1的定值,与未级过热器入口汽温求偏差后,在PID1中进行运算,其输出则为二级减温水指令的一部分。
在这里,未级过热器入口汽温实际上是一个导前信号,它能迅速地反映未级过热器全段蒸汽温度变化的趋势,因此,在系统中它能起到改善主汽温调节品质的作用。
图3中,二级减温水采用f(P1、P、△P)作为前馈指令,当锅炉负荷增加时,及主汽压力下降时,这一指令有所增加。
加入前馈指令,对于减轻锅炉负荷变化对主汽温度的扰动和由于锅炉运行压力变化对汽温特性的影响有积极作用。
前馈指令与PID1的输出相加,成为二级减温水量指令。
1.3减温水调节阀的分裂式(split)设计
如图1所示,每级每侧减温水调节阀都分成低流量调节阀和高流量调节阀,低流量调节阀的容量为该级该侧最大设计减温水量的25%,其余75%由高流量调节阀承担,这种设计有利于减小减温水调节阀体积,提高阀门的线性度和调节精度。
2.系统运行
2.1关断阀的控制
当下列条件全部满足时,自动打开关断阀。
①锅炉蒸汽流量>10%MCR。
②无主燃料跳闸MFT。
③控制系统已要求低流量阀有一定的开度(约2%)。
上述任一条件不满足(对于条件③是指开度指令小于约1%),以及当大、小调节阀都已关闭时,则关闭关断阀。
2.2调节阀的运行
当下列条件全部满足时,允许对调节阀进行控制。
①锅炉蒸汽流量>10%MCR。
②无主燃料跳闸MFT。
任一条件不成立,则关闭调节阀。
2.3手动/自动站的运行(共四只站)
2.3.1一级减温水控制站(两侧相似)
作用:控制一级减温水量。
显示:PV柱,显示本侧屏过入口汽温(测量故障时,指示为零)。
(℃)。
SP柱,显示本侧屏过入口汽温定值℃)。
下列任一条件出现,站切手动。
①本侧屏过出口温度或初过出口压力测量信号,或主汽压力、差压、流量信号测量质量不好,或传输到本系统后出现质量不好。
②本侧一级减温器出口温度测量系统发出“置手动”信号。
③本侧小流量调节阀开度已达6%,而关断阀仍处于关闭状态。
④主燃料跳闸MFT。
⑤主蒸汽流量小于10%MCR。
操作;
①无SP操作。
②手动方式时,可手操CO按扭,以改变减温水,但若由于MFT或主蒸汽流量小于10%MCR的原因而导致手动,站的输出将跟踪零,“TRACK”灯亮,此时不可手动改变控制输出。
2.3.2二级减温水控制站(两侧相似)
作用:控制二级减温水量。
显示:PV柱,显示未级过热器出口蒸汽温度(℃)。
SP柱,显示未级过热器出口温度定值(℃)。
下列任一条件出现,站切手动。
①未级过热器出口蒸汽温度测量系统发出“置手动”信号。
②主蒸汽流量、一级压力、压力、差压信号测量系统发出“置手动”信号或者在传输到本系统后发现质量不好。
③本侧未过入口汽温信号质量不好。
④本侧小流量调节阀开度已达6%,而关断阀仍处于关闭状态。
⑤主燃料跳闸MFT。
⑥主蒸汽流量小于10%MCR。
操作:
①无SP操作。
②手动方式时,可手操CO按扭,以改变减温水,但若由于MFT或主蒸汽流量小于10%MCR的原因而导致手动,站的输出将跟踪零,“TRACK”灯亮,此时不可手动改变控制输出。