筒体制造工艺设计流程通用模板
筒体制造工艺规程

文件号:
修改单:
第1页共3页
1.主题内容与适用范围
本标准规定了筒体制造的通用工艺。
本标准适用于我公司压力容器产品筒体的制造。
2.引用标准
2.1 压力容器安全技术监察规程。
2.2 GB150钢制压力容器。
2.3 QJG/JL01—2010《下料工艺规程》。
3.筒体成型
3.1筒体成型前应检查所准备的材料及坡口形式是否符合图样及工艺的要求,没有材料代号标记的,未作对角线(或中心线)检查及基准线标记的材料,不得成形。
10.承受外压及真空容器组装完成后,按如下要求检查壳体的圆度。
10.1用内弓形样板或外弓形样板测量。样板圆弧半径等于壳体的设计内半径或外半径,其弦长等于按GB150中图6—12查得的弧长的两倍。测量点应避开焊接接头或其它凸起部位。
10.2用样板沿壳体外径或内径径向测量的最大正负偏差e不得大于由GB150—1998图10—11中查得的最大允许偏差值。
3.2筒体成形一般采用卷板机冷卷工艺,按照板材厚度和公称直径,合理选用卷板机。
3.3卷板时必须清除板材上的铁屑及杂物,卷板过程中必须扫去剥落下来的氧化皮,以防产生压坑及损坏设备,滚制不锈钢板时应注意防止划伤和压坑产生。
3.4卷板时板材必须放正,保证两侧与滚轴轴线垂直,防止错边及大小口,注意板材坡口的方向,材料标记的位置,反正面不得颠倒。
当两板厚度差小于上列数值时对口错边量b按4.2条要求,且对口错边量b以较薄板厚度为基ቤተ መጻሕፍቲ ባይዱ确定。在测量对口错边量时,不应计入两板厚度的差值。
5.5.2壳体直线度允差不大于壳体长度的1‰或图样。
注:壳体直线度检查是通过中心线的水平和垂直面,即沿圆周0℃、90℃、180℃、270℃四个部位拉φ0.5mm的细钢丝测量,测量位置离A类接头焊缝中心线的距离不小于100mm,当壳体厚度不同时,计算直线度时应减去厚度差。
尿素合成塔筒体制造

6.3.3、筒体制造由6.3.1.1节讨论已知,本设备筒体采用以不锈钢衬里作为内筒的多层包扎焊接式筒体。
6.3.3.1筒体制造流程筒体由许多筒节组焊成,每一个筒节都是由外壳层板、盲层板和衬里内筒组成,内筒不锈钢耐蚀层,厚度为8mm,盲层板厚度为6mm,九层外壳层板厚度均为10mm,共104mm。
筒体的制造工艺过程是:内筒→卷园(DT)→纵坡口加工(DT)→焊接(带试板)→校圆→装配内衬胎→扎盲层板→焊接(不满焊)→包扎焊接层板→第一层MT、HT→继续包扎焊接层板→逐层检查包扎贴紧度→钻警报气→最后一层纵缝不铣磨平要作MT、HT→加工环缝坡口(DT)→钻镗检漏孔(DT)→环缝坡口封焊→PT→筒节与筒节组对焊接→筒体与(封头)组对焊接(DT)→焊装附件→充水进行水压试验→氨渗漏试验(验收依据)→最终检验→清理、打磨→外壁PT、MT→油漆→装运→发送。
注:DT-尺寸检验PT-液体渗透检测RT-射线探伤检测FT-铁素体检测MT-磁粉检测⑴主要零部件的制造主要零部件包括:内筒、盲板层、层板、筒节的包扎等①内筒制造内筒制造过程见表6-31表6-31 内筒制造过程焊缝表面着色探伤;纵焊缝X光探伤检查;焊接试板的晶间腐蚀倾向试验等检查内筒制造的主要工序:ⅰ制造的特殊要求a超低碳奥氏体不锈钢的制作,要求有一个清洁的场地和环境,避免铁素体污染和磕碰划伤,否则会影响不锈钢的耐蚀性能。
因此,参加尿素合成塔内筒衬里或其他内件制造的工人要接受这方面工艺守则的教育,并在施工过程中严格遵守;下料场地应打扫干净,消除杂物,可采用橡胶板铺地,并禁止穿带有铁钉子的皮鞋,撬具、吊耳也应采用奥氏体不锈钢制作。
卷制内筒时必须在专用的卷板机上进行。
不能与卷过铁素体钢的卷板机混合使用,除非将卷过碳钢的卷板机辊子表面进行认真的清洗。
当超低碳奥氏体不锈钢冷变形超过20%,应进行提高耐蚀性能的固溶热处理。
热处理炉内的气体应尽量减少硫的含量,防止硫化物对不锈钢的渗透降低耐蚀性能。
过程设备制造课程设计筒体制造实例

普通高等学校“十一五”规划教材过程设备制造课程设计——筒体制造实例科技大学编著化学工业教材出版中心第一章氮气储罐制造工艺设计说明书模板一,制造背景1.1液化石油气,英文名称: Liquefied petroleum ges,主要成分:乙烯、乙烷、丙烷、丙烯、丁烷、丁烯等。
随着石油化学工业的发展,液化石油气作为一种化工基本原料和新型燃料,已愈来愈受到人们的重视。
在化工生产方面,液化石油气经过分离得到乙烯、丙烯、丁烯、丁二烯等,用来生产合塑料、合成橡胶、合成纤维与生产医药、炸药、染料等产品。
用液化石油气作燃料,由于其热值高、无烟尘、无炭渣,操作使用方便,已广泛地进入人们的生活领域。
此外,液化石油气还用于切割金属,用于农产品的烘烤和工业窑炉的焙烧等。
而液化石油气储罐是具有较大危险性的储存容器,一旦出现问题,将给人民的生命、财产带来极大的损失。
、等地的液化气储罐事故给人们以深刻的教训。
为了保证液化石油气储罐的安全运行,避免事故发生,必须从个方面严格把关,其中,筒节的制作过程是关键中的关键。
产品名称: 40M3液化石油气卧式储罐产品类别:三按照《特种设备安全监察条例》的规定,该台产品经制造单位监督检验,安全性能符合《压力容器安全基数监察规程》,《GB150-1998 钢制压力容器标准》与设计图样的规定。
1.2设计参数1.3技术要求(1)本设备按照GB150-1998《钢制压力容器》进行制造,检测与验收,并接受《压力容器安全技术监察规程》的监督。
(2)制造筒体、封头、人孔接管、用16MnR钢板符合GB6654-1996与第二次改造通知单的规定,人孔法兰盖用钢板正火状态供货。
帯颈对焊法兰、接管用16MnR应符合4726-2000,壳体用16MnR钢板应逐进行冲击试验,方法按照GB/T229的规定,三个试样的平均值大于等于54J。
(3)设备焊接工艺规程按照/T4709-2000,焊接工艺评定按照4708-2000.所有角接接头的焊接表面须打磨圆滑过渡。
尿素合成塔主要零部件的制造工艺流程设计_图文(精)
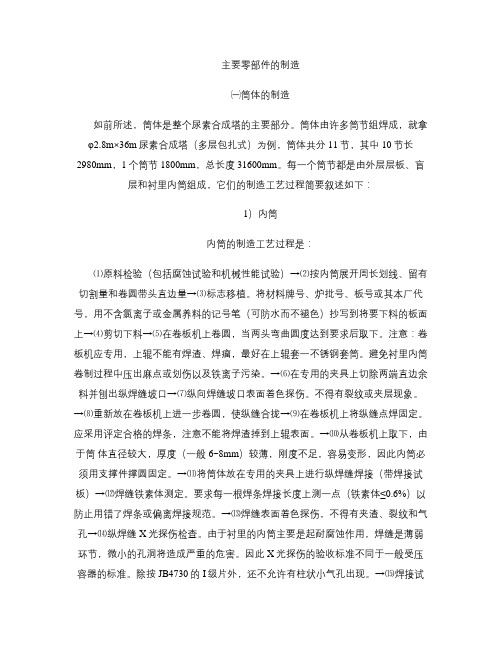
主要零部件的制造㈠筒体的制造如前所述,筒体是整个尿素合成塔的主要部分。
筒体由许多筒节组焊成,就拿φ2.8m×36m尿素合成塔(多层包扎式)为例,筒体共分11节,其中10节长2980mm,1个筒节1800mm,总长度31600mm。
每一个筒节都是由外层层板、盲层和衬里内筒组成,它们的制造工艺过程简要叙述如下:1)内筒内筒的制造工艺过程是:⑴原料检验(包括腐蚀试验和机械性能试验)→⑵按内筒展开周长划线、留有切割量和卷圆带头直边量→⑶标志移植。
将材料牌号、炉批号、板号或其本厂代号,用不含氯离子或金属养料的记号笔(可防水而不褪色)抄写到将要下料的板面上→⑷剪切下料→⑸在卷板机上卷圆,当两头弯曲圆度达到要求后取下。
注意:卷板机应专用,上辊不能有焊渣、焊瘤,最好在上辊套一不锈钢套筒。
避免衬里内筒卷制过程中压出麻点或划伤以及铁离子污染。
→⑹在专用的夹具上切除两端直边余料并刨出纵焊缝坡口→⑺纵向焊缝坡口表面着色探伤。
不得有裂纹或夹层现象。
→⑻重新放在卷板机上进一步卷圆,使纵缝合拢→⑼在卷板机上将纵缝点焊固定。
应采用评定合格的焊条,注意不能将焊渣掉到上辊表面。
→⑽从卷板机上取下,由于筒体直径较大,厚度(一般6~8mm)较薄,刚度不足,容易变形,因此内筒必须用支撑件撑圆固定。
→⑾将筒体放在专用的夹具上进行纵焊缝焊接(带焊接试板)→⑿焊缝铁素体测定。
要求每一根焊条焊接长度上测一点(铁素体≤0.6%)以防止用错了焊条或偏离焊接规范。
→⒀焊缝表面着色探伤,不得有夹渣、裂纹和气孔→⒁纵焊缝X光探伤检查。
由于衬里的内筒主要是起耐腐蚀作用,焊缝是薄弱环节,微小的孔洞将造成严重的危害。
因此X光探伤的验收标准不同于一般受压容器的标准。
除按JB4730的I级片外,还不允许有柱状小气孔出现。
→⒂焊接试板的晶间腐蚀倾向试验和选择性腐蚀检查及金相检查。
其方法按HG/T3172和HG/T3173、HG/T3174验收标准按GB9842或工程标准的规定。
【毕业设计】筒体制造工艺设计

筒体制造工艺设计目录引言 (1)1筒体概况 (3)化学成分和力学性能 (3)焊接性分析 (3))焊接方法与焊接材料 (4)遵守的规范和标准 (4)2筒体板的备料工艺 (4)备料 (4)材料复验、入库 (5)钢材的预处理 (5)钢板的娇平........................................................................... .. (5)钢板的除锈........................................................................... (6)—3筒体板的成形工艺 (7)一次号料 (7)一次下料 (8)筒体板的压形 (9)二次号料 (9)二次下料 (9)筒体板的修形 (10)4工装夹具........................................................................... (10){5筒体的焊接工艺 (10)施焊环境 (11)焊前准备 (11)焊接工艺评定 (11)焊条干燥........................................................................ (11)预热........................................................................... (12)焊接工艺........................................................................... .. (13)纵缝焊接参数........................................................................... (13)(点固焊........................................................................... (14)纵缝焊接参数........................................................................... (15)6焊接顺序及注意事项........................................................................... . (16)结论................................................................ (17)致谢................................................................ (20)参考文献 (21):摘要本次设计中的筒体,其壳板的材质为16MnR,本文对其母材的焊接性做了简要的分析,并在此基础上选择了筒体焊前的预热温度,以及焊接方法和焊接材料。
加氢反应器筒体制造
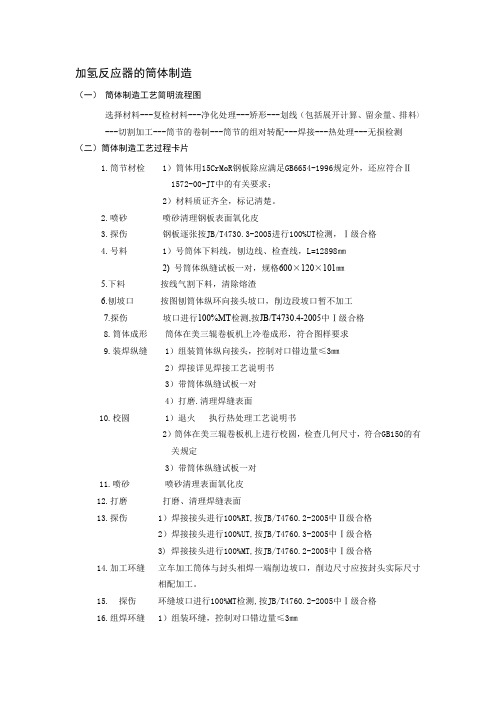
加氢反应器的筒体制造(一)筒体制造工艺简明流程图选择材料---复检材料---净化处理---矫形---划线(包括展开计算、留余量、排料)---切割加工---筒节的卷制---筒节的组对转配---焊接---热处理---无损检测(二)筒体制造工艺过程卡片1.筒节材检1)筒体用15CrMoR钢板除应满足GB6654-1996规定外,还应符合Ⅱ1572-00-JT中的有关要求;2)材料质证齐全,标记清楚。
2.喷砂喷砂清理钢板表面氧化皮3.探伤钢板逐张按JB/T4730.3-2005进行100%UT检测,Ⅰ级合格4.号料1)号筒体下料线,刨边线、检查线,L=12898㎜2)号筒体纵缝试板一对,规格600×120×101㎜5.下料按线气割下料,清除熔渣6.刨坡口按图刨筒体纵环向接头坡口,削边段坡口暂不加工7.探伤坡口进行100%MT检测,按JB/T4730.4-2005中Ⅰ级合格8.筒体成形筒体在美三辊卷板机上冷卷成形,符合图样要求9.装焊纵缝1)组装筒体纵向接头,控制对口错边量≤3㎜2)焊接详见焊接工艺说明书3)带筒体纵缝试板一对4)打磨.清理焊缝表面10.校圆1)退火执行热处理工艺说明书2)筒体在美三辊卷板机上进行校圆,检查几何尺寸,符合GB150的有关规定3)带筒体纵缝试板一对11.喷砂喷砂清理表面氧化皮12.打磨打磨、清理焊缝表面13.探伤1)焊接接头进行100%RT,按JB/T4760.2-2005中Ⅱ级合格2)焊接接头进行100%UT,按JB/T4760.3-2005中Ⅰ级合格3)焊接接头进行100%MT,按JB/T4760.2-2005中Ⅰ级合格14.加工环缝立车加工筒体与封头相焊一端削边坡口,削边尺寸应按封头实际尺寸相配加工。
15.探伤环缝坡口进行100%MT检测,按JB/T4760.2-2005中Ⅰ级合格16.组焊环缝1)组装环缝,控制对口错边量≤3㎜2)焊接详见焊接工艺说明书3)打磨、清理焊缝表面4)按热处理工艺进行炉外消氢处理17.打磨打磨、清理焊缝表面18.探伤1)焊接接头进行100%RT,按JB/T4760.2-2005中Ⅱ级合格2)焊接接头进行100%UT,按JB/T4760.3-2005中Ⅰ级合格3)焊接接头进行100%MT,按JB/T4760.2-2005中Ⅰ级合格19.堆焊过渡层1)堆焊过渡层,详见焊接工艺说明书2)按热处理工艺进行炉外消氢处理3)打磨、清理过渡层20.探伤过渡层进行100%PT检测,按JB/T4730.5-2005中Ⅰ级合格21.堆焊筒体表层1)堆焊表层,详见焊接工艺说明书2)测铁素体数3)打磨、清理表层22.筒体探伤1)表层进行100%PT检测,按JB/T4730.5-2005中Ⅰ级合格2)堆焊层及熔合面进行100%UT,符合Ⅱ1572-00-JT中的有关要求3)堆焊层进行厚度检测,符合图纸要求(三)、筒体制造工艺流程具体内容1、选择材料此加氢反应器筒体材料选择15CrMoR。
【最新文档】筒体划线步骤-word范文模板 (4页)

本文部分内容来自网络整理,本司不为其真实性负责,如有异议或侵权请及时联系,本司将立即删除!== 本文为word格式,下载后可方便编辑和修改! ==筒体划线步骤篇一:封头与筒体组装工序过程卡(划线)封头与筒体组装工序过程卡篇二:筒体制造工艺设计流程通用模板筒体整体结构分析筒体加工简明流程图【材检——喷砂——探伤】——号料——下料——【刨坡口——探伤】——筒体成形——【装焊纵缝】——校圆——喷砂——打磨——【探伤——加工环缝——组焊环缝——打磨——探伤】——【堆焊过渡层——探伤——堆焊表层——探伤】——组装受压元件成型前的工艺流程板材成型前的通用工艺流程列于表3-1。
续表3-1夹套材料夹套材料为16MnR16MnR是屈服强度350MPa的普通低合金高强度钢,具有良好的综合力学性能、焊接性能、工艺性能以及低温冲击韧性筒体材料筒体内层材料为304不锈钢,外层材料为16MnR。
304不锈钢化学牌号为06Cr19Ni10 旧牌号(0Cr18Ni9)含铬19%,含镍8-10%。
304不锈钢是应用最为广泛的一种铬-镍不锈钢,具有良好的耐蚀性、耐热性、低温强度和机械特性。
在大气中耐腐蚀,如果是工业性气氛或重污染地区,则需要及时清洁以避免腐蚀。
适合用于食品的加工、储存和运输。
具有良好的加工性能和可焊性。
板式换热器、波纹管、家庭用品、建材、化学、食品工业等。
304不锈钢为国家认可的食品级不锈钢。
16MnR是屈服强度350MPa的普通低合金高强度钢,具有良好的综合力学性能、焊接性能、工艺性能以及低温冲击韧性。
工艺设计选材聚酯反应器筒体材料选择复合钢板。
基层16MnR,复层304不锈钢。
16MnR是普通低合金钢,它的强度较高、塑性韧性良好。
常见交货状态为热轧或正火。
属低合金高强度钢304不锈钢是一种通用性的不锈钢材料,防锈性能比200系列的不锈钢材料要强。
耐高温方面也比较好,一般使用温度极限小于650℃。
304不锈钢具有优良的不锈耐腐蚀性能和较好的抗晶间腐蚀性能。
风电塔筒通常制造工艺标准
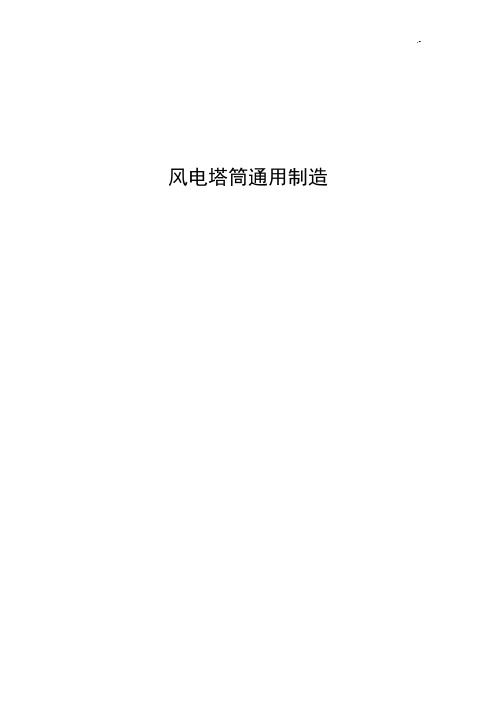
风电塔筒通用制造目录1.塔筒制造工艺流程图2.制造工艺3.塔架防腐4.吊装5.运输注:本工艺与具体项目的技术协议同时生效,与技术协议不一致时按技术协议执行一.塔架制造工艺流程图(一)基础段工艺流程图1.基础筒节:H原材料入厂检验→R材料复验→R数控切割下料(包括开孔)→尺寸检验→R加工坡口→卷圆→R校圆→100%UT检测。
2.基础下法兰:H原材料入厂检验→R材料复验→R数控切割下料→R法兰拼缝焊接→H拼缝100%UT检测→将拼缝打磨至与母材齐平→热校平(校平后不平度≤2mm)→H拼缝再次100%UT检测→加工钻孔→与筒节焊接→H角焊缝100%UT检测→校平(校平后不平度≤3mm)→角焊缝100%磁粉检测。
3.基础上法兰:外协成品法兰→H入厂检验及试件复验→与筒节组焊→100%UT 检测→H平面检测。
4.基础段组装:基础上法兰与筒节部件组焊→100UT%检测→H平面度检测→划好分度线组焊挂点→整体检验→喷砂→防腐处理→包装发运。
(二)塔架制造工艺流程图1.筒节:H原材料入厂检验→R材料复验→钢板预处理→R数控切割下料→尺寸检验→R加工坡口→卷圆→R组焊纵缝→R校圆→100%UT检测。
2.顶法兰:成品法兰→H入厂检验及试件复验→与筒节组焊→100%UT检测→平面度检测→二次加工法兰上表面(平面度超标者)。
3.其余法兰:成品法兰→H入厂检验及试件复验→与筒节组焊→100%UT检测→平面度检测。
4.塔架组装:各筒节及法兰短节组对→R检验→R焊接→100%UT检测→R检验→H划出内件位置线→H检验→组焊内件→H防腐处理→内件装配→包装发运。
二、塔架制造工艺(一)工艺要求:1.焊接要求(1)筒体纵缝、平板拼接及焊接试板,均应设置引、收弧板。
焊件装配尽量避免强行组装及防止焊缝裂纹和减少内应力,焊件的装配质量经检验合格后方许进行焊接。
(2)塔架筒节纵缝及对接环缝应采用埋弧自动焊,应采取双面焊接,内壁坡口焊接完毕后,外壁清根露出焊缝坡口金属,清除杂质后再焊接,按相同要求制作筒体纵缝焊接试板,产品焊接试板的厚度范围应是所代表的工艺评定覆盖的产品厚度范围,在距筒体、法兰及门框焊约50mm处打上焊工钢印,要求涂上防腐层也能清晰看到;(3)筒节纵环焊缝不允许有裂纹、夹渣、气孔、未焊透、未融合及深度>0.5mm 的咬边等缺陷,焊接接头的焊缝余高h应小于焊缝宽度10%;(4)筒节用料不允许拼接,相邻筒节纵焊缝应尽量错开180度,筒节纵焊缝置于法兰两相邻两螺栓孔之间。
大型筒体制作流程

大型筒体制作流程Creating a large cylindrical body involves a series of complex processes that require precision and attention to detail. From initial design to final assembly, each step plays a crucial role in ensuring the quality and integrity of the finished product. The process begins with the selection of materials, taking into account factors such as strength, durability, and resistance to corrosion.大型圆筒的制作涉及一系列复杂的流程,需要精密和对细节的关注。
从最初的设计到最终的装配,每个步骤在确保最终产品的质量和完整性方面都起着至关重要的作用。
该流程始于材料的选择,考虑到强度、耐用性和耐腐蚀性等因素。
Once the materials have been sourced, they are then shaped and manipulated into the desired form. This often involves techniques such as welding, bending, and cutting, which require skilled craftsmanship and specialized equipment. The goal is to create a seamless structure that is both functional and aesthetically pleasing. 一旦材料选择完毕,就会被塑造和加工成所需的形式。
DN4000×200厚壁筒体制造成型工艺

DN4000×200厚壁筒体制造成型工艺2017年,我单位承接了中国石油集团工程设计有限责任公司西南分公司大型化塔器试制筒体的制造任务。
试制筒体的材质为Q345R(R-HIC)正火板,壁厚为200mm,筒体内径φ4000mm,筒体的总长度3400mm(单节筒体长度1700mm,2节)。
筒体制造不仅技术要求高,而且制造难度大,尤其是筒体的卷制成型。
因此,需试制开发大型化塔器筒体的制造成型工艺,以填补公司目前大型厚壁筒体成型无成熟卷制工艺的空白。
二、试制筒体主要技术要求符合GB/T150.1~150.4-2011《压力容器》标准要求,圆度e≤25mm(e≤1%Di且不大于25mm);E≤5.0m(棱角E≤(δs/10+2)mm,且不大于5mm);直径允差±5mm。
三、DN6200×200试制筒体制造成型工艺:经公司领导和技术部门研究确定,筒体制造成型采用中温卷制成型方案,即:将钢板加热至600~620℃。
在此温度下进行卷制,既可使钢板获得比冷态稍大的塑性,减少卷板机超载的可能,又可减少冷卷脆断的危险。
氧化皮也不形成危害,操作也较方便。
克服了冷、热卷的缺陷,兼取冷、热卷的优点。
具体方法如下:(1)根据筒体图样划展开下料线:1)下料长度L按如下公式确定:L=π×Dm-△L式中:Dm表示筒体中径,△L表示卷制伸长量,按如下公式确定:△L=(0.04~0.055)π×Dm×S/Di,其中:S表示板厚,Di筒体内径;2)下料宽度为板材宽度;3)留预弯头子余量每头约800mm;4)留坡口加工余量;5)按规定作材质标记及移植。
在划下料线的同时划好基准线,并作出标记或采用其他便于对正对位、方便检查的方法。
(2)棱边倒角:采用半自动方法切割钢板,两长边棱角进行15×45°倒角,再手工砂磨至呈现金属光泽。
(3)中温热处理:按热处理工艺规定进行600℃~620℃中温卷制前的热处理,保温5小时立即出炉实施卷制。
筒体制造工艺设计流程通用模板

筒体整体结构分析筒体加工简明流程图【材检——喷砂——探伤】——号料——下料——【刨坡口——探伤】——筒体成形——【装焊纵缝】——校圆——喷砂——打磨——【探伤——加工环缝——组焊环缝——打磨——探伤】——【堆焊过渡层——探伤——堆焊表层——探伤】——组装受压元件成型前的工艺流程板材成型前的通用工艺流程列于表3-1。
表3-1,板材成型前的通用工艺流程序号工作内容要求、加工方法、加工设备或工具1 原材料入库2 原材料复验外观检验、几何尺寸检验、理化检验和钢板的超声波探伤,有时可委托钢厂进行,其中超声波探伤结果按ZBJ74003-88《压力容器用钢板超声波探伤》规定的质量分级,应不低于Ⅲ级。
3 划线及标记钢印标记、板材矫平、划线、钢印移植4 下料对于直边用剪切;曲线边用气割;对于不锈钢和有色金属,气割用等离子弧;对于特厚板材,若剪切困难则用气割。
续表3-15边缘加工用气割或等离子弧开V型、X型坡口,并用砂轮打磨;用机加工方法进行边缘加工或开坡口,其中牛头刨和龙门刨进行直线加工, 用立车或大型普通车床进行圆弧轮廓加工;用刨边机刨边和开坡口;夹套材料夹套材料为16MnR16MnR是屈服强度350MPa的普通低合金高强度钢,具有良好的综合力学性能、焊接性能、工艺性能以及低温冲击韧性筒体材料筒体内层材料为304不锈钢,外层材料为16MnR。
304不锈钢化学牌号为06Cr19Ni10 旧牌号(0Cr18Ni9)含铬19%,含镍8-10%。
304不锈钢是应用最为广泛的一种铬-镍不锈钢,具有良好的耐蚀性、耐热性、低温强度和机械特性。
在大气中耐腐蚀,如果是工业性气氛或重污染地区,则需要及时清洁以避免腐蚀。
适合用于食品的加工、储存和运输。
具有良好的加工性能和可焊性。
板式换热器、波纹管、家庭用品、建材、化学、食品工业等。
304不锈钢为国家认可的食品级不锈钢。
16MnR是屈服强度350MPa的普通低合金高强度钢,具有良好的综合力学性能、焊接性能、工艺性能以及低温冲击韧性。
2-6.3筒体工艺过程卡

产品编号
产品名称
冷凝液储罐
零件名称
筒体
工艺文件编号
FRF001
产品图号
YⅡ219-1
零件号
2
序号
工序名称
工艺内容及技术要求
操作者
日期
控制形式
检查
结果
检查员
日期
厂内
监检
用户
1
材料发放
材料应符合“压力容器材料领用单”、图样和有关标准要求,且经进货检验合格,材料标记齐全。
E
B
2
筒体划线
筒体展开周长尺寸按封头实测周长尺寸确定,宽度尺寸按产品图样要求确定。并按Q/DPS2.04-2004《材料标记移植规定》进行材料标记移。按产品图样要求校圆,棱角度E≤2.8mm,筒体圆度e≤9mm。
E
*按B类监检项目监检时,产品焊接试板与筒体纵缝连接处必须进行射线检测,并保留射线底片。
工艺员:年月日责任工程师:年月日
E
3
筒体切割
按划线位置切割,并打磨出筒体纵、环焊缝坡口,坡口尺寸应符合焊接工艺规程要求
E
4
预弯、滚圆
按产品图样要求预弯、滚圆,滚圆后筒节两端应对齐。
E
5
试板划线
划产品试板线,长度400mm,宽度150mm,数量为2块。并按Q/DPS2.04-2004《材料标记移植规定》进行材料标记移。
E
6
试板切割
按划线位置切割,并打磨出试板焊缝坡口,坡口尺寸应符合《焊接工艺规程》要求。
E
7
组对点固
筒体纵向焊缝、试板焊缝组对、点固,坡口间隙应符合焊接工艺规程要求,对口错边量b≤2mm。试板焊缝应在筒体纵向焊缝一端延长线上。
011.00筒体工艺流程10-28

011.00筒体加工工艺流程
1、白铁:件②用δ1
2、06Cr19Ni10板按2150(展开长度1733.28+直边400)×1537.5(实际尺寸1370+废料尺寸150+加工余量20-焊口2.5)下料,件④用δ16、Q235B板按2820(展开长度2411+直边400)×1269.5(实际尺寸1252+加工余量20-焊口2.5)下料,件⑥用δ16、Q235B板割外形按(展开长度+直边400),100尺寸加宽至250。
2、外协:卷筒,注意件②内外均留3mm余量。
④⑥内外均留4mm余量。
沿中缝焊接组合,牢固规整。
注意控制尺寸。
3、质检:焊缝无损检测PT。
4、车:件②平头,与件①配车外圆,Φ540+12尺寸按照0~-0.1加工。
件④内孔与件①配车,Φ752尺寸按照0~+0.1加工。
加工长度尺寸1252。
件③两头平端面,加工内锥孔,不留加工量,Φ768尺寸与件④配车一致,倒焊口。
件②外表面、件④内表面喷砂处理,要求处理完毕后清楚表面沙垢。
5、焊:等待厂方技术人员到后,现场组焊件①②④⑥焊接,共同检测。
(厂方技术人员全程监控,否则不允许加工)
6、质检:焊缝无损检测PT、RP。
(厂方技术人员全程监控,否则不允许加工)
7、浇铸:按照浇铸工艺文件浇铸。
(厂方技术人员全程监控,否则不允许加工)。
8、质检:密实性检测。
(厂方技术人员全程监控,否则不允许加工)
9、车:按图加工件①②④⑥各尺寸,件②Φ540尺寸与018配车。
10、焊:与件⑤焊接,牢固规整,整形修磨焊缝。
筒节制造工艺流程

XX大桥主桁下弦杆目录引言 41 钢板检验 51.1 钢板检验 51.1.1 钢号核对 51.1.2 化学成分检验 51.1.3 力学性能检验 51.1.4 缺陷检验 51.2 钢板预处理 61.3 板材的矫正 71.4 钢板的划线、号料 91.4.1 划线 101.4.2 号料 102 划线下料 102.1下料 102.1.1 切割 102.2.2 边缘加工 113 组对 124 焊接工艺过程124.1坡口准备 124.1.1 坡口清洁度 124.2焊前准备 124.3焊接过程 134.3.1 焊缝的焊接 155 焊后矫正 156 焊接检验 16 7工装夹具设计 177.1 工装卡具概述 177.2 工装夹具的组成 187.3 工装夹具的特点 187.4 工装夹具的设计要点 197.5 工装夹具的设计原则 197.6 手动拉紧式夹紧器 207.6.1 手动拉紧式夹紧器概述 207.6.2 手动拉紧式夹紧器的特点 20参考文献 21引言世界现代焊接技术以高效、节能、优质及其工艺过程自动化、数字化、智能化控制为显著特征。
在国内,无论是从目前焊接设备和材料构成比的发展趋势,还是从焊接设备和材料的制造技术和发展方向上来看,我国现代化焊接技术已经有了很大的发展,部分产品技术已经达到或接近国外先进水平。
随着我国焊接技术的迅猛发展,焊接设备的应用也日益广泛。
建筑钢结构用钢材及焊接填充材料的选用应符合设计图的要求,并应具有钢厂和焊接材料厂出具的质量证明书或检验报告;其化学成分、力学性能和其它质量要求必须符合国家现行标准规定。
当采用其它钢材和焊接材料替代设计选用的材料时,必须经原设计单位同意。
钢材的成分、性能复验应符合国家现行有关工程质量验收标准的规定;大型、重型及特殊钢结构的主要焊缝采用的焊接填充材料应按生产批号进行复验。
复验应由国家技术质量监督部门认可的质量监督检测机构进行。
钢结构工程中选用的新材料必须经过新产品鉴定。
加氢反应器筒体制造工艺设计课程设计说明书

SHAANXI UNIVERSITY OF SCIENCE & TECHNOLOGY过程装备制造与检测课程设计说明书题目:加氢反应器筒体制造工艺设计学生姓名:学号:院(系):专业: 指导教师:目录1. 设计题目 (1)2. 设计背景 (1)3. 设备介绍及其发展 (1)4. 设计相关内容 (1)4.1引用的主要标准及规范 (1)4.2主要技术参数 (2)4.3产品特点及问题分析 (2)5. 加氢反应器筒体制造 (3)5.1 筒体制造过程简明流程图 (3)5.2筒体制造工艺过程卡片 (4)5.3工艺设计 (5)5.3.1 选材 (5)5.3.2 材检 (5)5.3.3 划线 (7)5.4下料 (8)5.5筒节的成形 (8)5.5.1 筒节弯卷成形分析 (8)5.5.2 成形设备分析 (10)5.5.3 弯卷成形的设计及相关计算 (9)5.6 装焊纵缝 (11)5.7 筒体内壁堆焊 (11)5.6.1 堆焊原理 (11)5.6.2 工艺参数选择 (12)5.6.3 优缺点及应用范围 (13)5.6.4 堆焊工艺设计 (14)6. 心得体会 (15)参考文献16一设计题目氢反应器筒体制造工艺设计二设计背景工程科学是关于工程实践的科学基础,现代过程装备与控制工程是工程科学的一个分支,因此,生产实习是工科学习的重要环节。
在兰州兰石集团实习期间,对化工设备的发展前景和各种化工容器如反应釜、换热器、储罐、分液器和塔器等的有所了解和学习。
生产实习的主要任务是学习化工设备的制造工艺和生产流程,将理论知识与生产实践相结合,理论应用于实际。
因此,过程装备与检测的课程设计的设置是十分必要的。
由于我们实习的加工车间正在进行加氢反应器的生产,而加氢反应器是石油化工行业的关键设备,其生产工艺和设计制造在化工设备中具有显著的代表性,为此,选择加氢反应器这一典型的化工设备作为课程设计的设计题目。
三设备介绍及其发展石油工业中常用的加氢反应器有两类:一类用于高沸点液体或固体(固体需先溶于溶剂或加热熔融)原料的液相加氢过程,如油脂加氢、重质油品的加氢裂解等。
压力容器制造工艺流程

材质
06Cr19Ni10
规 格
δ=5
本厂材编
B2014-07
零件加工数量
共1件第1件
序号
控制点
工艺过程工艺要求
检验项目及数据
自检(操作者)
专检(检查员)
工序名称
工艺要求
项目
数据
结论
签名
结论
签名
日期
1
R
备料
领出人孔法兰及制备好的人孔筒节
确认材质规格及检号
/
2
E
组对
四点定位点固,接管与法兰密封面的垂直度偏差不超过1%Di。
棱角度
≤2.5mm
7
R
无损检测
对焊缝进行100% RT检测,按JB/T4730.2-2005标准Ⅲ级合格。
见无损检测报告单
/
8
E
准备
转入人孔法兰与人孔筒节组对工序
检验结论:检查员:年 月 日
产品名称
制 造 工 艺 流 程卡
人孔法兰
产品编号
产品图号
零件名称
人孔法兰
筒体图号
4
部件编号
RK2014-01
件 号
打磨质量
表面无缺陷
5
准 备
转入总装工序
检验结论:检查员:年 月 日
产品名称
制 造 工 艺 流 程卡
说明
产品编号
产品图号
零件名称
支座底板
部件图号
2
支座底板编号
2
件 号
\
材质
Q235B
规 格
10mm
本厂材编
B2014-08
零件加工数量
共3件
序号
控制点
筒体制造工序过程卡

4
组对焊接 焊,打磨清理焊缝表面,作出焊缝标记和焊
工标记
卷圆后点焊固定, 对口错边量 b≤ ㎜,将
5
卷 板 产品试板焊于纵缝延长线上
按焊接工艺施焊,清理焊缝表面,作出焊缝
6
焊 接 标记与焊工标记
使最大最小直径差 e <
7
校
圆 E≤角线
坡口尺寸
对角线 焊缝标记 焊工标记 焊缝外观
规格
检
验
结论
焊接环缝,打磨飞溅,清理焊缝表面,作焊缝
9
焊 接 标记,焊工标记
焊缝外观 焊缝标记
10
划
线
画出开孔中心线, 以开孔中心线为圆中心, 倍开孔为半径画出扩探焊缝位置
1.5
开口方位及位 置,扩探位置
11
探伤
%X 射线探伤,
级合格
RT
续表一 签字
精品文档 可编辑
精品文档 可编辑
筒体制造工序过程卡
产品名称: 工令号
材料牌号
标准
件号
序号 工序名称
工序内容及工序要求
操作责任人
1
备 料 确认材质标记,进行标记移植
2
划
线
按封头外圆周长确定筒体展开长度,划产品 试板 500×150 ㎜两块
3
加工坡口 按坡口尺寸加工焊接坡口
组对拼板,组对错边量 < 1 ㎜,按焊接工艺施
错边量
焊缝外观 焊缝标记 焊工标记 椭圆度 棱角度
规格
检
验
结论
精品文档 可编辑
签字
精品文档 可编辑
筒体制造工序过程卡
产品名称: 工令号
序号 工序名称
材料牌号
标准
- 1、下载文档前请自行甄别文档内容的完整性,平台不提供额外的编辑、内容补充、找答案等附加服务。
- 2、"仅部分预览"的文档,不可在线预览部分如存在完整性等问题,可反馈申请退款(可完整预览的文档不适用该条件!)。
- 3、如文档侵犯您的权益,请联系客服反馈,我们会尽快为您处理(人工客服工作时间:9:00-18:30)。
筒体整体结构分析筒体加工简明流程图【材检——喷砂——探伤】——号料——下料——【刨坡口——探伤】——筒体成形——【装焊纵缝】——校圆——喷砂——打磨——【探伤——加工环缝——组焊环缝——打磨——探伤】——【堆焊过渡层——探伤——堆焊表层——探伤】——组装受压元件成型前的工艺流程板材成型前的通用工艺流程列于表3-1。
续表3-1夹套材料夹套材料为16MnR16MnR是屈服强度350MPa的普通低合金高强度钢,具有良好的综合力学性能、焊接性能、工艺性能以及低温冲击韧性筒体材料筒体内层材料为304不锈钢,外层材料为16MnR。
304不锈钢化学牌号为06Cr19Ni10 旧牌号(0Cr18Ni9)含铬19%,含镍8-10%。
304不锈钢是应用最为广泛的一种铬-镍不锈钢,具有良好的耐蚀性、耐热性、低温强度和机械特性。
在大气中耐腐蚀,如果是工业性气氛或重污染地区,则需要及时清洁以避免腐蚀。
适合用于食品的加工、储存和运输。
具有良好的加工性能和可焊性。
板式换热器、波纹管、家庭用品、建材、化学、食品工业等。
304不锈钢为国家认可的食品级不锈钢。
16MnR是屈服强度350MPa的普通低合金高强度钢,具有良好的综合力学性能、焊接性能、工艺性能以及低温冲击韧性。
工艺设计选材聚酯反应器筒体材料选择复合钢板。
基层16MnR,复层304不锈钢。
16MnR 是普通低合金钢,它的强度较高、塑性韧性良好。
常见交货状态为热轧或正火。
属低合金高强度钢304不锈钢是一种通用性的不锈钢材料,防锈性能比200系列的不锈钢材料要强。
耐高温方面也比较好,一般使用温度极限小于650℃。
304不锈钢具有优良的不锈耐腐蚀性能和较好的抗晶间腐蚀性能。
夹套选择16MnR低合金钢。
材检一般来说,为了保证工程质量,所有原材料、构配件等,均要进行进场复检,并做好记录。
有些原材料需要抽样送检,并取得合格报告后方可使用。
具体实施按照工程验收规范、国家标准执行。
划线(1)、展开计算见图3-1(a)展开前的形状及尺寸(b)展开后的形状及尺寸图3-1 筒节展开已知:H=2100mm、Dg=2200mm、δ=22+6mm则有:Dm=Dg+δ=2200+22+6=2228mmL=π×Dm=3.14×2228=6995.92mmh=H=2100mm(2)、留余量(a)、筒体卷制的伸长量:与被卷材质、板厚、卷制直径的大小、卷制次数等条件有关,而本次采用冷卷,钢板冷卷的伸长量较小,约为7~8mm。
(b)、主要考虑内容为机加工余量和热切割加工余量见图3-2:图3-2 筒节的划线及公差要求(3)、焊缝变形量对于尺寸要求严格的焊接结构件,划线时要考虑焊缝变形量(焊缝收缩量),可以查相关的标准。
对于简单结构在自由状态下进行电弧焊接时,也可以对焊缝收缩量等变形进行大致的估算。
实际用料线尺寸=展开尺寸-卷制伸长量+焊缝收缩量-焊缝剖开间隙+边缘加工余量切割下料线尺寸=实际用料线尺寸+切割余量+划线公差(4)、划线公差长度L和宽度h如图二所示,对角线之差不大于1mm,两平行线的不平行度不大于1mm,若考虑相对长度、宽度的关系则更为完善。
一般情况下划线公差也可以考虑为制造公差的一般。
筒体的排料(1)、每节筒节,其纵向焊缝数量,公称直径Dg不大于1800mm时,拼接焊缝不多于2条;公称直径Dg大于1800mm时,拼接焊缝不多于3条;(2)、每一节筒体的纵向焊缝中心线间的弧长不应小于300mm.(3)、相邻筒体的纵向焊缝与筒体纵向焊缝应互相错开,并且两焊缝中心间的弧长不得小于100mm,见图3-3:图3-3 排料要求图(4)、最短筒节长度不应小于300mm;坡口加工坡口加工按机加工制备,按焊接工艺刨纵、环缝坡口,在12m的刨边机上加工,刨边机在下尽料的钢板两端按焊卡刨坡口,另两块钢板一端按焊卡刨坡口,另一端待筒体滚圆后制作。
根据实际生产情况,直缝和环缝坡口型式分别如图1所示。
焊接前要检查坡口型式及装配质量,坡口处要进行清除铁锈、油污、氧化皮等影响焊接质量的杂质,并对坡口进行PT表面探伤检测,确认无缺陷后方可进行焊接。
开设焊接坡口的目的主要是为了保证电弧能深入接头根部,使接头根部焊透,其次是便于清理熔渣,获得较好的焊缝成形,再次是调节焊缝中金属和母材的比例。
开设坡口主要是为了焊透,能否焊透主要由坡口的尺寸和形式决定的,焊接坡口应根据板厚、焊接方法以及图样要求或工艺条件选用标准坡口或自行设计坡口。
选择和设计坡口形式和尺寸应综合考虑以下因素:(1)保证焊缝焊透;(2)坡口形状易于加工;(3)便于装配;(4)尽量减少焊缝金属填充量,提高生产效率;(5)保证焊接接头质量,避免产生焊接缺陷;(6)减少焊接残余应力与变形;(7)有利于焊接防护,改善劳动条件;(8)方便焊工操作;(9)复合钢板坡口应有利于减少过渡层焊缝金属的稀释率。
因此,焊接坡口形式与尺寸设计见图3-4:图3-4 复合板筒节环缝示意该坡口形式具有以下优点:(1)过渡层位置明确基层与复层界面一目了然, 过渡层的位置有明确标记, 不会将碳钢焊条焊到复层上, 焊工无心理负担, 施焊时得心应手。
(2)避免夹渣的产生复层边缘远离焊缝中心, 因此在焊接热循环过程中, 最高峰值温度大大降低, 避免了因基层焊接时反复受热膨胀, 引起复层张口, 并出现夹渣的可能。
(3)保证了过渡层厚度的要求过渡层能完全覆盖基层, 并且能达到技术条件中要求的a、b 值, 保证过渡层的焊接质量,使其真正起到承上启下的作用。
多年的实践证明,坡口能更好的保证不锈钢复合板的焊接质量, 同时对其它类型的复合材料焊接坡口的设计有一定的参考价值。
、焊接工艺焊前准备为了保证焊接接头的耐蚀性,防止焊接缺陷,在焊前准备中,对下列问题应予以特别注意。
⑴下料方法根据材料厚度查得,坡口加工方法可选用切削或磨削。
此盘管坡口加工适宜选择磨削加工方法。
其优点是现在的磨削工具小型轻便,使用起来比较方便,总成本低,而且用途广,对于厚度小于8mm的部件,多采用磨削方法加工坡口,这种方法更适用于现场修磨坡口。
⑵焊前清理为了保证焊接质量,焊前应将坡口及两侧20~30mm范围内的焊件表面清理干净,如有油污,可用丙酮或酒精等有机溶剂擦拭。
对表面质量要求特别高的焊件,应在适当范围内涂上用白垩粉调制的糊浆,以防止飞溅金属损伤钢材表面。
⑶ 表面防护 在搬运,坡口制备、装配及点焊过程中,应注意避免损伤不锈钢表面,以免使产品的耐蚀性能降低,如不允许在钢材表面随意打弧及用利器划伤钢板表面等。
⑷ 自冷作硬化现象 因奥氏体不锈钢的线胀系数大,对冷作硬化敏感,在刚性固定条件下焊接时,焊缝在冷却中会产生较大的塑性变形,而发生自发的冷作硬化现象,经“自冷作硬化”的焊缝,屈服点提高40%左右,塑性有所降低。
⑸ 焊丝应有制造厂的质量合格证,领取和发放有焊材管理员统一管理。
焊丝在使用前应清除油锈及其他污物,露出金属光泽。
⑹ 氩气氩气瓶上应贴有出厂合格标签,其纯度≥99.95%,所用流量6-9升/分钟,气瓶中的氩气不能用尽,瓶内余压不得低于0.5MPa ,以保证充氩纯度。
⑺ 焊接工具a 采用直流电焊机,用WSE-315和TIG400两种型号焊机。
b 选用的氩气减压流量计应开闭自如,没有漏气现象。
切记不可先开流量计、后开气瓶,造成高压气流直冲低压,损坏流量计;关时先关流量计而后关氩气瓶。
c 输送氩气的胶皮管,不得与输送其它气体的胶皮管互相串用,可用新的氧气胶皮管代用,长度不超过30米。
⑻其它工器具焊工应备有:手锤、砂纸、扁铲、钢丝刷、电磨工具等,以备清渣和消缺。
筒节与筒节环缝焊接方法及焊接工艺 复合板筒节与筒节环焊接如图4-222+670°70°3230°5图4-1 堆焊工艺 图4-2 筒节环缝焊接4.2.2筒节与筒节环焊缝焊接工艺续表4-14.2.3 材料时应注意遵循以下原则:a. 复层用焊材应考虑有10% 的合金元素烧损, 选择合金成分高的焊材。
过渡层用焊材应考虑碳钢对不锈钢的稀释作用, 合金成分应比母材高25% 左右。
b. 焊材的含碳量应尽可能的低, 有条件时可选择超低碳钢焊条。
c. 当压力容器产品设计计算了复合钢板复层的强度, 选择焊条也要考虑焊材强度对焊接接头的影响。
d. 基层焊接材料, 按强度匹配即可。
在焊接工艺评定的基础上, 操作时应选用小直径焊条, 采用小热输入、反极性、快速多道焊接, 焊条不允许做横向摆动, 这样可以避免基层金属对过渡层的稀释, 减少马氏体组织的形成, 防止产生裂纹。
需要说明, 焊接复层时严禁采用埋弧自动焊, 因为它具有很大的熔深, 会使过多的基层材料熔入焊缝, 焊后易产生大量的焊后冷裂纹, 而且会对焊接接头的抗腐蚀性产生影响。
e. 焊接材料的选择按JB/ T4709 2000《钢制压力容器焊接规程》的规定, 分别选择基层和复层的焊接材料。
过渡层的焊接材料按异种钢的焊接进行选择. 4.2.4 检验(1)基层:100%UT,按JB/T4730-2005 I级;超声波针对缺陷性质如裂纹、气孔、夹渣的分析、判别进行定性评估,并可对缺陷定位、定量评价,因此用于基层检测。
(2)基层内表面磨平后,按JB/T4730-2005 I级;(3)过渡层及盖面层逐层:100%PT,按JB/T4730-2005 I级;渗透检测适用材料广泛,是检测各种工件裸露出表面开口缺陷的有效无损检测方法,灵敏度高,设备简单,操作方便,因此用于过渡层焊好后及盖面层的逐层表面检测。
夹套与筒体焊接方法及焊接工艺(1) 夹套与筒体选择封闭件进行连接封闭件材料封闭件的材料选用与夹套相同的材料,即16MnR,低合金钢。
封闭件几何尺寸确定封闭件厚度计算:封闭件厚度等于夹套厚度16mm,带圆弧过渡锥形封闭件的锥角一般取45o,过渡部分圆弧半径一般为R20~R40mm。
封闭件大小端直径的确定:确定封闭件小端内直径时,应考虑筒体卷制时出现的不圆度以及封闭件、容器留有的装配间隙,其值比容器外直径大2mm~3mm。
封闭件大端内径与夹套筒体内径相同。
焊接的接口图4-3:图4-3 密封件末端与通体焊接(2焊接方法及规范参数双面埋弧自动焊,一侧焊后另一侧碳弧气刨后再施焊;正、反各焊一层;直流反接,H10Mn2ф5,HJ431,焊接电流(750~800)A,电弧电压(34~38)V,焊接速度~40cm/min。
图4-4 密封件末端与夹套焊接接管与筒体焊接方法及焊接工艺(1)焊接示意图4-5图4-5 筒体与接管焊接(2)接管与复合板筒体的焊接在筒节组对过程中采用定心器和光学准直望远镜配合,控制筒节间同轴度,最后完成上、下两大部分环焊缝焊接、容器内件组装焊接和容器整体热处理。
焊后清理低合金钢焊后,焊缝必须进行酸洗、钝化处理。