酸洗槽TC801分析方法
钢管酸洗工艺流程

钢管酸洗工艺流程钢管酸洗工艺流程是一种常见的表面处理技术,可以去除钢管表面的氧化皮、锈蚀、油污等物质,提高钢管的表面质量和使用寿命。
以下是钢管酸洗工艺流程的简单介绍:首先,将待处理的钢管放入酸洗槽中,确保槽内的酸液能够完全覆盖钢管表面。
然后,将酸洗槽中的酸液预热至一定温度,一般在50-70℃之间。
高温可以加快酸洗反应速度,但需要注意不要超过钢管的耐热温度。
在钢管浸泡于酸液中一段时间后,酸液会与钢管表面的氧化皮、锈蚀、油污等物质发生化学反应。
这些物质会被酸液溶解,从而将钢管表面的污染物质去除。
在酸洗过程中,可以通过搅拌酸液或者采用气泡搅拌的方式来增加反应的速度和均匀性。
此外,还可以向酸洗槽中加入一些表面活性剂,以提高酸洗液的湿润性,使酸液能够更好地接触并清洁钢管表面。
经过一段时间的酸洗后,酸洗槽中的酸液会逐渐被污染物质所消耗,酸液的酸度也会下降。
这时,需要定期检测酸液的酸度,并根据需要进行添加或更换酸液,以维持酸洗效果的稳定性。
当钢管酸洗结束后,需要将钢管从酸洗槽中取出并进行清洗。
清洗时可以使用清水或者碱水进行冲洗,以将酸液残留物和其他残留物彻底洗净。
在清洗过程中,还可以通过喷淋方式来冲洗钢管内部和外部,以确保清洗效果的完整性。
最后,将清洗干净的钢管进行干燥处理,常见的干燥方法包括自然干燥、热风干燥和烘箱干燥等。
干燥后的钢管即可投入使用或进行进一步的加工处理。
总结来说,钢管酸洗工艺流程主要包括准备工作、酸液处理、酸洗反应、酸液调整、清洗和干燥等环节。
通过合理运用各个环节的处理方法,可以使钢管表面的氧化皮、锈蚀、油污等物质得到有效清除,从而提高钢管的表面质量和使用寿命。
硫酸或盐酸酸洗槽的分析

硫酸总量的测定
取5毫升试样于250毫升锥形瓶中,加入70毫升蒸馏水及数滴P.P(酚酞)指示剂,以1.0mol/l-NaOH滴定,当溶液由无色变为粉红色30秒钟内不退时为终点,并记录滴定所使用毫升数为V1。
计算:总硫酸(g/l)=N×V1×9.8
游离硫酸的测定
取5毫升试样于250毫升锥形瓶中,加入70毫升蒸馏水及数滴溴酚兰指示剂,以1.0mol/l-NaOH滴定,当溶液滴定至溶液由淡黄色变为淡蓝色为止并记录滴定所使用毫升数为V2。
计算:游离硫酸(g/l)=N×V2×9.8
盐酸的测定
取5毫升试样于250毫升锥形瓶中,加入70毫升蒸馏水及数滴溴酚兰指示剂,以1.0mol/l-NaOH滴定,当溶液滴定至溶液由淡黄色变为淡蓝色为止并记录滴定所使用毫升数为V。
计算:盐酸(g/l)=N×V×3.65
注:此方法检测的是纯盐酸的含量,如果换算成商业盐酸,则要进行换算。
如商业盐酸的浓度为50%,
则商业盐酸(g/l)=N×V×3.65÷0.5
酸洗槽也可用波美度测定浓度,见下表:
盐酸浓度与密度对照表
硫酸浓度与密度对照表。
酸洗原理及工艺

?
?
?
ARP
到此告一段落!
由于准备得较仓促,讲 得比较粗浅,敬请原谅。
谢谢大家的关注,并请批
评指正。
酸槽是钢板衬橡胶并内砌耐酸砖的结构。对于耐酸砖衬,在与
酸液直接接触的部分,是两层耐酸砖 (2×65mm) 配合灰浆(共厚 150mm) 砌成。其余部分是一层耐酸砖 (70mm) 砌成。
两层耐酸砖结构的优点在于提高了酸洗线安全运行的系数,也
就是说缩短了事故停机的时间,减少了相应的产量损失。
槽盖为分段式,每个酸槽有 4个槽盖,液压动力开闭。分段式
的要求。而超浅槽紊流酸洗的优势就是体现在这些参数
需要变更的时候。
紊流度
板带运行速度
不需任何额外的介质
由于超浅槽紊流酸洗工艺高效的控制能力, SMS
Demag 的酸洗工艺不需添加任何额外的介质,如增强 剂、抑制剂等。
有些酸洗工艺需要这些添加剂,无疑是增加了酸
洗的成本。
紊流度
板带运行速度
超浅槽酸洗其他优势
因此,板带的高速通过,再加上喷排和侧喷口
的作用,就更容易引起酸液产生较强的紊流效果。
而对喷酸压力和流量的调整,就会很容易地控制紊 流的强弱。 SMS Demag 的酸洗工艺中喷酸的压力可
达 2.5~3bar ,约是其竞争对手压力的 10倍。高的喷酸 压力保证了紊流度的最大值和较大的调整范围。
酸洗中紊流的必要性
先选取一个静态的酸
洗环境,大家就会看到如 右图的一个反应分层。
当板带运动起来时,
如果没有大的紊流效果, 由于分子间作用力的影响, 反应层和临界层只是变薄, 而不能消除。
要提高酸洗效率,就 要将这个反应的分层破坏
掉,使新酸尽可能多地接
酸洗线工艺流程

酸洗线工艺流程
《酸洗线工艺流程》
酸洗线是一种重要的表面处理工艺,用于去除金属表面的氧化皮、锈斑和其他杂质,使金属表面更加光洁、平整,增强金属的耐腐蚀性能和美观度。
下面我们来看一下酸洗线的工艺流程。
首先,需要准备一个酸洗槽,槽内填满酸性溶液,通常采用的酸洗溶液有盐酸、硫酸和硝酸等。
然后,将待处理的金属板材或管材浸入酸洗槽中,进行浸泡酸洗。
在酸洗的过程中,酸洗溶液会与金属表面的氧化皮和杂质发生化学反应,将其溶解掉。
接下来是漂洗环节,将经过酸洗的金属材料从酸洗槽中取出,进行清洗。
清洗的目的是将残留的酸性溶液洗净,以免影响金属的耐腐蚀性能。
通常采用的清洗方法包括喷淋清洗、浸泡清洗和水刷清洗等。
最后,经过酸洗和漂洗处理后的金属材料需要进行烘干和防锈处理。
通过烘干可以去除金属表面的水分,防止金属表面再次氧化。
而防锈处理则是为了进一步增强金属的耐腐蚀性能,通常采用的方法有涂漆、喷塑或热浸镀锌等。
总的来说,酸洗线工艺流程包括酸洗、漂洗、烘干和防锈处理四个环节。
通过这一系列的处理,金属材料的表面质量可以得到有效提升,使得金属产品在使用过程中更加耐磨、耐腐蚀,外观也更加美观。
酸洗工程试验方案
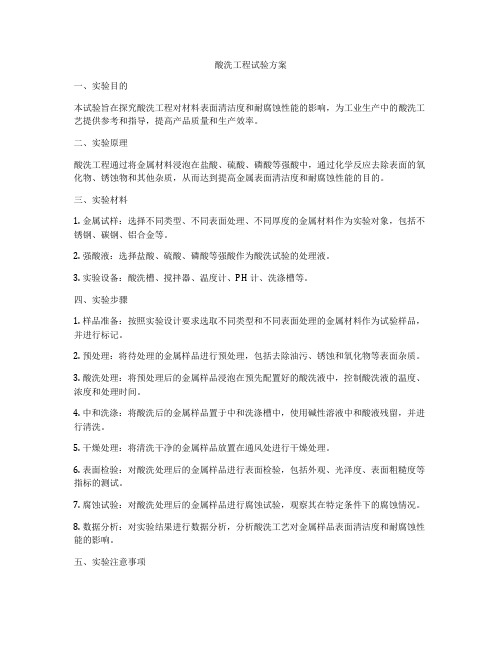
酸洗工程试验方案一、实验目的本试验旨在探究酸洗工程对材料表面清洁度和耐腐蚀性能的影响,为工业生产中的酸洗工艺提供参考和指导,提高产品质量和生产效率。
二、实验原理酸洗工程通过将金属材料浸泡在盐酸、硫酸、磷酸等强酸中,通过化学反应去除表面的氧化物、锈蚀物和其他杂质,从而达到提高金属表面清洁度和耐腐蚀性能的目的。
三、实验材料1. 金属试样:选择不同类型、不同表面处理、不同厚度的金属材料作为实验对象,包括不锈钢、碳钢、铝合金等。
2. 强酸液:选择盐酸、硫酸、磷酸等强酸作为酸洗试验的处理液。
3. 实验设备:酸洗槽、搅拌器、温度计、PH计、洗涤槽等。
四、实验步骤1. 样品准备:按照实验设计要求选取不同类型和不同表面处理的金属材料作为试验样品,并进行标记。
2. 预处理:将待处理的金属样品进行预处理,包括去除油污、锈蚀和氧化物等表面杂质。
3. 酸洗处理:将预处理后的金属样品浸泡在预先配置好的酸洗液中,控制酸洗液的温度、浓度和处理时间。
4. 中和洗涤:将酸洗后的金属样品置于中和洗涤槽中,使用碱性溶液中和酸液残留,并进行清洗。
5. 干燥处理:将清洗干净的金属样品放置在通风处进行干燥处理。
6. 表面检验:对酸洗处理后的金属样品进行表面检验,包括外观、光泽度、表面粗糙度等指标的测试。
7. 腐蚀试验:对酸洗处理后的金属样品进行腐蚀试验,观察其在特定条件下的腐蚀情况。
8. 数据分析:对实验结果进行数据分析,分析酸洗工艺对金属样品表面清洁度和耐腐蚀性能的影响。
五、实验注意事项1. 在酸洗处理过程中,必须严格遵守操作规程,做好相关安全防护工作,避免酸液溅洒和腐蚀伤害。
2. 实验过程中需要定期检测酸洗液的PH值和浓度,保持处理液的稳定性和处理效果。
3. 对实验设备和试验场地进行定期清洁和消毒,确保实验环境的清洁和安全。
4. 对实验结果进行准确记录和存档,保证实验数据的真实性和可靠性。
六、实验结果与分析通过酸洗处理后的金属样品表面检验和腐蚀试验,可以得出酸洗工程对材料表面清洁度和耐腐蚀性能的影响。
酸洗 操作规程
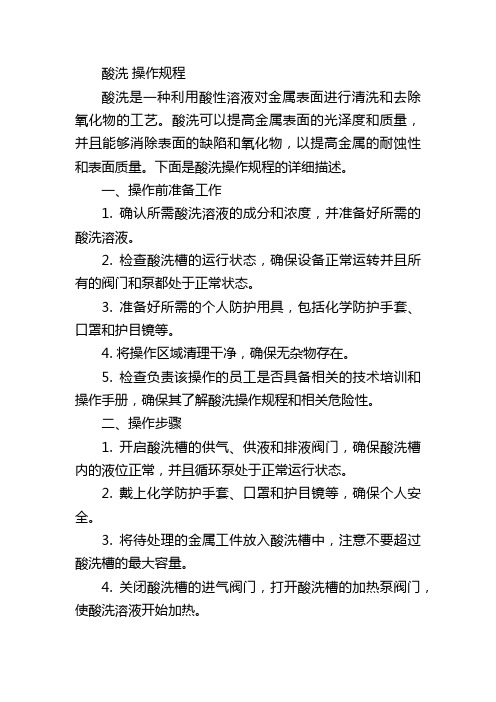
酸洗操作规程酸洗是一种利用酸性溶液对金属表面进行清洗和去除氧化物的工艺。
酸洗可以提高金属表面的光泽度和质量,并且能够消除表面的缺陷和氧化物,以提高金属的耐蚀性和表面质量。
下面是酸洗操作规程的详细描述。
一、操作前准备工作1. 确认所需酸洗溶液的成分和浓度,并准备好所需的酸洗溶液。
2. 检查酸洗槽的运行状态,确保设备正常运转并且所有的阀门和泵都处于正常状态。
3. 准备好所需的个人防护用具,包括化学防护手套、口罩和护目镜等。
4. 将操作区域清理干净,确保无杂物存在。
5. 检查负责该操作的员工是否具备相关的技术培训和操作手册,确保其了解酸洗操作规程和相关危险性。
二、操作步骤1. 开启酸洗槽的供气、供液和排液阀门,确保酸洗槽内的液位正常,并且循环泵处于正常运行状态。
2. 戴上化学防护手套、口罩和护目镜等,确保个人安全。
3. 将待处理的金属工件放入酸洗槽中,注意不要超过酸洗槽的最大容量。
4. 关闭酸洗槽的进气阀门,打开酸洗槽的加热泵阀门,使酸洗溶液开始加热。
5. 根据酸洗溶液的成分和浓度,设定合适的温度和时间,进行酸洗过程。
一般情况下,酸洗温度为50-70摄氏度,时间为5-15分钟。
6. 在酸洗过程中,定期检查槽内酸洗溶液的温度和浓度,确保其处于设定的范围内。
7. 酸洗完成后,打开酸洗槽的排液阀门,将酸洗溶液排出,并用清水进行冲洗,以确保酸洗溶液彻底清洗干净。
8. 关闭酸洗槽的排液阀门,关闭酸洗槽的加热泵阀门。
9. 将酸洗槽内的金属工件取出并放置在干燥区域进行晾干,或者进行下一步的处理。
三、操作注意事项1. 进行酸洗操作时,必须佩戴个人防护用具,确保个人安全。
2. 使用酸洗溶液时,必须掌握酸洗溶液的成分和浓度,并按照规定的操作参数进行操作。
3. 在酸洗过程中,必须定期检查酸洗溶液的温度和浓度,并保持其处于合适的范围内。
4. 酸洗槽的运行状态必须处于正常状态,如发现泵或阀门异常,应及时进行维修和更换。
5. 酸洗结束后,必须将酸洗槽内的酸洗溶液彻底清洗干净,以防止残留物对下一批金属工件造成污染。
(工艺技术)酸洗工艺

槽号
TFe2+(g/l)
∑HCl(%)
温度(℃)
1#
90~140
5~11
78~82
2#
80~120
8~14
76~80
3#
70~95
12~17
74~78
4#
40~80
14~19
72~75
5#
20~57
16~20
70~74
2.检查上班组设备运行情况记录,确认推拉式酸洗机组各组成部分工作正常,如有故障及时通知维修工进行修理。
2、新剪刃因受热变化,间隙要多调约0.05mm。
2.带钢导入时,必须使带钢在剪刃中左右放平,不能有瓢曲,特别是剪刃区带钢应通过导板压板十分紧凑地沿剪刃外边导入。
10
涂油
1.根据用户需求给带钢上表面涂上防锈油
11
卷取
1.在卷取不能跑偏、监督带钢表面质量,带钢的张力按工艺执行。
12
卸料
1.尾部带钢卷到一定位置时停机,缩紧、小车配合卸料。
数量
备注
1
推拉式酸洗机组
1450
1
1.1
钢卷小车
1
1.2
开卷机
1
1.3
侧导对中装置
1
1.4
五辊矫直机
1
1.5
切头剪
1
1.6
切角剪
1
1.7
挤干辊
1
1.8
酸槽
1
1.9
冲洗槽
1
1.10
热风干燥机
1
1.11
夹送辊
1
1.12
活套摆动导板
1
1.13
圆盘剪
酸洗工艺流程

酸洗工艺流程酸洗工艺是金属表面处理的一种方法,通过使用酸溶液,可以去除金属表面的氧化物、尘埃、油脂等杂质,使金属表面变得洁净。
以下是一种常见的酸洗工艺流程:首先,准备酸洗槽。
选择具有良好腐蚀性能的酸溶液,常用的酸洗溶液包括鹽酸、硝酸和硫酸等。
在进行酸洗之前,需要将酸洗槽清洗干净,并检查槽的密封性能。
接下来,进行预处理。
对于金属表面存在的较重的油脂、尘埃和氧化物等污染物,可以进行预处理,以提高酸洗的效果。
预处理可以采用碱洗、机械刮擦等方法,将金属表面的污染物去除干净。
然后,进行酸洗。
将待处理的金属件放入酸洗槽中,确保所有表面都能与酸溶液接触。
在酸洗过程中,酸洗槽中的酸溶液会与金属表面发生化学反应,去除表面的杂质。
酸洗时间一般为数分钟至数十分钟,具体时间取决于金属的种类和表面污染的程度。
在酸洗过程中,需要注意酸洗槽内酸溶液的浓度和温度。
酸洗槽中的酸溶液的浓度应该控制在合适的范围内,如果浓度过低,可能会导致酸洗效果不佳;如果浓度过高,可能会对金属表面造成腐蚀。
酸洗槽的温度一般会控制在40℃至60℃之间,过高的温度可能会加速金属的腐蚀速度,过低的温度可能会降低酸洗效果。
酸洗完成后,进行中和处理。
将酸洗槽中的酸溶液中和,防止酸溶液对环境产生污染。
中和可以通过加入碱性物质如氢氧化钠来进行,同时要进行充分搅拌,直到酸洗槽中的酸溶液中和至中性为止。
最后,进行清洗和干燥。
将经过酸洗和中和处理的金属件取出,用水进行清洗,确保酸溶液等化学物质被完全洗净。
清洗后,金属件需要进行干燥,可以采用自然风干或热风干燥的方式,确保金属件的表面不再有水分存在。
以上就是酸洗工艺的大致步骤。
酸洗工艺在金属表面处理中应用广泛,可以有效地去除金属表面的污染物,使金属表面变得洁净。
然而,在进行酸洗工艺时,需要注意酸洗槽内酸溶液的浓度、温度和中和处理等环节,以确保酸洗工艺的顺利进行。
酸洗工程实验方案

酸洗工程实验方案一、实验背景与意义酸洗是一种常见的金属表面处理工艺,通过酸性溶液的作用去除金属表面的氧化物、锈蚀物和杂质,以达到清洁表面和改善表面腐蚀性能的目的。
酸洗工程实验可以通过模拟工业生产过程,探究不同工艺参数对酸洗效果的影响,为工业生产提供科学依据,同时对化工原理和实验操作技能进行训练。
二、实验原理1. 酸洗工艺原理:酸洗工艺是一种物理化学结合的清洁表面方法,主要原理是通过酸性溶液对金属表面进行酸洗,去除氧化物和杂质,提高金属表面的清洁度和腐蚀性能。
2. 酸洗实验工艺参数:酸洗工艺参数包括酸洗溶液的成分、浓度、温度、酸洗时间和机械搅拌等因素,不同参数对酸洗效果有不同影响。
三、实验材料与设备1. 实验材料:待酸洗金属试样2. 实验设备:酸洗槽、酸洗溶液、酸洗槽搅拌器、温度计、电子天平等实验仪器。
四、实验步骤与方法1. 准备工作:将待酸洗金属试样放入酸洗槽中,准备酸洗溶液。
2. 调整酸洗工艺参数:根据实验要求,调整酸洗溶液的成分、浓度、温度和酸洗时间等参数,记录每组参数设置。
3. 进行酸洗实验:依次将不同参数的酸洗溶液加入酸洗槽,启动搅拌器,并控制酸洗时间。
4. 实验数据记录:记录每组酸洗参数下金属试样的酸洗时间、溶液温度、质量变化等数据。
5. 实验结果分析:根据实验数据,分析不同酸洗参数对金属试样的清洁度和腐蚀性能的影响。
五、实验注意事项1. 酸性溶液具有一定的腐蚀性和刺激性,操作时应佩戴防护眼镜、手套和口罩。
2. 实验过程中应注意酸洗槽的搅拌和温度控制,确保酸洗效果和安全操作。
3. 实验结束后,将酸洗槽和实验仪器进行清洗和消毒,将废液妥善处理,避免污染环境。
六、实验结果与讨论经过酸洗工程实验得到不同酸洗参数下金属试样的清洁度和腐蚀性能数据,可根据实验结果进行分析和讨论,探究不同工艺参数对酸洗效果的影响规律。
七、实验结论通过酸洗工程实验,得出对酸洗工艺参数进行优化的结论,为工业生产提供科学依据,并对化工原理和实验操作技能进行训练。
几种酸洗技术讲解及对比

几种酸洗技术讲解及对比酸洗工序主要是通过酸洗液与带钢表面的氧化铁皮发生化学反应和物理冲击使氧化铁皮从带钢表面脱落,从而形成较为理想的表面,酸洗后带钢质量好坏直接影响轧制带钢质量。
随着酸洗工艺技术的发展,特别是盐酸酸洗技术的发展,现在国内的酸洗机组、酸轧机组主要分为几种酸洗形式,浅槽喷射式酸洗技术JBOX酸洗技术、TUrbof1o酸洗技术。
1、几种常见酸洗技术1.1浅槽喷射式酸洗技术浅槽喷射式酸洗技术在国内应用最为广泛,技术发展比较成熟,目前代表机组商为西马克和国内一些酸洗机组商。
每个酸洗槽都有自己的酸洗循环系统,通过酸槽循环系统的泵和换热器控制酸液温度和流量,每个槽之间用酸洗泵或酸洗循环罐的连通器来实现酸液梯度递流。
酸洗槽槽盖分为内盖和外盖,内盖在酸液上方浮动以增强紊流效果,槽底部设有若干个托石,与酸槽内盖之间形成紊流的酸洗通道,酸槽头尾两端设置喷射梁,两侧设置侧喷,带钢在较大张力作用下运行,酸液与带钢流动方向相反,槽内液面的高度大概在15O mm-20OnIm,酸液流动的通道断面狭窄处时产生高速动能,在多种因素下形成紊流。
从图1中可以看出,酸洗紊流效果与,酸槽结构、酸洗喷头压力、带钢速度,酸液流动等多种因素相关。
图I浅精素流喷射酸洗1.2Turbof1。
酸洗技术TUrbof1o酸洗技术是达涅利公司的专利,目前在国内有多条酸洗线应用,在薄带钢酸洗上可以达到较高速度。
每个酸洗槽都有自己的酸洗循环系统,通过酸槽循环系统的泵和换热器控制酸液温度和流量,每个槽之间用酸洗泵或酸洗循环罐的连通器来实现酸液梯度递流。
酸洗槽内每个酸槽通过酸槽底部的设计和一个与上盖连接的特殊内盖分成几个单独的酸洗单元。
每个酸洗单元长约2m。
如图2所示,每个单元结构增加了带钢上下表面的酸液动态压力,而且这个压力仅与带钢速度有关,同时产生高的紊流效果。
图2TUrbOnO酸洗技术酸洗单元13IBOX酸洗技术[BOX酸洗技术是日本三菱公司的专利,目前在国内有多条酸轧机组应用,在国内没有单独IBoX酸洗机组,只与三菱公司轧机配合的酸轧机组。
槽液分析方法

宏兴铝业有限公司槽液分析方法文件编号:QWC-08版本号:C版版次号:0次受控状态:发布时间:2012年01月25日实施时间:2012年02月01日编写:审核:批准:1.脱脂槽1.1分析方法:吸取槽液5ml于250ml的锥形瓶中,加蒸馏水80ml、1%的酚酞 2滴,用1N的NaOH滴定,颜色由无色变为红色为终点,记下所消耗的毫升数V。
1.2计算方法:游离酸 = 9.8 x V x NV-----NaOH滴定消耗ml数N-----NaOH的当量浓度2.酸蚀槽2.1分析方法:吸取5ml槽液于250ml的锥形瓶中,加80ml蒸馏水,加2滴溴百里香酚兰指示剂,用1N的NaOH滴定,颜色由无色变为兰色为终点,记下所消耗的毫升数V。
2.2计算方法:氟化氢胺 = 57/5 x V x NV---NaOH滴定消耗ml数N---NaOH的当量浓度3.碱蚀槽3.1分析方法:吸取5ml槽液于250ml的锥形瓶中,加蒸馏水80ml、2滴酚酞、用1N的HCL滴到乳白色,记下所消耗的毫升数Va ;再加入 20–30ml 50%的KF溶液,继续滴到白色,记下所消耗的毫升数Vb。
3.2计算方法:总NaOH = 8 x Va x N游离NaOH = 8 x ( Va - Vb/3) x N铝离子 = 1.8 x Vb x NN----为HCL的当量浓度4.中和槽、氧化槽4.1分析方法:吸取两个5ml槽液分别于两个250ml的锥形瓶中,各加入80ml蒸馏水、2滴酚酞,其中一只加入20-30ml KF,分别用1N的NaOH滴到红色为终点,记下所消耗的毫升数Va , Vb (加有KF)4.2计算方法:氧化游离硫酸=9.8 x Vb x N铝离子=1.8 x(Vb-Va) x N中和游离硫酸=9 .8 x V b x NN----为NaOH的当量浓度5.着色槽5.1 NiSO45.1.2分析方法:吸取2ml槽液于250ml的锥形瓶中,加80ml蒸馏水、5ml洒石酸溶液,在电炉上加热至沸,稍冷,加10ml30%的双氧水再煮沸5min, 加几滴氨水、10ml PH=10的缓冲液、少许紫脲酸胺,用0.02mol∕L的EDTA滴到紫红色为终点,记下所消耗的毫升数V。
如何解决冶金行业酸洗槽腐蚀问题?

如何解决冶金行业酸洗槽腐蚀问题?关键词:酸洗槽腐蚀,酸洗槽防腐,防腐材料,冶金行业●冶金行业酸洗槽腐蚀问题酸洗槽是工件在酸洗过程中用来盛放水溶液、除去金属表面薄膜的容器,广泛应用于冶金、电镀等工业酸洗行业:用于钛镍合金,不锈钢等各种铜铝金属表面酸洗使用,起到除油、除锈等功效;促进金属表面顽固氧化皮的清除,特别是热扎、退火、回火过程中生成的高温难清除氧化皮,同时防止氢脆的产生;降低金属的腐蚀速度,成倍的延长酸液的使用寿命,最终使产品表面清洁干净,形成均匀的银白色亚光结构。
目前国内酸洗槽的使用寿命相差很大,一般可用3至5年,好的可以用7至8年或更长,差的仅使用几个月就发生腐蚀渗漏。
这不仅影响酸洗的正常运行,而且由于大量的渗酸还会造成地基和建筑物的腐蚀,同时还严重污染环境。
酸洗槽使用寿命相差悬殊的原因是多方面的,有材料本身的、设计上的、施工上的和生产使用中维护管理上的。
●虽然酸洗槽具有一定的耐碱、耐酸、耐高温、抗腐蚀特性,但是鉴于其工作环境,酸洗槽防腐工作仍然是重中之重。
索雷CMI重防腐材料是设备防腐常用到的一种防腐材料,其们采用独特的聚合物技术制造而成,可具有良好的耐腐蚀性能,对众多种类的腐蚀性化学品进行防护,包括强酸、强碱、气体、溶剂和氧化剂。
并且该防腐材料分子交联主要是以醚键方式(C-O-C),醚键是一种极强的化学键,与环氧树脂相比不含羟基,与乙烯基酯相比又没有酯键,因此能够经受水解和酸的侵蚀。
与其他防腐材料相比,该材料还具有良好的耐高温和耐冷热循环性能,耐高温可达400°F(204°C),耐冷热循环范围从-40°F至+400°F(- 40°至204°C)。
●索雷CMI重防腐材料不仅可以解决冶金行业酸洗槽腐蚀问题,还可以用于解决以下行业设备腐蚀问题:。
管道酸洗方法

管道酸洗方法管道安完毕后要进行管道酸洗处理,管道酸洗的目的是通过化学作用将金属管道表面的氧化物和油污去掉,以获得金属的光泽表面。
保证管道内壁的清洁度。
同时酸洗后的防锈处理也使管壁的底层金属得到保护,防止时一步腐蚀。
管道酸洗是管道施工的一个关键环节。
目前施工现场采用的管道酸洗方式有槽式酸洗方法和循环酸洗法。
循环酸洗又分为线上酸洗和线外酸洗法。
槽式酸洗法:在以往的管道施工中均采用这种方法,就是将一次安装好的管道拆下来,分段放在酸洗槽内浸泡。
管道酸洗处理合格后再进行二次安装。
循环酸洗法:将管道用软管联接构成路,用酸泵将酸液打入管道内进行循环酸洗。
它可以将一次安装好的管道不拆卸下来,只要把液压元件断开用软管连好,即可进行。
这也就是所谓的线上循环酸洗。
如将一些较短的管件或不能在安装位置构成回路的管拆下,就地用软管或接头连接成回路进行循环酸洗,就属于线外循环酸洗。
这几种酸洗方法各有其优缺点,在今后的管道施工中不可偏废,应根据施工中的具体情况选用。
由于循环酸洗是一种较新的施工技术,有必要简单地突出地介绍一下。
循环酸洗法优点是空出的,因为在流动过程中酸洗比槽式酸洗速度快,酸洗的效果好。
又由于不使用大型槽子,使酸洗场地面积大为减少,并可根据施工条件随地酸洗。
工序简单,操作方便,大大缩短了施工工期,降低了劳动强度,一般槽式酸洗需要10~20个人,而循环酸洗只需要4~5个人操作即可。
由于循环酸洗槽子可以做成封存闭式的,减少了酸对人体的侵害,改善了劳动条件。
特别是线上循环酸洗减少了二次安装和天车吊运的麻烦,也解决了弯弯曲曲的难拆难洗的长管路的酸洗问题。
并且对酸洗后管子的内壁容易保护,利于防止再次污染。
循环酸洗是管道酸洗施工的一种新方法。
在大量管道施工中应推广使用。
但它也有其不足之处,循环酸洗的操作和酸洗后的质量检查比槽式酸洗要困难得多,这样对一些管径较大的短管应辅以槽式酸洗为宜。
因此在管道施工量少,直管管多,容易拆卸的液压系统中还是采用槽式酸洗法为好。
酸铜槽电镀液分析指导书
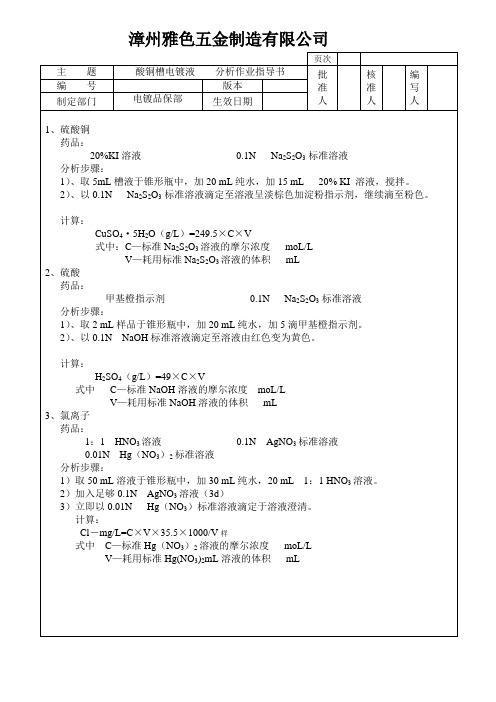
漳州雅色五金制造有限公司页次主题酸铜槽电镀液分析作业指导书批准人核准人编写人编号版本制定部门电镀品保部生效日期1、硫酸铜药品:20%KI溶液0.1N Na2S2O3标准溶液分析步骤:1)、取5mL槽液于锥形瓶中,加20 mL纯水,加15 mL 20% KI 溶液,搅拌。
2)、以0.1N Na2S2O3标准溶液滴定至溶液呈淡棕色加淀粉指示剂,继续滴至粉色。
计算:CuSO4·5H2O(g/L)=249.5×C×V式中:C—标准Na2S2O3溶液的摩尔浓度moL/LV—耗用标准Na2S2O3溶液的体积mL2、硫酸药品:甲基橙指示剂0.1N Na2S2O3标准溶液分析步骤:1)、取2 mL样品于锥形瓶中,加20 mL纯水,加5滴甲基橙指示剂。
2)、以0.1N NaOH标准溶液滴定至溶液由红色变为黄色。
计算:H2SO4(g/L)=49×C×V式中C—标准NaOH溶液的摩尔浓度moL/LV—耗用标准NaOH溶液的体积mL3、氯离子药品:1:1 HNO3溶液0.1N AgNO3标准溶液0.01N Hg(NO3)2标准溶液分析步骤:1)取50 mL溶液于锥形瓶中,加30 mL纯水,20 mL 1:1 HNO3溶液。
2)加入足够0.1N AgNO3溶液(3d)3)立即以0.01N Hg(NO3)标准溶液滴定于溶液澄清。
计算:Cl-mg/L=C×V×35.5×1000/V样式中C—标准Hg(NO3)2溶液的摩尔浓度moL/LV—耗用标准Hg(NO3)2mL溶液的体积mL。
配电箱酸洗钝化过程

配电箱酸洗钝化过程
可放入酸洗槽或钝化槽的零件采用浸渍法,但不适用于大型设备,酸洗液可长期使用,生产效率高,成本低;大体积设备充满酸液,消耗液体过多。
刷涂法适用于大型设备的内表面和局部处理,工作条件差,酸不可回收。
粘贴法用于安装或维修现场,尤其是手工操作焊接件,工作条件差,生产成本高。
安装现场采用喷涂方式。
大型容器内壁液体消耗量低、成本低、速度快,但需要配备喷枪和循环系统。
循环法用于大型设备,如换热器、管壳式等,施工方便,酸液可重复使用,循环系统需要连接管道和泵。
酸洗钝化处理的质量也可根据需要通过蓝点试验进行检查。
然后将溶液用滤纸浸泡后,贴在被测表面或直接将溶液涂滴在被测表面,30秒内观察表面蓝点,如有蓝点即为不合格。
需要注意的是,试验
应在酸洗钝化表面基本干燥后进行,试验结束后也应将试验溶液冲洗干净。
1、蓝点检验法一般用于不锈钢化学容器的制造,是一种非常严
格的检验方法。
为了通过检查,必须严格遵守工艺规程。
2、不锈钢要放在特殊的地方,必须铺木板或橡胶皮。
严禁与碳
钢混合。
3、各种加工设备,如卷板机、剪板机等。
应清洗干净,滚轮和
压力角应涂上清漆,以确保不锈钢不与碳钢直接接触。
4、夹具应由不锈钢或不锈钢垫圈制成。
5、不锈钢钢丝刷应用于酸洗钢丝刷。
通过以上不锈钢酸洗钝化的过程,大家对不锈钢酸洗钝化有了大致的了解,实际操作会因材料、温度、浓度的不同而略有调整。
酸洗钝化方式

酸洗钝化方式参考资料:/esite/detail10007651.htm根据操作方式不同,不锈钢酸洗钝化处理主要有浸渍法、膏剂法、涂刷法、喷淋法、循环法、电化学法等6种方法,其中,浸渍法、膏剂法、喷淋法比较适用于不锈钢化学品船及设备的酸洗钝化。
一、浸渍法。
不锈钢管线、弯头、小件等最适用该法,且处理效果最好。
因为处理件可充分浸泡在酸洗槽的钝化液中,表面反应完全、钝化成膜致密均匀。
很多造船厂利用威海云清化工开发院专业研发、生产、制造的“云清牌-不锈钢化学品船专用酸洗钝化膏、钝化液”批量酸洗不锈钢管线、弯头、小件,取得了较好的效果。
该法适合连续批量作业,但需随溶液反应浓度降低而不断补充新液。
其缺点是受酸槽形状及容量的限制,不适合大容量设备及形状过长过宽的管线;长期不用会因溶液挥发等原因而效果下降,需要专用场地、酸池及加热设备。
二、膏剂法。
主要成分由硝酸、氢氟酸、缓蚀剂、粘稠剂等按一定比例组成,船标《不锈钢酸洗钝化膏》CB/T3595-94有具体的检验规则,手工操作,适合现场施工,对不锈钢化学品船焊缝处理、焊接变色、甲板顶部、拐角死角、扶梯背面及液舱内大面积的涂抹钝化都适用。
膏剂法的优点是不需要专用设备和场地,不需要加热设备,现场操作灵活,酸洗钝化一次完成,独立性强;钝化膏保质期长,每次涂抹处理都用新的钝化膏一次性使用,表面一层钝化结束后反应即停止,不易过腐蚀,不受后续冲洗时间限制,焊缝等薄弱环节还可以加强钝化。
缺点是工人操作环境差,劳动强度高,成本较高,对不锈钢管线内壁处理效果稍差,需结合其它方法。
三、喷淋法。
适合于场地固定,封闭环境的单一产品或内部结构简单的设备酸洗钝化,如板材生产线上的喷淋酸洗工序,对不锈钢化学品船,可用于液货舱内壁酸洗。
其优点是连续操作速度快,操作方式简单,对工人腐蚀影响小,移液过程可将管线再酸洗一遍。
溶液利用率较高。
浸渍法用于可放入酸洗槽或钝化槽的零部件,但不适于大设备酸洗液可较长时间使用,生产效率较高、成本低;大容积设备充满酸液浸渍耗液太大。
碳钢管道酸洗钝化
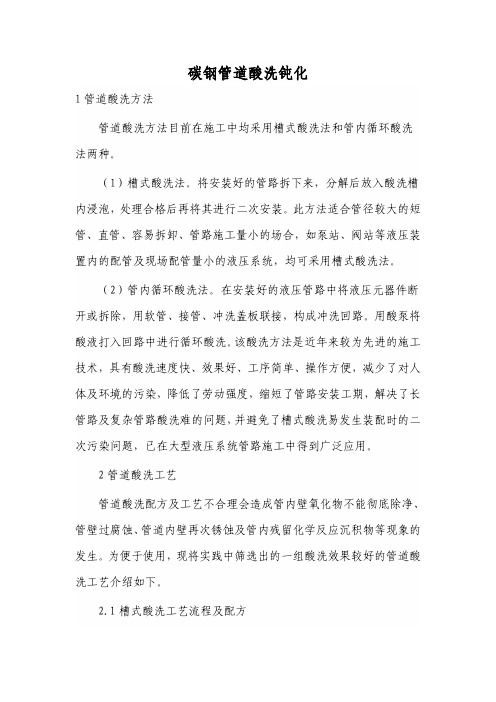
碳钢管道酸洗钝化1管道酸洗方法管道酸洗方法目前在施工中均采用槽式酸洗法和管内循环酸洗法两种。
(1)槽式酸洗法。
将安装好的管路拆下来,分解后放入酸洗槽内浸泡,处理合格后再将其进行二次安装。
此方法适合管径较大的短管、直管、容易拆卸、管路施工量小的场合,如泵站、阀站等液压装置内的配管及现场配管量小的液压系统,均可采用槽式酸洗法。
(2)管内循环酸洗法。
在安装好的液压管路中将液压元器件断开或拆除,用软管、接管、冲洗盖板联接,构成冲洗回路。
用酸泵将酸液打入回路中进行循环酸洗。
该酸洗方法是近年来较为先进的施工技术,具有酸洗速度快、效果好、工序简单、操作方便,减少了对人体及环境的污染,降低了劳动强度,缩短了管路安装工期,解决了长管路及复杂管路酸洗难的问题,并避免了槽式酸洗易发生装配时的二次污染问题,已在大型液压系统管路施工中得到广泛应用。
2管道酸洗工艺管道酸洗配方及工艺不合理会造成管内壁氧化物不能彻底除净、管壁过腐蚀、管道内壁再次锈蚀及管内残留化学反应沉积物等现象的发生。
为便于使用,现将实践中筛选出的一组酸洗效果较好的管道酸洗工艺介绍如下。
2.1槽式酸洗工艺流程及配方(1)脱脂。
脱脂液配方为:(NaOH)=9%~10%;(Na3PO4)=3%;(NaHCO3)=1.3%;(Na2SO3)=2%;其余为水。
操作工艺要求为:液体温度70~80℃,浸泡4h。
(2)水冲。
压力为0.8MPa的洁净水冲干净。
(3)酸洗。
酸洗液配方为:HCl为13%~14%;缓蚀剂为1%;其余为水。
操作工艺要求为:常温浸泡1.5~2h。
(4)水冲。
用压力为0.8MPa的洁净水冲干净。
(5)二次酸洗。
酸洗液配方同上。
操作工艺要求为:常温浸泡5min。
(6)中和。
中和液配方为:NH4OH稀释至pH值为10~11的溶液。
操作工艺要求为:常温浸泡2min。
(7)钝化。
钝化液配方为:钝化剂为8%~10%;NH4OH为2%;其余为水。
操作工艺要求为:常温浸泡5min。
- 1、下载文档前请自行甄别文档内容的完整性,平台不提供额外的编辑、内容补充、找答案等附加服务。
- 2、"仅部分预览"的文档,不可在线预览部分如存在完整性等问题,可反馈申请退款(可完整预览的文档不适用该条件!)。
- 3、如文档侵犯您的权益,请联系客服反馈,我们会尽快为您处理(人工客服工作时间:9:00-18:30)。
酸洗槽TC801分析方法
酸洗槽TC801分析方法
一、
二、试药:1N NaOH
M.O指示剂
三、操作:
(1) 取样10ml于250ml的锥形瓶中。
(2) 加水100ml,并加入M.O指示剂。
(3) 以1N NaOH滴定至蓝色为终点。
四、计算:
酸当量(N) = 滴定ml ×4.51%
五、控制范围:
酸当量(N):0.1-0.3N
过硫酸钠与过硫酸铵分析方法
一、
二、试药:0.1N-KMnO₄
三、指示剂:(1) 硫酸亚铁铵:FeSO₄ (NH₄)₂SO₄.6H₂O
(2) 磷酸
四、步骤:(1)取试样5ml于250ml锥形瓶中,加蒸馏水10c.c.
(2) 置入25cc 0.1N硫酸亚铁铵(39.2g/l). (加100 cc蒸馏水,
加5 c.c.浓硫酸,并稀释至1升)
(3)加入5 c.c.磷酸(25%)
(4)以0.1N-KMnO₄滴定至终点变色为A
(5)依上述步骤不加入Sampl重复步骤滴定至变色为B
五、计算:(B-A) ×2.43 = SPS g/l
附注:1.高锰酸钾配制方法, 称取决于.2GKMnO₄加热溶解静24小时, 稀释到1升,用棕色瓶保存。
2.制备Fe溶液时, 加10 ml浓硫酸。
取样时为1 ml试样, 加H₃PO₄ (5-10 ml).
3.加亚铁盐时要准确量体积。
铜槽分析方法
(1)
一、
二、试药:0.05N-NaOH
三、指示剂:M.O甲基橙指示剂
四、步骤:( 1)取槽液1 ml加纯水50ml于250ml锥形瓶中。
(2)加5滴M.O指示剂, 溶液显红色。
(3)用0.05N-NaOH滴定至溶液显黄色。
五、计算:
H₂SO₄含量(g/l)=24.5×滴定消耗体积(ml)六、操作范围:
150-225g/l (最佳值185 g/l)
铜槽分析方法
(2)
一、
二、试药:(1)浓氯水
(2)0.0575MEDTA
三、指示剂:MX指示剂
四、步骤:(1)取1 ml槽液于250 ml锥形瓶中, 加纯水30ml。
(2)加浓氯水5滴, 加MX指示剂1小匙。
(3)用0.0575N-EDTA滴定至呈紫色。
五、计算:
CuSO₄5H₂O含量(g/l)=14.36×滴定消耗量(ml)六、成份控制:
CuSO₄.5H₂O = 60~100g/l (最佳值75 g/l)
铜槽液分析方法
(3)
一、
二、试药:(1)1:1 HNO₃
(2)0.1 NAgNO₃
(3)0.01NHg(NO₃)₂
三、步骤:(1)取槽液25ml,加纯水30ml于250 ml锥形瓶中。
(2)向上液加入1:1HNO₃ 10ml。
(3)以0.1NAgNO₃滴定至溶液浑浊。
(4)以0.01NHg(NO₃)₂滴定至澄清。
四、计算:
Cl (mg/l) =7.1 ×2 ×滴定消耗Hg(NO₃)₂ml 五、控制范围:
30~80ppm (最佳值50 ppm)。