热轧板坯跟踪与精准定位系统研发
热轧CSP轧钢机的监测和故障诊断系统的发展

一
炼轧 厂
苏
波
1 引 言
C P( 凑 式 热 带 生 产 技 术 . o p c S 紧 C m at Sr rd c o tpPo ut n的缩 写 ) 较 为成 熟 的 典 型 i i 是 薄板坯 连铸 连轧 工艺 之一 … 。C P工 艺具 有 S 投 资少 、 厂周 期 短 、 产 流 程 短 、 效 率 和 建 生 高 低 成本 等 优势 , 到 广 大 热轧 板生 产 厂 家 的 受
处理 为 核 心 的 过 程 所 代 替 , 展 了 专 家 系 开 统 、 经 网络 和模 糊 分 析 等理 论 、 法 和 应 神 方
用 技术 的研究 。
设 备故 障诊 断技术 又 称设 备状态 诊 断技 术 , 一种通 过监 测设备 的状态参 数 , 如振 是 例 动、 噪声 、 温度 、 液 、 油 工作 参数 、 电磁 辐射 、 气
少, 检测数 据 不充 足 ; b 缺 乏专 业 知识 和实 ()
4 3 网络化 远程诊 断技术 的发展 .
随着计算 机 网络 技 术 的发 展 , 合 网络 结
践经验丰富 的维修 人员 ; c 设 备诊 断维修 体 () 系不完善 , 存在 故障 漏检 和漏报 等现 象 。 只追 求短期效益 ;d 研制 与开发 的诊 断仪器 和设 () 备 可靠 性差 , 通用 性差 , 没有统 一的标 准 。
2 热 轧 C P轧 钢 机 监 测 与 故 障 诊 断 S 系统 的研 究 现 状
机 械 监 测 是 对 运 转 中 热 轧 C P轧 钢 机 S 或 其部 件 的技术状 态进 行检 查测 定 。其 内容
1750热轧厂二级自动化系统控制简述

步运行 , 实现真 正意义 上 的容错 。 轧 线过程 服 务 器有 2 台冗 错 式 P 服 务器 , C 所
2 2 软 件 开 发 平 台 .
1 服务器 软件 系统 )
2 工程师 站软件 系统 )
有过程 自动化 的操作终 端将 通过 以太 网与 服务器进 行通讯 。设置 2台工 程 师站 用 于服 务 器进 行 编程 、
作者简介 : 马占福 , , 男 工程师 , 在读博 士 , 主要负责热轧板厂工艺技 术 、 过程控制 、 板形 控制方面 工作 , E—m i w e in@ ht a : m rag o l j ’
mal c n i. o
第 6期
ScunM t l g i a e l ry h au
开发 、 护 和监 控 。轧 线 过 程 服 务 器 与 L 维 3之 间是 通过 T P I C /P+D B的方 式 进 行通 讯 , 与加 热 炉过 程 自动化之 间通过 T P I C /P进行 通讯 , L 与 l之 间通过 T PI C /P进行通 讯 。
( . o Sr l o B y So k C m a y 2 X ’ nv r t o rht tr a d T c n lg ) 1 H t t p Mi f a i t o p n ; . i n U i s y f c i cuen e h o y i l c a e i A e o
[ src] L o pt s m cnrln b oe cn oigraz epemia aapoes Abtat 2cm ue s t ot l g,ym dl otln , let rl nr dt rcs— ry e oi rl e i h i y
i g o lb a d srp, tra r c i g, t smo e a c l t g,e h o o y p r mee n cme to ts n fsa n ti mae ilta k n ma d lc lu ai t c n lg a a t re a t n fma h n h mo li h o s fp o u i de n te c ureo r d cng,fnih d t o lci g,h o g e d t e ie mo g L1, 2, 3, i s a a c l tn t r u h t aa d l r a n e h vy L L MES
八钢1750mm热轧二级自动化系统结构简述

L 级 用 于生产 计划 、 坯库 、 卷库控 制管 理 ; 3 板 钢 L 2级计 算 机 系统 主要 完 成 板 坯 / 钢 初 始数 据 处 带 理、 材料跟 踪 、 学模 型计算 及设 定 、 程数据 收集 、 数 过 数据 通讯 以及操 作指 导等任 务 。 1 系统进 行动态 L级 控制 , 行 L 执 2级 的命 令 , 完成 厚 度 、 宽度 、 度 等相 温
在 生 产 中进 行 数 学 模 型 的 工 艺 参 数 的设 定 , 成 过 程 数 据 的 收集 , 过 对 L 级 、3级 ME 完 通 l L S系 统 的 数据 通 讯 , 来
实 现 对 成 品精 度 的控 制 。
关键字 : 系统结构 ; 系统环境 ; 模型 ; E M S 中图分类号: T 2 P9 文献标识码 : B 文章编 号: 17- 4 2 (0 8 0 —o l—0 62 2 4 2 0 )4 0 6 2
行通 讯 。 置 2台工 程师站 用 于服务 器进行 编程 、 设 开
发、 维护 和监控 。轧线过 程 服务器 与 L 间是通过 3之 T PI + B的方式进 行通 讯 ,与加 热炉 过程 自动化 C/ D P 之 间通过 T PI 行通 讯 , L 之 间 T PI C/ P进 与 1 C/ P进行
控制 机 B S相连 。 A
加 热炉
粗 除鳞
粗 轧机
热 卷箱
精除 鳞
秸 轧机
层 流冷却
卷 取
图 1 工 艺流 程 平 面 简 图
3 L 2级 控 制 系统 环 境 要 求
31 轧线 过程 服务器 采 用冗错 式 P 服务 器 . C 轧 线过 程服 务 器采 用 冗错 式 P C服 务 器 一
热轧生产线加热炉跟踪仿真的实现模式及其在速度控制中的应用

热轧生产线加热炉跟踪仿真的实现模式及其在速度控制中的应用摘要:跟踪仿真是用数学模型模拟工业加工中物料在生产线上的运动状态,为人机界面(HMI)提供数据支持,同时也是逻辑控制时序信号的重要组成。
跟踪仿真反映速度,也控制速度,因此,它具有积分和逻辑双重意义。
本文以唐钢1810热轧薄板生产线加热炉为例讨论了工业仿真中物料跟踪仿真的一种实现模式。
主要说明了建立跟踪数学模型,定义跟踪数组的数据结构的过程,并用控制逻辑流程图分析了跟踪模型的动态积分和指针移位算法,及其在速度控制中的应用。
关键词:工业仿真,跟踪仿真模型,控制逻辑设计0引言热轧薄板生产线工艺复杂紧凑,设备控制要求响应快速,自动化集中控制程度高,跟踪仿真模型为人机交互操作界面组态提供基础数据,也是PLC程序中触发和连锁信号构成中的重要组成。
在控制模型中起着逻辑、时间、空间上的协调作用,跟踪系统的准确性和可靠性关系顺控程序的有序执行,生产安全,控制精度,产品质量,对节约能源,降低原材料消耗,成本控制也具有非常实际的执行意义。
跟踪仿真模型模拟自动化生产线上物料的运动状态并产生速度控制,以及设备动作的协调同步控制,其时序在整个生产动作周期中是循环但不重复的时序。
跟踪仿真模型的模拟量因此是速度的时间反映,也随着时间产生不同的速度控制,有积分含意义,同时有逻辑意义。
以下是热轧生产线加热炉跟踪仿真的一种实现模式及其在速度控制中的应用。
1跟踪模型分析和实现算法1.1环境模型加热炉跟踪距离长,一线有加热段,横移段,保温段,三个区域;二线有加热段和横移段两个区域,如图1所示,其板坯通过一线或二线横移车输送到一线保温段。
并定义加热炉进口为模型参照0位。
1.2 逻辑算法连铸坯经摆剪剪切后进入加热炉区,加热炉区进口光电开关PHOTOCELL 的关断产生板坯头部,导通产生尾部,同时产生头部占用和尾部占用两个逻辑量。
头部和尾部跟踪点从零开始对速度设定值进行时间积分累加。
PLC通过CC-LINK网络对驱动每组炉辊的变频器进行速度设定,由变频器实现闭环速度控制。
北京科技大学科技成果——热轧L2级过程自动化控制系统
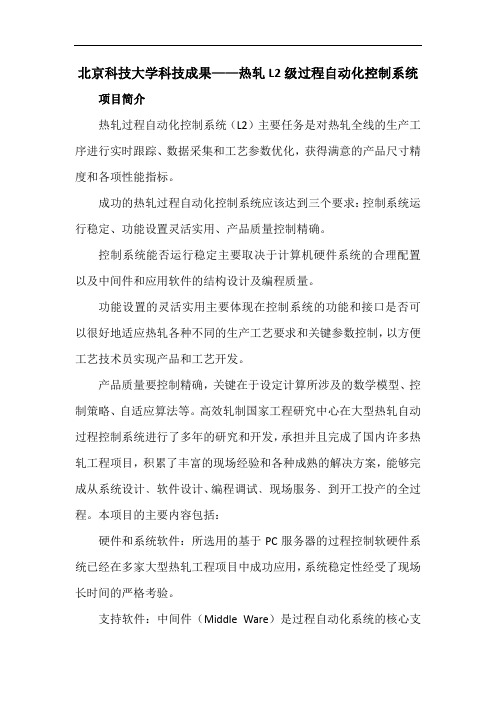
北京科技大学科技成果——热轧L2级过程自动化控制系统项目简介热轧过程自动化控制系统(L2)主要任务是对热轧全线的生产工序进行实时跟踪、数据采集和工艺参数优化,获得满意的产品尺寸精度和各项性能指标。
成功的热轧过程自动化控制系统应该达到三个要求:控制系统运行稳定、功能设置灵活实用、产品质量控制精确。
控制系统能否运行稳定主要取决于计算机硬件系统的合理配置以及中间件和应用软件的结构设计及编程质量。
功能设置的灵活实用主要体现在控制系统的功能和接口是否可以很好地适应热轧各种不同的生产工艺要求和关键参数控制,以方便工艺技术员实现产品和工艺开发。
产品质量要控制精确,关键在于设定计算所涉及的数学模型、控制策略、自适应算法等。
高效轧制国家工程研究中心在大型热轧自动过程控制系统进行了多年的研究和开发,承担并且完成了国内许多热轧工程项目,积累了丰富的现场经验和各种成熟的解决方案,能够完成从系统设计﹑软件设计、编程调试﹑现场服务﹑到开工投产的全过程。
本项目的主要内容包括:硬件和系统软件:所选用的基于PC服务器的过程控制软硬件系统已经在多家大型热轧工程项目中成功应用,系统稳定性经受了现场长时间的严格考验。
支持软件:中间件(Middle Ware)是过程自动化系统的核心支撑软件,即应用软件的开发平台和运行环境,本项目采用的中间件PCDP(Process Control Develop Platform)是由高效轧制国家工程研究中心自主研制开发的,具有完全知识产权。
应用软件:高效轧制国家工程研究中心提供的过程自动化应用软件涵盖了热轧的各项控制功能:初始数据管理、轧件跟踪、轧制节奏、设定计算(预计算、再计算、后计算、模型自适应)、通信管理、测量值处理、HMI画面管理、历史数据管理、报表管理、轧辊数据管理、模拟轧钢等。
数学模型:高效轧制国家工程研究中心能够提供如下数学模型:(1)自动燃烧控制模型;(2)轧制节奏控制模型;(3)轧制温度模型〔空冷温降、高压除鳞温降、形变热、轧件与轧辊接触时的传导温降等〕;(4)轧件变形模型〔变形抗力、轧辊压扁、轧制力和轧制力矩等〕;(5)自动宽度控制模型;(6)板形设定和控制模型;(7)终轧温度控制模型;(8)卷取温度控制模型;(9)卷取设定模型;(10)平面形状控制模型;(11)控温轧制模型;(12)轧制规程优化模型。
天车定位无线跟踪系统详细介绍

2.2.2现场设备的组成及功能、特性
交换机
2台
机柜
2个
光纤接线盒 2个
介质转换器 8个
基站
4个
基站防尘箱 4个
全向天线 4根
设备特性:
(一)交换机 WS-C2960-24TC-L
特性:(1)2960系列智能以太网交换机安装了LAN基本镜像;
(2)采用网络准入控制NAC、高级服务质量QoS、速率限制、ACL和
(2)工作于2.4GHz频段的符合IEEE 802.11g标准的多功能AP; (3)提供无线分布系统(WDS)功能; (4)支持点-点、点-多点无线连接; (5)802.11b/g双模,可以自由连接11b或11g无线网络设备
(6)支持高达128位的WEP加密,WPA,WPA2,802.1x安全认
证; (四)基站防尘箱 PHI-FC6000A 功能: 保护无线接入点AP; 特性:(1)底部线孔进线设计,满足防鼠的要求;
2.2设备组成
本系统主要分为机房设备、现场设备、天车设备三部分。机房 设备主要包括服务器、磁盘柜、机柜、中心交换机等;现场设备主 要包括机柜、光纤转换器、交换机、操作终端、基站等;天车部分 主要包括车载终端、激光测距仪、天线、UPS等。 2.2.1天车设备的组成及功能、特性
车载终端 10台 板坯库4个,钢卷库6个 激光测距仪 20台 防尘装置 20套 反光板 18块 车载基站 10台 车载天线 10根 UPS电源 10个 主要设备特性: (一)车载终端 PHI-CIT1560T-F 功能: (1)接收地面服务器传送来的作业命令和其它信息并显示; (2)整合测量数据并显示;
组播服务,提供网络控制和带宽优化;
(3)根据用户、端口和MAC地址,并通过多种不同的身份验证方
轧机控制系统TDC实践应用
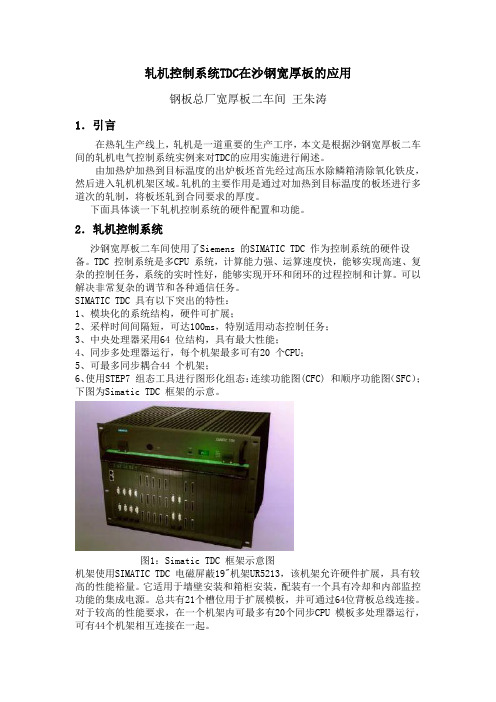
轧机控制系统TDC在沙钢宽厚板的应用钢板总厂宽厚板二车间王朱涛1.引言在热轧生产线上,轧机是一道重要的生产工序,本文是根据沙钢宽厚板二车间的轧机电气控制系统实例来对TDC的应用实施进行阐述。
由加热炉加热到目标温度的出炉板坯首先经过高压水除鳞箱清除氧化铁皮,然后进入轧机机架区域。
轧机的主要作用是通过对加热到目标温度的板坯进行多道次的轧制,将板坯轧到合同要求的厚度。
下面具体谈一下轧机控制系统的硬件配置和功能。
2.轧机控制系统沙钢宽厚板二车间使用了Siemens 的SIMATIC TDC 作为控制系统的硬件设备。
TDC 控制系统是多CPU 系统,计算能力强、运算速度快,能够实现高速、复杂的控制任务,系统的实时性好,能够实现开环和闭环的过程控制和计算。
可以解决非常复杂的调节和各种通信任务。
SIMATIC TDC 具有以下突出的特性:1、模块化的系统结构,硬件可扩展;2、采样时间间隔短,可达100ms,特别适用动态控制任务;3、中央处理器采用64 位结构,具有最大性能;4、同步多处理器运行,每个机架最多可有20 个CPU;5、可最多同步耦合44 个机架;6、使用STEP7 组态工具进行图形化组态:连续功能图(CFC) 和顺序功能图(SFC);下图为Simatic TDC 框架的示意。
图1:Simatic TDC 框架示意图机架使用SIMATIC TDC 电磁屏蔽19"机架UR5213,该机架允许硬件扩展,具有较高的性能裕量。
它适用于墙壁安装和箱柜安装,配装有一个具有冷却和内部监控功能的集成电源。
总共有21个槽位用于扩展模板,并可通过64位背板总线连接。
对于较高的性能要求,在一个机架内可最多有20个同步CPU 模板多处理器运行,可有44个机架相互连接在一起。
本框架使用的CPU 是CPU551。
I/O模板使用SM500,SM500 I/O模板提供有丰富的选项,用于连接分布式I/O。
除了16点二进制输入/ 输出以外,它还具有8 点模拟量输入/ 输出以及4 点积分型模拟量输入。
论文_热轧MES轧制计划管理

热轧MES作业计划管理1、引言MES的全称是制造执行系统( Manufacturing Execution System),MES的定义如下:“MES是一些能够完成车间生产活动管理及优化的硬件和软件的集合,这些生产活动覆盖从订单发放到出产成品的全过程。
它通过维护和利用实时准确的制造信息来指导、传授、响应并报告车间发生的各项活动,同时向企业决策支持过程提供有关生产活动的任务评价信息”。
MES系统是位于企业上层生产计划和底层工业控制之间,MES强调制造计划的执行,计划管理是MES的一个关键模块,体现了MES先进的技术核心。
它的任务就是“如何安排加工作业的顺序并合理地分配目前有限的制造资源从而使加工作业在合理的时间内加工完成”。
本文将对热轧MES计划制定过程及优化算法进行阐述。
2、作业计划管理作业计划管理将已放行生产的、有欠量的合同以及可以投入生产的原料按照合同要求、生产规程、设备要求等编制出各工序可执行的作业计划,以指导现场各工序的生产作业。
热轧MES系统作业计划的管理单位是物料,即每一块板坯和每一个钢卷。
热轧MES系统管理的计划类型有冷装轧制计划和热装热送轧制计划。
计划管理主要的执行过程图(图1)(图1)2.1、冷装轧制计划管理冷装轧制计划管理过程:计划编制人员根据生产合同、合同上所挂的在库板坯情况,进行作业计划收池,将需要生产的板坯编入作业池计划,再对池计划进行拆分,得到热轧轧机的初计划,对初计划进行顺序的优化和调整,形成正式计划,正式计划的核发功能可将材料的生产信息下发至板坯库管理系统,同时作业计划模块将材料相关的生产控制、工艺控制信息下发到加热炉及轧线L2系统,控制其生产。
冷装计划管理主要的执行过程图(图2)(图2)2.2、热装装轧制计划管理热装装轧制计划管理过程:计划编制人员根据生产管理模块生成的材料申请信息,直接按照其顺序,生成热装初计划,并对其进行计划确定。
对于热装作业计划不进行顺序调整及材料删除等动作,只能对整个计划进行回退或删除。
本钢三热轧二级跟踪系统优化
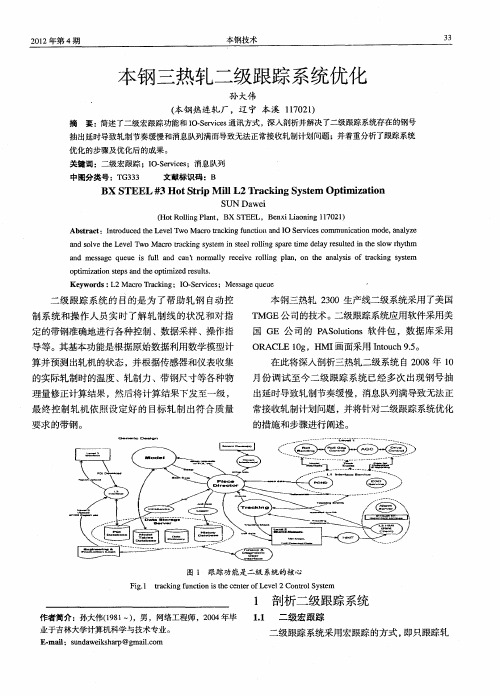
11 二级 宏跟踪 .
二级跟踪系统采用宏跟踪的方式 , 即只跟踪轧
本钢技术
21 0 2年第 4期
制线上带钢的头部 。二级跟踪功能 由来 自一级的 跟踪事件触发执行 以确定板坯的位置。宏跟踪为 板坯在轧制 区域 内的一个预 定义 的逻辑 Z N O E
爪
, 埔 | . F m.
部 的位置是可知的。宏跟踪为二级计算机完成的 功能 ,但是同时在经过传感器时支持一级的微跟
踪。
s c s n 日
图 3 I _ ev e 通 讯 方式 O Sri s c
F g3 I S r ie mmu i ai n meh d i . O e v c s Co nc t to o
Ab t a t I to u e e L v l wo M a r rc i g f n t n a dI S r i e o s r c : nr d c d t e e h T c o ta k n c o n u i O e c sc mmu i ai n mo e a a y e v n ct d , n lz o
o t z t n se sa d t e o t z d r s l . p mia o tp n p mie e u t i i h i s
Ke wo d L2M a r r c i g; I S r i e ;M e s g u u y r s: c oT a k n O— e v c s s a eq e e
本钢三热轧 20 30生产线二级系统采用 了美国 T E公司的技术。二级跟踪系统应用软件采用美 MG 国 G 公 司的 P S l i s软件包 ,数据库采用 E A o tn uo O A L 0 ,H 画面采用 I o c 5 R C E 1g MI n uh9 。 t . 在此将深入剖析三热轧二级系统 自 20 年 l 08 0 月份调试至今二级跟踪系统 已经多次 出现钢号抽
一种连铸板坯坯号自动跟踪系统

一种连铸板坯坯号自动跟踪系统本文通过对一种连铸板坯坯号自动跟踪系统进行相关的介绍,帮助相关的工作者更好的认识一种连铸板坯坯号自动跟踪系统,希望能够对具体的工作实践起到帮助。
标签:板坯;连铸;自动跟踪0 引言这种系统的组成包括板坯号识别计算机,板坯号识别摄像机,板坯跟踪PLC 系统,辊道速度检测装置以及热金属检测器。
其中,辊道速度检测装置以及热金属检测器,都连接到板坯跟踪PLC系统上;而板坯号识别摄像机,则连接上板坯号识别计算机;至于板坯号识别计算机,则连接上了板坯跟踪PLC系统。
这个系统可以实现自动跟踪连铸板坯,并且有着准确的跟踪结果,能够完美解决那些喷上了板坯号的连铸板前后的连接与跟踪问题,起到板坯最后输送至热轧接收板坯辊道的确认以及自送识别的作用。
1 一种连铸板坯坯号自动跟踪系统的特征其系统构成就是一种特征。
这种系统的组成包括板坯号识别计算机,板坯号识别摄像机,板坯跟踪PLC系统,辊道速度检测装置以及热金属检测器。
其中,辊道速度检测装置以及热金属检测器,都连接到板坯跟踪PLC系统上;而板坯号识别摄像机,则连接上板坯号识别计算机;至于板坯号识别计算机,则连接上了板坯跟踪PLC系统。
其中,上面提到的热金属检测器是在喷上板坯号后的建筑板坯输出辊道的上方来设置,其作用是用来输送检测的开关信号至板坯跟踪PLC 系统。
而上面提到的辊道速度检测装置,它的作用是对喷上板坯号后的连铸板坯输送辊道的速度进行一一检测,并对板坯跟踪PLC系统所传输检测到的输送辊道的速度信号。
上面提到的板坯跟踪PLC系统的作用就是接受各种信号。
包括辊道速度信号,辊道前进以及后退的状态信号,板坯喷印机喷印的板坯号,来自板坯切割机的板坯长度信号,热金属检测器的开关信号等等。
在计算板坯运行的长度时利用好热金属检测器信号,并配合板坯输送辊道的速度,并比较跟踪的板坯长度来识别跟踪的板坯。
另外,上面提到的板坯号识别摄像机是在热轧接收辊道与连铸辊道的连接部位的地方设置的,其作用是正确识别输送到热轧接收辊道的连铸板坯的坯号,并对着板坯号识别计算机传送正确的板坯号。
热轧板坯库自动化系统设计与实现

外购坯存放区。
收稿 日期 :o 2—0 2 1 4—2 0
’
作者简介 : 吕成军 ( 98一) 男 , 徽铜 陵人 , 17 , 安 马钢股 份公 司 自动
化工程公司 , 工程师。南京 大学软件工程专 业硕士毕业 , 主要从 事 计算机软件开发工作。
・
3 ・ 0
安 徽 冶 金 科 技 职 业 学 院 学 报
2 1 第 3期 02年
管理系统 发送入 库作业 完成 信息 , 坯管理 系统 自 板
垛规则 , 同时也可 定义 堆垛规 则 的优先级别 。这些
动修改板坯和垛位信息 。
( )板坯 出库优化 决 策 2 接 收生产制 造执行 系统 的出库计 划 , 坯库操 板 作 工核对 板坯数 据与 出库计 划 , 坯库 管理 系统将 板
只有 当所 有 的堆 垛 策 略 都符 合 时 ,( = 1 p ) ;
只要有一个堆垛策略不符合 , 对应 的 S =0 此时 i ,
p x =0 () 。
V0 . 2 N . 12 . o 3
J1 0 2 u .2 1
热 轧 板 坯 库 自动 化 系 统 设 计 与 实 现
吕成 军
( 马钢 自动 化 工程 公 司 安 徽 马鞍 山 2 30 ) 400
摘 要 : 连铸和热轧生产工序通过热轧板坯库进行生产的缓冲, 理水平将直接影响到连铸连轧生产的 性和成本。 其管 连续
关键 词 : 板坯库; 堆蛛策略; 信息管 统 物流管理 理系 中 图分 类号 : 9 F 5 . 3 文 献标识 码 : 文 章编 号 :6 2— 9 4 2 1 ) 3— 0 9- 4 : 2 2 1 A 1 7 9 9 (0 2 0 0 2 0
浅谈热轧带钢跟踪

浅谈热轧带钢跟踪摘要:在热轧工艺的生产过程中,带钢的跟踪系统正常工作至关重要。
本文通过对2250热轧带钢信号跟踪系统以及轧线高效轧制功能的描述,阐述了2250热轧跟踪系统的工作原理。
关键词:带钢跟踪轧制Study on signal tracking of strip and high efficiency rolling ofrolling lineAbstract:In the process of hot rolling process, the normal work ofthe track system of the strip is very important. book Basedon the description of the signal tracking system of2250 hot-rolled strip and the efficient rolling functionof rolling line, this paper expounds the working principleof 2250 Hot Rolling tracking system.Keyword: Strip tracking rolling1.引言2250热轧是一条技术含量极高的热轧生产线。
轧线电气采用日本TMEIC的V 系列控制器,引进了德国SMS先进的轧钢设备,采用了世界一流的工艺技术。
2250热轧的跟踪系统功能较为全面,通过对带钢的计算跟踪、影像移动、消除、更新、修正等功能来实现整条轧线的跟踪。
2.跟踪系统简介一级跟踪系统通过处理传感器反馈信号计算钢板位置,判断钢板分布状态并辅以跟踪校正和信号屏蔽等功能,最终获取钢板的精确位置,达到为轧线设备提供控制依据的目的。
2.1跟踪系统的功能一级跟踪系统主要功能包括:1. 处理传感器信号;2. 计算钢板的头尾位置;3. 判断钢板分布状态;4. 跟踪校正功能与信号屏蔽;5. 为轧线设备提供控制依据。
盲动化控制系统在热轧板坯库工序中的应用

操作工利用工业 电视监视现场上料情 况 板坯 物 料跟踪情况如 图 i 所示 。
3 . 自动控制状态下异常情况及 处理方法 .2 2
炉坯或者 中板也 由此辊道 下线。另外 , 在热轧板 坯库 与 连铸车 间设 有一个过跨 台车。 传送需 要往返连铸 精
的范 围是从板坯库人 口到加 热炉炉前辊道 。 3 自动化 控制系统功能的实现
符 , 录板坯重量 。但是也会有其 它因素 造成 一些 并记 不便 。
( ) 板坯称重时发现重量与计划表不符 i 上料板坯在通过 A 称重辊道时会称 出板坯重量 8
3I 自动化控制 系统概述 .
测 出长度 ,发 现和计划 表显示 的重 量和长度 信息 不
自 动化控制 系统在热轧板坯库工序 中的应用
自动化控制 系统在 热轧板坯库工序 中的应用
张慧丽
、
刘蕊
( 天津天铁冶金集团热轧板有限公司, 河北涉县 0 60 ) 544
[摘要 ] 针对热轧板坯库 的人库 、 倒跺 需要人 为干预手动操作的问题 , 通过将 自动化控制系统运用到入库 、 出库 、 轧制计
划 ” 面 , 活已下达的装钢计划 , 界 激 生成并发送形成 出 库作业命令 , 此时 出库 ( 送加热炉 ) 作业命令 完成 。然
后, 天车根 据命 令 到达指定跺 位 , 照计划 的顺序 以 按 及序号完成板坯上料 , 实现板坯 出库 。
输; 另一功 能是直 接热装 热送 连铸即时生产的板坯 。 B 辊道 为板 坯下线辊道 , 连铸 出坯辊道和热轧轧 制线 与
(微 机 应 用 与 自 动 化 >
一1 5—
划 等工 序的管理 中 , 使工序运行更加便捷 , 节省了人力资源 , 降低了企业成本 , 提高了设 备使 用率和生产质量 , 了企业生产 确保
武钢二热轧板坯库实时生产物流管理系统研究与设计【范本模板】

武钢二热轧板坯库实时生产物流管理系统研究与设计武钢二热轧板坯库主要接收来自连铸工序的冷、热连铸板坯、少量外购板坯,向热轧工序提供完全符合轧制计划单元要求的合格板坯,是热轧工序和连铸工序的联接纽带。
其进出库作业量大,时间性要求强,与生产系统中的作业环节有着密切的数量联系和时间联系。
因此,板坯库生产物流管理水平的高低直接影响着连铸一连轧生产秩序,影响生产、产品质量和经济效益.1板坯库概况库区平面布置与设计是物流合理化的前提,库区的平面布置一经决定,物流路线随之被决定,合理布置的目的是减少物料流的迂回、交叉以及无效的往复运输、避免物料运输中的混乱、路线过长等现象,同时库区的合理规划也有利于提高仓库的面积、容积利用率.因此,在对武钢二热轧现有物流及作业流程分析的基础上,对板坯库平面区域进行合理规划有着重要的现实意义.武钢二热轧板坯库是与主轧线垂直布置的.板坯库分为4跨,每跨宽度30m,每跨有两列板坯,配置有4台吊车,每跨一台。
有5条辊道,其中3条与轧线平行,编号分别为3CC组辊道,2CC组辊道,B组辊道。
2条与轧线垂直,编号分别为BC和AC。
板坯库有3个转盘,编号为1#,2#,3#。
2CC辊道为板坯下线辊道,即将从三炼钢过来的板坯送至板坯库存放;3CC辊道为板坯上料辊道,将板坯送入加热炉。
辊道由两台PLC控制.在3CC辊道,2CC辊道,B组辊道分别设置TOP点(连铸工序与板坯库的交接辊道).板坯库区域划分图如图1所示.2板坯库的组织和管理板坯库的组织和管理主要针对板坯的入库、出库以及在库的倒垛、吊运等一系列的操作而设计和管理的,操作人员通过客户机来掌握整个板坯库的物流状况,依靠生产物流信息的决策来对库内板坯进行管理。
其主要功能有:①板坯库作业管理包括入库、出库、倒垛作业管理和作业命令实绩收集。
板坯入库包括连铸板坯入库、外购板坯入库及炉前炉后拒收坯入库.生产物流信息系统为此提供连铸板坯信息接收、外购板坯的数据请求登录、板坯到达确认、建议板坯入库库位、指定传送路径、作成吊车搬送指令、入库吊车搬送实绩收集等功能。
步进梁式加热炉内板坯跟踪功能的实现

步进梁式加热炉内板坯跟踪功能的实现作者:陈铎来源:《机电一体化》2014年第03期【摘要】本文以某热轧厂步进梁式加热炉为背景,着重介绍了一种炉内板坯跟踪功能的实现方法,该方法逻辑清楚,编程容易,易于实现,在实际使用时未发生板坯数据跟踪错误,保证了生产的顺稳进行。
【关键词】加热炉;板坯;跟踪;实现方法引言炉内板坯跟踪功能是加热炉控制功能中不可缺少的部分,能够提供炉内板坯的真实位置,为板坯出炉温度的准确计算提供前提条件,并确保板坯按计划轧制,对于加热炉的连续性和稳定性生产有十分重要的作用[1]。
由于操作工无法看到炉内板坯的运行状况,一旦出现数据混乱,必须停产呼叫维修人员进行维修,造成一定的停产时间。
本文以某热轧厂步进梁式加热炉为背景,先简述了工艺流程和控制系统硬件配置,然后分四个步骤着重介绍了一种炉内板坯跟踪功能的实现方法。
1 工艺简述某热轧厂加热炉年计划完成400万t板坯的加热任务,拥有三座额定加热能力为 300t/h步进梁式加热炉。
加热炉有效长度是44870mm,板坯规格为厚度230mm、宽度850-1650mm、长度9000-11000mm,设计标准坯规格为230×1250×10500mm。
待加热板坯按轧制顺序进行校验,校验合格板坯由入炉辊道输送、定位到加热炉炉前;装料炉门开启,装钢机将板坯托起来,放到炉内步进梁上;步进梁执行正循环动作将板坯一步步运往出料端;待出钢条件满足后,出料炉门开启,出钢机将板坯从炉内托出来,放到出炉辊道上,最后由出炉辊道将板坯送往轧机轧制。
2 控制系统硬件配置每座炉子独自使用一套板坯输送控制系统。
每个系统均选用西门子416-3系列CPU作为主控制器,通讯网络采用Profibus-DP,包含3个DP主站系统。
其中,主控制器用来完成设备顺序控制、物料跟踪、与其它PLC通讯等功能;DP主站系统1包括4个ET200M子站和按钮盘,用来采集装出钢机、炉门的位置信号和发出控制命令;DP主站系统2包括2个300系列 CPU,分别用来实现对步进梁和液压站的逻辑控制;DP主站系统3用来与变频器通讯,实现对装出钢机电机、炉门电机的控制。
板坯热装在热轧板带厂的应用实践

正 常情 况下 . 炉 厂板坯 切割 时 的温 度约 8 0 2 然 后 转 59 ,
3 6块 堆垛 运 输至 热轧 原 料库 . - 在热 轧 原料 库 按 照 每垛 最 多 1 2块 板 坯堆 垛 . 等待 纳入 轧制 计划 后装 炉 。 装炉 时 的温 度取 决 于从 板坯 切割 到装 炉 时 的温 降时 间 . 炉温 度高 低 装
踪程 序 . 上料 辊道装 钢 时 由计算 机 自动记 录该 板坯 的入 在
21 冷 热坯 的煤 气 消耗差 异 大 . 使 用 标 准 断 面 尺 寸 2 0 mx 5 0 2 m 10 mmx 3 0 9 0 mm 钢 坯 . 在煤气 压力 正常 时轧制 牌号 Q 3 B规格 45 25 . mmx 5 O mx lOm C 钢 卷 . 续 生产 进 行 测算 : 坯 人 炉 温度 小 于 2 0C. 大 连 钢 0 ̄ 最 出炉 块数 2 1块 。0 th,煤 气 ( 焦 炉 煤 气 )流 量 为 5 4/ 纯 3 0 0 ah;钢 坯 入 炉温 度 大 于 4 0C。最 大 出炉块 数 2 70 m/ 0 ̄ 6 块 ,2 th, 气 ( 焦 ) 量 为 3 0 0 / ; 计 算 钢 坯 人 6 4/ 煤 纯 流 3 0 m3h 经 炉 温 度 < 0 ℃ 的 煤 气 单 耗 为 7 .m3 t 钢 坯 入 炉 温 度 20 34 / . > 0 %的煤 气 单耗 为 5 .m 40 29 22 加热 制度 不 能严 谨执 行 . 热轧 加热 炉未 上 自动 燃 烧控 制模 型 ( 二级 ) 可实 现人 , 工 设 定 自动燃 烧 ( 级 ) 由于 坯料 尺寸 变 化 多 、 热坯 交 一 , 冷
炉温 度 的测算 以及 加 热炉 的 温度 控制 使 用 。因此 , 必须 建
板坯库实时生产物流管理系统的研发

板坯库实时生产物流管理系统的研发在钢铁企业炼钢-连铸-热轧一体化生产模式下,板坯库作为连铸、热轧生产工序间的缓冲环节,其管理自动化水平的高低,直接影响着连铸-热轧生产的连续性和一体化生产的成本。
在以往的研究中,人们主要集中在炼钢、连铸和热轧的计划与调度中,忽视了对板坯库管理与控制的研究。
因此,本文根据重钢热轧厂1780mm热连轧生产线的实际情况,对板坯库实时生产物流管理系统进行研究,采用Justep Business业务架构平台和Oracle数据库,以Delphi为开发语言,设计并开发满足重钢热轧厂生产需要的板坯库实时管理系统软件。
本文的主要工作如下:①分析了板坯入库选择垛位的原则,对影响板坯库作业效率的主要因素进行了归纳,以板坯库有限储位和垛位选择原则为约束,建立了一种基于铸轧作业计划协同优化的板坯入库决策模型,实现需入库的板坯批次的全局优化运算,算法可快速优化出板坯入库垛位和铸机板坯产出序。
为了克服遗传算法和模拟退火算法在实际应用中显现的不足,构造了遗传模拟退火算法,该算法充分发挥了遗传算法良好的全局搜索能力和模拟退火算法有效避免陷入局部极小的优点,从而提高了算法的全局寻优能力。
基于遗传模拟退火算法实现了板坯入库优化程序,并进行了大量的计算。
②详细分析板坯库实时管理系统的需求、热轧和炼钢的物流和信息流,完成了板坯库实时管理系统总体设计和系统实现。
③基于Justep Business业务架构平台和Oracle数据库在MES 系统中实现所提出的板坯库管理系统。
该生产管理系统对热连轧产线的物料库存、技术质量、生产计划、设备、数据采集等进行管理,实现物流和信息流的协调统一。
重钢热轧厂板坯库实时管理系统软件开发采用软件工程设计方法,依次经过需求分析、详细设计、软件编程、和软件测试等步骤,应用图形界面友好,较好地实现设计目标,得到重钢现场专家们的肯定。
- 1、下载文档前请自行甄别文档内容的完整性,平台不提供额外的编辑、内容补充、找答案等附加服务。
- 2、"仅部分预览"的文档,不可在线预览部分如存在完整性等问题,可反馈申请退款(可完整预览的文档不适用该条件!)。
- 3、如文档侵犯您的权益,请联系客服反馈,我们会尽快为您处理(人工客服工作时间:9:00-18:30)。
热轧板坯跟踪与精准定位系统研发作者:翟秋菊
来源:《中国科技纵横》2020年第04期
摘要:结合现有技术积累和经验总结,深入研究热轧板坯库内设备功能和作业工艺流程。
以实现热轧板坯跟踪与精准定位为目的,以升降辊道、输送辊道、吊装天车三种主要输送设备为动作跟踪对象。
将热轧板坯跟踪与精准定位系统划分为三个主要功能:板坯全行程跟踪功能,板坯精准定位功能,通讯功能。
用于定位板坯在成品库内的实时位置,满足热轧板坯库所有作业的跟踪需求,实现板坯在连铸、成品库、加热炉等多工艺流程中的信息统一,为板坯成品库的信息化和智能化管理提供了坚实的基础。
关键词:板坯;跟踪;精准定位
0引言
热轧板坯成品库是连接连铸和加热炉的重要纽带,也是热轧板坯入库和出库的门户。
随着自动化和信息化技术在钢铁企业的应用不断深入发展,板坯成品库的现有技术也在不断提升。
作为实现板坯成品库全自动的前提,热轧板坯跟踪与精准定位系统已经是整个库区不可或缺的部分。
轧板坯跟踪与精准定位系统不仅能够保证板坯在输送辊道上实时跟踪,还能够保证板坯在成品库内的精准定位,是实现热轧板坯成品库信息化和智能化的基石。
1 总体思路
结合现有技术积累和经验总结,深入研究热轧板坯库内设备功能和作业工艺流程,以实现热轧板坯跟踪与精准定位为目的,以升降辊道、输送辊道、吊装天车三种主要输送设备为动作跟踪对象,将热轧板坯跟踪与精准定位系统划分为三个主要功能:板坯全行程跟踪功能,板坯精准定位功能,通讯功能,用于定位板坯在成品库内的实时位置,满足热轧板坯库所有作业的跟踪需求,实现板坯在连铸、成品库、加热炉等多工艺流程中的信息统一,为板坯成品库的信息化和智能化管理提供了坚实的基础。
2 系统构成
为了实现板坯跟踪和精准定位,提高热轧库区管理和调度的整体质量,根据现场实际情况,按照安全第一、保证效率的方针,将系统分为L1和L2两层,其中L1包括两套PLC,采用西门子S7-300架构。
L2采用C#语言编程,Oracle数据库存储数据。
L1和L2之间通讯采用TCP/IP协议,两套PLC之间采用无线网络通讯。
整个系统均采用模块化编程,将整个程序分为若干个功能块。
系统构成如图1所示。
3板坯全行程跟踪
热轧板坯库内的板坯全行程跟踪是对板坯在热轧库区内的全方位跟踪,功能聚焦点在板坯所处区域和位置。
板坯跟踪范围为连铸出口升降辊道、板坯热送辊道、板坯称重辊道、保温炉区域、板坯修磨区域、板坯合格品区域、修磨机、待手修区、外采板坯码放区、无计划区等,包括了从连铸出口到加热炉入口的所有区域。
板坯跟踪的实现首先考虑板坯数据存储,将数据区分为三部分,分别为:原始数据区、跟踪数据区、备份数据区,如表1所示。
原始数据区用于存储所有连铸产出的热板坯和存储在热轧板坯库内的热板坯基础原始数据,包括:ID、板坯号、材质、板坯尺寸、生产日期等内容;跟踪数据区用于存储辊道上、天车上和板坯库内所有板坯的跟踪信息,包括:板坯号、板坯当前位置、板坯当前状态、板坯头部位置等内容;备份数据区用于存储7天以内的出库板坯数据,用于板坯回退和信息回溯功能。
板坯全行程跟踪是板坯在热轧库内的宏跟踪,功能实现基础依靠板坯精准定位功能,跟踪数据由PLC内的板坯精准定位程序提供。
4板坯精准定位
板坯精准定位是板坯全行程跟踪的基础,更是热轧板坯成品库实现全自动控制的重要手段。
在板坯成品库全自动控制中,板坯定位、天车定位、辊道定位、跺位占用信息、板坯码放状态等都离不开板坯精准定位技术的使用。
板坯精准定位功能的高低直接影响着板坯成品库自动化水平的高低。
板坯精准定位的工作对象是指板坯在库房内由天车或辊道动作所引起的一系列位置和状态变化,此种变化由天车PLC或辊道PLC负责记录分析。
其目的是通过确定板坯在库房内具体位置和状态决定是否启动相关的功能程序,对跟踪的板坯准确地进行各种控制、数据采样、操作指导并将其跟踪信息发送至板坯全行程跟踪功能中以实现板坯的全行程可视化跟踪管理。
当板坯在库房内或辊道上的实际位置与PLC系统中计算位置不一致时,板坯精准定位系统自动修正,从而防止放歪、放空等事故的发生,满足安全生产的要求。
精准定位由PLC完成,毫秒级的循环周期保证了跟踪的实时性和准确性。
精准定位和设备控制是互为犄角的关系,两者同时工作,前者为后者提供板坯位置信息,后者为前者提供动作和状态依据。
根据运输板坯的设备不同,板坯精准定位分为两部分,即天车吊运板坯精准定位和辊道输送板坯精准定位。
4.1天车吊运板坯精准定位
在整个板坯吊运过程中,板坯精准定位实时监控天车的大车位置、小车位置、主钩高度、板坯宽度、负载状态,依据内部逻辑综合判断天车动作所在过程;实时记录板坯取、放跺位信息;实时记录板坯信息等。
汇总所有信息形成以时间为X轴,空间为Y轴,板坯信息为Z轴的精准定位信息。
将精准定位信息通讯至板坯全行程跟踪功能,为板坯全行程跟踪提供详实可靠的数据。
由于板坯多层码放,会造成Z轴方向的累积误差,因此设置板坯高度激光校正功能,当板坯的计算高度与实际检测高度偏差值大于预设值时,系统自动修正偏差预设参数。
系统实时采集偏差预设参数,通过长时间运行形成专家库,逐步提高板坯吊运高度设定精准度。
4.2辊道输送板坯精准定位
辊道定位跟踪主要采用的方式是当板坯头部到达首个热金属检测器(HMD)时开始跟踪,当前段辊道的编码器开始计数,直至板坯进入下一组辊道,当前段辊道的编码器清零并将终止距离值赋值给下一组辊道的编码器作为起始值,依次类推,直至板坯移除辊道。
在不同辊道之间安装有热金属检测器(HMD),用于校正编码器数值,防止因板坯打滑而出现的计数误差。
系统还会实时监视热金属检测器(HMD),当发现热金属检测器(HMD)损坏后,會发出报警。
5通讯功能
热轧板坯跟踪与精准定位系统与天车控制系统、辊道控制系统和库区管理系统均有通讯接口,传输数据包括天车传感器信息、天车动作状态信息、天车控制命令信息、辊道传感器信息、辊道动作状态信息、辊道控制命令信息、库区跺位信息、库区板坯初始信息等内容。
6结语
热轧板坯跟踪与精准定位系统的研发,实现了热轧板坯在热轧成品库内的实时跟踪和精准定位,实现了板坯在连铸、成品库、加热炉等多工艺流程中的信息统一,为板坯成品库的信息化和智能化管理提供了坚实的基础。