文档 塑料封条色差的原因有哪些
塑胶产品外观常见不良分析
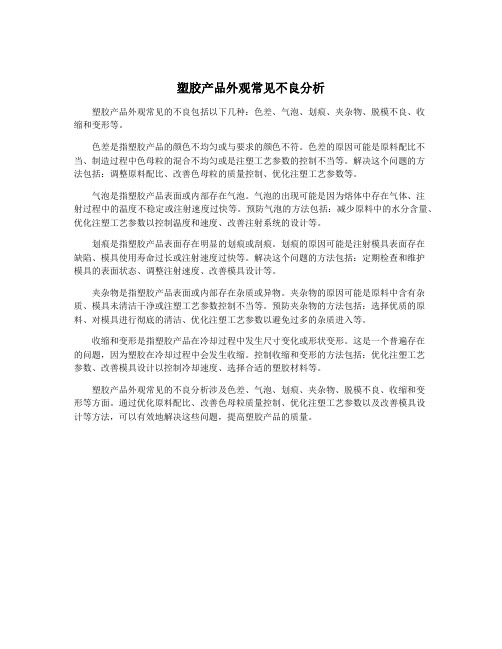
塑胶产品外观常见不良分析塑胶产品外观常见的不良包括以下几种:色差、气泡、划痕、夹杂物、脱模不良、收缩和变形等。
色差是指塑胶产品的颜色不均匀或与要求的颜色不符。
色差的原因可能是原料配比不当、制造过程中色母粒的混合不均匀或是注塑工艺参数的控制不当等。
解决这个问题的方法包括:调整原料配比、改善色母粒的质量控制、优化注塑工艺参数等。
气泡是指塑胶产品表面或内部存在气泡。
气泡的出现可能是因为熔体中存在气体、注射过程中的温度不稳定或注射速度过快等。
预防气泡的方法包括:减少原料中的水分含量、优化注塑工艺参数以控制温度和速度、改善注射系统的设计等。
划痕是指塑胶产品表面存在明显的划痕或刮痕。
划痕的原因可能是注射模具表面存在缺陷、模具使用寿命过长或注射速度过快等。
解决这个问题的方法包括:定期检查和维护模具的表面状态、调整注射速度、改善模具设计等。
夹杂物是指塑胶产品表面或内部存在杂质或异物。
夹杂物的原因可能是原料中含有杂质、模具未清洁干净或注塑工艺参数控制不当等。
预防夹杂物的方法包括:选择优质的原料、对模具进行彻底的清洁、优化注塑工艺参数以避免过多的杂质进入等。
收缩和变形是指塑胶产品在冷却过程中发生尺寸变化或形状变形。
这是一个普遍存在的问题,因为塑胶在冷却过程中会发生收缩。
控制收缩和变形的方法包括:优化注塑工艺参数、改善模具设计以控制冷却速度、选择合适的塑胶材料等。
塑胶产品外观常见的不良分析涉及色差、气泡、划痕、夹杂物、脱模不良、收缩和变形等方面。
通过优化原料配比、改善色母粒质量控制、优化注塑工艺参数以及改善模具设计等方法,可以有效地解决这些问题,提高塑胶产品的质量。
塑料件批次色差产生的原因

塑料件批次色差产生的原因
首先,原材料的质量和稳定性是造成塑料件批次色差的重要原
因之一。
不同批次的原料供应商可能存在一定的质量差异,比如颜
料的纯度、分散性等。
这些差异会直接影响到塑料制品的色彩表现。
另外,原料的储存条件和保质期也会对颜色稳定性产生影响,例如
光照、温度和湿度等因素都可能导致颜料的老化变质,从而引起色差。
其次,生产工艺对塑料件色差的影响也非常重要。
比如注塑工
艺中的温度、压力、冷却时间等参数的控制会直接影响成型件的色
彩均匀性。
不同的生产工艺流程可能会导致塑料件的收缩率、熔体
流动性等物理性能发生变化,进而影响颜色的表现。
此外,环境因素也是导致塑料件批次色差的原因之一。
比如生
产车间的温湿度、粉尘、异味等环境因素都可能对塑料制品的色彩
产生影响。
特别是在染色过程中,环境的干扰可能会导致色彩的不
稳定性,从而产生色差。
综上所述,塑料件批次色差的产生原因是一个复杂的综合问题,需要从原材料、生产工艺和环境因素等多个方面进行全面分析和控
制,以确保塑料制品色彩的稳定性和一致性。
只有全面把握这些影响因素,才能有效地减少塑料件批次色差的发生。
塑料软包装印刷色差的影响因素

3、闭环颜色控制技术
将密度计、色度计等安装在凹印机上,对色标或图案进行 扫描并与预先设定的标准值进行比较,得出色差的数 值。一旦超差就会自动进行修正。使用在线色彩控制 装置对色彩稳定性进行测量监控、修正将是一个重要 的发展趋势。
判断色差一直以来都是行之有效的。有时颜色在普通光照下看上去相同,但 在另外一种光源下看上去却不一致,因此应选用标准的光源进行观色或比色。 但是视觉观察方法存在一些局限: 靠视觉观察的结果很难与数值对应起来。 人的身体、精神、情绪等因素会影响到观察色彩的能力。 尽管肉眼善于观色,但是不善于记忆颜色(如果不把产品并排放在一起,肉 眼便无法准确地测定颜色)。或者说人眼对色彩的记忆力很差,只有在进行 直接色彩对比时才表现出精确性。 人眼的疲劳效应、视觉暂留、视觉记忆等对颜色观察产生不利影响。 一般情况下,印刷操作者工作一定时间后,对颜色的敏感性降低。这样连续 工作势必造成眼睛的疲劳,从而导致对色彩判断的误差。因此不能总盯着看, 否则就看花了。同时视觉暂留、视觉记忆也会对观察颜色产生不利影响。
塑料软包装印刷色差的影响因素
1
一、综述
在印刷工艺中,如何使一批印刷品或几批印刷品的墨色 保持一致是一个最基本的要求,也是一个重要的难题。 对于生产商来说,产品所采用包装的颜色已成为辨别产 品的重要手段和象征(甚至成为企业的标志色)。无 论在哪里,消费者都能认出可口可乐的红色、汰渍洗衣 粉的橙黄色以及许多产品的颜色。如果外包装看起来 外观有差异,消费者就可能会认为产品质量不稳定甚 至怀疑产品的真实性。所以这些知名企业非常重视产 品的包装的颜色,要求印出的墨色必须稳定一致。
差可以通过密度或色度来监控,密度控制法适用于监控印刷过程。 但对于多色印刷而言,密度测量结果和人们的视觉密度测量语言无 法明确有效地跟顾客进行信息交流,而这样的信息交流目前变得越 来越重要。因此必须用顾客能领会的方法说明产品的规格。色度控 制法已经成为印刷者着重研究的对象,原因就在于它在检测中显示 出明显的优点:
色差原因分析及改善

原因確認
整批顏色不對樣板,也可能同批顏色不一致,或駁口盒兩片顏色不一致,但從首 件樣來看,還是沒有跟準樣板。 機器速度變化,水墨平衡被打破,同批顏色有深淺不同,但數量不是很多。 在不停機狀態下同時開下來的顏色深淺變化較大,且是連續的。
結果 V X X
壓力過大 水路不暢通
墨輥磨損 油墨調和不當 水大 酒精質量不佳 紙張底色不對樣板 印版使用次數較多 曬版時間不當 拼版方式 印刷過程中變差
色差改善計劃表
1116w 1117w 1118w 1119w
D1主 題 選 定 D2緊 急 對 策 D3現 狀 分 析 D4初 步 原 因 分 析 與 驗 證 D5細 步 原 因 分 析 與 對 策 D6效 果 確 認 D7防 呆 及 水 平 展 開 D8標 準 化 計劃 實際
D1→D2→D3→D4→D5→D6→D7→D8
4月24日料號3517307400有送貨編號SH11040969
補不良品200PCS給台達,客戶沒有再次投訴。 4月22日-27日台達沒有色差方面的投訴。
D1→D2→D3→D4→D5→D6→D7→D8
防呆及水平展開
塑料件油漆产生色差的原因

塑料件油漆产生色差的原因 一、材料 二、施工工艺 三、参数 四、人为因素
• 材料
• • • • • • • • • 1、油漆 本色漆 金属漆 极易产生色差的颜色 白色 亮黄 2、油漆批次差别 3、塑料件材质差别 ABS 白色 黑色 4、油漆过期(变质) 5、塑料件装配几何状态不同
• 塑料件装配几何状态的不同 • 也是导致油漆产生色差的主要因素 • 当油漆塑料件与车身装配界面不同时,光 源的反射角度就会不同,目视色差效果就 会产生差异。 • 例如:塑料件油漆保险杠与车身翼子板装 配,若在同一平面颜色过渡不好,就会导 致明显的色差,所以塑料件装配几何状态 是产生色差的重要因素。
• 施工工艺的影响
• 静电喷涂 • 金属铝粉排列整齐 • 空气喷涂 • 金属色漆中的铝粉排列比较杂乱
• ቤተ መጻሕፍቲ ባይዱ艺参数
• • • • • 工艺参数的稳定性是影响色差的重要因素: 如油漆黏度、喷漆房内温度、湿度 晾干时间 漆膜厚度 过烘烤等
• 人为因素
• • • • • 人为补漆 搅拌不充分 手法错误 膜厚喷涂不均 输漆设备清洗不净
PVC封边条产品色差改善报告

资料整理及发表
月份 10
P DCA
责任人
11
1
要因分析
P DCA
机
人
同批次料不同 规格不同机台
抽粒机参数调整
挤出机没清理干净,加 过滤网,时有时无
员工品质意识不够高
抽粒机换色
清理不干净
标准存放与使用
不受控制,导致
表面亮度
标准变异
与压纹影响
来料检验
员工操作技术不够熟练 换颜色时搅拌桶未清理干净
磅色粉不够精准,色粉磅错
PVC封边条素色色差
改善小组
课题改善报告
报告人: x文新 报告日期:2015年 01月 23日
P DCA
主
素色色差问题
题
1、素色产品退货较多,尤其色差问题最多,影响公司形象,带来成本损失。 2、因为素色色差造成素色产品质量不稳定,客户不接受,素色产品占总销售
选 比例过低。
题
理
由
(文字说 明+表格或
P DCA
项目
完成情况
设定11月份工作计划,素色退货不良率降到2% 截至11月25日合计 素色退货2批次
1 美格利生,SP9278 14000米,表面易刮花
表面过UV处理OK,后 续调整配方,已实 施。
百利文仪 ABS SP1615 退货400米表面线条,光 亮度不够
10月30日
本月完成30个客户,合计 180款颜色档案建立
10月30日
4
打粉冷却温度过高,长时间储存导致变黄,现设定
冷却温度40℃以下
A/B班领班每隔一个小时抽 查冷却情况一次
10月30日
5
基料配方调整后需试产2次以上,确认OK后方可生 产大货。
塑料软包装印刷色差的影响因素
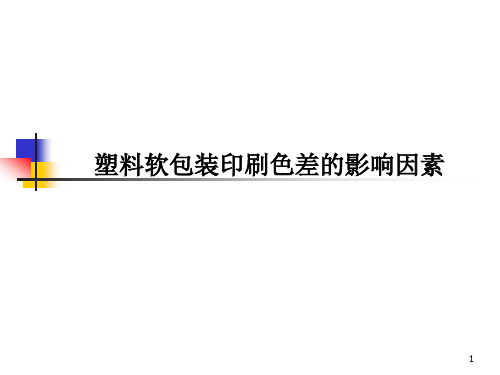
2)、色度控制法 用光谱分光光度计测色块的光谱反射率,并由此计算出三刺激值或 者由色度、 仪测量色块直接得到三刺激值,经过色度检测公式转换得出L*、a*、 b*及△E,作为颜色标准,再根据此标准对印刷颜色进行检测调整, 直到色差符合要求。 通过标准色与样品色的色差值可以知道彩色复制品与色样之间的色 偏情况。 △L*>0 偏白, △L*<0 偏黑; △a*>0 偏红, △a*<0 •偏绿; △b*>0 偏黄, △b*<0 偏蓝。 通过对色差信息的分析,可以为确定专色油墨配方调整方向提供 准确依据,从而缩小色差,使彩色复制品的颜色与用户提供的色样 更趋于接近。
11
三、塑料凹印色差问题产生的原因和影响因素
一)、油墨
油墨是决定印刷品颜色一致性的主要因素之一,它直接影响印品 颜色的正确性和稳定性。 1、选用质量稳定、颜色没有偏差的油墨 油墨本身也存在一个同批色差和不同批次之间 的色差问题,这是 反映油墨质量的重要指标。 要解决塑料凹印的色差问题,首先就 要选用质量稳定、色相没有偏差的油墨。一批印刷品最好使用同 一批次的油墨(配制专色墨时最好一次足量调制),因为不同批 的油墨中,有些油墨很难保证批次间油墨的色相没有差别。如果 油墨色相偏差过大,就很难通过其它方法来控制印刷 墨色的一致 性,尤其是印刷层次版时就更是如此。
15
墨色偏浅可适当增加待测油墨的重量,如在小烧杯中再加入2g待 测油墨,搅拌均匀后再次刮样,如果同标准色样一致,则按(10 +2)∶100=10∶x计算,即可推出x=100×10÷12=83.3 (g),说明此色墨的着色力仅为标准色墨的83.3%,也可说弱 16.7g。 墨色偏深可适加白色油墨的重量,如果在小烧杯中再加入 10g标准白墨后刮样同标准色卡一致,则按10∶(100+10)= 10∶x推出=110(g),说明待测油墨的着色力是标准油墨的110 %,也可说强10g。 上面的x都代表10g待测油墨中加入一定量白色油墨后符合标 准着色力色卡时白色油墨的重量,也就是说,着色力的强弱是用 白墨的量来衡量的。
塑制品加工中产品颜色不均的原因分析与解决

塑制品加工中产品颜色不均的原因分析与解决造成注塑制品颜色不均的主要原因及解决方法如下:(1)着色剂扩散不良,这种情况往往使浇口附近出现花纹。
(2)塑料或着色剂热稳定性差,要稳定制件的色调,一定要严格固定生产条件,特别是料温、料量和生产周期。
(3)对结晶型塑料,尽量使制件各部分的冷却速度一致,对于壁厚差异大的制件,可用着色剂来掩蔽色差,对于壁厚较均匀的制件要固定好料温和模温。
(4)制件的造型和浇口形式,位置对塑料充填情况有影响,使制件的某些局部产生色差,必要时要进行修改。
注塑制品加工中产品白霜的原因分析与解决有些聚苯乙烯类制件,在脱模时,会在靠近分型面的局部表面发现附着一层薄薄的白霜样物质,大多经抛光后能除去。
这些白霜样物质同样会附在型腔表面,这是由于塑料原料中的易挥发物或可溶性低分子量的添加剂受热后形成气态,从塑料熔体释出,进入型腔后被挤迫到靠近有排气作用的分型面附近,沉淀或结晶出来。
这些白霜状的粉末和晶粒粘附在模面上,不单会刮伤下一个脱模制件,次数多了还将影响模面的光洁度。
不溶性填料和着色剂大多与白霜的出现无关。
白霜的解决方法:加强原料的干燥,降低成型温度,加强模具排气,减少再生料的掺加比例等,在出现白霜时,特别要注意经常清洁模面。
注塑制品加工中产品颜色不均的原因分析与解决造成注塑制品颜色不均的主要原因及解决方法如下:(1)着色剂扩散不良,这种情况往往使浇口附近出现花纹。
(2)塑料或着色剂热稳定性差,要稳定制件的色调,一定要严格固定生产条件,特别是料温、料量和生产周期。
(3)对结晶型塑料,尽量使制件各部分的冷却速度一致,对于壁厚差异大的制件,可用着色剂来掩蔽色差,对于壁厚较均匀的制件要固定好料温和模温。
(4)制件的造型和浇口形式,位置对塑料充填情况有影响,使制件的某些局部产生色差,必要时要进行修改。
塑料制品加工中产品出现熔接痕的原因分析与解决熔接痕熔融塑料在型腔中由于遇到嵌件、孔洞、流速不连贯的区域、充模料流中断的区域而以多股形式汇合时以及发生浇口喷射充模时,因不能完全融合而产生线状的熔接痕。
注塑件色差的原因及解决方法
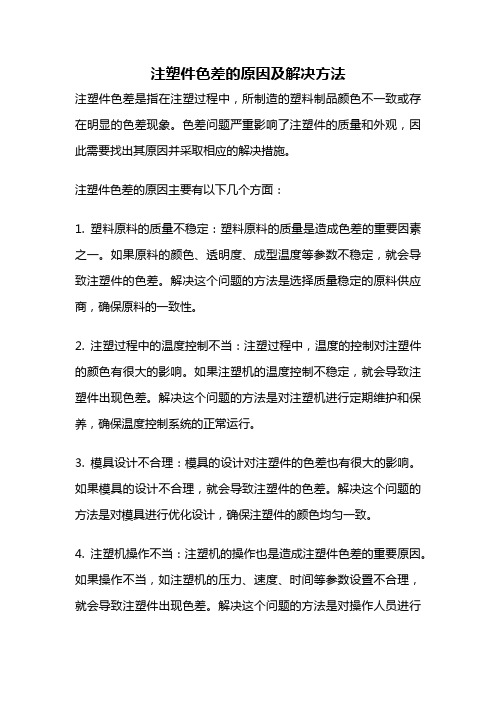
注塑件色差的原因及解决方法注塑件色差是指在注塑过程中,所制造的塑料制品颜色不一致或存在明显的色差现象。
色差问题严重影响了注塑件的质量和外观,因此需要找出其原因并采取相应的解决措施。
注塑件色差的原因主要有以下几个方面:1. 塑料原料的质量不稳定:塑料原料的质量是造成色差的重要因素之一。
如果原料的颜色、透明度、成型温度等参数不稳定,就会导致注塑件的色差。
解决这个问题的方法是选择质量稳定的原料供应商,确保原料的一致性。
2. 注塑过程中的温度控制不当:注塑过程中,温度的控制对注塑件的颜色有很大的影响。
如果注塑机的温度控制不稳定,就会导致注塑件出现色差。
解决这个问题的方法是对注塑机进行定期维护和保养,确保温度控制系统的正常运行。
3. 模具设计不合理:模具的设计对注塑件的色差也有很大的影响。
如果模具的设计不合理,就会导致注塑件的色差。
解决这个问题的方法是对模具进行优化设计,确保注塑件的颜色均匀一致。
4. 注塑机操作不当:注塑机的操作也是造成注塑件色差的重要原因。
如果操作不当,如注塑机的压力、速度、时间等参数设置不合理,就会导致注塑件出现色差。
解决这个问题的方法是对操作人员进行培训,确保他们对注塑机的操作熟练并且合理。
解决注塑件色差问题的方法有以下几点:1. 选择质量稳定的原料供应商:选择质量稳定的原料供应商可以保证原料的一致性,减少色差的发生。
2. 加强对注塑机的维护和保养:定期对注塑机进行维护和保养,确保其温度控制系统的正常运行,减少色差的发生。
3. 优化模具设计:对模具进行优化设计,确保注塑件的颜色均匀一致。
4. 做好注塑机的操作:培训操作人员,确保他们对注塑机的操作熟练并且合理,减少色差的发生。
5. 进行严格的质量控制:建立严格的质量控制体系,对注塑件进行质量检验,及时发现和解决色差问题。
注塑件色差是一个常见的问题,但可以通过选择质量稳定的原料供应商、加强对注塑机的维护和保养、优化模具设计、做好注塑机的操作和进行严格的质量控制来解决。
如何解决塑料凹印的色差问题

——————————————一●l包装印刷、、、.......................,.....~…一….大.印品墨色变浅;压力变小,印品墨色则有变深的倾向。
{三.印版对Fp品墨色一致性的影响——《》——————一——————…—————————~印版质量不好对印品墨色一致性的影响主要表现在以下几个方面。
1。
堵版造成印品墨色不一致堵版是由于某种原因造成网穴堵塞《油墨中的固化物、高黏度物质或者异物等不溶性物质均会堵塞网穴),从而引起油墨转移率降低。
由于油墨转移量减少.印品颜色必将发生变化。
发生堵版时,要用溶剂或专用的清洗剂(使用一般的去污粉容易引发其他故障)清洗印版,同时针对堵版产生的原因采取相应措施。
导致堵版的因素较多,除使用双组分油墨等易发生化学反应的油墨会造成不溶性物质堵塞网穴外.其他因素还有油墨千固于版诬、油墨中混入杂质、制版质量低等。
此外.在印刷过程中,如果油墨中混入水分或其他类型的油墨,也会影响油墨的流动性.造成颜料再凝聚,导致堵版。
另外。
如果印版滚筒上粘附了油污等杂质.也会在印刷中产生与堵版相类似的印刷故障。
所以.在印刷前要对印版进行详细的检查。
2.印版磨损造成印品墨色不一致当印刷批量较大时,印版磨损程度也较大,随着连续印刷持续时间的延长.印刷品墨色就会发生变化,总体趋于变淡(因为网穴变浅.上墨量减少了)。
每经过一定印数的印刷后.都需要重新镀版。
因为经过长时问印刷后,印版表面会有一些磨损,导致网穴变浅.此时虽然可以通过其他工艺调整来保持印刷品颜色稳定.但是过度使用的印版滚筒会失去再镀版的价值,只有重新制版了。
印版在使用过程中还可能发生各种故障或遭到损坏。
由于制作凹印版滚筒时影晌因素很多,重新制版几乎不可能完全重复原来的制版工艺条件,这样,重薪制作的印版滚筒即使在同样的印刷条件下使用.往往也难以达到原来的印刷效果。
为了解决这个问题.在印刷批量较大并且是经常重复印刷的产品时.可以为一套印件同时制作两套印版滚筒甚至多套印版滚筒。
塑料件色差问题处理方案以及标准建

塑料件色差问题处理方案以及标准建【摘要】随着塑料制品在工业、民用领域的广泛应用,其色差问题越来越受到人们的关注。
本文对塑料件色差问题进行分析,总结了造成塑料件色差的主要原因,并提出了相应的处理方案,同时介绍了塑料件色差评价标准和建议制定的标准。
【关键词】塑料件;色差问题;处理方案;评价标准;标准建议一、问题分析随着塑料制品在工业、民用领域的广泛应用,其色差问题越来越受到人们的关注。
在生产过程中,塑料件的色差可能会对产品品质造成影响,甚至会导致产品无法使用。
因此,处理塑料件色差问题非常重要。
造成塑料件色差的主要原因有以下几点:1.原材料不同批次之间的色差;2.注塑工艺参数不同导致的色差;3.模具加工精度不高导致的色差;4.环境温湿度变化引起的色差。
二、处理方案针对以上造成塑料件色差的主要原因,我们可以采取以下措施:1.选择同一批次的原材料,以保证原材料的一致性;2.优化注塑工艺参数,包括模具温度、注塑压力、注塑速度等,以减少色差;3.加强模具加工精度的控制,保证模具的精度达到要求;4.控制生产环境的温湿度,以减少环境温湿度变化对产品色差的影响。
三、评价标准为了对塑料件色差进行评价,我们可以采用以下标准:1.颜色差异度数(△E)的测量值。
△E值越小,表示色差越小。
2.色光学性能分析。
通过分析塑料件的发光性能、透光性能和折射率等参数,评价其色差。
3.视觉评价。
通过人眼对比色差样品与标准色板的颜色差异,评价塑料件的色差。
四、标准建议为了规范塑料件色差的评价和控制,我们可以制定以下标准: 1.塑料件色差评价标准。
制定基于△E值、色光学性能和视觉评价的评价标准。
2.塑料件色差控制标准。
根据塑料件色差评价标准,制定针对不同颜色塑料件的色差控制标准。
3.模具加工精度标准。
制定模具加工精度标准,以保证模具的精度符合要求,从而减少色差的产生。
综上所述,塑料件色差问题是一个非常重要的问题,处理塑料件色差问题需要综合考虑多个方面的因素,并制定相应的处理方案和标准,以保证产品的质量和稳定性。
塑料软包装印刷色差的影响因素39页PPT

6、纪律是自由的第一条件。——黑格 尔 7、纪律是集体的面貌,集体的声音, 集体的 动作, 集体的 表情, 集体的 信念。 ——马 卡连柯
8、我们现在必须完全保持党的纪律, 否则一 切都会 陷入污 泥中。 ——马 克思 9、学校没有纪律便如磨坊没有水。— —夸美 纽斯
10、一个人应该:活泼而守纪律,天 真而不 幼稚, 勇敢而 鲁莽, 倔强而 有原则 ,热情 而不冲 动,乐 观而不 盲目。 —财富 ❖ 丰富你的人生
71、既然我已经踏上这条道路,那么,任何东西都不应妨碍我沿着这条路走下去。——康德 72、家庭成为快乐的种子在外也不致成为障碍物但在旅行之际却是夜间的伴侣。——西塞罗 73、坚持意志伟大的事业需要始终不渝的精神。——伏尔泰 74、路漫漫其修道远,吾将上下而求索。——屈原 75、内外相应,言行相称。——韩非
包装产品专色油墨印刷色差分析

包装产品专色油墨印刷色差分析引言现代包装行业对于产品包装的要求越来越高,色彩在包装设计中扮演着重要的角色。
专色油墨印刷是一种常见的印刷技术,但在实际应用中,由于各种原因,往往会出现色差的问题。
本文将从色差的定义、产生原因、分析方法等方面进行详细讨论。
色差的定义色差是指同样颜色在不同环境下的显示差异。
在包装产品专色油墨印刷中,色差通常指的是印刷品与目标色之间的差异。
色差可以通过人眼来感知,也可以通过仪器来测量。
色差的产生原因包装产品专色油墨印刷色差的产生主要有以下几个方面原因:1. 油墨配方差异不同油墨配方的差异会导致印刷品的颜色有所不同。
不同的油墨配方包含不同的颜料、树脂和添加剂,其光学特性各不相同。
2. 印刷设备参数差异印刷设备的差异也会对印刷色差产生影响。
例如,印刷机的压力调整、墨辊和印版的磨损程度等因素都会对印刷结果产生影响。
3. 印刷基材差异不同的印刷基材也会产生色差。
例如,不同的纸张颜色、材质、光泽度等因素会影响印刷品的色彩呈现。
4. 外界环境因素外界环境因素如光线、湿度、温度等都可能导致印刷色差。
不同的光源会对颜色的感知产生影响,湿度和温度的变化也会导致油墨表面的光学特性发生改变。
色差分析方法在包装产品专色油墨印刷色差分析中,通常采用以下几种方法进行:1. 视觉比较法视觉比较法是最常用的色差分析方法之一。
它通过人眼观察印刷品与目标色之间的差异来判断色差程度。
人眼对颜色的感知是主观的,因此需经过专业的训练来提高判断的准确性。
2. 仪器测量法仪器测量法通过使用色差测量仪器来对印刷品的色差进行精确测量。
常用的仪器有色差计、光谱测量仪等。
这些仪器可以测量印刷品在不同光源下的颜色数值,从而得出色差值。
3. 物理模拟法物理模拟法是一种通过模拟不同的印刷工艺和环境条件来观察色差的方法。
这种方法可以帮助我们理解不同因素对印刷色差的影响程度,并通过调整相应参数来优化印刷结果。
色差分析结果及改进措施在进行色差分析之后,我们可以得到具体的色差数值。
塑胶件常见不良状况及形成原因、改善对策.doc档

9、进料口尺寸过小位置不当
10、塑料中或模具型腔表面有可燃性挥发物
11、水敏性塑料干燥不良水解变黑
12、染色不均有染料里水份
2、调节适当料温及模温
3、减小注塑压力
4、防止模具循环水管漏水,擦干净润滑油,选用适当脱模剂
4、塑料流动性差
5、模具冷却系统不当
6、流程太长,入水口位置不当及尺寸不当,融料受阻
7、胶件盛壁薄,面积大,形状复杂
8、供料不足
9、流道曲折狭窄光洁度
1、压力(射胶枪)
2、增加料温及模温
3、增大压力及加快射胶速度
4、改良模具之冷却系统
5、改良水口位置及尺寸
6、供料要足
7、抛光模具改良光洁度
8、使用适当脱模剂
1、调节顶针伸展速度
2、减小压力
3、适当使用脱模剂
11、缩水:指胶件冷却后变形一般因冷却不够或循环水温不符所致
1、压力小
2、冷却及保压时间不够
3、模温因循环水受阻太高
4、胶位太厚
1、增大压力
2、延长冷却及保压时间
3、检查循环水是否受阻降低模温
4、减胶(在不影响工程结构的前提下)
12、断裂:指胶件因受力不当而引起的拉裂或爆裂现象
1、工模离隙配合不良
2、工模强度或刚性不良
3、模具平行度不良
4、受力不当或未压紧
5、压力太大、锁模力不足、注塑机模板不平行
6、塑料流动性太好、料温或模温高
7、射胶速度太快
8、加料量大
1、使模具配合良好,不得有离隙
2、检验模具强度及刚性是否好
3、检验模具平行度是否良好
4、安装时必需使模具压紧
5、减小压力检查注塑机模板是否平行
注塑产品颜色不匀原因分析
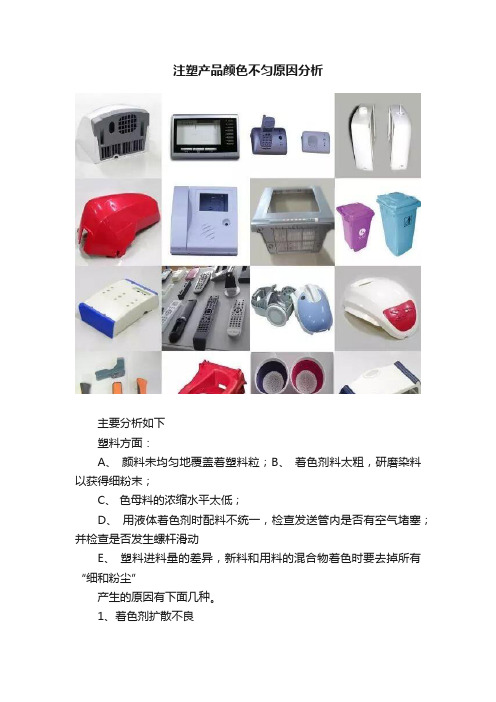
注塑产品颜色不匀原因分析主要分析如下塑料方面:A、颜料未均匀地覆盖着塑料粒;B、着色剂料太粗,研磨染料以获得细粉末;C、色母料的浓缩水平太低;D、用液体着色剂时配料不统一,检查发送管内是否有空气堵塞;并检查是否发生螺杆滑动E、塑料进料量的差异,新料和用料的混合物着色时要去掉所有“细和粉尘”产生的原因有下面几种。
1、着色剂扩散不良滚压着色的干颜料微粒只粘附在塑料颗粒的表面,尤其用柱塞式注射机成型,若注射后颜料并没有均匀地扩散开,则浇口附近出现花纹是不可避免的,干颜料着色难以消除这种缺陷;对于要求外观质量的制件,应使用已着色的颗粒料。
2、热稳定性差引起塑料的着色剂热稳定性较差,受热变色或褪色时,或者塑料本身热稳定性差而变色时,在料筒内局部就已变色或褪色,这都会造成制件颜色不匀。
要稳定制件的色调,一定要严格固定生产条件,特别是料温、料量和生产周期。
降低熔料温度、缩短熔料在料筒内的滞留时间即可防止或消除这种缺陷。
3、由着色剂的性质引起铝箔或颗粒等片状着色剂具有平行于熔料流动方向的性质。
因此,在平坦的熔料流动面上呈现出理想的光泽和色调,而在与着色剂流向不平行的浇口附近、浇口对面、熔合处附近及熔料流动的末端,着色剂流向为任意方向。
因为这样的原因,这些部位的色调与其他部位明显不同。
连采用普通着色剂色差并不明显的熔接痕处,也出现鲜明的色差。
这种现象是着色剂本身性质所造成的,也是无法避免的,即使采用片状以外的其它着色刘,也容易在熔合处产生色差。
多浇口成型时,要消除中间部位的色差大多是困难的(参照熔接痕)。
4、由冷却速度引起结晶性共聚物的结晶度,随着冷却速度而变化。
结晶度越低透明度越好,透明度总要随厚度变化,因此结晶度的差异表现为色差。
因为要消除这种差异极其困难,所以想要掩饰透明度的差异,除了用颗料着色之外没有更好的解决办法。
对结晶型塑料,尽量使制件各部分的冷却速度一致,对于壁厚差异大的制件,可用着色剂来掩蔽色差,对于壁厚较均匀的制件要固定好料温和模温。
塑料软包装印刷色差的影响因素39页PPT

谢谢!
51、 天 下 之 事 常成 于困约 ,而败 于奢靡 。——陆 游 52、 生 命 不 等 于是呼 吸,生 命是活 动。——卢 梭
53、 伟 大 的 事 业,需 要决心 ,能力 ,组织 和责任 感。 ——易 卜 生 54、 唯 书 籍 不 朽。——乔 特
1、不要轻言放弃,否则对不起自己。
2、要冒一次险!整个生命就是一场冒险。走得最远的人,常是愿意 去做,并愿意去冒险的人。“稳妥”之船,从未能从岸边走远。-戴尔.卡耐基。
梦 境
3、人生就像一杯没有加糖的咖啡,喝塑料软包装印刷色差的影响因素 4、守业的最好办法就是不断的发展。 5、当爱不能完美,我宁愿选择无悔,不管来生多么美丽,我不愿失 去今生对你的记忆,我不求天长地久的美景,我只要生生世世的轮 回里有你。
塑料制品颜色变化原因分析及解决方案

塑料制品颜色变化原因分析及解决方案:利用干粉或色母粒等方法着色塑料制品时,可能出现颜色变化现象,从而影响产品质量。
变色可能由下述方面原因引起:(1)高温成型时,基体树脂的氧化降解引起;(2)由于塑料制品的某些组分,如基体与助剂,或基体与着色颜料,亦或助剂与颜料间发生化学反应所致;(3)由于着色颜料或助剂等不耐高温所引起,等等。
我们通过剖析这些因素引起色变之机理,为诸多塑料制品厂家提供参考,以便正确选择原材料,从而生产出合格的塑料制品。
一、塑料成型加工所引起的颜色变化1. 高温成型时,基体树脂氧化降解变色当塑料成型加工设备之加热圈或加热板因失控而一直处于加热状态时,容易导致局部温度过高,使得树脂在高温下发生氧化分解,对于那些热敏性塑料,如PVC等,在成型加工时更易出现这种现象,严重时,将烧焦变黄,甚至变黑,并伴随大量低分子挥发物逸出。
这种降解包括解聚、无规断链、侧基和低分子物的脱除等反应。
1.1 解聚解聚反应系先在大分子未端断裂,,然后按连锁机理迅速脱除单体,在聚合上限温度以上尤其容易进行。
现以聚甲基丙烯酸甲酯与聚甲醛的解聚反应为例,其自由基脱除单体的反应如下:1.2 无规断链(降解)对于诸如PE等聚合物在高温成型时,其主链任何位置都可能断裂,分子量迅速下降,但单体收率很少,这类反应称作无规断链,有时也称作降解,聚乙烯断链后形成的自由基活性很高,四周又有较多的二级氢,易发生链转移反应,几乎无单体产生,其基理如下:不少聚合物热解时同时伴有降解和解聚反应,聚苯乙烯(PS)就是例子。
1.3 取代基的脱除聚氯乙烯、聚醋酸乙烯酯、聚丙烯腈、聚氟乙烯等受热时,取代基将脱除。
以聚氯乙烯(PVC)为例,PVC在180~200℃以下温度加工成型,但在较低的温度(如100~120℃)下,即开始脱氢(HCl),200℃左右失去HCl很快,而使聚合物变成深色,强度变低,总反应简示如下:﹏CH2CHCIH2CHCl~~→~~CH=CHCH=CH~~+2HCl游离HCl对脱氯化氢有催化作用,金属氯化物,如氯化氢与加工设备作用形成的氯化铁,促进催化。
- 1、下载文档前请自行甄别文档内容的完整性,平台不提供额外的编辑、内容补充、找答案等附加服务。
- 2、"仅部分预览"的文档,不可在线预览部分如存在完整性等问题,可反馈申请退款(可完整预览的文档不适用该条件!)。
- 3、如文档侵犯您的权益,请联系客服反馈,我们会尽快为您处理(人工客服工作时间:9:00-18:30)。
塑料封条色差的原因有哪些
色差影响因素众多,涉及原料树脂、色母、色母同原料的混合、注塑工艺、注塑机、模具等,正因为牵涉面广泛,因此色差控制技术同时也是注塑中公认较难掌握技术之一。
1、消除注塑机及模具因素的影响要选择与注塑主品容量相当的封条,如果注塑机存在物料死角等问题,最好更换设备。
对于模具浇注系统、排气槽等造成色差的,可通过相应部分模具的维修模来解决。
必须首先解决好注塑机及模具问题才可以组织生产,以削减问题的复杂性。
塑料封条、钢丝封条、高保封条、施封锁、集装箱封条、铁皮封条、子单封条。
2、消除原料树脂、色母的影响控制原材料是彻底解决色差的关键。
因此,尤其是生产浅色制品时,不能忽视原料树脂的热稳定性不同对制品色泽波动带来的明显影响。
鉴于大多数注塑生产厂家本身并不生产塑料母料或色母,这样,可将注意的焦点放在管理生产和原材料检验上。
即加强原材料入库的检验;生产中同一产品尽可能采用同一塑料封条、尼龙封条、钢丝封条、高保封条、施封锁、集装箱封条、封条厂家、铁皮封条、子单封条厂家、同一牌号母料、色母生产;对于色母,我们在批量生产前要进行抽检试色,既要同上次校对,又要在本次中比较,如果颜色相差不大,可认为合格,如同批次色母有轻微色差,可将色母重新混合后再使用,以减少色母本身混合不均造成的色差。
同时,我们还需重点检验原料树脂、色母的热稳定性,对于热稳定性不佳的,我们建议塑料封条、尼龙封条、钢丝封条、高保封条、施封锁、集装箱封条、封条厂家、铁皮封条、子单封条厂家进行调换。
3、消除色母同母料混合不均的影响塑料母料同色母混和不好也会使产品颜色变化无常。
将母料及色母机械混合均匀后,通过下吸料送入料斗时,因静电作用,色母同母料分离,易吸附于料斗壁,这势必造成注塑周期中色母量的改变,从而产生色差。
对此种情况可采取原料吸入料斗后再加以人工搅拌的方法解决。
现在有很多公司采用喂料机来加入色母,这样节省了大量人力,并且为色差控制提供了很大的帮助,但不少公司因使用不当,结果往往难以令人满意。
固定转速下喂料机加入色母的多少取决于塑化时间,而塑化时间本身是波动的,有时波动甚至还比较大,因此要保证恒定的加料量,需将喂料机加料时间加以固定,且设定时间小于最小塑化时间。
在使用喂料机时需注意,因喂料塑料封条、钢丝封条、高保封、施封锁、集装箱封条、子单封条机较小,使用一段时间后,可能会因为喂料机螺杆中积存的原料粉粒造成下料不准,甚至造成喂料机停转,因此需定期清理。
4、减少料筒温度对色差的影响生产中常常会遇到因某个加热圈损坏失效或是加热控制部分失控长烧造成料筒温度剧烈变化从而产生色差。
这类原因产生的色差很容易判定,一般加热圈损坏失效产生色差的同时会伴随着塑化不均现象,而加热控制部分失控长烧常伴随着产品气斑、严重变色甚至焦化现象。
因此生产中需经常检查加热部分,发现加热部分损坏或失控时及时更换维修,以减少这类色差产生几率。
5、减少注塑工艺调整时的影响非色差原因需调整注塑工艺参数时,尽可能不改变注塑温度、背压、注塑周期及色母加入量,调整同时还需观察工艺参数改变对色泽的影响,如发现色差应及时调整。
尽可能避免使用高注射速度、高背压等引起强剪切作用的注塑工艺,塑料封条、尼龙封条、高保封条、钢丝封条、集装箱封条、封条厂家、子单封条防止因局部过热或热分解等因素造成的色差。
严格控制料筒各加热段温度,特别是喷嘴和紧靠喷嘴的加热部分。
6、掌握料筒温度、色母量对产品颜色变化的影响在进行色差调整前还必须知道产品颜色随温度、塑料封条、
尼龙封条、钢丝封条、高保封条、施封锁、封条厂家、子单封条色母量变化的趋势。
不同色母随生产的温度或色母量的改变,其产品颜色变化规律是不同的。
可通过试色过程来确定其变化规律。
除非已知道这种色母颜色的变化规律,否则不可能很快地调好色差,尤其是在采用新色母生产的调色时。