新型分级进给机构解决深孔加工
机械加工过程中的深孔加工技术分析

机械 - r . 过程中的深孔加工技术分析
粱 俊
( 合肥 力威 汽车油泵有 限公 司,安徽合肥
2 3 0 0 4 1 )
摘 要 : 机械加 工行 业是保 证我 国工业化进程顺利 实施 的关键 。随着机械加 工业的发展 ,其各项工 艺技 术也得 到 了快速的 演 变。同时,在机械k _ T - 过程 中,深孔加 工技 术是 整个机械加 工的关键 所在。下面,就一起跟随本 文对机械加 工过程 中的深孔 加 工技术进行一个 简单的分析与探讨 。
关键词 : 机械加工 ; 深 孔加 工 ; 技 术 中图分类号 : T U7 文献标识码 : A
文章编号 : 1 6 7 1 . 5 5 8 6( 2 0 1 5 )1 0 . 0 0 0 8 - 0 1
在机械加 工过程 中,深孔加工是一项十分复杂的工序 ,同 交错齿 内排 削深 孔加 工技 术是 目前 应用较为 广泛 的一种深 它主要应用于钢件 的深孔加工技术 中。一般来说 , 时也是出现问题较 多的一道工序 。因此,为保证机械加 工过程 孔加工技术 , 中的各项工序顺 利实施,就必须要对深 孔加工技术进 行优 化, 在钢件上进行深孔加工远 比在 铸件 上进 行加 工要难得 多,所产 这也是 目前机械加工行业所最为重要的任务之一。 生 的铁屑也较多 。因此,必须采用像交错齿钻具这种 刀片排列 1什么是深孔 加工技术 顺序为错开式的刀具 。由于交错齿钻具的刀片的特殊 构造 ,从 所谓 的深孔 加工主 要是指在 机械 加工过程 中孔 的长度 与 而可 以使切 削通过 刀具 的两个 孔排入 到刀具 自身 的空心 刀杆 孔 的直径之 比大于 1 O 的孔。深 孔加 工技术在我 国的起步较早 , 中,切 削再 由空心刀杆 中排 出,从而实现 了排 出切削 的整个过 目前 各项技 术均 已相对较为 成熟 。 目前就 一般机械加 工企 业 程 。另外 ,刀片是在刀具 的两侧 内呈交错排列方式 的,这种排 来看 ,深孔加工时深孔与直径 的比值一般为 L / d 1 0 0 。例如 : 列方式可 以起着很好 的分屑作用 ,同时还能够使钻具两侧刀片 油箱孔、各种轴的轴向孔、空心主轴孔等 。 的受力度里平衡状态 ,即不会对刀片造成损害 ,又保证 了钻孔 2 深子 L 加工技术 的难点 的直线 性。另外 ,在 刀片 前加 工断屑槽 ,就会使钻孔 的切 削形 深孔加工 中由于对质量及其他方面 的要求均较高 ,因此在 成一种小 c形 的状态 ,从 而保证 了钻具 在高压 切削状 态下切 技术加工上有着诸多的难点 : 首先,由于机械加工过程 中深孔 削分较 容易被冲 走排 向外面 。同时,由于刀 具的钻 头沿径 向上 加工时速度不能太快 ,因此一般作业 效率均不高 ,其次在深孔 的切削在各 点的速度均不 同,例如 : 钻孔外 围部分的切削速度 加工时工作人员无法观察到设备切削时的情况 ,而 只能通过设 相 对较快,因此可采用耐磨性能较强 的 YT类硬材质 的合 金材 备切割 时所发 出的声音来判断深孔加工是否达 到一 定的标准要 料。而靠近刀具钻头中心的切 削速度 由较慢,在切削相互挤压 求 ,这种方 式在一定程度上是很容易出现误差 的。再次 ,一般 的过程 中刀片容 易受到损伤 ,因此必须采用 Y A类 型的硬质合 而 言,深孔加工 的长径距离是较大的,因此用 于切 削深孔 的刀 金 。 具等设备就相对较长较细 。但 由于刀具较长较 细的特 点,导致 另外 ,在深 孔加 工时 ,如果深 孔 的直径 大 于 6 . 5 厘 米 时, 钻 具 自身的钢性 强度较差 ,同时 由于该设备刀具刃 口偏差等 问 则可采用机械夹固式不重磨深孔加工技术,它的结构与施工方 题 ,从而在 工作 时产生较大 的振动 ,很容易在作业过程 中使钻 式与交错齿深孔加工技术基本相 同。它在作业时刀片 的内部会 孔因受到的振动较大等原 因而发生偏离设计的现象。针对这 一 出现一个阶 台,并用螺丝固定在刀头部分 ,以上刀片做为断屑 点难点 , 就必须要求工作人员在深孔加工时, 首先要 间断切削 , 板 ,并将导 向板作为半 圆形状 ,从而使导 向块与孔壁形成一个 并且要 同时不断提升 刀具 ,要具备较强的判断力来对深 孔加 工 很好 的接触点 。而后再采用 4 0 C的金属制成 的钻头体将空心钻 中切削的长度及 形状进行判断 。最后 ,一般在深孔加工时会 产 杆 与 其 连 接 在 一 起 。 生较大 的热量,而这些热量受一些 因素 的影响无法在深孔加工 3 . 3喷 吸钻深子 L 加工技术 过程 中快速释放 出来, 再加之深孔加工钻具排削条件较为恶劣 。 使用该方法进行深孔加工时 ,必须要 同时配备 一套相应 的 因此在深孔加工 中必须采用冷 却法对刀具设备进行冷却, 以保 设备 ,并将管夹头 安装于车床板 的夹具 中,同时利用大拖板 的 证深孔加工质量的有效性 。深孔加工 中一定要有较好的钻具冷 自动进给使物件钻 出深度 ,另外 ,为 了防止钻 头刚钻人 工件 时 却方法 以及 良好的排削系统,因此 目前机械加工企业均采用 内 发生扭 断,要在工件前 安装一个 导向设备 ,从而使 喷吸钻 的高 排 削深钻孔机械来对大直径深孔进行加工 。 压深孔钻工作时获得一个很好的结果。 3机械加工过程 中深F U J O 工技术 例如 : 在使用 喷吸式刀 具和高压式 刀具进行深 孔加工 时, 3 . 1单刀深孔钻加工技术 切削 的液 流量需在达 到每分钟 1 5 0 L以上 ,压力 要控制在每 立 所谓 的单刀钻具的主要特 点在于它 的刀片和导 向的部位均 方厘米 3 5 公斤 以上。在这 种大流 量和压 力下 ,传 统的车床 冷 是采用材质较为坚硬的金属合 金材料构成 ,并且单刀 的刀尖部 却系统是无法满足大热量冷却需求的 ,因此必须同时配备一系 分偏离整个钻具 的中心点约 3 毫米的距离,从而使刀具在深孔 列大流量 的冷却系统支持 ,从而达到喷吸刀具 比高压刀具 内所 加 工切 削过程 中形成 了一种定心尖状态 ,因此该钻具可 以在切 排 出的切 削液压力低 的 目的 。这种方法下 的冷却系统 的功率消 削过程 中分担一部分 的径 向切割力。另 外,单刀深钻孔钻具 的 耗及钻具 的损害程度都会降低 ,因此在深孔加工时 ,要尽时 多 主 削刀在工作 中形成一种阶台型的结构 ,从而 能够很好地起到 采用喷吸式刀具进行深孔加工 。 分 削的 目的,因此在操作过程 中可以根据深孔直径 的大小要求 4 结语 来设置 单刀的使用数量 ,以此来保证排削的有效性。 综上所述 ,机械加 工过程 中深孔加工 技术 直接 关系着整个 另外,在深孔加工整个过程中 ,单刀钻 具中各刀削部分的 机械加工 的质 量,因此 ,在深孔加工 中必须针对 不同的深孔加 应 面与被加 工的深孔之 间形成一种错开的孔径距 离,从而防范 工要 求采 用不 同的加工技术措施 ,最大限度保 证深 孔加工的质 了刀具在加 工过程 中对深孔表面可能会造成的损伤。 同时,单 量 安 全 。 刀刀具 的导 向部分 的尺 寸距离 要 比单 刀尖部 的直径 尺寸距 离 参考文献 小0 . 1 毫米 ,以防止刀具钻孔时出现偏 离直线距 离的状况 发生。 [ 1 ] 王峻 . 现代深 孔加工技 术 [ M] . 哈尔滨 : 哈 尔滨工 业大学 出 最后,在使用单 刀刀 具进行深孔加工时 ,该刀具导 向垫 的倒角 版社 ,2 0 0 5 . 角度应 设计为 1 8 度 角,这种角 度更有利 于将物件 切 削排 除 出 【 2 】 邓文英 . 机械加 工过程 中深孔加工技术探讨 [ J ] . 2 0 1 3( 0 8 ) : 去。 目前该种 刀具深孔加工方法广泛应用于种类实心 的铸件油 1 4 . 1 5 . 箱上,并在 其中起着较好 的应 用效 果。 [ 3 】 李伟光 . 机械 制造 中深孔加工技术 【 J 】 . 机械 工业论坛 ,2 0 1 4 3 . 2交错齿内排 削深 孔加工技术 ( 】 7) .
组合机床深孔钻分级进给机构的改进.

组合机床深孔钻分级进给机构的改进
日期: 2011-10-26 19:10:15 浏览: 0 来源: 学海网收集整理作者: 佚名
摘要:对深孔钻削组合机床分级进给机构提出改进方案。
简化了结构,减少了故障率,并方便调整。
关键词:深孔钻削组合机床分级进给控制系统改进
拖拉机内燃机的不少零件如:曲轴、连杆、缸体等都有深孔配置。
由于深孔钻头工作条件恶劣,散热困难,切削力大,切削不易排出,冷却液很难到达切削部位,加之细长钻头的强度、刚变的严重不足,使深孔钻削加工成为关键工序。
目前,国内多用具有分级进给的机床钻削深孔,我公司在拖拉机、内燃机生产线上也配备了不少用了分级进给机构的组合机床。
组合机床上的分级进给机构主要有两种型式,每种型式无论从结构、调整方法和可靠性等诸多方面,都存在不尽人意的地方。
我们根据多年组合机床电气系统的设计和生产经验,对这两种分级进给机构进行改进。
实践证明,改进后的机构具有结构简单,调整方便,可靠性高等优点。
......。
深孔加工的几种方法

深孔加工的几种方法深孔加工是一种用于加工深孔孔径大、长径比高的工件的专业加工方法。
在工业制造中,深孔加工广泛应用于航空航天、汽车、模具、电子等领域。
下面是关于深孔加工的十种常见方法,并对每种方法进行详细描述。
1. 长钻杆深孔加工(Gun drilling)长钻杆深孔加工是最常见的深孔加工方法之一。
它使用带有镶有硬质合金刀片的长钻杆进行加工。
钻杆被安装在特殊的深孔钻床上,通过旋转和进给,将刀片带动至工件内部进行加工。
该方法适用于孔径较小、长径比较高的工件。
2. 刀具旋转切削深孔加工(Boring)刀具旋转切削深孔加工是使用铰孔刀或车刀进行加工的方法。
刀具通过旋转,将材料从工件中间逐渐取出,形成深孔。
由于切削力较大,工件需要具备较好的稳定性,并配备适当的刀具冷却和切屑排出系统。
3. 杆料直插深孔加工(Trepanning)杆料直插深孔加工是一种适用于大孔径深孔加工的方法。
在该方法中,一个圆柱形工具的中心用于插入工件,通过旋转工件和工具,将材料从工件中间逐渐取出,形成深孔。
该方法适用于孔径较大、长径比较高的工件。
4. 进给滚压深孔加工(Skiving)进给滚压深孔加工是一种高效的深孔加工方法。
在该方法中,刀具会逐渐滚动进入工件,并通过旋转和进给来形成深孔。
与切削加工相比,滚压加工具有更高的切削速度和更少的切削力,可以减少加工产生的热量和变形。
5. 穿切切削深孔加工(Reaming)穿切切削深孔加工是一种通过旋转和进给来加工深孔的方法。
与其他深孔加工方法相比,穿切切削深孔加工具有更高的切削速度和更少的切削力。
该方法适用于孔径较小、长径比较高的工件。
6. 穿孔切削深孔加工(Counterboring)穿孔切削深孔加工是一种在工件的底部形成平坦的底座的方法。
通过旋转和进给,切削刀具穿过工件,形成孔径较大的底孔。
该方法广泛应用于需要准确定位或加工底孔的工件。
7. 表面喷涂深孔加工(DLC Coating)表面喷涂深孔加工是一种在工件表面喷涂高硬度的钻石碳涂层的方法。
普通车工中级工技能鉴定试题 一、 判断题:(每题1分, …
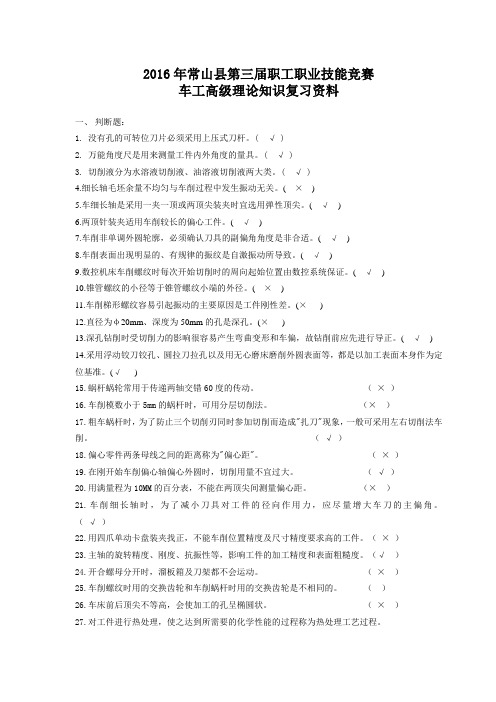
2016年常山县第三届职工职业技能竞赛车工高级理论知识复习资料一、判断题:1. 没有孔的可转位刀片必须采用上压式刀杆。
( √ )2. 万能角度尺是用来测量工件内外角度的量具。
( √ )3. 切削液分为水溶液切削液、油溶液切削液两大类。
( √ )4.细长轴毛坯余量不均匀与车削过程中发生振动无关。
( ×)5.车细长轴是采用一夹一顶或两顶尖装夹时宜选用弹性顶尖。
( √)6.两顶针装夹适用车削较长的偏心工件。
( √)7.车削非单调外圆轮廓,必须确认刀具的副偏角角度是非合适。
( √)8.车削表面出现明显的、有规律的振纹是自激振动所导致。
( √)9.数控机床车削螺纹时每次开始切削时的周向起始位置由数控系统保证。
( √)10.锥管螺纹的小径等于锥管螺纹小端的外径。
( ×)11.车削梯形螺纹容易引起振动的主要原因是工件刚性差。
(×)12.直径为φ20mm、深度为50mm的孔是深孔。
(×)13.深孔钻削时受切削力的影响很容易产生弯曲变形和车偏,故钻削前应先进行导正。
( √)14.采用浮动铰刀铰孔、圆拉刀拉孔以及用无心磨床磨削外圆表面等,都是以加工表面本身作为定位基准。
(√)15.蜗杆蜗轮常用于传递两轴交错60度的传动。
(×)16.车削模数小于5mm的蜗杆时,可用分层切削法。
(×)17.粗车蜗杆时,为了防止三个切削刃同时参加切削而造成"扎刀"现象,一般可采用左右切削法车削。
(√)18.偏心零件两条母线之间的距离称为"偏心距"。
(×)19.在刚开始车削偏心轴偏心外圆时,切削用量不宜过大。
(√)20.用满量程为10MM的百分表,不能在两顶尖间测量偏心距。
(×)21.车削细长轴时,为了减小刀具对工件的径向作用力,应尽量增大车刀的主偏角。
(√)22.用四爪单动卡盘装夹找正,不能车削位置精度及尺寸精度要求高的工件。
FANUC系统(加工中心)的11种孔加工固定循环指令

FANUC系统(加工中心)的11种孔加工固定循环指令”FANUC系统共有11种孔加工固定循环指令,下面对其中的部分指令加以介绍。
1)钻孔循环指令G81G81钻孔加工循环指令格式为:G81G△△X__Y__Z__R__F__X,Y为孔的位置、Z为孔的深度,F为进给速度(mm/min),R为参考平面的高度。
G△△可以是G98和G99,G98和G99两个模态指令控制孔加工循环结束后刀具是返回初始平面还是参考平面;G98返回初始平面,为缺省方式;G99返回参考平面。
编程时可以采用绝对坐标G90和相对坐标G91编程,建议尽量采用绝对坐标编程。
其动作过程如下(1)钻头快速定位到孔加工循环起始点B(X,Y);(2)钻头沿Z方向快速运动到参考平面R;(3)钻孔加工;(4)钻头快速退回到参考平面R或快速退回到初始平面B。
该指令一般用于加工孔深小于5倍直径的孔。
编程实例:如图a所示零件,要求用G81加工所有的孔,其数控加工程序如下:图a图bN02T01M06;选用T01号刀具(Φ10钻头)N04G90S1000M03;启动主轴正转1000r/minN06G00X0.Y0.Z30.M08;N08G81G99X10.Y10.Z-15.R5F20;在(10,10)位置钻孔,孔的深度为15mm,参考平面高度为5mm,钻孔加工循环结束返回参考平面N10X50;在(50,10)位置钻孔(G81为模态指令,直到G80取消为止) N12Y30;在(50,30)位置钻孔N14X10;在(10,30)位置钻孔N16G80;取消钻孔循环N18G00Z30N20M302)钻孔循环指令G82G82钻孔加工循环指令格式为:G82G△△X__Y__Z__R__P__F__在指令中P为钻头在孔底的暂停时间,单位为ms(毫秒),其余各参数的意义同G81。
该指令在孔底加进给暂停动作,即当钻头加工到孔底位置时,刀具不作进给运动,并保持旋转状态,使孔底更光滑。
深孔加工——精选推荐
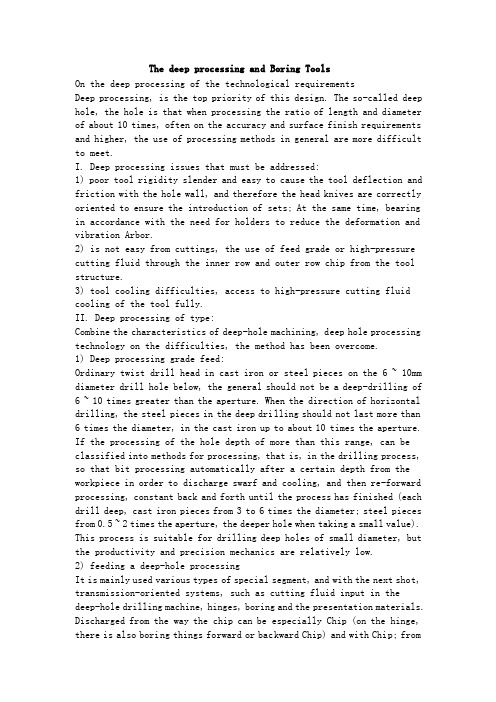
The deep processing and Boring ToolsOn the deep processing of the technological requirementsDeep processing, is the top priority of this design. The so-called deep hole, the hole is that when processing the ratio of length and diameter of about 10 times, often on the accuracy and surface finish requirements and higher, the use of processing methods in general are more difficult to meet.I. Deep processing issues that must be addressed:1) poor tool rigidity slender and easy to cause the tool deflection and friction with the hole wall, and therefore the head knives are correctly oriented to ensure the introduction of sets; At the same time, bearing in accordance with the need for holders to reduce the deformation and vibration Arbor.2) is not easy from cuttings, the use of feed grade or high-pressure cutting fluid through the inner row and outer row chip from the tool structure.3) tool cooling difficulties, access to high-pressure cutting fluid cooling of the tool fully.II. Deep processing of type:Combine the characteristics of deep-hole machining, deep hole processing technology on the difficulties, the method has been overcome.1) Deep processing grade feed:Ordinary twist drill head in cast iron or steel pieces on the 6 ~ 10mm diameter drill hole below, the general should not be a deep-drilling of 6 ~ 10 times greater than the aperture. When the direction of horizontal drilling, the steel pieces in the deep drilling should not last more than 6 times the diameter, in the cast iron up to about 10 times the aperture. If the processing of the hole depth of more than this range, can be classified into methods for processing, that is, in the drilling process, so that bit processing automatically after a certain depth from the workpiece in order to discharge swarf and cooling, and then re-forward processing, constant back and forth until the process has finished (each drill deep, cast iron pieces from 3 to 6 times the diameter; steel pieces from 0.5 ~ 2 times the aperture, the deeper hole when taking a small value). This process is suitable for drilling deep holes of small diameter, but the productivity and precision mechanics are relatively low.2) feeding a deep-hole processingIt is mainly used various types of special segment, and with the next shot, transmission-oriented systems, such as cutting fluid input in thedeep-hole drilling machine, hinges, boring and the presentation materials. Discharged from the way the chip can be especially Chip (on the hinge, there is also boring things forward or backward Chip) and with Chip; froma number of cutting edge, can be divided into single-blade, double-edged and multi-blade, cutting edge can be high-speed steel or carbide. Cutter head have a different number of block-oriented support in theprocess-oriented role play to ensure flatness of the hole, but also from the role of squeezed light to improve the processing of the surface finish hole.Chip has a deep-hole drilling in a single tube and dual tube Chip Chip (ie, jet drilling). Chip fear of double tube drill pipe than Chip Chip fear deep-hole drilling and drilling outside the processing efficiency and higher accuracy. The deep hole on the barrier is expected to set at the completion of unloading Nesting Nesting knife, cut off the mandrel fitted with a knife and the knife folder to make it against the mandrel, the feed through a dedicated device to cut off, cut to the core diameter rod 4 / 5 ~ 5 / 6 will be back to cut off the knife, a little outside the mandrel to break out.In general, the use of inside than outside the Chip Chip processing large diameter, obtained by processing high precision and surface finish. III. The main points of deep-hole processingMachine tools and processing of the previous process, and attention should check the following:1) axis-oriented tool sets, Bar sets of bearings, such as the centerline of the workpiece support different sets of axis degrees should meet the requirement.2) check whether the system is cutting fluid flow and normal work is a multi-edge special deep-hole drilling with Chip (jet drilling suction) of the spray suction effect, in particular, should seriously check.3) the workpiece should be the upper end of the processing center hole, and to avoid drilling in the slope.4) Does the shape of a normal chip. With the workpiece material, tool geometry, cutting parameters and so on. The two separated by a certain direction of each curl inward cutting the best shape to avoid the formation of the ribbon cuttings straight.5) The higher the speed of processing through-hole, when the drill bit is about to pass, it is best to stop or deceleration to prevent damage to the bit and the exit.6) should be avoided in the processing of parking, such as the need to stop, they should first stop into the tool and return to some distance, and then stop the pump and the rotation of the main campaign to prevent the tool in the hole a "killed" phenomenon.Productivity increases through advancements in boring tool designs. Boring tools are often regarded as the best method for producing accurateholes in parts of every size and configuration. A steady stream of productivity increases have come about through advancements in the design of boring tools.Four newer developments include:■ digital readout displays in precisio n boring heads;■ aluminum construction;■ combination boring tools; and■ self-balancing tools.Digital Readout DisplaysCNC and coordinate measuring machines that utilize digital displays have been around since the beginning of NC technology. And, micrometers and vernier calipers with electronic digital displays are commonplace.Adapting electronic display technology to precision boring has been slower because of the coolant and the high rotational speeds used when boring.Coolant has a way of getting into any tool used on a machining center, so extreme care must be taken to prevent it from entering any electronic device.With newer designs, throughcoolant tools are possible. The coolant is directed through internal passages that are completely isolated from the digital display. The exterior of the tool is also sealed to keep coolant from contacting the electronics.High rotational speeds, centrifugal loads and any inherent unbalance can cause vibration severe enough to damage sensitive digital displays. High rotational speeds are achievable by using an internal balancing feature that reduces or eliminates this potentially harmful vibration. Precision boring heads are available with digital displays that can handle speeds up to 16,000 rpm.The digital display of the boring head shows the movement of the boring tool slide, rather than the rotation of a lead screw. Because the boring bar is mounted in the tool slide, the digital readings are a true measurement of tool movement. The digital display gives a true backlash-free reading. This feature enables quicker and more accurate diameter changes and allows for deflection or tool wear compensation.Most boring tool settings are determined with the cut-and-measure process.This involves boring a small portion of the hole being produced, then gaging it. Frequently, this means the boring tool is removed from the machine and put on a tool presetter in order to make the small corrections necessary to obtain the proper hole size.The process is required because the vernier dials commonly seen on boring heads can be difficult to read and set on the machine. However, the process introduces the possibility of boring oversize holes and scrapping the part.Because of unpredictable tool-point deflection in the machine setup, the cut-and-measure process is required. However, with an easy-to-read digital display, small diameter changes are possible right on the machine. Diameter changes of 0.0001" can be made with the tool in the machine spindle. If the tool must be removed from the machine to change diameter settings because of spindle access restrictions, the digital display makes this a quick and precise task.Aluminum ConstructionAluminum’s relatively light weight makes it a common material for to ol bodies. Weight reduction is critical with today’s higher-speed, and sometimes lighter, CNC machines.Most of these machines’ toolchangers have weight limits. By using aluminum construction, boring tools can be produced that stay under these weight limits while still being able to bore holes from 4" in diameter on up. (Generally, tools smaller than 4" in diameter, whether made of aluminum or steel, meet toolchanger weight limits.) The reduced weight lessens spindle deflection, which results in more accurate bores. Thereis also less wear and tear on the machine spindle itself.There is a considerable productivity gain if the need for loading large, heavy boring tools into the machine by hand or with the aid of an overhead crane is eliminated. For example, one shop in Kansas replaced a 14"-dia. steel boring tool that weighed approximately 40 lbs. with an aluminum tool that weighed less than 25 lbs. The customer went from manual loading witha jib crane to using his automatic toolchanger.Setting a boring tool with a digital display can be performed withoutremoving the tool from the machine.关于深孔加工的工艺要求深孔加工,是本设计的重中之重。
高精度深长孔加工方法

学院: 机械工程学院专业班级: 学号: 姓名:高精度深长孔的精密加工一、历史背景枪钻与内排屑深孔钻两种加工孔的刀具分别出现于20世纪30年代初和40年代初的欧洲兵工厂,这并非历史的偶然。
其主要历史背景是:一次世界大战(1914〜1918年)首次使战争扩大到世界规模。
帝国主义列强为瓜分殖民地而需要大量现代化的枪炮(特别是枪械和小口径火炮的需求量极大)。
而继续使用传统的扁钻、麻花钻、单刃炮钻,已经完全不能满足大量生产新式武器的要求,迫切需要进行根本性的技术更新。
于是高精度深长孔的制造就成为了一个摆在制造者面前的一个首要问题,并且一直延续到了现今。
第一次世界大战中的火炮二、传统加工工艺及存在的问题在现代机械加工中,也经常会遇到一些深孔的加工,例如长径比(L/D)≥10,精度要求高,内孔粗糙度一般为Ra0.4~0.8的典型深孔零件,过去我们采用的传统工艺路线一般是:钻孔(加长标准麻花钻)→扩孔(双刃镗扩孔刀)→铰孔(标准六刃铰刀)→研磨此工艺虽可达到精度要求,但也存在诸多缺点,特别是在最初工序采用加长麻花钻钻孔时,切削刃越靠近中心,前脚就越大。
若钻头刚性差,则震动更大,表面形状误差难以控制,加工后孔的直线度误差,钻头易产生不均匀的磨损等现象,生产效率和产品合格率低,而且研磨抛光时,工作环境比较脏,由于钻孔工序的缺点,而带来的影响难以在后面的工序中克服,形状误差不能得以修正,因此加工质量差。
传统深孔的加工流程三、工艺路线与刀具的改进本着提高生产效率提高产品合格率的原则,结合深孔加工的一些特性,对加工工艺及刀具进行了改进,改进后的工艺路线是:钻孔(BTA钻)→扩孔(BTA扩)→铰孔(单刃铰刀)→研磨1、钻孔与扩孔刀具及工艺的改进单管内排屑深孔钻的由来单管内排屑深孔钻产生于枪钻之后。
其历史背景是:枪钻的发明,使小深孔加工中自动冷却润滑排屑和自导向问题获得了满意的解决,但由于存在钻头与钻杆难于快速拆装更换和钻杆刚性不足、进给量受到严格限制等先天缺陷,而不适用于较大直径深孔的加工。
深孔加工技术
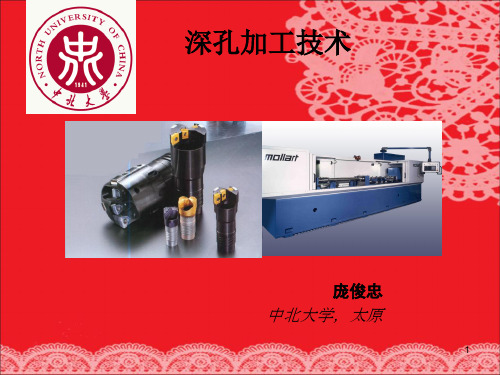
图12 套料加工
25
u 内排屑深孔机床
2.3.2 BTA钻深孔机床
作为BTA深孔刀具和深孔加工技术的载体----BTA钻深孔机床,随着 刀具材料及控制技术的发展,同样向着高速、高效、多功能、精密、环 保的方向发展。
BTA钻深孔机床主要以卧式形式较多,由于钻孔大而长,所以显得这 类机床身长个大,其运动配置有工件旋转,刀具进给;工件旋转,刀具 进给并旋转;工件进给,刀具旋转;工件固定,刀具旋转并进给。
5
二、深孔加工系统
2.1 分类 深孔加工系统通常以深孔加工中所用的冷却、排
屑装置来分类的。可分为枪钻系统、BTA系统、喷吸 钻系统和DF系统。下面分别就上述系统作一介绍: 2.2 枪钻系统及其配置 枪钻系统属于外排屑方式,其结构如图1所示,主要 由机床、枪钻、中心架、钻套、钻杆联结器和冷却润 滑油路系统组成。其工作原理是:切削液通过尾架上 输油入口进入钻杆内部,到达钻头头部进行冷却润滑 ,并将切除的切屑从钻头外部的V型槽中排出。由于 切屑由钻头和钻杆外部排出,容易擦伤已加工孔表面 ,其加工质量要低于内排屑方式的系统(随后介绍) 。该系统主要用于小直径(一般<20 mm)深孔加工 。
目前,这类机床的主轴转速多在4000-6000RPM。这充分体现了深孔机 床向高速、高效、多功能、高自动化。绿色加工的方向发展。
26
u 内排屑深孔机床
图13 BTA深孔机床
钻削范围:18-65mm(18-100mm) 转速:0-6000RPM 进给速度:0-1000mm/min 快进速度:4m/min
图6 微型深孔枪钻数控机 轴或4轴可选)
床(2
16
u 枪钻机床
钻削范围:6mm - 50mm 转速:0 – 4500RPM 进给速度:0 - 4000mm/min 快进速度:12m/min
关于深孔缺陷的原因与防治措施

选用合适钻头
根据加工需求选择合适类 型和规格的钻头,以减小 钻底应力。
控制钻深
合理控制钻孔深度,避免 因钻头过长或过短导致钻 底应力过大或过小。
调整机床参数
根据实际情况调整机床转 速、进给速度等参数,以 减小钻头在钻底时的振动 和冲击。
孔身缺陷的防治措施
保持钻头锋利
定期检查和修磨钻头,确保其锋利度 和切削性能良好。
关于深孔缺陷的原因与防治 措施
汇报人: 2024-01-01
目录
• 深孔缺陷的种类与特征 • 深孔缺陷产生的原因 • 深孔缺陷的防治措施 • 深孔缺陷的检测与评估 • 深孔缺陷的案例分析 • 未来研究方向与展望
01
深孔缺陷的种类与特征
孔口缺陷
总结词
孔口缺陷通常表现为孔口边缘不整齐 、出现缺口或毛刺,有时还伴有裂纹 。
新型防治措施的开发与推广
总结词
针对深孔缺陷的防治,新型防治措施的 开发和推广是未来的重要研究方向。这 些措施能够有效地减少或避免深孔缺陷 的产生,提高产品质量和可靠性。
VS
详细描述
目前,新型防治措施如改进加工工艺、优 化切削参数、使用新型刀具和材料等正在 被积极研究。这些措施能够显著减少深孔 缺陷的产生,提高深孔加工的质量和效率 。未来,这些措施将进一步得到开发和推 广,为深孔加工行业的发展提供有力支持 。
可能对飞机的性能和安全性造成潜在威胁。
06
未来研究方向与展望
新型检测技术的研究与应用
总结词
随着科技的发展,新型检测技术的研究和应用对于深孔缺陷的检测和预防具有重要意义。这些技术能 够更精确、快速地检测出深孔缺陷,提高产品质量和生产效率。
详细描述
目前,新型检测技术如超声波检测、射线检测、涡流检测等正在被深入研究。这些技术能够检测出微 小的缺陷,甚至在产品制造过程中实时监测,有效避免了产品的不合格率。未来,这些技术将进一步 应用于实际生产中,为深孔缺陷的防治提供有力支持。
航空发动机铝镁机匣深孔如何加工?
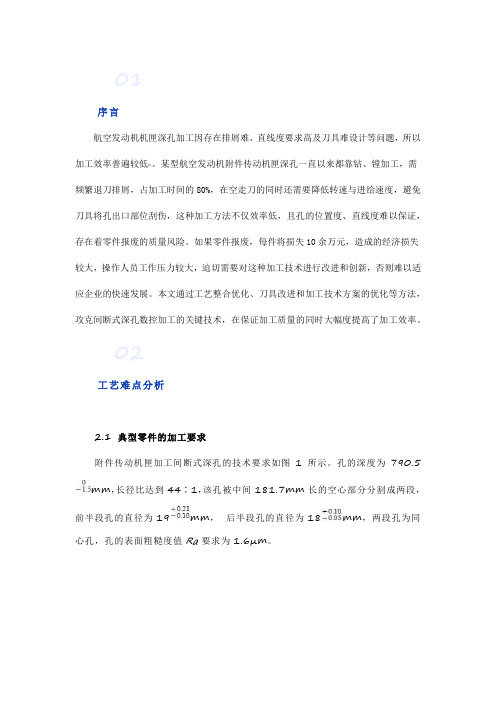
01序言航空发动机机匣深孔加工因存在排屑难、直线度要求高及刀具难设计等问题,所以加工效率普遍较低。
某型航空发动机附件传动机匣深孔一直以来都靠钻、镗加工,需频繁退刀排屑,占加工时间的80%,在空走刀的同时还需要降低转速与进给速度,避免刀具将孔出口部位刮伤,这种加工方法不仅效率低,且孔的位置度、直线度难以保证,存在着零件报废的质量风险。
如果零件报废,每件将损失10余万元,造成的经济损失较大,操作人员工作压力较大,迫切需要对这种加工技术进行改进和创新,否则难以适应企业的快速发展。
本文通过工艺整合优化、刀具改进和加工技术方案的优化等方法,攻克间断式深孔数控加工的关键技术,在保证加工质量的同时大幅度提高了加工效率。
02工艺难点分析2.1 典型零件的加工要求附件传动机匣加工间断式深孔的技术要求如图1所示。
孔的深度为790.5 mm,长径比达到44∶1,该孔被中间181.7mm长的空心部分分割成两段,前半段孔的直径为19mm,后半段孔的直径为18mm,两段孔为同心孔,孔的表面粗糙度值Ra要求为1.6μm。
图1 某机匣间断式深孔技术要求2.2 典型零件的加工难点加工难点具体如下。
1)加工的2个孔为大长径比深孔,加工所需的刀具非常细长、刚性差,排屑困难,加工效率低。
2)间断式深孔加工如图2所示,空心间断处钻头定心困难,易钻偏。
该孔需穿过两处筋板,加工后筋板壁厚仅为2.0~2.5mm,钻孔位置控制不好就会钻穿支板,导致零件报废,属于典型的难加工深孔类型之一。
图2 某机匣间断式深孔加工示意03深孔加工技术3.1 原加工工艺方案深孔加工原工艺方法(见图3)为:φ24mm埋钻(埋平孔的端面)→φ10mm中心钻(钻中心孔)→φ16mm钻头粗加工前半段孔→φ19mm镗刀镗正孔口处做引导→φ 19mm平底埋钻(加工φ19mm孔径部分,同时埋平间断处φ18mm的孔端面)→φ 18mm长钻头慢速加工此深孔→φ18mm埋钻精修φ18mm孔。
数控深孔钻镗床进给机构的设计

数 控 深 孔 钻 镗 床 进 给 机 构 的设 计
展 海 瑜
( 水 星火机 床有 限责任公 司, 肃 天水 7 12 ) 天 甘 404
摘 要 : 绍 了数 控 深孔钻 镗 床 的加工 特点 及进 给传 动机 构 的设计 。新 的进给 传动 机构 传 动平 稳精 确 。 介 加工 精 度高 , 长 了刀具 的使 用寿 命 。 延
此 来保 护 刀具 , 以防过 载损 坏 。
图3绍 的深 孔 钻 镗床 的进 给 传 动 机 构 , 用 滚 采 珠丝杠 进 行驱 动 , 用单 轴数 控 系统进 行控 制 , 利 可实现 对不 同孔 形 的加工 , 如盲 孔 、 阶梯 孔 等 , 传 动 平稳 精 且 确、 深孔 加工精 度 较 高 。 由于 在 不 同 规格 T J 中对 L  ̄z ] 刀具 进 给 的扭 矩 加 以 限制 , 效 保 护 了刀 杆 的安 全 使 有 用 。本 装置 在我公 司深 孔 加 工 机床 上 推 广 使 用后 , 得
深孔 是 指有 大 的深径 比的孔 。深孔 钻 削是 钻BIL t  ̄ -
的进 给传 动系 统是 必 不 可 少 的 , 其传 动 系 统 的精 度 对 深 孔 的加 工质 量及 刀具 的合 理使 用都 至关 重 要 。在 深 孔 加 工设备 中 , 各种 刀 杆 及 刀 具 占有 相 当 大 的投 资 成 本 。一 台深孔 钻镗机 床 在它 的生 命期 限 内所 用之 刀具
到用 户 的一致 认 可 。
参 考 文 献
3 进给传动 的扭矩设计计算
机床 进 给传 动 中 , 大切 削 负 载 不 得 超 过 电动机 最
额定 转 矩 。折 算 到 电 动 机 轴 的 最 大 切 削 负 载 转 矩
看看这种深盲孔加工新方法-精度够高吗?

1 序言高精密深盲孔的加工一直是机加行业的技术难题,本文以某深盲孔零件为研究对象,通过工艺试验,为深盲孔加工提供一种新方法,并进行加工应用。
2 产品特性及加工难点本文介绍的精密深盲孔轴承座为某型号长寿命电动机内重要部件,主要作用是固定内部零件。
电机芯轴转速极高,对轴承座的内孔尺寸、几何公差加工要求较高,其结构如图1所示。
图1 深盲孔轴承座结构该轴承座材料为9Cr18Mo,热处理硬度48~53HRC,为型腔结构,形状规则,壁薄,端面为基准面。
其加工精度和表面质量要求高,难点在于内孔的加工,要求端面与内孔垂直度≤0.002mm,内孔圆度≤0.002mm,内孔直线度≤0.002mm。
盲孔深70mm,退刀槽宽2.6mm。
3 加工工艺及存在问题内孔磨削加工原工艺:以外径为定位支撑,采用电磁无心卡装夹工件→粗磨内孔→靠底面精磨内孔→靠底面研磨内孔。
该工艺加工内孔无法通过常规设备一次加工合格,只能通过后期研磨保证内孔精度要求。
存在加工问题如下。
1)深盲孔磨削时内孔精度检测难度大,检测频繁。
采用常规模拟量规无法对盲孔进行测量;三坐标仪需采用加长测头离线检测,检测效率低;由于内孔精度高,检测时受温度影响较大,不适合工序间的检测。
2)孔深度大,磨削时易产生锥度、尺寸超差。
盲孔较深,采用内圆磨床加工内孔,砂轮轴向移动时易形成砂轮前端比后端损耗大,砂轮接杆受径向切削力弯曲变形等因素影响,使内孔产生锥度,锥度≥0.01,导致尺寸精度、几何公差无法满足要求。
3)内孔精度靠手工研磨保证,产品一致性差,易出现划伤现象。
采用研磨棒对内孔研磨,留研磨量0.02mm;研磨时易出现喇叭口,内孔直线度要求0.002mm,研磨难度较高,需反复研磨、检测;单件研磨时间约2h,研磨成品需恒温4h检测,效率较低且极易出现研磨划伤现象。
4 工艺改进为解决根据原工艺进行内孔加工时存在的问题,需对该轴承座的内孔加工工艺进行优化调整。
4.1 设备选择为满足根据轴承座设计要求中内孔表面粗糙度及几何公差的精度要求,拟采用高速(最高转速20000r/min)五轴加工中心进行加工。
- 1、下载文档前请自行甄别文档内容的完整性,平台不提供额外的编辑、内容补充、找答案等附加服务。
- 2、"仅部分预览"的文档,不可在线预览部分如存在完整性等问题,可反馈申请退款(可完整预览的文档不适用该条件!)。
- 3、如文档侵犯您的权益,请联系客服反馈,我们会尽快为您处理(人工客服工作时间:9:00-18:30)。
相 同定 值 ) 。 4 .滑 台快 速 退 回至分 级进 给 退 离 线 。 台快 速 滑
滑 台快速 向前 , 位开 关 1 限 4和 2被 放开 。 3 .滑 台工 作 进 给 。滑 台快 进 过 程 中 , 滑块 4 大 压下 伸 缩 销 8 同 时压 下 开 关 7和 限 位钩 9 此 时 滑 , , 台转 为工 作进 给 , 台 工 作进 给 3 米 后 ( 长度 即 滑 毫 此 为 工 作进 给 缓进 值 , 亦即 切 入量 。 值 大 小可 根 据需 此
5 .滑 台再 一次 工 作进 给 。 当滑 台再 一次 快 速 向
下 限位 开 关 1 , 由于 滑 台 在 滑 座 死 挡 铁 上 停 留 , 2且
故 压 力 继 电器 亦 相 继 起 作 用 , 合 发 出滑 台快 速 退 联 回讯 号 ( 图 2 ) 见 e 。此 时 无 论 小 滑块 5上 的挡 铁 6 是 否 已压 上开 关 l , 台均 快速 退 回至 原位 停 止 。 l滑 8 .当 滑 台 工 作 进 给 至 终 点 , 铁 1 挡 9压 下 开 关
退 回一段 距 离 ( 一般 是 钻 头退 离 工 件表 面 , 此距 离可
借 助调 整 挡铁 1 8的位 置 而改 变 ) , 后 挡铁 1 8压 下 限
位开关 1 5时 , 发 出 滑 台再 一 次 快 速 向前 的 讯 号 。 便
大 滑 块 4和 小 滑 块 5均 随 滑 台后 退 , 退 回过 程 中 在
’
口 捣司
熏
图 1
●—昌■—__-- _————_ — 昌置 .
-
所 加 工 的 孔 深 15 8 mm, 径 8 普 通钻 床 无 法 直 , 满足加 工要求 , 常 规的解决 方法是 用深孔钻 , 而 这 样 , 备投 资 大 , 键 是提 高 了使 用 成 本 。 设 关 1 .深 孔 钻 头 为 中空 ( 为需 要 从钻 头 心部 冲 出 因
原理图 :
其全 部 工 作过 程 为 :
{ f
l
f
●
I {
_ I f I 1 f _
{
1 .滑 台停 止 于 原 位 , 滑 台 处于 滑 座 后 端 初 始 即
位置 ( 动 位 置 ) 见 图 2 。挡 铁 1 起 , a 6压 下 限 位 开 关
本 机构 由于 滑 台 第一 次转 为工 作 进 给 时大 小滑
小滑 块 5以其斜 面 压 下 限位 钩 9 退 到 钩 子 的左 面 而
禹
维普资讯
2 0 ( ) 1 1 轻 型 汽 车 技 术 0 23 总 5
( 图 2 ) 见 c。
技 术 纵横
4 3
工 作 循 环加 工 至终 点 ( 即钻 至 全孔 深 ) , 时 挡铁 1 压 9
1 2时 , 型 电 磁铁 3接 电吸 合 , 动 挡 销 伸 出 , 滑 微 推 在 台快 速 退 回过 程 中 , 住 大 滑 块 4与 大 滑 块 5 使 它 挡 , 们沿 导杆 1 回至 初 始位 置 。 台退 回至 原 位 时 , 滑 滑 挡
高 压冷 却 液 )这 样 钻 头 成 本高 。 ,
审 -
圈 2
审 - r
2 .设 备 会 经常 产 生 油 水 混 合 而 造 成设 备 故 障 , 因而设 备 维 护 保养 难 度 增 加 。
要 , 整 螺钉 1 调 0而 变 化 ) 大 滑块 4被 螺 钉 1 , 0顶 住 , 不能 随 滑 台前 进而 在 导 杆 1 滑 动 。在工 作 进 给过 上 程 中 , 关 7始 终 被 压 住 , 开 小滑 块 5可 以越 过 限 位 钩 9而 继 续 随 着 滑 台 前 移 , 滑 台工 作进 给 到 每 级 步 当 进 长度 时 ( 长度 可 根 据需 要 调 整 限 位开 关 1 此 l的 位 置 来 实 现 ) 小 滑 块 5前 端 的 挡 铁 6压 下 限 位 开 关 ,
项 工 作进 给 过 程 , 并实 现 步进 工 作 循 环 。 6 .滑 台 工 作进 给 至危 险 区 。 机床 左 滑 台 与右 本 滑台的工作循环之间有危险区互锁要求 , 当右 滑 台 按 步 进 工 作 循 环 到达 危 险 区时 , 铁 1 ( 右 滑 台 挡 7仅
具 有 ) 下 开 关 1 , 时 无 论 小 滑 块 5上 的 挡 铁 6 压 3此 是 否 已 压 下 开 关 l , 发 令 使 右 滑 台快 速 退 回 ( l均 图
{ f 回 讯 l j 1 , 出“ 速 退 ; ” /号 ( 图 2 ) 1发 { 快 见 l j} b。
现提出用普通的钻削动力头 , 增加 分级 进 给 挡 块 机 构 和 电气 控 制 挡 块 机 构 联 合 作用 , 现 分级 进 实
给 钻 削 而 成 功 地 解 决 了深 孔钻 削 加 工 , 分 级进 给 见
块 是 互 相 靠 紧 的 , 此 可 实 现 第 一 次工 作 进 给 长 度 因
大 于 以后 每 级 步进 工 作 进 给 长度 ( 每级 步 进 长 度 为
一
1, 4 大滑 块 4压 下 限位 开关 2 。大 滑块 4与 小滑 块 5
相互 靠 紧 , 卡 在 电磁 铁 挡销 3上 。 并 2 .滑 台快 速 引 进 。按 “ 动 ” “ 起 和 向前 ” 钮 后 , 按
前 时 , 滑块 5则 被 限位 钩 9挡住 , 在 导杆 1上滑 小 而
动, 当大 滑块 4压 下伸 缩 销 8时 , 同时 压下 开 关 7与 钩 子 9 滑 台又 转 为 工 作进 给 , 小 滑 块 5可 以越 过 , 且 钩 子 9而 随 滑 台前 移 , 样 滑 台便 又 重 复 上述 第 3 这
维普资讯
4 2
技 术 纵横
轻 型汽 车技 术 2 0 ( ) 1 1 0 2 3 总 5
新 型 分 级 进 给 机 构 解 决 深 孔 加 工
■ 娄 彦 昌
目前 我 公 司 开发 生 产 的液 压 助力 转 向器 的壳 体
需 要 深孔 加 工 , 图 1 如 :