设计硬点概念
汽车工程师年终总结范文5篇

汽车工程师年终总结范文5篇汽车工程师年终总结范文1不知不觉,进入公司已有_年的时间了,我的主要负责的设计工作,在领导的关心指导下,在同事的支持帮助下,我勤奋踏实地完成了本职工作,也顺利完成了领导交办的各项任务,自身在各方面都有所提升,现将这一年的学习、工作情况等作如下汇报:一、加强学习,兢兢业业,提升工作业绩扎实勤奋工作,提高工作业绩、坚持学习业务知识,提升自身业务素质。
为了更好地适应人才工作的新形势要求,体现全面贯彻落实的要求,这一年来我还是紧抓业务学习,认真学习了与工作相关的劳动人事新政策法规,向领导前辈们学习他们好的经验,好的方法,进一步提高自身的业务知识能力水平。
片面的掌握自己的工作业务是不够的,平时我也注重向其他业务往来单位学习熟悉了解各种工作流程,在多学习、多接触中提升了自己的业务水平,提高了办事效率,也使自己更好地服务企业、服务群众。
二、坚持热情细致服务,认真完成各项工作在中心日常工作期间,我能严格遵守中心的各项规章制度,认真完成上级、领导交给的任务。
也能恪守为民服务的宗旨,做到礼貌待人、热情服务,耐心细致。
我主要负责的是__项目。
“路漫漫其修远兮,吾将上下而求索”,在公司工作并不是那样简单的,我只好做到我能够做到的一切,我知道我的能力还是不够,但是谁也不能做到完美,我应该继续的工作下去,不是一步就能走到尽头的,在前进的道路上会有很多的荆棘和路途的。
三、具备专业设计水平那就需要加强自己的专业设计水平。
那什么是专业?从一门开始,或者家装,或者餐厅,或者酒店,单选一门然后触类旁通。
无论是什么样的室内设计都是空间上的设计,所以功能规划,色彩,灯光,材质,造型及工艺,是你主要掌握的核心内容。
在设计上你所反复应用的就是这些。
如果连一个卧室的正常照度都不知道,灯光对材质的的色彩影响都没有清晰的概念,那距离做设计还有一段距离。
辅助的而且也是必不可少的是人文历史,人体工程,视觉或者说空间心理。
做设计不是能画漂亮的效果图,能绘制标准的施工图纸就是设计了。
《汽车车身结构与设计》个人总结

一、汽车车身功能:
1、为乘员提供安全舒适的乘坐环境,满足:
1)乘坐舒适性,包括居住性、振动的舒适性及空气调节等。
2)密封性、隔热性、防振性和防噪声性。
3)操纵方便性。
4)视野性。
5)上下车方便性。
6)行驶安全性。
2、提供发动机及底盘等部件的装配。
3、汽车美观造型的体现。
二、车身的技术特点:
1、车身技术涉及当代科技领域的多门学科,而且各学科之间高度交叉和融合。
2.汽车表面及周围的流谱和局部流场的研究,分析作用在汽车上的气动力机理。
3.发动机和制动装置空气冷却问题的研究。
4.汽车内部自然通风和换气问题的研究。
二、流场:将流经物体的气流的属性如速度、压强、密度等表示为空间坐标和时间t的函数,、分别称为速度场、压强场、密度场,其总合称为流场。定常流场、非定常流场。
4.车身的外形和布置必须保证驾驶员和乘员有良好的视野。
5.车身材料必须是轻质的,以降低整车质量。
6.车身外形具有低的空气阻力,节省能源。
7.必须能在发生事故时对乘员提供保护。
8.车身材料必须来源丰富、成本低,所选择的材料必须能够实现高效率的制造和装配。
9.结构设计和选材必须保证车身在整个使用期间满足对冷、热和腐蚀的抵抗能力的要求。
七、客车蒙皮种类及特点:
应力蒙皮:蒙皮参与承载,可使骨架比较细,车身自重较轻。
预应力蒙皮:蒙皮不参与承载,只起到装饰作用,因为有应力,垂直于地板的刚度得以提高。
八、三化问题:
1.“系列化、通用化、标准化”:产品系列化、零部件通用化、零件设计的标准化。
2.平台化:指使用相同的底盘结构,生产不同的汽车产品。往往造型、功能、目标市场不一样,但是底盘和车身结构却是一样的,零部件也有很强的通用性。
关于总布置设计硬点

关于总布置设计硬点由于零部件设计要在整车总布置基本完成后才开始,在总布置设计阶段中往往没有零部件的详细资料,还不能解决零部件和总成内部的细节问题。
所以在布置设计图上出现的是各总成的主要控制点、主要中心线,也包括重要的外廓线和由这些轮廓线构成的控制面以及运动极限位置等。
这些控制点称为硬点(Hard point),包括整车及关键零部件的各种控制点、线、面以及控制特征等。
汽车整车设计硬点分类:概括了描述整车、总成及关键零部件的尺寸、结构型式、空间位置等的关键参数,它主要包括以下内容:整车外廓形状及尺寸:整车长度、整车宽度、整车高度、轴距、轮距等;驾驶区控制尺寸:踏板点、踵点,仪表板、转向柱及方向盘控制位置等;整车乘员空间内部尺寸:H点位置、头部空间、伸腿空间等;主要总成的设计硬点:总成的最大包络空间、定位点、配合点等;设计硬点构成了汽车总布置设计的骨架。
汽车总布置设计的过程就是设计硬点不断明确、逐步确定的动态过程。
所谓硬点,是通过英文的"hardpoint"直译过来的,它是个布置的概念,在整车开发中(由于整车由成千上万个零部件组成,那么怎么样来协调这些部件间的安装配合呢?硬点由此而生)为保证零部件之间的协调和装配关系,及造型风格要求所确定的控制点(或坐标),控制线,控制面及控制结构的总称。
所以会有底盘的硬点(这也是大家所熟知的),车身的硬点,内外饰的硬点,成员的硬点(例如H点)等等。
一般一个整车项目开发过程中,最先确定的就是这些硬点,这也是决定所开发的车型平台能否成功的关键因素之一,这些硬点必须要在满足PACKAGE要求的同时,也要满足性能的要求(例如底盘的硬点要满足整车的操纵稳定性和平顺性的要求),硬点将是汽车零部件设计和选型, 内外饰附件设计及车身钣金设计的最重要的设计原则,也是各项目组公共认可的尺度和设计原则.同时也是使项目组分而不乱,并行设计的重要方法. 一般确定后设计硬点不轻易调整, 如需调整设计硬点,需要和所有的设计人员协商,得到所有子项目组认可。
整车设计硬点公差分析标准

上海同济同捷科技有限公司企业标准TJI/YJY·00XX·A1—2003整车设计硬点公差分析(总布置公差分析和装配尺寸链公差分析)2005-XX-XX 发布2005-XX-XX 实施上海同济同捷科技股份有限公司发布TJI/YJY·00XX·A1—2005前言本标准分析整车设计硬点中存在各种偏差,为同济同捷公司设计的整车控制硬点和样车测量提供指导性依据。
本规定的内容适合各种设计车型(轿车,卡车和客车等),具体内容可按各种设计车型的需要可增减。
本规定于2005年X月X日起实施。
本规定由同济同捷科技有限公司提出。
本规定由同济同捷科技有限公司质量与项目管理中心负责归口管理。
主要起草人:严壮渝1.范围本标准分析整车设计硬点中存在各种偏差,为同济同捷公司设计的整车控制硬点和样车测量提供指导性依据。
本规定的内容适合同济同捷公司设计各种设计车型(轿车,卡车和客车等),2.引用标准GB 19234 乘用车尺寸代码GB/T 17347 商用车尺寸代码TJI/CZ.0004.AI 形状和位置公差的未知公差值TJI/CZ.0005.AI 汽车加工零件线性尺寸的未知公差3.定义术语3.1 设计硬点(HardPoint): 设计硬点是确定车身、底盘与零部件相互关系的基准点、线、面及控制结构的统称。
3.2 轮廓硬点∶整车在支承面上的位置尺寸。
3.3 性能硬点(PFH)∶整车或总成主要性能特征。
3.4 运动硬点(MTH)∶整车或总成运动特征和要求。
5.5 安装硬点(ASH)∶总成在整车上的位置尺寸。
4.要求4.1轮廓硬点按GB 19234规定,轮廓硬点尺寸不标注整车坐标系坐标值(X,Y,Z),而采用名义尺寸值;4.1.1 车辆总长公差 +/- 5 mm车辆总长公差△= 白车身全长制造焊接公差+前保险杠总成制造公差+后保险杠总成制造公差+前后保险杠总成和白车身装配公差△ = +/- (3 + 0.5 + 0.5 + 1 )= +/- 5 mm4.1.2 车辆总宽公差 +/- 2 mm车辆总宽公差△=白车身全宽制造焊接公差=+/- 2 mm4.1.3车辆总高公差 +/-6 mm车辆总高△=白车身高度制造焊接公差+ 前后悬架制造装配公差+轮胎尺寸公差△=+/- ( 2 + 0.5 + 3 )=+/-5.5 mm≈ +/- 6 mm4.1.4 轴距公差 +/-3mm ,左右轴距公差 +/- 3 mm轴距公差△=白车身总成制造焊接公差+前后悬架制造装配公差+前后悬架与白车身总成连接装配公差+车轮制造安装公差+弹簧刚度公差引起车轮位移△=+/- (0.5 + 0.5 +1 + 0.2+ 0.5)= +/-2.7 m m ≈+/- 3 mm4.1.5 轮距公差 +/- 6 mm,轮距公差△=白车身总成制造焊接公差+左右悬架制造装配公差+左右悬架白车身总成连接装配公差+ 轮胎外倾角公差 +轮胎前束公差△ = +/-(0.2 +0.25 +0.5 +4 + 1)=+/-5.95mm≈ +/- 6 mm4.1.6 前悬公差 +/- 2 mm前悬公差△=前保险杠总成制造公差+前保险杠总成和白车身装配公差+车轮中心制造安装公差△ =+/-(0.5 + 0.5 + 1 )=+/-2mm车轮中心制造安装公差分析见 4.4.54.17后悬公差 +/- 2 mm后悬公差△=后保险杠总成制造公差+后保险杠总成和白车身装配公差+车轮中心制造安装公差△=+/-( 0.5 + 0.5 +1 )=+/- 2 mm4.18 接近角公差 +/- 1°4.19离去角公差 +/- 1°4.20 纵向通过角公差 +/- 1°4.21最小离地间隙公差 +/- 4 mm最小离地间隙公差△=白车身总成制造焊接公差+部件制造安装公差+轮胎尺寸公差+ 弹簧刚度公差△=+/- (0.25+ 0.5 + 3+ 0.25 )= +/- 4 mm4.2 性能硬点(PFH)由于受到发动机制造公差的影响,造成功率,扭矩和油耗上的差异以及机械效率简化或忽略轮胎的侧偏刚度,这些因素均不能用尺寸数据估算,因此,性能硬点(PFH)控制的整车性能指标,一般控制它的性能限值。
整车总布置硬点设计规范
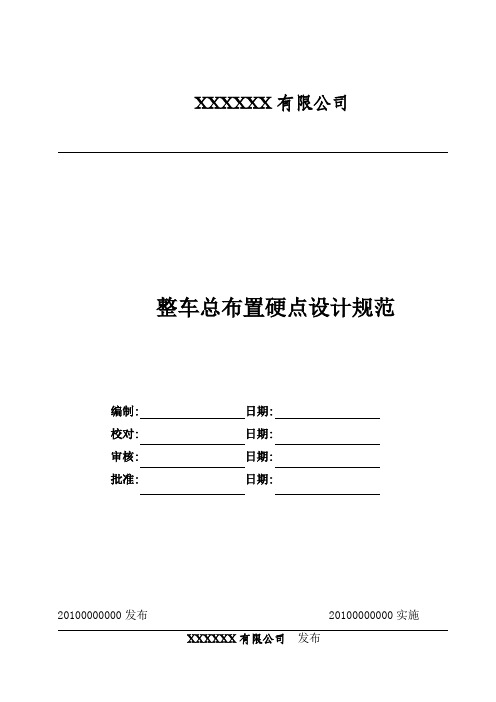
XXXXXX有限公司整车总布置硬点设计规范编制:日期:校对:日期:审核:日期:批准:日期:20100000000发布 20100000000实施XXXXXX有限公司发布目录一概述 (2)二整车设计基准 (2)1.1 整车坐标系 (2)1.2 整车设计状态 (2)三整车总体设计硬点 (3)3.1整车外部尺寸参数控制硬点 (3)3.2底盘系统布置主要控制硬点 (5)3.3人机工程布置设计硬点 (8)四结束语 (9)一概述整车的总布置设计过程是设计硬点(Hard Point)和设计控制规则逐步明确、不断确定的过程。
设计硬点是确定车身、底盘与零部件相互关系的基准点、线、面及控制结构的统称,主要分为安装装配硬点(简称ASH,包括尺寸与型式硬点)、运动硬点(简称MTH)、轮廓硬点及性能硬点等四类。
设计硬点的确定过程就是总布置设计逐步深化的过程,后续的设计工作必须以确定的设计硬点为基础展开。
但随着设计的深入和方案的修改完善,部分设计硬点还有进一步调整的可能。
所有硬点值都是在整车坐标系下的坐标值,长度值表示到小数点后一位,十分位为估计值(四舍五入)。
角度值表示到小数点后一位,十分位为估计值(四舍五入),用度分秒表示时书写到分。
长度单位未注明均为mm,角度单位未注明均为°。
所有未注明的安装硬点均指与车身配合面上车身孔的几何中心点的坐标,例如:配合圆孔的坐标指配合面车身圆孔圆心坐标,椭圆孔或长圆孔的坐标指配合面椭圆孔或长圆孔的几何中心点的坐标,方形孔的坐标指配合面对角线交点的坐标。
二整车设计基准1.1 整车坐标系电动乘用车设计过程中,整车总布置在设计软件三维环境下进行。
整车坐标系采用右手坐标系,它是总布置设计和详细设计中的基准线。
整车坐标系与设计软件中整车文件的绝对坐标系重合。
整车坐标系的定义如下:高度方向,取汽车车架中间平直段的上平面为Z轴零线,上正下负;宽度方向,取汽车的纵向对称中心线为Y轴零线,以汽车前进方向左负右正;长度方向,取通过设计载荷时汽车前轮中心的垂线为X轴零线,前负后正;整车坐标系原点即为三个坐标轴的交点。
汽车设计过程中的硬点研究与控制
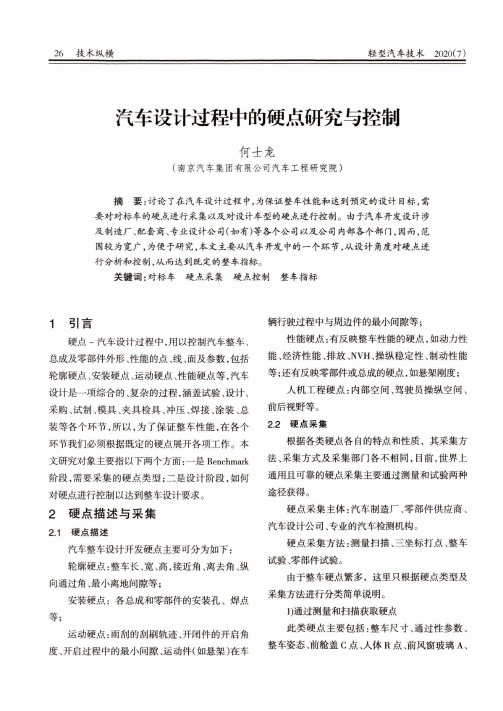
26 技术纵横轻型汽车技术2020(7)汽车设计过程中的硬点研究与控制何士龙(南京汽车集团有限公司汽车工程研究院)摘要:讨论了在汽车设计过程中,为保证整车性能和达到预定的设计目标,需要对对标车的硬点进行采集以及对设计车型的硬点进行控制。
由于汽车开发设计涉及制造厂、配套商、专业设计公司(如有)等各个公司以及公司内部各个部门,因而,范围较为宽广,为便于研究,本文主要从汽车开发中的一个环节,从设计角度对硬点进行分析和控制,从而达到既定的整车指标。
关键词:对标车硬点采集硬点控制整车指标1引言硬点-汽车设计过程中,用以控制汽车整车、总成及零部件外形、性能的点、线、面及参数,包括 轮廓硬点、安装硬点、运动硬点、性能硬点等,汽车 设计是一项综合的、复杂的过程,涵盖试验、设计、采购、试制、模具、夹具检具、冲压、焊接、涂装、总 装等各个环节,所以,为了保证整车性能,在各个 环节我们必须根据既定的硬点展开各项工作。
本 文研究对象主要指以下两个方面:一是Benchmark 阶段,需要采集的硬点类型;二是设计阶段,如何 对硬点进行控制以达到整车设计要求。
2硬点描述与采集2.1硬点描述汽车整车设计开发硬点主要可分为如下:轮廓硬点:整车长、宽、高,接近角、离去角、纵 向通过角、最小离地间隙等;安装硬点:各总成和零部件的安装孔、焊点 等;运动硬点:雨刮的刮刷轨迹、开闭件的开启角 度、开启过程中的最小间隙、运动件(如悬架)在车辆行驶过程中与周边件的最小间隙等;性能硬点:有反映整车性能的硬点,如动力性 能、经济性能、排放、NVH、操纵稳定性、制动性能 等;还有反映零部件或总成的硬点,如悬架刚度;人机工程硬点:内部空间、驾驶员操纵空间、前后视野等。
2.2硬点采集根据各类硬点各自的特点和性质,其采集方 法、采集方式及采集部门各不相同,目前,世界上 通用且可靠的硬点采集主要通过测量和试验两种 途径获得。
硬点采集主体:汽车制造厂、零部件供应商、汽车设计公司、专业的汽车检测机构。
浅析电气化铁路接触网硬点的危害及处理措施

硬点的主要特征是具有较大的冲击力 和加速度,使得受电弓在通过时受到 瞬时的强烈冲击,从而导致受电弓磨 损、振动和噪声等问题。
硬点的分类
根据硬点的形成原因,可分为静态硬点和动态硬点。静态硬 点是由于接触线自重、悬挂点位置不正确等因素引起的,而 动态硬点则是由于接触线的振动、风力等因素引起的。
硬点可能改变受电弓的振动频率和幅度,影响受电弓的稳定运行,进而影响列车 的安全运行。
03
电气化铁路接触网硬点的处理 措施
施工阶段预防硬点产生的措施
严格控制材料质量
选用优质、高强度的材料,确保接触网结构稳定性和 耐久性。
优化施工工艺
采用先进的施工技术和方法,提高施工精度和稳定性 ,减少硬点产生的可能性。
浅析电气化铁路接触网硬点 的危害及处理措施
汇报人:文小库 2023-12-28
目录
• 电气化铁路接触网硬点的基本 概念
• 电气化铁路接触网硬点的危害 • 电气化铁路接触网硬点的处理
措施 • 案例分析 • 结论与展望
01
电气化铁路接触网硬点的基本 概念
硬点的定义
硬点
在电气化铁路接触网中,硬点是指悬 挂点与接触线之间的非线性突跳点, 通常是由于接触线受到外界因素的影 响而产生的。
接触网硬点检测与定位方法
检测方法
采用先进的检测仪器和设备,如 激光检测仪、超声波检测仪等, 对接触网进行实时监测和检测。
定位方法
根据检测结果,结合接触网的几 何参数和电学特性,采用数学模 型和算法对硬点进行定位和分析 。
04
案例分析
某铁路局接触网硬点事故案例
事故概述
某铁路局在运营过程中,发生了 一起因接触网硬点引起的列车震 动和颠簸事故,导致部分列车晚
整车总布置硬点分析

-427.5 427.5
45.4 45.4
855
总布置:
1
前减震器总成 (2905-100)
1
5
2
2
4
3
6
3
5
6
4
序号
1 2 3 4 5 6
硬点名称
左前减振器安装孔中心(翻边、上表面)前 右前减振器安装孔中心(翻边、上表面)前 左前减振器安装孔中心(翻边、上表面)后左 右前减振器安装孔中心(翻边、上表面)后右 左前减振器安装孔中心(翻边、上表面)后右 右前减振器安装孔中心(翻边、上表面)后左
-17.7
前悬架上支点 X:15.8;Y:±555.5;Z:596.4
后副车架前安装点 X:2553.3;Y:±469.9;Z:
142.8
后悬架后衬套中心点 X:2718.3;Y:±621.4;
Z:-28.3
后悬架上支点 X:2629.7;Y:±566;Z:
622.4
安装硬点
1
底盘部件,如悬架,副车架与车身的定位面,安 装螺丝孔等是车身设计的基准和控制点。
重要底盘部件之间安装控制点,如转向器输 入端,转向拉杆与转向节安装点
门锁,玻璃升降器等内饰件,车身附件与车身安 装的点线面,是车身设计的基准和控制点。
空调和电器部件与车身安装的点线面
序 号
设计硬点
发动机曲轴中心线
整车总布置硬点分析
1.汽车硬点定义
总布置设计过程中,为保证零部件之间的协调 和装配关系,及造型风格要求所确定的控制点 (或坐标)、控制线、控制面及控制结构的总称, 俗称设计硬点,英美称为HARDPOINT。 这是 汽车零部件设计和选型,附件设计及车身设 计的最重要的各项目组公共认可的尺度和设 计原则。
车身设计复习要点

第一章车身产品开发流程和设计方法车身设计技术主要包括造型设计技术,工程设计技术以及先进的设计理念等几个方面,具体有计算机辅助造型技术,虚拟现实技术,空气动力学模拟,人机工程技术,数字样机技术,CAE分析和验证技术,模块化设计技术,性能设计技术和并行工程等。
名词解释:第一节概述计算机辅助造型技术(CAS):是随着扫描技术和矢量化技术的发展,在现代车身设计中得到应用的一门新兴的造型技术。
它区别于传统的仿形法设计,是将表达完整的造型胶带图由三维扫描仪直接输入工作站中,经过矢量处理后得到原始的数据点,再运用CAS系统进行实体造型,最后得到三维可加工的数字模型。
虚拟现实技术(VR):是一种先进的计算机用户接口,它强调将用户和计算机视为一体,通过多媒体的方法将信息进行可视化,展现在用户面前。
空气动力学模拟:汽车空气动力学主要是运用流体力学的知识,研究汽车行驶时,即与空气产生相对运动时,汽车周围的空气流动情况和空气对汽车的作用力(称为空气动力),以及汽车的各种外部形状对空气流动和空气动力的影响。
人机工程技术:是从人的生理和心理特点出发,研究人,机,环境的互相关系和相互作用的规律,以优化人-机-环境系统的一门学科。
数字样机技术(DMU):从宏观上说,DMU是一套基于协同作业机制与理念的并行工程开发技术,在产品的设计阶段就充分考虑产品的装配环节及其相关的各种因素的影响,在满足产品性能与功能的条件下,通过改变零部件装配结构来降低装配时的复杂性;从微观上说,它是一套结合一系列专用模块,如浏览,运动干涉分析,空间漫游及拆装模拟,结构优化等分析工具的实用高新技术。
CAE分析和验证技术:CAE分析和验证大至白车身的结构分析,小至密封条结构与材料的优化,主要涉及白车身和部件的静态,动态,安全和疲劳分析,空间和管路的CFD分析,钣金件的冲压成形可行性分析,塑料件注塑过程的模拟分析等方面。
模块化设计技术:原则是,力求以尽可能少的模块组成尽可能多的产品,并在满足要求的基础上使产品精度高,性能稳定,结构简单及成本低廉,且模块结构应尽量简单,规范,模块间的联系也尽可能简单。
汽车设计-下车身重要安装硬点结构设计规范模板
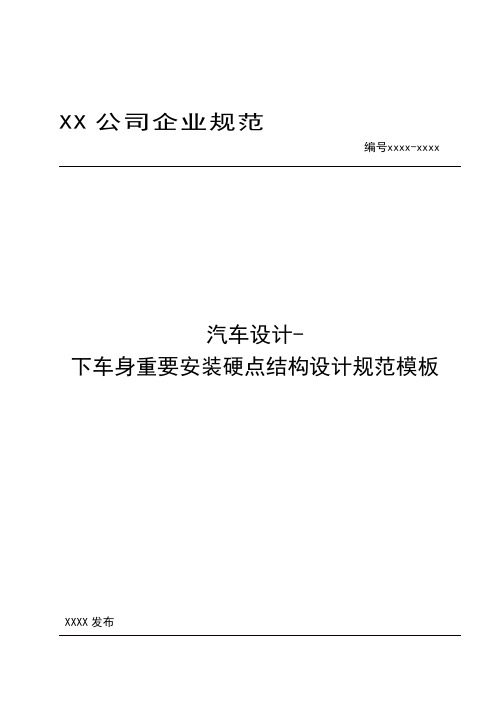
汽车设计-下车身重要安装硬点结构设计规范模板XXXX发布下车身重要安装硬点结构设计规范1范围该规范适应于M1类车辆下车身重要安装硬点(动力总成装配硬点、悬架装配硬点、排气系统装配硬点)结构的设计。
主要介绍了汽车开发过程中下车身重要安装硬点的作用及在整车中的影响。
对下车身重要安装硬点在整车中的功能进行了概述,同时对下车身重要安装硬点设计要点作了描述。
2规范性引用文件下列文件对于本文件的应用是必不可少的。
凡是注日期的引用文件,仅注日期的版本适用于本文件。
凡是不注日期的引用文件,其最新版本(包括所有的修改单)适用于本文件。
QCS 05 034-2015 前减震器座设计指南3术语和定义3.1动刚度是指计算结构在周期振荡载荷作用下对每一个计算频率的动响应,也称为频率响应。
4安装硬点及分布介绍下车身主要安装硬点有:发动机悬置安装点、副车架安装点、排气系统安装点、前减震器安装点等,其位置如图1所示。
11图1 下车身主要安装硬点位置5、功能介绍 5.1一般功能提供发动机、悬挂系统、排气系统等功能块的固定安装要求,起到连接底盘、动力总成与车身的作用。
5.2 特殊功能发动机的振动、轮胎的动不平衡和路面的不平所产生的振动、排气系统的振动等一切振源的振动,最终都是通过动力系统、悬挂系统、排气系统和车身的连接点,把振动的能量传入车身的,最终车身的振动转换为人感觉得到的振动和噪声。
连接点动刚度是室内怠速噪声与路面噪声的重要影响因素。
5.3性能要求考虑到安装硬点的一般功能,固定时需满足可靠耐久性。
考虑到本系统的特殊功能,还需要满足以下性能要求: a) 足够的强度能为动力总成、悬挂、排气系统提供足够的连接强度,以便操控良好。
因此关键部件通常采用高强度钢板。
需要通过CAE 计算满足强度要求。
b) NVH 性能满足动力总成悬置点、悬挂、排气连接点等的噪声、振动、平稳要求,需要通过CAE 计算满足动刚22355552233度性能要求。
乘用车悬架系统-车身硬点设计
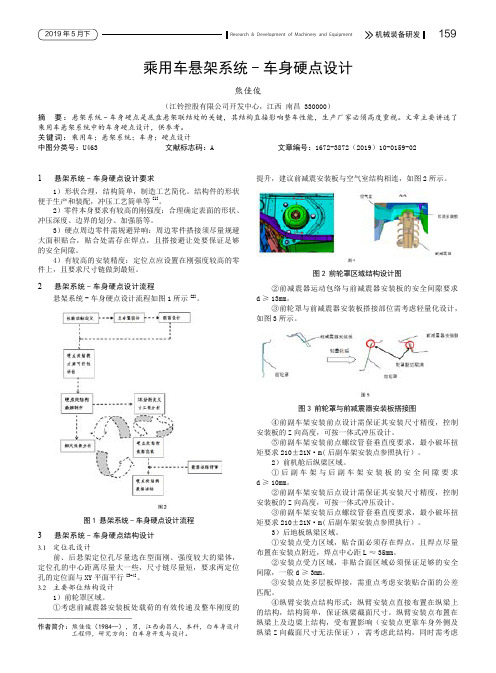
159机械装备研发Research & Development of Machinery and Equipment-车身硬点设计熊佳俊(江铃控股有限公司开发中心,江西 南昌 330000)摘 要:悬架系统-车身硬点是底盘悬架联结处的关键,其结构直接影响整车性能,生产厂家必须高度重视。
文章主要讲述了乘用车悬架系统中的车身硬点设计,供参考。
关键词:乘用车;悬架系统;车身;硬点设计中图分类号:U463 文献标志码:A 文章编号:1672-3872(2019)10-0159-02——————————————作者简介: 熊佳俊(1984—),男,江西南昌人,本科,白车身设计工程师,研究方向:白车身开发与设计。
1 悬架系统-车身硬点设计要求1)形状合理,结构简单,制造工艺简化。
结构件的形状便于生产和装配,冲压工艺简单等[1]。
2)零件本身要求有较高的刚强度:合理确定表面的形状、冲压深度、边界的划分、加强筋等。
3)硬点周边零件需规避异响:周边零件搭接须尽量规避大面积贴合,贴合处需存在焊点,且搭接避让处要保证足够的安全间隙。
4)有较高的安装精度:定位点应设置在刚强度较高的零件上,且要求尺寸链做到最短。
1所示[2]。
3 悬架系统-车身硬点结构设计3.1 定位孔设计前、后悬架定位孔尽量选在型面刚、强度较大的梁体,定位孔的中心距离尽量大一些,尺寸链尽量短,要求两定位孔的定位面与XY 平面平行[3-4]。
3.2 主要部位结构设计1)前轮罩区域。
①考虑前减震器安装板处载荷的有效传递及整车刚度的图1 悬架系统-车身硬点设计流程图2 前轮罩区域结构设计图图3 前轮罩与前减震器安装板搭接图提升,建议前减震安装板与空气室结构相连,如图2所示。
②前减震器运动包络与前减震器安装板的安全间隙要求d ≥13mm。
③前轮罩与前减震器安装板搭接部位需考虑轻量化设计,如图3所示。
④前副车架安装前点设计需保证其安装尺寸精度,控制安装板的Z 向高度,可按一体式冲压设计。
硬点设计流程
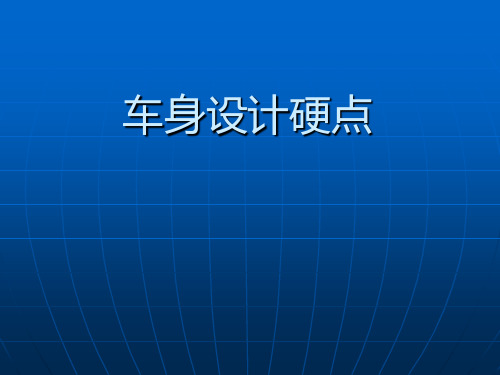
一、硬点的定义
设计硬点(HardPoint)
是指控制车身、底盘等零部件间相互关系 的基准点、线、面及控制结构的统称。
二、硬点的分类
1、轮廓硬点∶整车在支承面上的位置尺寸; 2、性能硬点∶整车或总成主要性能特征; 3、运动硬点∶整车或总成运动特征和要求;
4、安装硬点∶总成在整车上的位置和配合要求。
五、基于硬点的正向设计
五、基于硬点的正向设计
五、基于硬点的正向设计
五、基于硬点的正向设计
请思考,在后背门的设计中,我们考虑了 哪些设计硬点要求?
将逆向用点云通过取特 征,然后精确的移动、 转动到整车点云位置。 并通过断面保证主要安 装面误差0.2mm,其他 的面误差0.5mm。 并将数模通过点云布置 到整车位置,此为初步 布置数模
3、确定散热系统整车姿态以及安装基准面
将初步数模安装点调成 X、Z方向坐标一致,Y 方向左右对称。 此为正向布置过程。主 要考虑系统布置要求, 以及反推原车正向设计 思路。
1、确定散热系统上悬置安装硬点间距:
校核车身安装点间距 由于安装散热器上悬 置的车身支架没有三 坐标测量数据,车身 支架建模工作也未完 成。所以我们现通过 点云拟合圆,并测量 出其间距650.86mm
1、确定散热系统上悬置安装硬点间距:
通过以上的工作
考虑到测量误差、精度,并进行圆整,将散热系统上悬置安 装硬点间距定为650mm。
注:如果底盘与车身安装硬点间距相差过大,总布置将组织 底盘和车身相关设计工程师进行协商讨论,并进行实物测量, 综合分析,确定安装设计硬点间距。
2、确定散热系统下悬置安装硬点间距:
测量底盘安装点间距 可以看出其设计硬点 间距为601mm
车门系统设计的主要硬点和设计过程

车门设计的主要硬点和设计过程车门设计是汽车车身设计的重要组成部分,车门系统包括4大部分:车门开闭系、玻璃升降系、门锁系、车门密封系。
车门质量的好坏对整车质量有很大的影响。
车门设计也是车身设计中相对复杂的部分。
设计硬点是总布置设计过程中,为保证零部件之间的协调和装配,及造型风格要求所确定的控制点(或坐标)、控制线、控制面及控制结构的总称。
这是汽车零部件设计和选型、附件及车身设计最重要的尺度和设计原则,能使项目组分而不乱,是并行设计的重要方法,一旦确定后不要轻易调整。
开始粗定的硬点随着开发逐步深化,变得更加“硬”起来,越接近设计终结硬点越“硬”,不要轻易改动。
设计硬点是所有设计的灵魂。
车身结构主断面是对车身结构方案的具体描述,分布在车身各个位置以决定车身结构设计。
车门设计的主要硬点和设计过程车门设计总的设计原则是由外而内、先外板再内板、先断面再数模、先周边再内部的过程。
主要设计硬点有外板曲面、分缝线、门锁结构、内板结构、密封间隙、铰链中心线长度姿态、玻璃升降器位置和玻璃曲面等。
1.1 车门外板设计车门外板设计是在光顺好的整体造型面和车门轮廓线的切割面片基础上加周边翻边和门锁等特征后的车身零件。
分缝线和锁机构等是门外板的设计硬点。
分缝线通过2种方法获得:(1)一般先将汽车内外观面整体造型面光顺到A级曲面(CLASS A),同时将造型边界线投影到XZ铅垂平面后光顺到A级曲线,然后采用该投影的边界线投影到光顺好的A级大造型面与造型面相交,获得边界线,该交线理论上定为A级曲线。
(2)另外也可以采用空间曲线光顺后与曲面相交,反复相交反复光顺的方法,相交后将交线进一步光顺,重新获得边界线,再将该线投影到光顺面上获得更新的边界线,重复这一过程直到边界线达到A级曲线要求,用最后获得的边界线作为车门边界线,并与大的光顺面相切割得到车门外板面。
外板面设计好后,将门锁机构等有关设计硬点特征加上去便完成了车门外板设计(见图1),较大的门外板需与内板或车门侧向防撞梁,采用传力胶进行支承,不允许直接接触外板焊接,以防止热变形和几何干涉变形。
汽车内外饰主断面设计指导

表1:门饰板断面位置(示例)
序号 断面代号
表示的内容
断面位置及方向
1 NS-01 前门饰板与吸能块安装 过前门饰板与吸能块安装点中心与
点
ZY平面平行
2 NS-02 前门饰板本体与中饰板 过前门饰板本体与中饰板卡扣安装
卡扣安装点
点中心与ZY平面平行
3 NS-03 前门饰板与车身支架连 过抠手处安装点与支架安装点法向 接安装点
5.2 开闭件要描述开启和闭合两种极限状态。沿中 心转动的应描述转动中心。在2D图中须标注与周边 件的间隙尺寸。
(断面示例:仪表板杂物箱断面)
闭合状态
全开状态
5.3 密封件要描述非压缩变形状态。
(断面示例:B柱下饰板安装点)
门框密封条
断面示例:件(螺钉、螺母、螺栓、卡扣、塑料螺 母)可以不剖切。
4 NS-04 前门上饰板与中饰板卡 过前门上饰板与中饰板卡扣安装点
扣安装点
中心与ZY平面平行
备注
图1:门饰板断面位置(示例)
NS-01
NS-02
NS-03
NS-04
4.1 主断面位置的确定原则
• 表达零部件的主要结构,应尽可能多的反映该处 的特征信息。
• 外观要数:分缝、间隙、圆角、段差、拔模等; • 安装关系:螺纹、铆接、粘结、卡接等; • 配合关系:搭接件的配合、运动件的轨迹及周边
汽车内外饰主断面设计指导
目录
一.主断面概述……………………………………………………1 二.附件主断面设计输入 ……………………………………… 2 三.附件主断面设计输出…………………………………………3 四.附件主断面方案设计…………………………………………4
4.1主断面位置的确定原则……………………………………………………… 4 4.2主断面剖切方向选择原则…………………………………………………… 4
高速铁路接触网硬点产生的原因与预防
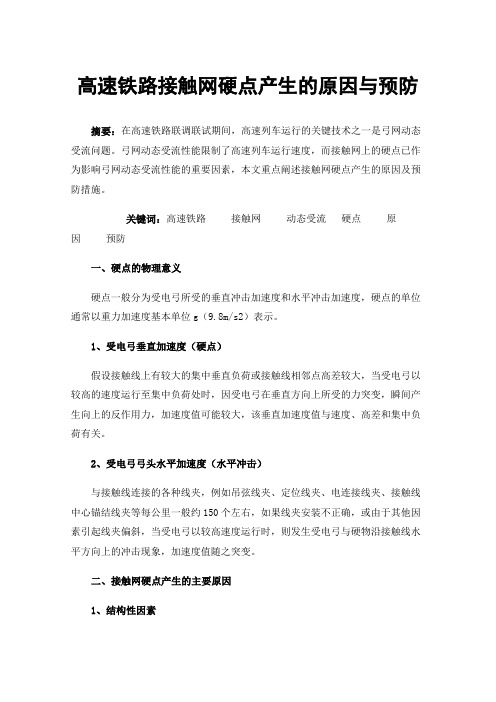
高速铁路接触网硬点产生的原因与预防摘要:在高速铁路联调联试期间,高速列车运行的关键技术之一是弓网动态受流问题。
弓网动态受流性能限制了高速列车运行速度,而接触网上的硬点已作为影响弓网动态受流性能的重要因素,本文重点阐述接触网硬点产生的原因及预防措施。
关键词:高速铁路接触网动态受流硬点原因预防一、硬点的物理意义硬点一般分为受电弓所受的垂直冲击加速度和水平冲击加速度,硬点的单位通常以重力加速度基本单位g(9.8m/s2)表示。
1、受电弓垂直加速度(硬点)假设接触线上有较大的集中垂直负荷或接触线相邻点高差较大,当受电弓以较高的速度运行至集中负荷处时,因受电弓在垂直方向上所受的力突变,瞬间产生向上的反作用力,加速度值可能较大,该垂直加速度值与速度、高差和集中负荷有关。
2、受电弓弓头水平加速度(水平冲击)与接触线连接的各种线夹,例如吊弦线夹、定位线夹、电连接线夹、接触线中心锚结线夹等每公里一般约150个左右,如果线夹安装不正确,或由于其他因素引起线夹偏斜,当受电弓以较高速度运行时,则发生受电弓与硬物沿接触线水平方向上的冲击现象,加速度值随之突变。
二、接触网硬点产生的主要原因1、结构性因素(1)接触网电连接线(含供电线上网点、加强线上网点、隔离开关、避雷器处电连接线)线夹和接触线中心锚结线夹处以及两接触线转换或交叉处(如锚段关节的中心柱、交叉式线岔处)因短范围内接触线的质量较为集中,其垂直集中载荷较大受电弓通过时有瞬间的集中负荷,垂直方向上可能会产生垂直加速度(硬点)。
(2)分段绝缘器作为一个集中负荷较大的地方,因其为一刚性物件,与柔性的接触线连接必将有刚柔过渡,形成冲击,产生水平和垂直方向上的加速度,在受电弓通过时形成沿接触线方向上的直接碰撞,产生水平冲击硬点;这些地方为非正常接触,在车速较高的情况下受电弓所受到的冲击较大,可造成电受电弓损毁和接触网断线的危险,因此,一般情况下分段绝缘器允许通过速度不大于120km/h。
- 1、下载文档前请自行甄别文档内容的完整性,平台不提供额外的编辑、内容补充、找答案等附加服务。
- 2、"仅部分预览"的文档,不可在线预览部分如存在完整性等问题,可反馈申请退款(可完整预览的文档不适用该条件!)。
- 3、如文档侵犯您的权益,请联系客服反馈,我们会尽快为您处理(人工客服工作时间:9:00-18:30)。
车门设计的主要硬点和设计过程
加入时间:2007-3-31 9:11:00 来源于:中国汽车工业信打印关闭
车门设计是汽车车身设计的重要组成部分,车门系统包括4大部分:车门开闭系、玻璃升降系、门锁系、车门密封系。
车门质量的好坏对整车质量有很大的影响。
车门设计也是车身设计中相对复杂的部分。
设计硬点是总布置设计过程中,为保证零部件之间的协调和装配,及造型风格要求所确定的控制点(或坐标)、控制线、控制面及控制结构的总称。
这是汽车零部件设计和选型、附件及车身设计最重要的尺度和设计原则,能使项目组分而不乱,是并行设计的重要方法,一旦确定后不要轻易调整。
开始粗定的硬点随着开发逐步深化,变得更加“硬”起来,越接近设计终结硬点越“硬”,不要轻易改动。
设计硬点是所有设计的灵魂。
车身结构主断面是对车身结构方案的具体描述,分布在车身各个位置以决定车身结构设计。
车门设计的主要硬点和设计过程
车门设计总的设计原则是由外而内、先外板再内板、先断面再数模、先周边再内部的过程。
主要设计硬点有外板曲面、分缝线、门锁结构、内板结构、密封间隙、铰链中心线长度姿态、玻璃升降器位置和玻璃曲面等。
1.1 车门外板设计
车门外板设计是在光顺好的整体造型面和车门轮廓线的切割面片基础上加周边翻边和门锁等特
征后的车身零件。
分缝线和锁机构等是门外板的设计硬点。
分缝线通过2种方法获得:(1)一般先将汽车内外观面整体造型面光顺到A级曲面(CLASS A),同时将造型边界线投影到XZ铅垂平面后光顺到A级曲线,然后采用该投影的边界线投影到光顺好的A级大造型面与造型面相交,获得边界线,该交线理论上定为A级曲线。
(2)另外也可以采用空间曲线光顺后与曲面相交,反复相交反复光顺的方法,相交后将交线进一步光顺,重新获得边界线,再将该线投影到光顺面上获得更新的边界线,重复这一过程直到边界线达到A级曲线要求,用最后获得的边界线作为车门边界线,并与大的光顺面相切割得到车门外板面。
外板面设计好后,将门锁机构等有关设计硬点特征加上去便完成了车门外板设计(见图1),较大的门外板需与内板或车门侧向防撞梁,采用传力胶进行支承,不允许直接接触外板焊接,以防止热变形和几何干涉变形。
1.2 门锁设计
车门内板设计是先建立门锁。
门锁与上下铰链共同构成车门的3个受力点,因此要求门锁高度的理想位置居于铰链轴线的中心垂直面;门锁的位置还应保证车门顺利开启和锁止,因此在后视图中锁舌的中心线必须与铰链轴线平行。
锁扣到门内板鱼嘴口的距离设计有2种方案:(1)当锁扣超出车门内板表面时,直接留足锁开启和闭合的余量,超出锁体口边缘3 mm;(2)当锁扣不超出车门内板表面时,锁扣到门内板鱼嘴口的距离在超出锁体口边缘的情况下为7 mm以上。
这考虑到保证碰撞后车门
仍能顺利打开。
1.3 车门内板设计
车门内板设计首先依靠主断面来进行,预先考虑车门密封要求,确定好设计断面,断面便成为设计硬点。
各汽车厂商为了缩短开发周期、节省设计成本,更多的是根据已有成熟车型的主断面加以调整修改,得到新车的设计主断面。
主要方法有:(1)肥边调整法(见图2)。
当新车的外造型面与原车在y方向相差-3~+5 mm,分缝线x方向相差不超过50 mm时,可直接调整原车内板断面肥边,其他部分不变,得到新的车门内板结构。
(2)断面平移(见图3)。
当新车外造型面相对于原车较大时,采用肥边调整法,将造成肥边过短、车门刚度强度不足、车门过重等情况,采用断面平移法,使原车主断面平移至原车外造型面与新车外造型面重合,得到新车内板结构设计断面。
1.4 车门密封系设计和检查
车门密封系的设计主要是车门内板与周边零件如侧围等的间隙,密封条及其压缩量的设计。
这两项车门设计硬点应在设计之初根据制造商制造精度确定,制造精度高、公差小,则间隙可设计得相对较小,密封条压缩量也可设计得较小;制造精度低、公差较大,则间隙必须设计得相对较大,密封条及其压缩量也要设计得相对较大。
如果设计得较小,在公差较大的情况下,将出现关门力过大关不上或者密封条压缩量太小关不紧的情况。
车门密封系的设计以断面为主要手段。
在车门内板和侧围建模完成后,取车门周边不同位置的断面,逐一检查修改,根据国内厂商的生产精度水平,车门周边密封间隙应取15 mm左右,日本车厂车身制造精度较高,密封间隙多取在10~12 mm。
密封条的断面应处于装配状态,这样可以根据密封条断面进行检查和修改。
密封面密封条处于干涉状态,干涉不能太大或太少,一般为有效压缩尺寸的1 /3~1/2,这样既保证了密封效果,又不至于运动件在运动过程中产生过大的噪声和关门力。
另外在车门与侧围之间没有密封的部分要留9~12mm的腾空间隙,以防止干涉。
1.5 车门铰链布置和运动校核
车门铰链的设计是车门设计的一项重要工作,直接关系到车门能否正常开启。
在铰链设计中,铰链中心线定位和铰链中心距是重要的设计硬点。
铰链轴线一般设计成具有内倾角和后倾角。
内倾角指铰链轴线在x=0平面上的投影与z轴之间的夹角,内倾角一般为0~4°,见图4;后倾角指铰链轴线在y=0平面上的投影与z轴之间的夹角,一般为0~2°,见图5。
内倾角和后倾角都是为了使车门开启时获得自动关门力,也有个别汽车门铰链具有前倾角,但一般不会有外倾角。
车门铰链轴线的设计先确定铰链轴线沿车身方向的尺寸变化范围(X1,X2),并在此范围内任选一值Xm,将轴线限制在与x轴垂直的平面x=Xm内,在x=Xm平面内确定铰链轴线的倾斜状态:先分别求出x=Xm平面与内外板曲面的交线C1和C2,并求出C1和C2对应的y方向的极限坐标位置Ymin(内板投影线最左端)、Ymax(外板投影线最右端);在x=Xm平面内通过输入直线方程y=B,B∈(Ymin,Ymax)来生成一条与z轴平行的轴线Z1Z2;确定铰链轴线中心点的z坐标值:通过内板上下边框或外板上下边框求出平均位置坐标z=C,并根据它在y=B直线上求出一点O;根据铰链轴线内倾角范围θ∈(0°,
4°),将y=B直线绕O点逆时针旋转θ角度,得到轴线位置O1O2。
根据铰链间距L∈(300 mm,500 m m),以铰链中心O为初始点,沿直线y=B确定两点D和E,使两点间线段长度为L,调整L值以及轴线外板的距离,保证在铰链宽度方向不与外板干涉的情况下,轴线尽量靠近外板的极限位置(L值确定已知时)。
若L值可以改变,则可以考虑稍微减小L值,轴线更靠近外板(车门外板曲率较大时)。
可以通过改变最初的B值重新生成轴线O3O4或作O1O2的平行线来改变轴线到外板的距离。
当轴线位置最终确定后,根据D、E两点位置可将铰链模型正确地放入车门门腔内,待进一步运动校核及干涉检验。
铰链中心距的确定可参考车门长度,一般铰链中心距/车门长度=33%,或者更长。
需要说明的是在布置铰链时,应注意在结构允许的情况下,车门上下两铰链之间的距离应尽可能大。
为了避免打开车门时与其它部分干涉,铰链的轴线应尽可能外移,使其靠近车身侧面。
铰链中心线位置和中心距确定后,需要进行运动干涉校核,这也在主断面设计中完成,可能出现的干涉位置有前后门干涉、前门与A柱翼子板干涉、门与铰链干涉等,在可能干涉的位置取主断面,将车门延中心线旋转,即可一目了然,如图6。
1.6 车门玻璃设计以及车门玻璃升降器的设计布置
玻璃要设计为双圆环面,可以和外造型匹配,达到玻璃升降的平顺性,圆环面的数学方程如下,其思想简图与基本参数见图7、8:当R足够大且圆柱半径r远远小于R时,从圆环面上截取的玻璃曲面仍近似为柱面。
玻璃的运动可以认为是一种绕圆环面中心引导线的旋转运动,其运动轨迹是与引导线成一定夹角的圆环截面线的一部分。
R=15~25km,r=1200~2000m;大客车为R=∞,r=4000~7000 m。
玻璃升降器是车门设计中很重要的一个环节,它的合格与否直接影响到车窗的开闭。
玻璃升降器在设计过程中,关键在于安装和玻璃导轨的曲线确定。
有了玻璃的数据后,可求出玻璃的质心位置,根据以往设计经验和一些样车数据,一般单导轨的位置是在玻璃质心位置向B柱方向偏移15~25mm,双导轨的间距应在不干涉内门板和其它附件的情况下尽可能大,但两个导轨的中线应该在玻璃质心位置向B柱方向偏移15~25mm。
导轨位置确定后,通过偏置玻璃面求出导轨的弧度,此导轨弧度为空间螺旋曲线。
由于玻璃运动近似圆弧运动,但升降器的长导轨在自由状态下是平面运动,所以在玻璃升降过程中,升降臂和平衡臂会变形随长导轨一起运动。
为了提高升降器的寿命,应使运动过程中升降臂和平衡臂的变形量尽可能小。
图9表示了玻璃运动轨迹和长导轨在自由状态下的运动轨迹,A、B、C分别表示了玻璃在上、中、下3个位置时升降臂和平衡臂的最大变形量,其中C>A=B。
设计硬点控制在车门设计的灵魂,主断面是车门设计的重要手段,以此为思路,使车门设计有条不紊,效率得以提高,质量得以保证。
车门设计是车身设计中最复杂、难度最大,实际过程中可能会遇到很多情况,有时甚至会出现控制硬点之间相互矛盾,需要具体问题具体分析,不断调整以达到最优结果。