计算机辅助塑料模具设计和工艺改进
塑胶模具设计概述

塑胶模具设计概述塑胶模具设计是指通过计算机辅助设计软件对塑胶制品的实物模型进行数值分析、虚拟制造等技术手段,设计出合理的塑胶模具,在压制塑胶制品时使用,从而使得塑胶制品的生产工艺得到优化完善。
因此,塑胶模具设计是塑料制品生产中至关重要的一环。
一、塑胶模具设计思路塑胶模具设计,需要从整体上考虑塑料制品的结构、要求、生产工艺等多方面因素,进行全面综合的设计。
具体来说,设计思路应该包括以下方面:1. 塑料制品的形状和尺寸:首先,要了解塑料制品的形状和尺寸,根据产品的轮廓线和尺寸,完成上模和下模的设计。
2. 塑料制品的材质要求:考虑到不同塑料材料对模具、生产工艺的影响,应该综合考虑材料性能、加工工艺、成本等因素,选择合适的材料,对模具进行合理的热处理和表面处理,提高模具的耐磨性和使用寿命。
3. 塑料制品的表面要求:考虑到塑料制品表面的光洁度、平整度、尺寸稳定性等因素对产品外观质量的影响,设计师要在模具表面处理和抛光方面下功夫,使得产品表面光洁度达到要求,使产品的质量得以确保。
4. 塑料制品的生产效率要求:考虑到企业的生产效率问题,设计上模和下模时,应充分考虑压力、温度等控制因素,从而提高塑料制品的生产效率。
二、塑胶模具设计的主要步骤1. 模具设计的准备工作:首先,对于塑胶模具设计者而言,应该通过多方面了解产品的基本情况,确定产品要求,以及了解市场情况,明确用户的具体需求。
同时,根据产品的尺寸、形状、材料选择等多种因素,确定模具的工艺方案。
2. 模具设计方案的确定:在进行模具设计时,需要整合不同的信息资源,形成具体的设计方案。
在确定设计方案的过程中,需要充分考虑塑料产品的生产工艺、模具制作的技术、模具使用寿命等多种因素,从而设计出合理的模具。
3. 模具零件设计:模具设计的核心是模具零件的设计。
在进行模具零件设计时,需要考虑到气动元件、油压系统、电器控制系统等多种因素,确定模具零件的结构、材料、尺寸以及配合精度等要求。
基于CAE技术的塑料模具设计方法

0引言一般塑料制品都是采用模塑成型的基础制造工艺,因此塑料模具是塑料制造行业的主要生产工艺装备,并且在我国国民经济中占有重要作用。
近几年,随着我国汽车、电子、航空等工业领域的迅速发展,对塑料制品的需求量更是急剧增加,因此对塑料制造业效率要求也逐渐提升。
由于塑料模具具有种类多、更新速度快、小批量加工等基本特征,我国的传统塑料模具设计方式已经难以适应新时期工业生产的需求,所以将电子制造技术应用于塑料模具设计就成为塑料制造行业发展的必然趋势。
CAE 技术为塑料制造行业的人员提供了快捷高效地计算机辅助软件,可以帮助塑料模具设计人员从塑料产品开发、模具设计到产品成型进行一系列的设计与完善,从而大大缩短了设计制造周期,提高了效率,降低了企业成本。
1塑料模具CAE 概述CAE (Computer Aided Execution )指的是一种计算机辅助工程技术,是为了深入发展计算机辅助设计工程技术与计算机辅助制造工程技术而出现的一种新的应用软件。
一般可以认为它是一个包括了数值运算技术、信息数据库、多媒体构图学、应用工程分析与仿真模具等元素在内的具有综合性功能的软件系统,而它的核心技术就是对技术工程数据的模具化与信息数据的实现方法。
对于塑料模具设计制造工艺的计算机辅助工程来说,主要是依靠高分子流变学、函数计算与构图形式等基本理论,对制造工艺直接进行数据模拟,这样可以让塑料模具在制造之前能够形象逼真地模拟出塑料产品成型的一系列过程,防止制造过程中塑料模具对最终产品产生影响,及时发现将要出现的问题,为设计与制造过程中条件是否允许提供了较为科学的依据。
基于CAE 计算机辅助技术的塑料模具设计过程(图1)与我国传统的塑料模具设计过程有较大差别,可以说这种新型的生产过程属于典型的并行路线。
在塑料模具设计与制造前,设计人员通过利用计算机CAE 分析软件,在计算机上对将要出来的成型产品进行模拟仿真分析,这样可以科学预测到材料的填充、压缩、冷清及纤维取向分布等情况,进而让工作人员能够迅速了解到需要改进的工艺参数,优化塑料模具工艺过程,将多数出现的问题改正,避免了出来成品之后再修改模具,能够用最短的时间来优化塑料模具的设计过程,从而提高了塑料产品的质量和制造效率。
注塑模cae技术1注塑模cae的内容
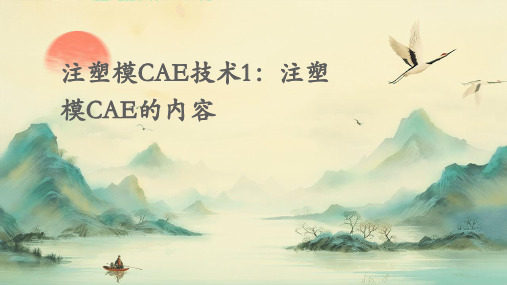
总结词
确保医疗用品结构完整性和安全性
详细描述
医疗用品的成型过程要求非常高,需要保证产品结构的 完整性和安全性。通过注塑模CAE技术进行成型过程模 拟,可以预测产品在成型过程中的可能问题,如收缩、 翘曲、裂纹等,并及时进行调整,确保最终产品的质量 和安全性。
THANKS
感谢观看
模型简化
为了提高计算效率,对模型进 行简化,如忽略倒角、小孔等 细节。
网格划分
将模型划分为有限元网格,以 便进行模拟计算。
边界条件设定
根据实际情况,设定模具与注 射机的连接方式、注射压力、
注射温度等边界条件。
模拟计算
01
02
03
充填模拟
模拟塑料在模具中的流动 行为,预测可能出现的填 充不足、熔接痕等问题。
06
注塑模CAE技术应用案例
案例一:手机壳流动与翘曲分析
总结词
通过流动模拟预测填充行为,翘曲模拟预测产品变形程 度
详细描述
在生产手机壳的注塑过程中,利用CAE技术进行流动模 拟可以预测塑料在模具中的填充行为,优化注射时间和 压力,确保均匀填充。同时,翘曲模拟可以预测产品在 冷却过程中的变形程度,为后续的模具优化和工艺调整 提供依据。
案例二:汽车保险杠冷却分析
总结词
优化冷却管道设计,缩短冷却时间,提高生产效率
详细描述
在汽车保险杠的注塑过程中,通过CAE技术进行冷却 分析可以优化模具中的冷却管道设计。通过模拟冷却 过程中的温度场分布和冷却时间,可以找到最佳的管 道布局和冷却液温度,从而缩短冷却时间,提高生产 效率。
案例三:医疗用品成型过程模拟
塑料制品质量预测
通过模拟塑料在注塑过程中的流动 和冷却过程,注塑模CAE可以预测 塑料制品的质量和可靠性,如尺寸 精度、翘曲变形等。
在塑料模具设计中CAD/CAM/CAE的应用

在塑料模具设计中CAD/CAM/CAE的应用本文论述了Pro/E在模具设计中的应用标签:塑料CAD/CAE/CAM模具设计一、前言塑料产品从设计到成型生产是一个十分复杂的过程,它包括塑料制品设计、模具结构设计、模具加工制造和模塑生产等几个主要方面,它需要产品设计师、模具设计师、模具加工工艺师及熟练操作工人协同努力来完成,它是一个设计、修改、再设计的反复迭代、不断优化的过程。
传统的手工设计、制造已越来越难以满足市场激烈竞争的需要。
计算机技术的运用,正在各方面取代传统的手工设计方式,并取得了显著的经济效益。
塑料模具CAD集成技术是一项先进的模具制造技术,它的制造包括塑料产品的造型设计、模具的结构设计及分析、模具的数控加工、抛光和配试模以及快速成形制造等,各个环节所涉及的CAD单元技术又包括产品外形的快速反求、结构分析与优化设计、辅助制造、加工过程虚拟仿真、产品及模具的快速成形、辅助工艺过程和产品数据管理技术等。
塑料模具CAD集成技术,就是把塑料模具在制造过程中所涉及的各项单元技术集成起来,统一数据库和文件传输格式,实现信息集成和数据资源共享,从而大大缩短模具设计的制造周期,提高制模质量。
二、塑料制品及模具结构设计进行塑料模具设计制造的第一步是塑料产品的设计。
现代设计方法是设计者在电脑上直接建立产品的三维模型,根据产品的三维模型进行模具结构设计及优化设计,再根据模具结构设计三维模型进行加工编程及编制工艺计划。
而商品化三维CAD造型软件如Pro/Engineer、UG、CATlA等为设计师提供了方便的设计平台,其强大的曲面造型和编辑修改功能以及逼真的显示效果使设计者可以运用自如地表现自己的设计意图,真正做到所想即所得,而且制品的质量、体积等各种物理参数一并计算保存,为后续的模具设计和分析打下良好的基础。
同时,这些软件都有专门的注塑模具设计模块,提供方便的模具分型面定义工具,使得复杂的成型零件都能自动生成,而且标准模架库、典型结构及标准零件库品种齐全,调用简单,添加方便,这此功能大大缩短了模具设计时间。
模具发展现状

模具发展现状模具是一种用于制造各种产品的工具或设备,它们扮演着工业生产中至关重要的角色。
模具的质量和性能对产品的质量、成本和生产效率具有重要影响。
因此,模具行业一直以来都是工业发展的重要支撑。
当前,随着制造技术的不断进步和需求的不断变化,模具行业也在不断发展演变。
以下是模具发展现状的几个方面:1.技术创新:随着科技的进步,模具行业也在不断引入新的技术。
例如,计算机辅助设计(CAD)和计算机数控加工(CNC)技术的应用使得模具设计和制造变得更加精确和高效。
三维打印技术也开始应用于模具行业,为设计和制造带来了全新的可能性。
智能制造技术的快速发展也为模具行业的智能化和自动化提供了支持。
2.材料应用:不断改进和引入新的材料是模具行业的一个重要趋势。
例如,新型金属材料、耐磨材料和导热材料的应用,可以显著提高模具的使用寿命和性能。
此外,复合材料和高性能塑料等新材料的引入,也为模具设计师提供了更多的选择和创新空间。
3.高精度模具的需求增长:随着社会对产品精度要求的不断提高,对高精度模具的需求也在不断增长。
例如,电子设备、汽车零部件和航空航天等领域对高精度模具的需求非常大。
因此,高精度模具的设计和制造成为模具行业的一个重要发展方向。
4.模具服务的需求变化:随着制造业结构的变化和全球化竞争的加剧,对模具服务的需求也在发生变化。
客户对模具制造的速度、质量和成本的要求越来越高。
因此,模具制造企业需要不断提高自身的技术水平和服务能力,以满足客户的需求。
此外,一些企业还开始将模具制造外包给专业模具服务公司,以降低成本和提高效率。
5.环保意识的提升:随着环境保护意识的提升,对模具制造过程中的环境污染和资源浪费的关注也在增加。
模具制造企业需要采取相应的措施来减少废水、废气和固废的排放,同时优化能源利用和循环利用。
一些企业还开始使用环保材料和生产工艺,以降低对环境的影响。
总的来说,模具行业正面临各种挑战和机遇。
技术创新、材料应用、高精度模具需求的增长、模具服务需求变化和环保意识的提升,将推动模具行业向更高水平发展。
塑料模具设计中Pro∕E软件的应用

塑料模具设计中Pro∕E软件的应用Pro/Engineer(Pro/E)是目前最先进和最为广泛使用的三维计算机辅助设计(CAD)软件之一,它拥有强大的建模工具,能够帮助用户设计和制造各种产品,特别是在塑料模具设计中,Pro/E软件的应用更是发挥了重要作用。
一、Pro/E对塑料模具设计的重要性塑料模具设计是塑料加工过程中不可或缺的一环。
它的设计结果直接决定了塑件的质量、精度和生产效率。
因此,为了在塑料加工后期得到高质量的产品,塑料模具的设计必须精确、准确并且可行性强。
而Pro/E作为一个全面的三维建模软件,在构建复杂模型和分析过程中的效率高、准确性高,并能够更好的满足塑料模具设计的需求。
二、Pro/E在塑料模具设计中的应用1、模型建立在Pro/E中,用户可以根据需要构建很多种类型的模型,例如实体模型、表面模型、线框框架模型等,并且可以为每个部件设置材料属性、表面特性等。
这种规范化的设计方式,可以帮助用户更好地组织和控制模型的构建过程。
Pro/E还可以自动生成各种固体体和空间体,然后进行分解、和部件拆分,最后将模型细化和变形操作。
除此之外,用户还可以进行细节设计和加工细节设计,使得模型更符合实际操作要求。
2、动态仿真在塑料制品加工过程中,动态仿真分析起着极为重要的作用。
而Pro/E则拥有强大的模拟和仿真功能,它可以为用户提供各种模拟方式,例如碰撞模拟、动态膨胀模拟、数据捕获分析等,这些仿真方法可以考虑真实物资的应力和变形情况,并以此为基础为模型优化提供数据支持。
3、模型优化在模具设计过程中,往往需要详细理解既有模型的现状,以便对其进行优化和调整。
Pro/E软件可以为用户提供专业的模型优化方案,包括配合最优化方法和模拟算法等。
Pro/E还拥有着快速的改进过程,用户可以通过对连续的历史版本进行比较,重新判断和抉择模型的优劣之处,以期在最短时间内将模型调整到最好的状态。
4、模拟分析在塑料模具设计及生产过程中,需要进行各种质量和效益检查。
塑料制品使用CADCAE集成的注塑模具设计系统
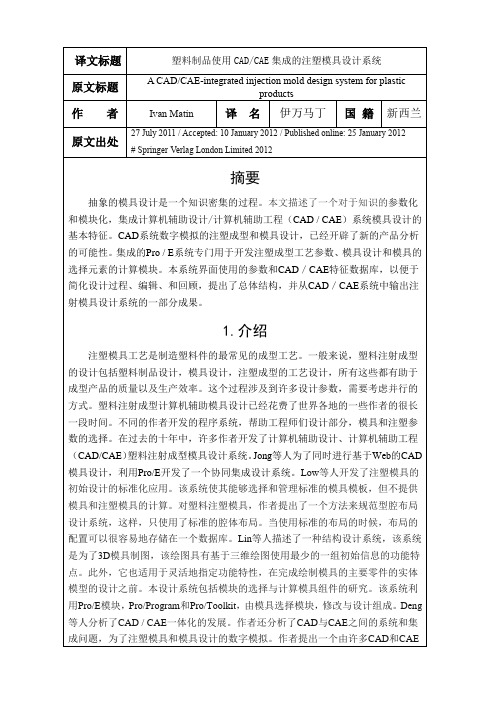
向对象的模具组件库模型将不同的几何和非几何信息的拓扑结构。
多年来,许多研究人员试图使用的各种知识工程(KBE)方法使其自动完成整个模具设计过程,如基于规则推理(RBR),和案例(CBR)和参数化设计模板(PDT)。
陈等人开发了一个基于辅助注射模具设计系统的三维CAD知识(IKB模型)。
在他们的研究中,设计规则和模具设计的专业知识来自经验丰富的模具设计手册,通过各种传统的知识获取过程。
传统的知识工程的方法,如RBR,CBR,和简单的PDT已成功地应用于塑造腔和一个产品的模具流道布局设计的自动化。
YE等人提出一种用简单的几何形状和符号分层表示基本特征和对象的方法进行自动化装配模具,前面提到的各个系统分析表明,作者用不同的方法解决模具设计中简化模具配置器(选择器)的问题,他们用CAD/CAE一体化技术为模具基础选择器创建基础法则,很多作者用CAE系统数字模拟注塑成型来定义注塑参数,还开发了几种注塑成型模具原始CAE模块,然而,先前提及的所有系统缺少模具计算模块,注射参数将允许数字模拟积分运算结果,导致有必要建立一个软件系统,它集成了注塑成型参数,通过注塑成型的数字模拟获得的结果来进行模具计算和选择,所有这一切都将被集成到模具塑胶制品CAD/CAE集成注塑模具设计系统。
图1 用于塑料产品塑料模具集成设计系统的一般结构图2 用于注射成型工艺的数字模拟模块的结构图3 定义模具几何形状的形式图4 确定冷却水道和模腔之间距离的形式图5 模具基准的选择形式2. 集成CAD/CAE系统的结构众所周知,不同的作者支持不同的计算方法,其涉及的模具设计系统自动化技术也不同,如KBE(RBR,CBR,PDT)或设计优化技术,如传统的(NLP,LP,BB,GBA,IR,HR)或启发式搜索(TS,SA,GA)和其他特殊技术如(SPA,分布,注塑压力分布,剪切应力的分布,对仿真模型的表面温度分布,一个仿真模型的填充质量,冷却时间,冷却质量,及注射成型。
《塑料模具设计》课程的教学改革和实践

#甲”盟垫丝盘查堡.登塾里丝《塑料模具设计》课程的教学改革和实践袁长颂(安徽理工大学机械工程学院,安徽淮南232001)摘要:《塑料模具设计》课程作为机械专业课,涉及到机械制图、机械零件、工程材料、互换性与技术测量等专业基础课程。
随着模具设计和高等教育的发展,该课程面临着教学模式的改变、教学手段的调整。
本文结合教学实践和探索,提出了调整和优化教学内容、改进教学方法和手段,改变传统的考核方法,调动学生的学习积极性、注重实践性教学环节的培养和试验,加强学生设计能力培养的改革措施。
这对提高教学质量,培养创新型人才具有重要意义,并在实际教学中取得了一定的成效。
关键词:塑料模具设计;教学模式;教学手段;教学质量;创新.1<塑料模具设计》课程原教学安排《塑料模具设计》课程足讲授塑料成型模具的结构、成型原理及设计方法的一门专业课。
教学大纲的基本要求是:使学生能了解塑料模具的分类及各类塑料模具的典型结构;基本掌握塑料模具的成犁原理和成型r T艺;掌握典型的翅料模具的设计计算方法;基本能完成典型的注射塑料模具的设计。
目前我校选用的教材是机械工业出版社出版,申树义,高济编著的《塑料模具设计》。
针对大纲要求,《塑料模具设计》课程作为指定机械专业课,总学时数为40学时,教学计划安排如下:第一章塑料:甥料的基本概念;组成;特性;分类。
2学时;第二章塑料的成型工艺:塑料的成型工艺及成型原理;塑件的结构性设计。
8学时;第三章塑料注射模具设计:塑料模具的分类;各注射模具的结构;注射模与注射成型机的关系;成型零件的设计;导向机构的设计;推}f{机构的设计;抽芯机构的设计;加热与冷却装置的设计;热同性坦料注射模的设计。
16学时;第四章压缩模具的设计:压缩模具的分类和基本结构;压缩模具结构的选择;成型零件结构设计;导向机构设计;开模和推出机构设计;抽芯机构设计。
8学时;第五章传递和吹塑模具设计:传递模具设计;吹塑模具设计。
4学时;第六章塑料模具的材料:模具零件材料的基本要求;模具成型零件常用材料;塑料模具新材料的发展趋势。
塑料模具设计与制造的计算机辅助教学
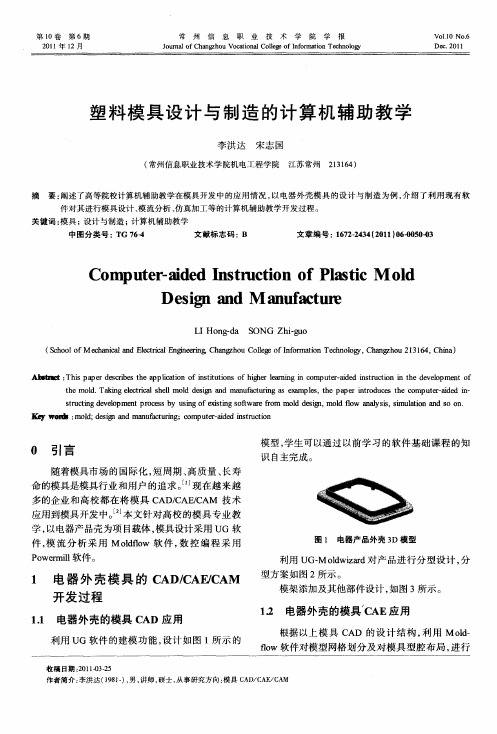
M
型方 案如 图 2所示 。
模 架添加 及其 他部 件设计 , 图 3所 示 。 如
12 电器外 壳的模具 AE应用 . C
根 据 以上 模 具 C AD 的 设 计 结 构 , 用 M o — 利 l d l f w 软件对 模 型 网格 划 分 及对 模 具 型 腔 布局 , 行 o 进
成 型工 艺参数 等方 式 , 次进行 优化 后 的分析 计算 , 再 直 至产 品注 塑成型 过程符 合生 产要求 。经 过几 次分
t e mo d Ta i gee tia s e l e in a d ma u a t r g a x mp e , h a r mto u e h mp t — ie n h l . k n l r l h U mo d d sg n fc u i s ea l t e p pe r d c s t e c c c n n s o u e ad d i— r sr c ig d v lp n r c s y u i go xs ig s f r r m l e i , l lw a i, i lt n a d S n tu t e eo me tp o e sb s fe it o wae fo mod d  ̄ mo f n n n t s d o a l s smu a i O o . n ys o n
模型 , 学生可 以通 过 以前 学 习 的软件 基 础 课 程 的 知 识 自主完成 。
图 1 电 器产 品 外 壳 3 模 型 D
利 用 UG— lwzr Mod ia d对产 品进行 分 型设 计 , 分
1 电器 外 壳 模 具 的 C DC A /A 开 发 过程
1 电器外 壳的模具 C D 应用 . 1 A
Moldflow/IMoLD技术在注塑模设计中的应用

Moldflow/IMoLD技术在注塑模设计中的应用0 引言传统塑料模具设计往往是由设计人员凭经验与直觉设计模具,待模具制造、装配完毕通过试模后,才能发现问题。
运用Moldflow/IMOLD技术进行塑料模具设计,可以避免设计中的盲目性。
通过计算机的模拟,有目的地修正设计方案和工艺条件,克服因为经验少而造成的不良后果,缩短产品开发周期,提高生产效率。
1 Moldflow软件简介Moldflow是一款具有强大功能的专业注塑成型CAE软件,目前被广泛应用予注塑成型领域中的模拟分析。
Motdflow软件包括三部分:(1)Moldflow Plastics Advisers(产品优化顾问,简称MPA):塑料产品设计人员在设计完产品后,运用MPA软件模拟分析,在很短的时间内,就可以得到优化的产品设计方案,并确认产品表面质量。
(2)Moldflow Plastics Insight(注塑成型模拟分析,简称MPI):对塑料产品和模具进行深入分析的软件包,它可以在计算机上对整个注塑过程进行模拟分析,包括填充、保压、冷却、翘曲、纤维取向、结构应力和收缩,以及气体辅助成型分析等,使模具设计人员在设计阶段就找出未来产品可能出现的缺陷,提高一次试模的成功率。
(3)Moldflow Plastics Xpert(注塑成型过程控制专家,简称MPX):集软硬件为一体的注塑成型品质控制专家,可以直接与注塑机控制器相连,可进行工艺优化和质量监控,自动化注塑周期、降低废品率及监控整个生产过程。
2 IMOLD软件简介IMOLD是SolidWorks环境下进行注塑模三维设计的插件。
IMOLD主要的功能模块有:(1)数据准备:在模具设计前分析产品的造型,以便为后续设计提供合乎要求的三维模型。
(2)项目管理:对模具设计项目进行文档管理,可以输入特别的塑料原料及收缩率,并可以根据加工条件选择X、Y、Z3个不同方向的收缩率来设计模具。
(3)型芯、型腔设计:用于设计出型腔、型芯、侧面型芯。
模具设计-计算机辅助塑料注射模具的设计定稿 精品
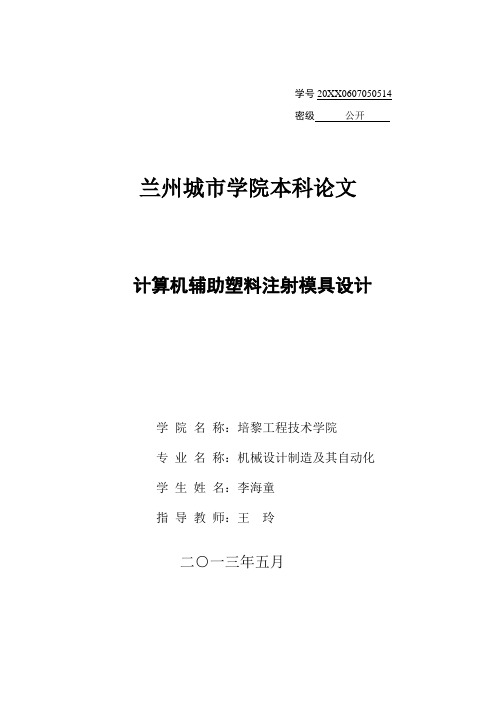
学号20XX0607050514密级公开兰州城市学院本科论文计算机辅助塑料注射模具设计学院名称:培黎工程技术学院专业名称:机械设计制造及其自动化学生姓名:李海童指导教师:王玲二○一三年五月目录第1章绪论1.1模具工业的发展现状 (1)1.2模具工业今后的主要发展方向 (1)1.4计算机辅助设计系统的发展状况和趋势 (3)1.5本课题研究的意义 (4)1.6论文的整体结构 (5)第2章注塑模具介绍2.1塑料概述 (6)2.1.1塑料的组成 (6)2.2塑料的特性 (6)2.3热塑性塑料成型的工艺特性 (6)2.4注塑成型过程简介 (6)2.5注塑模具分类 (7)2.6注塑模典型结构 (7)第3章CPU风扇支架加工工艺分析3.1塑件概况 (9)3.2材料选择 (10)第4章注射模具设计方案4.1注射机选择及注射机的校核 (11)4.1.1选择注射机 (11)4.1.2注塑机的校核 (11)4.2成型零部件设计 (13)4.2.1成型零部件分类及结构 (13)4.2.2 成型尺寸计算 (14)4.3浇注系统设计 (16)4.3.1浇注系统的作用 (16)4.3.2对浇注系统设计的具体要求 (16)4.3.3浇注系统的设计 (16)4.4侧向分型与抽心机构设计 (17)4.4.1 侧向分型与抽芯机构的分类 (18)4.4.2 侧向分型与抽芯机构的设计 (18)4.5注塑模导向机构设计 (20)4.5.1 导向机构的功能及其分类 (20)4.5.2设计要点及设计方案 (20)4.6顶出机构 (21)4.6.1顶出机构的分类 (21)4.6.2顶杆脱模机构的设计要点 (22)4.6.3设计采用方案 (22)4.7复位装置 (23)4.8冷却系统介绍 (23)4.9模具总体结构分析 (24)4.10模具用钢 (25)4.10.1塑料模具用钢的必要条件 (26)4.10.2选择钢材的条件 (26)4.10.3注塑模具常用材料 (26)4.11模具的装配与调试 (26)4.11.1 装配基准的确定 (26)4.11.2 塑料模的装配顺序 (27)结论 (28)........................................................................................................ 错误!未定义书签。
模具工艺改善方案

模具工艺改善方案前言模具是制造工业中非常关键的一环,它在机械加工、注塑成型等工序中扮演着重要的角色。
当前,制造业的竞争越来越激烈,如何提高模具的制造工艺和生产效率成为了制造企业关注的热点。
本文将介绍几种模具工艺改善方案,供读者参考。
方案一:提高模具的加工精度模具的精度要求非常高,它直接关系到最终产品的质量和企业的盈利能力。
提高模具的加工精度,可以考虑以下几种方案:1.加强设备维护。
机床、刀具等加工设备需要定期保养、检修,及时更换老化和磨损严重的部件。
这样可以保证加工设备运行的稳定性和精度。
2.优化加工工艺。
合理设置加工工艺参数,比如切削速度、进给速度、刀具转速等。
在加工时避免过快或过慢的速度和过深或太浅的切削等不良现象出现。
3.选用高质量的加工刀具。
刀具是影响加工精度的重要因素之一,选用高质量的加工刀具可以大大提高模具的加工精度。
方案二:提高模具的热处理效果模具的热处理效果决定了模具的硬度和强度,因此必须特别关注。
提高模具的热处理效果,可以考虑以下几种方案:1.优化热处理工艺。
根据不同的模具材料和形状,设置适当的热处理工艺参数,比如温度、时间、冷却速率等。
适当地延长退火时间、加快淬火冷却速率等措施可以有助于提高热处理效果。
2.提高热处理质量。
要从源头把控热处理质量,保证热处理过程中的温度稳定性和材料的均匀性。
采用高品质的热处理材料和设备也是提高热处理质量的重要措施。
3.合理的后处理。
热处理后的模具需要进行后处理,比如淬火后需要进行回火处理、冷却后需要进行去应力处理等。
合理的后处理可以使模具材料的金相组织更致密,从而提升模具的质量。
方案三:优化模具的结构设计模具的结构设计与制造工艺直接相关,优化结构设计可以提高模具的生产效率和制造成本。
以下是优化模具结构设计的建议:1.简化模具结构,压缩模具尺寸。
在不影响模具功能的前提下,尽可能压缩模具尺寸,减少材料的使用量。
简化和精简模具结构,同时采用先进的制造技术和工艺,可以大幅提升模具的制造效率。
塑胶模设计工程师职位说明

塑胶模设计工程师职位说明塑胶模设计工程师是一种专业领域的职位,该工程师应该具备专业技能和知识,以设计、开发和改进塑胶模具生产过程。
他们需要结合材料科学、机械工程和设计知识来进行塑胶模具的研究和开发。
下面我们将详细了解这个职位的描述。
职位描述塑胶模设计工程师是一种技术性职位,他们需要利用CAD 和其他设计软件来进行塑胶模具产品的设计。
他们还需要开发新的模具设计,为现有的操作流程进行改进以及出现机械故障时进行修理。
此外,该职位工程师还需要与研究部门合作,以研究不同的模具设计和技术趋势。
该工程师还需要与生产部门合作,以预测出现的生产问题并解决问题。
工作职责1.模具设计:塑胶模设计工程师的主要工作之一是利用计算机辅助设计软件进行模具的设计。
这些设计必须与客户的规格和要求相符,并符合其他标准和要求。
在设计过程中,他们需要考虑利用高质量塑料材料进行制造,并确保模具满足特定的设计要求。
2.模具改进:塑胶模设计工程师还应该有改进工作流程和设计的能力。
他们需要持续的开发和改进模具的设计,以适应不断变化的市场需求。
此外,工程师还需要开发和利用新的材料来制作模具,以提高性能和效率。
3.模具维护:该职位工程师还需要负责维护、保养和修理模具。
他们需要检查和识别模具的故障原因,然后进行修理和更换零部件。
4.完成项目:工程师需要在时间和预算的限制下完成项目,以确保模具能够按照规定的目标和要求完成。
职位要求1.教育背景:塑胶模设计工程师应该具有机械工程、计算机工程或材料科学方面的相关硕士、本科或研究生学位,并且应该执照考试并获得证书。
2.工作经验:候选人必须具有相关领域的工作经验。
如果没有经验,则应具有相关的实习经验或资格证书。
3.技能:塑胶模设计工程师应该具有设计软件、计算机辅助设计和机器操作的技能。
此外,他们还需要熟悉塑料材料、制造流程和机械设备。
4.团队合作:候选人应该具有与不同团队合作和沟通的能力,以确保项目的顺利进行。
探究塑料模具设计技术的创新实现

探究塑料模具设计技术的创新实现摘要:在现代社会中,塑料模具随处可见,因为塑料制品的成本较低,造型十分灵活,且硬度的可控性强、可靠性高,所以在人们日常生产生活中也占有着很重要的位置。
近年来,随着塑料模具应用范围的不断扩大,对其设计质量提出了较高的要求,因此,要想满足这种高要求,就要对现有的塑料模具设计技术进行相应的优化创新。
本文针对塑料模具设计技术创新现状进行着重分析,并在此基础上提出相应的实现途径,以便有关人士参考。
关键词:塑料模具;设计技术;创新现状;实现途径前言现如今,塑料制品在人们日常生产生活中发挥着极为重要的作用,随着其整体应用率的不断提升,塑料制品的综合硬件性能也在日渐增强。
尤其在塑料外形设计方面的性能,必须通过一定的创新技术才能得以实现。
因为塑料制品的应用范围十分宽泛,特别在航空航天、汽车工业等行业中,获得的应用效果也是十分显著。
因此,要想更好地满足各行业的发展需求,就要对塑料模具设计质量进行全面的加强,不仅要提高相关设计人员的专业化水平,而且还要对原有的设计技术进行相应的优化升级。
1..塑料模具设计技术创新现状分析1.1模具设计图创新信息时代下,计算机技术的应用已覆盖到各行业及各领域中,为人们日常生活提供了极大的便利条件。
其中,在塑料模具生产和开发过程中,CAE和CAD两种计算机辅助技术发挥出了最大的应用优势,通过与Pro/E和Moldflowd软件的有效结合,不仅实现了对塑料制品加工过程的仿真模拟,为模具设计结构的优化创新提供了可靠的技术保障,而且也大大提高了塑料制品的生产效率,降低了其整体加工成本。
由此可见,在塑料模具设计技术创新过程中,数控技术的合理运用十分可行,其为模具的设计创新打开了全新的视角,并做出了杰出的贡。
1.2模具设计收缩率问题的产生对于塑料模具而言,其外观质量和美观性等都需要合理的设计,才能达到相应的标准要求。
但是在设计过程中,却要对浇注系统与冷却系统对模具设计质量所造成的影响进行充分的考虑,尤其是前者中的热流道尺寸、浇口位置和浇注方式等的影响,很容易会导致塑料制品表面出现明显的熔接痕与气穴位置。
【doc】塑料模具壁厚及底板厚度计算机辅助设计

塑料模具壁厚及底板厚度计算机辅助设计塑料模具壁厚及底板厚度计算机辅助设计材料科学及工程系洪慎章王坚荣摘要本文介绍7计算机辅助设计塑料模具壁厚厦底板厚度的计算程序,通过塑料模具的使用条件,应分为刚度厦强度计算.文中提供了这个计算方法,韭举例说明程序的适用情况.语言简短,使用方便.一,概述近年来,由于塑料应用的扩大,塑料制件已广泛应用到建筑,机械,电子,仪器,仪表等各个工业领域,于是塑料成型加工机械和成型模具的增长十分迅速,高效率,自动化,大型,微型,精密,高寿命的模具在整个模具产量中所占的比重越来越犬.因此,对模具的各种设计的研究已成了专家,学者们所关注的重要课题.计算机的应用近年来发展是最快的,以计算机为叶|心的新技术革命浪潮正在世界范围内引起深刻的变化.计算机辅助设计(CAD)与计算机辅助制造(CAM)技术的应用,是工业革命以来发生的最重大的变化.毫无疑问,CAD技术对塑料模具设计也已产生了重要影响,传统的设计方法正逐渐为计算机辅助设计方法所取代.本文叙述如何利用CAD技术设计塑料模具的壁厚及底板厚度.二,成型腔壁厚及底板厚度的公式计算成型腔应具有足够的壁厚以承受塑料熔体的高压.如壁厚不够可表现为刚度不足,即产生过大的弹性变形值;也可表现为强度不足,即型腔发生塑性变形甚至断裂.模具的型腔在注射时(压制时),当型腔全部充满的瞬问,内压力达到一极大值,然后随着塑料的冷却和浇口的封闭,压力逐渐降低,在开模时接近常压.l,璧厚设计准射型腔壁厚计算以最大压力为准.强度计算的条件是各种受力形式下的许用应力(如拉仲许用应力,弯曲许用应力等).刚度计算的条件则由于模具的特殊性,可以从以下三方面加以考虑:(1)从模具型腔不发生溢等斗的角度出发当高压塑料溶体注入时,模具型腔的某些配合面会产生足以溢料的间隙,这时应根据不同塑料的最大不溢料同隙来决定其刚度条件.(2)从保证制件精度的角度出发塑料制件均有尺寸的要求,某些部位的尺寸常要求较高的精度,这就要求模具型腔有很一饨一好的刚性,印塑料注入时不会产生过大弹性变形(3)从保证制件顺利脱模出发如果塑料熔体的压力使模具产生过大的弹性变形,当变值大于制件的热收缩值时,制件的周边将被型腔紧紧包往丽难以脱出,强制顶出易使制件划伤或破裂,因此型腔允许弹性变形值应小于制件收缩值.2,常见的规嘲型腔模具型腔可分为规则和不规则二大类.对于不规则型腔,应简化成规则型腔进行计算.模具的规则型腔分为下列两大类:(1)圆形型腔圆形型腔指型腔内外壁横断面皆为圆形者,依其结构又可分为下列两种:a,整体式圆形型腔b,组合式圆形型腔.(2)矩形型腔'矩形型腔的四壁和底部都是矩形平板,同样,依其结构也可分为下列两种;a,整体式矩形型腔b,组合式矩形型腔3,璧厚计算公式理论和实践都证明:对于大尺寸的型腔,月日度不足是主要矛盾,应按剐度计算}而小尺寸的型腔在发生大的弹性变形前,箕内应力往往就超过许用应力,应按强度进行计算.至于型腔尺寸在多大以上应进行刚度计算,而在该值以下则进行强度计'算,这个舟界值取决于型腔的形状,模具材料的许用应力,型腔的允许变形量以及塑料熔体压力.因此,在分界尺寸不知道的情况下,则应分别按强度条件和刚度条件算出壁厚值,取其大者作模具的壁厚表1为各种型腔的壁厚及底板厚度的计算公式.表1所列各公式中:L一型腔侧壁长度,厘米jh-一侧壁厚度,厘米;Ll一底板受压长度,厘米h一底板厚度,厘米jh一型腔总高度,厘米;P一熔料对型腔的压力,公斤/厘米;a一型腔深度,厘米}E一弹性模量,公斤/厘米C钢为2.i×B一底板总宽度,厘米j10.)}B1一底板受压宽度,厘米r一型腔内半径,厘米;M一弯曲力矩,公厅?厘米jr~底板半径,厘米,C~常数,随L/a而不同,其值可查表.m一泊桑比(钢为.25)J~本文是利用近似公式来计算C值[6)~许用应力,公斤/厘米'(_45号钢为一3L/a160o)}一2L'/a'+966~容许变形量,毫米}一79—三,程序框图根据如上分析及使用条件的计算公式,可得出如下的计算塑料嵌具壁厚及底板厚度的程序框图I,程序变量说明圉1计算塑料横具壁厚及底板厚度的程序董圈四,程序说明N一整型量(I.2.3.4),用来判别型腔类型.P一实型量,型腔内压力,公斤/厘米zM~泊桑比.E一弹性模量.R一型腔内半径,厘米.一8O:?Lt一底板受压_长度.B一底板总宽度Bt一底板受压宽度.H一型腔腺高l崖..s1l一侧壁厚度(按刚度计算).sl2一侧壁厚度(按强度计算).寰1摸侧壁及底板辱度计算公式壹喝都位按刚座计算按强度fl-算铡r'(嚣【√器))整.壁体底式√,/一板J倒('幕E-I~一,…(√一t)组音,壁式上底二√板倒一芒一,/簪整壁体冒底式√柱——懈磊√二组缚壁合式伍底夏.√蒜板一8lG一允许变形量..lq量您登s2l一底板厚度(按刚度计算)e^一许用应力.-s22一腐板厚瘦'圭朝虽痉计算>,.6一型腔深度.sl最终壁厚值(Sl1.Sl2中大者).L一型腔内边长.s2一最终底板厚度(s21.$22中大者),MAj(M一最大弯矩.?一,.--,.1_l2,程序说明,本文设计了两种程序:带汉卡和不带汉卡,监且对带汉卡的程序谤置了两个子程序,这商个子程序是利用汉字输入变量值的,这样的设置就大大缩短了程序长度,使程序简洁,紧凑.另外,程序采用了人一机对话方式,使用者能毫无困难地进行上机演算.-.五,程序运算结果说明对两种形式(带汉卡及不带汉卡)的程序都进行了上视演算,对N不同值(N=1.2.3.4),程序均能准确无误地算出不同类型型腔的壁厚sl和底扳厚度s2.下面所举艘是不带汉卡的程亭的演算实例..No1'PLEASEENTERNlPLEASEENTERDA TA4P,{,E,R,G.A 500.00.25~2.1E+61a.60?051600.00S1;8.6Sa=6.6No2PLEASEENTERN2.PLEASEENTERDA TA500.00.252.1E+68.40.051600.0S1=5.3S2=5.2No8PLEASEENTERN一8窖一PLEASEENTERDA TA$00一2.IE-I"60.0530.01600.0.0$OO.O岛-8.2S*c1.5Nol PLEASEENTERN4 PLEASEENTERDA TA 500.02.1E+60.0515.0t1600.025.02口.015.O10.022.0SI:3.4S2;7.9P.E.G.D.A.L,MAX'!;≮措:圆麓掩敏嘲ln{P.E,G.D,A,L.L1.B,BI.H参考文献[]洪慎章<(CAD,CAEcAM在锻压生产中的应用1)).—:交通大学1985年(!]谭浩强等((FORTRAN语肓清华太学1983年,毫[3]塑料磺其设计北京啦靼工业公司轻工业出版社1鳃4年[4]塑料成型棋具成茕:科技大学轻工业出版社I982年,一[5]WHELANA等((DevelopmentsinInjectionMoul击n套》;198~F 一83—。
模具数字化设计与制造工艺
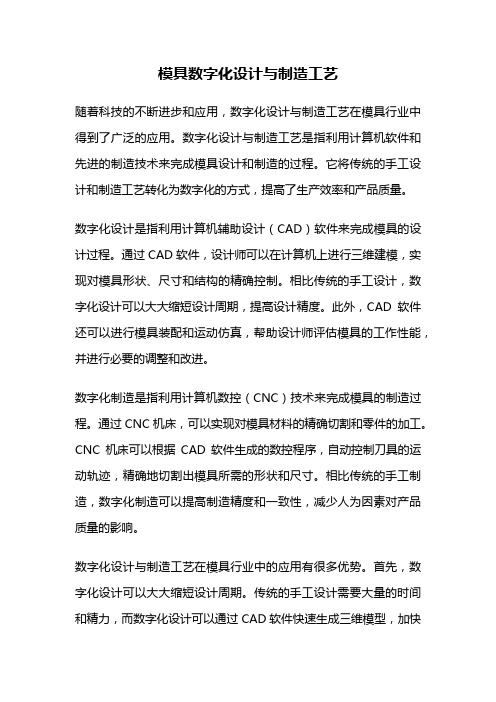
模具数字化设计与制造工艺随着科技的不断进步和应用,数字化设计与制造工艺在模具行业中得到了广泛的应用。
数字化设计与制造工艺是指利用计算机软件和先进的制造技术来完成模具设计和制造的过程。
它将传统的手工设计和制造工艺转化为数字化的方式,提高了生产效率和产品质量。
数字化设计是指利用计算机辅助设计(CAD)软件来完成模具的设计过程。
通过CAD软件,设计师可以在计算机上进行三维建模,实现对模具形状、尺寸和结构的精确控制。
相比传统的手工设计,数字化设计可以大大缩短设计周期,提高设计精度。
此外,CAD软件还可以进行模具装配和运动仿真,帮助设计师评估模具的工作性能,并进行必要的调整和改进。
数字化制造是指利用计算机数控(CNC)技术来完成模具的制造过程。
通过CNC机床,可以实现对模具材料的精确切割和零件的加工。
CNC机床可以根据CAD软件生成的数控程序,自动控制刀具的运动轨迹,精确地切割出模具所需的形状和尺寸。
相比传统的手工制造,数字化制造可以提高制造精度和一致性,减少人为因素对产品质量的影响。
数字化设计与制造工艺在模具行业中的应用有很多优势。
首先,数字化设计可以大大缩短设计周期。
传统的手工设计需要大量的时间和精力,而数字化设计可以通过CAD软件快速生成三维模型,加快设计速度。
其次,数字化制造可以提高制造精度和一致性。
通过CNC机床的精确控制,可以保证模具的形状和尺寸的一致性,提高产品的质量稳定性。
此外,数字化设计与制造还可以实现模具的自动化生产,减少人力成本,提高生产效率。
在数字化设计与制造工艺的应用过程中,还需要解决一些技术难题。
首先是CAD软件的选择和使用。
不同的CAD软件具有不同的功能和特点,需要根据具体需求选择合适的软件,并培训设计师掌握相关技术。
其次是CNC机床的操作和维护。
CNC机床是一种复杂的设备,需要专业的操作和维护人员来保证其正常运行。
此外,数字化设计与制造还需要建立完善的数据管理系统,确保设计和制造数据的安全和可追溯性。
模具的改善方案
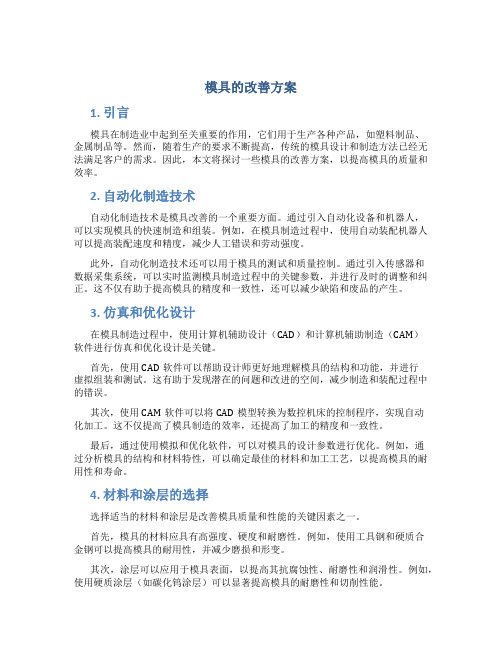
模具的改善方案1. 引言模具在制造业中起到至关重要的作用,它们用于生产各种产品,如塑料制品、金属制品等。
然而,随着生产的要求不断提高,传统的模具设计和制造方法已经无法满足客户的需求。
因此,本文将探讨一些模具的改善方案,以提高模具的质量和效率。
2. 自动化制造技术自动化制造技术是模具改善的一个重要方面。
通过引入自动化设备和机器人,可以实现模具的快速制造和组装。
例如,在模具制造过程中,使用自动装配机器人可以提高装配速度和精度,减少人工错误和劳动强度。
此外,自动化制造技术还可以用于模具的测试和质量控制。
通过引入传感器和数据采集系统,可以实时监测模具制造过程中的关键参数,并进行及时的调整和纠正。
这不仅有助于提高模具的精度和一致性,还可以减少缺陷和废品的产生。
3. 仿真和优化设计在模具制造过程中,使用计算机辅助设计(CAD)和计算机辅助制造(CAM)软件进行仿真和优化设计是关键。
首先,使用CAD软件可以帮助设计师更好地理解模具的结构和功能,并进行虚拟组装和测试。
这有助于发现潜在的问题和改进的空间,减少制造和装配过程中的错误。
其次,使用CAM软件可以将CAD模型转换为数控机床的控制程序,实现自动化加工。
这不仅提高了模具制造的效率,还提高了加工的精度和一致性。
最后,通过使用模拟和优化软件,可以对模具的设计参数进行优化。
例如,通过分析模具的结构和材料特性,可以确定最佳的材料和加工工艺,以提高模具的耐用性和寿命。
4. 材料和涂层的选择选择适当的材料和涂层是改善模具质量和性能的关键因素之一。
首先,模具的材料应具有高强度、硬度和耐磨性。
例如,使用工具钢和硬质合金钢可以提高模具的耐用性,并减少磨损和形变。
其次,涂层可以应用于模具表面,以提高其抗腐蚀性、耐磨性和润滑性。
例如,使用硬质涂层(如碳化钨涂层)可以显著提高模具的耐磨性和切削性能。
此外,根据具体的应用需求,还可以选择其他特殊材料和涂层,如陶瓷材料和防粘涂层,以满足不同的制造要求。
注塑模具计算机辅助设计的要求与步骤

注塑模具计算机辅助设计的要求与步骤随着注塑模具制造技术的不断发展和进步,计算机辅助设计已经逐渐成为注塑模具制造中必不可少的工具之一。
借助计算机辅助设计技术,注塑模具制造企业能够极大地提升生产效率和产品质量,降低生产成本和制造周期。
因此,在注塑模具制造过程中,要求设计人员具备一定的计算机辅助设计技能,能够根据所设计的产品的要求,依据一定的步骤进行计算机辅助设计,以达到生产高质量的注塑模具的目的。
一、注塑模具计算机辅助设计的要求1.掌握CAD软件的基本操作要求注塑模具设计人员能够熟练掌握AutoCAD等CAD软件的基本操作,包括文件的打开、关闭、保存等操作,掌握基本的绘图命令和编辑命令,熟练应用纹理、渐变、填充等效果,以及掌握尺寸标注、表格制作等功能,能够熟练制图并输出高品质的图纸。
2.了解注塑模具的结构和原理注塑模具是一种复杂的机械结构,设计人员需要理解注塑模具的结构组成和原理,掌握各种复杂部件的构造和工作原理,并且能够预测设计中可能出现的问题,提前进行优化和改进。
3.具有高超的三维建模技能注塑模具的设计需要使用三维建模技术,注塑模具设计人员需要具备高超的三维建模技能,能够准确、快速地创建三维模型,进行数字化设计和优化。
4.熟练掌握仿真软件利用仿真软件进行注塑模具设计可以有效预测在生产中可能出现的问题,作为设计人员需要掌握仿真软件的操作原理,能够进行预测、分析和优化。
二、注塑模具计算机辅助设计的步骤1.确定产品的要求和特性注塑模具设计的第一步是确定产品的要求和特性,根据产品的用途、使用条件、尺寸和形状等方面的要求来确定注塑模具的设计参数。
2.设计注塑模具的三维模型根据产品的要求和特性,利用三维建模软件,创建注塑模具的立体模型。
在进行模型设计时需要考虑模具的结构和组成,模具的开口方向和动态点位,以及各种复杂部件的内部结构和工作原理等各种因素,确保模具在生产中能够高效准确地完成注塑模具的制造。
3.进行数值模拟分析在完成注塑模具的三维建模后,需要利用分析软件进行数值模拟,对模具的受力情况、温度分布等进行分析,以预测制造过程可能出现的问题。
为计算机辅助设计工具用于塑料注射模具设计的标准元件库设计

用计算机辅助设计工具对塑料注射模具设计的标准元件库设计Y. –S. Ma* G. A. Britton, S. B. Tor,E. Gunawan C. H. Lee大学机械与生产工程,南洋理工大学南阳大道,新加坡*电子邮件:mysma@.sg摘要本文介绍了设计一个三维参数化标准件库(SCL)的基础上的计算机辅助设计工具。
这个库可以有效地生成标准件自动从不同的供应商的基础上构造实体几何(CSG)的方法。
成组技术(GT)方法适用于控制几何配置的组件模型:在内部没有使用预先定义的模板时,用一个原型已经开发的有可行的设计与模块化特征基元进行设计。
这个新的设计已经证明相比现有的库具有预期的优势。
关于这个问题未来的研究与发展是值得被探讨的。
1简介在塑料注射成型工业,市场是越来越小。
这种情况对模具计算机辅助设计工具形成了一个巨大的挑战。
一个注塑模具标准件由许多不同的部件,诸如模架板,定位圈,浇道衬套,顶针,软管接头,插头。
用相似的结构建立模具使之适应一定的标准化的需要。
这允许标准组件集中生产,从而降低制造成本。
许多公司,如DME, HASCO, FUTABA, MISUMI,都有提供服务的标准模架的模具产业。
一些计算机辅助设计系统的注射模设计有标准纳入模具单位的库,这被认为是这种软件的一个最重要的特点。
然而,如果库的目的是使操作浓缩和有效,那么大量数据存储和开发时间需要交给计算机辅助设计系统。
因此需要一个有效的和有效率的设计标准件库(SCL)。
2文献综述传统的塑料模具设计研究工作集中在概念设计早期工程的决定[ 1,2 ]。
最近,模具结构设计工具被强调。
金等人[ 3]提出了一个自动销顶针设计系统,它由四个模块组成,计算针的推力,最小尺寸的顶针,顶针和数量,以及设计的喷射格栅。
李等人[ 4]和福等人[ 5 ]的在产生模具系统的基础上建立一定的实用程序设计。
他们的努力,涉及多个功能子系统,如进料,冷却,脱模,和标准工具的子系统。
模具加工工艺改善方案
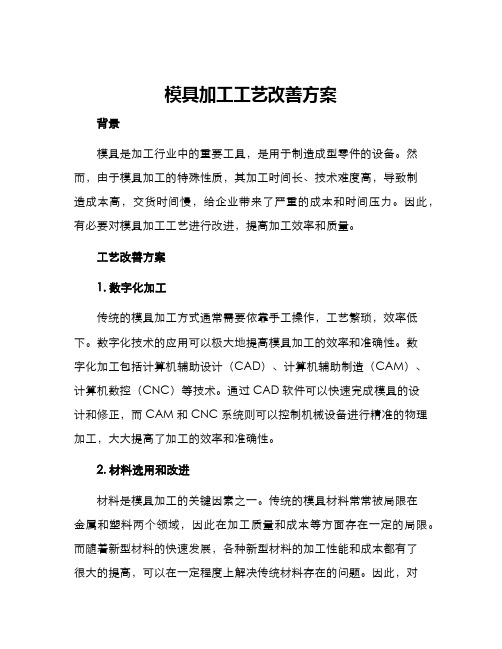
模具加工工艺改善方案背景模具是加工行业中的重要工具,是用于制造成型零件的设备。
然而,由于模具加工的特殊性质,其加工时间长、技术难度高,导致制造成本高,交货时间慢,给企业带来了严重的成本和时间压力。
因此,有必要对模具加工工艺进行改进,提高加工效率和质量。
工艺改善方案1. 数字化加工传统的模具加工方式通常需要依靠手工操作,工艺繁琐,效率低下。
数字化技术的应用可以极大地提高模具加工的效率和准确性。
数字化加工包括计算机辅助设计(CAD)、计算机辅助制造(CAM)、计算机数控(CNC)等技术。
通过CAD软件可以快速完成模具的设计和修正,而CAM和CNC系统则可以控制机械设备进行精准的物理加工,大大提高了加工的效率和准确性。
2. 材料选用和改进材料是模具加工的关键因素之一。
传统的模具材料常常被局限在金属和塑料两个领域,因此在加工质量和成本等方面存在一定的局限。
而随着新型材料的快速发展,各种新型材料的加工性能和成本都有了很大的提高,可以在一定程度上解决传统材料存在的问题。
因此,对于不同类型的模具,必须根据其加工目标和要求来灵活选择材料,并不断推进新材料的研发和应用。
3. 加工工艺改进在数字化加工技术的基础上,还需要进行加工工艺方面的改进。
在加工工艺方面,主要包括刀具加工、成型加工、表面处理等。
在刀具加工方面,可以采用高硬度刀具和多刃刀具,以提高加工速度和加工质量。
在成型加工方面,可以采用多工位多道次加工和多层次材料流加工,以提高成型效率和成型质量。
在表面处理方面,可以采用喷砂、抛光等工艺,以提高产品表面的光洁度和美观度。
4. 质量检验和改进质量检验是制造流程中非常重要的环节。
传统的模具加工质量检验主要依靠人工目测,精度及其不稳定。
而通过数字化技术的应用,可以实现动态检测和自动记录等功能,实现质量控制的有效监管。
同时还可以采用在线故障诊断系统和数据挖掘分析技术,及时发现生产中的问题和隐患,进行改进。
结论模具加工是制造行业的重要一环,而在现代制造中数字化技术的应用已成为必然趋势。
- 1、下载文档前请自行甄别文档内容的完整性,平台不提供额外的编辑、内容补充、找答案等附加服务。
- 2、"仅部分预览"的文档,不可在线预览部分如存在完整性等问题,可反馈申请退款(可完整预览的文档不适用该条件!)。
- 3、如文档侵犯您的权益,请联系客服反馈,我们会尽快为您处理(人工客服工作时间:9:00-18:30)。
文章编号:1001-4934(2000)01-0073-06计算机辅助塑料模具设计和工艺改进项辉宇1,孙 胜2,赵国群2(1.山东工业大学机械学院C AD中心,山东济南 250061;21山东工业大学模具中心,山东济南 250061)摘 要:介绍了塑料注射成型工艺中,影响制品质量的主要工艺参数,总结并补充了这些参数的选择原则,实例说明了采用计算机辅助流动模拟技术对于塑料模具结构设计和工艺参数优化配置的指导作用。
关键词:塑料;模具;计算机辅助工程中图分类号:TG241 文献标识码:AAbstract:Based on com puter aided simulation,this paper introduces the main process parame2 ters which determine the quality of injection parts as well as the defects prediction method.This paper als o analyzes an injection m olding case with quality defects,and points out the method to s olve the problem by mean of m old structure im provement and process parameter recon figuration.K ey w ords:plastics;m old;com pute aided engineering0 引言对于模具设计者来讲,如果能在设计方案构思阶段,预测出塑料熔体在型腔内的流动情况,以便尽早发现问题,修改设计图样,而不是等待模具制造完成,试模后发现问题进行返修,将极大地提高模具的设计水平和一次试模成功率。
因此注射流动过程C AE软件的出现,不仅是注塑模具设计和制造程序上的一次变革,而且对减少模具的返修率,提高模具设计水平和注塑制品的质量,都具有重要意义。
注塑零件的质量优劣受其成型过程中的工艺条件的影响很大。
注射成型的工艺条件主要包括注射量、注射温度、注射压力、注射速度等。
工艺参数合理与否,对制品的质量影响很大,如图1所示[3],注射过程中,如果注射温度过低,就需要较大的注射压力来迫使塑料填满型腔;如果注射温度过高则会引起塑料的化学分解;如果注射压力过低,则容易出现填充不足,发生短射现象;而压力过高,则易产生飞边。
因此合理的搭配注射工艺参数是关系注射成型质量的重要因素。
合理的工艺参数必须同时考虑特定的模具结构和所采用的树脂材料。
目前多数厂家采用经验加试模定工艺的方法,由于缺乏量化指标指导,有时会出现废品率高和质量不稳定等缺陷,特别是对于精密注射成型,这种方法显然不适应现代生收稿日期:1999-06-29作者简介:项辉宇(1966~),男,讲师。
产对制品高质量高效率的要求。
运用注塑模C AE 技术,设计师能在模具制造之前,预测所设图1 注射温度和注射压力的关系计的模具在采用某种塑料在某种注射机注射成型时的结果,从中发现问题并作出修改,同时还可以获得上述条件下可采用的合理的工艺参数,对注射工艺提供指导性意见。
随着塑料注射成型工艺在汽车、摩托车、家用电器、仪器仪表等行业中的广泛运用,有关注射过程规律的把握和注射工艺参数优化的配置方面的研究在国际上得到了广泛的重视,取得了大量成果,并且推出了一些有代表性的软件系统应用于工程实践[1,2],如美国AC -TECH 公司著名的注塑模C AE 软件C -M O LD ,澳大利亚M O LDF LOW 公司的M O LDF LOW 等。
C -M O LD [3]建立在K.K.Wang 教授领导的CI MP (C ornell Injection M old 2ing Project )近20年的理论和实验研究工作的基础上,提供了模拟非等温状态下,不可压缩性粘性聚合物熔体在流道或模腔内作一般Hele -Shaw 流动时的充模流动和热动力学过程的分析程序,采用混合的有限元、有限差分方法求解压力场和温度场,并采用控制体积法跟踪流动熔体的前沿位置。
分析可得出一系列对于评价和改进模具结构和成型工艺的有价值的信息,供设计师和工艺师在进行模具设计和制定工艺参数时参考。
1 主要工艺参数及选用原则影响注射成形工艺质量的因素很多,C -M O LD 在大量实验基础上,提出了影响注射成型工艺质量的一些工艺参数及这些参数的选用原则[4],本文进行了综合,并对其中一些主要参数加以说明。
1.1 注射温度注射温度是注射成型过程中最重要的技术参数之一。
温度过低,聚合物可能熔化不完全或者粘度太高而使得流动性能变差。
反之如果温度太高,聚合物又容易产生分解,特别是象POM 和PVC 类树脂,特定树脂的注射成型温度和对应的模具温度可以从材料供应商处得到,表1列出了几种常用工程塑料的注射温度和相应模具温度的参考值。
实际上不同牌号的同一类聚合物的熔融温度和对应的模具温度也稍有不同,对于精密塑料件注射成型,应选用供应商提供的推荐值。
生产过程中,型腔表面温度一般高于冷却介质的温度。
因而,冷却介质的温度一般比相应模具温度低10~20℃,如果模具温度是40~50℃或者更高,则应考虑在模具固定板和模具之间增加隔热装置,以节省能源并增强工艺的稳定性。
表1[4]推荐了各种几种塑料对应的模具的低限温度,对零件表面质量要求较高的,模具温度应相应提高一些。
1.2 注射压力注射压力是注射成型过程中又一个重要的工艺参数。
注射压力指注射过程中,注射机螺杆对塑料施加的压力,用以克服流道系统和型腔等处产生的流动阻力。
在一定注射温度下,注射压力的大小受注射零件的厚度、浇口尺寸、流动长度、制作表面复杂程度及注射填充时间的影响。
一般而言,零件厚度越小、浇口截面越狭窄、流动长度越长、表面越复杂所需的注射压力越大。
而注射填充的时间对注射压力的影响比较复杂,相对太短或太长的注射时间都将加大对注射压力的需求,选择合理的注射时间对注射成型的质量影响较大,通常在生产中,需反复试模获得。
目前可以采用C AE软件系统计算获得。
表1 常用工程塑料注射温度和对应模具温度材料注射温度℃注射温度推荐值℃模具温度℃模具温度推荐值℃结晶温度℃ABS200-27023050-8060105PA12230-30022570-11080190PA6230-30025570-11080185PA66270-32029070-11080235P BT220-28025040-8060200PC280-33030570-11070144PET280-33030080-120100220POM180-23520550-9070130PP200-28023020-7040135PS180-28023020-7050100PVC160-22019020-70401001.3 设置螺杆行程转换开关位置螺杆行程转换开关位置是指螺杆的位置处于注射向保压过程转换的位置,缓冲距离指从转换开关位置到螺杆行程的终点,缓冲距离内应包含足量的塑料以保证后注射阶段的少量塑料进入型腔,以补偿由于熔体冷却而引起的收缩,否则补偿量不足,制品表面易产生缩痕。
1.4 设置注射速度及排气注射速度高,有助于流动阻力的降低,并可提高熔接痕处的强度,但是,注射速度的提高,必须设置好排气孔。
排气不畅,易在型腔内产生气穴,当型腔内温度和压力都很高时,易引起烧痕和聚合物的化学分解和充不足现象。
一些注射流动模拟软件提供了熔接痕和气穴产生的位置预测方法,设计时应予以参考。
另外,应注意经常清洗模具型芯、型腔表面及排气系统,特别是象PVC和ABSΠPVC之类的材料。
注射成型生产中,注射工艺参数的合理选用对于制品的质量起着重要的作用,目前广泛采用的试模定工艺的方法显然不适应对注塑零件高质量、低成本的要求。
注射工艺参数的合理配置必须将特定的模具结构和工艺参数结合一起来考虑,这种要求对于传统的以经验为主的选取方法是难以统筹的。
以计算机仿真和模拟技术为主要表征的C AE技术可较好地预测成型结果,并提供有价值的工艺参数。
这些优点体现了现代并行设计思想,受到了广泛重视。
2 设计实例本文采用C-M O LD软件系统对某家电产品的过滤网架在生产过程中经常出现的问题,进行了充模过程流动模拟,分析了缺陷原因,在以下几个方面提出了改进方案:浇口的数目和位置;预测可能存在的气穴位置,以确定正确的排气位置;预测制品中的分子流动或纤维取向并使之处于预先设想的状态;提供注射机注射过程中螺杆运动速度曲线指导注射工艺。
过滤网架采用聚丙稀树脂注射成型,零件结构对称,长约200mm,宽约40mm,高约25mm,表面分布有许多方孔,采用双点浇口对称分布,其成型过程主要工艺参数如下:设备最大锁模力 150t;设备最大注射量 286cm3;设备最大注射速率 7100cm3Πs;环境温度 24.50℃;塑料注射温度 230℃;注射时间 1.6s。
塑料过滤网架对外表面质量要求不高的零件,零件中方形通孔较多,壁厚较均匀,一般为2mm,采用进口PP.7728聚丙稀材料,易发生的缺陷主要是孔间薄壁填充量不足,有时表面有缩痕,另外零件边缘位置有时出现焦化痕。
注射成型件表面质量不均匀和产生缩痕的主要原因有两方面:一方面是由于保压阶段补缩量不足;另一方面,在注射过程中,聚合物熔体在流经型腔不同截面时流速不均匀,造成制件不同部位质量不匀、分子纤维取向不统一也是造成这种缺陷的一个主要原因。
制件边缘位置出现焦化痕则是由于部分工艺参数和结构不合理,如注射压力过高,熔体流动速度太快,部分边缘位置排气不畅,造成了这些部位高温高压气体的瞬间火花,产生了焦化痕。
解决填充量不足和表面缩痕这个问题的关键有两点,一是合理的选择流道和浇口的尺寸及位置,二是选择根据模拟结果得到合理的注射参数,如注射温度、注射时间、注射压力和优化的螺杆运动曲线等。
流动场合理与否,可根据流动场的均匀性来判断。
所谓流场均匀,即流动前沿速度MFV(Melt Front Velocity)在注射过程不同时刻,流经不同截面时保持均匀,这样制品质量好,不易出现缩痕等缺陷,同时熔体在型腔内的流动场均匀,保证了合理的聚合物分子纤维取向,可获得较高的零件表面质量和机械性能。
该零件机构对称,长度较长而宽度较小,为减少注射压力,采用双点侧浇口对称分布,浇口在中间部位(图2),这样可缩短流动长度,降低注射压力。
分析前,先构造零件中面的三维模型,中面模型的构造可采用两种方法,一种方法是在通用C AD环境中完成零件的设计,提取出零件的中面模型,然后通过合适的数据接口转换成C-M O LD可接受的数据模型;另一种方法是利用C-M O LD中的M ODE2 LER模块直接构造零件中面模型。