高速切削加工技术的现状与发展
高速高效切削加工技术的现状及发展趋势

高速高效切削加工技术的现状及发展趋势一、前言目前,我国已成为世界飞机零部件的重要转包生产国,波音、麦道、空客等世界著名飞机制造公司都在我国转包生产从尾翼、机身、舱门到发动机等各种零部件,这些飞机零部件的加工生产必须采用先进的加工装备和加工工艺。
为此,国内各飞机制造公司均进行了大规模的技术改造,引进了大量国外先进的加工装备,使我国的飞机制造业设备的数控化率越来越高。
与此同时,大量高速、高效、柔性、复合、环保的国外切削加工新技术不断涌现,使切削加工技术发生了根本的变化。
刀具在航空航天加工领域的应用技术进入了以发展高速切削、开发新的切削工艺和加工方法、提供成套技术为特征的新阶段。
与此形成鲜明对比的是,我国的装备制造业和以制造业为主要服务对象的传统的工具工业却无法满足航空航天工业对现代制造装备和先进加工工艺的要求。
下面结合我国航空航天工业加工技术的现状及发展趋势,着重介绍我国高效、高速切削刀具的生产应用情况,对我国工具工业的发展现状和存在的问题提出自己的看法。
二、航空航天工业加工技术的现状及发展趋势1.航空结构件材料的发展趋势及其特点①以整体件为代表的铝合金结构件为了提高零件的可靠性、降低成本和减轻重量,传统的铆接结构逐步被整体薄壁的机加工结构件所代替。
这类零件由于大部分是用整体实心铝合金材料制成的薄壁、细筋结构件,70%~95%的材料要在加工中去除掉,而高速切削产生的热量少、切削力小、零件变形小,因此提高生产效率的唯一途径是采用四轴或五轴联动机床进行高速铣削加工。
②以钛基和镍基合金零件为代表的难切削材料零件由于钛(镍)合金具有比强度高、热强度好、化学活性大等特点,目前飞机发动机重要部件采用钛基和镍基合金材料的逐渐增多。
采用高速切削后,其切削速度可提高到100m/min以上,为常规切削速度的10倍。
这类材料的加工特点是:切削力大、切削温度高、加工硬化和粘刀现象严重、刀具易磨损。
③以碳纤维复合材料零件为代表的复合材料结构件复合材料现已成为新一代飞机机体结构主要材料之一,如飞机上的大型整体成形的翼面壁板、带纵墙的整体下翼面等。
我国高速加工技术现状及发展趋势
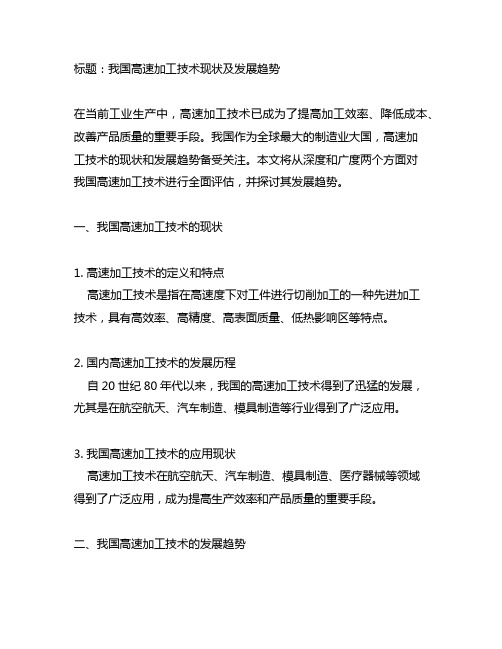
标题:我国高速加工技术现状及发展趋势在当前工业生产中,高速加工技术已成为了提高加工效率、降低成本、改善产品质量的重要手段。
我国作为全球最大的制造业大国,高速加工技术的现状和发展趋势备受关注。
本文将从深度和广度两个方面对我国高速加工技术进行全面评估,并探讨其发展趋势。
一、我国高速加工技术的现状1. 高速加工技术的定义和特点高速加工技术是指在高速度下对工件进行切削加工的一种先进加工技术,具有高效率、高精度、高表面质量、低热影响区等特点。
2. 国内高速加工技术的发展历程自20世纪80年代以来,我国的高速加工技术得到了迅猛的发展,尤其是在航空航天、汽车制造、模具制造等行业得到了广泛应用。
3. 我国高速加工技术的应用现状高速加工技术在航空航天、汽车制造、模具制造、医疗器械等领域得到了广泛应用,成为提高生产效率和产品质量的重要手段。
二、我国高速加工技术的发展趋势1. 技术创新推动高速加工技术的发展随着科技的进步和不断创新,高速加工技术将会更加高效、精密、稳定,能够满足更加复杂的加工需求。
2. 智能制造与高速加工技术的融合智能制造将成为未来高速加工技术发展的重要方向,通过智能化、自动化技术,提高生产效率和产品质量。
3. 绿色制造与高速加工技术的结合高速加工技术在减少碳排放、节能减排方面将会有更大的发展空间,应用于绿色制造领域。
4. 人工智能在高速加工技术中的应用随着人工智能技术的快速发展,其在高速加工技术中的应用将会成为新的发展趋势,将提高生产效率和产品质量。
三、总结与展望我国高速加工技术在不断发展创新的过程中,已经取得了令人瞩目的成绩,但与发达国家相比仍有一定差距。
在未来发展中,需要加大科技投入力度,加强技术研发和创新,培养更多高端技术人才,不断提升我国的高速加工技术水平,推动制造业向高质量发展。
个人观点:高速加工技术作为先进制造技术的代表,将会对我国工业生产产生深远影响。
在未来,我相信随着科技的进步和不断创新,我国的高速加工技术将不断迈向更加高效、精密、稳定的发展方向,并为我国制造业的转型升级和智能制造提供重要支撑。
高速切削加工技术及其进展
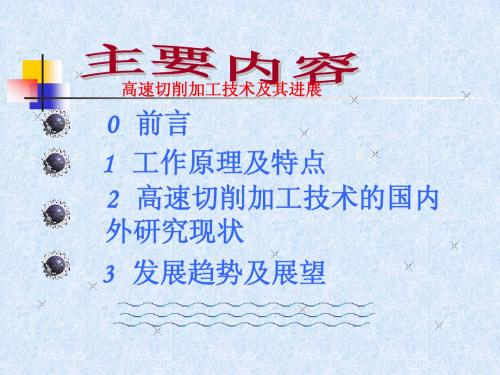
1 工作原理及特点
1.1 高速切削加工的提出
1.高速切削加工技术 于20世纪30年代由德 国 人 Salomon 提 出 。 大量铣削试验发现, 随切削速度不断增加 ,切削温度上升到一 峰值,随着切削速度 进一步提高,切削温 度达到峰值后反而下 降。 2.随上世纪80 年代末 和90 年代初数控机床 和刀具技术的进步, 开始应用并快速发展 到广泛应用。
1 工作原理及特点
1.3 高速切削加工的特点
加工精度高 切削力减少 降低了切削热对 被加工工件的影 响 可以以切代磨 刀具寿命是制约 高速切削进一步 发展的主要因素 之一。
图2 高速加工的一般特征
2 高速切削加工技术的国内外研究现状
2.1 高速切削刀具材料
涂层刀具,主要 有硬涂层、软涂 层和金刚石膜涂 层。 立方氮化硼 聚晶金刚石 金属陶瓷刀具 陶瓷刀具
图3 高速加工技术的研究体系
2 高速切削加工技术的国内外研究现状
2.2 高速切削切屑形成及其变形机理 主要集中在淬硬 的研究
钢、高温高强度 钢、钛合金等难 加工材料高速切 削切屑形成机理 的研究。 锯齿形切屑形成 机理---两大理论 体系,即突变剪 切或绝热剪切理 论和周期性脆性 断裂理论。
图3 高速加工技术的研究体系
高速切削加工技术及其进展
0 前言 1 工作原理及特点 2 高速切削加工技术的国内 外研究现状 3 发展趋势及展望
0 前言
1. 生产力构成中, 制造技术的
作用往往占60% 左右
2. 工业发达国家制造技术发展
计划 ,如美国的先进制造技 术计划(AMT)、关键技术( 制造)计划,日本的智能制造 系统国际合作计划(IMS), 德国的制造 2000 计划等。 3.现代切削加工技术的重要发 展方向 :以高生产率和高加 工精度与表面质量等特点著称 的高速切削技术
高速加工的发展趋势
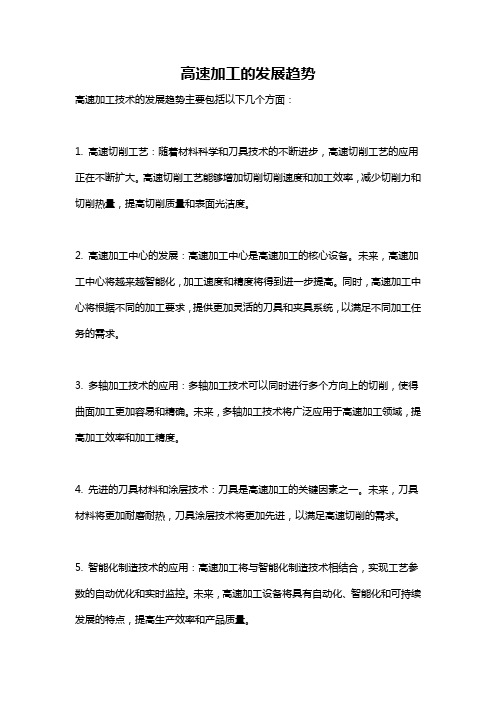
高速加工的发展趋势
高速加工技术的发展趋势主要包括以下几个方面:
1. 高速切削工艺:随着材料科学和刀具技术的不断进步,高速切削工艺的应用正在不断扩大。
高速切削工艺能够增加切削切削速度和加工效率,减少切削力和切削热量,提高切削质量和表面光洁度。
2. 高速加工中心的发展:高速加工中心是高速加工的核心设备。
未来,高速加工中心将越来越智能化,加工速度和精度将得到进一步提高。
同时,高速加工中心将根据不同的加工要求,提供更加灵活的刀具和夹具系统,以满足不同加工任务的需求。
3. 多轴加工技术的应用:多轴加工技术可以同时进行多个方向上的切削,使得曲面加工更加容易和精确。
未来,多轴加工技术将广泛应用于高速加工领域,提高加工效率和加工精度。
4. 先进的刀具材料和涂层技术:刀具是高速加工的关键因素之一。
未来,刀具材料将更加耐磨耐热,刀具涂层技术将更加先进,以满足高速切削的需求。
5. 智能化制造技术的应用:高速加工将与智能化制造技术相结合,实现工艺参数的自动优化和实时监控。
未来,高速加工设备将具有自动化、智能化和可持续发展的特点,提高生产效率和产品质量。
总体来说,高速加工的发展趋势是向着高效、智能和精准的方向发展,以满足不断变化的制造需求。
超高速切削现状和趋势
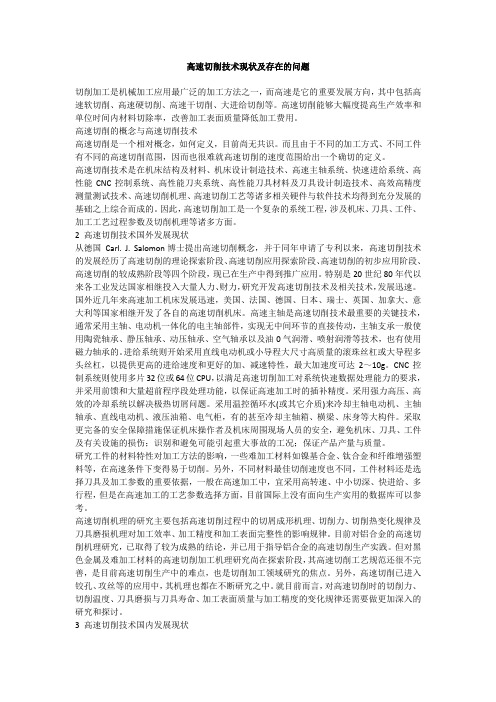
高速切削技术现状及存在的问题切削加工是机械加工应用最广泛的加工方法之一,而高速是它的重要发展方向,其中包括高速软切削、高速硬切削、高速干切削、大进给切削等。
高速切削能够大幅度提高生产效率和单位时间内材料切除率,改善加工表面质量降低加工费用。
高速切削的概念与高速切削技术高速切削是一个相对概念,如何定义,目前尚无共识。
而且由于不同的加工方式、不同工件有不同的高速切削范围,因而也很难就高速切削的速度范围给出一个确切的定义。
高速切削技术是在机床结构及材料、机床设计制造技术、高速主轴系统、快速进给系统、高性能CNC控制系统、高性能刀夹系统、高性能刀具材料及刀具设计制造技术、高效高精度测量测试技术、高速切削机理、高速切削工艺等诸多相关硬件与软件技术均得到充分发展的基础之上综合而成的。
因此,高速切削加工是一个复杂的系统工程,涉及机床、刀具、工件、加工工艺过程参数及切削机理等诸多方面。
2 高速切削技术国外发展现状从德国Carl. J. Salomon博士提出高速切削概念,并于同年申请了专利以来,高速切削技术的发展经历了高速切削的理论探索阶段、高速切削应用探索阶段、高速切削的初步应用阶段、高速切削的较成熟阶段等四个阶段,现已在生产中得到推广应用。
特别是20世纪80年代以来各工业发达国家相继投入大量人力、财力,研究开发高速切削技术及相关技术,发展迅速。
国外近几年来高速加工机床发展迅速,美国、法国、德国、日本、瑞士、英国、加拿大、意大利等国家相继开发了各自的高速切削机床。
高速主轴是高速切削技术最重要的关键技术,通常采用主轴、电动机一体化的电主轴部件,实现无中间环节的直接传动,主轴支承一般使用陶瓷轴承、静压轴承、动压轴承、空气轴承以及油0气润滑、喷射润滑等技术,也有使用磁力轴承的。
进给系统则开始采用直线电动机或小导程大尺寸高质量的滚珠丝杠或大导程多头丝杠,以提供更高的进给速度和更好的加、减速特性,最大加速度可达2~10g。
超高速切削的发展现状
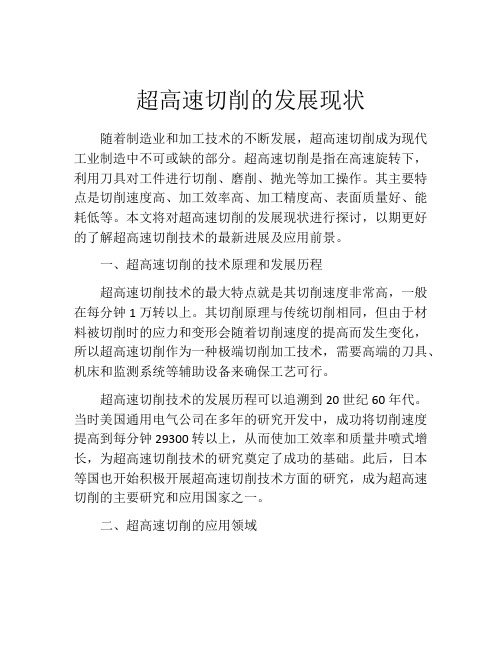
超高速切削的发展现状随着制造业和加工技术的不断发展,超高速切削成为现代工业制造中不可或缺的部分。
超高速切削是指在高速旋转下,利用刀具对工件进行切削、磨削、抛光等加工操作。
其主要特点是切削速度高、加工效率高、加工精度高、表面质量好、能耗低等。
本文将对超高速切削的发展现状进行探讨,以期更好的了解超高速切削技术的最新进展及应用前景。
一、超高速切削的技术原理和发展历程超高速切削技术的最大特点就是其切削速度非常高,一般在每分钟1万转以上。
其切削原理与传统切削相同,但由于材料被切削时的应力和变形会随着切削速度的提高而发生变化,所以超高速切削作为一种极端切削加工技术,需要高端的刀具、机床和监测系统等辅助设备来确保工艺可行。
超高速切削技术的发展历程可以追溯到20世纪60年代。
当时美国通用电气公司在多年的研究开发中,成功将切削速度提高到每分钟29300转以上,从而使加工效率和质量井喷式增长,为超高速切削技术的研究奠定了成功的基础。
此后,日本等国也开始积极开展超高速切削技术方面的研究,成为超高速切削的主要研究和应用国家之一。
二、超高速切削的应用领域随着超高速切削技术的不断发展和完善,其在航空航天、汽车制造、机械制造等领域的应用越来越普及。
目前,超高速切削技术已经广泛应用于以下几个领域:1、航空航天领域在航空航天领域,超高速切削技术被广泛应用于飞机发动机叶片、航空轴承等零部件的加工中。
由于这些零部件具有较高的加工难度和质量要求,而超高速切削技术的高加工效率和高加工质量正好能够满足这些要求。
2、汽车制造领域在汽车制造领域,超高速切削技术被广泛应用于汽车发动机零部件、车轮、减震器等汽车零部件的加工中。
由于该技术具有高效率、高质量、高精度的特点,能够大大提高汽车零部件的生产效率、降低生产成本。
3、机械制造领域在机械制造领域,超高速切削技术被广泛应用于高精度、高难度的零部件加工中。
由于该技术能够大大提高加工效率和精度,能够满足顾客对高精度、高质量零部件的要求,从而提高制造业的竞争优势。
高速切削加工技术介绍

美国于 1960 年前后开始进行超高速切削试验。试验将刀具装在加农炮里,从滑台上射向工件;或将工件当作子弹射向固定的刀具。 1977 年美国在一台带有高频电主轴的加工中心上进行了高速切削试验,其主轴转速可以在 180 ~ 18000r / min 范围内无级变速,工作台的最大进给速度为 7 . 6m / min。
1979 年美国防卫技术研究总署( DARPA )发起了一项“先进加工研究计划”,研究切削速度比塑性波还要快的超高速切削,为快速切除金属材料提供科学依据。
在德国, 1984 年国家研究技术部组织了以 Darmstadt 工业大学的生产工程与机床研究所 PTW )为首,包括 41 家公司参加的两项联合研究计划,全面而系统地研究了超高速切削机瓜刀具、控制系统以及相关的工艺技术,分别对各种工件材料(钢、铸铁、特殊合金、铝合金、铝镶铸造合金、铜合金和纤维增强塑料等)的超高速切削性能进行了深入的研究与试验,取得了切削热的绝大部分被切屑带走国际公认的高水平研究成果,并在德国工厂广泛应用,获得了好的经济效益。日本于 20 世纪 60 年代就着手超高速切削机理的研究。日本学者发现在超高速切削时,工件基本保持冷态,其切屑要比常规切屑热得多。日本工业界 35善于吸取各国的研究成果并及时应用到新产品开发中去,尤其在高速切削机床的研究和开发方面后来居上,现已跃居世界领先地位。进人 20 世纪 90 年代以来,以松浦( Matsuora )、牧野 ( Makino )、马扎克( Mazak )和新泻铁( Niigata )等公司为代表的一批机床制造厂,陆续向市场推出不少超高速加工中心和数控铣床,日本厂商现已成为世界上超高速机床的主要提供者.
2 高速切削刀具
刀具是实现高速加工的关键技术之一。生产实践证明,阻碍切削速度提高的关键因素是刀具能否承受越来越高的切削温度在萨洛蒙高速切理研究和高速切削试验的不断深人,证明高速切削的最关键技术之一就是所用的刀具。舒尔兹教授在第一届德国 ― 法国高速切削年会( 1997 年)上做的报告中指出:目前,在高速加工技术中有两个基本的研究发展目标,一个是高速引起的刀具寿命问题,另一个是具有高精度的高速机床.
高速切削刀具的发展现状

质合金焊接刀具的应用仍十分普遍;铝高速钢、粉末冶金高速钢的使用很少;由于市场供应的国产高速钢质量下滑,使含钴高速钢刀具品质较差;高性能硬质合金及细(超细)颗粒硬质合金较少,几乎无专用牌号。
我国的刀具涂层技术与国外相比差距较大,金刚石膜涂层技术尚处于研发阶段;尚无商品化TiCN涂层产品;TiAIN、MoS2涂层、纳米涂层等新技术尚待研究;具有优良耐磨性、抗高温、抗热震性的高速切削刀具材料也函待开发。
国内对于陶瓷刀具的研究较为充分,已基本建立了融切削学和陶瓷学为一体的、基于切削可靠性的陶瓷刀具材料设计、研究理论新体系。
国产氧化铝基陶瓷刀具已有近20个品种(部分产品性能及用途见表3) ,氮化硅基陶瓷刀具已有近10 个品种,陶瓷刀具的生产能力也较大。
目前陶瓷刀具的研发水平已达到国际先进水平,陶瓷刀具的性能水平也不低于国外同类产品。
已开发成功陶瓷—硬质合金复合刀片、梯度功能陶瓷刀片、多种采用协同增韧机理的陶瓷刀具等国外尚未见报道的新产品。
目前与国外的差距主要表现在制造工艺水平较低,高精度陶瓷刀片和某些品种的陶瓷刀具(如加入氮化物的陶瓷刀具)质量欠佳,陶瓷刀具的推广应用也不如发达国家普遍。
国内已开发出可分别用于车削、镗削、铣削等加工领域的多种不同CBN含量的CBN刀具和不同颗粒尺寸的PCD刀具,其中CBN刀具主要用于高速加工淬硬钢、高硬铸铁及某些难加工材料,PCD刀具则用于加工铝合金。
不足之处是品种规格不够齐全,某些产品质量欠佳,推广应用尚不普遍。
高速切削的技术装备作者:佚名文章来源:网络转载点击数: 112 更新时间:2006-4-24内容摘要: 高速切削(High Speed Cutting-HSC)概念起源于德国切削物理学家Carl Salomn的著名切削实验及其物理引伸。
他认为一定的工作材料对应有一个临界切削速度,其切削温度最高。
在常规切削范围内切削温度Tv随着切削速度Vc的增大而提高,当切削速度到达临界切削速度后,切削速度再增大,切削温度反而下降(见图1C区),所以越过B区,在高速区C区进行切削,则可用现有的刀具进行高速切削,从而大大地减少切削工时,成倍提高机床的生产率,同时提高加工质量管理,并可用于切削各种硬、韧性、难加工材料的工件。
超高速切削的发展现状

超高速切削的发展现状超高速切削是一种先进的切削加工技术,采用高速转速和小切削深度进行切削,能够有效提高切削效率和加工精度。
本文将对超高速切削的发展现状进行详细介绍。
超高速切削技术的发展可以追溯到20世纪60年代,当时由于切削过程容易产生几何形状的误差和表面质量问题,因此一直未能得到广泛应用。
随着计算机数控技术和精密制造技术的快速发展,超高速切削技术在上世纪80年代出现了突破性的进展。
发展初期,超高速切削主要用于加工金属材料,如铝合金、镁合金等,通过提高切削速度和减小切削深度,大大提高了切削效率和表面质量。
随着材料科学和刀具制造技术的进步,超高速切削技术逐渐应用到切削硬度较高的材料,如钢、铁等。
近年来,随着新材料和复杂工件的出现,超高速切削技术迎来了新的发展机遇。
首先是新材料的应用,如高性能陶瓷、纳米材料等,这些材料具有高硬度和高韧性,传统切削技术难以满足对其加工精度和表面质量的要求,而超高速切削技术能够有效解决这一问题。
其次是复杂工件的加工,如汽车发动机缸体、飞机发动机叶片等,这些工件形状复杂,表面精度要求高,传统加工方法效率低、成本高,而超高速切削技术具有快速、高效的优势。
随着超高速切削技术的不断发展,相关设备和工具也在不断更新迭代。
首先是刀具材料的优化,采用纳米材料、复合材料等先进材料制造刀具,能够提高切削效率和切削质量。
其次是机床的改进,采用高刚性、高速度的数控机床,能够满足高速切削的要求。
同时,先进的控制系统和传感器技术的应用,能够实时监测切削过程中的温度、压力等参数,保证整个加工过程的稳定性和安全性。
超高速切削技术的发展带来了巨大的经济效益和社会效益。
首先是加工效率的提高,相比传统切削技术,超高速切削能够大幅度提高切削速度和加工效率,节约了生产时间和成本。
其次是加工精度和表面质量的提升,超高速切削能够实现微米级的精度和纳米级的表面粗糙度,满足了高精度工件的需求。
此外,超高速切削技术还可以减少切削力和切削温度,降低刀具磨损和能量消耗,从而延长刀具寿命,减少了对自然资源的消耗,对环境保护具有积极意义。
高速切削加工技术的现状和发展
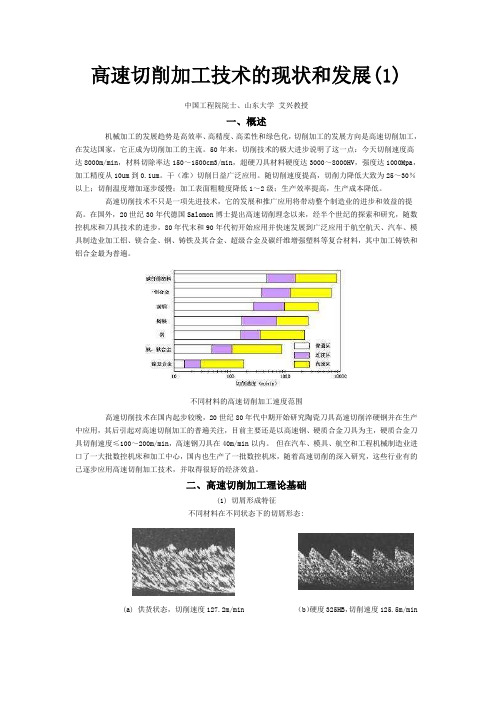
高速切削加工技术的现状和发展(1)中国工程院院士、山东大学艾兴教授一、概述机械加工的发展趋势是高效率、高精度、高柔性和绿色化,切削加工的发展方向是高速切削加工,在发达国家,它正成为切削加工的主流。
50年来,切削技术的极大进步说明了这一点:今天切削速度高达8000m/min,材料切除率达150~1500cm3/min,超硬刀具材料硬度达3000~8000HV,强度达1000Mpa,加工精度从10um到0.1um。
干(准)切削日益广泛应用。
随切削速度提高,切削力降低大致为25~30%以上;切削温度增加逐步缓慢;加工表面粗糙度降低1~2级;生产效率提高,生产成本降低。
高速切削技术不只是一项先进技术,它的发展和推广应用将带动整个制造业的进步和效益的提高。
在国外,20世纪30年代德国Salomon博士提出高速切削理念以来,经半个世纪的探索和研究,随数控机床和刀具技术的进步,80年代末和90年代初开始应用并快速发展到广泛应用于航空航天、汽车、模具制造业加工铝、镁合金、钢、铸铁及其合金、超级合金及碳纤维增强塑料等复合材料,其中加工铸铁和铝合金最为普遍。
不同材料的高速切削加工速度范围高速切削技术在国内起步较晚,20世纪80年代中期开始研究陶瓷刀具高速切削淬硬钢并在生产中应用,其后引起对高速切削加工的普遍关注,目前主要还是以高速钢、硬质合金刀具为主,硬质合金刀具切削速度≤100~200m/min,高速钢刀具在40m/min以内。
但在汽车、模具、航空和工程机械制造业进口了一大批数控机床和加工中心,国内也生产了一批数控机床,随着高速切削的深入研究,这些行业有的已逐步应用高速切削加工技术,并取得很好的经济效益。
二、高速切削加工理论基础(1) 切屑形成特征不同材料在不同状态下的切屑形态:(a) 供货状态,切削速度127.2m/min (b)硬度325HB,切削速度125.5m/min连续带状切屑(D.LEE)锯齿状切屑(c)硬度325HB,切削速度250m/min锯齿状切屑(d)硬度325HB,切削速度2600m/min即将分离的锯齿状切屑高速切削不同状态AISI4340钢(40CrNiMoA)时的切屑形态(纵截面微观照片)((b)、(c)、(d)从komarduri)切削渗碳淬硬20CrMnTi钢(HRC60~62)在100~110m/min时的切屑形貌工件材料及其性能和切削条件对切屑形态起主要作用,其中工件材料及其性能有决定性的影响。
超高速切削的发展现状

超高速切削的发展现状金属切削加工已进入了一个以高速切削为代表的新的发展阶段,由于高速切削加工能极大地提高材料的切除率和零件的加工质量,降低加工成本,因而成为当今金属切削加工的发展方向之一。
高速切削刀具技术是高速切削加工的一个关键技术,它包括高速切削刀具材料、刀柄系统、刀具系统动平衡技术、刀具监测技术等。
本文就作一概述。
1.高速切削加工对刀具系统的要求所谓刀具系统是指由刀柄、夹头和切削刀具所组成的完整的刀具体系,刀柄与机床主轴相连,切削刀具通过夹头装入刀柄之中。
要使刀具系统能在高速下进行切削加工,应满足以下基本条件:较高的系统精度系统精度包括系统定位夹持精度和刀具重复定位精度,前者指刀具与刀柄、刀柄与机床主轴的连接精度;后者指每次换刀后刀具系统精度的一致性。
刀具系统具有较高的系统精度,才能保证高速加工条件下刀具系统应有的静态和动态稳定性。
较高的系统刚度刀具系统的静、动刚度是影响加工精度及切削性能的重要因素。
刀具系统刚度不足会导致刀具系统振动,从而降低加工精度,并加剧刀具的磨损,降低刀具的使用寿命。
较好的动平衡性高速切削加工条件下,微小质量的不平衡都会造成巨大的离心力,在加工过程中引起机床的急剧振动。
因此,高速刀具系统的动平衡非常重要。
2.传统实心长刀柄结构存在的问题目前,在数控铣床、数控镗床和加工中心上使用的传统刀柄是标准7:24锥度实心长刀柄。
这种刀柄与机床主轴的连接只是靠锥面定位,主轴端面与刀柄法兰端面间有较大间隙。
这种刀柄结构在高速切削条件下会出现下列问题:刀具动、静刚度低刀具高速旋转时,由于离心力的作用,主轴锥孔和刀柄均会发生径向膨胀,膨胀量大小随旋转半径和转速的增大而增大。
这就会造成刀柄的膨胀量小于主轴锥孔的膨胀量而出现配合间隙,使得本来只靠锥面结合的低刚性连接的刚度进一步降低。
动平衡性差标准7:24锥度柄较长,很难实现全长无间隙配合,一般只要求配合前段70%以上接触,而后段往往会有一定间隙。
高速切削加工的发展及需求

高速切削加工的发展及需求高速切削加工是当代先进制造技术的重要组成部分,拥有高效率、高精度及高表面质量等特征。
本文介绍此技术的定义、发展现状、适用领域以及中国的需求情况。
高速切削加工的定义高速切削加工是面向21世纪的一项高新技术,它以高效率、高精度和高表面质量为基本特征,在汽车工业、航空航天、模具制造和仪器仪表等行业中获得了愈来愈广泛的应用,并已取得了重大的技术经济效益,是当代先进制造技术的重要组成部分。
高速切削是实现高效率制造的核心技术,工序的集约化和设备的通用化使之具有很高的生产效率。
可以说,高速切削加工是一种不增加设备数量而大幅度提高加工效率所必不可少的技术。
高速切削加工的优点主要在于:提高生产效率、提高加工精度及降低切削阻力。
有关高速切削加工的含义,目前尚无统一的认识,通常有如下几种观点:切削速度很高,通常认为其速度超过普通切削的5-10倍;机床主轴转速很高,一般将主轴转速在10000-20000r/min 以上定为高速切削;进给速度很高,通常达15-50m/min,最高可达90m/min;对于不同的切削材料和所釆用的刀具材料,高速切削的含义也不尽相同;切削过程中,刀刃的通过频率(Tooth Passing Frequency)接近于“机床-刀具-工件”系统的主导自然频率(Dominant Natural Frequency)时,可认为是高速切削。
可见高速切削加工是一个综合的概念。
1992年,德国Darmstadt工业大学的H. Schulz教授在CIRP上提出了高速切削加工的概念及其涵盖的范围。
认为对于不同的切削对象,过渡区(Transition)即为通常所谓的高速切削範围,这也是当时金属切削工艺相关的技术人员所期待或者可望实现的切削速度。
高速切削加工技术现状高速切削加工对机床、刀具和切削工艺等方面都有一些具体的要求。
下面分别从这几个方面阐述高速切削加工技术的发展现状和趋势。
机床设备现阶段,为了实现高速切削加工,一般釆用高柔性的高速数控机床、加工中心,也有釆用专用的高速铣、钻床。
高速加工技术现状及发展趋势

高速加工技术现状及发展趋势1 引言对于机械零件而言,高速加工即是以较快的生产节拍进行加工。
一个生产节拍:零件送进--定位夹紧--刀具快进--刀具工进(在线检测)--刀具快退--工具松开、卸下--质量检测等七个基本生产环节。
而高速切削是指刀具切削刃相对与零件表面的切削运动(或者挪移)速度超过普通切削 5~10 倍,主要体现在刀具快进、工进及快退三个环节上,是高速加工系统技术中的一个子系统;对于整条生产自动线而言,高速加工技术表征是以较简捷的工艺流程、较短、较快的生产节拍的生产线进行生产加工。
这就要突破机械加工传统观念,在确保产品质量的前提下,改革原有加工工艺(方式):或者采用一工位多工序、一刀多刃,或者以车、铰、铣削替代磨削,或者以拉削、搓、挤、滚压加工工艺(方式)替代滚、插、铣削加工…等工艺(方式),尽可能地缩短整条生产线的工艺流程;对于某一产品而言,高速加工技术也意味着企业要以较短的生产周期,完成研发产品的各类信息采集与处理、设计开辟、加工创造、市场营销及反馈信息。
这与敏捷创造工程技术理念有相同之处。
高速加工技术产生于近代动态多变的全球化市场经济环境。
在激烈的市场竞争中,要求企业产品质量高、成本低、上市快、服务好、环境清洁和产品创新换代及时,由此牵引高速加工技术不断发展。
自二十世纪八十年代,高速加工技术基于金属(非金属)传统切削加工技术、自动控制技术、信息技术和现代管理技术,逐步发展成为综合性系统工程技术。
现已广泛实用于生产工艺流程型创造企业(如现代轿(汽)车生产企业);随着个性化产品的社会需求增加,其生产条件为多品种、单件小批创造加工(机械创造业中,这种生产模式将占到总产值的 70%),高速加工技术势必在生产工艺离散型或者混和型企业中(如模具、能源设备、船舶、航天航空…等创造企业)得到进一步应用和发展。
二十世纪末期,我国变革计划经济体制,改革开放,建成有中国特色社会主义市场经济体制。
实用的高速加工技术尾随引进的先进数控自动生产线、刀具(工具)、数控机床(设备),在机械创造业得到广泛应用,相应的管理模式、技术、理念随之融入企业。
高速高效切削加工技术的现状及发展趋势

高速高效切削加工技术的现状及发展趋势一、前言目前,我国已成为世界飞机零部件的重要转包生产国,波音、麦道、空客等世界著名飞机制造公司都在我国转包生产从尾翼、机身、舱门到发动机等各种零部件,这些飞机零部件的加工生产必须采用先进的加工装备和加工工艺。
为此,国内各飞机制造公司均进行了大规模的技术改造,引进了大量国外先进的加工装备,使我国的飞机制造业设备的数控化率越来越高。
与此同时,大量高速、高效、柔性、复合、环保的国外切削加工新技术不断涌现,使切削加工技术发生了根本的变化。
刀具在航空航天加工领域的应用技术进入了以发展高速切削、开发新的切削工艺和加工方法、提供成套技术为特征的新阶段。
与此形成鲜明对比的是,我国的装备制造业和以制造业为主要服务对象的传统的工具工业却无法满足航空航天工业对现代制造装备和先进加工工艺的要求。
下面结合我国航空航天工业加工技术的现状及发展趋势,着重介绍我国高效、高速切削刀具的生产应用情况,对我国工具工业的发展现状和存在的问题提出自己的看法。
二、航空航天工业加工技术的现状及发展趋势1.航空结构件材料的发展趋势及其特点①以整体件为代表的铝合金结构件为了提高零件的可靠性、降低成本和减轻重量,传统的铆接结构逐步被整体薄壁的机加工结构件所代替。
这类零件由于大部分是用整体实心铝合金材料制成的薄壁、细筋结构件,70%~95%的材料要在加工中去除掉,而高速切削产生的热量少、切削力小、零件变形小,因此提高生产效率的唯一途径是采用四轴或五轴联动机床进行高速铣削加工。
②以钛基和镍基合金零件为代表的难切削材料零件由于钛(镍)合金具有比强度高、热强度好、化学活性大等特点,目前飞机发动机重要部件采用钛基和镍基合金材料的逐渐增多。
采用高速切削后,其切削速度可提高到100m/min以上,为常规切削速度的10倍。
这类材料的加工特点是:切削力大、切削温度高、加工硬化和粘刀现象严重、刀具易磨损。
③以碳纤维复合材料零件为代表的复合材料结构件复合材料现已成为新一代飞机机体结构主要材料之一,如飞机上的大型整体成形的翼面壁板、带纵墙的整体下翼面等。
超高速切削的发展现状整理

超高速切削的发展现状整理超高速切削的进展现状金属切削加工已进入了一个以高速切削为代表的新的进展阶段,由于高速切削加工能极大地提高材料的切除率和零件的加工质量,降低加工成本,因而成为当今金属切削加工的进展方向之一。
高速切削刀具技术是高速切削加工的一个关键技术,它包括高速切削刀具材料、刀柄系统、刀具系统动平衡技术、刀具监测技术等。
本文就作一概述。
1. 高速切削加工对刀具系统的要求所谓刀具系统是指由刀柄、夹头和切削刀具所组成的完整的刀详细系,刀柄与机床主轴相连,切削刀具通过夹头装入刀柄之中。
要使刀具系统能在高速下进行切削加工,应满意以下基本条件:较高的系统精度系统精度包括系统定位夹持精度和刀具重复定位精度,前者指刀具与刀柄、刀柄与机床主轴的连接精度;后者指每次换刀后刀具系统精度的全都性。
刀具系统具有较高的系统精度,才能保证高速加工条件下刀具系统应有的静态和动态稳定性。
较高的系统刚度刀具系统的静、动刚度是影响加工精度及切削性能的重要因素。
刀具系统刚度不足会导致刀具系统振动,从而降低加工精度,并加剧刀具的磨损,降低刀具的使用寿命。
较好的动平衡性高速切削加工条件下,微小质量的不平衡都会造成巨大的离心力,在加工过程中引起机床的急剧振动。
因此,高速刀具系统的动平衡特别重要。
2. 传统实心长刀柄结构存在的问题目前,在数控铣床、数控镗床和加工中心上使用的传统刀柄是标准7:24锥度实心长刀柄。
这种刀柄与机床主轴的连接只是靠锥面定位,主轴端面与刀柄法兰端面间有较大间隙。
这种刀柄结构在高速切削条件下会消失下列问题:刀具动、静刚度低刀具高速旋转时,由于离心力的作用,主轴锥孔和刀柄均会发生径向膨胀,膨胀量大小随旋转半径和转速的增大而增大。
这就会造成刀柄的膨胀量小于主轴锥孔的膨胀量而消失协作间隙,使得原来只靠锥面结合的低刚性连接的刚度进一步降低。
动平衡性差标准7:24锥度柄较长,很难实现全长无间隙协作,一般只要求协作前段70%以上接触,而后段往往会有肯定间隙。
高速切削加工技术的现状和发展
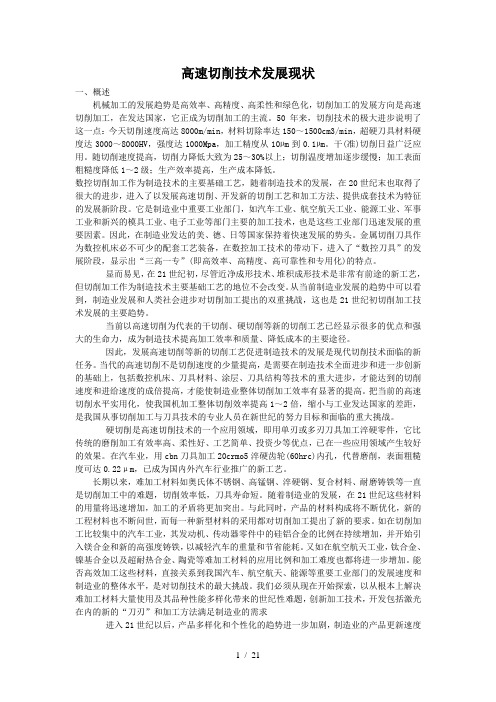
高速切削技术发展现状一、概述机械加工的发展趋势是高效率、高精度、高柔性和绿色化,切削加工的发展方向是高速切削加工,在发达国家,它正成为切削加工的主流。
50年来,切削技术的极大进步说明了这一点:今天切削速度高达8000m/min,材料切除率达150~1500cm3/min,超硬刀具材料硬度达3000~8000HV,强度达1000Mpa,加工精度从10µm到0.1µm。
干(准)切削日益广泛应用。
随切削速度提高,切削力降低大致为25~30%以上;切削温度增加逐步缓慢;加工表面粗糙度降低1~2级;生产效率提高,生产成本降低。
数控切削加工作为制造技术的主要基础工艺,随着制造技术的发展,在20世纪末也取得了很大的进步,进入了以发展高速切削、开发新的切削工艺和加工方法、提供成套技术为特征的发展新阶段。
它是制造业中重要工业部门,如汽车工业、航空航天工业、能源工业、军事工业和新兴的模具工业、电子工业等部门主要的加工技术,也是这些工业部门迅速发展的重要因素。
因此,在制造业发达的美、德、日等国家保持着快速发展的势头。
金属切削刀具作为数控机床必不可少的配套工艺装备,在数控加工技术的带动下,进入了“数控刀具”的发展阶段,显示出“三高一专”(即高效率、高精度、高可靠性和专用化)的特点。
显而易见,在21世纪初,尽管近净成形技术、堆积成形技术是非常有前途的新工艺,但切削加工作为制造技术主要基础工艺的地位不会改变。
从当前制造业发展的趋势中可以看到,制造业发展和人类社会进步对切削加工提出的双重挑战,这也是21世纪初切削加工技术发展的主要趋势。
当前以高速切削为代表的干切削、硬切削等新的切削工艺已经显示很多的优点和强大的生命力,成为制造技术提高加工效率和质量、降低成本的主要途径。
因此,发展高速切削等新的切削工艺促进制造技术的发展是现代切削技术面临的新任务。
当代的高速切削不是切削速度的少量提高,是需要在制造技术全面进步和进一步创新的基础上,包括数控机床、刀具材料、涂层、刀具结构等技术的重大进步,才能达到的切削速度和进给速度的成倍提高,才能使制造业整体切削加工效率有显著的提高。
高速切削技术的发展与展望

高速切削技术的发展与展望切削加工是机械加工应用最广泛的加工方法之一,而高速是它的重要发展方向,其中包括高速软切削、高速硬切削、高速干切削、大进给切削等。
高速切削能够大幅度提高生产效率和单位时间内材料切除率,改善加工表面质量降低加工费用。
高速切削的概念与高速切削技术高速切削是一个相对概念,如何定义,目前尚无共识。
而且由于不同的加工方式、不同工件有不同的高速切削范围,因而也很难就高速切削的速度范围给出一个确切的定义。
高速切削技术是在机床结构及材料、机床设计制造技术、高速主轴系统、快速进给系统、高性能CNC控制系统、高性能刀夹系统、高性能刀具材料及刀具设计制造技术、高效高精度测量测试技术、高速切削机理、高速切削工艺等诸多相关硬件与软件技术均得到充分发展的基础之上综合而成的。
因此,高速切削加工是一个复杂的系统工程,涉及机床、刀具、工件、加工工艺过程参数及切削机理等诸多方面。
高速切削技术国外发展现状从德国Carl. J. Salomon博士提出高速切削概念,并于同年申请了专利以来,高速切削技术的发展经历了高速切削的理论探索阶段、高速切削应用探索阶段、高速切削的初步应用阶段、高速切削的较成熟阶段等四个阶段,现已在生产中得到推广应用。
特别是20世纪80年代以来各工业发达国家相继投入大量人力、财力,研究开发高速切削技术及相关技术,发展迅速。
国外近几年来高速加工机床发展迅速,美国、法国、德国、日本、瑞士、英国、加拿大、意大利等国家相继开发了各自的高速切削机床。
高速主轴是高速切削技术最重要的关键技术,通常采用主轴、电动机一体化的电主轴部件,实现无中间环节的直接传动,主轴支承一般使用陶瓷轴承、静压轴承、动压轴承、空气轴承以及油0气润滑、喷射润滑等技术,也有使用磁力轴承的。
进给系统则开始采用直线电动机或小导程大尺寸高质量的滚珠丝杠或大导程多头丝杠,以提供更高的进给速度和更好的加、减速特性,最大加速度可达2~C控制系统则使用多片32位或64位CPU,以满足高速切削加工对系统快速数据处。
高速切削加工工艺的现状与优化趋势
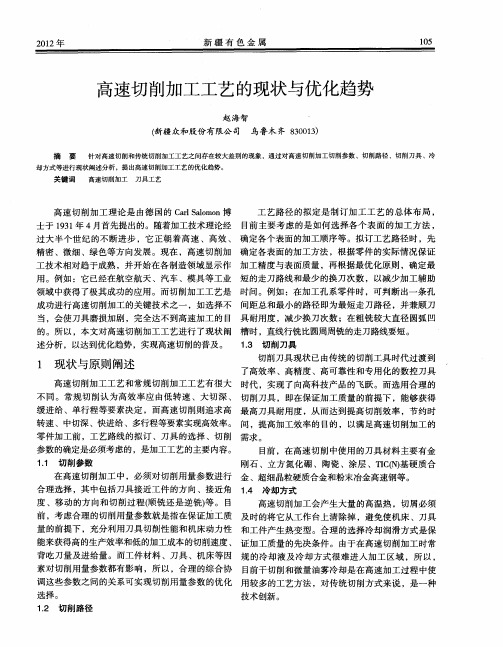
精密、微细 、绿色等方 向发展 。现在 ,高速切削加 确定各表面的加工方法 ,根据零件的实际情况保证 工技术相对趋于成熟 ,并开始在各制造领域显示作 加工精度与表面质量 ,再根据最优化原则 ,确定最 用。例如 :它已经在航空航天 、汽车、模具等工业 短 的走刀路线和最少 的换刀次数 ,以减少加工辅助
热冲击性等优化性能要求 。高速切削要求刀具结构 吃刀量等参数 的选择 。而进给量是精加工时决定生 和刀具夹紧机构具有更严格的要求 ,以确保生产安 产 率 的主要 因素 ,增 大进 给 量将 会 增 大加 工 表 面 的 全的可靠性 。可综合以下几个要点进行考虑 : 粗 糙度数 值 ,所 以要 慎重 选择 与协调 。 首先选择刀具材料 :在高速切削加工系统 中优 主要 考 虑 刀具 的影 响 ,考虑 工 件 材料 的 加工 性 先选 用 硬质 合金 ,甚 至超 细粒 度 硬质 合 金 或具 有 涂 能 。在确 定切 削用 量 参数 时 ,首 先 应 采用 尽 可 能大 层技 术等 材料 的高性 能刀具 ,以提 高使 用 的可靠性 。 的背吃刀量 ,其次选用较大 的进给量 ,最后确定合 其 次 选择 刀 具结 构 :根 据 零 件 的结 构 和尺 寸选 理 的切 削速度 。 择合适的刀具与其相适应 ,优先选用机夹式可转位 总之 ,无论在何种加工场合 ,都应在保证加工 结构 ,甚 至复合 结构 或专用 结构 刀具 ,以减 少换 刀 、 质 量 的前 提下 ,认 真 选 择切 削参 数 ,并兼 顾 切 削效 对 刀和刃磨 的时间 。 率 、经济性和加工成本。而具体数值的确定 ,可根 最后选择刀柄结构 :保证刀具能够迅速 、准确 据 实 际情 况及 机 床说 明 书 、切 削用 量 手册 ,并结 合 地安装到机床主轴或刀库 中去 ,优先选用标准化或 加工经验而确定 。综合协调这些参数之间的关系可 系 列化 刀柄 ,并 且尽 可能 选用 短 刀柄 ,以提 高刀 具 实 现切 削用 量参数 的优 化选择 。 的 刚性 。 22 切 削路径 优化 . 般 情 况下 ,选 用 高 耐用 度 、高精 度 和专 用 化 切削路径的选择与优化在高速切削加工 中,除 的刀具 ,会增加刀具使用成本 ,但是 ,它却提高 了 了刀具 材 料 和刀 具几 何参 数 的选 择 外 ,还 要 采取 不 零件 的加工 效率 和加 工 质 量 ,可 以使 整 个 加 工成 本 同的切 削路径 才能 得到 较好 的切削效 果 。 大大降低。因此 ,在加工系统 中选择合理的切削刀 切削路径优化 的目的是提高刀具耐用度 ,提高 具 ,利用刀具 自身优势来完成高速切削加工。 切削效率 ,获得最小的加工变形 ,提高机床走刀利 24 冷却 方式优 化 . 用 率 ,充 分发 挥 高速 加工 的优 势 。 传 统 切 削加 工 的冷 却方 式 一 般采 用 冷却 液 ,这 ( 走刀方 向的优化在走刀方 向的选择上 ,以曲 1 ) 对加 工环境 带来危 害 ,不符 合绿 色加工 的概 念范 畴 。 面平坦 性 为评 价 准则 ,确定 不 同 的走刀 方 向选 取方 而 高速 切 削 加 工 可采 用 干 式 ( 干 式 ) 削 技 术 ,不 准 切 案 ;对于 曲率变化大的曲面 以最大 曲率半径方向为 采用 切 削液 或采 用微 量 的切削 液 ,这可 以提 高切 屑 最 优进 给 方 向 ,对 曲率 变化 小 的面 , 以单 条 刀 轨平 的回收利用率 ,降低切削成本 、降低切削过程对环 均 长度最 长 为原则选 择走 刀方 向。 境的危害 、提高切屑的回收利用率等。 () 位轨 迹 生成按 照 刀位路 径 尽可 能简 化 ,尽 2刀 25 研究 与展 望 . 量走直线 ,路径尽量光滑的要求选择加工策略 ,选 高速切削加工技术系统而复杂 ,离不开机床 、 择合适 的插补方 法 ,保证加工面残 留高度 的要求 , 刀具 、夹具 及其 控制 软件 的配 合 。该 工 艺 的许 多 问 采 用过 渡 圆弧 的 方法处 理 加 工 干涉 区 ,样 在 加工 时 题现在 并没 有得 到充分 解决 ,其发 展前 景十 分广 阔 。 就不需要减速 ,提高加工效率 。 随着 技术 的 日益 成熟 ,特 别是 高 速 主轴 的 出 现 ,切 () 性加 减速 和 断刀 的几率 。选取 合适 的加减 3柔 削速度将进一步提高。但也要追求高速切削转速和 速方式 ,减少启动冲击 ,保持机床 的精度 ,减少刀 进给速度 的最佳参数 ,简化工序 ,这样高速切削的 具 颤振 。 “ 高速 ”才 能充分 发挥 出来 。刀具 的磨 损 以及 轴承 技 23 切 削刀具 优化 . 术将会是今后一段时间内制约高速切削发展的关键 高 速切 削 刀具 是 高速 加 工工 艺 系 统 中最 活跃 的 因素 。 要素 ,是实现高速加工 的关键技术之一 。高速切削
高速切削加工稳定性研究的现状和发展趋势
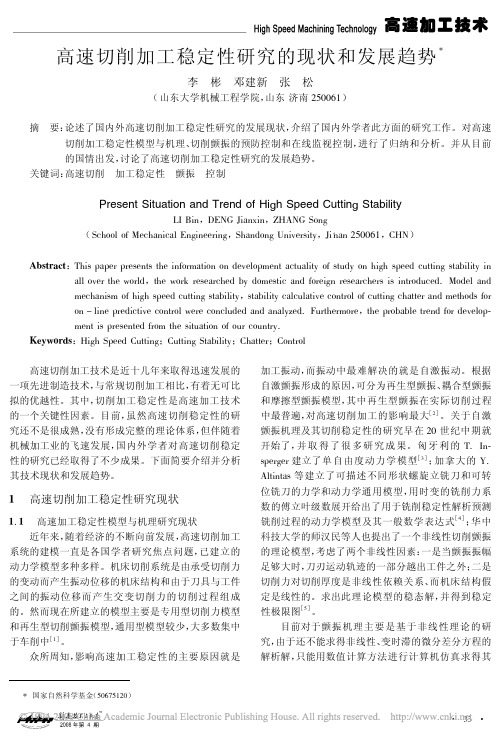
削试验时, 充分整合了检测系统和计算机分析计算的 功能。通过采集系统 ( 图 )) 得到各种在线参数, 进行 相应的存储、 分析、 数据库匹配等步骤 ( 如图 + 所示) 输出相应的切削参数来保证加工的稳定性。
!% "
颤振预防与控制的研究现状 对于切削加工中颤振的控制, 国内外的研究人员
( !
[ () ] (() 电流变技术在切削颤振控制中的应用
吴雅? 机床切削系统的颤振及其控制? 北京: 科学出版社, $’’!? I-:F12D12 ;, N,-- O @, >01PF,P- Q, 10 ,4? ? >0,R8480H AB /F M C8448-D ,-9 F,20 $ : ,4012-,0831 ,-,4H08E,4 C107A9:, F,20 ( 1TF128C1-0,4 9AS- M C8448-D, 3128B8E,08A-? I-012-,08A-,4 =A/2-,4 AB N,E78-1 ;AA4:UN,-/B,E0/21, ())! : (" M !* , !" M *)
主要是利用三维造型技术在计算机上设计出满足 视觉动感效果的三维虚拟主轴系统模型, 并将其离散 为有限个单元的组合体, 得到系统的动态特性, 然后进 行分析。利用有限元法研究高速切削系统稳定性相关 问题, 如切削温度、 切削力等。图 ! 所示为有限元法模 拟高速切削温度场所得的图样。分析过程中, 只要有 限元分析软件和计算机的计算能力以及计算效率就可 以把有限元模型的网格划分的足够细, 使其最大程度 地接近研究对象的实际情况, 所获得的研究结果也就 更有实际意义。
[ )+ . )/ ] 报参数值的计算要花费较长时间 。
!% #
金属切削机床高速切削技术的发展分析

金属切削机床高速切削技术的发展分析目录一、前言 (2)二、高速切削技术的发展 (3)三、技术研发与创新驱动的投资策略 (7)四、技术创新推动市场升级 (11)五、技术研发与创新的风险 (17)六、绿色环保与节能技术的进展 (22)一、前言自动化技术的引入不仅体现在单台机床的智能化改造上,还在于生产线整体的自动化集成。
企业投资自动化生产线,通过与机器人、自动仓储系统及高效输送系统相结合,可以大幅提高生产线的灵活性、自动化程度以及产能。
例如,智能化的自动化机床可以实现无人工干预的全程加工,极大提高了生产效率。
这一技术趋势推动了机床行业从单台机床的自动化向整条生产线的自动化过渡,为行业带来了新的投资机遇。
金属切削机床作为工业制造的重要装备之一,广泛应用于汽车、航空航天、电子、模具、精密零部件等行业,是现代制造业中不可或缺的生产工具。
随着全球制造业的发展和技术创新,金属切削机床市场的规模持续扩大,市场竞争也日益激烈。
随着工业互联网、人工智能、大数据分析等技术的广泛应用,智能制造成为中国制造业转型的关键方向。
智能化机床设备不仅能够提高生产效率,还能通过自我学习、远程监控、故障预测等手段提升设备运行的稳定性和生产精度。
智能化、数字化和自动化机床的需求在中国市场中不断攀升,成为企业选择机床时的重要标准之一。
行业整合不仅有助于提升产品的研发能力和生产效率,还能通过提升产业链的协同效应,进一步增强市场的供应能力和响应速度。
这将进一步推动市场格局的优化,促进金属切削机床行业的健康、可持续发展。
声明:本文内容来源于公开渠道或根据行业大模型生成,对文中内容的准确性不作任何保证。
本文内容仅供参考,不构成相关领域的建议和依据。
二、高速切削技术的发展(一)高速切削技术的关键技术突破1、数控技术的进步高速切削技术得以快速发展的一个关键因素是数控技术的不断进步。
通过高精度的数控系统,机床能够在极高的转速下保持稳定的操作,确保加工过程中的精度和表面质量。
- 1、下载文档前请自行甄别文档内容的完整性,平台不提供额外的编辑、内容补充、找答案等附加服务。
- 2、"仅部分预览"的文档,不可在线预览部分如存在完整性等问题,可反馈申请退款(可完整预览的文档不适用该条件!)。
- 3、如文档侵犯您的权益,请联系客服反馈,我们会尽快为您处理(人工客服工作时间:9:00-18:30)。
品
’
切削基本 相同 ,从 而能大大减 少切削工 时 ,大幅度提 高机床
生产 效 率 。
年 发 表 了著 名 的高 速切 削 理 论…。现 在人 们 常 用 “ 洛 蒙 萨
曲 线 ” 来 表 示 , 如 图 1 示 。 他 认 为 ,在 常 规 切 削 速 度 范 围 所 内 , 切 削 温 度 随 着 切 削 速 度 的 提 高 而 升 高 ,一 定 的 工 件 材 料
质量。本文详细 介绍 了高速切 削加 工技术的概念 与特点 、关键 技术、j要应用领域 和发展 动向。 三 关键词 :高速切 削;高速加工 ;金属加] ;高速 度;高精 度 二
The Pr s n t t nd D e o e e t S a e a e l pm e ti i h S e ti v n n H g pe d Cu tng Te hno o y c lg
意 高 加 ‘ 速 工
高速 切 削加 工技 术 的现 状 与发 展
寅 斌 , 彭满 华 l J ( 南 理 工 大 学 机 械 与 汽 车 工 程 学 院 ,广 州 , 1 6 0 华 50 4 )
摘 要 :随着科学技 术的突飞猛进 和经济发展的强 大推动 ,高速加 工机 床、月具技术和丰 关技术迅速进步 ,使 高速 切削加工技术应用于航 l I 空 、航天 、汽车 、模具和机 床等行业中,尤其足高速铣削和高速车 削发展 神速。高速切 削加工 技术能大大减少切削工时 ,提高 生产效率和加工
Li n u Bi Pe a ng M nhua
( c o lo e h n c l n t mo ieE gn e ig,S uh C i aUnv ri f c n l g , S h o f c a ia d Au o t n i e rn M a v o t h n iest o h o o y y Te Gu n z o , 1 6 0) a gh u 504
1前言
I—■一 速 切 削 加 工 ( g p e C tig,简 称HS ) Hih S e Байду номын сангаас u t n C
太 高 ,刀 具 材 料 无 法 承 受 ,切 削 加 工 不 能 进 行 , 这 个 区 域 称 之 为 “ 谷 ” 。 如 果 切 削 速 度 能 越 过 “ 谷 ” , 在 高 速 区工 死 死 作 ,则 有 可 能 用 现 有 的 刀 具 进 行 切 削 加 工 ,切 削 温 度 与 常 规
A bs r t W ih he tac : t t de l veopm e c e e a t c nt of s i nc nd e hnol y,t a og he m chi nd uti ne a c tng oo e hnol t lt c ogy n hi h s ed i g pe pr e sng v l oc s i de e op a dl r pi y,e peca l n g s ed c tng.The hi s e c tng t c s i ly i hi h pe ut i gh pe d uti e hno og s w i l pple i a i to l y i dey a i d n v a n, i
彭 满 华 ,男 , 1 8 年 生 ,华南 理 工 大 学 聚合 物 新 型 成 型装 95
备 国 家 工 程 研 究 中 心 在 读 硕 士 研 究 生 , 研 究 方 向 为 模 具 C D/ A
CA E/CAM 。
切削速度V ( mi ) / m/ n
固1萨洛蒙 曲线
6 模具工程 M U D IP O E T 2  ̄ 1 期 ( 0 O L &DE R J C oo 0 N 总第 13 1 期J
s ed uti pe c tng r nt oduce n t i n hi pe . a ei r d i de a li t spa r
Ke wo d : g p e ti y r s Hi h S e d Cu t ng;Hi h S e d Pr e sn g p e oc si g; M e a r c si g;H i h S e d;Hi h Pr c s n t lP o e sn g p e g e ii o
对 应 有 一 个 临 界 切 削 速 度 V ,此 处 切 削 温 度 最 高 ,但 当 切 削 速 度 超 过 V ,切 削 温 度 不 但 不 升 反 而 下 降 。 由于 切 削 温 度 后
作者 简 介 :刘 斌 ,男 ,1 6 年生 ,工 学 博士 ,华 南 理 工 大 99
学聚 合物 新型 成 型装 备 国家 工程 研 究 中心 副教 授 。
a o o i , o l n a h ne t o n u t y I all r e y r d c u t i e i c e s r du t n e i i n y a d i p o e ut m b e m u d a d m c i o l d sr . t c l a g l e u e c ti t l i ng m , n r a e p o c o f c e c n m r v i p o e sn u f y r c si g q a t .Th a i o c pt n a e t r s e e h l g ,m an a p i a i n fe d a d d v l p e r nd o i h i e b sc c n e i nd f a u e ,k y t c no o o y i p l t l n e e o m ntte f h g c o i