风险分析工具FMEA培训教材
FMEA培训教材
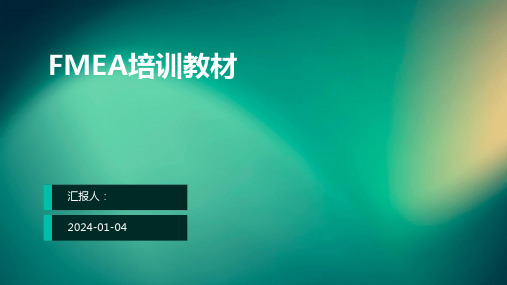
总结词
汽车刹车系统FMEA分析是一个典型的故障模式与影响 分析案例,通过对刹车系统的各个组成部分进行故障 模式分析,评估其对整个系统性能的影响。
详细描述
汽车刹车系统FMEA分析首先识别刹车系统中的各个组 成部分,然后对每个组成部分进行故障模式分析,包括 可能的故障类型、故障发生概率和故障影响程度。接着 ,根据分析结果,评估每个故障模式对刹车系统整体性 能的影响,并确定优先改进顺序。最后,制定相应的改 进措施和预防措施,降低故障发生概率和影响程度。
高级功能
介绍FMEA软件的高级功能,如 影响分析、优先级排序、报告 生成等。
常见问题与解决方案
列举使用FMEA软件过程中可能 遇到的问题,并提供相应的解 决方案。
FMEA软件应用实例
01
汽车刹车系统FMEA分析
通过实际案例,演示如何使用FMEA软件对汽车刹车系统进行故障模式
、影响和优先级分析,并提出相应的改进措施。
FMEA软件应用领域
FMEA软件广泛应用于汽车、航空、电子、医疗等制造业 领域,用于提高产品质量、降低产品风险和优化产品设计 。
FMEA软件操作教程
软件安装与启动
介绍如何下载和安装FMEA软件 ,以及如何启动软件并进入操 作界面。
基础操作
介绍FMEA软件的基本操作,如 创建项目、添加部件、设置故 障模式等。
感谢您的观看
FMEA的应用范围
总结词
FMEA可以应用于各种行业和领域,如汽车 、航空、医疗、电子等,用于评估产品设计 或流程的可靠性和安全性。
详细描述
FMEA是一种通用的质量工具,可以应用于 各种行业和领域。在汽车行业中,FMEA可 以用于评估汽车零部件的可靠性,提高车辆 的安全性能;在航空领域,FMEA可以用于 评估飞机设计和制造过程中的潜在故障模式 ,确保飞行的安全;在医疗领域,FMEA可 以用于评估医疗设备的可靠性和安全性,提 高患者的治疗效果;在电子行业,FMEA可 以用于评估产品的设计和制造流程,提高产 品的质量和可靠性。
FMEA培训资料
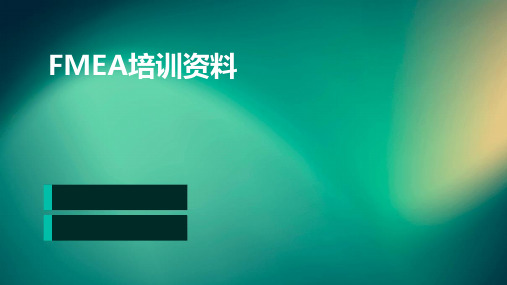
实施步骤介绍
01
步骤六:评估故障影响
02
评估故障模式对系统或产品性能、安全性、可靠性的影响程度
。
确定故障模式的严重度等级。
03
实施步骤介绍
步骤七:制定预防措施
1
2
针对每种故障模式和原因,制定相应的预防措施 。
3
评估预防措施的有效性和可行性。
实施步骤介绍
步骤八:确定风险优先数
综合故障模式的严重度、发生概率和检测难度 ,计算风险优先数。
医疗健康
FMEA可用于评估医疗设备的可 靠性和安全性,减少故障对患 者和医护人员的影响。
能源与环保
FMEA可用于评估能源设备和环 保设施的潜在故障和风险,确 保设备和设施的稳定运行和环 境保护。
02 FMEA核心原理
故障模式与影响分析
01
02
03
故障模式识别
识别产品或过程中可能出 现的故障模式,包括功能 失效、性能下降等。
制定措施 针对高风险故障模式,制定预防 措施和探测措施,以降低故障发 生的可能性和影响。
针对生产过程特点的FMEA策略
关注工艺流程
针对生产过程中的工艺流程进行详细 分析,识别关键工艺步骤和潜在故障 点。
考虑设备因素
分析生产过程中使用的设备,识别设 备故障对生产过程的影响,并制定相 应的预防措施。
重视人员操作
实施效果
通过实施FMEA分析,成功识别并解决了多个潜在的设计问题,提高了产品的可靠性和安 全性。同时,也为后续产品的设计和开发提供了宝贵的经验教训和改进方向。
05 FMEA在生产过程中的应 用
生产过程FMEA实施流程
定义范围
明确FMEA分析的对象和边界,包括产品、过程、系统或服务等 。
FMEA培训教材-PPT精选全文

客户要求 方便调整
舒适 移动顺畅
ቤተ መጻሕፍቲ ባይዱ
产品规格 调节高度 坐垫厚度 旋转角度 椅轮松紧
9
1
3
9
3
1
9
9
重要性 60% 30% 10%
分值
640
330
180
90
FMEA 得原理
客户要求 方便调整
舒适 移动顺畅
分值
产品规格 调节高度 坐垫厚度 旋转角度 椅轮松紧
9
1
3
9
3
1
9
9
640
330
180
90
参数
上升50CM
FMEA 得原理
一、FMEA基本知识
练习:
公司产品:车门 客户要求:
•方便开关 •噪音小 •安全
FMEA 得原理
FMEA 得原理
FMEA 得原理
客户质量要求 Input
客户质量目标
FMEA Output
CTQ 清单 CP 控制计划
FMEA
FMEA 得原理
Output
CTQ 清单
CTQ产出原则:
压 合 状 态
方法
特
样本Sample
殊 特 性 分
产品特 性/过程 参数规 格/公差
评价/ 测量技
术
容 量
频率
类
《
首检
MODULE 检验标
准》
5-20倍 显微镜
6P CS
:6PCS/ 抽检 : 每10PCS
抽1PCS
反应计
控制方法/ 统计技术
责任人
划
《CD-HFM0419701 LCM 镜检 不良明细
措施?
fmea培训资料最新版(141页)

FMEA培训资料最新版(141页)FMEA(失效模式和影响分析)是一种系统的、结构化的方法,用于识别和评估产品或过程中的潜在失效模式,以及这些失效模式对最终用户的影响。
FMEA培训资料旨在帮助参与者了解FMEA的基本概念、方法和工具,以便在实际工作中应用FMEA来提高产品或过程的质量和可靠性。
一、FMEA概述FMEA是一种预防性的质量工具,它通过系统性地识别和分析潜在的失效模式,以及这些失效模式对产品或过程的影响,来降低失效风险。
FMEA通常分为两个阶段:设计FMEA(DFMEA)和过程FMEA (PFMEA)。
DFMEA关注于产品设计和开发阶段,而PFMEA关注于制造和装配过程。
二、FMEA的基本步骤1. 定义项目范围:确定要分析的系统和子系统的范围。
2. 建立团队:组建一个跨职能的团队,包括设计、工程、制造和质量等部门的代表。
3. 识别失效模式:团队成员共同识别潜在的失效模式,并记录下来。
4. 分析失效影响:评估每个失效模式对最终用户的影响,包括安全性、成本、性能和可维护性等方面。
5. 评估失效严重性:根据失效影响的严重程度,对每个失效模式进行评分。
6. 评估失效发生概率:根据失效模式的已知历史数据或专家经验,评估每个失效模式的发生概率。
7. 评估检测难度:评估检测每个失效模式的难度,包括检测方法的有效性和成本。
8. 计算风险优先级数(RPN):将严重性、发生概率和检测难度相乘,得到每个失效模式的风险优先级数。
9. 采取预防措施:根据RPN,制定和实施预防措施,以降低失效风险。
10. 跟踪和更新:定期跟踪和更新FMEA,以确保其持续有效。
三、FMEA工具和模板FMEA工具和模板可以帮助团队更有效地进行FMEA分析。
常用的FMEA工具包括:1. FMEA表格:用于记录失效模式、影响、严重性、发生概率、检测难度和RPN等信息。
2. FMEA软件:提供自动化的FMEA分析功能,包括数据输入、计算和分析报告。
FMEA培训课件(五大工具)
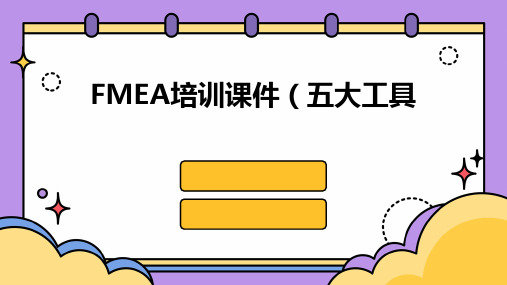
FMEDA不仅关注故障模式的影响,还特别强调对检测性的评估,以便更全面地了解潜在问题的影响以及在出现故障时能否及时发现并进行修复。
在FMEDA中,检测性的评估通常采用量化的方式进行,以便更准确地确定故障模式的可检测性。通过提高检测性,可以降低因未及时发现故障而导致的事故风险。
详细描述
在FMESi中,严重度评估通常采用量化的方式进行,以便更准确地确定故障模式对系统性能的影响程度。
总结词:故障模式、影响与风险优先数分析(FMERP)是一种综合性的质量工具,旨在识别、评估和解决潜在的故障模式及其对系统性能的影响。
总结词
故障模式、影响与检测性分析(FMEDA)是一种质量工具,用于评估潜在的故障模式及其对系统性能的影响以及检测的可能性。
详细描述
DFSS(Design for Six Sigma)是一种设计方法论,旨在提高产品的设计质量和可靠性。通过结合FMEA,可以对产品设计中的潜在失效模式进行分析和预防,从而提高产品的设计质量和可靠性。这种结合有助于在设计阶段就考虑产品的性能、可靠性和安全性,从而减少后期的改进成本和时间。
THANKS
总结词
电子产品行业对质量和可靠性要求极高,FMEA在此领域的应用同样广泛且重要。
在电子产品案例中,FMEA被用于分析电子产品的设计和生产过程。通过FMEA分析,可以发现潜在的故障模式,并采取相应的预防措施,提高产品的可靠性和稳定性。此外,FMEA还可以帮助企业优化产品设计,降低生产成本,提高市场竞争力。
FMEA培训课件(五大工具
FMEA基础介绍FMEA实施流程FMEA分析方法FMEA应用案例FMEA与其他工具的结合应用
FMEA培训教材(ppt)(2024)

后果分析
针对每种失效模式,分析 其可能对产品功能、安全 性、可靠性等方面造成的 影响和后果。
风险评估
对每种失效模式及其后果 进行风险评估,确定其严 重度、发生度和检测度等 级。
14
评估风险等级并采取预防措施
风险等级评估
综合考虑严重度、发生度 和检测度等级,对每种失 效模式进行风险等级评估 。
2024/1/30
4
FMEA发展历程
起源
FMEA起源于20世纪40年代的军事领域,当 时主要用于评估武器系统的可靠性。
发展
随着工业技术的进步,FMEA逐渐应用于民 用领域,如汽车、航空航天、电子、医疗等 。
标准化
为了规范FMEA的实施,国际标准化组织( ISO)和美国汽车工程师学会(SAE)等制定 了相应的标准和指南。
。
2024/1/30
可靠性增长
在产品设计阶段,通过不断测试和 验证,提高产品的可靠性和稳定性 ,降低失效模式的发生概率。
持续改进
在产品设计和生产过程中,持续关 注失效模式的变化和趋势,及时采 取改进措施,确保产品质量的持续 改进和提升。
16
04
FMEA在生产过程控制中应用
2024/1/30
17
识别生产过程中潜在失效模式及后果
通过引入先进设备、优化工艺流程、提高员工技能等手段 ,提升生产过程的能力和效率,降低潜在失效模式的发生 概率。
风险管理机制完善
建立完善的风险管理机制,包括风险识别、评估、预防、 监控和应对等环节,形成闭环管理,确保生产过程风险的 有效控制和持续改进。
20
05
FMEA在设备维护保养中应用
2024/1/30
21
FMEA培训教程(共10)

失效模式识别
针对关键质量特性,分析 可能出现的失效模式及其 对产品性能的影响。
控制措施制定
针对识别出的失效模式, 制定相应的控制措施,如 设计优化、工艺改进、检 验加强等。
提升产品质量水平,降低缺陷率
缺陷预防
01
通过FMEA分析,提前识别并消除可能导致缺陷的因素,从而降
低缺陷发生的概率。
过程控制
02
THANKS
感谢观看
高产品质量和生产效率。
操作FMEA分析
对生产操作进行FMEA分析,识 别操作过程中潜在的故障模式、 影响及原因,制定操作规范和培 训计划,提高操作人员的技能和
意识。
提高生产效率,减少故障
优化生产布局
合理规划生产布局, 减少物料搬运和设备 调整时间,提高生产 效率。
强化设备维护
建立完善的设备维护 制度,确保设备的正 常运行,减少设备故 障对生产的影响。
FMEA定义及作用
FMEA作用 01
识别潜在的故障模式及其影响 02
评估故障模式的严重度、发生概率和可检测性 03
FMEA定义及作用
01 优先排序故障模式,确定改进措施
02 提高产品或过程的可靠性和安全性
FMEA发展历程
01 初始阶段
FMEA起源于20世纪40年代的军事领域,用于分 析飞机系统的故障模式。
收集生产过程的历史数据、故 障记录、操作规范等相关信息 。
制定改进措施
针对识别出的风险,制定相应 的改进措施,降低故障发生的 概率和影响。
设备、工艺及操作FMEA分析
设备FMEA分析
对生产设备进行FMEA分析,识 别设备潜在的故障模式、影响及 原因,制定相应的维护和改进措
施。
2024版FMEA培训教材全版

分配团队成员的任务和职责, 确保各项工作有序进行。
建立有效的沟通机制,促进团 队成员之间的信息交流和协作。
收集并分析相关数据资料
收集与FMEA分析对象相关的设计、 制造、测试、使用等过程中的数据资 料。
运用统计工具和方法,对数据进行分 析和处理,提高分析的准确性和效率。
对数据资料进行整理、筛选和分析, 识别潜在的故障模式、原因和影响。
FMEA培训教材全版
contents
目录
• FMEA基本概念与原理 • FMEA实施流程与步骤 • 故障模式识别与评估方法论述 • 故障原因分析及纠正措施制定 • FMEA报告编写与评审要求 • FMEA在企业实践中的应用案例
01
FMEA基本概念与原理
FMEA定义及作用
FMEA定义
FMEA(Failure Modes and Effects Analysis,失效模式与影 响分析)是一种预防性的质量工具,用于识别、评估和优先处 理潜在的产品或过程失效模式,以减少或消除其对产品质量、 安全性和可靠性的负面影响。
常见问题及解决方案
问题2
风险评估不准确
解决方案
提高评估人员的专业素质和经验水平,采用科学的评估方法和工具,确保风险评估的准确性。
常见问题及解决方案
问题3
建议措施不具体
解决方案
针对每种故障模式提出具体可行的预 防或改进措施,明确责任人和完成时 间,确保建议措施的有效实施。
常见问题及解决方案
问题4
案例二
某汽车零部件供应商在生产过程中,采用 FMEA方法对生产流程中的潜在问题进行识 别和改进,降低了产品缺陷率和生产成本。
电子产品行业FMEA应用案例剖析
案例一
某电子制造公司在产品研发阶段,运用FMEA 方法对电路板设计中的潜在故障进行分析和 预防,提高了产品的可靠性和稳定性。
FMEA培训教材4版new

FMEA手册的历程: 第一版:1993年2月 第二版:1995年2月 第三版:2001年7月 第四版:2008年6月 第四版的主要变动:
-强调FMEA的过程和结果需要管理者支持、关注和评审; -改进了严重度、发生频度、探测度的评级表; -不再强调“标准表格”; -建议不要把RPN作为风险评估的首要方法。使用RPN阀值是一种
SOP
………
批量爬 坡
2TP
100 初步设计
1000 A样件
仅有思维、图纸
10000
图纸释 放
100000
OTS样 件
有思维、图纸、 模具、检具、设 备、试制场所等
小批量 确认
有思维、图纸、模具、 检具、设备、人员、厂 房、仓储等
时间阶段
10 11 12 1 2 3 4 5 6 7 8 9 10 11 12 1
23
FMEA 成 功 的 条 件
适时性:在“时间之窗”关闭之前
+
小组的努力:集体的智慧
24
适时性
成功实施FMEA项目的最重要因素之一
FMEA是预防性的 不是反应性的
应当尽量避免失效 而不是等着顾客提出申诉
25
成功实施FMEA项目的最重要因素之一是时间性。其含义 是指“事件发生前”的措施,而不是“事实出现后”的演练。为 实现最大价值,FMEA必须在产品或过程失效模式被纳入到产品 或过程之前进行。事先花时间很好地完成FMEA分析,能够最容 易、低成本地对产品或过程进行更改,从而最大程度地降低后期 更改的危机。FMEA能够减少或消除实施可能会带来更大隐患的 预防/纠正性更改的机会。
FMEA由多功能小组开发,小组规模会根据设计的复杂性和 公司的规模大小而有所不同。小组要有相关的技术知识、足够的 时间,以及管理者批准的权限。
FMEA培训教材
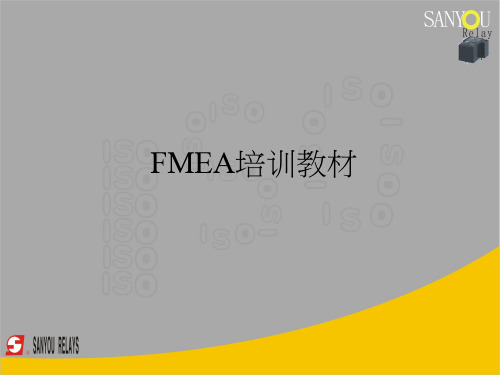
课程大纲
• FMEA基础定义 • FMEA的四大特点 • FMEA的作用 • FMEA的模型 • FMEA的格式 • FMEA的四大类型 • FMEA的效益 • FMEA的使用时机 • FMEA流程图
课程大纲
• FMEA的三大要素:严重度、频度、探测度 • 失效/后果/原因三者之关系 • 风险顺序数值(RPN)的计算 • FMEA改善的执行流程 • FMEA运作重点 • FMEA运用注意事项
FMEA的四大特点
FMEA 的特点(4)
• 动态性
• FMEA是动态文件,应始终反映 最新水平以及最近的相关措施。 应及时评估与更新.
FMEA可帮助确认
• 何种失效会发生? • 发生后会造成何种影响? • 该影响的重要性如何? • 何种原因导致失效? • 失效发生的可能性或频率多高? • 我们有何种控制方式? • 我们如何避免异常品流出? • 侦测失效的能力如何? • 总风险指数多高? • 用何种方法消除及降低风险?
FMEA的效益
• 预防潜在异常
– 去除潜在原因 – 选择较佳方法 --发展预防维护系统 --发展异常反应计划
FMEA的效益
• 制程改善
– 降低 制程异常, 检查点的最佳化。
• 其它
– 保留、移转及分享知识。 – 训练 – 提供设备制造者改善方向。
何时使用 FMEA?
• 新技术开发:
– 新技术发展时使用 – 依优先性改善制程/设备/物料
– 可为一组制程或仅为一部份或仅为特性值.
确认潜在失效模式
• 以过去数据为基础
• 列出所有可能失效模式
• 确认所有细项制程
– 考虑 4 M 1E • 列出于细项制程中所有可能之失效模式
2024年FMEA培训教材

FMEA培训教材引言:故障模式与影响分析(FlureModesandEffectsAnalysis,简称FMEA)是一种系统化的方法,用于识别和评估产品、过程或服务中潜在的故障模式及其影响。
本培训教材旨在为您提供FMEA的基本概念、方法和应用技巧,帮助您更好地理解和应用FMEA,以提高产品或过程的可靠性和安全性。
第一部分:FMEA的基本概念1.1故障模式与影响分析的定义1.2FMEA的目的和重要性1.3FMEA的类型和应用范围第二部分:FMEA的步骤和方法2.1FMEA的准备工作2.2故障模式识别2.3影响分析2.4严重度评估2.5发生概率评估2.6检测难度评估2.7风险优先级评估2.8制定改进措施和行动计划第三部分:FMEA的实践应用3.1FMEA团队的组建和培训3.2FMEA实施过程中的常见问题及解决方法3.3FMEA报告的编制和评审3.4FMEA与其他质量管理工具的结合应用第四部分:FMEA的持续改进4.1FMEA的跟踪和监控4.2FMEA的回顾和更新4.3FMEA的最佳实践分享和推广结论:通过本培训教材的学习,您应该能够了解FMEA的基本概念、方法和应用技巧。
FMEA是一种重要的质量管理工具,可以帮助组织识别和评估潜在的故障模式及其影响,从而采取相应的改进措施,提高产品或过程的可靠性和安全性。
希望本教材能够为您在FMEA的实际应用中提供指导和支持。
注意事项:1.本教材的内容仅供参考,具体应用时需结合实际情况进行适当调整。
2.FMEA的实施需要团队合作和专业知识的支持,建议在实施前进行相关培训和能力提升。
3.FMEA是一种持续改进的过程,需要定期回顾和更新,以适应组织的发展和变化。
关键词:FMEA、故障模式、影响分析、风险管理、质量改进、可靠性、安全性重点关注的细节:FMEA的步骤和方法详细补充和说明:1.故障模式识别:故障模式是指产品、过程或服务中可能出现的问题或失效方式。
在故障模式识别阶段,需要对产品、过程或服务进行全面的分析,列出所有可能的故障模式。
2024版FMEA培训教材(共14)

FMEA核心思想
预防性
FMEA强调在产品设计或过程设 计阶段进行预防性的分析,识别
并消除潜在的失效模式。
结构化
FMEA采用结构化的分析方法, 通过系统的、有条理的分析过程 来识别潜在的失效模式及其影响。
优先级
FMEA根据失效模式的严重度、 发生频度和探测度来评估其风险 优先级,以便优先处理高风险失 效模式。
01
02
03
04
FMEA报告
编写FMEA报告,包括分析过 程、结果汇总、风险控制措施
和建议等。
风险矩阵图
绘制风险矩阵图,直观展示各 种失效模式的风险等级和分布
情况。
改进措施计划
针对高风险失效模式,制定详 细的改进措施计划,明确责任
人、时间节点和预期效果。
经验教训总结
总结FMEA实施过程中的经验 教训,为后续产品设计和制造
跟踪改进措施实施情况
对制定的改进措施进行跟踪,确保措 施得以有效实施并取得预期效果。
产品设计阶段FMEA案例分析
案例一
案例二
某型号手机电池过热问题。通过对手 机电池设计进行FMEA分析,发现电池 过热可能导致手机性能下降甚至引发 安全问题。经过评估,该故障模式的 严重性较高。针对这一问题,改进措 施包括优化电池散热设计、提高电池 热稳定性等。
可靠性等方面的人员。
收集资料和信息
03
收集与产品、过程、历史数据等相关的资料和信息,以便进行
全面分析。
FMEA实施过程
识别潜在失效模式
通过分析设计、制造过程、使用条件 等方面,识别产品可能出现的潜在失 效模式。
确定风险等级
综合考虑失效模式的严重度、发生频 度和探测度,确定每种失效模式的风 险等级。
FMEA培训教材PPT完整版(2024)

产品设计阶段FMEA案例分析
案例一
某型号汽车发动机设计FMEA分 析。针对发动机系统可能出现的 故障模式进行分析,如气缸磨损 、活塞环断裂等,制定相应的改
进措施。
案例二
某型号手机电池设计FMEA分析 。针对电池可能出现的过热、短 路等故障模式进行分析,优化电 池结构和电路设计,提高电池安
全性。
26
过程控制阶段FMEA流程
定义过程范围和功能
01
识别潜在的故障模式
02
评估故障影响的严重度、发生
度和检测度
03
计算风险优先数(RPN)并排 序
04
制定并实施控制措施
2024/1/29
05
跟踪验证控制措施的有效性并
更新FMEA
06
27
过程控制阶段FMEA案例分析
案例一
某汽车制造厂涂装车间过程FMEA分 析
为生产过程FMEA提供支持
产品设计阶段FMEA的输出可以为生产过程 FMEA提供重要的输入和支持。
20
产品设计阶段FMEA流程
组建FMEA团队
由多部门、多学科的专业 人员组成,包括设计、制 造、质量、采购等。
2024/1/29
定义系统和子系统
明确产品的结构和功能, 划分系统和子系统。
识别故障模式
针对每个子系统或部件, 识别所有可能的故障模式 。
9
组建FMEA团队并分配任务
02
01
03
2024/1/29
组建多学科团队
包括设计、制造、质量、采购等相关领域专家。
分配角色与责任
明确团队成员的角色和责任,确保任务有效执行。
提供培训与支持
为团队成员提供FMEA培训,确保掌握相关知识和技 能。
FMEA培训教材ppt完整版

FMEA培训教材ppt完整版•FMEA概述与基本原理•失效模式识别与评估方法•故障原因分析技巧与工具应用•风险等级划分标准与应对措施制定目录•FMEA在产品设计阶段应用实践•FMEA在生产过程监控和持续改进中作用•总结回顾与展望未来发展趋势01FMEA概述与基本原理FMEA定义及发展历程FMEA定义故障模式与影响分析(FailureModes and Effects Analysis)发展历程起源于军事领域,后广泛应用于航空、汽车、电子等各个行业FMEA核心思想与目标核心思想预防性分析,识别潜在故障模式及其对系统的影响,提前采取措施降低风险目标提高产品可靠性、减少维修成本、增强客户满意度032. 功能分析识别系统或部件的功能及潜在故障模式01适用范围产品设计、生产过程、服务流程等各个环节021. 定义范围明确分析对象及目标评估故障模式对系统性能、安全、经济等方面的影响3. 故障影响分析综合考虑故障发生概率、严重度及可检测性,对故障模式进行风险等级排序4. 风险等级评估针对高风险故障模式,制定预防措施和应急计划5. 制定措施定期回顾FMEA 结果,更新措施并持续改进6. 跟踪与持续改进02失效模式识别与评估方法产品无法实现设计功能或性能不达标,如电子设备无法开机、机械部件卡滞等。
功能性失效安全性失效可靠性失效产品存在安全隐患,可能导致人身伤害或财产损失,如汽车刹车失灵、电器短路引发火灾等。
产品在规定条件下和规定时间内无法完成规定功能,如电池寿命短、设备频繁故障等。
030201常见失效模式类型介绍失效模式识别技巧与工具技巧了解产品工作原理及结构特点分析历史故障数据及维修记录•运用头脑风暴等方法集思广益工具故障树分析(FTA)事件树分析(ETA)因果图(Cause-Effect Diagram)01020304•方法选择:根据失效模式的性质和影响程度选择合适的评估方法,如风险矩阵、风险指数等。
实施流程1. 明确评估目标和范围2. 收集相关数据和信息3.选择合适的评估方法并建立评估模型4.对失效模式进行定量或定性评估5.根据评估结果制定相应的改进措施并跟踪验证03故障原因分析技巧与工具应用故障树分析法概述故障树的建立故障树的定性分析故障树的定量分析故障树分析法(FTA )原理及应用01020304介绍FTA 的基本概念、原理、作用及适用范围。
2024年干货新版FMEA培训教材

本次培训成果回顾
01
掌握了FMEA的基本概 念、原理和实施步骤;
02
学习了如何识别和评估 潜在失效模式、影响及 原因;
03
了解了如何制定有效的 控制措施以降低风险;
04
通过案例分析和实战演 练,加深了对FMEA方 法的理解和掌握。
企业实施FMEA建议与注意事项
01
02
03
04
建立完善的FMEA团队,包括 跨部门的专家和技术人员;
生产过程改进中FMEA应用
优化生产流程
针对FMEA分析中发现的问题, 对生产流程进行优化,减少潜在
的故障点。
引入先进技术
采用先进的生产技术和管理方法 ,提高生产过程的稳定性和效率
。
加强员工培训
提高员工技能和素质,减少人为 错误对生产过程的影响。
生产过程监控与持续改进
实时监控生产过程
通过传感器、数据分析等手段实时监控生产过程,及时发现并处 理潜在问题。
评估供应商性能
通过对供应商的历史数据进行分析,利用FMEA 工具可以对其未来的性能进行评估,从而选择最 合适的供应商。
制定风险应对措施
针对识别出的供应商风险,可以制定相应的应对 措施,如增加库存、采用更严格的检验标准等。
供应链风险管理中FMEA应用
识别供应链风险
FMEA可以帮助企业识别出供应链中潜在的风险,如自然灾害、政 治风险等。
产效率、优化库存管理等。
02
制定改进计划
针对识别出的改进机会,可以制定相应的改进计划,包括目标、时间表
、划的实施情况进行监控,可以评估出改进的效果,从而决
定是否需要进行进一步的改进。同时,FMEA也可以帮助企业识别出新
FMEA培训教材

FME培训教材的主 要内容
FME培训教材的特 点和优势
FME培训教材的应 用范围和效果
FME培训教材的未 来发展趋势和展望
FME未来发展趋势和展望
技术进步:FME将更加智能化、自动化提高分析效率和准确性 应用领域:FME将在更多行业和领域得到应用如医疗、航空航天等 培训需求:FME培训需求将持续增长培训内容将更加丰富、多样化 国际合作:FME国际合作将加强共同推动FME的发展和应用
汽车行业背景:全球汽车市场发展迅速竞争激烈 FME在汽车行业的应用:用于产品设计、制造、质量管理等环节 案例分析:某汽车制造商通过FME分析发现并解决了产品设计中的潜在问题 结论:FME在汽车行业中的应用可以有效提高产品质量和生产效率
案例二:医疗器械中的FME应用
医疗器械:包括医疗设备、医疗耗材等 FME在医疗器械中的应用:风险评估、质量控制、故障分析等 案例分析:某医疗器械公司的FME实践 结论:FME在医疗器械行业中的应用效果显著有助于提高产品质量和患者安全。
掌握FME 报告的编 写和审核 技巧
学会如何 将FME应 用于实际 工作中提 高产品质 量和生产 效率
FME实践操作案例分析
案例背景:某汽车制造企业 问题描述:产品质量问题 FME分析:识别潜在失效模式、失效原因、失效影响 改进措施:优化生产工艺、加强质量控制、提高员工技能 效果评估:产品质量提升、生产效率提高、客户满意度提高
THNK YOU
汇报人:
FME的实施需要跨部门团队的参与 包括设计、制造、质量、采购、销 售和服务等部门。
FME培训教材内容
FME的分析阶段
确定分析对象:选择需要分析的产品或过程 收集数据:收集与分析对象相关的数据 分析风险:分析可能导致失效的原因和影响 制定措施:制定预防或纠正措施降低风险
2024全新第五版fmea培训教材

2024全新第五版fmea培训教材一、教学内容1. 章节一:FMEA概述内容:介绍FMEA的定义、目的、历史和发展趋势。
2. 章节二:FMEA的步骤内容:详述FMEA的准备工作、执行过程、数据收集与分析、制定改进措施等步骤。
3. 章节三:FMEA的应用内容:举例说明FMEA在各种领域的应用,如制造业、医疗设备、航空航天等。
4. 章节四:FMEA与风险管理内容:探讨FMEA在风险管理中的作用、优势和局限性。
二、教学目标1. 学生能理解FMEA的基本概念和目的。
2. 学生能掌握FMEA的步骤和应用。
3. 学生能认识到FMEA在风险管理中的重要性。
三、教学难点与重点重点:FMEA的基本概念、步骤和应用。
难点:FMEA的数据收集与分析、制定改进措施。
四、教具与学具准备教具:PPT、投影仪、白板、马克笔。
学具:教材、笔记本、彩色笔。
五、教学过程1. 实践情景引入:以一次飞机事故为例,引导学生思考如何预防类似事故的发生。
2. 章节一:FMEA概述细节:介绍FMEA的定义、目的、历史和发展趋势,通过实例让学生了解FMEA的实际应用。
3. 章节二:FMEA的步骤细节:详述FMEA的准备工作、执行过程、数据收集与分析、制定改进措施等步骤,并以一个具体案例进行讲解。
4. 章节三:FMEA的应用细节:举例说明FMEA在各种领域的应用,如制造业、医疗设备、航空航天等,让学生了解FMEA的广泛应用。
5. 章节四:FMEA与风险管理细节:探讨FMEA在风险管理中的作用、优势和局限性,引导学生思考如何充分利用FMEA进行风险管理。
6. 随堂练习:让学生以小组为单位,选取一个感兴趣的领域,运用FMEA进行风险分析,并分享分析结果。
7. 例题讲解:针对教材中的典型例题,进行详细讲解,引导学生学会运用FMEA进行实际问题的分析。
六、板书设计板书内容:FMEA的基本概念、步骤、应用及其在风险管理中的重要性。
七、作业设计答案:由于作业需要根据具体产品或项目进行分析,故答案不固定。
FMEA_培训教材

引言概述:正文内容:1.FMEA的背景和目的1.1FMEA的起源和发展1.1.1FMEA的起源1.1.2FMEA在质量管理中的地位1.2FMEA的目的和应用领域1.2.1FMEA的目的和价值1.2.2FMEA的应用领域2.FMEA的基本原则2.1风险分析的基本原则2.1.1风险分析的基本概念2.1.2风险分析的基本原则2.2FMEA的基本原则2.2.1FMEA的基本概念2.2.2FMEA的基本原则和要求3.FMEA的工作步骤3.1FMEA的准备阶段3.1.1确定分析团队和目标3.1.2收集相关资料和信息3.2FMEA的分析阶段3.2.1确定系统、功能和失效模式3.2.2评估失效后果和严重性3.2.3判断失效发生的可能性和频率3.3FMEA的解决阶段3.3.1确定改进措施和对策3.3.2评估改进方案的效果和风险3.4FMEA的跟踪和监控阶段3.4.1实施改进方案并跟踪效果3.4.2监控失效模式和指标4.FMEA分析的技巧4.1风险评估和优先级排序4.1.1风险评估的方法和指标4.1.2优先级排序的技巧和要点4.2利用工具和方法辅助分析4.2.1使用流程图和树状图4.2.2应用统计分析和数据挖掘技术5.FMEA的实施挑战与解决方案5.1团队合作和意识培养5.1.1培养团队合作和沟通意识5.1.2增强风险意识和质量意识5.2数据收集和信息管理5.2.1高效收集和整理相关数据5.2.2建立完善的信息管理系统5.3持续改进和监控5.3.1建立持续改进机制5.3.2定期监控和评估FMEA的效果总结:。
风险分析工具FMEA培训教材
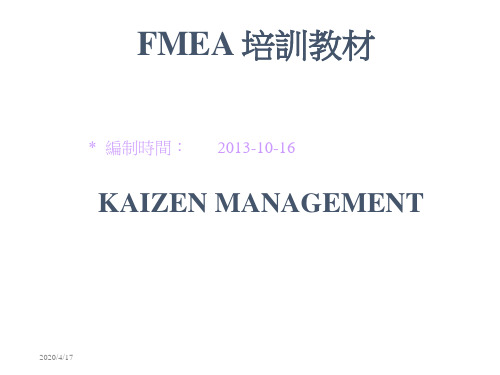
4、評估影響的嚴重程度 (severity), 附表1、2。 5、分析失效的可能原因 (failure cause),人、机、料、法、環等原
因。見因果圖。 6、評估其發生的可能性 (occurance), 附表1、3。
Medium risk
Oven curing
Medium risk
Soldering
Low risk
Grounding
Low risk
2020/4/17
對危險性高的工序作“* ”標記,表示將對此工序進行 Process FMEA.
8、PFMEA 案例与相關表格
2、确定所要分析的失效模式 (potential failure mode), 附表1。
* 檢測失效的能力?
Detection
* 風險优先指數? * 建議行動?
Risk Priority Number (RPN) Recommended action
2020/4/17
風險优先指數(RPN)
RPN 評价 理解或行動 1 < RPN< 50 對產品有較小的危害
51 < RPN <100 對產品有中等的危害,需進一步改善
2
返工,產品的不足被很敏銳的客戶所注意
無
1
2020/4/17
附表3 :評估其發生的可能性
失效的可能性 很高;失效是不可避免
可能的失效率 >> = 1 in 2
CPk < 0.33
等級 10
高:通常与工序聯系在一起,類似于 經常出現失效的前工序
中等:通常与工序聯系在一起,類似 于偶爾出現換效的前工序。但不 是主要的部分。
- 1、下载文档前请自行甄别文档内容的完整性,平台不提供额外的编辑、内容补充、找答案等附加服务。
- 2、"仅部分预览"的文档,不可在线预览部分如存在完整性等问题,可反馈申请退款(可完整预览的文档不适用该条件!)。
- 3、如文档侵犯您的权益,请联系客服反馈,我们会尽快为您处理(人工客服工作时间:9:00-18:30)。
* 當前工序控制方法?
* 檢測失效的能力? * 風險优先指數? * 建議行動?
Current Process Control Plan
Detection Risk Priority Number (RPN) Recommended action
風險优先指數(RPN)
RPN 評价 理解或行動
對產品有較小的危害
8、PFMEA 案例与相關表格
以分析Cosmos HFA 在組裝過程中對Slider profile影響為例
1、确定工序 Flow chart / Risk Assessment 工序流程 / 危險性評估
Process step (工序步驟)
* Pot mounting block & gimbal with epoxy Oven curing
較低水平的控制 低水平的控制
難于控制
很難控制 几乎無法控制
非常多
几乎全部
1 in 5
>1 in 2
7.2 FMEA 風險評估
O 1 1 1 1 10 10 10 10 S 1 1 10 10 1 1 1 10
風險評估參考
評估等級 D 1 10 1 10 1 10 10 10 理想狀態 完全可控制 不會流到客戶方 流到了客戶方 頻繁發生的失效 頻繁流到客戶方 造成重大影響 最主要的問題 無要求 無要求 無要求 Ye s Ye s Ye s Ye s Ye s 失效原因 采取行動
3、設備維護的FMEA (EFMEA---Equipment FMEA):
如新設備的投入運行,我們亦可以預先進行 EFMEA,分析、考慮由于設備可能造成的
產品品質問題及可靠度問題等原因,預防采取措施消除不良因素;現有設備、特定的一种設
備在運行中出現的設備故障等均可采用FMEA進行改善,以确保設備的正常運轉。
Risk Assessment 危險性評
High risk Medium risk
A、B、C dimension & skew check
Mount FPC Pot shield ring with epoxy
Low risk
Low risk Medium risk
Oven curing
Sold生概率? 測試性?
否
* 收集數据 * 排定原因 * 選定主因 * 确認改善
修定文件, 重新排列
FMEA Development Process Work Sheet
Page:
of
潛在的原因
法
Design or Process Function
潛在影響 机
料
失敗模式
人
環境
1、FMEA 的開發与發展
20世紀 60年代,美國宇航界首先研究開發 FMEA; 1974年,美國海軍建立一個 FMEA 標准; 1976年,美國國防部首次采用 FMEA 標准;
70年代后期,美國汽車工業開始運用 FMEA;
80年代中期,美國汽車工業將 FMEA 運用于生產過程中; 90年代,國際 ISO 標准組織將 FMEA 納入 QS9000 標准;在 TQS9000体系中,是4.20統計技術這個要素中的首要審核項目
RPN
Recommended Actions
7.1 FMEA 計分標准
FMEA 定義 概念性 說明 原因, 失效模式, 效應 和 控制方案 風險評估 分數
1 2 3
清單式控制
全檢 產品測試 控制方案
效應
FMEA 類型
系統 功能 組件 功能
原因 裝錯配件 未插入
系統
設計
測試時組件失效
設備功能
設備
培訓不足
99年12月,由 TDK 公司主持對我厂進行的 TQS9000 審核在“
統計技術”這個要素的審核中正式提出“FMEA”的審核要求。
2、什么是 FMEA (1)
FMEA 的英文全稱是 Failure Mode & Effect Analysis ;
FMEA 的中文意思是失效模式和效應分析 ; 失效模式 (Failure Mode): 指制造過程無法達到預定或規定的要 求所表現出的現象;如:坏品、不良設備狀況等;
附表1:在附表 1 中包含以下 6 個方面的內容,因附表 1 容量
太大,另存在 Excel 中
* 确定所要分析的失效模式。
* 分析失效模式對客戶的所造成的影響 。
* 評估影響的嚴重程度。 * 評估其發生的可能性。
* 确定當前的工序控制方法并評估其檢測失效的可能性。
* 确定 RPN 值并根据 RPN 值采取相應的改善措施。
隊組選擇
*組員需多個部門組成. * 多層次 (對原因与效果進行研究, 在 應用方 面有足夠經驗). * 可推動改善措施實施.
确定工序/功能 * 使用流程圖以顯示當前/計划的
工序/功能. 計算風險 (一個失效模式一個值). * 嚴重性 Severity. * 各失效模式的嚴重性出現概率 (S x O) . * 風險指數 RPN = S x O x D.
5、FMEA 的應用范圍(2)-品質改善程序
DFMEA
PFMEA
控制方案 投入 工序 出貨 研究 / 測量 否 是否 變 异? 是 与控制界限 進行比較 產品
改善行動 消除變异 惡性 合并 良性
改善系統
尋找預期 的變异
研究變异 的性質 研究變异 的原因
6、開展FMEA 的程序步驟(1)
FMEA 主要目標: * 測試性 * 失效模 式 * 標識 原因 和效應 * 文件 * 控制方 案* 制作 Pareto圖 * 標識必 要 的改善 結果 和時 机。
4、評估影響的嚴重程度 (severity), 附表1、2。
5、分析失效的可能原因 (failure cause),人、机、料、法、環等原
因。見因果圖。
6、評估其發生的可能性 (occurance), 附表1、3。
7、确定當前的工序控制方法并評估其檢測失效的可能性,附表1、4。
8、确定 RPN 值并根据 RPN 值采取相應的改善措施,附表1。
效應 (Effect): 指失效模式在客戶處(包括下工序)所造成的結果;
2、什么是 FMEA (2)
FMEA 是一种用來确認風險的分析方法,它包含: 确認潛在的失效模式并評价其產生的效應;
确認失效模式對客戶所產生的影響;
确認潛在的產品/過程失效原因; 确認現有控制產品/過程失效的方法; 确定排除或降低失效改善方案; 設計之前預先進行風險分析,确保設計水平。
1、 FMEA 是 一种統計工具:
* 控制工具: 設計控制 / 生產控制 / 過程控制; * 風險性分析工具; * 管理工具: 識別和評估潛在的失效模式及其影響; 确定能夠消除或減少潛在的失效發生的改善措施。
4、FMEA 的作用(2)
2、FMEA 可幫助我們量化确認:
* 哪一种失效會發生? Failure mode * 發生后會造成什么影響? Effect * 其影響的嚴重性有多大? Severity * 是哪一种原因導致失效? Cause * 失效發生概率? Occurrence
FMEA 培訓教材
* 編制時間: 2013-10-16
KAIZEN MANAGEMENT
Thanks a lot !
FMEA培訓教材目錄
FMEA 的開發与發展
什么是 FMEA FMEA 的特點 FMEA 的作用 FMEA 的應用范圍
開展 FMEA 的程序步驟
FMEA 計分標准与風險評估參考 FMEA 案例与相關表格
具体的原因-失效-效應研究 * 腦力激蕩 / 定義失效模式. * 標識主要原因. * 定義失效模式的效應. 測試性柏拉圖 * 指標為 S, SxO 和 RPN. * 標識失效模式中的“關鍵的少數".
開展改善行動 * 集中于“關鍵的少數".
6、開展FMEA 的程序步驟(2)
(續)
失效模式. 功能性缺陷. 失效原因 * 失效模式的主要潛在原因.
6、PFMEA 的程序步驟(2)
繪出流程圖 确定各個工序的功能 RPN =O x S x D 制作 Pareto 圖 選擇失效模式 進行改善 標識其效應 標識其原因 標識當前控制 方法 估計嚴重性 估計發生概率 估計測試性
是
确定失效模式
RPN= 風險指數
完成? 是 否
* 收集數据 * 致力改善 * 确認效果 * 推廣行動
1 < RPN< 50
51 < RPN <100
101 < RPN <1,000
對產品有中等的危害,需進一步改善
對產品有嚴重危害,需深入調查分析
5、FMEA 的應用范圍(1)
1、設計階段的FMEA (DFMEA---Design FMEA):
如新工序的設計,我們可以預先進行DFMEA,盡可能周全地考慮產品規格,工序操作 水平、工序能力等諸多因素,使工序符合規定的要求。
2、生產過程的FMEA (PFMEA---Process FMEA):
針對工序間的首要坏品,可運用 PFMEA 作量化分析,在影響坏品產生的諸因素中,哪 一個系統原因影響最大?是否主要原因。。。。。其它,如 CPk 低、生產過程异常等等都可
以通過采用 PFMEA 直觀地找出主要原因,進行改善達到應有的效應。
失效模式
組件無功能
工序
功能工序 測試性(D): 在客戶方發生 失效的可能性的等級。 可靠的測試控制 比較可靠的測試控制 良好的測試控制 測試控制
不完全的測試控制
嚴重性(S): 對應于某潛 在 失效效應的嚴重程度。 對工序或客戶無影響 客戶可能忽略的失效 對性能有微小影響 對性能有較小影響 對性能有影響 工序/產品性能會降 低但安全 工序/產品性能會降低 很嚴重以致不可修 复或無法使用 非常嚴重 (帶有 警報提示的影響) 安全性或可靠性故障 (不帶有警報提示的影響)