零部件审核作业指导书
SOP标准作业程序与作业指导书

SOP标准作业程序与作业指导书作业名称:装配产品A的一、背景介绍装配产品A是我公司的主要产品之一,为了确保产品质量的稳定性和生产效率的提高,制定SOP标准作业程序与作业指导书非常重要。
本文将详细介绍装配产品A的SOP标准作业程序与作业指导书的内容和要求。
二、SOP标准作业程序1. 目的SOP标准作业程序的目的是确保装配产品A的每个步骤都按照标准操作进行,以减少错误和提高生产效率。
2. 适用范围本SOP标准作业程序适用于装配产品A的生产线。
3. 责任与权限3.1 生产主管负责制定和更新SOP标准作业程序。
3.2 操作员需严格按照SOP标准作业程序进行操作。
4. SOP标准作业程序的编写和更新4.1 SOP标准作业程序由生产主管编写,并定期更新。
4.2 更新SOP标准作业程序需要经过生产主管的审核和批准。
4.3 更新后的SOP标准作业程序需及时通知相关操作员。
5. SOP标准作业程序的内容5.1 工作环境准备5.1.1 检查工作区域是否整洁,无杂物。
5.1.2 检查所需工具和设备是否齐全,正常工作。
5.1.3 确认所需材料是否准备充足。
5.2 操作步骤5.2.1 步骤1:取出产品A的零部件。
5.2.2 步骤2:根据装配图纸将零部件按序装配。
5.2.3 步骤3:使用扭力扳手进行紧固。
5.2.4 步骤4:进行产品A的功能测试。
5.2.5 步骤5:清洁和包装成品。
5.3 安全注意事项5.3.1 操作员需佩戴防护手套和眼镜。
5.3.2 操作过程中注意避免尖锐物品的伤害。
5.3.3 发现异常情况及时上报。
6. SOP标准作业程序的记录和保存6.1 操作员需按照SOP标准作业程序进行操作,并记录操作时间和结果。
6.2 操作记录需保存至少一年。
三、作业指导书1. 目的作业指导书的目的是为操作员提供装配产品A的详细步骤和操作要点,以确保操作的准确性和一致性。
2. 适用范围本作业指导书适用于装配产品A的操作员。
3. 作业指导书的编写和更新3.1 作业指导书由生产主管编写,并定期更新。
《组装作业指导书》

《组装作业指导书》组装作业指导书引言概述:组装作业指导书是为了帮助工人正确、高效地进行组装工作而编写的指导性文件。
它包含了组装流程、注意事项、安全提示等内容,能够提高工作效率、保证产品质量,确保工人的安全。
下面将详细介绍组装作业指导书的内容。
一、组装前准备1.1 清点零部件:在开始组装之前,首先要对所有零部件进行清点,确保没有遗漏。
1.2 准备工具:根据组装所需工具清单,准备好所有需要的工具,以免中途中断。
1.3 检查工作环境:确保组装工作的环境安全整洁,避免因为杂物干扰而影响工作进度。
二、组装流程2.1 按照指导书步骤进行:严格按照组装作业指导书中的步骤进行组装,不得随意更改顺序。
2.2 注意零部件的方向和位置:在组装过程中,要注意零部件的方向和位置,确保组装正确。
2.3 注意配件的搭配:对于需要搭配使用的配件,要确保搭配正确,避免因为搭配错误导致组装失败。
三、注意事项3.1 注意安全:在组装过程中,要注意安全,避免因为疏忽导致意外发生。
3.2 注意细节:组装过程中要注意细节,确保每一个步骤都做到位,避免因为细节问题导致产品质量不达标。
3.3 注意保养:组装完成后,要对产品进行保养,延长产品的使用寿命。
四、质量检验4.1 外观检查:组装完成后,进行外观检查,确保产品外观完整无损。
4.2 功能检测:对产品进行功能检测,确保产品功能正常。
4.3 安全检查:对产品进行安全检查,确保产品符合安全标准。
五、组装后清理5.1 清理工作台:组装完成后,要清理工作台,保持工作环境整洁。
5.2 整理工具:将使用过的工具整理归位,确保下次使用时能够方便取用。
5.3 归档资料:将组装作业指导书和相关资料进行归档,以备日后查阅。
结语:组装作业指导书是组装工作中必不可少的工具,它能够指导工人正确进行组装工作,提高工作效率、保证产品质量,确保工人的安全。
因此,在进行组装工作时,一定要严格按照组装作业指导书的要求进行操作,遵循操作规程,做好每一个细节,确保组装工作顺利进行。
零部件一级总成检具开发评审及认可作业指导书

工程师在检具供应商处预评审;
输出《检具三坐标测量报告》
检具供应商、零
首先由零部件供应商对检具进行制造预评审,根据《检具制造检查表》逐项检查,评审问题
部件供应商
清单提交福田检具工程师,检具供应商组织预评审问题整改;
零部件供应商输出《检具制造检查表》和《问题 检具供应商、零
检具通过零部件供应商制造评审认可后再由SQE、检具工程师和零部件供应商进行检具预验 整改报告》
性和再现性报告、检具操作指导书;
更新《APQP问题清单》、检具图纸和数模
检具工程师
6 检具验收小组根据《检具验收报告》项目,⑴检具检测报告,⑵检具重复性和再现性报告,⑶
检具操作指导书,⑷检具图纸和数模,⑸检具设计检查表,⑹检具制造检查表,逐项进行检具综 输出《检具验收会议纪要》
检具工程师
合验收;
检具验收小组对检具制造评审的问题进行确认,问题写入检具验收APQP问题清单;
检具工程师
检具制作加工: 4 检具供应商根据评审认可的检具设计方案和设计评审问题清单制作加工检具
检具供应商的检具制造满足福田要求和进度,零 检具供应商、零
部件供应商负责监督
部件供应商
检具制造认可:
检具图纸和3D数模
检具供应商完成检具三坐标检测报告,检具图纸和3D数模等资料,通知零部件供应商和检具
检具供应商、零 部件供应商
保存期限: □普通 ■秘密 □机密 □绝密
责任人
产品工程师
《整车测点图》、《零部件测点图》
尺寸工程师
输出《检具设计制作计划时间进度表》
零部件供应商、 SQE
输出《检具设计方案》符合福田对检具质量和进 零部件供商 度等方面的要求
流程步骤示意图
产品审核作业指导书(两篇)
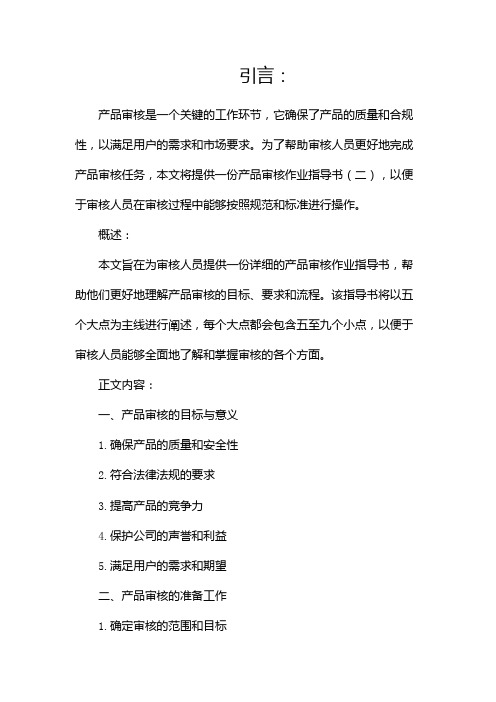
引言:产品审核是一个关键的工作环节,它确保了产品的质量和合规性,以满足用户的需求和市场要求。
为了帮助审核人员更好地完成产品审核任务,本文将提供一份产品审核作业指导书(二),以便于审核人员在审核过程中能够按照规范和标准进行操作。
概述:本文旨在为审核人员提供一份详细的产品审核作业指导书,帮助他们更好地理解产品审核的目标、要求和流程。
该指导书将以五个大点为主线进行阐述,每个大点都会包含五至九个小点,以便于审核人员能够全面地了解和掌握审核的各个方面。
正文内容:一、产品审核的目标与意义1.确保产品的质量和安全性2.符合法律法规的要求3.提高产品的竞争力4.保护公司的声誉和利益5.满足用户的需求和期望二、产品审核的准备工作1.确定审核的范围和目标2.收集和准备审核的相关文件和资料3.组织和安排审核的时间和地点4.选拔合适的审核团队成员5.制定审核计划和时间表三、产品审核的流程和方法1.审核前的准备工作(1)审核文件和资料的审查(2)审查审核计划和时间表(3)分配审核任务和责任2.审核的实施过程(1)与被审核单位的沟通和协调(2)实地考察和观察(3)文件和资料的复核和核对(4)采集样品进行实验和测试(5)进行访谈和讨论3.审核结果的处理和记录(1)编写审核报告(2)提出问题和发现的整改要求(3)确定审核结果和结论(4)归档审核文件和资料四、产品审核的注意事项1.保持独立和客观的态度2.遵守保密和道德规范3.注意审核过程中的信息安全4.注意与被审核单位的沟通和协调5.充分利用审核工具和方法五、产品审核的优化与改进1.审核流程的优化和简化2.提高审核团队成员的能力和素质3.借鉴和应用最佳实践4.不断学习和更新审核知识5.审核结果的跟踪和评估总结:产品审核是一个复杂和严谨的工作,它需要审核人员具备扎实的专业知识和丰富的实践经验。
本文提供的产品审核作业指导书(二)致力于帮助审核人员更好地理解和掌握产品审核的各个方面,从而提高审核的质量和效率。
汽车制造专业审核作业指导书
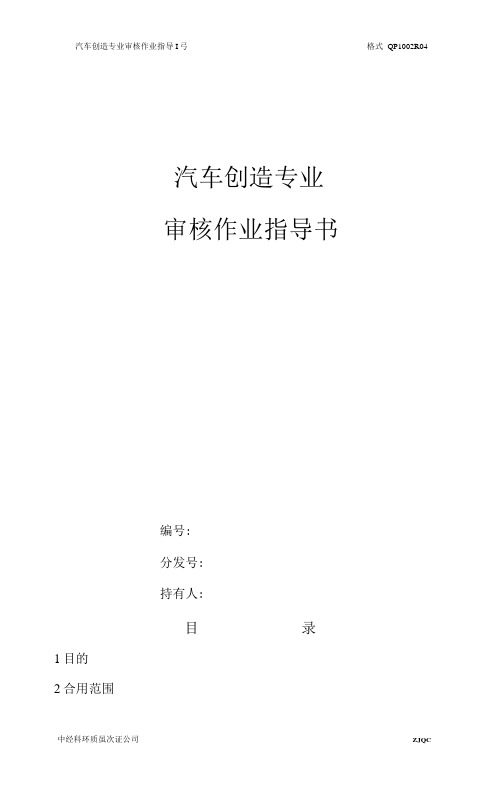
汽车创造专业审核作业指导书编号:分发号:持有人:目录1目的2合用范围3流程简介4专业特点5审核要点和审核方法6合用的法律、法规强制性标准7其他需要说明的问题附录A QC/T900-1997 (汽车整车产品质量检验评定方法〉附录B GB7258-1997 (机动车安全运行技术条件〉1、目的结合汽车整车创造行业的生产特点进行质量管理体系的审核,作为部份标准条款的审核内容的替代或者补充。
以全面满足GB/T19001—2000 idt 1509001:2000质量管理体系标准要求。
2、合用范围本审核作业指导书合用于22DM34.10汽车整车创造企业加工(汽车零部件创造详见34.30;车身创造详见34.20)、组装调试、成品车的检验和试验、仓储、运输交付和售后服务的全过程。
3、生产和服务流程简介4.专业特点:汽车创造业的产品具有功能性、安全性、环保性,是一个特殊的行业。
其特点为:1)结构复杂,专业众多,需要广泛的社会协作,分承包方众多。
每一个创造厂都有多种车型,每一种车型都具备动力及传动系统,制动系统、转向系统,悬挂系统,车身、内饰、电气系统、空调系统等;每一个系统由多个部件或者总成组成。
每一组装厂都有众多的零部件分供方,提供配套产品,因此对分供方评价和控制是审核的一个重点。
2)汽车产品既有功能性要求又有安全性、环保性、舒适性要求。
其产品组成部份包括:实现行驶功能部件,如:发动机、传动轴、先后桥、车轮、制动器等;汽车电气设备:发机电、起动机、点火系统、电喷系统、灯具、喇叭等;实现安全性要求的部件:ABS防抱死装置、安全带等;实现舒适性要求的部件:悬挂系统、1=1减震器、座椅、内饰等;实现环保功能的:消声器、尾气净化等。
应按各类不同的法规要求和进行审核。
3)汽车整车创造具冇流程长的特点,在任何一个环节浮现的问题都会导致对最终产品的影响。
必须重点检查各个环节的检验和试验记录。
4)汽车作为安全性产品具有可追溯性惟一标识,应在现场审核中加以注意:车架号码、发动机号码等标识是否清晰并记载在车辆档案中。
汽车审核作业指导书版.doc

汽车审核作业指导书3版11. 范围本指导书适用于本中心审核员对汽车产品的质量管理体系审核提供指导。
2引用文件国家发展和改革委办公厅2003/11/10关于公布车辆生产企业世界制造厂识别代号的通知GB7258-1997《机动车运行安全技术条件》QC/T 3-1992《汽车产品图样及设计文件完整性》QC/T 4-1992《汽车产品图样及设计文件采用与更改办法》QC/T900-1997《汽车整车产品质量检验评定方法标准》GB/T1332—91《载货汽车定型试验》GB/T13043—91 《客车定型试验规程》GB/T13044—91 《轻型客车定型试验规程》QC/T29020—91 《微型货车定型试验规程》ZBT50001—84 《专用汽车定型试验规程》JB/T3693—91《重型矿用自卸汽车定型试验规程》GB/T5397—85《摩托车定型试验规程》3.行业特点我国汽车标准法规体系主要参照ECE/EEC技术法规制定,目前以强制性标准形式体现,其构成及制定情况详见附件A。
我国现行汽车行业政府主管部门为国家发展和改革委员会。
但原国家机械工业局作为汽车行业政府主管部门时颁布的汽车行业标准依然有效。
原国家机械工业局1999年发布文件,规定自2000年4月1日起对行业生产的新车实行40项强检规定,但不同车型其强检的项目有所差异。
我国在用车辆的技术状态应符合GB7258—1997《机动车运行安全技术条件》的规定。
对整车厂(含底盘生产厂及各种改装厂)不得删减7.3。
即使该厂的产品设计为外包(这种情况实际是存在的),但该厂也应对产品满足顾客要求的能力与责任负责。
国家机械工业部明确规定,汽车的强检项目是以整车为单位,而不以其零部件是否符合规定,而对整车进行评价。
所以整车厂(最终制造厂)对车辆的技术指标负责。
另一方面,国家机械工业局于1999年1月18日以国机管[1999]20号文发布了《车辆识别代号(VIN)管理规则》(即CMVR A01-01),规定从文件发布之日起,国内生产的整车产品必须按VIN的规则进行标识,以便提高车辆故障信息反馈的准确性。
汽车零部件行业 MSA作业指导书
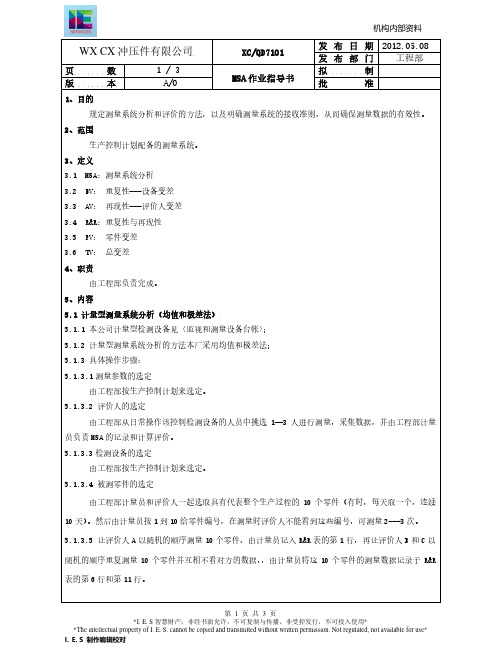
页 数 1 / 3MSA作业指导书拟 制版 本 A/0 批准1、目的规定测量系统分析和评价的方法,以及明确测量系统的接收准则,从而确保测量数据的有效性。
2、范围生产控制计划配备的测量系统。
3、定义3.1 MSA:测量系统分析3.2 EV: 重复性---设备变差3.3 AV: 再现性---评价人变差3.4 R&R:重复性与再现性3.5 PV: 零件变差3.6 TV: 总变差4、职责由工程部负责完成。
5、内容5.1 计量型测量系统分析(均值和极差法)5.1.1 本公司计量型检测设备见〈监视和测量设备台帐〉;5.1.2 计量型测量系统分析的方法本厂采用均值和极差法;5.1.3 具体操作步骤:5.1.3.1测量参数的选定由工程部按生产控制计划来选定。
5.1.3.2 评价人的选定由工程部从日常操作该控制检测设备的人员中挑选1--3人进行测量,采集数据,并由工程部计量员负责MSA的记录和计算评价。
5.1.3.3检测设备的选定由工程部按生产控制计划来选定。
5.1.3.4 被测零件的选定由工程部计量员和评价人一起选取具有代表整个生产过程的10个零件(有时,每天取一个,连续10天)。
然后由计量员按1到10给零件编号,在测量时评价人不能看到这些编号,可测量2---3次。
5.1.3.5 让评价人A以随机的顺序测量10个零件,由计量员记入R&R表的第1行,再让评价人B和C以随机的顺序重复测量10个零件并互相不看对方的数据,,由计量员将这10个零件的测量数据记录于R&R 表的第6行和第11行。
页 数 2 / 3MSA作业指导书拟 制版 本 A/0 批准5.1.3.6 使用不同的随机测量顺序重复上述操作过程,把数据填入第2、7和12行,如果需实验三次,则重复上述操作,记录于R&R表的第3、8和13行。
5.1.3.7 如果评价人在不同的班次,可以使用一个替换的方法。
让评价人A测量10个零件,并将数据记录于第1行,然后,让评价人A按不同的顺序重新测量,由计量员将结果记录于第2行和第3行,评价人B和C,也同样做。
(完整版)检验作业指导书

1.5.3.3重工
送检批几乎全部不合格,但经过加工处理后,货品即可接受。在此情况下,由公司抽调人力进行来货再处理。IQC对加工后的货品进行重检,对合格品接受,对不合格品开出《IQC退货报告》交相关部门办理退货。此类货品由IQC统计加工工时,对供应商做扣款处理。
2.1.3通过过程检验,防止不合格品流入下一道工序,甚至可能装在最终的产品上,以致造成不合格品出厂。
2.2首件检验
2.2.1定义及目的
首件检验是在生产开始时(上班或换班)或工序因素调整后(换人、换料、换活、换工装、调整设备等)对制造的第1件(大件产品)或前3件(非大件)产品进行的检验。目的是为了尽早发现过程中影响产品质量的系统因素,防止产品成批报废。
适用于来货数量少、价值高、不允许有不合格品物料或公司指定进行全检的物料。
1.4.2免检方式
适用于低值、辅助性材料或经认定的免检厂来料以及生产急用而特批免检的,对于后者IQC应跟进生产时的品质状况。
1.4.3抽样检验方式
适用于平均数量较多、经常性使用的物料。
样本大小:批量的10%(不少于20件),允收数AC=0,拒收数RE=1。
检验作业指导书
1.进料检验
1.1定义
进料检验又称来料检验,是制止不良物料进入生产环节的首要控制点。进料检验由IQC执行。
1.2检测要项
IQC在对来货检验前,首先应清楚该批货物的品质检测要项,不明之处要向本部门主管问询,直到清楚明了为止。在必要时,IQC验货员可从来货中随机抽取两件来货样,交IQC主管签发来货检验临时样品,并附相应的品质检测说明,不得在不明来货检验与验证项目、方法和品质允收标准的情况下进行验收。
进料检验作业指导书

1.0目的:为检验员提供检验规则和检验方法,指导其正确检验从而稳定产品质量,保证产品满足符合性要求及生产计划用料及时入库。
2.0 范围:所有非本公司生产加工的外协、外购件,经过加工或不经过加工而直接用于本公司产品上的零部件的检验。
3.0 检验工具:卡尺(300㎜/150㎜)/卷尺(300㎜)/千分尺(0-25㎜)扭力批/样板/自制检具、推力计、色差仪、百个格刀、盐雾实验箱、ROHS测试仪等4.0 引用标准:国家标准/客户标准/公司检验标准/作业指导书等5.0 术语和定义:5.1拉丝:是一种砂带磨削加工,通过砂带对金属表面进行磨削加工,去除金属表面缺陷,并形成具有一定粗糙度、纹路均匀的装饰表面。
5.2镀前划痕:指电镀或氧化之前因操作不当、或对明显缺陷进行粗打磨等人为造成的基体材料上的一般呈细线型划伤或局部磨擦的痕迹。
5.3浅划痕:膜层表面划伤,但未伤至底层(即底层未暴露);对其它无膜层表面则为:目测不明显、手指甲触摸无凹凸感、未伤及材料本体伤痕。
5.4深划痕:表面膜层划伤且已伤至底层(即底层已暴露出来);对无膜层表面则为:目测明显手指甲触摸有凹凸感、伤及材料本体的伤痕。
5.5基材花斑:电镀或氧化前因基体材料腐蚀、或者材料中的杂质、或者材料微孔等原因所造成的、与周围材质表面不同光泽或粗糙度的斑块状花纹外观。
5.6凹坑:由于基体材料缺陷、或在加工过程中操作不当等原因而在材料表面留下的小坑状痕迹。
5.7水印:电镀或氧化后因清洗水未及时干燥或干燥不彻底所形成的斑纹、印迹。
5.8水纹:塑胶或压铸件成形时,熔体流动产生的可见条纹。
5.9缩水:因材料、工艺等原因使塑胶或压铸件表面出现凹陷的收缩现象。
抄送:□总经理□市场部□工艺技术部□计划部□采购部□生产部□品质部□人力资源部□财务部□文控中心5.10气泡:批塑胶件因工艺原因内部出现的可见空气泡。
5.11砂眼:塑胶或压铸件表面的疏松针孔。
5.12披锋:压铸件或塑胶件的分模面上出现或残留的毛刺。
关键零部件和材料确认检验作业指导书

受控副本
作业指导书
文件名称:关键零部件和材料确认检验作业指导书 文件编号:
受控正本 编制:审核:批准:
4、
并对检验报告进行检查;
5.3.2如供应商无法提供有效的产品型式试验报告,由技术工程部会同质量管理科将采购的关键零部件和
材料送有资质的检测机构进行检验,并对检验报告进行检查。
其它确认检验方式
5.4.1针对型式试验报告中有列出,但本身是没有3C或CQC认证零部件和材料(如塑胶材料、发热管
等),则需供应商提供在规定的时间内提供有效的检测报告,或者定期抽样送样到CNAS认可测试能力的检测机构进行检验(如新宝产品验证中心或其它第三方机构)。
5.4.2检验的项目、要求、频次等具体参考附件《相关零部件确认检验要求》。
5.4.3确认检验过程中若出现不合格,则及时通知相关部门处理,具体按《不合格品管理程序》处理。
&相关文件
《不合格品管理程序》
7.相关记录
《关键零部件和材料确认检验记录表》
8.附件:
《相关零部件确认检验要求》
相关零部件确认检验要求。
零部件检测作业指导书
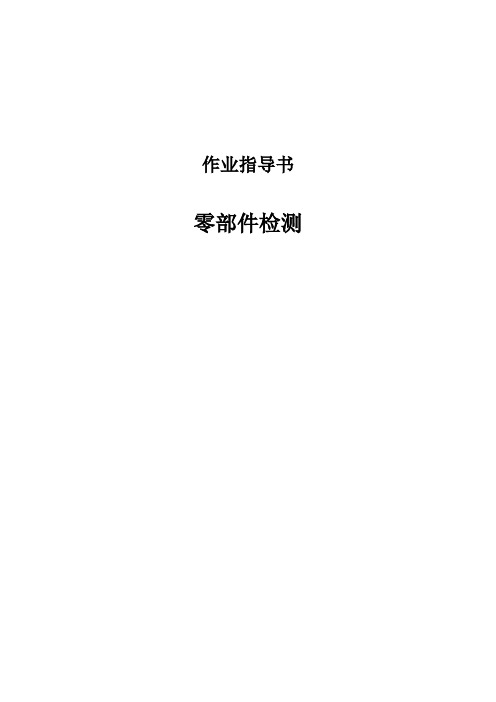
4.1.2.1 用扫描枪扫描主阀条形码,检查核对读取的编号与实物一致,确保
条形码信息正确录入 HMIS 检修系统中。
4.1.2.2 主阀配件检修限度需符合表 1 规定。
表 1 零件检修限度表
序号
名称
检测项目
原型 (mm)
限度 (mm)
检测器具
滑阀厚度不小于
17±0.15
16
1
滑阀
游标卡尺
缓解槽深度不小于
图5
4.3.2.2 用通针疏通触杆Φ1.5mm 孔及Φ4mm 孔,疏通时,采用小于各孔径的 通针疏通,通针硬度小于零部件硬度,如图 6。
图6
4.3.3 KZW 系列调整阀配件检查 4.3.3.1 各零部件状态良好,不得有损伤,裂纹。 4.3.3.2 各零部件连接部位或铆接部位状态良好,不松动。 4.3.4 KZW 系列调整阀配件测量 4.3.4.1 测量显示活塞Φ8 mm 柱面,柱面直径小于Φ17.6mm 时更换,划伤时 可用细砂纸或油石打磨修理,各柱塞及铜套表面须光滑,如图 7。
0.5mm 刀口尺
1mm
游标卡尺或 样板
4.3.7 T-1 系列调整阀配件检查
4.3.7.1 各零部件状态良好,不得有损伤,裂纹。各零件表面不得有目视可 见的污垢、沙尘、水分、纤维物和其它污物。 4.3.7.2 各零部件连接部位或铆接部位状态良好,不松动。
各零部件检测不合格者严禁使用。 4.4 检查阀体双头螺柱 对主阀、半自动缓解阀、紧急阀要双头螺栓逐一检查,双头螺柱松动时,须 分解检查,重新组装时,装入阀体端螺纹须均匀涂抹螺纹锁固剂,并严格执 行先紧固双头螺柱再组装压紧阀盖螺母的组装顺序,不得在双头螺柱上先装 上阀盖螺母再向阀体上组装双头螺柱。 4.5 检修记录填写 4.5.1 将 120/120-1 阀检测结果录入 HMIS 系统,在《型货车空气控制阀主阀 检修记录》(ZG-03),《120/120-1 型货车空气控制阀紧急阀检修记录》(ZG05)的 “零部件检查”填写相应的检测数据(检测数据精确到小数点后 2 位),并在“检测”栏录入工作者名,检查录入无误。 4.5.2 将 KZW 系列传感配件的检测结果填入《KZW 系列传感阀检修记录》(ZG16)“检测结果”栏,并在“检测”栏加盖工作者名章。 4.5.3 将 KZW 系列调整阀配件检测结果填入《KZW 系列调整阀检修记录》(ZG18)“检测结果”栏,并在“检测”栏加盖工作者名章。 4.5.4 将 WG-1A/C 型传感阀配件检测结果填入《WG-1A/C 型传感阀检修记录》 (ZG-20)“检测结果”栏,并在“检测”栏加盖工作者名章。 5. 设备故障处置 工作者在设备点检和操作过程中,要注意观察设备状态,发现异常,立即停 机检查处理,属于自修范围的故障由工作者处理。超出自检自修范围的故
【精品文档】零件作业指导书-word范文模板 (6页)

本文部分内容来自网络整理,本司不为其真实性负责,如有异议或侵权请及时联系,本司将立即删除!== 本文为word格式,下载后可方便编辑和修改! ==零件作业指导书篇一:零件作业指导书存档文件,操作人员必须妥善保存,以便回收。
1 / 9存档文件,操作人员必须妥善保存,以便回收。
2 / 9存档文件,操作人员必须妥善保存,以便回收。
3 / 9存档文件,操作人员必须妥善保存,以便回收。
4 / 9存档文件,操作人员必须妥善保存,以便回收。
5 / 9篇二:某公司零件加工作业指导书样本篇三:轴类零件作业指导书轴类零件作业指导书一、认真审阅图纸及相关技术文件,了解清楚技术要求。
认真查验有无设计更改通知单。
做到:明确要求、精细加工。
二、严格执行工艺纪律,按工序工步进行加工。
三、认真核对检测量具,做到准确无误定期检定。
四、对使用设备,定期调整保证加工零部件的精度要求。
五、细致的了解图纸的尺寸公差、形位公差及表面粗糙度的要求,并按要求达到标准。
六、认真执行“三按”要求,做到无磕碰、无油污、无腐蚀等。
工位器具合理到位。
以保证加工部件符合图纸要求。
篇四:模具零部件检作业指导书模具零部件检验作业指导书SC/DC-8.2.4-JY02一、总则1.1 检验人员应具有机械加工方面的专业知识和五年以上实际工作经验,且能满足单件加工对检验工作的各项要求。
检验员须经总经理任命授权。
1.2 检验人员所使用的计量器具必须是经计量部门校验合格并在检定周期内。
1.3 检验人员验收前应该熟悉相关模具图样和技术文件及加工方法,了解模具的关键尺寸及装配关系控制要点。
1.4 检验人员必须严格按照模具图样和技术文件所规定的要求对模具进行检测和判定。
1.5 检验人员负责对检验区域及所检的产品进行状态标识。
1.6 检验人员必须定期(三个月、最长六个月)参加专业知识培训,学习和接受先进的检测方法,以提高自身的业务水平。
二、检验制度2.1 自检制度2.1.1定义:操作者对自己加工的工件进行的独立的、自主的检查。
汽车零部件生产作业指导书【毕业论文-绝对精品】.doc

题目:汽车零部件生产作业指导书学院:专业: 工业工程学号:学生姓名:指导教师:日期:摘要随着市场经济的发展以及汽车生产的全球化趋势,汽车零部件企业面临着准时交货、提高产品质量、降低产品成本以及应对快速变化的需求市场做出及时响应的多重压力,这一严竣的形势使得人们认识到生产作业标准化对企业获取竞争优势的重大作用。
本文针对汽车零部件企业的现状,分析企业生产作业的实际情况。
以企业标准化生产作业为目标,提出应用作业指导书指导企业生产作业的重要思想和方法。
通过研究作业指导书的设计,包括编制的原则、编制的方法和基本表格的格式设计,同时针对作业指导书在汽车零部件企业对工时和质量的控制研究,得出作业指导书可以大大降低次品率,甚至实现无次品。
企业通过作业指导书的应用可进一步实现企业的标准化,而一个能够做到标准化的企业在将来的国际化市场竞争环境下才能够立于不败之地。
关键词:汽车零部件;工时;质量;作业指导书ABSTRACTWith the globalization of information network and globalization, the formation of market economy, automobile parts enterprises are facing the on time delivery, improve product quality, reduce product cost and deal with the fast changing market demand to make a timely response to the multiple pressures, the grim situation makes people realize the production of standardization for the enterprise to obtain the competitive advantage of the important role. This paper introduces the analysis of auto parts enterprises the status quo, analysis of enterprise production operation situation.With the standardization of production enterprises operation as the goal, put forward the operating instructions of the application.Through the study of the operating instructions of the design, including the preparation principle, preparation methods and basic form of format design, according to the instructions in the auto parts enterprises to work and quality control research.Get SOP can greatly reduce failure rate, even without defects, at the same time instructions is that raw material is received important basis.The enterprise through the operating instructions of the application can further realize the standardization of enterprise, and one can achieve the standardization of enterprise in the future competition in global market environment can remain invincible.Through the application of the operating instructions can be further standardization of the enterprise, and one can do the standardization of the competitive environment of the future international market in an invincible position.Key words: Auto parts;Working hours;Quality;Working instructions目录1.1 背景及意义 (1)1.2 国内外研究现状 (1)1.3 研究内容 (3)2. 生产计划与作业指导书 (4)2.1汽车零部件生产计划 (4)2.2作业指导书 (4)3. 汽车零部件作业指导书设计 (5)3.1作业指导书编制设计方法 (5)3.1.2编制原则 (5)3.1.2编制方法 (5)3.2 作业指导书基本表格设计 (6)4. 基于作业指导书的作业管理和控制 (9)4.1 SOP的修改 (9)4.2 SOP的持续改进 (9)4.3对工时的控制 (10)4.3.1工时定额制定 (10)4.3.2 SOP进行标准化 (13)4.4对汽车部件质量的控制 (13)4.4.1检验文件标准化 (13)4.4.1 SOP缺陷评定 (15)5. 结论与展望 (16)参考文献 (17)1 概述1.1 背景及意义20世纪末,随着我国汽车产业的蓬勃发展,汽车配件的需求量也急剧增长,于是,国内大量的汽车零部件企业如雨后春笋般涌现出来。
检验作业指导书

检验作业指导书1.目的规范检验工作,提高产品质量,确保产品满足组织的品质要求。
2.范围适用于我司自制或委外协作加工的所有加工件。
3.职责品质部是本公司的质量管理部门,负责产品检验工作并记录验收结果。
4.内容检验流程-检验方法-判定标准-检验报告-不良品处理-纠正预防措施4.1检验流程供应商按照采购订单送货到公司将送货单给仓库,仓库按照采购订单及收货单上的名称、编号、数量对来料进行验收;如发现有缺件、编号与名称不符等情况验可退货给供应商,验收合格后,仓库开立《来料检验通知单》交品质部检验,品质部按照图纸、技术规范、及抽样水准对来料进行抽样检验。
接到仓库开立的来料检验通知单后,检验员需在半小时内进行检验工作,整理好该批次的相关图纸及检验工具,到现场进行验收工作,检验合格的部件粘贴“绿色”合格标签;检验不合格粘贴“红色”不良标签,并填写《品质异常处理单》召集相关部门进行原因分析和改善;将检验结果记录每日检验日报表中;并跟进不合格品的处理及改善效果,将检验合格的产品交由仓库入库。
相关表单文件及抽样水准《进料品质控制流程》《来料检验通知单》《机架过程品质控制流程》《品质异常处理单》《来料检验日报表》《问题点记录表》4.2 检验方法原材料核对:核对产品的名称、材质、型号规格、图号、材质证明、厂家的出厂检验记录。
成品外观检验:表面不允许有砂孔、毛刺、裂纹、塑性变形,不允许有明显的划痕、凹凸、折痕、污渍、色差等,必须符合工艺或技术文件标准,零部件的编号规则及位置与相关技术文件或图纸规定要一致。
尺寸、角度、形位误差的检验:根据标准要求选择合适的检验器具或配合其他辅助检测工具进行检验,并详细真实的记录检验结果。
按照图纸标注的长宽、孔径、距离、角度、槽、标注公差、螺纹长宽及纹牙、表面处理,逐一进行检验,重要部件做好检验数据记录,必要时可进行简单的装配查看配合是否异常,必须符合图纸技术要求。
机架件注意其图纸要求的材质及表面处理要求,严格按照图纸尺寸公差验收,加工成型后不得有沟痕、碰伤等损坏表面,降低强度及寿命的缺陷,去边角及毛刺。
样件认可作业指导书(汽车零件)

南京依维柯采购部样件认可流程操作指导书版/次:A/0 NA VECO 06 /G ****-2010 1 目的和范围为细化样件认可的流程,本标准规定了样件条件认可的具体要求和操作方法。
本文件适用于NAVECO公司样件认可的具体操作,并将条件认可的相关信息体现于样件检测/认可报告上。
2 引用标准及文件NAVECO G/0627-2009 样件认可流程3 定义条件认可:外购零部件样件认可的方式之一,指零件不符合技术要求(或符合性尚未经检验/试验判定),但其不符合的程度可以在一定条件下(如:一定时间、一定数量或一定商务条件等)接受,用于指定的用途(如:装用于产品车或试验车等)。
4 职责4.1 质保部对产品车使用零件的条件认可进行审批4.2 产品部对各种样车使用零件的条件认可进行审批4.2 物流部对条件认可的零件进行专项管理。
4.2 采购部对责任范围内的外购件不符合情况进行风险评估,提出条件认可申请。
5 管理内容5.1 条件认可的范围及条件认可申请的提出:5.1.1当外购件不符合技术要求时(或对零件是否符合技术要求的判定未完成时),在下列情况下,可开展条件认可工作:A、零件的可靠性试验(含NAVECO开展的)未完成;B、零件不符合技术要求,但责任单位已找到问题原因、能够评估其危害并制定了相应后续计划;C、零件尺寸不符合技术要求,但装车后能够实现产品的预期功能;或装车后(部分)功能不能实现,但与不符合项目无因果关系。
D、供应商已完成零件的自我认可,但NAVECO公司未完成相应项目试验检验。
E、除上述情况外,其他能够表明零件的不符合不会导致顾客满意下降的情况。
5.1.2下列情况不列入条件认可,应予以正式认可:A、产品部修改、补充技术要求(含试验方法等)以后,零件符合要求(或重新检验符合要求);B、材料代用经NAVECO批准且在有效期内;C、经评审认为不需要纠正的(或需要纠正但不需要进行监控的)不符合。
5.1.3 重要特性、安全特性经检验被判定不符合时,原则上不得办理装用于产品车的条件认可。
美的钣金喷涂件检验作业指导书--内部资料

包装质量
★包装质量 ★涂层颜色
喷涂件需用专用器具装运,专用器具须结实牢靠.喷 涂件的装箱摆放须合理,且需加隔离保护层,堆放 高度要适合,以避免运输过程中碰伤、压坏、变形.
外观面与标准样板色差值(△E 相对色差)不大于 0。 8,相邻部件色差值(△E)不大于 0。8,同一外观 部件的各部位色差值(△E)不大于 0.5 非外观面与标准样板色差值(△E)不大于 1.8; 柜机室内机蒸发器右侧挡板类喷涂件涂膜颜色不做 色差要求. 柜机室内机左右侧板(白色)与相邻塑料件(白色) 色差值(△E)不大于 6。0.
区域 A;交叉中心部位涂层剥离不超过直 下图所示,划线时必须用力均匀,以划到
径 20mm 的圆圈范围,检测部位如图所示 底材为准,划线过程不允许有间断,直线
区域 B。
长度不小于 100mm,夹角为 60º(如下图所
2、室内机冷轧板
示);零部件划叉部位必须是平面,且平面
按 GB/T1766 评级。工件边缘、划叉 区域不少于 70mm×120mm。涂层厚度 60—
标志欠缺或内容与图纸不符
/
C
标志内容模糊无法辨认
不合格 (缺陷)编码
C101
C102
抽样判定
/
C
包装不符合
C201
色差仪
C
颜色不符合要求
C301
/
C
外表面质量不符合
C302
QMN-J11.00 1-2007(Ⅰ)
★海绵件粘贴
冲压件上粘贴的海绵件、绒布等,应粘贴牢固平整, 不得有变形、撕裂、破损、松脱、翘起等现象。
求涂膜附着力不大于 0 级(百格无脱落)。
深处、孔位等部位划格时不允
许整格脱落。
QMN-JH55.005-2009 钣金喷涂件检验 作业指导书
- 1、下载文档前请自行甄别文档内容的完整性,平台不提供额外的编辑、内容补充、找答案等附加服务。
- 2、"仅部分预览"的文档,不可在线预览部分如存在完整性等问题,可反馈申请退款(可完整预览的文档不适用该条件!)。
- 3、如文档侵犯您的权益,请联系客服反馈,我们会尽快为您处理(人工客服工作时间:9:00-18:30)。
零部件审核指导书
1 零部件缺陷分类的依据
2 零部件缺陷严重性分级原则(表1)
a ) 对产品的功能特性的影响;
b )外观质量和包装质量对市场的影响;
c ) 对企业的信誉和形象的影响;
d )对效益和成本的影响等。
3 缺陷权数的确定 (表2)
4 质量指数的计算(QKZ )
QKZ =(1-所有特性缺陷分数之和÷所有特性已加权的抽样数之和)×100% 4.1 缺陷点数之和:为所有特性的缺陷数与缺陷等级系数乘积之和。
4.2 平均质量指数:为同期审核的同型号产品的质量指数的平均值。
5 不合格的处置
5.1现场审核发现次要缺陷,应由相关责任人进行纠正,如返工或返修。
5.2现场审核发现主要缺陷,由相关责任人对缺陷进行纠正,返工,在彻底整改前不允许放行或让步放行;
5.3现场审核发现关键缺陷,由相关责任人对缺陷进行纠正,返工,并分析原因,制定纠正措施并实施,产品在彻底整改前不允许放行或让步放行。
6 每一零部件质量缺陷严重性分级,详见《产品缺陷严重性分级表》 名称/规格: 序号 项目 质量特性
质量缺陷描述
缺陷级别 1
外观 A 、B 、C
缺陷级别 严重程度 缺 陷 后 果
A 级
关键缺陷 涉及产品安全性
B 级 主要缺陷 预计功能会出现故障,影响产品使用性
C 级 次要缺陷 对使用缺陷无影响
缺陷级别 严重程度 缺陷等级系数(加权系数)
A 级 关键缺陷 10
B 级 主要缺陷 5
C 级
次要缺陷
1
2 功能/性能
3 尺寸
2。