粉末冶金模具设计资料
粉末冶金模具设计
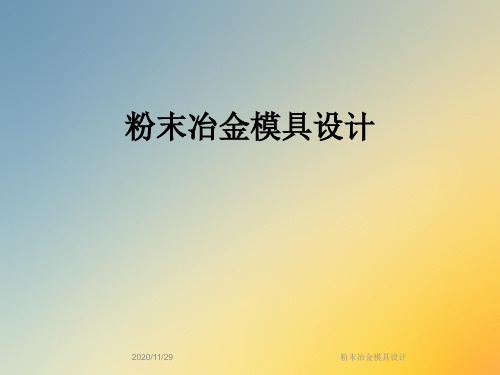
2020/11/29
粉末冶金模具设计
•带斜面的第五类压坯
当压坯斜面与垂直方向的夹角超过25°~30°,或 者具有多个斜面和平面时,一般按照斜面和平面的 分界线设计组合下模冲。斜面的装粉高度等于斜面 的压坯平均高度乘以粉末填装系数。
x=(d2-d1)h/d1
或者 y=x/l=100(d2-d1)/d1(k-1)
其中:d2为要求的压坯平均密度;d1为单向压 制的平均密度;h为压坯高度;k为压缩比;l 为装粉高度与压坯高度之差。
2020/11/29
粉末冶金模具设计
非同时双向压制原理为压模结构设计提供了 压坯密度均匀分布的理论基础;也为粉末压 机的设计提供了重要基础,使得多凸轮和凸 轮曲柄粉末压机更好地满足粉末压坯密度均 匀分布的要求。
2020/11/29
粉末冶金模具设计
摩擦压制
在压制过程中,让阴模或芯杆与样品侧面产 生同向相对移动,即运动得更快,借助粉末 与模壁之间的摩擦,带动与阴模或芯杆接触 的粉末层移动,从而可改善沿压坯高度方向 的密度分布均匀性。
2020/11/29
粉末冶金模具设计
2020/11/29
粉末冶金模具设计
2020/11/29
距离,用先压缩高区粉末再同时压缩高低区粉末的
方法,使压坯各横截面上的粉末受到相同的压缩程
度。
2020/11/29
粉末冶金模具设计
2020/11/29
粉末冶金模具设计
如果压坯中间带内、外台阶,除不同横截面需要 设计组合下模冲外,还有根据粉末移动成形法的 要求设计组合上模冲。
粉末冶金模具的设计与制造

粉末冶金模具的设计与制造1. 引言粉末冶金是一种重要的金属制造工艺,广泛应用于汽车、航空航天、电子、能源等领域。
在粉末冶金工艺中,模具的设计与制造是关键环节,直接影响产品的质量和性能。
本文将介绍粉末冶金模具的设计与制造过程,包括模具材料的选择、模具的结构设计、加工工艺等内容,以帮助读者全面了解粉末冶金模具的制造方法和技术要点。
2. 模具材料的选择模具材料的选择是粉末冶金模具设计的第一步。
模具材料需要具备一定的硬度、耐磨性和耐各种腐蚀介质的能力。
常用的模具材料有以下几种:•工具钢:具有较高的硬度和韧性,适用于大部分粉末冶金模具的制造。
•高速钢:具有更高的硬度和耐磨性,适用于对模具耐磨性要求较高的情况。
•硬质合金:具有较高的硬度和耐磨性,适用于对模具耐磨性要求极高的情况。
在选择模具材料时,需要根据具体应用场景和成本考虑,综合各种性能指标做出合理选择。
3. 模具的结构设计模具的结构设计是粉末冶金模具制造中的核心环节。
良好的模具结构设计可以提高产品的制造效率和质量,降低生产成本。
以下是模具结构设计的几个要点:•模具的整体结构应该合理,易于安装和拆卸。
模具的结构应简洁、牢固,能够承受制造过程中的力和压力。
•模具的导向和定位系统要设计到位,以确保模具在制造过程中的稳定性和精度。
•模具的开合系统要灵活可靠,能够实现快速开合和调节。
对于大型模具,可以考虑采用液压或气动开合系统。
•模具的冷却系统要充分考虑,以保证模具在制造过程中能够及时散热,提高产品质量和生产效率。
4. 模具的制造过程粉末冶金模具的制造过程主要包括以下几个步骤:4.1 模具设计在模具设计阶段,根据产品的形状和尺寸要求,通过CAD软件进行三维建模。
在设计过程中,要充分考虑模具的可行性和制造工艺,以确保模具的质量和可生产性。
4.2 模具加工模具加工是模具制造的关键环节。
常用的模具加工方法包括数控加工、线切割、铣削等。
在加工过程中,需要根据模具材料和结构要求选择合适的加工工艺,精确控制加工尺寸和表面质量。
粉末冶金材料模具设计
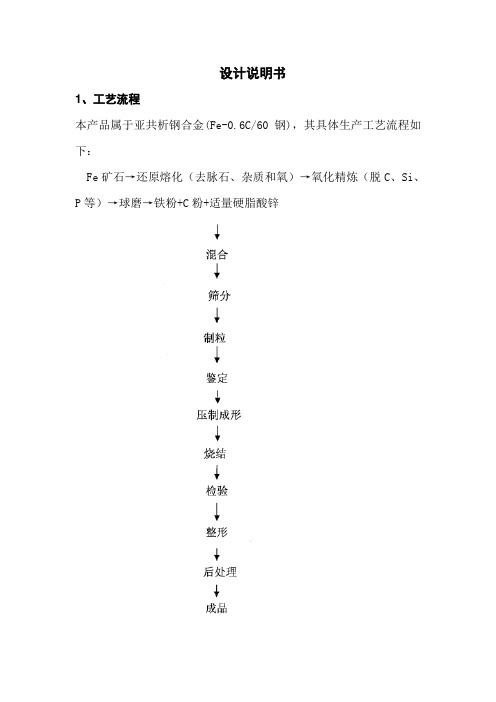
设计说明书1、工艺流程本产品属于亚共析钢合金(Fe-0.6C/60钢),其具体生产工艺流程如下:Fe矿石→还原熔化(去脉石、杂质和氧)→氧化精炼(脱C、Si、P等)→球磨→铁粉+C粉+适量硬脂酸锌2、压坯设计2.1产品零件分析该产品采用Fe-0.6C(60钢),属于铁基制品,其制品密度依靠较高的压坯密度来达到,因此,在压制成形时需要采用较高的单位压力(一般在400-500MPa)。
由于该产品零件形状比较简单,带一个外台阶,采用简单的单上双下模冲即可成形,并使其密度分布均匀。
有配合、定位、相对运动要求的零部件,产品尺寸精度和形位精度及表面粗糙度要求较高,因此,该产品的的尺寸精度定义为IT8、形位精度如图所示为7级,表面粗糙度精度要求为7级。
2.2压坯精度设计由模具设计任务书的零件成品图可得知该产品压坯同轴度需控制在0.08mm,相当于IT10级;压坯垂直度控制为0.1mm,相当于IT11级;压坯侧面平行度为0.15mm,相当于IT12级。
2.3压坯密度和单重的确定由于已知压坯密度ρ=6.6g/cm3,因此压坯单重W=ρ×V ,由成品图给数据计算其压坯体V=h×S,算的V=166.8cm3 ,所以求的压坯单重W=6.6×166.8=1100.8g。
3、压机与压制方式选择3.1压机压力选择铁基制品一般采用固相烧结,其制品密度除了依靠烧结温度、保温时间之外,在一定程度上还依靠较高的压坯密度来达到,因此该产品采用500MPa的单位压力。
根据任务书要求,截面积S=74.0cm2 ,所以F=P×S=5×74=370t脱模压力,根据实际生产经验,铁基压坯的脱模压力P脱模≈0.13P=0.13×500MPa=65MPa3.2压制类型的选择年生产量为50万件,假设每年的工作时间为300天,每天工作时间为8小时,则p=500000/300/8/60=3.47=4件/min,所以选择自动压制。
粉末冶金设计范文第1篇 (2)
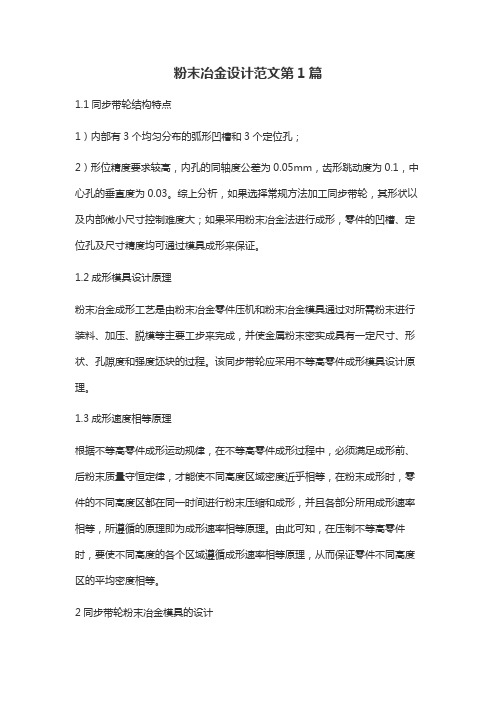
粉末冶金设计范文第1篇1.1同步带轮结构特点1)内部有3个均匀分布的弧形凹槽和3个定位孔;2)形位精度要求较高,内孔的同轴度公差为0.05mm,齿形跳动度为0.1,中心孔的垂直度为0.03。
综上分析,如果选择常规方法加工同步带轮,其形状以及内部微小尺寸控制难度大;如果采用粉末冶金法进行成形,零件的凹槽、定位孔及尺寸精度均可通过模具成形来保证。
1.2成形模具设计原理粉末冶金成形工艺是由粉末冶金零件压机和粉末冶金模具通过对所需粉末进行装料、加压、脱模等主要工步来完成,并使金属粉末密实成具有一定尺寸、形状、孔隙度和强度坯块的过程。
该同步带轮应采用不等高零件成形模具设计原理。
1.3成形速度相等原理根据不等高零件成形运动规律,在不等高零件成形过程中,必须满足成形前、后粉末质量守恒定律,才能使不同高度区域密度近乎相等,在粉末成形时,零件的不同高度区都在同一时间进行粉末压缩和成形,并且各部分所用成形速率相等,所遵循的原理即为成形速率相等原理。
由此可知,在压制不等高零件时,要使不同高度的各个区域遵循成形速率相等原理,从而保证零件不同高度区的平均密度相等。
2同步带轮粉末冶金模具的设计1)齿形成形通过控制材料的流动方向,成形出理想的形状尺寸,是同步带轮成形模具中最关键的环节。
由于成形过程中单位压力增大,载荷集中,因此要求模具工作部位刚性好。
另外还应设置过载保护,防止毛坯的超差、材料不均匀等导致的过载。
2)同步带轮属于轴类零件,在成形过程中轴向密度差较大,因此模具应采用芯棒成形结构,以保证同步带轮轴向密度分布均匀。
3)该同步带轮有3个定位孔,应采用芯棒成形结构成形定位孔,可以延长模具使用寿命,提高装配精度。
该同步带轮采用德国DORST压机进行压制,铁粉的松装密度约为3.2g/cm3,零件的毛坯密度不得小于6.6g/cm3,为了节约成本,模具配件采用已有的五档同步器齿毂模具配件,例如,垫板、压盖等。
由此可知,该同步带轮成形模具的设计主要包括中模、上模冲(2个)、下模冲(3个)、芯棒(2个)的设计。
粉末冶金:钢压模具设计

好的材料 ➢ 高密度、高精度件用耐磨性好的材料 ➢ 整形模用耐磨性好的材料
绘制模具装配图和零件图
➢ 绘制模具装配图和零件图 ➢ 标注尺寸偏差和形位公差 ➢ 标注其他加工要求
绘制模具装配图和零件图
模具示例
模具示例
设计模具结构
根据制品图纸设计坯件,选择压机和压制方式,设计 模具结构草图 ➢ 从生产工艺、压制成形和经济成本方面分析制品图纸 及技术要求,看是否适于用粉末冶金方法生产 ➢ 根据制品图纸及技术要求和粉末冶金生产工艺的特点, 设计坯件的几何形状、精度和密度 ➢ 为了使制品适于压制成形,或为了简化模具结构,常 对制品形状进行修改,设计出适合于压制的压坯 ➢ 在设计坯件形状的同时要确定压制方向,然后根据压 坯的形状、高径比、生产批量和压机来选择压制方式、 压模结构类型
粉末成形模具分类
➢ 压模、精整模、复压模、锻模、挤压模、 热压模、等静压模、粉浆浇注模、松装 烧结模
➢ 钢模、硬质合金模、石墨模、塑料橡皮 模和石膏模
钢压模具结构
钢压模具一般由 阴模、模冲、芯棒 组成
钢压模具结构
1—模柄 2,9—法兰圈 3—上模冲 4—模套 5—阴模 6—模座 7—弹簧 8—下模冲 10—下模冲座 11—压垫 12—下模板 13—顶杆 14—顶板
➢ 制品生产工艺流程及工艺参数:粉末混合料成分、杜 装密度、流动性、压制性、单位压制压力、压坯密度、 压缩比、弹性后效、烧结收缩率、精整余量、机加工 余量、复压装模间隙和压下率等
➢ 压机类型及主要技术参数:公称压力、脱模压力、压 机行程、每分钟压制次数、工作台面积、压机自动化 程度和安全保险装置等
粉末冶金模具设计说明书样板
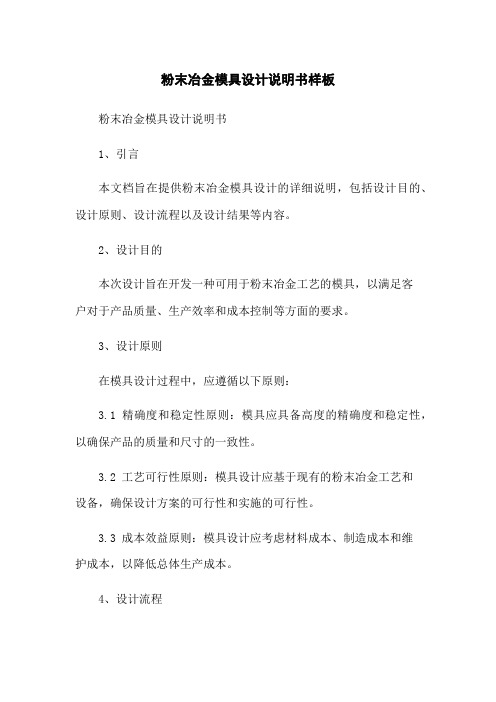
粉末冶金模具设计说明书样板粉末冶金模具设计说明书1、引言本文档旨在提供粉末冶金模具设计的详细说明,包括设计目的、设计原则、设计流程以及设计结果等内容。
2、设计目的本次设计旨在开发一种可用于粉末冶金工艺的模具,以满足客户对于产品质量、生产效率和成本控制等方面的要求。
3、设计原则在模具设计过程中,应遵循以下原则:3.1 精确度和稳定性原则:模具应具备高度的精确度和稳定性,以确保产品的质量和尺寸的一致性。
3.2 工艺可行性原则:模具设计应基于现有的粉末冶金工艺和设备,确保设计方案的可行性和实施的可行性。
3.3 成本效益原则:模具设计应考虑材料成本、制造成本和维护成本,以降低总体生产成本。
4、设计流程4.1 产品需求分析:了解客户对于产品性能、尺寸和表面质量等方面的要求,获得设计的基础数据。
4.2 材料选择:根据产品需求和工艺要求,选择适合的材料,包括模具材料和涂层材料等。
4.3 模具结构设计:设计模具的整体结构和零部件结构,考虑模具的可装卸性、易维护性和生产效率等。
4.4 模具零部件设计:设计模具的各个零部件,包括模具芯和模具腔等,确保其几何形状和尺寸的准确性。
4.5 涂层选择和设计:根据模具的使用环境和工艺要求,选择合适的涂层材料,并设计涂层的厚度和结构等。
4.6 模具制造和调试:根据设计图纸和规范,制造和组装模具,并进行调试和试产,以确保模具的正常使用。
4.7 模具维护和管理:建立模具维护和管理体系,包括清洗、保养和修复等工作,延长模具的使用寿命。
5、设计结果基于以上设计流程和原则,我们提供了粉末冶金模具的设计方案。
设计方案包括模具结构图纸、材料选择和涂层设计等内容,请参阅附件1:附件:1、粉末冶金模具设计图纸本文涉及的法律名词及注释:1、粉末冶金:一种通过将金属粉末压制成形并经过烧结过程得到制品的金属加工工艺。
2、模具:用于塑料、金属等物质加工中的一种工具,用于赋予材料所需的形状和尺寸。
第六章+粉末冶金模设计
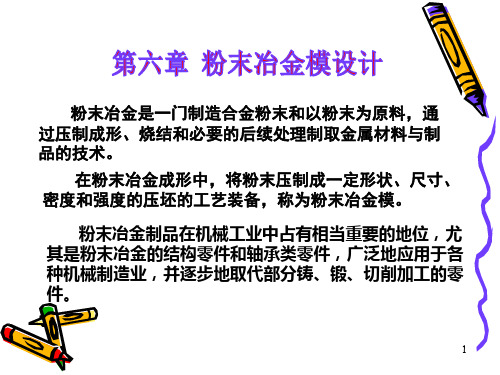
粉末冶金制品在机械工业中占有相当重要的地位,尤 其是粉末冶金的结构零件和轴承类零件,广泛地应用于各 种机械制造业,并逐步地取代部分铸、锻、切削加工的零 件。
3
<压铸模、锻模及其他模具>
一.粉末冶金制坯成形方法和特点 1.制粉和粉末的混合:
(1)粉末的制造方法通常分两 大类:物理化学法和机械粉碎法。 工业上应用最广泛的是还原法、 电解法和雾化法。 (2)粉末的混合:是指将金属 粉末及添加剂等混合及其他预处 理,如掺加成形剂、增塑剂制粒、 烘干、过筛等。
24
<压铸模、锻模及其他模具>
2.压机分类:
按传统机构可分为:液压式压机和机械式压机两类。 按模具操作方式可分为:下模冲固定式压机、凹模固定式压机和上 模冲固定式压机三大类。 按模冲动作方式可分为:上模冲单向压制压机、下模冲单向压制压 机、双向压制压机、多模冲压制压机和模冲回转压制压机等五大类。
在选用时,要考虑的因素主要有压制压力、脱模压力、 工作台面尺寸和行程等因素。 二.压机参数的确定
使用范围
h / >4-6; h / D 2 3;
5
强动压制
拉下式
零腔装粉法
11
<压铸模、锻模及其他模具>
3.烧结
烧结是将粉末冶金压坯在低于其基体材料熔点的温度下进行加热, 粉末颗粒直接产生原子还原、扩散、固溶、化合与熔接、溶解和再结 晶等物理化学过程,致使压坯收缩并强化。
12
<压铸模、锻模及其他模具>
粉末冶金模具设计
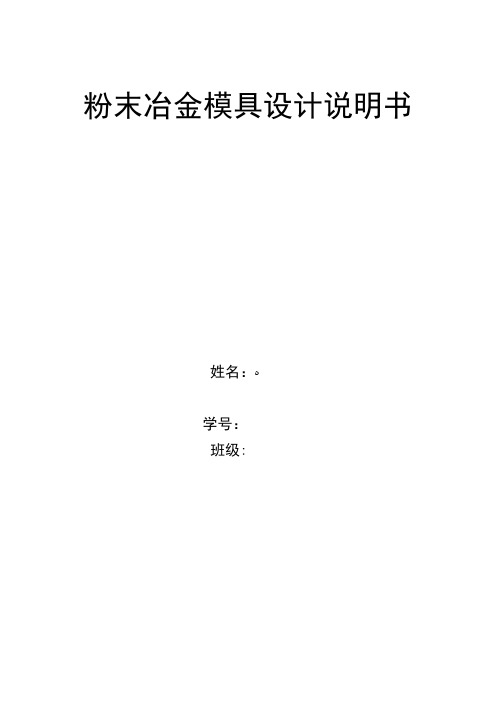
粉末冶金模具设计说明书姓名:ﻩ学号:班级:粉末冶金模具设计说明书设计任务生产一批圆柱状钢制模坯,直径20mm,高度40mm压坯设计1。
产品分析该产品采用Fe—0。
6C(60钢),属于铁基制品,在压制成型时需要采用较高的单位压力(一般在400~500MPa).该产品零件形状比较简单,采用上下模冲压制成型.2.松装密度和压坯密度的确定采用水雾化铁粉压制,松装密度为:ρ松=2.8g/cm3压坯密度为:ρ压=6。
6g/cm3材料选择1.阴模要求:①阴模高度应能容纳压制所需的松散粉末,并使上、下模冲有良好定位和导向;ﻩ②能保证压坯外形的几何形状和尺寸精度;③工作面的粗糙度Ra≤0。
8um;ﻩ④工作表面要有高的硬度和良好的耐磨性;;⑤在工作压力下应具有足够的强度和刚性;ﻩ⑥根据产品的批量和复杂程度,选择合适的阴模材料⑦结构上应便于制造和维修,使用安全,操作方便⑧能使压坯完好的脱出ﻩ⑨平磨后需退磁选材:硬质合金2.上下模冲要求:①工作表面要有足够高的硬度和良好的耐磨性,材料的选择与处理应考虑有适当的韧性;②上、下模冲对阴模和芯棒应有良好的配合、定位和导向,并有合理的配合间隙,复合的模冲(即有压套时)应能脱出压坯③上下模冲的工作面和配合面的粗糙度Ra≤0。
8um,非工作段的外径可适当缩小,内径可适当放大,减少精加工量和阴模、芯棒之间的摩擦ﻩ④有关部位应能保证垂直度、平行度和同轴度等技术要求⑤平磨后需退磁选材:合金工具钢3.模架及升降装置要求:耐磨性好,能承受高负荷,韧性好,强度硬度高。
选材:合金工具钢4.压坯选材:铁粉力学分析1.压制压力F取铁基粉单位压制压力为500MpaS=3.14cm2总压制压力F=P*S=500Mpa*3。
14cm2=157KN2.侧压力和剩余侧压力泊松比v=0.28P侧=P*v/(1-v)=500*0。
28/(1—0。
28)=195MPaP侧余=(0。
2~0.3)P=100~150Mpa3.压制类型选择因为采用大批量生产,故使用自动压制。
粉末冶金模具设计
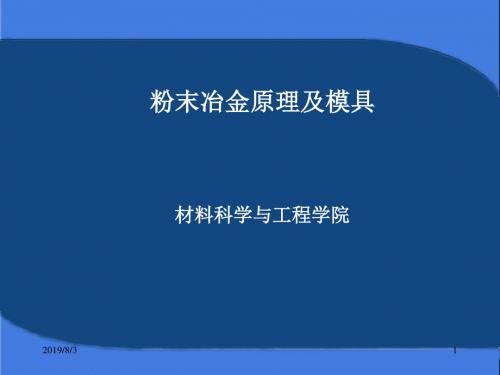
3
在低速高单位压制压力条件下,塑性金属粉 末易发生“模瘤”;模具表面质量差、润滑 不良和模温过高,加重模瘤现象。
严重时脱模压力超过压制压力,使得模具拉 伤。
无润滑塑性金属粉末应当避免高压压制
F脱=μ静P侧剩S侧 P侧剩=E∑R剩(m2-1)/2R
P侧剩=jξ0ρP
2019/8/3
4
其中:
∑R剩:卸压后阴模半径上剩余的变形量; j: 剩余侧压强与侧压强之比,决定于模具的刚度;
19
摩擦芯杆压制
上模冲强迫芯杆一起向下移动,且芯杆下 移的速度大于粉末下移的速度,因而靠芯 杆与粉末之间的摩擦力带动粉末向下移动。
[(S侧阴-S侧芯)/S]max=[1-(ρ下/ρ上)m]/μξ=K 对于圆筒形压坯的高与壁厚之比:
h/T=K(1+D内/T)/2 摩擦芯杆压制特别适合于大孔薄壁压坯
2019ห้องสมุดไป่ตู้8/3
2019/8/3
13
2019/8/3
14
2019/8/3
15
•压制方式的选择依据
压制方式和方法不同,上、下模冲、芯杆和阴 模相对于粉末压坯的相对运动方向及速度也不 同,从而使外摩擦对压坯密度的均匀分布产生 有害或者有利的影响。
单向压制
S侧max/S=[1-(ρ下/ρ上)m]/μξ=K
当柱状压坯S侧/S<K或者圆柱体压坯高径比 H/D<K/4时,采用单向压制可以满足压坯密度 分布均匀性的要求
整形区的单位精整压力为
Pc=σ/[1+(S+μQ)/2S2]
在此: σ为单向压缩条件下材料塑性变形的抗 力
通常内胀外精整方式的精整压力几乎只有外箍 内精整方式的十分之一
材料塑性变形抗力与材质、组织和孔隙率密切
粉末冶金及模具设计
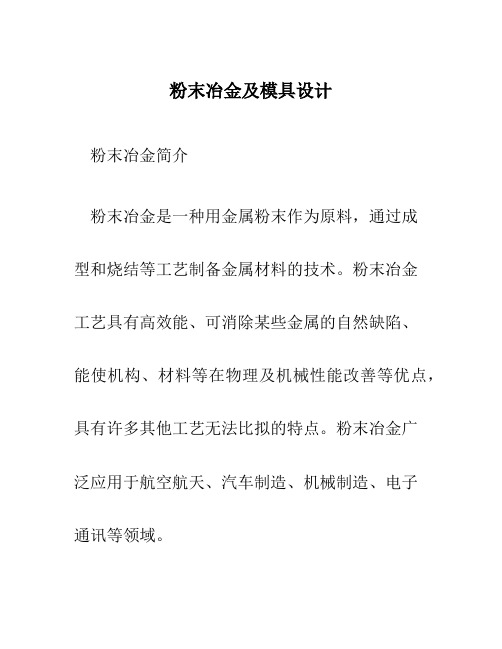
粉末冶金及模具设计粉末冶金简介粉末冶金是一种用金属粉末作为原料,通过成型和烧结等工艺制备金属材料的技术。
粉末冶金工艺具有高效能、可消除某些金属的自然缺陷、能使机构、材料等在物理及机械性能改善等优点,具有许多其他工艺无法比拟的特点。
粉末冶金广泛应用于航空航天、汽车制造、机械制造、电子通讯等领域。
粉末冶金工艺步骤粉末冶金工艺可大致分为粉末的制备、成型、烧结和后处理等步骤。
粉末制备粉末冶金的首要步骤是粉末的制备。
粉末可采用物理方法(如雾化法、机械球磨法等)或化学方法(如溶胶凝胶法、羟基磷灰石法等)进行制备。
制备出的粉末应具有一定的粒度和化学成分,以满足后续成型、烧结工艺的要求。
成型成型是将粉末冶金原料粉末按照设计要求形成所需形状的工艺。
成型方法包括压制法、注塑法、挤压法等。
其中,压制法是最常用的成型方法之一,通过将粉末与模具施加压力,使粉末颗粒间相互结合,形成所需形状。
烧结在成型之后,粉末会经过烧结工艺。
烧结是将成型的粉末在高温条件下进行加热,使粉末颗粒之间相互结合,形成致密的材料。
通过烧结,可以消除粉末冶金材料中的毛孔及气孔等缺陷,提高材料的密度和力学性能。
后处理粉末冶金材料在烧结后可能还需要进行后处理,包括表面处理(如涂层、抛光等)和热处理(如退火、淬火等)。
后处理的目的是进一步改善材料的性能,满足特定的应用要求。
模具设计模具在粉末冶金工艺中起到至关重要的作用。
模具设计的好坏直接影响到成品的质量和生产效率。
模具类型根据成型方式的不同,模具可分为压制模具、注塑模具、挤压模具等。
不同的模具用于不同的成型工艺,具有不同的结构和特点。
模具设计要点模具设计需要考虑的要点主要包括模具结构设计、材料选择、表面处理、冷却系统和顶针结构等。
模具结构设计应保证成型质量和生产效率。
不同形状的工件可能需要不同类型的模具结构,需要考虑工件的形状、大小、复杂度等因素。
材料选择是模具设计中的关键因素之一。
模具材料需要具有足够的硬度、耐磨性和耐腐蚀性,以满足长时间的生产需求。
粉末冶金模具设计

粉末冶金模具设计粉末冶金含油轴承的模具设计1.零件图以下是传送带用电动机转自轴的含油轴承图,批量生产,采用粉末冶金工艺。
见零件图—精整件。
2.产品分析使用工况:用于物料输送带的驱动电动机,有轻度冲击载荷,电机转速15000到20000转/分,要求强度大于200MPa,含油率大于15%,且含油量能满足较长使用寿命。
机构简介:电动机转子轴通过联轴器与减速器相连,含油轴承套在转子轴上,架于电机壳体上,起承受径向载荷和润滑作用。
材料选择:电机功率1500w以上,功率较大,载荷不平稳,根据“烧结金属含油轴承的ISO5755:2001”标准,选用压坯烧结强度较大的Fe-C-Cu系列金属粉末,牌号为-F-00C2-K250/ISO5755:2001。
干态密度:6.2g/cm3 。
成分:Fe,余量;C<0.3%;Cu,(1~4)%。
3.制造工艺及模具设计参数选择含油轴承需要进行内外精整才能达到允许公差要求。
拟定为烧结后精整再浸油,工艺参数如下:产品工艺:压制-烧结-外箍内胀精整-浸油。
工艺参数:产品外径:D=3006.0﹢02.0﹢,内径d=22﹢0.03﹢0.01外径变化量:精整回弹量:δ外=0.02mm,精整余量:Δ外=0.06mm,烧结收缩率:C外=0.15%,压制回弹率:e外=0.2%。
内径变化量:δ内=0.01mm, Δ内=0,C内=0.15%,e内=0.15%。
4.设计计算(1)成型模结构:由压坯尺寸和“成形模结构方案及适用范围”表,选用双向压制结构,(阴模和芯棒液压浮动实现)。
结构图如下:有孔类压坯浮动压制成形模1-上模冲 2-阴模 3-脱模套 4-阴模板 5-下模冲 6-芯棒 7-导柱 8-导套 9-下模板 10-外连接板 11-垫铁 12-弹簧 13-装粉调节垫 14-内连接板(2)成形模径向尺寸d m=(d max-δ内) ×(1+ C内- e内)+Δ内=22.01mmD m=(D min-δ外) ×(1+ C外- e外)+Δ外=30.05mmd max ,D min分别为产品内外经允许值的最大最小值。
粉末冶金模具设计算
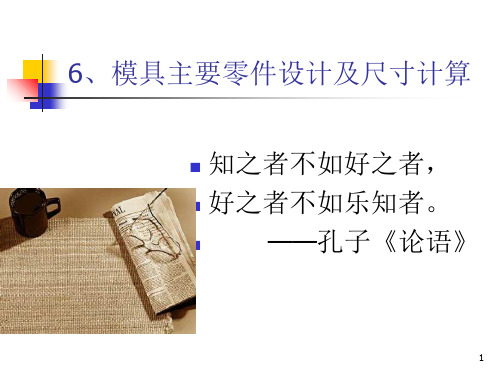
29
Hf—阴模高度 H1—压坯台阶高度 H10—压坯台阶1的装粉高度
H2—压坯总高度 H20—压坯台阶2的装粉高度
30
(二)模具高度的计算
(1)阴模
阴模高度 Hf一般由三部分高度组成, 即
Hf=H0+H1+H2
式中
Hf——阴模高度(mm); H0——装粉高度(mm) ; H1——下模冲定位高度。一般为10~50mm ; H2——手动模装粉锥高度(mm)。不需要时H2=031
4
单层整体阴模
5
双层组合阴模
6
7
2.芯棒要求 1)保证压坯的几何形状和尺寸精度; 2)粗糙度要低; 3)与模冲配合良好; 4)高的硬度; 5)压坯容易脱出芯棒,方便操作,利于加工; 6)较长较大芯棒采用组合结构。
8
3.模冲 1)高硬度和耐磨性,适当的韧性; 2)模冲与阴模、芯棒配合良好,有合理的配合 间隙; 3)表面有较低的粗糙度; 4)保证平行度、垂直度、同轴度;
压坯密度ρ, 压缩比c, 单位压力 p等。
38
(一)金属粉末的松装密度
金属粉末的松装密度直接影响模腔的高度。此参 数选择不当,自动装粉时则会造成粉料装不下, 或粉料装得太多的现象。 实际生产中,松装密度在一定范围内有波动,为 此,在结构设计中一般考虑了调节装粉高度的装 置,但调节范围不宜过大。
压坯密度提高时,[σ压]侧向则增大,但与此同
时 p侧也剧增。
具体粉料压坯的[σ压]侧向应由实验测定。
66
铁基压坯侧向许用抗压强度[σ压]侧向
67
从表可看出: 1)相同成分的压坯,压坯密度越高,虽然[σ压]侧向提
高,但 p侧增加得更快,对强度条件不利;
2)石墨含量增加,使[σ压]侧向下降,对刚性条件不利。
粉末冶金模具及设计介绍
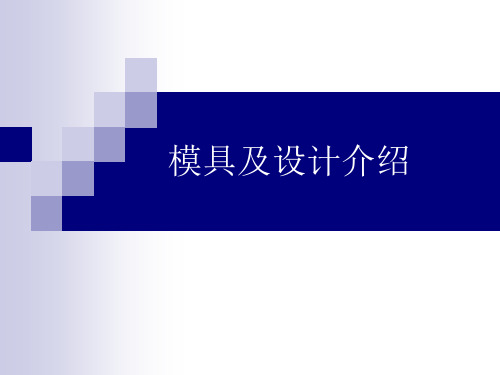
淬火
HRA91YG6 HRA89YG8 HRA87YG15
国600 G代表钴含量,越高韧性越好, 进口 耐磨性也较差,一般采用超微 中模和芯棒 1000 粒(春宝),国产稍差
常用模具材料热处理工艺
牌号
SLD V4 SKH9 Cr12 40Cr
使用硬度 HRC57~59 HRC60~61
HRC56~57 HRC60~61 HRC57~59 HRC60~61 HRC45~50 HRC45~50
模具制造技术特点----内外圆磨床
在工件直径回转的磨床上,使用砂轮对装夹好的旋 转工件进行内外径,台阶及端面及磨削加工。操 作步骤如下:
1. 在磨床的三爪卡盘上,将模具轻轻夹住,用千分表
先校正模具的端面偏心再校正外径的偏心,最后将 模具夹紧。 选择合适砂轮安装在磨床的磨头主轴上并夹紧; 选择合适的车床转速,走刀量和吃刀深度。 依模具图尺寸和形状的要求,对模具进行磨削加工。 抛光完毕后,停车先将三爪卡盘松开一点,用手 将模具托住再将三爪卡盘完全松开后,取下模具 依照模具图要求进行自我尺寸检查。
模具制造技术特点----平面磨床
平面磨床加工特点:
在砂轮直径高速回转的平面磨床上,对装 夹好的 工件,进行往复的平面磨削加工。操作步骤如下:
1. 选择合适磨床夹具,用千分表先校正模具的垂直度 和平行度,将模具夹住。 2. 选择合适的砂轮将之在磨床主轴上夹紧; 3. 选择合适的砂轮转速,走刀量和吃刀深度。
1. 在车床的三爪卡盘上,将模具轻轻夹住,用百分表先校正模 具的端面偏心再校正外径的偏心,最后将模具夹紧。 2. 选择合适的车刀将之刃磨 OK; 3. 将已选择的车刀在车床的刀架上,校正刀尖中心高和刀具的 角度后并夹紧; 4. 选择合适的车床转速,走刀量和吃刀深度。 5. 依模具图尺寸和形状的要求,对模具进行车削加工。 6. 对已车加工面采用较高的车床转速,用油石和砂纸进行研磨 抛光。 7. 抛光完毕后,停车先将三爪卡盘松开一点,用手将模具托住 再将三爪卡盘完全松开后,取下模具依照模具图要求进行自 我尺寸检查。
- 1、下载文档前请自行甄别文档内容的完整性,平台不提供额外的编辑、内容补充、找答案等附加服务。
- 2、"仅部分预览"的文档,不可在线预览部分如存在完整性等问题,可反馈申请退款(可完整预览的文档不适用该条件!)。
- 3、如文档侵犯您的权益,请联系客服反馈,我们会尽快为您处理(人工客服工作时间:9:00-18:30)。
影响压坯密度分布均匀性的因素:• Nhomakorabea末成分和性能
•模具表面质量
•摩擦力
•压制时粉体产生柱式流动,几乎不产生明显
的横向流动 7/4/2019
8
压坯中中立层的位置可以表示压坯密度分布
的均匀程度。通过压制方式和压模结构合理
选择使中立层2边受相同压缩,提高密度分布
均匀性 7/4/2019
9
7/4/2019
7/4/2019
16
7/4/2019
17
双向压制
S侧max/S=[1-(ρ中/ρ上)m]/μξ=2K
当柱状压坯K<S侧/S<2K,或者圆柱体 K/4<H/D<K/2时,采用双向压制、非同时双 向压制、浮动阴模双向压制或者下拉式压制 可以满足压坯密度分布均匀性要求
7/4/2019
18
7/4/2019
7/4/2019
13
7/4/2019
14
7/4/2019
15
•压制方式的选择依据
压制方式和方法不同,上、下模冲、芯杆和阴 模相对于粉末压坯的相对运动方向及速度也不 同,从而使外摩擦对压坯密度的均匀分布产生 有害或者有利的影响。
单向压制
S侧max/S=[1-(ρ下/ρ上)m]/μξ=K
当柱状压坯S侧/S<K或者圆柱体压坯高径比 H/D<K/4时,采用单向压制可以满足压坯密度 分布均匀性的要求
11
非同时双向压制原理为压模结构设计提供了 压坯密度均匀分布的理论基础;也为粉末压 机的设计提供了重要基础,使得多凸轮和凸 轮曲柄粉末压机更好地满足粉末压坯密度均 匀分布的要求。
7/4/2019
12
摩擦压制
在压制过程中,让阴模或芯杆与样品侧面产 生同向相对移动,即运动得更快,借助粉末 与模壁之间的摩擦,带动与阴模或芯杆接触 的粉末层移动,从而可改善沿压坯高度方向 的密度分布均匀性。
m:阴模外径与内径之比; ρ:压坯的相对密度 当相对密度为:0.80~0.85时,m=2~4,可粗略 估算:
对于铁基:P侧剩=0.18~0.20P 对于铜基: P侧剩=0.20~0.22P
7/4/2019
5
•精整压力的计算
外箍内的精整: 精整压力Fc=F1+F2+F3
其中:F1为实现轴套纯变形所需要的力;
7/4/2019
21
7/4/2019
22
7/4/2019
23
不等高压坯压模的设计原理
影响压制过程中粉末流动方式的因素: 粉末的流动性 装粉方法 外摩擦力 上下模冲设计 压坯横截面形状
在压制的不同阶段,粉末流动方式也不同
7/4/2019
24
装粉阶段
粉末以散状流动的方式充填模腔,由于摩擦力的 影响容易产生“拱桥”现象。
压力相等时双向压制与非同时双向压制的效 果相同
非同时双向压制中第二次压制的模冲移动距 离:
x=(d2-d1)h/d1
或者 y=x/l=100(d2-d1)/d1(k-1)
其中:d2为要求的压坯平均密度;d1为单向压 制的平均密度;h为压坯高度;k为压缩比;l 为装粉高度与压坯高度之差。
7/4/2019
3
在低速高单位压制压力条件下,塑性金属粉 末易发生“模瘤”;模具表面质量差、润滑 不良和模温过高,加重模瘤现象。
严重时脱模压力超过压制压力,使得模具拉 伤。
无润滑塑性金属粉末应当避免高压压制
F脱=μ静P侧剩S侧 P侧剩=E∑R剩(m2-1)/2R
P侧剩=jξ0ρP
7/4/2019
4
其中:
∑R剩:卸压后阴模半径上剩余的变形量; j: 剩余侧压强与侧压强之比,决定于模具的刚度;
20
选择原则
•(S侧阴+S侧芯)/S<K或者圆筒形压坯h/T<K/2时,可 采用单向压制;
•(S侧阴+S侧芯)/S>K时,如果(S侧阴+S侧芯)/2< (S侧阴-S侧芯), 或者圆筒形压坯D内<T,可采用双向压制;
•(S侧阴+S侧芯)/S>K时,如果(S侧阴+S侧芯)/2> (S侧阴-S侧芯), 或者圆筒形压坯D内>T,可采用摩擦芯杆压制
粉末冶金原理及模具
材料科学与工程学院
7/4/2019
1
第3章 粉末冶金模具设计原理
3.1 压制过程和精整过程中力的计算
3.2 压坯密度分布与压制方式的关系
3.3 不等高压坯压模的设计原理
粉末装填系数相同或相近 压制时压缩比相同或相近 压制速率相同或相近
目的
压坯:相对均匀的压实密度
3.4 组合模具的设计原理
形状完整,具有一定强度
3.5 压制过程的图示
7/4/2019
2
•压制压力的计算
模压过程的总压制力等于净压力与外摩擦力 之和
单位压制压力与压坯密度定量关系的研究, 是近60年来粉末成形理论研究的主要内容
•脱模力的计算
压制压力去掉后,侧压力因为高度方向的弹 性后效,侧压力会下降35~77%
7/4/2019
19
摩擦芯杆压制
上模冲强迫芯杆一起向下移动,且芯杆下 移的速度大于粉末下移的速度,因而靠芯 杆与粉末之间的摩擦力带动粉末向下移动。
[(S侧阴-S侧芯)/S]max=[1-(ρ下/ρ上)m]/μξ=K 对于圆筒形压坯的高与壁厚之比:
h/T=K(1+D内/T)/2 摩擦芯杆压制特别适合于大孔薄壁压坯
7/4/2019
整形区的单位精整压力为
Pc=σ/[1+(S+μQ)/2S2]
在此: σ为单向压缩条件下材料塑性变形的抗 力
通常内胀外精整方式的精整压力几乎只有外箍 内精整方式的十分之一
材料塑性变形抗力与材质、组织和孔隙率密切
关连7/4/2019
7
•压坯密度分布与压制方式的关系
压坯密度分布不均匀的地方,常常是压坯截 面积发生变化的分界处;脱模时这种部位也 容易产生裂纹,烧结时易引起变形。
d粉—粉末松装密度; d1—第一次压制后压坯平均密度; 第一次压制后:d粉H粉=d1h1 x=h1-h
d粉H粉=d1(h+x) ∴x=(d粉H粉-d1h)/d1 第二次压制后:d粉H粉=dh
d粉=d ·h/H粉 x=(d-d1)h/d1; k=H粉/h=(l+h)/h ∴x=(d-d1)l/d1(k-1); y=x/l ·11000%
F2为克服整形区外摩擦所需的力;
F3克服内摩擦所需的力。
精整压力计算公式Fc=Pc (S+μQ)+0.58σαS2
其中:Pc 为精整区的平均单位压力;Q为阴模精
整区的工作面积;σ为精整件的塑性变形抗力
(三向压力);α为阴模入口端的角度;S2为精整
区轴套的横截面积
7/4/2019
6
内胀外精整
精整压力计算与外箍内时相同;