车床操作规程
车床规程15篇

车床规程15篇【第1篇】仪表车床平安操作规程一、操作人员经考试合格取得操作证,方准进行操作,操应熟识本机的性能、结构等,并要遵守平安和交接班制度。
二、清除车床上阻碍工作的杂物,检查防护装置、刀架等是否正常、坚固,各手柄是否敏捷、定位精确,电源及接地装置是否良好,确认无误后方可开动三、按润滑图表规定加油,检查油质、油量是否正常,油路是否通畅。
四、安装卡盘时要将锁紧螺丝固紧在主轴上,以免开车时滑脱造成事故。
五、常常检查刀架转动是否正常,定位是否精确,快速机构是否敏捷牢靠。
六、不得在机床滑动部位放置扳手等物,不准在机床顶尖上或床身台面上修整锤击工作。
不得任意摩挲机床的运转部位,或用手制动机床转动部位。
七、机床消失特别现象时,应马上停车排解,或通知检修工人检修。
八、工作完毕或下班时,必需清扫机床,保持干净和在导轨、滑动面上涂油防锈,将各手柄放置空档位,并切断电源。
九、做好班后清扫工作,保持清洁,仔细执行交接班制度。
【第2篇】木车床平安操作规程1、木料卡紧后,必需用手转动卡盘校正,刀架、顶尖螺栓必需坚固,然后接通电源试车。
2、装刀具时,刀杆伸出刀架的长度要短于5cm,刀杆要保持50cm的长度。
加工大件时(直径50cm以上)进刀不行过猛。
3、车削带有棱角的不规章木料,应先用固定车刀去棱角后,再用车刀进行细加工。
4、车削第一刀时,进刀量要小。
用砂布磨光时,刀架先落下,必需右手在前左手在后,用力要匀称。
防止过热灼手,不准用手去摸工件。
5、用胶粘合的木料,必需放置24h之后,方能在车床上加工。
6、车床转速应依据形状尺寸和结构而定,不行过高,防止飞出伤人。
【第3篇】曲轴主轴颈车床操作规程1.操作人员经考试合格取得操作证,方准进行操作,操应熟识本机的性能、结构等,并要遵守平安和交接班制度。
2.根据润教导加油,检查油质,油量是否正常。
3.检查各操纵手柄是否敏捷牢靠,电机电源、接地装置及防护装置等是否良好。
4.检查各按钮的功能,手动、自动工作状况及各部件工作是否正常。
普通车床安全操作规程(10篇范文)

普通车床安全操作规程(10篇范文)第1篇普通车床安全操作规程一、操作者必须严格遵守维护和使用设备的四项要求、五项纪律,严禁超负荷使用设备。
二、开车前,必须按照巡回检查点仔细进行检查,并按照润滑图进行润滑。
三、停车八小时以上再开动设备时,应先低速转动三至五分钟,确认滑润系统畅通,各部位运转正常后,再开始工作。
四、使用中严禁开车变速,校正装卸工作时,必须关闭主电机。
五、装卡工作时,必须牢固可靠,卡盘扳手必须随时拿掉,加工偏重工件时,必须加以平衡。
装卸卡盘和较重工件时,导轨面必须垫好木板。
六、顶尖顶持工件时,尾座套筒伸出量不得大于套筒直径的两倍。
七、床身上禁止放置工、卡、量具及工件等。
八、加工材料改变时,必须清扫设备。
九、运转时,经常注意机床润滑情况及声音,严禁将开动着的机床委托他人照看,不准拆卸安全防护装置。
十、非电工不准打开电器箱门,使用机床者必须仔细清扫,每周至少清洗一次。
第2篇普通车床安全技术操作规程1 必须遵守金属切削加工安全技术操作《通则》。
2 用卡盘装卡工件时,其卡爪不得超出卡盘三分之一。
3 转动刀具时;必须将刀盘退到安全区转动。
4 装卸卡盘时,卡盘下必须垫木板,卡爪必须退到卡盘内。
卡盘、工装必须有保险装置。
装卡工件所用扳手的开口,必须与螺母尺寸相符。
5 装卡工件必须停机,装卡要牢固,装卸大型工件床面必须垫木板,装卸工件要轻拿轻放,不准滑脱抛掷。
6 加工细长工件必须用顶尖、跟刀架,床头箱后面外露部分超过300mm。
时,必须加托架设防护栏及防弯装置。
7 用挫刀抛光工件时,挫刀必须装有木柄,右手在前。
用砂布磨光外国时,严禁把砂布裹在工件上;光内孔时必须用专用工具。
8 床头箱、刀架、床面上不准放置任何物品。
9 攻丝或套丝时必须用专用工具,严禁一手扶攻丝架(扳牙架),一手开车工作。
10 切断工件时,大料必须留有一定余量,卸下后断开,小料严禁用手接工件。
11 使用四爪卡盘夹紧工件时,必须均衡用力。
车床的操作规程

车床的操作规程
《车床操作规程》
一、车床的基本操作规程
1. 在使用车床之前,必须仔细阅读车床的操作说明书,并按照说明书中的要求进行操作。
2. 在操作车床时,必须穿上工作服和防护眼镜,并将头发固定好,以免被旋转的机床零部件缠绕。
3. 车床操作前需要检查机床各部位润滑油情况,保证润滑系统正常工作。
4. 在进行车床操作时,必须使用相应的夹具以及夹具保持装置来确保工件在车削过程中的稳定性,严禁手持工件或者其他方式来进行固定。
5. 在进行车削操作时,必须使用合适的切削刀具,并根据工件的材质和要求选择适当的转速、刀具进刀深度和进给速度。
6. 在车床操作过程中,切勿将手或其他物品靠近旋转的刀具和工件,以免发生意外。
7. 车削完毕后,需要关闭车床并等待所有部件停止运转后,才能进行卸载工件和清洁车床。
二、车床的安全操作规程
1. 在操作车床时,必须保持清醒和专注,切勿受到外界干扰或者情绪波动影响,以免发生意外。
2. 在操作车床过程中,严禁戴手套进行操作,以免被卷入旋转部件中。
3. 在操作车床时,需要保持机台周围整洁,清除积木和杂物,保证操作空间通畅和安全。
4. 在操作车床时,需要留意机床各个部位的运转情况,一旦发现异常现象应立即停机检查。
5. 在进行车削操作时,必须遵守机床的使用规范和使用限制,严禁超负荷操作。
6. 在操作车床时,必须随时保持通讯畅通,以便在意外情况发生后及时求助和处理。
7. 在操作车床时,必须严格遵守现场安全操作规程,并接受相关安全培训,确保自身安全和设备完好。
以上是关于车床的操作规程,希望能够帮助操作人员正确、安全地使用车床,保障生产过程中的安全和效率。
车床安全操作规程
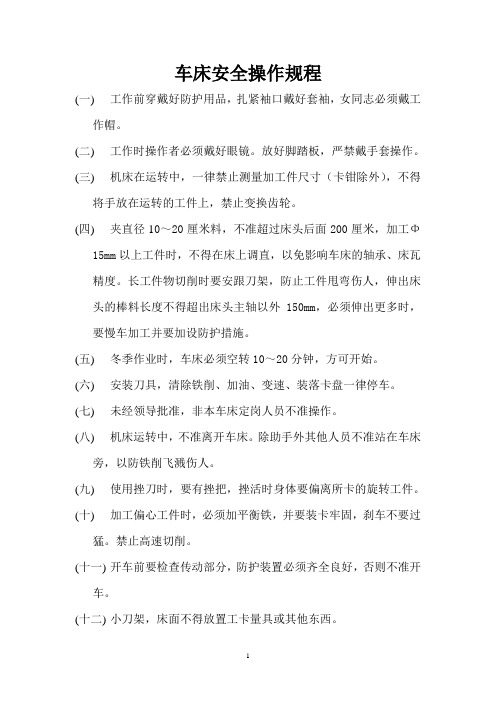
车床安全操作规程
(一)工作前穿戴好防护用品,扎紧袖口戴好套袖,女同志必须戴工
作帽。
(二)工作时操作者必须戴好眼镜。
放好脚踏板,严禁戴手套操作。
(三)机床在运转中,一律禁止测量加工件尺寸(卡钳除外),不得
将手放在运转的工件上,禁止变换齿轮。
(四)夹直径10~20厘米料,不准超过床头后面200厘米,加工Φ
15mm以上工件时,不得在床上调直,以免影响车床的轴承、床瓦精度。
长工件物切削时要安跟刀架,防止工件甩弯伤人,伸出床头的棒料长度不得超出床头主轴以外150mm,必须伸出更多时,要慢车加工并要加设防护措施。
(五)冬季作业时,车床必须空转10~20分钟,方可开始。
(六)安装刀具,清除铁削、加油、变速、装落卡盘一律停车。
(七)未经领导批准,非本车床定岗人员不准操作。
(八)机床运转中,不准离开车床。
除助手外其他人员不准站在车床
旁,以防铁削飞溅伤人。
(九)使用挫刀时,要有挫把,挫活时身体要偏离所卡的旋转工件。
(十)加工偏心工件时,必须加平衡铁,并要装卡牢固,刹车不要过
猛。
禁止高速切削。
(十一)开车前要检查传动部分,防护装置必须齐全良好,否则不准开车。
(十二)小刀架,床面不得放置工卡量具或其他东西。
(十三)机床开车时必须检查卡盘,防止回转的安全装置,必须牢固可靠,否则不准开车。
(十四)上落卡盘或花盘时,必须车头孔穿入保险杠杆做保险支架,以免卡盘突落垫手。
数控车床操作规程(3篇)

数控车床操作规程一、工作前准备1.携带并佩戴个人防护用品,包括安全眼镜、耳塞、手套等。
2.检查数控车床的各个部件是否正常,如电源、控制系统、主轴等。
3.检查工作区域是否整洁,确保没有杂物。
4.检查工件与夹具是否正确安装,夹具是否紧固。
5.根据工艺要求设置好数控车床的刀具,包括刀具的进给量、转速等参数。
二、开机操作1.打开数控车床的电源开关,并确保控制面板上的开关处于关机状态。
2.将电源和控制系统连接。
3.操作人员根据工艺要求启动数控车床,确保主轴的转速正常。
4.根据工艺要求调整刀具的切削深度,并开始数控车床的工作。
三、操作规程1.操作人员应保持警觉,注意观察数控车床的运行状态,确保安全。
2.操作人员应掌握数控编程操作,按照工艺要求进行编程。
3.操作人员应根据工件的形状和尺寸,选择合适的刀具,并调整刀具的位置和角度。
4.开始加工前,操作人员应检查刀具的质量和磨损情况,及时更换。
5.操作人员应根据工艺要求调整数控车床的进给速度和主轴转速。
6.操作人员应注意数控车床的润滑和冷却系统是否正常工作,及时调整。
四、加工操作1.操作人员应严格按照工艺要求,合理安排加工顺序。
2.操作人员应精确控制数控车床的进给量和主轴转速,确保加工质量。
3.操作人员应根据实际情况,合理调整刀具的进给速度和切削深度。
4.操作人员应根据工件的特点,灵活应用刀具的进给方式和切削方法。
5.加工过程中,操作人员应随时注意数控车床的运行状态,及时排除故障。
6.操作人员应合理利用数控车床的各项功能,提高加工效率。
五、加工结束1.加工结束后,操作人员应关闭数控车床的电源。
2.操作人员应对数控车床进行清洁和维护,保持其良好状态。
3.操作人员应将使用过的刀具归位,并及时更换需要修整的刀具。
4.操作人员应整理工作区域,清理杂物和废料。
5.操作人员应记录加工过程中的关键参数和故障情况,以便后期分析和改进。
六、安全注意事项1.操作人员应严格遵守安全操作规程,禁止违章操作。
车床安全操作规程
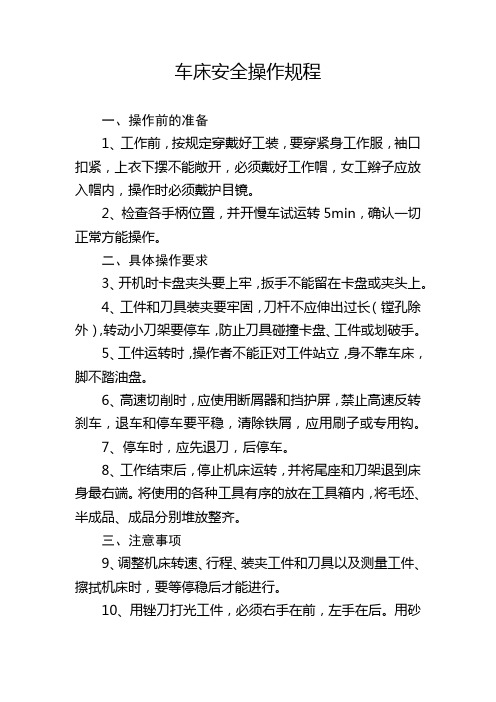
车床安全操作规程一、操作前的准备1、工作前,按规定穿戴好工装,要穿紧身工作服,袖口扣紧,上衣下摆不能敞开,必须戴好工作帽,女工辫子应放入帽内,操作时必须戴护目镜。
2、检查各手柄位置,并开慢车试运转5min,确认一切正常方能操作。
二、具体操作要求3、开机时卡盘夹头要上牢,扳手不能留在卡盘或夹头上。
4、工件和刀具装夹要牢固,刀杆不应伸出过长(镗孔除外),转动小刀架要停车,防止刀具碰撞卡盘、工件或划破手。
5、工件运转时,操作者不能正对工件站立,身不靠车床,脚不踏油盘。
6、高速切削时,应使用断屑器和挡护屏,禁止高速反转刹车,退车和停车要平稳,清除铁屑,应用刷子或专用钩。
7、停车时,应先退刀,后停车。
8、工作结束后,停止机床运转,并将尾座和刀架退到床身最右端。
将使用的各种工具有序的放在工具箱内,将毛坯、半成品、成品分别堆放整齐。
三、注意事项9、调整机床转速、行程、装夹工件和刀具以及测量工件、擦拭机床时,要等停稳后才能进行。
10、用锉刀打光工件,必须右手在前,左手在后。
用砂布打光工件,要用“手夹”等工具,以防绞伤。
车刀要移到安全位置、刀架面上不准放置工具和零件,划针盘要放牢。
11、车床工作时间不能随意离开工作岗位,禁止玩笑打闹,有事离开必须停机断电,工作时思想要集中,机器运转中不能测量工件,不能在运转中的车床附近更换衣报。
12、凡两人或两人以上在同一台机床工作时,必须指定一人为机长,统一指挥,防止事故发生。
四、异常情况及处理13、机床发生异常时,如异响、冒烟、震动、臭味等,应立即停车并切断电源,通知专业人员检查处理。
14、突然停电时,要立即关闭机床,并将刀具退出工作部位。
15、设备操作人员受伤,应立即停车,并及时告知车间领导,立即进行包扎止血等初期应急处置,通知或转送医疗机构。
五、其他要求16、下班时对未加工完的重、长、大型工件应加好临时支撑,避免设备受力、工件和主轴变形。
17、保持工作环境的清洁,及时清理工作区域的切屑、余料等。
车床安全操作规程

车床安全操作规程一、车床操作前的准备1、操作人员必须经过专业培训,熟悉车床的结构、性能和操作方法,并取得相应的操作资格证书。
2、穿着合适的工作服,袖口要扣紧,严禁戴手套操作车床。
女生应将头发盘起并戴好工作帽,防止头发卷入旋转部件。
3、检查车床各部分是否正常,包括电气系统、润滑系统、防护装置等。
确保车床周围环境整洁,无杂物堆积。
4、安装刀具和工件时,应使用合适的工具,并确保安装牢固。
刀具的伸出长度不宜过长,以免发生振动和碰撞。
5、调整车床的转速、进给量等参数时,应根据工件的材料、尺寸和加工要求进行合理选择,并在停车状态下进行。
二、车床操作中的注意事项1、开机前,应先手动转动卡盘和各移动部件,检查是否有异常情况。
确认无误后,打开电源,启动车床。
2、加工过程中,操作人员应集中精力,不得擅自离开工作岗位。
时刻注意观察切削情况,如有异常,应立即停车处理。
3、严禁在车床运转时测量工件尺寸或用手触摸工件和刀具。
如需测量,应停车并使用量具进行测量。
4、切削过程中,应使用合适的切削液,以降低切削温度,减少刀具磨损,并防止切屑飞溅伤人。
5、当车床发生故障或出现异常声响时,应立即停车,并切断电源,进行检查和维修。
严禁在故障未排除的情况下继续操作车床。
6、加工细长轴类工件时,应使用跟刀架或中心架,以防止工件弯曲变形和甩伤人。
7、装卸较重的工件时,应使用吊车或其他辅助设备,并由专人指挥,确保操作安全。
三、车床操作后的清理与维护1、加工完成后,应先停车,然后切断电源,清理车床表面的切屑和油污。
2、卸下刀具和工件,并妥善存放。
对刀具进行检查和保养,如有磨损或损坏,应及时更换。
3、定期对车床进行润滑、保养和维护,检查各部件的连接是否松动,电气系统是否正常等。
4、填写设备运行记录和维护记录,以便及时发现问题并进行处理。
四、安全防护装置的使用1、车床应配备齐全的防护装置,如防护门、防护挡板等。
操作人员不得擅自拆除或损坏防护装置。
2、在操作过程中,应确保防护装置处于关闭状态,以防止切屑和冷却液飞溅伤人。
普通车床操作规程(三篇)

普通车床操作规程普通车床是一种用于金属加工的常见设备,操作规程是确保操作人员安全和正常操作的重要文件。
下面是普通车床操作规程的大致内容,主要包括安全操作、准备工作、操作步骤和常见问题及解决方法等。
一、安全操作1. 操作人员应经过必要的培训,并掌握基本的车床操作知识和技能。
2. 操作人员应穿戴好防护设备,如工作服、安全鞋、护目镜、手套等,以保证自己的安全。
3. 在使用车床前,应对车床进行检查,确保车床的各个部位正常工作,无损坏或松动。
4. 在操作车床时,不得戴有长项链、手链等物品,以免发生卡榫事故。
5. 操作人员应保持机器周围的清洁,防止杂物掉落,以免造成意外伤害。
二、准备工作1. 在进行车床操作前,需要准备好所需加工的工件和刀具,并对其进行检查,确保完好无损。
2. 对车床进行润滑保养,确保车床的润滑系统正常工作。
3. 准备好所需的测量工具和检测设备,以便进行加工后的质量检验。
4. 对车床进行调试,检验车床的各项功能是否正常。
三、操作步骤1. 根据加工要求,选择合适的刀具、夹具和好工件,并进行安装。
2. 调整车床的工作台和刀架,确保刀具与工件之间的距离、角度和方向正确。
3. 打开车床的主电源开关,启动车床,并进行试运行,确保各项功能正常。
4. 开始加工前,要根据实际情况设置好切削参数,如进给速度、主轴转速、刀具前进速度等。
5. 进行加工时,要注意切削方向和切削深度,避免因切削过大或切削反向引起的工件损坏或事故。
6. 在加工过程中,要始终保持专注,并经常检查加工质量和刀具状况,如有异常及时处理或更换。
7. 加工完成后,关闭车床的电源开关,清理车床周围的杂物,及时进行设备维护和保养。
四、常见问题及解决方法1. 刀具磨损或断裂:及时更换刀具,确保刀具的锋利和稳定性。
2. 加工质量不合格:检查加工参数和刀具状况,及时调整,保证加工质量。
3. 设备故障:及时停机并断电,清理故障现象,维修后方可重新启动。
4. 安全事故或人员伤害:及时报警并停机,提供紧急救助,记录事故过程并查明原因。
车床安全操作规程

车床安全操作规程
操作规程
(一)、启动前检查与准备
1、检查设备外观完好、电源线、接地线连接牢固,附属工具完好,检查齿轮箱润滑油位,调整导轨间隙,佩带护目镜。
2、开车前必须给各油润滑点、导轨注油,检查导轨上有无异物。
3、操作前检查各手柄的位置是否正确;检查正反刹车间隙,确保刹车过程可靠;检查各刀架间隙是否合适,不合适时进行调整。
(二)、启动操作
1、开始使用前车床应经过2-5分钟低速空转润滑、热车、检查润滑油检查窗口是否上油,试运转正常后,才能开始工作。
2、根据加工件材质选用合适的刀具、按照加工要求来调整角度,确认刀具安装紧固可靠。
3、车削前,检查工件的装夹是否正确、紧固、可靠。
4、工件转动时,才允许进刀或退刀操作,在车刀退出后才能停车。
5、测量工件或调整车床都应在停止运转后方可进行,车床运转时严禁用手接触工件或戴手套操作。
(三)、停机
1、正常停机
(1)每日加工工作完成后,各手柄回位,刀架回位,尾部顶尖座回位至车床尾部,切断床身电源、总电源。
(2)每日加工工作完成后,必须清理设备铁屑及油污。
2、紧急操作及紧急停车作业中发生电气故障、控制失灵、机械故障等异常失控时可紧急关闭电源或紧急停车按钮,排除故障。
普通车床安全操作规程

普通车床安全操作规程一、工作前1、操作者必须全面了解和掌握本床的结构原理,熟悉机床的加工知识。
2、检查操作手柄、开关、旋钮是否在正确位置,操纵是否灵活,限位及安全装置是否齐全、可靠。
3、接通电源,空车低速运转是否正常,如有异常应停机检查或报告维修人员。
4、检查油标中的液面指示高度是否合适,特别是导轨油路是否畅通,并在规定部位加足润滑油。
5、确认润滑、电气系统及各部位运转正常后方可开始工作。
6、做好安全防护工作,袖口不得敞开、女生要戴防护帽,并将头发塞入帽子内。
二、工作中1、严禁超性能使用。
2、操作时,不准戴手套,为防止崩碎铁屑伤人,要戴防护眼镜。
3、机床边的工件要摆放整齐,要便于拿放。
严禁在机床上面摆放任何工量具、产品、杂物等。
4、严禁在卡盘、顶尖或导轨面上敲打、校直和修整工件。
5、装夹工件、刀具必须牢固、可靠。
严禁在主轴或尾座内安装锥度不符或锥面有严重伤痕和不清洁的刀具、顶尖等。
6、装夹完工件后立即取下卡盘扳手,以免开机后发生事故。
7、装卸卡盘或较重工件时,必须选择安全、可靠的吊具和方法,同时要对导轨进行防护。
8、合理选择转速及切削用量,严禁开车时进行变速。
9、机床尚在运转,禁止装卸、测量、触摸工件,禁止换档。
10、在车削过程中,绊上铁屑,应用铁钩清除,不准徒手清除;车内孔后抛光,切勿徒手打磨,要用专用工具。
11、操纵反车时应先停车后反向。
12、使用中心架、跟刀架、靠模板时,必须经常检查其与工件接触面上的润滑和磨损状况。
13、机床运转时,操作者不准擅自离开工作岗位及闲谈、打闹、睡觉等,杜绝醉酒、疲劳、听音乐操作机床。
14、运行中出现异常现象,应立即停机,查明原因,及时处理。
三、工作后必须将各操纵手柄置于“停机”位置,尾座、溜板箱移至床身右端,导轨加注润滑油,切断电源。
保管好工量器具,放置好加工工件,清除铁屑。
车床操作操作规程15篇

车床操作操作规程15篇【导语】车床操作操作规程怎么写受欢迎?本为整理了15篇优秀的车床操作操作规程范文,为便于您查看,点击下面《名目》可以快速到达对应范文。
以下是我为大家收集的车床操作操作规程,仅供参考,盼望对您有所关心。
名目【第1篇】车床操作规程1. 装卸卡盘,应在主轴孔内穿进铁棍或坚实木棍作爱护。
2. 加工偏心工件,应加配重铁平衡,并低速切削。
3. 瘦长工件应装中心架,工件长度超过床头箱外一米时,必需搭设支架。
4. 高速切削大型工件时,不准紧急制动和突然变换旋转方向。
如需换向,要先停车。
5. 打磨或抛光工件时,刀架要退到平安位置,防止衣秀触及工件或胳膊遇到卡盘。
6. 在立车上装卸工件时,应先将刀架放在平安位置,人不能站在转盘上。
车销薄壁工件时,应留意卡紧,并严格掌握切削量和切削速度,随时紧固刀架螺丝,车刀不宜伸出过长。
7 车床运转中,不准找正和卡紧工件。
【第2篇】卧式单轴、多轴自动半自动、车床操作规程适用机型:1、单轴自动车床:cg110(1a10),c1318(1a118),c1325(1a124),c1336(1a136),a12,a20,a40。
2、多轴自动、半自动车床:c24・4(1240・4),c25・4,c2140・p4,c2150・4d,c2132・6d,c2132・6,c24・6(1240・6),c2150・6d,c2216・6,bsa1/2 4,1290,ank135, ank155,1261m,1261,1265・6,1265m・6,12400一、仔细执行《金属切削机床通用操作规程》有关规定。
二、仔细执行下述有关补充规定:(一)工作前仔细做到:1、检查安排轴及凸轮上的凸轮、撞块应完好无裂纹,安装正确,紧固牢靠。
2、调正机床时,棒料、毛坯的夹紧,只准用手动不准用机动。
(二)工作中仔细做到:1、不准加工弯曲、未经冷拨和未经倒角的棒料。
2、装料时须将料头对准夹头孔,轻轻击进。
棒料长度一般以不超出料管200毫米左右为宜。
车床安全操作规程

车床安全操作规程为保证实践教学质量,标准实验设备使用,防止出现机床及人身事故,特制定本规程:一文明操作1.操作前应检查车床各部机构是否完好,传动手柄和变速齿轮手柄位置是否正确,以防开车时因突然撞击而损坏车床。
2.在车床运行中主轴需要变速时,必须先停车。
变换走刀箱手柄位置,要在机床低速运转时进行。
3.不允许在卡盘或床身导轨上敲击工件,床面上不准摆放工具、量具或工件。
4.装夹大型及较重工件时应用木板保护床面及导轨。
5.为了保证丝杠的精度,除车削螺纹外,不得使用丝杠进行自动走刀。
6.切削铸件时,导轨面的润滑油要清理干净,以防止铁屑研磨坏机床导轨面。
7.使用切削液时要在床面上涂抹润滑油,加工结束后要及时清理床面上残存的冷却液以防止床面生锈。
冷却液要定期更换。
8.机床周围应经常保持清洁整齐,工作完毕后应将大拖板摇至床尾并给机床导轨加油后关闭电源。
9.定时为机床各注油孔及导轨添加润滑油。
二操作1.工作时操作人员必须穿紧口工作服,女同志应戴工作帽。
操作时不准带手套。
2.工作时身体不准直对卡盘,切削时头不应靠工件太近,以防切屑进入眼内。
3.工作时必须精神集中,开车后不允许擅自离开机床或做与加工无关的工作。
4.工件和车刀必须装卡牢固,以防飞出发生人身事故。
5.不允许试图用手去刹住正在转动着的卡盘。
6.车床开动时,不准测量工件,也不能用棉纱去擦拭工件。
7.开车时不能去除铁屑,更不允许用手去直接去除铁屑。
8.工件装卡完毕后,应随手取下卡盘扳手。
9.车床电器出现故障时,应及时找电工维修,不准擅自装拆电器设备。
车床安全操作规程

车床安全操作规程一、安全生产规程1、实习学生进车间必须穿好工作服,并扎紧袖口。
女同学须戴安全帽,并将长发塞入帽子内。
夏季严禁穿裙子,短裤和凉鞋上机操作。
冬天不准带围巾。
2、工作时,头不能离工件太近,以防切屑飞入眼中。
为防止铁屑崩碎,必须戴防护眼镜。
3、工作时候必须集中精力,注意手、身体和衣服不能靠近正在旋转的机件。
如工件、带轮、皮带、齿轮等。
4、工件、刀具和夹具,都必须装夹牢固,否则会飞出伤人。
卡盘必须装有保险装置。
装夹好工件后,卡盘扳手必须从卡盘上取下。
5、凡装卸工件、更换刀具、测量加工表面及变换速度时,必须先停车。
6、车床运转时,不得用手去摸工件的表面,尤其是加工螺纹时,严禁用手抚摸罗纹面,以免伤手。
严禁用棉纱插摸转动的工件。
7、应用专用铁钩清除铁屑,绝不允许用手直接清除。
8、在车床上操作不准戴手套。
9、毛胚棒料从主轴孔的尾端伸出不得太长,并使用料架或挡板,防止甩弯后伤人。
10、不允许用手去刹住转动的卡盘。
11、不要随意拆装电器设备,以免发生触电事故。
12、工作中发现机床、电器设备有故障,应及时申报,由专业人员检修,未修好不得使用。
二、文明生产要求1、开车检查车床各部分机构及防护设备是否完好,各手柄是否灵活,位置是否正确。
检查各注油孔,并进行润滑。
然后使主轴空运1-2min,待车床运转正常后才能工作。
若发现车床有毛病,应立即停车、申报检修。
2、主轴变速必须先停车,变换进给箱手柄要在速进行。
为保持丝杠的精度,除车削螺纹外,不得使用丝杠进行机动进给。
3、刀具、量具及工具等的放置要稳妥、整齐、合理,分开放置在工具架上,用后应放回原处。
主轴箱盖上不准放置任何物品。
4、工具架上应分类摆放物件。
精度高的应放置稳妥,重物放下层、轻物放上层,不可随意乱放,已免损坏和丢失。
5、正确使用和爱护量具。
经常保持清洁、用手擦净、涂油,放置盒内,并及时归还工具室。
6、不允许在卡盘及床身导轨上敲击或校直工件,床面上不准放置工具或工件。
车床安全操作规程

1..装卸卡盘及大工件时要用木板垫在导轨面上,以防止伤人或碰伤车床导轨。
2.车床上不准摆放工件、工具、量具、刀具及其他物品,成品、半成品堆放要整齐。
3.装卸工件后,卡盘扳手不准放在卡盘上,应随时取下,切削过程中禁止用手触摸工件或测量工件尺寸。
4.加工细长工件时,要用顶尖、跟刀架或中心架,车头前面伸出部分不得超过工件直径的20-25mm,车头后伸出部分超过300mm时,必须装设防护板和托架。
5.加工偏心工件或使用弯板夹工件时,应加平衡铁,紧固螺栓不应少于两个,加工前应开慢车检查,刹车时应缓慢停车。
6.车内孔时,不得用锉刀、刮刀倒角,用砂布打光内孔时,不得将手指伸进去打磨。
三、工作后1.将各手柄扳到空挡位,将尾座、溜板箱移到床身尾端。
2.切断电源,清理机床及现场。
车床安全操作规程
一、工作前
1.开启前认真阅读工艺文件及图纸,做好准备工组并穿戴好安全防护用品,操作过程中不得戴手套。
2.开启前,应先检查机床各手柄位置是否正确,防护装置是否可靠,润滑是否良好。
3.工件和刀具必须装夹牢固、可靠,加工偏心工件时,要加配重装夹保护平衡,重装夹牢固并进行试运转。
4.此设备要求定人定岗操作。
车床安全技术操作规程
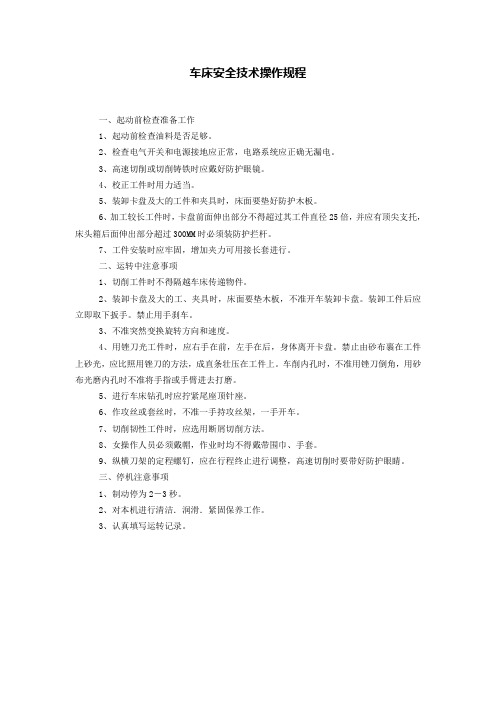
车床安全技术操作规程
一、起动前检查准备工作
1、起动前检查油料是否足够。
2、检查电气开关和电源接地应正常,电路系统应正确无漏电。
3、高速切削或切削铸铁时应戴好防护眼镜。
4、校正工件时用力适当。
5、装卸卡盘及大的工件和夹具时,床面要垫好防护木板。
6、加工较长工件时,卡盘前面伸出部分不得超过其工件直径25倍,并应有顶尖支托,床头箱后面伸出部分超过300MM时必须装防护拦杆。
7、工件安装时应牢固,增加夹力可用接长套进行。
二、运转中注意事项
1、切削工件时不得隔越车床传递物件。
2、装卸卡盘及大的工、夹具时,床面要垫木板,不准开车装卸卡盘。
装卸工件后应立即取下扳手。
禁止用手刹车。
3、不准突然变换旋转方向和速度。
4、用锉刀光工件时,应右手在前,左手在后,身体离开卡盘。
禁止由砂布裹在工件上砂光,应比照用锉刀的方法,成直条壮压在工件上。
车削内孔时,不准用锉刀倒角,用砂布光磨内孔时不准将手指或手臂进去打磨。
5、进行车床钻孔时应拧紧尾座顶针座。
6、作攻丝或套丝时,不准一手持攻丝架,一手开车。
7、切削韧性工件时,应选用断屑切削方法。
8、女操作人员必须戴帽,作业时均不得戴带围巾、手套。
9、纵横刀架的定程螺钉,应在行程终止进行调整,高速切削时要带好防护眼睛。
三、停机注意事项
1、制动停为2-3秒。
2、对本机进行清洁.润滑.紧固保养工作。
3、认真填写运转记录。
车床操作规程
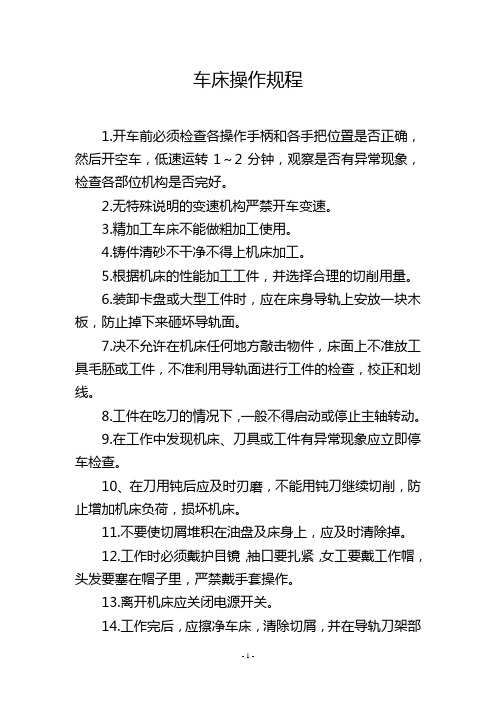
车床操作规程
1.开车前必须检查各操作手柄和各手把位置是否正确,然后开空车,低速运转1~2分钟,观察是否有异常现象,检查各部位机构是否完好。
2.无特殊说明的变速机构严禁开车变速。
3.精加工车床不能做粗加工使用。
4.铸件清砂不干净不得上机床加工。
5.根据机床的性能加工工件,并选择合理的切削用量。
6.装卸卡盘或大型工件时,应在床身导轨上安放一块木板,防止掉下来砸坏导轨面。
7.决不允许在机床任何地方敲击物件,床面上不准放工具毛胚或工件,不准利用导轨面进行工件的检查,校正和划线。
8.工件在吃刀的情况下,一般不得启动或停止主轴转动。
9.在工作中发现机床、刀具或工件有异常现象应立即停车检查。
10、在刀用钝后应及时刃磨,不能用钝刀继续切削,防止增加机床负荷,损坏机床。
11.不要使切屑堆积在油盘及床身上,应及时清除掉。
12.工作时必须戴护目镜,袖口要扎紧,女工要戴工作帽,头发要塞在帽子里,严禁戴手套操作。
13.离开机床应关闭电源开关。
14.工作完后,应擦净车床,清除切屑,并在导轨刀架部
分涂润滑油,整理加工成品。
车床操作规程

车床操作规程一、操作前准备1.检查车床各部件是否完好无损;2.清理车床及工作台面,确保清洁卫生;3.检查电源插头是否插紧;4.检查润滑系统是否足够,油量是否充足,油路是否畅通;5.检查切削刃具是否正确安装,刀柄是否牢固。
二、操作时注意事项1.操作车床时应佩戴眼镜、手套等防护用品,戴好口罩,注意安全;2.车床车削工件前,应先试运转一段时间以确保各部件正常运转。
3.车削时需要精确的控制旋转速度、进给量,不可超出机床规定范围。
4.刀具的移动速度不得过快,暴力操作应被限制;不宜使用过度锋利的刀具。
5.加工时,应密切注意料件表面,如有问题应及时停车处理。
6.操作人员应始终注意保持清晰的头脑,注意安全。
三、车削技术技巧1.调整切削刃具,刃口及刃角应符合车削要求;2.通过选择合适的转速和进给速度,确保车削进给尺寸精度和表面粗糙度的要求;3.飞切与自动进给的关系:飞切多用于手动进给、粗车及半精车,自动进给多用于车削中等精度、精加工。
4.深度及轴向进给的处理:深度进给应逐次进行,以防止切屑太厚影响表面质量,轴向进给应适当掌握留刨余量、切割刀刃及切屑处理等问题。
5.车床咬死、抖动等问题应尽量避免。
如发现有异常情况应立即停车,排除相关隐患,以保证机器的正常运转。
四、操作后维护1.关闭机器,切断电源,保持机器干净,检查是否有杂物残留,及时清理。
2.对润滑系统和其他部件进行检查和维护,及时补充润滑油。
3.对车削刀具进行清理和保养,储存在指定的地方,并确保它们的安全。
4.对车床的配件进行分类,储存在指定的地方,并确保它们的完整。
5.对车床的使用情况进行记录,完成相关报告,及时向上级反映机器故障及解决方案。
以上为车床操作规程,希望每个使用车床的用户都能按照规程操作,使用更加安全得心应手。
车床设备操作规程
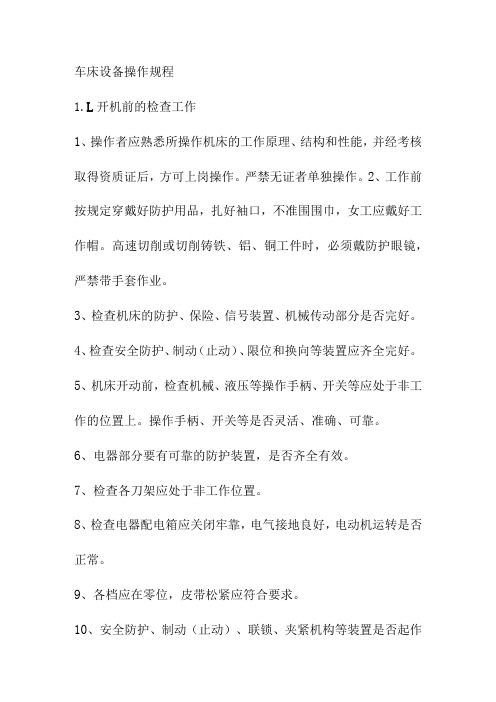
车床设备操作规程1.L开机前的检查工作1、操作者应熟悉所操作机床的工作原理、结构和性能,并经考核取得资质证后,方可上岗操作。
严禁无证者单独操作。
2、工作前按规定穿戴好防护用品,扎好袖口,不准围围巾,女工应戴好工作帽。
高速切削或切削铸铁、铝、铜工件时,必须戴防护眼镜,严禁带手套作业。
3、检查机床的防护、保险、信号装置、机械传动部分是否完好。
4、检查安全防护、制动(止动)、限位和换向等装置应齐全完好。
5、机床开动前,检查机械、液压等操作手柄、开关等应处于非工作的位置上。
操作手柄、开关等是否灵活、准确、可靠。
6、电器部分要有可靠的防护装置,是否齐全有效。
7、检查各刀架应处于非工作位置。
8、检查电器配电箱应关闭牢靠,电气接地良好,电动机运转是否正常。
9、各档应在零位,皮带松紧应符合要求。
10、安全防护、制动(止动)、联锁、夹紧机构等装置是否起作用。
校对机构运动是否足够行程,调正并固定限位、定程挡铁和换向碰块等。
11、机床导轨面上、工作台上禁止摆放工具或其它物品。
检查机床、工作台、导轨以及主要滑动面,如有障碍物、工具、铁屑、杂物等,必须清理,擦拭干净、上油;12、按机床润滑图表规定加油,油路是否畅通。
保持润滑系统清洁,油杯、油眼不得敞开。
13、凡两人或两人以上在同一台机床工作时,必须指定1人为机长,统一指挥,防止事故发生。
1.2、工作过程中的操作规定。
1、坚守岗位,精心操作,不做与工作无关的事。
因事离开机床时要停车,必须关闭电源,停车。
2、机床开动后,应低速运转3—5分钟,确认各部位正常后方可工作,在冬季操作车床时一定要跑温、检查管线是否冻裂,不得在运转部位传递或取拿物品。
在热车期间,不得离开岗位。
3、机床开动后,要站在安全位置上,以避开机床运动部位和铁屑飞溅。
4、未夹工件前必须进行空车试运转,确认一切正常后,方能装上工件。
工件、刀具、夹具必须装卡牢固,浮动力具必须将引刀部份伸入工件,方可启动机床。
5、机床上特别是导轨面和工作台面,不准直接放置工具,工件及其他杂物,以免损坏床面。
- 1、下载文档前请自行甄别文档内容的完整性,平台不提供额外的编辑、内容补充、找答案等附加服务。
- 2、"仅部分预览"的文档,不可在线预览部分如存在完整性等问题,可反馈申请退款(可完整预览的文档不适用该条件!)。
- 3、如文档侵犯您的权益,请联系客服反馈,我们会尽快为您处理(人工客服工作时间:9:00-18:30)。
车床操作规程
车床操作规程
1目的
为了明确车工的工作职责。
2范围
适用于本分厂生产部车工作业。
3职责和权限
3.1按质按量完成上级安排的任务;
3.2工作中有权提出自己的工作方法和意见,并保证工作的
正确性;
3.3对工作中存在的不安全因素和隐患,有权拒绝工作,直
至不安全因素和隐患消除。
3.4有权对部门管理和班组建设提出切实可行的改进方法和
措施,以便更好地促进班组建设向更高的目标迈进。
4工作内容与要求
4.1工作目标:设备保养率100%,废品率低于2%。
4.2认真执行《切削加工通用作业指导书》的规定。
在两顶尖间装夹工件,刚性较差,因此,车削一般轴类零件,尤其是较重的工件,不能采用两顶尖装夹的方法,而采用一端夹住(用卡盘),另一端用(尾座)顶尖顶住的装夹方法。
4.3切削用量的选择
4.6.1切削用量是衡量切削运动大小的参数.它包括切削深
度(a
)、进给量(f)、切削速
p
)。
合理选用切削用量能有效地提高生产效率。
度(u
c
4.6.2合理的切削用量应能满足以小见大几点基本要求:4.6.2.1保证安全,不致发生人身事故或损坏机床、刀具等
事故。
4.6.2.2保证工件以加工表面的粗糙度和精度.
4.6.2.3在满足以上两项要求的前提下,应充分发挥机床的
潜力和刀具的切削性能,尽可能选用较大的切削用量,使切削时间少、生产率最高,成本最低。
4.6.2.4允许超过机床功率,在工艺系统刚性条件下,工件
不能产生过大的变形和振动。
4.6.3选择切削用量的步骤
4.6.3.1切削深度(a
)和行程次数的选择:粗车时,一般
p
把半精车和精车的余量留出来,剩下的加工余量尽可能一次切完。
只有当粗车余量太大时。
一次切去会产生明显的振动。
甚至刀具强度不允许、机床功率不够,才分几次进给。
一般是把第一次或头几刀的切削深度选的大些,最后留半精车和精车余量:半精车余量大致留1~3mm;精车余量为0.2~0.5mm。
当用硬质合金车刀切削时,最后一次的切削深度不宜太小,否则加工表面比较粗糙。
4.6.3.2进给量(f):切削深度选定以后,进给量应选得
大些。
但是,进给量的大小主要受刀杆、刀片、工件和机床的强度、刚性或扭矩、工件精度和表面粗糙度的限制。
当进给量太大时,可能会引起机床最薄弱零件的损坏、刀片碎裂、工件弯曲、加工表面粗糙度增大等。
粗车时,可选择大一些的进给量,一般为0.3~1.5mm/r。
精车时,考虑工件的表面粗糙度,所以进给量应选小些,一般为
0.1~0.35mm/r。
4.6.3.3切削速度(u
)的选择:当切削深度和进给量选好
c
以后,切削速度也应选取较为合理的数值。
应当做到既能发挥车刀的切削性能,又能发挥车床的潜力,并且保证加工表面质量和降低成本。
选择切削速度的一般原则如下:
4.6.3.4车刀材料:使用硬质合金车刀可比高速钢车刀的切
靴速度高。
4.6.3.5工件材料:切靴强度和硬度较高的工件时,因为产
生的热量和切靴力都比较大,车刀易磨损,所以切削速度应选得低些。
脆性材料如铸铁,车削时形成崩碎切削,热量集中在切削刄附近,不易传散。
因此,切削速度应取得低一些。
4.6.3.6表面粗糙度:要求表面粗糙度值小的工件,如用硬
质合金车刀车削,切削速度应取得高些;如用高速钢车刀车削,切削速度应取得低些。
4.6.3.7切削深度和进给量:切削深度和进给量增大时,切
削时产生的热量和切削力都较大,所以应适当降低切削速度。
反之,切学速度可取得高些。
4.6.3.8切削液:切削时加切削液可降低切削区域的温度,
并起润滑作用。
所以切削速度可适当提高。
4.6.4车刀主要角度的选择
4.6.4.1前角(γo)前角的大小与工件材料、加工性质和
刀局材料有关,但影响最大的是工件材料。
选择前角主要根据以下几个原则:
a)工件材料较软,可选择较大的前角;工件材料较硬,
可选择较小的前角。
b)粗加工时应取较小的前角;精加工时应选较大的前角。
c)车刀材料韧性较差,前角应取较小值;车刀材料韧性
较好,前角可取较大值。
4.6.4.2后角(αo)后角太大,会降低车刀的强度;后角
太小,会增加车刀后刀面跟工件表面的摩擦。
选择后角,主要根据以下几个原则:
a)粗加工时,应取较小的后角(硬质合金车刀:α
o=5O~70);精加工时,应取较大的后角(硬质合金车刀:αo=8O~100)。
b)工件材料较硬,后角宜取小值;工件材料较软,后角
取大值。
)一般磨成与后角相等。
4.6.4.3副后角(α′
4.6.4.4主偏角(κr)一般使用的车刀主偏角有450、600、
450、750、和900等几种。
主偏角还受到工件形状的限制;加工中间切入的工件,一般采用45O~600的主偏角。
4.6.4.5副偏角(κ′r)减小副偏角,可以减小工件的表
面粗糙度值,相反,副偏茑太大时,刀尖角就减小,影响刀头强度。
4.6.4.6刄倾角(λo)一般车削时(指工件圆整、切削厚
度均匀),选择零度刄倾角断续切削和强力切削时,为了增加刀头强度,刄倾角应取负值;精车时,为了减小工件表面粗糙度值,刄倾角应取正值。