齿轮副最大与最小侧隙的计算
齿轮位置校正计算公式

齿轮位置校正计算公式在机械传动系统中,齿轮是一种常见的传动元件,用于传递动力和转速。
然而,由于制造和安装误差等原因,齿轮的位置可能会出现偏差,导致传动系统的性能下降甚至故障。
因此,对齿轮位置进行校正是非常重要的。
本文将介绍齿轮位置校正的计算公式及其应用。
齿轮位置校正的计算公式可以通过几何原理和数学方法推导得出。
在实际应用中,常用的齿轮位置校正计算公式包括齿轮的中心距离调整公式、齿轮的轴向位置调整公式和齿轮的侧隙调整公式等。
下面将分别介绍这些计算公式的推导和应用。
首先是齿轮的中心距离调整公式。
齿轮的中心距离是指两个相互啮合的齿轮齿顶圆的中心之间的距离。
如果齿轮的中心距离偏差过大,会导致齿轮啮合不良或者产生噪音和振动。
为了调整齿轮的中心距离,可以使用以下的计算公式:Δa = (Δm Δm') / 2。
其中,Δa表示需要调整的中心距离偏差,Δm表示实际中心距离,Δm'表示设计中心距离。
通过这个公式,可以计算出需要调整的中心距离偏差,然后进行相应的调整。
接下来是齿轮的轴向位置调整公式。
齿轮的轴向位置是指齿轮轴线与机床主轴线之间的距离。
如果齿轮的轴向位置偏差过大,会导致齿轮与主轴的啮合不良或者产生轴向载荷。
为了调整齿轮的轴向位置,可以使用以下的计算公式:Δl = (Δm Δm') / 2。
其中,Δl表示需要调整的轴向位置偏差,Δm表示实际轴向位置,Δm'表示设计轴向位置。
通过这个公式,可以计算出需要调整的轴向位置偏差,然后进行相应的调整。
最后是齿轮的侧隙调整公式。
齿轮的侧隙是指齿轮啮合时齿宽方向的间隙。
如果齿轮的侧隙偏差过大,会导致齿轮啮合不良或者产生啮合不稳定。
为了调整齿轮的侧隙,可以使用以下的计算公式:Δs = (Δs Δs') / 2。
其中,Δs表示需要调整的侧隙偏差,Δs表示实际侧隙,Δs'表示设计侧隙。
通过这个公式,可以计算出需要调整的侧隙偏差,然后进行相应的调整。
齿轮副法向齿侧间隙的计算与检测
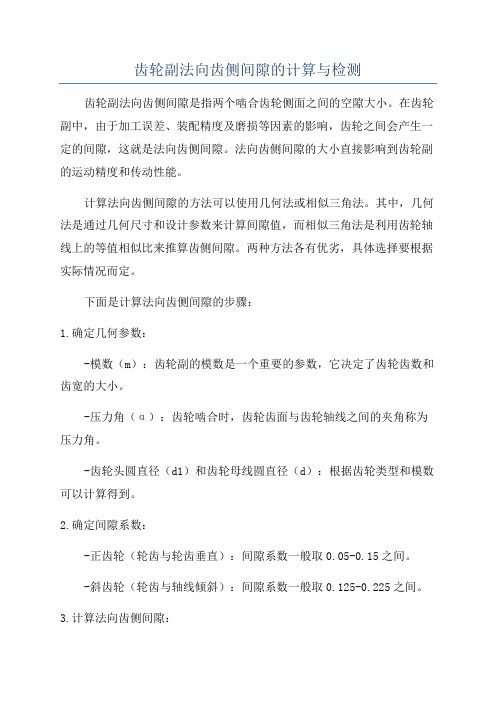
齿轮副法向齿侧间隙的计算与检测齿轮副法向齿侧间隙是指两个啮合齿轮侧面之间的空隙大小。
在齿轮副中,由于加工误差、装配精度及磨损等因素的影响,齿轮之间会产生一定的间隙,这就是法向齿侧间隙。
法向齿侧间隙的大小直接影响到齿轮副的运动精度和传动性能。
计算法向齿侧间隙的方法可以使用几何法或相似三角法。
其中,几何法是通过几何尺寸和设计参数来计算间隙值,而相似三角法是利用齿轮轴线上的等值相似比来推算齿侧间隙。
两种方法各有优劣,具体选择要根据实际情况而定。
下面是计算法向齿侧间隙的步骤:1.确定几何参数:-模数(m):齿轮副的模数是一个重要的参数,它决定了齿轮齿数和齿宽的大小。
-压力角(α):齿轮啮合时,齿轮齿面与齿轮轴线之间的夹角称为压力角。
-齿轮头圆直径(d1)和齿轮母线圆直径(d):根据齿轮类型和模数可以计算得到。
2.确定间隙系数:-正齿轮(轮齿与轮齿垂直):间隙系数一般取0.05-0.15之间。
-斜齿轮(轮齿与轴线倾斜):间隙系数一般取0.125-0.225之间。
3.计算法向齿侧间隙:-正齿轮:间隙值=(0.167-0.33*W)*m- 斜齿轮:间隙值 = (0.167 - 0.33 * W * sin(α)) * m其中,W为间隙系数。
在实际应用中,还需要通过检测方法来验证计算的间隙值是否符合要求。
常用的检测方法包括以下几种:1.游标测量法:-使用游标卡尺等工具对齿轮侧面进行测量,测量方法可以采用直接测量或间接测量两种方式。
-需要注意测量时的测量位置和角度,以及测量时使用的测量工具的精度。
2.哥仑卡片法:-将哥仑卡片插入齿轮侧面与齿轮轴线的交接处,通过空隙的大小来判断间隙的大小。
-需要根据实际情况选择合适的哥仑卡片厚度。
3.摆线尺测量法:-利用摆线尺的刃尖与齿轮侧面接触,通过尺尖的移动距离来测量间隙的大小。
-需要保证摆线尺的刃尖与齿轮侧面的接触稳定,并注意测量时的摆线尺的刻度精度。
4.视觉检测法:-利用光学仪器或高精度显微镜等观察齿轮侧面,通过目测或图像处理等方法来判断间隙的大小。
齿轮传动中的齿轮副侧隙调整

齿轮传动中的齿轮副侧隙调整摘要:齿轮转动时,为了保证齿轮安全稳定的生产工作模式,常常需要考虑齿轮副的侧隙大小,来保障齿轮副工作的稳定性,也有一些精度要求过高的齿轮转动机构中需要消除侧隙,避免其造成的往复运动而带来的精度缺失。
本文系统分析常见的的几种影响齿轮副侧隙的因素和计算方法,在传统的基础上给出了几种利用结构设计来调整侧隙的方法,从而可以减少生产成本。
关键词:齿轮传动;侧隙;调整1齿轮副侧隙概述1.1 齿轮误差来源齿轮误差的主要来源来自于:传动时造成的齿轮间误差、安装时产生的系统误差、设计图纸和施工之间的误差、加工精度缺失而产生的误差、受温度影响造成的系统误差等。
其中,传动时产生的误差成为转动误差,常见于多轮工作时,与轴承、齿轮之间的的传动链在输出转角和理论转角不一致造成的误差,记为Δφ。
传动链中,齿轮加工中的零部件和安装都会造成齿轮加工误差,不同齿轮的粗糙度、孔轴间隙值、滚动轴承与机架配合的公差带及轴承动环的偏心值,都是单个齿轮中的切向综合误差ΔFi及装置误差所产生误差集合。
这些误差都将通过传动链传递到齿轮,在执行部件中显现出对应的参数值,可以对照理论值,产生的偏差即为误差大小。
1.2 齿轮副侧隙定义及作用齿轮副侧隙是指在一对齿轮啮合时,非工作齿面间的间隙。
在齿轮传动时,会产生摩擦作用而产生发热碰撞现象,在受力下也会造成齿轮表面变形,如果采取合适的间隙就会补偿其所产生的空隙,降低制造误差,起到齿廓润滑的作用。
通常情况下,可以通过制造公差来保证齿轮副侧隙大小。
而在一些精度要求过高的齿轮转动中,常见一些伺服系统,会出现因齿侧间隙造成的传动死区现象,造成闭环系统工作,这会造成齿轮系统工作的不稳定性,因此,在这种精度高的伺服系统中通常要采取较低的齿侧隙值、精度较高的齿轮副传动,以便提升传动精度,增强系统的稳定性。
工作齿轮齿面要求有润滑油膜,非工作齿面需要增加补偿升温和受力变形的影响,而渐开线圆柱齿轮副在正常传动中,齿轮副必须始终呈单齿面啮合工作状态。
齿轮、齿轮副误差及侧隙的代号和定义 (GB11365-89)
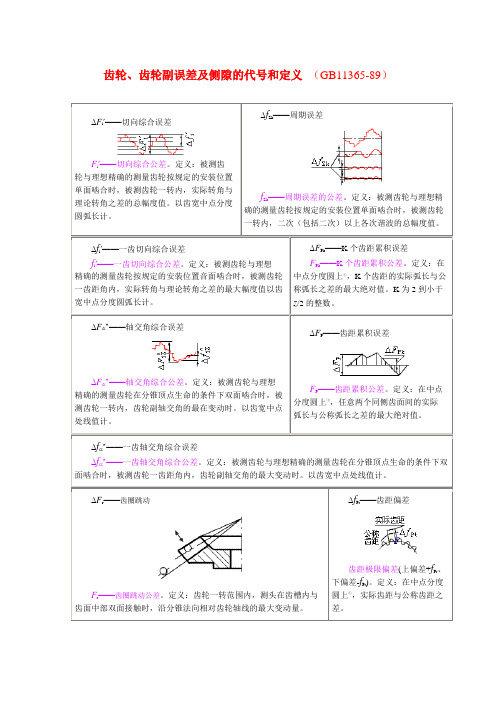
齿轮、齿轮副误差及侧隙的代号和定义(GB11365-89)
之比的百分数即
注:①允许在齿面中部测量。
②齿轮副转动整周期按下式计算:n2=z1/x
式中:n2——大轮转数,z1——小轮齿数,x——大、小轮齿数的最大公约数。
什么是齿轮副的侧隙
指的就是两个齿轮在啮合状态下一个齿轮(一)一个齿(1)和另一个齿轮(二)的一个齿(2)的齿面接触时,这个齿(一中的1号)的另一个齿面和另一个齿轮(二)的和这个齿(一中的1号)相啮合的齿(二中的2号)相邻的齿在分度圆上的间隙,一中的1号齿在二中的两个齿中间,在理论上齿轮副分析中这个侧隙为零,但实际中齿轮运行中会齿型会变大(温度上升)。
要是在常温没侧隙就会咬死,而且为了在齿轮的侧隙上留下空间储油。
在齿型变到最大时也要留有空间给储油。
所以都会有侧隙。
有侧隙也有缺点就是当齿轮副转换转向时会带来回程误差和冲击。
但不同场合的齿轮副的侧隙要求不同,像仪表为了减小回程误差就要小侧隙,而经常转换转向的地方防止冲击过大也要小侧隙。
太小的侧隙容易咬死而且因为储油问题而润滑不良。
而其他地方的侧隙可以大一些,但侧隙太大的问题也不用多
说,肯定不行的。
会有不同的用场会有一些合理的推荐值。
具体数据查询手册。
在装配中多用铅丝法测量侧隙,用一个粗细合适的铅丝让在啮合的两个齿在啮合过程中夹一下,然后测量铅丝变形后的厚度来测量侧隙。
齿轮副侧隙计算方法

润滑方式 油池润滑
喷油润滑
齿 轮 线 速 度%&&+:"
1#"% "%#1#(* (*#1#.%
1$.%
/-8%#& #*""%$0-
"%0(%0’%0#’%"*%$0-
注’0- 为法向模数
#($/-9是考虑齿轮传 动 的 温 度 变 化! 这 时 由 于 齿 轮 和箱体的材料不同!温度不同以及材料的线膨胀系数不 同!而使原侧隙/-8发 生 减 小 #或 增 大$! 所 以! 除 前 述 /-8外! 还需加上/-9的补偿" 所以
;%!$"&&! "理论值# 最 大 法 向 侧 隙/-&8F;/E&8F<=+!;%!.$6<=+(%1&&
;%!.%&&! "理论值# 若考虑加工及安装产生的基节$轴向$轴线平行度 和中心距偏差%则有! 最小法向侧隙/-&,-;%!$":%38% (+,-!-:4
;%!’$" "&&# 最大法向侧隙/-&8F;%!.%7%38% (+,-!-74
%!%"#
3B
% ! 基节极限偏差 3C9
?%!%(%
3C9
&!齿向公差 :’ 接触斑点 按齿高不小于
%!%(% *%D
:’ *%D
按齿长不小于 /%D
%!%"# ?%!%(% %!%(%
/%D
%!%$";%!’$* "&&# /-&8F; "%2+," 72+,( % #<=+"<=+!- 7 %38% (+,-!-
直齿圆柱齿轮变位系数、公法线长度、齿厚、最小法向侧隙的计算

外啮合直齿圆柱齿轮变位系数、公法线长度、齿厚、最小法向侧隙的计算1,直齿圆柱齿轮变位系数计算:Case1:a,此处例子仅计算用齿条型刀具加工时的情况(插齿刀加工见相关手册公式):小结:由此可知本例选取的齿数在不变位的情况也不会产生根切现象。
b,根据下图选择大小齿轮的变位系数和x∑。
本例在P6-P7区间取值。
即齿根及齿面承载能力较高区,进行选择。
因大小齿轮的齿数和为18+19=37。
所以本例选择的变位系数和x∑=0.8。
本例我们的两个齿轮在工作时属于减速运动,所以按减速运动的变位系数分配线图,进行2个齿轮的变位系数的选择。
先按(z1+z1)/2=18.5,作为横坐标,做一条垂线(图中蓝色的线),再按x∑/2=0.4,作为纵坐标,做一条水平线(图中橙色的线),接着沿着L线的趋势,穿过上面2条线的交点做一条射线(图中红色的线)最后按大小齿轮的齿数做相应的垂线(图中紫色的线),即得到需要的各自变位系数。
最后我们选择的变位系数即为:小齿轮x1=0.42,大齿轮x2=0.38。
【基本保障其和与之前x ∑一致,即可】。
c,验算变位后的齿顶厚度:注:一般要求齿顶厚Sa≥0.25m;对于表面淬火的齿轮要求Sa≥0.4m下表中的da的计算见后面的计算表格中的计算公式(因为当齿轮变位后,齿顶圆的计算和未变位齿轮的计算稍有差别-涉及到变位系数和中心距变位系数。
)。
分度圆直径db mm 73.8 77.9齿轮的齿顶圆直径da mm 83.027 86.799齿轮的齿顶压力角αa °27.27 26.17中间值invα0.0215 0.0215中间值invαa 0.0587 0.0347齿顶厚Sα 5.77 7.47判断值0.25m 1.025 1.025判断值0.4m 1.64 1.64小结:计算发现变位后的齿轮齿顶厚满足设计需求。
根据上面确定的变位系数,计算齿轮的中心距变位系数和节圆直径、齿根圆直径、齿顶圆直径。
第三章第齿轮副中心距极限偏差和轴线平行度公差节齿轮精度指标的公差及其精度等级

团结 信赖 创造 挑战
§7 齿轮侧隙指标的公差和齿轮坯公差 2.齿厚上偏差的确定
齿厚上偏差(齿厚最小减薄量)作用: 保证齿轮副所需的最小法向侧隙jbn min;补偿齿轮和齿轮箱的
制造误差和安装误差所引起的侧隙减小量Jbn; 制造误差影响因素:基圆齿距偏差△fpb和螺旋线总偏差△Fβ; 安装误差影响因素:△f∑δ和△f∑β;
由齿厚上偏差和齿厚公差根据下式求得
其中
Esni Esns Tsn
Tsn2tan n br2F r2
其中,br推荐值见表10-8,Fr可从表10-3查取
团结 信赖 创造 挑战
§7 齿轮侧隙指标的公差和齿轮坯公差
二. 公法线长度极限偏差的确定 公法线的上、下偏差分别由齿厚的上、下偏差换算得到。
外齿轮公法线长度上、下偏差换算公式为:
一、齿厚极限偏差的确定
侧隙的获得: (1). 改变齿轮副中心距; (2). 切薄轮齿。 齿厚上下偏差的获得: 上偏差:根据齿轮副所需的最小侧隙通过计算或类比法确定 。 下偏差:由齿轮等级、径向进刀公差、几何偏心确定。 齿轮精度等级和齿厚极限偏差确定后,齿轮副的最大侧隙就
团结 信赖 创造 挑战
§7 齿轮侧隙指标的公差和齿轮坯公差
团结 信赖 创造 挑战
§7 齿轮侧隙指标的公差和齿轮坯公差
其中
J b n ( f p t 1 2 f p t 2 2 ) c o s 2 n F 1 2 F 2 2 ( f s i n n ) 2 ( f c o s n ) 2
可以简化计算为
J b n1 .7 6 fp t2 2 0 .3 4 ( L /b ) 2 F 2
团结 信赖 创造 挑战
§6 齿轮副中心距极限偏差和轴线平行度公差
第五节 渐开线圆柱齿轮的啮合计算
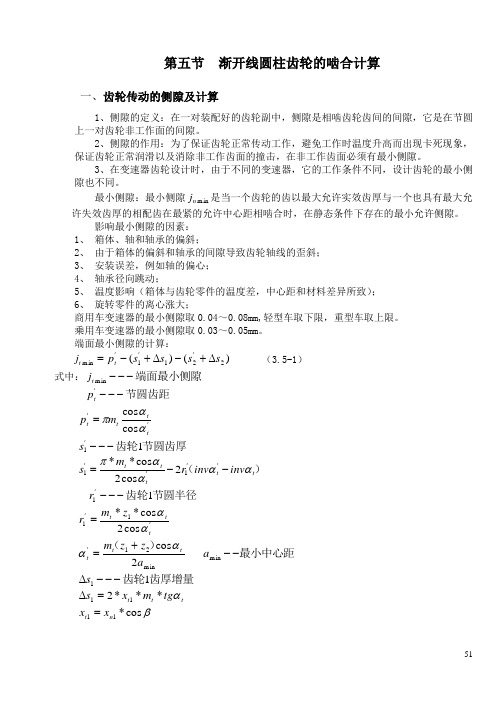
第五节 渐开线圆柱齿轮的啮合计算一、齿轮传动的侧隙及计算1、侧隙的定义:在一对装配好的齿轮副中,侧隙是相啮齿轮齿间的间隙,它是在节圆上一对齿轮非工作面的间隙。
2、侧隙的作用:为了保证齿轮正常传动工作,避免工作时温度升高而出现卡死现象,保证齿轮正常润滑以及消除非工作齿面的撞击,在非工作齿面必须有最小侧隙。
3、在变速器齿轮设计时,由于不同的变速器,它的工作条件不同,设计齿轮的最小侧隙也不同。
最小侧隙:最小侧隙min n j 是当一个齿轮的齿以最大允许实效齿厚与一个也具有最大允许失效齿厚的相配齿在最紧的允许中心距相啮合时,在静态条件下存在的最小允许侧隙。
影响最小侧隙的因素: 1、 箱体、轴和轴承的偏斜;2、 由于箱体的偏斜和轴承的间隙导致齿轮轴线的歪斜;3、 安装误差,例如轴的偏心;4、 轴承径向跳动;5、 温度影响(箱体与齿轮零件的温度差,中心距和材料差异所致);6、 旋转零件的离心涨大;商用车变速器的最小侧隙取0.04~0.08mm,轻型车取下限,重型车取上限。
乘用车变速器的最小侧隙取0.03~0.05mm 。
端面最小侧隙的计算:)()(2211min s s s s p j t t ∆+-∆+-=''' (3.5-1) 式中:端面最小侧隙---min t j节圆齿距---'t p''=tttt m p ααπcos cos 节圆齿厚齿轮11---'s)(t t tt t inv inv r m s ααααπ--=''''112cos 2cos ** 节圆半径齿轮11---'r''=t tt z m r ααcos 2cos **11min212cos a z z m tt t αα)(+=' 最小中心距--min a 齿厚增量齿轮11---∆s t t t tg m x s α***211=∆ βcos *11n t x x =nn n t m n tg z z z m dp inv inv x αααα221cos 11111)(+--=)奇数齿(或)偶数齿(!!111111190cos *cos cos cos cos z M z m M z m MAx t t m MAxtt m αααα--==式中:(奇数齿)或(偶数齿)dp z z M M dp z M M m tt MAX m tt MAX +⎪⎪⎭⎫ ⎝⎛=+=111111190cos cos cos **cos cos **αααα节圆齿厚齿轮22---'s)(t t tt t inv inv r m s ααααπ--=''''222cos 2cos ** 节圆半径齿轮22---'r''=ttt z m r ααcos 2cos **22 齿厚增量齿轮22---∆s t t t tg m x s α***222=∆ βcos *22n t x x = nn n t m ntg z z z m dp inv inv x αααα221cos 22222)(+--=)奇数齿(或)偶数齿(22212121290cos *cos cos cos cos z M z m M z m MAx tt m MAxtt m αααα--==(奇数齿)或(偶数齿)dp z z M M dp z M M m tt MAXm tt MAX +⎪⎪⎭⎫ ⎝⎛=+=222222290cos cos cos **cos cos **αααα法向最小侧隙的计算:‘''⨯⨯=t t n j j αβcos cos min min'β--节圆螺旋角''⨯=tttg tg ααββcos cos 最大侧隙的计算:将式(3.5-1)中的min a 替换成MAX a ,将MAX M 替换成MIN M 即可计算出最大侧隙。
齿轮副最大与最小侧隙的计算

齿轮副最大与最小侧隙的计算齿轮副的侧隙是指齿轮副两齿轮齿廓间的间隙,它是齿轮副正常运转时所必需的重要参数之一、侧隙的大小直接影响齿轮副的传动效率、传动精度、噪音和寿命等性能。
因此,在设计和制造齿轮副时,必须合理计算齿轮副的最大和最小侧隙。
齿轮副的侧隙可分为两种情况进行计算,即直齿轮副和斜齿轮副。
一、直齿轮副的最大和最小侧隙计算方法:直齿轮副的最大和最小侧隙是通过计算法向侧隙和径向侧隙来确定的。
1.法向侧隙计算:法向侧隙是指齿轮两齿廓垂直于齿轮轴线方向的侧隙大小,一般用等效径向侧隙来表示。
法向侧隙等效于一个半径为r的圆上的弧长s,通过下式计算:s=π*r*ε/180其中,π为圆周率,ε为齿轮的法向侧隙角(单位为度),r为齿轮的基圆半径。
2.径向侧隙计算:径向侧隙是指齿轮两齿廓平行于齿轮轴线方向的侧隙大小,一般用法线模数mn与齿数z来计算。
径向侧隙等于模数mn与齿数z的乘积,通过下式计算:e=m*n其中,m为法线模数,n为齿数,e为齿轮的径向侧隙。
最大侧隙:最大侧隙为法向侧隙与径向侧隙之和。
最小侧隙:最小侧隙为法向侧隙减去径向侧隙。
二、斜齿轮副的最大和最小侧隙计算方法:斜齿轮副的最大和最小侧隙的计算方法与直齿轮副有所不同,需要考虑齿轮副的斜面系数。
1.法向侧隙计算:法向侧隙通过法向侧隙系数Kn乘以齿轮的法向分度圆压力角tanφ来计算。
法向侧隙等于法向侧隙系数Kn乘以齿轮的法向分度圆压力角tanφ,通过下式计算:s = Kn * tanφ其中,Kn为法向侧隙系数,tanφ为齿轮的法向分度圆压力角,s为齿轮的法向侧隙。
2.径向侧隙计算:径向侧隙的计算与直齿轮副相同,通过模数mn与齿数z的乘积计算。
径向侧隙等于模数mn与齿数z的乘积,通过下式计算:e=m*n其中,m为法线模数,n为齿数,e为齿轮的径向侧隙。
最大侧隙:最大侧隙为法向侧隙与径向侧隙之和。
最小侧隙:最小侧隙为法向侧隙减去径向侧隙。
需要注意的是,在实际的齿轮副设计和制造过程中,还需要考虑齿轮副的加工误差、装配误差以及工作环境等因素的影响,从而对最大和最小侧隙进行一定的修正。
齿轮传动中的齿轮副侧隙调整

齿轮传动中的齿轮副侧隙调整摘要:在近些年经济高速发展的进程中,数控锥齿轮研齿机,大齿轮与小齿轮进行双面啮合,在双齿侧对滚的过程中,将Z轴方向的综合跳动偏差测量出来,并且借助西门子数控系统中的固定停功能,使小齿轮与大齿轮之间进行间隙啮合作用,同时,将磨合期间的大轮安装方向的坐标值记录下来,经过精确地计算之后,得出最佳的研磨点侧隙值。
借此,为了能够进一步提高数控锥齿轮研齿机实现自动侧隙,本文就数控锥齿轮研齿机自动侧隙的控制方法进行研究和分析。
关键词:数控锥齿轮研齿机;自动;侧隙;控制方法引言数控锥齿轮研齿机实际上指的就是锥齿轮副啮合过程中的产生的滑动速度,在啮合期间加入研磨剂之后进行的齿轮副的齿面啮合,齿轮副的齿面啮合这种操作方式,主要也是为了能够进一步降低齿面的粗糙度,从而提高齿面接触质量,减少噪音,进一步增强齿轮副运行过程中的稳定性和运行的有效性。
一、数控锥齿轮研齿机自动侧隙概念认知啮合的过程并不是独立存在的,而是需要一些附加的运动,使两个齿轮之间发生位置上的移动,使得全部的齿面都能够被研磨到一起。
当数控锥齿轮研齿轮机需要对一对相互啮合的锥齿轮的接触面进行研磨时,不仅要对各个研磨点,即锥齿轮的齿高H、齿长V、侧隙J进行准确的定位,而且还要对该研磨点的齿高方向坐标值,以及研磨点齿长的方向坐标值进行有效的把控,同时,确定其侧隙值也是必要的,一旦齿高H和齿长V发生数据上的变动,那么,其侧隙J的值也会随之发生一定的改变。
另外,调齿轮副的侧隙指的就是齿轮副研磨面进行接触的过程中,与非研磨区域之间形成的最小距离,一旦研齿过程中的侧隙趋向最小,或者是侧隙不存在时,那么,轮齿的两个齿轮会同时进入齿轮的研磨运动,这种研齿运动不仅不符合机械运动原理,而且还会造成机械设备的损伤,产生极大的噪音。
反之,一旦研齿过程中的侧隙趋向最大,那么,齿顶在边缘区域就会产生影响。
所以,侧隙不仅可以起到保证研齿运动研磨剂充分的渗入,而且还能够达到最佳的研磨效果,因此,各个研磨区域研磨点侧隙值的有效把控是至关重要的。
齿轮副的精度指标和侧隙指标讲解

齿轮传动是通过齿轮副实现的,其误差 直接影响齿轮的使用要求。对齿轮副的检验, 是按设计中心距安装后进行的一种综合检验, 从满足齿轮使用要求出发,规定的齿轮副检 验参数有中心距极限偏差和轴线的平行度偏 差,接触斑点,侧隙等。
11.3.1齿轮副的精度 1.中心距极限偏差fa:
因为齿轮为机床主轴箱的传动齿轮,由表11-13 可大致得出齿轮精度在3-8级之间.而 V=πdn1/1000×60=(3.14×2.75×26×1650)/1000×60
=6.2m/s
参考表11-14确定该齿轮为7级精度,表示为
7GB/T100095.1-2001
2确定侧隙和齿厚偏差
中心距 a= m/2(Z1+Z2)=2.75/2(26+56)=112.75mm 由公式11-1得:
轴线平面:包含用两
轴承跨距中较长的一根轴 线和另一轴上的一个轴承 中心所形成的平面。
(2)轴线平行度偏差 f 和 f
轴线平面内的平行度偏差f是在两轴线的公
共平面上测量的,此公共平面是用两轴承跨距中
较长的一个L和另一根轴上的一个轴承来确定的。
如果两个轴承的跨距相同,则用小齿轮轴和大齿
轮轴的一个轴承确定。垂直平面上的平行度偏差
Fr=0.03mm
由11-3 和2-2表查: br=IT9=0.074mm Tsn =√Fr²+br²2tan αn = 0.058mm Esni = Esns-Tsn = - 0.071-0.058= - 0.129mm
f
是在与轴线公共平面相垂直的平面上测量的。
f 和 f的最大推荐值为:
式中,L为轴承跨距,b为齿宽。
(3)接触斑点
接触斑点是指装配好的齿轮副,在轻微的制
齿轮公法线上下偏差计算公式
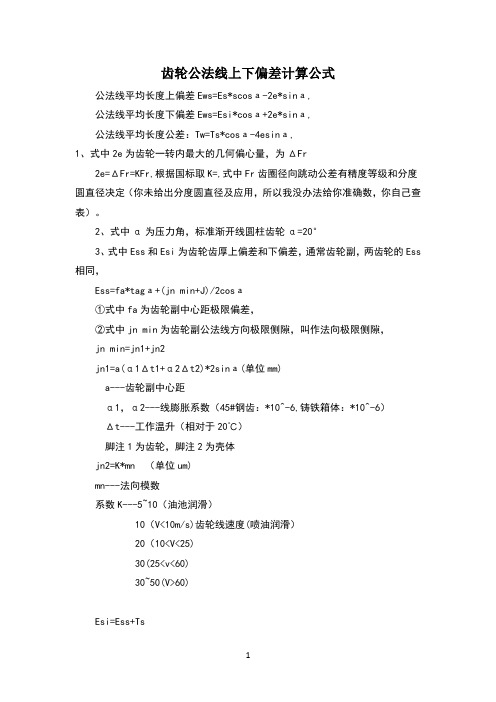
齿轮公法线上下偏差计算公式公法线平均长度上偏差Ews=Es*scosа-2e*sinа,公法线平均长度下偏差Ews=Esi*cosа+2e*sinа,公法线平均长度公差:Tw=Ts*cosа-4esinа,1、式中2e为齿轮一转内最大的几何偏心量,为ΔFr2e=ΔFr=KFr,根据国标取K=,式中Fr齿圈径向跳动公差有精度等级和分度圆直径决定(你未给出分度圆直径及应用,所以我没办法给你准确数,你自己查表)。
2、式中α为压力角,标准渐开线圆柱齿轮α=20°3、式中Ess和Esi为齿轮齿厚上偏差和下偏差,通常齿轮副,两齿轮的Ess 相同,Ess=fa*tagа+(jn min+J)/2cosа①式中fa为齿轮副中心距极限偏差,②式中jn min为齿轮副公法线方向极限侧隙,叫作法向极限侧隙,jn min=jn1+jn2jn1=a(α1Δt1+α2Δt2)*2sinа(单位mm)a---齿轮副中心距α1,α2---线膨胀系数(45#钢齿:*10^-6,铸铁箱体:*10^-6)Δt---工作温升(相对于20℃)脚注1为齿轮,脚注2为壳体jn2=K*mn (单位um)mn---法向模数系数K---5~10(油池润滑)10(V<10m/s)齿轮线速度(喷油润滑)20(10<V<25)30(25<v<60)30~50(V>60)Esi=Ess+TsTs=(Fr^2+br^2)^1/2*2tagαFr---齿圈径向跳动(查表)br---切齿径向进刀公差(查表)4、小结要得到公法线长度上下偏差必须根据应用环境来确定精度等级,有三组公差精度分别为:运动精度、平稳性精度、接触精度,示例一、7-6-6GM、示例二、7FL第一个示例表示运动精度7,平稳性精度和接触精度6,G和M代表齿厚上下偏差分别为-6fpt和-20fpt(买本书或下载齿轮手册上面有标准),fpt查表得,它属平稳性精度参数,第二个示例表示三组公差精度都为7,其他同上,只是齿厚公差带偏上一点了,F=-4fpt,L=-16fpt。
齿轮副法向齿侧间隙的计算与检测[整理版]
![齿轮副法向齿侧间隙的计算与检测[整理版]](https://img.taocdn.com/s3/m/e8e11239443610661ed9ad51f01dc281e53a568b.png)
齿轮副法向齿侧间隙的计算与测量一、齿轮副法向侧隙的计算为保证齿轮副始终呈单面啮合的正常运转。
其工作齿面之间需有油膜润滑,而非工作齿面之间则要考虑到温升变形的影响,故齿轮副的工作齿面间和非工作齿面间都应有一足够而不过大的最小侧隙。
前者用于储油,后者用于弥补热膨胀所需。
这两者最小法向值之和称为齿轮副的最小法向齿侧间隙(简称最小侧隙jnmin) 其最小值取决于齿轮副的工作速度,润滑方式和温升。
与齿轮副的精度等级无关。
关于齿轮副的侧隙.GB10095—88规定采用基齿厚制,即利用减薄相配齿轮齿厚的办法获得。
为获得jnmin齿厚应有一最小减薄量(Ess齿厚上偏差)又因齿轮副的加工和安装不可能没有误差,如:-fpb、-fn.、Fβ和fx、fy等。
所以齿厚的最小减薄量,除取决于jnmin外还应考虑以上诸多误差都会对侧隙值产生减小的影响。
1.1齿轮副的最小法向齿侧间隙jnmin的计算:1)温升变形所需的最小法向侧隙jnmin1:jnmin1=a(α1△t1-α2△t2)×2sinαn式中:a——齿轮中心距(mm);α1,α2——齿轮和箱体材料的线膨胀系数;αn——齿轮法向啮合角;△t1,△t2——齿轮和箱体工作温度与标准温度之差:△t1=t1-20℃;△t2=t2-20℃。
2)保证正常油膜润滑所需的最小法向侧隙jn2:保证正常油膜润滑所需的最小法向侧隙jn2,取决于齿轮副的润滑方式和工作速度.当油池润滑时,jn2=(5~10)Mn(μm)。
当喷油润滑时,对于低速传动(工作速度v <10m/s ),jn2=10Mn ;对于中速传动(v =10~24m/s ),jn2=30Mn ;对于高速传动(v >60m/s ),jn2=(30~50)Mn 。
Mn 为法向模数(mm )。
所以:齿轮副最小极限侧隙(jnmin )应为:jnmin =jn1+jn21.2齿轮副实际的最小法向侧隙(安装后的侧隙)的计算Jnmin ′=|EssA+EssB|cos αn+(-fa )2sin αn-jn式中:EssA 和EssB ——AB 齿轮的齿厚上偏差;jn ——齿轮加工误差和齿轮副的安装无误差(fx ,fy )对侧隙的影响的最小量2f a ·sin αn —当齿轮副A/B 的中心距处于下偏差(-fa )时,对侧隙影响的最小值其中jn=222n 22)cos ()sin (cos 2n y n x pbB pbA f f F f f ααβ⋅+⋅++)α(+ 当=n α20°,F β=fx=2fy 时222104.2βF f f J pbB pbA n ++=1.3齿轮副最大法向侧隙jnmax 的计算:当AB 齿轮的精度等级,齿厚公差和AB 齿轮副的中心局极限偏差都确定时,jnmax 也就自然形成,一般齿轮副对其要求不严,可以免算,只作为检测的一个判定参考。
计算齿轮侧隙范文

计算齿轮侧隙范文齿轮侧隙是指两个相互啮合的齿轮的齿槽之间的距离。
齿轮侧隙的大小对齿轮的传动精度和使用寿命有着重要的影响。
本文将介绍齿轮侧隙的计算方法以及其在实际应用中的重要性。
一、齿轮侧隙的计算方法齿轮侧隙的计算方法通常有以下几种:1.几何计算法:根据齿槽的几何形状参数来计算侧隙大小。
具体计算方法如下:-首先,计算出齿槽高度h,齿宽b和齿槽角度α等几何参数;-然后,根据几何关系,计算侧隙大小:侧隙大小= h / tan(α/2)2.弹性变形法:考虑到齿轮在工作过程中会发生弹性变形,弹性侧隙需要通过试验和实际测量来确定。
3.标准侧隙法:根据国家标准对齿轮侧隙进行规定,在设计和制造过程中直接按照标准来确定。
二、齿轮侧隙的重要性齿轮侧隙的大小对齿轮传动的精度和性能有着重要的影响,主要体现在以下几个方面:1.传动精度:齿轮侧隙会引起齿轮传动的回程误差,降低传动的精度。
过大的侧隙会导致剧烈的齿根载荷变化,从而影响传动的稳定性和精度。
2.噪声和振动:齿轮侧隙会引起啮合时的冲击和振动,产生噪声。
过大的侧隙会增加齿轮的冲击载荷,导致噪声和振动增加。
3.使用寿命:过大的齿轮侧隙会导致齿端载荷集中,加速齿面疲劳破坏的发生,从而降低齿轮的使用寿命。
三、齿轮侧隙的影响因素齿轮侧隙的大小受到多个因素的影响,主要包括以下几个方面:1.齿轮尺寸和材料:齿轮的几何尺寸和材料的选择会直接影响齿轮侧隙的大小。
一般来说,齿轮尺寸越大,侧隙越大;而齿轮材料的弹性模量越大,侧隙越小。
2.加工精度:齿轮的加工精度对齿轮侧隙有很大影响。
加工精度低会导致齿槽尺寸不准确,从而影响侧隙的准确计算。
3.齿轮啮合方式:齿轮的啮合方式也会对侧隙产生一定的影响。
相对于直齿齿轮,斜齿轮和蜗杆齿轮等特殊形式的齿轮传动通常需要更小的侧隙。
四、总结齿轮侧隙的计算方法涉及到几何计算法、弹性变形法和标准侧隙法等。
齿轮侧隙的大小对齿轮的传动精度、噪声和振动以及使用寿命有着重要的影响。
齿轮传动中的齿轮副侧隙调整研究
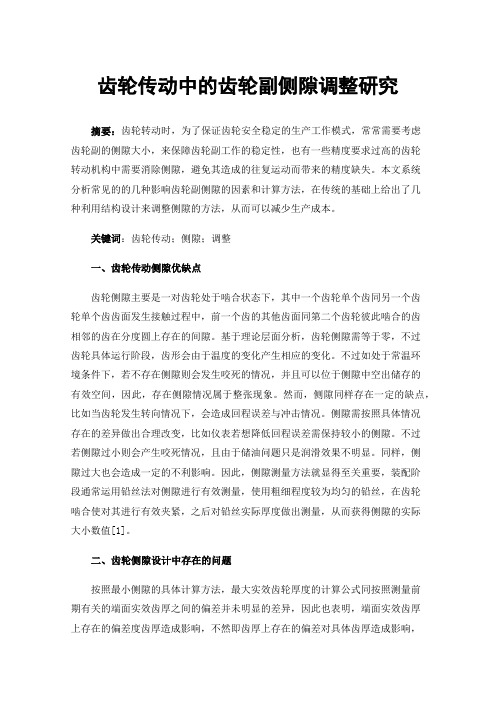
齿轮传动中的齿轮副侧隙调整研究摘要:齿轮转动时,为了保证齿轮安全稳定的生产工作模式,常常需要考虑齿轮副的侧隙大小,来保障齿轮副工作的稳定性,也有一些精度要求过高的齿轮转动机构中需要消除侧隙,避免其造成的往复运动而带来的精度缺失。
本文系统分析常见的的几种影响齿轮副侧隙的因素和计算方法,在传统的基础上给出了几种利用结构设计来调整侧隙的方法,从而可以减少生产成本。
关键词:齿轮传动;侧隙;调整一、齿轮传动侧隙优缺点齿轮侧隙主要是一对齿轮处于啮合状态下,其中一个齿轮单个齿同另一个齿轮单个齿齿面发生接触过程中,前一个齿的其他齿面同第二个齿轮彼此啮合的齿相邻的齿在分度圆上存在的间隙。
基于理论层面分析,齿轮侧隙需等于零,不过齿轮具体运行阶段,齿形会由于温度的变化产生相应的变化。
不过如处于常温环境条件下,若不存在侧隙则会发生咬死的情况,并且可以位于侧隙中空出储存的有效空间,因此,存在侧隙情况属于整张现象。
然而,侧隙同样存在一定的缺点,比如当齿轮发生转向情况下,会造成回程误差与冲击情况。
侧隙需按照具体情况存在的差异做出合理改变,比如仪表若想降低回程误差需保持较小的侧隙。
不过若侧隙过小则会产生咬死情况,且由于储油问题只是润滑效果不明显。
同样,侧隙过大也会造成一定的不利影响。
因此,侧隙测量方法就显得至关重要,装配阶段通常运用铅丝法对侧隙进行有效测量,使用粗细程度较为均匀的铅丝,在齿轮啮合使对其进行有效夹紧,之后对铅丝实际厚度做出测量,从而获得侧隙的实际大小数值[1]。
二、齿轮侧隙设计中存在的问题按照最小侧隙的具体计算方法,最大实效齿轮厚度的计算公式同按照测量前期有关的端面实效齿厚之间的偏差并未明显的差异,因此也表明,端面实效齿厚上存在的偏差度齿厚造成影响,不然即齿厚上存在的偏差对具体齿厚造成影响,不过实际恶言,以上情况均无法作为对齿厚是否满足标准进行分析判断的理论基础依据,因此,对齿厚是否满足标准进行分析判断的主要因素为最大检测半径。
如何计算齿轮副的侧隙
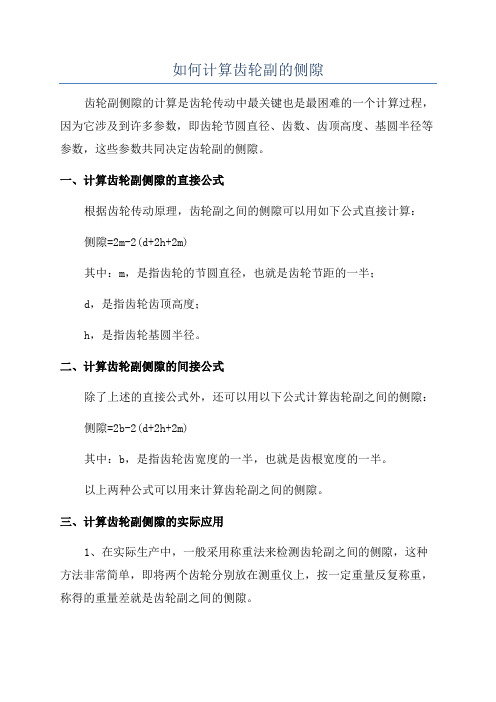
如何计算齿轮副的侧隙
齿轮副侧隙的计算是齿轮传动中最关键也是最困难的一个计算过程,因为它涉及到许多参数,即齿轮节圆直径、齿数、齿顶高度、基圆半径等参数,这些参数共同决定齿轮副的侧隙。
一、计算齿轮副侧隙的直接公式
根据齿轮传动原理,齿轮副之间的侧隙可以用如下公式直接计算:侧隙=2m-2(d+2h+2m)
其中:m,是指齿轮的节圆直径,也就是齿轮节距的一半;
d,是指齿轮齿顶高度;
h,是指齿轮基圆半径。
二、计算齿轮副侧隙的间接公式
除了上述的直接公式外,还可以用以下公式计算齿轮副之间的侧隙:侧隙=2b-2(d+2h+2m)
其中:b,是指齿轮齿宽度的一半,也就是齿根宽度的一半。
以上两种公式可以用来计算齿轮副之间的侧隙。
三、计算齿轮副侧隙的实际应用
1、在实际生产中,一般采用称重法来检测齿轮副之间的侧隙,这种方法非常简单,即将两个齿轮分别放在测重仪上,按一定重量反复称重,称得的重量差就是齿轮副之间的侧隙。
2、根据等分原理,也可以采用边数累加法来检测齿轮副之间的侧隙,即齿轮上的每一节沿全节线进行沿均等划分,并将每一节的划分点按顺序
依次加以累加,最后累加得出的总值。
齿轮副侧隙的确定

齿轮副侧隙的确定佟金玉;徐坤【摘要】目前齿轮副侧隙的计算仍使用材料平均热膨胀系数的方法,造成较大误差.本文根据计算所得齿厚偏差来确定侧隙的最大值及最小值.齿轮副侧隙的大小与齿轮齿厚减薄量有着密切的关系,齿厚上偏差,即齿厚的最小减薄量可以根据齿轮副所需要的最小侧隙通过计算确定,齿厚下偏差则按齿轮精度等级和加工齿轮时的径向进刀公差和几何偏差确定.齿轮精度等级和齿厚极限偏差确定后.齿轮副的最大侧隙就自然形成.%The calculation of gear backlash is still adopting the material average coefficient of thermal expansion means, resulting in large errors.Confirming the maximum and minimum value according to tooth thickness deviation is obtained by calculating.The size of gear backlash is closely related to gear tooth thickness and thinning, tooth thickness upper bias, that is, minimum thinning can be confirmed by minimum required gear backlash, tooth thickness lower deviation is confirmed by and geometry based on accuracy grade and processing gear radial feed tolerance and deviation.And after tooth thickness of gear accuracy and class limit of deviation are determined, the maximum gear backlash is formed naturally.【期刊名称】《价值工程》【年(卷),期】2011(030)006【总页数】1页(P11-11)【关键词】侧隙;齿厚偏差;齿厚的最小减薄量【作者】佟金玉;徐坤【作者单位】安徽山河矿业装备有限公司,淮北,235000;安徽山河矿业装备有限公司,淮北,235000【正文语种】中文【中图分类】TH13齿轮副的侧隙要求,应根据工作条件用最大极限侧隙jbnmax与最小极限侧隙jbnmax来规定。
- 1、下载文档前请自行甄别文档内容的完整性,平台不提供额外的编辑、内容补充、找答案等附加服务。
- 2、"仅部分预览"的文档,不可在线预览部分如存在完整性等问题,可反馈申请退款(可完整预览的文档不适用该条件!)。
- 3、如文档侵犯您的权益,请联系客服反馈,我们会尽快为您处理(人工客服工作时间:9:00-18:30)。
Ts1、Ts2—分别为小齿轮、大齿轮的齿厚公差(μm);
Ta—齿轮副的中心距公差(μm);
αn’—齿轮压力角(0)。
≤10
>10-25
>25-60
>60
喷油润滑
10
20
30
30-50
油池润滑
5-10
2.齿轮副最大法向侧隙值的计算
计算齿轮副的最大法向侧隙时,主要考虑齿轮的加工精度。其计算公式如下
Jnmax=Jmin+【(Ts12+Ts22)Xcos2αn+(TaX2Xsinαn)】(1/2)
式中 Jnmax—最大法向侧隙(μm);
式中Jnmin—最小法向侧隙(μm);
a—齿轮副中心距(μm);
α1
△t1、△t2—分别为齿轮、箱体温度与标准温度(200C)之差(0C);
αn’—齿轮副法向啮合角(0);
δ—润滑状况系数(检附表);
mn—齿轮模数。
δ表值
润滑方式
齿轮节圆圆周速度v(m/s)
齿轮副侧隙探讨
一、由最小侧隙推导大小齿轮齿厚上偏差:
二、齿轮副最大侧隙计算
齿轮副最小和最大法向侧隙值计算
2010-04-28 12:16
1.齿轮副最小法向侧隙值的计算
计算齿轮副的最小法向侧隙时,主要考虑齿轮副的热变形和润滑状况的工作条件。其计算公式如下:
Jnmin=2a·(α1△t1-α2△t2)sinαn’+δmn