齿轮副最小侧隙和最大侧隙计算表
1圆柱齿轮精度(GB10095-88)
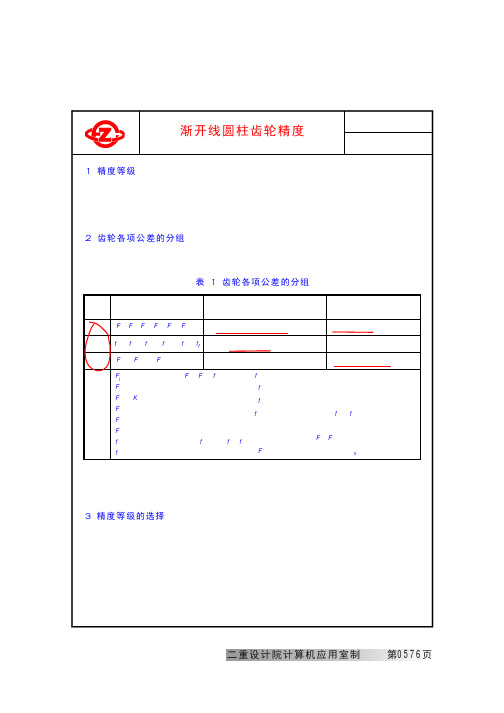
注:主传动齿轮或重要的传动,偏上限选择;辅助传动或一般传动,居中或偏下限选择。
表2各类机器所用齿轮传动的精度等级范围机器类别机器类别精度等级精度等级汽轮机金属切削机床航空发动机轻型汽车载重汽车3 ̄63 ̄84 ̄85 ̄87 ̄9拖拉机通用减速器锻压机床起重机农业机械6 ̄86 ̄86 ̄97 ̄108 ̄11表3常用精度等级齿轮的加工方法及应用范围精度等级5级(精密级)6级(高精度级)7级(比较高的精度级)8级(中等精度级)9级10级(低精度级)加工方法齿面最终精加工齿面粗糙度Ra/μm应用范围效率(%)③在周期性误差非常小的精密齿轮机床上展成加工精密磨齿。
大型齿轮用精密滚齿滚切后,再研磨或剃齿0.8在高精度的齿轮机床上展成加工精密磨齿或剃齿在高精度的齿轮机床上展成加工不淬火的齿轮推荐用高精度的刀具切制。
淬火的齿轮需要精加工(磨齿、剃齿、研磨、珩齿)精密的分度机构用齿轮;用于高速、并对运转平稳性和噪声有比较高的要求的齿轮;高速汽轮机用齿轮;8级或9级齿轮的标准齿轮①①用于在高速下平稳地回转,并要求有最高的效率和低噪声的齿轮;分度机构用齿轮;高速减速器的齿轮;飞机、汽车和机床中的重要齿轮②①用于高速、载荷小或反转的齿轮;机床的进给齿轮;需要运动有配合的齿轮;中速减速器的齿轮;飞机、汽车制造中的齿轮②①对精度没有特别要求的一般机械用齿轮;机床齿轮(分度机构除外);特别不重要的飞机、汽车拖拉机齿轮;起重机、农业机械、普通减速器用齿轮、用于对精度要求不高,并且在低速下工作的齿轮99(98.5)以上99(98.5)以上98(97.5)以上97(96.5)以上96(95)以上用展成法或仿型法加工用任意的方法加工不磨齿。
必要时剃齿或研磨不需要精加工12.5253.2 ̄6.31.600.8注:本表不属国家标准,仅供参考。
①Ⅱ组精度可以降低1级;②Ⅰ组精度可以降低1级;③括号内的效率是包括轴承损失的数值。
表4齿轮圆周速度与最低精度(Ⅱ组)的关系直齿斜齿(平行轴)最低精度Ⅱ组等级()ν≥1515>ν≥1010>ν≥66>ν≥22>ν≥3030>ν≥1515>ν≥1010>ν≥44>ν56789圆周速度ν/(m/s)注:本表不属国家标准,仅供参考。
齿轮副最大与最小侧隙的计算

Ts1、Ts2—分别为小齿轮、大齿轮的齿厚公差(μm);
Ta—齿轮副的中心距公差(μm);
αn’—齿轮压力角(0)。
≤10
>10-25
>25-60
>60
喷油润滑
10
20
30
30-50
油池润滑
5-10
2.齿轮副最大法向侧隙值的计算
计算齿轮副的最大法向侧隙时,主要考虑齿轮的加工精度。其计算公式如下
Jnmax=Jmin+【(Ts12+Ts22)Xcos2αn+(TaX2Xsinαn)】(1/2)
式中 Jnmax—最大法向侧隙(μm);
式中Jnmin—最小法向侧隙(μm);
a—齿轮副中心距(μm);
α1
△t1、△t2—分别为齿轮、箱体温度与标准温度(200C)之差(0C);
αn’—齿轮副法向啮合角(0);
δ—润滑状况系数(检附表);
mn—齿轮模数。
δ表值
润滑方式
齿轮节圆圆周速度v(m/s)
齿轮副侧隙探讨
一、由最小侧隙推导大小齿轮齿厚上偏差:
二、齿轮副最大侧隙计算
齿轮副最小和最大法向侧隙值计算
2010-04-28 12:16
1.齿轮副最小法向侧隙值的计算
计算齿轮副的最小法向侧隙时,主要考虑齿轮副的热变形和润滑状况的工作条件。其计算公式如下:
Jnmin=2a·(α1△t1-α2△t2)sinαn’+δmn
锥齿轮副啮合侧隙的控制
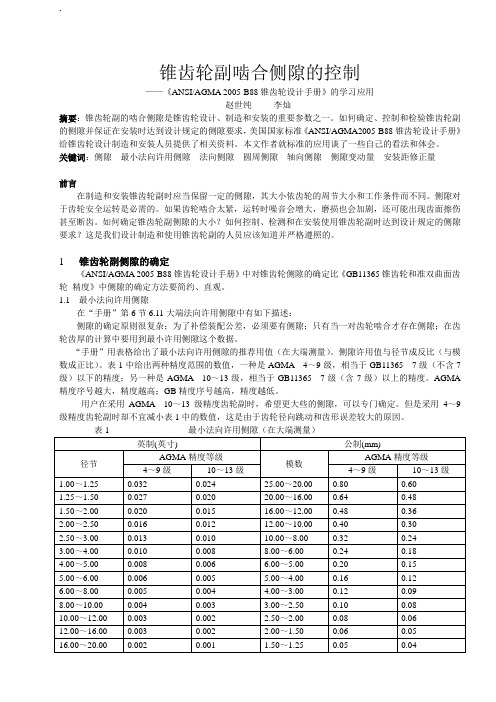
锥齿轮副啮合侧隙的控制——《ANSI/AGMA 2005-B88锥齿轮设计手册》的学习应用赵世纯李灿摘要:锥齿轮副的啮合侧隙是锥齿轮设计、制造和安装的重要参数之一。
如何确定、控制和检验锥齿轮副的侧隙并保证在安装时达到设计规定的侧隙要求,美国国家标准《ANSI/AGMA2005-B88锥齿轮设计手册》给锥齿轮设计制造和安装人员提供了相关资料。
本文作者就标准的应用谈了一些自己的看法和体会。
关键词:侧隙最小法向许用侧隙法向侧隙圆周侧隙轴向侧隙侧隙变动量安装距修正量前言在制造和安装锥齿轮副时应当保留一定的侧隙,其大小依齿轮的周节大小和工作条件而不同。
侧隙对于齿轮安全运转是必需的。
如果齿轮啮合太紧,运转时噪音会增大,磨损也会加剧,还可能出现齿面擦伤甚至断齿。
如何确定锥齿轮副侧隙的大小?如何控制、检测和在安装使用锥齿轮副时达到设计规定的侧隙要求?这是我们设计制造和使用锥齿轮副的人员应该知道并严格遵照的。
1 锥齿轮副侧隙的确定《ANSI/AGMA 2005-B88锥齿轮设计手册》中对锥齿轮侧隙的确定比《GB11365锥齿轮和准双曲面齿轮精度》中侧隙的确定方法要简约、直观。
1.1 最小法向许用侧隙在“手册”第6节6.11大端法向许用侧隙中有如下描述:侧隙的确定原则很复杂;为了补偿装配公差,必须要有侧隙;只有当一对齿轮啮合才存在侧隙;在齿轮齿厚的计算中要用到最小许用侧隙这个数据。
“手册”用表格给出了最小法向许用侧隙的推荐用值(在大端测量)。
侧隙许用值与径节成反比(与模数成正比)。
表1中给出两种精度范围的数值,一种是AGMA 4~9级,相当于GB11365 7级(不含7级)以下的精度;另一种是AGMA 10~13级,相当于GB11365 7级(含7级)以上的精度。
AGMA 精度序号越大,精度越高;GB精度序号越高,精度越低。
用户在采用AGMA 10~13级精度齿轮副时,希望更大些的侧隙,可以专门确定。
但是采用4~9级精度齿轮副时却不宜减小表1中的数值,这是由于齿轮径向跳动和齿形误差较大的原因。
齿轮传动参数表
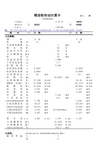
锥齿轮传动计算卡编号:16(弧齿锥齿轮)产品型号:订货号:10026零件件号:①30201②30202计算人 :计算日期:注:“度.分秒”标注示例 — 56.0638 表示56度6分38秒;35.596 表示35度59分60秒(即36度)。
项目①小轮②大轮几何参数:旋 向右 旋左 旋齿数Z1529大端端面模数m4毫米轴交角Σ90度法向压力角αn20度中 点 螺 旋 角βm35度齿宽b20毫米全齿高系数x t 1.888工作齿高系数x w 1.7顶隙 系 数c0.188高度变位系数x0.2857-0.2857切向变位系数x s0.0069-0.0069分度圆直径d60毫米116毫米外锥距Ra65.2993毫米毫米分度圆锥角δ27.206度.分秒62.39度.分秒顶锥角(等顶隙)δa31.5908度.分秒65.1719度.分秒根锥角δf24.4241度.分秒58.0052度.分秒齿顶高h a 4.543毫米 2.257毫米齿根高h f 3.009毫米 5.295毫米全齿高h t7.552毫米毫米工作齿高h 6.8毫米毫米大端分度圆理论弧齿厚Sa7.358毫米 5.209毫米大端顶圆直径d a68.07毫米118.074毫米分锥顶点至轮冠距离A k55.913毫米27.995毫米大端法向弦齿厚S n 5.644毫米(单号单面切削法) 4.059毫米大端法向弦齿高H n 4.497毫米 2.224毫米重合度ε总 1.826ε纵向 1.334ε端面 1.247大 端 螺 旋 角βa37.2203度.分秒小 端 螺 旋 角βi33.4029度.分秒刀盘名义直径选定值Dc152.4毫米公差值:(按 GB11365--89 锥齿轮和准双曲面齿轮精度)精度等级Ⅰ:7Ⅱ:6Ⅲ:6最小法向侧隙种类c法向侧隙公差种类C图样标 注7-6-6c GB 11365--89齿厚上偏差Ess-0.048毫米-0.053毫米齿厚下偏差Esi-0.118毫米-0.123毫米齿厚公差Ts0.07毫米0.07毫米最小法向侧隙jn min0.074毫米最大法向侧隙jn max0.262毫米切向综合公差F'i0.042毫米0.051毫米一齿切向综合公差f'i0.013毫米0.013毫米齿距累积公差F P0.036毫米0.045毫米齿距极限偏差±f pt0.01毫米0.01毫米齿形相对误差的公差f c0.005毫米0.005毫米接触斑(沿齿长)50% 至70%(沿齿高)55% 至75%轴交角极限偏差±EΣ(齿宽中点处的线值)0.032毫米齿坯顶锥母线跳动公差0.025毫米0.025毫米基准端面直径25毫米320毫米齿坯基准端面跳动公差0.025毫米0.015毫米齿坯轮冠距极限偏差-0.075毫米-0.075毫米齿坯顶锥角极限偏差8分8分齿坯尺寸公差轴径IT5GB 1800--79孔径IT6GB 1800--79外径尺寸极限偏差上偏差0下偏差-IT8GB 1800--79承载能力:名义转矩T 150N·m290N·m 名义功率P 31.42kW60.75kW 小 轮转速n2000r / min1034.48r / min 材质合金钢渗碳淬火支 承 形 式大小轮都是两端支承许用接触应力ζHP1249.1N/mm21249.1N/mm2计算接触应力ζH1168.31N/mm21168.31N/mm2接触强度安全系数S H 1.34 1.34许用齿根应力ζFP798.84N/mm2797.17N/mm2计算齿根应力ζF509.95N/mm2360.12N/mm2弯曲强度安全系数S F 1.31 1.84结论意见: ·安全系数过大,造成浪费!·重合度符合要求。
齿轮副侧隙计算方法

润滑方式 油池润滑
喷油润滑
齿 轮 线 速 度%&&+:"
1#"% "%#1#(* (*#1#.%
1$.%
/-8%#& #*""%$0-
"%0(%0’%0#’%"*%$0-
注’0- 为法向模数
#($/-9是考虑齿轮传 动 的 温 度 变 化! 这 时 由 于 齿 轮 和箱体的材料不同!温度不同以及材料的线膨胀系数不 同!而使原侧隙/-8发 生 减 小 #或 增 大$! 所 以! 除 前 述 /-8外! 还需加上/-9的补偿" 所以
;%!$"&&! "理论值# 最 大 法 向 侧 隙/-&8F;/E&8F<=+!;%!.$6<=+(%1&&
;%!.%&&! "理论值# 若考虑加工及安装产生的基节$轴向$轴线平行度 和中心距偏差%则有! 最小法向侧隙/-&,-;%!$":%38% (+,-!-:4
;%!’$" "&&# 最大法向侧隙/-&8F;%!.%7%38% (+,-!-74
%!%"#
3B
% ! 基节极限偏差 3C9
?%!%(%
3C9
&!齿向公差 :’ 接触斑点 按齿高不小于
%!%(% *%D
:’ *%D
按齿长不小于 /%D
%!%"# ?%!%(% %!%(%
/%D
%!%$";%!’$* "&&# /-&8F; "%2+," 72+,( % #<=+"<=+!- 7 %38% (+,-!-
直齿圆柱齿轮变位系数、公法线长度、齿厚、最小法向侧隙的计算

外啮合直齿圆柱齿轮变位系数、公法线长度、齿厚、最小法向侧隙的计算1,直齿圆柱齿轮变位系数计算:Case1:a,此处例子仅计算用齿条型刀具加工时的情况(插齿刀加工见相关手册公式):小结:由此可知本例选取的齿数在不变位的情况也不会产生根切现象。
b,根据下图选择大小齿轮的变位系数和x∑。
本例在P6-P7区间取值。
即齿根及齿面承载能力较高区,进行选择。
因大小齿轮的齿数和为18+19=37。
所以本例选择的变位系数和x∑=0.8。
本例我们的两个齿轮在工作时属于减速运动,所以按减速运动的变位系数分配线图,进行2个齿轮的变位系数的选择。
先按(z1+z1)/2=18.5,作为横坐标,做一条垂线(图中蓝色的线),再按x∑/2=0.4,作为纵坐标,做一条水平线(图中橙色的线),接着沿着L线的趋势,穿过上面2条线的交点做一条射线(图中红色的线)最后按大小齿轮的齿数做相应的垂线(图中紫色的线),即得到需要的各自变位系数。
最后我们选择的变位系数即为:小齿轮x1=0.42,大齿轮x2=0.38。
【基本保障其和与之前x ∑一致,即可】。
c,验算变位后的齿顶厚度:注:一般要求齿顶厚Sa≥0.25m;对于表面淬火的齿轮要求Sa≥0.4m下表中的da的计算见后面的计算表格中的计算公式(因为当齿轮变位后,齿顶圆的计算和未变位齿轮的计算稍有差别-涉及到变位系数和中心距变位系数。
)。
分度圆直径db mm 73.8 77.9齿轮的齿顶圆直径da mm 83.027 86.799齿轮的齿顶压力角αa °27.27 26.17中间值invα0.0215 0.0215中间值invαa 0.0587 0.0347齿顶厚Sα 5.77 7.47判断值0.25m 1.025 1.025判断值0.4m 1.64 1.64小结:计算发现变位后的齿轮齿顶厚满足设计需求。
根据上面确定的变位系数,计算齿轮的中心距变位系数和节圆直径、齿根圆直径、齿顶圆直径。
精密齿轮传动中齿轮副侧隙的调整方法

精密齿轮传动中齿轮副侧隙的调整方法标题:精密齿轮传动中齿轮副侧隙的调整方法在精密齿轮传动系统中,齿轮副的侧隙对于确保传动精度和平稳性至关重要。
合理的侧隙调整可以降低齿轮运行时的噪音,减少磨损,并提高系统的整体性能。
本文将详细介绍在精密齿轮传动中调整齿轮副侧隙的具体方法。
一、齿轮副侧隙的重要性齿轮副侧隙,即齿轮在非接触状态下的间隙,对于齿轮传动系统的性能有着直接影响。
适当的侧隙可以保证齿轮在运行过程中有足够的空间进行热膨胀,以及补偿制造和安装过程中的误差。
过大的侧隙会导致传动不稳定,产生冲击和噪声,而侧隙过小则可能导致齿轮卡死,增加磨损。
二、齿轮副侧隙的调整方法1.齿轮副的选配在齿轮副制造过程中,首先应通过精确的加工和测量,确保齿轮的基体尺寸和齿形精度。
在装配前,应根据实际应用需求,选择合适的侧隙范围,然后进行齿轮副的选配。
选配时可以通过以下方法:a.根据齿轮的实际尺寸和公差,选择相应的齿轮副进行匹配。
b.使用塞尺或千分尺等量具,测量齿轮副的侧隙,确保其在规定范围内。
2.调整齿轮副侧隙的方法a.调整齿轮位置:通过移动齿轮的位置,改变齿轮副的侧隙。
如采用调整垫片、调整螺钉等方式。
b.修磨齿轮齿面:在齿轮齿面进行微量修磨,以改变齿轮副的侧隙。
此方法需注意齿面修磨量的控制,避免过度修磨。
c.调整齿轮轴的安装位置:通过调整齿轮轴的安装位置,改变齿轮副的侧隙。
3.侧隙检测与验证在调整齿轮副侧隙后,需进行侧隙检测与验证,确保侧隙在规定范围内。
常用的检测方法有:a.塞尺法:将塞尺插入齿轮副的齿隙中,测量侧隙大小。
b.千分尺法:使用千分尺测量齿轮副的侧隙。
c.涂色法:在齿轮副的齿面涂上颜色,通过齿轮运转后的颜色变化判断侧隙是否均匀。
三、总结在精密齿轮传动中,合理调整齿轮副侧隙对于提高系统的传动性能具有重要意义。
通过精确的齿轮副选配、调整齿轮位置、修磨齿面等方法,可以有效地控制齿轮副的侧隙,确保传动系统的稳定性和可靠性。
第五节 渐开线圆柱齿轮的啮合计算
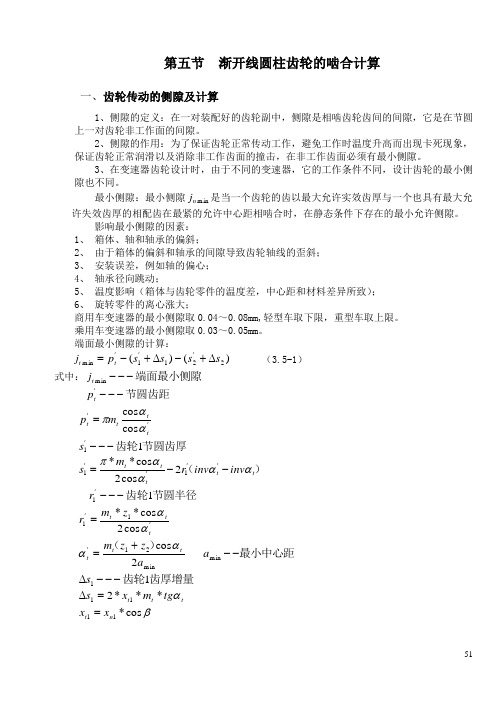
第五节 渐开线圆柱齿轮的啮合计算一、齿轮传动的侧隙及计算1、侧隙的定义:在一对装配好的齿轮副中,侧隙是相啮齿轮齿间的间隙,它是在节圆上一对齿轮非工作面的间隙。
2、侧隙的作用:为了保证齿轮正常传动工作,避免工作时温度升高而出现卡死现象,保证齿轮正常润滑以及消除非工作齿面的撞击,在非工作齿面必须有最小侧隙。
3、在变速器齿轮设计时,由于不同的变速器,它的工作条件不同,设计齿轮的最小侧隙也不同。
最小侧隙:最小侧隙min n j 是当一个齿轮的齿以最大允许实效齿厚与一个也具有最大允许失效齿厚的相配齿在最紧的允许中心距相啮合时,在静态条件下存在的最小允许侧隙。
影响最小侧隙的因素: 1、 箱体、轴和轴承的偏斜;2、 由于箱体的偏斜和轴承的间隙导致齿轮轴线的歪斜;3、 安装误差,例如轴的偏心;4、 轴承径向跳动;5、 温度影响(箱体与齿轮零件的温度差,中心距和材料差异所致);6、 旋转零件的离心涨大;商用车变速器的最小侧隙取0.04~0.08mm,轻型车取下限,重型车取上限。
乘用车变速器的最小侧隙取0.03~0.05mm 。
端面最小侧隙的计算:)()(2211min s s s s p j t t ∆+-∆+-=''' (3.5-1) 式中:端面最小侧隙---min t j节圆齿距---'t p''=tttt m p ααπcos cos 节圆齿厚齿轮11---'s)(t t tt t inv inv r m s ααααπ--=''''112cos 2cos ** 节圆半径齿轮11---'r''=t tt z m r ααcos 2cos **11min212cos a z z m tt t αα)(+=' 最小中心距--min a 齿厚增量齿轮11---∆s t t t tg m x s α***211=∆ βcos *11n t x x =nn n t m n tg z z z m dp inv inv x αααα221cos 11111)(+--=)奇数齿(或)偶数齿(!!111111190cos *cos cos cos cos z M z m M z m MAx t t m MAxtt m αααα--==式中:(奇数齿)或(偶数齿)dp z z M M dp z M M m tt MAX m tt MAX +⎪⎪⎭⎫ ⎝⎛=+=111111190cos cos cos **cos cos **αααα节圆齿厚齿轮22---'s)(t t tt t inv inv r m s ααααπ--=''''222cos 2cos ** 节圆半径齿轮22---'r''=ttt z m r ααcos 2cos **22 齿厚增量齿轮22---∆s t t t tg m x s α***222=∆ βcos *22n t x x = nn n t m ntg z z z m dp inv inv x αααα221cos 22222)(+--=)奇数齿(或)偶数齿(22212121290cos *cos cos cos cos z M z m M z m MAx tt m MAxtt m αααα--==(奇数齿)或(偶数齿)dp z z M M dp z M M m tt MAXm tt MAX +⎪⎪⎭⎫ ⎝⎛=+=222222290cos cos cos **cos cos **αααα法向最小侧隙的计算:‘''⨯⨯=t t n j j αβcos cos min min'β--节圆螺旋角''⨯=tttg tg ααββcos cos 最大侧隙的计算:将式(3.5-1)中的min a 替换成MAX a ,将MAX M 替换成MIN M 即可计算出最大侧隙。
齿轮侧隙及齿厚偏差自动计算表
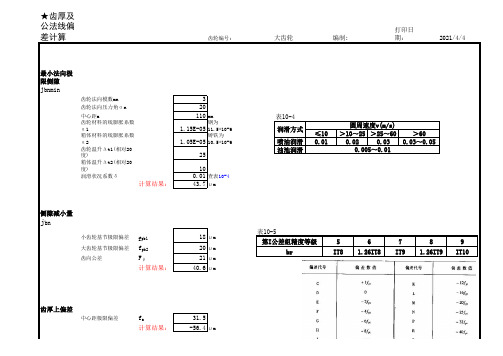
Ess
-66.0 μm
Esi
-176.0 μm
Ess*cosα n0.72Fr*sin αn
计算结果: Esi*cosα n+0.72Fr*s inαn 计算结果:
-75.80997 μm -151.5956 μm
Ewms/(sin αMt*cosβ b) 计算结果 Ewms/(sin αMt*cosβ b)*cos(π /2z)
★齿厚及 公法线偏 差计算
最小法向极 限侧隙
jbnmin
jnmin=1000* a(α1*Δ
t1-α2*Δ
t2)*2*sin
αn+δ
*mn*1000
齿轮法向模数mn
齿轮法向压力角αn
中心距a 齿轮材料的线膨胀系数 α1 箱体材料的线膨胀系数 α2 齿轮温升Δt1(相对20 度) 箱体温升Δt2(相对20 度)
>60
喷油润滑 0.01
0.02
0.03 0.03~0.05
油池润滑
0.005~0.01
表10-5 第I公差组精度等级 br
5
6
7
8
9
IT8 1.26IT8 IT9 1.26IT9 IT10
齿厚公差
齿圈径向跳动公差
径向切深公差
齿厚下偏差
齿距极限偏差Fpt 齿厚上偏差/Fpt 齿厚下偏差/Fpt
Ts=2*tanα n*(Fr^2+br ^2)^0.5 Fr
-180.9787
偶数齿
本表不属 于国家标 准,仅供 注:1 参考.
2 αMt1= 25 3 螺旋角β 8.1094
见标准齿轮 参数计算
4
βb= 0.132949
齿轮副最大与最小侧隙的计算

齿轮副最大与最小侧隙的计算齿轮副的侧隙是指齿轮副两齿轮齿廓间的间隙,它是齿轮副正常运转时所必需的重要参数之一、侧隙的大小直接影响齿轮副的传动效率、传动精度、噪音和寿命等性能。
因此,在设计和制造齿轮副时,必须合理计算齿轮副的最大和最小侧隙。
齿轮副的侧隙可分为两种情况进行计算,即直齿轮副和斜齿轮副。
一、直齿轮副的最大和最小侧隙计算方法:直齿轮副的最大和最小侧隙是通过计算法向侧隙和径向侧隙来确定的。
1.法向侧隙计算:法向侧隙是指齿轮两齿廓垂直于齿轮轴线方向的侧隙大小,一般用等效径向侧隙来表示。
法向侧隙等效于一个半径为r的圆上的弧长s,通过下式计算:s=π*r*ε/180其中,π为圆周率,ε为齿轮的法向侧隙角(单位为度),r为齿轮的基圆半径。
2.径向侧隙计算:径向侧隙是指齿轮两齿廓平行于齿轮轴线方向的侧隙大小,一般用法线模数mn与齿数z来计算。
径向侧隙等于模数mn与齿数z的乘积,通过下式计算:e=m*n其中,m为法线模数,n为齿数,e为齿轮的径向侧隙。
最大侧隙:最大侧隙为法向侧隙与径向侧隙之和。
最小侧隙:最小侧隙为法向侧隙减去径向侧隙。
二、斜齿轮副的最大和最小侧隙计算方法:斜齿轮副的最大和最小侧隙的计算方法与直齿轮副有所不同,需要考虑齿轮副的斜面系数。
1.法向侧隙计算:法向侧隙通过法向侧隙系数Kn乘以齿轮的法向分度圆压力角tanφ来计算。
法向侧隙等于法向侧隙系数Kn乘以齿轮的法向分度圆压力角tanφ,通过下式计算:s = Kn * tanφ其中,Kn为法向侧隙系数,tanφ为齿轮的法向分度圆压力角,s为齿轮的法向侧隙。
2.径向侧隙计算:径向侧隙的计算与直齿轮副相同,通过模数mn与齿数z的乘积计算。
径向侧隙等于模数mn与齿数z的乘积,通过下式计算:e=m*n其中,m为法线模数,n为齿数,e为齿轮的径向侧隙。
最大侧隙:最大侧隙为法向侧隙与径向侧隙之和。
最小侧隙:最小侧隙为法向侧隙减去径向侧隙。
需要注意的是,在实际的齿轮副设计和制造过程中,还需要考虑齿轮副的加工误差、装配误差以及工作环境等因素的影响,从而对最大和最小侧隙进行一定的修正。
齿轮圆周侧隙计算公式
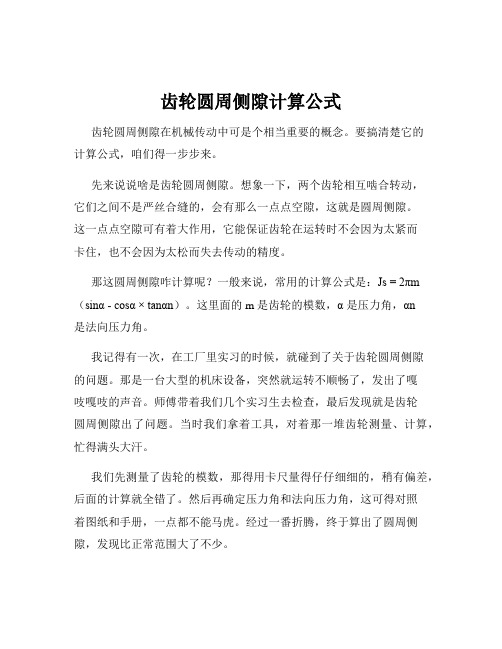
齿轮圆周侧隙计算公式齿轮圆周侧隙在机械传动中可是个相当重要的概念。
要搞清楚它的计算公式,咱们得一步步来。
先来说说啥是齿轮圆周侧隙。
想象一下,两个齿轮相互啮合转动,它们之间不是严丝合缝的,会有那么一点点空隙,这就是圆周侧隙。
这一点点空隙可有着大作用,它能保证齿轮在运转时不会因为太紧而卡住,也不会因为太松而失去传动的精度。
那这圆周侧隙咋计算呢?一般来说,常用的计算公式是:Js = 2πm (sinα - cosα × tanαn)。
这里面的 m 是齿轮的模数,α 是压力角,αn是法向压力角。
我记得有一次,在工厂里实习的时候,就碰到了关于齿轮圆周侧隙的问题。
那是一台大型的机床设备,突然就运转不顺畅了,发出了嘎吱嘎吱的声音。
师傅带着我们几个实习生去检查,最后发现就是齿轮圆周侧隙出了问题。
当时我们拿着工具,对着那一堆齿轮测量、计算,忙得满头大汗。
我们先测量了齿轮的模数,那得用卡尺量得仔仔细细的,稍有偏差,后面的计算就全错了。
然后再确定压力角和法向压力角,这可得对照着图纸和手册,一点都不能马虎。
经过一番折腾,终于算出了圆周侧隙,发现比正常范围大了不少。
找到了问题所在,接下来就是调整。
这可不是个轻松的活儿,得一点点地调试,边调试边测量,直到圆周侧隙达到合适的范围。
经过那次经历,我对齿轮圆周侧隙的计算公式有了更深刻的理解。
可别小看这公式,它能让机械运转得稳稳当当,不出差错。
在实际的工程应用中,准确计算齿轮圆周侧隙至关重要。
如果侧隙过大,会导致传动精度降低,产生振动和噪声;侧隙过小,又会增加摩擦,甚至导致齿轮咬死。
所以,掌握好这个计算公式,并且能够准确地测量和调整,对于机械工程师来说,那可是必备的技能。
总之,齿轮圆周侧隙的计算公式虽然看起来有点复杂,但只要我们认真对待,多实践、多琢磨,就能熟练运用,让齿轮在机械传动中发挥出最佳的性能。
齿轮侧隙及齿厚偏差自动计算表
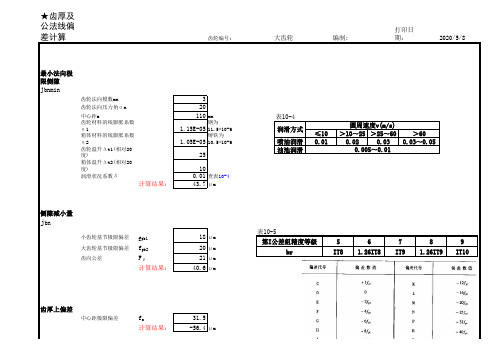
★齿厚及公法线偏差计算齿轮编号:编制:打印日期:最小法向极限侧隙j bnmin j nmin =1000*a(α1*Δt1-α2*Δt2)*2*sin αn+δ*m n *1000齿轮法向模数mn 3齿轮法向压力角αn 20 中心距a 110mm 齿轮材料的线膨胀系数α1 1.15E-05钢为11.5*10-6箱体材料的线膨胀系数α2 1.05E-05铸铁为10.5*10-6齿轮温升Δt1(相对20度)25箱体温升Δt2(相对20度)10润滑状况系数δ0.01查表10-4计算结果:43.7μm 侧隙减小量j bnJn=(F pb 1^2+F pb 2^2+2.104*F β^2)^0.5小齿轮基节极限偏差f pb118μm 大齿轮基节极限偏差f pb220μm 齿向公差F β21μm 计算结果:40.6μm 齿厚上偏差Ess=-((j nmin +J n )/(2cos αn)+fa*tan αn)中心距极限偏差f a 31.5计算结果:-56.4μm 齿厚公差Ts=2*tan αn*(Fr^2+br^2)^0.5齿圈径向跳动公差Fr 56径向切深公差br 145根据分度圆直径从表10-5查取计算计算结果:113.1μm 齿厚下偏差Esi=Ess-Ts 齿距极限偏差Fpt22.0μm 齿厚上偏差/Fpt-2.6-3按齿厚极限偏差表取整齿厚下偏差/Fpt-7.7-8按齿厚极限偏差表取整计算结果:-169.5μm 齿厚上偏差取值:Ess -66.0μm 注:1本表不属于国家标准,仅供参考.齿厚下偏差取值:Esi -176.0μm 2αMt1=25见标准齿轮参数计算3螺旋角β=8.1094公法线平均长度上偏差EwmsEss*cos αn-0.72Fr*sin αn 4βb=0.132949计算结果:-75.80997μm 5齿数z=20大,小齿轮分别计算公法线平均长度下偏差Ewmi Esi*cos αn+0.72Fr*sinαn 计算结果:-151.5956μm 2016/12/20大齿轮表10-4≤10>10~25>25~60>60喷油润滑0.010.020.030.03~0.05油池润滑圆周速度v(m/s)润滑方式0.005~0.01表10-5第I 公差组精度等级56789br IT8 1.26IT8IT9 1.26IT9IT10。
齿轮副的精度指标和侧隙指标讲解

齿轮传动是通过齿轮副实现的,其误差 直接影响齿轮的使用要求。对齿轮副的检验, 是按设计中心距安装后进行的一种综合检验, 从满足齿轮使用要求出发,规定的齿轮副检 验参数有中心距极限偏差和轴线的平行度偏 差,接触斑点,侧隙等。
11.3.1齿轮副的精度 1.中心距极限偏差fa:
因为齿轮为机床主轴箱的传动齿轮,由表11-13 可大致得出齿轮精度在3-8级之间.而 V=πdn1/1000×60=(3.14×2.75×26×1650)/1000×60
=6.2m/s
参考表11-14确定该齿轮为7级精度,表示为
7GB/T100095.1-2001
2确定侧隙和齿厚偏差
中心距 a= m/2(Z1+Z2)=2.75/2(26+56)=112.75mm 由公式11-1得:
轴线平面:包含用两
轴承跨距中较长的一根轴 线和另一轴上的一个轴承 中心所形成的平面。
(2)轴线平行度偏差 f 和 f
轴线平面内的平行度偏差f是在两轴线的公
共平面上测量的,此公共平面是用两轴承跨距中
较长的一个L和另一根轴上的一个轴承来确定的。
如果两个轴承的跨距相同,则用小齿轮轴和大齿
轮轴的一个轴承确定。垂直平面上的平行度偏差
Fr=0.03mm
由11-3 和2-2表查: br=IT9=0.074mm Tsn =√Fr²+br²2tan αn = 0.058mm Esni = Esns-Tsn = - 0.071-0.058= - 0.129mm
f
是在与轴线公共平面相垂直的平面上测量的。
f 和 f的最大推荐值为:
式中,L为轴承跨距,b为齿宽。
(3)接触斑点
接触斑点是指装配好的齿轮副,在轻微的制
弧锥齿铣齿计算表格

-33.913 -0.60078 -0.79941
0.099418 -12.4747 0.995818 -0.04985 0.995818 -0.04985 0.707107 22.53278 0.639546 0.768753 0.863311 1.146317
弧齿锥齿轮铣齿计算表格 何顺洪2022.08.12
大轮齿数 小轮齿数 大端模数 压力角 中点螺旋角 齿宽 小轮变位系数 大轮节圆直径 小轮节圆直径 大端锥距 端面周节 大轮外端齿根高 大轮外端齿顶高 小轮外端齿根高 小轮外端齿顶高 大轮节锥角 大轮根锥角 大轮齿根角 小轮节锥角 小轮根锥角 大轮齿根角 小轮齿根角 大端齿厚 最小侧隙 最大侧隙 计算刀号 按附表选取刀号 △N 中点锥距 内锥距 小轮中点齿根高 大轮中点齿根高 小轮内端齿根高 大轮内端齿根高 初算刀盘直径 按附表选取刀盘直径 外端螺旋角 内端螺旋角 大轮计算刀错距 按848 4.471484342 3.575199787 3.605914487 5.065297338 6.74689716
1:05 1:01 0.625 0.558935543 0.771770364 0.446899973 0.450739311 0.633162167 0.843362145 0.776646214 0.694315168 0.694552277 0.959028051 0.555333076 0.560103967 0.911362408 0.914224087 7.100765386
大轮用切入法粗切滚比检查值
大轮精切滚比检查角
小轮粗切滚比检查角
小轮凹面精切滚比检查角
减速机点检实务(第二版)

目录减速机分类及基本结构———————————————————————————2 减速机点检要点——————————————————————————————3 齿轮副安装要求——————————————————————————————5 接触斑点检查要点—————————————————————————————5 齿侧间隙要求———————————————————————————————7 齿侧间隙检查方法—————————————————————————————9 减速机安装及调整要点———————————————————————————10 偏心套的应用———————————————————————————————11 典型齿轮磨损和损伤————————————————————————————12减速机分类ЁЭ※¤分类方法减速机类型传动类型齿轮减速机、蜗杆减速机、行星减速机以及组合的减速机传动级数单级和多级减速机齿轮形状圆柱齿轮、圆锥齿轮和圆锥—圆柱齿轮减速机布置形式展开式、分流式和同轴式减速机基本结构减速机主要由传动零件(齿轮或蜗杆)、轴、轴承、箱体及附件所组成,图1举例说明其基本构造。
1—箱座2—箱盖3—上下箱连接螺栓4—通气件5—检查孔6——吊环7—定位销8—油标尺9—放油孔10—键11—油封12—齿轮轴13—挡油盘14—轴承15—轴承端盖16—轴17—齿轮18—轴套图1 减速机基本结构1、 速箱体是常见的一种齿轮箱体,将铸造结构改为焊接结构是箱体结构设计的趋势,采用焊接结构可以使齿轮箱制造成本降低,结构紧凑,对于重载齿轮箱要重视其焊缝的检查。
2、 检查减速机运转中的噪音以及异音情况。
3、 轴承温升检查,可以通过手感方式,也可以通过简易测温笔进行测量,一般的判定润滑油温升不得超过35度,轴承温升不得超过40度,如不正常应停机检修4、 轴承振动检查,要求在轴承座部位测量,可以通过简易的测振笔进行测量,一般测量振动速度:轴向、垂直、水平三个方向测量。
齿轮参数计算表

0.47
0.135045625 1
0.027163502 0.035457701
1 1.000880289
900
1.293426574 1.293426574
1.05 0.895121983 1.258990703 1.272792206 5222285.098 0.814271435 1.017060626 1.017060626 1.017060626 1.028136959
9 1 0.925
承受单向脉动负荷
1
0.7 0.9 0.8 1 1 0.910884442 0.85
接触应力基本值
σho
计算接触应力
σh
齿根弯曲应力基本值
σfo
计算弯曲应力
σf
接触安全系数
SH
弯曲安全系数
SF
1951.597452 2239.368791 1186.687513 1520.855224
无干涉刀具最大齿顶圆角 基节极限偏差 齿形公差 螺旋线公差
切向力 输入齿轮节圆线速度
传动比 负载分配系数 单位齿宽柔度 单对齿刚度理论值
啮合刚度 基本齿廓系数 齿形平均直径
诱导质量 主动齿轮临界转数
临界转数比
齿距偏差对Kv影响系数 齿形误差对Kv影响系数 周期性变化对Kv影响系数 扭转共振对Kv影响系数
20 20 1 0.4 9 右 角度变位 0.3975
6 0.054 0.027 0.017 0.028 0.044 900
68
-0.233 -0.387
3 158.849 -0.229 -0.375
Jn
0.36--0.669
Da
460.236
d
齿轮侧隙计算

一jn1
1补偿热变形法向侧隙jn1 um-0.01
2箱体(铝合金)线膨胀系数(α2) 1/℃0.00
3齿轮线膨胀系数(α1)1/℃0.00
4箱体温差(Δt2)℃20.00
5齿轮温差(Δt1)℃20.00
6法向压力角(αn)20.00
7中心距 a mm63.00二、jn2
保证齿轮间润滑油膜形成的侧隙jn20.02
模数 m 2.00
齿数 z32.00
发动机转速 n rpm8500.00
角速度 ω /s890.12
分度圆直径 d mm64.00
圆周速度 ν m/s28.48三、 k
算法1齿轮副安装引起的侧隙减少量 um0.01738925算法2齿轮副安装引起的侧隙减少量 um0.01738867
fpb10.0075
fpb20.0075
Fβ0.0095
fx0.0095
fy0.00475四、jnmin
考虑热态后侧隙最小侧隙0.03冷态下侧隙0.04考虑齿厚、中心距、安装
等0.09581976五、齿厚极限偏差的确定
保证最小侧隙量的齿厚实际上偏差 Ess'-0.0308132
中心距极限偏差 fa0.03
nss-4.1084272
对应齿厚公差代号F
保证最小侧隙量的齿厚实际下偏差 Esi'-0.0681763
齿轮侧隙公差 Ts0.03736308
齿圈径向跳动公差 Fr0.036
切齿进刀公差 br0.01
nsi-9.0901717
对应齿厚公差代号J
六、公法线极限偏差的确定
公法线上偏差 Ews-0.0378201
公法线下上偏差 Ewi-0.0551996。
齿轮副法向齿侧间隙的计算与检测[整理版]
![齿轮副法向齿侧间隙的计算与检测[整理版]](https://img.taocdn.com/s3/m/e8e11239443610661ed9ad51f01dc281e53a568b.png)
齿轮副法向齿侧间隙的计算与测量一、齿轮副法向侧隙的计算为保证齿轮副始终呈单面啮合的正常运转。
其工作齿面之间需有油膜润滑,而非工作齿面之间则要考虑到温升变形的影响,故齿轮副的工作齿面间和非工作齿面间都应有一足够而不过大的最小侧隙。
前者用于储油,后者用于弥补热膨胀所需。
这两者最小法向值之和称为齿轮副的最小法向齿侧间隙(简称最小侧隙jnmin) 其最小值取决于齿轮副的工作速度,润滑方式和温升。
与齿轮副的精度等级无关。
关于齿轮副的侧隙.GB10095—88规定采用基齿厚制,即利用减薄相配齿轮齿厚的办法获得。
为获得jnmin齿厚应有一最小减薄量(Ess齿厚上偏差)又因齿轮副的加工和安装不可能没有误差,如:-fpb、-fn.、Fβ和fx、fy等。
所以齿厚的最小减薄量,除取决于jnmin外还应考虑以上诸多误差都会对侧隙值产生减小的影响。
1.1齿轮副的最小法向齿侧间隙jnmin的计算:1)温升变形所需的最小法向侧隙jnmin1:jnmin1=a(α1△t1-α2△t2)×2sinαn式中:a——齿轮中心距(mm);α1,α2——齿轮和箱体材料的线膨胀系数;αn——齿轮法向啮合角;△t1,△t2——齿轮和箱体工作温度与标准温度之差:△t1=t1-20℃;△t2=t2-20℃。
2)保证正常油膜润滑所需的最小法向侧隙jn2:保证正常油膜润滑所需的最小法向侧隙jn2,取决于齿轮副的润滑方式和工作速度.当油池润滑时,jn2=(5~10)Mn(μm)。
当喷油润滑时,对于低速传动(工作速度v <10m/s ),jn2=10Mn ;对于中速传动(v =10~24m/s ),jn2=30Mn ;对于高速传动(v >60m/s ),jn2=(30~50)Mn 。
Mn 为法向模数(mm )。
所以:齿轮副最小极限侧隙(jnmin )应为:jnmin =jn1+jn21.2齿轮副实际的最小法向侧隙(安装后的侧隙)的计算Jnmin ′=|EssA+EssB|cos αn+(-fa )2sin αn-jn式中:EssA 和EssB ——AB 齿轮的齿厚上偏差;jn ——齿轮加工误差和齿轮副的安装无误差(fx ,fy )对侧隙的影响的最小量2f a ·sin αn —当齿轮副A/B 的中心距处于下偏差(-fa )时,对侧隙影响的最小值其中jn=222n 22)cos ()sin (cos 2n y n x pbB pbA f f F f f ααβ⋅+⋅++)α(+ 当=n α20°,F β=fx=2fy 时222104.2βF f f J pbB pbA n ++=1.3齿轮副最大法向侧隙jnmax 的计算:当AB 齿轮的精度等级,齿厚公差和AB 齿轮副的中心局极限偏差都确定时,jnmax 也就自然形成,一般齿轮副对其要求不严,可以免算,只作为检测的一个判定参考。
侧隙计算

1、曲轴齿轮与惰齿轮A啮合时的法向侧隙计算曲轴齿轮、惰齿轮A均是变位斜齿轮,其标准中心距计算如下:a=m n(z1+z2)/(2cosβ),已知m n=2.5,z1=21,z2=31,β=18°计算得a=68.35mm设计图纸给定安装中心距为69.77~69.82mm,查阅资料得法向侧隙计算公式为:Cn= m n(z v1+z v2)cosαn(invαn′- invαn0′)当量齿数z v1= z1/cos3β=24.42,z v2= z2/cos3β=36.05法向压力角αn=15°αn0′为两齿轮无侧隙安装时的啮合角invαn0′=2tanαn(x t1+ x t2)/(z v1+z v2)+ invαn端面变位系数x t1= x n1cosβ,x t2= x n2cosβ,已知法面变位系数x n1=0.417,x n2=0.176,则,x t1=0.397,x t2=0.167,计算得invαn0′=0.01115αn′为实际安装后的啮合角,设实际安装后的中心距为a′,有这样一个公式:a′cosαn′=a cosαn取a′=69.77mm时,αn′=18.87°,Cn=0.1853mm取a′=69.82mm时,αn′=18.99°,Cn=0.2234mm所以该对齿轮安装后的法向侧隙范围是0.1853~0.2234mm经验公式:J nbmin=2(0.06+0.0005a i+0.03 m n)/3,其中J nbmin为最小法向侧隙,a i为最小安装中心距,计算得J nbmin=0.1133mm2、凸轮轴齿轮与惰齿轮A啮合时的法向侧隙计算凸轮轴齿轮、惰齿轮A均是变位斜齿轮,其标准中心距计算如下:a=m n(z1+z2)/(2cosβ),已知m n=2.5,z1=42,z2=31,β=18°计算得a=95.95mm设计图纸给定安装中心距为96.49~96.54mm,查阅资料得法向侧隙计算公式为:Cn= m n(z v1+z v2)cosαn(invαn′- invαn0′)当量齿数z v1= z1/cos3β=48.84,z v2= z2/cos3β=36.05法向压力角αn=15°αn0′为两齿轮无侧隙安装时的啮合角invαn0′=2tanαn(x t1+ x t2)/(z v1+z v2)+ invαn端面变位系数x t1= x n1cosβ,x t2= x n2cosβ,已知法面变位系数x n1=0.002,x n2=0.176,则,x t1=0.0019,x t2=0.167,计算得invαn0′=0.00722αn′为实际安装后的啮合角,设实际安装后的中心距为a′,有这样一个公式:a′cosαn′=a cosαn取a′=96.49mm时,αn′=16.15°,Cn=0.1005mm取a′=96.54mm时,αn′=16.26°,Cn=0.1357mm所以该对齿轮安装后的法向侧隙范围是0.1005~0.1357mm经验公式:J nbmin=2(0.06+0.0005a i+0.03 m n)/3,其中J nbmin为最小法向侧隙,a i为最小安装中心距,计算得J nbmin=0.1222mm3、惰齿轮B与惰齿轮A啮合时的法向侧隙计算惰齿轮B不是变位齿轮,但可以看成是法面变位系数x n1=0的变位斜齿轮,惰齿轮A是变位斜齿轮,其标准中心距计算如下:a=m n(z1+z2)/(2cosβ),已知m n=2.5,z1=29,z2=31,β=18°计算得a=78.86mm设计图纸给定安装中心距为79.29~79.34mm,查阅资料得法向侧隙计算公式为:Cn= m n(z v1+z v2)cosαn(invαn′- invαn0′)当量齿数z v1= z1/cos3β=33.72,z v2= z2/cos3β=36.05法向压力角αn=15°αn0′为两齿轮无侧隙安装时的啮合角invαn0′=2tanαn(x t1+ x t2)/(z v1+z v2)+ invαn端面变位系数x t1= x n1cosβ,x t2= x n2cosβ,已知法面变位系数x n1=0,x n2=0.176,则,x t1=0,x t2=0.167,计算得invαn0′=0.00743αn′为实际安装后的啮合角,设实际安装后的中心距为a′,有这样一个公式:a′cosαn′=a cosαn取a′=79.29mm时,αn′=16.12°,Cn=0.0390mm取a′=79.34mm时,αn′=16.24°,Cn=0.0678mm所以该对齿轮安装后的法向侧隙范围是0.0390~0.0678mm经验公式:J nbmin=2(0.06+0.0005a i+0.03 m n)/3,其中J nbmin为最小法向侧隙,a i为最小安装中心距,计算得J nbmin=0.1164mm。
- 1、下载文档前请自行甄别文档内容的完整性,平台不提供额外的编辑、内容补充、找答案等附加服务。
- 2、"仅部分预览"的文档,不可在线预览部分如存在完整性等问题,可反馈申请退款(可完整预览的文档不适用该条件!)。
- 3、如文档侵犯您的权益,请联系客服反馈,我们会尽快为您处理(人工客服工作时间:9:00-18:30)。
a(mm)а1∆t1(℃)а2∆t2(℃)
3000.0000122600.000011160
j n1 =0.07(mm)
j n2 =0.013544(mm)
j nmin =0.083544(mm)齿轮副的最小极限间隙侧隙
a齿轮副中心距
а1齿轮线膨胀系数,查手册
∆t1齿轮工作时相对于基准温度(20℃)的温升(即由测量温度减去20℃)
а2箱体线膨胀系数,查手册
∆t2箱体工作时相对于基准温度(20℃)的温升(即由测量温度减去20℃)
Fr1br1Fr2br2fa
0.0860.1260.10.19530.0405
T s1=2tanаn√Fr1^2+br1^2=0.1110485(mm)小齿轮齿厚公差
T s2=2tanаn√Fr2^2+br2^2=0.1597196(mm)小齿轮齿厚公差
T j =√(T s1cosаn)^2+(T s2cosаn)^2+(2fa*2sinаn)^2=0.191012(mm)侧隙公差j nmax=j nmin+T j0.274556(mm)齿轮副最大侧隙
Fr齿圈径向跳动公差,查手册(第I组公差组精度等级)
br切齿径向进刀公差,查手册(第I组公差组精度等级)
fa齿轮副的中心距公差,查手册(第II公差组精度等级)。